五原则表教材资料
第16课 独立自主的和平外交 教案(表格式)

第16课独立自主的和平外交设计说明本课主要讲述我国的外交政策和中华人民共和国成立初期我国取得的外交成就,以周恩来的外交活动为主线展开教学。
学习目标1.通过自主学习和小组合作,知道独立自主的和平外交政策,掌握和平共处五项原则提出的时间、内容及影响,知道万隆会议及“求同存异”方针的内容和意义。
2.通过分析图片、视频等资料,领略周恩来等外交家的外交智慧,认识到外交活动的根本目的是维护国家利益,激发学生的爱国主义情感和民族自尊心、自豪感,培育家国情怀。
重点难点教学重点:和平共处五项原则、“求同存异”方针。
教学难点:我国外交政策的确定,和平共处五项原则、“求同存异”方针的提出与国际形势的关系。
教学方法讲解法自主学习法合作探究法史料分析法问题探究法资源与工具(一)资源周恩来图片文字资料(二)工具图书馆资源网络搜索工具课时安排1课时教学过程一、教学情境出示周恩来的图片,同时提出问题:他是谁?回顾中国近代史,与他有关的史事有哪些?教师讲述:革命时期,周恩来为革命的胜利作出了贡献;中华人民共和国成立后,周恩来担任国务院总理,同时兼任外交部长,以非凡的才能、智慧与精力,为中国的外交事业作出了杰出贡献。
由此导入新课。
二、预习检查1.中华人民共和国成立后,我国的外交政策是什么?2.中华人民共和国成立初期,我国取得的外交成就有哪些?三、学习任务一四、学习任务二五、学习任务三六、过程性评价课堂练习七、课堂小结中华人民共和国成立后,我国始终奉行独立自主的和平外交政策,结束了近代以来百年屈辱的外交史。
中国以积极主动的姿态走向世界,与苏联等国家建交,注重发展与周边国家和新兴独立国家的外交关系。
1953年,周恩来创造性地提出了和平共处五项原则,产生了广泛且深远的影响,被世界上越来越多的国家接受。
1955年,在万隆会议上,周恩来提出“求同存异”的方针,促进了会议的圆满成功,加强了中国同亚非各国的团结与合作。
八、布置作业1.基础型作业:制作中华人民共和国成立初期外交大事记。
广本5原则培训资料

☆集体创造性思考 ☆特性要因图
• 调查结果总结、变化点和推断原因总结
4、现在的対応状况(緊急処置後的)
• 用X-R管理图 、矩形图、CP值等
可以说问题一定源于变化点(人、物、设备等,4M1E)
1、老七种工具: 调查表 分层法 排列图 因果图 直方图 控制图 散布图 2、新七种工具 亲和图 树图 关联图 矩阵图 箭条图 PDPC法(过程决策程序图法) 矩阵数据分析法
・可用于解决开发、生产、销售、供应、管理等 所有领域发生的问题。
来自顾客的意见、投诉产品、服务不好 设备、机械、机器的问题 精确度与效率不高的工作
解决问题、防止再发
五原则工作表
重要度的决定及处置判断
• 重要度、麻烦度、重要保安部品判断
零件品质科
重要度
麻烦度
重要保安部品
A 不良时判断为危害人身安 A 已进行整车的检测、修理 HS
17 240±5 +7 +8 +9
P21
10 270 SET SET SET
(工序概要) No 工程名 1 来料仓库 2 端末加工 3 弯管加工 4 最終検査 5 出荷
加工機種名 起因 西岛端末加工机 T型弯管机 ★ -
*根据现品确认,弯管形状有同样倾向
■ 5原则工作表(解析报告)
是指从发生问题的初期对应到彻底解决问题,防止再发的问题解 决手法。是本田特有的问题解决手法。
目的:通过对不良问题进行有条理的、理论性的分析(三现主 义) ,查找真正的原因,采取适当的对策,防止问题再发。
・解析报告要将解决问题流程的结果用1张纸(A3)总结后进行报告。
■ 使用范围
集、整理)
• 工序中现正生产的零部件的品质状况、良品批次确认(根据X-R管理图、工程
精益生产与现场管理教材

让用户满意 无差错生产 持续改进
精益思想告诉我们
• 企业经营的目的是制造利润
–在不同的历史阶段,企业获得利润的方 法是不同的。 售价=成本+利润(计划经济时)
售价—成本=利润(市场经济时) 售价—利润=成本(精益思想 TPS)
