故障模式影响及危害性分析和故障树分析共70页
故障模式影响和危害性分析

故障模式影响和危害性分析(FMECA)1、定义:故障模式影响分析(Failure Mode and Effects Analysis,简记为FMEA )是一种系统化的故障预想技术,它是运用归纳的方法系统地分析产品设计可能存在的每一种故障模式及其产生的后果和危害的程度。
通过全面分析找出设计薄弱环节,实施重点改进和控制。
实践表明,对系统功能可靠性要求的制定及可靠性分配相对结果是可靠性分配与指标调整的基础。
故障模式影响及危害性分析(Failure Mode,Effects and Criticality Analysis,简记为FMECA )是故障模式影响分析(FMEA)和危害性分析(Criticality Analysis-CA)的组合分析方法。
故障模式影响分析(FMEA)包括故障模式分析、故障原因分析和故障影响分析。
FMEA的实施一般通过填写FMEA表格进行。
故障模式影响分析包括故障模式分析、故障原因分析、故障影响分析。
为了划分不同故障模式产生的最终影响的严重程度,在进行故障影响分析之前,一般对最终越南故乡的后果等级进行预定义,最终影响的严重程度等级又成为严酷度(指故障模式所产生火锅的严重程度)类别。
危害性分析(CA)的目的是按每一故障模式的严重程度及该故障模式发生的概率所发生的综合影响对系统中的产品划等分类,以便全面评价系统中各种可能出现的产品故障的影响。
CA是FMEA的补充或扩展,只有在进行FMEA的基础上才能进行CA。
CA常用的方法有两种,即风险优先数(Risk Priority Number,PRN)法和危害矩阵法,前者主要用于汽车等民用工业领域,后者主要用于航空、航天等军用领域[4]。
3.5 故障树分析(FTA)故障树分析法由美国贝尔电话研究所的沃森(Watson)和默恩斯(Mearns)于1961年首次提出并应用于分析民兵式导弹发射控制系统的。
其后,波音公司的哈斯尔(Hasse)、舒劳德(Schroder)、杰克逊(Jackson)等人研制出故障树分析法计算程序,标志着故障树分析法进入了以波音公司为中心的宇航领域。
故障模式影响及危害分析报告

故障模式影响及危害分析报告一、引言故障模式、影响及危害分析(Failure Mode, Effects, andCriticality Analysis,FMECA)是一种系统性的方法,用于识别和评估系统各个组成部分的潜在故障模式、其可能的影响以及引发的危害程度。
本报告将针对其中一具体系统的故障模式、影响及可能的危害进行详细分析与评估。
二、分析方法本次分析采用FMECA方法进行,该方法的基本步骤包括:确定分析范围、识别故障模式、评估故障后果、确定故障严重程度等。
三、分析结果1.分析范围本次分析针对X系统的核心组件进行,包括A、B、C三个重要的部件。
2.故障模式及可能影响A部件:故障模式1:部件损坏可能影响:A部件损坏将导致系统无法正常工作,停止运行。
故障模式2:部件失效可能影响:A部件失效会引起系统性能下降,并且可能导致其他部件失效。
B部件:故障模式1:部件漏堵可能影响:B部件的漏堵将导致系统无法正常循环,进一步导致系统过热。
故障模式2:部件连接松动可能影响:B部件的连接松动会导致系统间隙扩大,影响系统的密封性能。
C部件:故障模式1:部件精度下降可能影响:C部件精度下降将导致系统测量结果的不准确,给系统带来误导。
故障模式2:部件过载可能影响:C部件过载将导致系统超负荷运行,进而引发短路甚至火灾。
3.故障危害评估为了对故障危害进行评估,我们采用了一个评估矩阵,将故障严重性分为轻微、中等和严重三个等级,评估结果如下:A部件:故障模式1:部件损坏危害等级:严重故障模式2:部件失效危害等级:中等B部件:故障模式1:部件漏堵危害等级:严重故障模式2:部件连接松动危害等级:中等C部件:故障模式1:部件精度下降危害等级:中等故障模式2:部件过载危害等级:严重四、决策和建议根据故障模式、影响及危害分析的结果,我们提出以下决策和建议:1.对于危害等级为严重的故障模式,应优先进行预防措施的制定和执行,以降低系统故障的风险。
