宣钢中型材轧机主传动调速和控制系统的应用与技术攻关
浅述轧钢自动化控制系统应用优化

浅述轧钢自动化控制系统应用优化随着社会和经济的发展,轧钢工业也在不断发展和进步。
而在轧钢工业中,自动化控制系统的应用优化是提高生产效率和质量的重要手段。
本文将浅述轧钢自动化控制系统应用优化的相关内容。
轧钢自动化控制系统应用优化可以提高生产效率。
传统的轧钢生产过程中,大部分工作都是通过人工操作完成的,不仅效率低下,而且容易出现操作失误。
而自动化控制系统的应用可以实现生产线的自动化运行,减少人工操作,提高生产效率。
在轧钢生产线上,可以通过自动控制系统实现轧辊的自动调整和轧辊间隙的自动控制,从而提高轧材的生产速度和质量。
轧钢自动化控制系统应用优化可以提高产品质量。
在轧钢生产过程中,轧辊的调整和轧辊间隙的控制是影响产品质量的关键因素。
传统的人工操作存在调整不准确和间隙不均匀等问题,容易导致产品的不良率增加。
而自动化控制系统可以实时监测轧辊的位置和轧辊间隙,通过自动调整控制系统对轧辊的位置和轧辊间隙进行精确控制,确保产品质量的稳定和一致性。
轧钢自动化控制系统应用优化还可以降低生产成本。
传统的轧钢生产过程中,人工操作需要大量的人力资源,并且存在操作失误和调整不准确等问题,增加了企业的生产成本。
而自动化控制系统的应用可以减少人工操作,降低了人力资源的投入,并且通过精确的控制调整,减少了废品和不良品的产生,降低了生产成本。
轧钢自动化控制系统应用优化可以提高生产效率、产品质量和生产线的安全性,同时也可以降低生产成本。
在轧钢工业中,积极推进自动化控制系统的应用优化是一个重要的任务。
还需要不断研究和开发新的自动化控制技术和设备,不断提高轧钢生产线的自动化程度和智能化水平,以适应市场的需求和发展的要求。
天钢中厚板粗轧机压下电机的交-直-交变频调速控制系统

整 桥反 桥 流 馈
由 + 臼_
F6 3
l 兰
P E= l
图 I 交一 交变频调速控制系统图 直一
3 SD P MR整 流 回馈 装 置的基 本原理 2 SD R主要应用于异步 电机 的传动系统 中, 以 PM 可
3 交一 一 直 交变频 调 速控 制 系统
轧制工艺压下规程的要求 。压下装置 由两 台交流 电动
机通 过蜗轮蜗杆减速 机 。 带动压 下螺丝转 动来 实现压
编码 器进行 速度反 馈 , 实现 了 F C矢量控制 , O 保证 了 压下量 的准确性 。 直一 变频 调速控制系统见 图 1 交一 交 。
主要元件 的型号 :
sD P MR整流 回馈 3 S 2 0 /5 K G 5 0A7 0V 变频器 S G 2 2 7 3 D V T K Y 6 5M90V C
一 I j
“
l
l l
} _ _
”
T T
-
●
l I
棚电设苗
维普资讯
⑥ ⑤ 第 ⑥ 年 期 总 晷 第 圆期
天 中 板 轧 压 电 的 一 一变 调 控 系 钢 厚 粗 机 下 机 交 直交 频 速 制 统
制、 电流震荡补偿等 。系统图见 图 3 。
直流母线
I . v2
在其直 流母线上连接一个或 多个变 频器 。它的整流装 置是 由晶 闸管构 成两个反并联 的三相桥 组成 的 。 向 正
桥提供直流 电 , 向桥将 变频装置 产生的能量送 回主 反
电网。大多数 的整流装置仅将 电机 突然制动产生 的能
L V3
一
L1 P lP V E +
L3 v P 』 P V 气 1 E + .
河钢宣钢精轧机变频调速技术创新

the implementation method of domestic sabstitution of main drive inverter, sammarizhs the control technical
characteristics of mebium voltaoe variable freyuench speeb reyulation, aod foerses on the aoalysis of the
功率
、电机利用率低、效率低、谐波 高、电
动脉动大、动态响应慢、 缺点⑶。
复杂等 「
为满足主传动系统的改造升级,根据现场产线
的实际情况,在保
压器和动
的I
上,通过技术优化,使用电压源型 器(VSI)替换
负载换向逆变器(LCI)⑷。此次改造项目在技术上
完美适配了原LCI传动系统的
子漏抗的六相
(相差30。)同步
可以看出,应用器件保护策略,可以在系统发 2 软硬件系统
生故障前及时预判及保护,防止故障扩大化。在已 2.1变频器
发生 的情况下,其系统有序保护,相互关系,不
2.1.1变频器电流能力
产生次生故障。
变频器的功率单元采用模块化结构设计和积
1.2.2 模块轻量化设计
木式的组合2#逆变器和2#逆变器的功率单元采用
不明。精轧机主传动系统如继续升级为新一代LCI 系统,则工艺和产 法 ,如按 常用方式升
