生产小批量试产表格
小批量试产流程图(1)
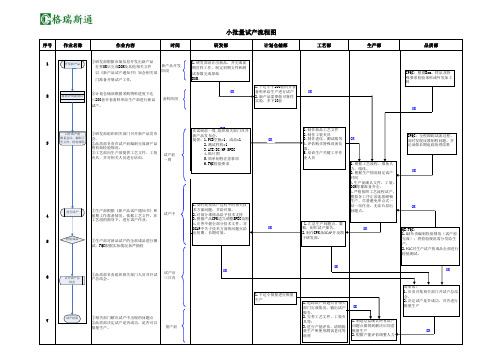
序号作业名称作业内容时间研发部计划仓储部工艺部生产部品质部①研发部根据市场信息开发出新产品打样OK后完成BOM及其他相关文件 以《新产品试产通知书》知会相关部 门准备开展试产工作.②计划仓储部根据采购物料进度下达<200套齐套备料单给生产部进行新品试产。
46①品质部负责组织相关部门人员召开试产总结会。
①生产部根据《新产品试产通知书》和前期工作准备情况,依据工艺文件,在工艺组的指导下,进行试产作业。
①相关部门解决试产中出现的问题点②品质部决定试产是否成功,是否可以批量生产。
①生产部对新品试产的全部成品进行测试,FQC根据实际情况加严抽检2735小批量试产流程图①研发部组织相关部门召开新产品发布会。
②品质部负责在试产前编制完成新产品的初始检验规范。
③工艺部向生产部提供工艺文件、工装夹具,并对相关人员进行培训。
1OK OK 试产中试产后三日内 1.研发部设计出新品,并完成前期打样工作,制定初期文件和测试参数完成原始BOM 。
1.下达小于200套的齐套备料单给生产进行试产2.新产品需要做可靠性实验,多下10套QE/FQC :1.QE 负责编制检验规范(试产前完成);将检验规范需分发给生产。
2.FQC 对生产试产的成品全部进行检验测试。
1.制作新品工艺文件2.制作工装夹具3.制作老化、测试线等4.评估购买特殊设备仪器。
5.培训生产关键工序作业人员 1.根据工艺流程,准备人力、线体。
2.根据生产情况制定试产时间3.生产前确认文件、工装、BOM 等都准备齐全。
4.严格按照工艺流程试产,模拟各工序正常连续顺畅生产,尽量避免单点式一站一站作业,无法凸显出问题点。
1.及时处理试产过程中的相关技术方面问题,并给对策。
2.对部分难修品给予技术支持3.根据产品CPK 适当调整SPEC 范围4.完善不健全部分技术文件,对OCAP 中关于技术方面的问题点给出短期、长期对策。
在试制前一周,组织相关部门召开新产品发布会。
提供:1.PCB 空板*1、成品*12.测试样机*13.ATE/BI/HP SPEC 4.贴片图5.简单制程注意事项6.FQC 检验要求 1.汇总生产问题点、数据,制作试产报告。
汽车零部件量产批量生产评价表

检证日供应商检证者总达成率:0%车型:重要项NG 0小于50%项目序号重要项类别评价参考基准○/△/X得分得分小计课题责任人完成日期GAMC确认结果日期符合性物料标签与实物一致,符合图纸/制造要求★材料、性能材料、性能符合法规、图纸等技术要求,材质证明书/检验报告等齐全0外观、尺寸来料外观、尺寸管控责任明确,与二级供应商建立健全的异常处理流程,批次检查有记录8管理来料有入/出库品质规范,库存管理清晰,记录完整,与生产系统相关可回溯★布局各制造工序现场布局是否与工艺设计相符,与工艺设计一致,并达成量产状态布局节拍与预设周期一致,连续生产总计节拍达成目标瓶颈重点工序有目视标识。
识别出瓶颈工位,并有相关增产应对方案★合格率良品率达到产量预设的目标0工序检测工序布局及人员体制能检测工序不良,后工序有防错漏检测前工序不良,并形成批次内的追溯12关键特性关键品质分解至制造工序并重点标识重点工序★人员数量全部班次按计划配置人员满足岗位要求,并且实现定人定岗★作业标准所有作业标准齐全,并容易理解,操作实际与指导书一致。
