合金管件制造工艺说明
管道通用工艺规程
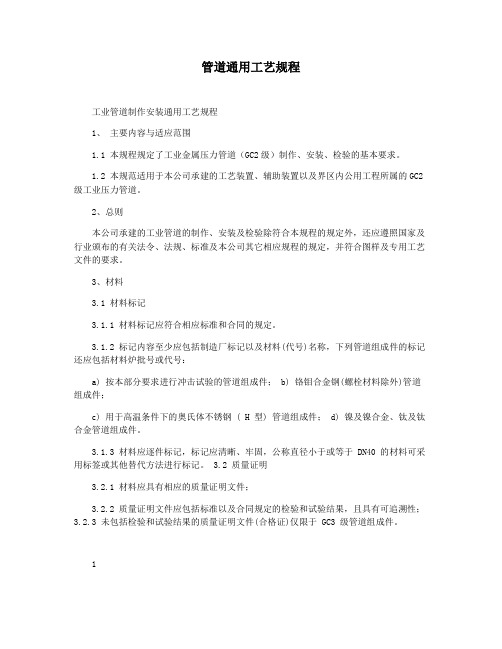
管道通用工艺规程工业管道制作安装通用工艺规程1、主要内容与适应范围1.1 本规程规定了工业金属压力管道(GC2级)制作、安装、检验的基本要求。
1.2 本规范适用于本公司承建的工艺装置、辅助装置以及界区内公用工程所属的GC2级工业压力管道。
2、总则本公司承建的工业管道的制作、安装及检验除符合本规程的规定外,还应遵照国家及行业颁布的有关法令、法规、标准及本公司其它相应规程的规定,并符合图样及专用工艺文件的要求。
3、材料3.1 材料标记3.1.1 材料标记应符合相应标准和合同的规定。
3.1.2 标记内容至少应包括制造厂标记以及材料(代号)名称,下列管道组成件的标记还应包括材料炉批号或代号:a) 按本部分要求进行冲击试验的管道组成件; b) 铬钼合金钢(螺栓材料除外)管道组成件;c) 用于高温条件下的奥氏体不锈钢 ( H 型) 管道组成件; d) 镍及镍合金、钛及钛合金管道组成件。
3.1.3 材料应逐件标记,标记应清晰、牢固,公称直径小于或等于 DN40 的材料可采用标签或其他替代方法进行标记。
3.2 质量证明3.2.1 材料应具有相应的质量证明文件;3.2.2 质量证明文件应包括标准以及合同规定的检验和试验结果,且具有可追溯性;3.2.3 未包括检验和试验结果的质量证明文件(合格证)仅限于 GC3 级管道组成件。
13.3 外观检查管道组成件及管道支承件的材料牌号、规格、外观质量应按相应标准进行目视检查和几何尺寸抽查,不合格者不得使用。
3.4 材质检查对于合金钢、含镍低温钢、含钼奥氏体不锈钢以及镍基合金、钛和钛合金材料的管道组成件,应采用光谱分析或其它方法进行材质抽样检查,抽样数量取每批(同炉批号、同规格,下同)的5%且不少于一个管道组成件。
3.5 阀门试验阀门应按标准要求进行壳体压力试验和密封试验: a) 用于GC2 级管道的阀门应每批抽查10%,且不得少于一个。
b) 用于GC3 级管道的阀门应每批抽查5%,且不少于一个。
钛合金曲面类零件的热冲压工艺

钛合金曲面类零件的热冲压工艺摘要:钛合金具有良好的屈强比、高低温性能、抗疲劳性能和耐腐蚀性能等优点,其复杂薄壁曲面和中空整体结构广泛应用,部分零件兼具耐高温、良好气动性能等。
国内各研究院所及主机厂的研究工作多偏重于成形工艺本身,如模具设计、工艺参数、工艺缺陷、尺寸精度、组合工艺方法、工艺仿真和组织性能、国产热塑性成形机床研制等,高校开始逐渐转向热变形机理及形性控制、新材料开发、新热塑性成形工艺等研究方向。
相比于国外,国内在热塑性变形基础理论、可持续开发的自主仿真软件平台、热塑性成形基础数据库及智能调用等研究上还有一定差距。
本文分析了热塑性成形工艺,讨论了钛合金薄壁件热塑性成形工艺。
关键词:钛合;热冲压;工艺钛合金 (Ti-6Al-4V) 具有比强度高、密度小、抗腐蚀性能强等特点,被广泛用于加工航空发动机涡轮叶片、涡轮盘等复杂曲面等零件。
目前,加工行业普遍采用切削力小、切削速度高的高速铣削方式来满足钛合金材料的高质量、高效率的绿色加工。
然而由于加工工件复杂的几何特性,导致铣削过程中材料去除率不稳定,由瞬时铣削量变化导致铣削热波动,极易加剧刀具磨损,降低工件表面完整性,进而影响加工工件服役性能,故对钛合金复杂曲面高速铣削中铣削热开展研究具有重要意义。
一、钛合金的工艺发展钛合金薄壁件及热塑性成形装备已基本实现“造得出”,并提出“造得精、造得好”的更高要求。
对新型高温钛合金、Ti2AlNb、TiAl 等难加工新材料,其投影面积 2m2 以上的高精度超薄件、局部棱角尖锐的新结构件、带功能的中空复杂结构件等需求增加,迫切需要制造工艺的快速发展。
为此,可开展以下研究。
1、“材料–设计–制造–装备”一体化协同发展。
多层、蜂窝、点阵的热塑性成形方法为混合结构提供了设计空间,结合非均匀材料分布、梯度材料、异种材料连接等,可使钛合金薄壁件结构实现轻量化、自主冷却、吸声隔热等功能,满足装备提出的新要求。
2、形性预测控制及仿真软件。
钢制管件工艺流程及技术特点

钢制管件工艺流程及技术特点一、钢制管件的生产工艺流程包括以下步骤:1.材料准备:选择合适的钢材,包括碳钢、合金钢等,进行切割、焊接等预处理工作。
2.管件设计:根据管件的应用需求和要求,进行产品设计和模具制造。
3.冷弯:通过冷弯机对钢材进行冷弯成型。
4.焊接:将冷弯后的零件进行焊接,包括TIG焊、MIG焊、电弧焊等。
5.补强处理:对焊接处进行补强处理,包括笼焊、焊缝焊接等。
6.热处理:通过加热和冷却处理,使钢制管件的性能得到提升和调整。
7.表面处理:对钢制管件的表面进行除锈、喷涂等防腐处理。
8.检测:对成品进行各项检测,包括尺寸检测、焊缝探伤、压力测试等。
9.包装和出厂:将合格的钢制管件进行包装,并进行出厂发货。
二、钢制管件工艺流程的技术特点如下:1.精确性:钢制管件工艺要求精确,每个环节都需要严格控制尺寸和焊接质量,确保其与管道的连接紧密、牢固。
2.强度:钢制管件工艺要求强度高,能够承受大压力和重负荷的作用,以确保管道系统的安全和可靠性。
3.耐腐蚀性:钢制管件工艺要求抗腐蚀能力强,可以在恶劣的环境下使用,如化工厂、海上平台等。
4.工艺稳定性:钢制管件工艺要求工艺稳定,能够充分满足大规模生产的需求,提高生产效率和产品质量。
5.环保性:钢制管件工艺要求环保,减少对环境的污染,采用低排放和可再生的材料和工艺。
6.灵活性:钢制管件工艺具有一定的灵活性,能够适应不同形状、尺寸和材质的管道系统的要求。
7.经济性:钢制管件工艺追求经济性,既要保证产品的质量和性能,又要降低生产成本,提高市场竞争力。
