Lean精益生产基础知识-精选文档
精益生产基础知识
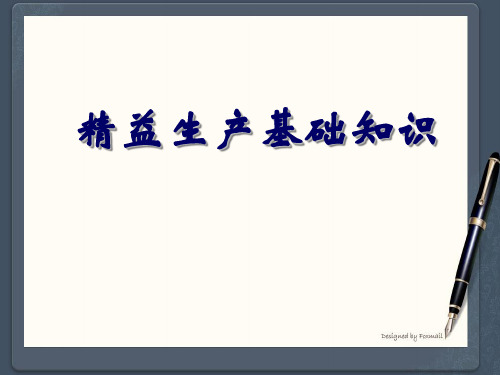
2007-6-7 工业革命
1775(英)
1868(日)
1918 77年工业化历史
1945
1978 62年
29年
2007
139年工业化历史
什么是丰田生产方式,就是丰田式工业工程。 (20世纪)五十年代全日本都在研究和学习美 国的工业工程这种赚钱的工具”
2.、IE的五个意识 问题意识:最大的问题是能否看到和提出问题。 效率意识:提高效率是IE 的基本任务。 成本意识: 降低成本是永恒的追求。 质量意识:追求完美之中质量是灵魂。 改善意识:就是创新,永五休止的创新。 IE意识→IE的理念,所以精益的概念、消除 浪费的概念都由此而来。
十、开展准时化生产方式10步: 第一步:领导决策,统一认识,制定规划。 第二步:,明确思想,清楚内涵,,了解实 施难点、要点 第三步:全员讨论,现状,有针对性地提 出实施意见、措施和办法。 第四步:设立实领导小组和办公室, 制定方案规划,,逐步实施准时化生产。 第五步:深入持久地开展生产现场达 标活动。 第六步:改进生产线布置,采用U 型线实行“一个流”生产或多品种混 流 生产。 第七步:在实施中研析总结具体业务 上的问题,边实践,边巩固,边提高。 第八步:进行现场管理准时化条 件的分析并进行不断改进和完善。 第九步:总结并评价。由试点开始 逐步全面铺开,继续巩固完善。 第十步:在本企业实行准时化生 产的条件下逐步推广到协作配套厂, 达到主机厂、协作配套厂同步实施准 时化生产。
四 精益基础词汇
精益生产基础知识
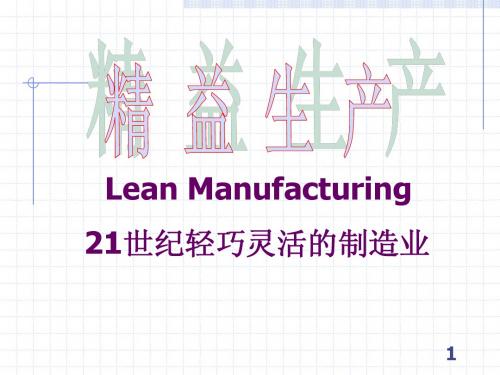
应时间,尽可能多使用掌握多门技能的 员工,使管理结构扁平化,并把资源集 中于需要它们的地方。
例:指导客户QRQC(Quickly Response Quality Control )技术
12
1、源起:名词定义 1.4适用领域
在80年代,这套实践被归纳成精益生产 的10条准则,并且被美国和欧洲和众多 制造企业所采纳。这一管理方法在服务 性组织、物流机构和供应链的应用获得 了不同程度的成功。在网络热潮之后, 人们正在重新对精益生产的原则产生兴 趣,特别是精益哲学对库存削减的强调。
8
1、源起:名词定义
1.1源自丰田生产系统
丰田生产方式反映了日本在重复性生 产过程中的管理思想,其指导思想是 (1)通过生产过程整体优化 (2)改进技术 (3)理顺各种流动(Flow) (4)杜绝超量生产
9
1、源起:名词定义
1.1源自丰田生产系统
(5)消除无效劳动与浪费 (6)充分、有效地利用各种资源 (7)降低成本 (8)改善质量 达到用最少的投入实现最大产出 的目的。
16
1、源起:名词定义
从而削弱中国在过去20年里所依赖的劳 动力成本优势,削弱中国产品在世界 市场上的竞争力和产品出口对于中国 经济增长的推动力。 这些都决定了我们的企业不能够再 粗放生产、盲目管理,安于低生产率、 高能耗、高次品率和低质低价格的现状, 而必须着力于企业管理尤其是生产管 理的改进。
3、成功的精益生产优越性举例
3.4 工厂占用空间——可减至采用大量 生产方式工厂的1/2;(五S的整理)
3.5 成品库存——可减至大量生产方 式工厂平均库存水平的1/4; 3.6 产品质量——可提高3倍(质量 预测方法)
Lean Manufacturing
精益生产基础知识

全 员 生 产维护 Tot a l
Productive Maintenance
拉 系 统 Pull Syst ems
ECRS Elimin ate Co mb in e Rearran g e Simp lify
三、精益屋
改善四原则: ECRS
该作业可以取消吗?
