8D培训教材-20100304
8D新编培训教材

四. 发8D的充要条件 的充要条件
符合以下任一条件的,均需发出8D报告: 1. 客户正式投诉时; 2. OQA发现严重不良时; 3. 各工序(包括IQC)发现批量性不良或多次(定义为3次)重复发生的问题时; 4. 各工序(包括IQC)发现功能测试失效时(按《不合品管制程序》执行); 5. 可靠性测试不合格时; 6. 必须要采取长期纠正措施方可解决问题时; 7. 被相关程序文件明确要求提交8D时.
七. 8D作业流程 作业流程
Q&A (Questions and Answer)
过程概述-D1 三. 过程概述
D1 建立小组 –D1过程的中心是建立解决问题和执行修正行动所需的小组 确定小组成员时应考虑: 将人数限制在4-10人 选取具有恰当的技能知识资源权威等的人员确保代表顾客的观点并使 小组成员知道他们为什么被选取参加 从小组中选一个小组领导,由他来监控和推动改善活动的执行 小组成员的名字,职务及联系方式应输入报告 根据需要变更小组成员 小组活动: 1. 澄清问题,收集相关的资料并评估它的可用性; 2. 定义小组的角色,责任,范围和目标 3. 挖出问题周围潜在的因素 4. 考虑处理问题的办法
过程概述-D8 三. 过程概述
D8 传达结果/庆贺团队 目的:庆贺工作成绩, 激励整个团队做持续改善. 内容: 传达改善改果 1. 收集数据, 改善前后做一对比; 2. 将已改善和进步的内容公告整个团队; 3. 将8D报告打印出来,交权威人员签名后存档; 庆贺团队 (小组活动) 1. 开会或以其它合适的方式予以表彰; 2. 激励整个团队做持续改善;
过程概述-D4 三.ห้องสมุดไป่ตู้过程概述
D4 定义和核实根本原因 小组活动: 自由讨论问题发生和逃出的原因; 原因分类,级别评估并收集支持的数据; 选出根本原因; 核实、验证根本原因; 做好不良历史记录。
8D 培训教材

8D培训教材质量管理部甘斌Copyright © Sieyuan Electric Co., Ltd. All Rights Reserved.一、纠正预防措施的几个定义1、纠正:为消除已发现的不合格所采取的措施。
(返工和降级可作为纠正的示例)2、纠正措施:为消除已发现的不合格或其他不期望情况的原因所采取的措施。
(一个不合格可以有若干个原因,采取纠正措施是为了防止再发生。
)3、预防措施:为消除潜在不合格或其他不期望情况的原因所采取的措施情况的原因所采取的措施。
(采取预防措施是为了防止发生。
防错手段是一种预防措施。
)4、遏制措施:防止不合格的继续发生采取的措施。
Sieyuan Electric 施Copyright © Sieyuan Electric Co., Ltd. All Rights Reserved.1序言8D是福特以及福特供应商必须要用的解决质量问题的工具Sieyuan ElectricSieyuan Electric概述8D 概述8D8D⏹分析某个产品或过程为什么会运行于其标准之外⏹对故障的定义和理解⏹提供一种识别故障根本原因的方法,并执行正确提供种识别故障根本原因的方法并执行正确的纠正措施⏹识别系统的变化,预防同一故障及其他类似故障识别系统的变化预防同故障及其他类似故障的重现⏹强调团队的协作Sieyuan Electric案例没有真解故障(中门异响)我们容易犯的错误⏹没有真正理解故障(中门异响)⏹不会用数据来陈述事实(投产DPU的运用)有时施案臂⏹没有优先寻求临时措施和追溯方案(发动机摇臂)⏹可信度低的验证(投产样本量的选取)⏹没有找到根本原因,措施太多(减振器)⏹不使用质量工具⏹没有预防同类问题再发生的行动Sieyuan Electric运用范围(变异或特殊原因)8D运用范围8D⏹起初,系统按预期效果运行,但是在某个节点上它突然背起初系统按期效果行但是在某个节点上它突然背离了预期的性能水平⏹这种背离也许会持续、间断或者仅仅是一次事件(在潜在的某个位置会重新发生)⏹如果这种背离是间断的,它也许会无规律地发生,或者按照某种模式发生⏹变异导致的故障直到根本起因发现之后才会消失Sieyuan Electric6-SIGMA SIGMA解决范围从未发生过或普通原因)解决范围(从未发过或普原因)⏹一种系统的性能从未达到过预期的水种系统的性能从未达到过预期的水平⏹系统从实施那天起就低于预期水平⏹从未发生过的故障有时称为本身背离故障⏹从未发生过的故障可能是由于许多因素所致包括不适当的设计和共通起因素所致,包括不适当的设计和共通起因的变更Sieyuan Electric6-Sigma DMAIC Sigma DMAIC和8D 8D的区别g 和的区别8D程序6-Sigma方法⏹8D程序对于解决变异⏹6-Sigma 方法尤其适或者特殊原因导致的故障,效果是显著的合解决从未发生过的或者普通原因导致的故障Sieyuan Electric6-Sigma (DMAIC)的五个步骤DMAICDMAIC的五个步骤⏹定义:定义故障,6-Sigma项目范围确定⏹测量:测量当前过程的数据⏹分析:分析数据,确定故障来源以及过程改进方法,除从而消除故障⏹改进:选择并执行合适的改进方法⏹控制:控制监控执行Sieyuan