总之,钢制管件工艺流程及技术特点是针对钢制管件的生产过程和要求进行的总结和归纳,只有在遵循相关工艺流程和技术要求的基础上,才能生产出满足高质量和高性能要求的钢制管件产品。
6061铝合金超薄壁弯管制造工艺及组织性能研究

6061铝合金超薄壁弯管制造工艺及组织性能研究丁月霞;马燕楠;郭群;王辉;马福业;郭训忠【摘要】通过单向拉伸试验建立了材料的本构方程,对6061铝合金板材半片拉深成形过程进行了有限元模拟,研究了摩擦系数与压边力对拉深成形结果的影响规律模拟结果表明:拉深成形时,应采用较大的压边力和较小的摩擦系数,以避免外管的外弧处易出现明显的起皱缺陷;基于模拟结果,进行了6061铝合金Φ202mm×1mm 弯管半片拉深成形;最后对半片焊接后的超薄壁弯管进行了耐压爆破试验及关键部位微观组织分析.【期刊名称】《航空制造技术》【年(卷),期】2016(000)017【总页数】5页(P50-54)【关键词】6061铝合金;超薄壁弯管;有限元模拟;拉深成形【作者】丁月霞;马燕楠;郭群;王辉;马福业;郭训忠【作者单位】江苏华阳金属管件有限公司,镇江212400;南京航空航天大学先进材料及成形技术研究所,南京211100;江苏核能装备材料工程实验室,南京211100;南京航空航天大学材料科学与技术学院,南京211100;南京航空航天大学先进材料及成形技术研究所,南京211100;江苏核能装备材料工程实验室,南京211100;南京航空航天大学材料科学与技术学院,南京211100;南京航空航天大学先进材料及成形技术研究所,南京211100;江苏核能装备材料工程实验室,南京211100;南京航空航天大学先进材料及成形技术研究所,南京211100;江苏核能装备材料工程实验室,南京211100;南京航空航天大学材料科学与技术学院,南京211100;南京航空航天大学先进材料及成形技术研究所,南京211100;江苏核能装备材料工程实验室,南京211100;南京航空航天大学材料科学与技术学院,南京211100【正文语种】中文导管是现代军机、民机上的关键部件之一,将各种介质输送到飞机发动机、起落架、座舱等关键部位,满足飞机包括燃油、氧气、液压、环境控制等方面的系统需求[1-3]。
材料成型第3章金属的铸造形成工艺2

61
3. 离心铸造应用范围
用离心铸造法生产产量很大的铸件有以下几种: (1) 铁管,世界上每年球墨铸铁管件总产量的近一半是用离心铸造法生产的; (2) 柴油发动机和汽油发动机的气缸套。 (3) 各种类型的铜套。 (4) 双金属钢背铜套、各种合金的轴瓦。 (5) 造纸机滚筒。
材料成型第3章金属的铸造形成工艺2
冷压室卧式压铸(目前应用最多)
(3)取出铸件:铸件凝固之后,抽芯机构将型腔两侧型芯同时抽 出,动型左移开型,铸件则借冲头的前伸动作离开压室。此后, 在动型继续打开过程中,由于顶杆停止了左移、铸件在顶杆的作 用下被顶出动型(图d)。
材料成型第3章金属的铸造形成工艺2
冷室压铸机的压室 和熔炉是分开的, 压铸时要从保温炉 中舀取金属液倒入 压室内,再进行压 铸。
材料成型第3章金属的铸造形成工艺2
冷压室卧式压铸(目前应用最多)
(1)注入金属 先闭合压型,将勺内金属液通过压室上的注 液孔向压室内注入(图a)。 (2)压铸压射冲头向前推进,金属液被压人压型中(图b)。
材料成型第3章金属的铸造形成工艺2
1、压力机工作原理及应用 (1)热压室压铸机
热室压铸机的压室 与合金熔化炉联成一体, 压室浸在保温坩埚的液 体金属中,压射机构装 在坩埚上面,用机械机 构或压缩空气所产生的 压力进行压铸。
图3-23为热室压铸机工作原理示意图。
材料成型第3章金属的铸造形成工艺2
(2)冷压室压铸机
材料成型第3章金属的铸造形成工艺2
二、 压力铸造
定义:在高压(30~70MPa) 下将液态或半液态合金 快速( 5~100mm/s,t=0.05~0.2s))地压入金属铸型中, 并在压力下凝固,以获得铸件的方法。
管件MPS文件

郑州万达重工股份有限公司文件号:项目号:钢制管件制造工艺规范日期:2016.11.阶段:A版钢制管件制造工艺规范(MPS文件)说明编制审核批准日期供招标目录1 范围 (2)2 规范性引用文件 (2)3 制造工艺流程 (3)4 管件基本参数 (4)5 原材料要求 (5)6 制造工艺要求 (6)7 性能要求 (15)8 几何尺寸、形状允许偏差 (16)9 工艺质量和缺陷处理 (18)10 检验和试验 (18)11 设计验证试验 (22)12 标志 (24)13 防护与包装 (24)14 产品质量合格证明书 (25)1 范围1.1 本文件规定了山东港联化董家口港-潍坊-鲁中、鲁北输油管道工程管(一期)管件采购项目用L245N、L360M、L450M等材质钢制管件生产的基本参数、原材料、制造工艺、材料性能、几何尺寸与允许偏差、工艺质量与缺陷修补、检验与实验、标志、涂层与保护、质量证明书及装运的要求。
1.2 本MPS文件应和GB/T 12459-2005《钢制对焊无缝管件》、GB/T 13401-2005《钢板制对焊管件》、GB/T 19326-2012《钢制承插焊、螺纹和对焊支管座》标准及D1630D-GI00-PR01-SP14《清管三通技术规格书》一起使用,凡是出现与GB/T 12459-2005 《钢制对焊无缝管件》、GB/T 13401-2005 《钢板制对焊管件》、GB/T 19326-2012《钢制承插焊、螺纹和对焊支管座》标准及D1630D-GI00-PR01-SP14《清管三通技术规格书》相冲突的条款,应以最严格的为准。
2 规范性引用文件下列文件中的条款通过本文件的引用而成为本文件的条款。
凡是注日期的引用文件,其随后所有的修改单(不包括勘误的内容)或修订版均不适用于本文件,然而,鼓励根据本文件达成协议的各方研究是否可使用这些文件的最新版本。