• 确保利润的成本倒留法
利润是如何产生的
获得利润的两大手法:
手法1: 降低成本
③ 调动部属的机动性(motivate:do的阶段)
在完成目标的过程中,不断地和部属交换意见,给部属提供 情报,给部属出主意,帮助、鼓励部属。
④ 评价业绩(see)
亲自评价部门的总体成果,另外,还要评价部属的业绩。
⑤ 培训部属
现场管理者的工作职责
1 生产任务管理 2 生产技术管理 3 设备管理 4 品质管理 5 考勤管理 6 效率管理 7 成本控制 8 部属教育 9 部属考核 10 安全生产督导 11 环境管理
(1)以最终用户的需求为生产起点
(2) 强调物流平衡,即工序间、部门间不设置仓库 (3)组织生产线依靠看板的形式,即由看板传递工
序间需求信息 (4) 生产中的节拍可由人工干预、控制 (5)生产均衡化
指总组装线在向前工序领取零部件时,应均衡地使 用各种零部件,混合生产各种产品,均衡化是通过专 用设备通用化和制定标准作业来实现的。
设备的改善 自动化,设备自动预警
工厂布局的改善 消除浪费
作业的改善 观察操作者的工作方式并制定标准工作法
5S 整理 整顿 清扫 清洁 素养
第一部分 5S活动
源于日本
整理(SEIRI) 整顿(SEITON) 清扫(SEISO) 清洁(SEIKETSU)素养(SHITSUKE)
发展于美国
三现五原则over[1]1
![三现五原则over[1]1](https://img.taocdn.com/s3/m/698f88d076eeaeaad1f33070.png)
对策:首末件检查→全检
10.要因:焊接后H方向尺寸NG
对策:焊接治具H方向调整
质量培训专用教材
16
核准
对策单位 复核
承办
1.发生状况 机种
零件编号
零件名称
发生时间
发生地点
数量
不良现象/抱怨内容
反应单位
生产日期
责任单位
临时措施:
3.问题点五层分析
问题 ①
WHY ②
发 生 源
WHY ③
WHY ④
流 出 面
实例:不良现象:踩剎车时BrakePedal有上、下作动感觉
1
2
3
4
5
為什
目視檢查時
麼之 Drum 內徑黑 未檢查
五層 皮產生
Drum 內徑
分析
尺寸 NG
無檢查基準 鑄造時 Drum 加熱變形 模具與 Drum 間隙過大
溫度過高加熱不 無溫度控制
均勻(500℃↑ ) (180℃~200℃)
模具磨損
無標準規定
分析方法: 1.制造面:分析4M的变化点→真因对策。 2.流出面: a.分析制造中的流程→作业环境、作业检验工程标准; b.分析检验的流出面:检验标准、限度样品、自动检测、 防呆装置。
质量培训专用教材
13
十、解析对策应五层分析内容连贯
意义:五层分析是一个形容词,代表追根究底的意思,其目 的在寻找真正的原因,并不是一次要作五次为什么分 析,可以比五次少,也可以比五次多。
担当 期限
效果确认
判定
7.效果确认(收集改善后一段时间的数据判断改善的效果) 确认者
单责 位任 主单 管位 核接 准单 后后 回应 复立 品即 保采 部取 ;临 品时 保措 部施 将消 稽除 核顾 对客 策/ 的下 实工 施程 状的 况抱 和怨 实; 施对 的策 效报 果告 。原
教材管理制度

教材管理制度教材管理制度1教材是老师组织实施教学和学生学习的重要依据,选择使用及编写高质量教材是提高我校教学质量和知名度的紧要保证和前提,为杜绝、防止低水平教材流入我校,规范教材选用、编写程序,明确各环节具体要求,特订立本制度。
(一)、教材供应范围和种类1、教材供应对象为学校在读的学生及任课老师。
2、教学计划中的各门课程的教学用书和讲义、配套教学参考资料、自印教材等,均由教务处负责组织供应。
3、其他部门或个人不得向学生推销教材。
(二)、教材选购和预订方法1、选购和预订教材的原则:A、基础课教材应优先选用获国家级或部委级的“优秀教材”和“介绍教材”;其次选用规划统编教材,一般不能选用其它教材。
B、专业及专业基础课教材,一般以各专业出书社出书的、纳入国家教材统一征订的教材为主,除特殊情况外,一般不使用其它教材。