Electric6-Sigma (DMAIC)-Sigma(DCOV)6Sigma (DCOV)DCOV 运用6-Sigma工具使顾客感知的性能和实际设计之间的⏹关系达到最优化定义:将顾客的需求综合到产品和/或过程的特征里⏹特征:产品和制造过程的设计,使之满足顾客需求⏹最优化:最优化产品和制造过程设计的可靠性⏹验证:验证新过程或者产品的期待性能水平Sieyuan Electric⏹流程图是完成8D步骤的向导图⏹使团队集中精力于目标范围⏹相当于工作计划⏹使团队清楚工作内容,时间节点帮助别些资需的什么时候获⏹帮助识别哪些资源是需要的,什么时候可以获得Sieyuan Electric检查清单⏹评估流程的执行情况⏹使团队集中精力于目标范围⏹记录会议参加情况⏹检查工作执行情况⏹检查资源准备情况Sieyuan Electric8D分析故障的两种方法演绎法(结合头脑风暴使用)vs. 演绎法归纳法vs.⏹归纳法:基于观测数据,旨在形成一种与数据一致的推测⏹演绎法:以某种推测为基础并将这种推测运用于某一特殊情况,通过某情收集并分析数据,验证数据是否与推测一致推测致Sieyuan Electric8D 8D的步骤的步骤DO ——8D程序的准备程序的准备D1——创建工作团队D2——问题描述D3——制定临时措施——D4定义并验证根本原因和忽略点D5——选择并确定永久措施——D6执行并验证永久措施D7——预防问题的重现——Sieyuan Electric D8肯定团队及个人的贡献D0 Sieyuan ElectricD0 –8D 程序准备D0D0的目标的目标⏹确定是否需要紧急反应行动,以保⏹选定、验证、执行护顾客或相关组织不蒙受损失(停止⏹确定是否使用8D 来解决问题紧急反应行动发运、停止生产、全部更换、全检)Sieyuan ElectricD0–8D程序准备故障vs症状的区别⏹症状是某一个或更多故障表现出来效应两者的区别⏹症状是由顾客所经历⏹没有症状,你就无法得知故障的存在我们往往先知道症状,如风扇电机失效Sieyuan ElectricD0–8D程序准备用工具量化症状⏹适用于趋势可以被测量或者量化的情况⏹通常有许多工具可以量化故障✓Paynter Chart / Paynter图✓Pareto / 柏拉图柏拉图✓Run (trend) chart / 运行(趋势)图Sieyuan ElectricD0–8D程序准备y/y图◆Paynter charts / PayntePaynter charts / Paynter r⏹以图表或者数据表格的形式显示⏹跟踪行动所产生的效果,或是过程的变化出厂检验Sieyuan Electric◆运行(趋势)图⏹运行图显示了在绩效上随着时间而产生的方向性变化⏹运行图用来辨别数据变化趋势或数据类型⏹问题验证跟踪、系统提升验证Sieyuan Electric案例————问题解决重点新品质量目标单项质量 案例问题解决重点,新品质量目标,单项质量问题目标的确定,问题目标的确定,AUDIT AUDIT分值的预测分值的预测哪种故障要引起关注?Sieyuan Electric 哪种故障要引起关注案例————措施a a 、b 案例措施是否有效上表中叙述的故障,紧急应变行动”a”和”b”分别有?Sieyuan Electric 什么效果是否要采取应急反应行动⏹基于你所掌握的信息而决定;故障的严重性和它对顾客产生的影响⏹它可能大到停止生产、停止所有发运,也可能小到什么都不做⏹如果是立即就要采取措施的——你不必花更多时间来研究⏹在成立8D团队之前就可以采取紧急反应行动⏹为了确定应急措施可以保护消费者,需要验证它以保证它按照期望的状态进行,并且不会导致新的失效模式⏹可以在非产品上面做验证,比如采用模型或者计算机模拟的方式⏹强调验证的方法、样本量Sieyuan Electric的标准启动8D的标准启动8D启动标准⏹故障是已经被定义的⏹顾客是已经被识别的客是经被识别的⏹该故障存在改进的空间⏹起因未知⏹管理层致力于从根本起因的层面去解决故障并采取预防措施防止故障再次发生⏹故障很复杂,单凭一个人的能力很难完成启动8D需满足六个要求Sieyuan Electric8DD1 Sieyuan ElectricD1—成立工作团队建立一个团队意味着8D程序的真正开始,D1阶段的目的是组建一个团队,它的成员需要具有解决该故障的相关技能Sieyuan Electric选择团队成员的准则⏹按需要调整⏹⏹选择具有相⏹各类成员之团队成员团队成员的人数控制在4到10个之间应技能、知识、资源、权力等间职责、任务合理搭配个间的人作为团队成员Sieyuan Electric建作团队运作程序三要素⏹建立团队运作规则团队运作程⏹设置分配任务,保持到会成员序三要素的一致性,监控过程执行情况⏹运用沟通、协调技能Sieyuan ElectricD1—成立工作团队团队会议⏹就团队运作规则达成共识就队作规则达成共识⏹制定计划,分配任务(使用流程图和检查清单)⏹明确下一次会议的时间⏹会议签到表、会议记录是必须的会议签到表会议记录是必须的Sieyuan Electric8DD2 Sieyuan