位置度超差五原则表
位置度超差五原则表

W2011021602
编 号:
标题 零件图号 发起人 签发日期
前轮辋装不上制动盘
54111H05712 谭晓武
零件名称 审批人
前轮辋 潘小平
2011-02-17
请于2011-03-14前返回
五原则表
责任单位
金华今飞
年月日
制作
确认
徐申
批准
确认/日期 批准/日期 接受 报告
得分
发生状况(发生件数、发生现象、处置情况等)
一
不良品的确认结果
1.现象说明:位置度超差是导致碟刹盘无法装配的直接原因。
2.不良品与正常品的外观差异:
不良品
不良品
正常品
正常品:四个螺纹孔中心距尺寸无偏差; 不良品:四个螺纹孔中心距尺寸明显存在偏差。 3.与作业指导书的对比:
产品 序号
类型 模具号
生产日期
合格证 日期
1
尺寸33mm
2
3
4
示意图
1
L
2
1
5
L
2010.12.30 1.3 31.92 33.12 34.04 32.94
6 7
不良品
L L
8
L
9
L
2010.12.30 2010.12.30 2010.12.30 2010.12.30
1.3 1.3 1.3 1.3
31.96 31.72 32.02 32.02
33.12 33.22 33.3 33.2
内 发生 容 流出
1
位置度超差 位置度超差
2
刀具中心与工装中心不同心 检验员没有检查
三 、
序号
问题点
标准
让你更容易理解的位置度公差
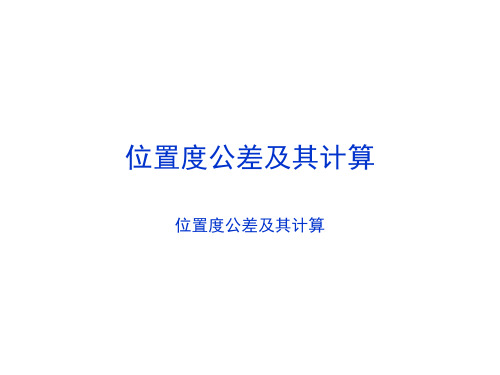
③复合位置度公差注 法:图6-13。
• 四个孔的实际轴线应同时位 于孔组位置度公差带和各孔 位置度公差带内,即四个孔 的实际轴线应位于两个公差 带的重叠部分,但各孔位置 度公差带中心不必位于孔组 位置度公差带内,则满足设 计要求。
三、位置度公差的计算
• 1. 孔组内各孔位置度公差的计算 • 孔组内各孔的位置度公差带计算公式由紧固件与被连接零 件的连接方式决定。 • 通孔连接方式:用螺栓、销钉等紧固件穿过两个或几个被 连接零件上的通孔; • 螺孔连接方式:把双头螺柱、螺钉等紧固件拧入一个被连 接零件的螺孔中,且穿过其余的被连接零件上的通孔。 • (1)通孔连接方式的位置度公差计算(图6-14) t=DM-dM=Xmin • 上式中,紧固件采用包容要求
二、位置度公差的标注
孔组的两种设计要求 • (1)第一种设计要求。装配时不仅要求被连接的两个零件上对应孔组内各孔的位
置分别对准,是孔组内部的孔的位置要对准,而且要求这两个零件上的某些其他要素 也应分别对准。(对孔组的位置和各孔的位置变动量都应规定较严格的位置度公差。) • • 换句话说就是既要保证孔组的位置度公差还要保证各孔的位置度公差,孔组的位置度 公差可以保证零件的边是不是对齐的。 (2)第二种设计要求。装配时仅要求被连接的两个零件上对应孔组内各孔的位置分别 对准,而不要求这两个零件上的某些其他要素也分别对准。(对各孔的位置变动量应 规定较严格的位置度公差,而对孔组位置度公差或定位尺寸公差则应规定的较松。) 孔组位置度公差与各孔位置度公差的关系是孔组的位置度公差一定要大于或等于各个 孔的位置度公差。
孔组位置度公差
பைடு நூலகம்
各孔位置度公差
二、位置度公差的标注
• ②位置度公差与定位尺寸公差组合注法:图6-4和6-8。
(优选)位置度影响因素及调整步骤注意事项
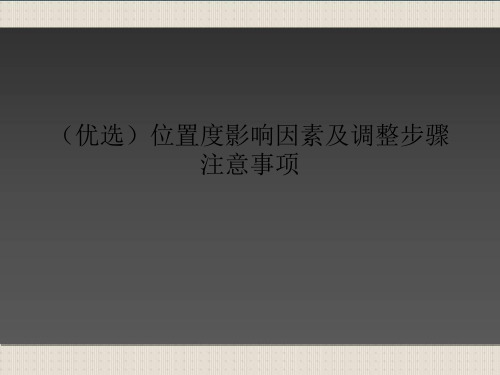
位置度定义
如下图, φ3孔的位置度要求
位置度
• 位置度是关联实际要素对基准在位置上允 许的变动全量.包括点的位置度公差,线的位 置度公差,和平面或中心平面的位置度公差.
