5原则表
问题解决5原则表的作成和运用指南

■不良现象的要因调查
・「什么时间、在哪个工序、发生了 什么?」
⇒锁定对象工程和对象批量 ・一般的记入内容
・工程的确认 ・每次确认的时候有无引起相关 不良的可能性 ・工程调查结果
工程履历、数据、作业记录 调查作业者的结果
5原则表的作成 (2)原因の究明
实施2种原因的究明!
別紙デ-タ10参照
○:マツダ様にて確認結果、 接点部導通しっぱなしなし
○:メカでの強制 O FF構造であ
接点溶着
り接点溶着なし
別紙デ-タ11参照
組み付け手順 間違い
○:マツダ様にて確認結果、 組付け手順に問題なし
スイッチ内部ズレ
バネ 不良
×:現象確認
別紙デ-タ3,4参照
下ケース
摺動体
接点
ランプ 接点組成
第2阶段 <对象扩大>
出荷
顾客
顾客索赔
必须! 第1阶段
5原则表的作成运用要点
①首先要优先于开始活动! 不要对策后才报告 ⇒中途经过也可以要向顾客迅速报告!
②不能只有QC担当者作成! 由主要因部门作成、QC协助、承认是基本的途径。 ⇒若是生产的要因那就是制造、设计的要因是技术… 当然要用CFT作成讨论
通过对问题进行4个合理的思考过程分析,从而得出正确的结论。
自然人的思考过程=从以下4个角度进行反复提问,对其结论进行持续考虑。 ①什么课题?(WHAT) ②为什么会那样?(WHY) ③怎样入手解决?(HOW) ④若什么的话会不会引起什么?(IF)
◎状况把握过程(略称SA=Situation Appraisal) 引起什么?→课题是什么?
要点:「目前的处置怎么办?」 首先要检讨不能扩大顾客困惑的处置方法。
五原则表填写规范

1.对策内容(明确对策责任人及期限)
·根据KT法等选择、决定对策方法 要点:
·即使是人为因素也要考虑从硬件
1、从发生、流出
方面的对策
两方面原因决定可
2.对策年月日、对象部品、机种、车身号 3.暂定对策与恒久对策的效果预测
(根据问题再现试验或检查确认数据
以排除问题的,有 针对性的对策. 2、在不得不由人 来对策 时,要充
判定
2、全工序检证(对全工序确认,查找不良发生工序和流出工序)
3、不良发生要因调查(尽量使用图、表等来表达)
发生要
O
.利用特性要因图、FMEA、KT法进行分析
因
X
.对发生要因、流出要因和事实的验证
4、调查结果总结、变化点和推断原因总结
流出要
X
可以说问题一定源于变化点(人、物、设备等) 因
O
2-B 原因调查(发生的途径、问题再现试验, WHY WHY分析)
要点: 1、确认数据的取样数量,最终确认需要的时间 也很重要 2、确认所实施对策对正常作业程序有无不良影 响 (确认工程熟练度) 3、确认人的熟练程度(确认对人有无风险)
无法通过数据进行比较的对策不是 真正对策
2-A 原因调查(“WHY WHY”分析)
步骤
1
要点:与要因相关的管理标准及事实,利用系统的、有条理的Q&A(提问和回答)方法,抓住找出真正的 原因,从大骨到小骨,因果关系要清晰明了,要将各种要素尽可能完整准确地归纳、整理出来
的NO.1~5,要确认对比有没有按大骨到小骨的顺序排列清楚 (如果顺序不对那就是其中的一个不妥)
从问题的主要原因找出真正原因
EG设备,HG仕样) 5.为更好地实施对策和遏制不良的再发,需要将对策内容落实到组织及 管理体制当中 6.根据需要再开展FMEA
五原则表(pdf 3页)

原本保存期限:
年
月
பைடு நூலகம்
~2. 问题件、制造年月日