ElectricD2-描述问题问题描述的目的⏹把问题陈述清楚并拟定清晰的目标⏹帮助团队关注问题本身,避免凭主观的假设判断问题,或者对问题作出毫无现实根据的判断实的判断⏹解决问题之前,知道尽可能多的关于该问题的信息Sieyuan ElectricD2-描述问题多个问题的情况⏹问题多样性:✓复杂的、多样的和含混不清的问题应该分开解决,每次解决一个问题✓目的是为了把顾客的报怨转变为问题概述✓根据现有数据判断是否存在一个以上的问题根据现有数据判断是否存在个以上的问题✓分解问题✓按优先次序去解决✓决定怎样去解决Sieyuan ElectricD2-描述问题——描述问题依据检查报告检查报告VS VS结论结论⏹由可见的和可测量的信息组成(基于事实和数据)精确影响◆检查报告⏹精确性影响大⏹因为通常是例举事实,所以无须争议⏹通常需要描述5W:什么问题、什么人、什么时间、什么地点、多大的问题间什么点多大的问题⏹需要第一时间完成Sieyuan ElectricD2D2-描述问题检查报告检查报告VS VS结论结论⏹◆结论使用归纳法,是推理后的决定⏹在通过有效的验证之前,都会有争议⏹需要频繁的测试Sieyuan ElectricD2-描述问题检查报告检查报告VS VS结论结论◆检查报告和结论的区别⏹从检查报告到产生结论,就像一条单行道—不能倒退。
8D培训教材
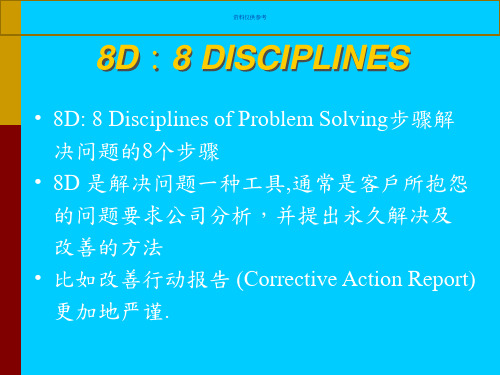
UCL=0.1253 Avg=0.0704 LCL=0.0155
资料仅供参考
如何管理异常良率
• 有效管理异常可以 – 将干扰降低 – 提升 X bar 水准 (帮助不大, 因为属于少数)
• 暂时管制措施是重要的 – 第一件事就是将产品 “Hold” – 再来才是解決解决, 预防问题的再发
• 异常管理 – 三现: 现时, 现地, 现物 – 以Problem 7 Steps 来解决及预防问题 – SDCA
型的PDCA循环,直到问题改善为止 • 小规模的改进,非大刀阔斧的改革
资料仅供参考
CA-PDCA 循环轮
3.要因解析
7.效果维持
2.现状的把握
1.主题选定 6.效果确认
A
P
Action Plan
C Check
D AP
CD
8.反省及今后计划 4.对策拟订 5.对策实施
资料仅供参考
S-D-C-A
• 标准化Standardization-实行-检查-行动 • 所有制程在开始运作时都会不稳定, 在这个
cause,但复杂的或许要5 Why, 6 Why, 7 Why…最后要加 1H,How to fix it.
资料仅供参考
5 Why 范例: 为何停机
• 问1:为什么机器停了? • 答1:因为机器超载, 保 险丝断了
资料仅供参考
5 Why 範例: 為何停機
• 问1:为什么机器停了? • 问2:为什么机器会超
资料仅供参考
PDCA , CA-PDCA 与 SDCA
AP CD
AS CD
(+) GAP
Analysis
(-)
列出问题点
AP CD
福特(Ford)8D培训教材

也不要写工作报告
Page 10 of 47
成员包括:
❖ 指导员(CHAMPION) 一般为主管阶层,对小组的进度有 监督, 支持及决策决定 权力.
❖ 组长(LEADER)-负责协调,活动进行的引导,汇总小组的意 见及决策并呈报,尽量不要深入某部份细节,以免迷失方向.
❖ 问5次为什么的做法:
➢对于某个问题,为何会引起?其原因①先搞明白。 ➢为何会引起原因①的发生?将原因②也搞清楚。 ➢为何会引起原因②的发生?将原因③弄明白。 ➢为何会引起原因③的发生?将原因④弄明白。 ➢为何会引起原因④的发生?将原因⑤弄明白。
Page 20 of 47
❖ 用这种方式持续地去做,根本的原因就能显現出来。 ❖ 分析出来的根本的原因必须是能导出具有効果、
且有効率的再发防止对策才行。 ❖ 要注意的是问题发生的原因不一定只有一个。
❖ 通常第一个答案不会是真正的答案 ❖ 5 Why 可以找出真正的原因 ❖ 简单的案子可能4Why,3Why或2Why即找出根本原
因,但复杂的或许要5 Why, 6 Why, 7 Why…
Page 21 of 47
做5 Why 分析时应注意事项
因会影响结果时,不能说有因果关系)。
Page 23 of 47
5 Why 范例: 为何停机
❖ 问1:为什么机器停了? 答1:因为机器超载, 保险丝烧断了
❖ 问2:为什么机器会超载? 答2: 因为轴承的润滑不足
❖ 问3:为什么轴承会润滑不足? 答3: 因为润滑系统失灵了
❖ 问4: 为什么润滑系统会失灵? 答4: 因为润滑系统的轮轴耗损了
8D培训教材
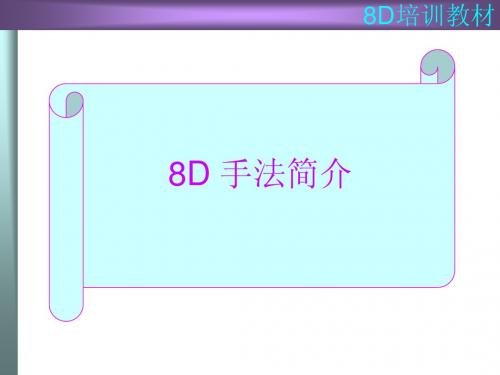
8D培训教材
6D-执行效果验证 执行效果验证
执行效果验证 1、验证效果OK 、验证效果 验证人 验证日期 梁晓秋20XX/11/18 梁晓秋
BOM培训资料 BOM培训资料 基础知识部分
8D培训教材
7D-预防措施 预防措施
*理解:为消除潜在不合格或其他潜在不期望情况的原因所 理解: 理解 采取的措施(防止类似问题重犯) 采取的措施(防止类似问题重犯) *长期措施要可执行且能标准化,要落实到日常的管理监控 BOM培训资料 BOM培训资料 体系中去,要在流程,操作指导书,质量计划,控制计划, 基础知识部分 管理规定等文件中有体现。 *每个根本原因必须有一个或一个以上的对应的长期措施。 *要遵循SMART原则,并有对应的完成时间,责任人。
