moog D791 D792
DiGiCo SD7数字调音台产品介绍中文

香港葵涌梨木道73-77号海晖中心五楼505室大中华区总代理華匯DiGiCo SD7,一步跨过两个时代。
DiGiCo D系列调音台邀您步入一个全新的数字调音世界。
使用全新的SD7数字调音台,我们将带您穿越两个时代。
结合了Stealth Digital Processing 技术与壮观的用户界面,再一次为世界各地的调音师解除了许多使用障碍。
目录2 一步跨过两个时代2 目录3 介绍5 创建12年,领先12年8 受启发的工程学9 Stealth音频处理能力11 一些调音台使人想起模拟的根源…13 20/20视觉:从一开始就非常直观15 SD7的工作界面:让您一目了然18 谁是我们最优先考虑的人?您!19 F.0.H的首选21 监听调音师们的梦想23 世界级剧场缩混25 从现场到转播:提供稳固的工作状态27 真正灵活的操作伙伴30 高达192KHz的纯正音质:耳听为实31 12输入通道为一组,仅仅是符合操作逻辑吗?33 4段均衡,也同样的4段动态均衡器34 “多段压缩”,不正是您想要的吗?36 不仅是音频桌面设置,也是您个性的体现!37 IDM:动态交互电平表桥40 诱人的效果Tiger SHARC®41 MADI,光纤,备份,AES,D-Tube,一应俱全42 调音台I/043 双备份44 12年传承45 技术信息当专业音频领域第一次将目光投向DiGiCo D5 Live时,它提供了在数字音频环境可以提供的最好的模拟工作实用性与音频通用性,以及丰富的功能。
许多年过去了,D系列调音台一直是标准的制定者,并且其精美的用户界面从来没有被其他调音台击败过。
对于大多数调音师来说,D系列调音台也继续提供了模拟平滑度和数字清晰度的最佳结合。
但人们的期待一直在增加。
当今世界,无论对音响工程师还是调音台生厂商而言,竞争都非常激烈。
您希望得到可以依赖的最好的工具;您同时也希望调音台考虑到每个主要应用,并且为艺术和音响工程科学而设计。
ICP DAS I-7045D 16 Ch DO DAQ Module 快速入门指南说明书

I-7045D16 Channel Digital Output Data AcquisitionModuleQuick Start GuideProduct Website:https:///i_7045_d.html/dcon_utility_pro.html1. IntroductionI-7045D is intelligently designed to provide signal conditioning system monitoring and safe value settings. I-7045 is a cost-effective solution for a wide range of valuable industrial control signals and systems. The DCON utility can help users to configure and test I-7045 16-Channel Isolated Digital Output modules. Plenty of library functions and demo programs are provided to let users develop programs easily under Windows, Linux and DOS operating systems. Users may mount the modules on a DIN rail, panel or wall. Modules have a screw-terminal block to connect to the signals.2. Terminal AssignmentI-7045D 16 Ch DO DAQ Module- QuickStart (May/2017)3. Block/ Wiring DiagramI-7045D 16 Ch DO DAQ Module- QuickStart (May/2017)4. Default SettingsDefault settings for the I-7045D DIO modules are as follows:。
精轧机液压AGC系统分析

AGC液压伺服系统仿真分析设计研究院二○○六年十二月十三日我公司中标的1580轧机,是我公司总成套项目。
液压室完成了全线液压、润滑、高压水系统的设计工作。
为了更好的作好将来的现场调试工作,特作精轧机液压AGC 伺服系统仿真分析。
精轧机液压AGC 系统的简图如下:图-1 热连轧精轧机液压AGC 系统简图1 系统的数学模型1.1控制调节器位移、轧制力控制器均采用PI 调节器:sK K G i P C 1+= 式中:p K ——比例放大系数,位移控制器为90,轧制力控制器为50;I K ——积分放大系数,位移控制器为30,轧制力控制器为3;1.2伺服放大器伺服放大器输入±5V ,所对应输出为±10mA ,故V A V A K a /102)5/(101033--⨯=⨯=1.3电液伺服阀伺服阀阀芯位移和输入电流的关系可用二阶振荡环节表示1212++=svsv svcv svK I x ωξω以伺服阀阀芯位移作为输入信号,伺服阀输出流量L Q 的方程为⎪⎪⎩⎪⎪⎨⎧<>-=02)(2v L v d v L s v d L x P dxC x P P dx C Q ρπρπ式中:v x ——伺服阀阀芯位移量; L P ——负载压力变化; d C ——滑阀阀口流量系数; d ——阀芯直径; ρ——油液密度; s P ——供油压力;精轧机液压压下系统同样选择的是Moog 公司型号为D791-4001/S25JOQB6VSX2-B 电液伺服阀,由样本得到其动态特性参数如下:Hz sv 100=ω7.0=sv ξ该阀在35bar 压降时,流量为250L/min 。
因为:P dx C Q v d ∆=ρπ2maxN s m Pas m P Q dx C v d //1023.2103560/102502566330max--⨯=⨯⨯=∆=ρπ这里是±10mA 对应阀芯最大开口比例系数应为:)/(1023.201.0/1023.2546A N s m K sv ⋅⋅⨯=⨯=--1.4 液压缸基本方程从阀进入油缸的流量除了推动活塞运动外,还要补偿缸内的各种泄漏,补偿液体的压缩量和管道等的膨胀量。
MOOG直动式伺服阀接线方式资料
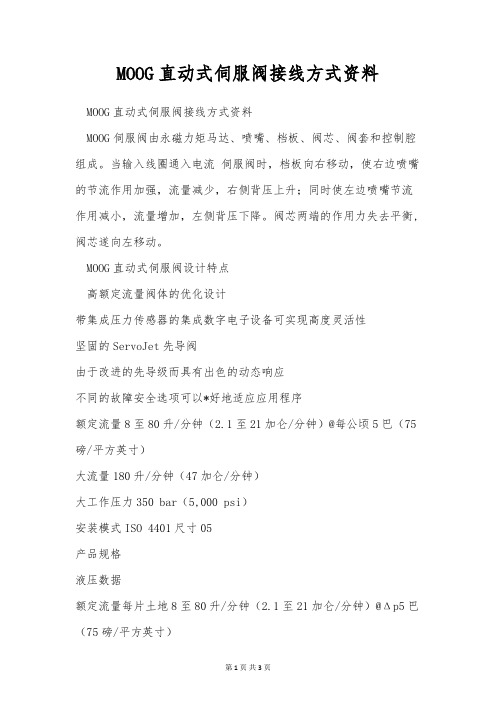
MOOG直动式伺服阀接线方式资料MOOG直动式伺服阀接线方式资料MOOG伺服阀由永磁力矩马达、喷嘴、档板、阀芯、阀套和控制腔组成。
当输入线圈通入电流伺服阀时,档板向右移动,使右边喷嘴的节流作用加强,流量减少,右侧背压上升;同时使左边喷嘴节流作用减小,流量增加,左侧背压下降。
阀芯两端的作用力失去平衡, 阀芯遂向左移动。
MOOG直动式伺服阀设计特点高额定流量阀体的优化设计带集成压力传感器的集成数字电子设备可实现高度灵活性坚固的ServoJet先导阀由于改进的先导级而具有出色的动态响应不同的故障安全选项可以*好地适应应用程序额定流量8至80升/分钟(2.1至21加仑/分钟)@每公顷5巴(75磅/平方英寸)大流量180升/分钟(47加仑/分钟)大工作压力350 bar(5,000 psi)安装模式ISO 4401尺寸05产品规格液压数据额定流量每片土地8至80升/分钟(2.1至21加仑/分钟)@Δp5巴(75磅/平方英寸)大流量180升/分钟(47加仑/分钟)大工作压力350 bar(5,000 psi)安装模式ISO 4401尺寸05(NG 10)100%步骤响应33毫秒@ 210 bar(3,000 psi)电气数据电源电压24 VDC(18至32 VDC)额定信号选项+/ 10 V,+ / 10 mA和420 mA选项现场总线接口MOOG直动式伺服阀D633和D634 ISO 4401系列,尺寸03和05额定流量:5至100升/分钟(1.3至26.3 gpm)的ΔP35巴(500 psi)的每土地z大流量:180升/分钟(47加仑)大小05z大工作压力:350巴(5000磅)安装模式:ISO 4401尺寸03和05D636和D637 ISO 4401系列,尺寸03和05额定流量:5至100升/分钟(1.3至26.3 gpm)的ΔP35巴(500 psi)的每土地z大流量:180升/分钟(47加仑)大小05z大工作压力:350巴(5000磅)安装模式:ISO 4401尺寸03和05可选的现场总线接口的数码电子MOOG穆格G761系列伺服阀是具有机械反馈先导级的两级流量控制伺服阀。
t7910主板详解
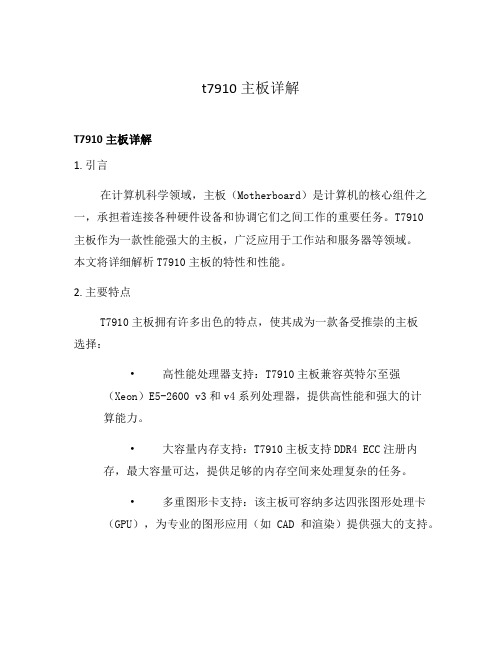
t7910主板详解T7910主板详解1. 引言在计算机科学领域,主板(Motherboard)是计算机的核心组件之一,承担着连接各种硬件设备和协调它们之间工作的重要任务。
T7910主板作为一款性能强大的主板,广泛应用于工作站和服务器等领域。
本文将详细解析T7910主板的特性和性能。
2. 主要特点T7910主板拥有许多出色的特点,使其成为一款备受推崇的主板选择:•高性能处理器支持:T7910主板兼容英特尔至强(Xeon)E5-2600 v3和v4系列处理器,提供高性能和强大的计算能力。
•大容量内存支持:T7910主板支持DDR4 ECC注册内存,最大容量可达,提供足够的内存空间来处理复杂的任务。
•多重图形卡支持:该主板可容纳多达四张图形处理卡(GPU),为专业的图形应用(如CAD和渲染)提供强大的支持。
•扩展性强:T7910主板提供多个PCIe插槽、USB接口和存储接口,使其具备良好的扩展性,能够满足用户不断增长的需求。
•稳定可靠:采用优质的电子元件和严格的质量控制,T7910主板保证了其稳定性和可靠性,能够在长时间高负载工作环境下表现出色。
3. 性能表现T7910主板在性能方面表现出众,具备以下出色的性能特点:•高速数据传输:T7910主板支持PCIe 技术,可实现高达8GT/s的数据传输速度,大大提高数据传输效率。
•卓越的图形处理能力:T7910主板的多重图形卡支持加速了图形处理应用的运行速度,有效提升了工作效率。
•快速存储速度:T7910主板提供多个SATA接口和接口,支持高速的SATA 6Gb/s和PCIe Gen3 x4接口,确保数据存储的快速读写。
•稳定的供电系统:T7910主板采用优质的供电系统,为高性能处理器和其他硬件设备提供稳定可靠的电源支持。
4. 总结T7910主板作为一款性能强大、稳定可靠的主板,广泛应用于工作站和服务器等领域。
其高性能处理器支持、大容量内存支持和多重图形卡支持等特点,以及卓越的性能表现,使其成为创作者们的首选。
莫贾V2416A系列迷你型无风扇、振动防护计算机产品介绍说明书
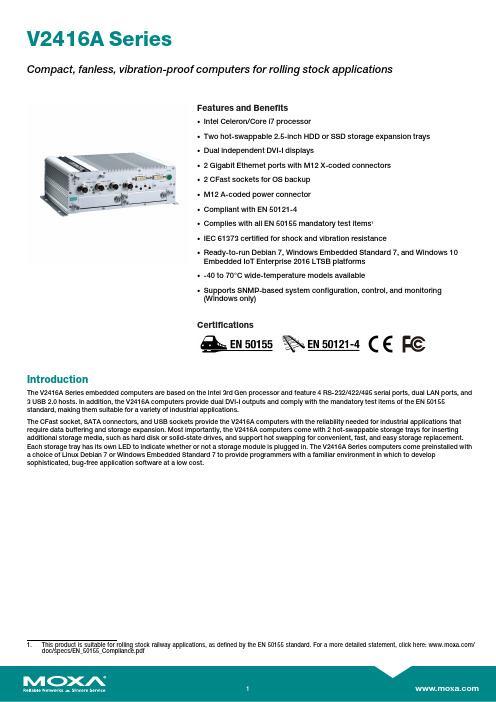
V2416A SeriesCompact,fanless,vibration-proof computers for rolling stock applicationsFeatures and Benefits•Intel Celeron/Core i7processor•Two hot-swappable2.5-inch HDD or SSD storage expansion trays•Dual independent DVI-I displays•2Gigabit Ethernet ports with M12X-coded connectors•2CFast sockets for OS backup•M12A-coded power connector•Compliant with EN50121-4•Complies with all EN50155mandatory test items1•IEC61373certified for shock and vibration resistance•Ready-to-run Debian7,Windows Embedded Standard7,and Windows10Embedded IoT Enterprise2016LTSB platforms•-40to70°C wide-temperature models available•Supports SNMP-based system configuration,control,and monitoring(Windows only)CertificationsIntroductionThe V2416A Series embedded computers are based on the Intel3rd Gen processor and feature4RS-232/422/485serial ports,dual LAN ports,and 3USB2.0hosts.In addition,the V2416A computers provide dual DVI-I outputs and comply with the mandatory test items of the EN50155 standard,making them suitable for a variety of industrial applications.The CFast socket,SATA connectors,and USB sockets provide the V2416A computers with the reliability needed for industrial applications that require data buffering and storage expansion.Most importantly,the V2416A computers come with2hot-swappable storage trays for inserting additional storage media,such as hard disk or solid-state drives,and support hot swapping for convenient,fast,and easy storage replacement. Each storage tray has its own LED to indicate whether or not a storage module is plugged in.The V2416A Series computers come preinstalled with a choice of Linux Debian7or Windows Embedded Standard7to provide programmers with a familiar environment in which to develop sophisticated,bug-free application software at a low cost.1.This product is suitable for rolling stock railway applications,as defined by the EN50155standard.For a more detailed statement,click here:/doc/specs/EN_50155_Compliance.pdfAppearanceFront View Rear ViewSpecificationsComputerCPU V2416A-C2Series:Intel®Celeron®Processor1047UE(2M cache,1.40GHz)V2416A-C7Series:Intel®Core™i7-3517UE Processor(4M cache,up to2.80GHz) System Chipset Mobile Intel®HM65Express ChipsetGraphics Controller Intel®HD Graphics4000(integrated)System Memory Pre-installed4GB DDR3System Memory Slot SODIMM DDR3/DDR3L slot x1Supported OS Linux Debian7Windows Embedded Standard7(WS7E)32-bitWindows Embedded Standard7(WS7E)64-bitStorage Slot CFast slot x2Computer InterfaceEthernet Ports Auto-sensing10/100/1000Mbps ports(M12X-coded)x2Serial Ports RS-232/422/485ports x4,software selectable(DB9male)USB2.0USB2.0hosts x1,M12D-coded connectorUSB2.0hosts x2,type-A connectorsAudio Input/Output Line in x1,Line out x1,M12D-codedDigital Input DIs x6Digital Output DOs x2Video Input DVI-I x2,29-pin DVI-D connectors(female)Digital InputsIsolation3k VDCConnector Screw-fastened Euroblock terminalDry Contact On:short to GNDOff:openI/O Mode DISensor Type Dry contactWet Contact(NPN or PNP)Wet Contact(DI to COM)On:10to30VDCOff:0to3VDCDigital OutputsConnector Screw-fastened Euroblock terminalCurrent Rating200mA per channelI/O Type SinkVoltage24to40VDCLED IndicatorsSystem Power x1Storage x1Hot-swappable2LAN2per port(10/100/1000Mbps)Serial2per port(Tx,Rx)Serial InterfaceBaudrate50bps to921.6kbpsFlow Control RTS/CTS,XON/XOFF,ADDC®(automatic data direction control)for RS-485,RTSToggle(RS-232only)Isolation N/AParity None,Even,Odd,Space,MarkData Bits5,6,7,8Stop Bits1,1.5,2Serial SignalsRS-232TxD,RxD,RTS,CTS,DTR,DSR,DCD,GNDRS-422Tx+,Tx-,Rx+,Rx-,GNDRS-485-2w Data+,Data-,GNDRS-485-4w Tx+,Tx-,Rx+,Rx-,GNDPower ParametersInput Voltage12to48VDCPower Connector M12A-coded male connectorPower Consumption(Max.) 3.3A@12VDC0.82A@48VDCPower Consumption40W(max.)Physical CharacteristicsHousing AluminumIP Rating IP30Dimensions(with ears)250x86x154mm(9.84x3.38x6.06in)Dimensions(without ears)275x92x154mm(10.83x3.62x6.06in)Weight4,000g(8.98lb)Installation DIN-rail mounting(optional),Wall mounting(standard) Protection-CT models:PCB conformal coating Environmental LimitsOperating Temperature Standard Models:-25to55°C(-13to131°F)Wide Temp.Models:-40to70°C(-40to158°F) Storage Temperature(package included)-40to85°C(-40to185°F)Ambient Relative Humidity5to95%(non-condensing)Standards and CertificationsEMC EN55032/24EMI CISPR32,FCC Part15B Class AEMS IEC61000-4-2ESD:Contact:6kV;Air:8kVIEC61000-4-3RS:80MHz to1GHz:20V/mIEC61000-4-4EFT:Power:2kV;Signal:2kVIEC61000-4-5Surge:Power:2kVIEC61000-4-6CS:10VIEC61000-4-8PFMFRailway EN50121-4,IEC60571Railway Fire Protection EN45545-2Safety EN60950-1,IEC60950-1Shock IEC60068-2-27,IEC61373,EN50155Vibration IEC60068-2-64,IEC61373,EN50155DeclarationGreen Product RoHS,CRoHS,WEEEMTBFTime332,173hrsStandards Telcordia(Bellcore),GBWarrantyWarranty Period3yearsDetails See /warrantyPackage ContentsDevice1x V2416A Series computerInstallation Kit8x screw,for storage installation2x storage key1x wall-mounting kit8x washer,for HDD/SSDDocumentation1x document and software CD1x quick installation guide1x warranty cardDimensionsOrdering InformationModel Name CPU Memory(Default)OS CFast(CTO)Backup CFast(CTO)Hot-SwappableSSD/HDD Tray(CTO)Operating Temp.ConformalCoatingV2416A-C2Celeron1047UE4GB or optional1(Optional)1(Optional)2(Optional)-25to55°C–V2416A-C2-T Celeron1047UE4GB or optional1(Optional)1(Optional)2(Optional)-40to70°C–V2416A-C2-CT-T Celeron1047UE4GB or optional1(Optional)1(Optional)2(Optional)-40to70°C✓V2416A-C7i7-3517UE4GB or optional1(Optional)1(Optional)2(Optional)-25to55°C–V2416A-C7-T i7-3517UE4GB or optional1(Optional)1(Optional)2(Optional)-40to70°C–V2416A-C7-CT-T i7-3517UE4GB or optional1(Optional)1(Optional)2(Optional)-40to70°C✓V2416A-C2-W7E Celeron1047UE4GB8GB1(Optional)2(Optional)-25to55°C–V2416A-C2-T-W7E Celeron1047UE4GB8GB1(Optional)2(Optional)-40to70°C–V2416A-C7-T-W7E Core i7-3517UE4GB8GB1(Optional)2(Optional)-40to70°C–Accessories(sold separately)Battery KitsRTC Battery Kit Lithium battery with built-in connectorCablesCBL-M12XMM8PRJ45-BK-100-IP67M12-to-RJ45Cat-5E UTP gigabit Ethernet cable,8-pin X-coded male connector,IP67,1mCBL-M12(FF5P)/Open-100IP67A-coded M12-to-5-pin power cable,IP67-rated5-pin female M12connector,1mConnectorsM12A-5PMM-IP685-pin male circular threaded D-coded M12USB connector,IP68M12X-8PMM-IP678-pin male X-coded circular threaded gigabit Ethernet connector,IP67M12A-5P-IP68A-coded screw-in sensor connector,female,IP68,4.05cmM12A-8PMM-IP678-pin male circular threaded A-codes M12connector,IP67-rated(for field-installation)Power AdaptersPWR-24270-DT-S1Power adapter,input voltage90to264VAC,output voltage24V with2.5A DC loadPower CordsPWC-C7AU-2B-183Power cord with Australian(AU)plug,2.5A/250V,1.83mPWC-C7CN-2B-183Power cord with two-prong China(CN)plug,1.83mPWC-C7EU-2B-183Power cord with Continental Europe(EU)plug,2.5A/250V,1.83mPWC-C7UK-2B-183Power cord with United Kingdom(UK)plug,2.5A/250V,1.83mPWC-C7US-2B-183Power cord with United States(US)plug,10A/125V,1.83mAntennasANT-WDB-ANF-0407 2.4/5GHz,omni-directional antenna,4/7dBi,N-type(male)Wall-Mounting KitsV2400Isolated Wall Mount Kit Wall-mounting kit with isolation protection,2wall-mounting brackets,4screwsDIN-Rail Mounting KitsDK-DC50131DIN-rail mounting kit,6screws©Moxa Inc.All rights reserved.Updated Jun12,2019.This document and any portion thereof may not be reproduced or used in any manner whatsoever without the express written permission of Moxa Inc.Product specifications subject to change without notice.Visit our website for the most up-to-date product information.。