C、上述条件不能满足,可考虑采用非统一征订正式出书的教材。
D、在确实购买不到较适用的教材的情况下,方可考虑自编教材。
E、选用教材要首先考虑原用教材,以保持教材的稳定性,减少库存,遇特殊原因,不使用原来教材改版的,须提出报告说明理由。
2、预订程序A、每年6月与12月分别办理秋季和次年春季教学用书的选订。
B、依照春秋季教学用书征订目录选订教材,各专业部及教研组填写教材订购申请单后,经教务处审核后汇总,办理预订。
C、为做好教材预订工作,教务处应掌握有关课程的教材库存数,以避开多订、错订。
D、确因计划更改或其他原因,不能通过预订而须即时采购者,应及时提出选购教材报告,及时解决。
E、教材一经选定一般不得更改,特殊情况须经教务处同意后,提请分管副校长批准,方可执行。
F、由于人为原因而重订、错订造成的教材积压挥霍,由责任人负责推销或赔偿经济损失。
G、参编教材认购数量以使用两年为限,不得向学生硬性摊派推销各种教材和教学参考资料。
(三)、自编教材管理方法1、凡确实征订不到或必需增补的教材,方可考虑本身编印。
2、首先由专业部或教研组打报告,确定编写责任者、审稿责任人、使用年限、编写大纲、完成编写的约莫时间等,经教务主任同意后,提请分管副校长批准,方可执行。
义务教育课程标准实验教科书《科学》(3-6年级)

义务教育课程标准实验教科书《科学》(3-6年级)基本框架及整体特色本套教材是由胡军任主编,与DC加拿大国际交流中心合作编写,由河北人民出版社出版的小学科学教材,是一套依据国家小学科学课程标准编写的教材。
在2001年12月教育部教材编写立项审批会上,获得小学科学教材惟一的A类。
适合全国各个地区小学3-6年级学生使用。
本套教材以《国家基础教育课程改革纲要》为指导,全面落实《全日制义务教育科学(3-6年级)课程标准(实验稿)》提出的基本理念、课程目标和课程内容,开展科学启蒙教育,培养学生的科学素养和创新精神及实践能力为目的,致力于为学生后继的科学学习和其他学科的学习,乃至终身学习打下基础。
教材编写以建构主义理论、多元智能理论、内化学说以及科学与技术的结合、科学与艺术的结合、科学教育与人文教育的结合等思想为理论基础,整体规划全套科学教材的编写目的、原则、指导思想及要落实的目标和体现的特色。
在教材编写前期,对我国及其他国家或地区(加拿大、美国、澳大利亚、日本、英国、台湾、香港等)的科学课程标准和教材进行比较、分析和研究,吸取其长,并结合我国国情实际,力求创新并形成自己的特色。
我们坚持教材编写过程就是科学研究的过程,充分吸收多年来相关课题的研究成果(如列入国家“九五”规划的教育部科技部重点课题——中小幼科技教育研究;正在进行的“十五”国家青年基金课题——小学科学教材的开发与应用模式研究),力图将科学课程开发的研究与教材编写有机地结合起来。
总的来说,在教材编写过程中,我们遵从了以下原则:原则之一:精选教学内容,全面培养学生科学素养的原则。
从学生身心发展特点和生活经验出发组织学习内容,根据有利于学生亲历科学学习过程,有助于实现多领域学习目标,有利于培养学生情感态度和价值观的原则等思想,来精选科学知识和技能方面的内容。
尤其重视社会普遍关注的现实性内容以及具有综合性和关联性的内容。
原则之二:注重科学、技术、社会、环境相互联系的原则。
解决问题的五原则-培训资料

•填入内容:
•1、零件确认结果 • ①故障品写真 • ②故障品确认结果:尺寸、材质等与图纸规定事项的对比,直接 找 • 出在何处、怎样不好、有何变化、 良品与不良品的特征和变 化 • 点比较、信息收集、整理 • ③对象范围、批次、生产日期把握 • ④工序中现正生产的零部件的品质状况、良品批次确认(根据 • X•-①R不管良理品图制、造工工程序能条力件 直方图对现状进行把握) •2、全•②工不序良品检证制(造对年月全日工序确认,…查等,找用不工序良系发列生、工时序间和系列流整出理工。序)
•
(WHAT)什么-问题的症状,尽可能地使用图表等工具将问题表达清楚.