有实施签字确认流程,对关键控制点有明确的指示。
能力有包括必须的培训项目的培训计划和矩阵表。
所有作业者按日程安排接受培训,有按计划确认培训进度。
0异常处理1)异常升级流程清晰,发现不良工序内员工报警器报警并且停止作业;2)有控制点和处理方法;3)生产现场可根据实情进行对应10追溯从工序到作业员的追溯无课题★素性设备/工装齐全,运行无课题,设备开动率达到预定目标★素性模/夹具已全工装,验收时已完成小批量(>50件)的生产验证并达到量产条件。
已开始按计划执行保养计划。
按照量产初期要求对重点模/夹具执行强化措施★工艺参数管理制造条件规格包含日常点检、记录、设定、管理、变更等内容,造条件规格值的修改权限规定明确,重点工艺条件设定及更改需要设备密码保护等措施0功能防错检测的校准系统是合适的,检证工序也没问题20生产启停及首件生产开始前,维修后所有重要项目已检证。
试生产-生产鉴定表

2
拉伸1
988
988
4S
YJ-80T
拉伸1模具
3
ቤተ መጻሕፍቲ ባይዱ拉伸2
988
987
4S
YJ-80T
拉伸2模具
4
拉伸3
987
987
4S
YJ-80T
拉伸3模具
5
成型
987
987
4S
YJ-80T
成型模具
6
切边
987
987
4S
YJ-125T
切边模具
7
清洗
987
987
30分钟
8
生产过程描述(调试时间):
生产按作业指导书进行
宁波****汽车部件有限公司
生产-鉴定表-APQP
项目编号:
产品名称
或零件名
支架总成
图号
209590-00-04
生产形态
□样件生产□批量生产
■试生产:□4H□8H□2TP
生产日期
运行时间
各工序生产情况
工序编号
工序名称
操作人
投入数
合格数
单件
时间
设备型号
工装
主要参数
1
下料
1000
988
4S
YJ-125T
同意
签字: 年 月 日
签字: 年 月 日
检验者结论(存在主要问题及改进意见)(附检验报告):
目前新产品处于开发阶段需要严格按照程序进行检查
签字: 年 月 日
主管技术人员意见(问题及改进意见)(附工程能力指数)::
目前可以进行样件制造
签字: 年 月 日
车间意见(运行中存在的问题及改进建议):
小批量试产流程
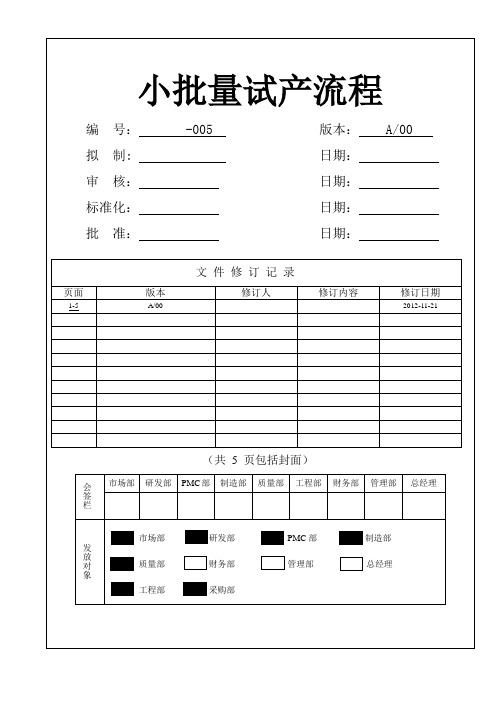
:
制定日期:2012-11-21
三阶文件
小批量试产流程
修订日期:2012-11-21
版本:A/00
页数:4/5
6.相关文件与记录
1
QP-001
《文件控制程序》
2
QP-020
《设计开发控制程序》
3
《试产通知单》
4
《订单评审表》
5
《试产问题跟踪表》
6
《小批量试产总结报告》
7
小批量试产报告

小批量试产报告(装配)
版本/修改状态:A/0
产品名称及型号
职行情况及小批量供货的质量2)生产工艺执行情况及小批量生产的质量
2) 成品检验:功能、结构及安全(含耐久性、IP测试及温升),有条件应进行跌落、震动试验及短路试验等
3) 生产后的总结并提出预防纠正措施5)输出文件的理正并开成适合批量生产的文件