威姆科KD7911E型十程序段数字式微机点焊同步控制器使用说明书
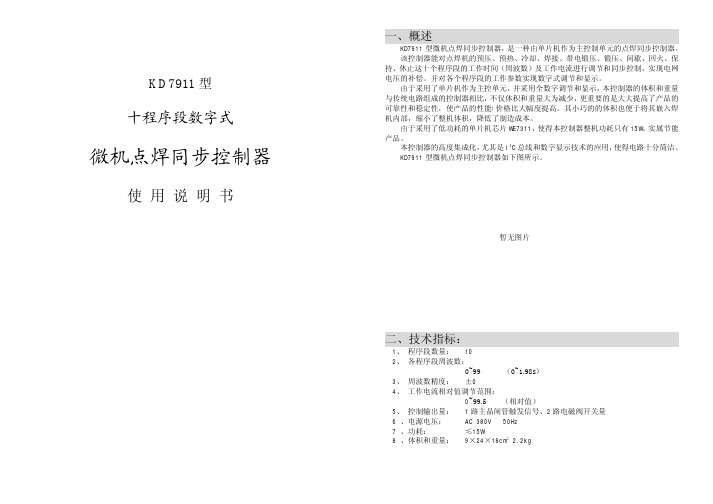
KD7911型十程序段数字式微机点焊同步控制器使用说明书北京威姆科焊接器材有限公司一、概述KD7911型微机点焊同步控制器,是一种由单片机作为主控制单元的点焊同步控制器。
该控制器能对点焊机的预压、预热、冷却、焊接、带电锻压、锻压、间歇、回火、保持、休止这十个程序段的工作时间(周波数)及工作电流进行调节和同步控制,实现电网电压的补偿。
并对各个程序段的工作参数实现数字式调节和显示。
由于采用了单片机作为主控单元,并采用全数字调节和显示,本控制器的体积和重量与传统电路组成的控制器相比,不仅体积和重量大为减少,更重要的是大大提高了产品的可靠性和稳定性,使产品的性能/价格比大幅度提高。
其小巧的的体积也便于将其嵌入焊机内部,缩小了整机体积,降低了制造成本。
由于采用了低功耗的单片机芯片WE7311,使得本控制器整机功耗只有15W。
实属节能产品。
本控制器的高度集成化,尤其是I2C总线和数字显示技术的应用,使得电路十分简洁。
KD7911型微机点焊同步控制器如下图所示。
暂无图片二、技术指标:1、程序段数量: 102、各程序段周波数:0~99 (0~1.98s)3、周波数精度:±04、工作电流相对值调节范围:0~99.5 (相对值)5、控制输出量: 1路主晶闸管触发信号、2路电磁阀开关量6 、电源电压: AC 380V 50Hz7 、功耗:≤15W8 、体积和重量: 9×24×18cm3 2.2kg三、安装方式:KD7911型控制器的外部接线图如上图所示。
机箱后面布置有接线插座。
现将各个插座的功能和接线方式介绍如下:8线航空插座是控制信号输出插座。
其中1、2线输出的是“晶闸管触发”信号,用户可通过与其相适配的插头,将其中一线接至主晶闸管的第二电T2,另一线通过一个200至500欧、20W的电阻与主晶闸管的触发极相连。
该电阻的大小应根据主晶闸管的触发性能确定,应在确保晶闸管可靠触发的前提下尽量选取较大的电阻值,以防止触发极过流。
Blonder Tongue DHDP系列数字高清定义处理器说明书

800-523-6049©2015 Blonder Tongue Laboratories, Inc. All rights reserved. Specifications are subject to change without notice. Trademarks are the property of their respective owner .DHDP SeriesDigital High Definition Processor SeriesStatus Date Document No.Issue No.Author ACTIVEJuly 15, 2015651211000G1KK6264A/6265A Stock No. 6264A/6265A 6261A/6262A USER MANUALModel Stock No.Description DHDC-DV 6264A Downconverter DHDC-UV 6265A UpconverterDHDC-DH 6261A Downconverter-Horizontal DHDC-UH 6262A Upconverter-HorizontalDHDP-V 6266B Vertical Combo Pack (Combo: 6264A + 6265A)DHDC-H6263AHorizontal Combo Pack (Combo: 6261A + 6262A)2DHDPInstruction ManualWARNING: TO PREVENT FIRE OR SHOCK HAZARD, DO NOT EXPOSE THIS UNIT TO RAIN OR MOISTURENOTE TO CATV SYSTEM INSTALLERThis reminder is provided to call the CATV System Installer’s attention to Article 820-40 of the NEC that provides guidelines for proper grounding and, in particular, specifies that the cable ground shall be connected to the grounding system of the building, as close to the point of cable entry as practical.TO REDUCE THE RISK OF ELECTRICAL SHOCK, DO NOT REMOVE COVER FROM THIS UNIT. NO USER-SERVICEABLE PARTS INSIDE. REFER SERVICING TO QUALIFIED SERVICE PERSONNEL.3DHDP Instruction Manual4DHDPInstruction ManualFront Panel1. 2-Digit LED Display — 2 digit LED Channel display2. Up/Down Channel Buttons — Up & down push button controls for setting the channel.3. Enter Button - Button used to enter the displayed channel into memory.4. Up/Down RF Level Buttons — Up & down push button controls for RF level.5. Up/Down Channel Buttons — Up & down push button controls for channel and mode adjustment.6. 2-Digit LED Display — 2 digit LED display for Channel, mode and RF level information.7. Enter Button — Button used to “enter” channel, mode or RF level selection into memory.8. +100 Channel LED Indicator — LED illuminates to indicate CATV channels 100 to 135.Operating Controls and IndicatorsFront Panel ViewsRear Panel ViewsDHDC-DV/DHDHDC-UV/UHRear Panel9. IF Output - “F” Connector 10. IF Input - “F” Connector 11. Power Connector12. RF Input - “F” Connector 13. RF Output - “F” ConnectorDescriptionThe DHDP Series consists of 2 parts, the DHDC-D (Downconverter) and the DHDC-U (Upconverter). The units are intended to operate as a system in order to process digital & high definition television (HDTV) signals.SpecificationsDHDC-D Down ConverterInput Tuning Range (Off-Air 8VSB) (54-216, 470-864 MHz) VHF: CH 2-13, UHF: CH 14-69, CH 70-78 Extended UHF Operating Input Level Range: -20 to +25 dBmV Installation Input Range: -15 to +20 dBmV(any undesired channel < +25 dBmV)Max undesired to desired channel ratio: < +25 dBc Max adjacent to desired channel ratio: < +15 dBc IF Output Level Digital: +30 dBmV*Rejection of Adjacent Analog Channels: -70 dB Typical Power Requirements:110 mA @ +12 VDC, 370 mA @ +5 VDCDHDC-U Up Converter IF Input Level: +30 dBmV Output Frequency Range:Standard CATV, IRC, HRC & Broadcast 54-864 MHz RF Output Level Digital: +45 dBmV*Display Error: ±2 dBOutput Level Adjustment Range: +35 to +45 dBmV Spurious Output (54-864 MHz): -60 dBc Phase Noise @ 10 kHz Offset: -95 dBc/HzBroadband Noise, Out of Channel: -70 dBc (5.5 MHz BW)Power Requirement:310 mA @ +12 VDC, 320 mA @ +5 VDC* Average MeasurementDHDC-UHDHDC-DH5DHDPInstruction Manual Setting Up the Units1. P lace each of the units into the appropriate Blonder Tongue Micromodular chassis by sliding the unit into the retaining rails.a. I t is recommended to physically place one Downconverter and one Upconverter next to oneanother in the chassis.2. Connect the digital or HDTV signal (8VSB format) to the RF ‘F’ connector on the DHDC-D unit.3. Connect the IF ‘F’ connector of the DHDC-D to the IF ‘F’ connector of the DHDC-U.4. Connect the RF ‘F’ connector of the DHDC-U to the appropriate combining device.5. Connect each unit to the power supply using one of the power supply cables.Programming the UnitThe DHDC-D unit is intended to accept any digital UHF or VHF signal and convert it to IF. The DHDC-U unit is intended to accept any digital IF signal and process it to any channel from 54-864 MHz. The unit has 4 valid operating modes, STD CATV, IRC, HRC & Broadcast UHF/VHF. It comes factory set to operate in Standard CATV Mode. If you wish to change the operating mode skip to the Operating Mode Selection section.Programming the DHDC-D1. Navigate to the desired channel number by depressing the CH p UP and q DN buttons.a. P ress and hold the CH p UP or q DN arrow button for fast scrolling.2. Press the ENTER button when you reach the desired channel setting. This will tune the downconverter input to the corresponding frequency for this entry.a. T he LED display will blink continuously during the channel programming process and will not change the channeluntil the ENTER button is depressed.b. T he unit has a special feature that alerts an operator of an inadvertent or desired change to the unit by flashingLED readout. The LED will continue to flash for 30 seconds if the ENTER button is not depressed and if no additional entries are made then the readout will return to the display of the previously programmed channel entry setting.Programming the DHDC-UThe DHDC-U unit comes factory set to operate in the Standard CATV mode. The unit has 4 valid operating modes: STD, CATV, IRC, HRC & Broadcast UHF/VHF (see the operating mode selection section for programming information). Programming a Channel1. Navigate to the desired channel number by depressing the CH p UP and q DN buttons.a. C ontinue past 99 for channels 100-135, the +100 LED will illuminate.b. P ress and hold the CH p UP or q DN arrow button for fast scrolling.2. Press the ENTER button when you reach the desired channel setting. This will tune the upconverter output to the corresponding frequency for this entry.a. T he LED display will blink continuously during the channel programming process and will not change the outputchannel until the ENTER button is depressed.b. T he unit has a special feature that alerts an operator of an inadvertent or desired change to the unit by flashingLED readout. The LED will continue to flash for 30 seconds if the ENTER button is not depressed and if no additional entries are made then the readout will return to the display of the previously programmed channel entry setting.6DHDPInstruction ManualOperating Mode SelectionThe unit has 4 valid operating modes: STD CATV, IRC, HRC & Broadcast UHF/VHF.The DHDC-U unit comes factory set to operate in the Standard CATV mode. To change the operating mode1. S imultaneously depress the RF Level p UP and q DN buttons for approximately 5 seconds.2. The Channel LED display will switch to the operating mode selection.3. Use the RF Level p UP and q DN buttons to select the desired mode: a. C = STD CATV b. H = HRC c. I = IRCd. U = Broadcast (VHF/UHF)4. After selecting the desired mode depress the ENTER button to set the mode.5. The unit will return to the channel display mode. a. P rogramming will reflect the mode chosen – See Appendix for detailed frequency plans. b. T he operating mode will also flash continuously during the mode selection process. The LED display willcontinue to flash for 30 seconds if the ENTER button is not depressed and then will return to the display of the previously programmed channel & mode entry setting. NOTE: THE MODE PRESENTLY IN MEMORY WILL BE DISPLAYED WITHOUT FLASHING DURING THE MODE SELECTION PROCESS.A continuously flashing Channel Display indicates an Error Condition detected by the unit microcontroller.Sample conditions include:• C hannel Selector Entry does not match the channelnumber on which the unit is operating, the display will flash for 30 seconds and then revert back to the previous CH entry • E1 is displayed if the Input VCO is Not Locked • E2 is displayed if the Output VCO is Not LockedThe User should perform the following steps to correct an Error Condition:1. C heck that the Channel Display is set to the desiredchannel & reset as appropriate.2. C heck that the unit is set to the appropriate desiredoperating mode. 3. V erify the unit output on a spectrum analyzer . 4. D isconnect and reconnect power to the unit.If an error condition continues to be displayed, unit should be replaced and serviced.Trouble ShootingCorrection SuggestionProgramming RF Level 1. D epress the RF Level p UP or q DN buttons to increment or decrement the RF output level to the desired setting.a. T he unit has a specified adjustment range of +35 dBmV to +45 dBmV output. The unit software however, will permit entries from +33 to +47 dBmV, the out of range entries of 33-34 & 46-47 dBmV are meant for usage to correct any display error, allowing the unit to be operated in the specified range.It is also recommended to set the output level to +45 dBmV for optimum noise performanceand externally attenuate down to a desired level.corresponding level entry.a. T he LED display readout will also flash continuously during the RF Level programming process. The LED display will continue to flash for 30 seconds if the ENTER button is not depressed and then will return to the display of the previously programmed channel entry setting.Programming the DHDC-U (Continued)7DHDP Instruction ManualVHF Broadcast Channels Channel (MHz) 2 57 3 63 4 69 5 79 6 85 7 177 8 183 9 189 10 195 11 201 12 207 13 213UHF Broadcast Channels Channel (MHz) 14 473 15 479 16 485 17 491 18 497 19 503 20 509 21 515 22 521 23 527 24 533 25 539 26 545 27 551 28 557 29 563 30 569 31 575 32 581 33 587 34 593 35 599 36 605 37 611 38 617 39 623 40 629 41 635 42 641 43 647 44 653 45 659 46 665 47 671 48 677 49 683 50 689 51 695 52 701 53 707 54 713 55 719 56 725 57 731 58 737 59 743 60 749 61 755 62 761 63 767 64 773 65 779 66 785 67 791 68 797 69 803Appendix ADHDC-D Input & DHDC-U OutputCenter FrequenciesAppendix BDHDC-U OutputCenter FrequenciesEIA Standard Incremental Harmonic Chan. CATV (IRC) (HRC) 2 57 57 55.75 3 63 63 61.75 4 69 69 67.75 1 75 73.75 5 79 81 79.75 6 85 87 85.75 95 93 93 91.75 96 99 99 97.75 97 105 105 103.75 98 111 111 109.75 99 117 117 115.75 14 123 123 121.75 15 129 129 127.75 16 135 135 133.75 17 141 141 139.75 18 147 147 145.75 19 153 153 151.75 20 159 159 157.75 21 165 165 163.75 22 171 171 169.75 7 177 177 175.75 8 183 183 181.75 9 189 189 187.75 10 195 195 193.75 11 201 201 199.75 12 207 207 205.75 13 213 213 211.75 23 219 219 217.75 24 225 225 223.75 25 231 231 229.75 26 237 237 235.75 27 243 243 241.75 28 249 249 247.75 29 255 255 253.75 30 261 261 259.75 31 267 267 265.75 32 273 273 271.75 33 279 279 277.75 34 285 285 283.75 35 291 291 289.75 36 297 297 295.75 37 303 303 301.75 38 309 309 307.75 39 315 315 313.75 40 321 321 319.75 41 327 327 325.75 42 333 333 331.75 43 339 339 337.75 44 345 345 343.75 45 351 351 349.75 46 357 357 355.75 47 363 363 361.75 48 369 369 367.75 49 375 375 373.75 50 381 381 379.75 51 387 387 385.75 52 393 393 391.75 53 399 399 397.75 54 405 405 403.75 55 411 411 409.75 56 417 417 415.75 57 423 423 421.75 58 429 429 427.75 59 435 435 433.75 60 441 441 439.75 61 447 447 445.75 62453453451.75EIA Standard Incremental HarmonicChan. CATV (IRC) (HRC) 63459 459 457.75 64 465 465 463.75 65 471 471 469.75 66 477 477 475.75 67 483 483 481.75 68 489 489 487.75 69 495 495 493.75 70 501 501 499.75 71 507 507 505.75 72 513 513 511.75 73 519 519 517.75 74 525 525 523.75 75 531 531 529.75 76 537 537 535.75 77 543 543 541.75 78 549 549 547.75 79 555 555 553.75 80 561 561 559.75 81 567 567 565.75 82 573 573 571.75 83 579 579 577.75 84 585 585 583.75 85 591 591 589.75 86 597 597 595.75 87 603 603 601.75 88 609 609 607.75 89 615 615 613.75 90 621 621 619.75 91 627 627 625.75 92 633 633 631.75 93 639 639 637.75 94 645 645 643.75 100 651 651 649.75 101 657 657 655.75 102 663 663 661.75 103 669 669 667.75 104 675 675 673.75 105 681 681 679.75 106 687 687 685.75 107 693 693 691.75 108 699 699 697.75 109 705 705 703.75 110 711 711 709.75 111 717 717 715.75 112 723 723. 