FMEA_详细解说与导入步骤
实施系统fmea的5个步骤

实施系统FMEA的5个步骤1. FMEA简介FMEA(Failure Mode and Effects Analysis),即故障模式与影响分析,是一种常用的风险管理工具,用于评估系统、过程或产品的潜在故障模式以及它们对系统性能的影响。
FMEA帮助识别潜在的故障模式,并提前采取措施以减少这些故障对系统造成的危害。
在实施系统FMEA的过程中,可以有效地对系统的风险进行定量分析和管理,以确保系统的可靠性和安全性。
2. 系统FMEA的步骤步骤一:确定要分析的系统范围在开始FMEA之前,首先需要明确要分析的系统范围。
这可以是一个产品、一个过程或一个系统。
明确系统范围有助于确定所需的资源和参与者,并确保分析的焦点正确。
步骤二:制定团队和计划在FMEA过程中,需要组建一个专门的团队来执行分析工作。
团队应包括不同领域的专家,以确保对系统的全面分析。
团队成员可以包括设计工程师、质量工程师、生产工程师等。
同时,制定一个详细的计划,包括FMEA的时间表和分工,以确保分析工作按照预期进行。
步骤三:识别系统的故障模式在第三步中,团队需要对系统进行全面的故障模式识别。
这包括对每个组成部分的潜在故障模式进行分析,以及这些故障模式对系统性能的影响。
可以使用多种工具和方法,如故障树分析、故障模式描述等,来识别系统的故障模式。
步骤四:评估故障的严重程度与发生概率在评估故障模式时,需要考虑故障的严重程度以及其发生的概率。
严重程度指的是故障发生后对系统造成的影响程度,包括安全性、可靠性、生产效率等方面。
发生概率指的是故障模式发生的概率。
通过对故障的严重程度和发生概率进行评估,可以帮助确定需要重点关注和处理的故障模式。
步骤五:制定改进措施与风险控制计划在分析完系统的故障模式后,团队需要制定相应的改进措施和风险控制计划。
改进措施可以包括改进设计、改变工艺、提供培训等。
而风险控制计划则是针对故障模式的风险制定的具体措施,包括监控、预防控制、纠正控制等。
最全的FMEA教程和讲解

目
CONTENCT
录
• FMEA概述与基本原理 • FMEA实施流程与步骤 • FMEA关键技术与方法论 • FMEA在各行业应用案例分析 • FMEA与其他质量管理工具结合应
用探讨 • 总结回顾与未来发展趋势预测
01
FMEA概述与基本原理
FMEA定义及发展历程
FMEA定义
通过对汽车设计、制造过程中可能出现的故障 模式进行识别,以便在产品投放市场前采取预 防措施。
制定改进措施
针对识别出的故障模式和影响,制定相应的设 计、制造、检验等改进措施,提高产品质量和 安全性。
航空航天:确保飞行安全可靠性
分析系统复杂性
航空航天器系统复杂,涉及多个子系统和部件,FMEA可 帮助识别各部件之间的潜在故障和相互作用。
评估风险等级
分析故障模式对能源设备运行和人员安全的影响程度, 评估风险等级。
制定预防措施
针对识别出的安全隐患和风险等级,制定相应的预防 措施和应急预案,确保能源领域生产安全。
05
FMEA与其他质量管理工具结合应用探讨
FMEA与六西格玛管理法相结合
01 02
流程优化
六西格玛管理法强调流程优化与变异减少,而FMEA可以在流程设计初 期识别潜在失效模式,为六西格玛的DMAIC(定义、测量、分析、改 进、控制)循环提供输入。
FMEA(Failure Mode and Effects Analysis,失效模式与影响分析) 是一种预防性的质量工具,用于识别、评估和优先处理潜在的问题 或故障模式,以减少产品或过程在设计和开发阶段的风险。
发展历程
FMEA起源于20世纪40年代的军事领域,后来逐渐应用于航空、汽 车、电子等各个行业。随着质量管理理念的不断发展和完善,FMEA 已经成为一种广泛应用于产品设计和过程控制的重要工具。
fmea的7步法

fmea的7步法FMEA的7步法随着现代工业的发展,各行各业对产品质量和安全性的要求越来越高。
为了确保产品在设计和生产过程中的质量和可靠性,FMEA(失效模式与影响分析)成为一种被广泛采用的方法。
FMEA通过对潜在失效模式的分析和评估,可以帮助我们识别和减少潜在的风险和问题,从而提高产品的质量和可靠性。
本文将介绍FMEA的七个步骤,以帮助读者更好地理解和应用FMEA。
第一步:确定团队和范围在进行FMEA之前,首先需要确定一个专门的团队来进行分析。
团队成员应包括设计师、工程师、生产人员等相关人员。
确定团队后,需要明确分析的范围,包括产品、过程或系统等。
确定团队和范围是FMEA分析的基础,确保分析的全面性和准确性。
第二步:收集产品和过程信息在进行FMEA之前,需要收集关于产品和过程的相关信息。
这些信息可以包括产品规格、设计图纸、工艺流程、设备参数等。
通过收集这些信息,可以全面了解产品和过程的特点和要求,为后续的分析提供准确的基础。
第三步:识别潜在失效模式在这一步骤中,团队成员需要识别出产品或过程中可能出现的潜在失效模式。
失效模式是指产品或过程在特定条件下的失效形式。
通过集思广益和经验分享,团队成员可以识别出多种可能的失效模式,包括设计失效、工艺失效、材料失效等。
第四步:评估失效的严重性在这一步骤中,团队成员需要评估每个失效模式的严重性,即失效对产品或过程的影响程度。
评估严重性可以从多个方面考虑,如安全性、可靠性、经济性等。
通过评估失效的严重性,可以确定优先处理的失效模式,以确保资源的合理利用。
第五步:确定失效的原因在这一步骤中,团队成员需要分析并确定每个失效模式的原因,即导致失效发生的根本原因。
原因分析可以使用各种方法,如鱼骨图、5W1H法等。
通过确定失效的原因,可以为下一步的控制措施提供指导和依据。
第六步:制定控制措施在这一步骤中,团队成员需要制定相应的控制措施,以减少或消除潜在失效的发生。
控制措施可以包括改进设计、优化工艺、改进材料等。
FMEA分析讲解
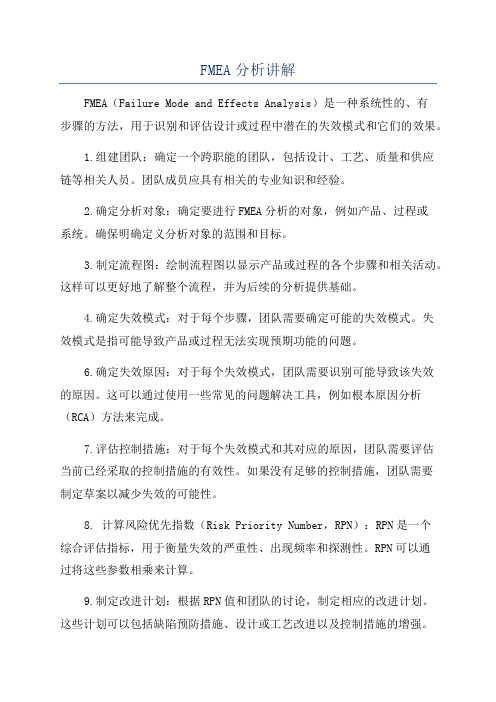
FMEA分析讲解FMEA(Failure Mode and Effects Analysis)是一种系统性的、有步骤的方法,用于识别和评估设计或过程中潜在的失效模式和它们的效果。
1.组建团队:确定一个跨职能的团队,包括设计、工艺、质量和供应链等相关人员。
团队成员应具有相关的专业知识和经验。
2.确定分析对象:确定要进行FMEA分析的对象,例如产品、过程或系统。
确保明确定义分析对象的范围和目标。
3.制定流程图:绘制流程图以显示产品或过程的各个步骤和相关活动。