4)其他
要求及计划安排
生产车间:数量:完成日期:
输出文件及工装是否齐备□是□否
签字(生产线长):
生产反馈:
1、来料:
2、工艺及质量:
3、成品检验:
4、生产总结:
签字:
原因分析:
改进措施:
签字:
审 批 备 注
质检部:
工程部:
销售部:
审批(车间主任):批准(生产经理):页码:第页/共页
第 页,共页
物料试产管理规范(含表格)
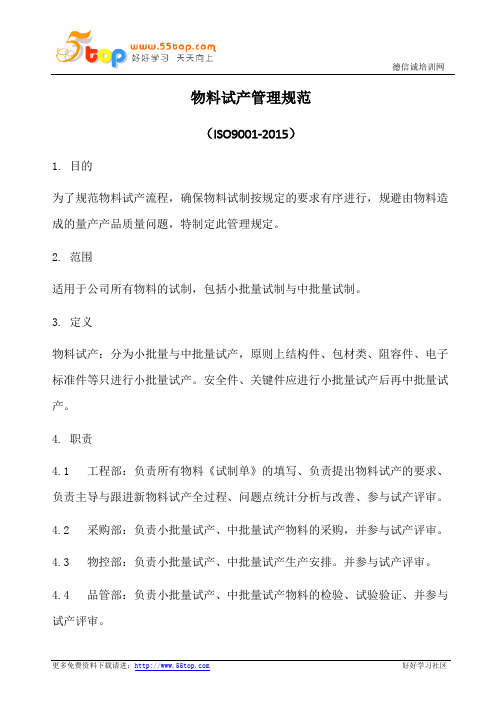
物料试产管理规范(ISO9001-2015)1. 目的为了规范物料试产流程,确保物料试制按规定的要求有序进行,规避由物料造成的量产产品质量问题,特制定此管理规定。
2. 范围适用于公司所有物料的试制,包括小批量试制与中批量试制。
3. 定义物料试产:分为小批量与中批量试产,原则上结构件、包材类、阻容件、电子标准件等只进行小批量试产。
安全件、关键件应进行小批量试产后再中批量试产。
4. 职责4.1 工程部:负责所有物料《试制单》的填写、负责提出物料试产的要求、负责主导与跟进新物料试产全过程、问题点统计分析与改善、参与试产评审。
4.2 采购部:负责小批量试产、中批量试产物料的采购,并参与试产评审。
4.3 物控部:负责小批量试产、中批量试产生产安排。
并参与试产评审。
4.4 品管部:负责小批量试产、中批量试产物料的检验、试验验证、并参与试产评审。
5. 作业内容5.1 新物料小批量试产5.1.1 工程部确定供应商所送样品为合格后,认为有必要进行小批量试产时,工程部负责开出试制单及相关试制条件及要求。
5.1.2 小批量试产物料到仓库后,IQC依据《来料检验规范》实施抽样检验判定、及不合格处理等。
5.1.3 物控部安排生产部进行试产。
5.1.4 生产部按照生产计划安排在要求机型上来试制,问题点记录在《试制单》上。
5.1.5 品质部对试产进行检验/试验验证,并做好检验/试验记录在《试制单》上。
5.1.6 工程部全程跟踪试产整个过程,对生产部提供技术支持,试产不良问题点进行原因分析。
5.1.7 针对试产问题点,由工程部进行汇总与统计,并进行分析与提出改善方案。
5.1.8 小批量试产后,由管理者代表裁决试产结论;若试产不通过时,决定是否继续小批量试产或者更换新供应商物料,并依5.1条款来执行。
品质部IQC 将试产结果扫描发放到相关部门。
5.2 物料中批量试产5.2.1物料小批量试产完成后,由采购部下中批量试产订单。
5.2.2中批量试产物料到仓库后,IQC依据《来料检验规范》实施抽样检验判定、及不合格处理等。
生产小批量试产工作流程表格

年 月 日,试产 套。
试产结果总结
试产负责人确认
分 发 单 位 □PMC □采购 □品质部 □生产部 □仓库 □其他:
制作
批准
作业流程:工程师填写试产申→请各部门确认→技术副总批准→分发
物料认可书
物料编号
名称
规格
要求完成时间
送样数量
物料类别 □重要物料 □一般物料 □辅料
申 请
认可目的
□降低成本 □新物料 □提高质量 □更换供货商 其它
附 □产品规格书 □物料规格书 □设计验证报告 □试产反馈单 □其 件 他:
申请人
审
核
评审项目及结果
项目要求
评审结果
