电池线碎片分析
电池片碎片改善方案及措施

电池片碎片改善方案及措施引言随着电子产品的普及和需求的增长,电池的重要性不言而喻。
然而,电池片的碎片化问题依然困扰着人们。
碎片化问题不仅影响了电池的寿命和性能,还给环境带来了一定的压力。
针对电池片碎片化问题,本文将提出一些改善方案及措施,以期能够解决这一问题。
分析现状电池片碎片化主要体现在以下几个方面:1. 技术碎片化不同类型的电子设备使用的电池片种类繁多,技术水平不一。
比如锂电池、镍氢电池、铅酸电池等,每种电池都有自己独特的特点和适用场景,因而电池制造商需要根据不同的需求开发不同类型的电池片。
这种技术碎片化导致了电池片研发和生产的成本增加。
2. 尺寸碎片化不同电子设备对电池片的尺寸要求各异,尺寸碎片化是电池片碎片化的体现之一。
由于电子设备的尺寸多样化,电池片生产商需要根据不同尺寸的需求进行生产,这对电池片生产厂商来说是一种挑战。
3. 容量碎片化电子设备对电池容量的要求也各不相同,容量碎片化是电池片碎片化的另一方面。
容量碎片化导致了电池生产商需要生产不同容量的电池片,这在一定程度上增加了电池片生产的难度和成本。
4. 损耗碎片化电池片在使用过程中会出现不同程度的损耗,这导致了电池片的性能下降。
损耗碎片化不仅降低了电池片的使用寿命,还容易导致电池的性能不稳定。
改善方案及措施为了解决电池片碎片化问题,需要从技术、尺寸、容量和损耗几个方面进行改善。
技术方面1. 加强标准化:制定通用的电池片技术标准,使得不同类型的电子设备可以使用相同规格的电池片。
2. 提高研发水平:加大对电池片研发的投入,提升电池片的技术水平,降低生产成本。
3. 推广成熟技术:在电池片生产中更多采用成熟技术,避免为了应对特定需求而开发新的技术,降低技术碎片化的问题。
尺寸方面1. 统一尺寸标准:在电子设备的设计中尽量采用统一的尺寸标准,减少尺寸碎片化的问题。
2. 加强市场调研:从市场需求出发,准确把握不同尺寸的需求,以满足不同用户的要求。
光伏组件检验不良类别及实例图解.

品保部 李廷
序号Biblioteka 项目分 类实例图1实例图2
不良描述
碎片
EL不良(碎片)
EL工 序
隐裂
EL不良(隐裂)
低效片
EL不良(低效片 )
工序
不良类别
实例图1
实例图2
不良描述
断栅
EL不良(断栅)
EL工 序
黑芯片
EL不良(黑芯片)
电池片污 染(硅片 )
EL不良(污染)
工序
不良类别
外 观 检 查 工 序
电池片污 渍
外观不良(电池片 污渍)
崩边/缺 角
外观不良(崩边) 外观不良(缺角)
可视碎片
外观不良(可视碎片 )
外 观 检 查 工 序
间距不良
间距不良(过大) 间距不良(过小) 并片
整体偏移
四边等距偏差控 制在3mm之内,且 在1m处目视不明 显。
异物(锡 丝、锡渣 、焊带残 留)
层压气泡
层压不良(气泡)
脱层
层压不良(脱层)
外 观 检 查 工 序
背板凹坑
层压不良(背板凹 坑)
背板移位
层压不良(背板移 位)
焊带未剪
外观不良(焊带头 未剪)
外 观 检 查 工 序
母线偏移
母线偏移(外露)
焊带偏移 (露白)
焊带偏移 露白
型材不良(边角错 位) 型材不良(边角缝 隙过大)
外 观 检 查 工 序
型材不良
型材不良(角码松 动) 型材不良(边框划 伤)
型材不良(边框损 伤)
型材不良
型材不良(边框损伤 ) 型材不良(边角不良 )
外 观 检 查 工 序
组件隐裂定义及抽样方法
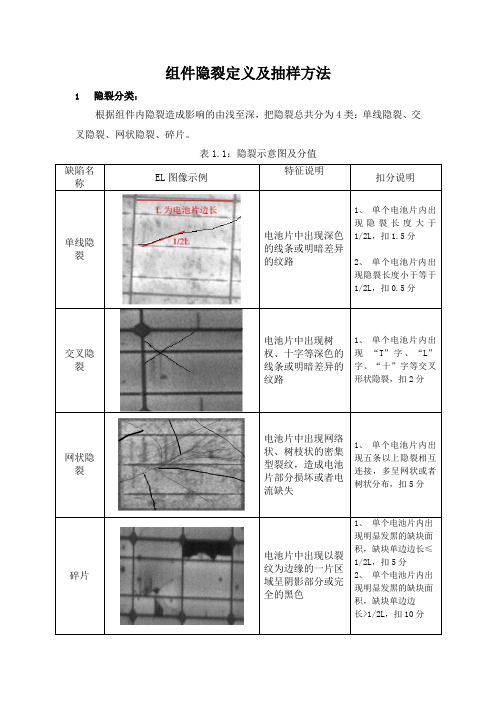
组件隐裂定义及抽样方法1隐裂分类:根据组件内隐裂造成影响的由浅至深,把隐裂总共分为4类:单线隐裂、交叉隐裂、网状隐裂、碎片。
表1.1:隐裂示意图及分值缺陷名称EL 图像示例特征说明扣分说明单线隐裂电池片中出现深色的线条或明暗差异的纹路1、 单个电池片内出现隐裂长度大于1/2L ,扣1.5分2、 单个电池片内出现隐裂长度小于等于1/2L ,扣0.5分交叉隐裂电池片中出现树杈、十字等深色的线条或明暗差异的纹路 1、 单个电池片内出现 “T ”字、“L”字、“十”字等交叉形状隐裂,扣2分网状隐裂电池片中出现网络状、树枝状的密集型裂纹,造成电池片部分损坏或者电流缺失 1、 单个电池片内出现五条以上隐裂相互连接,多呈网状或者树状分布,扣5分碎片电池片中出现以裂纹为边缘的一片区域呈阴影部分或完全的黑色 1、 单个电池片内出现明显发黑的缺块面积,缺块单边边长≤1/2L ,扣5分2、 单个电池片内出现明显发黑的缺块面积,缺块单边边长>1/2L ,扣10分2隐裂评分说明及合格标准:2.1 组件隐裂合格判定标准实行评分制,无任何隐裂的组件满分100分,隐裂特别严重的组件最低可扣至0分。
2.2 单个电池片中同时出现多种类型隐裂,按最严重的一项进行扣分。
2.3 到货后组件得分99-100分视为组件合格,99分以下记为组件隐裂一片。
2.4 安装后组件得分96-100分视为组件合格,96分以下记为组件隐裂一片。