级
压源型
器(VSI),
动
,升级改 本较高⑴。
换变压器及
GL150变频器是负载换向逆变器(LCI)变频
器,
流源(CSI)特性,使用半控型晶闸管
(SCR)作为主功率器件,直流电感作为储能器件,输
浅述轧钢自动化控制系统应用优化

浅述轧钢自动化控制系统应用优化轧钢自动化控制系统是钢铁生产中的关键设备,直接影响着生产效率和产品质量。
随着现代工业技术的发展,轧钢自动化控制系统逐渐成为生产中的重要组成部分。
如何优化轧钢自动化控制系统的应用,提高生产效率,降低能耗,成为钢铁生产企业面临的重要课题。
目前,轧钢自动化控制系统在钢铁生产中已经得到广泛应用。
通过PLC(可编程逻辑控制器)、DCS(分散控制系统)、SCADA(监控和数据采集系统)等先进的自动化控制设备,可以实现对轧钢生产过程的精细化控制。
自动化控制系统可以监测和调节轧制过程中的各项参数,确保生产过程的稳定运行,提高生产效率,降低人为因素对产品质量的影响。
1. 数据采集与分析在轧钢生产中,各项工艺参数的及时准确的数据采集和分析是保证生产过程稳定运行的基础。
通过监测轧钢设备的运行状态、产品质量数据等,实现对轧钢生产过程的实时监控和数据分析。
通过对数据的深入分析,可以及时发现生产过程中的问题,预测生产设备的故障隐患,提高生产过程的稳定性和可靠性。
2. 参数调整与优化轧钢自动化控制系统可以根据生产需求实时调整轧制过程中的各项参数,以实现产品规格的精确控制。
通过优化轧制轧辊的位置、形状、轧制力等参数,实现对产品厚度、宽度、形状的精确控制。
自动化控制系统还可以通过优化轧制速度等参数,实现对产品表面光洁度、硬度等性能的提升。
3. 能耗监控与节约轧钢生产过程中,大量的能源消耗是不可避免的。
通过自动化控制系统的应用优化,可以实现对能源消耗的有效监控和管理。
通过监测轧钢设备的能耗数据,分析生产过程中的能效问题,优化生产过程中各项设备的运行状态和参数设置,实现对能源的节约和利用效率的提高。
4. 故障诊断与预防轧钢设备的故障对生产过程稳定运行造成严重影响,同时也给企业带来了巨大的经济损失。
通过自动化控制系统的优化应用,可以实现对轧钢设备的故障诊断和预防。
通过实时监测设备的运行状态和参数数据,及时发现生产设备的故障隐患,通过预测性维护等手段,实现对设备故障的预防和及时修复,保证生产过程的稳定运行。
浅述轧钢自动化控制系统应用优化
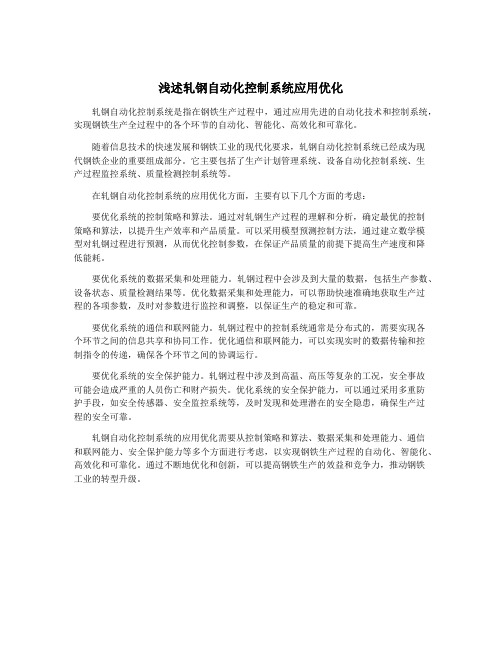
浅述轧钢自动化控制系统应用优化轧钢自动化控制系统是指在钢铁生产过程中,通过应用先进的自动化技术和控制系统,实现钢铁生产全过程中的各个环节的自动化、智能化、高效化和可靠化。
随着信息技术的快速发展和钢铁工业的现代化要求,轧钢自动化控制系统已经成为现代钢铁企业的重要组成部分。
它主要包括了生产计划管理系统、设备自动化控制系统、生产过程监控系统、质量检测控制系统等。
在轧钢自动化控制系统的应用优化方面,主要有以下几个方面的考虑:要优化系统的控制策略和算法。
通过对轧钢生产过程的理解和分析,确定最优的控制策略和算法,以提升生产效率和产品质量。
可以采用模型预测控制方法,通过建立数学模型对轧钢过程进行预测,从而优化控制参数,在保证产品质量的前提下提高生产速度和降低能耗。
要优化系统的数据采集和处理能力。
轧钢过程中会涉及到大量的数据,包括生产参数、设备状态、质量检测结果等。
优化数据采集和处理能力,可以帮助快速准确地获取生产过程的各项参数,及时对参数进行监控和调整,以保证生产的稳定和可靠。
要优化系统的通信和联网能力。
轧钢过程中的控制系统通常是分布式的,需要实现各个环节之间的信息共享和协同工作。
优化通信和联网能力,可以实现实时的数据传输和控制指令的传递,确保各个环节之间的协调运行。
要优化系统的安全保护能力。
轧钢过程中涉及到高温、高压等复杂的工况,安全事故可能会造成严重的人员伤亡和财产损失。
优化系统的安全保护能力,可以通过采用多重防护手段,如安全传感器、安全监控系统等,及时发现和处理潜在的安全隐患,确保生产过程的安全可靠。
轧钢自动化控制系统的应用优化需要从控制策略和算法、数据采集和处理能力、通信和联网能力、安全保护能力等多个方面进行考虑,以实现钢铁生产过程的自动化、智能化、高效化和可靠化。
通过不断地优化和创新,可以提高钢铁生产的效益和竞争力,推动钢铁工业的转型升级。
轧机控制系统TDC实践应用
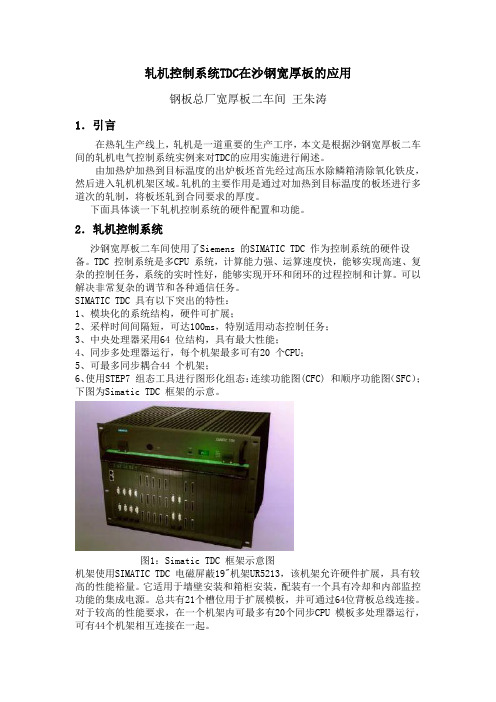
轧机控制系统TDC在沙钢宽厚板的应用钢板总厂宽厚板二车间王朱涛1.引言在热轧生产线上,轧机是一道重要的生产工序,本文是根据沙钢宽厚板二车间的轧机电气控制系统实例来对TDC的应用实施进行阐述。