故障模式影响及危害性分析与故障树分析

故障概率等级或数据来源
故障概率等级——定性分析方法
A级--经常发生 B级--有时发生 C级--偶然发生 D级--很少发生 E级--极少发生 预计值 分配值 外场评估值等
>20% 10% >20% 1% >10% 0.1% >1% <.0.1%
数据来源
故障模式危害度
根据严酷度类别和故障模式概率等级综合考虑, 危害度分为如下四级:
缓冲瓶 451110 油箱 451120 液压助塞泵ZB-34 451130
液压系统 4120
泵轴 451131 轴承组件 451132 柱塞 451133
故障影响
故障影响
局部影响:某产品的故障模式对该产品自身和与该产 品所在约定层次相同的其他产品的使用、功能或状 态的影响 高一层次影响:某产品的故障模式对该产品所在约定 层次的高一层次产品的使用、功能或状态的影响 最终影响:指系统中某产品的故障模式对初始约定层 次产品的使用、功能或状态的影响
严酷度类别
严酷度:产品故障造成的最坏后果的严重程 度 严酷度类别定义(GJB1391)
严酷度类别 严 重 程 度 定 Ⅰ类(灾难的) 这是一种会引起人员死亡或系统(如飞机、坦克、 导弹及船舶等)毁坏的故障。 Ⅱ类(致命的) 这种故障会引起人员的严重伤害、重大经济损失 或导致任务失败的系统严重损坏。 Ⅲ类(临界的) 这种故障会引起人员的轻度伤害,一定的经济损 失或导致任务延误或降级的系统轻度损坏。 Ⅳ类(轻度的) 这是一种不足以导致人员伤害、一定的经济损失 或系统损坏的故障,但它会导致非计划性维护或 修理。
故障原因
故障模式影响及危害性 (修复的)
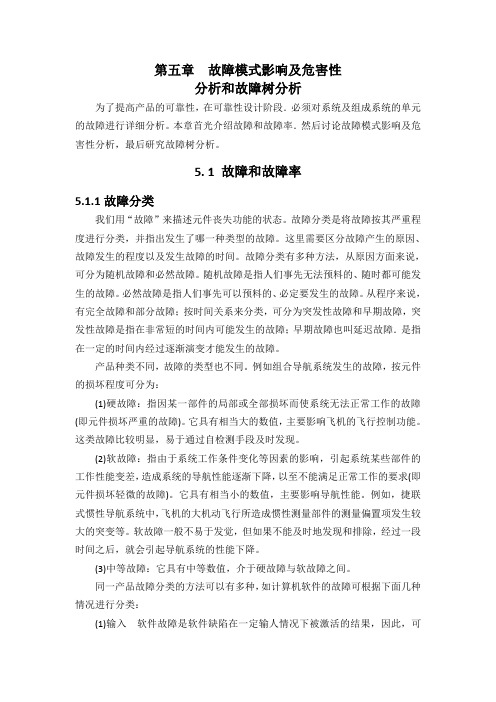
第五章故障模式影响及危害性分析和故障树分析为了提高产品的可靠性,在可靠性设计阶段.必须对系统及组成系统的单元的故障进行详细分析。
本章首光介绍故障和故障率.然后讨论故障模式影响及危害性分析,最后研究故障树分析。
5. 1 故障和故障率5.1.1故障分类我们用“故障”来描述元件丧失功能的状态。
故障分类是将故障按其严重程度进行分类,并指出发生了哪一种类型的故障。
这里需要区分故障产生的原因、故障发生的程度以及发生故障的时间。
故障分类有多种方法,从原因方面来说,可分为随机故障和必然故障。
随机故障是指人们事先无法预料的、随时都可能发生的故障。
必然故障是指人们事先可以预料的、必定要发生的故障。
从程序来说,有完全故障和部分故障;按时间关系来分类,可分为突发性故障和早期故障,突发性故障是指在非常短的时间内可能发生的故障;早期故障也叫延迟故障.是指在一定的时间内经过逐渐演变才能发生的故障。
产品种类不同,故障的类型也不同。
例如组合导航系统发生的故障,按元件的损坏程度可分为:(1)硬故障:指因某一部件的局部或全部损坏而使系统无法正常工作的故障(即元件损坏严重的故障)。
它具有相当大的数值,主要影响飞机的飞行控制功能。
这类故障比较明显,易于通过自检测手段及时发现。
(2)软故障:指由于系统工作条件变化等因素的影响,引起系统某些部件的工作性能变差,造成系统的导航性能逐渐下降,以至不能满足正常工作的要求(即元件损坏轻微的故障)。
它具有相当小的数值,主要影响导航性能。
例如,捷联式惯性导航系统中,飞机的大机动飞行所造成惯性测量部件的测量偏置项发生较大的突变等。
软故障一般不易于发觉,但如果不能及时地发现和排除,经过一段时间之后,就会引起导航系统的性能下降。
(3)中等故障:它具有中等数值,介于硬故障与软故障之间。
同一产品故障分类的方法可以有多种,如计算机软件的故障可根据下面几种情况进行分类:(1)输入软件故障是软件缺陷在一定输人情况下被激活的结果,因此,可根据软件输入类型对软件故障进行分类。
