OpenCFDver1.7.2使用手册
OpenCms中文用户手册
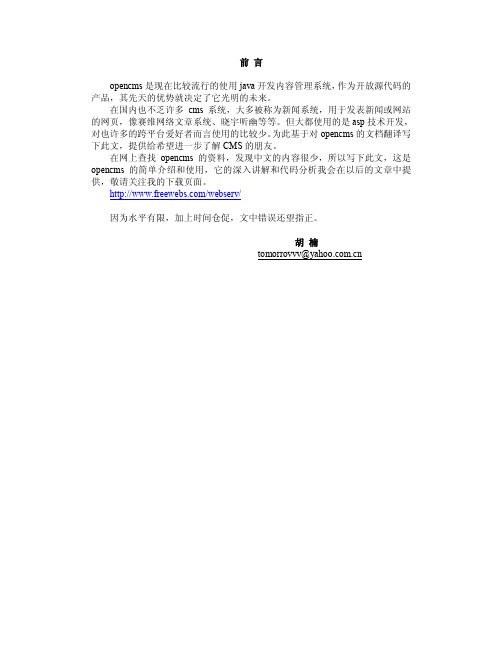
前言opencms是现在比较流行的使用java开发内容管理系统,作为开放源代码的产品,其先天的优势就决定了它光明的未来。
在国内也不乏许多cms系统,大多被称为新闻系统,用于发表新闻或网站的网页,像赛维网络文章系统、晓宇听幽等等。
但大都使用的是asp技术开发,对也许多的跨平台爱好者而言使用的比较少。
为此基于对opencms的文档翻译写下此文,提供给希望进一步了解CMS的朋友。
在网上查找opencms的资料,发现中文的内容很少,所以写下此文,这是opencms的简单介绍和使用,它的深入讲解和代码分析我会在以后的文章中提供,敬请关注我的下载页面。
/webserv/因为水平有限,加上时间仓促,文中错误还望指正。
胡楠tomorrovvv@1. OpenCms 用户手册1.1. 介绍1.1.1.什么是OpenCmsOpenCms是一套基于开放源代码标准的内容管理系统。
无论是复杂的内部还是外部网站它都可以快速高效的进行创建,维护和管理。
OpenCms可以让您在非在线的情况下建立复杂的站点,当您编辑满意时再发布。
持有不同许可的用户在非在线的项目中可以同时执行团队工作。
您可以用OpenCms来轻松的实现成员的合作,进行编写,设计和管理内容等工作。
您也可以管理项目的流程。
当项目令人满意地完成了,非在线的项目可以通过项目管理器来进行发布。
在非在线情况下完成并发的修改和维护。
站点所需的升级1.2.第一部分:OpenCms 演示下面的演示是基于真实的情景并以你的适用与快速运行设计的。
Org.opencms.welcome模块一定已经在您的OpenCms系统中了(使用OpenCms的默认安装)。
打开您的网络浏览器并输入http://localhost:8080/opencms/opencms可以连接OpenCms欢迎界面。
OpenCms欢迎界面(图1.1)。
导航器位于页面的首部提供了所有页面的联接。
单击“Release note”。
VN2700系列安装指南说明书
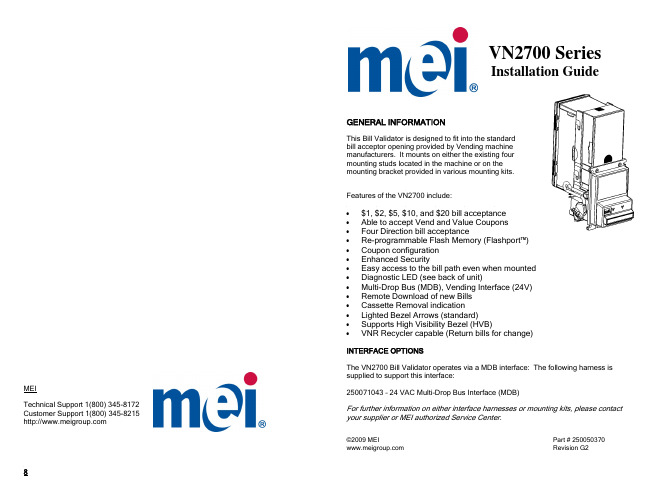
MDB MASTER TXD SERIAL LINK TXD DC RETURN
Pin 17 Pin 18 Pin 19
MDB SLAVE COMMON MDB SLAVE RXD MDB SLAVE TXD
Pin 20 Pin 21 Pin 22
24 VAC NEUTRAL POWER
KEY NOT USED
2
Electronic copies of this manual will not have the coupon
included. Please contact MEI if you need a configuration coupon.
7
PINOUT INFORMATION FOR 30 PIN CONNECTOR
8. Remove bills and check status • Instructions for bill removal are on label at the back of magazine. • Once the magazine is installed, verify that the LED status indicator remains steady ON.
3
COUPON CONFIGURATION (ALL SWITCHES OFF)
1. Carefully cut the coupon around the edges. Copies are usable if made on a standard, carbon based, non-color copier, AND have the same dimensions as a $1 bill (66 mm wide by 155 mm long).