•
(WHEN)何时-记入问题发生的日期
•
(WHERE)何地-记入问题发生的场所
•
(WHY)为什么-具体的内容
•.2H: (HOW)怎么样-(问题)是怎么样被发现的
•
(HOW MANY)什么程度-(问题)发生的量、程度
解决问题的五原则-培训资料
解决问题的五原则-培训 资料
2020/12/7
解决问题的五原则-培训资料
•五 原 则 的 定 义
•“五原则”是指从“三现主义”(现场、现物、现 实)出发,分五个步骤解决问题。
•1 •充分掌握事实情况 •2 •查明真正的原因
•五个步骤是 •3 •实施切实的对策 :
•4 •确认所采取的对策是否有效
•5 •反馈到发生问题的源流
关部门传达。
•写好五原则报告表的关键:运用五原则手法解决问题
•6、减少问题再次发生的次数
解决问题的五原则-培训资料
•五原则的填写说明-发 生 状 况(现象、投诉内容、发生件数、处置内容)
•填写目标: •1、为体现到下一个行动、目标 •2、为更鲜明体现部品、部位, 应直接写下事实现象,并如实写 明该时的动机、变化
5原则表填写说明

作业要领书的修改
□要 □否
条件表的修改 其他
□要 □否 □要 □否
18/23
19/23
通过对标准类(QC工程图、检查基准书、作业指示书)的 完善,明确再发防止策、对策实施效果的继续・维持方法。 ①判断需要对哪些文书进行修改。
作业标准类:PQC、检查基准书、作业指导书、包装 类指导书、作业要领书,条件表等
①取得正确的事实. ②针对发生及流出原因,用分析图明确表示 ③明确不具合发生基本原因. ④反复为什么为什么找到真正发生的原因. (更进一步使用春风分析图分析原因) ⑤进行适当对策并实施. ⑥反映到标准类、体系中. ⑦确认效果及数值.
1 3
6/23
2
5 4
6
1.发生状况(现实)
7/23
①.现象·投诉内容
□要 □否
担当
纳期
检查基准书的修改
□要 □否
作业指导书的修改 手顺书的修改
□要 □否 □要 □否
PIR记录项目变更
□要 □否
日常/定期点检项目变更
□要 □否
保养项目变更 异常处理方法变更
□要 □否 □要 □否
图面(治工具/金型/制品)的修改 □要 □否
FMEA的修改 包装类指导书的修改
□要 □否 □要 □否
发 生
内
容
流 出
探明原因[采用系统图法进行分析。] 从各个角度反复重复为什么为什么,抓住根本性真 正原因明确填写认为是最受影响的项目。
现象
为何发生
为什么
为什么
为何流出
为什么
为什么 为什么
为什么 为什么 为什么 为什么
为什么 为什么 为什么 为什么 为什么 为什么 为什么 为什么
解决问题的五原则分析

解决问题的五原则
五 原 则 的 定 义
“五原则”是指从“三现主义”(现场、现物、现 实)出发,分五个步骤解决问题。
2
1
充分掌握事实情况
2 查明真正的原因
五个步骤是:
4
3 实施切实的对策 确认所采取的对策是否有效
5 反馈到发生问题的源流
三现主义的定义
不但适用于制造现场,也适用 于广泛的其它工作 。
五原则的填写说明-Байду номын сангаас
8
事 实 的 把 握(部品的确认结果、原因分析、生产品的品质状况)
目标 1、为探明部品、部位的原因; 2、变化(工序与用户的使用方法)产生不良, 为了一针见血找到变化和限定批次。 见下页
五原则的填写说明-
填入内容:
9
事 实 的 把 握(部品的确认结果、原因分析、生产品的品质状况)
◆等待生产现场的联系或生产现场对于技术、品质、资材等部门服务、指导、指示、供应的等待。等待下级 的汇报,任务虽已布置,但是没有检查,没有监督。不主动去深入实际调查研究,掌握第一手资料,只是被动 地听下级的汇报,没有核实,然后作决定或向上级汇报,瞒天过海没有可信度,出了问题,责任往下级身上 一推。“三现主义”的缺乏是等待中的最致命原因之一,严重影响生产现场工作的及时解决。