由加热炉加热到目标温度的出炉板坯首先经过高压水除鳞箱清除氧化铁皮,然后进入轧机机架区域。
轧机的主要作用是通过对加热到目标温度的板坯进行多道次的轧制,将板坯轧到合同要求的厚度。
下面具体谈一下轧机控制系统的硬件配置和功能。
2.轧机控制系统沙钢宽厚板二车间使用了Siemens 的SIMATIC TDC 作为控制系统的硬件设备。
TDC 控制系统是多CPU 系统,计算能力强、运算速度快,能够实现高速、复杂的控制任务,系统的实时性好,能够实现开环和闭环的过程控制和计算。
可以解决非常复杂的调节和各种通信任务。
SIMATIC TDC 具有以下突出的特性:1、模块化的系统结构,硬件可扩展;2、采样时间间隔短,可达100ms,特别适用动态控制任务;3、中央处理器采用64 位结构,具有最大性能;4、同步多处理器运行,每个机架最多可有20 个CPU;5、可最多同步耦合44 个机架;6、使用STEP7 组态工具进行图形化组态:连续功能图(CFC) 和顺序功能图(SFC);下图为Simatic TDC 框架的示意。
图1:Simatic TDC 框架示意图机架使用SIMATIC TDC 电磁屏蔽19"机架UR5213,该机架允许硬件扩展,具有较高的性能裕量。
它适用于墙壁安装和箱柜安装,配装有一个具有冷却和内部监控功能的集成电源。
总共有21个槽位用于扩展模板,并可通过64位背板总线连接。
对于较高的性能要求,在一个机架内可最多有20个同步CPU 模板多处理器运行,可有44个机架相互连接在一起。
本框架使用的CPU 是CPU551。
I/O模板使用SM500,SM500 I/O模板提供有丰富的选项,用于连接分布式I/O。
除了16点二进制输入/ 输出以外,它还具有8 点模拟量输入/ 输出以及4 点积分型模拟量输入。
轧钢机主传动同步电机调速系统动态速降与扭振的研究
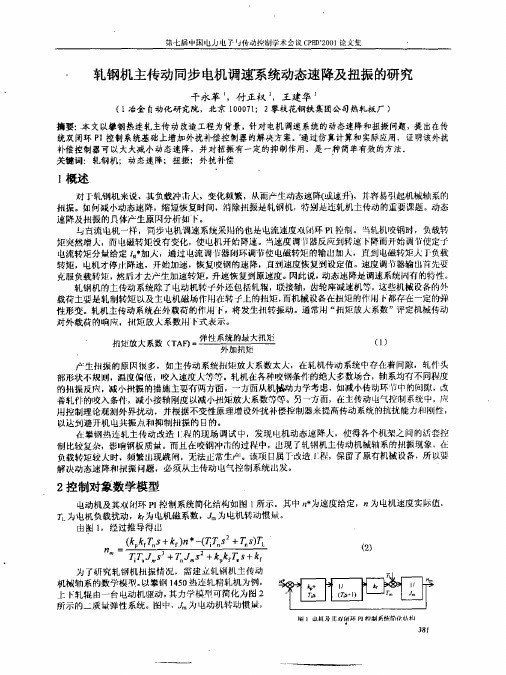
第七届中国叱山}扯了1,传动拌制学术含泼c阳D’2001论义集轧钢机主传动同步电机调速系统动态速降及扭振的研究干永革。
,付正权2,王建华2(1冶金自动化研究院,北京【0007l;2攀枝花钢铁集团公司热轧板厂)摘要:本文以肇钢熟连轧主传动政造工程为背景,针对电机调运系统的动态速降和扭振问题,提出在传统双闭环PI控制系统基础上增加外扰补偿控制器的解决方案。
‘通过仿真计算和实际应用,证明该外扰补偿控制器可以大大减小动态速降,并对扭振有一定的抑制作用,是一种简单有效的方法。
关键词:轧钢机;动态速降;扭振;外扰补偿1概述对丁轧钢机来说,其负载冲击人,变化频繁,从而产生动态速降(域速}n,并容易引起机械轴系的H振。
如何减小动态速降,缩短恢复时问,消除扭振是轧钢机,特别是连轧机士传动的重要课题。
动态速降及抖i振的贝体产生原冈分析如F。
与直流电机一样,同步电机调遣系统采Ⅲ的也是电流速度烈州环PI控制。
当轧机咬钢时,负载转矩突然增人,而Lb磁转矩没有变化,使电机开始降速。
当速度凋。
¨器反应到转述卜降而开始调1y使定子L乜流转矩分鼙给定‘·加人,通过电流调坩器闭环调:竹使电磁转矩的输山加人,直到电磁转矩人r负载转矩,电机才停fr降速,开始加速,恢复咬钢的速降.直到速度恢复到设定值。
速度调仃器输山首先要克服负载转矩,然后才去产生加述转矩,升速恢复到原述度。
冈此说,动态速降是调遮系统I朴仃的特性。
轧钢机的士传动系统除了电动机转子外还包括轧辊,联接轴,齿轮摩减速机等.这些机械设备的外载荷土要是轧制转矩以及主电机磁场作_L||在转子上的扣矩,而机械设备在捌矩的作川卜部存在一定的弹性形变。
轧机主传动系统在外载荷的作川r,将发生jI}i转振动。
通常川“手H矩放人系数”评定机械传动对外载荷的响应.{:}【矩放人系数_L|j卜式表示。
扣矩放大系数(TAF)=型型塑萼譬篓罂(¨外邪于儿m产生手H振的原因根多,如土传动系统扭矩放人系数太人.在轧机传动系统中存在着间隙.轧什头部形状不规则,温度偏低,咬入速度人等等。
控制轧制及控制冷却技术在型钢生产中的应用
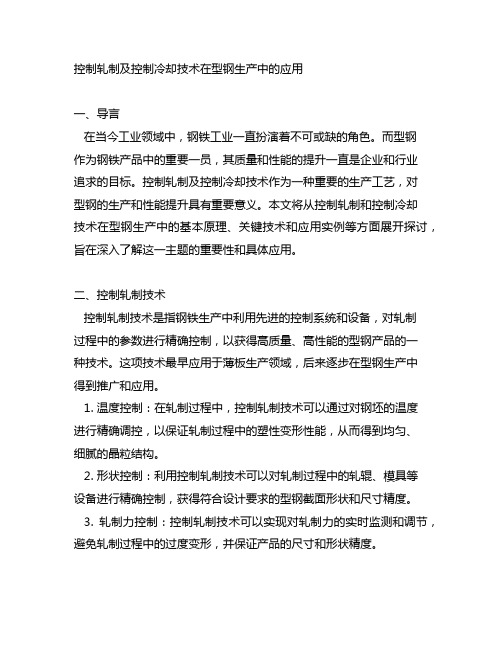
控制轧制及控制冷却技术在型钢生产中的应用一、导言在当今工业领域中,钢铁工业一直扮演着不可或缺的角色。
而型钢作为钢铁产品中的重要一员,其质量和性能的提升一直是企业和行业追求的目标。
控制轧制及控制冷却技术作为一种重要的生产工艺,对型钢的生产和性能提升具有重要意义。
本文将从控制轧制和控制冷却技术在型钢生产中的基本原理、关键技术和应用实例等方面展开探讨,旨在深入了解这一主题的重要性和具体应用。
二、控制轧制技术控制轧制技术是指钢铁生产中利用先进的控制系统和设备,对轧制过程中的参数进行精确控制,以获得高质量、高性能的型钢产品的一种技术。
这项技术最早应用于薄板生产领域,后来逐步在型钢生产中得到推广和应用。