( Eliminate )
该作业可以合并吗?
按双手能同时动作布置现在不妨碍动作的前提下作 采用最舒适的作业位置高
场
业区域应尽量窄
度
3.治具和设备
①.使用便于抓取零件的 物料容器; ②.将两个以上的工具合 并为一个; ③.采用动作数少的联动 快速夹紧机构; ④.用一个动作操作设备 的装置。
①.利用专用夹持机构长 时间拿住目的物; ②.使用设备或者治具完 成简单或者需要力量的作 业; ③.设计双手能同时动作 的夹具;
Lean Production 精益生产
目录
一、精益生产简介 二、精益生产五原则 三、精益屋
一、精益生产简介
精益生产(Lean Production):简称“精益”,是衍生自丰田生产方式(Toyota
Production System)的一种管理哲学。是美国麻省理工学院数位国际汽车计划组
织(IMVP)的专家对日本丰田准时化生产JIT(Just In Time)生产方式的赞誉称
三、精益屋
“取消”具体操作
对程序图上的每一项工序都加以审查,确认其保留的必要性,凡可以取消者一律取消: 取消所有多余的步骤或动作(包括身体、四肢、手和眼的动作); 减少工作中的不规则性,比如将工具存放地点固定,形成习惯性机械动作等; 尽量取消或减少手的使用,如抓握、搬运等; 取消笨拙的或不自然、不流畅的动作; 尽量减少一切肌肉力量的使用; 减少对惯性、动量的克服; 杜绝危险动作和隐患; 除必要的休息外,取消工作中的一切人员和设备的闲置时间。
精益生产知识大全

精益生产知识大全!1、为什么推行精益生产?企业利润公式:售价=成本+利润(计划经济时)售价-成本=利润(市场经济时)2、什么是精益生产?生产方式发展历史:精益生产定义:精益生产(lean production )是美国麻省理工学院数位国际汽车计划组织(IMPV)的专家对日本“丰田生产方式”的赞誉之称。
▪精:即少而精,不投入多余的生产要素,只在适当的时间生产必要数量的市场急需品(或下道工序急需产品);▪益:即所有的经营活动都需要有益有效,具有经济性▪精益生产是当前工业界公认最佳的一种生产系统。
精益生产目标:精益求精,尽善尽美,永无止境追求“七个零”①“零”转产工时浪费(多品种混流生产)②“零”库存(消减库存)③“零”浪费(全面成本控制)④“零”不良(高品质)⑤“零”故障(提高运转率)⑥“零”停滞(快速反应、短交期)⑦“零”灾害(安全第一)3、精益生产推行步骤意识变革:▪取得老板或高层主管支持:精益培训、标杆参观、宣传(员工支持)造势、寻找项目人员组织保障:▪参与者(决策/经营/执行层);“真伪”精益;公平绩效考核体系;跟踪与检核计划与目标:▪三年目标:效率提高50%,库存降低80%,生产周期降低80%,一次性通过率提高40%,货期准时性提高60%。
执行与及时沟通:▪保证项目各个阶段的执行力;项目进展及时与老板或高层沟通;项目人员之间及时沟通,保证信息共享过程中问题解决:▪PDCA循环;要因分析法;5W1H与5WHY;脑力风暴……持续改善:4、精益生产之七大浪费的原因及对策工作分类:浪费:不产生附加价值的工作方法。
即使该工作增值,可花费的时间,资源精力超过了最小的界限。
