产线平衡
生产线平衡

生产线平衡率的计算方法
平衡率是评价一条产线的重要指标,平衡率高就表示在同等 条件下平衡损失就少,也就是说平衡率高的产线人均产能就 高。
目的:通过平衡生产线提高生产效率同时使生产现场更 加容易理解“一个流”的必要性及对于真正实现“OPF”进 而导入“cell production”的重要意义。
平衡生产线的意义
游戏时间
平衡生产线的意义
通过Line balancing我们可以达到以下几个目的:
有效减少工时损失进而提高作业员及设备工装的工作效率; 减少产品的C/T和pitch time,最终导致Takt time 的减少,提高productivity. 提高OEE & OME. 减少WIP,更容易真正实现“OPF”。 在Line balancing 基础上,实现单元生产,提高了生产对柔性化市场的应变能 力。
Line balance rate = ∑Standard time/(bottleneck time*person qty) = ∑ Standard time/(Pitch time*person qty)
Line imbalance rate =1-Line balance rate
Remark: Pitch time 是指生产线每产出一个batch产品所消耗 的时间,这里我们定义batch size 为1pcs, 所以pitch time=bottleneck time, 理想情况下pitch time=Takt time.
1.不同产品的特性差异
产线均衡与优化
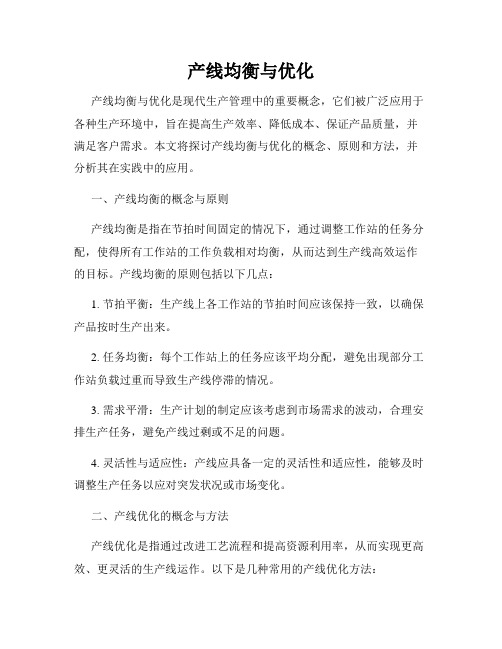
产线均衡与优化产线均衡与优化是现代生产管理中的重要概念,它们被广泛应用于各种生产环境中,旨在提高生产效率、降低成本、保证产品质量,并满足客户需求。
本文将探讨产线均衡与优化的概念、原则和方法,并分析其在实践中的应用。
一、产线均衡的概念与原则产线均衡是指在节拍时间固定的情况下,通过调整工作站的任务分配,使得所有工作站的工作负载相对均衡,从而达到生产线高效运作的目标。
产线均衡的原则包括以下几点:1. 节拍平衡:生产线上各工作站的节拍时间应该保持一致,以确保产品按时生产出来。
2. 任务均衡:每个工作站上的任务应该平均分配,避免出现部分工作站负载过重而导致生产线停滞的情况。
3. 需求平滑:生产计划的制定应该考虑到市场需求的波动,合理安排生产任务,避免产线过剩或不足的问题。
4. 灵活性与适应性:产线应具备一定的灵活性和适应性,能够及时调整生产任务以应对突发状况或市场变化。
二、产线优化的概念与方法产线优化是指通过改进工艺流程和提高资源利用率,从而实现更高效、更灵活的生产线运作。
以下是几种常用的产线优化方法:1. 价值流映射:通过绘制产品从原材料到最终交付的价值流程图,找出其中的瓶颈和浪费,优化生产流程。
2. SMED工具:通过减少设备换型时间,提高生产线的灵活性和响应能力。
3. 连续流水线设计:通过将工作站有机地连接在一起,优化物料流动,减少物料的等待时间,提高生产效率。
4. 自动化技术:引入自动化设备和系统,提高生产线的自动化水平,降低人工干预,减少错误率。
5. 设备维护与保养:定期对设备进行维护和保养,确保设备正常运转,避免因设备故障导致的生产线停产。