凡是不注日期的引用文件,其最新版本适用于本文件。
主要钛产品生产工艺流程
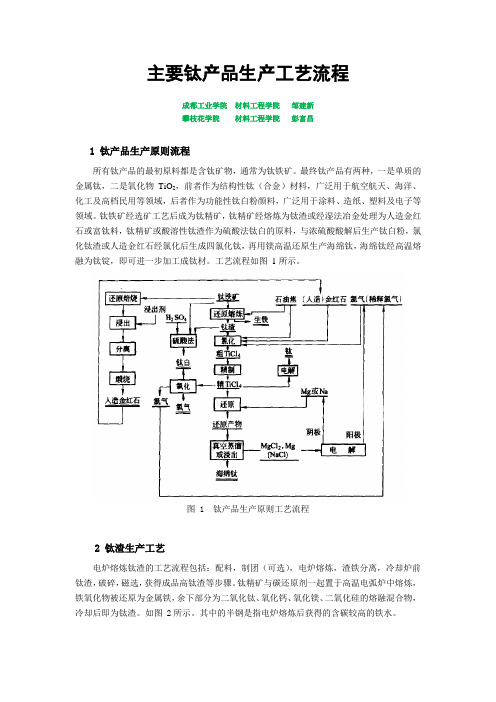
主要钛产品生产工艺流程成都工业学院材料工程学院邹建新攀枝花学院材料工程学院彭富昌1 钛产品生产原则流程所有钛产品的最初原料都是含钛矿物,通常为钛铁矿。
最终钛产品有两种,一是单质的金属钛,二是氧化物TiO2,前者作为结构性钛(合金)材料,广泛用于航空航天、海洋、化工及高档民用等领域,后者作为功能性钛白粉颜料,广泛用于涂料、造纸、塑料及电子等领域。
钛铁矿经选矿工艺后成为钛精矿,钛精矿经熔炼为钛渣或经湿法冶金处理为人造金红石或富钛料,钛精矿或酸溶性钛渣作为硫酸法钛白的原料,与浓硫酸酸解后生产钛白粉,氯化钛渣或人造金红石经氯化后生成四氯化钛,再用镁高温还原生产海绵钛,海绵钛经高温熔融为钛锭,即可进一步加工成钛材。
工艺流程如图1所示。
图 1 钛产品生产原则工艺流程2 钛渣生产工艺电炉熔炼钛渣的工艺流程包括:配料,制团(可选),电炉熔炼,渣铁分离,冷却炉前钛渣,破碎,磁选,获得成品高钛渣等步骤。
钛精矿与碳还原剂一起置于高温电弧炉中熔炼,铁氧化物被还原为金属铁,余下部分为二氧化钛、氧化钙、氧化镁、二氧化硅的熔融混合物,冷却后即为钛渣。
如图 2所示。
其中的半钢是指电炉熔炼后获得的含碳较高的铁水。
图 2 电炉熔炼钛渣的原则工艺流程3 硫酸法钛白粉的生产工艺钛白生产方法包括如下三种:①硫酸法,可生产金红石型和锐钛型钛白;②氯化法,国内仅中信锦州钛业、云南新立、洛阳万基、漯河兴茂、攀钢在生产或在建,国外55%企业采用,只能生产金红石型钛白;③盐酸法,尚未产业化,新西兰曾进行试生产,国内不少学者也开展过实验研究。
生产钛白的硫酸法与氯化法各有优缺点,业界评价褒贬不一。
硫酸法会产生绿矾和废酸,但可综合利用,氯化法产生的氯化废渣处理难度较大,一般只能深埋,国内攀钢集团已开发了一种可以有效回收利用氯化废渣的专有技术。
硫酸法可生产锐钛型钛白,但氯化法不行。
随着环保成本的增加,硫酸法钛白粉厂只要愿意增大资金投入,其“三废”污染问题是可以得到较好解决的。
压力管道元件制造工艺

压力管道元件制造工艺压力管道元件制造工艺压力管道元件是压力管道系统中的重要组成部分,包括法兰、弯头、三通、承插、管件和管接头等,并在工业、建筑、交通等领域中广泛应用。
为了确保管道系统的安全可靠性,保护环境,压力管道元件的制造工艺必须严格遵守国家标准和相关规定。
本文将从材料选择、加工工艺、质量检测等方面介绍压力管道元件的制造工艺。
一、材料选择压力容器和压力管道元件的材料必须符合国家标准或相关规定,主要有碳素结构钢、低合金结构钢、不锈钢、铝合金等。
根据使用要求,可以选择不同的材料类型和级别。
材料的质量决定了元器件的耐腐蚀性、机械强度和耐高温性等重要性能。
制造压力管道元件时应确保材料无缺陷、裂纹、疏松、夹杂等质量问题,以保证其可靠性和使用寿命。
二、设计和加工工艺压力管道元件的设计应满足国家标准和技术要求,并应符合安全、可靠、节能、环保等基本原则。
在加工前要按照工艺流程进行材料切割、热处理、成型、加工、修整等工作,掌握好材料的加热温度、冷却条件、成形压力、加工方法等工艺参数,以确保元件的准确性和质量。
在锻造、铸造、冲压等加工过程中,要确保选用合适的压力和温度,避免材料硬化、变形、疲劳和其他质量问题。
三、质量检测压力管道元件的质量检测非常重要,它可以确保元件的耐高压、耐腐蚀、耐磨、耐热等性能。
检测覆盖材料化学成分、物理特性、外形尺寸、机械性能、非破坏性检测等多个方面,包括压力试验、磁粉探伤、射线探伤、超声波探伤等多种技术手段。
其中,压力试验是检测压力管道元件强度和密封性能的重要方法,它可以模拟实际工作环境下的压力并检查待测物件是否漏气、漏油、发生爆炸等情况。
质量检测也是保证元件的生产质量和后续工程的安全运行的重要保障手段。
四、总结综上所述,压力管道元件的制造工艺是非常严格和复杂的,需要选用合适的材料、设计和加工工艺,并进行严格的质量检测。
压力管道元件作为压力容器系统中的核心部件,质量问题直接影响到整个系统的安全和可靠性。
铜合金的冶炼与铸造工艺

化学氧化处理
通过化学反应在铜合金表面形成一 层氧化膜,提高耐腐蚀性和装饰性 。
04
铜合金的应用领域
建筑领域的应用
01
铜合金在建筑领域的应用主要涉及管道系统、供暖系统、屋顶和外墙 材料等。
02
由于铜合金具有优良的耐腐蚀性和导热性,因此被广泛用于建筑行业 的管道系统,能够保证水质的清洁和管道系统的长期稳定运行。
搅拌器
用于在熔融状态下混合和均匀 化铜合金,保证成分的稳定性 。
模具和浇注系统
用于将熔融状态的铜合金浇注 或注入到铸型中,形成所需的
形状和尺寸。
02
铜合金的铸造工艺
铜合金的铸造方法
砂型铸造
利用砂型作为模具进行 铜合金的铸造,适用于
小批量生产。
熔模铸造
通过制作蜡模后进行熔 脱、焙烧、浇注等工序 ,可生产复杂形状的铜
电解冶炼
利用电解原理将铜和其他 金属元素从其化合物中还 原出来,生成金属单质。
湿法冶炼
通过化学反应将铜和其他 金属元素从其化合物中提 取出来,再进行精炼和提 纯。
铜合金的熔炼设备与工具
熔炼炉
用于熔化铜和其他金属元素, 一般采用电炉或燃气炉。
坩埚
用于盛放熔融状态的铜合金, 具有耐高温、耐腐蚀的特性。
03
在供暖系统中,铜合金的导热性能优异,能够快速传递热量,提高供 暖效率。
04
此外,铜合金还被用于屋顶和外墙材料,具有美观、耐久和防火等特 点。
机械制造领域的应用
01
铜合金在机械制造领域的应用非常广泛,涉及到各 种零部件和工具的制造。
02
由于铜合金具有良好的加工性能和耐磨性,因此被 用于制造各种轴承、齿轮、蜗轮等机械部件。
管件生产工艺流程

