品质改善之三现五原则对策表
品质的三现五原则
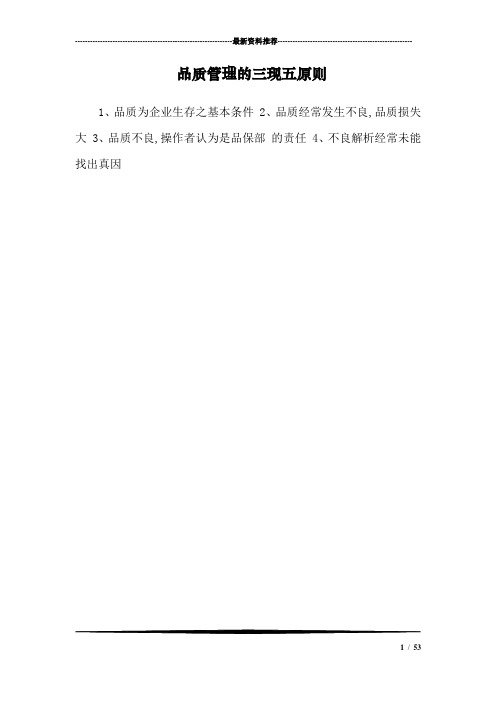
---------------------------------------------------------------最新资料推荐------------------------------------------------------品质管理的三现五原则1、品质为企业生存之基本条件2、品质经常发生不良,品质损失大3、品质不良,操作者认为是品保部的责任4、不良解析经常未能找出真因1/ 531、了解并运用三现五原则解析手法,真正改善重要品质问题2、解决问题→持续有效解决问题→不再是问题3、解决客诉品质问题挑战“零不良”---------------------------------------------------------------最新资料推荐------------------------------------------------------ 三、三现现物三现现状现场3/ 53现状把握确认项目1、机种、零件名称/号码 2、发生场所/环境/使用条件 3、发生的现象/问题 4、发生日期 5、引擎号码---------------------------------------------------------------最新资料推荐------------------------------------------------------ 现状把握确认项目6、发生件数/严重性 7、行驶里程/耐久性 8、制造日期/批重性 9、出车日期/库存性 10、不良品品质确认5/ 53现状把握确认项目11、量产中品质水准确认 12、开发阶段品质水准比对 13、设计变更履历 14、其他异常履历 15、标准确认(图面、作业、控制计划、检验标准…)---------------------------------------------------------------最新资料推荐------------------------------------------------------ 四、五原则五原则7/ 531、把握现况现状把握目的针对问题,全盘调查事实掌握变异(机遇/非机遇原因) 归纳可疑方向---------------------------------------------------------------最新资料推荐------------------------------------------------------ 1、把握现况 - 5W2H–类型、种类、受影响的部分。
三现五原则-品保部
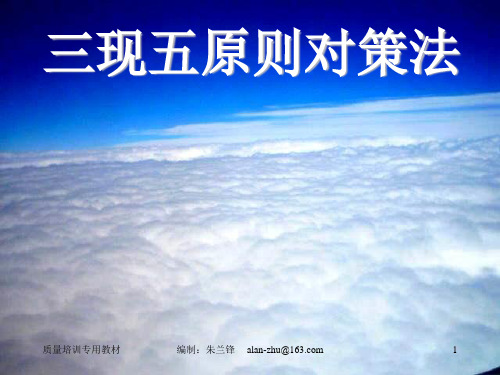
质量培训专用教材
编制:朱兰锋
alan-zhu@
1
何 谓 三 现 五 原 则
三现 现物 现场 现状 事实把握 1. *机种、零件名称/号码 机种、零件名称 号码 机种 *发生场所 环境 使用条件 发生场所/环境 发生场所 环境/使用条件 *发生现象 问题 发生现象/问题 发生现象 *发生日期 发生日期 *引擎号码 引擎号码 *发生件数 严重性 发生件数/严重性 发生件数 *行驶里程 耐久性 行驶里程/耐久性 行驶里程 *制造日期 批量性 制造日期/批量性 制造日期 *出车日期 库存性 出车日期/库存性 出车日期 *不良现物品质确认 不良现物品质确认 *量产中品质水准确认 量产中品质水准确认 *开发阶段品质水准比对 开发阶段品质水准比对 *设计变更履历 设计变更履历 *其它异常履历 其它异常履历 *标准确认 图面、作业、QC工程检验 标准确认(图面 工程检验…) 标准确认 图面、作业、 工程检验 查明要因 2. 真因追查 4M分析 5W分析法 特性要因图 再现试验 NG再现 再现 OK再现 再现
质量培训专用教材 编制:朱兰锋 alan-zhu@ 4
一、解析对策应有科学的数据依据
疑问点: 疑问点:常发生的直觉判断 1.焊接强度不足 对策:焊道加长2mm 正确吗? 焊接强度不足→ 2mm, 1.焊接强度不足→对策:焊道加长2mm,正确吗? 2.模温不足变形 对策:模温提高10℃ 没问题吗? 模温不足变形→ 10℃, 2.模温不足变形→对策:模温提高10℃,没问题吗? 思考:加长2mm、提高10℃如何得到的? 2mm、 10℃如何得到的 思考:加长2mm 提高10℃如何得到的? 直觉+经验≠ 直觉+经验≠事实 100个直觉或经验不如 100个直觉或经验不如1个数据 个直觉或经验不如1 分析方法: 分析方法: 1.科学的根据 1.科学的根据=实验数据 科学的根据= 2.有实验的数据才能决定新的标准 2.有实验的数据才能决定新的标准 3.要去试验出焊道加长2mm及模温提高10℃是最好的条 3.要去试验出焊道加长2mm及模温提高10℃是最好的条 要去试验出焊道加长2mm及模温提高10℃ 件作业。 件作业。
五原则表的应用 (1)

4对策效果确认—效果实绩
5反馈—需落实到体制、组织的内容
⑤
⑥
跟进日期
⑦
⑦ 反馈—需落实到体制、组织的内容
目的: 1、向体制、机构的反映是防止同种/类似问题发生
2、将从问题学到的向全公司或全科推广
⑦ 反馈—需落实到体制、组织的内容
填写的内容
1.将持续维持硬件对策的项目反馈到相关部门(基准、标准、设备 的管理等) 2.将问题反馈到其他部门(横向展开)(规程、基准、技术积累等)
发生搬入异常的不良事项后,要尽快要 求供应商提交五原则报告!!!