三、产线均衡与优化的应用案例产线均衡与优化的应用广泛,以下是一些实际案例:1. 汽车制造业:汽车生产线的均衡与优化可以提高车辆的生产效率和质量,降低成本,满足不同地区和市场的需求。
通过合理安排工作站的任务和优化生产流程,实现生产线的平衡和优化。
2. 电子制造业:电子产品的生产线均衡与优化可以提高生产效率和质量,缩短产品上市时间。
产线平衡率计算公式标准
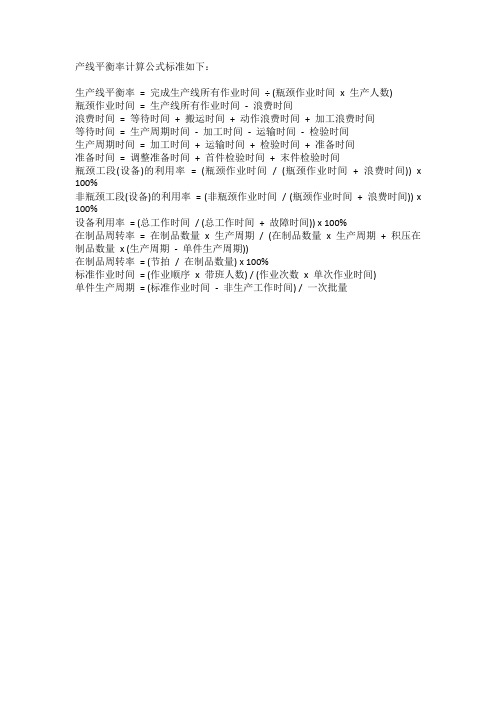
产线平衡率计算公式标准如下:
生产线平衡率= 完成生产线所有作业时间÷ (瓶颈作业时间x 生产人数)
瓶颈作业时间= 生产线所有作业时间-浪费时间
浪费时间= 等待时间+ 搬运时间+ 动作浪费时间+ 加工浪费时间
等待时间= 生产周期时间-加工时间-运输时间-检验时间
生产周期时间= 加工时间+ 运输时间+ 检验时间+ 准备时间
准备时间= 调整准备时间+ 首件检验时间+ 末件检验时间
瓶颈工段(设备)的利用率= (瓶颈作业时间/ (瓶颈作业时间+ 浪费时间)) x 100%
非瓶颈工段(设备)的利用率= (非瓶颈作业时间/ (瓶颈作业时间+ 浪费时间)) x 100%
设备利用率= (总工作时间/ (总工作时间+ 故障时间)) x 100%
在制品周转率= 在制品数量x 生产周期/ (在制品数量x 生产周期+ 积压在制品数量x (生产周期-单件生产周期))
在制品周转率= (节拍/ 在制品数量) x 100%
标准作业时间= (作业顺序x 带班人数) / (作业次数x 单次作业时间)
单件生产周期= (标准作业时间-非生产工作时间) / 一次批量。
生产线平衡(实例版)
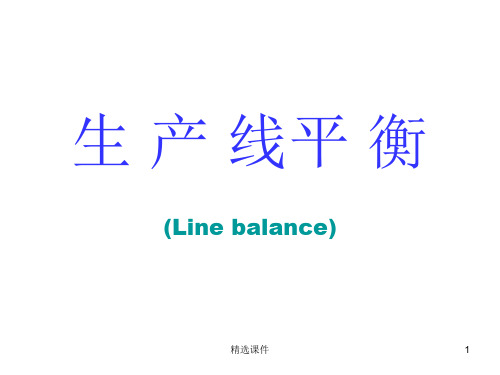
时间
T2
T1
T3 T4 T5
工站 S1 S2 S3 S4 S5
单件标准时间= T1+T2+T3+T4+T5
(流程中各工站所有动作标准时间之和)
精选课件
13
1﹑生产线平衡的相关概念
1.5生产线平衡
生产线平衡﹐又称工序同期化﹐是通过技朮组 织措施调整生产线的工序时间定额﹐使工站的 单件作业时间等于生产线节拍﹐或与节拍成整 数倍关系。
精选课件
7
1﹑生产线平衡的相关概念
1.2工站及周期时间
时间
T2
T1
T3 T4 T5
工站 S1 S2 S3 S4 S5
CycleTime ﹕每工站中1个循环的作业所需的标
准工时(如图中所示﹕T1,T2,T3,T4,T5)
精选课件
8
1﹑生产线平衡的相关概念
1.3瓶颈时间
时间
T2 瓶颈时间
T1
T3 T4 T5
所有工站时间之和
平衡率=
瓶颈工站时间*工站总数
100 %
精选课件
16
1﹑生产线平衡的相关概念
1.6平衡率﹐平衡损失及其计算
例:某产线有6个工站,各工站时间分别 为20秒,24秒,18秒,22秒,20秒,21秒, 试计算该产线的平衡率?
平衡率:
=(20+24+18+22+20+21)/(24*6)*10 0%
=125/144*100%
=86.8%
精选课件
17
1﹑生产线平衡的相关概念
1.6平衡率﹐平衡损失及其计算
平衡损失是因为产线间不平衡造成各工站 间的等待而造成的损失.