OpenCFDver1.7.2使用手册

据文件
定义模块决定
建立一个子目录,将这些文件拷贝到这个目录,在并行计算机上提交作业即 可 运 行 。 不 同 计 算 机 上 提 交 作 业 的 方 法 不 同 , 例 如 mpirun -np 32 ./opencfd-1.7.2.out, 或 bsub -n 32 "mpijob ./opencfd-1.7.2.out" 等。 具体作 业提交方法可查阅该计算机系统的使用手册。
Mass_target
12000.d0 288.15
16 17 18 19 20 21 22 23 24 25 26 27 28 29 30 31 32 33 34 35 36 37 38 39 40 41 42 43 44 45
# dt
end_time NUM_Time_Advance 10000.d0 3 10
# Scheme_z0 NL NR 204 # IBC 101 # nk 1 # N_ana 1 #Ian1 Kstep_ana1 nk nr 110 100 1 0 IF_Statistics_init 1 nr 0 nk 0 0 nr 1 0 Tw 1.d0
Turb_model ! RANS & LES modeling 0
# npx0 npy0 npz0 2 4
# N_MSG_SIZE 0
BLOCK_COMPACT_Z BLOCK_COMPACT_Y OCFD_Barrier 5 5 Iperiodic(1:3) 1 SLz 3.14159265358979d0 Pr
4
0
# Iflag_grid(1),Iflag_grid(2),Iflag_grid(3) 0 # SLx, 1 SLy 0
5
ORG 447X Series 评估套件快速引导说明书

ORG447X Evaluation Kit Quick Start Guide1.P a c k a g i n g L i s tThe ORG447X Evaluation Kit contains:4472 module mounted on the Demo BoardB.Passive patch antenna assemblyB to UART cableD.Support CD2.S e t u p2.1 Open CD. Select ORG447X series from the main menu.2.2 Install FTDI USB-UART driver by pressing Driver button.The driver setup is done in silent mode.The presence and enumeration of the Virtual COM port can be verified via ControlPanel→System→Device Manager.2.3 Install SiRFLive software by pressing SiRF Live Setup button.Follow on-screen instructions during SiRFLive setup process.Uninstall any previous SiRFLive version before current setup attempt.2.4 Connect antenna assembly cable into RF input connector.2.5 Connect FTDI USB to UART cable between the Demo Board and the PC.3.E v a l u a t i o n K i t E s s e n t i a l s3.1 Patch antennaGPS patch antenna should be placed up towards the sky to keep GPS satellites in view. 3.2 Tactile switchThe tactile switch is used to wake up to GPS module from the Hibernate state of one of the low power modes, typically for triggering Push-To-Fix (PTF™).4.S i R F L i v e E s s e n t i a l s4.1 Linking with EVKA. Open SiRFLive by clicking desktop iconB. Press Receiver Settings button on the main toolbarC. Rx Port Settings window will openSelect GSD4e in Product Family box.Select RS232/USB for Physical Connection.Select the Virtual COM port as assigned by the driver. Typically it would be the highestavailable.Select 4800 for Baud Rate.Press OK button when finished.D. Press Connect button on the main toolbarThe NMEA messages will start bursting in Debug View window.4.2 Switching ProtocolsExtended functions like TTFF measurement are available after switching the receiver into OSP binary protocol.A. Goto Receiver → Command → Switch ProtocolsB. Switch Protocols window will openClick Set button to transfer the EVK into OSP binary protocol @ 115,200 bps.4.3 The TTFF MeasurementsA. Press TTFF button of the main toolbarB. TTFF/Nav Accuracy window will openC. Click the Setup Reference Location button (for accuracy measurements)D. Set Reference Location window will openSelect USER_DEFINED under Reference Location.Input location name.Press Fix Pos button to use current position coordinate.Press Set as Default button to use current location for position reference.Press OK button when finished.E. Press Reset button on the main toolbar.F. Reset window will openSelect Reset Mode.Reset Modes are:Hot Start - Ephemeris, Almanac, clock and last position data are kept in receiver’s RAM.Warm Start (No Init) – Ephemeris and last position data are discarded.Warm Start (Init) - Ephemeris data is discarded, position data is loaded.Cold Start – All data except reference Almanac is discarded.Factory Reset – All data, including reference Almanac and power settings is discarded.Factory (Clear XO learning) – Not relevantFactory (Keep Flash/Eeprom data) – Not relevantCheck Enable Navlib Data box and Enable Development Data box.Press Send button to start the procedure.The EVK will perform reset sequence.G. TTFF/Nav Accuracy window will show TTFF measurements data4.4 Sequential TTFF Measurements - LOOPIT functionA. Goto Receiver → Automation Test → LoopitB. Information pop-up window will openPress Yes button to continue.C. Loopit window will openSelect the Reset TypeSet the number of iterations.Checking Allow Early Iteration Completion box is an option to allow the next reset to be sent immediately after the previous cycle finish.Leave Switch Protocol/Baud on Factory and Perform Aiding on Factory unchecked.Press Start button to commence the procedure.D. Log file pop-up window will openPress Yes button to continue.H. TTFF/Nav Accuracy window will show sequential TTFF measurements data4.5 Data LoggingA. Press Log File button on the main toolbarB. Log File window will openPrior to logging set the receiver to appropriate data protocol.For NMEA messages log select TXT format in Log Format combo box.The log file will be created with .TXT extension.For OSP binary messages log select GPS format in Log Format combo box.The log file will be created with .GPS extension.Press Start button to commence logging.Press Log File button while logging to stop the procedure.ORG447X Series Evaluation Kit Quick Start Guide Fully Integrated GPS ModuleDocument number: 120111 Fortechnicalquestions,contact:****************** Revision: A01 15-11-1111 4.6 Data PlaybackA. Press Play File button on the main toolbarB.File browser will openSelect saved file.C.File Playback Warning pop-up will openPress Yes button to continue.D. Navigate through recorded file with toolbar controlsE. View windows are selected via main toolbarFor extended support for SiRFLive software refer to the SiRF Live Manual on this CD.。
Atomos Shinobi 7 快速启动指南说明书