3抽样方案及接收水平:3.1 组件到货后检验,组织相关方进行到货检验,抽样方案按照《计数抽样检验程序》- GB/T 2828.1-2012内要求的程序进行,如果不可接受样品在限值内,可以认为本批货物符合要求,并单独更换不可接受的组件。
3.1组件安装后检验,组织相关方进安装检验,抽样方案按照《计数抽样检验程序》- GB/T 2828.1-2012内要求的程序进行,如果不可接受样品在限值内,可以认为本方阵或电站符合要求,并单独更换不可接受的组件。
电池测试生产日报表
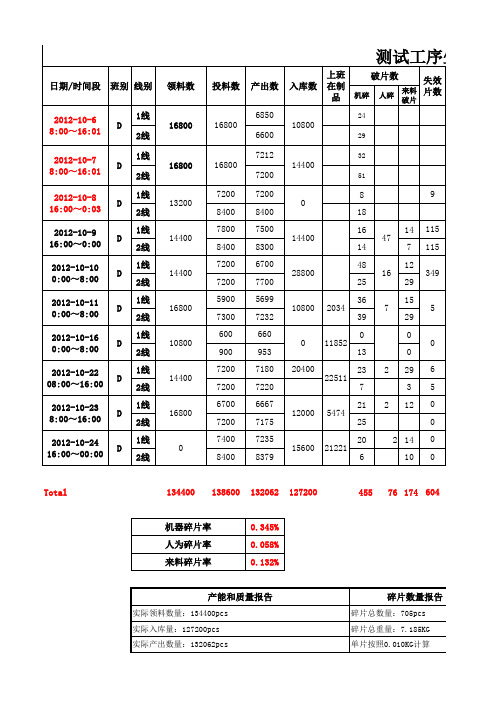
领料数
投料数
产出数 6850ቤተ መጻሕፍቲ ባይዱ
入库数
上班 在制 品
破片数
机碎 24 来料 人碎 破片
失效 片数
2012-10-6 8:00~16:01 2012-10-7 8:00~16:01 2012-10-8 16:00~0:03 2012-10-9 16:00~0:00 2012-10-10 0:00~8:00 2012-10-11 0:00~8:00 2012-10-16 0:00~8:00 2012-10-22 08:00~16:00 2012-10-23 8:00~16:00 2012-10-24 16:00~00:00
实际领料数量:134400pcs 实际入库量:127200pcs 实际产出数量:132062pcs
碎片数量报告
碎片总数量:705pcs 碎片总重量:7.185KG 单片按照0.010KG计算
Q2外观不良:64pcs 缺角片:149pcs 10/26号转给B班统一入库:5406pcs 碎片总数:705pcs
管理员确认
郭焕宾
郭焕宾
郭焕宾
郭焕宾
郭焕宾
10800
29 32
8 18 16 14 48 25 2034 36 39 0 13 23 7 21 25 20 6 2 14 10 2 2 47 14 7 12 29 15 29 0 0 29 3 12
9
D
14400
14400
115 115 349
D
14400
28800
16
D
16800
10800
7
1200
6000
3600
2400
8400
3600
电池片碎片或隐裂分析及改善措施

电池片碎片或隐裂分析及改善措施
一、电池片碎片或隐裂分析
1、焊接
2、敷设
二、碎片或隐裂改善措施
1、焊接
①、在互检过程中要加强警惕性;
②、员工在进行电池片作业时要做到“一轻二柔三无声”,轻拿轻放,动作柔和,作业过程中无电池片引起的声音;
③、烙铁头温度要进行有效控制,不能过高或者过低,最好3~4小时检查一次;
④、返修电池片时尽量要在加热台上进行,减少受热应力影响照成的碎片。
2、敷设
①、拧串时手捏在主栅线的焊带上而不是电池片的边沿上,且用力要适度;
②、在互检时认真检查异物,并防止异物掉落到EVA上,在焊接汇流条前必须认真检查异物
本帖隐藏的内容。
电池碎片原因

主题:电池碎片1.焊接电池片尾部时操作不正确2.铝苞片太多,拿取时容易导致裂片3.手工焊人为接在电池片盛放盒上4.缺边缺角没有检查出来,经焊接报废5.电烙铁温度过高6.互联条太厚,片子太薄7.电池串运载车最上层太窄,承载盒易搭起来8.新承载盒下面的垫板易卡住,电池串移位9.弯曲片导致互联条变形10.新员工焊接质量较差,经常需要返工11.层叠人员排串前两手夹片用力不均匀12.员工心理作用(负担较大)13.层叠,层压前检验的手势不正确14.层叠员工未及时发现裂纹片而流入下道工序15.电池串背电场上的锡堆太高16.背面虚焊17.手工焊互联条扭曲18.层压员工抬组件手势不当搬运的次数太多手指捏住铝苞片易碎19.手工焊正面员工的操作方法不统计20.互联条太干,导致电烙铁来回焊接温度过高,电池报废21.返工在观察架上返工22.检查人员返工(混乱)23.电池片尾部互联条弯曲24.盖层压布时操作不当25.层叠人员剪互连条电池片震动导致裂片26.电池串承载盒长度太短27.抬组件时,组件上TPT有可能碰到员工衣服28.翻串模板翻两遍后会出现裂纹片29.焊好的正面堆的太高30.正面虚焊,返工时造成裂纹31.层叠员工粘胶带用力过度32.承载盒撞到档块33.反面人员拎串时,两只手用力不一样34.返工时流程卡粘在电池片上35.返工撕胶带纸的时候36.分片,手工焊各工序缺少检查37.手工焊桌面5S较差(助焊剂的结晶)38.手工焊残余锡渣未及时清理39.扭曲的互联条焊在电池片上40.操作不小心,剪刀易砸碎电池片41.叠台放烙铁的夹具不固定42.翻EV A时将电池片刮碎43.员工检查电池片在翻转过程中受力44.铺TPT时,TPT成螺旋状,边角将电池片串带起来45.放EV A时,如果速度过快,会将两边的电池串掀起来46.层叠剪刀不锋利,拉动整个组件47.层叠出头有毛刺48.正面焊接有毛刺49.直接用手拿取多片电池,不使用泡沫垫50.员工直接用手将电池串直接拿至手工焊51.运输电池承放的方法不当52.使用翻串模板,桌面太紧,易撞53.承载盒用酒精洗过后,电池片粘在上面54.由于散包装比较多,拿取多包时,易捏碎55.原包装碎片(未发现)56.日光灯灯架易撞到57.承载盒内电池串排放不整齐58.拿小组件时,角度太斜,滑落59.电池串运送车靠的太近60.在制品太多时,电池串易叠起来61.拿串一个人拿比较危险62.生产线人流物流控制不到位63.反面翻电池片时未将电池片理齐。