生产线平衡

生产线平衡什么是生产线平衡?生产线平衡是指在制造业中,通过合理安排工作站的工作内容和工作时间,使得各个工作站之间的工作负荷达到一致,从而实现整个生产线的高效运行和提高生产效率。
生产线平衡可以有效地减少生产过程中的浪费,并降低生产成本。
生产线平衡的优势1.提高生产效率:通过合理安排工作站的工作负荷,避免因工作站负荷过大或过小而导致的生产效率低下的情况发生,从而提高生产效率。
2.减少生产过程中的浪费:生产线平衡可以避免一些工作站因工作内容过多而产生等待时间,以及其他工作站因工作内容过少而导致的工作站闲置的情况。
这样可以最大程度地减少生产过程中的浪费,提高资源利用率。
3.增强生产线的灵活性:通过生产线平衡,可以使得生产线上各个工作站之间的工作负荷相对均衡,从而增强生产线的灵活性和应对能力。
当需要进行产品类型或生产数量的调整时,可以比较容易地实现,而不需要对整个生产线进行大幅度的调整。
4.提高产品质量:生产线平衡可以减少生产过程中的等待时间和工作站的闲置时间,从而减少了生产线上人为因素对产品质量的影响。
工人在有充足时间完成任务的情况下,可以更加专注和仔细地完成工作,提高产品质量。
实施生产线平衡的步骤1.确定生产线的结构:首先需要明确生产线中包含哪些工作站,以及它们之间的工作关系。
这有助于确定工作站之间的工作负荷平衡目标。
2.测量工作站的工作时间:对于每个工作站,需要测量其完成工作所需的具体时间。
这有助于了解每个工作站的工作负荷情况,为后续的平衡安排提供依据。
3.分配工作到每个工作站:根据上一步测量得到的工作时间,合理地分配工作到每个工作站。
将工作任务合理分配,并确保每个工作站的工作负荷均衡。
4.调整工作站的工作时间:如果发现某些工作站的工作负荷过重或过轻,可以适当调整工作站的工作时间,使得工作负荷达到平衡。
5.定期评估和调整:生产线平衡并非一次性的过程,而是需要定期评估和调整。
随着生产线上产品类型和数量的变化,需要及时地对生产线进行评估和调整,以保持生产线的平衡状态。
生产线平衡的技术
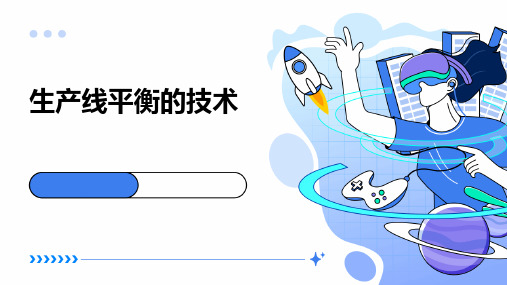
06
生产线平衡的未来
发展趋势
数字化与智能化技术的应用
01
物联网技术应用
通过物联网技术实现设备间的互联互通,提高生产线的透明度和协同效
率。
02
大数据分析与优化
运用大数据技术对生产线数据进行挖掘和分析,发现瓶颈环节并进行优
化。
03
人工智能与机器学习
应用人工智能和机器学习技术,实现生产线的自适应调整和智能化决策。
目的
消除作业间不平衡,提高生产线 的整体效率,降低成本,提高产 能。
生产线平衡的重要性
01
02
03
04
提高设备利用率
平衡的生产线可以减少设备空 闲时间,提高设备利用率。
降低在制品库存
减少工序间的等待时间和在制 品数量,降低在制品库存。
提高产品质量
减少工序间的等待和停滞,有 利于减少生产过程中的不良品
动。
04
05
生产线平衡的实践
应用
汽车制造行业的应用
总装线平衡
在汽车制造的总装线上,通过合理分配作业任务和时间,使得每个 工作站的节拍保持一致,提高生产效率。
焊接线平衡
针对汽车车身的焊接线,通过优化焊接工艺和布局,实现生产线的 平衡和高效运行。
涂装线平衡
在汽车涂装过程中,通过调整涂装设备的参数和工艺流程,确保生产 线各环节的协调和平衡。
04
05
利用物联网技术远程监控设 备状态,提前预警并安排维
护。
员工技能与培训不足
挑战:员工技能不足或缺乏培训 可能导致生产效率低下和产品质 量问题。
04
实施交叉培训,使员工能够掌握 多种技能,提高生产线的灵活性 。
01 03
生产线平衡

精益 IE第六讲: 生产线平衡精益 IE一、生产线平衡的概念生产线上的各道工序布置的效益取决于将所需工作划分成一系列 单元而工作的能力,而此单元工作能迅速而例行化地由技术工人 和专业设备来执行。
大部分的加工时间都很短,以至于只指定一 项工作给每个工人是很不实际的。
相反的,工作经常组成容易管 理的群组,并分发到一两位操作者的工序去。
平衡生产线(LineBalancing)指的就是这种分配 工作到各道工序上的决策过程,通过对人力、机械设备和工作任 务的恰当分配,使整个生产线达到平衡状态。