721.75 113 729 729 727.75 114 735 735 733.75 115 741 741 739.75 116 747 747 745.75 117 753 753 751.75 118 759 759 757.75 119 765 765 763.75 120 771 771 769.75 121 777 777 775.75 122 783 783 781.75 123 789 789 787.75 124 795 795 793.75 125 801 801 799.75 126 807 807 805.75 127 813 813 811.75 128 819 819 817.75 129 825 825 823.75 130 831 831 829.75 131 837 837 835.75 132 843 843 841.75 133 849 849 847.75 134 855 855 853.75 135861861859.75One Jake Brown RoadOld Bridge, NJ 08857-1000 USA(800) 523-6049 • (732) 679-4000 • FAX: (732) 679-4353Limited WarrantyBlonder Tongue Laboratories, Inc. (BT) will at its sole option, either repair or replace (with a new or factory reconditioned product, as BT may determine) any product manufactured by BT which proves to be defective in materials or workmanship or fails to meet the specifications which are in effect on the date of shipment or such other specifications as may have been expressly agreed upon in writing (i) for a period of one (1) year from the date of original purchase (or such shorter period of time as may be set forth in the license agreement specific to the particular software being licensed), with respect to iCentral™ (hardware and software) and all other software products (including embedded software) licensed from BT, (ii)) for a period of one (1) year from the date of original purchase, with respect to all MegaPort, IPTV products and fiber optics receivers, transmitters, couplers and integrated receivers/distribution amplifiers (including TRAILBLAZER™, RETRO-LINX™ and TWIN STAR™ products) as well as for VideoCipher® & DigiCipher® satellite receivers, and (iii) for a period of three (3) years from the date of original purchase, with respect to all other BT products. Notwithstanding the foregoing, in some cases, the warranty on certain proprietary sub-assembly modules manufactured by third party vendors and contained in BT products and on certain private-label products manufactured by third parties for resale by BT are of shorter duration or otherwise more limited than the standard BT limited warranty. In such cases, BT’s warranty with respect to such third party proprietary sub-assembly modules and private-label products will be limited to the duration and other terms of such third party vendor’s warranty. In addition, certain products, that are not manufactured but are resold by BT, carry the original OEM warranty for that product. The limited warranty set forth in this paragraph does not apply to any product sold by BT, which at the time of sale constituted a Closeout Product.BT will at its sole option, either repair or replace (with a new or factory reconditioned product, as BT may determine) any product sold by BT which at the time of sale constituted a refurbished or closeout items (“Refurbished Product” and “Closeout Product”), which proves to be defective in materials or workmanship or fails to meet the specifications which are in effect on the date of shipment or such other specifications as may have been expressly agreed upon in writing, for a period of ninety (90) days from the date of original purchase. Notwithstanding the foregoing, in some cases, the warranty on third party software and on certain proprietary sub-assembly modules manufactured by third party vendors and contained in BT products and on certain private-label products manufactured by third parties for resale by BT are of shorter duration or otherwise more limited than the BT limited warranty for Closeout Products. In such cases, BT’s warranty for Closeout Products constituting such third party software, third party proprietary sub-assembly modules and private-label products will be limited to the duration and other terms of such third party vendor’s warranty. In addition, notwithstanding the foregoing, (i) certain Closeout Products that are not manufactured (but are resold) by BT, carry the original OEM warranty for such products, which may be longer or shorter than the BT limited warranty for Refurbished or Closeout Products. All sales of Refurbished or Closeout Products are final.To obtain service under this warranty, the defective product, together with a copy of the sales receipt or other satisfactory proof of purchase and a brief description of the defect, must be shipped freight prepaid to: Blonder Tongue Laboratories, Inc., One Jake Brown Road, Old Bridge, New Jersey 08857.This warranty does not cover damage resulting from (i) use or installation other than in strict accordance with manufacturer’s written instructions, (ii) disassembly or repair by someone other than the manufacturer or a manufacturer-authorized repair center, (iii) misuse, misapplication or abuse, (iv) alteration, (v) lack of reasonable care or (vi) wind, ice, snow, rain, lightning, or any other weather conditions or acts of God.OTHER THAN THE WARRANTIES SET FORTH ABOVE, BT MAKES NO OTHER WARRANTIES OR REPRESENTATIONS OF ANY KIND, EXPRESS OR IMPLIED, AS TO THE CONDITION, DESCRIPTION, FITNESS FOR A PARTICULAR PURPOSE, MER-CHANTABILITY OR AS TO ANY OTHER MATTER, AND SUCH WARRANTIES SUPERSEDE ANY ORAL OR WRITTEN WAR-RANTIES OR REPRESENTATIONS MADE OR IMPLIED BY BT OR BY ANY OF BT’S EMPLOYEES OR REPRESENTATIVES, OR IN ANY OF BT’S BROCHURES, MANUALS, CATALOGS, LITERATURE OR OTHER MATERIALS. IN ALL CASES, BUYER’S SOLE AND EXCLUSIVE REMEDY AND BT’S SOLE OBLIGATION FOR ANY BREACH OF THE WARRANTIES CONTAINED HEREIN SHALL BE LIMITED TO THE REPAIR OR REPLACEMENT OF THE DEFECTIVE PRODUCT F.O.B. SHIPPING POINT, AS BT IN ITS SOLE DISCRETION SHALL DETERMINE. BT SHALL IN NO EVENT AND UNDER NO CIRCUMSTANCES BE LIABLE OR RESPONSIBLE FOR ANY CONSEQUENTIAL, INDIRECT, INCIDENTAL, PUNITIVE, DIRECT OR SPECIAL DAMAGES BASED UPON BREACH OF WARRANTY, BREACH OF CONTRACT, NEGLIGENCE, STRICT TORT LIABILITY OR OTHERWISE OR ANY OTHER LEGAL THEORY ARISING DIRECTLY OR INDIRECTLY FROM THE SALE, USE, INSTALLATION OR FAILURE OF ANY PRODUCT ACQUIRED BY BUYER FROM BT.All claims for shortages, defects and non-conforming goods must be made by Buyer in writing within five (5) days of receipt of merchandise, which writing shall state with particularity all material facts, concerning the claim then known to Buyer. Upon any such complaint, Buyer shall hold the goods complained of intact and duly protected, for a period of up to sixty (60) days. Upon the request of BT, Buyer shall ship such allegedly nonconforming or defective goods, freight prepaid to BT for examination by BT’s inspection department and verification of the defect. BT, at its option, will either repair, replace or issue a credit for products determined to be defective. BT’s liability and responsibility for defective products is specifically limited to the defective item or to credit towards the original billing. All such replacements by BT shall be made free of charge f.o.b. the delivery point called for in the original order. Products for which replacement has been made under the provisions of this clause shall become the property of BT. Under no circumstances are products to be returned to BT without BT’s prior written authorization. BT reserves the right to scrap any unauthorized returns on a no-credit basis. Any actions for breach of this contract must be commenced by Buyer within thirteen (13) months after the cause of action has accrued. A copy of BT’s standard terms and conditions of sale, including the limited warranty, is available from BT upon request. Copies of the limited warranties covering third party proprietary sub-assembly modules and private label products manufactured by third parties are also available from BT on request. VideoCipher® & DigiCipher® are registered trademarks of Motorola Corp.。
MOOG伺服阀资料大全

J761-004 RT7625M-004 G50SD4V3D4PN D765-1603-5 S38JOGMGUSXO RT7625E-1603-5 K38SM5N5B6B15G D765-1089-4 S63JOGAEVSXO RT7625E-1089-4 K63SF4V5B6B15G D631-335B H60FOFMANBR RT6215E-335B H60SM4N2B4BP D630Z067A/D663Z4307K H20J0GAEVBL RT7613M-Z067A K20SF4V3C4AJN D630-072A/D662Z4311K S10JOGAEVBL RT7613M-072A D630-272D/D662Z4336K S10JOGAEVBL RT7613M-272D D761-2617/D791-4002 H19J0GAEVAL RT7625M-2617 K19SM4V3C4AJN MOOG 伺服阀 D761-2612/D791-5009 H19J0GBEVAL RT7625M-2612 K19SM4V3C4AJN D761-2619/D791-4028 H10J0GAEVAL RT7625M-2619 K10SM4V3C4AJN D061-8411/D662-4010 J15HOBA4VB1 RT6111-8411 JJCFV1D4A D061-8412/D663-4007 J15HOBB4VB1 RT6111-8412 JJCFV1D4A D633-333B R16KO1F0NSS RT6314E-333B L40SX4NT1D6BYA 072-559A S15F0FA4VBL RT7626M-559A G160SF4V3D4AN 072-558A S22FOFA4VBL RT7626M-558A G228SF4V3D4AN RT7626M-SQ G761-3001 H04JOFM4VPL RT7625M-3001 K4SM4V3D4PN G761-3002/RT7625M-3002 G761-3003 H19JOFM4VPL MOOG 伺服阀 G761-3004 H38JOFM4VPL RT7625M-3004 K38SM4V3D4PN G761-3005 S63JOGM4VPL RT7625M-3005 K63SM4V3D4PN D661 D664Z4306K D663Z4305K E062 D662 M040 G2L20G422-615 G3L15G423-416 G3L25G423-612 D634 D634-521P40KA2M0NSM2 G122 D NE122 E128 BG040 G040-125-001 G123 G123-815A001 G631 G631-3006D D635Z681EP16XX1AORSS2M D691Z2086GQ80XUAAAVVS2N D631-335CF-4 D631 N122-001 D791Z106AS16JPNAFU680 60-302 60-304 6005GB3NM 6040GA3NM 60A0218 60A023H 60A203G 60A203H 60B-053H 60B021H 60B023H 60B053H 60B103H 61-601A 61-603C 62-100 62-300 62-321 62-500 62-600 62-104 62-105 62-106 62-107 62-108 62-109 62-110 62-112 MOOG 伺服阀 62-114 62-115 62-117 62-118 62-119 62-119NC 62-120 62-129 62-136 62-140 62-148 62-153 62-185 62-191 62-191C 62-1NC 62-206 62-229 62-303 62-303B D630-053AH020HB200VE RT7625M-3003 K19SM4V3D4PN AEMRT10-2-40 0061-201 0062-191 010-225-44 010-60298-C 062-314A 062-321 065302HG200F 071-60299 071-60707 07160177 072-162 072-163C 078-130C 100-2371-1 100-58953 10058953 115 -129 130A151 133-102 16-101B 17-136E 17-136F 17136F 17136G 17340B 1EK2931V3010002510001500 2057A 2057B 208A-502-1 215A-310 215A-311 2163A MOOG 伺服阀 2164A 22-131A 22-132 22-132A 22-148A 23720-1 240-530-2 29509351 30-156 47659-001 50-009B 60 SERIES 60-122 60-270A 60-272A 60-274A 60-275 60-275A 62-306 62-307 62-307A 62-321 62-408 62-428 62-500 62-500B 62-501 62-501B 62-502 62-502B 62-508 62-508B 62-512 62-512B 62-523B 62-600 62-600B 62-60530-326A 30326A 305-131A 31-111 31-154 31-185A 31-297D 31-304 31-306 31-393 31410C 31-436 31S020 31X393 32-01501 32-195 32-229A 33-153 43586-AM-7 MOOG 公司的运动控制技术广泛应用于民用机座舱、发电风机、一级方程式赛车、医用输 液系统等众多的市场和应用领域, 有效提高相关产品的性能。 我们的文化为本公司的人才提 供有力支持,使他们在工作时干劲十足,满怀激情,并且对未来的成功充满希望。本公司历 史起源于公司创建者威廉 C 穆格,他是一位发明家、企业家,也是一位远见卓识者。 美国 MOOG 伺服阀、MOOG 阀、MOOG 液压泵、MOOG 电液伺服阀、MOOG 比例阀、