• 对于我们公司来说,位置度的要求大多是 对于孔,所以我们这篇文章的重点也在于 孔和外圆,我们的以下内容都是基于对于 孔来讲述的。
始与此 6、液压气动系统---夹具的动力源 7、冷却系统---刀具的保护神
影响位置度的因素
• 那现在我们就可以来说位置度的影响因素了。简 单的说,设备的各组成部分都会对位置度有一定 的影响,只不过是重不重要的问题,但值得注意 的是,有的时候看似次要的部位有可能反而是问 题的关键。
• 位置度的影响因素有:(排名分前后☺) 1、夹具2、主轴箱3、导向机构4、液压气动系统5、 刀辅具6、冷却系统7、床身8、其它
二、夹具夹紧后检查各夹紧点是否与工件压紧,若 没有压紧就需要检查夹紧机构有无问题;
三、夹具夹紧后检查各定位块、辅助支撑与工件是 否贴死,这样可以针对具体的情况得出响应的判 断;
四、在以上都 没有问题的情况下开始试切工件,但 需在此状态下感受工件是否有移动或者震动;
夹具对位置度的影响
五、若发生了第四项的情况,则需要对系统 的夹紧力来进行检查;
(优选)位置度影响因素及调整步骤 注意事项
加工零件位置度超差调整前的检查步 骤及注意事项,位置度变化影响因素
编稿:李军
位置度定义
• 位置公差(俗称位置度)——位置度公差是指各实 际要素相互之间或它们相对一个或多个基准位置 所允许的变动全量,也就是加工后实际存在的位置 相对设计上规定的理想位置所允许偏离的极限范 围。换成我们的话讲,就是目标(孔、外圆等)相 对于某一规定基点或者面的实测坐标值与要求坐 标值间的误差,这个误差在要求范围内既位置度 合格,超过范围既位置度超差,这时就需要调整 位置度了。
位置度影响因素及调整步骤、注意事项
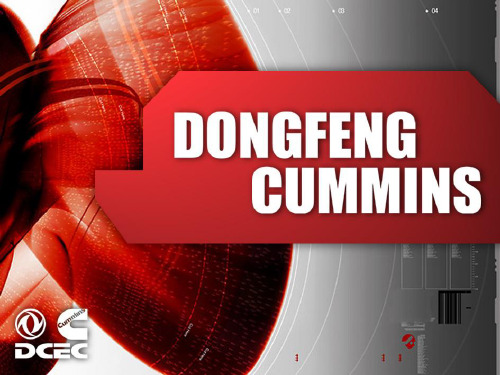
刀辅具对于位置度的影响
• 这是一个比较常见的问题,刀具的磨损程 度直接决定了加工质量的一切参数,包括 对位置度产生影响,比如刀具直径磨损就 会导致钻套起不到很好的导向作用而导致 位置度不稳定;刀具切削刃磨损就会导致 刀具跳动加工孔变大位置度不稳定等。
冷却系统对位置度的影响
在高速主轴设备中就会突出的表现冷却液的 作用,冷却液的流量和压力不够就会导致 刀具过热,被加工孔变大或者椭圆,这样 位置度当然就会变差。这个时候就相应的 对于冷却系统进行检查和修理,确保冷却液 的流量.
钻模板对位置度的影响
钻模板对位置度的影响
主轴箱对位置度的影响
• 在主轴箱出现异常的情况下,也会造成位 置度不稳定的情况出现,所以也相应需要 对主轴箱来做针对性检查。 1、检查主轴箱内部有无异响,有无震动,可 判断主轴箱传动机构是否有问题,震动较 大则会造成孔干大或位置度波动。
主轴箱对位置度的影响
加工零件位置度超差调整前的检查步 骤及注意事项,位置度变化影响因素
编稿:李军
位置度定义
• 位置公差(俗称位置度)——位置度公差是指各实 际要素相互之间或它们相对一个或多个基准位置 所允许的变动全量,也就是加工后实际存在的位置 相对设计上规定的理想位置所允许偏离的极限范 围。换成我们的话讲,就是目标(孔、外圆等)相 对于某一规定基点或者面的实测坐标值与要求坐 标值间的误差,这个误差在要求范围内既位置度 合格,超过范围既位置度超差,这时就需要调整 位置度了。
钻模板对位置度的影响
三、对于活动钻模板要检查模板是否贴死定 位面,模板定位销、定位块是否磨损,定 位销是否松动等异常;这里检查可以通过 气检压力读数、用塞尺等办法,夹具定位 面检查类似。
钻模板对位置度的影响
检测位置度误差

线的圆柱面内,图b所示。
位置度误差的检测
(1)准备的检具 坐标测量装置、心轴。 (2)检测步骤 如图所示。
步骤l:按基准调整被测零件,使其与测量装置的
坐标方向一致。 步骤2:将心轴放置在孔中,在靠近被测零件的板
面处,测量x1,x2,y1,y2。
步骤3:按下式分别计算出坐标尺寸x,y: x=(x1+x2)/2;y=(y1+y2)/2 步骤4:将x,y分别与相应的理论正确尺寸比较,得出fx和fy 步骤5:然后把被测件翻转,对其背面按上述方法重复测量,取其中的误 差较大值,作为该零件的位置度误差。 (3)评定检测结果 如果测得的最大误差值≤0.1 nlnl,该零件的位置度 符合要求;如果测得的最大误差值>0.1mm
检测位置度误差
☞ 知识点
(1)位置度公差;
(2)位置度公差的检测。
位置度公差
定位公差是关联实际要素对基准在位置上允许的变动量。 根据被测要素和基准要素之间的功能关系,定位公差分为位置度、同 轴度和对称度3个项目;
位置度公差
(1)位置度公差的标注和公差带 如图所示。
位置度公差
(2)识读位置度的标注 图a所示被测孔φ28mm轴线相对于基准面A, 基准面B和基准面C组成的基面体系的位置度公差为φ0.1 mm。 (3)解释位置度公差带的含义 被测轴线必须位于直径为公差值0.1 mm,且以相对于A,B,C基准表面(基准平面)所确定的理想位置为轴
利用Excel制作各类品质图表
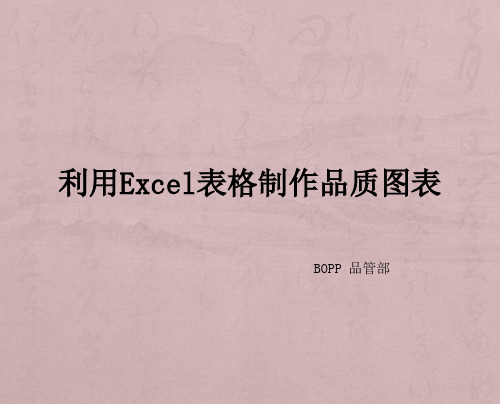
所涉及的函数:
1. 逻辑函数:
AND
执行真假值判断,根据逻辑计算的真假值,返回不同结果。可以使 用函数 IF 对数值和公式进行条件检测。
OR
在其参数组中,任何一个参数逻辑值为 TRUE,即返回 TRUE;任
何一个参数的逻辑值为 FALSE,即返回 FALSE。