管件生产工艺流程一、概述管件是连接管道的重要组成部分,其生产工艺流程关系到管件的质量和性能。
本文将详细介绍常见管件生产工艺流程,包括原材料准备、模具制作、加工成型、热处理、表面处理、检测验收等环节。
二、原材料准备1. 材料选择:根据管件的要求选择合适的原材料,常见的包括碳钢、不锈钢、合金钢等。
2. 材料采购:选择正规、可信赖的供应商采购合格的原材料,确保材料的质量和完整性。
3. 材料检验:进行原材料的外观检查、化学成分分析和力学性能测试,确保原材料符合相关标准。
三、模具制作1. 模具设计:根据管件的尺寸、形状和结构要求,设计合适的模具结构,并考虑到生产效率和成本因素。
2. 模具制造:根据模具设计图纸,选择合适的材料,进行切割、铣削、车削、磨削等加工工艺,制造出精确的模具。
四、加工成型1. 切削或冲压:根据模具的设计,通过切削或冲压工艺,将原材料进行切削或冲压,形成初步的管件形状。
2. 热成型:采用热成型工艺,通过加热和模具压力,使原材料在模具中塑性变形,形成精确的管件形状。
3. 机加工:对加工成型后的管件进行车削、钻孔、铆接等工艺,进行加工精度校验和表面光洁度处理。
五、热处理1. 退火:对加工的管件进行退火处理,通过加热和冷却的控制,改善材料的结晶结构,消除应力,提高管件的韧性和强度。
2. 淬火和回火:对某些特殊要求的管件,进行淬火和回火处理,增加管件的硬度和耐磨性。
六、表面处理1. 清洗处理:对管件进行清洗,去除表面的油污、灰尘等杂质。
2. 酸洗和酸洗前处理:采用酸洗工艺,使管件表面达到一定的光洁度和粗糙度要求,提高管件的耐腐蚀性。
3. 镀锌或喷涂:对一些需要防腐蚀的管件,进行镀锌或喷涂工艺,形成保护层,延长管件的使用寿命。
七、检测验收1. 外观检查:对管件进行外观检查,包括尺寸、表面质量、形状等方面的检验。
2. 物理性能测试:通过拉伸试验、冲击试验、硬度测试等手段,对管件的物理性能进行测试,确保符合相关标准要求。
02S403钢制管件

02S403钢制管件是一种非常重要的管道连接件,其在工业生产和建筑领域中具有广泛的应用。
本文将从材料特性、制造工艺、应用领域以及市场前景等方面详细介绍02S403钢制管件。
首先,我们来了解一下02S403钢制管件的材料特性。
02S403是一种低碳合金钢,其具有优良的机械性能和强度。
其主要成分包括铁(Fe)、碳(C)、硅(Si)、锰(Mn)等元素。
含有适量的碳元素可提高钢材的强度和硬度,同时还具有良好的可塑性和可焊性。
此外,硅和锰等元素的添加使钢材具有良好的耐磨性和耐腐蚀性。
这些优良的材料特性使得02S403钢制管件在各种工况下都能够保持稳定的性能。
接下来,我们将介绍02S403钢制管件的制造工艺。
首先,选取符合标准的02S403钢材,经过热轧、锻造或冷加工等工艺加工成成型坯料。
然后,通过热挤压、锻压、冲压、焊接等加工工艺,将成型坯料加工成各种形状的管件。
最后,经过热处理、表面处理等工艺,使得管件的性能得以优化。
制造工艺的优劣直接影响着02S403钢制管件的质量和性能。
02S403钢制管件具有广泛的应用领域。
首先,在工业生产中,02S403钢制管件主要用于管道的连接和支撑。
无论是在化工、石油、天然气还是其他工业领域,02S403钢制管件都能够承受高压、高温和腐蚀等恶劣条件下的工作环境。
其稳定的性能和可靠的连接方式,保证了管道系统的安全和稳定运行。
此外,02S403钢制管件还广泛应用于建筑领域,如管道系统的安装、暖通系统的连接等方面。
最后,我们来谈一谈02S403钢制管件的市场前景。
随着国家经济的不断发展和工业化进程的加快,对于高品质、高性能的管道连接件需求也日益增加。
02S403钢制管件作为一种质量可靠、性能稳定的管道连接件,将具有广阔的市场前景。
尤其是在石油、化工等行业中,对于管道系统的要求更高,对高质量的管道连接件需求更大。
因此,02S403钢制管件有望在未来的市场中得到更多的应用和推广。
综上所述,02S403钢制管件作为一种重要的管道连接件,在工业生产和建筑领域中具有广泛的应用。
管件生产总结

管件生产总结管件是一种常用的连接材料,在管道系统中起到连接和转换流体的作用。
为了确保管件的质量和生产效率,本文对管件生产进行了总结和梳理,以期对今后的生产工作有所指导和借鉴。
一、生产工艺流程管件生产工艺流程包括材料准备、成型加工、热处理、表面处理和质量检测等环节。
首先,材料准备是确保产品质量的基础,包括选材、切割和装料等工序。
成型加工阶段通过冷挤压、热挤压或锻造等方式将材料成型成管件的预形状。
热处理是为了改善材料的力学性能和组织结构,通过调控温度和时间来保证产品的性能稳定。
表面处理是为了提高管件的耐腐蚀性和装饰性,常见的处理方法有喷丸、镀锌和喷涂等。
最后,通过质量检测环节来评估产品的合格率,确保产品满足客户的需求。
二、生产过程中的问题与对策1.材料质量不稳定:管件生产所使用的原材料具有一定的特殊性,因此材料的质量稳定性对于产品的可靠性至关重要。
为了解决这个问题,我们需要与供应商建立长期合作关系,加强对原材料的质量控制,严格按照规范要求进行抽样检测和验收。
2.成型精度不高:由于管件形状和尺寸的要求较高,成型过程中的不合格率较高。
针对这个问题,我们需要引进先进的成型设备和工艺技术,并加强操作工人的培训,提高他们的技能水平。
同时,建立完善的质量管理体系,进行跟踪检测和及时调整。
3.热处理引起的变形:在热处理过程中,由于温度和冷却速度的不均匀性,容易导致管件变形。
为了避免这个问题,我们应该优化热处理工艺,控制好加热温度和冷却速度,避免过度变形。
同时,加强对热处理过程的监控和检测,及时调整工艺参数。
4.表面处理不合格:表面处理工艺的不合格会影响管件的耐腐蚀性和装饰性。