MOOG_D636_D638_operatinG_instructions
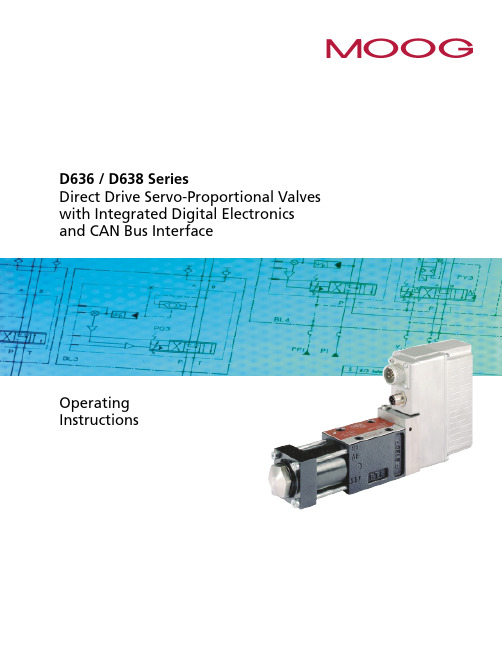
D636 / D638 SeriesDirect Drive Servo-Proportional Valves with Integrated Digital Electronics and CAN Bus InterfaceOperatingInstructions© 2002 Moog Industrial Controls DivisionMoog Inc., East Aurora, NY 14052-0018Telephone: 716/655-3000, Fax: 716/655-1803, Toll Free: 1-800-272-MOOGAll rights reserved. No part of these operating instructions may be reproduced in any form (print, photocop-ies, microfilm, or by any other means) or edited, duplicated, or distributed with electronic systems without the prior written consent of Moog.Exclusion of LiabilityThese operating instructions were prepared with the greatest possible care and the contents generated ac-cording to the best of the authors' knowledge. However, the possibility of error cannot be prevented and im-provements may be possible. We would be pleased to receive your comments about possible errors or in-complete information.Nevertheless, Moog does not offer any guarantee that the contents conform with applicable legal regula-tions, nor does Moog accept any liability for possible remaining incorrect or incomplete information and the consequences thereof.Changes are possible at any time without prior notice.Part number of the D636 / D638 operating instructionsPlease contact us at the above address and indicate the following part number when ordering these operat-ing instructions:CDS6818TrademarksNote:All product designations mentioned in these operating instructions are trademarks of the respective manufacturers. The absence of the trademark symbols ® or ™ does not indicate that the name is free from trademark protection.Table of Contents1General Information (1)1.1Using the Operating Instructions (1)1.2Proper Use (1)1.3Selection and Qualification of Personnel (1)1.4Electromagnetic Compatibility (EMC) (2)1.5Guarantee and Liability (2)1.6Explanation of Symbols (2)1.7Abbreviations (3)2Safety Instructions (5)3Function and Operational Characteristics of the Servo-Proportional Valves (7)3.1General Information (7)3.1.1Representative Depiction of a Direct Drive Valve (8)3.1.2Permanent Magnet Linear Force Motor (8)3.2Servo-proportional Valve Operational Modes (9)3.2.1Flow Control (Q-Control) (9)3.2.2Pressure Control (p-Control) (9)3.2.3Flow Control and Pressure Control (pQ-Control) (optional for D638) (9)3.2.4Notes on Controller Behavior (10)3.3CAN Bus and CANopen (10)3.4Analog Command Inputs (11)3.4.1Flow Command Input ±10 V Floating (12)3.4.2Flow Command Input ±10 mA Floating (12)3.4.3Flow Command Input ±10 mA Single-Ended (13)3.4.4Flow Command Input 4–20 mA Floating (13)3.4.5Flow Command Input 4–20 mA Single-Ended (14)3.4.6Pressure Command Input 0–10 V Floating (D638) (14)3.4.7Pressure Command Input 0–10 mA Floating (D638) (15)3.4.8Pressure Command Input 0–10 mA Single-Ended (D638) (15)3.4.9Pressure Command Input 4–20 mA Floating (D638) (16)3.4.10Pressure Command Input 4–20 mA Single-Ended (D638) (16)3.5Analog Actual Value Outputs (17)3.5.1Actual Flow Value Output 4–20 mA (17)3.5.2Actual Pressure Output 4–20 mA (D638) (17)3.5.3Evaluation of the 4–20 mA Actual Value Output (17)3.6Digital Inputs/Outputs (18)3.6.1Enable Input (optional) (18)3.6.2Digital Outputs (18)3.7Status Display (18)3.7.1Module Status LED (MS) (18)3.7.2Network Status LED (NS) (19)4Technical Data and Scope of Delivery (21)4.1General Technical Data (21)4.2Hydraulic Data (22)4.2.1Servo-Proportional Valve Configurations (23)4.2.2Leakage Port Y (24)4.3Electrical Data (24)4.4Characteristic Curves (25)4.4.1Step Response, Frequency Response, and Flow Diagram (25)4.4.2Flow Characteristic Curve (26)4.4.3Pressure Characteristic Curves (26)4.5Dimensions (Installation Drawing) (27)4.6Mounting Pattern and Mounting Surface (27)4.7Scope of Delivery (28)5Transport and Storage (29)5.1Packaging/Transport (29)5.2Storage (29)6Mounting/Removing and Connection to the Hydraulic System (31)6.1Mounting the Servo-Proportional Valve (32)6.2Removing the Servo-Proportional Valve (33)7Electrical Connection (35)7.1Pin Assignment (36)7.1.1Valve Connector (36)7.1.2CAN Connector (37)7.2Wiring CAN Networks (38)7.2.1Cable Lengths and Cable Cross Sections in CAN Networks (39)7.2.2Suitable Cable Types (40)8Starting-Up the Servo-Proportional Valve (41)8.1Filling and Flushing the Hydraulic System (42)8.2Venting (D638) and Starting-Up the Hydraulic System (43)8.3Connection to the CAN Bus (43)9Maintenance and Repair (45)10Trouble Shooting (47)11Tools, Replacement Parts, and Accessories (49)11.1Tools for 6+PE Pin Connectors (49)11.2Replacement Parts and Accessories D636 / D638 (49)12Appendix (51)12.1Additional Literature (51)12.2Quoted Standards (51)12.3Addresses (52)13Index (53)For your notes.1 General Information Using the Operating Instructions 1 GeneralInformation1.1 Using the Operating InstructionsThese operating instructions apply only to Direct Drive Valve series D636 (flow control valves) and D638 (pressure control valves) with integrated digital electronics and CAN bus interface. The instructions contain the most important information for ensuring safe operation of servo-proportional valves.The operating instructions must be stored near the servo-proportional valve or the upper level machine so that they are readily accessible at all times.All persons responsible for mechanical planning, assembly, and operation must read, understand, and follow all points contained in these operating in-structions. This requirement applies especially to the safety instructions. Complying with the safety instructions helps to avoid accidents, problems, and errors.It is absolutely essential for the user to know the safety instructions as well as nationally and internationally applicable safety regulations in order to handle the servo-proportional valve safely and operate it trouble-free.1.2 Proper UseD636 and D638 Direct Drive Valves are always operated as a component of a complete upper level system, for example in a machine.They must be used only as control elements to control flow and/or pressure in hydraulic circuits that regulate position, speed, pressure, and power. The valves are intended for use with mineral oil-based hydraulic oils. The use of other media must be approved by Moog.Use for other purposes or for purposes that extend beyond this description is not allowable.Operation is allowable only in industrial environments in accordance with the DIN EN 50081-2 standard.Operation in potentially explosive areas is not allowable.Proper use also includes observation of the operating instructions and com-pliance with the inspection and maintenance regulations.1.3 Selection and Qualification of PersonnelOnly properly trained and instructed personnel with the necessary knowl-edge and experience must work with and on servo-proportional ing the operating instructionsProper useSelection and qualifica-tion of personnel1 General Information Electromagnetic Compatibility (EMC) 1.4 Electromagnetic Compatibility (EMC)The D636 and D638 servo-proportional valves comply with the following standards:DIN EN 50081-2Electromagnetic compatibility (EMC) - Generic emis-sion standard - Part 2: Industrial environment DIN EN 61000-6-2Electromagnetic compatibility (EMC) - Part 6-2: Ge-neric standards - Immunity for industrial environ-mentsDIN EN 55011Industrial, scientific and medical (ISM) radio-fre-quency equipment - Radio disturbance characteris-tics - Limits and methods of measurementsThe D636 and D638 servo-proportional valves must not be used in residen-tial, commercial and light industry as defined by the DIN EN 50081-1 and DIN EN 50082-1 standards.1.5 Guarantee and LiabilityIn general, our "General Terms and Conditions for Sales" apply. These con-ditions are given to the operator upon contract closure.Among other things, guarantee and liability claims for personal and property damages will not be considered if they are caused by one or more of the following:•Improper use of the servo-proportional valve•Improper mounting, start-up, and maintenance of the servo-propor-tional valve•Improper handling of the servo-proportional valve, such as the use in a potentially explosive, excessively hot, or excessively cold envi-ronment•Failure to follow the operating instructions regarding transport, stor-age, mounting, start-up, and maintenance of the servo-proportionalvalve•Unauthorized structural changes to the servo-proportional valve •Improperly performed repairs•Disasters caused by foreign objects or force majeure1.6 Explanation of SymbolsThe following symbols are used in these operating instructionsImportant informationDanger of damage to machine or materialGeneral danger of injury and deathSpecific danger of injury and deathRegulatory symbols Electromagnetic compatibility (EMC) Guarantee and liabilitySymbols used1.7 AbbreviationsAbbreviations used The following abbreviations are used in these operating instructions:Symbol for filter finenessXSymbol for viscosityµP MicroprocessorCAN C ontroller A rea N etworkCiA C AN i n A utomation user's associationDDV D irect D rive V alveDIN D eutsches I nstitut für N ormung e. V.(German Institute for Standardization)DS D raft S tandard (published by CiA)DSP D raft S tandard P roposal (published by CiA)DSP D igital S ignal P rocessorEMC E lectro m agnetic C ompatibilityEMI E lectro m agnetic I nterferenceEN E uropa-N orm (European standard)FPM Fluorocarbon rubberF.S.F ull S cale output of transducerGND G rou nd (signal ground)ID Id entifierID I nner D iameter (of O-rings for example)ISO I nternational S tandardizing O rganizationLED L ight E mitting D iodeLSS L ayer S etting S ervicesLVDT L inear V ariable D ifferential T ransformer(senses the position of the spool in the valve [position transducer])MS M odule S tatus LEDNAS N ational A merican S tandardNBR N itril B utadiene R ubber (Perbunan, Buna)NS N etwork S tatus LEDp Symbol for p ressurePC P ersonal C omputerPE P rotective E arthPWM P ulse W idth M odulationQ Symbol for volumetric flowVDMA V erband D eutscher M aschinen- und A nlagenbau e. V.(German Machinery and Plant Manufacturers' Association)For your notes.2 SafetyInstructionsSafety instructions The D636 and D638 servo-proportional valves must only be put intooperation and used as described in these operating instructions.They must be operated only as a component of a complete upperlevel system, for example a machine, and only in industrial environ-ments as defined by the DIN EN 50081-2 standard.The D636 and D638 servo-proportional valves must not be used inresidential, commercial and light industry as defined by the DIN EN50081-1 and DIN EN 50082-1 standards.Operation in potentially explosive areas is not allowable.During equipment planning and the use of servo-proportional valves,the safety and accident prevention regulations specific to the type ofusage must be followed. These include, for example:DIN EN 292Safety of machinery - Basic concepts, generalprinciples for designDIN EN 982Safety of machinery - Safety requirements forfluid power systems and their components -HydraulicsDIN EN 60204Safety of machinery - Electrical equipment ofmachinesThe manufacturer and the operator of the complete upper levelsystem (mechanical equipment, for example) are responsible forcompliance with the national and international safety and accidentprevention regulations that apply to each particular case.Modifying, changing, and interfering in the internal area of the servo-proportional valve may cause serious injuries and as such is forbid-den.Only properly trained and instructed personnel with the necessaryknowledge and experience must work with and on servo-proportion-al valves.The servo-proportional valves must only be mounted and removed,and electrical and hydraulic connections made by suitably trainedtechnical personnel with the necessary authorization. They mustperform such tasks in accordance with the applicable regulationsand the valve must be in an idle and depressurized state and themachine switched off.While this work is in progress, the machine must be securedagainst restarting, for example by:•Locking the main command device and removing the keyand/or•attaching a warning sign to the main switchOperating machines with leaking servo-proportional valves or aleaking hydraulic system is dangerous and not allowed.When starting-up a servo-proportional valve on a field bus for the first time, we recommend operating the valve in a depressurized state.The servo-proportional valve must only be operated via the configu-ration software if doing so does not endanger the machine and its immediate surroundings.The configuration software must not be operated on a CAN bus if CAN communication is still running.If the valve cannot be operated safely via the configuration software even when the CAN communication is switched off, it must only communicate via a direct (i.e. point-to-point) connection with the configuration software. The valve must be depressurized for this purpose.