步骤1: 计算人与人交叉(A*B,B*C,A*C)
步骤1:计算数据中的最大最小值 步骤2:计算全距(最大值-最小值) 步骤3:计算组数K
温馨提示:右图为组数的参考值 步骤4:计算组距(全距/组数K )
數據數 50~100 100~250 250以上
組數 6~10 7~12 10~20
步骤5:计算上下组列
用CONCATENATE函数合并上下界 数值文本,计算如下:
了解制程变异手法特点与作用会在?spc与excel的结合运用?部分细说柏拉图与excel的结合运用09第四季度散热片不良状况5032184310706986219138948396551000020406080100螺纹不良位置度超差导通不良表面赃物来错物料变形其它不良类别0102030405060708090100不良数量累积不良率首先让我们来看以下一个关于某款产品进行季度的质量分析
CONCATENATE
计算区域中满足给定条件的单元格的个数。 返回一组值中的最大值。 返回一组值中的最小值。 将几个文本字符串合并为一个文本字符串。
2. 数学与三角函数:
LOG 3.文本函数:
FIXED
按所指定的底数,返回一个数的对数。
将数字按指定的小数位数进行取整,利用句号和逗号,以小 数格式对该数进行格式设置,并以文本形式返回结果。
品质七大手法与EXCEL的结合运用
位置度
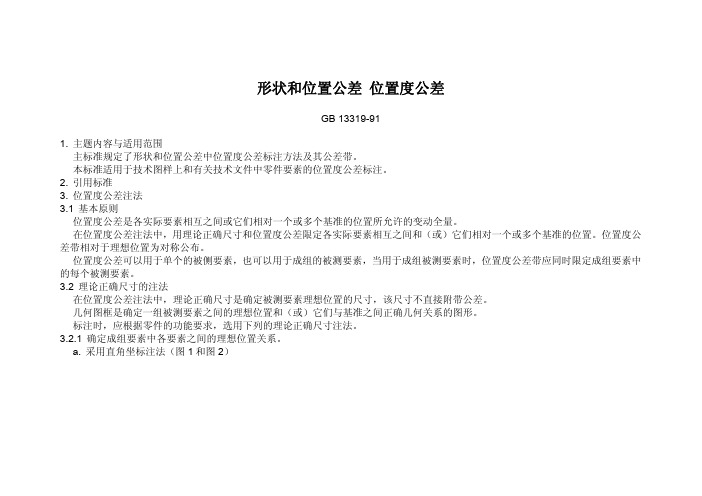
形状和位置公差位置度公差GB 13319-911. 主题内容与适用范围主标准规定了形状和位置公差中位置度公差标注方法及其公差带。
本标准适用于技术图样上和有关技术文件中零件要素的位置度公差标注。
2. 引用标准3. 位置度公差注法3.1 基本原则位置度公差是各实际要素相互之间或它们相对一个或多个基准的位置所允许的变动全量。
在位置度公差注法中,用理论正确尺寸和位置度公差限定各实际要素相互之间和(或)它们相对一个或多个基准的位置。
位置度公差带相对于理想位置为对称公布。
位置度公差可以用于单个的被侧要素,也可以用于成组的被测要素,当用于成组被测要素时,位置度公差带应同时限定成组要素中的每个被测要素。
3.2 理论正确尺寸的注法在位置度公差注法中,理论正确尺寸是确定被测要素理想位置的尺寸,该尺寸不直接附带公差。
几何图框是确定一组被测要素之间的理想位置和(或)它们与基准之间正确几何关系的图形。
标注时,应根据零件的功能要求,选用下列的理论正确尺寸注法。
3.2.1 确定成组要素中各要素之间的理想位置关系。
a. 采用直角坐标注法(图1和图2)b. 采用极坐标注法(图3和图4)若成组要素中的各要素在圆周上均匀分布时,各要素间的理论正确角度允许省略不注,在公差框格上方加注“均布”两字(图4)。
此时,各要素间的角向位置关系为圆周理想等分的角度关系。
c. 采用混合法(图5)。
d. 采用表格注法(图6)。
图1至图6中各理论正确尺寸仅确定成组要素组内各要素(孔的轴线)相互间的理想位置关系,在图中分别用相应的几何图框表示。
3.2.2 确定各要素之间及相对基准的理想位置关系a. 采用直角坐标法(图7至图9)图7中基准线A作为确定各条被测线理想位置的尺寸起始线。
图8中基准平面A、B构成的互相垂直的基准体系作为确定各孔理想位置的坐标尺寸起始面。
有对中心基准要求的要素,其理论正确尺寸应从基准中心平面注起(图9)。
图9中基准中心平面A确定了孔组的定位和定向要求。
位置公差与误差

四、 跳动公差
跳动公差为关联实际被测要素绕基准轴线回转一周 或连续回转时所允许的最大变动量。可用来综合控制被 测要素的形状误差和位置误差。
跳动公差是针对特定的测量方式而规定的公差项目。 跳动误差就是指示表指针在给定方向上指示的最大与最 小读数之差。
liuq1217@
二、 定向公差
2.垂直度公差 1)一个方向
d
0.1 A 基准平面
A
liuq1217@
2)任意方向
d
0.05 A
A
liuq1217@
d 基准平面
二、 定向公差
3.倾斜度公差 倾斜度公差用来控制面对线、线对线、面对面和线对
面的倾斜度误差,只是将理论正确角度从0°或90°变为 0°~90°的任意角。
1)径向圆跳动和圆度的公差带都为半径差为公差 值 t的两个同心圆之间的区域,即公差带形状相 同。
2)径向圆跳动:两个同心圆的圆心与基准同轴 (圆心固定)。 圆度:两个同心圆的圆心随着被测实际圆的位 置而变动(圆心浮动)。
3)径向圆跳动:位置公差项目,关联要素(有基 准)。 圆度:形状公差项目,单一要素(无基准)。
图样标注时应将角度值用理论正确角度标出。
liuq1217@
二、 定向公差
0.06 B
α
60°
t
B
基准线
liuq1217@
二、 定向公差
定向公差带特点: 1. 定向公差用来控制被测要素相对于基准保持一定的 方向(夹角为0°、90°或任意理论正确角度)。
2.定向公差带具有综合控制定向误差和形状误差的能力。 因此,在保证功能要求的前提下,对同一被测要素给出 定向公差后,不需再给出形状公差,除非对它的形状精 度提出进一步要求。
五原则表教材

过程再现:再现试験状态
当上冲向下运动时,被异物垫起的 齿尖部分损伤阴模。
标记点
齿顶处与阴模内腔接触
上冲
齿轮 ● 下冲
铁异物 2φmm
由于有杂物存在,产品被垫起
发生1°的倾斜
在通常的sizing加工条件下 阴模 模具内侧咬入2φ的铁异物进