七大浪费:1)七大浪费--过量生产:过量生产即生产超出客户(或下道工序)所需求的数量以及过早生产过量生产表现形式:1.物流阻塞2.库存、在制品增加3.产品积压4.资金周转率低5.材料、零件过早取得6.影响计划弹性及生产系统的适应能力原因①人员过剩;②设备过剩;③生产浪费大;④业务订单预测错误;⑥生产计划不准确对策a.建立顾客为中心的弹性生产系统b.实现单件流生产c.快速换款d.实施拉动,看板生产e.均衡化生产2)七大浪费--不良改正原因①品质意识淡薄;②标准作业欠缺;③人员技能低;④品质点设置错误;⑤设备,模具造成的不良;⑥品质制度不完善对策a.提高品质意识,做出“三不”品质保证b.完善标准化作业制度c.单件流生产模式d.建立防错机制e.设备,模具定期保养f.推行7S制度3)七大浪费--等待原因①生产线布置不当,物流混乱;②设备配置、保养不当;③生产计划安排不当;④工序生产能力不平衡;⑤材料未及时到位;⑥管理控制点数过多;⑦品质不良对策a.采用均衡化生产(线平衡)b.单件流生产c.自动化及设备保养加强d.备用设备e.实施目视管理f.加强进料控制4)七大浪费--搬运原因①生产线配置不当;②未均衡化生产;③半成品放置区;④生产计划安排不当对策a.厂房精益布局b.单件流生产5)七大浪费--动作12种动作上的浪费1.两手空闲的浪费;2.单手空闲的浪费;3.作业动作停止的浪费;4.作业动作太大的浪费;5.拿的动作交替的浪费;6.步行的浪费;7.转身角度太大的浪费;8.动作之间没有配合好的浪费;9.不了解作业技巧的浪费;10.伸背动作的浪费;11.弯腰动作的浪费;12.重复动作的浪费。
精益生产基础培训-资料

Father of Motion-Time Study 动作-时间研究之父
Father of Assembly Line Concept 组装线概念之父
P – Plan 计划,它包括方针和目标的确定,行In动du计str划y Q的ua制lity定T。ransformation
工业质量变革
D – Do运作,执行计划中的活动。
时间
不可再分的,这是一个比较精确分析动作的方法。
Father of Motion-Time Study 动作-时间研究之父
差别计件工资制:虽然工厂要对工人付出较高的平均日工资,但却能因此而取得更高
Father of Assembly Line Concept
的经济效益。
组装线概念之父
动作经济原则: 关于人体的运用, 关于操作场所的布置 关于工装夹具的设计
还有个一重大贡献就是:在1914年的时候,
Father of Assembly Line Concept 组装线概念之父
首次推行8小时工作制。
Industry Quality Transformation 工业质量变革
Birth of TPS* / Lean Concepts TPS* / 丰田生产方式诞生
标准Lean基础知识简介

LEAN衡量指标--VA
VA(附加价值率):任何改变原物料, VA(附加价值率):任何改变原物料,使它成为顾客愿 附加价值率):任何改变原物料 意花钱支付的产品之作业及活动; 意花钱支付的产品之作业及活动; 计算公式:VA=该鞋型所有工序作业时间之和/ 计算公式:VA=该鞋型所有工序作业时间之和/总制 :VA=该鞋型所有工序作业时间之和 造时间(MLT); 造时间(MLT);
何谓小组设计?