评审结论 评 审 人
□通过 □ 未通过
□通过 □ 未通过
电 子
装 配
其 他 评审总结:
□通过 □ 未通过
□通过 □ 未通过
□通过 □ 未通过
□通过 □ 未通过
□通过 □ 未通过
□通过 □ 未通过
责任人
作业流程:试产人员填写→提交试产申请人
制 作:
试产评审报告
时 间: 产品 编号
年月日
名称/规格
评审 类别
□新产品首次评审 □新产品再次评审 □其他:
评审 目的
□评估生产工艺可行性 □其他:
评审 地点
评审时间
主持 人
参加 □技术部 □品质部 □电子车间 □包装车间 □总装车间 □物料部 部门 务部 □其他:
部 门 供货商名称
供货商状况态
□合格供方 未评估
认可形式 □认可实物(样品) □认可资料(图纸、说明书)
送样人
时间
适用机型
功能说明
小批量试产流程图
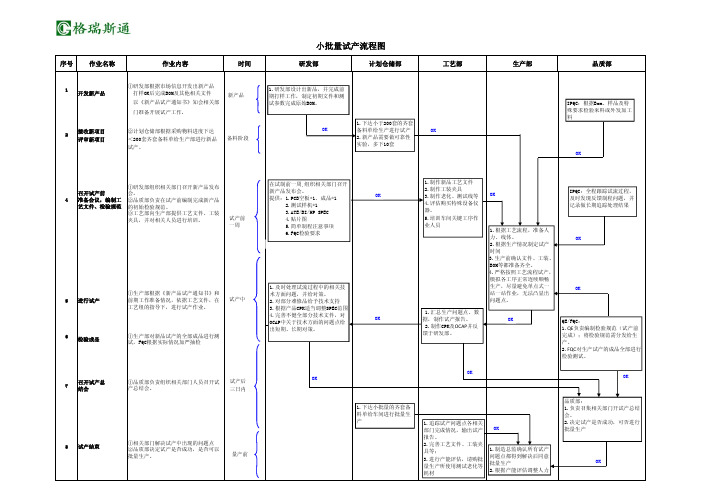
OK
1.制作新品工艺文件 2.制作工装夹具 3.制作老化、测试线等 4.评估购买特殊设备仪 器。 5.培训车间关键工序作 业人员
1.汇总生产问题点、数 据,制作试产报告。 2.制作CPK及OCAP并反 馈于研发部。
OK
IPQC:全程跟踪试流过程, 及时发现反馈制程问题,并
记录做长期追踪处理结果
1.根据工艺流程,准备人
会。
4 准备会议,编制工 ②品质部负责在试产前编制完成新产品
艺文件、检验规范 的初始检验规范。
③工艺部向生产部提供工艺文件、工装 夹具,并对相关人员进行培训。
试产前 一周
5 进行试产 6 检验成品
①生产部根据《新产品试产通知书》和 前期工作准备情况,依据工艺文件,在 工艺组的指导下,进行试产作业。
试产中
①生产部对新品试产的全部成品进行测 试,FQC根据实际情况加严抽检
7
召开试产总 结会
①品质部负责组织相关部门人员召开试 产总结会。
试产后 三日内
8 试产结束
①相关部门解决试产中出现的问题点 ②品质部决定试产是否成功,是否可以 批量生产。
量产前
在试制前一周,组织相关部门召开
新产品发布会。
提供:1.PCB空板*1、成品*1
备料阶段
1.研发部设计出新品,并完成前 期打样工作,制定初期文件和测 试参数完成原始BOM。
1.下达小于200套的齐套
OK
备料单给生产进行试产
OK
2.新产品需要做可靠性
实验,多下10套
生产部
品质部
IPQC:根据Bom、样品及特 殊要求检验来料或外发加工 料
OK
①研发部组织相关部门召开新产品发布
召开试产前
新物料试产跟踪单模板
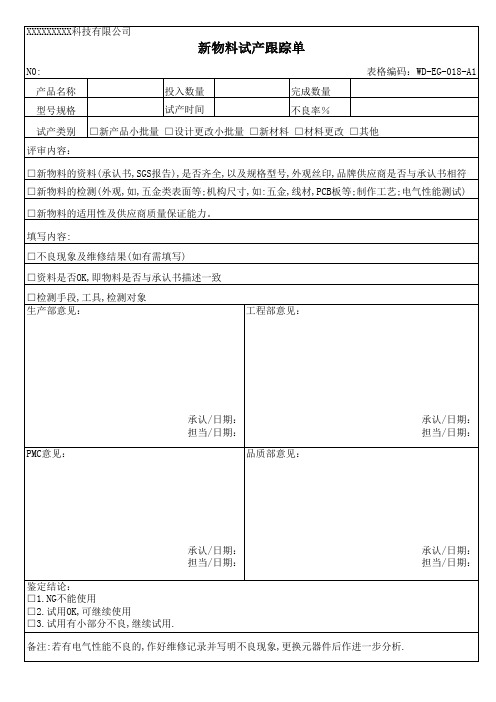
新物料试产跟踪单
N0:
表格编码:WD-EG-018-A1
产品名称 型号规格
投入数量 试产时间
完成数量 不良率%
试产类别 □新产品小批量 □设计更改小批量 □新材料 □材料更改 □其他
评审内容:
□新物料的资料(承认书,SGS报告),是否齐全,以及规格型号,外观丝印,品牌供应商是否与承认书相符 □新物料的检测(外观,如,五金类表面等;机构尺寸,如:五金,线材,PCB板等;制作工艺继续使用 □3.试用有小部分不良,继续试用.
备注:若有电气性能不良的,作好维修记录并写明不良现象,更换元器件后作进一步分析.