ContentsThank you for purchasing the Atomos Shinobi 7, utilizingprofessional HD-SDI and HDMI connectivity to monitor up to professional 4Kp60 (via HDMI) and 1080p60 (via 3G-SDI). The class leading AtomHDR monitor lets you visualize 10+ stops of dynamic range, with 2200nits brightness for daylight viewing and 10-bit processing for smooth gradations. Please take the time to read through this Quick Start Guide and register your product for free updates.DOWNLOAD THE FULL SHINOBI 7 USER MANUAL /supportIntroductionIntroduction . . . . . . . . . . . . . . . . . . . . . . . .2Checklist . . . . . . . . . . . . . . . . . . . . . . . . . .3Y ou will also need . . . . . . . . . . . . . . . . . .3AtomX Accessories . . . . . . . . . . . . . . . .3Getting started . . . . . . . . . . . . . . . . . . . . .4Connect and Power-up . . . . . . . . . . . . .4Input . . . . . . . . . . . . . . . . . . . . . . . . . . . . . . .5Physical features . . . . . . . . . . . . . . . . . . .6T ouchscreen/User Interface . . . . . . . .8Monitor assist tools . . . . . . . . . . . . . . . .9Warranty & Conditions . . . . . . . . . . . . .10Notifications . . . . . . . . . . . . . . . . . . . . . .11Y ou will also need (sold separately)SDI CableSDI cables are robust physically and electrically. You should rarely have problems with signal transmission unless your cables are either damaged or too long. Please remember that SDI cables use locking connectors and will not simply pull out if they are pulled or tripped over. They are therefore a significant trip hazard, and also a hazard to your equipment, which may be damaged if the cables are mishandled or of a low grade. Please ensure you test and check your SDI cables; for longer runs cables of a Belden 1694A specification are recommended.HDMI CableAtomos have a range of HDMI cables with die cast connectors and coiled cables in a range of lengths and connections (sold separately).Checklistq 1 x Shinobi 7q 1 x AC Power Adaptor q 1 x Quick Start GuideAtomos have a range of accessories tailored to usage with the Shinobi 7. Visit your nearest Atomos reseller to discover the range of available accessories that will get you up and running enhance your production workflow.Batteries and power:- ATOMOS 5200mAh 4 Cell NPF Style Battery NP-770- ATOMOS 7800mAh 6 Cell NPF Style Battery NP-970- ATOMOS Fast Battery Charger with Multi plug PSU -ATOMOS Power Kit for all Atomos 5” & 7”Monitor RecordersCables:-ATOMOS AtomFLEX HDMI 4K60p Full to Full (30cm/40cm/50cm)-ATOMOS AtomFLEX HDMI 4K60p Full to Micro (30cm/40cm/50cm)- HDMI Coiled cable 4Kp30 Full to Full (30cm/50cm)- HDMI Coiled cable 4Kp30 Full to Micro (30cm/50cm)Connect and power-upBatteryShinobi 7 provides dual battery slots that combined with the DC input allow for continuous power operation. With both batteries connected Shinobi 7 will draw power from them simultaneously, if a battery is removed it will automatically switch over to the second battery or the DC power input. This allows you to swap out a depleted battery without having to shut down the monitor.Touching the battery icons in the top right of your screen will allow you to accurately see remaining battery life. Refer to the User Manual for more information.AC/DC PowerAlternatively power your Shinobi from mains power using the included AC Power Adaptor. Simply attached the AC power adaptor to mains power, carefully attach to the DC port on theShinobi 7 and rotate the locking nut to secure.The DC input port can also be used with the optional AtomosDTAP to DC cable (ATOMDTPCB2) to supply power to the Shinobi 7 from a DTAP power output.Battery indicators will show that no batteries are attached andthe unit is being powered via DC power input.PowerYou can power the device using the supplied AC power supply, but if you plan to use a battery we recommend you fully charge before use.We recommend using Atomos NP-F series batteries.Getting startedInputAccess Input MenuINT o access the Input Menu simply tap the INPUT (IN) area located in the top left of the Shinobi screen. Choose signal - HDMI or SDISOURCEDisplays the input source currently connected to the Shinobi, simply tap to toggle between HDMI & SDI inputs. Y ou can have both HDMI and SDI inputs connected at the same time and use this menu to toggle between active inputs.HDMIBattery releaseOn/Off Remote/CalibrationportHeadphone/audio outSDCardSlot1/4” screw hole1/4” screw holeOn/Off and Screen LockT o turn the Shinobi 7 on, press the power button. T o shut down, hold the button for at least 4 seconds (until unit turns off).SDI InThe SDI inputs support 3G in both level A and B standards. SDI OutThis is for connection to an external monitor or other device with an SDI input. It carries a loop-through of the incoming SDI (limited to 3G 1080p60) or HDMI signal in monitor and standby mode. HDMI InHDMI input connection to the Shinobi 7 supports up to 4Kp60. HDMI OutHDMI output connection from the Shinobi 7 supports up to 4Kp60. Remote Calibration PortThe Shinobi 7 screen can be calibrated using the X-Rite i1Display Pro. T o connect you will need a USB to serial cable. (ATOMCAB004) Battery ReleasePress the release buttons and slide batteries upwards to remove. Headphone / Audio outStandard 3.5mm audio output for audio monitoring.Screw Holes / Mounts + LockPin Holes (Arri)1/4” screw hole top and bottom.SD Card SlotUse SD cards to load LUT s and/or update firmware.T ouchscreen / User InterfacePress to access settings for monitoring toolsT ap to reveal monitoring features. T ap again to hide.See next pageWarranty & ConditionsNoticeCopyright © 2021 ATOMOS Global Pty Ltd (‘referred to as ATOMOS’). All rights reserved. All information in this document is subject to change without notice. No part of the document may be reproduced or transmitted in any form, or by any means, electronic or mechanical, including photocopying or recording, without the express written permission of ATOMOS. A