这样可以更好地了解整个流程,并为后续的分析提供基础。
4.确定失效模式:对于每个步骤,团队需要确定可能的失效模式。
失效模式是指可能导致产品或过程无法实现预期功能的问题。
6.确定失效原因:对于每个失效模式,团队需要识别可能导致该失效的原因。
这可以通过使用一些常见的问题解决工具,例如根本原因分析(RCA)方法来完成。
7.评估控制措施:对于每个失效模式和其对应的原因,团队需要评估当前已经采取的控制措施的有效性。
如果没有足够的控制措施,团队需要制定草案以减少失效的可能性。
8. 计算风险优先指数(Risk Priority Number,RPN):RPN是一个综合评估指标,用于衡量失效的严重性、出现频率和探测性。
RPN可以通过将这些参数相乘来计算。
9.制定改进计划:根据RPN值和团队的讨论,制定相应的改进计划。
这些计划可以包括缺陷预防措施、设计或工艺改进以及控制措施的增强。
10.更新FMEA文档:根据改进计划的实施和反馈,更新FMEA文档,确保记录和通信的准确性。
通过执行FMEA分析,可以识别并解决潜在的问题,并提供改进计划来提高产品质量和过程可靠性。
它还可以帮助组织更好地理解产品或过程中的失效模式及其影响,并采取相应的预防措施。
需要注意的是,FMEA分析并不是一次性的任务,而是一个持续改进的过程。
随着时间的推移和业务环境的变化,FMEA分析需要进行定期评估和更新,以确保保持其有效性和准确性。
最全的FMEA教程和讲解
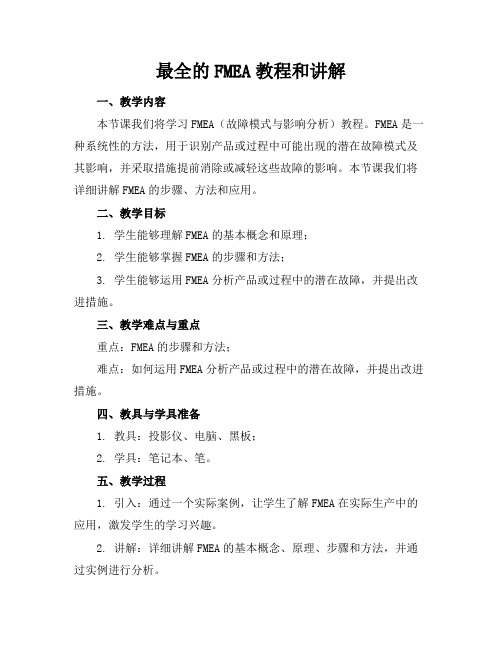
最全的FMEA教程和讲解一、教学内容本节课我们将学习FMEA(故障模式与影响分析)教程。
FMEA是一种系统性的方法,用于识别产品或过程中可能出现的潜在故障模式及其影响,并采取措施提前消除或减轻这些故障的影响。
本节课我们将详细讲解FMEA的步骤、方法和应用。
二、教学目标1. 学生能够理解FMEA的基本概念和原理;2. 学生能够掌握FMEA的步骤和方法;3. 学生能够运用FMEA分析产品或过程中的潜在故障,并提出改进措施。
三、教学难点与重点重点:FMEA的步骤和方法;难点:如何运用FMEA分析产品或过程中的潜在故障,并提出改进措施。
四、教具与学具准备1. 教具:投影仪、电脑、黑板;2. 学具:笔记本、笔。
五、教学过程1. 引入:通过一个实际案例,让学生了解FMEA在实际生产中的应用,激发学生的学习兴趣。
2. 讲解:详细讲解FMEA的基本概念、原理、步骤和方法,并通过实例进行分析。
3. 练习:让学生分组进行练习,运用FMEA分析给定的产品或过程,并提出改进措施。
4. 讨论:让学生分享各自的分组练习成果,讨论改进措施的可行性和有效性。
六、板书设计1. FMEA的基本概念和原理;2. FMEA的步骤和方法;3. 实例分析。
七、作业设计1. 题目:请运用FMEA分析给你们分组的产品或过程,并提出改进措施。
2. 答案:根据实际分析结果,给出改进措施。
八、课后反思及拓展延伸1. 反思:回顾本节课的教学内容,思考如何更好地让学生掌握FMEA的方法和应用。
2. 拓展延伸:研究FMEA在其他领域的应用,如质量管理、安全管理等,并尝试将其应用于实际工作中。
教学内容完毕。
重点和难点解析一、教学内容本节课我们将学习FMEA(故障模式与影响分析)教程。
FMEA是一种系统性的方法,用于识别产品或过程中可能出现的潜在故障模式及其影响,并采取措施提前消除或减轻这些故障的影响。
本节课我们将详细讲解FMEA的步骤、方法和应用。
重点和难点解析:1. 重点:FMEA的步骤、方法和应用;2. 难点:如何运用FMEA分析产品或过程中的潜在故障,并提出改进措施。
FMEA分析流程

FMEA分析流程FMEA(Failure Mode and Effects Analysis)是一种用来识别、评估和减少产品或过程中潜在故障模式及其危害的方法。
它是一种系统性的分析方法,用于确保产品或过程具备高度的可靠性和质量。
FMEA分析流程由以下六个主要步骤组成:1.制定FMEA团队:选择合适的团队成员来执行FMEA分析,团队成员应具备相关领域的知识和经验,如设计、工艺、制造和质量控制。
2.定义FMEA范围:明确FMEA的范围和目的。
确定所要分析的产品或过程,以及分析的具体阶段(设计、制造等)。
3.识别潜在故障模式:团队成员会通过分析产品或过程的各个环节来识别潜在故障模式。
这些模式包括设计、材料、加工、装配等环节中可能导致故障或错误的步骤。
4.评估故障模式的严重性:对识别出的潜在故障模式进行评估,确定其对产品质量和可靠性的影响程度。
这包括通过风险矩阵或其他评估工具对故障模式进行定量或定性的评价。
5.分析故障原因和控制措施:确定导致故障模式发生的原因,并提出相应的控制措施来减少或消除这些原因。
控制措施可能包括改进设计、改变工艺、引入新的材料等。
6.制定FMEA报告和跟踪措施:根据分析结果制定FMEA报告,该报告包括识别出的故障模式、评估结果和控制措施。
同时,制定FMEA跟踪措施,以确保控制措施的有效实施和监控。
以上就是FMEA分析的主要流程。
FMEA分析的目的是提前识别和解决潜在的故障模式,以此改进产品的可靠性和质量。
FMEA方法既可以应用于产品设计阶段,也可以应用于生产过程的改进和优化。
通过系统性的分析和评估,FMEA分析有助于提高产品的可靠性、降低故障率,并帮助企业遵循相关质量标准和规范。
FMEA的概要和导入指引

FMEA概要和导入指引"FMEA"这个文字,在品质管理和产品开发中经常出现."FMEA"是可靠性技术的一部分.但是如果具体来讲的话,它又是指那些东西呢?让我们来探讨一下设计/生产流程设计/材料 · 部品的供应/制造现场等各部门包括其失败事例的导入方法吧!第一部分第一章1. FMEA是··········P4(1) FMEA的起源.2. 机能展开FMEA的导入P5(1) "机能展开FMEA"· Case 1: 从哪里开始入手呢? ~在试作设计方面~P5· Case 2: 要确认的项目有哪些? ~在生产流程设计方面~P6· Case 3: 要把握的关键在哪里? ~在材料/部品的供应方面~P7· Case 4: 稳定性的关键在哪里? ~在制造现场~P8(2) 在那个时候我们推荐机能展开FMEA.P9(3) 机能展开FMEA的推进方法P10·决定主题如果无明确的目的……P11·人员的选定和情报的收集P12如果人员的选定和情报的收集不充分的话……P13·研究范围和对象的定义P14如果研究范围和对象不明确的话……P15·作成展开图P16如果没有能很好地作成展开图……P17·进行创造性的集团研究讨论P18创造性和集团研究……P19·记入表格(*如果能够记入表格的话,会很方便)P20/21表格……P22·计算重要度P23重要度的评价不是很清楚的话……P24·结果的活用P25如果不能很好地活用表格的话……P26(3) 总结P27第二部分第二章1. FMEA的见解和特色.P282. FMEA的优点P283. FMEA的实施法P284. FMEA的种类和使用分类P295. 