问题描述
供应商名称
部门
确认 制作
CHAC接收部门
解决问题的5原则表
1-A发生状况--现象、投诉内容、发生件数、处置内容(5W2H)
日期
审批
审批
确认
1-B事实把握--确认结果、分析要因、品质状况
事实: (此表背后可用头脑风暴Fra bibliotek(1-C)和特性要因图(1-D)
的情况再次发生; 2、对策可能带来新的问题进行分析(P.P.A)、评价(预 测),并制定预防的计划
⑤ 对策—对策内容、预期效果、潜在问题分析
填写的内容
临时对策
永久对策
对策内容 / 对策 年 月 日 ① ②
・发生对策
对策内容 / 对策 年 月 日(预定日)
① ② ③
・流出对策
对策内容 / 对策 年 月 日(预定日) ① ②
问题① 为什么② 为什么③ 为什么④ 为什么⑤
②
2-B原因分析—分析问题和答案、问题产生过程、问题再现测试
③
④
3对策—对策内容、预期效果、潜在问题分析
4对策效果确认—效果实绩
三现五原则表
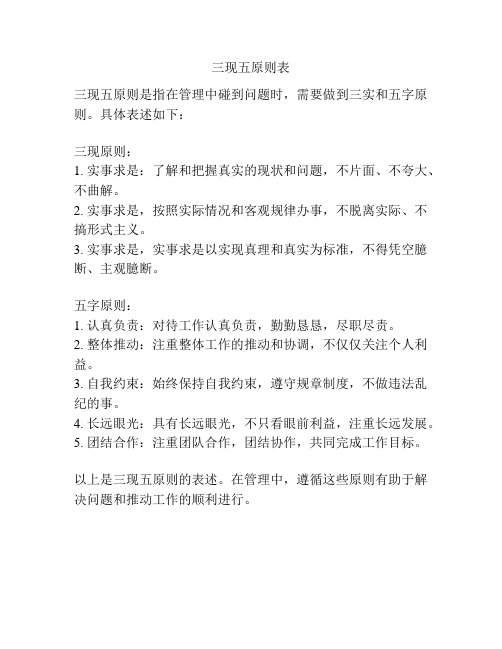
三现五原则表
三现五原则是指在管理中碰到问题时,需要做到三实和五字原则。
具体表述如下:
三现原则:
1. 实事求是:了解和把握真实的现状和问题,不片面、不夸大、不曲解。
2. 实事求是,按照实际情况和客观规律办事,不脱离实际、不搞形式主义。
3. 实事求是,实事求是以实现真理和真实为标准,不得凭空臆断、主观臆断。
五字原则:
1. 认真负责:对待工作认真负责,勤勤恳恳,尽职尽责。
2. 整体推动:注重整体工作的推动和协调,不仅仅关注个人利益。
3. 自我约束:始终保持自我约束,遵守规章制度,不做违法乱纪的事。
4. 长远眼光:具有长远眼光,不只看眼前利益,注重长远发展。
5. 团结合作:注重团队合作,团结协作,共同完成工作目标。
以上是三现五原则的表述。
在管理中,遵循这些原则有助于解决问题和推动工作的顺利进行。
三现五原则over[1]1
![三现五原则over[1]1](https://img.taocdn.com/s3/m/698f88d076eeaeaad1f33070.png)
对策:首末件检查→全检
10.要因:焊接后H方向尺寸NG
对策:焊接治具H方向调整
质量培训专用教材
16
核准
对策单位 复核
承办
1.发生状况 机种
零件编号
零件名称
发生时间
发生地点
数量
不良现象/抱怨内容
反应单位
生产日期
责任单位
临时措施:
3.问题点五层分析
问题 ①
WHY ②
发 生 源
WHY ③
WHY ④
流 出 面
实例:不良现象:踩剎车时BrakePedal有上、下作动感觉
1
2
3
4
5
為什
目視檢查時
麼之 Drum 內徑黑 未檢查
五層 皮產生
Drum 內徑
分析
尺寸 NG
無檢查基準 鑄造時 Drum 加熱變形 模具與 Drum 間隙過大
溫度過高加熱不 無溫度控制
均勻(500℃↑ ) (180℃~200℃)
模具磨損
無標準規定
分析方法: 1.制造面:分析4M的变化点→真因对策。 2.流出面: a.分析制造中的流程→作业环境、作业检验工程标准; b.分析检验的流出面:检验标准、限度样品、自动检测、 防呆装置。
质量培训专用教材
13
十、解析对策应五层分析内容连贯
意义:五层分析是一个形容词,代表追根究底的意思,其目 的在寻找真正的原因,并不是一次要作五次为什么分 析,可以比五次少,也可以比五次多。
担当 期限
效果确认
判定
7.效果确认(收集改善后一段时间的数据判断改善的效果) 确认者
单责 位任 主单 管位 核接 准单 后后 回应 复立 品即 保采 部取 ;临 品时 保措 部施 将消 稽除 核顾 对客 策/ 的下 实工 施程 状的 况抱 和怨 实; 施对 的策 效报 果告 。原
三现五原则对策教材
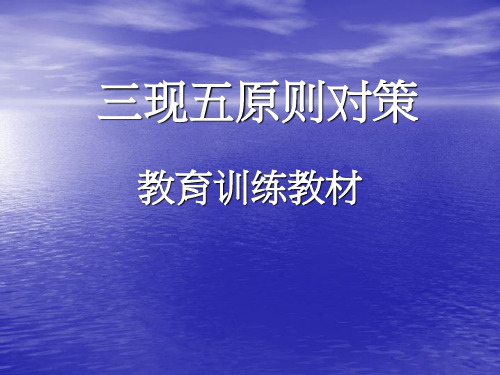