为了确保表面处理效果,我们需要严格按照工艺要求操作,并加强对操作工人的培训和指导,保证工艺的标准化和稳定性。
此外,加强质量检测环节,对表面处理效果进行抽查和评估。
三、生产管理与优化为了提高生产效率和产品质量,我们需要加强生产管理和优化流程。
首先,建立规范的生产作业指导书,明确每道工序的工艺要求和操作规范,提高生产工人的工作效率和准确性。
Al6063_管件外增量成形工艺研究

第15卷第12期精密成形工程2023年12月JOURNAL OF NETSHAPE FORMING ENGINEERING19 Al6063管件外增量成形工艺研究肖征宇,杨晨*(南京理工大学机械工程学院,南京 210094)摘要:目的研究6063铝合金管件外增量成形过程,分析管件的成形效果,改进管件成形质量。
方法设置3组目标成形管件,使用Abaqus软件进行成形过程的数值模拟,通过考察成形管件的几何精度、壁厚分布、表面质量、成形力,分析成形质量和可能出现的问题。
通过使用长120 mm、直径50 mm、壁厚1.5 mm的Al6063铝管进行管件外增量成形实验,验证数值模拟结果的可靠性。
结果成形管件会发生管端变形现象,具体表现为管端不圆与轴向伸长,成形件管端椭圆度为10.11%,管端变形程度与成形道次成正比,且在距离管端越近的成形区域,管端变形越明显。
管壁成形区厚度增大并呈现不均匀分布。
成形件管壁直线度偏差为0.34,且表面质量与径向进给量和轴向进给速度成反比,管件的圆角尺寸难以严格控制。
径向力是成形过程中主要的成形力,其大小与工具头直径成正比。
结论管件外增量成形原理可靠,基于此能够实现多种目标管件的成形。
由于成形原理的限制,成形件的成形质量还有很大的提升空间,合理制定工艺参数对提高成形质量十分重要。
关键词:外增量成形;管端变形;表面质量;数值模拟;管件成形DOI:10.3969/j.issn.1674-6457.2023.12.003中图分类号:TG376.9 文献标识码:A 文章编号:1674-6457(2023)12-0019-08External Incremental Forming Process of Al6063 Pipe FittingXIAO Zheng-yu, YANG Chen*(School of Mechanical Engineering, Nanjing University of Science and Technology, Nanjing 210094, China)ABSTRACT: The work aims to explore the external incremental forming process for 6063 aluminum alloy pipe fittings, ana-lyze the forming effects, and enhance the quality of the formed pipe fittings. Three sets of target fittings were selected, and nu-merical simulations of the forming process were conducted with Abaqus software. The geometric accuracy, surface quality, and forming forces of the formed pipe fittings were analyzed. Experimental research on incremental forming was carried out with AL6063 aluminum alloy pipe fittings with dimensions of 120 mm in length, 50 mm in diameter, and 1.5 mm in wall thickness.The simulation results were validated by physical experiments. The findings indicated that deformation occurred at the end of the formed pipe fittings, resulting in non-roundness and axial elongation. The pipe end ovality of the formed pipe fittings was10.11%. The extent of the end deformation increased proportionally with the number of forming passes, and the deformationwas more pronounced as the forming region approached the end of the fittings. The wall thickness in the forming region exhib-ited uneven distribution with an overall increase. The pipe wall straightness deviation of the formed pipe fittings was 0.34, and the surface quality was inversely proportional to the radial feed rate and axial feed velocity. It was difficult to control the fillet size of pipe fittings accurately. The main forming force during the process was the radial force, which was directly related to the收稿日期:2023-08-21Received:2023-08-21引文格式:肖征宇, 杨晨. Al6063管件外增量成形工艺研究[J]. 