工程FMEA的目的P296. FMEA的分析和步骤P307. FMEA开始的准备事项P308. FMEA的实施顺序P319. FMEA流程图的作成P3210. 将工程流程图的信息记入FMEA表格P3211. 工程机能"目的"和"手段"的记录法P3312. 予测故障码P3313. 被预测故障码和发生原因的关系P3414. 重要故障的选定和处理P3415. 活用SEDAC图表,提高[工程FMEA]的追踪效果P35依照SEDAC图表,进行FMEA的追踪方法(事例)P36工程FMEA的分析顺序P37 ·顺序1~4P38 ·顺序5~8P39 ·顺序9~11P40付录 - 1用于工程FMEA的工程流程图P41付录 - 2工程FMEA表P42付录 - 3SEDAC图表单P431. FMEA 是·······FailureModeand Effect Analysis(故障)(状态)(影响)(解析)所谓FMEA 就是提炼出在设计阶段和材料/部品供应, 生产部的生产流程设计, 制造现场等各个环节潜在的能够预测到的各种将会发生的不良,并且分析它可能会给产品带来什么样的影响,最后对此不良状况作出相应对策的一种手法.预防形式的品质管理1. FMEA 的起源美国1950年初期,在喷气式引挈装备的新型战斗机的开发上,出现了油压和电子操纵系统等方面的问题.为了解决这个问题,美国海军和glamour 公司进行了与原来不同的新的解析方法的开发.最后终于发展到了具有可靠性和安全性的解析方法,也就是我们所说的FMEA.特别有名的是,在60年代NASA Apollo 计划的实施上,更加提高了可靠性和安全性的评价成果. 1965年FMEA 作为论文发表,安全性作为强有力的手法被广泛应用于产业界. 1974年在美国原子力委员会的的报告会上,FMEA 也被作为一种手法而发表.1976年日本化学技术连盟信赖性小组发行了<FMEA 解说书>,并且从80年代开始此手法被导入日本主要产业.机能展开FMEA的导入2. "机能展开FMEA"(1) 此时我们推荐的是<机能展开FMEA>.我们在安装或设备的开发,生产流程的设计等项目的进程中,常常会遇到各种各样的技术性的问题,但有些时候我们却不明白问题是出现在哪里的,此时不知大家有没有用过诸如下面的解析方法.case 1 : 从什么地方入手呢? ~在试作设计方面~case 2 : 要确认的项目是什么? ~在生产流程设计方面~case 3 : 要把握的关键是什么? ~在材料/部品的供应方面~case 4 : 稳定的关键在哪里? ~在制造现场~(2) 那个时候我们向您推荐机能展开FMEA.FMEA是[Failure Mode Effect Analysis]的简略,日本又叫做[故障模式影响解析],它是具有代表性的可靠性设计手法的一种.把影响着眼改善的机能的各种要素之间的关系明确化以后,就能够很好地把握住其中对机能的达成起重要影响作用的要素.根据各要素的重要度进行排位,从最重要的开始,一个一个地采取对应的有效的改善活动,这样的话就可以把我们提出的课题一个一个地有效地解决.但是这种机能展开与原来我们在一个工程或一种部品上展开的FMEA是不同的,这种机能的展开是接合/接续/接触/滑动等多个方面中无一泄漏地将问题列出来进行解决.所以此FMEA并不是以对象为单位的,它可以应用于一部分的构成要素/技术中.更为重要的是要将我们着眼研究的课题成为与此课题有关系的所有技术人员的共同课题,在前工程与后工程中同时进行这种课题的研究的情况也时有出现.然后再将研究的课题数据化,使同样的技术可以应用到下一个模型的研究,并起到很好的作用.如今的FMEA,越来越进化成为一种自由度很高的手法.不管是在大规模的系统研究中还是在一些电子制品,设备,部品材料,软件,生产流程设计,制造,运用的工程中,都把此手法作为一种提高产品可靠性安全性,使生产效率向上,低减成本的一种研究手法.(3)机能展开FMEA推荐的方法在实际的开发设计现场中,经常能够听到FMEA是条件要求很高的方法.其理由是"通过教材做无效果" , "对象项目不适合FMEA" , "要做的事情像山一样多,根本抽不出时间来" , "进行了FMEA的改善没有效果"等等.的确如果能够很好地进行FMEA是会有好的效果出来的.但是如果没有抓住要领就进行FMEA的话,那么往往会导致"有劳无功"或"半途而法废"的结果出现.在这里我们就机能展开FMEA的推进方法,结合各阶段中成功与失败的事例来进行一下实践的解说.决定主题在实施FMEA的时候,首先我们要明确针对"哪个项目" , "什么目的"而进行的FMEA?进行FMEA 是想得到一种什么样的结果?并且把这种结果怎样进行活用?这是相当重要的.我们在后边介绍的记录表格里边将会出现这些内容,明确了这些内容以后,责任者再结合自己的前进(改善)方向,进行FMEA,这样做就能够防止在FMEA时迷失方向,达到意想不到的效果.·进行什么项目的FMEA?计划, 开发, 生产流程, 制造, 资材, 保养, 物流·什么目的?提高可靠性, 提高作业性, 降低成本, 设计改善, 工程改善, 评价/检验方法的开发,试验计划的作成, 工程/材料研究项目的提出, 作业标准化,下个机型投产时的可靠性研究资料.决定主题 ··· ·· ··失败事例<没有能够明确目的>如果没有明确为什么要进行FMEA?进行FMEA想要改善什么课题?这些必要的内容的话,那么 在对应时就不能够提出明确的意见,反而会担心这个,担心那个,结果造成的主题内容偏移,这种情况 也是时有出现的.★目的不明确的话 ·· ·· ··究竟想要改善什么呢?讨论(结应)的结果结果成为这样的结果 ·· ·· ··为了避免造成上面的结果, 就要求每一个参加FMEA的人员都要有决心,首先最重要的还是一 开始就要有明确的目的.第 11 页成员的选定和消息的收集FMEA研究的深度和广度,取决于参加人员的知识量与经验量.因此此活动最好尽量让大范围内 的人员参加,收集消息越多越好,但尽量不要收集与主题关系不大的内容.