基于DEFORM的数控钻削仿真研究
基于Deform仿真平台的铣削加工切削深度和进给速度分析

先通过UG软件构建尺寸为φ=0.4mm其导入ABAQUS内完成建模过程。
为提高计算精度与处理效率,对工件结构进行简化得到图2所示的结果。
具体包含了以下各仿真步骤:高的运算效率,将质量缩放因子设定在10。
2仿真结果分析图3显示了在铣削期间发生切屑脱落而造成温度与切屑的改变情况。
可以明显看到,铣削加工切削温度在刀面处获得最高的温度,这是因为铣削时在刀面处会产生明显的摩擦生热现象,产生很多的热量进而转变成刀具的温度,只剩下少量热量会残留于工件上,应重点对最高切削温度进行研究。
切削深度处于恒定的进给速率与进给速度条件下,随着切削深度的变化,将会引起工件达到不同的温度。
从图1000r/min转速下设定进给速度为10mm/min0.01~0.05mm的切削深度范围内工件形成的最高温度。
图1摩擦接触模型图2工件与刀具装配关系图3铣削切削过程图4温度随切削深度变化情况根据图4可知,当切削深度增大后,将会引起切削温度的升高,这是由于当切深度增大后,将会引起切削部位形成更多的热量,同时获得更大的切屑长度、体积与表面由此得到不同的加工环境,导致切削温度不会发生同等比例的提高。
2.2进给速度图5显示了在其它参数恒定的状态下,在不同的进给速度下切削温度发生的改变。
可以发现,切削温度同样受到进给速度的较大影响,当进给速度逐渐增大后,切削温度开始上升,而在达到某一临界值后,切削温度发生降低的现象,最大值发生在进给速度20mm/min时。
这是因为在更大进给速度下,将会引起材料去除体积的显著增加,从而造成热量积累,但增加幅度变化相对稳定,甚至发生降低的情况。
进给速度增大,会引起切削温度的上升,同时表现为温度上升速率不断增大的特征,产生这一变化趋势的原因是切削热来自第一变形区塑性变形过程以及刀具发生摩擦时产生的热量,大部分切削热都是出现在靠近刀具面的3结论先通过UG软件构建刀具,再将其导入ABAQUS成建模过程。
仿真结果得到:①铣削加工切削温度在刀面处获得最高的温度,这是因为铣削时在刀面处会产生明显的摩擦生热现象,产生很多的热量进而转变成刀具的温度。
基于deform—3d车削TC4加工过程仿真

基于deform—3d车削TC4加工过程仿真作者:陈卓来源:《科技视界》2016年第19期[摘要]Deform-3D是一套基于工艺模拟系统的有限元仿真(FEM)软件,是模拟3D材料流动的理想工具。
它不仅鲁棒性好,而且易于使用。
借助于该模拟分析环境,能够对切削过程中切削条件以及加工过程中的其他因素产生的影响进行研究。
应用DEFORM-3D自带的切削仿真模型,分析加工过程中工件对不同刀具的影响,以及对切削力、切削温度、切削应力结果进行分析。
模拟结果对减少产品试验、降低开发成本、缩短开发新产品及新工艺的时间等方面都具有重大意义。
[关键词]车削;Deform-3D;切削力;切削温度;切削参数0引言金属切削过程是一个非常复杂的工艺过程,它涉及到弹性力学、塑性力学、断裂力学、热力学、摩擦学等多个学科,刀具形状,温度分布、刀具磨损等因素都会对切削过程产生重要影响。
因此利用传统的解析方法,很难对切削过程进行分析和研究,但随着现代制造技术和计算机软件技术的不断进步,出现了很多针对金属切削过程进行数值模拟和仿真的软件,如DEFORM、ANSYS、ABAQUS等等,为金属切削过程仿真提供了非常有效的方法和技术手段。
本文选择三维有限元软件DEFORM,以硬质合金刀具切削钛合金TC4作为研究对象,对切削过程进行仿真,利用控制变量的方法得出了刀片在不同切削参数下的切削力、切削温度、以及切削应力的影响。
1有限元模型的建立1.1几何模型及仿真参数设置使用有限元分析软件DEFORM-3D模拟分析车削钛合金的加工过程,应用DEFORM-3D 中的Machining(Cutting)模块进行建模。
建立的切削模型如图1所示。
本分析中是直接从Deform封装的刀片库中选取刀片,所选取的刀片代号是CNMA432。
模拟过程中关于网格划分方面,DEFORM-3D提供了两种网格划分方式,分别为相对网格划分方式和绝对网格划分方式。
本文中工件采用的是绝对网格类型,最大网格单元尺寸和最小网格单元尺寸之比为7。
DEFORM钻削

第十二章钻削本章导读:钻削加工是孔加工的一种基本方法,在航空航天、汽车制造、电子等领域中的应用非常广泛,孔加工量约占机械加工总量的30%。
钻削力、钻削温度等参数对钻削加工性能有着重要的影响,因此有必要对钻孔机理进行深入的研究,模拟钻削过程对生产加工制造具有指导性意义。
Dform-3D自带有模拟钻削过程的模块,方便用户设置前处理参数。
本章在钻削模块中进行了钻削过程的模拟,并总结了钻削模拟过程中易出现的问题和解决方法。
12.1 钻削模块简介用户进入钻削模块后,只需根据提示输入模拟所需的参数即可。
该过程包括进入钻削前处理界面、设置钻削运动参数、添加钻头及工件模型、划分网格、设置模拟参数、生成数据、模拟运算、后处理。
12.2前处理本章对标准麻花钻钻孔过程进行了模拟,加工参数为:钻头直径d=6mm,转速n=1000r/min,进给量f=0.3mm/rev。
麻花钻材料为WC硬质合金,工件材料为AISI-1045(对应国标牌号为45号钢)。
12.2.1 新建项目打开DEFORM-3D软件,进入DEFORM-3D主界面,单击【File】→【New Problem】,选择【Guided templates】中的【Machining[Cutting]】,SI单位制,如图12-1所示。
图12-1 新建项目单击【Next>】,默认存储位置。
Problem name定义为Drilling,单击【Finish】进入切削加工前处理界面,如图12-2所示。
图12-3 前处理界面12.2.2 钻削参数设置Project name(项目名)默认,确定单位制为SI,单击【Next>】,Operation Name默认。
单击【Next>】,加工方式选择钻削【Drilling】,如图12-3所示。
图12-4 选择加工方式单击【Next>】对钻削运动参数进行设置,本例中设置n=1000r/min,进给量f=0.3mm/r,如图12-4所示。
DEFORM的车削仿真案例
