PLC在远程阀门监控中的运用
基于PLC的电力系统远程监控与控制
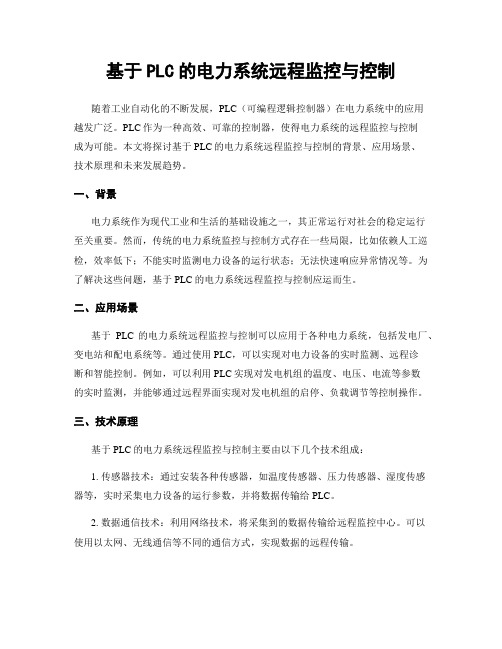
基于PLC的电力系统远程监控与控制随着工业自动化的不断发展,PLC(可编程逻辑控制器)在电力系统中的应用越发广泛。
PLC作为一种高效、可靠的控制器,使得电力系统的远程监控与控制成为可能。
本文将探讨基于PLC的电力系统远程监控与控制的背景、应用场景、技术原理和未来发展趋势。
一、背景电力系统作为现代工业和生活的基础设施之一,其正常运行对社会的稳定运行至关重要。
然而,传统的电力系统监控与控制方式存在一些局限,比如依赖人工巡检,效率低下;不能实时监测电力设备的运行状态;无法快速响应异常情况等。
为了解决这些问题,基于PLC的电力系统远程监控与控制应运而生。
二、应用场景基于PLC的电力系统远程监控与控制可以应用于各种电力系统,包括发电厂、变电站和配电系统等。
通过使用PLC,可以实现对电力设备的实时监测、远程诊断和智能控制。
例如,可以利用PLC实现对发电机组的温度、电压、电流等参数的实时监测,并能够通过远程界面实现对发电机组的启停、负载调节等控制操作。
三、技术原理基于PLC的电力系统远程监控与控制主要由以下几个技术组成:1. 传感器技术:通过安装各种传感器,如温度传感器、压力传感器、湿度传感器等,实时采集电力设备的运行参数,并将数据传输给PLC。
2. 数据通信技术:利用网络技术,将采集到的数据传输给远程监控中心。
可以使用以太网、无线通信等不同的通信方式,实现数据的远程传输。
3. 数据处理技术:远程监控中心接收到传感器采集的数据后,需要经过数据处理和分析,可以利用数据挖掘、机器学习等技术,实现对电力设备的状态监测和故障诊断。
4. 远程控制技术:远程监控中心可以通过与PLC连接实现对电力设备的远程控制。
通过编写控制程序,可以实现对电力设备的启停、负载调节、故障排除等操作。
四、未来发展趋势基于PLC的电力系统远程监控与控制在未来将会有更广阔的应用前景。
1. 智能化发展:随着人工智能技术的不断进步,基于PLC的电力系统远程监控与控制将会更加智能化。
PLC技术在电气工程及其自动化控制中的应用

PLC技术在电气工程及其自动化控制中的应用随着科技的不断发展,PLC(可编程逻辑控制器)技术在电气工程及其自动化控制领域中的应用越来越广泛。
PLC技术的引入使得传统的电气控制系统得以升级,使得生产过程更加高效、可靠。
本文将就PLC技术在电气工程及其自动化控制中的应用进行详细介绍。
一、PLC技术概述PLC是一种专门用于工业自动化领域的控制器,它可以根据预设的逻辑程序对各种工业生产过程进行自动控制。
其优点在于可编程、灵活性强、易于维护、抗干扰能力强等特点。
PLC主要由CPU、输入/输出模块、通信模块和电源模块等组成,通过这些组件实现对机器设备的监控和控制。
PLC技术广泛应用于电力系统、冶金自动化控制、化工生产过程控制、包装机械控制、制造业自动化生产线控制等领域。
二、PLC技术在电气工程中的应用1.电力系统控制在电力系统中,PLC技术可以被用于对电力生产、输配电及用电进行监控和控制。
通过PLC控制器可以实现对发电机、变电站设备、配电设备等的自动化控制,提高了电力系统的可靠性和安全性。
2.电机控制3.照明控制PLC技术也可以被应用于照明系统的控制,通过对照明设备的控制来实现能耗的节约和照明效果的优化。
PLC控制器可以根据光线强度、环境温度等参数自动调节照明设备,提高了能源利用效率。
4.管道控制在电气工程中的管道控制方面,PLC技术可以被用于对管道的流量控制、阀门控制、故障诊断等方面。
通过PLC控制器可以实现对管道控制的智能化管理,提高了管道系统的稳定性和安全性。
1.自动化生产线在制造业中,PLC技术被广泛应用于自动化生产线控制。
通过PLC控制器可以实现对生产线的自动监控和自动控制,包括物料输送、工艺流程控制、设备协调等方面。
这大大提高了生产线的生产效率和产品质量。
2.智能仓储系统3.机器人系统在工业机器人控制方面,PLC技术也发挥着重要作用。
通过PLC控制器可以实现对机器人的轨迹规划、动作控制、传感器反馈等方面的控制,实现了工业机器人的自动化操作。
PLC在流量控制系统中的应用案例

PLC在流量控制系统中的应用案例流量控制系统是自动化控制中的一个重要应用领域,可以应用于水处理、工业生产、环保等诸多领域。
PLC(可编程逻辑控制器)因其在工业自动化中的功能,特别是对数字和模拟输入/输出操作的能力,成为了流量控制系统中最重要的控制器之一。
本文将探讨PLC在流量控制系统中的应用案例。
一、PLC控制阀门的开闭PLC通过控制流量阀门的开闭,实现流量控制系统中流量的准确控制。
PLC控制阀门的开闭,需要对阀门位置进行反馈控制,即需要在PLC中安装反馈传感器,以检测阀门的位置。
在阀门的开关过程中,PLC可以根据预先设定的开启/关闭时间、阀门的旋转角度等参数实现对阀门的准确控制,从而实现流量控制。
二、PLC实现PID控制PID控制是一种用于工业自动控制中的一种自适应控制方法,其基本原理是按比例调节、积分时间和微调时间来调节控制器的输出,实现对被控制物(例如流量阀门或流量传感器)的精确控制。
传统的PID控制需要使用独立的PID控制器,为了实现在线程序修改,需要对现场的设备进行频繁的调整。
而PLC可以集成PID算法并在线实时调整参数,使控制系统更加智能化,大大简化了控制系统的维护。
三、PLC控制流量传感器流量传感器是流量控制系统中最重要的感应装置之一,可以实现对流量的实时监测。
