塑胶产品葵花宝典及设计规范实例
塑胶产品结构设计基本规则

塑胶产品结构设计基本规则设计基本规则壁厚的大小取决于产品需要承受的外力、是否作为其它零件的支撑、承接柱位的数量、伸出部份的多少以及选用的塑胶材料而定。
一般的热塑性塑料壁厚设计应以4mm为限。
从经济角度来看,过厚的产品不但增加物料成本,延长生产周期”冷却时间〔,增加生产成本。
从产品设计角度来看,过厚的产品增加引致产生空穴”气孔〔的可能性,大大削弱产品的刚性及强度。
最理想的壁厚分布无疑是切面在任何一个地方都是均一的厚度,但为满足功能上的需求以致壁厚有所改变总是无可避免的。
在此情形,由厚胶料的地方过渡到薄胶料的地方应尽可能顺滑。
太突然的壁厚过渡转变会导致因冷却速度不同和产生乱流而造成尺寸不稳定和表面问题。
对一般热塑性塑料来说,当收缩率”Shrinkage Factor〔低于0.01mm/mm时,产品可容许厚度的改变达;但当收缩率高于0.01mm/mm时,产品壁厚的改变则不应超过。
对一般热固性塑料来说,太薄的产品厚度往往引致操作时产品过热,形成废件。
此外,纤维填充的热固性塑料于过薄的位置往往形成不够填充物的情况发生。
不过,一些容易流动的热固性塑料如环氧树脂”Epoxies〔等,如厚薄均匀,最低的厚度可达0.25mm。
此外,采用固化成型的生产方法时,流道、浇口和部件的设计应使塑料由厚胶料的地方流向薄胶料的地方。
这样使模腔内有适当的压力以减少在厚胶料的地方出现缩水及避免模腔不能完全充填的现象。
若塑料的流动方向是从薄胶料的地方流向厚胶料的地方,则应采用结构性发泡的生产方法来减低模腔压力。
平面准则在大部份热融过程操作,包括挤压和固化成型,均一的壁厚是非常的重要的。
厚胶的地方比旁边薄胶的地方冷却得比较慢,并且在相接的地方表面在浇口凝固后出现收缩痕。
更甚者引致产生缩水印、热内应力、挠曲部份歪曲、颜色不同或不同透明度。
若厚胶的地方渐变成薄胶的是无可避免的话,应尽量设计成渐次的改变,并且在不超过壁厚3:1的比例下。
下图可供叁考。
塑胶产品技术范例标准

塑胶产品技术范例标准基本规定3.1模具的分类根据目前CEGZ的实际情况,我们将所涉及的模具分为精密模具和普通模具检验条件塑胶产品的检验应当在成型之后16~24小时,按塑胶成形件的制造要求或经“后处理”后实施。
在温度为23±2℃,相对湿度(65±5)%时测量,(试模或注塑生产过程中的现场抽检或要求现场签板的情况除外)。
在测量注塑模具制造的塑胶件的偏差时,应考虑由于吸湿或后结晶所造成的偏差,为此在CEGZ和客户之间必须对“后处理“作出规定。
经过协商对测量状态也作出规定,这是非常合适的。
4.塑胶产品尺寸公差产品尺寸公差项规定了CEGZ制造的注塑模具在试模或小批量(500啤或以下)生(试)产时,其注塑件的材质,胶件表面缺陷,变形,和检验条件等需符合CEGZ有关技术标准和技术规范,以及客户对塑胶产品胶料和品质的所有各项要求下,所检验的塑胶产品尺寸需满足的尺寸公差范围。
4.1未注偏差对于技术文件中塑胶件未标注偏差的尺寸,则应按附表一《塑胶产品的尺寸偏差数值及公差数值表》中“未注偏差的尺寸允许偏差”栏实施。
例如,基本尺寸30mm 的140B公差查《塑胶件的尺寸偏差数值及公差数值表》表得:±0.24,即其设计尺寸为:(30±0.24)mm。
4.2直接标注偏差的公差对于技术文件中塑胶件标注偏差的公差,则应按附表一《塑胶件的尺寸偏差数值及公差数值表》中“标注公差的尺寸公差值”栏实施。
例如,基本尺寸30mm的140B 公差查《一般公差和直接标注偏差的公差》表得:0.48,即其偏差可以设计为:±0.24,或+0 , 或-0.48+0.48,或+0.10,等等。
-0 -0.384.3 模具非活动部件决定的尺寸是指在同一个模具零件或互相间不可活动的模具零件中成型的尺寸。
例如,产品上孔直径的尺寸。
4.4模具活动部件决定的尺寸是指可活动的模具零件共同作用所构成的尺寸。
例如,壁厚尺寸和底厚尺寸,或受斜顶、行位影响的尺寸。
塑胶件设计规范范文
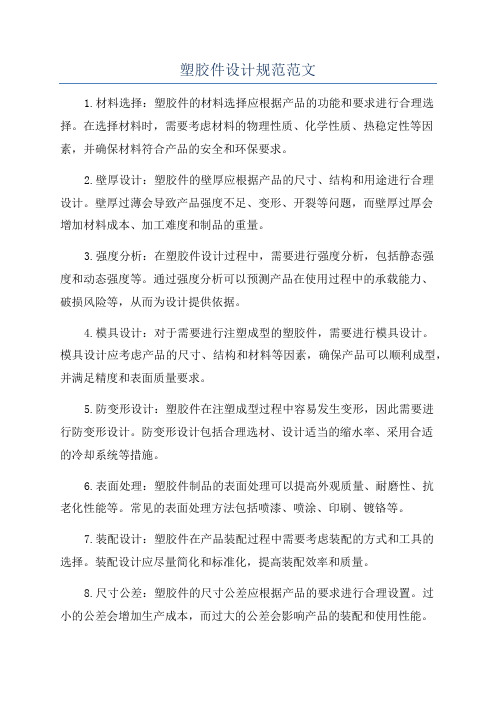
塑胶件设计规范范文1.材料选择:塑胶件的材料选择应根据产品的功能和要求进行合理选择。
在选择材料时,需要考虑材料的物理性质、化学性质、热稳定性等因素,并确保材料符合产品的安全和环保要求。
2.壁厚设计:塑胶件的壁厚应根据产品的尺寸、结构和用途进行合理设计。
壁厚过薄会导致产品强度不足、变形、开裂等问题,而壁厚过厚会增加材料成本、加工难度和制品的重量。
3.强度分析:在塑胶件设计过程中,需要进行强度分析,包括静态强度和动态强度等。
通过强度分析可以预测产品在使用过程中的承载能力、破损风险等,从而为设计提供依据。
4.模具设计:对于需要进行注塑成型的塑胶件,需要进行模具设计。
模具设计应考虑产品的尺寸、结构和材料等因素,确保产品可以顺利成型,并满足精度和表面质量要求。
5.防变形设计:塑胶件在注塑成型过程中容易发生变形,因此需要进行防变形设计。
防变形设计包括合理选材、设计适当的缩水率、采用合适的冷却系统等措施。
6.表面处理:塑胶件制品的表面处理可以提高外观质量、耐磨性、抗老化性能等。
常见的表面处理方法包括喷漆、喷涂、印刷、镀铬等。
7.装配设计:塑胶件在产品装配过程中需要考虑装配的方式和工具的选择。
装配设计应尽量简化和标准化,提高装配效率和质量。
8.尺寸公差:塑胶件的尺寸公差应根据产品的要求进行合理设置。
过小的公差会增加生产成本,而过大的公差会影响产品的装配和使用性能。
9.耐用性设计:塑胶件在使用过程中需要具有一定的耐用性。
耐用性设计包括选择合适的材料、优化结构、进行耐久性测试等。