1. 温度控制:在轧制过程中,控制轧制技术可以通过对钢坯的温度进行精确调控,以保证轧制过程中的塑性变形性能,从而得到均匀、细腻的晶粒结构。
2. 形状控制:利用控制轧制技术可以对轧制过程中的轧辊、模具等设备进行精确控制,获得符合设计要求的型钢截面形状和尺寸精度。
3. 轧制力控制:控制轧制技术可以实现对轧制力的实时监测和调节,避免轧制过程中的过度变形,并保证产品的尺寸和形状精度。
三、控制冷却技术控制冷却技术是指在型钢生产过程中,通过对冷却过程的控制,使钢材在冷却过程中获得理想的组织和性能。
这项技术的应用可以有效提高型钢的强度、韧性和耐磨性等性能,同时降低产品的变形和裂纹率。
1. 冷却介质控制:通过选择不同的冷却介质和控制冷却速度,可以使型钢获得不同的组织和性能,如马氏体组织、贝氏体组织等,从而满足不同领域对型钢性能的要求。
2. 温度控制:在控制冷却技术中,对冷却过程中的温度进行精确控制,可以有效控制组织相变,并获得理想的力学性能,如强度、韧性等。
3. 冷却速度控制:通过对型钢冷却速度进行控制,可以获得不同的组织和性能,如快速冷却可以获得细小的组织和高强度,而缓慢冷却则可以得到较好的塑性和韧性。
四、控制轧制及控制冷却技术在型钢生产中的应用实例1. 控制轧制技术在型钢生产中的应用:某钢铁企业引进了先进的控制轧制系统和设备,通过对轧制过程中的温度、形状和轧制力等参数进行精确控制,生产出了高精度、高强度的型钢产品,受到了市场的广泛认可。
大功率轧机主传动交流调速技术

大功率轧机主传动交流调速技术李崇坚冶金工业部自动化研究院1. 前言大功率轧钢机主传动要求电气传动系统具有很高动态响应和相当高的过载能力。
这一领域长期以来一直被直流电动机传动所垄断,由于直流电机存在着换向问题和换向器、电刷等部件维护工作量较大,使其在提高单机大容量、提高过载能力、降低转动惯量以及简化维护等方面受到了限制,已不能满足轧钢机向大型化、高速化方面的发展。
随着电力电子技术、微电子技术以及现代控制理论的迅速发展,在大功率轧钢机主传动领域已出现交流调速传动取代直流传动的趋势。
轧钢机是大容量高过载,快速响应的生产机械,交流变频调速不仅具有直流传动同样优越的调速性能,还有许多优于直流传动的特点。
1)单机容量不受限制众所周知,直流电机由于换向器的换向能力限制了电机的容量和速度,直流电动机的极限容量和速度之积约为106kW∙r/min,例如厚板轧机主传动直流电机功率2×8000kW(50/100r/min)已达到极限值,而交流电机单机容量可以突破这一限制,达到2×11000kW,为设备提供更大的动力。
2)体积小、重量轻、占地面积小由于交流电机结构简单、体积小、重量轻、占地面积大大减少。
而直流电机不仅单机体积大,为了减少转动惯量,常常采用双电枢或三电枢串联方式,占地面积很大。
日本某钢厂采用交交变频同步电机替代了原三电枢直流电机,电机功率同为11250kW,交流电机仅用了原直流电机1/3的占地面积。
交流电动机由于结构简单、坚固,因此有可能与机械合为一体,形成机电一体化产品,例如轧钢地下卷取机的卷取芯棒就作为同步电机的转子。
3)转动惯量小以宝钢2050mm热连轧机为例,直流主传动电动机2⨯4500kW(250/578r/min)双电枢传动,转动惯量76.8tm2,而交流主传动电动机9000kW(250/578r/min)单电枢传动,转动惯量17.2TM2,仅为直流电机的1/4.5。
4)动态响应好由于交流电机转动惯量大大减少,并且交流电机没有换向火花对过载能力的限制,电机可以具有更大的动态加速电流。
钢厂轧制辅助传动变频调速系统方案与应用分析

级调速 给定功能 , 取代 以太网网上给定的控制方式。它利 用逆 变器 的一个模拟量输入通道作 为调 速指令 ,实施对工作 辊道 的速度控 轧钢工作辊道是轧线常用 的辅传动 , 下面以某钢厂新轧钢连铸 制 ; 逆变器的两个模拟量输出通道用于显示 辊道电动机的转速值 和 连轧生产线 9 5 0粗轧可逆式轧机 的前 、 后工作辊道调速系统为例进 电流值 。外 围联锁控制 电路 , 应用 P L C进行逻辑控制 , 通过 P L C的 行 分析。 数字量输入 、 输出控制逆变器 的预充 电电路以及合闸 、 准备 、 就绪 、 2 . 1系统配置 使能 、 运行 、 故障等状态 。 某钢厂新轧钢连铸连轧生产线 9 5 0粗轧机为可逆式轧机 , 钢坯 参 考 文 献 往返输送 由前 、 后工作辊道 负责。前部 为 2 5个辊道 , 前端 5 个 辊为 【 1 ] 李长江.  ̄3 4 0 m m无缝钢管机组单辊传动定径机电气传 动 系统[ J ] . 延 伸辊道 , 机前 2 O个辊道和机后 2 0个 辊道 为工作辊 道。工作 辊道 冶金 自动 化 。 2 0 0 6 . 