组件前道降低电池片碎片率的方法

组件前道降低电池片碎片率的方法电池片的碎片率对于光伏组件的性能和寿命具有重要影响。
组件前道的质量控制和处理是降低电池片碎片率的有效手段。
以下是10条关于组件前道降低电池片碎片率的方法:1. 挑选较为均匀的硅片:电池片的碎片率与硅片质量、厚度、表面性质有关。
挑选硅片时需要选择表面平整度好、厚度均匀的硅片,并控制硅片厚度偏差在±20um以内。
2. 设计合理的切割工艺:切割过程可能会导致电池片断裂或受损,因此需要设计合理的切割工艺,确保硅片不会产生裂纹或割伤。
3. 控制切割时的力度:控制切割时的力度能够减少电池片的碎片率。
在切割幅度和频率相同的情况下,降低切割压力可使碎片率降低。
4. 防止硅片表面受污染:硅片表面的污染会对电池片性能产生影响,导致碎片率提高。
因此需要在组件前道时防止硅片表面受到污染。
5. 切割前清洁硅片表面:清洁硅片表面可以有效降低电池片碎片率。
使用合适的清洗工艺可以去除硅片表面的污染和松散物,确保切割时硅片不受损害。
6. 优化加工工艺:优化加工工艺可以提高组件前道的生产效率和稳定性。
采用合适的加工工艺,能够减少电池片的碎片率并保证组件性能。
7. 精细化管理生产环节:严格管理每个生产环节,确保每个加工工艺都符合要求,可有效降低电池片的碎片率和组件的缺陷率。
8. 采用高精度设备:采用高精度设备可以提高生产效率和稳定性,同时可以减少碎片率和缺陷率。
比如使用高精度的切割机、光刻机等设备。
9. 加强人员培训:组件前道操作人员的技能和经验对于电池片碎片率和组件性能具有重要影响。
加强人员培训,提高操作技能,能够减少电池片的碎片率和缺陷率。
10. 引进先进技术:引进先进的技术可以提高生产效率和组件性能,同时可以减少电池片的碎片率。
比如使用高效的太阳能电池切割机、晶圆清洗机、显微镜等。
以上是关于组件前道降低电池片碎片率的10条方法。
对于每一个方法,都需要详细地制定操作流程和质量标准,严格按照标准执行,以降低电池片的碎片率和组件的缺陷率。
电池线碎片分析

电池片碎片分析报告随着光伏市场逐渐回暖,公司的发展又迎来了新一轮的机遇,碎片率作为太阳能电池生产的一项重要指标对生产成本起着举足轻重的作用,因此控制好碎片率实际上也是在为公司追求更多的利润。
晶体断裂:碎片其实就是晶体断裂,晶体的断裂是指晶体在应力作用下应变大于其临界断裂应变时发生的结构上的解离。
从微观角度讲,即是在应力的作用下,晶体内部的原子偏离了平衡位置且超出了原子间结合力的范围,晶格发生了断裂。
硅材料为典型的金刚石型晶体结构,各原子间通过共价键结合,是典型的脆性材料,易发生脆断。
在单晶硅的生长过程中可能会由于尺寸大,原料纯度不高,生长工艺条件不合理等原因,而具有较大的内应力,甚至局部已突破断裂应变产生了微型隐裂。
晶体的内应力越大,就越容易在较小的冲击力作用下发生解理断裂。
下面就我司碎片情况做具体分析,下图是5月份我司采购的不同厂商的硅片制作电池片所产生的碎片统计图:图1 一线不同片源碎片情况统计(来源:生产日报表,下同)从图1可以看出单晶硅片中芯能的碎片率较其他厂商的碎片率有明显偏高,做了五批芯能的片子,平均碎片率为%,而昱辉、晟纳吉、金太阳、双鸽各只做了一批,明显比芯能的碎片率低。
图2 二线不同片源碎片情况统计从图2可以看出多晶片中金太阳做的很多,一共七批,平均碎片率为%,而雷迪做了四批,平均碎片率为%,山晟仅做了一批不具代表性暂不考虑。
通过一、二线不同片源的碎片率对比可以发现,片源对电池片生产过程中产生的碎片有很大的影响,其影响主要体现在硅片厚度、尺寸、崩边、线痕、隐裂等方面。
硅片厚度的影响不言而喻,比较薄的片子在人为操作,设备运行过程中所能承受的机械力会更小,发生碎片的几率更大;而厚薄不均的片子,会在等离子体刻蚀和印刷工序产生更多的碎片,在刻蚀前夹紧片子的时候由于片子厚薄不均,在拧紧夹具时可能由于某一边比另一边薄而拧得更紧造成碎片,而在印刷工序,厚薄不均的片子很容易造成印刷碎片,或者是由于厚薄不均导致烧结翘曲度比较大而产生更多的碎片。
太阳能电池片丝网印刷常见问题解决方法

太阳能电池片丝网印刷常见问题解决方法
1.印刷速度对印刷效果的影响?印刷速度提高,会使浆料对网孔的填充效果变差。
使印刷的平整性变差,容易造成葫芦状栅线。
在一定范围内,印刷速度提高,可以使栅线高度上升,宽度变小。
2.浆料黏度对印刷效果的影响?浆料的黏度如果太小,会导致印刷的图形易扩大。
产生气泡,毛边;浆料的黏度如果太大,会导致透墨性差,会产生橘皮,小孔。
在许可范围内,浆料的黏度越小越好。