PLC可以通过传感器检测实时流量信号并将其反馈给PLC,PLC再根据预设的控制程序进行反馈,从而实现精确控制。
同时,PLC还可以使用数据采集卡将流量传感器的信号转换为数字信号,以便于对数据进行存储、处理和分析。
四、PLC实现流量的计算PLC可以通过编写测量算法,将传感器的数字信号转换为流量值,并将其储存在控制器内存中。
此外,PLC还可以将流量数据转输到上位机等设备中,以便于进行数据存储、处理和报告分析。
PLC在流量控制系统中的应用模式基本类似,但实际应用却因环境和行业不同,而存在着各自的应用要求。
在任何情况下,PLC的优势在于其灵活可塑性,可根据不同环境的要求进行定制。
掌握PLC的远程监控和远程控制功能

PLC可以与家庭安防系统相连,实现 对门窗、烟雾报警器、摄像头等设备 的远程监控和控制,确保家庭安全。
能源管理系统案例
能源数据采集
通过PLC的远程监控功能,能源管理系统可以实时采集各 种能源设备(如电表、水表、燃气表等)的数据,为能源 分析和优化提供支持。
能源设备控制
通过PLC的远程控制功能,能源管理系统可以对能源设备 进行远程操控,实现能源设备的自动化和智能化管理,提 高能源利用效率。
数据加密
对传输的数据进行加密处理,防止数 据在传输过程中被窃取或篡改。
防火墙保护
在远程监控和控制系统中设置防火墙 ,防止未经授权的访问和攻击。
日志记录
记录所有用户的操作日志,以便在出 现问题时进行追溯和排查。
04
CATALOGUE
实际应用案例分析
工业自动化生产线案例
01
远程监控
通过PLC的远程监控功能,生产线管理人员可以实时查看生产设备的运
实时状态块,实时监 测现场设备的运行状态,如电机启停 、阀门开度等。
参数实时监测
实时监测PLC内部的各种参数,如 CPU负载率、内存占用率、网络通信 状态等,确保PLC稳定运行。
故障诊断与报警机制
故障诊断
通过PLC的故障诊断功能,对现场设备出现的故障进行快速定位和诊断,提高 维修效率。
能源数据分析与优化
PLC采集的能源数据可以通过数据分析工具进行处理和分 析,帮助管理人员了解能源消耗情况,发现潜在的节能措 施和优化方案,降低企业运营成本。
05
CATALOGUE
挑战与解决方案
网络通信延迟问题
延迟原因
网络通信延迟主要由网络带宽限制、 数据传输量过大、网络拥堵等因素引 起。
PLC技术在机械电气控制装置中的应用
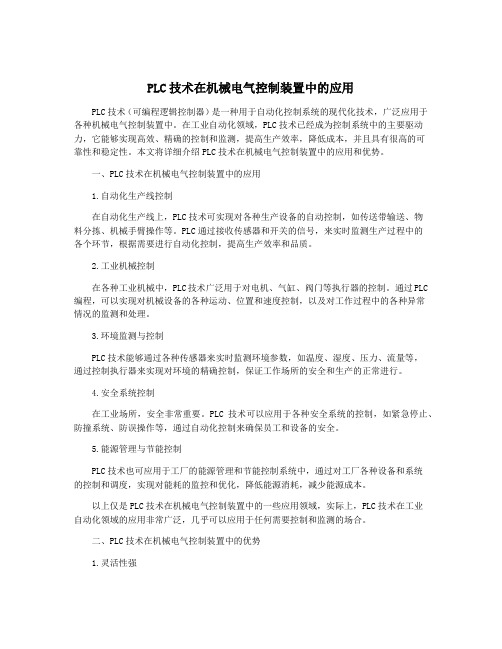
PLC技术在机械电气控制装置中的应用PLC技术(可编程逻辑控制器)是一种用于自动化控制系统的现代化技术,广泛应用于各种机械电气控制装置中。
在工业自动化领域,PLC技术已经成为控制系统中的主要驱动力,它能够实现高效、精确的控制和监测,提高生产效率,降低成本,并且具有很高的可靠性和稳定性。
本文将详细介绍PLC技术在机械电气控制装置中的应用和优势。
一、PLC技术在机械电气控制装置中的应用1.自动化生产线控制在自动化生产线上,PLC技术可实现对各种生产设备的自动控制,如传送带输送、物料分拣、机械手臂操作等。
PLC通过接收传感器和开关的信号,来实时监测生产过程中的各个环节,根据需要进行自动化控制,提高生产效率和品质。
2.工业机械控制在各种工业机械中,PLC技术广泛用于对电机、气缸、阀门等执行器的控制。
通过PLC 编程,可以实现对机械设备的各种运动、位置和速度控制,以及对工作过程中的各种异常情况的监测和处理。
3.环境监测与控制PLC技术能够通过各种传感器来实时监测环境参数,如温度、湿度、压力、流量等,通过控制执行器来实现对环境的精确控制,保证工作场所的安全和生产的正常进行。
4.安全系统控制在工业场所,安全非常重要。
PLC技术可以应用于各种安全系统的控制,如紧急停止、防撞系统、防误操作等,通过自动化控制来确保员工和设备的安全。
5.能源管理与节能控制PLC技术也可应用于工厂的能源管理和节能控制系统中,通过对工厂各种设备和系统的控制和调度,实现对能耗的监控和优化,降低能源消耗,减少能源成本。
以上仅是PLC技术在机械电气控制装置中的一些应用领域,实际上,PLC技术在工业自动化领域的应用非常广泛,几乎可以应用于任何需要控制和监测的场合。
二、PLC技术在机械电气控制装置中的优势1.灵活性强PLC技术可根据不同的控制要求进行编程,因此具有很强的灵活性。
通过对PLC程序的修改,可以方便地实现控制逻辑的变更和新增功能的增加,提高了设备的适应性和可扩展性。
PLC与HMI及MA在阀门自动化生产线改造中的应用

4结束 语
在 本 系统 中, 需 要 在线 更 新 的量 为母 管压 力 或 频 率 的设 定值 , 采 用触摸 屏作 为人机 交 互工 具, 简
单直观,便于操作。
( 2)各 台供 浆泵 控 制画面 ; ( 3)压 力 、频率 曲线画面 ;
P LC作 为 中央处理 单元 , 它与 触摸屏 在锅 炉供 浆 系 统 中结合 使 用, 发 挥 了其 稳定 可靠 性 , 为锅炉
制工程 :
韦 燕 (9 4 ) 1 6 一 ,男, 教授 , 究方向为控 制理论与控制 工程 。 研
锅炉 供浆触摸 屏与 P LC控制 系统 中触摸 屏 画面
( 2)P LC与 触摸屏 之 间距离 不能过 大, 触摸屏
本 身 比较 贵 。
由支持软件 AD 3中文软件进行设计, 然后从 支持 工 P
M
行 程 检 测
压 力检测 加 = 故障 I = = 电机故障
中用行 程 开关检 测 加工过 程 中 工件 的位 置, 用接 近 传感 器检 测 机械 手 位 置 。
122软件设计 ..