□新物料的适用性及供应商质量保证能力。
填写内容: □不良现象及维修结果(如有需填写) □资料是否OK,即物料是否与承认书描述一致 □检测手段,工具,检测对象 生产部意见:
工程部意见:
PMC意见:
承认/日期: 担当/日期:
品质部意见:
承认/日期: 担当/日期:
承认/日期: 担当/日期:
承认/日期: 担当/日期:
小批量试产报告

小批量试产报告
一、目的:
1、试验全制程设备运行情况;
2、试验全制程各物料试产运行情况;
3、测试各生产流程设计控制的产品品质;
4、评估生产制程的一次性良率
5、检验产品的最终品质
二、产前评估
1、产前会议及安排(详见产前会议记录)
2、投料安排(详见LOT卡)
生产型号:P1Hk13066D
生产数量:154 pnl
三、制作过程要求及跟进结果
1.生产流程设计:
开料→线路→蚀刻→打靶→阻焊→文字烤板→二次开料→二次打靶→通断测试→二次钻孔→V-CUT→成型→高压测试→FQC→OSP→FQC→FQA→包装。
在试产过程中各工序设备运转正常,无任何故障发生,完全能满足生产要求4、各流程品质情况:
附各生产工序记录、工艺分析记录及相关测试数据、QA检测数据
四、结论
1、经小批量试板生产,各工序设备运转正常;
2、当前各种物料能满足生产需求;
3、AOI、阻焊、文字、E-T、FQC工序一次性良率99%以上,高于90%标准;
4、各工序生产过程品质正常,无论是外观、功能还是制作要求均能完全满足客户要求。
综上所述,经小批量试产,我司设备、物料、在线品质控制均能满足生产需求,可批量生产。
试生产检查表
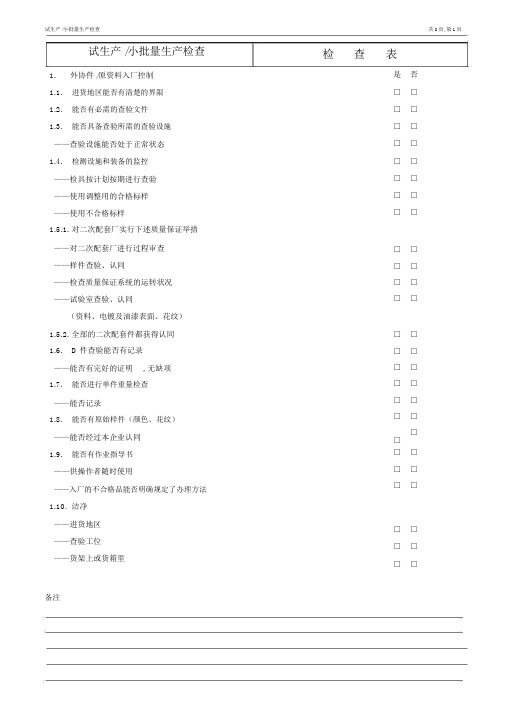
试生产 /小批量生产检查试生产 /小批量生产检查1.外协件 /原资料入厂控制1.1.进货地区能否有清楚的界限1.2.能否有必需的查验文件1.3.能否具备查验所需的查验设施——查验设施能否处于正常状态1.4.检测设施和装备的监控——检具按计划按期进行查验——使用调整用的合格标样——使用不合格标样1.5.1. 对二次配套厂实行下述质量保证举措——对二次配套厂进行过程审查——样件查验、认同——检查质量保证系统的运转状况——试验室查验、认同(资料、电镀及油漆表面、花纹)1.5.2. 全部的二次配套件都获得认同1.6. D 件查验能否有记录——能否有完好的证明, 无缺项1.7.能否进行单件重量检查——能否记录1.8.能否有原始样件(颜色、花纹)——能否经过本企业认同1.9.能否有作业指导书——供操作者随时使用——入厂的不合格品能否明确规定了办理方法1.10. 洁净——进货地区——查验工位——货架上或货箱里共8页,第1页检查表是否□□□□□□□□□□□□□□□□□□□□□□□□□□□□□□□□□□□□□□□□□□□□□□□□□□备注试生产 /小批量生产检查2.库房2.1.能否按照先进先出原则2.2.储藏预批量件,送入生产线前由质保部同意或由产品部同意2.3.隔绝库——用于外协件——用于自制件2.4.能否由以下部门参加隔绝库房的管理——质管部——生产车间——货物发运部门2.5.部件表记——使用标签——拥有可追忆性2.6.洁净——库区内——工作岗位——工位用具——工位用具能否有盖备注检查表是否□□□□□□□□□□□□□□□□□□□□□□□□□□□□□□试生产 /小批量生产检查3.生产线3.1.能否为专用生产线3.2.多产品使用同一设施加工3.3.能否确立了工艺文件3.4.能否确立了查验计划3.5.能否考证了重要部件的机器能力3.6.用于生产批量件的模具能否——制造完成——投入使用3.7.装置线流程——全自动——半自动——手动—— SPC 控制——逼迫控制(防差错装置)3.8.能否使用了适合的查验设施3.9.能否设置了SPC 质量控制点并作出表记3.10. D 件工位能否作了表记3.11. 工位上能否有作业指导书——关于废品能否有明确的办理规定——废品件能否有表记3.12. 能否有废品箱——有显然的表记——废品箱能否能够上锁3.13. 