21精益 IE平衡生产线的注意点为了较容易地达到生产线的平衡,需要关注瓶颈工序的工序改 善,整个生产线的效率最容易受到瓶颈工序的限制,对瓶颈工序 予以平衡显得尤为必要。
通过对瓶颈工序的分析,拆分作业动 作,尽可能地将瓶颈工序的动作分配到其它工序,由前后道的工 序来帮助完成。
在进行动作分配之前,首先计算瓶颈工序内作业人员的人均产 量,如果负荷过重,可以增加必要的操作人员,以便提高工序的 平衡率。
瓶颈工序内增加的操作人员,可能来源于其它工序合并 或简化所减掉的操作人员,这样,整个生产线的人员并不需要增 加,只是将多余的人员分配到更需要人员的地方,从而达到整条 生产线的平衡,实现效率和效能的最大化。
3精益 IE生产线平衡的改善方法分担转移的方法 作业改善压缩的方法 加人缩短循环时间的方法 拆解去除的方法 重排的方法 作业改善后合并的方法42精益 IE1.分担转移的方法5精益 IE2.作业改善压缩的方法63精益 IE3.加人缩短循环时间的方法7精益 IE4.拆解去除的方法84精益 IE5.重排的方法9精益 IE6.作业改善后合并的方法105精益 IE案例11精益 IE改善分析这条生产线可以发现,瓶颈工序就是钻孔的工序。
针对这八道工序的特 点,分解工序3(钻孔)的作业动作,提出以下的平衡改善措施: 改善瓶颈作业(即工序3钻孔),将工序3的定位动作(8秒)分担给工序2完 成。
生产线平衡
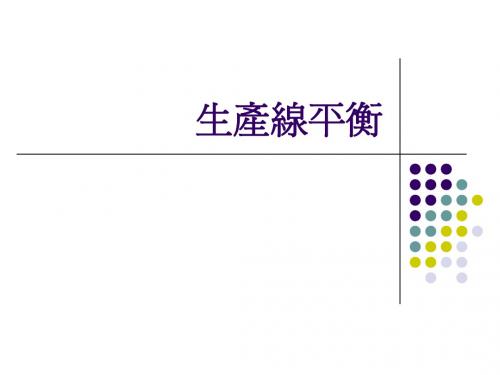
什麽是生產線平衡
生產線平衡就是指工程流動間或工序流動間 負荷之差距最小,流動順暢,減少因時間差 所造成之等待或滯留現象。
平衡的目的: 平衡的目的: 物流快速,減少生產周期。 減少或消除物料或半成品周轉場所。 消除工程“瓶頸”,提高作業效率。 穩定產品品質。 提升工作士氣,改善作業秩序。
生產綫平衡的標示法
工 作 時 間
缩短生产节拍
將工序2里一
工序 里﹐ 缩 生产节拍。
工序 1
2
3
4
5
生产线平衡-例 ﹕节减人手(1人 生产线平衡 例2﹕节减人手 人)
维持生产速率不变 工 作 時 間 节减人手(1) 节减人手(1)
將工序3里的工作时间分 工序 工序3里的人手 生产线 工序 时间 工作
工序 1
2
3
4
5
生产线平衡-例 ﹕节减人手(2人 生产线平衡 例3﹕节减人手 人)
须延缓生产速率 工 作 時 間 节减人手(2) 节减人手(2)
因生产需求量降低而可延缓 生产速率 2 生产线 而 人手可
1
2
3
4
5
生產線平衡,一般使用生產流動平衡來表示, 縱軸表示時間,橫軸表示工程順序,并標出其 標準時間,畫法可使用曲綫圖或柱狀圖。
生產線平衡分析主要相關要素
工程名:本工程的名稱或代號 各工程的標準時間 各工程的實測時間 節拍:根據生產計劃量所得出的一個工程所需 時間。 不平衡率:是指生產線個工程工作分割的不均 衡度。
節拍
净运作时间 / 时段 顾客需求 / 时段* 时段*
节拍时间= 节拍时间=
*时段必须要一致(班﹑日﹑周…)
舉例
可用时间 顾客需求 450 3000
生产线平衡的方法
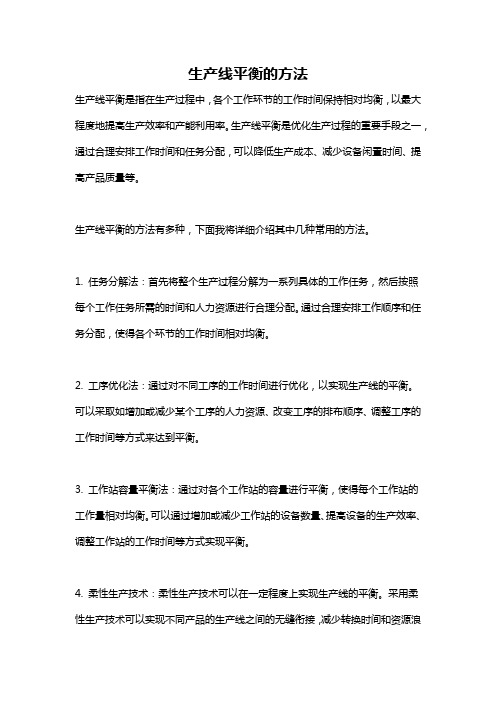
生产线平衡的方法生产线平衡是指在生产过程中,各个工作环节的工作时间保持相对均衡,以最大程度地提高生产效率和产能利用率。
生产线平衡是优化生产过程的重要手段之一,通过合理安排工作时间和任务分配,可以降低生产成本、减少设备闲置时间、提高产品质量等。
生产线平衡的方法有多种,下面我将详细介绍其中几种常用的方法。
1. 任务分解法:首先将整个生产过程分解为一系列具体的工作任务,然后按照每个工作任务所需的时间和人力资源进行合理分配。
通过合理安排工作顺序和任务分配,使得各个环节的工作时间相对均衡。
2. 工序优化法:通过对不同工序的工作时间进行优化,以实现生产线的平衡。
可以采取如增加或减少某个工序的人力资源、改变工序的排布顺序、调整工序的工作时间等方式来达到平衡。
3. 工作站容量平衡法:通过对各个工作站的容量进行平衡,使得每个工作站的工作量相对均衡。
可以通过增加或减少工作站的设备数量、提高设备的生产效率、调整工作站的工作时间等方式实现平衡。
4. 柔性生产技术:柔性生产技术可以在一定程度上实现生产线的平衡。
采用柔性生产技术可以实现不同产品的生产线之间的无缝衔接,减少转换时间和资源浪费,提高生产效率。