行了冲压。
5-3.查明原因-再现试験结果
测量验证:歯形测定
3.<再现试験>・・・以特性要因図、现场検证的因素为基础, 实施再现试验,找出原因。・・・ 测定结果的对比
[生产场所] 东睦(天津)粉末冶金有限公司(日系JV取引先:东睦工业)
不良从动齿轮生产日期:2008-7-19~2008-9-13
生产数量:期间共生产213256件,共为3套模具生产,编号分别
为:0704、0808、0809,其中0704生产97610件,
0808生产69389件,0809生产46257件。
3.工程検证结果
油 2.临时放置铁板
工程名
基准
事実と问题点
判定
1.涂整型油 要涂整型油
・无整型油涂布量的具体 指示(作标不恰当)
×
・无异物管理基准的指示和
管理方法(作标不恰当)
・无油槽、放置场所的清扫
指示、基准
・临时放置场所有铁异物付着
2.sizing
× ・型内及机械台上的异物
切实装入型内 管理指示无(作标不恰当)
特性要因図
设备
型材质不适 型カジリ伤
作动不良
模具拉伤
油量少い
人
产品附着杂物未检查
检查不 仔细
责任心不强
工件放置未检查
材料成分不适 异材
材料
检查作业指导书不完善
【20140104】广汽本田五原则工作表记入要领3

把握事实查明原因(采取)适当的对策确认(对策)效果对(问题)源头的反馈以下是广州本田(1998年)版5原则表的精粹·对于解决问题5原则表,各位同事需要理解以下的事项.5原则需按顺序可以记录.了解5原则各程序的目的.了解应该由谁使用5原则表.了解应该在何时使用5原则表·创立解决问题5原则表的目的.在广州本田内,使解决问题的方法标准化.使为解决问题所进行的全部活动,都能汇总成"キ干'总结到1页纸上.根据上面所做的工作,可以容易地了解到按各步骤所采取的行动有无遗漏.可以容易地评价针对每一步所采取的行动是否是最妥切的.将为解决问题所开展的活动内容作为技术诀窍记录下来,不断地积累技术经验.减少问题再次发生的次数·谁来使用5原则表.所有的广州本田员工都需要了解5原则表,要作到全体人员都能使用·应该在何时使用5原则表.在问题发生的真正原因不明确的时候.为了查明问题发生原因需要进行解析的时候.特别是在问题再一次发生时,一定要使用5原则表的各个流程.<广州本田版5原则表的展开步骤和内容>如果发生了问题,将问题(题目)记入,按照5条原则进行展开5原则1·(发生状况 1-A)·使用5W2H法收集尽可能多的信息..5W: (WHO)谁(什么)-,类型,种类,受影响的部分等(WHAT)什么-问题的症状,尽可能地使用图表等工具将问题表达清楚.(WHEN)何时-记入问题发生的日期(WHERE)何地-记入问题发生的场所(WHY)为什么-具体的内容.2H: (HOW)怎么样-(问题)是怎么样被发现的(HOW MANY)什么程度-(问题)发生的量、程度.问题点的概要(信息的收集、整理) 例如:针对部品或是工程.问题再现试验的结果.现行品的品质状况.发生的对象范围.利用绘图、图表、柱状图使问题明确化·集体创造性思考 1-C.将可能想得到的原因在集体创造性思考会上全部阐述、总结出来.而后将上面的内容尽可能地进行整理,在别的栏里明确地记入·特性要素图 1-D.在特性要素图中,将所有的要素全部记入.为了查找到真正的原因,作为一种工具要尽可能地使用特性要素图5原则2 查明原因、验证·Q&A (WHY WHY分析 2-A).通过WHY WHY的反覆(=)5次进行分析来找出真正的原因.WHY WHY的疑问必须使之与问题现象带关联性、建立起系统来进行.WHY WHY的分析要从问题的发生原因(或者叫硬件方面的原因)和流出原因(又叫软件方面原因)两方面来进行.WHY WHY分析的信息来源,基本上是以特性要素图为基础·<查明原因、验证、总结 2-B>.找到了真正的原因,要将连同可以证实它的内容一起记载在这里.还有,为了说明真正的原因,可以加入插图5原则3 (采取)适当的对策.(针对发生的问题)采取暂定对策与恒久对策.还需要发生对策、流出对策(或叫硬件对策、软件对策).因为可能由对策带来新的问题,需要对这些潜在的问题进行分析(P.P.A)、评价(预测).查明可能会演变成问题的潜在的要素.制订作为预防手段的计划5原则4 确认(对策)效果.对于实行的对策、实施追踪.在为确认效果进行检查时,取样数量可参考实际问题发生率、数据方面可以灵活使用统计手法5原则5 对(问题)向前反馈和向后反馈.针对类似的工程、相似的问题可以采取同样的修正对策.为了更好地实施对策内容和遏制住不良的发生,需要将对策内容落实到组织和管理体制中5原则表 使用特性要素图的目的和好处(要素分析在广州本田版查明原因这一工作中始终作为一项重要手段)重要点是使用特性要素图完整地实施Q&A之所以如此,是因为Q&A在5原则中起着关键作用,在这里大家需要了解作为主要工具的特性要素图的使用方法.我们在进行Q&A时,最重要是提出正确的问题.如果错误地提问,就会得出错误的答案,这时就不能抓住真正的原因在进行Q&A时经验会成为帮助,而最重要的还是理解Q&A的做法.即使是经验少的人,如果能正确实行Q&A,也能够发现真的原因使用特性要素图的好处.对于已完成的5原则表,(使用者)本人自不用说,评价者或者是第三者在看这个表的时候,以下的事情就容易明白.知道遗漏和不恰当的项目.Q&A的每一步的内容可以进行评价.在特性要素图中被列举出来的众多要素与特性有无关系容易判断.