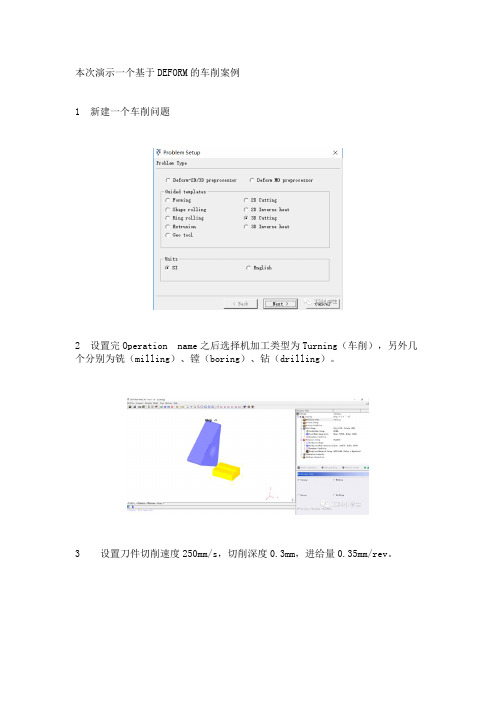
本次演示一个基于DEFORM的车削案例1 新建一个车削问题2 设置完Operation name之后选择机加工类型为Turning(车削),另外几个分别为铣(milling)、镗(boring)、钻(drilling)。
3 设置刀件切削速度250mm/s,切削深度0.3mm,进给量0.35mm/rev。
4 设置环境温度为20℃,空气对流传热系数保持默认,摩擦系数设为剪切摩擦0.5,刀件与工件的传热系数设为45.5 选择系统内置的TNMA332刀具,当然用户也可以通过Define a new tool来导入自己的刀具模型,支持STL格式。
通过Edit position来调整刀具的位置。
6 选择车刀角度,Side cutting Angle(主偏角)back rake angle 前角side rake angle副前角,除了导入自带的参数,用户可以通过Create a new toolholder自己设置对应参数。
具体这些参数修改会有什么变化如下图所示:7 给车刀划分网格8 设置工件基本参数。
9 设置工件长度为7mm。
Curved model可以生成一个圆环。
当然也可以通过Import Geometry来自己导入工件模型。
10 给工件划分网格,设置最小单元尺寸为0.06mm,尺寸比例为7。
11 给工件赋予材料,通过Import material from liabrary从材料库中导入相应材料。
12 设置模拟步数为10000,每25步存储一次,规定切削长度为3.5mm,也就是工件的一半长度。
注意,当设置了切削长度,那么步数就无效了,可以尽可能往大了设,当满足切削长度之后程序自动停止。
下面的刀具磨损模型采用的Usui模型,具体参数需要参照实验校准,其与所使用的材料和车削工艺有关。
13 查看结果后处理可以查看切削过程中,应力,应变,温度等的变化以及切屑的形态。
等效应力的变化等效应变的变化温度的变化。
基于DEFORM-3D的钛合金车削加工过程分析-毕业论文
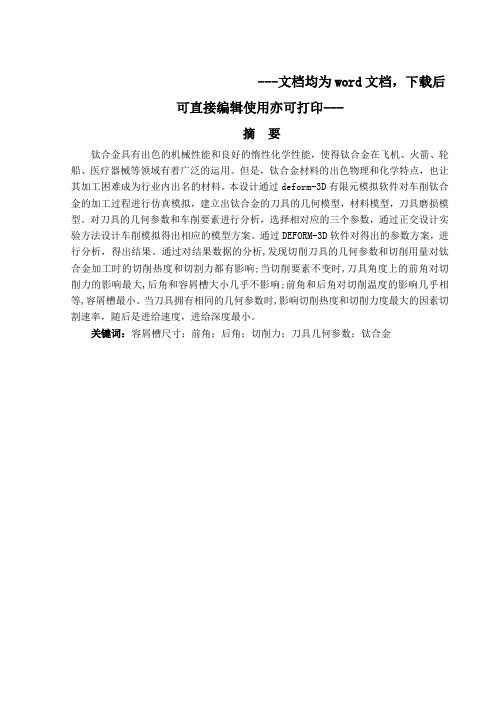
---文档均为word文档,下载后可直接编辑使用亦可打印---摘要钛合金具有出色的机械性能和良好的惰性化学性能,使得钛合金在飞机、火箭、轮船、医疗器械等领域有着广泛的运用。
但是,钛合金材料的出色物理和化学特点,也让其加工困难成为行业内出名的材料。
本设计通过deform-3D有限元模拟软件对车削钛合金的加工过程进行仿真模拟,建立出钛合金的刀具的几何模型,材料模型,刀具磨损模型。
对刀具的几何参数和车削要素进行分析,选择相对应的三个参数,通过正交设计实验方法设计车削模拟得出相应的模型方案。
通过DEFORM-3D软件对得出的参数方案,进行分析,得出结果。
通过对结果数据的分析,发现切削刀具的几何参数和切削用量对钛合金加工时的切削热度和切割力都有影响;当切削要素不变时,刀具角度上的前角对切削力的影响最大,后角和容屑槽大小几乎不影响;前角和后角对切削温度的影响几乎相等,容屑槽最小。
当刀具拥有相同的几何参数时,影响切削热度和切削力度最大的因素切割速率,随后是进给速度,进给深度最小。
关键词:容屑槽尺寸;前角;后角;切削力;刀具几何参数;钛合金目录1 绪论 (1)1.1本设计的目的、意义 (1)1.2本设计在国内外的发展概况及存在的问题 (2)1.3本设计应解决的主要问题 (3)2基于DEFORM-3D的钛合金车削加工过程分析 (3)2.1有限元模型的建立 (4)2.2刀具几何参数对切削力,切削温度影响的三维正交实验设计 (8)2.2.1 钛合金的车削参数选择 (8)2.2.2 正交设计变量的确定 (9)2.2.3正交试验设计方案 (9)2.2.4后处理结果对比分析 (10)2.2.5数据分析处理 (13)2.3切削用量对切削温度和切削力影响的三维正交试验分析 (15)2.3.1 钛合金的车削参数选择 (15)2.3.2 正交设计变量的确定 (15)2.3.3正交实验安排 (16)2.3.4后处理结果对比分析 (16)2.3.5数据分析处理 (20)3结论 (22)参考文献 (23)谢辞 (24)1 绪论在上世纪50年代初,钛合金被开发成为一种结构重要的金属,是具有出色的机械性能和良好的惰性化学性能的金属。
基于Deform3D的钻削力仿真研究

物体内部关系 (inter object Definition) 的目的是 定义仿真过程中不同的物体间的相互作用 。设刀具 为主动 ,工件为从动 。定义导热系数 45N/ sec/ mm/ C 和摩擦系数为常量 013 ,摩擦类型为剪切摩擦 ,该类 型可应用于大多数的变形仿真 。摩擦模型为 : fs =
图 1 工件局部网格划分
工件材料选为 ANSI - 1045 钢 (同 45 钢) ,钻头 沿 - Z 轴进给 ,进给量为 012mm/ r ,转动中心为 (0 ,0 , 0) (转动中心随进给运动的变化而变 ,此为初值) , 转速为 320r/ min ,转向为 (0 ,0 ,1) 。
在边界 (Object Boundary Condition (BCC) ) 设 置 中 ,BCC 定义了一个物体的边界如何与另一个物体 或环境相互作用 。设置工件四个侧面的速度在 X 、 Y 、Z 方向上为 0 ,限制工件的运动 ,工件和刀具的所 有面设定为与外界传热 ( Heat Exchange With Environ2 ment) ,激活工件的体积补偿选项 。
图 2 ALE 中自由面
52
工具技术
这个步数表示的是仿真引擎预测切屑几何形状和稳 态下热力求解的迭代次数 。
215 Lagrangian 分析( 瞬态分析) Lagrangian 公式的优点在于 :切屑是仿真的结果 并简化了瞬态切削过程和连续切屑形成的方案[6] 。 切削加工过程是一个不断变化的过程 ,每一时刻都 只能按照瞬态过程处理 ,因此继续运行瞬态分析 ,完 成最终的切削 。 216 钻头的应力分析 应力分 析 可 以 使 用 模 具 应 力 分 析 模 板 ( Die Stress Analysis Wizard) ,也可以参照模板生成的 key 文件 ,在前处理模块进行设置 。需要注意的是 ,选定 开始分析的步数必须是正的 。 217 Deform 3D2post 分析结束后 ,可在 Deform 3D2post 模块中查看切 削力 、切削温度 、刀具摩损以及应力等参数的仿真结 果 ,并能输出相关数据进行分析 ,如钻头应力的等值 线图 (图 3) 、钻削过程仿真图 (图 4) 等 。