图 1 自动方案 示意 图
应 用西 门子 S MATI T . I C S EP7 V53编程 软 件 , 用
机 全 自 动 控 制 层 面 、 下 位 机 操 作 、设 备 柜 手 动 操 作
层 面 3个 控 制 层 面
机 械手 的横 向运 动 由 富士 变频器 驱动 控 制, 纵 向升 降和抓 放 工件 由气动 装 置控 制 。每 台机 床 的加工 部
件 的 起 停 、 旋 转 , 由 各 机 床 电 机 分 别 控 制 。该 方 案
【】 9 , S,9 94 1
3注意 事 项
PLC在水泵控制系统中的应用
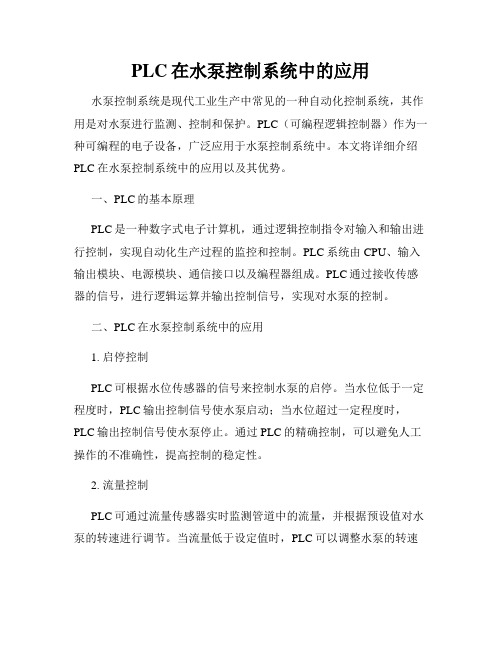
PLC在水泵控制系统中的应用水泵控制系统是现代工业生产中常见的一种自动化控制系统,其作用是对水泵进行监测、控制和保护。
PLC(可编程逻辑控制器)作为一种可编程的电子设备,广泛应用于水泵控制系统中。
本文将详细介绍PLC在水泵控制系统中的应用以及其优势。
一、PLC的基本原理PLC是一种数字式电子计算机,通过逻辑控制指令对输入和输出进行控制,实现自动化生产过程的监控和控制。
PLC系统由CPU、输入输出模块、电源模块、通信接口以及编程器组成。
PLC通过接收传感器的信号,进行逻辑运算并输出控制信号,实现对水泵的控制。
二、PLC在水泵控制系统中的应用1. 启停控制PLC可根据水位传感器的信号来控制水泵的启停。
当水位低于一定程度时,PLC输出控制信号使水泵启动;当水位超过一定程度时,PLC输出控制信号使水泵停止。
通过PLC的精确控制,可以避免人工操作的不准确性,提高控制的稳定性。
2. 流量控制PLC可通过流量传感器实时监测管道中的流量,并根据预设值对水泵的转速进行调节。
当流量低于设定值时,PLC可以调整水泵的转速提高流量;当流量超过设定值时,PLC可以减小水泵的转速以维持稳定流量。
PLC的精准控制使流量控制更加精确可靠。
3. 压力控制在一些需要稳定压力的场合,PLC可通过压力传感器实时监测管道中的压力,并通过控制阀门的开闭程度来调节水泵的流量。
当压力低于设定值时,PLC可以增大阀门的开启程度以提高流量;当压力超过设定值时,PLC可以减小阀门的开启程度以降低流量。
PLC的快速响应能力确保了系统的稳定性。
4. 防止故障PLC还可以通过监测水泵的温度、转速、电流等参数来判断水泵是否存在故障,并通过输出警报信号来提醒运维人员进行检修。
当发生过载、温度过高等情况时,PLC能够及时停止水泵以防止进一步的损坏。
PLC在故障诊断和保护方面的应用使水泵的安全运行得到了有效保障。
三、PLC在水泵控制系统中的优势1. 灵活可编程PLC具有良好的可编程性,可以根据实际需求灵活调整控制逻辑,并支持现场的实时调试和修改。
基于PLC的电动阀门智能控制装置的设计

电动 阀 门智能控 制装置 由远距 离传输模 块 、主控模 块和 H MI 模块组成 , 是一个闭环控制系统 。主控模块根据 远距 离传输模块传 送 的水位值和触摸屏模块 的设定值 比较来 控制步进 电机 的正反转 , 调节 电动 阀的开度 。主控模块选用 S i me n s C P U 2 2 6 ,采 用模 糊 P I D 算法来提高控制精度 和可靠性 ;采用触 摸屏 完成系统参数设置 、 状 图 1西门子 P L C与 电动 执 行 器 电 路 板端 子 接 线 图 态显示等功能 。采取软硬件抗干扰措施来 提高装置的抗干扰能力 , 保 证 系 统 的安 全 可 靠 。 节 约用水 , 提高农业灌溉水 资源的可持 续利用 。水位传感 器选用佛 本系统 以田间水位值为依据 ,对 电动阀门开合角度进行控制 , 山市顺 德 区宝智 电子科技有 限公 司的 B Z 0 5 0 1 电子式水位 开关 , 通 再 由水位 检测专用 芯片对检测 到的信 控制用水 水量 , 水位值通 过超声波液位传 感器获取 , 经过 处理传输 过 电子探头对水位进行检测 , 至智能控制系统。 然后 由其测算实际与预定 的数值差 , 判断决策 , 发 号进行处理 。当被测液体到达动作点时 , 芯片输 出高低 电平信 号或 出操 控电动调节阀的控制信号 , 驱 动电动执行机构来控制调节 阀的 继 电器 开关 信号 。B Z 0 5 0 1工作电压为 5 V, 判 断有水 时输出 5 V, 无 开度 。 P L C包括模拟量接 口设计 , 数字量接 口设计 , 以太 网模块接 口 水时 0 V, 适用温度范围为 一 2 0~ 6 0  ̄ C。 4 通 信 方 式 与 上 位 机 组 态 王 监控 系统 等。 作为主控模块 , 主要完成 系统模数信号 的通讯和处理 , 并运用模 糊P I D算法来调节 阀门的开度。 另外 , 还有故 障诊断功能 , 并通过触 上位机软件使用北 京亚 控公 司出品的组态 王 6 . 5 2 语 言设计 , 主 摸屏 完成操作 和显示 。本 文采用常用 的双输人单 输出模糊 控制器 要对采集数 据进 行保存并对各个参数进行实时监控 。 下位 机使用西 ( 二维模糊 控制器) , 模糊 控制是一种 以集合论 、 模糊数学 、 模糊 逻辑 门子的梯形 图进行编程 。上位工控机选用研华公 司生产 的计算机 , 推理为理论基础 , 应用单片机控制技术构成的闭环智能控制 。 为了能够使 现场工作人员更便 于操作 ,监控界面 主要有登 录界 面、 2 电 动 阀 电动 装 置 及 其 使 用 灌溉点设置 、 灌溉点状 态 、 灌溉 方式选择 、 灌溉记录 、 系统帮助 等界 阀门是控制 系统现场 的执行设 备 , 为了能够 实现远程控制和操 面组成 。利用 5 0 mW 微功率 工业用无线数传模块 S M5 1 实现数据的 作, 采用 电动阀门 , 即在普通 阀门的基础上安装 电动执行器。 上位机 无 线传输 , 该模块最大发射 功率 1 7 d b m ( 5 0 m W) ; 符合 I S M频段通 信 无需 申请频点 ; 多信道 、 半双工无线通信 , 实时收发通信 , 传输 不但可 以通过 P L C对阀门进行操作 , 对农 田的给水和排水进行 实时 标 准 , 控制 , 而且上位机 也可以通 过与 P L C的通信 , 对 现场 阀门的开 、 关状 距离远 , 可靠传输距离大于 1 2 0 0 m; 透明的数据传输 , 自动过滤掉空 态实 时监 控 。阀门执行器主要 由一 个单相交 流电机和 限位开关构 中产生 的噪音信号及 假数据 , 高抗干扰能力和低误 码率 ; 能够 同时 成 ,其功能是通过输入交流 2 2 0 V 的电压信号可实现对 阀门的开启 提供标 准 , I T L电平 U A R T接 口, 软件模拟 R S 2 3 2 , 模拟 R S 4 8 5三种 和关 闭 ,同时 能够输 出一对无 源信号作为到 达位置信号供 P L C使 接 口,支持休眠功能 ,休眠以后将 整个系统功耗 降到最 低 ; + 3 . 3 到 用。 本文电动阀选择近三十年仪表生产经验的天津贝尔 自动化仪表 + 5 . 