动作频 繁 , 起动 、 制动速度较快 , 要 求控制装 置运行可靠性 强。工作 [ 2 ] 李波. 公 共 直流母 线 系统在 钢 管生 产线 上 的应 用[ J 】 . 湖 南 冶金, 辊 道操 作系统采用无触点给定实现无级 调速 ,工作辊道 的全部 4 5 20 06 . 个辊道 , 用 3个控制器进行控制 。系统结构如图 1 所示 。 变 频器采用 的 S I MO V E R T Ma s t e r D r i v e r 6 S E 7 0系列逆变 器及 共 用直 流母线供诙系列变频器 D C — A C型 , 主要控制方式有 : 一般频 率 控制 、 矢量控制和伺服控制 于辊道电动机频繁起动 、 制动 的特点 , 选 用矢 量控制方式 。它具有磁通定 向控制功能 电方式 , 动态品质在 定的范围 内达到 了直流 电动机 的标 准。在 1 : 1 0的调速 范围内不 需要速度实 际值 的反馈 , 并 且与 电动机 的温升无关 , 能实现高 精度 的速度和转 矩控制 , 完全可以满足生产工艺 的要求。 工作辊道 的传动方式为 1 台电动机拖动 1 个辊道 。 本系统中有 2台逆变频分别拖动 l 0个辊道 , 1台逆变器拖动 5个辊 道 , 其余 2 0 个辊道 为 1台逆变器拖动 1 个辊道 。为实现 良好 的起动 、 制动的效
轧钢主机变频调速传动技术探究

轧钢主机 变频调 速传 动技术探 究
李 深 张有 琳 焦 晓东 梁 玉萍
( 山东 莱钢 集 团型钢 厂 , 山东 莱 芜 2 1 2 ) 7 16 摘 特点。 要 : 先介 绍 了 轧钢 主机 的分类 , 后探 讨 了轧钢 主机 传 动方 案 和变 频 传 动系 统 的控 制 技术 , 后分析 了轧机 的变 频 主 电机 的 首 然 最
活 动 进 行 控 制 , 其 在 实施 的过 程 中能 够 确 保 产 品 的 生 产 质 量 , 使 为其 今 后 的使 用 奠 定 基 础 。在 此 , 文 从 轧 钢 的主 机 分 类 、 本 轧钢 主 机 的传 统 方 案 、变 频 传 统 系 统 的 控 制 技 术 以及 轧机 的变 频 主
在使用 多绕组整流变压器结构的过程中,基于变压器 的容量较 大 , 电缆工程 提出了更 高的要求 , 对 这在很大程度上增加 了轧机
运 行 的成 本 。3 基 于 主 回 路 附 属 设 备 繁 多 的缘 故 , 地 面 积 大 。 ) 用 () 一 直 一 交 三 电平 P 2交 WM 变 频 方 案 。在 交一 直 一 交 三 电 平 P WM 变 频 方 案 中 ,其 运 行 的 整 体 核 心 在 于 可 关 断 电力 电 子 器 件 , 流 器 与逆 变 器 的 结 构 如 出 一 辙 , 主 回路 结构 比较 简 单 。 整 其
类型能够第一 时间响应主体系统 发生的号令 , 同时具 备极大的
调速范围 。
《 使用 说 明》 其 进 行 独 立 控 制 , 保 将 矢 量 控 制 的 优 势 充 分 发 对 确
挥 出来 。矢量 控制 的基本 思想在 于通过 交流 电动 机 的数学模 型、 求解 变量与参 数之 间的关系 , 将整个 设备运 行 中产 生 的变 量作为矢量进行控制 , 以此来对整个 力矩 进行控制 。 另外, 在矢
宣钢棒材连轧生产的速度控制

宣钢棒材连轧生产的速度控制本文简要分析了速度控制在连轧生产线的应用,及速度在连轧生产线的控制方法和措施。
标签:微张力控制;转矩电流;活套控制0 引言宣钢棒材生产线是2003年投产的一条全连续式生产线,共有18架轧机,平立交替布置,其中精轧14#、16#、18#轧机为平立转换轧机。
主轧线的设备有冷热坯上料设备、步进式加热炉、高压水除鳞、轧机、切头尾碎断剪、倍尺剪、冷床、冷剪、计数器、打捆、称重、收集。
在棒材生产中,为了保证生产的顺利进行和头尾尺寸的精度,在本生产线1#-10#架轧机采用微张力控制,11#-18#架之间采用活套控制。
在实际生产中,有诸多因素都会给速度的控制带来影响,如料型的大小、温度、钢种、以及钢坯尺寸等。
1 微张力控制在连轧生产中,张力来源于机架间的秒流量差,在实际生产中,绝对的秒流量相等是不可能完成的,这个连轧常数始终受各种因素的影响,如速度的影响、温度的影响、坯料尺寸的影响、轧槽磨损的影响及轧槽冷却的影响,甚至轧机滚动导卫也对连轧常数有影响。
微张力控制的目的就是使粗中轧机组各机架之间的轧件按微小的张力进行控制,从而保证棒材轧机轧制顺利和提高产品的质量。
微张力实际上是通过对相邻两工作机架中上游机架的电机转矩进行检测加以记忆储存,形成表示钢坯内张力大小的实际值,与设定的张力给定值加以比较的偏差。
通过比例积分控制校正上游机架的速度,协调两机架间的关系,实现微张力控制。
其控制的关键是准确测量各轧机的轧制力矩转矩,通过对相应机架的电枢转矩间接得到该值。