如果有谁想掌握具体的5原则的内容,即使没有文字、语言的说明只要有作为基干的特性要素图就可以弄懂.为了使5原则表更容易理解,特性要素图原则上是必须要的作成特性要素图的5个要点1.问题(特性)要尽可能详尽具体地表现出来.要牢牢地把握现状,正确抓住问题点.特性要尽可能地用具体的数字来表示例:服务不好服务的对应太慢在使用5原则表决定标题时使用这种手法服务的对应需要1个小时2.集体创造性思考的实施.把各部分的人集中到一起,作出特性要素图.据此找出真正原因的机会就会增加.这时候由一个人将众人提出的想法记入特性要素图3.汇集事实情报.在用'3现主义'制定对策前将事实和数据汇总起来4.确认全部的要素是否都已经提了出来.重复WHY WHY这一程序.根据需要从熟手那里求得帮助(光罗列现象无法解决问题)5.经常地进行研究、不断改良加以完善.特性要因图需要重复不断地加以修正.根据需要,如果有新的发现要加以追记.在最后总结时可能要将特性要素重写追记:实际上在研究讨论阶段,无拘束地、自由地将想法全部记下来的方法则更好好的特性要素图的确认卡·确认是否全部的要素都已经提炼出来了.可根据需要利用"4M"法或是插图等来防止遗漏.·确认最末端的要素(最小骨)是否已经挖掘,明确到可以采取具体的行动(加以对策)的程度..直到(挖掘出来的)要素细到可以采取具体的行动(加以对策)时为止,要不断地重复'WHY WHY"这一程序(据说5次较为妥当)·确认要素是否有条理地被整理出来了.特性是否保持了和大骨,中骨,小骨及最小骨的关联.确认全部的要素是否都和特性有关系(有无没有关系的要素)·确认要素中有没有意思不明确的东西.多次举行集体性创造会议.因为依据不同的人对选出来的要素的阐述可能不一样..在这里有必要确认全体人员对于各种要素的理解是否相同·确认针对各个要素所采取的解析等活动是否排定了先后顺序要按重要指向将各个要素依重要度排序,按先后顺序采取行动.。
位置度影响因素及调整步骤、注意事项
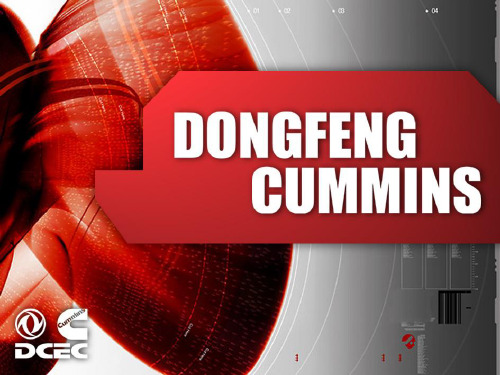
影响位置度的因素
• 那现在我们就可以来说位置度的影响因素了。简 单的说,设备的各组成部分都会对位置度有一定 的影响,只不过是重不重要的问题,但值得注意 的是,有的时候看似次要的部位有可能反而是问 题的关键。 • 位置度的影响因素有:(排名分前后) 1、夹具2、主轴箱3、导向机构4、液压气动系统5、 刀辅具6、冷却系统7、床身8、其它
夹具对位置度的影响
3、菱形定位销方向是否正确,正确的方向应 该为园弧连线垂直与两销连线。如下图:
夹具对位置度的影响
4、对于有些插拔销定位的设备还应该注意插 出销子的实际长度,插销是否到位。如下 图:
夹具对位置度的影响
三、在夹具没有夹紧的情况下检查定位面与工件是 否贴死,这可以知道工件是否在定位基面上;若 定位面上有气检装置只需读数即可,若没有就需 要用塞尺检查,若没有空间就需要在空工位的时 候在工件或者定位面上涂新鲜油漆或红丹粉等办 法来判断检查; 四、在夹具没有夹紧的情况下检查辅助支撑是否与 工件贴死,方法同上。如下图为较常用的两种辅 助支撑:
加工零件位置度超差调整前的检查步 骤及注意事项,位置度变化影响因素
编稿:李军
位置度定义
• 位置公差(俗称位置度)——位置度公差是指各实 际要素相互之间或它们相对一个或多个基准位置 所允许的变动全量,也就是加工后实际存在的位置 相对设计上规定的理想位置所允许偏离的极限范 围。换成我们的话讲,就是目标(孔、外圆等)相 对于某一规定基点或者面的实测坐标值与要求坐 标值间的误差,这个误差在要求范围内既位置度 合格,超过范围既位置度超差,这时就需要调整 位置度了。
位置度定义
如下图, φ3孔的位置度要求
位置度
• 位置度是关联实际要素对基准在位置上允 许的变动全量.包括点的位置度公差,线的位 置度公差,和平面或中心平面的位置度公差. • 对于我们公司来说,位置度的要求大多是 对于孔,所以我们这篇文章的重点也在于 孔和外圆,我们的以下内容都是基于对于 孔来讲述的。
坐标系超差位置度判定合格
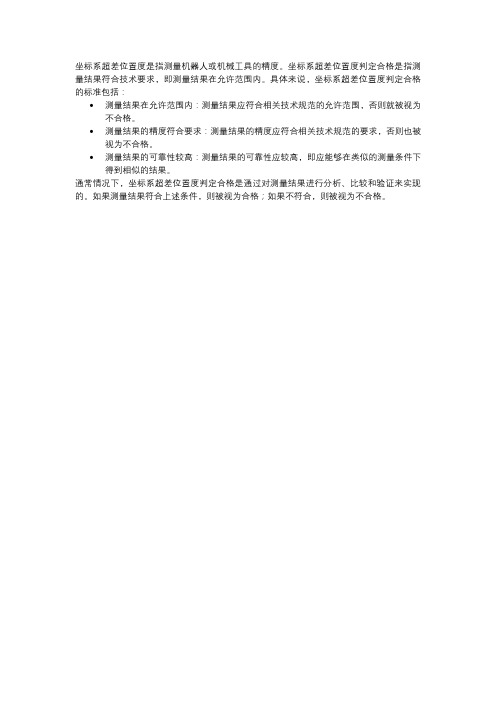
坐标系超差位置度是指测量机器人或机械工具的精度。
坐标系超差位置度判定合格是指测量结果符合技术要求,即测量结果在允许范围内。
具体来说,坐标系超差位置度判定合格的标准包括:
•测量结果在允许范围内:测量结果应符合相关技术规范的允许范围,否则就被视为不合格。
•测量结果的精度符合要求:测量结果的精度应符合相关技术规范的要求,否则也被视为不合格。
•测量结果的可靠性较高:测量结果的可靠性应较高,即应能够在类似的测量条件下得到相似的结果。
通常情况下,坐标系超差位置度判定合格是通过对测量结果进行分析、比较和验证来实现的。
如果测量结果符合上述条件,则被视为合格;如果不符合,则被视为不合格。
位置度超差分析报告
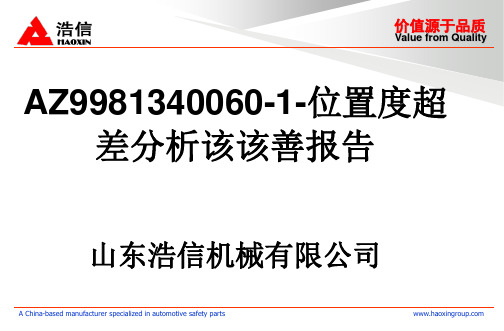
3、原因排查
1、A1毛坯料硬 经过复查成品硬度以及进货时的检验报告,发现其满足技术要求,故可排除; 2、A2不合格品混入 经查 该线不合格品均当班返修,不流转,故可排除; 3、B1程序变动 该工序是专机操作,不存在程序变动因素,故可排除; 4、B2工装超寿命使用 该工序工装使用镗刀杆、钻镗用的固定导套,经查镗刀杆的刀槽位置磕碰、高点、钻镗销套磨损,具有可能性; 5、B3设备状态不B2、B3、D2三因素可能性较大;