… 等、按工艺顺序和时间顺序整理。
~3. 问题件、发生个数、发生率
4. 预测发生件数及批次。
5. 确认重点。
~1. 与没出现问题的比较其特征及变化。
~2. 确认出现不良的日期和时间。
6. 工艺调查结果的归纳方法 … 按工艺流程和时间系列以变化为主填写。
7. 变化点和推断原因。
【目的】
1. 下次行动时锁定目标。 2. 真实填写发生的原因和状况,以便使不良零部件、部位更清晰
【填写内容】
1. 机种、机型等
2. 车身号码、发动机号码、批号等。
3. 发身地点。
4. 发生年月日。
5. (发生后在销售店)登记年月日。
6. 行使路程/时间。
7. 发生内容/原因
~1. 地理位置。
~2. 对象件的何部位。
~3. 何时。
~4. 发生方式。
~5. 什么条件下。
~6. 发生比例。
~7. 发生倾向。
8. 该车、该机的处置方法和程序。
9. 出货件的确认结果。
掌握事实 (零件确认结果・主要原因分析・产品质量状况)
【目的】
1. 事情发生的情况(最初原因)和再现试验 … 决定不良零件、部位。
2. 明确零件、部位的不良原因。
- 无法再现的问题会再次发生 -
【目标】
1.证明品质、成本、日程都是最合适的, 以防止出现的情况再次发生。
【填写内容】
1.引起问题零件/部位的硬件(设备、夹工具等)的临时对策、不能消 除真正原因时的适当对策、针对真正原因的纠正对策日程和责任人。
2.防止问题零件/部位流出的硬件(QA机、防出错装置等)的临时对策、 不能消除真正原因时的对策、消除真正原因的纠正对策推进日程和 责任人。
五原则表的应用 (1)

4对策效果确认—效果实绩
5反馈—需落实到体制、组织的内容
⑤
⑥
跟进日期
⑦
⑦ 反馈—需落实到体制、组织的内容
目的: 1、向体制、机构的反映是防止同种/类似问题发生
2、将从问题学到的向全公司或全科推广
⑦ 反馈—需落实到体制、组织的内容
填写的内容
1.将持续维持硬件对策的项目反馈到相关部门(基准、标准、设备 的管理等) 2.将问题反馈到其他部门(横向展开)(规程、基准、技术积累等)
发生搬入异常的不良事项后,要尽快要 求供应商提交五原则报告!!!
问题描述
供应商名称
部门
确认 制作
CHAC接收部门
解决问题的5原则表
1-A发生状况--现象、投诉内容、发生件数、处置内容(5W2H)
日期
审批
审批
确认
1-B事实把握--确认结果、分析要因、品质状况
事实: (此表背后可用头脑风暴Fra bibliotek(1-C)和特性要因图(1-D)
的情况再次发生; 2、对策可能带来新的问题进行分析(P.P.A)、评价(预 测),并制定预防的计划
⑤ 对策—对策内容、预期效果、潜在问题分析
填写的内容
临时对策
永久对策
对策内容 / 对策 年 月 日 ① ②
・发生对策
对策内容 / 对策 年 月 日(预定日)
① ② ③
・流出对策
对策内容 / 对策 年 月 日(预定日) ① ②
问题① 为什么② 为什么③ 为什么④ 为什么⑤
②
2-B原因分析—分析问题和答案、问题产生过程、问题再现测试
③
④
3对策—对策内容、预期效果、潜在问题分析
4对策效果确认—效果实绩
广本5原则培训资料

☆集体创造性思考 ☆特性要因图
• 调查结果总结、变化点和推断原因总结
4、现在的対応状况(緊急処置後的)
• 用X-R管理图 、矩形图、CP值等
可以说问题一定源于变化点(人、物、设备等,4M1E)