5 V直 流工作 电压 , 接收 电流 < 4 0 m A, 发射 电流 < 1 0 0 m A, 休 眠工 技术 有限公司 D N 2 0 0的电动 阀, 配套其生产 的电动执 行器 。阀门 作 < 5 u A; 看 门狗实 时监控 。S M5 1 与单片机连接时使用 串口 T I 1 L 电 最 大输 出转矩 2 0 0 N m, 最 大输 出转 速 3 6 r / mi n , 最 大转 圈数 1 2 0圈。 平接 口。 阀门电动装置 主要 由步进 电机 、 减速 器 、 开度和行程机构 、 力矩控制 5 结论 和 电气部 分等组成 。电动装置 使用 前 , 必须对 行程 和开度分别进行 本装 置经过系统联调和现场 的实际运行 , 验证 了设计 的正确性 调整 。在调整前 , 必须检查 电机 的旋 向, 控制线路是否正确 , 以防止 和可靠性 , 达到 了预期 目标 , 具有一定的推广应用价值 。 不仅节约了 电机失控 。步进电机型号 1 1 0 B YG 3 5 0 C , 选择 MS a 一 3 H1 1 0 M型驱动 人力资源 , 而且阀门 自动操作 也使 得准确性 和连续性 比以往得到显 器, 细分数达 2 8种 , 最大细分步数 6 0 0 0 0 , 最 大有 效输 出电流 5 . 2 A, 著提高 , 生产效率得到大幅提 升。 供 电电压 2 2 0 V A C 。利用 L C D1 6 0 2 液 晶显示模 块显示开度值 , 它是 参考文献 1 】 江春 红 . 基于 P L C 的 液位 模 糊 控 制 系统 设 计 【 D ] . 舍肥 : 合 肥 工 业 丸 种工业字符 型液晶 , 能够同时显示 1 6x2即 3 2个字符 。西门子 [ P L C接线端 与电动执行器 内部 电路板接线端相互接线如 图 1 所示 。 学, 2 0 0 7 . 3 田间管道控 制系统与水位传感器 [ 2 ] 李爱传, 衣淑娟 , 石建飞, 王 熙. 基于 P L c的寒地水稻灌溉控制 系统 结合 田间地形 , 采用 口径为 D N 2 0 0的镀锌钢管 , 内壁厚为 6 mm 的研 究[ J 】 . 农业工程技 术, 2 0 1 6 , 3 6 ( 6 ) : 6 7 ~ 7 1 . 的管道送水 , 管道放在池埂上 或者 2条 池埂 中间 , 不影 响大小机 械 [ 3 】 江英. 带死 区的增量式 P I D控制在湿度控制 中的应 用[ J 】 . 长沙通。 丸 作业 的地 方。用 西门子 P L C根据采集 到的水位高度 、 渠道 流量等精 职业技术 学院 学报, 2 0 0 8 , 7 ( 2 ) : 5 7 — 5 8 . 确信号 , 并综合天气预报等信息进行判 断决 策 , 控制灌溉 电动 阀 , 按 需供水 。 同时为满足不同农 田灌溉需求 , 可选择多种运行模式 , 达到
基于PLC的船舶阀门遥控与液位遥测教学实训系统设计

船 海 工 程
S HI P& 0 CE AN E NGI NE ER I NG
Vo 1 . 4 3 No .1
F e b . 2 0 1 4
D O I : 1 0 . 3 9 6 3 / j . i s s n . 1 6 7 1 - 7 9 5 3 . 2 0 1 4 . 0 1 . 0 2 1
2 ) 系统 所 配 置 的舱 室 液 位 检 测 传 感 器 和 液
工 作原 理是 : 由安 装 在 相关 舱 室 内 的液 位传 感 器 检 测液 位 , 送 至 系统 中的数据 采集 与处 理单元 , 最
收 稿 日期 : 2 0 1 3—1 2— 0 2 修 回 日期 : 2 0 1 3—1 2—1 0
包 含最新 技 术 的实 船 系 统 的基 本 功 能 , 同时 也 要
船 舶 液位遥 测 系统 主要 用于监 测 船舶各 压 载
舱、 淡水 舱 液位 以及 船 舶 吃 水 状 态 。系 统 的 主 要
兼 顾进行 系 统教 学 , 为学员 进行 系统 调试 、 参数 观 察、 故 障分析 与排 除 等操作 创造 条件 。
位控 制 阀 门的类 型 要 具 有典 型性 和 代 表 性 , 数 量
以满足实训要求 、 节约成本为准 , 区别于实船。
3 ) 液位 检测 、 阀 门 状 态 检 测 由传 感 器 送 入
作者简介 : 孙艳秋 ( 1 9 7 0一) , 女, 硕士, 副教授
研究方 向 : 船 舶 电气
般 由液位传感器 、 信号处理单元 、 显示单元和操
阀 门遥 控 系统 主要 用 于 船舶 压 载水 系统 、 舱
PLC在压力监测系统中的应用案例

PLC在压力监测系统中的应用案例压力监测是许多工业应用中的重要环节,它能够确保设备的安全运行和生产过程的稳定性。
而在压力监测系统中,PLC(可编程逻辑控制器)的应用发挥着关键作用。
本文将以一个实际的案例来介绍PLC在压力监测系统中的应用。
案例背景某化工公司生产过程中有一个压力监测系统,用于监测管道中的液体压力。
这个系统需要实时监测压力,并根据设定的阈值进行报警和控制处理。
在过去,这个压力监测系统使用传统的电子设备和开关来实现,但存在响应速度慢、精度不高等问题。
为了提高系统的性能和可靠性,该公司决定将PLC引入压力监测系统。
PLC优势PLC作为一种通用的工控设备,具有以下优势:1. 稳定可靠:PLC具有强大的抗干扰能力和高可靠性,能够在恶劣的工作环境中长时间稳定运行。
2. 可编程性:PLC可以根据需要进行编程,实现各种复杂的逻辑控制功能,能够满足不同应用场景的需求。
3. 高效灵活:PLC的处理速度快,能够实现实时监控和控制,同时具备较强的扩展性,能够适应各种变化的工艺要求。
PLC在压力监测系统中的应用经过深入研究和方案设计,该化工公司决定使用PLC来改造压力监测系统。
下面将介绍PLC在该系统中的主要应用方式:1. 压力传感器接口首先,需要将压力传感器接口与PLC连接,通过模拟信号输入模块将压力传感器的输出信号转换为数字信号。
PLC通过读取这个数字信号,可以获得实时的压力数值。
2. 设定阈值PLC可以通过编程,在设定的阈值范围内对压力数值进行监测。
当压力超出设定的上下限时,PLC将触发报警信号,并采取相应的措施,如断开电源、停止生产等。
3. 数据处理与存储PLC可以对获得的压力数据进行处理和分析,并将相关数据存储在其内部存储器中。
这些数据可以用于后续的运行日志记录和故障排除。
4. 远程监控PLC还可以通过网络通信模块与上位机或监控中心进行通信,实现远程监控和控制。
运维人员可以通过上位机实时查看压力数据,进行参数调整和设备监控,从而提高生产的效率和安全性。
PLC在生产过程控制中的应用案例

PLC在生产过程控制中的应用案例PLC(可编程逻辑控制器)是一种专门用于自动化控制系统的计算机控制器。
它被广泛应用于各个行业的生产过程控制中,以提高效率、降低成本和保证产品质量。
本文将介绍几个PLC在生产过程控制中的应用案例,展示其在实际工程中的作用和效果。
案例一:汽车生产线的自动化控制在汽车制造过程中,PLC被用于控制整个生产线的运行。