为了减少浪費并达到一双流程所连接附加价值活动的 少浪費并达到一双流程所连接附加价值活动 流程所 序性制造小组 顺序性制造小组。
达成Lean生产管理的工具、手段 ean生 管理的工具、
小组设计的目标
较高的附加价值比 高的附加价 短的前置時 较短的前置時间 少的空间 较少的空间使用 较简单的生 的生产 较简单的生产模式 人员使用的最佳化
LEAN基础概念
讲师:
内容简介
1. Lean 的定义 2. 原景 3. 改善的信念 4. Lean 的衡量指标 5. 幕僚部门的定位 6. 思考角度的转变 7. 拉式生产 8. 一双流 9. 小组设计 10. Lean的基本精神 Lean的基本精神
Lean 定义
定义:消除工厂内一切不必要的浪费,亦称精实生产(Lean 定义:消除工厂内一切不必要的浪费,亦称精实生产(Lean Production); 精干,少而精,意指不投入过多的生产资源; 精:精干,少而精,意指不投入过多的生产资源;益:意指所 有生产活动都有益有效,具有经济性; 有生产活动都有益有效,具有经济性; 精益生产即是一种以最大程度的减少企业生产所占用的资 源和降低企业管理和运营成本为主要目标的生产方式, 源和降低企业管理和运营成本为主要目标的生产方式,同 时它也是一种理念,一种文化; 时它也是一种理念,一种文化;
精益基础知识

2.缺乏系统原则的浪费
缺乏有效的组织管理导致项目研发过程中 缺乏系统的原则 主要体现在: ◆目标不明确; ◆项目管理的流程不清晰; ◆项目团队的职责、权利不明确; ◆员工培训不足。
缺乏系统原则又常常是导致其它浪费的主 要原因
三、 浪费与价值
其它浪费
3.管理中的浪费
◆不必要的批准或签字 ◆多次审阅 ◆多次转手 ◆搬运 ◆等待时间/队列 ◆批处理 ◆过度控制 ◆瓶颈 ◆不必要的信息
★ 走过流程(从头到尾) ★ 绘制流程图 ★ 收集数据 ★ 区分标示“有”与“无”附加价值的工作 ★ 计算生产速率 ★绘制下图(每个操作员每日8小时时间分配) ★消除或减少“无”附加价值的工作 ★挑战“有”附加价值的工作站是否真实 ★建立新布局或流程 ★均衡工作量并安排工作顺序
五、精益事例
五、精益事例
精益基础知识
廖翔 2013-01-18
目录
• • • • • • 何谓精益生产 成本 价值与浪费 如何发现浪费 精益事例 快速换模
一、何谓精益生产 精益生产 Lean Production 丰田生产模式
及时生产Just In Time 适品、适量、适时
只在需要的时候、按需要的量,生产所需的产品
精益生产方式的资源配置是以彻底消除无效劳动和浪费
八种浪费
1.不良、修理的浪费(校正、
返工)为了满足顾客的要求而对产品进
行返工修理 ◆ 额外的修复、选别、追加检查; ◆ 设备、人员、工时的损失; ◆ 材料的损失; ◆ 额外的检查预防人员; ◆ 降价处理; ◆ 出货延误取消订单;
2.加工的浪费(过程不当)
对最终产品或服务不增加价值的过程 ◆ 需要多余的作业时间和辅助设备; ◆ 生产用电、气压、油等的浪费; ◆ 管理工时; ◆ ◆ ……
LEAN-精益生产基础与工具
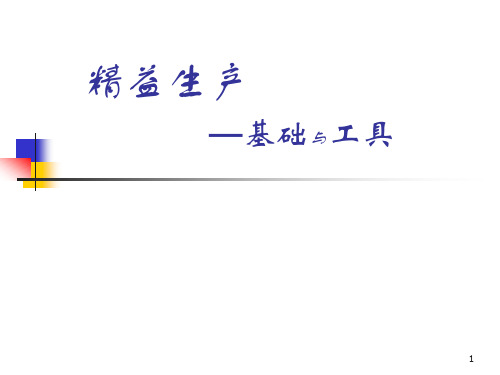
确定标准作业的5个程序 1、确定节拍
节拍=
一天的实际工作时间 一天必要的生产数量
一天的实际工作时间 不要扣除设备故障、等待材料、修正时间 不要扣除作业人员的疲劳、休息时间 不要扣除不合格品的富裕量
8
6 Sigma with Lean
标准作业
确定标准作业的5个程序 2、确定一个单位产品的完成时间
不良为零的结构
• 防误 • TPM
设备 人
• 单品流动 • 标准作业
方法
可视化管理Байду номын сангаас
信息
• 基础教育 • 多能工
物
不生产不良 的检查
27
6 Sigma with Lean
质量保证
防止失误 肯定人的作业有失误 发生率10-100ppm