3.压力与间距的关系?压力越大,间距越大。
因为压力大时,刮刀与网版接触的地方凸出来的也越多。
间距小的话,硅片承受的压力会变大,容易造成碎片。
两个参数不能单独改变,否则会影响印刷质量和增大碎片率。
4.烧结过程中,各温区的作用?室温~300℃:溶剂的挥发。
300℃~500℃,有机树脂排出,需要氧气。
400℃以上,玻璃软化。
600℃以上,玻璃与减反层反应,实现导电。
5.出现铝珠怎么办?如果是印刷过厚,就调整参数,降低板间距,提高印刷压力;如果是绒面过大,提醒制绒改善工艺;如果是浆料不匹配,就改善浆料。
12。
电池片检验标准

不允许
3
背电场粘结碎片
不允许
不允许
4
电极脱落
脱落面积≤3mm,≤1处
脱落面积≤3mm,≤1处
5
鼓包
鼓包高度≤0.2mm,单个鼓包面积≤10mm2累计鼓包面积≤20mm2
鼓包高度≤0.2mm,单个鼓包面积≤10mm2累计鼓包面积≤20mm2
6
铝浆脱落
脱落面积≤50 mm2
脱落面积≤50 mm2
7
缺角:宽≤3mm,深≤1mm,一片电池片≤1处。崩边:无穿透崩边一片电池片≤5处
9
色差
2m看无明显色差
2m看无明显色差
10
花斑
长≤5mm,宽≤2 mm,2m看无明显花斑
长≤5mm,宽≤2 mm,2m看无明显花斑
11
细栅线
断栅
长≤3mm,一片电池片≤3处,一条细栅线≤1处断栅,允许≤3根平行断栅
长≤3mm,一片电池片≤5处,一条细栅线≤1处断栅,允许≤5根平行断栅
12
划伤
宽≤0.5mm,划伤长度≤20mm,允许1条
宽≤0.5mm,划伤长度≤20mm,允许1条
13
正面漏浆(白点)
单个面积≤1 mm2,一片电池片上≤3个,不允许有小白点密集出现
单个面积≤1 mm2,一片电池片上≤5个,不允许有小白点密集出现
14
水纹印
水纹印面积≤10%
水纹印面积≤10%
15
印刷偏移
序号
项目
A级检验标准
B级检验标准
电池片正面
1
破片、隐裂
不允许
不允许
2
栅线氧化
不允许
不允许
3
针孔
不允许
180 μm电池焊接工艺及降低碎片率的研究

鳝遵姐..180I JL m电池焊接工艺及降低碎片率的研究张磊郎芳(保定天威英利新能源有限公司,河北保定071051)?:。
?。
4。
??。
j。
r。
1:。
j??j j j。
J。
j1。
‘?j j+!j。
j÷。
j j”j…?j÷j j。
i荫要1光侠发电是目前技术最为成熟的太阳能利用技术,目前正在向大型并网发电方向发展。
光欣发电要实埂飙摸化发展,必须大幅降。
?:,低光I佚发电成奉,做到基本平价入网。
本论文从太阳能电池细件封蓑的关键环节焊接进行内部挖潜,适应薄片自动焊接,提升内在品质,,’:降低碎片率,最终达至8低成本高品质的鼬挂_和】造。
:9籀枣词1多晶硅电池;焊接;碎片率;180pm/。
1引言为了降低光伏制造成本,为了保证良好的收益和组件可靠性,我们将电池厚度降低到180微米。
随之带来的是工艺、材料、设备必须适应薄片生产,保证产量和组件质量的可靠性。
我们通过对自动焊接设备和材料的优化,在薄片基础E提升焊接质量,隔氏碎片率。
2实验原理及改进方案2-1焊接原理钎焊是一种物理和化学连接。
它是在低于构件熔点的温度下,采用填缝材料,在液态下充填缝隙,通过毛细作用及表面化学反应,待填缝材料结晶或固化后,将两个分离的表面连接形成不可拆接头。
软钎焊为钎料熔点为45a℃以下,接头强度较低,一般不超过70M Pa,用于钎焊受力不大、工作温度较低的工件。
常用钎料是锡铅合金。
钎焊过程需要使用钎剂,作用是:清除被埠金属表面的氧化膜及杂质,改善钎料流八间隙的性能,保护钎料及焊件不被窜化。
电池的自动串焊即采用软钎焊,将铜基材焊带与硅基材电池,给予两种材料一定的压力及温度,使锡铅银合金短时间融化,将处于固态的焊带与电池栅线焊接起来。
22焊接材料太阳能电池:采用掺杂硼原子的180微米超薄多晶硅片,通过表面清洗、制绒、扩散制备P N结、气相沉积氮化硅减反射膜、印刷正背场电极、烧结成型。
电池正面覆盖银栅线,通过光生伏特效应,收集内部电子,通过导体输出电能。
锂离子电池负极极板花斑的刨析.
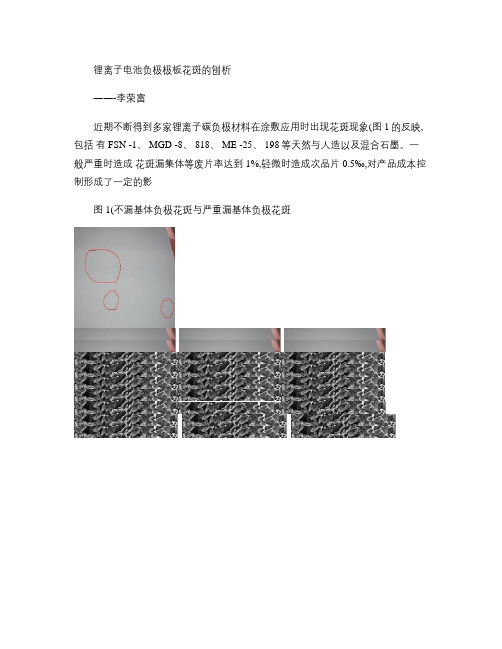
锂离子电池负极极板花斑的刨析――-李荣富近期不断得到多家锂离子碳负极材料在涂敷应用时出现花斑现象(图 1的反映,包括有 FSN -1、 MGD -8、 818、 ME -25、 198等天然与人造以及混合石墨。
一般严重时造成花斑漏集体等废片率达到 1%,轻微时造成次品片0.5‰,对产品成本控制形成了一定的影图 1(不漏基体负极花斑与严重漏基体负极花斑图 2花斑中心处 (漏基体花斑边缘正常处二、能谱扫描分析由于花斑经过扫描电镜分析 , 未在材料方面发现原因 , 我们对同一块样品又进行了 X 射线能谱分析 (EDS 分析元素组成及其相对含量 , 判定是否是由于粘合剂没有打开而造成花斑,花斑中心处 (漏基体位置能谱扫描 , 扫描出来有铜离子 8.92%重量比外 , 其他全部是碳, 没有发现有其他元素谱峰出现。