三现主义在中国用得很早:远点,“捉贼捉脏, 捉奸捉双”;近点,毛主席的“没有调查研究 就没有发言权”;再近点,;新闻工作者不也是 天天在掌握第一手材料么?谁和谁有拍拖之 嫌呀,哪个和哪个出现在某酒店啊,这都是三 现主义的运用,可是中国的三现主义只用于 政治或只用于整人,很少用于品质管理。
三现主义的定义
①不良品 制造工序条件 ②不良品 制造年月日 ③不良品 发生个数、概率 …等,用工序系列、时间系列整理。
教材编写规范

教材编写规范教材编写规范一、总体要求1.教材的内容要突出学科特色、体现科技成就、反映研究成果,力求具有“新、特、深、精”的特点。
同时要涵盖本门学科的主要内容,教材的深度和广度要符合教学大纲的要求,适应相应层次的培养目标,避免教材内容与课程内容之间相互脱节。
2.坚决杜绝投机取巧和剽窃、抄袭现象,避免侵犯他人知识产权的现象发生。
当为说明某一问题而引用他人观点、资料、数据、图表时,应以脚注和参考文献等形式加以说明。
如有侵权行为,一切法律责任和经济责任由作者自负。
3.教材实行主编负责制,主编负责大纲的制订、重点章节的编写、统稿、编写过程的质量控制、与参编的联系,并确保编写进度。
编写过程中如果出现人员变动应该及时通知出版社相关编辑,未经出版社同意主编不得私自添加作者。
4.书稿要由审稿人(本学科专家)审稿,交稿时要附带审稿意见,审稿意见必须由专家提出本书的特点、是否符合本科教育特色、目前存在的问题等内容。
5. 注意教材的系统性、科学性和先进性,突出知识性和适用性,总体结构、章节布局合理,内容详略得当、繁简适宜,概念、定义、名词等准确、规范。
二、编写要求(一)技术要求1.严禁出现政治性、知识性错误。
2.文字精练,层次分明,结构合理,概念表达准确无误。
3.图表清晰,术语统一,上下文连贯,逻辑关系正确。
4.各章节篇幅平衡,无过长的章幅和过短的章幅。
5.无自拟定义。
6.案例选取得当,不涉及真实单位名称、电话、账号等敏感数据。
7.教材要有参考文献。
主编对书中涉及的数据要核实其真实性、可靠性、科学性。
8.每本书的总页数控制在220~250页,即总字数控制在30~35万(版面字数)。
主编应该严格控制字数。
(二)内容要求1.封面和扉页书名:要求简明、准确。
编写人员名单:姓名用字正确。
2.目录目录是全书内容和层次结构的缩影,可使读者在短时间内了解该书的全貌,也是阅读时查寻的依据。
(1)列入目录的标题级数需视图书篇幅大小、复杂程度而定,原则上不超过二级;列入目录的标题级别要相互均衡,比如有一章列入了节标题,其他章的节标题也应该列入。
三现五原则-文档资料
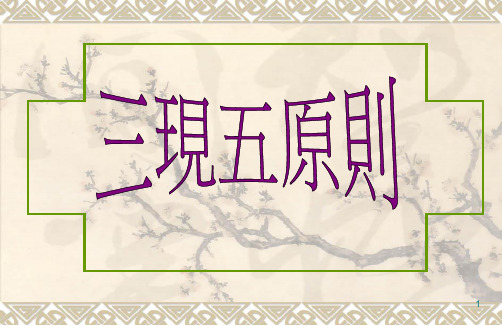
15
绘制特性要因图掌握原则
•大、小要因要确实可行。 •由大要因到小要因进行讨论,之后再由小要因往 • 大要因追溯,以确认其相关性 •在找小要因时,原则上不考虑其可能性的大小, • 一一列出。之后圈选可能原因时,再搭配查检表 • 做数量收集。
制造
物品
人 交货
为
什
么
延
特
迟
性
交
货
?
12
步骤三:决定中、小要因:可利用亲和图法来将决定中、小要因区分出来。 步骤四:讨论影响问题点的主要原因。 步骤五:填上制作目的,日期及制作者等数据。
製造
人
不良率高
生产计划不相吻合 没有危机感
情报错误 为 什 么
延
特
迟
性
会议目的: 会议日期: 与会者:
库存量低
存放位置不佳
3
发生状况 1.1数据来源 1.2发生地点
1.3发生日期 1.4发生批号 1.5发生件数
三現五原則
掌握发生状况
2.1数据来源 对书面资料所反 应的状况有所依据
2.2发生地点 对书面资料所反 应的状况有所不了 解,可直接到现场了解
2.3发生日期 可作为问题处理 时效的评估
2.4发生批号 可了解发生问题 的对象方便追查
具)
2. 内容
2.1发生要因
●使用特性要因图、FMEA等QC手法查明原因
●制造原因:设备、治具、工具、检具等原因追查
2.2原因未明,问题现象再现性 ●现场确认 ●现物确认 ●再现TE???