8D培训教材
D2-成立团队 成立团队
*选择并记录内部 外部成员。 选择并记录内部/外部成员 选择并记录内部 外部成员。 * 选择小组的指导者 可以帮助小组移走障碍的管理成员 。 选择小组的指导者(可以帮助小组移走障碍的管理成员 可以帮助小组移走障碍的管理成员)。 * 选择小组长 直接指挥并对小组负责的成员 。 选择小组长(直接指挥并对小组负责的成员 直接指挥并对小组负责的成员)。
8D培训教材
长期措施(案例 长期措施 案例1) 案例
改善措施 1、修改模具,将由 修改到 修改到XXX ; 、修改模具,将由XX修改到 负责人 XXX XXX 开始日期 1/18 完成日期 1/19
2、规范加工方法,精度要求在XXX以上者; 、规范加工方法,精度要求在 以上者; 以上者 使用慢走比加工; 使用慢走比加工; 3、将两种类似物料,分开来放置物料架上。 、将两种类似物料,分开来放置物料架上。 4、更改检验巡检抽检标准和检验的频率。 、更改检验巡检抽检标准和检验的频率。 备注: 备注 需量化。 BOM培训资料 BOM培训资料 基础知识部分
8D培训讲义

四、8D 精神
为什么要成立8D小组 “D1 成立8D小组” 为8D过程的真正开始。 成立8D小组是8D过程的基本部分。极少有一个人具有所有需要的资源、资料和技能来解决一个复杂的问题。另一方面,一组合适的人员能够包括所有必须的资源和聚集每一个人所具有的技能。
D3:临时措施
立即对线上品、库存品、在途品及发运给客户的产品采取紧急处理对策。 说明目前如何控制该项不合格,同时防止上述不良品再度流出。 由成本、交期及引发其他不合格可能性来评估紧急对策的有效性。 应明确执行临时措施的责任者。 临时措施是否会引起其它问题。
什么是根本原因 不同类型的原因。 #可能原因:在因果图上被确定的描述一种结果可能发生的任何原因 #最有可能原因:以可得到的数据为基础,最能描述问题的原因 #根本原因:验证过的产生问题的真正原因 D4过程能够帮助慢慢减小调查范围
D2: 问题描述
要想成为一个有效的问题解决者,必须在采取行动前知道尽可能多的关于问题的描述。在D2阶段的任何不清楚和不准确都会导致小组得到错误的原因和采取错误的纠正行动。 采用标准的语言,从客户观点来描述问题 描述尽量具体,事实清楚,证据充分,能 量化以量化表示. 所报告的应是真实、客观的问题 采取5W2H描述
8D培训讲义
内 容 一、什么是8D 二、8D有什么作用 三、何时采用8D 四、8D 精神是什么 五、怎么做8D
一、什么是8D?
8D:所谓8D方法(eight disciplines),又称团队导向问题解决对策TOPS(Team Oriented Problem Solving) ,是福特公司处理问题的一种方法,共分8个步骤。
不要忘记总结团队作战的经验 完成小组任务,衷心地肯定小组和个人的集体努力和贡献,并加以祝贺。由最高领导者签署。
8D培训教材
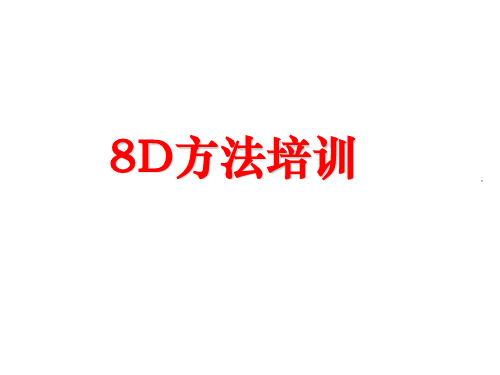
D0–8D程序准备
案例——措施a、b是否有效
上表中叙述的故障,紧急应变行动”a”和”b”分别有 什么效果?
D0–8D程序准备
是否要采取应急反应行动
基于你所掌握的信息而决定;故障的严重性和它对顾客产生的影响 它可能大到停止生产、停止所有发运,也可能小到什么都不做 如果是立即就要采取措施的——你不必花更多时间来研究 在成立8D团队之前就可以采取紧急反应行动 为了确定应急措施可以保护消费者,需要验证它以保证它按照期望 的状态进行,并且不会导致新的失效模式 可以在非产品上面做验证,比如采用模型或者计算机模拟的方式 强调验证的方法、样本量
STEP7
分析风险
决策过程的七步
STEP6
比较Y选ou择r te措xt 施in here
STEP5
列出可选措施
STEP4
确定满足标准的相对重要性
YSouTrEtePxt3in here
列出决Y策our标tex准t in(he强re 制和想要)
STEP2
描述最终结果
STEP1
D5 –定义永久措施Permanent
6-Sigma (DMAIC)
6-Sigma (DCOV)
DCOV 运用6-Sigma工具使顾客感知的性能和实际设计之间的 关系达到最优化
定义: 将顾客的需求综合到产品和/或过程的特征里 特征: 产品和制造过程的设计,使之满足顾客需求 最优化: 最优化产品和制造过程设计的可靠性 验证: 验证新过程或者产品的期待性能水平
精确性影响大 因为通常是例举事实,所以无须争议 通常需要描述5W:什么问题、什么人、什么时 间、什么地点、多大的问题 需要第一时间完成
D2
D2- 描述问题
8D报告培训教材(经典)

析和方案策划。
四. 8D步骤—D1建立小组
建立一个小组来解决问题和执行纠正计划, 小组成员应具有过程和/或产品知识、分配的 时间、权威和需要的技能。
建立小组需要考虑的要素:
小组的领导: 小组的资源: 小组的成员: 人员的数量:
谁来推动? 谁提供支持? 合作及分工? 多少为宜?