设计人员当然是要参加的, 最好是集中开发,生产流程,制造等各前后工序的责任人一起参加,这样的话就能够在早期就决定了主 题,这样后面的内内容便也能够顺利地进行了.活动中为了能够获得更多的新的建意和方法,不仅老手 要参加,一些年青的技术工作者也有必要参加.<专门性>★★在前期提出共同的问题点(主题).★★· 开发, 设计(电气, 机构, 软件), 材料, 生产技术, 制造, 物流, 可靠性, 服务消息. <经验> ★★ 为了扩大讨论事项的深度和广度. ★★ · 老手, 新手, 前机型的负责人. <职位> ★★ 一般职员, 企画领导, 管理职员. ★★第 12 页成员的选定和消息的收集 ··· ·· ··失败事例[成员的选定和消息的收集不充分的话··] ·· ··同一部门的人集中在一起进行研究,见解和想法都大致相同,又得不到其它部门的情报,所 以研究的课题虽然有深度,但是却不能够全方位的考察.这样的话必然导致会有重要的课题(问题) 被遗漏.到设计已经开始以后才变更,对策已经晚了.更可能会造成产品流入市场以后发生故障.★光是同一部门的人进行研究的结果···· ···啊~有这样的事!如果只从一个方面出发进行研究,就容易会像上图一样偏移方向。
FMEA作业指导书
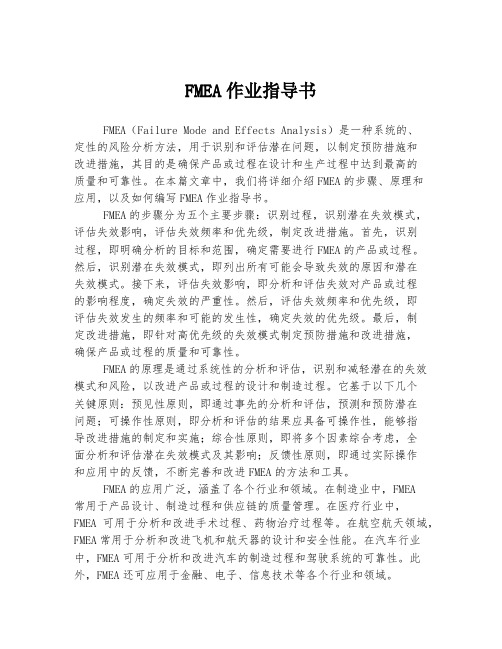
FMEA作业指导书FMEA(Failure Mode and Effects Analysis)是一种系统的、定性的风险分析方法,用于识别和评估潜在问题,以制定预防措施和改进措施,其目的是确保产品或过程在设计和生产过程中达到最高的质量和可靠性。
在本篇文章中,我们将详细介绍FMEA的步骤、原理和应用,以及如何编写FMEA作业指导书。
FMEA的步骤分为五个主要步骤:识别过程,识别潜在失效模式,评估失效影响,评估失效频率和优先级,制定改进措施。
首先,识别过程,即明确分析的目标和范围,确定需要进行FMEA的产品或过程。
然后,识别潜在失效模式,即列出所有可能会导致失效的原因和潜在失效模式。
接下来,评估失效影响,即分析和评估失效对产品或过程的影响程度,确定失效的严重性。
然后,评估失效频率和优先级,即评估失效发生的频率和可能的发生性,确定失效的优先级。
最后,制定改进措施,即针对高优先级的失效模式制定预防措施和改进措施,确保产品或过程的质量和可靠性。
FMEA的原理是通过系统性的分析和评估,识别和减轻潜在的失效模式和风险,以改进产品或过程的设计和制造过程。
它基于以下几个关键原则:预见性原则,即通过事先的分析和评估,预测和预防潜在问题;可操作性原则,即分析和评估的结果应具备可操作性,能够指导改进措施的制定和实施;综合性原则,即将多个因素综合考虑,全面分析和评估潜在失效模式及其影响;反馈性原则,即通过实际操作和应用中的反馈,不断完善和改进FMEA的方法和工具。
FMEA的应用广泛,涵盖了各个行业和领域。
在制造业中,FMEA常用于产品设计、制造过程和供应链的质量管理。
在医疗行业中,FMEA可用于分析和改进手术过程、药物治疗过程等。
在航空航天领域,FMEA常用于分析和改进飞机和航天器的设计和安全性能。
在汽车行业中,FMEA可用于分析和改进汽车的制造过程和驾驶系统的可靠性。
此外,FMEA还可应用于金融、电子、信息技术等各个行业和领域。
fmea使用方法

fmea使用方法一、FMEA是啥。
1.1 FMEA啊,就是失效模式与效应分析(Failure Mode and Effects Analysis)。
这可是个好东西呢,就像一个放大镜,能把潜在的问题找出来,防患于未然。
它不是什么高大上、让人摸不着头脑的玩意儿,简单来说,就是提前琢磨可能出岔子的地方,然后想办法解决。
1.2 这就好比你要出门旅行,你得提前想想路上可能遇到啥麻烦事,像车坏了、天气不好之类的。
FMEA在工程或者生产领域,就起着这样的作用。
二、FMEA的使用步骤。
2.1 第一步,得组建个团队。
这团队可不是乌合之众,得是各个方面的行家凑一块儿。
就像盖房子,你得有泥瓦匠、木工、电工这些个专业人士。
大家坐下来,八仙过海,各显神通,把自己懂的那一块可能出现的问题都给抖搂出来。
2.2 第二步,识别潜在的失效模式。
这就像是在鸡蛋里挑骨头,但这骨头不挑出来可不行。
比如说在汽车生产中,发动机启动不了、刹车失灵这些都是非常严重的失效模式。
这一步要把能想到的所有可能出问题的情况都列出来,一个都不能少,可不能做“马大哈”。
2.3 第三步,分析失效的后果。
这后果有轻有重,就像下象棋,一步走错,可能满盘皆输,也可能只是小损失。
比如在电子产品中,屏幕偶尔闪一下可能就是小问题,但要是整个系统崩溃了,那可就是大麻烦了。
要把这些后果都清清楚楚地写出来,让大家心里有数。
三、FMEA的好处。
3.1 首先呢,它能提高产品或者流程的可靠性。
这就好比给你的东西或者做事的方法上了一道保险。
有了FMEA,就像是给产品或者流程打了预防针,能避免很多不必要的麻烦。
就像俗话说的“未雨绸缪”,总比出了问题再去救火要强得多。
3.2 它能节省成本。
你想啊,如果产品到了用户手里才发现问题,那可就麻烦了。
召回啊、维修啊,这都是白花花的银子。
要是提前用FMEA把问题解决了,这钱不就省下来了嘛。
这就叫“吃不穷,穿不穷,算计不到就受穷”,在企业里也是这个理儿。
FMEA工作流程及说明

FMEA工作流程及说明---1. 背景介绍失效模式与影响分析(Failure Mode and Effects Analysis,简称FMEA)是一种旨在识别和评估潜在失效模式,并采取预防措施以降低风险的方法。
FMEA既可以在产品开发阶段进行,也可以在运营和生产过程中应用。
2. FMEA的目的FMEA的目的是识别潜在的失效模式、评估失效对系统、产品或过程的影响,并制定相应的纠正措施。
通过FMEA,可以提前预防和减少风险,确保产品质量和安全性。
3. FMEA工作流程FMEA通常包括以下步骤:步骤一:确定分析的范围和目标在开始FMEA前,需要明确分析的范围和目标,确定需要评估的系统、产品或过程。
步骤二:组建FMEA团队FMEA团队由相关专业人员组成,包括设计工程师、生产工程师、质量控制人员等。
团队成员应根据自身的专业知识和经验,共同参与FMEA分析。
步骤三:识别失效模式团队成员通过头脑风暴等方法,识别系统、产品或过程可能存在的失效模式,记录下潜在的失效模式。
步骤四:评估失效影响针对每个失效模式,团队成员评估失效对系统、产品或过程的影响程度,包括其严重性、故障频率和检测难度等方面。