精密成形工程, 2023, 15(12): 19-26.XIAO Zheng-yu, YANG Chen. External Incremental Forming Process of Al6063 Pipe Fitting[J]. Journal of Netshape Forming Engineering, 2023, 15(12): 19-26.*通信作者(Corresponding author)20精密成形工程 2023年12月tool head diameter. In conclusion, the principle of external incremental forming for pipe fittings is reliable and can achieve the forming of various types of pipe fittings. Due to the limitations of the forming principle, there is still a lot of room for improvement in the forming quality of the parts. It is crucial to develop reasonable process parameters in order to improve the forming quality.KEY WORDS: external incremental forming; end deformation of pipes; surface quality; numerical simulation; pipe forming管类零件具有强度高、灵活性好、节省材料等优点,在当今社会的各行各业中都有着十分广泛的应用。
dn350及以下管件通用技术条件

DN350及以下管件通用技术条件1. 简介DN350及以下管件是指管道系统中直径小于等于350毫米的管件,其在工程项目中起着至关重要的作用。
本文将就DN350及以下管件的通用技术条件进行深入探讨,以帮助读者更好地理解和应用这一主题。
2. 材质选择在选择管件材质时,我们要考虑到管道系统所处的工作环境、介质特性以及使用要求。
常见的管件材质包括碳钢、不锈钢、合金钢等。
对于不同的工程项目,我们需要根据具体条件选择合适的材质,以保证管道系统的安全运行。
3. 制造工艺管件的制造工艺对其质量和性能有着重要影响。
常见的制造工艺包括锻造、铸造、冷热成型等。
在制造过程中,我们需要确保管件的尺寸精度、表面光洁度以及物理性能符合标准要求,以满足工程项目的需要。
4. 连接方式管道系统中,连接方式对系统的密封性和稳定性有着直接影响。
常见的连接方式包括焊接、螺纹连接、法兰连接等。
在选择连接方式时,我们需要综合考虑系统压力、介质特性以及安装维护的便利性,以选择合适的连接方式。
5. 检测标准在使用DN350及以下管件时,我们需要进行严格的检测以确保其质量符合要求。
常见的检测标准包括射线检测、超声波检测、磁粉检测等。
通过对管件进行全面的检测,我们可以及时发现和解决质量问题,确保管道系统的安全运行。
6. 个人观点在工程项目中,DN350及以下管件作为管道系统的重要组成部分,其质量和性能直接影响整个系统的安全稳定运行。
我们在选择、使用和维护管件时需要严格遵守相关标准和要求,确保管道系统的质量和安全可靠性。
通过本文的探讨,希望读者能对DN350及以下管件的通用技术条件有更深入的了解,为工程实践提供帮助。
7. 结语通过对DN350及以下管件的材质选择、制造工艺、连接方式和检测标准等方面进行深入探讨,我们可以更好地理解和应用这一主题。
在工程项目中,我们需要严格遵守相关标准和要求,确保管道系统的质量和安全可靠性。
希望本文能对读者有所帮助,期待更多关于管件通用技术条件的深入研究和探讨。
钢制管件标准

钢制管件标准钢制管件是一种常见的管道连接材料,广泛应用于各种工业领域。
为了确保管道系统的安全和稳定运行,钢制管件必须符合一定的标准和规范。
本文将介绍钢制管件的标准,包括材料、制造工艺、质量控制等方面的内容,帮助读者更好地了解钢制管件的相关知识。
首先,钢制管件的材料应符合国家标准,一般采用碳素钢、合金钢、不锈钢等材料。
这些材料具有良好的机械性能和耐腐蚀性能,能够满足不同工况下的使用要求。
在选择材料时,需要考虑管道的工作压力、工作温度、介质性质等因素,以确保管件的材料符合实际工程需求。
其次,钢制管件的制造工艺也是至关重要的。
常见的制造工艺包括锻造、铸造、焊接等,不同的工艺对管件的性能和质量有着直接影响。
例如,锻造工艺可以提高管件的密实性和力学性能,适用于高压、大口径的管道系统;而焊接工艺则可以实现管件的定制化生产,适用于特殊形状或特殊材料的管件制造。
此外,质量控制是保证钢制管件符合标准的关键。
在整个生产过程中,需要严格控制原材料的质量、加工工艺的精度和产品的检测手段,以确保管件的尺寸精度、表面光洁度、化学成分和力学性能等符合标准要求。
只有通过严格的质量控制,才能生产出安全可靠的钢制管件,保障管道系统的正常运行。
总的来说,钢制管件的标准涉及材料、制造工艺、质量控制等多个方面,需要综合考虑工程实际需求和国家标准要求。
只有选择合适的材料、采用合理的制造工艺,并严格控制产品质量,才能生产出符合标准的钢制管件,保障管道系统的安全运行。