reference to ATOMOS includes its related entities, subsidiaries and parent company. TrademarksShinobi 7 / ATOMOS are registered trademarks of ATOMOS Pty Ltd. Apple, the Apple logo, AppleShare, AppleTalk, FireWire, iPod, iPod Touch, Mac, and Macintosh are registered trademarks of Apple Inc. Final Cut Pro, QuickTime and the QuickTime Logo are trademarks of Apple Inc. All other trademarks are the property of their respective holders. International Hardware Limited Warranty(1 Year Standard/3 Years if registered)ATOMOS warrants that:• The main product, not including the IPS screen, or any external accessories, will be free from defects in materials and workmanship for a period of 1 year from the date of purchase; or 3 years upon completion of product registration within 1 year from the date of purchase at • The TFT/LCD, batteries, case and master caddies will be free from defects in materials and workmanship for a period of 1 year from the date of purchase regardless of registration. This warranty is exclusively for the benefit of the original purchaser and is not assignable or transferable.If during the warranty period the product is shown to be defective ATOMOS may at its option:a) replace the goods or supply equivalent ones, b) repair the goods, c) pay the cost of replacing the goods or of acquiring equivalent ones and d)paying the cost of having the goods repaired; The customer must notify ATOMOS of any defect in the goods in writing prior to the expiry of the warranty periods set out above. The customer will be solely responsible for returning the goods to ATOMOS or its authorized distributor. Upon acceptance of a warranty claim by ATOMOS, where ATOMOS repairs or replaces the goods, it willbe responsible for reasonable shipping costs incurred in sending the goods to the Customer, provided that customer is located in a country in which ATOMOS has an authorized distributor or repair center or agent.Warranty ExclusionsThis warranty applies only to defects in workmanship and does not cover defects caused by:• A failure to comply with the then current operating instructions issued by ATOMOS;• Neglect;• Improper or negligent acts or omissions;• Unauthorized repairs or attempted repairs;• Tampering with or modification of the goods;• Connection to incompatible equipment or power sources;• Exposure to water or weather;• Exposure to magnetic fields or corrosive liquids or substances; EXCEPT AS STATED IN THIS WARRANTY, ATOMOS, IT’S VENDORS, AGENTS, RESELLERS AND DISTRIBUTORS DISCLAIM IN THEIR ENTIRETY ALL OTHER WARRANTIES, EXPRESS OR IMPLIED, INCLUDING WITHOUT LIMITATION ALL WARRANTIES OF MERCHANTABILITY OR FITNESS FOR A PARTICULAR PURPOSE. THE REMEDIES OUTLINED IN THIS WARRANTY ARE THE EXCLUSIVE REMEDY A CUSTOMER HAS ARISING FROM DEFECTIVE GOODS WHICH ARE SUBJECT TO THE WARRANTY. ATOMOS DOES NOT WARRANT THAT THE GOODS WILL OPERATE IN A MANNER WHICH IS ERROR FREE, OR UNINTERRUPTED. THE GOODS ARE NOT INTENDED TO BE THE PRIMARY OR ONLY DATA STORAGE DEVICE FOR DATA – CUSTOMERS ARE SOLELY RESPONSIBLE FOR BACK UP AND PROTECTION OF DATA.Software License AgreementIMPORTANT, PLEASE READ CAREFULLY. THIS IS A LICENSE AGREEMENT. This ATOMOS software, related documentation, any included sample images and other files (the “Software”), is protected by copyright laws and international copyright treaties, as well as other intellectual property laws and treaties. The Software is licensed, not sold.This End User License Agreement (“EULA”) is a legal agreement between you (either an individual or a single entity) and ATOMOS with regard to the copyrighted Software provided with this EULA. Use of the Software provided to you by ATOMOS in whatever form or media, will constitute your acceptance of these terms, unless separate terms are provided by the software supplier, in which casethis EULA, do not download, install copy or use the Software. By installing, copying or otherwise using the Software, you agree to be bound to the terms of this EULA. If you do not agree to the terms of this EULA, ATOMOS is unwilling to license the Software to you.1. Eligible licensees. This Software is available for license solely to purchasers of the ATOMOS Shinobi 7, who have purchased a unit manufactured by ATOMOS Shinobi 7 and purchased through an ATOMOS authorized reseller, with no right of duplication or further distribution, licensing or sub-licensing.2. License Grant. ATOMOS grants you a personal, non-transferable andnon-exclusive right to use the copy of the Software provided with this EULA.Y ou agree you will not copy the Software except as necessary to use it with the ATOMOS Shinobi 7. Y ou agree that you may not copy the written materials accompanying the Software. Modifying, reverse engineering, translating, renting, copying, transferring or assigning all or part of the Software or any rights granted hereunder, to any other persons or reverse engineering the hardware on which the Software runs, is strictly prohibited. The software is license, not sold. Y ou acknowledge that no title to intellectual property in the Software is transferable to you. Y ou further acknowledge that title and full ownership rights to the Software will remain the exclusive property of ATOMOS and/ or its suppliers, and you will not acquire any rights to the Software, except as expressly set forth above. All copies of the software will contain the same proprietary notices as contained in or on the Software. All title and copyrights in and to the Software (including but not limited to any images, animations, video, audio, text incorporated), the accompanying printed materials, and any copies of the Software are owned by ATOMOS or its suppliers.3. Reverse engineering. Y ou agree that you will not attempt, and