基于DEFORM的数控切削加工工艺参数优化

浅析基于DEF0RM的数控切削加工工艺参数优化口李宾口李蓓智口杨建国东华大学机械工程学院上海201620摘要:应用大型商用有限元分析软件DEFORM一3D建立了三维切削模型并对数控车削切削力等进行了模拟分析,与经验公式、实际值进行对比验证其准确性。
在此基础上提出基于DEFORM~3D数控切削加工工艺参数优化的可行性。
关键词:DEFORM有限元法切削力工艺参数优化中图分类号:TP391.73;TG501.2文献标识码:B文章编号:1000一4998(2007)05—0053—03切削加工是机械制造行业中应用最广的金属成形工艺,世界各国投入了大量的人力和物力用于切削加工的机理研究。
考虑在切削过程中各影响因素建立综合的数学一力学模型,对切削过程进行全面分析,预测在不同切削条件下所产生的切削力,以指导机床、夹具、刀具等的设计与制造,合理地选择工艺参数中的切削速度、切削深度及进给量;对刀具几何参数(前角,后角等)进行优化设计,减小切削力,提高金属切除效率并改善加工表面质量,优化加工工艺等。
现实中,切削力的预报与计算均采用基于试验的经验公式。
近年来,随着计算机性能和运算速度的迅速提高以及有限元法应用的日趋成熟与完善,并与其它技术相结合取得了较大进展,如自适应网格划分、三维场建模求解、耦合问题和开域问题等,有限元法在求解非线性和多场耦合方面的强大功能也日益明显。
与此同时,我国数控机床的使用日益增多,而机床的利用率远不如我们预想的那样。
如何最大限度地发挥机床的潜力,已成为一个紧迫的问题。
笔者利用大型商用有限元软件DEFORM3D对数控车削加工过程进行模拟仿真,充分考虑到在切削模拟过程中的刀具几何参数(刀片几何角度)及车削加工切削用量等工艺参数的实际情况,进行了车削过程切削力、应力应变模拟;讨论了车削工艺参数与加工过程切削力、应力一应变等的关系。
期望可以对实际加工工艺参数的选取和改进提供理论上的依据。
1基于DEFORM的切削模拟1.1关于DEFORM美国科学成型技术公司(scient浓cFonningTech—nologiescorporation)的大型有限元分析软件DEFORM3D—v5.0中含有切削分析模块Machiningwizard。
基于Deform-3D对手钻钻体预锻件的模拟加工处理。

(STL/SLA)格式。 集成有成形设备模型,如:液压压力机,锤锻机、螺旋
压力机、机械压力机等。 (6)表面压力边界条件处理功能适用于解决胀形工艺
模拟。
单步模具应力分析方便快捷,适用于多个变形体、组合 模具、带有预应力环时的成型过程分析。
材料模型有弹性、钢塑性、热弹塑性、热刚黏塑性、粉 末材料、刚性材料及自定义类型。
实体之间或实体内部的热交换分析既可以单独求解,也 可以耦合在成行模拟中进行分析。
具有FLOWNET和点迹示踪、变形、云图、矢量图、 力——行程曲线等后处理功能。
Deform-3D的特点
Deform-3D是在一个集成环境内综合建模、成形、热 传导和成形设备特性进行模拟仿真分析。适用于热、冷、 温成形,提供极有价值的工艺分析数据。如:材料流动、 模具填充、锻造负荷、模具应力、晶粒流动、金属微结 构和缺陷产生发展情况等Deform-3D处理的对象为复 杂的三维零件、模具等。
3 成型过程的模拟
图1 手工电钻钻体结构尺寸图 图2 手工电钻钻体预锻件结构图
(a)结构尺寸图 (b)实体图 图3 预锻件
(a)结构尺寸图
(b)实体图Leabharlann 图4 坯料模拟前处理
图5 锻压原理图 图6 锻压模型图
(a)第1步 (b)第100步 (c)第200步 图7 锻压运动过程
模拟后处理
图8 应力图
基于Deform-3D对手钻钻体 预锻件的模拟处理
1 课题的研究背景及意义
锻造的定义
锻造是一种利用锻压机械对金属坯料施加压 力,使其产生塑性变形以获得具有一定机械 性能、一定形状和尺寸锻件的加工方法,锻 压(锻造与冲压)的两大组成部分之一。通 过锻造能消除金属在冶炼过程中产生的铸态 疏松等缺陷,优化微观组织结构,同时由于 保存了完整的金属流线,锻件的机械性能一 般优于同样材料的铸件。相关机械中负载高、 工作条件严峻的重要零件,除形状较简单的 可用轧制的板材、型材或焊接件外,多采用 锻件。
基于DEFORM—3D的螺旋锥面钻尖的钻削仿真分析
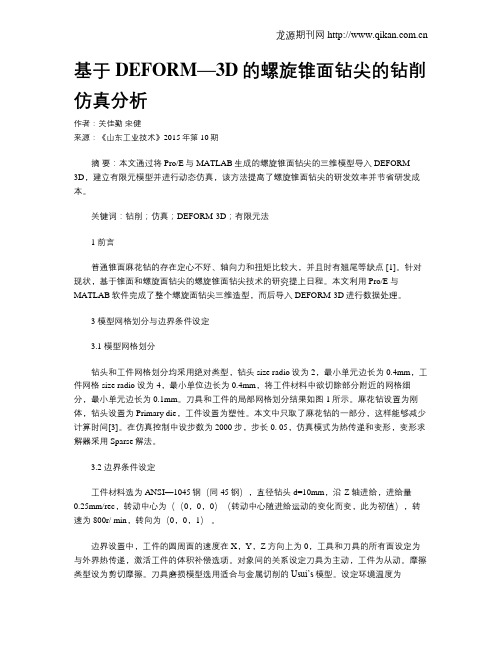
基于DEFORM—3D的螺旋锥面钻尖的钻削仿真分析作者:关佳勤宋健来源:《山东工业技术》2015年第10期摘要:本文通过将Pro/E与MATLAB生成的螺旋锥面钻尖的三维模型导入DEFORM-3D,建立有限元模型并进行动态仿真,该方法提高了螺旋锥面钻尖的研发效率并节省研发成本。
关键词:钻削;仿真;DEFORM-3D;有限元法1 前言普通锥面麻花钻的存在定心不好、轴向力和扭矩比较大,并且时有翘尾等缺点 [1]。
针对现状,基于锥面和螺旋面钻尖的螺旋锥面钻尖技术的研究提上日程。
本文利用Pro/E与MATLAB软件完成了整个螺旋面钻尖三维造型,而后导入DEFORM-3D进行数据处理。
3 模型网格划分与边界条件设定3.1 模型网格划分钻头和工件网格划分均采用绝对类型,钻头size radio设为2,最小单元边长为0.4mm,工件网格size radio 设为4,最小单位边长为0.4mm,将工件材料中欲切除部分附近的网格细分,最小单元边长为0.1mm。
刀具和工件的局部网格划分结果如图1所示。
麻花钻设置为刚体,钻头设置为Primary die,工件设置为塑性。
本文中只取了麻花钻的一部分,这样能够减少计算时间[3]。
在仿真控制中设步数为2000步,步长0. 05,仿真模式为热传递和变形,变形求解器采用Sparse解法。