故障模式影响和危害性分析

故障模式影响和危害性分析(FMECA)1、定义:故障模式影响分析(Failure Mode and Effects Analysis,简记为FMEA )是一种系统化的故障预想技术,它是运用归纳的方法系统地分析产品设计可能存在的每一种故障模式及其产生的后果和危害的程度。
通过全面分析找出设计薄弱环节,实施重点改进和控制。
实践表明,对系统功能可靠性要求的制定及可靠性分配相对结果是可靠性分配与指标调整的基础。
故障模式影响及危害性分析(Failure Mode,Effects and Criticality Analysis,简记为FMECA )是故障模式影响分析(FMEA)和危害性分析(Criticality Analysis-CA)的组合分析方法。
故障模式影响分析(FMEA)包括故障模式分析、故障原因分析和故障影响分析。
FMEA的实施一般通过填写FMEA表格进行。
故障模式影响分析包括故障模式分析、故障原因分析、故障影响分析。
为了划分不同故障模式产生的最终影响的严重程度,在进行故障影响分析之前,一般对最终越南故乡的后果等级进行预定义,最终影响的严重程度等级又成为严酷度(指故障模式所产生火锅的严重程度)类别。
危害性分析(CA)的目的是按每一故障模式的严重程度及该故障模式发生的概率所发生的综合影响对系统中的产品划等分类,以便全面评价系统中各种可能出现的产品故障的影响。
CA是FMEA的补充或扩展,只有在进行FMEA的基础上才能进行CA。
CA常用的方法有两种,即风险优先数(Risk Priority Number,PRN)法和危害矩阵法,前者主要用于汽车等民用工业领域,后者主要用于航空、航天等军用领域[4]。
3.5 故障树分析(FTA)故障树分析法由美国贝尔电话研究所的沃森(Watson)和默恩斯(Mearns)于1961年首次提出并应用于分析民兵式导弹发射控制系统的。
其后,波音公司的哈斯尔(Hasse)、舒劳德(Schroder)、杰克逊(Jackson)等人研制出故障树分析法计算程序,标志着故障树分析法进入了以波音公司为中心的宇航领域。
06 可靠性工程-故障模式影响及危害分析

3
简要描 述产品 所具有 的主要 功能
6
简要说 明发生 故障的 的任务 阶段与 产品的 工作方 式
7
9
11
简要描 述故障 检测方 法
12
简要描 述补偿 措施
13
本栏主 要记录 对其它 栏的注 释和补 充说明
根据故障影响分析的结果, 简要描述每一个故障模式的 局部、高一层次和最终影响 并分别填入第 7 栏--9 栏
FMECA方法分类
FMECA方法分类
单独FMECA分析 方法
综合FMECA分析 方法
*2 设计FMECA 过程FMECA FMECA与FTA综合 分析法(FTF 法)
*3 FMECA与ETA综合 分析法(ETF)
*1 功能 FMECA 硬件 FMECA 软件 FMECA DMEA
注: *1 DMEA 即Damage Mode Effects Analysis(损坏模式影响分析 *2 FTA 即Fault Tree Analysis(故障树分析) *3 ETA 即Event Tree Analysis(品功能故障的产品自身的那 些物理、化学或生物变化过程等,直接原因又 称为故障机理。 间接原因:由于其他产品的故障、环境因素和 人为因素等引起的外部原因。 例如——起落架上位锁打不开
直接原因:锁体间隙不当、弹簧老化等 间接原因:锁支架刚度差
任务阶段与工作方式
任务剖面又由多个任务阶段组成
起落架任务阶段:
起飞 着陆 空中飞行 地面滑行
工作方式:
可替换 有余度:上位锁开锁:液压、手动钢索、冷气
因此,在进行故障模式分析时,要说明产品的 故障模式是在哪一个任务剖面的哪一个任务阶 段的什么工作方式下发生的。
第六章失效模式、效应及危害度分析(FMECA)和故障树分析法(FTA).