if you area corporation, you will use your best efforts to prevent your employees and contractors from attempting to reverse compile, derive circuits, modify, translate or disassemble the Software and/or the ATOMOS Shinobi 7 in whole or in part. Any failure to comply with the above or any other terms and conditions contained herein will result in the automatic termination of this license and the reversion of the rights granted hereunder by ATOMOS.ATOMOS reserves the right to terminate this license without prejudice to any additional recourse ATOMOS may have against you if you violate any of its terms and conditions.NotificationsUSAWARNING:This product contains the chemical lead (Pb)which is known to the State of California to cause cancer.For more information, visit 11For more detailed instructions and important up-to-date information regarding Shinobi 7 please download the complete Shinobi 7 User Manual from:/support© Atomos 2021. TM ® All trademarks and registered trademarks are the property of their respective owners.。
分布式生成(DG)手册第7版第1次修订版说明书

Distributed Generation (DG) ManualDecember 3, 2020 (7th Edition)Revision 1.0December 3, 2020 Application for Interconnection of DG Page 46 of86Appendix DApplication for Interconnection of DGAPPLICATION FOR INTERCONNECTION OF DISTRIBUTEDGENERATION (DG Application)Must be completed for any size or type of DG1.All DG Owners must complete this Section regardless of size or typeDG Owner’s Name(s):__________________________________________________________DG Owner’s Mailing Address (specific including zip code):____________________________DG Site Address (include zip code):DG Owner’s Email Address: _____________________________________________________ Account Number (if applicable):Telephone (normal): (emergency):Information Prepared and Submitted By:Name:Address:Contact Number (24hrs. / 7days a wk.):______________________________________________ Email:Signature (required): Date:Name of DG Owner or DG Owner’s designated representative who can be contacted by CPS Energy at any time throughout ownership of DG system in case of emergency or important issues concerning the DG System.DG Owner or DG Owner’s designated representative(if not same as above):Contact Number (24hrs. / 7days a wk.):Email:Installer/Contractor (if not same as above):Contact Number (24hrs. / 7days a wk.):Email:The following information shall be supplied by the DG Owner or DG Owner’s designated representative and/or contractor. All applicable items must be accurately completed in order that the DG Owner’s generating facilities may be effectively evaluated by CPS ENERGY for interconnection.Is this DG System an upgrade to the existing DG System installed? Yes No Number of units/Configuration of modules:Module manufacturer:Type (Synchronous, Induction, Backup or Inverter):Fuel Source Type (Solar, Natural Gas, Wind, etc.):Kilowatt rating for this installation (95° F): kW ac Kilowatt rating for existing installation (95° F) (if applicable): kW ac Total aggregated Kilowatt Rating for DG installation (95° F): kW ac Kilovolt-Ampere Rating (95° F): kVA ac Power Factor:Voltage Rating: V ac Amperage Rating: A ac Frequency: Hz Number of Phases:If DG is a Grid-Tied system, amount expected to be exported to grid: kW acInstructions:For DG Systems with total capacity (including aggregate) less than 25 kW ac in a single parcel of property with single or multiple meters, complete section 2 and initial, sign, and date the last page of the application.For DG Systems with total capacity (including aggregate) of 25 kW ac and greater in a single parcel of property with single or multiple meters, or DG Systems of any size within the Downtown Network Area, complete sections 3 to 6 and initial, sign, and date the last page of the application.2.DG Systems with Total Capacity (Including Aggregate) Less Than 25 KW ac ina Single Parcel of Property with Single or Multiple MetersSubmit the following information:Detailed operational one-line diagramSite planMeter loop drawing (elevation view)/ Proposed Equipment Layout“Visible” disconnect device or breaker and include the following ratings as applicable: Full Load Rating, Momentary Rating, Interrupting ratingShow all protective devices and include as applicable size, rating, manufacturer, type, style, model, settingsNote: All drawings to scale – email in PDF format to****************Expected Start-up Date:Please describe the Normal Operation of Interconnection, provide operating procedure: (examples: provide power to meet base load, demand management, standby, back-up, other)Also, will the DG parallel continuously with CPS Energy? If only paralleling momentarily, forIf the type is not an Inverter, provide RMS Symmetrical Short Circuit Current and X/R Ratio at Rated Voltage at point of common coupling for:Line-to Ground Fault: X/R:3-Phase Fault: X/R:Wiring ConfigurationSingle or 3-Phase Winding Configuration Neutral Grounding System Used: (Choosewell if applicable6.Anti-Islanding ProtectionCPS Energy Instructions: Please describe in detail the anti-islanding protection scheme, as well as, the worst-case time delay for shutting down the DG system. Indicate how long it takes the DG system to disconnect from the grid. Anti-islanding sensing must meet the NEC, IEEE 1547-2018, and UL 1741.Specify the type of DG system you are applying for below:I am applying for a DG Systems with total capacity (including aggregate) of less than25 kW ac in a single parcel of property with single or multiple metersI am applying for a DG Systems with total capacity (including aggregate) of 25 kW ac orgreater in a single parcel of property with single or multiple metersIs the DG system on the Downtown Distribution Network system?