1、老七种工具: 调查表 分层法 排列图 因果图 直方图 控制图 散布图 2、新七种工具 亲和图 树图 关联图 矩阵图 箭条图 PDPC法(过程决策程序图法) 矩阵数据分析法
・可用于解决开发、生产、销售、供应、管理等 所有领域发生的问题。
来自顾客的意见、投诉产品、服务不好 设备、机械、机器的问题 精确度与效率不高的工作
解决问题、防止再发
五原则工作表
重要度的决定及处置判断
• 重要度、麻烦度、重要保安部品判断
零件品质科
重要度
麻烦度
重要保安部品
A 不良时判断为危害人身安 A 已进行整车的检测、修理 HS
17 240±5 +7 +8 +9
P21
10 270 SET SET SET
(工序概要) No 工程名 1 来料仓库 2 端末加工 3 弯管加工 4 最終検査 5 出荷
加工機種名 起因 西岛端末加工机 T型弯管机 ★ -
*根据现品确认,弯管形状有同样倾向
■ 5原则工作表(解析报告)
是指从发生问题的初期对应到彻底解决问题,防止再发的问题解 决手法。是本田特有的问题解决手法。
目的:通过对不良问题进行有条理的、理论性的分析(三现主 义) ,查找真正的原因,采取适当的对策,防止问题再发。
・解析报告要将解决问题流程的结果用1张纸(A3)总结后进行报告。
■ 使用范围
集、整理)
• 工序中现正生产的零部件的品质状况、良品批次确认(根据X-R管理图、工程
五原则表(填表说明)

日 批准
在发生、流出
问题点
定
●规定也
有不对的 ●不能遵 守的地方 生的可 很多 因 ●也有评 价方法不 好的
除要因
析
达出来)。
现试验)
②用对策后量 Cp/Cpk>1.33
似产品、工艺
制等。
要因
规定
事实
判定
问题点
从下列方面查 列出发生的事 ●规定也有不 找: 实 明确基准出自 〇:排除要因 对的 ●作业顺序 ●按照规定实 哪里 ●不能遵守的 ●产前准备 施 ●工程QC表 ╳:发生的可 地方很多 ●作业点检 ●没有遵守规 ●作业指导书 能原因 ●也有评价方 ●设备修理 定(明确和通常 法不好的 ……等等 作业有何不同)
发生原因
发生工序
流出原因
基于5M1E(人、机、料、法、环、测)调查。
3.生产过程同类问题发生情况调查:
流出工序
流出原因
9.处置情况:
①发生问题的车(机)及零件的处理:怎样处置(换装、挑选、调整、返修 等); ②发生日前生产的车(机)检查结果:X月X日XX辆 NG X辆; ③库存零件检查处置:X仓库库存XX个检查,NG XX个,如何处置。
要因 触点柄外径 偏小
规定 2.0-0.1
事实 抽查库存,触点 柄尺寸进行测 算,Cpk=1.52
判定 ○
问题点
抽查库存,触点 触点柄高度 1.4±0.1 柄尺寸进行测 偏小 算,Cpk=1.43 下触臂孔内 径大
+0.1
○
2.0
抽查库存,弹簧 片孔尺寸 进行测算, Cpk=1.38
○
抽查库存,弹簧 下触臂孔厚 片孔尺寸 0.4±0.02 度超差 进行测算, Cpk=1.44 要求检查 未进行过程 触点铆接 检查 后强度 作业环境 工装 外观检查 无要求 无要求 无要求 检查记录有触点 强度检查 现场灯光暗 无定位 没有铆偏限度样 板,不易操作
五原则表培训教材
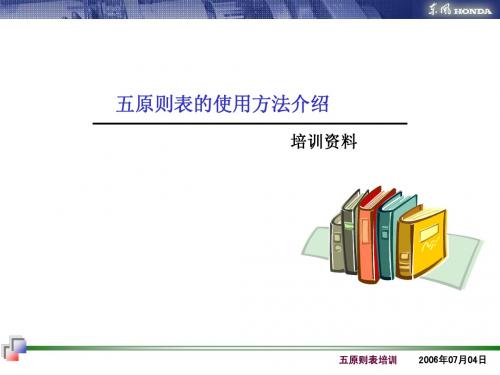
27.3333
11000-PWC-0202
零件名称 零件号
问题零件的名称 对应于部品表的零件编号
日期
批准日期
提出部门 批准 审核
管理科 自制品质系
审核
发现区域检技
自制品质不良主要由管理科提出五原则对策要求及跟踪推进!