它可以自动化地控制装配线上的各个工位,确保每个步骤的准确执行。
例如,在车身涂装环节,PLC可以精确控制涂装机械臂的移动速度和位置,确保车身被均匀涂装。
同时,PLC还可以实时监测设备状态和效率,减少生产线停机时间和故障率,提高生产效率和产品质量。
案例二:食品加工工厂中的温度控制在食品加工工厂中,温度是一个非常重要的参数。
PLC可以用于精确控制加工设备的温度,确保食品在适宜的温度条件下进行加工和贮存。
例如,在牛奶加工过程中,PLC可以根据设定的温度曲线,控制加热和冷却设备的运行,确保牛奶在恒温条件下进行杀菌和保鲜,防止细菌滋生和品质变质。
案例三:工业机械设备的运行监控在大型工业机械设备的生产过程中,PLC被用于监控和控制设备的运行状态。
它可以实时采集并处理各种传感器的信号,判断设备的工作状态和负荷情况,并根据设定的条件进行自动调整。
例如,在一台注塑机中,PLC可以监测温度、压力、速度等参数,实时控制模具的运作,保持产品的制造精度和生产效率。
案例四:油田采油自动化控制在油田进行采油作业时,PLC被用于控制采油设备的开关、阀门和泵的运行。
它可以根据井口的油压和液位变化,自动调整各个设备的工作状态,确保采油过程的稳定和高效。
同时,PLC还可以记录并传输井口的工况数据,为油田管理人员提供决策支持和远程监控。
综上所述,PLC在生产过程控制中的应用是多样且广泛的。
它不仅可以实现自动化控制,提升生产效率和产品质量,还可以监控和调整各个环节的运行状态,预防故障和质量问题的发生。
随着科技的不断进步和PLC技术的不断发展,相信PLC在生产过程控制中的应用将会越来越广泛,并为各行各业带来更多的机遇和挑战。
阀门控制方案
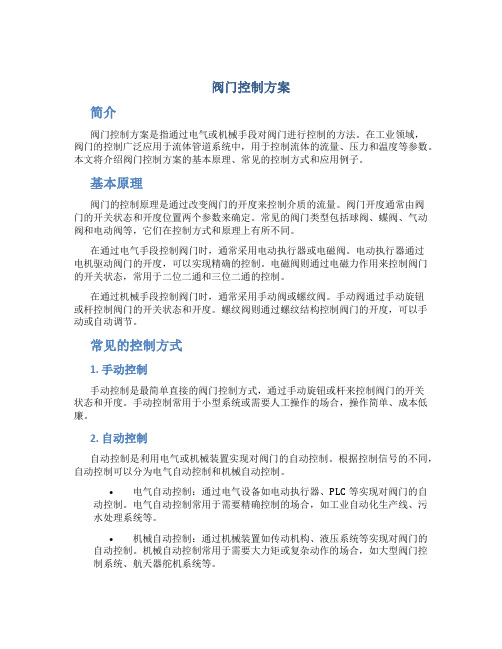
阀门控制方案简介阀门控制方案是指通过电气或机械手段对阀门进行控制的方法。
在工业领域,阀门的控制广泛应用于流体管道系统中,用于控制流体的流量、压力和温度等参数。
本文将介绍阀门控制方案的基本原理、常见的控制方式和应用例子。
基本原理阀门的控制原理是通过改变阀门的开度来控制介质的流量。
阀门开度通常由阀门的开关状态和开度位置两个参数来确定。
常见的阀门类型包括球阀、蝶阀、气动阀和电动阀等,它们在控制方式和原理上有所不同。
在通过电气手段控制阀门时,通常采用电动执行器或电磁阀。
电动执行器通过电机驱动阀门的开度,可以实现精确的控制。
电磁阀则通过电磁力作用来控制阀门的开关状态,常用于二位二通和三位二通的控制。
在通过机械手段控制阀门时,通常采用手动阀或螺纹阀。
手动阀通过手动旋钮或杆控制阀门的开关状态和开度。
螺纹阀则通过螺纹结构控制阀门的开度,可以手动或自动调节。
常见的控制方式1. 手动控制手动控制是最简单直接的阀门控制方式,通过手动旋钮或杆来控制阀门的开关状态和开度。
手动控制常用于小型系统或需要人工操作的场合,操作简单、成本低廉。
2. 自动控制自动控制是利用电气或机械装置实现对阀门的自动控制。
根据控制信号的不同,自动控制可以分为电气自动控制和机械自动控制。
•电气自动控制:通过电气设备如电动执行器、PLC等实现对阀门的自动控制。
电气自动控制常用于需要精确控制的场合,如工业自动化生产线、污水处理系统等。
•机械自动控制:通过机械装置如传动机构、液压系统等实现对阀门的自动控制。
机械自动控制常用于需要大力矩或复杂动作的场合,如大型阀门控制系统、航天器舵机系统等。
3. 远程控制远程控制是指通过远程通信手段实现对阀门的远程控制。
远程控制可以通过有线或无线的方式进行。
常见的远程控制手段包括以太网、Modbus、Profinet等通信协议。
远程控制常用于系统复杂、距离较远或需要远程监控的场合,提高了操作的便捷性和安全性。
应用例子1. 工业流程控制阀门在工业领域的流程控制中起到至关重要的作用。
基于PLC的家居安防系统的设计
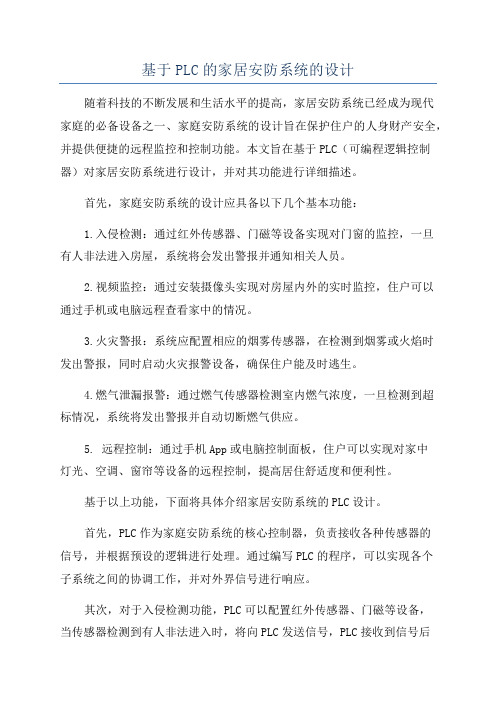
基于PLC的家居安防系统的设计随着科技的不断发展和生活水平的提高,家居安防系统已经成为现代家庭的必备设备之一、家庭安防系统的设计旨在保护住户的人身财产安全,并提供便捷的远程监控和控制功能。
本文旨在基于PLC(可编程逻辑控制器)对家居安防系统进行设计,并对其功能进行详细描述。
首先,家庭安防系统的设计应具备以下几个基本功能:1.入侵检测:通过红外传感器、门磁等设备实现对门窗的监控,一旦有人非法进入房屋,系统将会发出警报并通知相关人员。
2.视频监控:通过安装摄像头实现对房屋内外的实时监控,住户可以通过手机或电脑远程查看家中的情况。
3.火灾警报:系统应配置相应的烟雾传感器,在检测到烟雾或火焰时发出警报,同时启动火灾报警设备,确保住户能及时逃生。
4.燃气泄漏报警:通过燃气传感器检测室内燃气浓度,一旦检测到超标情况,系统将发出警报并自动切断燃气供应。
5. 远程控制:通过手机App或电脑控制面板,住户可以实现对家中灯光、空调、窗帘等设备的远程控制,提高居住舒适度和便利性。
基于以上功能,下面将具体介绍家居安防系统的PLC设计。
首先,PLC作为家庭安防系统的核心控制器,负责接收各种传感器的信号,并根据预设的逻辑进行处理。
通过编写PLC的程序,可以实现各个子系统之间的协调工作,并对外界信号进行响应。
其次,对于入侵检测功能,PLC可以配置红外传感器、门磁等设备,当传感器检测到有人非法进入时,将向PLC发送信号,PLC接收到信号后将会触发警报,同时将相关信息通过短信或手机App传输给用户,以便及时采取措施。
对于视频监控功能,PLC可以接收到摄像头传输的图像信号,并通过系统显示屏或手机App进行实时监控。
另外,PLC还可以配置运动检测传感器,当传感器监测到有可疑人员或物体移动时,PLC将自动调整摄像头的焦点并进行追踪,保证监控的完整性。
对于火灾警报和燃气泄漏报警功能,PLC可以接收到烟雾传感器和燃气传感器的信号,一旦检测到异常情况,PLC将会触发警报并自动启动相应的报警设备。
PLC在能源行业中的应用案例

PLC在能源行业中的应用案例近年来,随着科技的不断进步和能源需求的增加,自动化控制成为现代能源行业不可或缺的一部分。
可编程逻辑控制器(PLC)作为一种重要的控制设备,广泛应用于能源行业中的各个领域。
本文将介绍几个PLC在能源行业中的应用案例,以展示其在提高效率、降低成本、增强安全性等方面的优势。
案例一:发电厂中的PLC控制系统在发电厂中,PLC被广泛应用于控制和监控系统,以确保发电过程的稳定性和安全性。
通过PLC控制系统,运营人员可以实时监测电厂的运行状态,并对各个设备进行远程控制和调节。
例如,PLC可以控制发电机组的启动和停机,根据电网负荷自动调节发电机的输出功率,确保电网供电的平稳性和可靠性。
此外,PLC还可以监控电厂设备的温度、压力、流量等参数,及时报警并采取措施避免潜在的故障和事故发生。
通过PLC的应用,发电厂的运行效率得到提升,同时也降低了运营成本和人力资源的需求。