3.2 边界条件设定工件材料选为ANSI—1045钢(同45钢),直径钻头d=10mm,沿-Z轴进给,进给量0.25mm/rec,转动中心为((0,0,0)(转动中心随进给运动的变化而变,此为初值),转速为800r/ min,转向为(0,0,1)。
边界设置中,工件的圆周面的速度在X,Y,Z方向上为0,工具和刀具的所有面设定为与外界热传递,激活工件的体积补偿选项。
对象间的关系设定刀具为主动,工件为从动。
摩擦类型设为剪切摩擦。
刀具磨损模型选用适合与金属切削的Usui’s模型。
设定环境温度为20℃,对流系数为0.02N/sec/mm/C,热传导系数为45N/sec/mm/C。
基于Deform3D的铣削力仿真试验验证研究
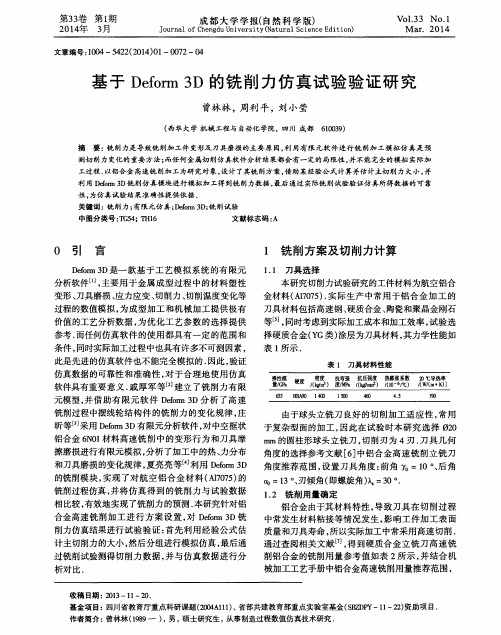
曾林林 , 等: 基于D e f o r m 3 D的铣 削 力仿 真 试验 验证研 究
表 5 试 验 铣 削 力统 计 表
・7 5・
切削力 进给抗力 , N 及 分组 情 况 变化区问 均值
主切削 力F y / N
切深抗力 F z I N
4 结 语
第3 3 卷 1 期 2 0 1 4 年 第 3 月
J o u r n a l o f C h e n g d u U n i v e r s i t y ( N a t u r a l S c i e n c eห้องสมุดไป่ตู้ E d i t i o n )
成 都 大 学 学 报( 自然 科 学 版)
1 . 2 铣 削 用量 确定
合金高速铣削加工进行方 案设置 , 对D e f o m r 3 D铣 削力仿 真结 果进行 试 验 验 证 : 首 先 利用 经 验 公 式 估
计主切削力的大小 , 然后分组进行模拟仿真 , 最后通 过铣削试验测得切削力数据 , 并与仿 真数据进行分 析对 比 .
( 西华 大学 机械 工程 与 自动化 学院,四川 成都
摘
6 1 0 0 3 9 )
要: 铣 削力是 导致铣 削加工件变形及刀具磨损的主要 原 因, 利 用有 限元 软件进行 铣 削加 工模 拟仿 真是预
测切 削力 变化的重要方 法; 而任何金属切削仿真软件分析结果都会有一 定的局 限性 , 并不能完全的模拟 实际加
铣削 力是 导致 工 件 加 工 变形 、 刀具 损 耗 的 主要 因素 , 同时也是 进 行零 件 工 艺 分 析 和夹 具 设 计 的前 提条件 . 运 用 软件 模 拟仿 真 是 预 测切 削 力 的重 要 途
毕业论文-基于DEFORM-3D的切削温度仿真
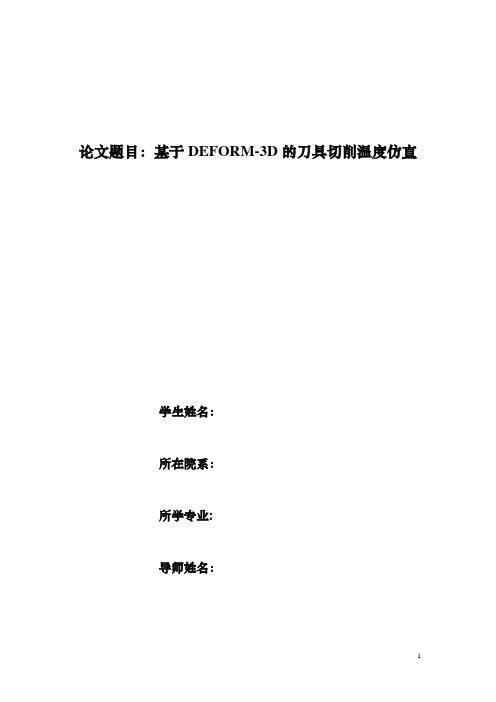
论文题目:基于DEFORM-3D的刀具切削温度仿真学生姓名:所在院系:所学专业:导师姓名:目录摘要 (1)第一章绪论……………………………………………………错误!未定义书签。
第二章仿真软件介绍 (6)第三章Deform—3D软件简介 (9)3。
1软件模块结构分析 (9)3。
2 前处理器及其设置 (9)3.3 模拟器 (9)3。
4 后处理器 (11)第四章有限元模型的建立 (13)4。
1 切削加工模型 (13)4。
2 切削模型建立 (14)第五章 DEFORM-3D对切削温度的仿真 (17)5。
1刀具和工件的温度场分析 (17)5.2 切削速度对切削温度的影响 (17)5.3切削过程中总体温度分布 (19)5。
4 切削厚度对切削温度的影响 (20)第六章结论 (22)第七章参考文献 (23)摘要在金属切削加工中,切削温度对切削加工过程有着非常重要的意义。
为了更好的研究金属材料的切削加工过程中切削温度的分布,本文以Deform—3D软件为平台,利用有限元方法对45号钢的切削过程中的温度进行了建模与仿真,分别分析了切削过程中刀具和工件的切削温度场分布,以及切削速度变化时对切削温度的影响。
仿真结果表明:刀-屑接触区及工件上的最高温度随切削速度的增加而升高,但工件上温度升高的趋势较平缓;无论切削条件怎么变化,切削温度的最高点总不在刀刃处,而是位于前后刀面上距离刀刃不远的地方;剪切面上各点的温度几乎相同.仿真结果表明,Deform—3D软件所得的仿真结果和理论依据的吻合度较高,说明仿真具有较高的可信度,为生产实践中切削速度的优化选择,刀具及工件材料的选择提供理论依据关键词:Deform-3D,有限元仿真,切削温度AbstractIn the process of metal cutting, the cutting temperature of the cutting process has very important significance. In order to better study the metal material cutting process of cutting temperature distribution,Based on the Deform -3D software as the platform,using the finite element method for45 steel cutting temperature by modeling and simulation,Analysis of the cutting process, the cutting tool and the workpiece cutting temperature field distribution,as well as the cutting speed change on cutting temperature effect.The simulation results show that:the tool-chip contact area and the workpiece on the maximum speed with cutting speed increases, but the workpiece temperature increased more gentle; No matter how the change of cutting temperature cutting conditions,highest point total in the blade,but are located before and after the knife surface