5、该善验证
5.1、B2工装超寿命使用 经过更换钻镗用的固定导套后,三坐标检查首三件,发现其位置度有降低趋向;
更换后固定导套
首三件调试结果
位置度降到0.20毫米以内
A China-based manufacturer specialized in automotive safety parts
6、验证结论
1、通过上述因素分析、验证发现B3设备状态不良是主因,其B2工装超寿命、D2检频低是次因;
7、预防措施
1、制动底板钻镗专机周期点检(充分发挥三坐标的功能,间断开机前进行3件或5件小批检验确认); 2、所有制动地板逐步更新工艺文件,提高检频(所有形位公差均执行首、中、末三检),封闭当班产品, 确保当班产品得以管控;
价值源于品质
Value from Quality
5.4、D2工艺规定检验频次低
该底板位置度检验频次仅仅是每班首件,频次明显偏低,且不能进行当班位置度闭环,存在一定的风险;
原工艺每班检测一件
更换后工艺每班首中末检测
A China-based manufacturer specialized in automotive safety parts
价值源于品质
Value from Quality
位置误差

为保证列车匀速运行,消除列车运行速度变化对计算结果的影响,将方向相反,大小相等的车钩力施加在列 车前后两端。施加的车钩力如图6所示。
图6
由图6可知,前5s车钩牵引力逐渐增大,之后逐渐变为制动力,车钩上施加最大制动力为500kN,与厂线实际 测试结果较接近。列车在平直线路上行驶,速度为60km/h,轨道不平顺采用美国五级谱,车钩钩尾与前从板摩擦 面之间的摩擦因数为0.2,车钩钩尾及前从板是半径分别为130和150mm的圆弧面,前后车钩箱偏离中心线距离分 别为D、-D。分别考察D取4、6、8和10 mm时,车钩5的车钩摆角、机车2A节车车体相对转向架5的横向错位、轮对 9的轮轴横向力、脱轨系数以及轮重减载率的变化。
测量方法
位置误差高效检测方法:直接利用数据采集仪连接百分表测量法。 测量仪器:偏摆仪、百分表、数据采集仪。 测量原理:数据采集仪可从百分表中实时读取数据,并进行位置误差的计算与分析,可直接通过我们数据采 集软件的计算,测量定位误差、定向误差以及跳动误差等位置误差值。 系统优势: 1)无需人工用肉眼去读数,可以减少由于人工读数产生的误差; 2)无需人工去处理数据,数据采集仪会自动计算出各种位置误差值。 3)测量结果报警,一旦测量误差值大于公差值时,数据采集仪就会自动报警。
当车钩箱偏离中心线4与6mm时,轮轴横向力较小,分别为22与29kN;当车钩箱偏离距离增大到8与10mm时, 轮轴横向力分别增大到66和89kN,约为偏离中心线4mm时的3~4倍。
采用机车轮轴横向力的安全限值为78kN,因此,当车钩箱偏离中心线10 mm时,轮轴横向力已超出安全限值; 当车钩箱偏离中心线不超过9 mm时,轮轴横向力满足安全行车要求。
谢谢7
从图7可以看出:车钩箱偏离中心线4与6mm时,制动后车钩摆角较小,最大车钩摆角分别为1.2°和3.3°; 车钩箱偏离中心线8 mm时,制动后车钩摆角较大,最大车钩摆角约7. 9°;车钩箱偏离中心线10mm时,制动后车 钩摆角进一步增大,最大车钩摆角约10.8°。
五大测量原则

阿贝原则阿贝原则又称布线原则、串联原则,是长度计量中一个基本的重要的原则。
定义:“如果要使测量仪器得出正确的测量结果,则必须将仪器的标尺安装在被测件测量中心线的延长线上。
”凡违反阿贝原则所产生的误差叫阿贝误差。
符合阿贝原则的测量示意如图2-3,不符合阿贝原则的测量示意如图2-4。
由图(2-3)知,∴由图(2-4)知,由于较小,故≈∴(一次误差,不可忽略)符合阿贝原则所产生的误差是二次误差,当a很小时,此误差可忽略不计。
不符合阿贝原则所产生的误差是一次误差,标准尺与被测件距离s越大,误差越大,,它是不可忽视的一种误差。
按阿贝原则设计的最典型的仪器是阿贝比长仪、立式光学计、测长仪等。
这样,由于导轨的不直度误差所造成的倾斜角a的影响只能产生二次误差,因此对仪器导轨直线度的要求可以降低,这就降低了仪器制造成本。
但缺点是串联布置,加大仪器长度尺寸,温度对变形影响也大。
因此,在某些情况下不得不违反阿贝原则,采用并联布置的方式。
如:游标卡尺测工件、万能工具显微镜纵向测量等。
为减少所产生的测量误差(一次误差),一方面要提高导轨的加工精度,另一方面在测量时尽量缩短标准尺与被测件的距离;阿贝原理图最小变形原则为了使测量结果准确可靠,在测量中应该尽力做到使测量链中硬件部分各个环节所引起的变形维最小,这就是测量的最小变形原则。
测量中考虑最小变形原则着重在以下几个方面:1 测量力引起的接触变形2 自重变形3 热变形最短測量鏈原則在精密測量中,被測量的微小變化量只能通過放大機構來體現。
如百分表的測量,被測量的變量首先由測杆感受並傳遞,通過齒條傳遞到軸齒輪,再通過一對齒輪放大,傳遞到表針上,通過表針與表盤刻度的角位移來指示被測當量。
從測杆接觸工件到表盤讀數就組成了百分表測量時的測量鏈。
測量鏈中每個構成元件,在制造和裝配中都存在誤差,構成元件越多,也即測量鏈越長,影響誤差的因素也就越多,誤差合成就越大。
因此測量鏈越短,誤差也就越小,這就是最短測量鏈原則。