当本机架咬钢而未进入下一架轧机时,系统计算出的力矩是本轧机的轧制力矩值。
当钢进入下一架时,计算得到新的力矩,两力矩之差便是轧件上的张力力矩。
若偏差值为正,表示机架间为堆钢轧制,若偏差为负,表示机架间为拉钢轧制。
棒材一般采用电流-速度间接微张力控制法。
张力的变化是由金属的秒流量差引起的,而调整轧机的速度就能改变金属是秒流量,已达到控制张力的目的。
宣钢高线电机速度调节系统

宣钢高线电机速度调节系统作者:孔海超孙伟衣松泉来源:《科技风》2016年第14期摘要:直流电机是高线生产过程中的最重要的设备之一,如何实现直流电机精确调速是高线生产过程中的问题之一。
本文以西门子6RA70系列直流调速装置为背景介绍了宣钢高速线材生产线直流传动系统的组成及速度调节方式。
关键词:6RA70;直流调速装置;闭环控制;弱磁控制一、概述宣钢高速线材生产线是一条全连轧热轧生产线,其主要产品为Φ5mm~Φ12mm盘条和盘螺。
直流传动系统的构成:宣钢高速线材轧机主传动(从粗轧至预精轧共18架轧机)及部分辅传动(包括飞剪、吐丝机等)使用西门子6RA70 SIMOREG?DC?MASTER直流调速系统。
控制系统采用西门子S7-400 PLC,采用三级控制系统和两层通讯网络的模式,三级控制系统包括人机界面(西门子WINCC画面)、控制单元(PLC)和远程执行单元(包括PLC远程站、交直流调速装置等),两层通讯网络包括工业以太网和Profibus-DP网络。
直流调速系统通过Profibus-DP网络连接PLC,完成直流调速系统的控制。
二、直流电机调速控制直流主电机的调速控包括:(一)设定速度给定电机启动时能够进行平稳加速控制,调速系统由远程和本地两种方式设定。
本地设定通过在PMU操作面板选择P401参数进行电机给定设置,用于电机调试运行;远程操作通过PROFIBUS-DP写入PLC中给定的控制字,写入调速装置中,从而完成对电机速度的设定。
电机的速度设定值的100%为直流电机的最大速度,速度给定为线性斜坡,可以使得电机平稳的启动。
在电机调速控制时,系统可进行手动人工干预功能,在允许范围可以使用手动给定干预进行调速。
例如在轧钢过程中,主操作人员使用调速杆对轧钢系统进行级联调速以满足正常的榨汁需求。
(二)直流电机速度反馈直流电机的实际运行速度可使用电机后轴的速度编码器获取。
脉冲编码器测速精度高,在电机运行过程中,每转一圈发出1024个脉冲信号(轧机为1024个脉冲,飞剪为2048个脉冲)。
连轧中型平立转换轧机主传动创新与应用

转 换 共 5架 轧 机 组 成 ( 8 0mm ×3+ 7 0im x 0 0 n 2 ; 轧 机 组 由 4架 水 平 轧 机 和 4架 平 立 转 换 轧 机 )精 共 8 轧 机 组 成 ( 7 0ml 8 。 粗 轧 前 3架 主 电 架 0 n× ) 机 功 率 为 6 0k , 轧 后 4架 主 电 机 功 率 为 12 0 0 W 精 0
平立 转换 轧 机 主 传 动 布 置 方 式 为 主 电 机 与 平 轧 减速 机 通 过 鼓 型 齿 联 轴 器 连 接 , 轧 减 速 机 与 平 水 平状 态 时 的 平 立 转 换 轧 机 连 接 、 轧 减 速 机 与 立
立 式 状 态 时 的 平 立 转 换 轧 机 连 接 , 轧 减 速 机 与 平 立 轧 减 速 机 通 过 与 水 平 方 向 呈 3 。 的 鼓 型 齿 联 5角
轧钢主传动变频调速系统

轧钢主传动变频调速系统【关键】本文主要阐述了交流调速在轧机主传动上的两种方式、轧制过程主传动使用交流变频调速状况、两种变频器的技术比较等问题。
【关键词】轧钢;主传动;变频调速系统轧钢主传动是轧线上轧机及大型相关设备,它的主要特点是居于生产线关键部位,功率大,动作指标要求严格。
在轧钢生产中,电动机的调速范围宽,动态、静态的调速性能好,并对轧制时的冲击负荷,要求过载倍数高,热轧系统大部分采用直流机传动。
但存在两大缺陷:一是整流换向问题难以解决,尽管在电动机制造和维护上采取了一些措施,如全补偿直流电动机的电枢反应已被充分抵消,但重载和加减速时的换向火花仍然是难题,维护工作量、维修成本、故障率都较高;二是单电枢电动机的容量不可过大,应在5000kw以下,超过5000kw时应采用双电枢或三电枢,转动惯量GD2几倍于同容量的交流机。
如:交流变频同步电动机调速系统具有比直流调速高得多的动、静态调速性能的指标,动态速降小于20%,动态恢复时间小于70s,静态调速精度小于0.1%,能满足轧机要求较严的热连轧机精轧主传动工艺。
1、交流调速在轧机主传动上的两种方式交流调速在轧机主传动的应用一般有晶闸管交一交变频调速方式(见图1)、采用大功率可关断器件(如GTO或IGCT等)(见图2)交一直一交变频调速方式。