10.产品标识:塑胶件在制造过程中需要进行产品标识,包括产品型号、批次号、生产厂家等信息。
产品标识有助于产品追溯和质量控制。
请注意,以上只是一些常见的塑胶件设计规范,具体的设计规范还需根据具体产品和行业的要求来确定。
在进行塑胶件设计时,还需充分考虑产品的使用环境、工艺要求和成本等因素,确保产品的质量和可生产性。
塑料产品设计规范
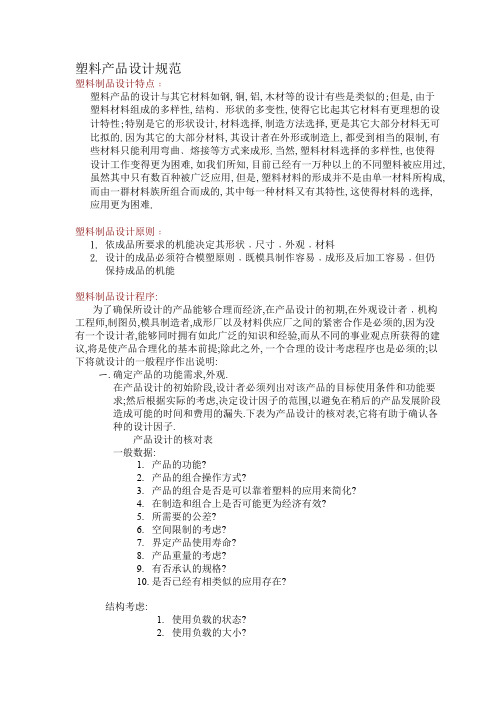
塑料产品设计规范塑料制品设计特点﹕塑料产品的设计与其它材料如钢,铜,铝,木材等的设计有些是类似的;但是,由于塑料材料组成的多样性,结构﹑形状的多变性,使得它比起其它材料有更理想的设计特性;特别是它的形状设计,材料选择,制造方法选择,更是其它大部分材料无可比拟的.因为其它的大部分材料,其设计者在外形或制造上,都受到相当的限制,有些材料只能利用弯曲﹑熔接等方式来成形.当然,塑料材料选择的多样性,也使得设计工作变得更为困难,如我们所知,目前已经有一万种以上的不同塑料被应用过,虽然其中只有数百种被广泛应用,但是,塑料材料的形成并不是由单一材料所构成,而由一群材料族所组合而成的,其中每一种材料又有其特性,这使得材料的选择,应用更为困难.塑料制品设计原则﹕1.依成品所要求的机能决定其形状﹐尺寸﹐外观﹐材料2.设计的成品必须符合模塑原则﹐既模具制作容易﹐成形及后加工容易﹐但仍保持成品的机能塑料制品设计程序:为了确保所设计的产品能够合理而经济,在产品设计的初期,在外观设计者﹐机构工程师,制图员,模具制造者,成形厂以及材料供应厂之间的紧密合作是必须的,因为没有一个设计者,能够同时拥有如此广泛的知识和经验,而从不同的事业观点所获得的建议,将是使产品合理化的基本前提;除此之外, 一个合理的设计考虑程序也是必须的;以下将就设计的一般程序作出说明:一.确定产品的功能需求,外观.在产品设计的初始阶段,设计者必须列出对该产品的目标使用条件和功能要求;然后根据实际的考虑,决定设计因子的范围,以避免在稍后的产品发展阶段造成可能的时间和费用的漏失.下表为产品设计的核对表,它将有助于确认各种的设计因子.产品设计的核对表一般数据:1.产品的功能?2.产品的组合操作方式?3.产品的组合是否是可以靠着塑料的应用来简化?4.在制造和组合上是否可能更为经济有效?5.所需要的公差?6.空间限制的考虑?7.界定产品使用寿命?8.产品重量的考虑?9.有否承认的规格?10.是否已经有相类似的应用存在?结构考虑:1.使用负载的状态?2.使用负载的大小?3.使用负载的期限?4.变形的容许量?环境:1.使用在什么温度环境?2.化学物品或溶剂的使用或接触?3.温度环境?4.在该种环境的使用期限?外观:1.外形2.颜色3.表面加工如咬花,喷漆等.经济因素:1.产品预估价格?2.目前所设计产品的价格?3.降低成本的可能性?二.绘制预备性的设计图:当产品的功能需求,外观被确定以后,设计者可以根据选定的塑料材料性质,开始绘制预备性的产品图,以作为先期估价,检讨以及原则模型的制作.三.制作原型模型:原型模型让设计者有机会看到所设计的产品的实体,并且实际的核对其工程设计.原型模型的制作一般有两种方式,第一种就是利用板状或棒状材料依图加工再接合成一完整的模型,这种方式制作的模型,经济快速,但是,缺点是量少,而且较难作结构测试;另一种方式,是利用暂用模具,可作少量生产,需花费较高的模具费用,而且所费的时间较长,但是,所制作的产品较类似于真正量产的产品(需要特殊模具机构的部分,可能成形后再以机械加工成形),可做一般的工程测试,而且建立的模具,成形经验,将有助于产品针对实际模具制作,成形需要而作正确的修正或评估.四.产品测试每一个设计都必须在原型阶段,接受一些测试,以核对设计时的计算和假想和实体之间的差异.产品在使用时所需要做的一些测试,大部分都可以籍着原型做有效的测试;此时,面对了所有设计的功能要求,并且能够达成一个完整的设计评估.仿真使用测试通常在模型产品阶段就必须开始,这种型态的测试价值,取决于使用状态被模拟的程度而定.机械和化学性质的加速化测速通常被视为模型产品评估的重要项目.五.设计的再核对与修正对设计的检讨将有助于回答一些根本的问题:所设计的产品是否达到预期的效果?价格是否合理?甚至于在此时,许多产品为了生产的经济性或是为了重要的功能和外形的改变,必须被发掘并改善,当然,设计上的重大改变,可能需要做完整的重新评估;假若所有的设计都经过这种仔细检讨,则能够在这个阶建立产品的细节和规格.六.制定重要规格规格的目的在于消除生产时任何的偏差,以使产品符合外观,功能和经济的要求,规格上必须明确说明产品所必须符合的要求,它应该包括:制造方法,尺寸公差,表面加工,分模面位置,毛边,变形,颜色以及测试规格等.七.开模生产当规格被谨慎而实际的订定之后,模具就可以开始被设计和制作,模具的设计必须谨慎并咨询专家的意思,因为不适当的模具设计和制造,将会使得生产费用提高,效率降低,并用可能造成质量的问题.八. 质量的控制对照一个已知的标准,订定对生产产品的规律检测是良好的检测作法,而检测表应该列出所有应该被检查的项目,另外,相关人员,如品管者或设计者也应与成形厂联合订定一个质量管理的程序,以利于在生产的产品能够符合规格的要求.产品设计细节确定:一.分模线之选定1.不得位于明显影响外观的位置2.开模时不形成死角(undercut)的位置3.位于模具易加工的位置4.位于成品后加工容易的位置5.位于不影响尺寸精度的位置(尺寸关系重要的部分尽量放在模具的同一边)二.脱模斜度脱模斜度是为了便于产品从模具中脱出而设置的。
塑胶产品设计规范
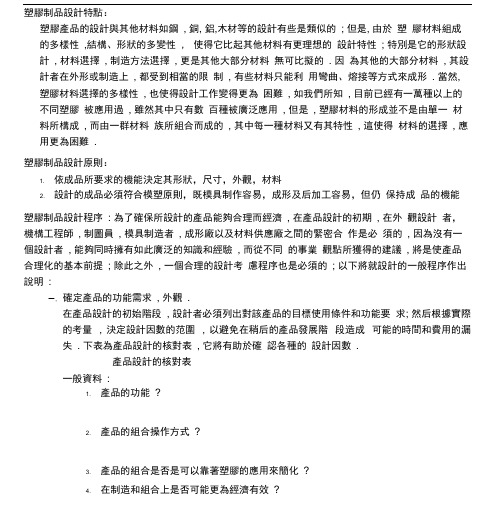