3.2
失效模式发生的概率等级可按以下方法划分:
A级:经常发生的事件,概率P>20%; B级:很可能发生的事件,10%<P<20%; C级:偶然发生的事件,1%<P<10%; D级:很少发生的事件,0.1%<P<1%; E级:极不可能发生的事件,0<P<0.1%;
②定量分析方法——危害度Cm计算
第六章失效模式、效应及危害度分析(FMECA)和 故障树分析法(FTA)
§6-1 FMEA与FTA分析方法概述 §6-2 故障模式与影响分析(FMEA) §6-3 危害性分析(CA) §6-4 对FMECA的评价 §6-5 故障树的建立 §6-6 故障树的定性分析 §6-7 故障树的定量分析
§6-1 FMECA与FTA分析方法概述
4.FMEA及FMECA的分析方法
1)表格分析法 2矩阵分析法(本书不详细介绍)
• 表格法是利用表格列出各单元故障模式,再通过故障模 式分析找出由此产生的后果
• 具体步骤:
• (1)绘制分级功能框图
• (2)对分级功能图中的每一个方框,自下而上逐级进行 FMECA分析,指出被分析方框对高一级的隶属等级产的 影响
4. 严酷度分类
2.3
对失效造成的后果的严重程度进行分类,是较笼统的、定性的分类。
Ⅰ类(灾难性的)——会引起人员死亡或系统毁坏的失效(机毁人亡)。
Ⅱ类(致命性的)——会引起人员严重伤亡、重大财产损失或导致任务失 败的系统严重失效。
Ⅲ类(临界的)——会引起人员的轻度损伤、一定人的财产损失或导致任 务延误或降级的系统轻度损坏。
Ⅰ、Ⅱ类故障,单点故障清单;
(单点故障指能导致系统失效的某一产品失效,即处于串联系统中的
第六章失效模式、效应及危害度分析(FMECA)和故障树分析法(FTA)
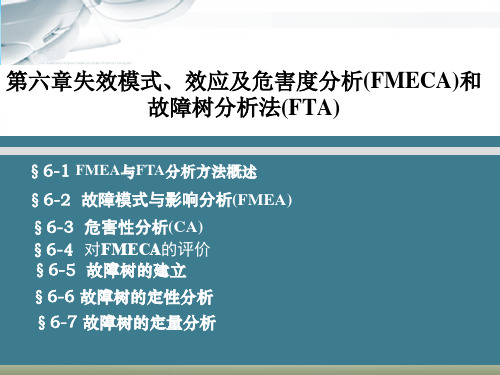
4.FMEA及FMECA的分析方法
1)表格分析法 2矩阵分析法(本书不详细介绍)
• 表格法是利用表格列出各单元故障模式,再通过故障模 式分析找出由此产生的后果 • 具体步骤: • (1)绘制分级功能框图 • (2)对分级功能图中的每一个方框,自下而上逐级进行 FMECA分析,指出被分析方框对高一级的隶属等级产的 影响 • (3)确定被分析单元的故障模式频数比aij • (4)计算单元危害度Cij • (5)计算产品危害度 • (6)编制单元故障影响分析一览表及相应的故障模式及危 害度表
3.2
②定量分析方法——危害度Cm计算 第j个失效模式的危害度为:
3.3
Cm j p j j t
式中:p——失效率(1/h) j——产品以模式j发生失效的频数比, j
j模式发生数
各模式发生数
j——模式j发生并导致系统失效的条件概率,即 j=P(Fs│Fj)
t ——产品在可能出现模式j失效状态下的工作时间(或循环次数) 注:j由分析人员判断,实际丧失 j=1,很可能丧失 0.1< j≤1, j= 0
可能成为主要系统丧失功能,从而导致该系统或其环境的 重大损坏的潜在原因,而又几乎不危及人身安全的任何事 件 能造成系统功能、性能的退化而对系统或人员的生命或肢 体没有可感觉的损伤的任何事件
可能成为系统功能、性能退化的原因而对系统或其环境几 乎无损坏,对人身安全无损害的任何事件