五原則
※現狀把握目的 1.針對問題,全 盤調查事實 2.掌握變異 (機遇 /非機遇原因 ) 3.歸納可疑方向
查明要因 查明原因
特性要因圖 4M分析法 5W分析 再現試驗 不良件再現 正向再現 反向再現
查明真因
※ 問題
不良原因 流出原因
要因
真因
(現象 )
適當對策
臨 時 對 策
(防止惡化擴大)
‧ ‧ ‧ ‧
~要去試驗出焊道加長2mm及模溫提高10℃是作業 最好的條件
二:以偏概全
疑 問 點:以1、2個數據來判斷,可靠嗎? 思 考:~1、2個DATA不能代表全部的不良 ~以偏概全可能僅會解決某比例之不良,而不是所有的不良 ~未徹底解決問題,不良會再發 分析方法:利用品管統計學來掌握解析手法之可靠性。 問題解析與效果確認,皆可使用品管統計手法。 1.掌握品質的準確程度 a.平均數X b.中位數 c.眾數。
前
二、基本想法:
言
1.藉由提高三現五原則解析能力,真正改善品 質問題,並確保問題不再發生 2.解決問題→持續有效解決問題→不再是問題
三、目標: 1.品質問題“零不良”.
何謂三現五原則
三現 現物 現場 現狀 ↓ 現狀把握 ‧ ‧ ‧ ‧ ‧ ‧ ‧ ‧ ‧ ‧ ‧ ‧ ‧ ‧ ‧ 機種、零件名稱/號碼 發生場所/環境/使用條件 發生的現象/問題 發生日期 引擎號碼 發生件數/嚴重性 行駛里程/耐久性 製造日期/批量性 出車日期/庫存性 不良現物品質確認 量產中品質水準確認 開發階段品質水準比對 設計變更履歷 其他異常履歷 標準確認 (圖面、作業、 QC 工程檢驗、標準樣品 …..)
4.技術合作契約。 5.依圖面設計製作之保障。 製程變異應從製程面去改善
三现五原则-现场管理

三现五原则-现场管理
三现五原则
1、三现:现场、现物、现实
2、五原则:A发生状况(现象、申诉内容、发生次数),把握事实(对零部件确认结果、原因分析、现正生产该部件品质状况);B查明原因(发生途径、问题再现试验,5个WHY的分析)C适当的对策(对策内容、效果预测)D确认效果(确认对策的实绩效果)E对源头的反馈(要落实到体系、组织标准化的内容)
现场-----解决问题要到问题发生的场所去
把现场看作问题发生的根源、管理水平提升的基石。
与其费尽心思追求制度的“完美”,不如踏踏实实搞好现场,才有“水到渠成”的效果。
现物-----对发生问题的对象进行确认
认为现场的问题往往有形有据,哪里发生了问题,对什么造成影响,都应加以明确。
“涓涓细流,汇聚成河”
不注意小事、细节,永远难以找出问题根源
现实-----依据事实和数据找出问题的根源
抛弃完全凭经验和感觉,工作中注重数据和事实。
比如发生了不良品,不是去讨论谁的责任,而是了解“不良品的数量、比率、什么样?在哪里发生?怎样发生?”事实胜于雄辩,事实胜于猜测,就是现实的意识。
品质管理三现五原则

品质管理三现五原则嘿,朋友们!今天咱们来聊聊品质管理的三现五原则,这可不像听起来那么枯燥哦。
先说说三现吧,所谓三现就是现场、现物、现实。
这就好比是破案,现场就是犯罪现场,那是所有线索的源头。
要是品质出了问题,你不到现场去,就像侦探光靠想象猜犯人一样不靠谱。
现场就像是一个充满秘密的魔法阵,每个角落都可能藏着解开品质谜题的关键。
现物呢,就是这个魔法阵里的魔法道具啦,那些产品、零部件就像是有话要说的小物件,你得仔细端详它们,就像端详宝藏一样。
而现实呢,就是要面对真实发生的情况,不要自欺欺人,别以为在办公室里瞎琢磨就能搞定品质问题,那是不可能的,这就像你想知道鱼的滋味,却只看画一样荒谬。
再来说说五原则,那可是品质管理的五大神器。
第一个原则就像是给品质问题照X光,要查明原因。
这原因啊,就像调皮的小怪兽躲在暗处,你得拿着放大镜,把它揪出来。
有时候原因可能超级复杂,就像一团乱麻,你得耐心地一点点解开。
第二个原则是要采取措施,这措施就像是超级英雄的技能。
针对那些品质小怪兽,得使出对应的绝招。