塑膠制品設計特點:塑膠產品的設計與其他材料如鋼, 銅, 鋁,木材等的設計有些是類似的; 但是, 由於塑膠材料組成的多樣性,結構、形狀的多變性,使得它比起其他材料有更理想的設計特性; 特別是它的形狀設計, 材料選擇, 制造方法選擇, 更是其他大部分材料無可比擬的. 因為其他的大部分材料, 其設計者在外形或制造上, 都受到相當的限制, 有些材料只能利用彎曲、熔接等方式來成形. 當然, 塑膠材料選擇的多樣性, 也使得設計工作變得更為困難, 如我們所知, 目前已經有一萬種以上的不同塑膠被應用過, 雖然其中只有數百種被廣泛應用, 但是, 塑膠材料的形成並不是由單一材料所構成, 而由一群材料族所組合而成的, 其中每一種材料又有其特性, 這使得材料的選擇, 應用更為困難.塑膠制品設計原則:1. 依成品所要求的機能決定其形狀,尺寸,外觀,材料2. 設計的成品必須符合模塑原則,既模具制作容易,成形及后加工容易,但仍保持成品的機能塑膠制品設計程序: 為了確保所設計的產品能夠合理而經濟, 在產品設計的初期, 在外觀設計者,機構工程師, 制圖員, 模具制造者, 成形廠以及材料供應廠之間的緊密合作是必須的, 因為沒有一個設計者, 能夠同時擁有如此廣泛的知識和經驗, 而從不同的事業觀點所獲得的建議, 將是使產品合理化的基本前提; 除此之外, 一個合理的設計考慮程序也是必須的; 以下將就設計的一般程序作出說明:一.確定產品的功能需求, 外觀.在產品設計的初始階段, 設計者必須列出對該產品的目標使用條件和功能要求; 然后根據實際的考量, 決定設計因數的范圍, 以避免在稍后的產品發展階段造成可能的時間和費用的漏失. 下表為產品設計的核對表, 它將有助於確認各種的設計因數.產品設計的核對表一般資料:1. 產品的功能?2. 產品的組合操作方式?3. 產品的組合是否是可以靠著塑膠的應用來簡化?4. 在制造和組合上是否可能更為經濟有效?5. 所需要的公差?6. 空間限制的考慮?7. 界定產品使用壽命?8. 產品重量的考慮?9.10. 有否承認的規格?是否已經有相類似的應用存在結構考慮1. 使用負載的狀態?2. 使用負載的大小?3. 使用負載的期限?4. 變形的容許量?環境:1. 使用在什麼溫度環境?2. 化學物品或溶劑的使用或接觸?3. 溫度環境?4. 在該種環境的使用期限?外觀:1. 外形2. 顏色3. 表面加工如咬花, 噴漆等.經濟因素:1. 產品預估價格?2. 目前所設計產品的價格?3. 降低成本的可能性?二.繪制預備性的設計圖:當產品的功能需求, 外觀被確定以后, 設計者可以根據選定的塑膠材料性質, 開始繪制預備性的產品圖, 以作為先期估價, 檢討以及原則模型的制作.三.制作原型模型:原型模型讓設計者有機會看到所設計的產品的實體, 並且實際的核對其工程設計. 原型模型的制作一般有兩種方式, 第一種就是利用板狀或棒狀材料依圖加工再接合成一完整的模型, 這種方式制作的模型, 經濟快速,但是, 缺點是量少, 而且較難作結構測試; 另一種方式, 是利用暫用模具, 可作少量生產, 需花費較高的模具費用, 而且所費的時間較長, 但是, 所制作的產品較類似於真正量產的產品(需要特殊模具機構的部分, 可能成形后再以機械加工成形), 可做一般的工程測試, 而且建立的模具, 成形經驗, 將有助於產品針對實際模具制作, 成形需要而作正確的修正或評估.四.產品測試每一個設計都必須在原型階段, 接受一些測試, 以核對設計時的計算和假想和實體之間的差異.產品在使用時所需要做的一些測試, 大部分都可以籍著原型做有效的測試; 此時, 面對了所有設計的功能要求, 並且能夠達成一個完整的設計評估.模擬使用測試通常在模型產品階段就必須開始, 這種型態的測試價值, 取決於使用狀態被模擬的程度而定.機械和化學性質的加速化測速通常被視為模型產品評估的重要項目.五. 設計的再核對與修正對設計的檢討將有助於回答一些根本的問題: 所設計的產品是否達到預期的效果? 價格是否合理? 甚至於在此時, 許多產品為了生產的經濟性或是為了重要的功能和外形的改變, 必須被發掘並改善, 當然, 設計上的重大改變, 可能需要做完整的重新評估; 假若所有的設計都經過這種仔細檢討, 則能夠在這個階建立產品的細節和規格.六.制定重要規格規格的目的在於消除生產時任何的偏差, 以使產品符合外觀, 功能和經濟的要求, 規格上必須明確說明產品所必須符合的要求, 它應該包括: 制造方法, 尺寸公差, 表面加工, 分模面位置, 毛邊,變形, 顏色以及測試規格等.七. 開模生產當規格被謹慎而實際的訂定之后, 模具就可以開始被設計和制作, 模具的設計必須謹慎並咨詢專家的意思, 因為不適當的模具設計和制造, 將會使得生產費用提高效率降低, 並用可能造成品質的問題.八. 品質的控制對照一個已知的標准, 訂定對生產產品的規律檢測是良好的檢測作法而檢測表應該列出所有應該被檢查的項目, 另外, 相關人員, 如品管者或設計者也應與成形廠聯合訂定一個品質管制的程序, 以利於在生產的產品能夠符合規格的要求.產品設計細節確定:一.分模線之選定1. 不得位于明顯影響外觀的位置2. 開模時不形成死角(undercut) 的位置3. 位于模具易加工的位置4. 位于成品后加工容易的位置5. 位于不影響尺寸精度的位置( 尺寸關系重要的部分盡量放在模具的同一邊)二.脫模斜度脫模斜度是為了便于產品從模具中脫出而設置的。
塑胶产品设计原则

(3)﹒縱肋 大多使用於增強﹐縱肋之拔 模角度﹐一般情形﹐側壁肉厚之 尺寸A及B已經決定﹐此种場 合﹐最常用以表示拔模角度﹒
圖9(a)示內側壁縱肋﹐圖9(b)示 外側壁之加強肋﹒ A=T X (0.5~0.7) 較少凸起之場合﹐亦得适用 (0.8~1.0)﹒ 由於工作上限制﹐ B=1.0~1.8mm.