备注:广泛用于QS9001/ ISO9001/ TS16949 (变更为
IATF16949/VDR6.3)解决质量问题的8D isciplines。
一.什么是8D
以团队运作导向以事 实为基础,避免个人 主见之介入,使问题 之解决能更具条理。
面对问题应群策群力, 互相帮助、相互提拔、 如此才能彻底解决问题。
• 确定并执行应先采取的临时措施,以遏制外界/内部客 户问题的扩大。
• 临时措施的确定应考虑从供应商零件库存---供应商零 件在途品--内部零件/材料—生产制程—仓库储存—交 付在途品—客户端减少和降低(消除)后果的产生。
• 临时措施一直要持续实施至后续的永久对策的执行有 效后,方可撤消。
• 临时措施实施中,应及时跟踪和验证其效果。
五.8D改善案例
D0.了解问题
2009年11月4日“众盛精密机械厂”投诉,在其包装 车间对“ALT-5检测器”进行包装时,使用公司的MHT 机用膜时一拉就断裂, 并发现使用的机用膜端口破裂 。造成ALT-5检测器包装工作进度延误,顾客要求派 人处理。
五.8D改善案例
D1.成立小组
•按问题涉及范围确定小组成员: •责属单位:生管部、业务部、仓储部、品管部 •责属人员:
五.8D改善案例
D5.长期对策
5.1决定采用长期对策
8d报告培训教材

三.定義:
• (1) 8D (8 Disciplines) 方法包含8個解決問題的步驟. 它基于使用 描述工具,格式化,分析,量化等工具,從而提供徹底解決問題的指引.
• (2)問題: 被發現的具体問題,它包括: • 1) 与正常狀況相比,屬于失常的現象,在這种情況下, 需要予以
四.在下列情形中須提交8D報告
:
• (1)當客戶在工厂現場的稽核中發現不合格項或缺陷時, 對于嚴重 不良,主要不良及重複發生的次要不良須提交8D報告.
• (2)OQC發現嚴重不良,主要不良及重複發生的次要不良時須提交 8D報告.
• (3)當市場上發現有重複發生的產品缺陷時須提交8D報告. • (4) 當ORT測試過程中發現缺陷時須提交8D報告. • (5)IPQC在同一生產現場連續發現三個位置相同不良現象或三個
七. 8 D steps 8D步驟
• (關文件. • 2) 長期糾正措施的功效可通過觀察問
題是否重復出現來評估.
七. 8 D steps 8D步驟
• (7)預防問題重復出現措施 • 1) 修正整個質量系統(特別是問題相
關的程序,技術說明書,工作說明書). • 2) 管理層同意並修正整個質量系統,
七. 8 D steps 8D步驟
• (2)問題描述: 問題及其所造成影響的描述. • 1) 描述在具体環境中觀察到的現象,或問題
造成的危險. • 2) 用4M+1E( Milieu)的方法定性,定量分析
問題的狀況. • 3) 推荐在8D報告中采用适當的圖表作為附
件來描述(what, who, where, when ,how).
8D方法培训教材

% Effective
Validation
% Effective
Page * of 110
掌握“問題”之要領
1)什麼是“問題”? 問題是實際與理想之間的差距 2)什麼是問題的型態? 1.異常性問題 (s 太大) 2.結構性問題 (Xbar 太低) 3)如何發掘問題? 把問題視作一座冰山 ( 使用工具: 5 Why, 親和圖法,關連圖法..)
為什麼潤滑幫浦會失靈?
為什麼潤滑幫浦的 輪軸會耗損?
平面度不佳關聯圖解析
平面度 良率不佳
人員疏失
設備問題
方法缺失
BUY OFF檢 查動作不確實
職前訓練 不足
疏忽
規格認識 不夠
Loading 過多
加班
精神不佳
模具異常
產品定位 不良
機台操作 不熟悉
材料問題
TRAY 設計不良
QA未執行 分散抽樣
打帶動作 不確實
5 Why 範例: 為何停機
問1:為什麼機器停了?
答1:因為機器超載, 保險絲燒斷了
5 Why 範例: 為何停機
問1:為什麼機器停了? 問2:為什麼機器會超載?
答1:因為機器超載, 保險絲燒斷了 答2: 因為軸承的潤滑不足
5 Why 範例: 為何停機
問1:為什麼機器停了? 問2:為什麼機器會超載? 問3:為什麼軸承會潤滑不足?