步骤五:确定风险优先级根据失效的严重性、故障频率和检测难度等因素,计算每个失效模式的风险优先级,以确定需要优先关注的失效模式。
步骤六:制定纠正措施针对风险优先级较高的失效模式,团队成员制定相应的纠正措施,包括风险预防措施和风险缓解措施。
步骤七:实施纠正措施团队成员负责实施制定的纠正措施,并监控其有效性和实施进度。
4. 总结FMEA是一种有效的风险管理工具,可以帮助企业识别和评估潜在失效模式,并采取预防措施降低风险。
在实施FMEA过程中,要明确分析的范围、组建专业团队、识别失效模式、评估失效影响、确定风险优先级以及制定和实施纠正措施。
通过不断改进和优化FMEA工作流程,可以提高产品质量和安全性,降低生产风险。
FMEA_详细解说与导入步骤

11/12/2019
FMEA是評估設計可靠度之一種方法。 在1950年由美國之GRUMMAN公司針對新型噴射戰
鬥機時,為了評估飛機操作系統某一元件之失效分析 所採用之解析方法。 1957年Boeing飛機公司與Martin公司正式將FMEA列入 工程指導手冊。在同時期,美國NASA與軍方也開始應 用FMEA技術,並於1974年訂定MIL-STD-1629 FMEA應用 程序。 1993年,美國汽車工業為連貫設計、 開發和製造的程 序,整合各汽車公司FMEA應用程序,三大汽車公司委 託ASQC整合SAE-J-1739(潛在失效模式與效應分析參 考手冊)。 我國在1970年左右引進,用於航空及汽車工業。
Cpk≧1.00 Cpk≧0.83
7 8
高:失效反覆發生
1/8~1/20 1/3~1/8
Cpk≧0.67 Cpk≧0.51
9 極高:失效幾乎無可 1/2~1/3
Cpk≧0.33
10 避免
1~1/2
Cpk<0.33
23
檢測度(D-Detect)
11/12/2019
等
級
設
計
製
程
1
幾乎肯定
設計控制時肯定檢測出失 現行控制方法能找出潛在
24
組成小組 蒐集資料
11/12/2019
定義流程
分析各工程功能
分析產品特性
分析失效模式
分析失效影響 故障嚴重度 S
分析失效原因 發生機率 P
現行管制方式 檢測難易度 D
計算風險率 (PRA)
決定高風險率項目 之改善措施
改善行動
修訂 FMEA 表
設計審查
流程設計
流程改善
檢驗程序
新FMEA实施的步骤

新FMEA实施的步骤引言随着产品质量管理的不断升级,FMEA(Failure Mode and Effects Analysis)作为一种有效的质量工具被广泛应用。
新FMEA实施的步骤是指在引入FMEA工具时的流程和方法。
本文将介绍新FMEA实施的步骤,帮助质量管理团队正确、高效地应用FMEA工具。
步骤一:确定FMEA实施的目标FMEA工具的应用可以有多个目标,如减少产品故障率、提高产品质量、降低生产成本等。
在实施FMEA前,需要明确具体的目标,以便确定方法和衡量标准。
•确定目标的过程应尽可能详细和具体;•目标可以通过质量管理团队的讨论和决策来确定。
步骤二:选择FMEA团队成员FMEA是一个协作的过程,需要各部门和岗位的人员共同参与。
选择FMEA团队成员时,需考虑以下几点:•各部门的专业知识和经验;•各岗位的解决问题和分析能力;•团队成员之间的合作和沟通能力。
步骤三:收集产品信息在实施FMEA之前,需要收集与产品相关的各类信息:•产品设计图纸、技术规范等;•已知的故障历史数据和客户反馈信息;•各部门或供应商提供的相关信息。
步骤四:建立FMEA团队会议FMEA团队会议是团队成员进行交流和讨论的场所,可以根据团队的实际情况安排会议的频率和时长。
FMEA团队会议主要包括以下内容:1.产品功能分解:–将产品功能分解为各个子功能;–分别讨论各个子功能的故障模式和影响。
2.故障模式与影响分析:–根据产品功能分解的结果,列出各个子功能的故障模式;–分析故障模式对产品造成的影响,并评定其严重程度。
3.探讨潜在的故障原因:–根据故障模式和影响,探讨可能导致故障的潜在原因;–针对每个潜在原因,分析其产生的机会和可能性。
4.制定纠正措施和预防措施:–针对每个潜在原因,制定纠正措施和预防措施;–确定责任人和实施时间。
5.评估控制措施的有效性:–对已实施的控制措施进行评估,以确定其有效性;–如需要,进行调整和改进。
步骤五:编写FMEA报告FMEA报告是对实施过程和结果的总结和记录,也是后续改进和追踪的依据。
fema的流程

FEMA的流程故障模式与影响分析(Failure Modes and Effects Analysis,简称FMEA)是一种预防性的质量管理工具,它通过对产品设计或流程控制过程中可能发生的故障模式进行预测、评估和优先排序,从而在产品发布或过程实施之前采取预防措施,以减少或消除潜在的故障及其影响。
FMEA广泛应用于汽车、航空航天、电子、医疗等领域。
本文将详细解析FMEA的流程,并探讨其在实际应用中的重要性。
一、FMEA的预备阶段在进行FMEA之前,需要做一些准备工作,包括组建FMEA团队、确定分析范围、收集相关信息等。
1. 组建FMEA团队:FMEA团队应由多学科背景的人员组成,包括设计工程师、制造工程师、质量工程师、可靠性工程师等。
团队成员应具备丰富的经验和专业知识,以便能够全面、准确地识别和分析潜在的故障模式。
2. 确定分析范围:明确FMEA分析的对象是产品设计还是过程控制,以及分析的具体范围。
这有助于团队成员集中注意力,针对关键部分进行深入分析。
3. 收集相关信息:收集与产品设计或过程控制相关的所有信息,包括设计图纸、技术规范、历史数据、相似产品的FMEA报告等。
这些信息将为后续的故障模式识别和分析提供有力支持。
二、FMEA的实施阶段FMEA的实施阶段包括故障模式识别、故障影响分析、严重度评估、发生度评估、检测度评估以及风险优先数(RPN)计算等步骤。
1. 故障模式识别:通过对产品设计或过程控制的深入分析,识别出所有可能的故障模式。
故障模式是指产品或过程中可能导致功能失效或性能降低的潜在问题。
2. 故障影响分析:针对每个故障模式,分析其可能对产品或过程造成的影响。
这些影响可能包括功能失效、性能降低、安全性问题、客户满意度下降等。
3. 严重度评估:根据故障影响的大小和严重程度,对每个故障模式进行严重度评估。
严重度评估通常采用1-10的评分制,其中1表示影响最小,10表示影响最大。
4. 发生度评估:根据故障模式发生的可能性进行评估。
FMEA详细解说与导入步骤培训(ppt 63页)63页PPT

谢谢!