1.2
FMECA包括以下三个部分:
功能法:是从每个产品可以完成许多功能,而功能是按输出分类的观点出 发,将输出一一列出,并对它们的失效模式进行分析。 ‚可能的失效‛——尽可能地收集类似产品在相似适用条件下积累的有ห้องสมุดไป่ตู้关信息。
故障模式效应及危害性分析FMECA课件

FMECA与可靠性-维修性分析
通过与可靠性-维修性分析相结合,FMECA可以更好地 评估系统的维修性和可用性,优化维修策略。
FMECA在智能制造领域的应用前景
智能制造中的设备故障预测
利用FMECA对智能制造设备进行故障预测,提前发现潜在故障,提高生产效率。
智能制造技术,为智能制造系统提供实时维护决策支持,降低维护成本。
确定故障模式和影响等级
总结词
根据收集的资料和相关标准,确定系统可能 出现的故障模式,并评估其对系统性能的影 响程度。
详细描述
在FMECA分析中,确定故障模式和影响等 级是关键步骤。根据收集的资料和相关标准 ,分析人员需要识别出系统可能出现的故障 模式,并评估其对系统性能的影响程度。这 有助于为后续的优先级和重要度等级的确定 提供依据。
故障影响和危害性分析
故障影响
故障发生后对系统性能、功能和安全性等方面的影响。
危害性分析
对故障影响的严重程度和发生概率进行评估,确定故障模式的危害程度和优先级。
03 FMECA分析流程
确定分析范围和目标
总结词
明确分析的目的和范围,确定分析的重点和对象,为后续分析提供基础。
详细描述
在进行FMECA分析之前,需要明确分析的目的和范围,确定分析的重点和对象。这有助于确保分析的 针对性和有效性,避免不必要的浪费和重复工作。
树状图法
总结词
树状图法是一种通过树状图展示故障模式、影响和危害性的方法。
详细描述
树状图法通过构建树状图,将故障模式、影响和危害性逐级展开, 有助于更全面地了解故障模式的连锁反应和潜在危害性。
适用场景
适用于故障模式较多、故障影响和危害性较复杂的系统或设备。
矩阵法
故障模式、影响与危害性分析
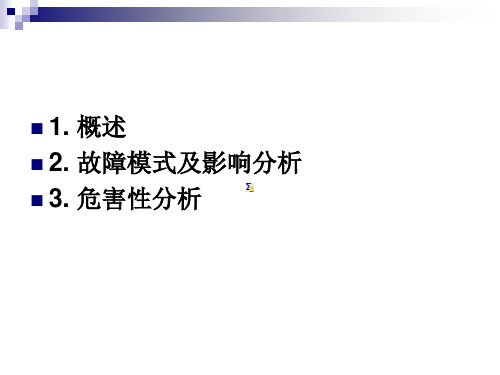
第二节 故障模式及影响分析
FMEA(Failure Mode and Effects Analysis) 故障模式及影响分析。是分析系统的每个 组成部件发生故障时洗头膏产生的影响, 划分各种故障的等级,并预先研究查找潜 在故障的方法。 FMEA 是进行系统可靠性设计的一种重要 方法。它实际上是FMA和FEA的组合。
1976年,美国国防部确定FMEA所有武器采购的 必要活动。七十年代后期,美国汽车工业采用FMEA 作为风险评估工具。 到80 年代以后许多汽车公司开始发展内部之 FMECA 手册,此时所发展之分析方法与美军标准渐 渐有所区别,最主要的差异在于引进半定量之评点方 式评估失效模式之关键性,后来更将此分析法推广应 用于制程之潜在问题模式分析,因此针对分析对象之 不同,将FMECA 分成「设计FMECA」与「制程 FMECA」,并开始要求供货商其所供应的零件进行 设计与制程FMECA,视为对供货商的重点考成项目。 1985 年由国际电工委员会(International Electronical Commission, IEC)所出版之FMECA 国 际标准「IEC 812」即是参考美军标准MIL-STD1629A 加以部份修改而成之FMEA 作业程序。 1991年,ISO9000 推荐采用FMEA;1994年, QS9000 强制采用FMEA,将FMECA 视为重要的设 计管制与安全分析方法。