其他两个能谱扫描位置 , 由于负极材料覆盖的比较致密 , 扫描谱线中未发现铜离子出现, 同样也未发现其他元素峰出现。
虽然采用能谱进行元素定量分析误差较大, 但我们应该在图谱上观察到其他元素杂峰。
三个图谱均未发现除铜以外的其他元素。
因此判定与粘合剂未分散均匀或者粘合剂在浆料中团聚无关。
具体数据见下列 :能谱元素扫描数据1、花斑中心处 (漏基体2、花斑边缘3、正常处三、其他分析通过电镜图片以及能谱分析 ,花斑形成的原因应该与材料微粉、导电剂团聚以及粘合剂未打开关系不大。
为了查找问题根源 , 我们在电池制造公司的负极涂敷车间连续观察拉浆机上浆工序 ,在上浆滚与基带接触处不断有汽泡出现,出现的气泡随着移动的浆液一同涂敷, 入炉前基带表面的浆液的气泡不断破裂 (图 3标示处 ,微小的气泡没有在烘干后的极板上留下痕迹 , 但过大的气泡破裂后形成了圆形的痕迹 , 经烘干后出现了花斑(图 4标示处。
图 3 图 4表面有众多的微孔与间隙 , 由于水表面的张力 , 我们在搅拌桨料过程中 ,水受外力影响不断湿润者进入到这些微孔与间隙中 ,不断将这些部位的气泡赶出, 这就是我们采用真空搅拌浆料气泡大量减少的缘故。
废旧电池破碎和物理筛选
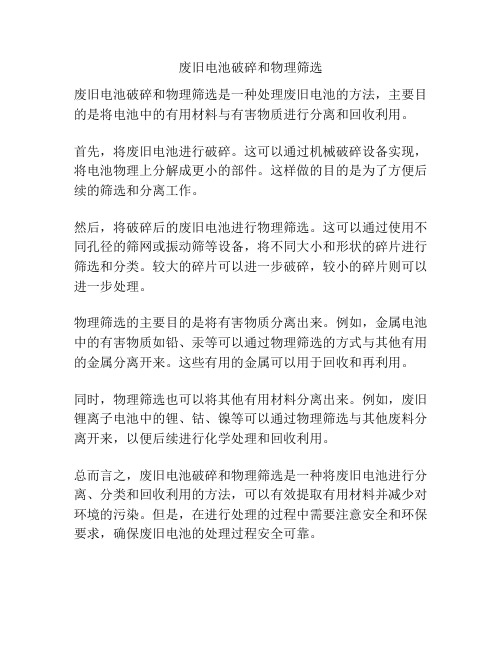
废旧电池破碎和物理筛选
废旧电池破碎和物理筛选是一种处理废旧电池的方法,主要目的是将电池中的有用材料与有害物质进行分离和回收利用。
首先,将废旧电池进行破碎。
这可以通过机械破碎设备实现,将电池物理上分解成更小的部件。
这样做的目的是为了方便后续的筛选和分离工作。
然后,将破碎后的废旧电池进行物理筛选。
这可以通过使用不同孔径的筛网或振动筛等设备,将不同大小和形状的碎片进行筛选和分类。
较大的碎片可以进一步破碎,较小的碎片则可以进一步处理。
物理筛选的主要目的是将有害物质分离出来。
例如,金属电池中的有害物质如铅、汞等可以通过物理筛选的方式与其他有用的金属分离开来。
这些有用的金属可以用于回收和再利用。
同时,物理筛选也可以将其他有用材料分离出来。
例如,废旧锂离子电池中的锂、钴、镍等可以通过物理筛选与其他废料分离开来,以便后续进行化学处理和回收利用。
总而言之,废旧电池破碎和物理筛选是一种将废旧电池进行分离、分类和回收利用的方法,可以有效提取有用材料并减少对环境的污染。
但是,在进行处理的过程中需要注意安全和环保要求,确保废旧电池的处理过程安全可靠。
电池片碎片或隐裂分析及改善措施

电池片碎片或隐裂分析及改善措施
一、电池片碎片或隐裂分析
1、焊接
2、敷设
二、碎片或隐裂改善措施
1、焊接
①、在互检过程中要加强警惕性;
②、员工在进行电池片作业时要做到“一轻二柔三无声”,轻拿轻放,动作柔和,作业过程中无电池片引起的声音;
③、烙铁头温度要进行有效控制,不能过高或者过低,最好3~4小时检查一次;
④、返修电池片时尽量要在加热台上进行,减少受热应力影响照成的碎片。
2、敷设
①、拧串时手捏在主栅线的焊带上而不是电池片的边沿上,且用力要适度;
②、在互检时认真检查异物,并防止异物掉落到EVA上,在焊接汇流条前必须认真检查异物
本帖隐藏的内容。
光伏组件隐裂检测标准及判定
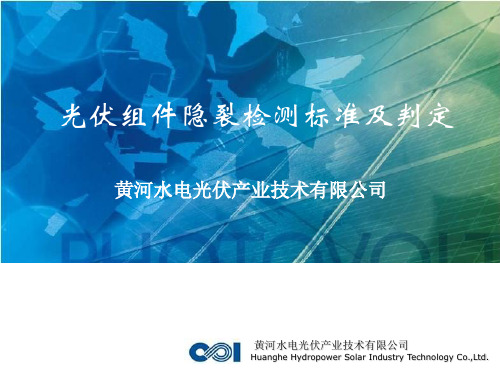
工艺污染 断栅 过焊
Байду номын сангаас
单片电池污染面积<1/3,污染片不超过8片。
1、单片断栅面积2%以内,片数不计; 2、单片断栅面积2%--10%,断栅片数占组件总 片数比例<30%; 3、不存在单片断栅面积大于10%的电池片。
不存在过焊
光伏组件光隐伏裂组的判件定隐裂的成因
关于光伏组件隐裂判定的几点说明
光伏组件的EL检测各制造企业均有相关的合格判定标准,但行业内目前 尚无统一标准。
短路
光伏组件光隐伏裂组的判件定隐裂的成因
断栅
×
光伏组件光隐伏裂组的判件定隐裂的成因
短路
谢 谢!
缺角:指在EL图像中边角位置呈现的三角形黑色区域,但在外观检验中这一区域并未
呈现缺损。
碎片:电池呈现尖锐的三角或不规则黑色区域,整个电池EL外观极差。 电池混档:电池之间电性能参数的不同导致EL图像明暗度呈现非常明显的差异。 电池短路:EL图像中单片电池或多片电池完全不发光。
集团公司隐裂检测标准
短路
面积>6mm²的缺角,同一组件上>5片。
高档位电池片混入低档位组件中大于3片,根据组 件功率判断
不存在短路现象
集团公司光隐伏裂组检测件标隐准裂的成因
隐裂的判定标准
项目
图例
不合格判定标准
黑心片
黑心程度不超过图二,单片电池黑心面积占整 片电池面积比例<25%,黑心片数量<15%组件数
量;黑心程度小于图一,片数不计。
光伏组件隐裂检测标准及判定
黄河水电光伏产业技术有限公司
黄河水电光伏产业技术有限公司
Huanghe Hydropower Solar Industry Technology Co.,Ltd.