21、要知道对好事的称颂过于夸大,也会招来人们的反感轻蔑和嫉妒。——培根 22、业精于勤,荒于嬉;行成于思,毁于随。——韩愈
23、一切节省,归根到底都归结为时间的节省。——马克思 24、意志命运往往背道而驰,决心到最后会全部推倒。——莎士比亚
就越令人高兴 。野心 是使人 勤奋的 原因, 节制使 人枯萎 。 12、不问收获,只问耕耘。如同种树 ,先有 根茎, 再有枝 叶,尔 后花实 ,好好 劳动, 不要想 太多, 那样只 会使人 胆孝懒 惰,因 为不实 践,甚 至不接 触社会 ,难道 你是野 人。(名 言网) 13、不怕,不悔(虽然只有四个字,但 常看常 新。 14、我在心里默默地为每一个人祝福 。我爱 自己, 我用清 洁与节 制来珍 惜我的 身体, 我用智 慧和知 识充实 我的头 脑。 15、这世上的一切都借希望而完成。 农夫不 会播下 一粒玉 米,如 果他不 曾希望 它长成 种籽; 单身汉 不会娶 妻,如 果他不 曾希望 有小孩 ;商人 或手艺 人不会 工作, 如果他 不曾希 望因此 而有收 益。-- 马钉路 德。
FMEA基础知识-FMEA的实施方法、步骤和程序
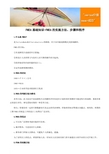
FMEA基础知识-FMEA的实施方法、步骤和程序1.什么是FMEA?是FailureMode&EffectsAnalysis的略称,在日本叫做故障模式及影响解析。
FMEA的目标:①在故障发生前做好纠正措施;②将设计人员的努力与技术人员可靠的操作结合起来;③把经验活用在新机能的设计上;④定性故障预测的模仿。
2.FMEA的历史1950→グラマン公司1960→NASA1970→日本科学技术联盟在日发表3.FMEA的考虑方法与特长思考方法:此方法法不是故障发生后的解析评价而是在计划阶段时预测有可能会发生的故障,系统有重点的进行评价,事先采取对策的一种思考方法。
特长:即便没有一定的可靠数据也可从过去的代表事例,经验者的知识等找出问题点。
相同的,所谓的工程FMEA在制造工序的设计上也得以广泛应用。
4.FMEA的优点a.可以从广泛围来考虑对象的可信度。
b.顺序简单,引进没有什么困难。
c.靠各部门经验人员推动,可避免个人的偏见,遗漏。
为了活用以上的优点,希望经验人员,有知识人员及相关部门的专家能以小组作业的方式开展工作。
5.FEMA的实施方法FMEA可找出设计上的隐藏故障,考察故障对系统的影响并作出定性的评价,以求得系统可靠性的问题点及必要的对策。
开展时,希望由设计、可靠性制造、品质保证、服务等经验丰富的人员以GP的形式进行解析,其理由是高精度的FMEA可以无偏见广泛地收集到以往欠缺点,故障处理等方面的信息。
6FMEA的种类和使用7.工程FMEA的目的工程FMEA的目的有以下两点:(1)改善不良率高的工序(2)改善工序设计中的弱点确立新机种增设新生产线时,事先模仿预测发生的不良并作好纠正措施。
8.工程FMEA的解析步骤9.工程FMEA开始前的应做事项(1)情报的收集→可靠的数据、投诉情况、经验、其他。
(2)对象的构成图。
10工程FMEA的实施程序1)制定确认加工工序合格与否的标准2)决定各工序的机能分析级别3)作成加工程序的组合图4)列举在每个加工工序中的不良类型5)整理不良类型,选定一种作为研究讨论的对象6)将所推测到的造成不良的各种原因列举出来7)将不良类型按等级分类8)研究讨论是否要进行设备的改善或工序的变更(1)加工程序的确认参考作业标准书作业指导书构成图,确认加工工序的流程,明确各工序的基准,规格。
FMEA工作步骤及主要内容
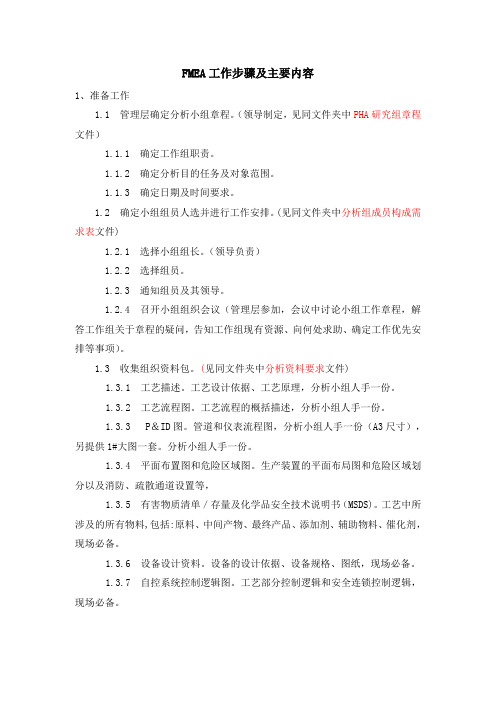
FMEA工作步骤及主要内容1、准备工作1.1 管理层确定分析小组章程。
(领导制定,见同文件夹中PHA研究组章程文件)1.1.1 确定工作组职责。
1.1.2 确定分析目的任务及对象范围。
1.1.3 确定日期及时间要求。
1.2 确定小组组员人选并进行工作安排。
(见同文件夹中分析组成员构成需求表文件)1.2.1 选择小组组长。
(领导负责)1.2.2 选择组员。
1.2.3 通知组员及其领导。
1.2.4 召开小组组织会议(管理层参加,会议中讨论小组工作章程,解答工作组关于章程的疑问,告知工作组现有资源、向何处求助、确定工作优先安排等事项)。
1.3 收集组织资料包。
(见同文件夹中分析资料要求文件)1.3.1 工艺描述。
工艺设计依据、工艺原理,分析小组人手一份。
1.3.2 工艺流程图。
工艺流程的概括描述,分析小组人手一份。
1.3.3 P&ID图。
管道和仪表流程图,分析小组人手一份(A3尺寸),另提供1#大图一套。
分析小组人手一份。
1.3.4 平面布置图和危险区域图。
生产装置的平面布局图和危险区域划分以及消防、疏散通道设置等,1.3.5 有害物质清单/存量及化学品安全技术说明书(MSDS)。
工艺中所涉及的所有物料,包括:原料、中间产物、最终产品、添加剂、辅助物料、催化剂,现场必备。
1.3.6 设备设计资料。
设备的设计依据、设备规格、图纸,现场必备。
1.3.7 自控系统控制逻辑图。
工艺部分控制逻辑和安全连锁控制逻辑,现场必备。
1.3.8 操作规程包括工艺卡片。
操作规程、应急预案、工艺卡片、设备修保规程,现场必备。
1.3.9 技术改造资料。
改造清单、改造原因、改造结果等,现场必备。
1.3.10 以往事故和危害事件分析报告。
事故原因、后果及整改措施,尽可能提供分析小组。
1.3.11 压力释放阀等安全装置的计算书和相关文件。
尽可能提供分析小组。
1.3.12 以往的PHA报告及类似分析文件。
尽可能提供分析小组。
1.3.13 设备设施检维修规程。
FMEA培训教程