位置度

位置度位置度定义﹕一形体的轴线或中心平面允许自身位置变动的范围﹐即一形体的轴线或中心平面的实际位置相对理论位置的允许变动范围。
定义轴线或中心曲面的意义在于避开形体尺寸的影响。
位置度的三要素:1.基准﹔2.理论位置值﹔3.位置度公差位置度公差带:位置度公差带是一以理论位置为中心对称的区域位置度是限制被测要素的实际位置对理想位置变动量的指标。
它的定位尺寸为理论正确尺寸。
位置度公差在评定实际要素位置的正确性, 是依据图样上给定的理想位置。
位置度包括点的位置度、线的位置度和面的位置度。
[1]点的位置度:如公差带前加S¢,公差带是直径为公差值t的球内的区域,球公差带的中心点的位置由理论正确尺寸确定。
线的位置度:如公差带前加¢,公差带是直径为公差值t的圆柱面内的区域,公差带的轴线的位置由理论正确尺寸确定。
一般来说我们算位置度都是X.Y两个值的偏差量去换算以基准A、B、C 建立坐标系,看具体的位置关系选择使用直角或极坐标,一般采用直角坐标,测出被测点到基准的X、Y尺寸,采用公式2乘以SQRT(平方根)((x2-x1)平方+(y2-y1)平方)就行,x2是实际尺寸,x1是图纸设计尺寸,计算出的结果就是:实际位置相对于设计的理想位置的偏移量,因为位置度是一个偏移范围¢,所以要乘以2这个常见的公式不是同心度就是插芯内径距离整个圆心的偏移程度.理想状态是0,就是不偏移.但是实际上都有偏移,一般单模PC同心度在1.0以下,算是比较好的产品了.同心度越小,光纤对接程度越好,光信号耗损就越小.位置度,是多种形位公差(形状和位置公差)中的一种。
如此一来这个“位置度”一词就好理解了。
它的意思是,被标注对象在实际物体上的位置,所允许出现的误差范围。
如你上面所写,意思为,以A,B,C三个面为基准面(标准平面)要保证所标注的物体与三个面之间的位置误差不得超过0.1。
而有φ者是说偏差是在一个圆面的范围内,而不带的则是表示直线上的偏差为多少。
- 1、下载文档前请自行甄别文档内容的完整性,平台不提供额外的编辑、内容补充、找答案等附加服务。
- 2、"仅部分预览"的文档,不可在线预览部分如存在完整性等问题,可反馈申请退款(可完整预览的文档不适用该条件!)。
- 3、如文档侵犯您的权益,请联系客服反馈,我们会尽快为您处理(人工客服工作时间:9:00-18:30)。
大长江纳 入时间
纳入数量
2010.12.28 240只 2010.12.31 120只 2011.1.8 170只 2011.1.10 160只
2011.1.12 190只 2011.1.14 170只
2011.1.16 180只 2011.1.16 60只
54111H05712 10.12.24 134只
1.车(机)型:
2133
型号
q72
2.发生时间: 2011-02-16 3.发生地点: 过程
4.发生数量: 12
5.不良比例:
6.批 次 号: H10200044 7.到货时间: 2011-01-29
8. 发 前轮辋4-M8-7H螺纹孔位置度超差要求ф0.15,实测不良件均 不过检具,三坐标检测1只数据为1.540,装不上制动盘。 9.处置情况:1、生产现场跟线挑选;2、库存退回厂家挑选
攻丝所有工序由原来的涂装车间加工完成改为机加车间
完成,在没交接完毕情况下,机加车间安排了1个气试
人员进行上机操作,其余没变化 。
3.生产过程同类问题发生情况调查:
通过调查,发现以往无类似情况发 生。
● ● ● ● ● ●
车削加工
☆发生工序 螺纹孔加工
巡检
☆流出工序
前处理
● ● ● ● ● ●
发送
要因
五、横向展开、反馈到源头(系统、体制等)
1.分批对机加工以及检验员就整车装配和异常处理进行培训
。
责任人:陈巧华/朱海贵
完成时间:11.02.26
2.分批对机加操作工就所有工序的工艺工装标准进行培训。
责任人:徐旭阳
完成时间:11.02.28
3.对车间管理人员的执行力进行培训。
责任人:朱丹华
完成时间:11.02.28
2010.12.30 1.3
32 32.7 34.18 33.26
2
L
2010.12.30 1.3 32.02 33.1 34.04 33.4
3 4
L
2010.12.30 1.3 32.02 32.82 33.08 33.1
L
2010.12.30 1.3 31.76 32.97 34.28 32.8
10.12.27 50只 10.12.28 84只
库存:12只
11.01.05 164只
2011.1.7 164只 库存:133只
2011.1.26 110只
54111H05712 10.12.27 60只
10.12.31 60只 库存:20只
11.01.06 52只
库存:23只 2011.1.8 52只
4.编制《巡检记录表》,检验员在巡检过程中及时记录检查
结果,并对检验员进行培训。
责任人:朱海贵
完成时间:11.02.20
A2版
2
1
5
L
2010.12.30 1.3 31.92 33.12 34.04 32.94
6 7
不良品
L L
8
L
9
L
2010.12.30 2010.12.30 2010.12.30 2010.12.30
1.3 1.3 1.3 1.3
31.96 31.72 32.02 32.02
33.12 33.22 33.3 33.2
一
不良品的确认结果
1.现象说明:位置度超差是导致碟刹盘无法装配的直接原因。