distance edge not far place;Shear plane of each point on the temperature is almost the same. The simulation results show that,the Deform - 3D software the simulation results and the theoretical basis of the anastomosis of a higher degree, a description of the simulation has high reliability,Production practice of cutting speed optimization,tool and workpiece material selection and provide a theoretical basisKey word:Deform—3D,Finite element simulation, Cutting temperature第一章绪论金属切削是机械制造中使用最广泛的加工方法,金属切削加工时在机床上利用个切削工具从工件上切除多余材料,从而获得具有一定形状精度、尺寸精度、位置精度和表面质量的机械零件,是机械加工的基本方法。
deform钻削步骤详解
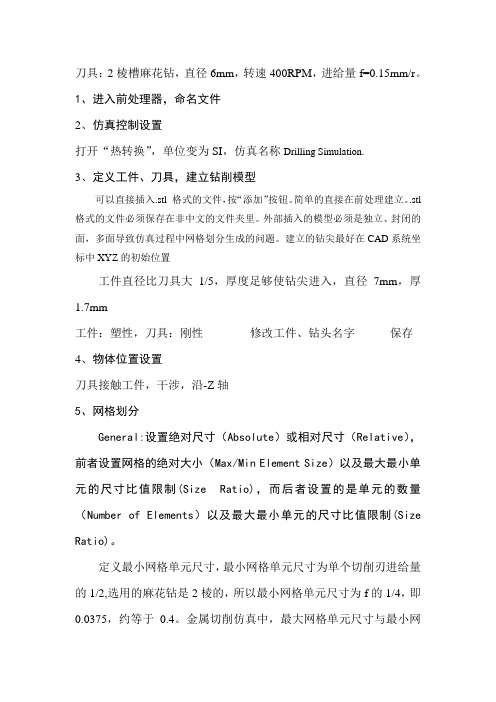
刀具:2棱槽麻花钻,直径6mm,转速400RPM,进给量f=0.15mm/r。
1、进入前处理器,命名文件2、仿真控制设置打开“热转换”,单位变为SI,仿真名称Drilling Simulation.3、定义工件、刀具,建立钻削模型可以直接插入.stl 格式的文件,按“添加”按钮。
简单的直接在前处理建立。
.stl 格式的文件必须保存在非中文的文件夹里。
外部插入的模型必须是独立、封闭的面,多面导致仿真过程中网格划分生成的问题。
建立的钻尖最好在CAD系统坐标中XYZ的初始位置工件直径比刀具大1/5,厚度足够使钻尖进入,直径7mm,厚1.7mm工件:塑性,刀具:刚性修改工件、钻头名字保存4、物体位置设置刀具接触工件,干涉,沿-Z轴5、网格划分General:设置绝对尺寸(Absolute)或相对尺寸(Relative),前者设置网格的绝对大小(Max/Min Element Size)以及最大最小单元的尺寸比值限制(Size Ratio),而后者设置的是单元的数量(Number of Elements)以及最大最小单元的尺寸比值限制(Size Ratio)。
定义最小网格单元尺寸,最小网格单元尺寸为单个切削刃进给量的1/2,选用的麻花钻是2棱的,所以最小网格单元尺寸为f的1/4,即0.0375,约等于0.4。
金属切削仿真中,最大网格单元尺寸与最小网格单元尺寸的比例通常选用10.为了仿真时网格自动生成计算,需要进行细节设置,工件:绝对型。
权重因子设置中,将Mesh Windows设置为1,其余为0,网格细化。
面网格划分——实体划分。
划分好后把细化窗口删除,权重因子重新设置Strain:0.65 ,Strain Rate:0.35 。
用于仿真过程中网格重新划分。
刀具:相对网格划分,20000个单元格,权重因子设置,网格细化,内外相对尺寸比例0.36、材料设置工件:AISI-1045(Machining) 铝刀具:Carbide (15%) 硬质合金7、运动控制设置钻头的运动、旋转,旋转速度单位换算radians/sec(弧度/秒),移动速度单位mm/sec换算公式:旋转中心:0,0,0 轴-Z进给量:8、边界条件进入Velocity,设置工件侧面在XYZ方向均为约束,Heat Exchange with the Environment所有面热转换仿真步数设置计算步长方式的选择:由时间决定;由模具行程决定(对于通常的变形问题,采用行程方式较好)对于钻削仿真,每个时间步内旋转1度,如果简化为300步完成一个变革(转一周),则当V为400RPM时,转一周需要1/6秒,每个时间步所占时间为(1/6) / 300,即每步0.0005秒With Constant Time Increment 常数时间增量设置为0.0005s.前面得知,沿-z轴移动速度为1mm/s,整个钻头穿过的路程约为3.5mm,则时间为3.5s,7000步。
DEFORM工艺仿真系统
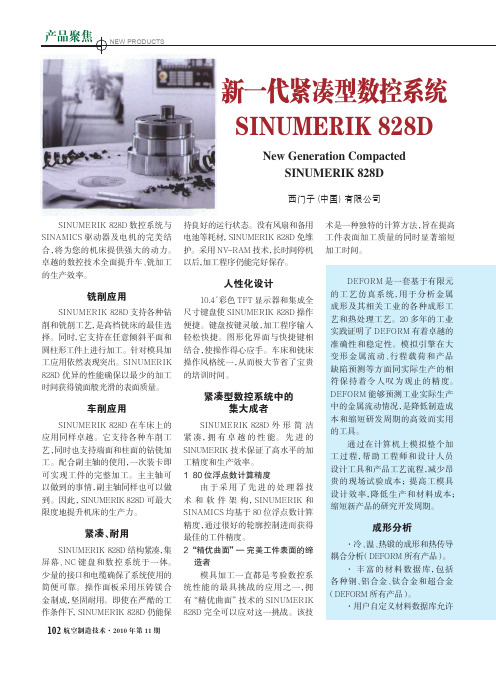
· 自我接触条件及完美的网 格再划分使得在成形过程中即便 形成了缺陷,模拟也可以进行到底 (DEFORM-2D,Pro)。
· 多变形体模型允许分析多 个成形工件或耦合分析模具应力 (DEFORM-2D,Pro,3D)。
的模具程序时,确保工件表面光滑。 编 程 灵 活,支 持 高 级 语
3 基于加工平面的坐标转换
言,通 过 采 用 编 程 向 导
智 能 坐 标 转 换 功 能 确 保 了 “programGUIDE”,高级语
SINUMERIK 828D 全方位自由加工, 言编程的灵活性和工艺循
无论是圆柱形工件的端面加工及柱 环编程的便利性实现有机
· 完整的成形设备模型可以分 析液压成形、锤上成形、螺旋压力成 形和机械压力成形(DEFORM 所有 产品)。
· 用户自定义子函数允许用户定 义自己的材料模型、压力模型、破裂准
则和其他函数(DEFORM-2D,3D)。 · 网 格 划 线(DEFORM-2D,
PC,Pro)和质点跟踪(DEFORM 所 有产品)可以分析材料内部的流动 信息及各种场量分布。
2010 年第 11 期·航空制造技术 103
产品聚焦 NEW PRODUCTS
新一代紧凑型数控系统 SINUMERIK 828D
New Generation Compacted SINUMERIK 828D
西门子(中国)有限公司
SINUMERIK 828D 数控系统与 SINAMICS 驱动器及电机的完美结 合,将为您的机床提供强大的动力。 卓越的数控技术全面提升车、铣加工 的生产效率。
面加工,还是在工件旋转表面铣削加 结合。
基于DEFORM-3D的转盘镗孔正交实验优化
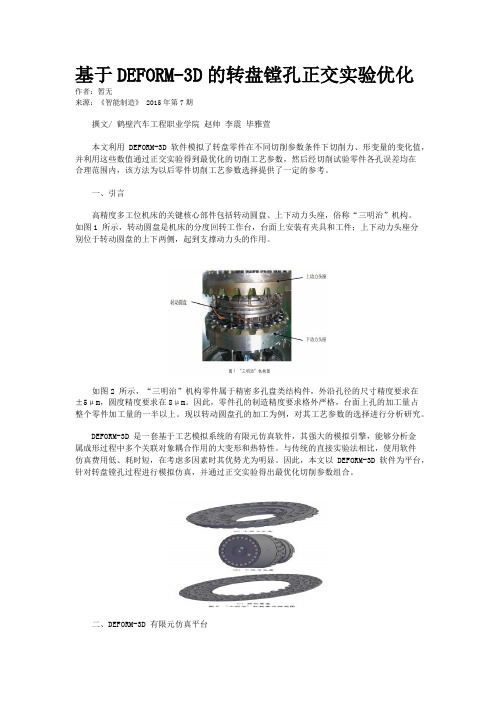