案例二:石油化工厂中的PLC控制系统石油化工厂是能源行业中另一个重要的领域,PLC在其中的应用也非常广泛。
在石油化工生产过程中,涉及到多个关键环节和复杂的控制要求,如原料进料、反应过程、分离和精炼等。
PLC通过其强大的控制能力和可编程性,在石化工厂的各个环节中发挥着重要作用。
例如,PLC可以实现对原料进料的精确计量和控制,使生产过程更加稳定和可控。
另外,通过PLC的控制,可以实现反应过程的自动控制和优化,提高产品的质量和产量。
此外,PLC还可以实时监测工艺参数,如温度、压力、液位等,并进行合理的调节,以确保石化工厂的安全运行。
案例三:能源管道的远程监测与控制能源行业中还有一个关键的环节是管道运输,如石油管道、天然气管道等。
PLC通过远程监测与控制系统,实现对能源管道的安全、高效运行。
通过在管道网络中设置PLC装置,可以实时监测管道的压力、流速、温度等参数,并且根据需要自动调整控制阀门和泵站等设备,以确保能源的顺畅传输和安全性。
如何进行PLC系统的网络通信与远程监控
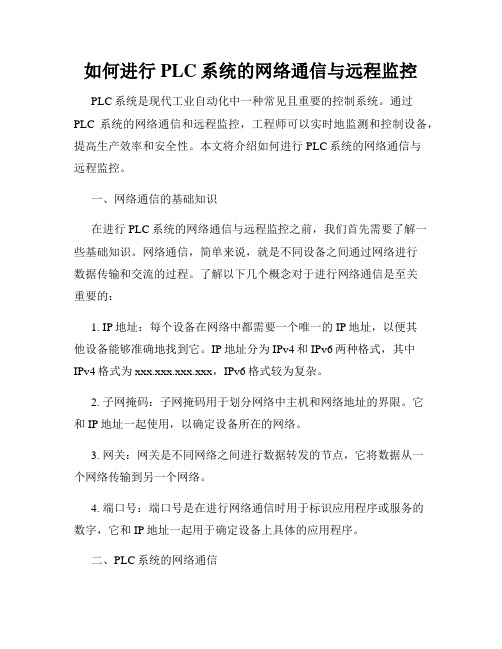
如何进行PLC系统的网络通信与远程监控PLC系统是现代工业自动化中一种常见且重要的控制系统。
通过PLC系统的网络通信和远程监控,工程师可以实时地监测和控制设备,提高生产效率和安全性。
本文将介绍如何进行PLC系统的网络通信与远程监控。
一、网络通信的基础知识在进行PLC系统的网络通信与远程监控之前,我们首先需要了解一些基础知识。
网络通信,简单来说,就是不同设备之间通过网络进行数据传输和交流的过程。
了解以下几个概念对于进行网络通信是至关重要的:1. IP地址:每个设备在网络中都需要一个唯一的IP地址,以便其他设备能够准确地找到它。
IP地址分为IPv4和IPv6两种格式,其中IPv4格式为xxx.xxx.xxx.xxx,IPv6格式较为复杂。
2. 子网掩码:子网掩码用于划分网络中主机和网络地址的界限。
它和IP地址一起使用,以确定设备所在的网络。
3. 网关:网关是不同网络之间进行数据转发的节点,它将数据从一个网络传输到另一个网络。
4. 端口号:端口号是在进行网络通信时用于标识应用程序或服务的数字,它和IP地址一起用于确定设备上具体的应用程序。
二、PLC系统的网络通信PLC系统的网络通信可以分为内部通信和外部通信两种类型。
内部通信是指PLC系统内部不同模块之间的通信,而外部通信则是指PLC系统与其他设备之间的通信。
1. 内部通信内部通信是PLC系统中各个模块之间的数据交换和传输。
在进行内部通信时,我们需要考虑以下几个方面:(1)PLC系统的硬件配置:不同的PLC系统在硬件上可能有差异,因此在进行内部通信时,我们需要根据具体的硬件配置来设计通信方式。
(2)通信协议:PLC系统的内部通信通常使用特定的通信协议来确保数据的稳定传输。
常见的通信协议包括Modbus、Profibus、CAN 等。
(3)数据传输方式:内部通信可以通过串行通信方式(如RS232、RS485)或者以太网通信方式进行。
2. 外部通信外部通信是指PLC系统与其他设备之间的数据交换和传输。
基于PLC的双控阀门控制实验平台设计

】 其 中:
Z 自动控制 D: S 手动控制 D:
双控 阀门控制 实验 平 台组 成 如 图 1 所示 。
工控机 ( 上位机 )
Z DK: 自动开 1 D 手动开 S K: J 检修
2 P C控 制 的双控 阀门控制 的程序 设计 L
位后 , D 常闭触点断 开, K W K继 电器 断电 , 开启过 程结束。K和 G分别为电机的正反转 , 以不能同 所
时得电, 要有互锁功能, 将各 自的常闭触点传人对方 的线圈中。第二行为双控 阀门的关闭控制 , 控制方
式和开启时类似 。 检修信号 (x 是 由上位机发 出的 , j) 检修时将其
和手动控制(D 两种开关 。若选择手动控制时 , S) 手
动 开关信 号 只控 制单 个 设 备 的 开启 或 关 闭 ; 选 择 若 自动控 制 , 自动 开 ( D 或 自动 关 ( D 有 效 时 , 当 Z K) Z G) 各个 有联 锁关 系 的设备会 按 照设 定 的顺序 自动 开启 或关 闭。 以下分 两种情 况设 计双 控 阀门控制 。
置 1使开 继 电器不 能得 电 , 而 可 以保 证 检 修人 员 , 从
在上位机 Wi e n 画面 中设 置有 自动控制 ( D c Z)
收 稿 日期 :2 1 —0 0 1 4—1 5
第 4期
陶炳坤等 : 基于 P C的双控 阀门控制实验平 台设计 L
2 1 年 8月 01
的安全。故障信号 ( Z 是 综合阀 门的故障 和线路 G) 的故障发 出的, 其原理为: 关 ) 开( 继电器得 电后 , 设 置为 正常 情 况 下 阀 门 应 该 在 十 分 钟 之 内 开 ( ) 关 到 位, 若十分钟后仍没有开( ) 关 到位信号 , G 则 Z置 1 , 停止开 ( ) 电器 。故 障信号还要接 到报警 电路 关 继 上, 有故障时引起报警 , 在上位机 中显示故障设备闪 烁, 提示工作人员处理故障, 一直等到工作人员按下 清零按钮 , 报警结束。 2. 有 联锁 关 系的 阀 门控 制程 序设 计 2 对于 有联 锁关 系 的 阀门 , 调用 以上模 块 时 , 在 将 对应的内部变量用外部变量代替 , 如污水处理过程 中组 合 池 1 泥 阀 1 继 电器 ( 为 Q1 ., 到 排 开 K) 85开 位( D 信号为 I7 6关继 电器( ) Q 8 6关 K w) 1., G 为 1 ., 到位 ( D 信号为 1 . 等。见表 1 G W) 1 7 7 。
电动阀门控制原理

电动阀门控制原理电动阀门控制是指利用电动执行器对阀门进行远程或自动控制的一种方法。
它常见于工业过程控制系统中,广泛应用于石油化工、电力、水处理、制药等领域。
下面将就电动阀门控制的原理进行详细阐述。
一、电动阀门的基本组成电动阀门由电动执行器和阀门本体两部分组成。
电动执行器包括电动机、行程控制器和驱动装置等组件。
阀门本体一般由阀体、阀瓣、阀杆和密封件等组件构成。
二、电动阀门的工作原理1. 信号输入:通过外部信号调节器、PLC或DCS等控制系统发送控制信号。
2. 信号解码:电动执行器接收到控制信号后,通过内部的信号解码器将其译码为相应的动作命令。
3. 电动驱动:电动执行器根据动作命令控制电动机的工作,电动机带动传动装置来完成阀门的开启、关闭或调节动作。
4. 反馈信号:电动执行器内置的行程控制器会不断检测阀门的位置,将实际位置信息反馈给控制系统,保证阀门与控制信号的一致性。
5. 补偿控制:根据反馈信号与设定值之间的偏差,控制系统可以实现对电动执行器速度和力矩的补偿控制,确保阀门的稳定运行和准确控制。
三、电动阀门控制的特点和优势1. 远程控制:电动阀门可以通过信号传输线路实现与控制系统的远程通信,方便实时监控和控制阀门的状态。
2. 自动化操作:电动执行器可根据预设的控制策略和逻辑,实现对阀门的自动开启、关闭或调节,提高生产过程的自动化程度。