能否明确规定了返修件的物流路线3.14. 能否出缺点采集卡——能否洁净、有序地使用采集卡——剖析评论的频率——能否制定举措——能否有记录归档——能否对举措的有效性进行考证3.15. 过程工艺参数控制卡——适合——按规定实行3.16.对装置线和生产设施实行监控:—— SPC 控制——调整用标准样件——不合格样件——巡检——计算机数字控制及故障诊疗3.17.工位用具能否适合——数目能否知足生产需求——最后产品能否需另行包装检查表是否□□□□□□□□□□□□□□□□□□□□□□□□□□□□□□□□□□□□□□□□□□□□□□□□□□□□□□□□□□□□□□□□□□□□□□□□□□□□□□□□□□□□试生产 /小批量生产检查3.18.在投入使用压铸及注塑设施时,能否有明确的操作规程3.19.何部门对马上投入批量生产的设施进行查收——生产车间——品管部3.20.调整、监测设施参数或工艺参数的方式——自动——手动—— SPC 控制——巡检3.21.能否采纳了在线检测设施——检测部件的百分比: % ——终检能否考证了在线检测的质量特征防备3.22.能否洁净——锻造线——工位——工位用具内检查表是否□□□□□□□□□□□□□□□□□□□□□□□□□□□□□□□□□□□□试生产 /小批量生产检查共8页,第5页试生产 /小批量生产检查检查表3.23.工序及机器能力考证部件名称额定技术要求额定值公差Cmk Cpk试生产 /小批量生产检查共8页,第6页试生产 /小批量生产检查检查表4.终检4.1.能否有效地管理合格部件的表记——能否能够有效地追忆过程查验的结果4.2.查验项目4.3.查验方式—— 100% 查验——依据质量控制的要求进行抽检——目视查验——其余查验:4.4.合格率% 4.5.能否对查验结果作记录——能否作统计剖析——频率——能否制定了举措——成效能否监控4.6.废品件能否表记4.7.能否对不合格件进行剖析——能否记录缺点——能否制定相应的改良举措——能否进行了有效的考证4.8.针对废品件有无明确的办理方法——各相应的检查点能否拟订了作业指导书4.9.重要的单件及总成件能否有生产日期是否□□□□□□□□□□□□□□□□□□□□□□□□□□□□□□□□□□□□备注试生产 /小批量生产检查试生产 /小批量生产检查5.增补的质保手段5.1.能否进行功能及寿命试验——试验结果能否知足技术要求——试验直至部件无效否——频率:5.2.能否约定了批量生产的查验项目有哪些:5.3.对花纹能否监控——能否记录——频率:——检测仪器:5.4.能否确立对润滑脂用量及质量进行监控——能否记录——频率:——依据TL/进行查验能否记录查验结果——能否作统计剖析5.6.依据的查验结果能否制定了相应的举措——能否对举措的成效进行考证备注共8页,第8页检查表是否□□□□□□□□□□□□□□□□□□□□□□□□5.5.试生产 /小批量生产检查共8页,第7页试生产 /小批量生产检查检查表6.发货6.1.能否实行发货审查(或发货前的开箱查验)——频率:6.2.能否对样件实行目视检查,防止发货件与拟发货件混装或错装。
样品试制及小批量试产程序(含表格)
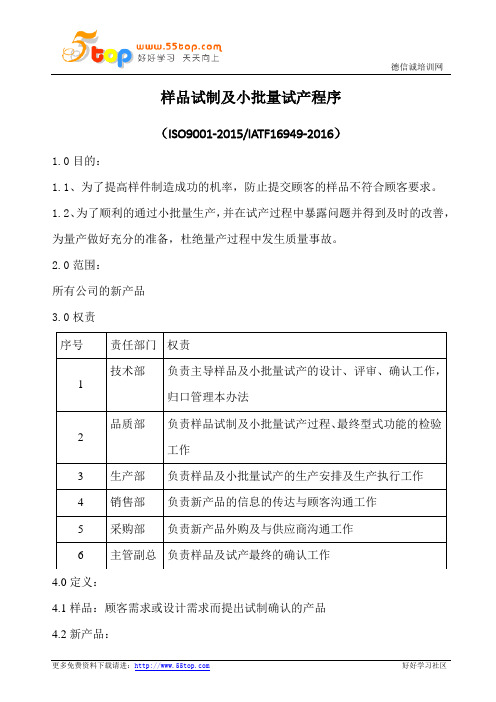
样品试制及小批量试产程序(ISO9001-2015/IATF16949-2016)1.0目的:1.1、为了提高样件制造成功的机率,防止提交顾客的样品不符合顾客要求。
1.2、为了顺利的通过小批量生产,并在试产过程中暴露问题并得到及时的改善,为量产做好充分的准备,杜绝量产过程中发生质量事故。