太阳能电池组件封装常见问题与对策
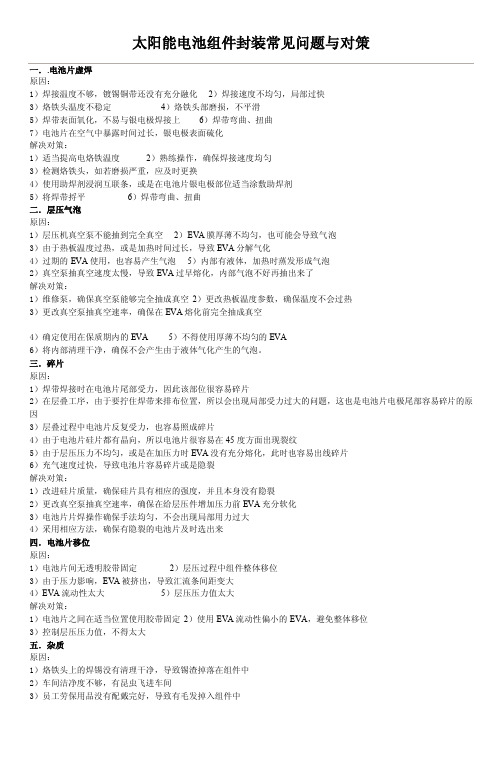
太阳能电池组件封装常见问题与对策一..电池片虚焊原因:1)焊接温度不够,镀锡铜带还没有充分融化2)焊接速度不均匀,局部过快3)烙铁头温度不稳定4)烙铁头部磨损,不平滑5)焊带表面氧化,不易与银电极焊接上6)焊带弯曲、扭曲7)电池片在空气中暴露时间过长,银电极表面硫化解决对策:1)适当提高电烙铁温度2)熟练操作,确保焊接速度均匀3)检测烙铁头,如若磨损严重,应及时更换4)使用助焊剂浸润互联条,或是在电池片银电极部位适当涂敷助焊剂5)将焊带捋平6)焊带弯曲、扭曲二.层压气泡原因:1)层压机真空泵不能抽到完全真空2)EVA膜厚薄不均匀,也可能会导致气泡3)由于热板温度过热,或是加热时间过长,导致EVA分解气化4)过期的EVA使用,也容易产生气泡5)内部有液体,加热时蒸发形成气泡2)真空泵抽真空速度太慢,导致EVA过早熔化,内部气泡不好再抽出来了解决对策:1)维修泵,确保真空泵能够完全抽成真空2)更改热板温度参数,确保温度不会过热3)更改真空泵抽真空速率,确保在EVA熔化前完全抽成真空4)确定使用在保质期内的EVA 5)不得使用厚薄不均匀的EVA6)将内部清理干净,确保不会产生由于液体气化产生的气泡。
三.碎片原因:1)焊带焊接时在电池片尾部受力,因此该部位很容易碎片2)在层叠工序,由于要拧住焊带来排布位置,所以会出现局部受力过大的问题,这也是电池片电极尾部容易碎片的原因3)层叠过程中电池片反复受力,也容易照成碎片4)由于电池片硅片都有晶向,所以电池片很容易在45度方面出现裂纹5)由于层压压力不均匀,或是在加压力时EVA没有充分熔化,此时也容易出线碎片6)充气速度过快,导致电池片容易碎片或是隐裂解决对策:1)改进硅片质量,确保硅片具有相应的强度,并且本身没有隐裂2)更改真空泵抽真空速率,确保在给层压件增加压力前EVA充分软化3)电池片片焊操作确保手法均匀,不会出现局部用力过大4)采用相应方法,确保有隐裂的电池片及时选出来四.电池片移位原因:1)电池片间无透明胶带固定2)层压过程中组件整体移位3)由于压力影响,EVA被挤出,导致汇流条间距变大4)EVA流动性太大5)层压压力值太大解决对策:1)电池片之间在适当位置使用胶带固定2)使用EVA流动性偏小的EVA,避免整体移位3)控制层压压力值,不得太大五.杂质原因:1)烙铁头上的焊锡没有清理干净,导致锡渣掉落在组件中2)车间洁净度不够,有昆虫飞进车间3)员工劳保用品没有配戴完好,导致有毛发掉入组件中解决对策:1)定时清理烙铁头,确保没有锡渣堆积2)车间内保持正风压,保证飞虫等不会进入车间3)员工劳保用品应配戴完整六.焊接不良原因:1)员工焊接手法不准,导致焊带和银电极没能完全的对应上2)如若是自动焊接设备焊接的话,那就是因为设备没有调试好3)焊花是由于在背面电极焊接的过程中,对正面焊带也造成了热冲击,导致正面焊带粘贴在串焊模板上产生焊花解决对策:1)熟练操作,确保焊带与银电极完全对齐2)如若是自动焊接机,则应调试好后再投产3)在串焊模板上,电池片银电极对应的位置开一定深度的槽,避免焊带与串焊模板接触产生焊花七.背板问题原因:1)背板凹坑是因为层压机内部有异物,层压过程中压下来导致背板凹坑2)背板鼓包是由于组件内部EVA受热分解气化,导致产生鼓包解决对策:1)清理层压机,特别是气囊和高温布2)调整层压的参数,包括降低温度和减少层压时间3)如若还是有鼓包,则应检测EVA是否在保证期以内,以及这批EVA原材料的性能八.型材问题原因:1)型材在运输过程中收到碰伤2)型材表面没有塑料保护膜3)型材鼓包、起皮是由于表面处理不好导致的4)型材颜色不均匀是由于边框在不同批次的氧化池里面表面处理,而其颜色又不太一致所导致的解决对策:1)在工厂内减少搬运环节,避免缺陷的产生2)表面鼓包、起皮的边框不能使用3)对于颜色不一致的边框要求供应商做挑选,确保一个批次的边框颜色基本保持一致组件在封装加工过程中,可能会出线各种各样的问题。
组件二部破片不良分析报告ppt课件

层压的定位,组件搬 抬时压碎
9
1501P6B60JK00929 16150B150103120000241113
1501P6B60JK02283
1501P6B60JK02410
16150B150106120000381614
16150B150106120000381677
碎片位置 1-10 6-1 4-7 1-1 5-10 4-1 2-1 4-1 1-1
各层压机台总破片数
系列1
7
6 6
5
4
3
3
3
2
2
2
2
1
1
1
1
1
1
1
1
0 0
0
0
1
2
3
4
5
6
7
8
9 10 11 12 13 14 15 16
结果:除1#、11#、12#外其他层压机台均有分布,其中3#、10#较多,8#层压机最多。
3
一、现状
破片位置分布:
破片位置分布图
5
5
3
①
4
2
②
3 2 1 0
-4.1
9s后稳定 8s后稳定
15s后稳定
-KPa
层压机实际压力对比
120 100 100
80 100 57.3 60
40
20 0 0
33.3 20
57.3 38.2
40
38.2 14
33.3
60 4.1
6#层压实际压力 8#层压实际压力
14 80 4.1 100
6#三段层压压力
8#三段层压压力
三段充气时间(s) 540
碎片产生的原因及解决的方法

碎片产生的原因及解决的方法经常出现的碎片有:
碰撞导致碎片
转移过程中导致碎片
内部隐裂导致碎焊接温度过高导致碎片
原因分析:
1,首先从源头找起。
检查电池片盒是否有问题,是否损坏,四周是否光滑,有毛刺等现象。
2,检查电池片升降器是否到合适的位置,并调整感应器开关上下位置。
3,转换电池片升降手臂,升降是否在合适的位置。