8
特性要因圖
•何谓特性要因图: • 一个问题的特性受到一些要因的影响时,我们将这些要因 •加以整理成为有相互关系而且有 条理的图形。这个图形称为 •特性要因图。
5原则表填写说明
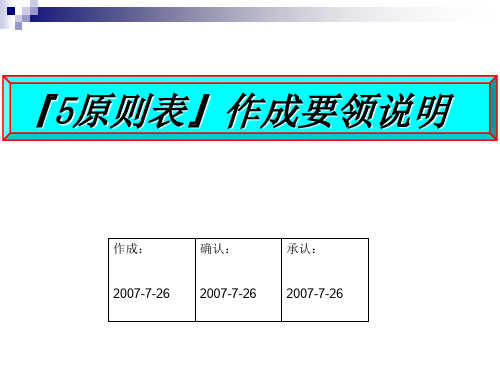
□要 □否
条件表的修改
□要 □否
其他
□要 □否
担当
纳期
18/23
19/23
通过对标准类(QC工程图、检查基准书、作业指示书)的 完善,明确再发防止策、对策实施效果的继续・维持方法。 ①判断需要对哪些文书进行修改。
作业标准类:PQC、检查基准书、作业指导书、包装 类指导书、作业要领书,条件表等
生产类:PIR、日常・定期点检项目、保养项目、异常 管理方法等
某某人的 头受伤了 好例
头撞到天 花板低处 的角
角处未铺 设保护材
天花板低 的部位的 角处铺设 保护材。
※避免向人的心理面追及原因。 ※分析的方向要向着能防止再发的硬件面、管理面等。
发生原因和流出原因的总结
发生原因和流出原因的总结 ①真正原因的再现试验
②发生原理
③流出原理
④批波及性
14/23
15/23
⑥.相关帐票管理№.(工程异常处理、NRS、CIS等)
⑦.希望事项(至急/重点确认事项及回复纳期)
发行部门期望的事项。
8/23
2.事实的把握(现场·现物·现实)
2.事实把握(现场・现物・现实)
① 不良确认结果(观察制品:确认异常制品与正常品的区别)
②工程要因确认结果(观察制造工程:确认工程的变化点和变更点、工程的运用规定和实际状态)<判定的类别有 OK,NG,不确定>
市场品质情报 最近卖桶商人
收入高涨
解决问题 作捕鼠装置
深入问题 解决
想办法让沙子 不能进入眼睛
真正原因的对策
注意点:为什么为什么分析的观点
坏例
现象
某某人的 头受伤了
为什么①
头撞到天 花板低的 部位的角
化学元素周期表教案(15篇)
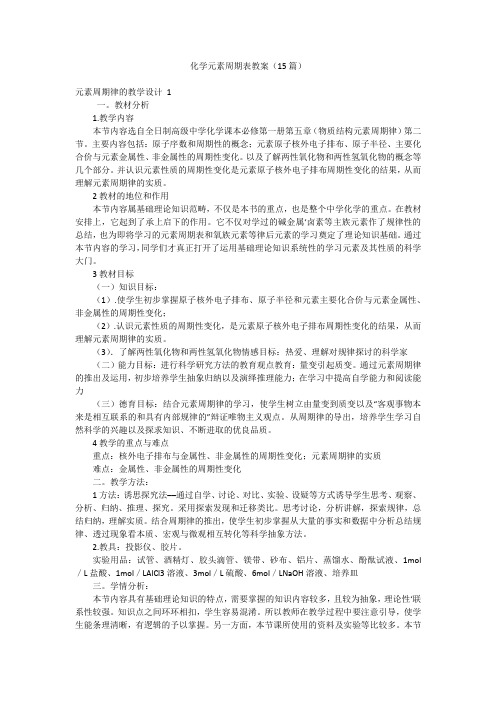
化学元素周期表教案(15篇)元素周期律的教学设计1一。
教材分析1.教学内容本节内容选自全日制高级中学化学课本必修第一册第五章(物质结构元素周期律)第二节。
主要内容包括:原子序数和周期性的概念;元素原子核外电子排布、原子半径、主要化合价与元素金属性、非金属性的周期性变化。
以及了解两性氧化物和两性氢氧化物的概念等几个部分。
并认识元素性质的周期性变化是元素原子核外电子排布周期性变化的结果,从而理解元素周期律的实质。
2教材的地位和作用本节内容属基础理论知识范畴,不仅是本书的重点,也是整个中学化学的重点。
在教材安排上,它起到了承上启下的作用。
它不仅对学过的碱金属‘卤素等主族元素作了规律性的总结,也为即将学习的元素周期表和氧族元素等律后元素的学习奠定了理论知识基础。
通过本节内容的学习,同学们才真正打开了运用基础理论知识系统性的学习元素及其性质的科学大门。
3教材目标(一)知识目标:(1).使学生初步掌握原子核外电子排布、原子半径和元素主要化合价与元素金属性、非金属性的周期性变化;(2).认识元素性质的周期性变化,是元素原子核外电子排布周期性变化的结果,从而理解元素周期律的实质。
(3).了解两性氧化物和两性氢氧化物情感目标:热爱、理解对规律探讨的科学家(二)能力目标:进行科学研究方法的教育观点教育:量变引起质变。
通过元素周期律的推出及运用,初步培养学生抽象归纳以及演绎推理能力;在学习中提高自学能力和阅读能力(三)德育目标:结合元素周期律的学习,使学生树立由量变到质变以及“客观事物本来是相互联系的和具有内部规律的”辩证唯物主义观点。
从周期律的导出,培养学生学习自然科学的兴趣以及探求知识、不断进取的优良品质。
4教学的重点与难点重点:核外电子排布与金属性、非金属性的周期性变化;元素周期律的实质难点:金属性、非金属性的周期性变化二。
教学方法:1方法:诱思探究法──通过自学、讨论、对比、实验、设疑等方式诱导学生思考、观察、分析、归纳、推理、探究。
本田五原则报告的作成

五原则的填写说明-
13
对 策 效 果 的 确 认(效果实绩)
填写目标: 为定量证明防止再发 见下页
五原则的填写说明-
14
对 策 效 果 的 确 认(效果实绩)
在工序上或客户处对对策实施效果进行跟踪(注明确认人及 确认日期,效果可以通过品质数据/测量对策前后的变化来确认, 充分活用统计手法) 1、用品质数据对对策效果进行前后比较; 2、偶发不良品时,制造条件的比较数据; 3、制品无法体现变化时,制造条件的比较数据; 在数值上无法对 4、适用方面包括到客户处确认。 比的对策不是真 正的对策 说明 定量进行效果的检证和结果的检查。 这些效果检证属: · 在客户条件下的确认 · 限度值的确认 · 试验等的确认 · 依照质量情况监视 要点: 1、确认数据的取样数量,最终确 认需要的时间也很重要 2、确认所实施对策对正常作业程 序有无不良影响 (确认工程熟练度) 3、确认人的熟练程度(确认对人有 无风险)
例:为什么机器停了?