日期
编制日期 科 长
批准
副 科 长
编制部门 检技
检技
系长
系长
班长
班长
编制
担当
责任部门负责五原则表的编制,由检查技术者审核后,交由科长批准!
不良发生对策 ・加工设备内铁屑清扫
对策人:刘×× 对策时间:5月6日
《恒久对策》
不良发生对策 ・在护板上安装吹气装置
・在作业标准书里,追加吹起 装置的确认项目.
对策人:刘×× 对策时间:6月6日
不良流出对策 ・车削QA机判定为不良品后的处理
对策人:王×× 对策时间:5月7日
不良流出对策 ・QA机排出不良品的处理方法明确化. ・车削QA机不良品处理台帐的作成 ・车削QA机不良品的处理作业标准书 作成.
再现品的不良现象和现品一样。从这样的结果 来看,这次的不良是由于铁屑的残留,工件在偏心的 状态在被加工所致的。
五原则表培训
2006年07月04日
【 为何-为何分析】
1-对主要原因进行五次为何为何分析,将问题反馈到源流进行改善。 2-对不良发生的为何-为何分析。 3-对不良流出的为何-为何分析。
记录查明原因的过程
五原则表培训
2006年07月04日
【 把握事实】 例
①
③
Y 方 向
測定箇所
① 中心孔深度 ② 小端面位置 ③ 螺纹上部轴径 ④ 螺纹大径 ⑤ 花键大径 ⑥ OP径 ⑦ 导向径 ⑧ 外圆直径 φ93.7 φ90.7
三现五原则表
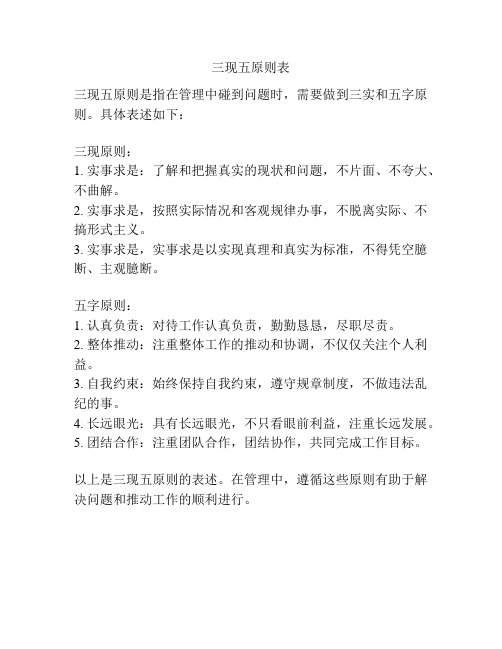
三现五原则表
三现五原则是指在管理中碰到问题时,需要做到三实和五字原则。
具体表述如下:
三现原则:
1. 实事求是:了解和把握真实的现状和问题,不片面、不夸大、不曲解。
2. 实事求是,按照实际情况和客观规律办事,不脱离实际、不搞形式主义。
3. 实事求是,实事求是以实现真理和真实为标准,不得凭空臆断、主观臆断。
五字原则:
1. 认真负责:对待工作认真负责,勤勤恳恳,尽职尽责。
2. 整体推动:注重整体工作的推动和协调,不仅仅关注个人利益。
3. 自我约束:始终保持自我约束,遵守规章制度,不做违法乱纪的事。
4. 长远眼光:具有长远眼光,不只看眼前利益,注重长远发展。
5. 团结合作:注重团队合作,团结协作,共同完成工作目标。
以上是三现五原则的表述。
在管理中,遵循这些原则有助于解决问题和推动工作的顺利进行。
5原则表填写说明

作业要领书的修改
□要 □否
条件表的修改 其他
□要 □否 □要 □否
18/23
19/23
通过对标准类(QC工程图、检查基准书、作业指示书)的 完善,明确再发防止策、对策实施效果的继续・维持方法。 ①判断需要对哪些文书进行修改。
作业标准类:PQC、检查基准书、作业指导书、包装 类指导书、作业要领书,条件表等
①取得正确的事实. ②针对发生及流出原因,用分析图明确表示 ③明确不具合发生基本原因. ④反复为什么为什么找到真正发生的原因. (更进一步使用春风分析图分析原因) ⑤进行适当对策并实施. ⑥反映到标准类、体系中. ⑦确认效果及数值.