要是问题是个大恶魔,你还慢悠悠地出招,那就等着品质灾难降临吧,就像面对洪水只拿个小勺子舀水一样可笑。
第三个原则是要确认效果。
这就像是考完试看成绩一样,你得看看你那些超级英雄的招数有没有打败小怪兽。
如果没效果,那就像放了个哑炮,白忙活一场。
第四个原则是要标准化,这就像把成功的魔法咒语记录下来,让所有人都能照着做。
要是不标准化,就像每个人都按照自己的想法做菜,那做出来的味道肯定千奇百怪,品质也就乱套了。
最后一个原则是要防止再发生,这就像是给品质城堡修个坚固的城墙。
不能让那些问题小怪兽再次入侵,要是不做好防范,就像补了东墙西墙又破了,永远在救火,忙得晕头转向。
品质管理的三现五原则啊,其实就是一场和品质问题斗智斗勇的有趣游戏。
我们得像勇敢的探险家一样,在现场这个神秘的世界里,通过现物这个神奇的媒介,找到现实中的答案,再挥舞着五原则这五把宝剑,把品质管理得妥妥当当。
三现五原则--最终版
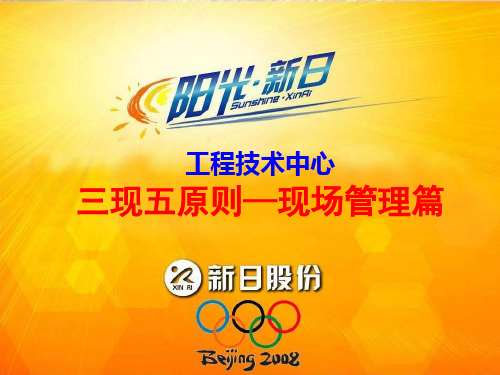
查明原因
查明原因
流出原因 问题 要因 真因
质 量 ● 创 新 ● 服 务
(流出面)
2、查明原因
WHY WHY分析 1、通过WHY、WHY的反复5次进行分析找 出真因。 2、WHY、WHY的疑问必须使之与问题现 象相关联,建立系统来进行。
质 量 ● 创 新 ● 服 务
3、WHY、WHY的分析要从问题发生的原 因(或叫硬件方面的原因)和流出 原因(又叫软件方面的原因)两方 面进行。 4、WHY、WHY分析的信息来源,基本上 是以特性要因图为基础。 5、为了说明真因,可以加入插图。
质 量 ● 创 新 ● 服 务
临时对策 适 当 对 策
(防止恶化扩大)
•已流入市场处理 •库存成品处理 •半成品处理 •不良品处理 •制造面、流出 面之治本对策 •水平展开对策
永久对策
(避免再发)
对策情报传达
质 量 ● 创 新 ● 服 务
•工程作业者 •进料检验者 •市场服务者 (品质通报)
3、采取对策
质 量 ● 创 新 ● 服 务
3.回复钱经理:已咨询技术部门,20ah配置的车型( 30A控制器)最低保障公里数在25公里,再加上目前的气候 属配置范围内正常公里数,如用户强烈可以更换(25A)控制 器;
商家表示要求技术部门的人员前往商家处实际了解 新日车和其它车的区别;建议客诉转质量部门进一 步和商家再次沟通安抚商家。
质 量 ● 创 新 ● 服 务
7、再现试验证明
疑 问 点:你如何知道解析不良原因是正确的吗? 思 考:科学的实验是最好的证明→再现试验。
分析方法:正向再现与反向再现。 1.正向:将不良要因排除(不良条件修正)后会制造 出良品。 2.反向:以不良条件生产会制造出不良品。 若上述二向再现结果与假设违背,则肯 定 所解析出之不良原因必定有偏差。 3.不良品再现。
8D报告三现五原则

通过充分掌握实时情况环节,查明异常变化点,确定要因,确定真因,查明真因
为下个环节做准备 b.查明真正原因的步骤:
4M目的:通过4M分析 找出变化点
5W目的:在4M分析处 变化方向后,找出变化 点,深入挖掘问题真相
4M+1M+1E 人(MAN) 机(MACHINE) 材料(MATERIAL) 制造方法(METHOD) 测量(MEASUREMENT) 环境(ENVIROMEN)
4、可以容易地评价针对每一 步所采取的行动是否是最妥 切的。
5、将为解决问题所开展的活 动内容作为技术诀窍记录下 来,不断地积累技术经验。同 时,便于向领导汇报,向相
关部门传达。
6、减少问题再次发生的次数
一、三现五原则定义
“五原则”是指从“三现主义”(现场、现物、现 实)出发,分五个步骤解决问题。
三.三现五原则注意事项
1.无科学根据的数据之解析对策
疑 问 点:常发生的直觉判断 ~ 焊接强度不足对策:焊道加长2mm.正确吗? ~ 模温不足变形对策:模温提高10℃.没问题吗?