真正的原因
课题是 构筑购买设备的体系
没有制定购买 设备时的 规则 · 渠道 在购买设备时 没有进行 充分的确认
20
最初的问题 (表象的)
为什么 机器停了
为什么-1
是因为过载造成 保险丝 断开
<防患于未然> ~管理水平~
购买了不带 过滤器的设备
为什么-2
轴承部位的 润滑 不充分
为什么-3
——依工序流程与时序,以变化为中心进行填写 3、不良发生要因调查(尽量使用图、表等来表达) ﹡ QC手法在发生要因分析中有效,利用特性要因图、FMEA进 行分析
﹡对发生要因、流出要因和事实的验证,不产生问题的条件的
特征与变化的比较,相对于集中找准的工序的不良点要因分析与 其结果 4、调查结果总结、变化点和推断原因总结 ——一针见血!变化与原因?
- 1、下载文档前请自行甄别文档内容的完整性,平台不提供额外的编辑、内容补充、找答案等附加服务。
- 2、"仅部分预览"的文档,不可在线预览部分如存在完整性等问题,可反馈申请退款(可完整预览的文档不适用该条件!)。
- 3、如文档侵犯您的权益,请联系客服反馈,我们会尽快为您处理(人工客服工作时间:9:00-18:30)。
1.对策 ・決定对策选择 ・人为引起的事件对策也要在 工具 面实施
2.对策年月日、对策地点 3.预测临时对策和恒久对策的效
果
4.对已交车和其他用户的对策 5. 对市场品和服务处置
1.确认进程和市场的对策效果 結果和确认时期 (效果选取对策前后的变化)
6、向源头反馈(向体制机构反映内容 ) 1.向实施对策的机构反映 (基准、标
2、把握事实(用事实确定投诉、异常、不良的状况)
1.问题类型(产品/服务的投诉等) 2.发生场所(市场、公司内部) 3.问题发生时的现象以及所述内容 4.发生年月日 5.发生件数 6.问题和紧急处理内容
1.问题数量 2.再现测试等的結果 3.问题发生的原因分析
・用FMEA分析特性原因图 ・原因和事实的验证、QC手法(7种工具) 4.现在的对应状况(临时对策后) 5.发生对象范围(发生率和台数)及其根据
检查不 仔细
责任心不强
工件放置未检查
材料成分不良
其他材 质
材料
检查作业指导书不完善
流出不良没跟踪控制
工艺流程变化
产品摆放方式不对
5S
人员没培训
停電
操作方法不当
作业标识不 完善
不良品放 置
方法
环境
齿形不良
检讨
1.<根据产品特性要素推断要因> 4M(man,machine,material,method,+α)
五原则解析表
齿轮齿形不良 从动齿轮不良报告
1.问题解决五原则的必要性
五原则的思路 推进品质管理, 重要的是发生问题時,通过现场、现物
现实的三现主义观察、把握事实,实施合适的对策,不使同样的问题重复发生 在产生不良时,如不认真找出真正的原因的话,就无法取得有效的对策,无
法做到再发防止。 查明原因,并且为去除产生不良的真正的发生原因,探讨为什么,
发生状况(现象.投诉内容.发生件数.处置内容)
[投诉内容] 在试车过程中,发现部分产品齿形不良引起噪音。
[信息反馈日] 反馈日2009年3月17日 1.<发生状况的把握>・・・情报的整理
[发生件数] 五次累积反馈70496件 ①.发生内容 ②.发生月日 ③.发生件数、比例
[发生场所] 生产现场
④.发生地点 ⑤.生产地点 ⑥.临时措施
4-4.把握事实-制造现场检证(整型和浸油)
1.油涂布
浸油后临时放在铁板上
油
5.<现场确认>・・・基准、标准的正确性和实际作业 对照 对①.作标 ②.点检表 ③.检基 ④.条件表 ⑤.基 准以及标准的执行情况
3.工程检证
工程名
标准
事实确认
判定
2.临时放置铁板
铁板上附有铁屑
1.涂油 2.成型 3.齿形检查