(To create a direct connection between the configuration software and the valve, unplug the CAN bus cable from the valve and con-nect the valve directly to the PC's CAN bus interface card.) Hydraulic oil can cause serious injuries, burns, and fires if it squirts out under high pressure.Before mounting or removing servo-proportional valves, all pressure lines and reservoirs in the hydraulic circuit must therefore be de-pressurized.Servo-proportional valves and hydraulic connection lines may be-come very hot while in operation.When mounting, removing, or servicing servo-proportional valves,always wear suitable protective equipment such as work gloves.When handling hydraulic fluids, always follow the safety guidelinesapplicable to the product.The instructions in these operating instructions, especially chapter 2(starting on page 5) and chapter 9 (starting on page 45) must beadded to the operating instructions of the complete upper level sys-tem.The allowable environmental conditions (see chapter 4, page 21)must be maintained at all times.Do not transport or store the servo-proportional valves without firstproperly installing the shipping plate.To avoid overheating the servo-proportional valve, mount it in a waythat ensures good ventilation.Do not mount valves directly onto mechanical parts that are subjectto strong vibrations or sudden movement.When mounted on units subject to sudden movement, the spool di-rection should not be the same as the unit's direction of movement.The servo-proportional valves must not be immersed in liquid.Safety instructions3 Function and Operational Characteris-tics of the Servo-Proportional Valves 3.1 General InformationThe D636 valves (flow control valves) and the D638 valves (pressure control valves) are Direct Drive Valves (DDV). The valves are throttle valves for 3-, 2-, 4-, 2x2-way applications and are suitable for electro-hydraulic control of po-sition, speed, pressure, and power - even under high dynamic requirements.A permanent magnet linear force motor is used to drive the spool. In contrast to proportional magnet drives, the linear force motor adjusts the spool in both working directions from the spring-loaded middle position. This gives the servo-proportional valve strong actuating power for the spool as well as good static and dynamic characteristics.The following operational modes are possible:•Flow control (Q-control) (D636)(see chapter 3.2.1, page 9)•Pressure control (p-control) (D638)(see chapter 3.2.2, page 9)•Flow control and pressure control (pQ-control) (optional for D638) (see chapter 3.2.3, page 9)The digital driver and control electronics are integrated into the valve. The valve electronics contain a microprocessor system which performs all im-portant functions via the valve software it contains. The digital electronics enable the valve to be controlled across the entire working range without drift and almost regardless of the temperature.The valves are parameterized, activated, and monitored via the built-in CAN bus interface in accordance with the CiA standard DSP 408 (device profile fluid power technology).In addition, up to two analog command inputs and up to two analog actual value outputs with programmable functions are available as options. Benefits of using D636 / D638 Direct Drive Valves:•Direct drive with permanent magnet linear force motor that provides high actuating power•Pilot oil not required•Pressure independent dynamics•Minimal hysteresis and high response characteristics•Minimal current requirement at and close to hydraulic null(hydraulic null is the position of the spool at which the pressures of asymmetrical spool are equally high in both blocked working ports)•Standardized spool position signal•Electrical null point adjustment is parameterizable•If the electrical supply fails, a line breaks, or emergency stop is activated, the spool returns to the predefined spring-loadedposition without overshooting a working position (fail-safe).•Flow control and optional pressure control (on D638) with only one valve•CAN bus interface•optional analog inputs and outputs Function of the servo-proportional valves: throttle valves Operational modes:Q-, p-, pQ-control Digital valve electronics CAN bus interface Benefits of the D636/D638 series3.1.1 Representative Depiction of a Direct Drive ValveFigure 1: Representative depiction of the servo-proportional valve3.1.2 Permanent Magnet Linear Force MotorFigure 2: Representative depiction of the permanent magnet linear force motorThe permanent magnet linear force motor is a permanently magnetically ex-cited differential motor. A portion of the magnetic force is already integrated with the permanent magnet. This makes the linear force motor's power re-quirement considerably lower than that of comparable proportional magnets. The linear force motor drives the spool of the servo-proportional valve. In the zero current condition, the centering springs determine the starting position of the spool. The linear force motor enables the spool to be guided in both directions from the starting position, the linear force motor's actuating power being proportional to the coil current. The strong forces from the linear force motor and the centering springs enable precise movement of the spool, even when working against flow and frictional forces.3.2 Servo-proportional Valve Operational Modes3.2.1 Flow Control (Q-Control)During this operating mode the spool position is controlled. The predefined command signal corresponds to a particular spool position. The spool posi-tion is proportional to the electrical signal.The command signal (spool position command) is fed to the valve electron-ics. A position transducer (LVDT) measures the spool's actual position and forwards this information to the valve electronics. The electronics compares the actual spool position and command signal and generates a current to drive the linear force motor, which then brings the spool into the correct po-sition.The position command can be influenced with parameters in the valve soft-ware (for example: linearization, ramping, dead band, sectionally defined amplification, etc.).3.2.2 Pressure Control (p-Control)During this operating mode of the D638 valve the pressure in port A is con-trolled. The predefined command signal corresponds to a particular pressure in port A.The command signal (pressure command in port A) is transmitted to the valve electronics. A pressure transducer measures the pressure in port A and feeds this to the valve electronics. The electronics compares the actual pressure signal and command signal and generates a current to drive the linear force motor, which then brings the spool into the correct position.The pressure control function can be influenced with parameters in the valve software (for example: linearization, ramping, dead band, sectionally defined amplification, etc.). The pressure regulator is carried out as an extended PID controller. In the valve software, you can set the parameters of the PID con-troller.3.2.3 Flow Control and Pressure Control (pQ-Control)(optional for D638)This is a combination of flow and pressure control for which both command signals (external flow and pressure limit command) must be present.The following are examples of possible combinations:•Flow control with pressure limiting control•forced changeover from one operating mode to the other Permanent magnet linear force motorQ-Control: Controlling the spool positionp-control: Controlling the pressure in port A pQ-control3.2.4 Notes on Controller BehaviorThe resulting flow depends not only on the position of the spool, but also onthe pressure drop ∆p on the individual control edges.At 100 % flow command signal with a rated pressure drop ∆p N of 35 bar(500 psi) per control edge, the result is the rated flow Q N . By altering thepressure drop, the flow Q also changes assuming a constant command sig-nal, as shown by the following formula:N Np p Q Q ∆∆=Q [l/min]=actual flowQ N [l/min]=rated flow ∆p [bar]=actual pressure drop per control edge∆p N [bar]=rated pressure drop per control edge The following exert significant influence on the controlled system:• Rated flow Q N• Actual pressure drop ∆p per control edge• Load stiffness• Control volume being regulated by port A (D638 only)Depending on differences in mechanical construction (such as volume,pipework, branching, reservoirs, etc.), different types of controller optimiza-tions may be required in pressure control. These controller optimizations canbe carried out with the configuration software via the CAN bus interface.3.3 CAN Bus and CANopenThe servo-proportional valve is equipped with a CAN bus interface and canbe operated within a CAN network.The CAN bus is a differential 2-wire bus and was initially developed to facili-tate rapid and interference-free networking of components in automobiles.But thanks to its many advantages and high level of reliability, the CAN busis also suitable for applications within machines and has proven its useful-ness as a widely accepted standard.CANopen is a standardized communication profile for simple networking ofCANopen-compatible devices from many different manufacturers.The communication profile complies with the DS 301 standard, version 4.0,and is provided by CiA.The CANopen standard defines various device profiles to enable connectionof different types of devices, including for example: drives, controllers, angletransmitters, etc.The function of the D636 and D638 series valves corresponds to the deviceprofile for proportional servo valves in accordance with the CiA standardDSP 408. This device profile is based on a profile established by a workinggroup within the VDMA entitled "Device Profile Fluid Power Technology".Formula for calculating the flow QCAN bus interface CANopen communica-tion profile (CiA stand-ard DS 301, version 4.0)Device profile for pro-portional servo valves (CiA standard DSP 408)The machine controller or other CAN bus nodes can use the CAN bus to ex-change data with the servo-proportional valve in real time. This data includes command signals and actual values as well as control and status reports. In addition to this real time transmission, configuration and parametric data can be exchanged between the controller and the valve at any time.The controller or other CAN bus