2.0范围:所有公司的新产品3.0权责序号责任部门权责技术部负责主导样品及小批量试产的设计、评审、确认工作,1归口管理本办法品质部负责样品试制及小批量试产过程、最终型式功能的检验2工作3 生产部负责样品及小批量试产的生产安排及生产执行工作4 销售部负责新产品的信息的传达与顾客沟通工作5 采购部负责新产品外购及与供应商沟通工作6 主管副总负责样品及试产最终的确认工作4.0定义:4.1样品:顾客需求或设计需求而提出试制确认的产品4.2新产品:4.2.1、新顾客或者顾客新开发的产品,且与公司之前生产的型号无100%重合4.2.2、因顾客或者内部设计变更后的第一批产品5.0作业内容:流程内容责任部门支持文件及记录1、销售部接到新顾客或者顾客新开发需要提交样品的需求时,遵守产品先期质量策划控制程序要求,填写顾客要求清单,并将所有与顾客沟通的信息,技术资料移转技术部销售部顾客要求清单2、技术部按产品先期质量策划控制程序要求,将新产品进行分类,依据新产品类型进行设计,组织多功能小组进行评审(I类产品会签评审。
Ⅱ、Ⅲ类产品会议评审),新产品设计信息记录于新产品开发目录3、设计评审结果为有修改要求的,技术部进行修改4、技术部提出设计验证计划及报告表,相关部门按验证计划在试制过程中进行验证。
技术部设计评审记录新产品开发目录设计验证计划及报告5、生产部负责安排样品试制及新产品试产的生产排期,确定好生产日期后提前三天以内部联络单通知相关部门做好相关试产,样品验证的准备6、样品及新产品试制时,必须由生产部现场负责人进行第一件的试制调试,并对员工进行培训教育,考核,技术部现场负责技术指导。
生产小批量试产表格

生产通知单生产单号开单日期产品编号生产数量名称规格开工日期年月日时完工日期年月日时式样配置客户销售订单特殊制程要求:□单个物料试产□整机批量试产□物料替代使用□其它:内容说明:完工记录完工入库数量完工入库时间完工异常说明:生产部:PMC:审核:试产确认表时间:年月日□试产产品□试产物料产品编号物料编号客户名称 /规格名称 /规格试产数量预计试产时间试产目的□试产新产品□试产新物料□评估新开发供应商的物料□其他:确认事项确认结果预计完成时间责任人物料齐备□已准备完善□未准备完善物料规格书□已准备完善□未准备完善物料认可书□已准备完善□未准备完善试工艺设备□已准备完善□未准备完善产工艺夹具□已准备完善□未准备完善准工位指导卡□已准备完善□未准备完善备排拉表□已准备完善□未准备完善确工位单价□已准备完善□未准备完善认制品单□已准备完善□未准备完善结论:拟于年月日,试产套。
试产重点事项试产结果总结试产负责人确认□电子工艺可操作性□总装工艺可操作性试产□配套工、夹具可操作性项□新物料的可操作性目及结果分发单位□ PMC□采购□品质部□生产部□仓库□其他:制作批准作业流程:工程师填写试产申→请各部门确认→技术副总批准→分发物料认可书物料编号名称规格要求完成时间送样数量申物料类别□重要物料□一般物料□辅料请认可目的□降低成本□新物料□提高质量□更换供货商□其它部供货商名称供货商状况态□合格供方□未评估门认可形式□认可实物(样品)□认可资料(图纸、说明书)送样人时间适用机型功能说明签收部门签收人 / 时间检验或测试项目及结果检项目名称项目要求检验或测试结果结论□合格□不合格验□合格□不合格或□合格□不合格测□合格□不合格综合结论:□合格□不合格□不需要试产确认□需要后续试产套。
试说明:认可或检验人审核试产结果总结:试制试制审核□采用□不采用结裁决:论作业流程:采购填单→认可→试制→裁决试产反馈单时间:年月日部门:产品编号名称规格试产数量试产时间年月日试产结果反馈NO试产问题描述改善措施预计完成时间责任人作业流程:试产人员填写→提交试产申请人制作:试产评审报告时间:年月日产品编号名称 /规格评审类别□新产品首次评审□新产品再次评审□其他:评审目的□评估生产工艺可行性□其他:评审地点评审时间主持人参加部门□技术部□品质部□电子车间□包装车间□总装车间□物料部□业务部□其他:附件□产品规格书□物料规格书□设计验证报告□试产反馈单□其他:申请人审核评审项目及结果电子装配其他评审总结:项目要求评审结果评审结论评审人□通过□未通过□通过□未通过□通过□未通过□通过□未通过□通过□未通过□通过□未通过□通过□未通过□通过□未通过□通过□未通过□通过□未通过□通过□未通过□通过□未通过□通过□未通过□通过□未通过□通过□未通过评审结论:□评审通过□评审未通过□须完成如下改善:NO待改善项目改善措施要求完成时间责任人总结人审核品质部确认作业流程:评审申请→组织评审→评审总结→审核→品质部确认。