5. 连续改进与优化:生产线平衡是一个动态过程,需要不断进行改进和优化。
通过对生产过程的数据分析和绩效反馈,及时调整和优化生产线的各个环节,确保生产线保持平衡状态。
6. 人机协同:合理利用自动化设备和人力资源的协同作用,可以优化生产线的平衡。
自动化设备可以完成一些重复性和繁琐的工作,提高生产效率,而人力资源可以进行更复杂和灵活的操作和监测。
7. 合理的物料供应链管理:物料的及时供应是生产线平衡的关键之一。
合理管理供应链,保持物料的稳定供应,确保生产过程中不会出现因物料不足而导致的生产线不平衡问题。
总结起来,生产线平衡是一个综合性的问题,需要从多个方面进行考虑和优化。
通过任务分解、工序优化、工作站容量平衡等方法,结合柔性生产技术和人机协同,有效管理物料供应链,不断改进和优化生产线,可以实现生产线的平衡,提高生产效率和产能利用率。
精益化管理——line balance training(生产线平衡)
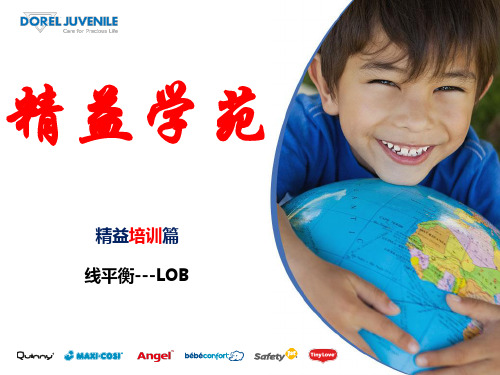
1. 生 定产义线平衡的定义 ② 瓶颈识别
时间 T1
一、定义
T2
瓶颈时间
T3
T4
T5
S1
S2
S3
S4
S5
生产线作业工时最长的工站的标准工时称之为瓶颈。 产出的速度取决于时间最长的工站
工站
一、定义
1. 生 定产义线平衡的定义
③ 节拍、增值时间、交付周期的定义
C/T
流程的“节拍”(Cycle time)是指连续完成同的两个产品(或两次服务,或两批
标准工时是一个熟练工用规定的作业方法以标准速度进行作业时间。 在熟练度、合理性、工作热情及其他所有方面都相同的“标准作业员”以标准的作业放 大及其合理的努力程度进行作业,完成某到工序所需的时间。
一、定义
1. 定义 ⑦ 标准工时的用途
科学化/高效化企业
企业发展与经营管理策略讨论参与
研发体系改善/咨询管理优化/企业流程再造
节拍
产品)之间的间隔时间。换句话说,即指完成一个产品所需的平均时间。节拍通
常只是用于定义一个流程中某一具体工序或环节的单位产出时间。如果产品必
须是成批制作的,则节拍指两批产品之间的间隔时间。在流程设计中,如果预
先给定了一个流程每天(或其它单位时间段)必须的产出,首先需要考虑的是流
程的节拍。
增值时间
增值时间(Valve-Creating Time,VCT) 产品生产过程中,客户愿意付费的工作时间(增值时间)。
平
衡
的
通过线平衡改善可以使用IE手法、动作分析、layout
意
义
实现单元化生产,柔性化生产,提升市场的应变能力
平衡员工心态,平衡工资水平,实现绩效合理化
生产线平衡

生产线平衡(line balance)什么是生产线平衡生产线平衡是依照流水线作业的工程顺序,以生产目标算出周期时间,将作业分割或者结合,使各个工序的负荷均匀,以提高生产效率的方法。
一个产品,少则两三个工程,多则几十个,而每个工程又是由多个作业要素所组成,在生产工场里,制造部门依物料的加工流程分为一组、二组、三组,而每组内又由许多的个别工序所组成,所以又把它联结成一条条的生产线。
流程的“节拍”(Cycle time)是指连续完成相同的两个产品(或两次服务,或两批产品)之间的间隔时间。
换句话说,即指完成一个产品所需的平均时间。
节拍通常只是用于定义一个流程中某一具体工序或环节的单位产出时间。
如果产品必须是成批制作的,则节拍指两批产品之间的间隔时间。
在流程设计中,如果预先给定了一个流程每天(或其它单位时间段)必须的产出,首先需要考虑的是流程的节拍。
而通常把一个流程中生产节拍最慢的环节叫做“瓶颈“。
流程中存在的瓶颈不仅限制了一个流程的产出速度,而且影响了其它环节生产能力的发挥。
更广义地讲,所谓瓶颈是指整个流程中制约产出的各种因素。
例如,在有些情况下,可能利用的人力不足、原材料不能及时到位、某环节设备发生故障、信息流阻滞等,都有可能成为瓶颈。
正如“瓶颈”的字面含义,一个瓶子瓶口大小决定着液体从中流出的速度,生产运作流程中的瓶颈则制约着整个流程的产出速度。
瓶颈还有可能“漂移”,取决于在特定时间段内生产的产品或使用的人力和设备。
因此在流程设计中和日后的日常生产运作中都需要引起足够的重视。
与节拍和瓶颈相关联的另一个概念是流程中的“空闲时间”空闲时间是指工作时间内没有执行有效工作任务的那段时间,可以指设备或人的时间。