底部大之場合﹐周邊接合R放大(圖20(b))﹐或設置效果較 大之分層底部(圖20(c))﹒
(3) 加裝增強肋 增強肋之效果為不增加肉厚厚度而持有剛性及強度﹐在廣平面之 場合﹐亦用以防止翹曲﹒
圖21(a)為對壁(A)作用厚度之增強肋 場合﹐增強肋根圓之面積約增加 5%﹐產生縮陷﹒圖21(b)之增強肋厚 為壁厚之1/2場合﹐增強肋根圓面積 約增加20%﹐不致產生縮陷﹒由於此 點﹐与其加厚增強肋之厚度﹐不如 增加其數量﹐再者﹐增強肋間不間 隔盡可能在壁厚之4倍以上﹒在必要 時﹐增強肋之厚度得為壁厚之 50%~80%以上﹒
所用之自攻螺絲為3 所用之自攻螺絲為 H盡可能在 盡可能在0mm以 上﹐應有必需強度之凸轂例﹒ 此种凸轂之拔模角度為 (固定側) (可動側)
固定側之退縮傾斜較可動側者 為大﹒
3.肉厚 肉厚
肉厚以各处均一为原则﹒但由于成形品之构造﹐或成形上肉厚 必需变化者﹐并且由于经济原因亦需对肉厚作适当之必需变 化﹒ 决定肉厚必需考虑下列各点. (1)﹒构造强度﹒ (2)﹒脱模强度﹒ (3)﹒能均匀分散冲击作用力﹒ (4)﹒嵌合金属件部份开裂防止(成菁材料与金属之膨胀不同﹐收 缩时发生开裂﹒) (5)﹒穴﹑孔﹑嵌合金属件部使用熔接加强﹒ (6)﹒薄肉部防止﹒ (7)﹒厚肉部防止﹒ (8)棱锐部及肉部阴碍流动﹐应防止充填不足﹒
下列示各种實例﹒ (1)﹒箱盒及蓋
設H為50mm以上者
塑胶产品设计规范标准
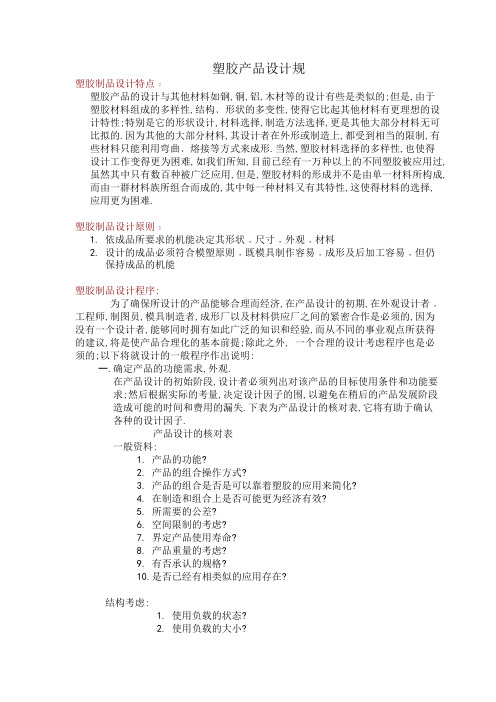
塑胶产品设计规塑胶制品设计特点﹕塑胶产品的设计与其他材料如钢,铜,铝,木材等的设计有些是类似的;但是,由于塑胶材料组成的多样性,结构﹑形状的多变性,使得它比起其他材料有更理想的设计特性;特别是它的形状设计,材料选择,制造方法选择,更是其他大部分材料无可比拟的.因为其他的大部分材料,其设计者在外形或制造上,都受到相当的限制,有些材料只能利用弯曲﹑熔接等方式来成形.当然,塑胶材料选择的多样性,也使得设计工作变得更为困难,如我们所知,目前已经有一万种以上的不同塑胶被应用过,虽然其中只有数百种被广泛应用,但是,塑胶材料的形成并不是由单一材料所构成,而由一群材料族所组合而成的,其中每一种材料又有其特性,这使得材料的选择,应用更为困难.塑胶制品设计原则﹕1.依成品所要求的机能决定其形状﹐尺寸﹐外观﹐材料2.设计的成品必须符合模塑原则﹐既模具制作容易﹐成形及后加工容易﹐但仍保持成品的机能塑胶制品设计程序:为了确保所设计的产品能够合理而经济,在产品设计的初期,在外观设计者﹐工程师,制图员,模具制造者,成形厂以及材料供应厂之间的紧密合作是必须的,因为没有一个设计者,能够同时拥有如此广泛的知识和经验,而从不同的事业观点所获得的建议,将是使产品合理化的基本前提;除此之外, 一个合理的设计考虑程序也是必须的;以下将就设计的一般程序作出说明:一.确定产品的功能需求,外观.在产品设计的初始阶段,设计者必须列出对该产品的目标使用条件和功能要求;然后根据实际的考量,决定设计因子的围,以避免在稍后的产品发展阶段造成可能的时间和费用的漏失.下表为产品设计的核对表,它将有助于确认各种的设计因子.产品设计的核对表一般资料:1.产品的功能?2.产品的组合操作方式?3.产品的组合是否是可以靠着塑胶的应用来简化?4.在制造和组合上是否可能更为经济有效?5.所需要的公差?6.空间限制的考虑?7.界定产品使用寿命?8.产品重量的考虑?9.有否承认的规格?10.是否已经有相类似的应用存在?结构考虑:1.使用负载的状态?2.使用负载的大小?3.使用负载的期限?4.变形的容许量?环境:1.使用在什么温度环境?2.化学物品或溶剂的使用或接触?3.温度环境?4.在该种环境的使用期限?外观:1.外形2.颜色3.表面加工如咬花,喷漆、印刷等.经济因素:1.产品预估价格?2.目前所设计产品的价格?3.降低成本的可能性?二.绘制预备性的设计图:当产品的功能需求,外观被确定以后,设计者可以根据选定的塑胶材料性质,开始绘制预备性的产品图,以作为先期估价,检讨以及原型模型的制作.三.制作原型模型:原型模型让设计者有机会看到所设计的产品的实体,并且实际的核对其工程设计.原型模型的制作一般有两种方式,第一种就是利用板状或棒状材料依图加工再接合成一完整的模型,这种方式制作的模型,经济快速,但是,缺点是量少,而且较难作结构测试;另一种方式,是利用暂用模具,可作少量生产,需花费较高的模具费用,而且所费的时间较长,但是,所制作的产品较类似于真正量产的产品(需要特殊模具的部分,可能成形后再以机械加工成形),可做一般的工程测试,而且建立的模具,成形经验,将有助于产品针对实际模具制作,成形需要而作正确的修正或评估.四.产品测试每一个设计都必须在原型阶段,接受一些测试,以核对设计时的计算和假想和实体之间的差异.产品在使用时所需要做的一些测试,大部分都可以籍着原型做有效的测试;此时,核对了所有设计的功能要求,并且能够达成一个完整的设计评估.模拟使用测试通常在模型产品阶段就必须开始,这种型态的测试价值,取决于使用状态被模拟的程度而定.机械和化学性质的加速化测试通常被视为模型产品评估的重要项目.五.设计的再核对与修正对设计的检讨将有助于回答一些根本的问题:所设计的产品是否达到预期的效果?价格是否合理?甚至于在此时,许多产品为了生产的经济性或是为了重要的功能和外形的改变,必须被发掘并改善,当然,设计上的重大改变,可能需要做完整的重新评估;假若所有的设计都经过这种仔细检讨,则能够在这个阶建立产品的细节和规格.六.制定重要规格规格的目的在于消除生产时任何的偏差,以使产品符合外观,功能和经济的要求,规格上必须明确说明产品所必须符合的要求,它应该包括:制造方法,尺寸公差,表面加工,分模面位置,毛边,变形,颜色以及测试规格等.七.开模生产当规格被谨慎而实际的订定之后,模具就可以开始被设计和制作,模具的设计必须谨慎并咨询专家的意思,因为不适当的模具设计和制造,将会使得生产费用提高,效率降低,并用可能造成质量的问题.八. 质量的控制对照一个已知的标准,订定对生产产品的规律检测是良好的检测作法,而检测表应该列出所有应该被检查的项目,另外,相关人员,如品管者或设计者也应与成形厂联合订定一个质量管制的程序,以利于在生产的产品能够符合规格的要求.产品设计细节确定:一.分模线之选定1.不得位于明显影响外观的位置2.开模时不形成死角(undercut)的位置3.位于模具易加工的位置4.位于成品后加工容易的位置5.位于不影响尺寸精度的位置(尺寸关系重要的部分尽量放在模具的同一边)二.脱模斜度脱模斜度是为了便于产品从模具中脱出而设置的。