8 D 手 法
质量管理报告培训经典教材含案例分析ppt课件

Possible
2016.11.09
2019 1
课堂纪律
1. 手机请关机或调成静音。 2. 请保持课堂安静,请勿交头接耳或大声讲话。 3. 如有问题请会后交流 。
2019
-
2
目录
一.什么是8D 二.为什么要推行8D 三.何时采用8D 四.8D步骤 五. 8D改善案例 六.八D报告经典案例
2019
-
4
一.什么是8D
此方法以团队运作导 向以事实为基础,避 免个人主见之介入, 使问题之解决能更具 条理。 2019
面对问题应群策群力, 互相帮助、相互提拔、 如此才能彻底解决问题。
5
二.为什么要推行8D
通过建立小组训练内部合作的技 巧。 提供问题有效解决的方法。
防止相同或类似问题的再发生。 提高顾客满意度,增强其对供方 的产品和过程的信心 。 -
临时措施与长期措施的区别
临时措施
消除问题及后果
只能治标 (可能再发)
长期措施
消除问题原因
可以治本 (不会再发)
2019
-
18
四. 8D步骤—D4原因分析
用统计工具列出可以用来解释问题起因的所 有潜在原因,再分别针对每一可能原因予以 测试,最终确定产生问题的根本原因。
需要考虑的问题:
1.列可能 原因时要 周全。
四. 8D步骤—D3临时对策
临时措施(对策)
为了不让问题不再扩大而采取的措施,相当于纠正。 常采取的动作如:隔离、全检、换货、报废、降级,员 工培训。
长期措施(对策)
为了问题不再发生所采取的措施。 一般必须进行根本原因分析才可以采取长期措施。 常见如:防错、更换原材料、设计变更等。
8d方法培训教材
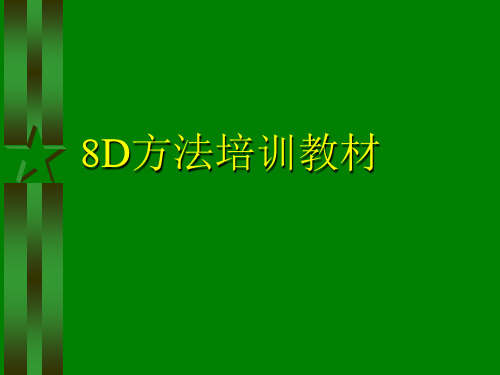
试验和演示。 比较新的行动和已验证过的相似行动。 在发布前回顾最近的设计文件(程序、政策、规范等)。
ERA可能很难用测量验证,因为它是以常识为基础。 例如,如果将受到影响的产品停止发运,那么顾客就 不会再经历症状。
D1过程的中心是建立解决问题和执行纠正行动 所需的小组并开始小组建立过程
• 目的:
描述成立8D小组的方针 描述小组的角色、角色的功能和他们是怎样执
行的 解释小组操作程序的三个要素 描述小组配合的特性
过程介绍- D1 成立8D小组
• 为什么要成立8D小组
“D1 成立8D小组” 为8D过程的真正开始。 D1的目的是组织一组具有所需特征和 动力的 人员来解决问题
8D过程概述(续)
• D7 防止问题再次发生。
修改必需的系统包括政策、程序等来防止同一 或相似问题的再发生。如果需要对系统改进提 出建议,并将学到的技术教训形成文件。
• D8 表彰小组和个人的贡献
完成小组的经验。真诚地表彰小组和个人的贡 献。
过程介绍-D0 准备8D
Frequency Count
• 这些步骤用来客观地确定、定义和解决问 题并防止相似问题的再次发生。通常是客 戶所抱怨的问題要求公司分析,并提出永 久解决及改善的方法。
8D 的本质: 问题解决程序
当我们观察到或 发现到………时 或发现时
现
象
确认并定义问题
例如: 人员出勤率93%
这现象是否正常?
WHAT, WHEN, WHERE, WHO, WHY, HOW, HOW MUCH
Percent
问题发生
顾客投诉; 发生质量事故; 生产不良率骤然升 高 控制图出现异常; σ变化很大; …….
8d培训教材
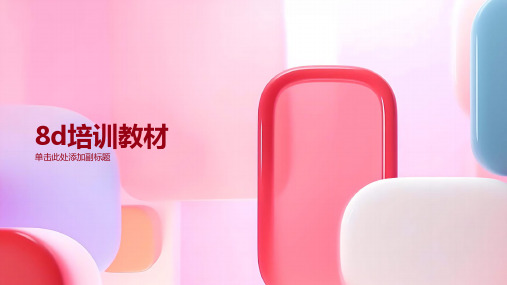
8D培训教材在 生产现场的应 用,可以帮助 员工提高工作 效率和质量。
8D培训教材在 生产现场的应 用,可以帮助 员工提高安全
生产意识。
8D培训教材在 生产现场的应 用,可以帮助 员工提高团队
协作能力。
在质量管理中的应用
8D培训教材是一种系统性的质量 管理方法,旨在帮助企业解决质 量问题。
8D培训教材可以帮助企业提高产 品质量,降低成本,提高客户满 意度。
8d培训教材
单击此处添加副标题
目录
8d培教材概述 8d培训教材的应用 编写8d培训教材的步骤
8d培训教材的内容
8d培训教材的优点 如何推广和应用8d培训教 材
01
8d培训教材概述
8d培训教材的定义和作用
8d培训教材是一种针对8d问题解决法的培训材料,旨在帮助学员掌握8d 问题解决法的基本原理和实践方法。 8d培训教材可以帮助学员提高问题解决能力,提高工作效率和质量,降低 成本和损失。
培训和宣传
培训内容:8D问题解决法、质量管理工具、团队协作等 培训方式:线上课程、线下讲座、企业内部培训等 宣传渠道:企业官网、社交媒体、行业论坛等 宣传策略:案例分析、成功故事、专家推荐等
03
8d培训教材的应用
在生产现场的应用
8D培训教材在 生产现场的应 用,可以帮助 员工提高解决 问题的能力。
8d培训教材的编写原则和标准
针对性:针对不同岗位和层级的员工,编写不同的教材内 容
系统性:教材内容应涵盖8d培训的所有知识点,形成完 整的知识体系
实用性:教材内容应结合实际工作场景,提供实用的方法 和技巧
通俗易懂:教材语言应简洁明了,易于理解和掌握
互动性:教材应设计互动环节,提高员工的参与度和学习 效果
非常出色的8D培训教材

改善範例
105 100
目標=100元
95 90
-20元
-10元
85
80
75
90
70
80
65
60 ²Ä ¤@ ¶g
²Ä ¤G ¶g
102
101
²Ä ¤T ¶g
²Ä ¥| ¶g
Page 33 of 110
兩種不同類型的良率損失
• 異常良率損失 Excursions: 良率損失的獨立 跳昇,由突然且嚴重的良率損失所引起, 影響範圍導致特別低良率的有限批數
問
題
分析原因 WHY
原
因
人員出勤率的目標為95% 低了2個百分比,而此差 異幅度根據以往資料判斷 差異過大為異常狀況。
請假人數太多
設定改善目標 並形成解決方案
對
策
處置:問題發生立即採 公佈人員出勤狀況取 治的標措:施解決問題的手段 強化請假 管治制本:避免問題再發生加強員工向心力的方法
衡量、追蹤及控制改善成效
準確, 但變異卻很大
Page 8 of 110
Cpk=0.816
Cpk=0.852
0 10 20 30 40 50 60
-6 4 14 24 34 44 54 64 74
Cpk=1.694
Cpk=0.852
-5 5 15 25 35 45 55 65
-6 4 14 24 34 44 54 64 74
客戶Release good Hold reject
工程師待 客戶指示
Hold Yield 太高不合理
客戶要求作 工程分析
客戶一直 未回覆
待客戶 新程式
平面度不佳關聯圖解析
QA未執行 分散抽樣
8D培训课件(doc 84页)

作的概率;
找出基本缘由运用(yùnyòng)的方法:
WHY? WHY? WHY? ……….