有无压到电池片。
4,升降手臂吸附值是否过大,
5,电池片定位台面的吹气量是否正常,不宜过大,气孔有无堵塞等。
6,转换电池片动作是否过快,通过气压调节速度,达到合适的位置。
7,检查455在放置焊带时和电池片的高度。
(前面0.25左右,后面0.65左右)
7,检查焊座是否完好,压爪变形很容易压碎电池片。
8,检查钢带是否干净,是否有杂质,异物,碎片等。
9,检查焊接温度是否保持正常状态,一般在(190-210)之间10,检查电池片翻转装置吸附嘴离电池片的距离是否合适。
11,观察机械手吸附值大小,吸附位置是否合适。
- 1、下载文档前请自行甄别文档内容的完整性,平台不提供额外的编辑、内容补充、找答案等附加服务。
- 2、"仅部分预览"的文档,不可在线预览部分如存在完整性等问题,可反馈申请退款(可完整预览的文档不适用该条件!)。
- 3、如文档侵犯您的权益,请联系客服反馈,我们会尽快为您处理(人工客服工作时间:9:00-18:30)。
电池片碎片分析报告随着光伏市场逐渐回暖,公司的发展又迎来了新一轮的机遇,碎片率作为太阳能电池生产的一项重要指标对生产成本起着举足轻重的作用,因此控制好碎片率实际上也是在为公司追求更多的利润。
晶体断裂:碎片其实就是晶体断裂,晶体的断裂是指晶体在应力作用下应变大于其临界断裂应变时发生的结构上的解离。
从微观角度讲,即是在应力的作用下,晶体内部的原子偏离了平衡位置且超出了原子间结合力的范围,晶格发生了断裂。
硅材料为典型的金刚石型晶体结构,各原子间通过共价键结合,是典型的脆性材料,易发生脆断。
在单晶硅的生长过程中可能会由于尺寸大,原料纯度不高,生长工艺条件不合理等原因,而具有较大的内应力,甚至局部已突破断裂应变产生了微型隐裂。
晶体的内应力越大,就越容易在较小的冲击力作用下发生解理断裂。
下面就我司碎片情况做具体分析,下图是5月份我司采购的不同厂商的硅片制作电池片所产生的碎片统计图:图1 一线不同片源碎片情况统计(5.2-5.31) (来源:生产日报表,下同)从图1可以看出单晶硅片中芯能的碎片率较其他厂商的碎片率有明显偏高,做了五批芯能的片子,平均碎片率为0.94%,而昱辉、晟纳吉、金太阳、双鸽各只做了一批,明显比芯能的碎片率低。
图2 二线不同片源碎片情况统计(5.2-5.31)从图2可以看出多晶片中金太阳做的很多,一共七批,平均碎片率为1.54%,而雷迪做了四批,平均碎片率为1.4%,山晟仅做了一批不具代表性暂不考虑。
通过一、二线不同片源的碎片率对比可以发现,片源对电池片生产过程中产生的碎片有很大的影响,其影响主要体现在硅片厚度、尺寸、崩边、线痕、隐裂等方面。
硅片厚度的影响不言而喻,比较薄的片子在人为操作,设备运行过程中所能承受的机械力会更小,发生碎片的几率更大;而厚薄不均的片子,会在等离子体刻蚀和印刷工序产生更多的碎片,在刻蚀前夹紧片子的时候由于片子厚薄不均,在拧紧夹具时可能由于某一边比另一边薄而拧得更紧造成碎片,而在印刷工序,厚薄不均的片子很容易造成印刷碎片,或者是由于厚薄不均导致烧结翘曲度比较大而产生更多的碎片。
硅片尺寸不一致也是导致碎片增加的一个重要原因。
主要体现在印刷工序,由于单晶印刷设备ASYS传送的特殊构造,所以传送带两边会加上矫正硅片位置的校正器,但是硅片尺寸不一致会导致硅片与校正器的碰撞导致碎片的增加。
崩边、线痕和隐裂片本身就是存在缺陷的硅片,在任何一道工序经过轻微的机械力作用都可能产生碎片。
从图3可以看出一线碎片主要是PECVD、印刷和分选测试产生的。
图4 二线各工序碎片统计(5.2-5.31)从图4可以看出二线的碎片主要是一洗、PECVD、印刷和分选测试产生的。
下面就各个工序产生的碎片做一一分析:一次清洗(一线)现状:下图是5月份一线一洗的碎片统计,可以看出清洗碎片占据近50%,而其他碎片都只占据很小的一部分。
图5 一线一洗碎片统计一线一洗产生碎片的主要原因是:a)人为操作手法不对造成的碎片,比如插片碎片、甩干后取篮时撞到片子等。
b)设备故障造成的问题,比如砸篮。
c)来料本身存在质量问题,比如隐裂、线痕、崩边、硅晶脱落等。
d)制绒时间过长,绒面过大,使硅片太薄也会增加碎片的几率。
改善措施:(1)来料方面的原因,我们应该及时找品控确认,以便对来料厂商进行投诉。
(2)在生产过程忠,人员要不断的对机器巡视,发现异常及时处理。
班与班交接一定要把问题及时告知下个班。
以便下个班在生产中对问题跟踪巡视。
组长在生产前首先应检查机器有无异常,确认后方可生产。
(3)人为碎片主要表现在上料手法不对,插片造成碎片。
在涉及到人为操作时手法一定要轻。
(4)要控制好减薄量,确保绒面不要太大。
一次清洗(二线)现状:5月份二线一洗的碎片数据统计如下图,可以看出下料碎片和机械故障导致的碎片占据绝大部分碎片。
图6 二线一洗碎片统计产生这些碎片的主要原因有a)员工操作手法不对,导致上下料碎片。
b)设备故障导致碎片,比如卡片、叠片等。
c)来料质量本身就有问题,比如线痕、崩边、隐裂等。
d)制绒时间过长,绒面过大,使硅片太薄也会增加碎片的几率。
改善措施:(1)来料方面的原因,我们应该及时找品控确认,以便对来料厂商进行投诉。
(2)在生产过程忠,人员要不断的对机器巡视,发现异常及时处理。
班与班交接一定要把问题及时告知下个班。
以便下个班在生产中对问题跟踪巡视。
组长在生产前首先应检查机器有无异常,确认后方可生产。
(3)人为碎片主要表现在上料手法不对,在生产过程忠尽量做到硅片与滚轮的无声接触。
接触声音大了,造成的隐裂的几率变大。
(4)要控制好减薄量,确保绒面不要太大。
扩散(一线、二线)现状:从5月份的统计数据来看,对于一线,扩散工序是产生的碎片最少的工序,占所有工序总碎片的7.7%;对于二线,扩散工序产生的碎片也比较少,占所有工序总碎片的9.8%。