塑胶件设计规范
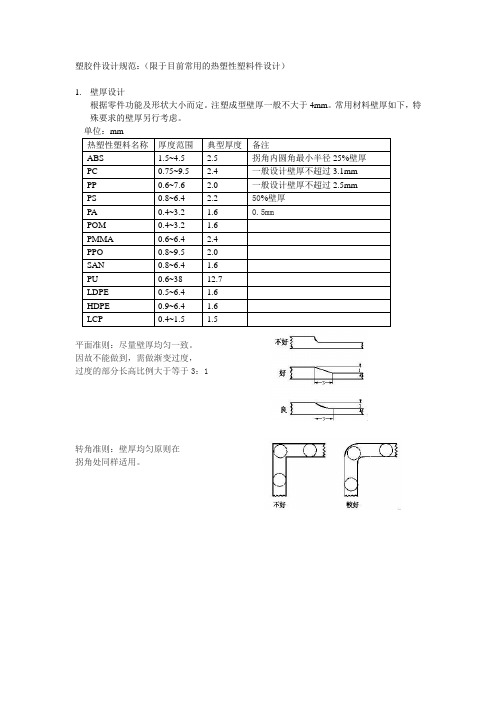
塑胶件设计规范:(限于目前常用的热塑性塑料件设计)1.壁厚设计根据零件功能及形状大小而定。
注塑成型壁厚一般不大于4mm。
常用材料壁厚如下,特殊要求的壁厚另行考虑。
单位:mm热塑性塑料名称厚度范围典型厚度备注ABS 1.5~4.5 2.5 拐角内圆角最小半径25%壁厚PC 0.75~9.5 2.4 一般设计壁厚不超过3.1mmPP 0.6~7.6 2.0 一般设计壁厚不超过2.5mmPS 0.8~6.4 2.2 50%壁厚PA 0.4~3.2 1.6 0.5mmPOM 0.4~3.2 1.6PMMA 0.6~6.4 2.4PPO 0.8~9.5 2.0SAN 0.8~6.4 1.6PU 0.6~38 12.7LDPE 0.5~6.4 1.6HDPE 0.9~6.4 1.6LCP 0.4~1.5 1.5平面准则:尽量壁厚均匀一致。
因故不能做到,需做渐变过度,过度的部分长高比例大于等于3:1转角准则:壁厚均匀原则在拐角处同样适用。
2.BOSS柱设计:(常用塑料)设计原则,首先考虑连接强度。
下表是对于一般结构件连接情况;对于重要外观件,BOSS 柱外径,在连接强度不高情况下,可以适当做小。
当连接有强度要求,又有外观要求时,需按下面参数设计,同时设计出火山口。
BOSS柱要求使用司筒顶出,斜度不大于0.25度。
说明:外径根据强度要求可以适当变化,以上值为要求说明:PC柱比ABS更容易打爆,若出现此现象,外径可适当加大材料螺钉内孔直径外径连接有效深度PP ST2.2 1.8±0.05 4 4.5ST 2.6 2.1±0.05 4.8 5ST2.9 2.3±0.05 5.5 6ST 3.3 2.6±0.05 6.0 6.5ST 3.5 2.8±0.05 6.5 7ST 3.9 3.2±0.057.2 8ST 4.2 3.4±0.057.8 8.5ST 4.8 3.8±0.059 9.5ST 5.5 4.4±0.0510 11ST 6.3 5.1±0.0511.5 12.5ST 8 6.4±0.0514.8 16材料螺钉内孔直径外径连接有效深度PA6,PA66,SAN /POM ST2.2 1.8±0.05 4 4.5 ST 2.6 2.2±0.05 4.8 5 ST2.9 2.4±0.05 5.5 6 ST 3.3 2.8±0.05 6.0 6.5 ST 3.5 3±0.05 6.5 7 ST 3.9 3.3±0.057.2 8 ST 4.2 3.5±0.057.8 8.5 ST 4.8 4±0.059 9.5 ST 5.5 4.6±0.0510 11 ST 6.3 5.3±0.0511.5 12.5 ST 8 6.8±0.0514.8 16说明:PA6,PA66螺钉有效深度可以比上表值缩短15%。
塑料产品设计规范
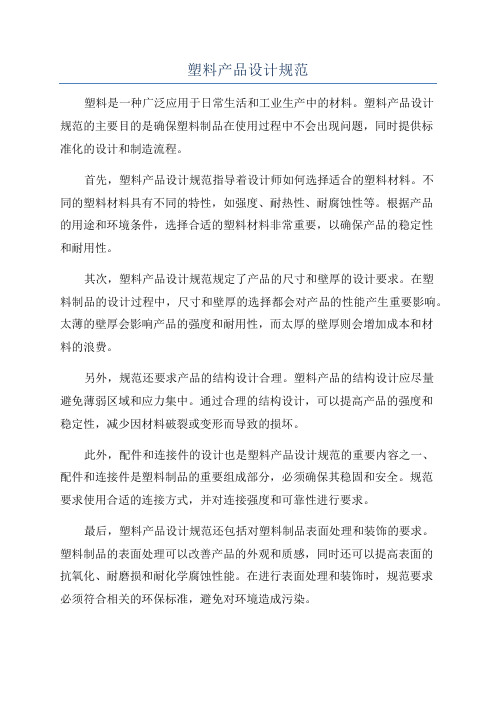
塑料产品设计规范塑料是一种广泛应用于日常生活和工业生产中的材料。
塑料产品设计规范的主要目的是确保塑料制品在使用过程中不会出现问题,同时提供标准化的设计和制造流程。
首先,塑料产品设计规范指导着设计师如何选择适合的塑料材料。
不同的塑料材料具有不同的特性,如强度、耐热性、耐腐蚀性等。
根据产品的用途和环境条件,选择合适的塑料材料非常重要,以确保产品的稳定性和耐用性。
其次,塑料产品设计规范规定了产品的尺寸和壁厚的设计要求。
在塑料制品的设计过程中,尺寸和壁厚的选择都会对产品的性能产生重要影响。
太薄的壁厚会影响产品的强度和耐用性,而太厚的壁厚则会增加成本和材料的浪费。
另外,规范还要求产品的结构设计合理。
塑料产品的结构设计应尽量避免薄弱区域和应力集中。
通过合理的结构设计,可以提高产品的强度和稳定性,减少因材料破裂或变形而导致的损坏。
此外,配件和连接件的设计也是塑料产品设计规范的重要内容之一、配件和连接件是塑料制品的重要组成部分,必须确保其稳固和安全。
规范要求使用合适的连接方式,并对连接强度和可靠性进行要求。
最后,塑料产品设计规范还包括对塑料制品表面处理和装饰的要求。
塑料制品的表面处理可以改善产品的外观和质感,同时还可以提高表面的抗氧化、耐磨损和耐化学腐蚀性能。
在进行表面处理和装饰时,规范要求必须符合相关的环保标准,避免对环境造成污染。
总之,塑料产品设计规范对确保塑料制品的质量和使用安全非常重要。
遵守规范可以帮助设计师选择适合的塑料材料、优化产品的尺寸和结构设计以及保证配件和连接件的质量。
只有遵守规范并进行有效的质量控制,才能生产出具有高质量和可靠性的塑料产品。
塑胶件设计规范
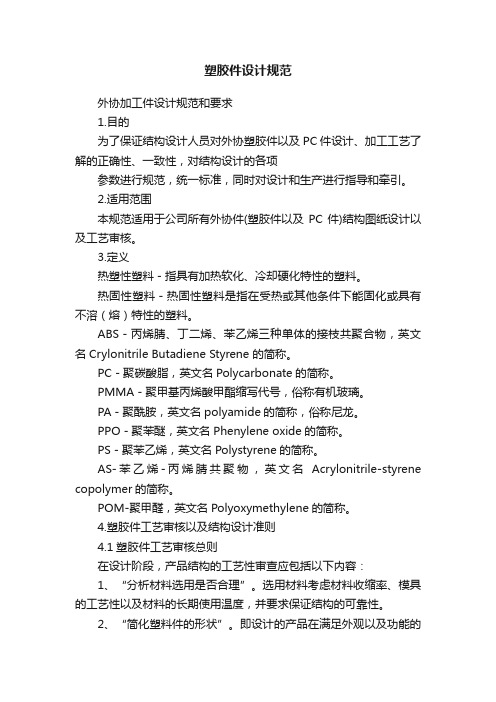
塑胶件设计规范外协加工件设计规范和要求1.目的为了保证结构设计人员对外协塑胶件以及PC件设计、加工工艺了解的正确性、一致性,对结构设计的各项参数进行规范,统一标准,同时对设计和生产进行指导和牵引。
2.适用范围本规范适用于公司所有外协件(塑胶件以及PC件)结构图纸设计以及工艺审核。
3.定义热塑性塑料-指具有加热软化、冷却硬化特性的塑料。
热固性塑料-热固性塑料是指在受热或其他条件下能固化或具有不溶(熔)特性的塑料。
ABS-丙烯腈、丁二烯、苯乙烯三种单体的接枝共聚合物,英文名Crylonitrile Butadiene Styrene 的简称。
PC-聚碳酸脂,英文名Polycarbonate的简称。
PMMA-聚甲基丙烯酸甲酯缩写代号,俗称有机玻璃。
PA-聚酰胺,英文名polyamide的简称,俗称尼龙。
PPO-聚苯醚,英文名Phenylene oxide的简称。
PS-聚苯乙烯,英文名Polystyrene的简称。
AS-苯乙烯-丙烯腈共聚物,英文名Acrylonitrile-styrene copolymer的简称。
POM-聚甲醛,英文名Polyoxymethylene的简称。
4.塑胶件工艺审核以及结构设计准则4.1塑胶件工艺审核总则在设计阶段,产品结构的工艺性审查应包括以下内容:1、“分析材料选用是否合理”。
选用材料考虑材料收缩率、模具的工艺性以及材料的长期使用温度,并要求保证结构的可靠性。
2、“简化塑料件的形状”。
即设计的产品在满足外观以及功能的需求下,塑胶件形状与结构尽量简单,以方面模具制造以及塑胶零件的拔模;还需考虑到使用手板加工时候的加工难易以及手板拆分粘结后结构可靠性等。