第十八页,共83页。
➢ 例如:如何(rúhé)找到基本缘由?
效果:有一辆汽车不能行走。 为什么不能行走?
------ 由于发起机缺点。 为什么发起时机出缺点?
------- 由于火花塞不能点火。 为什么火花塞不能点火?
真理降生于一百个问号(wènhào)之后
第二十三页,共83页。
2) 在断开的电路接触器被发现前,电镀槽由于没有通电所以零件没有电镀上。
3.反省消费日报
在5月26日0点,A公司消费了7F〔61128片〕,但没有任何没有电镀产品的记载。
第十三页,共83页。
D3
实施和验证临时措施
确定并执行应先采取的暂时(zànshí)对策, 控制外部/外部客户效果事态的扩展,直到执行永世对策,并验证所采取暂时 (zànshí)对策的效果。
第十四页,共83页。
D3
实施和验证临时措施
运用目前已经了解的 信息和有关问题的描 述,采取遏止措施;
↑ 选择 ↑ 事前验证 (yànzhèng) ↑ 执行
在每一个过程点阻止 缺陷,并将其退回原 处;
↑ 确认缺陷产品不再 存在(cúnzài),以及用 户的不满意不再存在 (cúnzài)
第十五页,共83页。
1、效果能否(nénɡ fǒu)用顾客的术语描画? 2、效果的末尾/完毕日期列出了吗? 3、缺陷率〔效果的多少〕列出了吗? 4、效果的频率列出了吗? 5、实践检测报告列出了吗? 6、要求〔规范〕列出了吗?
第十二页,共83页。
D2
问题描述
例:
A公司在接到顾客埋怨后,马上组成小组展开调查,确认(quèrèn)效果如下:
- 1、下载文档前请自行甄别文档内容的完整性,平台不提供额外的编辑、内容补充、找答案等附加服务。
- 2、"仅部分预览"的文档,不可在线预览部分如存在完整性等问题,可反馈申请退款(可完整预览的文档不适用该条件!)。
- 3、如文档侵犯您的权益,请联系客服反馈,我们会尽快为您处理(人工客服工作时间:9:00-18:30)。
12
2、清楚描述问題
将所遭遇的外界/內部客戶問題,以计量方 式,确认该问题的人,事,時,地,如何,为何, 及多少(即所謂5W,2H)。
13
何謂5W2H
何人 何事 何時 何地 为何 如何 多少 :识別哪一个客戶在抱怨 :适当、精确地识別问题 :从什么时候问题开始发生 :什么地方发生问题 :识別已知的解释 :在什么模式或状态下发生这问題 :量化问题的程度
2009-02-15
3
2009-02-15
4
杨 旭
2009-02-17
4D 原因分析-详细流程图
Cell test测试流程图
接货 打开盖板 拿取panel 放入治具 盖上盖板
N N 标识后放入tray盘 Y 切换画面
黑团检测 复判
报废
Y
X1:背光亮度 X2:画面均匀度 X3:环境照度 X4:人员MSA
5D 改善对策-前、后对比
1. 针对测试画面存在分屏的改善措施:将Gate开启时间由1.5ms加长到4.5ms; 确认方法:用示波器测量 确认人:杨旭 确认周期:一个月 Gate信号
环
环境照度
背光亮度
检出黑团能 力差
来料正常
作业手法
料
法
28
4D 原因分析-5why分析
为什么模组出现如此高比例 的黑团产品? 因为cell test 10.4寸黑团存在漏检。
为什么会有10.4寸黑团产品 漏检?
因为cell test 10.4寸测试机台对黑团 检出能力差。
为什么cell test 10.4寸测 试机台对黑团检出能力差?
14
3、执行和验证临时措施
根据问题的性质,确定并执行相应的临时 措施,以控制外界/內部客戶问題发生的效 应不致扩大,直到永久措施執行。 验证所采取临时措施的效果。
15
4、确定并验证根本原因
对问題之何以發生,指出其一切可能形成的 原因.再分別针对每一可能原因予以測試, 以验证真正之根因.然后找出消除该项根本 原因的各项纠正措施。
原因:分屏是因为产品设计问题;
示意图:
4.5ms 1.5ms 0 ms
因为10.4寸产品有两个信号驱动IC, 在VT时要用一个RGB输入去控制 所有的数据线。根据NPI的要求(为 了减少腐蚀)尽量减少SD金属在台 阶上,所以RGB的金属控制线路必 须通过一些接触孔和ITO连接起来。 根据钝化膜的过刻蚀时间以及孔的 TAPE ANGLE,接触孔电阻会增大。 因为信号总线的长度不同,以及通 孔的数目不同,或者在生产过程中 的电化学腐蚀,信号总线通到不同 区块的电阻会有不同。
预防措施
为消除潜在不合格或其他潜在不期望情况的 原因所采取的措施。 一个潜在不合格可以有若干个原因。 采取预防措施是为了防止发生。
5
What is Root Cause
解決了root cause那麼不良或失效模式就可 以不發生。 有些失效模式可能有好幾個root cause,那 麼解決了一個root cause,至少可以減少失 效模式發生的概率。 所以root cause就是只要解決它就可以解決 失效模式。 使用方法:5Why
33
4D 原因分析-
5why分析
为什么10.4寸测试治具背光亮度不足?