④、检验人员:成品检验人员无变化 ⑤、作业标准:检验基准书、限度封样没有变化(检验基准书有疏漏)
4-3.把握事实-現物检证
1.不良品检查结果
4.<不良品确认>・・・不良品与基准、标准的对照 与①.图纸 ②.SPEC ③.HES ④.法規 检查对比
不良齿形检 测结果
有一条凸起的棱
2.齿形检测结果
左齿形
3、查明原因(发生的原因・重现测试) 4、合适的対策(対策内容・效果顺序・PP 5、対策效果(效果实绩)
A)
1.相对发生原因的原因 ・根据特性要因图查明原因 ・特别是生产引起的问题、在工具面(设 备、 夹具、工具、检具等)查明原因
2.相对原因问题事象的再现性 3.预测临时对策和恒久对策的效果
(再现测试、现场、现物的检证)
工序
检查控制点
问题发生工序
混料
成形 巡回检验
烧结
尺寸检验
整型 巡回检验 热处理
硬度、压馈检验
机加工
尺寸检验
浸油
外观检查
包装
生产工序的变化点
3.<变化点的把握>・・・4M+α的变化点調査 ①.人 ②.设备 ③.材料 ④.方法 ⑤.问题等
①、生产设备:无变化
②、制造条件:精整工序模具出现不良
③、生产人员:无变化(考勤)
到体制、体质、组织架构为止做调整,为做源流改善实施根据五原则的問題解 決。
2.问题解決的流程
解决问题的五原则
1.发生状况: 发生状况
2.把握事实:
①.事实的把握
4.对策
③ .恰当的対策
3.究明原因
②.原因的究明
5.効果
④.效果的确认
6.源流改善、反省
⑤.源流改善
解析报告(5原则表)填写要领
1、发生状况(现象・所述内容・发生件数・处理内容)
或者使用FTA(故障树、解析)探讨要因。 ①.人 ②.设备、(模、夹具、检具、精度) ③.材料 ④.方法(作业、条件、检基、作业标准) ⑤.管理 ⑥.其他环境等
4-2.把握事实-工程和变化点
生产工序详细流程
2.<工程系列的把握>・・・工程的流程和问題工程的調査 ①.接收工程 ②.制造工程 ③.检查工程 ④.梱包等
右齿形
不良范围: 装配标记点开始 连续17齿 出现
3.在制品质量情况
規格内
規格外
齿形、齿向测量要求: 左、右齿形:0~0.011 左、右齿向:0~0.011
0.004~0.010
OK
齿形检查NG
0.004~0.008
NG
-13μ
-3μ 0
+11μ
左CPK=1.21 右CPK=0.19
左面的检验结果在数 值上均为合格,但是 右齿形在形状上出现 异常。NG現品是齿顶 凸起,不合格
2008-7-19至2008-9-13日。
产品流向:
不良产品只发往LX,没有向其它地方发送。
[临时处置] 全数挑选,并发送合格替代品,保证正常生产。
目前所有不良件的合格替代品已经全部发送。(费用全部由厂家承担)
4-1.把握事实-推定要因
特性图
设备
模具不合适 拉伤
运作不良
模具拉伤
润滑油量少
人产品附着杂物未检查Fra bibliotek[生产场所] 传动有限公司
不良从动齿轮生产日期: 2008-7-19~2008-9-13
生产数量:
期间共生产213256件,共为3套模具生产,编号分别
为: 0704、0808、0809,其中0704生产97610件,
0808生产69389件,0809生产46257件。
不良范围:
不良产品为模具编号0704生产。改模具产生不良时间从
准等)
6.对策的PPA
2.向排除项目原因的机构(横向联系部
原因分析(WHY、WHY分析 (填写查明原因的过程)
)步骤
1
2
3
门)反映(规定、基准、技术储备等)
4
5
内 容 成为特性要因图
小枝
问题的特性 大枝(大骨) 中枝(中骨) 小枝(小骨) (真正原因)
3.发生状況
标题 部品 部品名
初级从动齿轮齿形不良 125-A 从动齿轮
要涂油
・无润滑油涂布的具体 指示(作标不恰当)