希望通过本文的介绍,读者能够更加深入地了解钢制管件的标准,为工程实践提供参考和指导,确保管道系统的安全可靠运行。
钢制管件制造工艺标准规范
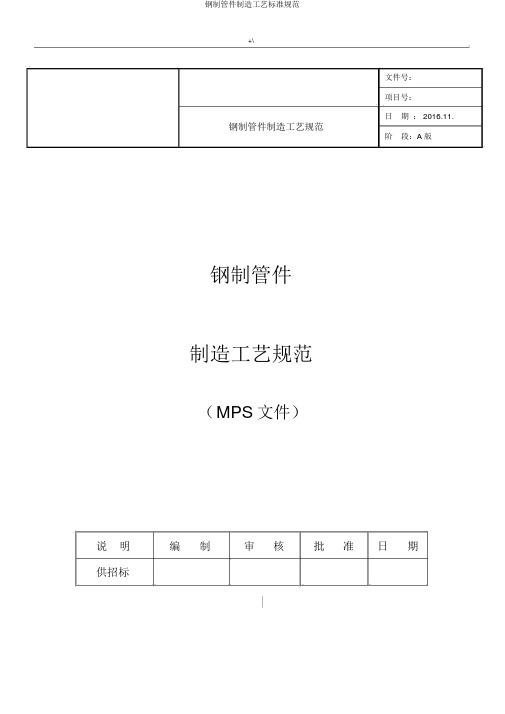
+\文件号:项目号:日期: 2016.11.钢制管件制造工艺规范阶段:A版钢制管件制造工艺规范(M PS文件)说明编制审核批准日期供招标+\目录1范⋯⋯⋯⋯⋯⋯⋯⋯⋯⋯⋯⋯⋯⋯⋯⋯⋯⋯⋯⋯⋯⋯⋯⋯⋯⋯⋯⋯⋯⋯⋯⋯⋯⋯⋯⋯⋯⋯⋯⋯⋯⋯⋯2 2范性引用文件⋯⋯⋯⋯⋯⋯⋯⋯⋯⋯⋯⋯⋯⋯⋯⋯⋯⋯⋯⋯⋯⋯⋯⋯⋯⋯⋯⋯⋯⋯⋯⋯⋯⋯⋯⋯⋯⋯2 3制造工流程⋯⋯⋯⋯⋯⋯⋯⋯⋯⋯⋯⋯⋯⋯⋯⋯⋯⋯⋯⋯⋯⋯⋯⋯⋯⋯⋯⋯⋯⋯⋯⋯⋯⋯⋯⋯⋯⋯⋯3 4管件基本参数⋯⋯⋯⋯⋯⋯⋯⋯⋯⋯⋯⋯⋯⋯⋯⋯⋯⋯⋯⋯⋯⋯⋯⋯⋯⋯⋯⋯⋯⋯⋯⋯⋯⋯⋯⋯⋯⋯⋯4 5原资料要求⋯⋯⋯⋯⋯⋯⋯⋯⋯⋯⋯⋯⋯⋯⋯⋯⋯⋯⋯⋯⋯⋯⋯⋯⋯⋯⋯⋯⋯⋯⋯⋯⋯⋯⋯⋯⋯⋯⋯⋯5 6制造工要求⋯⋯⋯⋯⋯⋯⋯⋯⋯⋯⋯⋯⋯⋯⋯⋯⋯⋯⋯⋯⋯⋯⋯⋯⋯⋯⋯⋯⋯⋯⋯⋯⋯⋯⋯⋯⋯⋯⋯6 7性能要求⋯⋯⋯⋯⋯⋯⋯⋯⋯⋯⋯⋯⋯⋯⋯⋯⋯⋯⋯⋯⋯⋯⋯⋯⋯⋯⋯⋯⋯⋯⋯⋯⋯⋯⋯⋯⋯⋯⋯⋯⋯15 8几何尺寸、形状允误差⋯⋯⋯⋯⋯⋯⋯⋯⋯⋯⋯⋯⋯⋯⋯⋯⋯⋯⋯⋯⋯⋯⋯⋯⋯⋯⋯⋯⋯⋯⋯⋯⋯⋯16 9工量和缺点理⋯⋯⋯⋯⋯⋯⋯⋯⋯⋯⋯⋯⋯⋯⋯⋯⋯⋯⋯⋯⋯⋯⋯⋯⋯⋯⋯⋯⋯⋯⋯⋯⋯⋯⋯⋯18 10和⋯⋯⋯⋯⋯⋯⋯⋯⋯⋯⋯⋯⋯⋯⋯⋯⋯⋯⋯⋯⋯⋯⋯⋯⋯⋯⋯⋯⋯⋯⋯⋯⋯⋯⋯⋯⋯⋯⋯⋯18 11⋯⋯⋯⋯⋯⋯⋯⋯⋯⋯⋯⋯⋯⋯⋯⋯⋯⋯⋯⋯⋯⋯⋯⋯⋯⋯⋯⋯⋯⋯⋯⋯⋯⋯⋯⋯⋯⋯⋯22 12志⋯⋯⋯⋯⋯⋯⋯⋯⋯⋯⋯⋯⋯⋯⋯⋯⋯⋯⋯⋯⋯⋯⋯⋯⋯⋯⋯⋯⋯⋯⋯⋯⋯⋯⋯⋯⋯⋯⋯⋯⋯⋯⋯24 13防与包装⋯⋯⋯⋯⋯⋯⋯⋯⋯⋯⋯⋯⋯⋯⋯⋯⋯⋯⋯⋯⋯⋯⋯⋯⋯⋯⋯⋯⋯⋯⋯⋯⋯⋯⋯⋯⋯⋯⋯⋯24 14品量合格明⋯⋯⋯⋯⋯⋯⋯⋯⋯⋯⋯⋯⋯⋯⋯⋯⋯⋯⋯⋯⋯⋯⋯⋯⋯⋯⋯⋯⋯⋯⋯⋯⋯⋯⋯⋯251范本文件定了山港化董家口港- 坊 - 中、北油管道工程管(一期)管件采目用L245N、L360M、L450M等材质钢制管件生产的基本参数、原资料、制造工艺、资料性能、几何尺寸与同意误差、工艺质量与缺点修理、查验与实验、标记、涂层与保护、质量证明书及装运的要求。
管件生产工艺流程

管件生产工艺流程管件生产是指以金属材料为主要原料,通过一系列的工艺加工和装配工作,制造出各种类型的管件产品。
管件是连接管道的重要组成部分,广泛应用于石油、化工、电力、造船、核能、航天等行业。
下面是管件生产的一般工艺流程:1.材料准备:选择适合的金属材料,通常是碳钢、不锈钢、合金钢等。
根据要求进行材料的切割、焊接等加工工作,并进行质量检验。
2.管料制作:按照设计要求,将材料切割为规定的长度,并进行尺寸修整和表面处理工作,如倒角、去毛刺等。
3.成型工艺:主要包括冷成型和热成型两种方式。
冷成型通常采用液压机等设备,将管材通过弯曲、膨胀等方式进行成型。
热成型则是通过高温加热和冷却的方式,使管材产生弯曲和收缩变形。
4.焊接工艺:将成型的管材进行焊接,主要包括手工焊接和自动焊接两种方式。
焊接时需要使焊缝达到要求的强度和密封性,并进行焊缝检测。
5.机械处理:包括铣削、车削、钻孔、螺纹加工等工序。
通过机械加工,将管件的各个部件进行加工,达到设计要求的尺寸和表面精度。
6.表面处理:根据需要对管件进行表面处理,通常包括酸洗、磷化、镀锌、喷涂等工艺,以防止管件腐蚀和提高其耐磨性。
7.装配工艺:将经过各项加工的管件进行组装,根据设计要求进行连接、固定和密封等工作,通常需要使用螺栓、螺母、垫圈等配件。
8.检测与质量控制:对成品管件进行各项检测,包括尺寸、外观、密封性能、强度等方面。
确保管件符合设计要求和相关标准,并进行质量控制记录。
9.包装与出厂:对检验合格的管件进行包装,根据运输方式选择合适的包装材料和方式,并标明相关的产品信息和技术参数。
对于高精度和重要管件,通常还需要提供相关的技术文件和证书。
以上是一般的管件生产工艺流程,具体的流程还会根据不同类型的管件和材料而有所变化。
随着科技的不断发展,管件生产工艺也在不断改进和完善,以提高产品的质量和性能。
- 1、下载文档前请自行甄别文档内容的完整性,平台不提供额外的编辑、内容补充、找答案等附加服务。
- 2、"仅部分预览"的文档,不可在线预览部分如存在完整性等问题,可反馈申请退款(可完整预览的文档不适用该条件!)。
- 3、如文档侵犯您的权益,请联系客服反馈,我们会尽快为您处理(人工客服工作时间:9:00-18:30)。
合金管件制造工艺说明
一、制造工艺说明
1.合金管件制造工艺流程
注:Ⅰ、Ⅱ、Ⅲ、Ⅳ、Ⅴ、Ⅵ、Ⅶ为控制环节
A、B、C、D、E、F、G、H、I为控制点
1、2、3、4、5、6、7、8、9、10、11、12、13、14为工序号
2、过程控制
2.1材料复检
2.1.1我公司拥有多台材料及成品检测用专业检测设备,对于新进厂的材料依据相应标准进行以下复检。
1)光谱仪进行材料光谱分析;
2)测厚仪测量管材、板材壁厚;
3)卡尺和盒尺测量管材的外径及端口圆度偏差;
4)目测管材(逐件进行)的外观无凹坑、裂纹、结疤、重皮、应光滑无氧化皮等缺陷;外观应符合有关标准的要求:检查其是否存在波浪度、皱纹、缩孔、
夹渣、粘砂、折叠、漏焊、重皮、腐蚀、尖锐划痕、凹坑(不得超过1.5mm)、凹陷(不得超过管子周长的5%且不大于40mm)等缺陷。
5)每炉批号抽检一件万能材料试验机进行力学性能复检;
6)每炉批号抽检一件用快速分析检测材料化学成分;
7)根据标准要求对所有来料原材料进行100% UT无损探伤,以确保原材料无裂纹、无夹层。
8)逐件进行硬度检测:任何一点的硬度应符合相应标准要求。