3. 精确控制:电动执行器具有高精度的位置控制性能,能够实现对阀门开度的准确控制,满足不同工艺过程对阀门流量或压力的精确要求。
4. 可编程性:电动阀门的控制系统多为可编程的,可以根据实际应用需求进行自定义编程,实现多种工作模式和逻辑控制策略。
5. 安全可靠:电动阀门的执行器具有过载保护、过压保护、断电保持等功能,能够保证在异常情况下安全可靠地工作。
综上所述,电动阀门控制通过电动执行器对阀门进行远程或自动控制,实现精准、便捷的操作。
其具有远程控制、自动化操作、精确控制、可编程性和安全可靠等特点和优势,广泛应用于各个行业的工业过程控制系统中,对提高生产效率和产品质量有着重要作用。
了解PLC的功能和特点

了解PLC的功能和特点PLC(Programmable Logic Controller,可编程逻辑控制器)是一种专业控制设备,广泛应用于工业自动化领域。
本文将介绍PLC的功能和特点。
一、功能1. 程序可编程:PLC通过编写控制程序,可以实现不同的逻辑功能。
用户可以根据具体的控制需求,采用编程语言编写程序。
2. 输入输出控制:PLC通过输入输出模块,接收外部信号,如传感器信号、按钮输入等,并通过输出模块控制执行器,如电机、阀门等。
3. 逻辑运算:PLC支持逻辑运算,如与、或、非等。
根据输入信号的逻辑关系,PLC可以实现复杂的逻辑控制。
4. 运动控制:PLC可以实现运动控制功能,通过控制电机的启停、速度、方向等参数来控制机械设备的运动。
5. 远程通信:PLC支持网络通信,可以与上位机、其他PLC或远程服务器进行数据交换,实现监控、调试和远程控制功能。
6. 定时控制:PLC内置时钟模块,可以实现定时功能,如定时开关机、定时浇水等。
7. 故障诊断:PLC具有故障诊断功能,可以检测系统中的错误和故障,并通过报警或输出信号通知用户。
二、特点1. 可靠性高:PLC采用工业级芯片设计,具有高可靠性和抗干扰能力。
它能够在恶劣的工业环境下正常工作,并保证系统的稳定性。
2. 可扩展性强:PLC系统可以根据需求进行灵活扩展。
用户可以根据实际需求添加模块或更换模块,以满足不同的控制要求。
3. 编程灵活:PLC采用符合国际标准的编程语言,如LD(梯形图)、IL(指令列表)和ST(结构化文本),用户可以选择适合自己的编程方式。
4. 调试方便:PLC具有在线调试功能,用户可以实时监测系统状态、修改参数,并进行故障诊断和修复,大大提高了维护效率。
5. 易于集成:PLC在物理接口和通信协议上具有通用性,可以与不同品牌的设备进行无缝集成,实现全面的自动化控制。
6. 灵活部署:PLC体积小巧、结构紧凑,易于安装在不同的设备或控制柜中,适应多样化的工业环境。
阀门智能化与自动化技术的研究与发展
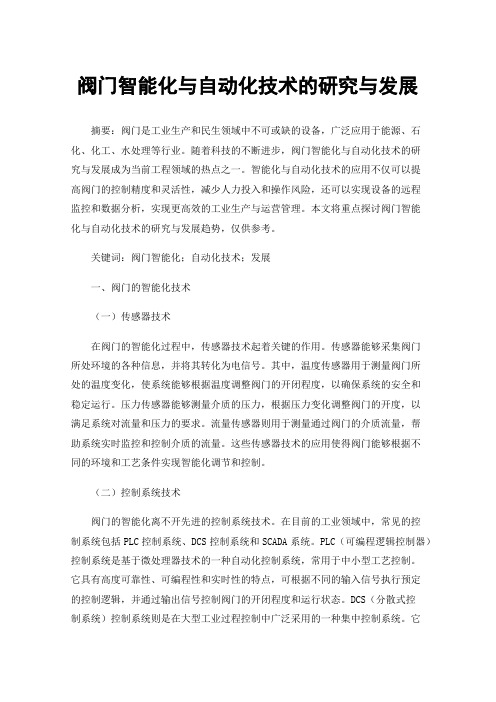
阀门智能化与自动化技术的研究与发展摘要:阀门是工业生产和民生领域中不可或缺的设备,广泛应用于能源、石化、化工、水处理等行业。
随着科技的不断进步,阀门智能化与自动化技术的研究与发展成为当前工程领域的热点之一。
智能化与自动化技术的应用不仅可以提高阀门的控制精度和灵活性,减少人力投入和操作风险,还可以实现设备的远程监控和数据分析,实现更高效的工业生产与运营管理。
本文将重点探讨阀门智能化与自动化技术的研究与发展趋势,仅供参考。
关键词:阀门智能化;自动化技术;发展一、阀门的智能化技术(一)传感器技术在阀门的智能化过程中,传感器技术起着关键的作用。
传感器能够采集阀门所处环境的各种信息,并将其转化为电信号。
其中,温度传感器用于测量阀门所处的温度变化,使系统能够根据温度调整阀门的开闭程度,以确保系统的安全和稳定运行。
压力传感器能够测量介质的压力,根据压力变化调整阀门的开度,以满足系统对流量和压力的要求。
流量传感器则用于测量通过阀门的介质流量,帮助系统实时监控和控制介质的流量。
这些传感器技术的应用使得阀门能够根据不同的环境和工艺条件实现智能化调节和控制。
(二)控制系统技术阀门的智能化离不开先进的控制系统技术。
在目前的工业领域中,常见的控制系统包括PLC控制系统、DCS控制系统和SCADA系统。
PLC(可编程逻辑控制器)控制系统是基于微处理器技术的一种自动化控制系统,常用于中小型工艺控制。
它具有高度可靠性、可编程性和实时性的特点,可根据不同的输入信号执行预定的控制逻辑,并通过输出信号控制阀门的开闭程度和运行状态。
DCS(分散式控制系统)控制系统则是在大型工业过程控制中广泛采用的一种集中控制系统。
它与PLC相比具有更高的容量和扩展性,能够实现多个控制站之间的信息共享和数据交互。
DCS控制系统将各个阀门通过网络连接起来,使得系统能够更加智能地协调和调度各个阀门的运行状态。
SCADA(监控与数据采集系统)系统是一种监控和数据采集系统,用于实时监测和控制远程设备和过程。
PLC在气动控制系统中的应用案例

PLC在气动控制系统中的应用案例气动控制系统是一种广泛应用于工业自动化领域的控制系统,它通过气动元件的配合使用以及气动信号的传输来实现对机械设备的控制。
而在气动控制系统中,PLC(Programmable Logic Controller,可编程逻辑控制器)作为一种集中控制设备,发挥着重要的作用。
本文将通过介绍一个实际的案例,来说明PLC在气动控制系统中的应用。
案例描述:某工厂生产线上有一台气动装配机器,该机器用于将产品进行组装和包装处理。
在过去,操作员需要手动控制气动装配机器的运行,但这种方式存在人为疏忽和操作不稳定的风险。
为了提高生产效率和质量,并确保工作人员的安全,工厂决定引入PLC来实现气动控制系统的自动化。
PLC系统的设计:1. 输入模块:PLC系统首先需要能够读取来自气动装配机器的各个传感器信号,以便实时监测气动装配机器的运行状态。
通过安装传感器并将其与PLC的输入模块相连接,可以将气动装配机器的信号输入到PLC中。
2. 输出模块:PLC系统需要能够控制气动装配机器的运行,因此需要将PLC与气动装配机器的执行元件(如气缸、阀门等)相连接。
通过PLC的输出模块,可以向执行元件发送气压信号,从而实现对气动装配机器的控制。
3. PLC程序:通过PLC程序,可以实现对气动装配机器的自动化控制。
在这个案例中,PLC程序可以包括以下几个方面:- 确定气动装配机器的工作流程,包括组装和包装等环节;- 监测气动装配机器的传感器信号,如检测产品是否到位、是否有堵塞等;- 根据传感器信号的反馈,控制执行元件的动作,如控制气缸的伸出和缩回;- 实现对气动装配机器的启动、停止和故障报警等功能。
4. 人机界面:为了方便操作员对气动装配机器的监控和控制,PLC系统需要提供一个人机界面。
通过人机界面,操作员可以实时了解系统状态,并进行必要的设定和调整。
人机界面可以通过触摸屏或者操作面板等形式来实现,具体根据工厂的需求来确定。
- 1、下载文档前请自行甄别文档内容的完整性,平台不提供额外的编辑、内容补充、找答案等附加服务。