3、“分析零件通用性”。
是否尽量采用了通用件(模块),能用成熟模具产品的地方应尽量采用。
4、“分析产品总装的可行性与方便性,产品各组成部分是否便于装配、调整、维修,能否进行并行装配和检查,各部件是否具有装配基准”。
在装配时应尽量避免再作加工,产品应有合理的、可靠的装配基准和调整要素,各部件能否进行独立装配(即并行装配)等等。
(完整版)塑胶产品结构设计注意事项

(完整版)塑胶产品结构设计注意事项塑胶产品结构设计注意事项目录第一章塑胶结构设计规范1、材料及厚度1.1、材料选择1.2、壳体厚度1.3、零件厚度设计实例2、脱模斜度2.1、脱模斜度要点3、加强筋3.1、加强筋与壁厚的关系3.2、加强筋设计实例4、柱和孔的问题4.1、柱子的问题4.2、孔的问题4.3、“减胶”的问题5、螺丝柱的设计6、止口的设计6.1、止口的作用6.2、壳体止口的设计需要注意的事项6.3、面壳与底壳断差的要求7、卡扣的设计7.1、卡扣设计的关键点7.2、常见卡扣设计7.3、第一章塑胶结构设计规范1、材料及厚度1.1、材料的选取a. ABS:高流动性,便宜,适用于对强度要求不太高的部件(不直接受冲击,不承受可靠性测试中结构耐久性的部件),如内部支撑架(键板支架、LCD支架)等。
还有就是普遍用在电镀的部件上(如按钮、侧键、导航键、电镀装饰件等)。
目前常用奇美PA-757、PA-777D等。
b. PC+ABS:流动性好,强度不错,价格适中。
适用于作高刚性、高冲击韧性的制件,如框架、壳体等。
常用材料代号:拜尔T85、T65。
c. PC:高强度,价格贵,流动性不好。
适用于对强度要求较高的外壳、按键、传动机架、镜片等。
常用材料代号如:帝人L1250Y、PC2405、PC2605。
d. POM具有高的刚度和硬度、极佳的耐疲劳性和耐磨性、较小的蠕变性和吸水性、较好的尺寸稳定性和化学稳定性、良好的绝缘性等。
常用于滑轮、传动齿轮、蜗轮、蜗杆、传动机构件等,常用材料代号如:M90-44。
e. PA坚韧、吸水、但当水份完全挥发后会变得脆弱。
常用于齿轮、滑轮等。
受冲击力较大的关键齿轮,需添加填充物。
材料代号如:CM3003G-30。
f. PMMA有极好的透光性,在光的加速老化240小时后仍可透过92%的太阳光,室外十年仍有89%,紫外线达78.5% 。
机械强度较高,有一定的耐寒性、耐腐蚀,绝缘性能良好,尺寸稳定,易于成型,质较脆,常用于有一定强度要求的透明结构件,如镜片、遥控窗、导光件等。
塑胶产品结构设计案例
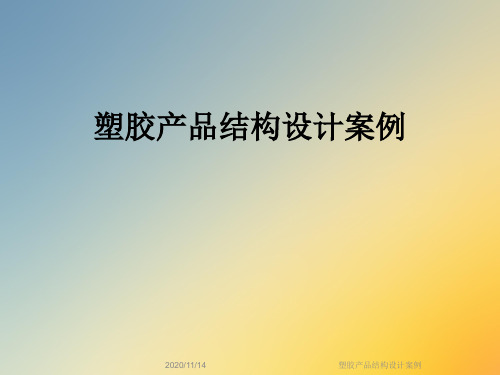
塑胶产品结构设计案例
• 门绞
– 以铁轴穿过两件或以上零件的擦穿位,令零件可 以像门绞般活动。
塑胶产品结构设计案例
3rew
演讲完毕,谢谢听讲!
再见,see you again
2020/11/14
塑胶产品结构设计案例
塑胶产品结构设计案例
超声波焊接
速度快 周期很短,使用标准机器每分 钟可处理三十件工作。
效果一致 只要接头设计完善,焊接参 数调校正确,便能获得清洁及一致的焊 接效果,因为焊接效果不受操作人员的 操作情况所影响。
强度高 将塑料熔合起来,因此能产生 出无内应力的高强的接合。
不需夹紧 当工件离开机器后便告完成, 不需进行焊接后加工。
塑胶产品结构设计案例
• PP(聚丙烯)
– 用途:玩具、日常用品、包装胶袋、瓶子 – 特性:有弹性、韧度强、延伸性大、但不可涂胶
水,工作温度-30℃~140℃ 。 – 应用:多数应用于一些因要接受跌落测试而拆件
的地方。
塑胶产品结构设计案例
• PVC(聚氯乙烯)
– 用途:软喉管、硬喉管、软板、硬板、电线、玩 具
水份完全挥发后会变得脆弱。 – 应用:因为精准度比较难控制,所以大多用于
一些模数较大的齿轮
塑胶产品结构设计案例
• Kraton(热塑性丁苯橡胶) • 用途:摩打垫,手工具把手 • 特性: 柔软,有弹性,韧度高,延伸性强。 • 设计上的应用:多数作为摩打垫,吸收摩
打震动,减低噪音。
塑胶产品结构设计案例
喇叭
• 必须要有一个喇叭筒来围着喇叭的四周,以便声
波在成品内发生共鸣,扩大音量。
塑胶产品结构设计案例
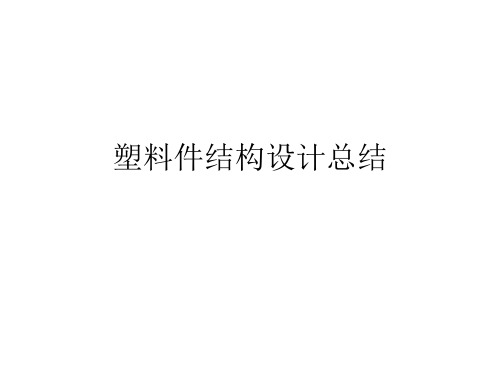
Ø 2.6 mm
Ø 3.0 mm
Ø 5.5 mm
Ø 6.0 mm
支柱的出模角一般会以支柱顶部的平面为 中性面,而且角度一般为0.5º ~1.0º 。如支 柱的高度超过15.0mm的时候,为加强支柱 的强度,可在支柱连上些加强筋,作结构 加强之用。
• 如支柱需要穿过PCB的时候,同样在支柱连上些加强筋,而且在加强 筋的顶部设计成平台形式,此可作承托PCB之用,而平台的平面与丝 筒项的平面必须要有2.0 ~ 3.0mm。
– 用途:玩具、日常用品、包装胶袋、瓶子 – 特性:有弹性、韧度强、延伸性大、但不可涂胶 水,工作温度-30℃~140℃ 。 – 应用:多数应用于一些因要接受跌落测试而拆件 的地方。
• PVC(聚氯乙烯)
– 用途:软喉管、硬喉管、软板、硬板、电线、玩 具 – 特性:柔软、坚韧而有弹性,工作温度-25℃~ 75℃ ;200 ℃ 易分解产生腐蚀、刺激性气体。 – PVC电线、电缆在制造、使用及废弃处理时, 都会产生大量的二恶英、氯氢酸、铅等有害物 质。 – 设计上的应用:多数用于玩具,或一些需要避震 或吸震的地方。
5<x≦10mm 10<x≦15mm x≦5mm 5<x≦10mm
2mm
1.4~1.5mm
10<x≦15mm 15<x≦20mm 20<x≦25mm 25<x≦30mm x≦5mm
5<x≦10mm
2.5mm 1.8mm 10<x≦15mm 15<x≦20mm 20<x≦25mm 25<x≦30mm
0.5°~1.0°
支柱套
• 跟据一般的安全规格标准,螺丝头必须收藏于不能触摸的 位置,所以高度必须有2.5mm或以上。由于加上支柱套后 会有锐边,所以在每一个支柱套上壳收螺丝的地方,必须 加上R1.0或以上的圆角。
- 1、下载文档前请自行甄别文档内容的完整性,平台不提供额外的编辑、内容补充、找答案等附加服务。
- 2、"仅部分预览"的文档,不可在线预览部分如存在完整性等问题,可反馈申请退款(可完整预览的文档不适用该条件!)。
- 3、如文档侵犯您的权益,请联系客服反馈,我们会尽快为您处理(人工客服工作时间:9:00-18:30)。