思 考:加长2mm、提高10℃如何得到的? 直觉+经验≠事实 100个直觉或经验不如1个数据
分析方法:科学的根据=实验数据 ~ 有实验的数据才能决定新的标准。 ~ 要去试验出焊道加长2mm及模温提高10℃是作业最好的条件。
质量管理三现五原则

2-B 查明原因(发生的途径、问题再现试验WHY WHY分析)
3 采取)适当的对策 (对策内容、效果预测PPA) 4确认(对策)效果(效果实绩) 5对(问题)源头的反馈(需落实到体制、组织的内容)
15、案例
右腕受伤
1- A 发生状况(现象、申诉内容、发生次数、5W1H处置内容)
1、发生场所:汽缸压铸NO.2生产线。 2、 发生状况:请参照右手腕受伤素描图
检验: 为何会检测不出来。
10、五层分析
意义:为什么之五层分析是一个形容 词,代表追根究底的意思,其目 的在寻求真正的原因,并不是一 次要作五次为什么分析,可以比 五次少,也可以比五次多,只要 能寻求出真正的原因。
10、五层分析
实例说明: 不良现象:踩刹车时有上、下作动感觉。
1
2
3
4
5
目视检查
为什 Drum内 未检查
3、五层分析是三现五原则单之中 心思想及布局。
11、要因 对策案例练习
1.要因:人为疏忽 对策:教育训练加强
2.要因:XX治具磨损 对策:更换新治具
3.要因:遗漏焊接 对策:后工程实施全检以确保
4.要因:半成品因台车太小不慎流入后工程 对策:台车修改加大
5.要因:修护车辆,等待时间长 对策:等待时间提供杂志阅读
1、把握现况 - 5W2H
WHERE 何地 – 记入问题发生的场所。 WHY 为什么 – 具体的内容 HOW 怎么样 – 问题是怎样发生的 HOW MANY 什么程度 – 问题发生量,
程度。
1、把握现况的填写方法
1、问题点的概要(信息的收集、整 理)。例:针对部品或工程。
2、问题再现试验的结果 3、现行品(现在生产)的品质状况 4、发生的对象范围
三现五原则

Drum内 未检验 为何 径黑皮
铸造时
热不均匀 (500↑℃)
之五 产生 层分 析
Drum内径 Drum加热 尺寸NG 变形
模具与
模具磨损
Drum间隙
过大
6
无温度 控制 (180200℃)
无原则 要求
10、五层分析
1、五层分析是三现五原则原因解 析之浓缩要点内容。
2、五层分析是同说故事一样,故 事必须连贯。
11、要因 对策案例练习
6. 要因:涂装后之成品受落尘污染 对策:将成品以防尘套保护
7. 要因:锁付之螺丝易松动 对策:螺丝追加LOCKTITE涂布
8. 要因:宿舍被单送洗频度高易破损 对策:送洗频度由15天/1次→30天/1次
9. 要因:检验疏忽 对策:首末件检验→全检
10.要因:焊接后H方向尺寸NG 对策:焊接治具H方向调整
3、五层分析是三现五原则单之中 心思想及布局。
11、要因 对策案例练习
1.要因:人为疏忽 对策:教育训练加强
2.要因:XX治具磨损 对策:更换新治具
3.要因:漏掉焊接 对策:后工程实施全检以确保
4.要因:半成品因台车太小不慎流入后工程 对策:台车修改加大
5.要因:修护车辆,等待时间长 对策:等待时间提供杂志阅读
制程变异应从制程面去改善
5、变化点分析不清楚
疑 问 点:此前为何不会发生不良,目前才发生? 一定是哪里有变更,变化点在哪里?
思 考:不良隐藏於变化点中。
分析措施:4M1D里寻找真因 人[Man]:人员有否更换,有否依原则作业、人员之 士气等。 机[Machine]:机器设备、镆、治、检、工具有否调 整、变更等。 料[Material]:材料有否变化、前工程流入件不良事 等。 措施[Method]: 原则有否要求?原则是否明确? 设计[Design]: 是否设计变更等。
质量管理中的三现五原则(解决问题的经典套路)

质量管理中的三现五原则(解决问题的经典套路)质量管理中的三现五原则(解决问题的经典套路)2020-08-05 17:00今天,九脑汇学院就来说⼀说质量管理中三现五原则,所谓三现即:现物、现状、现场,包含这三点,希望这份资料能对⼤家有所收获。
三现主义企业常见的缺乏“三现主义”的现象:等待⽣产现场的联系或⽣产现场对于技术、品质、资材等部门服务、指导、指⽰、供应的等待。
等待下级的汇报,任务虽已布置,但是没有检查,没有监督。
不主动去深⼊实际调查研究,掌握第⼀⼿资料,只是被动地听下级的汇报,没有核实,然后作决定或向上级汇报,瞒天过海没有可信度,出了问题,责任往下级⾝上⼀推。
注:“三现主义”的缺乏是等待中的最致命原因之⼀,严重影响⽣产现场⼯作的及时解决。
现场不要只坐在办公室决策,⽽是要⽴即赶到现场,奔赴第⼀线。
现场是⽣机勃勃的,每天都在变化,不具备正确的观察⽅法,你就没法感觉它的变化,包括异常。