- 2、"仅部分预览"的文档,不可在线预览部分如存在完整性等问题,可反馈申请退款(可完整预览的文档不适用该条件!)。
- 3、如文档侵犯您的权益,请联系客服反馈,我们会尽快为您处理(人工客服工作时间:9:00-18:30)。
PLC在阀门远程监控系统中的应用
为提高油气远程传输的安全可靠性,本文提出并设计了基于PLC远程阀门监控系统。
该系统由一个监控主站和若干阀门从站构成,主站与从站之间采用无线数传电台互连。
该系统的突出特点是现场数据采集和设备控制由PLC实现。
详细介绍了各阀门站的硬件结构及系统软件设计。
实践证明,该系统图形界面友好,可靠性高,操作方便,安全稳定,应用效果好。
1.引言
可编程控制器[1](Programmable Logic Controller,简称PLC)作为工业控制专用的计算机,由于其结构简单、性能优良,抗干扰性能好,可靠性高,编程简单,调试方便,在机械、化工、橡胶、电力、石油天然气等行业工业控制现场已日趋广泛地得到应用,成为工控现场进行实时控制的最主要的控制装置。
同时利用PLC所具有的串行通信和计算机的远程通信功能,可实现计算机对多台PLC控制装置的远程集中监控。
在石油、天然气远程输送管线上,大口径油气管道阀门是重要的基础设备之一,具有截止、开启、配送和调压等多种功能,一旦出现故障轻则影响管线的输送功能,重则导致管线的严重破坏甚至造成人生安全,因此对油气管道及阀门的全程状态监控显得尤为重要。
远程油气管道监控系统就是为提高油气远程输送的安全可靠性而提出来的,该系统允许系统操作员通过位于监控中心的计算机终端,进行对一定区域的阀门站进行远程,具有较高的可靠性和运行效率。
2.监控系统的组成结构
远程油气管线监控系统硬件组成示意图如图1所示。
该系统是以PLC作为远程控制终端,以工控PC机作为上位机的主从式一点对多点的远程无线监控网络,采用串行异步通讯协议。
下位机PLC安装在各阀门站,根据上位机的指令或自身的控制程序控制阀门的开启或关闭,并配置各种传感器等辅助设备,组成数据采集和控制系统。
上位机安装于油气调度控制中心,以半双工轮询方式同各阀门站PLC通讯,以此形成SCADA(数据采集与监控)系统。
无线数传电台采用透明方式工作,只起数据传输作用,整个网络数据收发采用同一频率,通讯时,站点的识别是通过PLC的不同地址编号来实现的。
各阀门站采用PLC作为系统的基本RTU单元,完成各种测量和控制任务,主要由PLC 本体、AD转换模块、传感器组与智能驱动装置四部分组成。
2.1 阀门电机主回路
图2为阀门电机主回路及PLC外部端子回路示意图。
三相交流电动机M分别由交流接触
器KMO和KMC的通断来驱动阀芯顺、逆时针转动实现阀门的开启或关闭。
图2 阀门电机主回路及PLC外部端子回路示意图
2.2 PLC外部端子回路
系统选用三菱电机公司生产的FX2N-32MR作为RTU单元。
智能驱动装置是引进美国Limitorque技术的SMC多回转型阀门电动装置,它可以单台控制,也可集中控制,可现场操
作,也可远程控制,除能驱动阀门动作外同时还能将自身的状态以标准信号的方式送出供PLC
进行状态检测[2]。
考虑阀门站兼有就地和远程两种控制方式,PLC共管理12路输入信号和8路输出信号。
其输入输出信号及端子分配如表1所示。
2.3 A/D转换模块
A/D转换模块选用与PLC本体配套的FX2N-4AD,其有四路独立的差分输入通道。
每个通道可选择为电流型(±20mA)或电压型(±10VDC)信号输入。
在每个阀门站管线或阀门的适当位置装上温度、压力和流量传感器,以采集油气管线的工作状态。
参数信号经传感器变送后分别与FX2N-4AD各独立通道相连,经AD转换后放到相应的数据寄存器中,供PLC程序定时读取。
2.4 数传电台选型与设置
计算机与PLC之间采用无线数传电台方式进行通讯,采用交错编码、收后重发技术,提高无线通讯的抗干扰能力,确保阀门站无线远程控制的安全可靠运行。
数据传输模块选用美国的MDS2710数字传输电台,它可为两点之间的数据传输提供全透明的半双工通讯连接[3]。
它一端与嵌入在PLC内的通讯FX2n-485-BD通过RS485接口方式相连,另一端则通过标准的RS232接口与监控中心服务器的串口连接,组成准双向的数据发送与接收无线通讯网络,网络的最大节点数可达32个。
电台数据帧格式设置为7位数据位、1位停止位、偶校验的方式,传输速率为9600bit/s。
电台发射功率为25W,采用收、发同频方式(235MHz),主站架设全向天线,阀门站架设定向八木式天线后,数据传输距离可达15Km以上,在地势平坦地区,通讯距离可达20Km。
与之相适应PLC通讯格式特殊数据寄存器D8120设置为-8058,D8121寄存器用来设置各阀门站ID号。
为了安全,除在天线安装了避雷针外,天线到电台之间的馈线也加装了避雷器。
3.监控系统软件实现
系统对阀门的监控能实现就地控制和远程控制两种控制方式。
系统控制过程流程为:传感器将测得信号通过屏蔽信号电缆传送到A/D转换模块的输入端,经过A/D转换模块转换后存入指定的数据寄存器供PLC读取。
PLC将数据通过无线数传电台送出,最后到监控中心供系统处理,完成一次数据采集过程。
系统控制信号当为就地控制方式时由操作者通过阀门站控制箱内的按钮直接控制;当为远程控制时则由监控中心发出,PLC接收到信号后通过输出端口控制智能驱动装置使阀门动作。
系统软件由两部分组成:一是PLC端实时测控软件;二是监控中心计算机测控数据实时处理软件。
3.1 阀门站PLC软件设计
PLC端阀门站实时测控软件控制过程流程图如图3所示。
它采用梯形图逻辑编制,编程方便且直观。
因篇幅原因,下面给出PLC本体从FX2N-4AD给取AD转换结果及部分控制程序梯形图[1,4],如图4所示。
图4 PLC控制程序梯形图(部分)
3.2 系统监控中心软件
本监控系统软件是利用KingView6.5[5]编写。
能充分利用Windows的图形编辑功能,方便地构成监控画面,以动画图形方式显示控制设备的状态,具有数据库ODBC接口、DDE功能、可便利地生成各种曲线和用户报表,也可将数据以Excel格式输出。
系统软件主要由实时监控、曲线动态生成、数据报表管理、数据库管理、报警及用户管理六大功能模块组成。
用户通过系统可随时清楚了解网内各阀门站的状态参数与阀门状态,对阀门实施远程控制,对所监测的各种参数均设有上、下限值,具有越限报警、紧急处理功能。
系统将历史数据以多种方式保存,便于管理者进行阀门站运行数据的分析统计和故障分析[6]。
图5为监控系统主画面。
图5 监控系统主画面
4.结语
系统监控中心通过数据传输电台对油气管线中多阀门站参数同时实时采集、对异常情况及时报警,消除了安全隐患,极大改善了我国目前油气管线监管不力的现状,系统有较强的数据处理功能,实现了数据报表的自动生成、数据库的访问、排序、查询等多种功能。
系统经半年多实际运行,其性能稳定,运行可靠,人机界面友好,易操作,使用维护方便,具有很好的可扩展性和较高的实用价值。