程度
0 Ⅰ Ⅱ Ⅲ Ⅳ
意识状态
生理状态
无意识、失神 兴奋
9
6 Sigma with Lean
标准作业
确定标准作业的5个程序 3、确定标准作业顺序
10
6 Sigma with Lean
标准作业
确定标准作业的5个程序 4、确定在制品的标准持有量 如果作业按工序的流转顺序进行,在制品只是设备上
加工的部分 如果作业与工序顺序相反,设备间至少保持一个在制
从原材料到成品
4
6 Sigma with Lean
标准作业
标准作业是: 工作的基础 改善的基础 培养人才的基础 对新员工的指导书
5
6 Sigma with Lean
标准作业
标准作业三要素: 1、节拍时间—制造1件成品(半成品)所必需的时间
这个时间不是由设备或人员的能力计算出的,而应该是由客户 (后工序)所需的数及工作时间决定的。 2、作业顺序—从原材料到成品的加工进度不断推进的工程中,作业 者的动作顺序。
精益生产基础知识概述
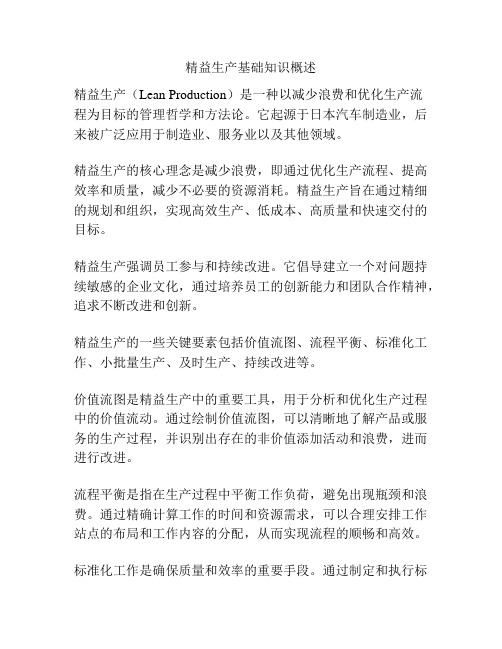
精益生产基础知识概述精益生产(Lean Production)是一种以减少浪费和优化生产流程为目标的管理哲学和方法论。
它起源于日本汽车制造业,后来被广泛应用于制造业、服务业以及其他领域。
精益生产的核心理念是减少浪费,即通过优化生产流程、提高效率和质量,减少不必要的资源消耗。
精益生产旨在通过精细的规划和组织,实现高效生产、低成本、高质量和快速交付的目标。
精益生产强调员工参与和持续改进。
它倡导建立一个对问题持续敏感的企业文化,通过培养员工的创新能力和团队合作精神,追求不断改进和创新。
精益生产的一些关键要素包括价值流图、流程平衡、标准化工作、小批量生产、及时生产、持续改进等。
价值流图是精益生产中的重要工具,用于分析和优化生产过程中的价值流动。
通过绘制价值流图,可以清晰地了解产品或服务的生产过程,并识别出存在的非价值添加活动和浪费,进而进行改进。
流程平衡是指在生产过程中平衡工作负荷,避免出现瓶颈和浪费。
通过精确计算工作的时间和资源需求,可以合理安排工作站点的布局和工作内容的分配,从而实现流程的顺畅和高效。
标准化工作是确保质量和效率的重要手段。
通过制定和执行标准化工作程序,可以减少变异和错误,提高产品和服务的一致性和可靠性。
小批量生产和及时生产是精益生产中的两个重要原则。
小批量生产可以减少库存和等待时间,降低成本和资源消耗。
及时生产则强调按需生产和按时交付,避免过产和库存积压。
持续改进是精益生产的核心精神。
它强调通过持续地观察、分析和改进,不断优化生产过程和提升绩效。
持续改进需要建立一个鼓励员工提出问题和改进建议的文化,同时提供必要的培训和支持。
总之,精益生产是一种在全球范围内被广泛应用的管理方法,它通过减少浪费和优化生产流程,实现高效生产、低成本、高质量和快速交付的目标。
它不断追求改进和创新,强调员工参与和持续学习,是现代企业管理中的重要理念和工具。
精益生产(Lean Production)是一种在制造业和服务业等领域中被广泛应用的管理哲学和方法论。
精益生产的培训资料
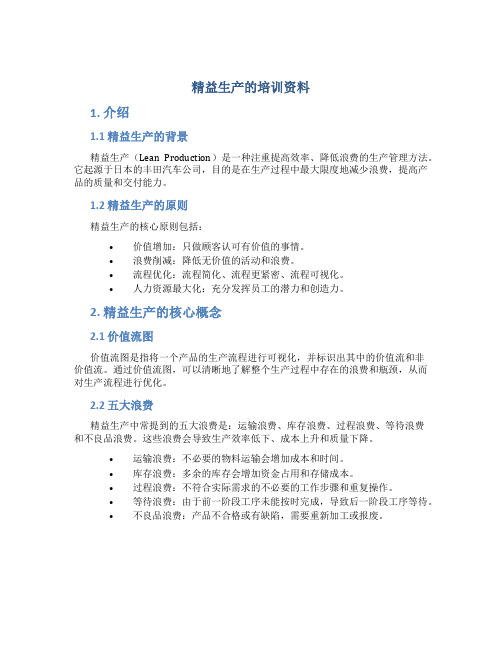
精益生产的培训资料1. 介绍1.1 精益生产的背景精益生产(Lean Production)是一种注重提高效率、降低浪费的生产管理方法。
它起源于日本的丰田汽车公司,目的是在生产过程中最大限度地减少浪费,提高产品的质量和交付能力。
1.2 精益生产的原则精益生产的核心原则包括:•价值增加:只做顾客认可有价值的事情。
•浪费削减:降低无价值的活动和浪费。
•流程优化:流程简化、流程更紧密、流程可视化。
•人力资源最大化:充分发挥员工的潜力和创造力。
2. 精益生产的核心概念2.1 价值流图价值流图是指将一个产品的生产流程进行可视化,并标识出其中的价值流和非价值流。