基于DEFORM-3D的转盘镗孔正交实验优化作者:暂无来源:《智能制造》 2015年第7期撰文/ 鹤壁汽车工程职业学院赵帅李震毕雅萱本文利用DEFORM-3D 软件模拟了转盘零件在不同切削参数条件下切削力、形变量的变化值,并利用这些数值通过正交实验得到最优化的切削工艺参数,然后经切削试验零件各孔误差均在合理范围内,该方法为以后零件切削工艺参数选择提供了一定的参考。
一、引言高精度多工位机床的关键核心部件包括转动圆盘、上下动力头座,俗称“三明治”机构。
如图1 所示,转动圆盘是机床的分度回转工作台,台面上安装有夹具和工件;上下动力头座分别位于转动圆盘的上下两侧,起到支撑动力头的作用。
如图2 所示,“三明治”机构零件属于精密多孔盘类结构件,外沿孔径的尺寸精度要求在±5μm,圆度精度要求在8μm。
因此,零件孔的制造精度要求格外严格,台面上孔的加工量占整个零件加工量的一半以上。
现以转动圆盘孔的加工为例,对其工艺参数的选择进行分析研究。
DEFORM-3D 是一套基于工艺模拟系统的有限元仿真软件,其强大的模拟引擎,能够分析金属成形过程中多个关联对象耦合作用的大变形和热特性。
与传统的直接实验法相比,使用软件仿真费用低、耗时短,在考虑多因素时其优势尤为明显。
因此,本文以DEFORM-3D 软件为平台,针对转盘镗孔过程进行模拟仿真,并通过正交实验得出最优化切削参数组合。
二、DEFORM-3D 有限元仿真平台1. 建立有限元模型由于DEFORM-3D 分析软件不具备三维造型功能,所以本文选择在SolidWorks 软件中建立模型。
在SolidWorks中建立的镗刀装配模型,如图3 所示,其中镗刀前角γ0=8 °,后角α0=10 °,刀尖圆弧半径rz=0.2mm。
模型文档另存为STL 文件格式,并在选项中选择“在单一文件”保存装配体的所有零件。
进入DEFORM-3D 软件中的MACHINING 模块后,导入预先构造的刀具模型,刀具材料选择硬质合金WC。
基于DEFORM-3D单颗磨粒切削仿真与研究
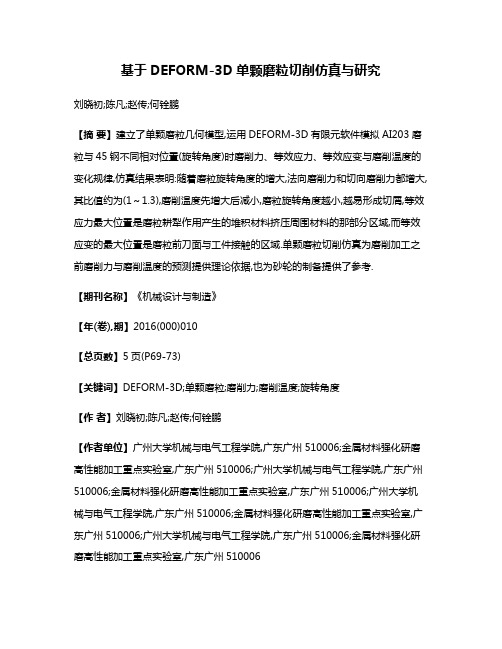
基于DEFORM-3D单颗磨粒切削仿真与研究刘晓初;陈凡;赵传;何铨鹏【摘要】建立了单颗磨粒几何模型,运用DEFORM-3D有限元软件模拟AI203磨粒与45钢不同相对位置(旋转角度)时磨削力、等效应力、等效应变与磨削温度的变化规律,仿真结果表明:随着磨粒旋转角度的增大,法向磨削力和切向磨削力都增大,其比值约为(1~1.3),磨削温度先增大后减小,磨粒旋转角度越小,越易形成切屑,等效应力最大位置是磨粒耕犁作用产生的堆积材料挤压周围材料的那部分区域,而等效应变的最大位置是磨粒前刀面与工件接触的区域.单颗磨粒切削仿真为磨削加工之前磨削力与磨削温度的预测提供理论依据,也为砂轮的制备提供了参考.【期刊名称】《机械设计与制造》【年(卷),期】2016(000)010【总页数】5页(P69-73)【关键词】DEFORM-3D;单颗磨粒;磨削力;磨削温度;旋转角度【作者】刘晓初;陈凡;赵传;何铨鹏【作者单位】广州大学机械与电气工程学院,广东广州510006;金属材料强化研磨高性能加工重点实验室,广东广州510006;广州大学机械与电气工程学院,广东广州510006;金属材料强化研磨高性能加工重点实验室,广东广州510006;广州大学机械与电气工程学院,广东广州510006;金属材料强化研磨高性能加工重点实验室,广东广州510006;广州大学机械与电气工程学院,广东广州510006;金属材料强化研磨高性能加工重点实验室,广东广州510006【正文语种】中文【中图分类】TH16磨削过程实际上就是磨具表面大量排列参差不齐、分布不规则的形状各异的磨粒共同完成的切削过程[1],由于磨粒的切入深度不同,因此磨削过程包括滑擦、耕犁和切削三个阶段。
磨削力与磨削温度是砂轮磨削加工中两个重要的参数。
磨削力产生于滑擦、耕犁和切削三个阶段,而每个阶段对磨削力的影响主要取决于磨料、工件材料、磨削液、化学反应及磨刃形状[2]。
磨削温度主要来自于磨粒与工件的耕犁和切削作用,而磨削力,磨削温度与砂轮耐用度、磨削表面粗糙度、比磨削能等均有直接的关系。
基于Deform-3D对手钻钻体预锻件的模拟加工处理
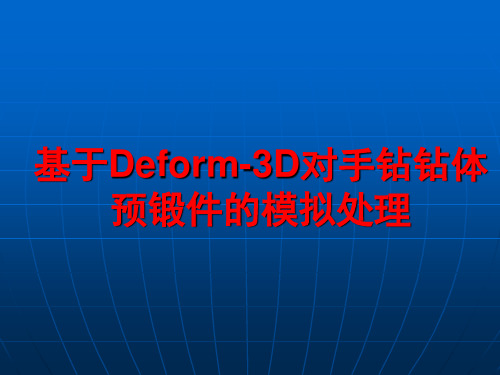
传统机械锻造存在的问题
锻件的锻压成形过程是一个非常复杂的弹塑性变 大过程,既有材料非线性,又有几何非线性,这 些因素使其变形机理非常复杂,很难用准确的数 学关系式进行描述,从而导致生产过程中对产品 质量控制的难度增大。 传统锻造工艺条件决定了锻造具有一定的危险性。 对于实力较弱的企业、教育、科研机构与单位来 说来说,传统锻造需要大量资金与材料,是进行 一项新的锻造工艺的开发的瓶颈。 传统机械锻造实验所需实验周期太长且效率太低。
速度的影响
上模速度在锻压 参数名称 参数值 过程中是一个重要参 800 温度(oc) 数,我们在考虑它对 锻压效果的影响的时 每步增量(mm/step) 0.1885 候,要将其他参数设 定在适宜的值,以期 模拟总步数(step) 200 获得较好的比较效果。 2 保存步数(step) 对我们的研究有重要 作用。参数设定如表 0.12 摩擦系数 网格数 12000
2 有限元与Deform-3D的概述
Deform-3D的原理 ——有限元
有限元法是目前CAE工程分析系统中使用最多、 分析计算能力最强、应用领域最广的一种方法。 有限元法是求解数理方程的一种数值计算方法, 是解决工程实际问题的一种有力的数据计算工具。 起初这种方法被用来研究复杂的飞机结构中的应 力问题,它是将弹性理论、计算数学和计算机软 件有机地结合在一起的一种数值分析技术;后来 由于这一方法的灵活、快速和有效性使其迅速发 展成为求解各领域的数理方程的一种通用近似计 算方法。目前,它在许多学科领域和实际工程问 题中都得到了广泛的应用,因此在工科院校和工 业界受到普遍的重视。
小结
模具的进给速度确实是一个重要的影响 因素,速度越小,充型效果越好,所受的载 荷、应力集中越小,锻压效果越好;可是我 们也应该看到,速度越小也影响实际生产中 的效率问题。
基于Deform2D的椭圆振动切削仿真研究