现物管理的最重要的概念是“总是以事实为基础⽽⾏动”,解决问题要求你找到事实真相。
因为只有⼀个真理存在,最通⽤的⽅法是“到问题中去,并客观地观察其过程”。
观察你看不到的地⽅,这时,事实将出现。
要发现其变化的原因,仔细观察事实。
当你这样做时,隐藏的原因将会出现,这样做,你可以提⾼发现真相的能⼒。
现实解决问题需要你⾯对现实,把握事实真相。
我们需要⽤事实解决问题,⽽事实总是变化⽆常的,要抓住事实就要识别变化,理想与实际总是有很⼤的差距。
很多问题如果我们不亲临现场,不调查事实和背景原因,就不能正确认识问题。
但为什么会发⽣那样的问题呢?我们要多问⼏次“为什么”,对“现物”、“现实”进⾏确认。
五原则五原则是指从三现主义(现场、现物、现实)出发,分五个步骤来解决问题:五原则的重要思想:①从“三现主义” (现场、现物、现实)出发解决任何问题都应当最先掌握现场、现物、现实中有⽤的实际情况。
如果没有掌握实际情况。
那么,从⼀开始就⾛弯路,⾛得越远,误差越⼤,当然最终得不出真正的结论。
品质管理的三现五原则

5、变化点分析不清楚
疑 问 点:以前为何不会发生不良,现在才发生? 一定是哪里有变更,变化点在哪里? 思 考:不良隐藏於变化点中。
分析方法:4M1D里寻找真因 人[Man]:人员有否更换,有否依标准作业、人员之 士气等。 机[Machine]:机器设备、镆、治、检、工具有否调 整、变更等。 料[Material]:材料有否改变、前工程流入件不良事 等。 方法[Method]: 标准有否规定?标准是否明确? 设计[Design]: 是否设计变更等。
疑 问 点:常发生的直觉判断 ~ 焊接强度不足对策:焊道加长2mm.正确吗? ~ 模温不足变形对策:模温提高10℃.没问题吗? 思 考:加长2mm、提高10℃如何得到的?
直觉+经验≠事实
100个直觉或经验不如1个数据
分析方法:科学的根据=实验数据 ~ 有实验的数据才能决定新的标准。 ~ 要去试验出焊道加长2mm及模温提高10℃是作 业最好的条件。
9、制造面、流出面未检讨
疑 问 点:1.为何会流出?为何会制造出?为何设备检不出? 2.流出面之解析对策经常被疏忽。 思 考:顾客所反应之问题必定制造面、流出面共同发生, 仅对策制造或流出面并未能彻底解决问题。 分析方法:1.制造面→分析4M之变化点→真因对策。 2.流出面→a.分析制程中之流程→作业环境、作 业检验工程标准。 b.分析检验之流出→出货检验标准、 限度样品、自动检测、防呆装置。 检验: 为何会检测不出来。
发生问题 零件号 零件名称
提出部门
日期 批准 审核 编制
日期
编制部门
批准 审核 编制
1-A 发生状况(现象、申诉内容、发生次数、5W2H处置内容)
1-B 把握事实(对零部件的确认结果、原因分析、现在正在生产的零件的品质状况)
三现五原则--最终版
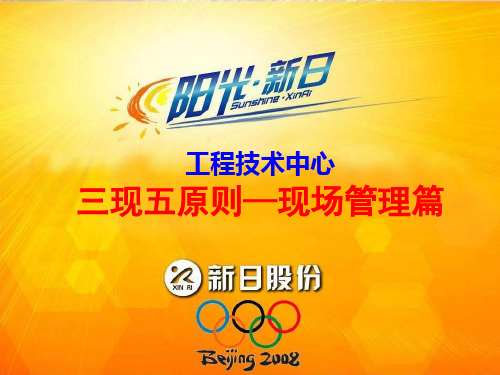
只有在 针对 才能通过观察、分析把握到 。在 我们即将讲到的“五原则”中,三现是其根本基础,离开三现,一切都 会沦为空谈。
现场
现物
现实
质 量 ● 创 新 ●● 创 新 ● 服 务
学习目的
1、了解并运用五原则解析 手法,真正改善重要品质问 题 2、把问题追溯到源头,从根本上解决问题 3、治理流程 4、制定、改善标准 5、重视“再现”,避免主观臆断或片面错断
质 量 ● 创 新 ● 服 务
WHERE 何地 – 记入问题发生的场所。 WHY 为什么 – 具体的内容 HOW 怎么样 – 问题是怎样发生的 HOW MANY 什么程度 – 问题发生量, 程度。
质 量 ● 创 新 ● 服 务
4M分析
5W分析法
查明原因
特性要因图 再现试验 NG再现 OK再现 不良再现 不良原因 (制造面)
解析对策必须手遵守三现主义
质 量 ● 创 新 ● 服 务
9、制造面、流出面未检讨
疑 问 点:1.为何会流出?为何会制造出?为何设备检不出? 2.流出面之解析对策经常被疏忽。 思 考:顾客所反应之问题必定制造面、流出面共同发生, 仅对策制造或流出面并未能彻底解决问题。
分析方法:1.制造面→分析4M之变化点→真因对策。 2.流出面→a.分析制程中之流程→作业环境、作 业检验工程标准。 b.分析检验之流出→出货检验标准、 限度样品、自动检测、防呆装置。 检验: 为何会检测不出来。
质 量 ● 创 新 ● 服 务
6、无回馈标准
疑问点:如何保证以后不会再发?或这样对策就不会再发吗? 欠缺了什么。 思 考:1.作业者不知道、不清楚、则不良问题仍然会再发生, 所以让作业者明白如何才能做良品是非常重要的。 2.