2、轧制过程主传动使用交流变频调速状况(1)邯钢CSP薄板坯连铸连轧。
电动机:主传动全为同步机;传动装置功率部分:晶闸管交-交变频调速装置;控制部分:全数字化控制器。
采用西门子SIMA-DYN D控制器,矢量控制技术。
(2)包钢CSP薄板坯连铸连轧。
电动机主传动全为同步机,六机架,每台电动机为7000kW;传动装置功率部分:晶闸管交-交变频调速装置;控制部分:全数字化SIMA-DYN D控制器,矢量控制技术。
(3)攀钢1450mm热轧带钢厂。
电动机:主传动全为同步机;传动装置功率部分:晶闸管交-交变频调速装置;控制部分:全数字化控制器。
钢材控制轧制技术的研究与优化

钢材控制轧制技术的研究与优化钢材控制轧制技术是现代冶金工业中一项十分关键的技术。
它能够对钢材的物理性能、化学成分、缺陷率等进行精细控制,从而获得品质更高、性能更优的钢材产品。
在未来的发展中,钢材控制轧制技术的研究与优化将是关系到钢铁行业未来发展的重要问题。
一、钢材的轧制控制技术在钢铁生产过程中,钢材的轧制控制技术是指对轧机的控制,从而精确地调节轧机工作过程中的加热温度、加压力度、轧辊角度等参数,以达到对钢材物理性能、化学成分、缺陷率等方面进行精细控制的目的。
钢材的轧制控制技术有以下几个方面的控制:1、轧制工艺流程控制:通过控制轧制过程中的加热温度、压力度和轧辊角度等参数,来调整轧制过程中的成形过程,从而使钢材的物理性能、化学成分、缺陷率等得到精细调控。
2、直线度控制:采用多种高精度测量仪器,如激光仪、光电子测距仪等对钢材在轧制过程中的直线度进行精确检测和调整。
3、表面质量控制:采用多种表面处理技术,如钢带水冷却、气体喷淋、四辊减速机、磨切边机等进行表面整形处理,以获得高品质钢材产品。
4、热力学控制:通过对钢材的加热温度、保温时间等参数进行精密调控,以降低钢材在轧制过程中的结晶温度和碳化温度,从而减少钢材的内部缺陷和杂质析出。
二、钢材轧制控制技术的研究与优化随着钢铁行业的不断发展和进步,钢材轧制控制技术研究与优化已经成为行业关注的重点。
本文将从计算机控制技术、节能减排、先进轧机设备、新材料研发等方面进行介绍。
1、计算机控制技术采用计算机控制技术已经成为现代冶金行业控制和优化钢材轧制过程的一种重要手段。
计算机控制技术集成了现代的控制算法和调节方法,可以对轧机的加热温度、加压力度、轧辊角度等参数进行高精度的控制和调节。
同时,计算机控制技术还可以对钢材的物理性能、化学成分、缺陷率等进行模拟和实验研究,从而为轧制过程的优化提供科学依据。
2、节能减排随着全球气候变暖和环境保护意识的提高,节能减排已经成为现代冶金行业探索的方向。
交流变频调速在轧机传动上值得推广应用
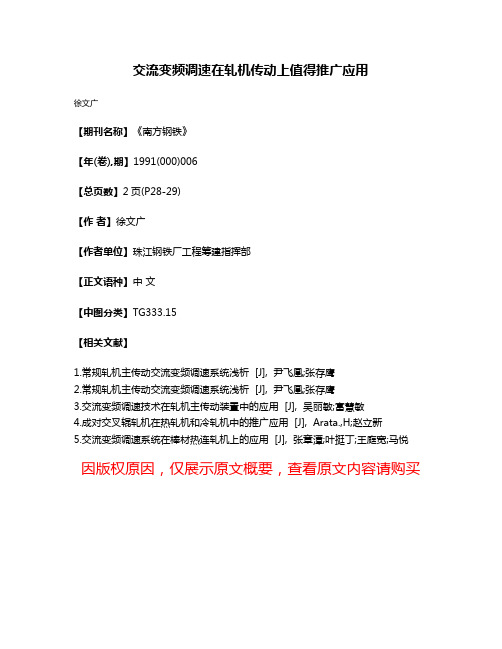
交流变频调速在轧机传动上值得推广应用
徐文广
【期刊名称】《南方钢铁》
【年(卷),期】1991(000)006
【总页数】2页(P28-29)
【作者】徐文广
【作者单位】珠江钢铁厂工程筹建指挥部
【正文语种】中文
【中图分类】TG333.15
【相关文献】
1.常规轧机主传动交流变频调速系统浅析 [J], 尹飞凰;张存鹰
2.常规轧机主传动交流变频调速系统浅析 [J], 尹飞凰;张存鹰
3.交流变频调速技术在轧机主传动装置中的应用 [J], 吴丽敏;富慧敏
4.成对交叉辊轧机在热轧机和冷轧机中的推广应用 [J], Arata.,H;赵立新
5.交流变频调速系统在棒材热连轧机上的应用 [J], 张章潭;叶挺丁;王庭宽;马悦因版权原因,仅展示原文概要,查看原文内容请购买。
- 1、下载文档前请自行甄别文档内容的完整性,平台不提供额外的编辑、内容补充、找答案等附加服务。
- 2、"仅部分预览"的文档,不可在线预览部分如存在完整性等问题,可反馈申请退款(可完整预览的文档不适用该条件!)。
- 3、如文档侵犯您的权益,请联系客服反馈,我们会尽快为您处理(人工客服工作时间:9:00-18:30)。
金属外壳 ,与后轴接触 ,产生 的轴 电流会流入
编 码 器 内部 ,极 易损 坏 速 度 编 码 器 内部 电路 。
不 通过 P L C和 P R OF I BUS网络 ,直接将 急停
因此 ,将 编码 器与 后轴 绝缘 隔离 ,即使 信号开关接入继 电器线 圈,并将常开 点接入相 用耐压绝缘材料使 编码器 本体 不直接 与电机 和 应 传动 柜 C uvC控制 模板 的输 入端 子上 。通 电机后轴直接接触 ,切 断转轴 电流流入 编码器 过修 改控制参数来 实现 急停功 能。改造后急停
拓 扑结构为 3 CS远程 站一 P L C一精轧 区远程
后 重 点 将 速 度 环 Kp和 T i 进 行 重 新 整 定 。Kp 站 1 一 精 轧 区远 程 站 2一 轧 机 区液 压 站 一 粗 轧