--------------------------------------------------------------------------------------------------------------------- CPS Energy internal use onlyCPS Energy Reviewer Comments:CPS Energy Reviewer Name (Print):Signature: Date:By executing this Application, the DG Owner, or its authorized representative, certifies that the information in the Application is true and accurate and DG Owner certifies that they have read, understand and agree to comply with all CPS Energy terms and conditions as stated or incorporated in the current DG Manual, including the Interconnection Requirements and the Interconnection Terms,applicable CPS Energy Rates and Riders, Rules and Regulations and Service Standards, which shall prevail over any inconsistent provisions in any form or acknowledgement submitted by the DG Owner. Any additional terms or different terms proposed by DG Owner are rejected unless expressly agreed to in writing by CPS Energy.DG Owner or authorized representative printed name, Title/Position:__________________________________________Signature: ____________________________ Date: ______________________________。
AIX 7.2快速入门指南说明书

AIX Installation Quick Start GuideVersion 7.2Quick Start GuideThis guide gets you started with a typical installation for the AIX Version 7.2 operating system.Product overviewUse these steps to install the Base Operating System (BOS) for AIX®from physical DVD media. The steps guide you through a new installation, also called an overwrite installation.1Step 1: Completing the prerequisitesPrepare for a new and complete overwrite:v Ensure that you have at least 4 GB of memory and a minimum of 20 GB of physical disk space. For additional release information, see the AIX Release Notes®that correspond to the level of your AIX operating system.v Ensure that your hardware installation is complete, including all external devices. See the documentation that is provided with your system unit for installation instructions.v Verify that your system is set to boot from the device in which the installation media is loaded. See the hardware documentation that accompanied your system for instructions about setting the boot device.v If your system must communicate with other systems and access their resources, make sure that you have the following information before you proceed with the installation:–Network interface–Host name–IP address–Network mask–Name server–Domain name–Gateway2Step 2: Preparing your system for installationFollow these steps to prepare your system for installation:1.Insert the AIX Volume 1 media into the media device.2.Shut down your system. If your system is running, turn it off by following these steps:v Log in as the root user.v Type the following command:shutdown-Fv If your system does not automatically turn off, place the power switch in the Off (0) position.Do not turn on the system unit until instructed to do so in Step 4: Booting from your installation media.3.Ensure that all external devices attached to the system (such as CD-ROM drives, tape drives, DVD drives, andterminals) are turned on. You must turn on the external devices first so that the system unit can identify eachperipheral device during the startup (boot) process.IBM®3Step 3: Setting up an ASCII terminalIf you have not set up ASCII terminal, set the communications, keyboard, and display options. Use the following criteriaand your terminal reference documentation to set the communications, keyboard, and display options. The following settings are typical, but your terminal might have different option names and settings than those listed here:Communication Options:Options SettingsLine speed(baud rate)9600Word Length(bits per character)8Parity no(none)Number of stop bits1Interface RS-232C(or RS-422A)Line control IPRTSKeyboard and display options:Options SettingsScreen normalRow and Column24x80Scroll jumpAuto LF(line feed)offLine Wrap onForcing Insert line(or both)Tab fieldOperating Mode echoTurnaround Character CREnter returnReturn new lineNew Line CRSend pageInsert Character space4Step 4: Booting from your installation mediaFollow this procedure for booting from your installation media:1.Turn on the system unit power switch.2.When the system beeps twice, press 5 on your ASCII terminal. The word keyboard is shown when the beeps occur.3.If you have more than one console, each one might display a panel that directs you to press a key to identify yoursystem console. A different key is specified for each console that is displayed on this panel. If this panel opens, press the specified key only on the console that you want to use for the installation. (The system console is the keyboard and display device that is used for installation and system administration.)4.Select the language that you prefer to use during installation, and press Enter.5Step 5: Verifying the installation settingsFollow this procedure to verify your installation settings:1.Display the installation settings before you install the BOS, by typing 2 in the Choice field to select 2 Change/Show2.Verify the default installation settings from the Overwrite Installation and Settings panel.3.If the installation and system settings are correct, type 0 in the Choice field and press Enter. Confirm that theselections on the installation summary panel are correct, and press Enter to begin the BOS installation. The system automatically reboots after the system installation is complete. Go to Step 9: Finishing the BOS installation.If your installation settings are not correct, or if you want to change the installation settings, go to Step 6. Changing the installation settings.6Step 6: Optional: Changing the installation settingsTo change the installation settings, complete the following steps:1.2.When the Change Method of