- 1、下载文档前请自行甄别文档内容的完整性,平台不提供额外的编辑、内容补充、找答案等附加服务。
- 2、"仅部分预览"的文档,不可在线预览部分如存在完整性等问题,可反馈申请退款(可完整预览的文档不适用该条件!)。
- 3、如文档侵犯您的权益,请联系客服反馈,我们会尽快为您处理(人工客服工作时间:9:00-18:30)。
□评估生产工艺可行性□其他:
评审地点
评审时间
主持人
参加部门
□技术部□品质部□电子车间□包装车间□总装车间□物料部□业务部□其他:
附件
□产品规格书□物料规格书□设计验证报告□试产反馈单□其 他:
申请人
审 核
评审项目及结果
项目要求
评审结果
评审结论
评审人
电子
□通过□未通过
□通过□未通过
□通过□未通过
生产通知单
生产单号
开单日期
产品编号
生产数量
名称
规格
开工日期
年月日时
完工日期
年月日时
式样
配置
客户
销售订单
特殊制程要求:□单个物料试产□整机批量试产□物料替代使用□其它:
内容说明:
完工记录
完工入库数量
完工入库时间
完工异常说明:
生产部:
PMC:审核:
试产确认表
时间:年月日□试产产品□试产物料
产品编号
名称/规格
制作
批准
作业流程:工程师填写试产申→请各部门确认→技术副总批准→分发
物料认可书
申请部门
物料编号
名称
规格
要求完成时间
送样数量
物料类别
□重要物料□一般物料□辅料
认可目的
□降低成本□新物料□提高质量□更换供货商□其它
供货商名称
供货商状况态
□合格供方□未评估
认可形式
□认可实物(样品)□认可资料(图纸、说明书)
结
论
□采用□不采用
裁决:
作业流程:采购填单→认可→试制→裁决
试产反馈单
时间:年月日部门:
产品编号
名称
规格
试产数量
试产时间
年月日
试产结果反馈
NO
试产问题描述
改善措施
预计完成时间
责任人
作业流程:试产人员填写→提交试产申请人制作:
试产评审报告
时间:年月日
产品编号
名称/规格
评审类别
□新产品首次评审□新产品再次评审□其他:
工位指导卡
□已准备完善□未准备完善
排拉表
□已准备完善□未准备完善
工位单价
□已准备完善□未准备完善
制品单
□已准备完善□未准备完善
结论:拟于年月日,试产套。
试产项目及结果
试产重点事项
试产结果总结
试产负责人确认
□电子工艺可操作性
□总装工艺可操作性
□配套工、夹具可操作性
□新物料的可操作性
分发单位
□PMC□采购□品质部□生产部□仓库□其他:
□通过□未通过
□通过□未通过
装配
□通过□未通过
□通过□未通过
□通过□未通过
□通过□未通过
□通过□未通过
□通过□未通过
其他
□通过□未通过
□通过□未通过
□通过□未通过
□通过□未通过
评审总结:
评审结论:□评审通过□评审未通过□须完成如下改善:
NO
待改善项目
改善措施
要求完成时间
责任人
总结人
审核
品质部确认
作业流程:评审申请→组织评审→评审总结→审核→品质部确认
物料编号
名称/规格
客户
试产数量
预计试产时间
试产目的
□试产新产品□试产新物料□评估新开发供应商的物料□其他:
试产准备确认
确认事项
确认结果
预计完成时间
责任人
物料齐备
□已准备完善□未准备完善
物料规格书
□已准备完善□未准备完善
物料认可书
□已准备完善□未准备完善
工艺设备
□已准备完善□未准备完善
工艺夹具
□已准备完善□未准备完善
送样人
时间
适用机型
功能说明
检
验
或
测
试
签收部门
签收人/时间
检验或测试项目及结果
项目名称
项目要求
检验或测试结果
结论
□合格□不合格
□合格□不合格
□合格□不合格
□合格□不合格
综合结论:□合格□不合格□不需要试产确认□需要后续试产套。
说明:
认可或检验人
审核
试
制
试产结果总结:
结论:□可用□不可用□其它:
试制
审核