FMEA培训教程引言:故障模式与影响分析(FlureModeandEffectsAnalysis,简称FMEA)是一种系统化的方法,用于识别产品或流程中的潜在故障模式,评估其对系统性能的影响,以及制定相应的改进措施。
本教程旨在为读者提供FMEA的基本概念、方法和应用技巧,帮助读者掌握FMEA的实施步骤和要点,以提高产品或流程的质量和可靠性。
一、FMEA的基本概念:1.1故障模式(FlureMode):故障模式是指产品或流程在特定条件下未能满足预定功能或性能要求的状态。
故障模式是FMEA分析的核心,通过对故障模式的识别和分析,可以揭示产品或流程的潜在问题和风险。
1.2影响分析(EffectsAnalysis):影响分析是指评估故障模式对产品或流程性能的影响程度。
通过影响分析,可以确定故障模式的重要性和优先级,为制定改进措施提供依据。
1.3FMEA的层次结构:FMEA通常分为三个层次:系统层次、子系统层次和组件层次。
每个层次都可以进行FMEA分析,以识别和评估潜在的故障模式及其影响。
二、FMEA的实施步骤:2.1组建FMEA团队:FMEA团队应由跨职能的人员组成,包括产品设计、工艺、质量控制、可靠性工程等相关领域的专家。
团队的成员应具备相关的知识和经验,能够全面地分析产品或流程。
2.2收集资料:收集与产品或流程相关的资料,包括设计图纸、工艺文件、质量控制计划等。
这些资料将有助于团队更好地了解产品或流程的特性和要求。
2.3识别故障模式:通过分析资料和与团队成员的讨论,识别产品或流程中潜在的故障模式。
可以使用头脑风暴、故障树分析等方法辅助识别故障模式。
2.4评估故障模式的影响:对识别出的故障模式进行影响评估,确定其对产品或流程性能的影响程度。
可以使用定性或定量的方法进行评估,如故障模式严重度(Severity)、发生度(Occurrence)和检测度(Detection)等指标。
2.5制定改进措施:根据故障模式的影响评估结果,制定相应的改进措施。
- 1、下载文档前请自行甄别文档内容的完整性,平台不提供额外的编辑、内容补充、找答案等附加服务。
- 2、"仅部分预览"的文档,不可在线预览部分如存在完整性等问题,可反馈申请退款(可完整预览的文档不适用该条件!)。
- 3、如文档侵犯您的权益,请联系客服反馈,我们会尽快为您处理(人工客服工作时间:9:00-18:30)。
如何進行FMEA? -PFMEA
蒐集資料
定義流程
分析各工程功能
分析產品特性
分析失效模式
分析失效影響
分析失效原因
現行管制方式
故障嚴重度 S
發生機率 P
檢測難易度 D
計算風險率 (PRA)
2017/1/31
失效模式與效應分析(FMEA)
1
2017/1/31
我們將學到
1. 如何創建FMEA及相關行動計畫 2. FMEA流程如何與流程圖相連接
3. 失效模式,起因和後果之間的關係
4. 不同類型FMEA
2
2017/1/31
課程大綱
1. 發展沿革 2. 概述
3. FMEA 應用
4. FMEA 準備階段
工厂端Focus 在PFMEA和部分產品的DFMEA
10
2017/1/31
製程的FMEA(PFMEA)
確認製造和裝配的失效原因與製程變異,找出 管制及改善方法。 確認製程潛在的失效模式及影響。 改善順序的依據。 包含:設備 / 機器、工具、工作站、生產線、 製程、治具。
11
2017/1/31
3
較多,較高
設計控制時較高機會檢測 現 行 控 制 方 法 有 可 能 找 出 出 失 效 原 因 或 潛 在 失 效 模 潛在失效模式 式
4
中上
設計控制時中上機會檢測 現 行 控 制 方 法 可 能 找 出 潛 出 失 效 原 因 或 潛 在 失 效 模 在失效模式 式
5
中等
設計控制時中等機會檢測 現 行 控 制 方 法 找 出 潛 在 失 出 失 效 原 因 或 潛 在 失 效 模 效模式可能性中等 式
失效發生率(P-Probability):
指失效模式發生的原因造成失效發生的機率。發生率的判定著重於經驗 及歷史數據發生的程度,不在於精確的數值。一般而言,DFMEA小組要 降低失效發生率常利用設計修改(eg.材料、零組件),來排除失效的 原因;PFMEA小組應針對影響失效控制參數進行改善。
檢測度(D-Detect):
6
2017/1/31
根據美國汽車工業小組的調查報告 -『客戶滿 品質預防-客戶滿意 意的品質槓桿研究』指出,在產品推出到市場 的過程中,愈早投入品質預防的努力,愈能令 客戶滿意,品質回收的利益亦愈大。
產 品 設 計 開 發 階 段 製 程 開 發 階 段 生 產 組 裝 階 段 銷 售 階 段 售 後 服 務 階 段 客 訴 處 理 階 段
產品設計及製程規劃
量產及客戶端
提前發現潛在性問題
事前改善措施
事後發生信賴性問題
事後矯正行動
FMEA
8D
9
2017/1/31
FMEA的類別
Types of FMEA
系統 (System)
-SFMEA
設計(Design) -DFMEA 製程(Process) -PFMEA
機器 (Machine) -MFMEA 設備 (Equipment) -EFMEA 維護 (Service) -SEFMEA
20
2017ESS):
指失效模式發生時引發其對零件本身或對其他零件、次系統、主系統的 特性、功能、可靠度的影響程度,乃至對顧客(內外部)安全性、經濟 性及環境的衝擊程度。一般而言,DFMEA小組要降低失效嚴重度只能藉助 系統重新設計來改善。PFMEA小組要降低失效嚴重度仍應與DFMEA小組協 助改善。
6
少,小
設計控制時較少機會檢測 現 行 控 制 方 法 找 出 潛 在 失 出 失 效 原 因 或 潛 在 失 效 模 效模式可能性小 式
7
很少,很小
設計控制時很少機會檢測 現 行 控 制 方 法 找 出 潛 在 失 出 失 效 原 因 或 潛 在 失 效 模 效模式可能性很小 式