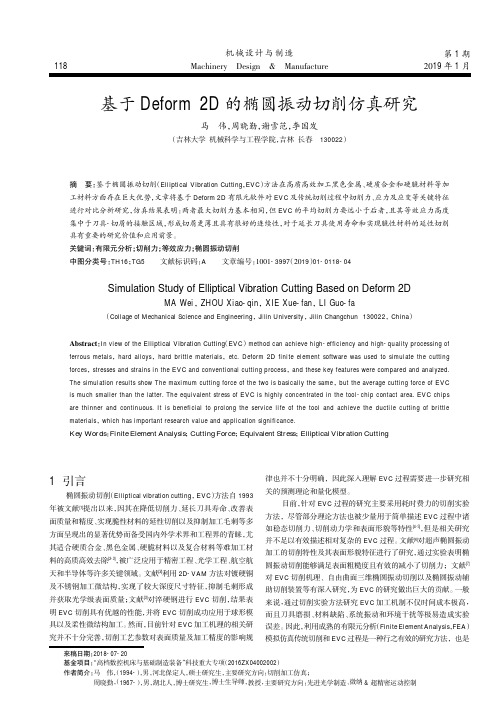
圆园19 年 1 月
基于 Deform 2D 的椭圆振动切削仿真研究
马 伟,周晓勤,谢雪范,李国发
(吉林大学 机械科学与工程学院,吉林 长春 130022)
摘 要:鉴于椭圆振动切削(Elliptical Vibration Cutting,EVC)方法在高质高效加工黑色金属、硬质合金和硬脆材料等加 工材料方面存在巨大优势,文章将基于 Deform 2D 有限元软件对 EVC 及传统切削过程中切削力、应力及应变等关键特征 进行对比分析研究,仿真结果表明:两者最大切削力基本相同,但 EVC 的平均切削力要远小于后者,且其等效应力高度 集中于刀具-切屑的接触区域,形成切屑更薄且具有很好的连续性,对于延长刀具使用寿命和实现脆性材料的延性切削 具有重要的研究价值和应用前景。 关键词:有限元分析;切削力;等效应力;椭圆振动切削 中图分类号:TH16;TG5 文献标识码:A 文章编号:员园园员-3997(圆园19)01-0118-04
律也并不十分明确,因此深入理解 EVC 过程需要进一步研究相 关的预测理论和量化模型。
目前,针对 EVC 过程的研究主要采用耗时费力的切削实验 方法,尽管部分理论方法也被少量用于简单描述 EVC 过程中诸 如稳态切削力、切削动力学和表面形貌等特性[4-5],但是相关研究 并不足以有效描述相对复杂的 EVC 过程。文献[6]对超声椭圆振动 加工的切削特性及其表面形貌特征进行了研究,通过实验表明椭 圆振动切削能够满足表面粗糙度且有效的减小了切削力;文献[7] 对 EVC 切削机理、自由曲面三维椭圆振动切削以及椭圆振动辅 助切削装置等有深入研究,为 EVC 的研究做出巨大的贡献。一般 来说,通过切削实验方法研究 EVC 加工机制不仅时间成本极高, 而且刀具磨损、材料缺陷、系统振动和环境干扰等极易造成实验 误差。因此,利用成熟的有限元分析(Finite Element Analysis,FEA) 模拟仿真传统切削和 EVC 过程是一种行之有效的研究方法,也是
钻削过程的数值模拟仿真分析论文
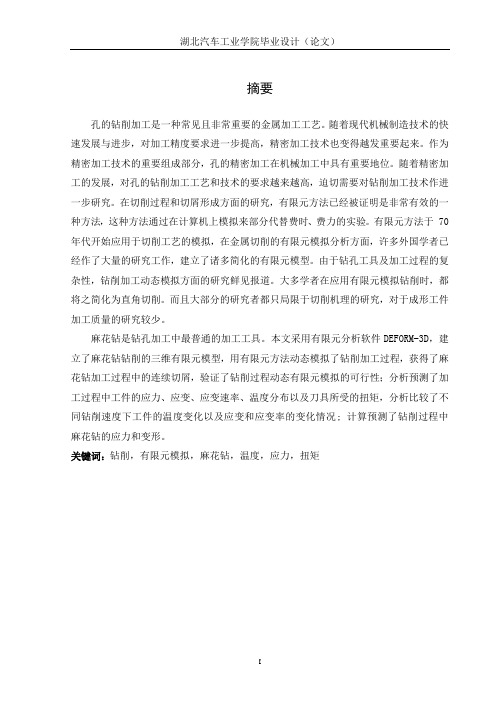
摘要孔的钻削加工是一种常见且非常重要的金属加工工艺。
随着现代机械制造技术的快速发展与进步,对加工精度要求进一步提高,精密加工技术也变得越发重要起来。
作为精密加工技术的重要组成部分,孔的精密加工在机械加工中具有重要地位。
随着精密加工的发展,对孔的钻削加工工艺和技术的要求越来越高,迫切需要对钻削加工技术作进一步研究。
在切削过程和切屑形成方面的研究,有限元方法已经被证明是非常有效的一种方法,这种方法通过在计算机上模拟来部分代替费时、费力的实验。
有限元方法于70 年代开始应用于切削工艺的模拟,在金属切削的有限元模拟分析方面,许多外国学者已经作了大量的研究工作,建立了诸多简化的有限元模型。
由于钻孔工具及加工过程的复杂性,钻削加工动态模拟方面的研究鲜见报道。
大多学者在应用有限元模拟钻削时,都将之简化为直角切削。
而且大部分的研究者都只局限于切削机理的研究,对于成形工件加工质量的研究较少。
麻花钻是钻孔加工中最普通的加工工具。
本文采用有限元分析软件DEFORM-3D,建立了麻花钻钻削的三维有限元模型,用有限元方法动态模拟了钻削加工过程,获得了麻花钻加工过程中的连续切屑,验证了钻削过程动态有限元模拟的可行性;分析预测了加工过程中工件的应力、应变、应变速率、温度分布以及刀具所受的扭矩,分析比较了不同钻削速度下工件的温度变化以及应变和应变率的变化情况; 计算预测了钻削过程中麻花钻的应力和变形。
关键词:钻削,有限元模拟,麻花钻,温度,应力,扭矩ABSTRACTDrilling is one of the most commonly used and important machining operations. As modern machinery manufacturing technology continues to envolve and progress , the requirement of precision machining is more exigent than before and the precision machining technology is much more important. Nowadays, a lot of work is urgent to do on drilling in order to meet the needs of precision machining. In recent years, the application of finite element method (FEM) to cutting operations has proved to be effective to study the cutting process and chip formation. It can reduce the experimental cost replace some experimental testing which may be difficult or impossible to obtain by numerical simulation on the computer. The first time FEM was applied in machining simulation was in 1970s. Many papers are available now on simulation of orthogonal and oblique cutting process but little of drilling because of the complexity of drilling processes. Though some is on drilling, they are simplified to orthogonal cutting. The cutting mechanism of drilling is similar to 3D orthogonal cutting