当一个流程中各个工序的节拍不一致时,瓶颈工序以外的其它工序就会产生空闲时间。
这就需要对生产工艺进行平衡。
制造业的生产线多半是在进行了细分之后的多工序流水化连续作业生产线,此时由于分工作业,简化了作业难度,使作业熟练度容易提高,从而提高了作业效率。
生产线平衡
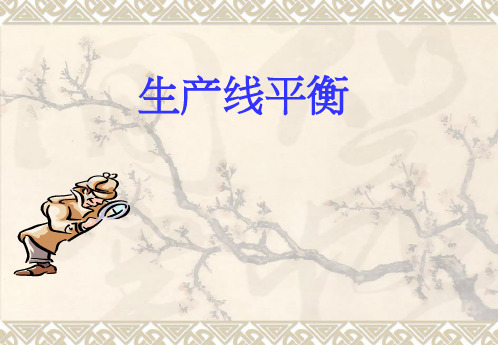
生产线负荷率在85%以上就可认为满意当达到90% 以上就可认为基本实现“一个流”
“一个流”生产追求理念:尊重人性的生 产方式,最大限度地适应市场变化
U型生产线 二字型生产线
皮带拉
加工设备独立
为了较容易地达到生产线的平衡,需要关注瓶颈 工序的工序改善,整个生产线的效率最容易受到瓶颈 工序的限制,对瓶颈工序予以平衡显得尤为必要。通 过对瓶颈工序的分析,拆分作业动作,尽可能地将瓶 颈工序的动作分配到其它工序,由前后道的工序来帮 助完成。
造成線上不平衡的主要問題
當傳送帶之速度遠慢於作業員的操作能力 • 低於計劃的產能 • 作業員無法積極作業,變得懶散 • 需要安排額外的工作時間以彌補未達成的產能 • 單位產品的成本增加 • 生產力降低 • 無法系統的控制和預估產能
1.分担转移的方法
分担转移的改善方法如图所示。在没有平衡改善前,工序1是整个作业过程的瓶颈工序。工序 1制约了整个生产,可以将工序1的一部分转移到工序2中。这样,整个作业的瓶颈工序变成了工序 5,但相对于原来的工序1来说,瓶颈口就相应地变宽了。
2中,从而大大提升整条生产线的平衡率。
6.作业改善后合并的方法
当用前面几种方法改善工序流程后,在重新思考新的工序之间是否还存在着合并的空间。 将可以合并的工序尽最大可能地合并和简化,这样,整条生产线的瓶颈自然也相应地越来越
少,使得平衡率和效率也能有效地得到持续的提升。如图10-6所示。
When are you going to finish your job????
I have been waiting so
long!!!!!!!!!你到底要 在什么时间才能做完, 我要等到什么时候?
造成在线不平衡的主要问题
生产线平衡

生产线平衡(line balance)什么是生产线平衡生产线平衡是依照流水线作业的工程顺序,以生产目标算出周期时间,将作业分割或者结合,使各个工序的负荷均匀,以提高生产效率的方法。
一个产品,少则两三个工程,多则几十个,而每个工程又是由多个作业要素所组成,在生产工场里,制造部门依物料的加工流程分为一组、二组、三组,而每组内又由许多的个别工序所组成,所以又把它联结成一条条的生产线。
流程的“节拍”(Cycle time)是指连续完成相同的两个产品(或两次服务,或两批产品)之间的间隔时间。
换句话说,即指完成一个产品所需的平均时间。
节拍通常只是用于定义一个流程中某一具体工序或环节的单位产出时间。
如果产品必须是成批制作的,则节拍指两批产品之间的间隔时间。
在流程设计中,如果预先给定了一个流程每天(或其它单位时间段)必须的产出,首先需要考虑的是流程的节拍。
而通常把一个流程中生产节拍最慢的环节叫做“瓶颈“。
流程中存在的瓶颈不仅限制了一个流程的产出速度,而且影响了其它环节生产能力的发挥。
更广义地讲,所谓瓶颈是指整个流程中制约产出的各种因素。
例如,在有些情况下,可能利用的人力不足、原材料不能及时到位、某环节设备发生故障、信息流阻滞等,都有可能成为瓶颈。
正如“瓶颈”的字面含义,一个瓶子瓶口大小决定着液体从中流出的速度,生产运作流程中的瓶颈则制约着整个流程的产出速度。
瓶颈还有可能“漂移”,取决于在特定时间段内生产的产品或使用的人力和设备。
因此在流程设计中和日后的日常生产运作中都需要引起足够的重视。
与节拍和瓶颈相关联的另一个概念是流程中的“空闲时间”空闲时间是指工作时间内没有执行有效工作任务的那段时间,可以指设备或人的时间。
当一个流程中各个工序的节拍不一致时,瓶颈工序以外的其它工序就会产生空闲时间。
这就需要对生产工艺进行平衡。
制造业的生产线多半是在进行了细分之后的多工序流水化连续作业生产线,此时由于分工作业,简化了作业难度,使作业熟练度容易提高,从而提高了作业效率。
产线平衡4大原则

产线平衡的概念和重要性产线平衡是指在生产过程中,合理分配工作任务和资源,使各工作站的工作负荷相对均衡。
它是提高生产效率、降低生产成本的重要手段之一。
下面将介绍产线平衡的4大原则。