1 3
6/23
2
5 4
6
1.发生状况(现实)
7/23
①.现象·投诉内容
□要 □否
担当
纳期
检查基准书的修改
□要 □否
作业指导书的修改 手顺书的修改
□要 □否 □要 □否
PIR记录项目变更
□要 □否
日常/定期点检项目变更
□要 □否
保养项目变更 异常处理方法变更
□要 □否 □要 □否
图面(治工具/金型/制品)的修改 □要 □否
FMEA的修改 包装类指导书的修改
□要 □否 □要 □否
发 生
内
容
流 出
探明原因[采用系统图法进行分析。] 从各个角度反复重复为什么为什么,抓住根本性真 正原因明确填写认为是最受影响的项目。
现象
为何发生
为什么
为什么
为何流出
为什么
为什么 为什么
为什么 为什么 为什么 为什么
为什么 为什么 为什么 为什么 为什么 为什么 为什么 为什么
5个基本原则
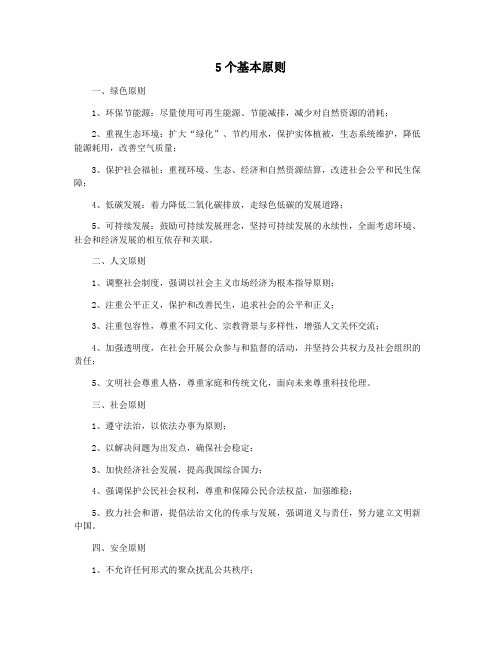
5个基本原则一、绿色原则1、环保节能源:尽量使用可再生能源、节能减排,减少对自然资源的消耗;2、重视生态环境:扩大“绿化”、节约用水,保护实体植被,生态系统维护,降低能源耗用,改善空气质量;3、保护社会福祉:重视环境、生态、经济和自然资源结算,改进社会公平和民生保障;4、低碳发展:着力降低二氧化碳排放,走绿色低碳的发展道路;5、可持续发展:鼓励可持续发展理念,坚持可持续发展的永续性,全面考虑环境、社会和经济发展的相互依存和关联。
二、人文原则1、调整社会制度,强调以社会主义市场经济为根本指导原则;2、注重公平正义,保护和改善民生,追求社会的公平和正义;3、注重包容性,尊重不同文化、宗教背景与多样性,增强人文关怀交流;4、加强透明度,在社会开展公众参与和监督的活动,并坚持公共权力及社会组织的责任;5、文明社会尊重人格,尊重家庭和传统文化,面向未来尊重科技伦理。
三、社会原则1、遵守法治,以依法办事为原则;2、以解决问题为出发点,确保社会稳定;3、加快经济社会发展,提高我国综合国力;4、强调保护公民社会权利,尊重和保障公民合法权益,加强维稳;5、致力社会和谐,提倡法治文化的传承与发展,强调道义与责任,努力建立文明新中国。
四、安全原则1、不允许任何形式的聚众扰乱公共秩序;2、加强食品安全监管,确保食品安全;3、维护少年儿童的安全和血液安全;4、坚持性贩运禁毒斗争,全面开展预防毒品滥用工作;5、强化消防安全,加强联动机制,确保公民生命财产安全。
五、创新原则1、实施科技创新政策,不断推进现有的先进技术的研发;2、注重协同创新,加强技术领域的国际合作;3、大力发展低碳和清洁能源,着力提升新能源产品;4、支持企业家创新社会,推动数字经济发展;5、加强与国际创新技术及标准的接轨,提升我国技术水平。
5原则表填写说明
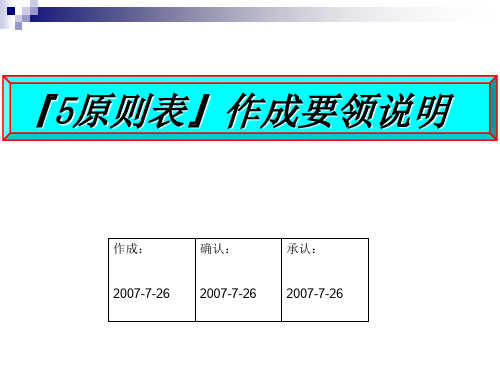
□要 □否
条件表的修改
□要 □否
其他
□要 □否
担当
纳期