原因一:检测方式决定的;
2000 1800 1600 1400 1200 1000 800 600 400 200 0
CCFL背光属性图
CFFL亮度值
0
1
2
3
4
5
6
7
8
10 11 15
时间(单位:分) CCFL背光亮度 单位:nits
改善前治具 画面图 片???? 亮度低,画 面分屏
事件
影响
24
3D 临时对策
序号 应急措施 对module产线10.4寸黑团不 良品进行确认,对产线已经 检测出来的不良品滞留,一 星期后复测。 执行人 完成日期 效果确认
1
乐文志 相晓丽 邓朝阳 相晓丽 邓朝阳 相晓丽
2009-02-15
最大程度减少 了产品报废。 一定程度上控 制了原料浪费。
√
√ √ √
√
√ √ √
√
√ √ √
√
√
√
√
√
23
2D 问题描述
顾客 时间
地点
Module 2009年2月13日
模组大线 Module产线生产10.4TC01-00时,投入400,电测发现 黑团42片,不良比例为10.5%,黑团位置不固定,R、 G、B、灰图下均可见 。 Module直通率下降10.5%,影响模组出货。 改善前的 测试画面
SHANGHAI TIANMA MICRO-ELECTRONICS CO.,LTD
22
1D 成立团队
团队成员
邓朝阳
杨旭 刁庚秀 李霄 乐文志 相晓丽 吴雪娟
职位(职责)
工程师 (leader)
工程师 工程师 工程师 工程师 培训员 工程师
各阶段分工 临时对策 原因分析 树立对策 改善实施 标准化
√
trimmer
外观检测
出货到Module
COG
FOG
Module一次ET
Y1:Module 一次ET检测到黑团不良
26
4D 原因分析-不良流出分析
黑团不良流出的主要原因:
Cell test 治具背光亮度不足
Cell test 治具测试画面不匀
27
4D原因分析-4M1E
分析1
人
MSA
机
画面均匀度
测试画面存在分屏, 背光源亮度不足 颜色不匀;
为什么10.4 寸测试画面 存在分屏?
为什么10.4 寸背光源亮 度不足?
分屏因为产品设计 问题;
10.4寸背光亮度不 足由CCFL背光属 性决定。
29
4D 原因分析-5why分析
为什么cell test 10.4寸测试机台对黑团的检出能力差?
原因一
21
8D报告名称:
提高Cell Test段10.4寸 黑团的检出能力
目录
1D 2D 3D 4D 5D 6D 7D 8D 成 问 临 原 改 改 标 财 立 题 时 因 善 善 准 务 团 描 对 分 对 实 化 节 队 述 策 析 策 施
姓名:邓朝阳 单位:TEST 日期:2009-04-08
余
上海天马微电子有限公司
31
4D 原因分析-5why分析
为什么10.4寸产品在cell test测试治具上画面会分屏?
尺寸 Gate打开 时间T (us)
T=1.5ms
Gate信号
1.8
2.2 2.4 2.83 3.5 4.7
999.99
999.97 999.99 999.99 999.86 999.97
Date信号
5.6
面对问题应群策群力, 互相帮助、相互提拔、 如此才能彻底解决问题。
4
纠正
为消除已发现的不 合格所采取的措施。 俗称:将错的改过来。 表现为:返工、返修、 降级、让步等。
纠正措施
为消除已发现的不合格或其他 不期望情况的原因所采取的措施。 一个不合格可以有若干个原因。 采取纠正措施是为了防止再发生
7
解決根本性問題
豐田員工提出“5個為什麼”。要找出問題的根本 原因,必須至少依次提出5個“為什麼?”這就象 一層層剝洋蔥一樣。
必須記住的是當你能夠“產生又消除”時,也就 是說能夠隨意地重現一個問題,然後又能使其解 決時,你就能确定已經找到了這個問題的根本原 因。—— “问题重现,根因即显”。
8
何时采用8D
並不是要求每一件发生的问题都必须采取 8D方法。 而是针对重复发生的,一直没有解决的比 较重大的问題。 制程能力(CPK)持续不达标 针对客戶要求回覆的客訴抱怨。
9
8D的八个步骤
所谓“八个步骤”,其每个步骤意义及其流程请参 阅附图.该图虽已列出解决问题的各个步骤,但各 个步骤的先后順序可视问题的困难度及复杂程度 而异,不必拘泥于图示順序.且问题解决经过应有 书面记录. 如:某一问题发生及团队组成时,可能制造人员已 经先行采取临时对策,惟其永久解决方案,则可能 尚需小组人员的共同参与,经多方研讨后才能产生。
一定程度控制 了cell test段10.4 寸黑团产品继 续流往module。 CCFL背光的亮 度比以前有了 50%的提高。
25
2
对module段未生产的10.4寸 产品用背光进行sorting。 cell test段检测黑团视角由 原来的45°变为75°。
将cell test10.4寸测试治具背 光接成常亮模式。
10
問題提出
识別可能原因
5、确定及 验证纠正措施
1、成立小組
选择最有可能 的原因
6、执行永久 纠正措施
2.清楚 描述問題
最有可能的原因 是否是根本原因
7、避免再发生 (预防措施)
3.执行和确认 临时措施
识別可能的 解决方案
8、恭贺小組
11
1、成立小组
邀请具备产品及制程知识、能支配时间,且 拥有职权及技能的人士,组成一个小组,解 决所见问题及采取纠正措施.此小组应指定 一位小组领导人员。
此时,应着手進行管理制度,作業程序及 作業指导等項目的修改, (比如FMEA\Control Plan\Procedure\SOP),以防止同一問題 及類似問題再度發生。
20
8、财务结余
财务节余=(改善前-改善后)×月产量×12个月×单价-项目所需投资 = =
1. 直接材料节省: 2. 直接人工节省: 3. 直接设备/能源节省: 4. 纠正/管理费用节省: 5. 减少调试/返工/排故费: 6.本项目所需投资