由l 5以上 降 至 1 O以下 ,降 低 比 例增 益 ;T i
由4 8~ 8 0 ms 增 至2 8 0 ms~ 3 0 0 ms , 延 长 积
形存在 许多高压脉冲 ,致使 调速 驱动系统中高 频谐波成分增多,这些谐波分量在转轴、定子 绕组 和接线部分等产生电磁感应 ,产生转轴对 原设 计中 ,轧机 急停控 制是 通过 在 P L C 2 . 4轧机 急停信号 改造
轧机主传动调速装置采用 M AS T E R
DR I VE S 6 S E 7 0系 列 变 频 器 。 轧 机 区 电气 控 制
地的脉冲电压,从而产生转轴电流。虽然在电 中编 制程 序,将 相应 区域 急停开 关接 入 P L C
机前轴上增加了接地碳刷 , 但测试轧钢过程 中, 主传 动电机产 生的轴 电流仍 可到 I O A~ 2 0 A。 的开 关量 输入 点 ,经 过 P RO F I BUS网络来 控 制实现急停 功能。此方式急停控制 中,若 P L C
P L C一 3 C S远程 站一 精轧 区远程 站 1 一 精轧 【 关键词 】轧机主传动 调速和控制 系统 技术 主传动逆变装置参数优化后 ,从根本上消 除了 转速和 电流振荡 问题 ,系统运行趋于稳定。 区远 程 站 2一 轧 机 区液 压 站 一 粗 轧 区远 程站 。 改 造 攻 关
2 . 2 速 度 反 馈 编 码 器 改造 该 网 络 拓 扑结 构将 P L C作 为 终 端 首 站 , 其
优 点在 于若 其他 远程 站 出现 问题 时,P L C的
1引言
宣钢 中型材 生产线 于 2 0 0 7 年6 月投产 ,
是一条 中型 型钢全连 轧生产线 。该生产线是宣 钢第 一条轧机 主传动 使用交 流调速 的轧钢 生产 线。
( P 2 2 3由 4改 为 1 0 . 2 0 ms 左 右 ), 以降 低速 瘫痪 ;并且增 大 了 C P U报故 障的范 围,使得 度环受到外界干扰的影响 。 参 数经重新整定后 , 轧钢主传动 设备运 行情况有 了较 大的提 升。对 故障点难于查找 。 因 此, 将 其 网 络 拓 扑 结 构 改 为
自动化控 制 ・ A u t o ma t i c C o n t r o l
宣钢中型材 轧机 主传 动调速和控制 系统 的应用与技术攻关 各 台电机参 数进 行重 新辨 识;之 本文 主要介 绍 了宣钢 中型材 生产 线轧机 主传 动调 速 和控 制 系 统,并 主要 叙 述 了主传动 控 制调 速、速 度 反 馈 编码 器、P R O F I B U S 网络 和轧机 急 停控 制在应 用 中遇 到 的 问题 ,通过 具体 攻 关方 法解 决 了 问题 ,提 高 了生 产作 业率 , 节约 了相关备 件的投入 。
工业 以太网通讯网络和P r o l f b u s — DP通讯网络。 随着该 生产 线 的产能 的不 断提 高,轧机 主传 动的调速 和控 制系统的各种故障隐患也逐 步暴 露出来 ,故障率随之 增多,严重影响生产 的正常进 行。 为解决制约生产的电控技术难题, 降低 主传动的调速和控制系统的故障率 ,满足 生产 需求,从 2 0 1 1年 l 1 月开始 ,检修 公司立 足 自身,对该生产线的主传动 电控系统进行技
系统采用三级控制 系统和 两层通 讯网络 ,其控 制系 统采用 西门子 ¥ 7 - 4 0 0系列 P L C系统 ,各
远程站 为西门子 E T 2 0 0 ;两 层 通 讯 网络 分 别 为
中型 材 生 产 线 主 传 动 电 机 速 度 编 码 器 采 模 块 出现 问题 或 P R OF I B US网 络 出现 瞬 间 中
2 . 2 . 1 轴 电流 问题 主传动 电机 是 由逆变 器提 供 电源,逆 变
CP U不会 报故 障,故 障点容 易从 硬件组 态和 报警记录查出,可 降低控 制系统和 网络 故障停
器采 用脉宽调制技术 ,其产生 的 P WM 电压波 机 发 生 ,并 且 故 障 容 易查 找 处 理 。
术攻关。
用无联轴器式编码器 ,即编码器为环形形状 ,
使 用 抱 箍 直 接 与 电机 后 轴 固定 。 由于 编 码 器 为
断时 ,急停信号进入 ,致使全线停车 。工作不
稳 定 ,容 易 出现 误 信 号 情 况 。 因 此 , 将 急 停 控 制 改 为 继 电 器 控 制 , 即
区远程站 。该 网络结构 中,3 C S远程站作为终
端 首站,而 P L C作 为 中 间 站 。 其 缺 点 为 P L C 作 为 中 间站 , 如 果 终 端 首 站 出现 问题 时 ,P L C 的C P U 一 定 报 故 障 ,整 个 控 制 系 统 及 其 网 络
分响应时 间;同时 ,还增加 了直流母线滤波环 节 ( P 2 8 7由 O改为 3 )并增 大编码器滤波时 间