标准回馈 明确 作业者知道 如何去做 作业者正确 的去做
三现五原则
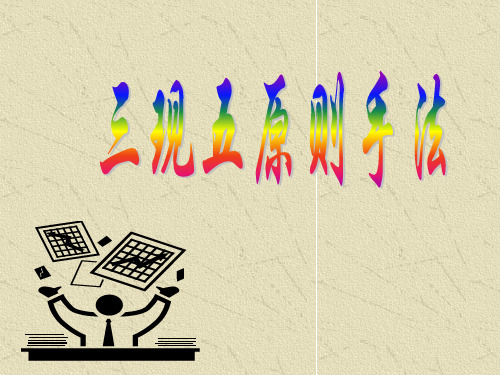
解析对策必须顾虑成本面
肆、以变更设计改善制程变异
疑 问:1.变更设计就不会有问题了吗? 2.新设计有新的问题,甚或比现在的问题更严重。 3.制程中4M问题未改善,新设计就不会发生相同问题 吗? 说 明: 1.设计者之原理念不祥,不能更改设计。 2.原设计时,GSK经过耐久的验证及市场之考验,其可靠 度甚高。 3.未依图制作及未依原设计制作面产生之问题(市怨、 厂异...) 经常有闻。 4.GSK 日本少技术合作契约。 5.依图面设计制作之保障。 制程变异应从制程面去改善
捌:无三现
疑 问 点:有至现场去看吗?有否实车确认、实物、 实地确认? 说 明:1.杂志与次讯:未三现,可能会得到错误之 讯息,或疏略重点资讯。 2.选择性事实:三现的目的,在於针对问题, 全盘掌握事实,而未三现,可能仅知道部份 事实。 3.有三现,才能相信自己,说服别人。
解析对策必须手遵守三现主义
标准化:减少人的风险
同时考虑下列状况: 听错、看错、想错、忘记、忘了忘记这回事。
解决问题5原则表
发生问题 零件号 零件名称
提出部门
日期 批准 审核 编制 日期
编制部门
批准 审核 编制
1-A 发生状况(现象、申诉内容、发生次数、5W2H处置内容)
1-B 把握事实(对零部件的无论结果、原因分析、现在正在生产的零件的品质状况)
玖:制造面、流出面未检讨
疑 问 点:1.为何会流出?为何会制造出?为何设备检不出? 2.流出面之解析对策经常被疏忽。 思 考:顾客所反应之问题必定制造面、流出面共同发生, 仅对策制造或流出面并未能彻底解决问题。 分析方法:1.制造面→分析4M之变化点→真因对策。 2.流出面→a.分析制程中之流程→作业环境、作 业检验工程标准。 b.分析检验之流出→出货检验标准、 限度样品、自动检测、防呆装置。 PS: 为何会检测不出来。
品质管理三现五原则

品质管理三现五原则品质管理,这可是个大学问!就像烹饪一道美味佳肴,得有精心的准备和严格的把控。
咱先来说说“三现”。
啥是“三现”?就是现场、现物、现状。
这就好比你去看病,医生总不能光听你描述就下诊断吧?他得亲自到现场,看看你的症状,摸摸你的脉象,这才叫了解现况。
搞品质管理也是一样,不能光坐在办公室里看报告,得走到实际的生产现场,亲眼看看产品,亲自感受生产的状况。
你想想,如果一个管理者只听别人说,不去现场,那能行吗?就像你要买一双鞋,只听别人说好看,自己不亲自试试,能买到合脚的吗?再说“现物”,就是实实在在的物品。
产品出了问题,光在那空想可不行,得把有问题的产品拿在手里,仔细瞧瞧,找找毛病到底出在哪。
这就像警察破案,得找到关键的物证,才能顺藤摸瓜找到真相。
“现状”就更好理解啦,就是当下的实际情况。
比如机器的运行状态、工人的操作流程,只有清楚了解这些,才能发现问题,解决问题。
接下来咱们聊聊“五原则”。
这“五原则”就像是五个武功秘籍,掌握好了,品质管理就能游刃有余。
第一个原则是“把握现状”。
这就像打仗之前要先摸清敌人的底细,知道问题到底是啥,有多严重。
不能稀里糊涂就开始行动,那不是瞎折腾嘛!第二个原则是“原因分析”。
出了问题就得找原因,不能头疼医头,脚疼医脚。
就像车子抛锚了,你得找出是发动机的问题,还是轮胎的问题,总不能随便修修就了事。
第三个原则是“对策树立”。
找到原因了,就得想办法解决。
这对策得有针对性,可不能乱出主意。
比如说房子漏雨了,你不能说在屋里打把伞就算解决问题了吧?第四个原则是“效果确认”。
对策实施了,得看看有没有效果。
这就像吃药治病,得复查看看病好了没。
要是没效果,那得赶紧调整对策。
第五个原则是“源流反馈”。
解决了一个问题,还得想想怎么防止类似的问题再次发生。
就像补了一个洞,得想想怎么不让别的地方再出现洞。
总之,品质管理的“三现五原则”就像是一套组合拳,只有把它们运用好了,才能打出漂亮的成绩。
5WHY解决问题的三现五原则【范本模板】
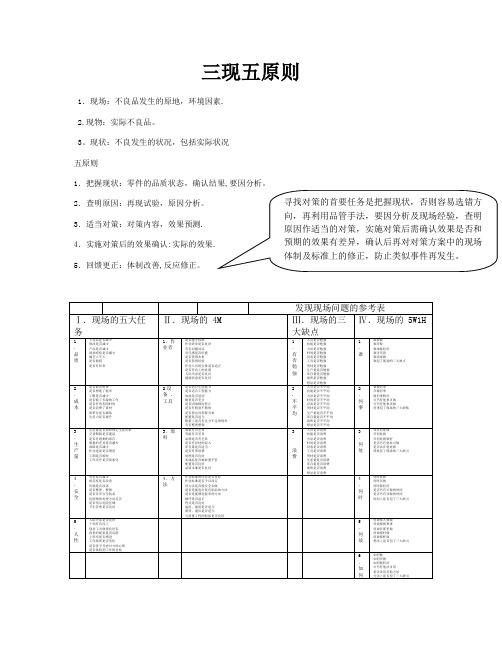
三现五原则
1.现场:不良品发生的原地,环境因素. 2.现物:实际不良品。
3。
现状:不良发生的状况,包括实际状况 五原则
1.把握现状:零件的品质状态,确认结果,要因分析。
2.查明原因:再现试验,原因分析。
3.适当对策:对策内容,效果预测. 4.实施对策后的效果确认:实际的效果5.回馈更正:体制改善,反应修正。
如何做有效的分析与报告
问题解决之五大原则
1.1 发生状况:现场、现物、现状、日期、数量、LOT NO。
1.2 把握现状:基准值与实测的差异,再现试验,要因分析。
现在生产品质状况。
发生对象与相关原材料、中间制品.