通过价值流图,可以清晰地了解整个生产过程中存在的浪费和瓶颈,从而对生产流程进行优化。
2.2 五大浪费精益生产中常提到的五大浪费是:运输浪费、库存浪费、过程浪费、等待浪费和不良品浪费。
这些浪费会导致生产效率低下、成本上升和质量下降。
•运输浪费:不必要的物料运输会增加成本和时间。
•库存浪费:多余的库存会增加资金占用和存储成本。
•过程浪费:不符合实际需求的不必要的工作步骤和重复操作。
•等待浪费:由于前一阶段工序未能按时完成,导致后一阶段工序等待。
•不良品浪费:产品不合格或有缺陷,需要重新加工或报废。
2.3 价值流分析通过对价值流进行分析,可以找到改善生产流程的机会。
分析包括识别价值和非价值流、测量价值流和非价值流的时间和成本,以及找出瓶颈和瓶颈的原因。
在分析的基础上,可以制定改进计划和实施措施。
3. 精益生产的实施步骤3.1 精益生产的基础准备在实施精益生产之前,需要进行一些基础准备工作,包括:•培训员工:让员工了解精益生产的基本原理和方法,以及其对企业的意义。
•设立团队:组建一个精益生产改善团队,负责推动和监督改进工作。
•确定目标:明确实施精益生产的目标,如提高产能、降低成本等。
•收集数据:对现有生产流程进行数据采集和分析,找出存在的问题和瓶颈。
3.2 精益生产的改进步骤根据实际情况,精益生产的改进步骤可以分为以下几个阶段:•价值流分析:通过价值流图和价值流分析,找出生产流程中的浪费和瓶颈。
- 1、下载文档前请自行甄别文档内容的完整性,平台不提供额外的编辑、内容补充、找答案等附加服务。
- 2、"仅部分预览"的文档,不可在线预览部分如存在完整性等问题,可反馈申请退款(可完整预览的文档不适用该条件!)。
- 3、如文档侵犯您的权益,请联系客服反馈,我们会尽快为您处理(人工客服工作时间:9:00-18:30)。
Creates a system which is intolerant of production abnormalities (不能容忍生产异常)
Eliminates waste in production processes (消除生产过程浪费)
Reduces lead times (缩短前置生产时间)
2019-10-13
Shenzhen Functional Excellence
Abnormality Response Process
(异常反应过程)
Q C D S
Measure impact (衡量影响)
React to problem (发现问题)
MAN MACHINE
EFFECT
Alert team (提醒 同事)
Raw materials (原料) Equipment (设备)
Labor (人力)
2019-10-13
Space (场地)
Shenzhen Functional Excellence
JIT Principles (及时生产三原理)
及时生产 JIT
Takt time (节拍生产)
METHOD
MATERIAL
Find root cause (找出原因)
(提出改善, 进行试 验)
Develop and test improvement
Ensures on-time delivery (保证准时交货)
Quality…Cost…Delivery…Safety…
2019-10-13
Shenzhen Functional Excellence
Jidoka is (自働化是)…
An immediate response to an abnormal condition within the