Installation panel is displayed, type 1 for New and Complete Overwrite Installation andpress Enter.When the Change Disk(s) Where You Want to Install panel is displayed, you can change the destination disk for the3.If the default settings shown are correct, type 0 in the Choice field and press Enter.To change the destination disk, complete the following steps:a.Type the number for each disk where you want to install the BOS in the Choice field and press Enter. Do not pressEnter a final time until you finish selecting all disks. If you must deselect a disk, type its number a second time andpress Enter.b.To finish selecting disks, type 0 in the Choice field and press Enter. The Installation and Settings panel is displayedwith the selected disks listed under System Settings.7Step 7: Changing Primary Language EnvironmentTo change the primary language that is used by this installation:1.Type 2 Primary Language Environment®Settings in the Choice field on the Installation and Settings panel.2.Select the appropriate set of cultural convention, language, and keyboard options. Most of the options are apredefined combination; however, you can define your own combination of options.3.To select a predefined Primary Language Environment, type the corresponding number in the Choice field and pressEnter.To configure your own Primary Language Environment, complete the following steps:a.Select More Choices.b.Page through the choices and select the Create Your Own Combination option.c.On the Set Primary Cultural Convention panel, type the corresponding number in the Choice field and press Enter.d.On the Set Primary Language panel, type the number in the Choice field that corresponds to your choice for theprimary language and press Enter.e.On the Set Keyboard panel, type the number in the Choice field that corresponds to the keyboard that is attachedto the system and press Enter.8Step 8: Verifying BOS installation settingsTo verify your BOS installation settings:1.2.Press Enter to begin the BOS installation.9Step 9: Finishing the BOS installationAfter the base runtime environment is installed, status information is displayed about other software that is beinginstalled. The system automatically reboots.The Installation Assistant guides you through the configuration tasks.Related informationFor more information about installing AIX, see the following resources:v For additional release information, see the AIX Release Notes that corresponds to your level of the AIX operatingsystem in the IBM®Knowledge Center (/support/knowledgecenter/ssw_aix_72/com.ibm.aix.base/ releasenotes_kickoff.htm).v For more detailed installation documentation, see the AIX Version 7.2 installation and migration topic collection in the IBM Knowledge Center (/support/knowledgecenter/ssw_aix_72/com.ibm.aix.install/insgdrf-kickoff.htm).AIX Version 7.2 Licensed Materials - Property of IBM. © Copyright IBM Corp. 2015. U.S. Government Users Restricted Rights - Use, duplication or disclosure restricted by GSA ADP Schedule Contract with IBM Corp.IBM, the IBM logo, and ®are trademarks or registered trademarks of International Business Machines Corp., registered in many jurisdictions worldwide. Other product and service names might be trademarks of IBM or other companies. A current list of IBM trademarks is available on the web at “Copyright and trademark information” (/legal/copytrade.shtml).Document Number:SA23-2267-03Printed in USA。
工行迪堡1072 OS2系统设置

工行迪堡1072 OS2系统设置方法1072os2系统的安装可以直接用ghost完成,我只将系统的设置进行整理。
一、网卡安装完系统开机时,显示器是否提示按回车键进入。
1、如果无提示,直接进入系统,说明网卡认到,则无须设置网卡。
2、如果有提示,说明无法认到网卡,可能是因为网卡设置出错。
以下是设置方法。
开机后系统提示按“回车”,大约要按四次“回车”后进入系统桌面(图1)时,同时按ctrl+c。
出现图2画面。
图1 图2如图2所示,输入“mpts”回车。
一直回车,出现图3画面,这就是网卡修改页面。
最下方下方的显示的为原来所配的网卡型号及协议,在重新配置前要先删除。
左上角为网卡型号,一般1072为G4主板,网卡是主板自带的,选“Intel(R) PRO PCI Adapter……”,选中后按"ADD"。
右上角为协议类型,选“0-IBM TCP/IP”,选中后按"ADD"。
选择完成后按“OK”保存即可。
图3二、IP、网关、掩码这三项为必设。
如图2中,输入“tcpcfg”回车。
一直回车,到图4。
1、在“ip address”内直接修改IP地址,在“subnet mask”中直接修改掩码。
2、在画面的右下角,有一个右向的箭头,点击后就进入下一页。
图5。
在图5中,点击“change”会跳出一个对话框,要求输入网关。
3、输入完成后,按“Alt+F4”退出,选保存即可。
图4 图5三、ATM号、网点号、地区号如图2所示,要先进入C:\IBOLD\REAR文件夹下,再输入“E ATM.CFG”回车。
进入图6画面。
直接修改ATM号、网点号、地区号,保存后退出。
重启。
图6四、密钥重启后等系统进入暂停服务画面,按“ESC”进入,输入密码六个零“000000”。
按“ALT”找到“KEY”下拉菜单中有“B KEY”时回车,直接用电脑键盘输入“7D19 C9B0 04A7 7373”然后选“OK”,再次找到“B KEY”回车,输入“B8EB 97C5 2273 8B86”再次选择“OK”,然后退出,重启。
OpenCNC_PLC开发工具操作手冊说明书

OpenCNC_PLC發展工具操作手冊匯出日期:2023-05-10修改日期:2020-08-30英文文件 English Document: PLC Editor Operation Manual.Ladder-Editor 軟體操作介紹Ladder編寫開發PLC元件介紹操作手冊下載文件履歷1.2.•••• a.i.1 PLC 編輯器介紹1.1 軟體下載進入新代網站 ,完成線上注冊手續并確定權限開通。
至『下載中心』 => 『04.應用工具』 => 『Ladder Editor 』下載PLC 編輯器。
1.2 軟體安裝2.26.3(含)以前為安裝版執行LadEdit_vx.xx.x.msi 并依畫面指示,即可完成安裝程序。
安裝完成後,依序點選『開始』 => 『程式集』 => 『OpenCNC 』 => 『MLCEdit.exe 』,即可開啟PLC 編輯器。
2.29.0(含)以後為免安裝版第一次執行時:下載完LadEditor_x.xx.x.zip ,解壓縮後右鍵點擊『Install.bat 』,選擇『以系統管理員身分執行』,將.lad 檔的預設開啟程式設定為PLC 編輯器ii.b.c.i.ii.•••••••執行『MLCEdit.exe』開啟PLC編輯器第二次之後執行:執行『MLCEdit.exe』,或直接雙擊.lad檔,皆可開啟PLC編輯器注意事項:搬移免安裝包位置時,請再次執行免安裝包內的『Install.bat』,否則會無法正常開啟.lad檔。
下載新版本PLC編輯器時,請執行新版本免安裝包內的『Install.bat』,否則仍會以舊版PLC編輯器開檔。
1.3 介面操作PLC編輯器介面共有七個區域,如下圖所示:下拉式功能區指令按鈕功能區指令區程式管理區指令編輯區元件注解區元件索引區下拉式功能區指令按鈕功能區指令區指令區提供各種元件讓使用者選取、應用,詳細說明請參閱後續章節。
FG257 MODULAR DECK UL 08 07 RAC 产品说明书