1.3 原因的查明:分析主要要因。
再现性原因的确认。
1.4 适当的额对策:暂时或者永久性的对策内容,日期、LOT NO。
在库品处理,已出库品处理. 1.5 确认对策的效果:比较对策前后都额差异。
1.6 回馈。
三现五原则对策报告-模板
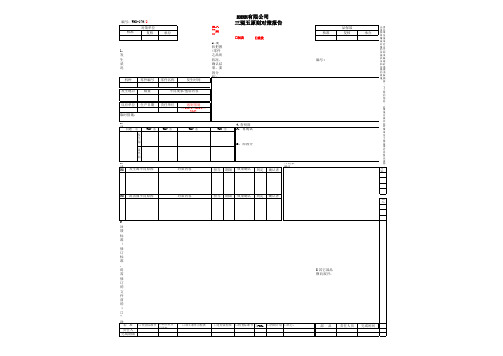
3. 问 问题 ①
发 生 源
WHY ②
WHY ③
WHY ④
流 出 面
5. 适NO 发生源不良原因
对策内容
WHY ⑤
4.查明原 A、再现试
B、原因分
7.效果 担当 期限 效果确认 判定 确认者 确认
核准 编号:
品保部 复核
承办
品责 保任 部单 将位 稽接 核单 对后 策应 的立 实即 施采 状取 况临 和时 实措 施施 的消 效除 果顾 。客
/ 下 工 程 的 抱 怨 ; 对 策 报 告 原 件 经 对 策 单 位 主 管 核 准 后 回 复 品 保 部
分;
发
NO 流出面效果确认 判定 确认者
6. 回 馈 标 准 ( 修 订 标 准 , 将 需 修 订 的 文 件 前 的 “ □ ” 涂
标准
责任人 完成期限
□作业标准书
□制程检查 记录表
□加工条件点检表
□过程流程图 □检查标准书 □FMEA □控制计划 □其它:
知 会
8.其它部品 横向展开:
部 品 责任人员 完成时间
编号:WHD-179/2
核准
对策单位 复核
承办
1. 发 生 状 况
机种 零件编号 零件名称
发生时间
发生地点 数量
不良现象/抱怨内容
重大 问一般 问
2.现 状把握 (零件 之品质 状况、 确认结 果、要 因分 析)
XXXX有限公司 三现五原则对策报告
□初发
□重发
反应单位 生产日期 临时措施:
责任单位
遏制措施 □100%□200%□
- 1、下载文档前请自行甄别文档内容的完整性,平台不提供额外的编辑、内容补充、找答案等附加服务。
- 2、"仅部分预览"的文档,不可在线预览部分如存在完整性等问题,可反馈申请退款(可完整预览的文档不适用该条件!)。
- 3、如文档侵犯您的权益,请联系客服反馈,我们会尽快为您处理(人工客服工作时间:9:00-18:30)。
二三 、、 请请 于附 对 策 1 后 0相 月关 1佐 8证 日资 前料
对策确认栏
2 3
5W 内容
表单编号:
1W
2W
3W
4W
5W
日期 数量 追踪人 判定 保存期限:2年
三 、 请 附 对 策 后 相 关 佐 证 资 料
发 文 单 位 1.日期: 3.地点:
批准
审核
制订
******有限公司
三现五原则对策表
1.发生状况:
收 文 单 位 2.要因分析:
年 批准
月 审核
日 制订
编号:
发生状况(不良现象、发生件数、临时措施)
事实把握(部品确认结果、要因分析、现生产品质状况)
年
月
日
3.现生产品质状况
2.时间: 10:50 4.反应人员: 5.问题现象: 6.抱怨内容: 7.发生频率:第 8.发生件数: 9.不良率: 10.临时措施:
原因调查(发生机构、再现试验、原因分析) 适当对策(对策内容、问题分析、责任人、期限) 对策效果确认(效果实情)
一 、 请 于 1
次
0 月 1
1.发生机构: 2.再现试验:
1.临时对策: 2.永久对策:
3.原因分析:
标准化(制度、技术基准类上的反映问题)
次数 1
8 日 回 1 复 0 点 至 我 公