FMECA Analysis
Failure Mode
Effect
Criticality
早在 5 0 年代初,美国格鲁门飞机公司在研制飞机 主操纵系统时就采用 FMEA 方法,应用于飞机主操纵 系统的失效分析,取得了良好的效果。 1957 年波音(Boeing)与马丁(Martin Marietta)公司在 其工程手册中正式列出FMEA 之作业程序。 到了 60 年代后期和 70 年代初期,FMEA方法开始 广泛地应用于航空、航天、舰船、兵器等军用系统的 研制中,并逐渐渗透到机械、汽车、医疗设备等民用 工业领域,取得显著的效果。60 年代初期,美国航空 太空总署(NASA)将FMECA 技术成功地应用于太空计 划,同时美国军方也开始应用FMECA 技术,并于 1974 年出版军用标准MIL-STD-1629 规定FMECA 作 业程序,1980 年将此一标准修订改版为MIL-STD1629A,延用至今,目前此一标准仍为全世界重要之 FMECA 参考标准之一。
故障模式效应及危害性分析故障树分析

故障模式效应及危害性分析故障树分析
故障模式:
一、故障模式:
1、硬件故障:由于计算机硬件的损坏或磨损,导致计算机无法正常
运行。
这种故障可以分为主板、内存、CPU、显示卡、显示器、硬盘、电
源等多个部分。
2、软件故障:由于软件的损坏、病毒感染或操作不当,导致计算机
无法正常运行。
3、网络故障:由于网络设备、传输介质及网络信号和路由而有诸多
问题,从而影响计算机网络的正常运行。
二、故障效应:
1、硬件故障:一旦发生硬件故障,计算机将无法正常运行,甚至无
法开机。
2、软件故障:一旦发生软件故障,计算机将出现软件异常,病毒感
染和操作不当等问题,使计算机无法正常运行。
3、网络故障:发生网络故障将导致计算机网络中断,无法在计算机
网络中进行数据交换和资源共享,从而使计算机无法正常工作。
三、危害性分析:
1、硬件故障:硬件故障会导致计算机无法正常运行,影响用户使用,严重的可能会使计算机无法开机,且经济损失较大;
2、软件故障:软件故障会使计算机出现软件异常,病毒感染和操作不当等问题,使计算机无法正常运行,影响用户使用,且经济损失较大;
3、网络故障:当发生网络故障时。
第七章故障模式影响及危害性分析与故障树分析
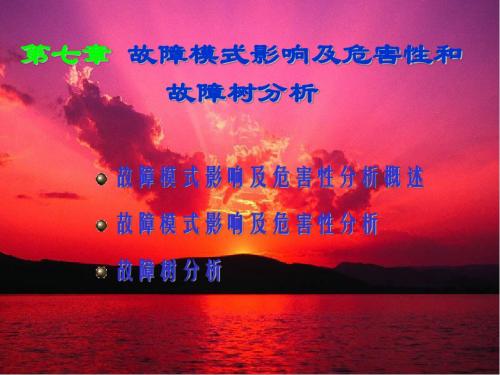
(2) 找出所有矩形事件的全部、直接起因。
(3) 对各级事件的定义要简明、确切。
(4) 正确运用故障树符号。
(5) 所有中间事件都被分解为底事件时,故障树建成。
例:家用洗衣机故障树
进水口
上盖
控制面板 外箱体
排水管
盛水桶
支撑拉杆
潘存云教授研制
波轮 脱水桶
电动机
带传动
减速器