8
極少,微小
設計控制時極少機會檢測 現 行 控 制 方 法 找 出 潛 在 失 出 失 效 原 因 或 潛 在 失 效 模 效模式可能性微小 式
Remark: 時間計劃的整合-絕大部份進行此類分析的人員, 都有原本的任務,一方面要能進行日常工作,另一 方面要能完成分析工作,因此時間的妥善安排是非 常重要的
15
2017/1/31
失效風險分析
以數據評估失效模式風險-風險關鍵指數 (RPN:Risk Priority Number) 風險關鍵指數由下列組成 S = 嚴重度 P = 發生率 D =偵測度
16
2017/1/31
RPN風險率的構成
效應(影響) 嚴重度S
失效模式(現象)
原因
發生率P
控制
偵測度D
17
2017/1/31
PFMEA風險的評估與改善評估
制程 管制 難易 度
管制 方式
D
改變製程管制方式
失 效 模 式
原 因 分 析
×
製程 條件
P
發生 機率
改變製程條件
影 響 分 析
×
S
失效 嚴重 度
新設計或工程更改 新製程或製程變更或製程轉移 新方法導入 新設備導入 應用及生產環境變動 材料更改
14
2017/1/31
準備階段
1. 確認產品的可靠度要求及目標。 2.掌握系統、次系統的構造(列出產品所有的機 構組件零件、製程、事務流程所有的步驟) 3.決定失效風險分析(RPN)水準。 4.準備失效模式分析表。
等 級 極低 低 中 高 極高 P 沒 有 非常低 輕 微 低 重要的 中 高 高 嚴重/致命 非常高 S D 易/早發現 低 中 高 難/晚發現
1.對SPD每一個項目必頇先定義出自己的等級 2.SPD的尺度可以不同 3.SPD的分級比率應用必頇持續、一致 4.SPD的分級必頇在構成要素展開之前被界定清楚 5.SPD的分級必頇隨著 FMEA 的結果一起發表
指零件、組件、機構裝置或系統投產前現行控制方法偵測發生失效 的原因或失效模式的評價指標。DFMEA小組要降低檢測度,常改變設 計測詴方式、驗證方式、實驗計畫或強化設計審查;PFMEA小組要降 低檢測度,改善檢驗對象、方式、方法與頻率。
21
2017/1/31
失效嚴重度(S-Seriousness)
1 2 3 4 5 6 7 8 9 等 級 非常低或沒有 很輕微 輕微 很低 低 中等 高 很高 有危害 設 計 製 程 沒有衝擊 沒有衝擊 缺 陷 輕 微 , 極 少 部 分 重 生產線有輕微缺陷,極少 工,很少顧客發現 部分重工,很少顧客發現 缺陷輕微,少部分重工, 生產線輕微缺陷,少部分 一半顧客發現 重工,一半顧客發現 缺陷不嚴重,部分重工, 生產線不嚴重缺陷,部分 多數顧客發現 重工,多數顧客發現 缺 陷 不 嚴 重 , 100 ﹪ 重 生產線不嚴重缺陷, 100 工,顧客有些不滿意 ﹪重工,顧客有些不滿意 缺陷不嚴重,部分報廢, 生產線不嚴重缺陷,部分 顧客感覺不好 報廢,顧客感覺不好 缺陷不嚴重,部分報廢, 生產線不嚴重缺陷,部分 顧客不滿意 報廢,顧客不滿意 缺陷嚴重, 100 ﹪報廢, 生產線嚴重缺陷, 100 ﹪ 顧客非常不滿意 報廢,顧客非常不滿意 危害作業者及使用者安 危害作業者及使用者安 全,不符法規,有發生警 全,不符法規,有發生警 告 告 嚴重危害作業者及使用 嚴重危害作業者及使用 者安全,不符法規,無發 者安全,不符法規,無發 生警告 生警告
12
2017/1/31
誰來作FMEA?(如何組小組)
為防止分析時的偏差 ,各個層面的代表 ,每個 功能單位要有 , 專業技術和管理人員都應 有,集思廣益. DFMEA:R&D,TE,QE,ME(材料工程師),QA,PE PFMEA:PE,ME,TE,QA,IE…
13
2017/1/31
應用FMEA的時機?
5. 失效風險分析
6. RPN 的分級 7. PFMEA 實施步驟 8. FMEA 報告標準格式 9. 常見製程失效原因
祝各位同仁今天”旅途”愉快!!!
3
2017/1/31
FMEA的發展沿革
FMEA是評估設計可靠度之一種方法。 在1950年由美國之GRUMMAN公司針對新型噴射戰 鬥機時,為了評估飛機操作系統某一元件之失效分析 所採用之解析方法。 1957年Boeing飛機公司與Martin公司正式將FMEA列入 工程指導手冊。在同時期,美國NASA與軍方也開始應 用FMEA技術,並於1974年訂定MIL-STD-1629 FMEA應用 程序。 1993年,美國汽車工業為連貫設計、 開發和製造的程 序,整合各汽車公司FMEA應用程序,三大汽車公司委 託ASQC整合SAE-J-1739(潛在失效模式與效應分析參 考手冊)。 我國在1970年左右引進,用於航空及汽車工業。
9
非 常 少 , 很 設計控制時非常少機會檢 現 行 控 制 方 法 找 出 潛 在 失 微小 測 出 失 效 原 因 或 潛 在 失 效 效模式可能性很微小 模式 設計控制時不可能檢測出 沒 有 已 知 的 控 制 方 法 能 找 失效原因或潛在失效模式 出失效模式
10
幾乎不可能
24
組成小組
2017/1/31
22
10
嚴重危害
2017/1/31
失效發生率(P-Probability)
等 級 設 計 極低:失效非常不可 0,1/150,000~1/1,500,000 能發生 1/15,000~1/150,000 低:失效相對很少發 1/2,000~1/15,000 生 1/400~1/2,000 1/80~1/400 中:失效偶爾發生 1/20~1/80 1/8~1/20 高:失效反覆發生 1/3~1/8 極高:失效幾乎無可 1/2~1/3 避免 1~1/2 製 Cpk≧1.67 Cpk≧1.50 Cpk≧1.33 Cpk≧1.17 Cpk≧1.00 Cpk≧0.83 Cpk≧0.67 Cpk≧0.51 Cpk≧0.33 Cpk<0.33 程