process (异常情况, 立即响应) Goal: Prevent a defective product from being passed to the next operation. (目的: 防止不良品流向下一工序) Equipment autonomation – capable machine processes that enable separation of machine and operator (设备自働化, 人机分开化) Goal: Multi-process handling, increased labor productivity. (目的: 实现多工序操作, 提升劳动生产力)
Pull system (拉动生产)
One piece follow (单件流生产)
2019-10-13
Shenzhen Functional Excellence
Takt Time (节拍时间)
Takt, 德语,意为节拍,与英文 Pace 意同。
2019-10-13
Shenzhen Functional Excellence
One Piece Follow (单件流)
(批量生产)
Batch
Fake Flow (假流线生产)
1-Piece Flow
(单件流生产)
2019-10-13
Shenzhen Functional Excellence
One Piece Follow (单件流)
“A Sea of WIP” (一大堆半成品)
• What the customer wants (客户所需产品) • In the quantity the customer wants (客户要求数量) • When the customer wants it (客户指定时间)
While using the minimum (使用最少的):
(站立操作, 边走边做)
Pull system discipline (拉动系统训练)
“Std operations” defined and implemented
(定义和实施“标准化运作”)
2019-10-13
Shenzhen Functional Excellence
JIT Benefits(及时生产的好处)
1 3
2
3 4 5 3
2019-10-13
Shenzhen Functioion System House 丰田生产方式(精益生产屋)
安全 品质 成本 交付
及时生产 • 流线生产 • 节拍生产 • 拉动系统
自働化 • 安灯 • 防错系统
均衡生产 设备综合效率
标准化作业 灵活的人力系统 稳定性(工艺,人员) 员工与管理者之间的相互信任
改善 5S
2019-10-13
Shenzhen Functional Excellence
Just-In-Time Is (及时生产是)...
A manufacturing system which produces (这个系统生产):
Shenzhen Functional Excellence
精益生产基础知识
(期刊版)
第一期(总第一期)
2019-10-13
Shenzhen Functional Excellence
Hot Topic目录
Lean House 精益生产屋 Just-In-Time 及时生产 Jidoka 自働化 Level Loading 均衡生产 8 Waste 八大浪费
Small, inexpensive machines in process order (小巧便宜机器) One-piece flow production, 单件流生产
JIT Elements (及时生产的要素)
Ergonomically-correct operations (人机正确结合)
Standing operations, moving while working
“Now You See It!” (“你看吧!”)
2019-10-13
Solectron Shenzhen Functional Excellence
Pull System (拉动系统)
2019-10-13
Shenzhen Functional Excellence
JIT Elements (及时生产的要素)