18/23
19/23
通过对标准类(QC工程图、检查基准书、作业指示书)的 完善,明确再发防止策、对策实施效果的继续・维持方法。 ①判断需要对哪些文书进行修改。
作业标准类:PQC、检查基准书、作业指导书、包装 类指导书、作业要领书,条件表等
生产类:PIR、日常・定期点检项目、保养项目、异常 管理方法等
某某人的 头受伤了 好例
头撞到天 花板低处 的角
角处未铺 设保护材
天花板低 的部位的 角处铺设 保护材。
※避免向人的心理面追及原因。 ※分析的方向要向着能防止再发的硬件面、管理面等。
发生原因和流出原因的总结
发生原因和流出原因的总结 ①真正原因的再现试验
②发生原理
③流出原理
④批波及性
14/23
15/23
⑥.相关帐票管理№.(工程异常处理、NRS、CIS等)
⑦.希望事项(至急/重点确认事项及回复纳期)
发行部门期望的事项。
8/23
2.事实的把握(现场·现物·现实)
2.事实把握(现场・现物・现实)
① 不良确认结果(观察制品:确认异常制品与正常品的区别)
②工程要因确认结果(观察制造工程:确认工程的变化点和变更点、工程的运用规定和实际状态)<判定的类别有 OK,NG,不确定>
市场品质情报 最近卖桶商人
收入高涨
解决问题 作捕鼠装置
深入问题 解决
想办法让沙子 不能进入眼睛
真正原因的对策
注意点:为什么为什么分析的观点
坏例
现象
某某人的 头受伤了
为什么①
头撞到天 花板低的 部位的角
五原则表(内部培训081113)
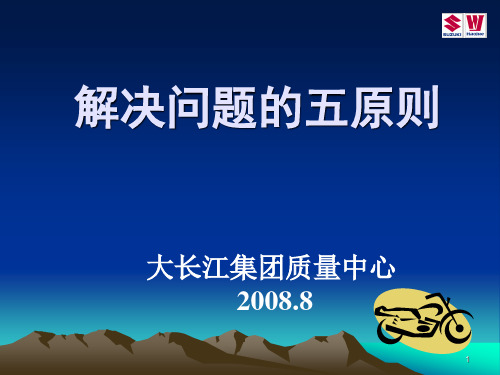
写好五原则表的关键:运用五原则手法分析、 写好五原则表的关键:运用五原则手法分析、解决问题
5
五原则表填写要领
01.标题 标题
发生状况 现状把握
02.发生状况 发生状况
1-1 不良品确认 结果
合适 的 对 策
1-2 批次跟踪 化点、 变化点、 异常点调查
1-3 原因分析
查 明原 因
检查对 策 效 果
其三 问题如果提出来了 决不能说: 决不能说: “这是不可能的”
其四 再现试验成功的 重要的因素是 现场的真实的数据』 『现场的真实的数据』和 决不能放弃的执着』 『决不能放弃的执着』
8
1
充分把握事实
五 个 步 骤
3 4 5
2
2 实 实
三现主义
不但适用于制 造现场, 造现场,也适 用于广泛的其 它工作。 它工作。
亲自接触实物
亲自到现场
(现物) 现物)
总是以事 实为基础 而行动
(现场) 现场)
亲自了解实际情况
(现实) 现实)
3
三现主义
• 现场:不要只坐在办公室决定,而是要立即赶 现场:不要只坐在办公室决定,
到现场。现场每天都在变化, 到现场。现场每天都在变化,不具备正确的观察 方法,你就没法感觉它的变化,包括异常。 方法,你就没法感觉它的变化,包括异常。
• 现物:不能脱离实物凭空推测,只有仔细接触 现物:不能脱离实物凭空推测,