塑膠產品葵花寶典及設計規范實例塑膠制品設計特點﹕塑膠產品的設計與其他材料如鋼,銅,鋁,木材等的設計有些是類似的;但是,由於塑膠材料組成的多樣性,結構﹑形狀的多變性,使得它比起其他材料有更理想的設計特性;特別是它的形狀設計,材料選擇,制造方法選擇,更是其他大部分材料無可比擬的.因為其他的大部分材料,其設計者在外形或制造上,都受到相當的限制,有些材料只能利用彎曲﹑熔接等方式來成形.當然,塑膠材料選擇的多樣性,也使得設計工作變得更為困難,如我們所知,目前已經有一萬種以上的不同塑膠被應用過,雖然其中只有數百種被廣泛應用,但是,塑膠材料的形成並不是由單一材料所構成,而由一群材料族所組合而成的,其中每一種材料又有其特性,這使得材料的選擇,應用更為困難.塑膠制品設計原則﹕1.依成品所要求的機能決定其形狀﹐尺寸﹐外觀﹐材料2.設計的成品必須符合模塑原則﹐既模具制作容易﹐成形及后加工容易﹐但仍保持成品的機能塑膠制品設計程序:為了確保所設計的產品能夠合理而經濟,在產品設計的初期,在外觀設計者﹐機構工程師,制圖員,模具制造者,成形廠以及材料供應廠之間的緊密合作是必須的,因為沒有一個設計者,能夠同時擁有如此廣泛的知識和經驗,而從不同的事業觀點所獲得的建議,將是使產品合理化的基本前提;除此之外, 一個合理的設計考慮程序也是必須的;以下將就設計的一般程序作出說明:一.確定產品的功能需求,外觀.在產品設計的初始階段,設計者必須列出對該產品的目標使用條件和功能要求;然后根據實際的考量,決定設計因數的范圍,以避免在稍后的產品發展階段造成可能的時間和費用的漏失.下表為產品設計的核對表,它將有助於確認各種的設計因數.產品設計的核對表一般資料:1.產品的功能?2.產品的組合操作方式?3.產品的組合是否是可以靠著塑膠的應用來簡化?4.在制造和組合上是否可能更為經濟有效?5.所需要的公差?6.空間限制的考慮?7.界定產品使用壽命?8.產品重量的考慮?9.有否承認的規格?10.是否已經有相類似的應用存在?結構考慮:1.使用負載的狀態?2.使用負載的大小?3.使用負載的期限?4.變形的容許量?環境:1.使用在什麼溫度環境?2.化學物品或溶劑的使用或接觸?3.溫度環境?4.在該種環境的使用期限?外觀:1.外形2.顏色3.表面加工如咬花,噴漆、印刷等.經濟因素:1.產品預估價格?2.目前所設計產品的價格?3.降低成本的可能性?二.繪制預備性的設計圖:當產品的功能需求,外觀被確定以后,設計者可以根據選定的塑膠材料性質,開始繪制預備性的產品圖,以作為先期估價,檢討以及原型模型的制作.三.制作原型模型:原型模型讓設計者有機會看到所設計的產品的實體,並且實際的核對其工程設計.原型模型的制作一般有兩種方式,第一種就是利用板狀或棒狀材料依圖加工再接合成一完整的模型,這種方式制作的模型,經濟快速,但是,缺點是量少,而且較難作結構測試;另一種方式,是利用暫用模具,可作少量生產,需花費較高的模具費用,而且所費的時間較長,但是,所制作的產品較類似於真正量產的產品(需要特殊模具機構的部分,可能成形后再以機械加工成形),可做一般的工程測試,而且建立的模具,成形經驗,將有助於產品針對實際模具制作,成形需要而作正確的修正或評估.四.產品測試每一個設計都必須在原型階段,接受一些測試,以核對設計時的計算和假想和實體之間的差異.產品在使用時所需要做的一些測試,大部分都可以籍著原型做有效的測試;此時,核對了所有設計的功能要求,並且能夠達成一個完整的設計評估.模擬使用測試通常在模型產品階段就必須開始,這種型態的測試價值,取決於使用狀態被模擬的程度而定.機械和化學性質的加速化測試通常被視為模型產品評估的重要項目.五.設計的再核對與修正對設計的檢討將有助於回答一些根本的問題:所設計的產品是否達到預期的效果?價格是否合理?甚至於在此時,許多產品為了生產的經濟性或是為了重要的功能和外形的改變,必須被發掘並改善,當然,設計上的重大改變,可能需要做完整的重新評估;假若所有的設計都經過這種仔細檢討,則能夠在這個階建立產品的細節和規格.六.制定重要規格規格的目的在於消除生產時任何的偏差,以使產品符合外觀,功能和經濟的要求,規格上必須明確說明產品所必須符合的要求,它應該包括:制造方法,尺寸公差,表面加工,分模面位置,毛邊,變形,顏色以及測試規格等.七.開模生產當規格被謹慎而實際的訂定之后,模具就可以開始被設計和制作,模具的設計必須謹慎並咨詢專家的意思,因為不適當的模具設計和制造,將會使得生產費用提高,效率降低,並用可能造成品質的問題.八. 品質的控制對照一個已知的標准,訂定對生產產品的規律檢測是良好的檢測作法,而檢測表應該列出所有應該被檢查的項目,另外,相關人員,如品管者或設計者也應與成形廠聯合訂定一個品質管制的程序,以利於在生產的產品能夠符合規格的要求.產品設計細節確定:一.分模線之選定1.不得位于明顯影響外觀的位置2.開模時不形成死角(undercut)的位置3.位于模具易加工的位置4.位于成品后加工容易的位置5.位于不影響尺寸精度的位置(尺寸關系重要的部分盡量放在模具的同一邊)二.脫模斜度脫模斜度是為了便于產品從模具中脫出而設置的。
脫模斜度一采用1~2度﹐最小不小于0.5度。
具體數值視成品形狀﹐成形材料的類別﹐模具結構﹐表面精度﹐以及加工方等會有所不同。
在不影響產品品質的前提下﹐脫模斜度愈大愈好。
三.產品外形及肉厚產品外形盡量采用流線外形﹐避免突然的變化﹐以免在成形時因塑膠在此處流動不順引起氣泡等缺陷﹔并且此處模具易產生磨損。
決定肉厚的主要因素﹕1.結構強度是否足夠2.能否抵脫模力3.能否均勻分散所受的沖擊力4.有埋入件時﹐能否防止破裂﹐如產生熔合線是否會影響強度5.成形孔部位的熔合線是否會影響強度6.盡可能肉厚均勻﹐以防止產生縮水7.棱角及肉厚較薄部分是否會阻礙材料流動﹐從而引起充填不足肉厚不均對成形性的影響﹕1.成形品之冷卻時間取決于肉厚較厚的部分﹐使成形周期延長﹐生產性能降低2.肉厚不均則成品冷卻后收縮不均﹐造成縮水﹐產生內應力﹐變形﹐破裂等我們經常用的材料有:PC,ABS,PMMA等幾種,它們的標准肉厚如下: PC:1.5-5.0 ABS:1.2-3.5 PMMA:1.5-5.0四.加強與防止變形方法﹕1.轉角部位加R塑膠產品的尖銳轉角常常是造成產品破壞的最大因素.消除產品尖銳的轉角,不但可以降低該處的應力集中,提高產品的結構強度,也可以使得塑膠材料成形時有流線型的流路,以及成品更易於頂出.另外,從模具的觀點,園角也是有益於模具加工和模具強度.