but not the same. Little research has been done on the FEM simulation of the drilling processes. Further more, most researchers just studied the cutting mechanism. V ery little has been investigated on machining quality of the workpiece.Twist drills are the most widely used tools for drilling holes.The present work aims to simulate three-dimensional drilling operations and 3D FE model of twist drilling is developed for the drilling simulation process. 3D FEM simulation of twist drilling is presented in the paper and get the continuous chip formation and indicate the feasibility of FEM simulation of drilling processes. FEM simulation of twist drilling is carried out to identify the characteristics and to analyze the drilling quality of these two classes of drilling, including stress, strain, strain rate and temperature distribution, material flow and chip formation in the workpiece, drilling torque, stress and elastic deformation of drilling tools.KEY WORDS:drilling, FEM simulation, twist drill,temperature,stress,torque目录摘要 (I)ABSTRACT (II)1 绪论 (1)1.1 本课题的来源、目的及意义 (1)1.1.1课题来源 (1)1.1.2 本课题研究的目的 (1)1.1.3 本课题研究的意义 (1)1.2 国内外研究现状及发展方向 (2)1.2.1有限元方法(FEM)在切削方面的研究应用 (2)1.2.2切削加工过程有限元模拟的研究现状 (3)1.2.3切削加工有限元模拟的发展方向 (4)1.3 本课题研究的主要内容 (4)2 有限元模拟原理 (6)2.1 有限元法理论基础 (6)2.1.1 有限元理论简介 (6)2.1.2 弹塑性有限元分析 (7)2.1.3 刚塑性有限元法 (8)2.2 切削理论 (8)2.2.1 金属的晶体结构 (9)2.2.2 塑性变形机理 (9)2.3 切屑断裂准则 (10)2.4 DEFORM V6.1 软件简介 (13)2.5 小结 (15)3 钻削模型的建立及参数设置 (16)3.1 引言 (16)3.2 三维建模 (16)3.3 麻花钻的三维模型 (16)3.4 模型初始网格划分及边界条件设定 (18)3.5 参数设置 (19)3.5.1 切削用量的设定 (19)3.5.2 材料设置 (19)3.5.3 运动参数的设定 (19)3.5.4 模拟参数的设定 (21)3.6 本章小结 (22)4 钻削过程的仿真结果及分析 (23)4.1 钻削过程仿真分析 (23)4.1.1 温度分布 (23)4.1.3 等效应力 (25)4.1.4 等效应变及等效应变率 (27)4.1.5 刀具所受扭矩 (31)4.2 本章小结 (32)5 总结与展望 (33)5.1 总结 (33)5.1.1 研究结果 (33)5.1.2 现存问题 (33)5.2 展望 (34)致谢 (35)参考文献 (36)1 绪论1.1 本课题的来源、目的及意义1.1.1课题来源本课题源于教学科研,对麻花钻钻削加工过程进行科学整理、归纳和完善,以期最终形成最佳的加工工艺。
基于Deform3D的高速车削加工仿真研究
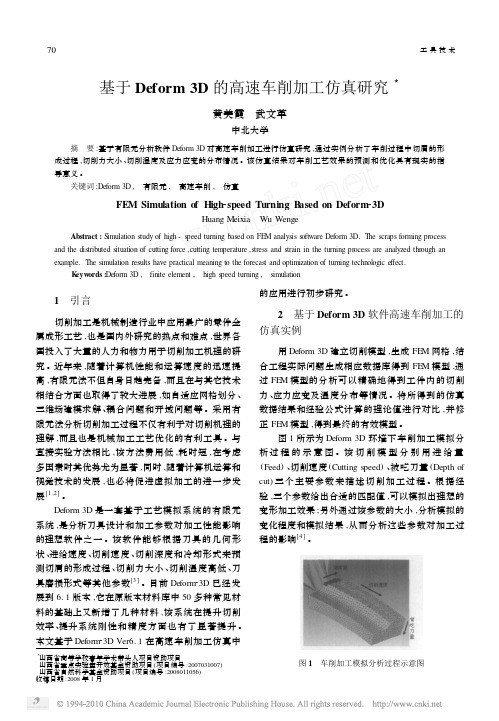
图 4 为试件等效应力的分布 。图 5 为切削区最
大主应力的分布 ,无论从图中的等效应力还是最大
主应力分布状态的等高线都可看出刃前区应力分布
状态最为复杂 ,在第一变形区等效应力数值最大并
有较大变化梯度 ; 第二变形区应力的分布较为均
匀[6] 。
图 6 为刀具的等效应力等值线图 。图 7 为刀具
的位移变化分布云图 。从两图中可以看出刀具的应
图 2 切削力 Fc 随着切削距离的变化
图
3a
和图
3b
分别为工件转过 1 后工件和刀具 12
的切削温度分布图 ,从两图中看出切削温度最高点
不在刀尖处 ,而是离开刀尖一段距离 。整个切削过
程中工件切削温度的峰值可达 1030 ℃℃以上 407 ℃以下 。
1030
3 结语
采用有限元法模拟切削加工可获得切削试验法 或难以直接测量的状态变量 ,如工件和刀具的切削 力分布 、切削温度等 ,有利于更好地理解切削加工机 理 、评价和优化切削加工过程 。而采用有限元法分 析和评价各种切削条件下的刀具磨损状况 ,费用低 耗时短 。但是由于车削加工尤其是高速车削加工过 程极其复杂 ,有关其切削机理的许多问题仍未得到 解决[7] 。如车削过程中积屑瘤 、分流等各种特定现 象的研究 ;车床振动 、冷却液等实际切削过程的工艺 因素对车削模拟的影响 ;刀具材料的磨损机制 、切削 力 、切屑变形和加工表面质量随实际加工过程中工 件材料的相变而发生相应变化的研究 ;其模拟运算 时间过长对制造车间在线控制的障碍 ;网格划分的 疏密和步长设置的大小都会影响仿真的精度 ,如何 设置才能实现最合理化等都有待进一步研究 。
力和变形区域主要集中在刀尖处 ,向外沿区域呈逐
渐减弱的趋势 。