1. 原则一:任务分配均衡任务分配均衡是指在产线上将任务合理地分配给各工作站,使得各工作站的工作负荷相对均衡。
具体来说,应该根据各工作站的工作能力和工作时间,合理分配任务数量和难度,避免某个工作站过多或过少的工作负荷,以确保整个产线的平衡运转。
2. 原则二:工作站节拍一致工作站节拍一致是指各工作站完成任务的速度要保持一致。
在产线平衡中,如果某个工作站的节拍过快,可能导致前后工作站的任务堆积,造成生产过程中的瓶颈;而如果某个工作站的节拍过慢,可能会导致其他工作站的闲置和资源浪费。
因此,保持工作站节拍一致是产线平衡的重要原则之一。
3. 原则三:资源合理利用资源合理利用是指在产线平衡中,要充分利用各种资源,包括设备、人员和材料,以确保生产过程的高效运转。
具体来说,应根据各工作站的实际需求合理配置资源,避免资源的浪费和不足。
例如,合理安排设备的使用时间,避免设备闲置或过度负荷;合理安排人员的分配,避免人员闲置或过度疲劳;合理控制材料的供应,避免材料的堆积或短缺。
4. 原则四:持续改进持续改进是产线平衡的关键原则之一。
生产过程中,市场需求和技术环境都在不断变化,因此,产线平衡需要不断审视和优化。
通过对生产过程的监控和数据分析,发现问题并及时采取改进措施,以实现产线的持续改进和优化。
例如,通过改进工作站的工艺流程、调整任务分配、优化资源配置等方式,不断提高产线的效率和质量。
结论产线平衡的4大原则包括任务分配均衡、工作站节拍一致、资源合理利用和持续改进。
这些原则的遵循和实施,可以提高产线的效率、降低生产成本、提高产品质量,从而为企业的发展和竞争提供有力支持。
产线平衡是一个复杂而重要的管理问题,需要综合考虑各种因素,并不断优化和改进。
- 1、下载文档前请自行甄别文档内容的完整性,平台不提供额外的编辑、内容补充、找答案等附加服务。
- 2、"仅部分预览"的文档,不可在线预览部分如存在完整性等问题,可反馈申请退款(可完整预览的文档不适用该条件!)。
- 3、如文档侵犯您的权益,请联系客服反馈,我们会尽快为您处理(人工客服工作时间:9:00-18:30)。
作业员在一周期时间 内可操作许多机器
调查故障,或者是 异常的根本原因
仅供给「良品」
人力操作和机器 作业可以分离
「指示灯」点亮
必要的数量或者 是作业完成,机 器会自动停止
故障被发觉之后, 机器会自动停止
自动化=偏差(异常)发觉后机器会自动停止
12
「省人化」的过程
「少人化」 为适应需要品的变动,对各制程作业人数作弹性变化
基础的改善
运用5S,现 时现地现物管 理,清除浪费
成本降低的整体 实现
通过VA/VE及流
程改善做最佳組
合
3
2. 造成成本高涨的因果图
第一次浪费 ① 设备过剩 ② 库存过剩 ③ 人员过剩
第二次浪费 生产过多浪费
多余折旧费用 多余的保养费用 多余的利息费用 多余的劳务费用
第三次浪费 库存过剩的浪费
第四次浪费 ①多余的仓库 ②多余的搬运人员 ③多余的搬运设备 ④多余的库存管理人员、
小集团活动
人的作业改善 机器的改善(自动化) 材料消耗品使用上的改善 QCC 提案
制度
改善的动机
看板制度
14
二. 工程分析及编排要点
1、工程分析
所谓的工程分析就是依照工程顺序为 了达成生产效果,把设备和人配置在连续 生产线的作业区域内所安排的设计。
15
2、工程分析的必要性
(一)投入新产品的大量生产。 (二)虽然是生产线生产,但经常更换形式,有
外协批量改善 简化生产的设计
易于生产的设计
设计更改的最优化
工序布局的改善 工具、夹具改善
5
加工条件最优化
S
机械设备故障和不良的排除 和
目视管理
减
自动化
少
批次大小最优化
浪
提高作业人员技能 日程计划和进度的管理
费
5
4. 生产管理的全貌
营销业务 客户讯息往来 确认订单
预测订单情况 销售计划
产品负责人 订单、出货管理
N.B = ((5 x 39) - 182 ) / 5 x 39) x 100% = 7.1 % 不平衡率降低.少一人˙
19
(F)流程布置(Lay Out)
a.搬运次数最少 b.搬运距离最短 c.弹性化安排,调整容易 d.安全为原则 (1)需要空间 (2)传送工具 (3)防火、防水、防震、噪音隔离 e.管理的容易性 f.与周边工程的关连性 g.作业性 h.治工具、半成品(WIP)等的置放区
一个流生产的魅力在那里?