nodes transmit command signals, device control commands, and configuration data via the CAN bus to the servo-pro-portional valve.The controller or other CAN bus nodes can read actual values, status infor-mation, and the current configuration from the servo-proportional valve.The integrated valve electronics can take over device-specific and drive-specific functions like command signal ramping or dead band compensation. This can relieve the external controller and the CAN communication because external controllers previously had to perform these functions themselves and the interpolated intermediate values had to be transmitted via the CAN bus.Monitoring, error recognition, and diagnostic functions enable recognition of device malfunctions via the CAN bus.3.4 Analog Command InputsDepending on the valve model, various analog command inputs for flow control and/or pressure control are available. (Pin assignment of the valve connector: see Table 6, page 36)Command input Benefits±10 V or 0-10 V Simple measurement of the signal with an oscillo-scope, for example±10 mA or 0-10 mA In contrast to the 4–20 mA command input, less power is required at low command signals; large transmissionlengths are possible4–20 mA Line break monitoring and large transmission lengthspossibleTable 1: Available Analog command inputsAll current inputs are available as floating or single-ended versions.All voltage inputs are floating, but can be connected externally assingle-ended inputs.Integrated valveelectronicsMonitoring, errorrecognition, anddiagnostic functionsAnalog commandinputs3.4.1Flow Command Input ±10 V FloatingFigure 3: Flow command input ±10 V floating (circuit and characteristic curve)The spool stroke is proportional to the input voltage U in .U in = +10 V100 % valve opening P ð A and B ð T U in = 0 VSpool in hydraulic null position U in = -10 V 100 % valve opening P ð B and A ð TThis command input is a floating, differential input. (The potential differ-ence of each input to GND must be between -15 V and +32 V.) If differ-ential voltage is not available, one input pin has to be connected to sig-nal ground according to the required operating direction.3.4.2Flow Command Input ±10 mA FloatingFigure 4: Flow command input ±10 mA floating (circuit and characteristic curve)The spool stroke is proportional to the input current I in .I in = +10 mA100 % valve opening P ð A and B ð T I in = 0 mASpool in hydraulic null position I in = -10 mA 100 % valve opening P ð B and A ð TThe input current I in must be between -25 mA and +25 mA!This command input is a floating input. (The potential difference of eachinput to GND must be between -15 V and +32 V.) If a floating currentsource is not available, one input pin has to be connected to signalground according to the required operating direction.Flow command input±10 V floatingFlow command input±10 mA floatingFigure 5: Flow command input ±10 mA single-ended (circuit and characteristic curve)The spool stroke is proportional to the input current I in .I in = +10 mA100 % valve opening P ð A and B ð T I in = 0 mASpool in hydraulic null position I in = -10 mA 100 % valve opening P ð B and A ð T The point of reference for this command input is GND.The input current I inmust be between -25 mA and +25 mA!Depending on the required operating direction, one of the two input pinsmust not be connected.3.4.4Flow Command Input 4–20 mA FloatingFigure 6: Flow command input 4–20 mA floating (circuit and characteristic curve)The spool stroke is proportional to the input current I in .I in = 20 mA100 % valve opening P ð A and B ð T I in = 12 mASpool in hydraulic null position I in = 4 mA 100 % valve opening P ð B and A ð TThe input current I in must be between -25 mA and +25 mA!This command input is a floating input. (The potential difference of eachinput to GND must be between -15 V and +32 V.) If a floating currentsource is not available, one input pin has to be connected to signalground according to the required operating direction.Command signals I in < 3 mA (due to line break, for example) indicate anerror during flow control. The valve is switched off for safety reasonsand goes into fail-safe position.Flow command input4–20 mA floating。
AK79G Tube 主板 线上手册
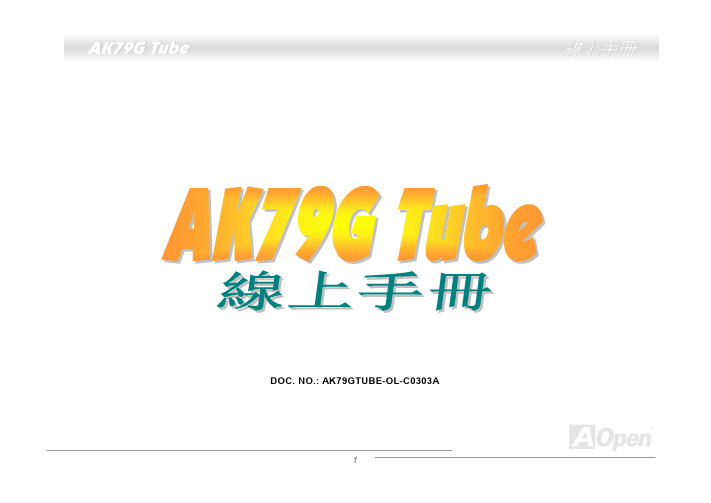
DOC. NO.: AK79GTUBE-OL-C0303AAK79G Tube (1)手冊內容簡介 (2)版權聲明 (8)使用須知 (9)前言 (10)功能特色 (11)快速安裝步驟 (15)主機板說明圖 (16)系統方塊圖 (17)硬體安裝 (18)關於“用戶選配” 及“製造商選配” (19)JP14清除CMOS資料 (20)安裝CPU (21)AOpen Overheat Protection (O.H.P.) 過熱保護技術 (23)CPU免跳線設計 (24)建碁“看門狗ABS”計時器 (25)CPU與機殼之散熱風扇接頭 (28)JP28 鍵盤/滑鼠喚醒功能跳線 (29)記憶體插槽 (30)STBY LED (待機指示燈) (32)Front Panel前面板接頭 (33)ATX電源接頭 (34)斷電自動回復 (34)及軟碟機接頭 (35)真空管電源開關 (38)接頭 (39)5.1聲道音效 (40) (41)紅外線接頭 (42)保護技術及AGP LED指示燈 (44)內建10/100 Mbps區域網路 (45) (46) (48)接頭 (49)接頭 (51) (52)CD音源接頭 (53)AUX外部音源輸入接頭 (54)前音源接頭 (55)免電池長壽命設計 (56)CPU過電流保護裝置 (57) (58) (61)2200μF低內阻 (Low ESR) 電解電容 (62) (63)技術 (68)---- SilentTek (69)72 (76)紅利包光碟片 (76)NVIDIA nForce驅動程式 (77)NVIDIA Windows 98/ME/2000/XP顯示卡驅動程式 (78)在現有的Windows XP系統中安裝USB2.0驅動程式 (79)在現有的Windows 98/ME/2000系統中安裝USB2.0驅動程式 (80)Phoenix Award BIOS (81)如何使用Phoenix-Award™ BIOS設定程式 (82)BIOS設定選單 (84)Windows環境下進行BIOS升級 (87) (89)AC97 CODEC (89)ACPI (Advanced Configuration & Power Interface, 先進規格與電源管理界面) (89)ACR (Advanced Communication Riser, 先進通訊升級卡) (89)AGP (Accelerated Graphic Port, 影像加速處理埠) (89)AMR (Audio/Modem Riser, 音效/數據升級卡) (90)ATA (AT Attachment, ATA介面) (90)BIOS (Basic Input/Output System, 基本輸出/輸入系統) (91)Bluetooth (藍牙) (91)CNR (Communication and Networking Riser, 網路通訊擴接卡) (91)DDR (Double Data Rate, 雙倍資料記憶體) RAM (91)ECC (Error Checking and Correction, 錯誤檢查與修正) (92)EEPROM (Electronic Erasable Programmable ROM, 可程式電子抹寫唯讀記憶體) (92)EPROM (Erasable Programmable ROM, 可抹寫式唯讀記憶體) (92)EV6 匯流排 (93)FCC DoC (Declaration of Conformity, 聯邦電信委員會電磁干擾認證) (93)FC-PGA (Flip Chip-Pin Grid Array, 覆晶片塑膠柵狀陣列封裝) (93)FC-PGA2 (Flip Chip-Pin Grid Array, 覆晶片塑膠柵狀陣列封裝) (93)Flash ROM (快閃記憶體) (93)Hyper Threading (高速執行緒) (94)IEEE 1394 (94)Parity Bit (奇偶同位檢查) (94)PCI (Peripheral Component Interface, 周邊元件介面) 匯流排 (95)PDF 格式 (95)PnP (Plug and Play, 隨插即用) (95)POST (Power-On Self Test, 開機自我測試) (95)PSB (Processor System Bus, 處理器系統匯流排) 時脈 (95)RDRAM (Rambus Dynamic Random Access Memory, 動態隨機存取記憶體) (96)RIMM (Rambus Inline Memory Module, Rambus記憶體模組) (96)SDRAM (Synchronous DRAM, 同步動態隨機存取記憶體) (96)SATA (Serial ATA, 序列式ATA) (96)SMBus (System Management Bus, 系統管理匯流排) (97)SPD (Serial Presence Detect) (97)USB 2.0 (Universal Serial Bus, 通用序列匯流排) (97)VCM (Virtual Channel Memory, 虛擬通道記憶體) (97)Wireless LAN (無線網路) – 802.11b (98)ZIP檔案 (98)故障排除 (99)技術支援 (103)產品註冊 (107)與我們聯絡 (108)Adobe, Adobe商標以及Acrobat是Adobe Systems Incorporated的註冊商標。
穆格D791-D792系列伺服阀样本
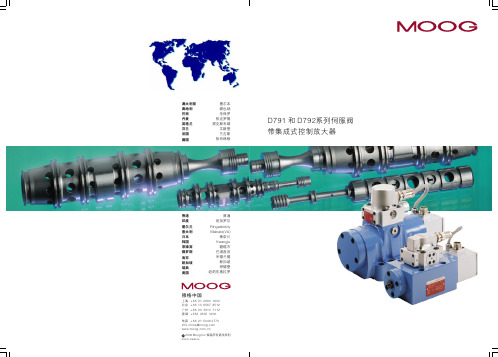
墨尔本 维也纳 圣保罗 伯克罗德 提克斯布瑞 艾斯堡 兰吉斯 伯布林根
D791 和 D792系列伺服阀 带集成式控制放大器
香港 印度 爱尔兰 意大利 日本 韩国 菲律宾 俄罗斯 南非 新加坡 瑞典 美国
葵涌 班加罗尔 Ringaskiddy Malnate(VA) 神奈川 Kwangju 碧瑶市 巴浦洛沃 米德兰德 新加坡 哥德堡 纽约东奥拉罗
要求的扭矩65Nm 65μm 常规
插拔所需 净空
D792系列伺服阀
带D761系列先导阀的安装图 转换说明
D792系列伺服阀
带D765系列先导阀的安装图 备件与附件
插拔所需 净空
插拔所需 净空
过滤器端盖
过滤器端盖 先导油供油口 (先导油回油口 Y在后侧) 螺纹M14×1.5 螺旋塞2 M14×1.5 (管接X 油口)
* 在先导级控制压力或系统工作压力为21MPa、油液粘度为32mm2/s和油液温度为40℃时测得。
典型特性曲线在先导级控制压力或系统工作压力为21MPa、油液粘度为32mm2/s和油液温度为40℃时测得。 阀的负载流量特性 频率响应 带不同额定流量和不同先导阀的伺服阀
幅值比[db] 幅值比[db]
典型特性曲线在先导级控制压力或系统工作压力为21MPa、油液粘度为32mm2/s和油液温度为40℃时测得。 阀的负载流量特性 频率响应 带不同额定流量和不同先导阀的伺服阀
D765系 列 先 导 阀 。 提 供 可 选 的标准响应或高响应系列。其 中 D791系列的额定流量最大 为 250 l/min, D792系 列 的 额 定流量最大为1000 l/min。 这类阀适用于位置、速度、力 (或压力)伺服控制系统,并 具有很高的动态响应。
MC7912BD2TG中文资料
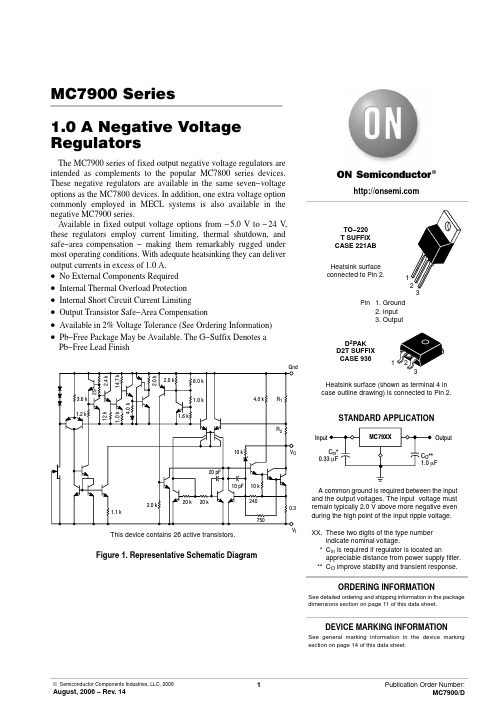
PD
Internally Limited
W
qJA
65
°C/W
qJC
5.0
°C/W
PD
Internally Limited
W
qJA
70
°C/W
qJC
5.0
°C/W
Storage Junction Temperature Range
Tstg
−65 to +150
°C
Junction Temperature
Symbol
Value
Unit
Input Voltage (−5.0 V ≥ VO ≥ −18 V) Input Voltage (24 V)
VI
− 35
Vdc
− 40
Power Dissipation Case 221A
TA = +25°C Thermal Resistance, Junction−to−Ambient Thermal Resistance, Junction−to−Case Case 936 (D2PAK) TA = +25°C Thermal Resistance, Junction−to−Ambient Thermal Resistance, Junction−to−Case
DEVICE MARKING INFORMATION
See general marking information in the device marking section on page 14 of this data sheet.
© Semiconductor Components Industries, LLC, 2006
1
Precision 7920 Tower 快速入门指南说明书
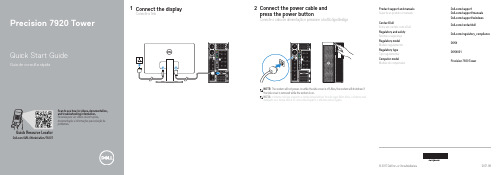
12Connect the power cable and press the power buttonConecte o cabo de alimentação e pressione o botão liga/desligaOTE: The system will not power-on while the side cover is off. Also, the system will shutdown if OTA: o sistema não liga enquanto a tampa lateral estiver fora do lugar. Além disso, o sistema será Quick Resource LocatorProduct support and manuals Suporte ao produto e manuais/support/support/manuals /support/windowsContact DellEntre em contato com a Dell /contactdellRegulatory and safety Normas e segurança /regulatory_compliance Regulatory model Modelo regulamentarD04X Regulatory type Tipo regulamentar D04X001Computer modelModelo do computadorPrecision 7920 Tower© 2017 Dell Inc. or its subsidiaries.2017-08Connect the displayConecte a tela1. Botão/luz de alimentação2. Luz de atividade da unidade3. Slot de cartão SD4. Portas USB 3.1 de 1ª geração5. Porta USB 3.1 Type-C de 1ª geraçãocom PowerShare 6. Porta USB 3.1 Type-C de 1ª geração 7. Porta para headset8. Trava de liberação da unidade 9. Slots da placa de expansão 10. Compartimento de 5,25 polegadas(opcional)11. Unidade óptica12. Conector do cabo de alimentação 13. Portas USB 3.1 de 1ª geração 14. Portadoras da unidade15. Slot da placa gráfica dedicada(opcional)16. Encaixe do cabo de segurança 17. Anel de cadeado 18. Porta de saída de linha19. Porta do microfone/entrada de linha 20. Porta serial21. Porta do mouse PS/222. Porta do teclado PS/223. Porta de rede (gerenciadaopcionalmente)24. Porta de rede25. Porta USB 3.1 de 1ª geração(compatível com Smart Power On, ativação inteligente)26. Slots da placa de expansão 27. Tampa lateral28. Trava de liberação da tampa lateralFeaturesRecursos1. Power button/Power light2. Drive activity light3. SD card slot4. USB 3.1 Gen 1 ports5. USB 3.1 Gen 1 Type-C port withPowerShare 6. USB 3.1 Gen 1 Type-C port 7. Headset port8. Drive access release latch 9. Expansion card slots 10. 5.25 inch bay (optional)11. Optical drive12. Power cable connector 13. USB 3.1 Gen 1 ports 14. Drive carriers15. Discrete graphics card slot (optional)16. Security cable slot 17. Padlock ring 18. Line-out port19. Microphone/Line-in port 20. Serial port 21. PS/2 Mouse port 22. PS/2 Keyboard port23. Network port (managed optionally)24. Network port25. USB 3.1 Gen 1 port (supportssmart Power-On)26. Expansion card slots 27. Side cover28.Side cover release latch。
MOOG伺服阀J761-原理……MOOG办事处

MOOG伺服阀J761-003原理……MOOG办事处美国穆格MOOGJ761-003,J761-003系列直动式伺服阀型号:D633,D634系列生产厂家:MOOG 产品说明:高性能直动式伺服阀,由线性力马达直接驱动阀芯运,阀内带有电子放大器对阀芯位置进行闭环控制。
直动式设计避免了先导级的泄漏损失,且动态响应与系统工作压力无关。
安装底面符合ISO4401标准。
频率响应:70HZ阶跃响应:15ms流量控制:3.8-100l/min(1-26gpm)最大工作压力:31.5Mpa该阀适应于金属压制设备,例如剪板机,折弯机,弯管机,木材压机.另外我司优势提供意大利atos阿托斯全系列!备有常规阀现货期待您的来电咨询!!!MOOG伺服阀J761-003原理……MOOG办事处MOOG伺服阀J761-003原理……MOOG办事处格公司(MOOG)是全球电液伺服元件及伺服系统设计及制造领域的领导者,由电液伺服阀的发明者William C. Moog于1951年创立。
产品广泛应用于飞机、卫星、航天飞机、火箭以及各种工业自动化设备。
在工业领域,注塑设备及吹塑设备的伺服控制是我们的重要研究领域之一。
MOOG 是最早进入全电动注塑行业的专业控制厂商之一,向合作伙伴提供DBS、DBM、DS2000 系列驱动器FASTACT 系列电机。
DS2000 驱动器和FAS T 交流伺服电机具有以下一些特点:驱动器可接受三相,50HZ,65到506V间的任意电压;可设定控制交流伺服电机或异步电机;电流环可根据伺服电机特点配置,并按DC BUS变化自动调节,同时提供 B.E.M.F 补偿以及相位自校正功能;速度环内集成了三种数字滤波器,动态性能良好,等等MOOG伺服阀原理J761-003&MOOG办事处MOOG伺服阀J761-003 现货供应!常用系列:D634系列,J761系列,G761系列, D791系列;D792系列,D661系列;D662系列;D663系列;D664系列;D665系列;D633系列等MOOG品牌最早起源于航空航天军事工业领域伺服阀及系统制造,主要经营伺服阀,伺服控制器,电动缸,伺服电机,伺服控制软件,行业应用领域广泛,涉及钢铁冶金,电力电站系统,注塑吹塑成型,材料试验,汽车测试仿真系统,航空测试仿真系统等,MOOG伺服阀J761-003/J761-004稳定可靠全部采用进口低飘移、高稳定度的运算放大器,使控制系统能长期、可靠、稳定地工作。
Frsky Taranis X9E 说明书
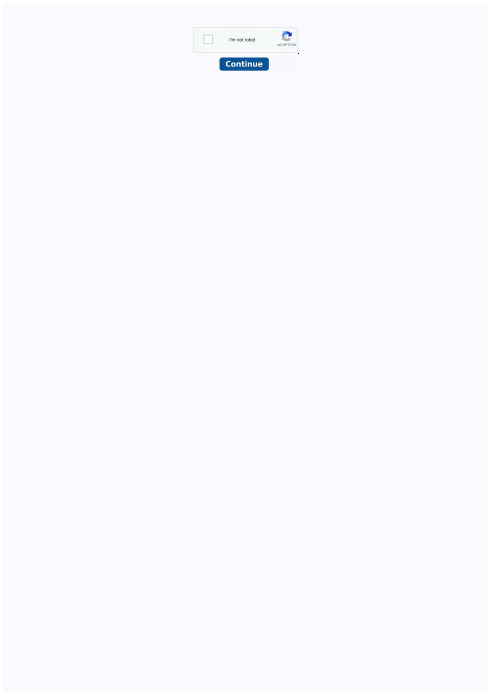
Tarani
Frsky taranis x9 lite firmware update. Frsky taranis x9d+.