实物并客观地观察其过程,掌握第一手资料( 实物并客观地观察其过程,掌握第一手资料(包 括人的因素),才能找到隐藏的原因。 ),才能找到隐藏的原因 括人的因素),才能找到隐藏的原因。
• 现实:解决问题需要你面对现实,把握事实真 现实:解决问题需要你面对现实,
五原则表-解析报告(广本资料)

对策前
对策后
品质科 11/30 品质科 11/30
洞穴
溶接固定 实车 同条件
实车
同条件
标准
五原则表培训
零件品质科
4、对策效果(效果实绩)
1. 工序、市场的对策效果确认结果和确认时间 (・效果是由品质数据、数量等在对策前后的变化而取得 的)
五原则表培训
原因分析常用统Q计C工小具:组因活果图动系的统具图 体关联程图序
零件品质科
2、正确、恰当的应用统计方法 方法名称原因适分用析场常合用统计工具原:因因之果间图的关系系统图展 关开联层图次
三种图示方法的运用
因果图 针对单一问题
原因之间没
/鱼骨图 进行原因分析
有交叉关系
一般不超过四层 超过用系统图
• 重要度、麻烦度、重要保安部品判断
零件品质科
重要度
麻烦度
重要保安部品
A 不良时判断为危害人身安 A 已进行整车的检测、修理 HS
全的重大危害 操纵、行走、制动
火灾、感电、公害、安全 不能保护
除A外,产品机能和商品
已进行零件的检测、修理
性受到损害
B
B
HA
不良时,重要机能丧 失,可能引发重大事 故
不良时,重要机能丧 失,可能引发重大事 故,但可预知并进行 安全处置
(要因分析)
(零件的批次追踪)
11月
3日
弯管
60
最終検査
出荷
物流仓库
广州本田
15日
调机
16日
30 90
17日 18日 21日 22日 23日
90 90
不良
30
对象零件范围:11月15日调机后所生产的30根(LOT)全判定为NG品。
五原则表教材

[信息反馈日] 反馈日2009年3月17日 1.<発生状況的把握>・・・発生情報的整理
[发生件数] 五次累积反馈70496件 ①.发生内容 ②.発生月日 ③.発生件数、率
[发生场所] 越南本田(HVN)
④.発生場所 ⑤.生産場所(責任区) ⑥.処置
[生产场所] 东睦(天津)粉末冶金有限公司 (日系JV取引先:東睦工業)
作動不良
模具拉伤
油量少い
人
产品附着杂物未检查
检查不 仔细
责任心不强
工件放置未检查
材料成分不適 異材
材料
检查作业指导书不完善
流出不良没跟踪控制
工艺流程变化
产品摆放方式不对
5S
人员没培训
停電
操作方法不当 作標不完善
異物付着
方法
环境
齿形不良
歯型NG的要因
検討
1.<根据特性要因図推断要因>・・・推定原因検討
現場検証的因素为基础,实施再現试 验,找出原因。 ・・・①.試験条件、方法的明確化
过程再现:再現試験状態
当上冲向下运动时,被异物垫起的 齿尖部分损伤阴模。
标记点
齿顶处与阴模内腔接触
上冲
齿轮 ● 下冲
鉄異物 2φmm
由于有杂物存在,产品被垫起
发生1°的倾斜
在通常的sizing加工条件下 阴模 模具内側咬入2φ的鉄異物进