2.不良品与正常品的外观差异:
不良品
不良品
正常品
正常品:四个螺纹孔中心距尺寸无偏差; 不良品:四个螺纹孔中心距尺寸明显存在偏差。 3.与作业指导书的对比:
产品 序号
类型 模具号
生产日期
合格证 日期
1
尺寸33mm
2
3
4
示意图
1
L
○
业指导书 判定方法
涂装车间与机
新员工在上岗 加车间在没交
前需要经过培 接完毕情况
员工技能不足 训和考核,合 下,机加车间
×
格后才能上岗 安排了1个气
操作 试人员进行上
机操作。
检验员没有巡 要求检验员进 当班检验员没
检
行巡检 有进行巡检
×
○:排除在要因外 ×:致命要因
要因分析概括: 1.操作工属于无证上岗。 2.当班检验员没有进行巡检。
规定
事实
判定
抽查库存,轮
轮辋跳动不良
轮辋跳动≤ 0.5
辋跳动 进行测算,
○
Cpk=1.55
机床精度不良 Cpk≥1.33 Cpk=1.38
○
四个方向的等 等高块尺寸一
工装不良 高块尺寸相等
样
○
定芯跳动≤ 定芯跳动为
0.02mm
0.02mm
○
要求各道工序 该工序有明确
工艺文件无 都有完善的作 的检验标准及
2011.02.16 2.20
33 33.14 33.04 33.06
5
L
2011.02.16 2.20 33.08 33.02 33
33
平均
33.04 33.06 33.04 33.01
判定
OK
4.确认结果的总结: 4个螺纹孔中心距圆心往第3个螺纹孔方向偏移了1mm,造成位置 度超差,直接导致碟刹盘无法装配。
置架,便于和正常品区分 品全部归放到不良品放置
架上 1.建立 《异常品处理流
5
没有异常品处理规定
/
程》 2.对现场检验员以及操作
工进行培训与考核
1.制作首末检产品放置
6
现场无首末检产品放置架
/
架,并放在该道工序的现
场
调机完成后检验员进行首
7
检验员没有进行首检
调机完成后检验员进行首检 检,首检合格的产品放到
2011.1.29 240只
11.01.08 72只
2011.1.11 72只
54111H05712 10.12.30 274只
11.01.02 130只 11.01.03 144只
11.01.10 36只
2011.1.12 36只 2011.1.13 108只
库存:222
11.01.11 108只
2.变化点调查: 54111H05712 11.01.04 205只 54111H05712 11.01.06 150只
11.01.08 105只 11.01.09 100只 11.01.10 96只
库存:703只
针对上述不良批次从11人.01库.1存1:145只4只、机、料、法、环、测量进行变
化点调查,发现人员状况有变化,2010年12月份我司将
11.02.19
11.02.19 11.02.27
已完成 11.02.27
已完成 11.02.20 11.03.10
3
4
5
调机时未对中心用杠杆百分表进 行校正
员工上岗未经过培训
管理人员没有按制度执行
/
检验员没有按照制度执行
/
/
/
四、检查对策效果(量化的实际效果)
1.今飞外租库库存品1100只进行全检,有13只不良品。 2.今飞库存品1290只进行全检,未发现类似不良产品。 3.对策实施后对该产品的位置度进行CPK测试,测试结果 为:1.3595>1.33 OK
库存:12只 10.12.22 22只 10.12.23 38只 10.12.25 86只
库存:42只
发货时间 发货数量 10.12.30 380只 11.01.03 116只
今飞外租 库接收时
间
今飞外租 库数量
截止12月25日外租 库库存量为763只
库存:73只
2011.1.1 380只
库存:93只 2011.1.5 116只
问题点
1.新员工上岗 不具备调机能 力,造成调机 不良 2.新员工不了 解该道工序的 送检频次 检验员没有巡 检造成不良品 流出
二 、
再现试验:
发生机理: 新员工调机
刀具中心与
四个螺纹孔
发生原因:
1.刀具和工装定芯没有同心。
流出原因: 1.操作工没有自检和送检。 2.调机后检验员未进行巡检。
分析为什么、为什么 阶段
装的中心不同心。
操作
3.该道工序的操作工实行
每月考核一次,合格后上
岗
3
操作工不了解该尺寸的重要性 操作工掌握本道工序的作业 对操作工在工艺方面的知
没有自检和送检
指导书上的全部内容
识进行系统的培训
在攻丝工序机床旁边划分 各道工序现场都应该划分一 不良品放置区和不良品放
4
现场无异常品放置区域
个不良品放置区和不良品放 置架,生产过程中的不良
库存:78
54111H05712 11.01.01 203只
11.01.04 90只
库存:51只
11.01.05 113只
2011.2.14 180只
54111H05712 11.01.02 210只
11.01.06 100只
11.01.07 110只
11.01.17 832只
2011.1.19 832只
大长江编 号:
W2011021602
编 号:
标题 零件图号 发起人 签发日期
前轮辋装不上制动盘
54111H05712 谭晓武
零件名称 审批人
前轮辋 潘小平
2011-02-17
请于2011-03-14前返回
五原则表
责任单位
金华今飞
年月日
制作
确认
徐申
批准
确认/日期 批准/日期 接受 报告
得分
发生状况(发生件数、发生现象、处置情况等)