FrSky Electronic Co., FrSky 2.4GHz ACCST Taranis X9E Manual FrSky Electronic Co., Cautions on handling antennaDo not touch the antenna during operation. Doing so could interfere with transmission, causing a crash.Do not carry the transmitter by the antenna. The antenna wire could break and prevent transmission.Do not pull the antenna forcefully. The antenna wire could break and prevent transmission.SpecificationsModel Name: Taranis X9ENumber of Channels: 16 Channels (extensible to 32 channels)Operating Voltage Range: 6~15V (2S, 3S Lipos are acceptable)Operating Current: 260mA maximum (both RF module and backlit are on)Operating Temperature: -10~60℃Backlight LCD Screen: 212*64Model Memories: 60 (ex
西门子d791和t791卸载器维修手册说明书
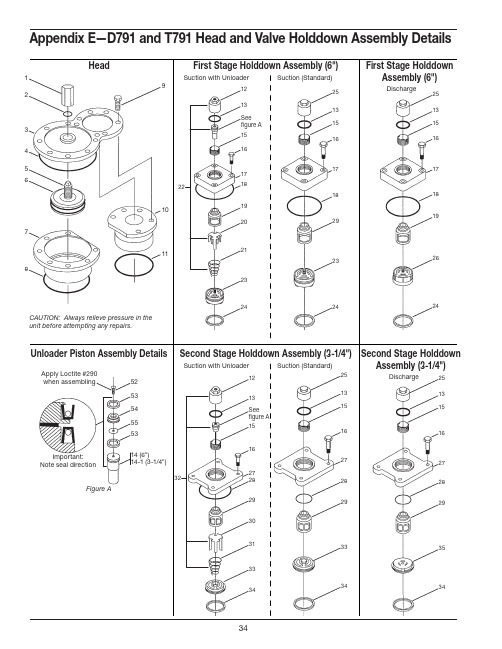
Important:Note seal directionApply Loctite #290when assemblingsecond stage holddown Assembly (3-1/4")Dischargesecond stage holddown Assembly (3-1/4")Suction with Unloader Suction (Standard)Figure AAppendix e—d791 and t791 head and valve holddown Assembly detailsO-ring Code A Buna-N B Neoprene D Viton E PTFE K Kalrez descriptionAdjusting screw nut Cylinder cap Adjusting cup Cylinder head (6")Bolt (1/2–13x1-1/2" hex hd gr 5)(Torque to 65 ft•lbs)Cylinder head (3-1/4")Unloader cap Unloader piston (6")Unloader piston (3-1/4")Holddown screwBolt (7/16–14x1-1/2" hex hd)(Torque to Valve cover plate Valve cage Unloader assembly (6")Suction valve assembly (6")Valve gasket Discharge valve assembly (6")Valve cover plate Valve cage part no.3690c 3689-X Unloader assembly (3-1/4")2438-X Suction valve assembly (3-1/4")1418-2b 2439-X Discharge valve assembly (3-1/4")3827Valve seat (6")38283830d Outer valve plate 3831d Inner valve plate 3829d 3805-X1Valve repair kit 3826Valve bumper (6")24462438Suction valve seat (3-1/4")24422445e Spacer (two per valve)335514072440Suction valve bumper (3-1/4")2441Discharge valve bumper (3-1/4")2439Discharge valve seat (3-1/4")1910c 2619-X c Unloader piston seal assembly 2857c Unloader piston cap 2858c_ denotes O-ring code. See O-ring chart for details.Included with valve assembly.Included with unloader assembly.Included with valve repair kit.Install spacers back to back.Registered trademark of the DuPont company.DischargeSuctionDischargeAppendix e—d791 and t791 head and valve holddown Assembly detailsImportant:Note seal directionApply Loctite #290when assembling2122232425262726222324252127Appendix e—d891 and t891 head and valve holddown Assembly detailsvalve Assemblies (4-1/2")Suction ValveDischarge ValveFigure AAppendix e—d891 and t891 head and valve holddown Assembly detailsCompressor head and valve bill of materialsa _ denotes O-ring code. See O-ring chart below for details.bIncluded with valve assembly cIncluded with unloader assembly dIncluded with valve repair kit.eRegistered trademark of the DuPont company.ref no.part no.description18.2714-1Valve cap 19.3569Valve cage20.3733-X Discharge valve assembly (4-1/2")21.3827Valve seat (4-1/2")22.3828Stud23.3830d Valve plate (outer)24.3831d Valve plate (inner)25.3829d Spring26.3826Valve bumper (4-1/2")27.3805-X1Valve repair kit 28.1910c Bolt29.2619-X c Unloader piston seal assembly 30.2857c Unloader piston cap 31.2858cGasket123454545456789Piston Rod9Piston bottom dead center Piston top dead centerpiston Assembly bill of materialsAppendix e—d791, t791, d891 and t891 piston Assembly detailsref.no.part no.descriptionQtyd/t791 1st stage3879-x1 (6")d/t791 2nd stage3884-x1 (3-1/4")d/t891 3925-x1 (4-1/2")1.7002-025-TP100A 7002-010-TP100A 7002-025-TP100AScrew, orlo gr. 8 (torque to 8 ft•lbs)42.3562a 3561a 3927a Piston cap 13.362537312902Shim washer (thick)As req.3625-13731-12902-1Shim washer (thin)4.175217561739Piston rings 41752-21756-41739-2Alloy 50 rings (opt.)1752-31756-31739-3Peek rings (opt.)5.175317571740Expander ring 46.3604Lock nut (torque to 150 ft•lbs)17.3730Thrust washer 28.3879a(6" diameter)3884a(3-1/4" diameter)3925a(4-1/2" diameter)Piston19.3603Shim washer (thick)As req.3603-1Shim washer (thin)10.3812 (not shown)Loctite tube (620)1piston Clearance (Cold)CAUTION: Always relieve pressure in the unit before attempting any repairs.aMC1002 coated piston and cap available. Add “C” to end of a standard part number (e.g. 3562C)1 23763854Notealignmentmarks52Appendix E—D791, T791, D891 and T891 Connecting Rod and Crosshead Assembly Detailsa Included with connecting rod assemblyb Torque connecting rod nut to 40 ft. lbs.c Must be rebored after replacing (1.1258/1.1254 dia.)d Not sold separatelyNever attempt to separate the piston rod and crosshead. Whenrepair becomes necessary, the entire crosshead assembly mustbe replaced.CAUTION: Always relieve pressure in the unit before attemptingany repairs.1161Appendix e—d791 and d891 packing Assembly detailsspecification “k”specification “J”16117packing Assembly bill of materialsIMPORTANT: Identify and line up the rings before installing. Be sure they face the way shown here and that the pin and hole are aligned when assembled.a _ denotes O-ring code. See O-ring chart for details.bDeflector ring is loose within the packing cartridge until fitted on the piston rod. Must be put in from the bottom of the cartridge.cStarting with S.N. NN51397. dPacking cup O-ring not included in packing set.eRegistered trademark of the DuPont company.Appendix e—d791 and d891 packing Assembly detailsPiston (Pressure) SidePiston (Pressure) Side specification “r”Appendix e—t791 and t891 packing Assembly detailsAppendix e—t791 and t891 packing Assembly detailspacking Assembly bill of materialsIMPORTANT: Identify and line up the rings before installing. Be sure they face the way shown here and that the pin and hole are aligned when assembled.a _ denotes O-ring code. See O-ring chart for details.bDeflector ring is loose within the packing cartridge until fitted on the piston rod. Must be put in from the bottom of the cartridge.cStarting with S.N. NN51397. dPacking cup O-ring not included in packing set.eRegistered trademark of the DuPont company.Piston (Pressure) Side Piston (Pressure) Side13Appendix e—d791 Crosshead guide Assembly detailsNOTE:Packing barrel installation:1. Use packing installation cone #3905 on the piston rod.2. Insert small barrel first, use finger holes to align slinger ring on to the rod. Slip the packing barrel into place.3. Align pin with slot in large packing barrel.4. Slip large packing barrel in place.Appendix e—d891 Crosshead guide Assembly detailsCrosshead guide bill of materialsAppendix e—t791 Crosshead guide Assembly detailsbRegistered trademark of the DuPont company.CAUTION: Always relieve pressure in the unit before attempting any repairs.NOTE:Packing barrel installation:1. Use packing installation cone #3905 on the piston rod.2. Insert small barrel first, use finger holes to align slinger ring on to the rod. Slip the packing barrel into place.3. Align pin with slot in large packing barrel.4. Slip large packing barrel in place.Crosshead guide bill of materialsAppendix e—t891 Crosshead guide Assembly detailsabRegistered trademark of the DuPont company.CAUTION: Always relieve pressure in the unit before attempting any repairs.NOTE:Packing barrel installation:1. Use packing installation cone #3905 on the piston rod.2. Insert small barrel first, use finger holes to align slinger ring on to the rod. Slip the packing barrel into place.3. Align pin with slot in large packing barrel.4. Slip large packing barrel in place.542861(Includes all parts shown except #52 and #53)Bearing CarrierOil Passage Hole Pumpside of adapter shown for proper orientation of cover and location of pump cover pin.Appendix e—Crankcase Assembly detailsAppendix e—Crankcase Assembly detailsCrankcase Assembly bill of materialsrefno.part no.description 47.3219Pump shaft adapter 48.2-112_c O-ring49.2805-X a Pump shaft bushing 50.1629Pipe plug (1/16 NPT fl. seal)51.1736Bearing cup 52.1302Oil pressure gauge 53.1044Bushing (1/8 x 1/4 NPT)54.3220-2Bearing carrier55.3289Pipe plug (1/4 NPT fl. seal)56.2131Bearing carrier gasket 57.2961-X Air release valve assembly 58.2590Pipe plug (1/8 NPT fl. seal)59.4225Filter60.2798Pump cover pin (included w/4222-X)61.3220-2X Bearing carrier assembly 62.4222Oil filter adapter63.3289Pipe plug (1/4" x 18 NPTF x 7/8")Back Side Front SideAssembly Number Assembly Name3852-X Flywheel assembly (flywheel, hub, and three bolts)3852Flywheel: 21.2" O.D., 5 groove H J-2.125Hub with three bolts and lockwashersflywheel Assembly bill of materialsAppendix e—flywheel Assembly details。
YEMAYA DATA RECORDING SOFTWARE FOR PC 说明书
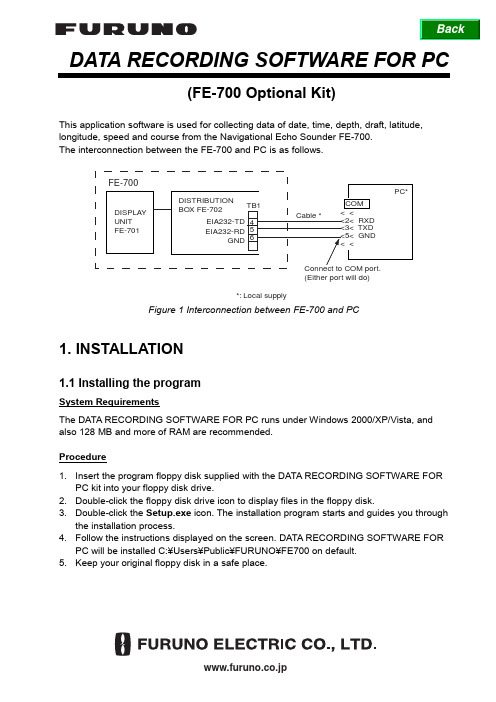
DATA RECORDING SOFTWARE FOR PC(FE-700 Optional Kit)This application software is used for collecting data of date, time, depth, draft, latitude, longitude, speed and course from the Navigational Echo Sounder FE-700.The interconnection between the FE-700 and PC is as follows.(Either port will do)*: Local supplyFigure 1 Interconnection between FE-700 and PC1. INSTALLATION1.1 Installing the programSystem RequirementsThe DATA RECORDING SOFTWARE FOR PC runs under Windows 2000/XP/Vista, and also 128 MB and more of RAM are recommended.Procedure1. Insert the program floppy disk supplied with the DATA RECORDING SOFTWARE FORPC kit into your floppy disk drive.2. Double-click the floppy disk drive icon to display files in the floppy disk.3. Double-click the Setup.exe icon. The installation program starts and guides you throughthe installation process.4. Follow the instructions displayed on the screen. DATA RECORDING SOFTWARE FORPC will be installed C:¥Users¥Public¥FURUNO¥FE700 on default.5. Keep your original floppy disk in a safe place.www.furuno.co.jp2 1.2 Setting up the program1. Click the START button on the Windows to open the Start menu.2. Move the mouse pointer on the PROGRAM option to open the Program menu.3. Move the mouse pointer on the Fe700 option. The application menu opens.4. Move the mouse pointer on the application program icon Fe700 and click it. The DATA RECORDING SOFTWARE FOR PC will start up. The following screen appears.Figure 2 Start-up Display1.3 Setting the serial port1. Select Setting-Serial port from the menu bar.2. Select the port (COM 1 to COM 9) which has been connected to the PC.3. Press OK button.2. OPERATION PROCEDURESNote: If you open the system menu 1, 2 or 3 of the FE-700 during downloading, “Communication error!” will appear. Press the OK button and repeat from beginning.32.1 Downloading dataTo download real time data (one second intervals data) from the FE-700, press the Start button on the toolbar, or select Download - Start from the menu bar. Also, pressing F9 key on your keyboard downloads real time data. The data is downloaded at one second intervals and displayed in log (Log mode) or graph (Graph mode) form.Figure 3 Log Mode (text screen)Line (green)Figure 4 Graph Mode (graphic screen)4To change the mode, press theor button on the screen or select Mode – Log Data / Graph from the menu bar. Also, pressing F7 key or F8 key on your keyboard changes the mode to log mode or graph mode, respectively.To inscribe line (s) on the graphic screen, click the Markbutton on the toolbar, or select Option-Mark from the menu bar (or F1 key) at the moment you want to pay attention. M mark is displayed on the text screen.To stop downloading at any time, press the Stopbuttonon the toolbar or select Download - Stop from the menu bar. Also, pressing F10 key on your keyboard stops downloading.2.2 Downloading RAM data in the FE-700To download one hour of data (one second intervals data) or 24 hours of data (five seconds intervals data) in the RAM of the FE-700 (accumulated at the Echo Sounder FE-700), select Download - Loading Option - 1h Data or 24h Data . The Download dialog box appears, showing "Now downloading" and indicating data volume. You can cancel downloading at any time by selecting Cancel.Figure 5 Download dialog boxWhen downloading is completed, "Download Completed" is shown. Click the OK button. The downloaded data is saved at a file named after date of the moment you just startdownloading. For example, one hour data file is named as “20000717_1h.dat”. (This file has created at July 17, 2000.) When you open the file from the FILE menu, you can observe the data in the log mode.2.3 Setting option itemsThe Option menu provides various settings for downloading real time data or depicting graphics.To open the File dialog box, select Option - Option on the menu bar. Click the File tab if it is not already selected. The File dialog box appears.Figure 6 File tab on the Option dialog boxFile Saving optionCreate new files at 00:00:New files will be automatically created every day at 00:00. (Initial file iscreated when the Start button is pressed.) Files will be named as“yyyymmdd” (year+month+day).Create a new file at specific time period (1h - 24h):A new file is created and data is saved at a period of specified time (hour).Set hour(s) between 1 and 24 hours at 1-hour period. If you set one hour,for example only the recent one hour data is saved and old data isoverwritten. The file is named as “userfile.dat”.Not saving:Data received from the FE-700 is displayed on the screen, but not saved tothe hard disk of the PC.Time Interval optionSelect time interval to extract received data. Extracted data is displayed onthe text screen or graphic screen.Auto Printing optionLog: Printing is automatically performed every 60 lines of text data.Graphic: Printing is automatically performed every graphic page.Off: No automatic printing.To change a setting, press appropriate radio buttons or press up/down arrow button. After setting as desired, press the OK button. The dialog box closes.5To open the Graphic dialog box, select Option - Option on the menu bar and click the Graphic tab if it is not already selected. The Graphic dialog box appears.Figure 7 Graphic tab on the Option dialog boxScale option: Select an appropriate depth scale for graphics, between 5 m to 800 m. Pixels option: Select appropriate number of pixels to display per one received data from the dropdown list to depict the contour of the seabed. The choices are 1, 2,5 and 10 pixels.Mode option: Select the drawing method for graphics among Solid, Line (Wide) and Line (Narrow).Line Color option: Select seabed color for graphics among gray, red, yellow and black. Back Color option: Select background color for graphics, between black and white.Set Depth option: Select Off to display all depth data. Select On to display depth datawhich is shallower than depth setting. For On, set the depth you wish todisplay. A red line (blue when “Line Color” is set for “Red”) appears at setdepth position.To change a setting, press appropriate radio buttons or press down-arrow button. After setting as desired completed, press the OK button. The dialog box closes.62.4 Opening a fileThere are two methods to open a file: File option and Time Selection option.To open a file and display it on the text screen, select the File - Open from the menu bar (or Ctrl +O) or click File Open button.The normal Windows Open File dialog box appears. Select an appropriate file and click the Open button and the Select Data dialog box appears. The Select Data dialog box lets you specify which data to read in. After choosing data, click the OK button. The data is displayed in the log or graph mode.Read in all data.Read in data from a specificdate.Read in data from a specifictime frame.Figure 8 Select Data dialog boxNote: No data is denoted with a black double line. The color is light-blue when there is no data for more than one day.To read data from specified start date/time to end date/time and display it on the text or graphic screen, select File - Time Selection from the menu bar. The Time Selection dialog box appears. Enter start date/time and end date/time, then click the OK button. You can display the time selection data on the text screen or graphic screen. (In this method, the1h-data file (xxxxxxx-1h.dat), 24h-data file (xxxxxxx-24h.dat) and userfile.dat can not be opened.)You can set the from/to period for maximum 11 hours 59 minutes.Example: From Year 2000/Month 7/Day 5/Hour 13/Minutes 1To Year 2000/Month 7/Day 6/Hour 1/Minutes 0Figure 9 Time Selection dialog box78 2.5 Saving a fileData can be saved with any name in Excel format. Select File - Save as CSV-file from the menu bar or click the Save as CSV-file button . The normal Windows Save as dialog box appears. Type file name, select the location to save and click the OK button.2.6 Printing a fileYou may print out data. Select File - Print from the menu bar and then click one of thefollowing depending on your objective. The normal Windows Print dialog box appears. Click the OK button to print out the data.Log Data : Print log mode data. This can also be done by clicking Print Log Databutton . Graph (Hardcopy): Print graph mode data. This can also be done by clicking Print GraphHardcopybutton .Graph (All Data): C ompress all graph data into one page and print. This can also be doneby clicking Print Graph All Databutton .2.7 Displaying version informationSelect About – Program Version from the menu bar to show the version information, see Figure 2 in section 1.2. To close the display, click the OK button.2.8 Exiting the programSelect File – Program Exit from the menu bar. The program closes and return to the Windows screen.2.9 Error MessagesBelow is a list of error messages shown on the screen.Message Meaning Remedy Initializing error!: COM Failed initialization of COM port. For example, other application uses COM port. Match the “serial port”setting (section 1.3) withthe COM port connectionof the PC.Communication error! Failed communication with FE-700. Confirm the connectionbetween FE-700 andCOM port of PC.Can not open! Could not read or save data.No dataNot enough memory to save! There was not enough space on the hard disk onthe PC.Delete unnecessary files. Invalid data! Specified time was wrong.Try to specify date/time again. (less than 12hours).Not found the data! There was no data in the file at specified time. Try to specify date/timeagain.Pub. No.OM E-23661-H F E -700 D ATA R E C.S O F T (YOSH)A : J U L. 2000 H : D E C. 4, 2007。