5月份扩散碎片分类统计如下图:图7 一线扩散碎片统计(5.2-5.31)图8 二线扩散碎片统计(5.2-5.31)这些碎片又大体可以分成三大类:(1)、扩散前碎片,包括扩散前测少子寿命碎片和插片碎片。
产生测量少子寿命碎片的原因有:a)来料有微型隐裂,在突然性的真空吸力的作用下隐裂扩大并导致碎片;b)放片和取片时,硅片易磕碰到测试仪导致崩边、缺角;c)测试完成后,系统会在2秒钟后才解除真空吸力,在此之前去取片极易产生碎片。
产生插片碎片的原因有:a)来料有隐裂,真空吸笔吸持受力后产生碎片;b)插片入石英舟时,硅片与石英舟磕碰而产生崩边、缺角;c)插入石英舟时,因角度不正而受力形变导致碎片。
(2)扩散碎片。
在扩散过程中产生的碎片一般与硅片的质量和热应力有关。
硅片在进炉管过程中急剧升温,由于边缘比中心部分温度升得快,在硅片径向产生很大温度梯度,并由此产生很大的热应力。
如果硅片本身存在微型隐裂或内应力较大(如位错密度过高),那么在这个过程中极易导致晶格断裂,出现碎片。
硅片在出炉过程中急剧冷却,也容易受到和强的热应力冲击而产生碎片。
(3)扩散后碎片,包括卸片碎片、测量碎片和后工序退回碎片。
产生卸片碎片的原因有:a)扩散过程中热应力导致的隐裂;b)卸片时角度不正使硅片受力形变导致碎片;c)卸片时力度过大导致碎片,特别是薄片在这种情况下极易发生碎片。
测量碎片的原因参考扩散前测少子寿命的原因。
后工序退回的碎片一般以崩边片、缺角片居多。
产生的原因主要是来料缺角和插片手法不当造成。
以上三类碎片中,以扩散后碎片的比例最高,占该工序碎片的3/4强。
改善措施:根据以上对碎片状况和原因的分析,我们认为应从以下几点加于改善:(1)测量硅片时手法要轻柔,避免与测试设备发生碰撞。
待设备对硅片解除约束后方可取出硅片。
(2)插片和卸片时动作要轻柔,角度要正,在生产不紧的情况下应降低作业速度。
插片时,避免硅片与石英舟发生磕碰,硅片入舟时无碰撞声,并要注意检查来料崩边、缺角。
(3)进舟前要检查舟在桨上是否放平稳,尽量不要修改进出舟的速度。
出舟时,应等舟停止移动后再下舟。
二洗(一线、二线)现状:二洗是产生碎片较少的工序,5月份数据显示,一、二线二洗碎片占所有工序总碎片的比例为8.6%、6.9%。
5月份二洗碎片分类统计如下图:图9 一线二洗碎片统计(5.2-5.31)图10 二线二洗碎片统计(5.2-5.31)图9、图10表明,插片碎片在该工序的碎片占最大比重,分别达55%(一线)和53%(二线)。
各类碎片的产生原因分析如下:(1)造成插片碎片的主要原因有:a)片子偏薄(主要是制绒过度的返工片),手持片时用力过大导致碎片;b)硅片插入片盒时,因角度不正而受力产生碎片;c)硅片插入片盒过程中与片盒发生磕碰导致崩边、缺角。
(2)刻蚀碎片主要原因有:a)垫板不平整,导致硅片受力不均匀引起碎裂;b)硅片偏薄,受力过度时发生碎裂。
c)另外,硅片过薄时刻蚀容易发生崩边现象,我们认为在硅棒(或硅锭)的切割过程中会在硅片的边缘留下损伤,这些损伤边缘在等离子体的冲击下容易发展成崩边。
(3)清洗和甩干碎片应该主要是插片时留下的隐裂片,当然机械臂砸篮、甩干时操作不当也会产生大量碎片。
改善措施:(1)控制返工片的减薄厚度,操作薄片时一定要仔细,轻拿轻放。
(2)装夹硅片前要检查刻蚀垫板是否平整,如果有问题应及时更换。
(3)硅片插入片盒时,手用力要得当,角度要正,避免与片盒发生碰撞。
(4)时刻关注机械臂的运行情况,避免机械砸篮。
(5)操作甩干机时,操作要规范。
(6)在生产不紧的情况下,应尽量放慢操作速度。
PECVD(一线)现状:PECVD是一线各工序中产生碎片较多的工序,从5月份的数据来看,该工序碎片占所有工序总碎片的比例为24.5%,仅次于分选。
5月份该工序碎片分类统计如下图:图11 一线PECVD碎片统计(5.2-5.31)从上图可以看出,上料和下料碎片占该工序总碎片的绝大部分,比例都分别达到35%以上。
我们认为,造成上、下料碎片的主要原因有:a)硅片在前面的工艺处理过程中产生隐裂,在真空吸笔吸持受力后碎裂;b)真空吸笔操作过程中,片子未吸持稳定而掉落在石墨框上碎裂,或是片子未放置到石墨框指定位置却松开吸笔,导致片子掉落石墨框而冲击受力导致碎裂;c)下片过程中,用真空吸笔吸持硅片时,硅片与石墨框发生碰撞,引起硅片碎裂。
另外,设备碎片也占有相当一部分比重,设备碎片的主要原因为石墨框在腔室内发生卡板或跳板,造成硅片与石墨框或腔室盖板发生强烈冲撞,导致大量碎片。
5月份发生卡板的次数相对较多,故而造成设备碎片较多。
改善措施:针对当前的碎片情况,我们认为可以从以下几点加以改善:(1)控制返工片的减薄厚度,对于薄片尽量不返工,操作薄片时一定要仔细,轻拿轻放。
(2)吸持硅片时要稳,待片子放置到指定位置后再松开吸笔,确保片子与石墨框接触时无声。
(3)下片时,硅片应垂直吸离石墨框,避免硅片与石墨框发生碰撞。
(4)关注导轨条的磨损情况,发现导轨条磨损严重应及时更换。
(5)在生产允许的情况下,尽量放慢上下片速度。
PECVD(二线)现状:从5月份的数据结果来看,二线PECVD是整条生产线产生碎片最多的工序,占生产线碎片总数的31%。
5月份该工序的碎片分类统计如下:图12 二线PECVD碎片统计(5.2-5.31)该工序的各类碎片中,设备碎片占的比例最高达46%。
导致设备的主要原因有:a)插片时,硅片未与舟壁贴合,未被三个定位柱固定住,硅片在工艺气流的冲击下从石墨舟上振动掉落而碎裂;b)硅片本身有隐裂或有较大的内应力,在热应力和高频电场的冲击下产生碎裂。
上料碎片和下料碎片的原因除了来料隐裂外,主要是操作不当,硅片与定位柱或石墨舟体发生碰撞造成崩边、缺角。
而且后工序退回的碎片也都是这类缺角碎片。
改善措施:(1)在能达到预期产量目标时,尽可能的降低上下片的速度。