(1)及早暴露潜在的问题 (2)迫使管理层面对各项问题 (3)实实在在的减少各种浪费 (4)发挥「事半功倍」的最佳生产力 (5)快速反应,交期较快 (6)为自动化流程建立基础
39
一个流交期最快
接
投
单
产
入
出
收
库
货
货
生产交期
出货交期 收货交期
9
SDCA 与 PDCA
PD AC
現有 水準
PD AC
SD AC
SD AC
具體落實的方法:QC Story
SD AC
期望 水準
S:標準化程序,SOP (P:Plan計劃)
D:Do執行 C:Check檢查 A:Action行動
‧維持:(Standardization)DCA 依標準SOP而DCA
‧改善:I(Improvement)DCA 依改善之計劃而DCA
结果
• 高成本 • 低品质 • 低利润 • 反应慢 • 竞争力低 • 少创新
结局
企 业 没 有 明 天
28
迈向一个流的流线生产
传统的批量生产方式的结果 一个流的流线生产方式
• 将产品之加工工程连接起来,并以生产一个、流动 一个的方式来作业的生产方式
29
四. 一个流流线生产的特色与优点
产品别垂直式布置 多能工,多工序操作 整流生产,源流清楚 设备速度适当,小型化,专用化 后拉式,一个流生产
36
五. 一个流的生产方式
流线生产的演变过程 一个流生产的魅力在那里 ? 一个流交期最快 快速反应,交期最快
37
流线生产演变过程
第一步 传统功能别布置 第二步 产品别流线布置 第三步 粗的流线生产方式 第四步 细的流线生产方式 第五步 冒牌的一个流生产方式 第六步 正统的一个流生产方式
38
场区空间分析
•作业空间 •保管空间
装配顺序的决定
时间分析
主线、副线区分 编成条件分析
•优先顺位 •作业位置 •设备
生产线平衡 (工程分割结合)
所要工程数
所要作业人员
人员编成
全面工厂 布置计划
生产计划 规制时间推算
产品的尺寸 作业性其他 工程间隔 生产线长度
搬运设备选定
生产线布置设计
工厂 布置原则
稼动时间 预测不良率等
品质管理及保证
改善质量,提供 质量保证
车间之间的协调
以满足顾客为目标, 以“下一道工序是 客户”的认知,推 动车间之间的协调
用“生产管 理”改善和 改变工厂, 完成做强做 大的目标
保证及缩短交期 创建-灵活及可 目视管理的工厂
最低库存 确保库存最低量, 没有无用或多余 东西
个别工序的改善
让每个人都成为多 能高手,提高个人 的改善意识和技巧
22
功能别,水平式布置
按功能分别摆放机台 需要搬运来连接 尽量减少搬运次数 每次搬运批量大
等待加工半成品增加
延
在厂 不
增
长
制房 良
加
时车
品面 品
管
间间
数积 批
理
流
量大 量
难
程
大
大
度
23
产能不平均,产生乱流
不同工序,速度不一 为达平衡,不同工序,机器数量不同
「乱流」现象产生 源流不清楚
无法找出不良原因
必要重新安排。 (三)虽然使用批量生产,因生产量增加,有必
要改用生产线化。 (四)现在实施生产线生产,由于产品一部分变
更,修正工程分析必要。 (五)工序间的负荷不平衡,要改善生产线,其
工程分析的顺序或重点会改变其编排。
16
3、生产线工程分析及编排要点
(A)装配顺序的考量。 (B)时间的分析。 (C)主生产线和副生产线串联。 (D)必要条件的分析:
设备速度适当、小型化、专用化
适当速度 速度适当即可 小型化 生产一个最好 专用化 专用机器
可动率高
零成品库存
价格低廉,可自行制造
追求可动率,稼动率由市场决定 为市场需求而生产 JIT及时生产方式
减 设少 备仓
储
容 成易 本管 低理
,
保流 证动 品迅 质速
,
的 库 存
没 有 睡 觉
投 最资 佳效
益
35
多
解
多
较
容
重
决
种
难
易
制
问
问
原找
产
程
题
题
因出
生
抽
费
并
问
误
检
时
发
题
判
24
单能工,多机台操作
功能水平式布置 作业员,操作单一工序
单能工 一人同工序多机台操作
只
人
熟
数 固
序
练 单
定
一
工
自 扫 门 前 雪
追 求 高 速 机 台
追 求 个 别 效 率
缺乏广变市场的能力
25
前推式,大批量生产
①
②
前工程有空有货便做, 不管后工程是否需要
输送带上 的产品间隔 生产线速度
产品特性 作业特性
7
缩短准备时间方法
步骤1 对准备作业分析,把内部作业准备和外部作业准备 区分开来。
步骤2 分开外部作业准备,尽可能进行外部作业准备,缩 短机械停待的时间。
步骤3 改善内部作业准备,缩短准备的时间。 工具的改善 确定下一个要加工零部件的摆放位置 确定加工完毕零部件的摆放位置 改善零部件的装卸方法 减少调整作业 对于模具、夹具之高度,可进行标准化
工作點總數 x 耗時最多工作點數標準工時
18
範例
工作點
1 2 34 5 6
標準工時(秒) 29 23 20 37 39 34
N.B=((6 x 39) - 182) / 6 * 39) x 100% = 22%
如將1.2.3合併並改由兩人操作則
工作點
123 4 5 6
標準工時(秒) 36 x 2 37 39 34
a.优先顺序位分析 b.作业位置分析 c.设备限制分析 (E)生产线平衡(Line Balance)
17
生產線平衡
1.測定標準工時 2.決定不平衡率(N.B)-----目標為 5% 以下
(工作總點數*耗時最多工作點之標準工時 ) --工作總工時 不平衡率 = --------------------------------------------------------------------------- x 100%
研发设计部门 研发设计 技术资料整理
生产管理部门
大日程计划
材料计划
产能负荷计划
中日程计划
发行作业指示书
制造工程部门 生产技术、安排、作业指导书
采购
外购、外发、计划, 库存管理
制造部门 小日程管理/作业指导 进度/在制/工具/品质管理
质量管理 成本管理
6
5、装配生产线安排流程
图面
试作
出勤率其他
支援人员 间接人员
生产线平衡的秘笈
1
一. 生產綫平衡概要
没有赚钱的企业是罪恶 ~松下幸之助~