產品所有的內側和外側的周邊轉角園弧都必須盡可能的大,以消除應力集中;但是,太大的園弧可能造成縮水,特別是在肋或突柱根部轉角園弧.原則上,最小的轉角園弧為0.020到0.030inch(即0.5~0.8mm).綜上所述,園角對於成形品的設計會有以下的一些優點:(1) 園角使得成形品提高強度以及降低應力.(2) 尖銳轉角的消除,自動地降低了龜裂的可能性,就是提高對突然的震動或沖擊的抵抗能力.(3) 塑膠的流動狀態將被重大的改善,園形的轉角,使得塑膠能夠均勻,沒有滯留現象以及較少應力的流入模穴內所有的斷面,並且改善成形品斷面的密度之均勻性.(4) 模具強度獲得改善,以避免模具內尖銳的轉角,造成應力集中,導致龜裂,特別是對於需要熱處理或受力較高的部分,園弧轉角更為重要.園角加大,應力集中減少.內圓角R<0.3T ----應力劇增內圓角R>0.8T ----几乎無應力集中2.增設加強肋肋根部厚度約為(0.5~0.7)TPS T<0.6T肋間間距>4T肋高L<3T3.利用變化肉厚及形狀1)側壁加強既可防止變形﹐也可改善流動性2)邊緣加強用變化的邊緣形狀來加強﹐防止變形3)周邊加強較大的平面易發生翹曲變形﹐用周邊凹凸或波浪形來防止變形4)底部加強箱形件底部﹐為加強及防變形常采用如下方法﹕五.BOSS之設計1.BOSS的長度一般不超過本身直徑的兩倍﹐否則必須加加強肋。
(長度太長時會引起氣孔﹐燒焦﹐充填不足等)2.BOSS的位置不能太接近轉角或側壁3.BOSS的形狀以圓形為主﹐設計在底部時取3個 (其它形狀則加工不易﹐且流動性也不好)4.BOSS周圍可用除去部分肉厚(即开火山口)來防收縮下陷(如下右图)六.孔及凹陷之設計孔的形狀和位置的選擇,必須避免造成產品的脆弱性以及生產上的復雜性.在成形孔的一般方法中,塑料被射出模穴,然后沿著心梢的周邊流動而形成孔,因此,當塑料在心梢一端會合時,會形成接合線,這些接合線位置就成為成品本身的潛在脆弱性.1.孔與孔之間距離為孔徑2倍以上2.孔與成品邊緣之間距離為孔徑3倍以上3.孔與側壁之間距離為孔徑3/4倍以上4.孔周邊的肉厚宜加強(尤其針對有裝配性﹐受力的孔)﹐切開的孔周邊也宜加強5.垂直于材料流動方向的盲孔﹐孔徑在1.5mm以下時﹐孔深不得超過孔徑的2倍(只有一端支撐的模仁梢比起兩端都有支撐的模仁梢會高出48倍的變形量)6.孔徑不同的通孔不宜設計為兩邊對合成形﹐會產生偏心﹐可將任一邊的孔徑加大﹐或設計為不用對合成形的孔孔的形狀設計比較﹕七.成形螺紋及輥紋設計成形螺紋設計注意事項﹕1.避免使用32牙/inch(螺距0.75mm)以下的螺紋﹐最大螺距可采用5mm2.長螺紋會因收縮的關系使螺距失真﹐應避免使用﹐如結構需要時可采用自攻螺絲鎖緊3.螺紋公差小于成形材料收縮量時應避免使用4.螺紋不得延長至成品末端﹐因如此產生的尖銳部會使模具及螺紋的端面崩裂﹑壽命降低﹐所以至少要留0.8mm的平坦部分5.螺紋需有2~4度的拔模角輥紋通常是平行于脫模方向的溝槽﹐輥紋間距通常為3.0mm,最小為1.5mm。
為防模具崩裂及使后加工容易﹐輥紋與分模面間至少留0.8mm的平坦部分。
八.埋入件設計埋入件舉例﹕埋入件需注意點﹕1.由于流動性的關系﹐會在埋入件的周圍產生熔接痕﹔由于塑膠與金屬的收縮率不一樣﹐成形后易產生開裂2.使用埋入件成形時﹐會使周期延長3.埋入件高出成形品少許﹐可避免在裝配時被拉動而松脫成形品設計要點改善:(1)外觀的改善:A.原肋為表面形成收縮下陷之原因盡量減薄,肋厚=0.5-0.6TB.光澤表面可施行一些如放電,噴砂,腐蝕加工等防止收縮下陷及保持表面無痕跡C.盡可能地使分模面變得容易,可使模具加工容易及毛邊,澆口切除容易D.肉厚均一,可防收縮下陷E.內部肉厚去除,使肉厚均一,防止收縮下陷F.凸彀周圍,除去部分肉厚,防止收縮下陷G.凸彀之設置在同樣強度下,可以多數以小凸彀代替,可防止收縮下陷H.格子連接凸彀之場合,可防收縮下陷,並可使強度顯著增加(2)強度的改善A.肉厚較薄之孔,把孔邊肉厚增加及高度增高以補強B.切離之孔周邊肉厚宜增加C.曲面的設置,可使強度增強D.脫模時,心型銷受收縮力,使成形品頂出時造成破裂,可設置凸彀承受頂出力量E.角隅設R ,可改善強度,防止應力集中,變形破裂F.加設補強肋及角隅部設R,增強凸彀之強度G.孔與孔之間距,孔與邊緣之距離,應有適當之距離,可防止破裂之發生(3)模具及成形品的改善A.銳角薄內部分,易使材料充填不足B.透明成形品,肩角部設充分之脫模斜度,頂出時不被刮痕,才不致於影響透明性C.斜向凸彀,使模具構造變為復雜,改善凸彀方向的形狀,使成直角向之分模D.將側面之孔癖開,可消除UNDERCUT 而不用側向心型E.上下對合,可免除使用側向心型,使模具構造簡化F.上對對合之孔,恐有偏心之處,宜將另一方孔擴大G.外緣波紋之成形品,后加工(毛邊去除,澆口切離)不易,可改為直線邊緣,使變為容易H.手扭止滑部,凸形場合模具之切削加工容易I.分模線為階斷形,模具制作困難,毛邊修整不易,宜改為直線形式曲線形.J.底部設置凸緣,可使分模線單純,后加工容易K.切削時左右對稱形狀加工容易,非對稱者加工困難L.車削加工比銑削加工速度快且廉價,成形品應盡量設計為圓形M.成形品加飾,宜設計凸出,模具加工時為下凹,雕削容易N.模具成形加工,在成形品之孔,一般以心型銷來成形.所以在模具構造上,宜避免上部內厚過薄O.薄內部位,易造成充填不足P.成形品凸出文字,於模具加工時,反為凹入文字,雕削加工容易Q.內部托架上開孔,模具成本增加,且易發生故障,可改在成形后,鉆孔加工R.深凹穴,應盡量為於成形品之同一側(頂出,成形需要)改變模具固定側之心型形狀,使減少與成形品之接觸面積(有利脫模)S.斷面內厚較厚時,可改為補強肋,但內厚應與其它內厚均一T.深入之補強肋,盡量使用最大之脫模斜度,以利脫模,波形面之谷底,宜避免銳角形成.銳角部會阻礙材料流動,使模具強度減弱,成形品產生應力集中.其它:a.成形品與組合件,組合時宜在任何一方角部設置間隙b.埋入件螺紋部至成形品頂面留一平坦部避免成形時材料進入螺紋部c.兩件成形品熔接,給予t之間隙,使熔接毛邊進入d.螺紋埋入件制作成本高,成形時使成形周期延長,應盡量避免使用,成形品可預留攻絲用孔再與攻螺絲配合使用e.埋入件高出成形品少许,固定時可避免被拉取而松脫f.凸殼之預留攻絲用孔,前端,宜予倒角,以便于自攻螺絲導入g.貫穿孔使模具加工變為困難,可預留鉆孔定位孔,待成形后,再次加工.h.心型銷之分割面,位於埋入件之端面,埋入件受抵壓,於成形時能確保固定i. 鉸鏈成形品﹐宜設兩段圓弧﹐使用效果更佳。