9)所有材料的检验结果应与原材料的质量证明书相对应;无标记、无批号、无质量证明书或质量证明书项目不全的材料不能使用。
2.1.2材料经检测部门检验合格后开具检验合格通知单允许转入下道工序,并填写材料复检记录。
(详见高压管件理化检验控制图、压力管件材料管理质量控制图)
2.2切割下料
2.2.1材料下料切割前首先由技术部门根据产品成形后外形尺寸和加工方式,考虑管件在生产过程中出现的减薄、变形、各种加工损耗等诸多因素选择有足够余量的材料。
必要时制作样板,生产部门按样板要求的尺寸下料。
2.2.2按设计要求在切割下料时对原材料的外径、壁厚、材质、管号、炉批号及管件坯料流水编号等内容做好标识移植,标识采用低应力钢印和油漆喷涂的方式,并在生产作业工序流程卡上记录操作内容。
以保证材料在加工过程中的可追溯性。
2.2.3首件下料后,操作人员进行自检,并报检测中心专检人员进行专检,检验合格后再进行其它件的下料,且每件都进行检测和记录。
对于下料不合格的产品填写不合格通知单,在通过技术部门论证后再决定材料能否进行加工,否则应将材料报废。
2.3成型
5.3.1.管件和的压制成型工艺过程是重要的过程,
5.3.2.清理胎具内杂物,检查电路、油路、台车是否正常;油料是否充足,电路是否完好;
5.3.3.成型过程中严格控制成型速度及压力机采用多次挤压成型的加工工艺。
2.4 焊接
2.4.1 对于钢板制对焊管件,焊接工作均由有多年焊接经验的专业焊工进行焊接,拼根据要求做合适的焊接工艺评定,对焊缝进行力学性能试验,在严格的工艺规程指导下进行焊接生产。
焊接过程采用合格的焊接工艺评定,此工艺评定应符合NB/T47014-2011等相关标准的规定,焊工也按此标准考核为合格的焊工。
在焊接过程中焊工施焊的项目与其考试合格的项目不符,不能进行焊接。
在焊接过程中制质量保证工程师对焊接工序的停止点和见证点进行规定监控和测量,保证焊接这一关键过程不出现任何缺陷和问题。
2.4.2 焊接过程严格按公司制订的《焊接工艺指导卡》进行。
首先根据焊条质量证明书的说明对焊条进行烘干,烘干后的焊条放在保温箱中待用。
采用氩弧焊打底手弧焊填充和盖面,打底时管道内部充氩保护,以防过热氧化。
焊接过程控制层间温度低于200℃。
焊接时注意层道间的搭接处用铁锤或砂轮打磨,并清理焊渣和飞溅。
2.4.3 施焊时不允许用碳钢材质作为地线搭铁,应将地线搭铁紧固在工件上,禁止点焊紧固。
钢板圈圆时,卷板机应用无铁离子的材料覆盖扎辊表面。
组装过程中不得使用可能造成铁离子污染的工具。
进行酸洗钝化时,应尽量避免对碳钢部件的酸洗,无法避免时,碳钢部件必须预先做好保护措施。
2.4.4 对于焊制管件应进行焊后热处理,保证焊接接头具有同母材相近的力学性能和其它技术指标。
2.4.5焊制管件的焊缝必须进行100%射线检测,并向贵方提供射线探伤报告。
(详见焊接质量控制流程图)
2.5热处理工艺
2.5.1热处理
A、管件需要按照标准的规定做正火+回火热处理。
有记录曲线和热处理报告并做为交工资料的一部分存入产品档案。
2.5.2 对于合金管件半成品,严格按照相关标准中规定的热处理制度进行热处理。
2.5.3 热处理前首先保证热处理炉炉膛清洁干净,炉内无油、灰、锈及与处理材料不同的其它金属。
2.5.4所有经热处理的管件应逐件进行硬度检测,并提供相应硬度报告。
2.5.5工件在炉内摆放要均匀,全部放在有效加热区内,最小间隔不得小于200mm。
2.5.6加热设备为4m*20m*2.5m燃气炉。
每炉均应放置随炉试件。
2.5.7准备工作:认真检查设备、导线、热电偶等,确认设备正常,连接可靠后,方可开机。
2.5.8温差控制:每炉次应力求各管道内外壁温度均匀,恒温时在加热范围内任意两测点间的温差应低于50℃。
2.5.9测温点布置:热电偶的安装位置,应以保证测温准确可靠、有代表性的原则。
水平管道,测温点应上下对称布置;分区控温时,热电偶的布置应和加热装置相适应。
2.5.10测温要求:热处理的测温必须准确可靠,应采用自动温度记录。
所用仪表、热电偶及其附件,应根据计量的要求进行标定和校验。
2.5.11测温方式:热电偶、红外测温仪。
2.5.12记录方式:温度记录表和热处理曲线
焊缝热处理:采用履带加热片加热的热处理方式。
所有经热处理的管件应逐件进行硬度检测,并提供相应硬度报告。
(详见热处理质量保证体系图)
2.6机加工及坡口加工
管件的坡口加工采用机械切削方式进行,我公司拥有各种车床、动力头等机加工设备20余台,可根据订单规定的相关标准及买方要求加工各种厚壁管个采用的双V型或单V型坡口及内坡口和外坡口,我公司可完全按照标准及技术要求进行坡口机加工,保证管件在焊接过程中便于操作和焊接。
2.7表面处理
2.7.1碳钢及合金管件内外表面在机加工完成以后用喷砂机对管件的内外表面时行喷砂除锈处理,经喷砂和打磨后的管件内外表面光滑呈现出金属光泽,管件不允许锈蚀、氧化皮、重皮等不良缺陷存在。
2.8成品管件检测
2.8.1所有管件均应进行外观检查。
外观检查应逐件进行,并符合以下要求。
对不浸入最小壁厚的结疤、裂纹、折叠、夹渣等缺陷,允许研磨清除,消除缺陷后剩余壁厚不得小于壁厚。
否则,该管件应予以报废。
2.8.2对于管件在出厂前按订货要求所对应的标准要求或买方指定要求进行各种检测,各种检测均由国家技术监督局认可的具有相应资质的专业人员完成。
2.8.3管件成品进行以下检测
1)所有管件均应按指定相关标准要求做几何尺寸检测。
检测项目允许的偏差符合相关标准。
2)所有碳钢及合金管件,应逐件进行100%MT检验,对于MT检测出的深度不大于0.8mm的微裂纹,允许研磨清除。
否则,该管件予以报废。
3)所有管件的焊接坡口,均应进行100%MT或100%PT检验,检验执行
JB/T4730-2005。