五原则表教材
1.問題解決的五原則的必要性
「問題解決的五原則」的思路 推进品質管理活動后, 重要的是发生問題時,通过現場、現物
現実的三現主義很好的观察、把握事実,实施合适的対策,不使同样的两次 或者同種的問題发生。
在不適合発生時,如不认真找出真正的原因的话,就无法取得有效的対策, 无法做到再発防止。
- 1、下载文档前请自行甄别文档内容的完整性,平台不提供额外的编辑、内容补充、找答案等附加服务。
- 2、"仅部分预览"的文档,不可在线预览部分如存在完整性等问题,可反馈申请退款(可完整预览的文档不适用该条件!)。
- 3、如文档侵犯您的权益,请联系客服反馈,我们会尽快为您处理(人工客服工作时间:9:00-18:30)。
※所谓再发是同一产品、因同一原因一年内再次发生(在判明原因阶段决定是新规还是再发)
QA001-04
解决问题的5项原则
发生状况
发生日 发生场所 发生状况
事实的掌握
(部材的确认结果・ 原因分析・ 生产品的品质状况) 2-2 不合格品的发生状况·原因分析
◇制造流程(发生・流出工序的明确化) ◇工序変更/変化点的有无 ◇原因分析 ◇对象批次范围
◇ ◇ ◇
2-1 不合格确认
◇实物确认・解析结果 ◇良品/不良品的高精度分析测定结果→(环境品质适用) ◇工序履历调查结果 <>解析结果汇总
3-1 原因分析
步骤
1
2
3
4
5
内 容
发生原因
<>体制方面 ・ 管理工序图 ・ 作业指导书 ・ 记录表单 现场确认 ・ 评价
要修正 要修正 要修正 (
不要修正 不要修正 不要修正 要 ・ 不要)
修正实施日 修正实施日 修正实施日
年 年 年
月 月 月
日 日 日
购买担当责任者
流出原因
确认实施日 年 月 日 ・ 确认者 / /
◇ 不合格内容 ◇ 产品编号
◇ 生产线(设备)
不合格品的处理
P在库 流通在库 仓库在库 工序在库 其它
处理内容数量等
(ナゼナゼ分析 ・メカニズム ・再現テスト) (原因分析・ 发生原理 ・ 再现试验) 3-2 发生・ 流出的发生原因 (归纳.图示) 3-3 再现试验(装置检证,确认)
3
原因的究明
4
适应对策
(环境品质/部品 ・ 材料适用)
供应商 件名 产品品番 厂检查不合格 其它 工序品质异常 设计 工艺/设备 测定仪器 环境品质入厂检查不合格 材料 人为原因 作业方法
(品质改善处理报告书)
购入先
№:
5
新规 再发
2
原
则
表
公司名称
SK
FSK
品管课长
责任部门
作 成 者
部门 姓名
(対策内容 ・効果予測) (对策内容・ 效果预测) 対策日 担当部門
5
对策效果的确认
确认日 确认者
4-1 发生原因对策
5-1 对策效果的确认
5-2 对策的横向展开(对象品・ 内容・ 对象部门) ・他部材品番的横向展开 ( 要 ・
不要) 不要)
4-2 流出原因对策
・采购其他设备的横向展开
(
要 ・
5-3 再发防止〔向源头的反馈〕 ◇技術方面