- 1、下载文档前请自行甄别文档内容的完整性,平台不提供额外的编辑、内容补充、找答案等附加服务。
- 2、"仅部分预览"的文档,不可在线预览部分如存在完整性等问题,可反馈申请退款(可完整预览的文档不适用该条件!)。
- 3、如文档侵犯您的权益,请联系客服反馈,我们会尽快为您处理(人工客服工作时间:9:00-18:30)。
Servovalveswith integrated Electronics D791 and D792 Series23Q [l/min]=max. flowΔp [bar]=valve pressure dropwith Q A K [cm 2]=spool drive area p X [bar]=pilot pressure The pilot pressure p X has to be at least 15 bar above the returnpressure of the pilot stage.D791 and D792 SeriesThree stage servovalvesPrinciple of operationAn electrical command signal (set point, input signal) is applied to the integrated control amplifier which drives a current through the pilot valve coils. The pilot valve produces differential pressure in its control ports. This pressure difference results in a pilot flow which causes main spool dis-placement.The position transducer which is excited via an oscillator measures the position of the main spool (actual value, position voltage).This signal then is demodulated and fed back to the control amplifier where it is compared with the command signal. The control amplifier drives the pilot valve until the error between command signal and feedback signal is zero. Thus, the position of the main spool is proportional to the electrical command signal.Q Q p p NN=ΔΔp 2,510QA pX -2K≥⋅⋅ΔThe actual flow depends on the electrical command signal and the valve pressure drop, and may be calculated using the square root function for a sharp-edged orifice.The flow value Q calculated in this way should not exceed an average flow velocity of 30 m/s in ports P, A, B and T.Q [l/min]=calculated flow Q N [l/min]=rated flowΔp [bar]=actual valve pressuredropΔp N [bar]=rated valve pressuredrop4If large flow rates with high valve pressure drops are required, an appropriate higher pilot pressure has to be chosen to overcome the flow forces. An approximate value can be calculated as follows:Our quality management system is certified in accordance with DIN EN ISO 9001.This catalogue is for users with technical knowledge. To ensure that all necessary characteristics for function and safety of the system are given, the user has tocheck the suitability of the products described here.In case of doubt please contact Moog.The flow control servovalves D791and D792 Series are throttle valves for 3-way and preferably 4-way applications. These three stage servovalves have been especially developed for such demanding applications where high flow rates and at the same time extreme dynamic performance require-ments must be met. The design of these valves is based on the well known D079 Series. The inte-grated electronics has been replaced by a new design applying SMD technology. The valves areoffered with pilot valves of D761or D765 Series, optional standard response or high response versions are available. Series D791 can de-liver rated flow up to 250 l/min,Series D792 is available with rated flow up to 1000 l/min.These valves are suitable for pres-sure or force control, position and velocity control systems with high dynamic response requirements.D791 and D792 SeriesGeneral technical dataOperating pressure rangeMain stage Ports P, A and B with X internal up to 315 bar with X externalup to 350 bar Port T with Y internal up to 210 bar Port T with Y external up to 350 barPilot valve Ports P, A and B D761, D765 Series up to 315 bar Port Tup to 210 barTemperature rangeAmbient -20 to +60 °C Fluid-20 to +80 °CSeal material FPM, others on requestOperating fluid Mineral oil based hydraulic fluid (to DIN 51524), others on request Viscosityrecommended 15 to 100 mm²/s Class of cleanlinessThe cleanliness of the hydraulic fluid greatly effects the per-formance (spool positioning, high resolution) and wear (metering edges, pressure gain, leakage) ofthe valve.5T B P A3 stage Servovalve D792with Pilot valve D765 SeriesRecommended cleanliness classfor normal operation:ISO 4406 < 17/14/11for longer life:ISO 4406 < 16/13/10System filtrationPilot valve:High pressure filter (without by-pass, but with dirt alarm) mountedin the mainflow and if possible,directly upstream of the servo-valve.Main stage:Main stage: high pressure filter asfor the pilot stage. In combination with a fast regulating VD-pump a bypass filter is possible.Filter rating recommendedfor normal operation:ß10 ≥ 75 (10 μm absolute)for longer life:ß5 ≥ 75 ( 5 μm absolute)Installation options any position, fixed or movable Vibration 30 g, 3 axes Degree of protection EN 60529: IP 65 (with mating con-nector mounted)Shipping plate Delivered with an oil sealed ship-ping plate6Model . . . .TypeD791 . . . . S . . .Mounting patternISO, but X and Y do not corres-ISO 10372-06-05-0-92pond to ISOValve body version 4-way3-stage with bushing spool assembly Pilot valve2-stage, optional D761 or D765 SeriesPilot connection optional, internal or externalX and Y Mass[kg]13Rated flow (± 10%) at Δp N = 35 bar per land [l/min]100160250Response time*for 0 to 100% stroke (depen-dent on pilot valve)[ms]3 to 10Threshold*[%]< 0,2Hysteresis*[%]< 0,5Null shiftwith ΔT = 55 K [%]< 2Null leakage flow*total, max.[l/min]5710Pilot leakage flow*max., for 100% step input (de-pendent on pilot valve)[l/min]4 to 11Main spool stroke [mm]1,41,22,0Main spool drive area[cm²]2,85* measured at 210 bar pilot or operating pressure, fluid viscosity of 32 mm²/s and fluid temperature of 40 °CValve flow diagramTypical characteristic curves measured at 210 bar pilot or operating pressure, fluid viscosity of 32 mm²/s and fluid temperature of 40 °CFrequency responsefor valves with different rated flows and different pilot valvesD791 SeriesTechnical dataModel . . . .TypeD792 . . . . S . . .Mounting pattern Moog StandardValve body version 4-way3-stage with bushing spool assembly Pilot valve2-stage, optional D761 or D765 SeriesPilot connection optional, internal or externalX and Y Mass[kg]17Rated flow (± 10%) at Δp N = 35 bar per land [l/min]4006308001000Response time*for 0 to 100% stroke (depen-dent on pilot valve)[ms]4 to 12Threshold*[%]< 0,2Hysteresis*[%]< 0,5Null shiftwith Δ T = 55 K [%]< 2Null leakage flow*total, max.[l/min]10141414Pilot leakage flow*max., for 100% step input (de-pendent on pilot valve)[l/min]6 to 16Main spool stroke [mm]1,81,92,64,0Main spool drive area[cm²]3,87,147,147,14* measured at 210 bar pilot or operating pressure, fluid viscosity of 32 mm²/s and fluid temperature of 40 °CValve flow diagramTypical characteristic curves measured at 210 bar pilot or operating pressure, fluid viscosity of 32 mm²/s and fluid temperature of 40 °C Frequency responsefor valves with different rated flows and different pilot valvesD792 SeriesTechnical data7D791 SeriesInstallation drawing with Pilot valve D761 Series Conversion instructionThe mounting manifold mustconform to ISO 10372-06-05-0-92.Note: The X port to ISO Stan-dard must not be machined.The X and Y ports of Moogvalve body do not correspondto ISO Standard.Mounting surface needs to beflat within 0,02 mm. Averagesurface finish value, Ra, betterthan 1μm.89Spare parts and accessories for D791 SeriesD791 SeriesInstallation drawing with Pilot valve D765 SeriesSpare parts, AccessoriesNote: The X and Y tubes have to be connected to the Moog valve body by fittings.Mounting surface needs to be flat within 0,02 mm. Average surface finish value, Ra, better than 1μm.D792 SeriesInstallation drawing withPilot valve D765 SeriesSpare parts, AccessoriesSpare parts and accessories for D792 Series1112General requirementsD791 and D792 SeriesValve electronics with supply voltage ± 15 VoltCommand signal 0 to ±10 V Valves with voltage command inputThe spool stroke of the valve is proportional to (U D – U E ). 100%valve opening P ± A and B ± T is achieved at (U D – U E ) = +10 V . At 0 V command the spool is in a centred position.The input stage is a differential amplifier. If only one command signal is available, pin D or E is connected to signal ground ⊥(pin C) according to the required operating direction (to be done at the mating connector).Command signal 0 to ±10 mA Valves with current command inputThe spool stroke of the valve is proportional to (I D – I E ). 100%valve opening P ± A and B ± T is achieved at (I D – I E ) = +10 mA. At 0 mA command the spool is in a centred position.Either pin D or E is used according to the required operating direc-tion. The unused pin is left open (not connected at the mating con-nector). The input pins D and E are inverting.Actual value 0 to ±10 VValves with voltage command inputThe actual spool position value can be measured at pin F. This signal can be used for monitoring and fault detection purposes.The spool stroke range corres-ponds to ±10 V. 100% valve ope-ning P ± A and B ± T corresponds to +10 V.Actual value 0 to ±10 mA or 4 to 20 mAValves with current command inputThe actual spool position value can be measured at pin F. This signal can be used for monitoring and fault detection purposes.The spool stroke range cor-responds to ±10 mA (4 to 20 mA).100% valve opening P ± A and B ± T corresponds to +10 mA (20 mA).ÌSupply ± 15 VDC ± 3%. Ripple <50 mV pp . Current consumption max. ± 250 mAÌAll signal lines, also those of external transducers, shieldedÌShielding connected radially to ⊥ (0V), power supply side, and connected to the mating connector housing (EMC)ÌEMC : Meets the requirements of EN 55011/03.91 class B ,EN 50081-1/01.92, and EN 50082-2/03.95, performance criterion class AÌProtective grounding lead ≥ 0,75mm 2ÌNote: When making electrical connections to the valve (shield,protective grounding) appropriate measures must be taken to ensure that locally different earth potentials do not result in excessive ground currents. See also Moog Application Note AM 353 E.Wiring for valves with 6+PE pole connector to DIN 43563 and mating connector (metal shell) with leading protective grounding connection ().Input rated command 0 to ± 10 mA 0 to ± 10 V Valve flowLoad resistance (diff.) 1 k ΩInput resistance 10 k ΩInput rated command (differential)Valve flowOutput actual value 0 to ± 10 mA 0 to ± 10 VMain spool position Load resistance max. 500 ΩOutput resistance 50 ΩFunctionCurrent commandVoltage commandSupply + 15 VDC ± 3Supply– 15 VDC ± 3Supply / signal ground ⊥ (0V)Input command I D = –I E : 0 to ±10 mAInput command (inverted)I E = –I D : 0 to ±10 mA U D–E = 0 to ±10 V (R e= 10 k Ω)(R e = 200 Ω)Input voltage for U D–B and U E–B for both signal types is limited to min. –15 V and max. +32 VProtective groundingD791 and D792 SeriesValve electronics with supply voltage 24 VoltActual value 4 to 20 mAThe actual spool position value can be measured at pin F (see diagram below). This signal can be used for monitoring and fault detection purposes.The spool stroke range corres-ponds to 4 to 20 mA.The centred position is at 12 mA.20 mA corresponds to 100 %valve opening P ± A and B ± T.The position signal output 4 to 20 mA allows to detect a cable break when I F = 0 mA.For failure detection purposes it is advised to connect pin F of the mating connector and route this signal to the control cabinet.Command signal 0 to ±10 V,Valves withvoltage command input The spool stroke of the valve is proportional to (U D – U E ).100 % valve opening P ± A and B ±T is achieved at (U D – U E ) = +10 V.At 0 V command the spool is in centred position.The input stage is a differential amplifier. If only one command signal is available, pin D or E is connected to signal ground at cabinet side, according to the required operating direction.Command signal 0 to ±10 mA floating,Valves withcurrent command inputThe spool stroke of the valve is proportional to I D = –I E .100 % valve opening P ± A and B ± T is achieved at I D = +10 mA.At 0 mA command the spool is in centred position.The input pins D and E are inver-ting. Either pin D or E is used according to the required ope-rating direction. The other pin is connected to signal ground at cabinet side.General requirementsÌSupply 24 VDC, min. 18 VDC, max. 32 VDC Current consumption max. 300 mAÌAll signal lines, also those of external transducers, shielded.ÌShielding connected radially to ⊥ (0 V), power supply side, and connected to the mating connector housing (EMC).ÌEMC : Meets the requirements of EN 55011:1998, class B ,EN 50082-2:1995, performance criterion class A.ÌMinimum cross-section of all leads ≥ 0,75 mm 2.Consider voltage losses between cabinet and valve.ÌNote: When making electric connections to the valve (shield, protective earth) appropriate measures must be taken to ensure that locally different earth potentials do not result in excessive ground currents.See also Moog Application Note AM 353 E.Wiring for valves with 6+PE pole connectorto EN 175201 Part 804 2), and mating connector (type R and S , metal shell) with leading protective earth connection (). See also wiring instructions AM 426 E.Note: Enable inputWith enable signal off, the main spool will move to a safe position.a)Centred position (unbiased pilot valve)function code A 1)b)End position(biased pilot valve)function code B 1)1)see type designation2)formerly DIN 4356313Notes 14D791 und D792 SeriesOrdering information15Preferred configurations are highlighted.All combinations may not be available.Options may increase price.Technical changes are reserved.Type designationModel-NumberK R H /W A /50 P r i n t e d i n G e r m a n yMoog GmbHHanns-Klemm-Straße 28D - 71034 Böblingen Postfach 1670D - 71006 Böblingen Telefon (07031) 622-0Telefax (07031) 622-191Australia Melbourne Austria Vienna Brazil São Paulo Denmark Birkerød England Tewkesbury Finland Espoo France Rungis Germany B öblingenHong Kong Kwai Chung India Bangalore Ireland Ringaskiddy Italy Malnate Japan Hiratsuka Korea Kwangju Philippines Baguio Russia Pavlovo South Africa Midrand City Singapore Singapore Spain Orio Sweden Gotenborg USA East Aurora (NY)D791/2 - EN / 01.04。