解: (1)系统情况 此处主要分析洗衣机主系统,主要由电动 机、传动系统和波轮组成。 (2)确定顶条件 主系 统不希望发生的故障有 波轮不转、波轮转速过 低、振动过大等。其中 最严重的故障事件是波 轮不转。
危害度分析危害度分析危害性分析危害性分析caca的目的是按每一故障模式的严重程度及该故障模式的目的是按每一故障模式的严重程度及该故障模式发生的概率所产生的综合影响对系统中的产品划等分类以便全面评价系发生的概率所产生的综合影响对系统中的产品划等分类以便全面评价系统中各种可能出现的产品故障的影响是统中各种可能出现的产品故障的影响是fmeafmea的补充或扩展只有在进的补充或扩展只有在进行行fmeafmea的基础上才能进行的基础上才能进行caca
7.2.3、故障模式影响及危害性分析的基本思路与程序
实际上在常规设计思路中已经运用到了FMEA的思想。 FMEA的基本思路如图7-2所示。
根据GJB 1391—92《故障模式、影响及危害性分析程序》 的要求,对产品进行故障模式、影响及危害度分析,需要按如 下步骤进行: 1.熟悉和掌握有关资料 1)产品结构和功能的有关资料; 2)产品启动、运行、操作、维修资料; 3)产品所处环境条件的资料。 2.系统定义 1)任务功能 2)环境条件 3)任务时间 4)功能框图 5)可靠性框图
故障模式——精选推荐

故障模式、影响及危害性分析(FMECA)故障模式、影响及危害性分析(FMECA)是针对产品所有可能的故障,并根据对故障模式的分析,确定每种故障模式对产品工作的影响,找出单点故障,并按故障模式的严酷度及其发生概率确定其危害性。
所谓单点故障指的是引起产品故障的,且没有冗余或替代的工作程序作为补救的局部故障。
FMECA包括故障模式及影响分析(FMEA)和危害性分析(CA)。
故障模式和影响分析(FMEA)是在产品设计过程中,通过对产品各组成单元潜在的各种故障模式及其对产品功能的影响进行分析,提出可能采取的预防改进措施,以提高产品可靠性的一种设计分析方法。
危害性分析(CA)是把FMEA中确定的每一种故障模式按其影响的严重程度类别及发生概率的综合影响加以分析,以便全面的评价各种可能出现的故障模式的影响。
CA是FMEA的继续,根据产品的结构及可靠性数据的获得情况,CA可以是定期分析也可以是定量分析。
FMECA分析方法可用于整个系统到零部件任何一级,一般根据要求和可能在规定的产品层次上进行。
故障模式是指元器件或产品故障的一种表现形式。
一般是能被观察到的一种故障现象。
如断裂、接触不良、短路、腐蚀等。
故障影响是指该故障模式会造成对安全性、产品功能的影响。
故障影响一般可分为:对局部、高一层次及最终影响三个等级。
如分析飞机液压系统中的一个液压泵,它发生了轻微漏油的故障模式,对局部即对泵本身的影响可能是降低效率,对高一层次即对液压系统的影响可能是压力有所降低,最终影响即对飞机可能没有影响。
严酷度是指某种故障模式影响的严重程度。
一般分为四类:Ⅰ类(灾难性故障),它是一种会造成人员死亡或系统(如飞机)毁坏的故障。
Ⅱ类(致命性故障),这是一种导致人员严重受伤,器材或系统严重损坏,从而使任务失败的故障。
Ⅲ类(严重故障)这类故障会使人员轻度受伤、器材及系统轻度损坏,从而导致任务推迟执行、或任务降级、或系统不能起作用(如飞机误飞)。