OPERATION AND MAINTENANCE MANUALMODULAR DECK OVENMANUAL No. Y-DXT ULEnter Serial Nos. hereIn the event of an enquiry please quote these serial numbers.FAN (IF FITTED)DECK 1 DECK 2 DECK 3DECK 4DECK 5WARNING LABEL, TO REDUCE RISK OF FIREOR ELECTRIC SHOCKDO NOT REMOVE COVER (OR BACK)The lights are low voltage, sealed from the chamber and easily accessed from outside the oven.Fitted with a choice of hinged easy to clean double glazed doors (using low energy- loss reflective glass for high visibility) or metal doors, means low energy consumptionW5 HIGH ……………….H = 84”(2135mm) 4 HIGH ……………….H = 79.5”(2020mm) 3 HIGH ……………….H = 79.5”(2020mm)4 DECK OVENDECK PLATE HEIGHTS3 DECK OVENDECK PLATE HEIGHTS1310mm – 3 TRAY836mm - - 2 TRAY 858mmWHEN ALL MODULES ARE POSITIONED AND FIXED AT THE FRONT,(SELF-TAPPING SCREWS)If this method of fixing down is used, enough space should be left surrounding theoven to allow for maintenance and cleaning, without moving the oven.bracket (247-01-00075) over frame and fix to floor in 2 positionsThe base structure should be held in place by bolting down to the floor with suitable fixings, using bracket part CLAMPING DOWN IN EARTHQUAKE ZONESSCREWSREAR VIEW OF OVENREMOVE SCREWS (2 PER BRACKET, NOT SHOWN). TURN BRACKET 180 DEGREES.ADJUST BRACKET TO TOUCH TILE AND REFIT SCREWS. THIS MUST BE DONE ON EACH DECK.BRACKET PART No.M257-06-00015POSITION ON DELIVERYPOSITION AFTER INSTALLATIONRETAINING BRACKETS IN 2 POSITIONS ON EACH DECKTILE RETAINING BRACKETSADJUSTING SCREW SET TO 0.75 bar FILTERTEST VALVE WATER REGULATOR SET UP LOCATED ON REAR OF OVENCONNECTION POINT9 ½”CANOPYROOFWITH EXTRACTION FAN FITTED13”WARNINGTHE “POWER OFF” BUTTON ON THE FRONT OF THE OVEN DOES NOT ISOLATE THE POWER SUPPLY.10.0 TOUCHSCREEN OPERATING INSTRUCTIONSSLEEPTHE OVEN STAYS AT 100c AND HEATS TO LAST PROGRAM TEMPERATURE WHEN THE SCREEN IS TOUCHED.OPTION SCREEN THEN SHOWS.STANDBYTHE OVEN TURNS OFF. TOUCH THE SCREEN TO GO TOTHE OPTION SCREEN.OPTION SCREEN SELECT SCREEN LOAD SCREENBAKE TIME LEFT ACTUAL OVEN TEMPERATUREThis will rise and fallREADY SCREENHEATING SCREENBAKE OVER SCREENVIEW SCREENSET BAKE TIME TOUCH TIME ON THE SCREEN TO ACTIVATE THE KEYBOARD SCREEN.KEY IN REQUIRED TIME TOUCH “OK”TIME DOES NOT HAVE TO BE SET IN MANUAL MODE. (ONLY TEMPERATURE) WHEN “START” IS PRESSED, THE TIME WILL COUNT UP INSTEAD OF DOWN.TOUCH “STOP” TO FINISH THE BAKE.2MANUAL BAKE SCREEN SET BAKE TIME AND TEMPERATUREOPTION SCREENTOUCH AT ANYTIME TOGO BACK TO THETOUCHSETTING SCREEN.MANUAL BAKE SCREEN 3SAVE SETTINGSIF NO TIME WAS ENTERED AT THE START OF THEBAKE, WHEN STOP IS TOUCHED “SAVE” WILLAPPEAR AT THE BOTTOM OF THE SCREEN.“SAVE” CAN BE TOUCHED AND AN OPTIONSCREEN WILL APPEAR.NOTE: In manual mode, only one operation of the steam or damper is saved.LOAD SCREENSCROLL DOWN FOR MORE PRODUCTS IF AVAILABLESELECT SCREENORMORE CHOICESCATEGORY SCREENPROGRAM CHOICEPICTORIALORNUMERICALOPTION SCREENHEATING SCREENREADY SCREEN BAKE TIME LEFTBAKE OVER SCREEN VIEW SCREENSELECT SCREENTOUCH “ i ” BUTTON NEXT TO THE BLANK CATEGORY SCREENOPTION SCREENENTER “SUPERVISOR” PASS CODE ANDTHEN TOUCH O K.(DEFAULT CODE = 123456. THIS CAN BECHANGED IN HIGH LEVEL SETTINGS )5PASS CODE SCREEN TOUCH OPTION TO GO TO PASS CODE SCREEN4INFORMATIONTOUCH EACH ITEM AND CHANGE THE VALUE BY USING THE UP AND DOWNKEYS OR BY USING THE KEY PAD.TOUCH “HALF LOAD ” TO CHANGE TO “HALF LOAD” SETTINGS IF REQUIRED.TOUCH “FULL LOAD ” TO GO BACK TO “FULL LOAD”TOUCH “SAVE ” WHEN SATISFIED WITH THE SETTINGS.ENTER AMOUNT REQUIREDAND TOUCH DONEVALUE CHANGE SCREENTOUCH “CHANGE PRODUCT ”6OPTION SCREENWWHEN SATISFIED WITH THE TRAY LAYOUT TOUCH SAVE TO RETURN TOTHE “OPTIONS” SCREENTOUCH TO ADJUST NUMBER OF PRODUCTSDOWN THE TRAYTOUCH TO ADJUST NUMBER OF PRODUCTS ACROSS THE TRAY TOUCH “CHANGE TRAY LAYOUT ”8OPTION SCREENTYPE IN THE NEW NAME AND TOUCH “SAVE”11TOUCH “SAVE AS”OPTION SCREENCATEGORY SCREEN SELECT SCREEN OPTION SCREENUp to four on/off times can be set for each day.” to clear the settings on the day shown.” to activate the times set.TIMER SETUP SCREENOPTION SCREENENTER “SUPERVISOR”CODE AND THEN PRESS“OK”.(DEFAULT CODE = 123456)CHOOSE THE SETTING TO ALTERWHEN ALL INFORMATION IS CORRECT,TOUCH “SAVE ”.THIS WILL RETURN TO THE SETTINGS SCREEN USE THE INCREASE / DECREASE BUTTONS TO ALTER THE SETTINGSTOUCH THE SCREEN TO HIGHLIGHTTHE ITEM TO CHANGESELECT WALLPAPER. GENERAL SETTINGS ” AND THE FOLLOWING SCREEN WILL APPEAR.SCROLL DOWN TO MOVE THROUGH ALL CHOICES AND ADJUST EACH ONE AS REQUIRED, USING THE ARROW KEYS.TOUCH “BACK” TO CONFIRMSETTINGS SCREENSCROLL DOWN TO MOVE THROUGH ALL CHOICESAND ADJUST EACH ONE AS REQUIRED,USING THE ARROW KEYS.THE FOLLOWING SCREEN WILL APPEAR.ENTER “HIGH LEVEL” PASSCODEAND THEN TOUCH OK.SETTINGS” AND THE FOLLOWING SCREEN WILL1LIGHT OUTPUT SOFT START –On/Off Some lights need this for cold start up to stop them blowing.HEATER CONTROL –Contactor or solid state. Defaults to contactor. (solid state not used at the moment) I/O DIAGNOSTIC –Displays outputs and inputs at the top of the screen to aid fault finding if needed.PASSCODES WILL BE REQUIRED TO GO THROUGH THESE SCREENS AND MAKE CHANGES.。
OpenCFD-EC理论手册-2014-11

与
FDS
方法相同,首先重构出界面(I+1/2,J)处的函数值:
U
L I +1/
2
及
U
R I +1/
2
。
利用 Steger‐Warming 流通矢量分裂,将控制界面上的通量分解为正通量及负通量:
H = H + H I +1/2,J
+ I +1/2,J
− I +1/2,J
具体公式见 傅德薰《计算空气动力学》158‐159 页 (请留意书中的印刷错误)。 (2.5)式中的系数为:
UL I +1/2
=UI
+1/
2 min mod(U I +1
−UI ,UI
− U I −1)
UR I +1/2
= U I +1
−1/
2 min mod(U I +1
方程及如下初值条件:
U
=
⎧⎪U ⎨ ⎪⎩ U
L I +1/2
lt; xI +1/2 otherwise
即可得到穿过(i+1/2,j)界面的通量 Hi+1/2, j 。
需要注意,由于本问题属于二维问题,可通过坐标旋转,转化成为垂直界面方向的 (扩展)一维 Riemann 问题,然后求解。具体公式见 任玉新 《计算流体力学基础》
8
(p164‐168). 本软件目前使用 HLL/HLLC 积分型近似 Riemann 求解器及 Roe 微分型近似 Riemann
求解器计算通量。具体公式见 Toro: Riemann Solvers and numerical methods for fluid dynamics。
HP OpenView Operations 7.x for Windows系统账户白皮书说明书

Using the SYSTEM account for Windows agentswhite paperhp OpenView operations 7.x forWindowsVersion 1.0Publication Date: 07/2002Warranty InformationThe information contained in this document is subject to change without notice.HEWLETT-PACKARD PROVIDES THIS MATERIAL "AS IS" AND MAKES NO WARRANTY OF ANY KIND,EXPRESSED OR IMPLIED, INCLUDING, BUT NOT LIMITED TO, THE IMPLIED WARRANTIES OFMERCHANTABILITY AND FITNESS FOR A PARTICULAR PURPOSE. HEWLETT-PACKARD SHALL NOT BE LIABLE FOR ERRORS CONTAINED HEREIN OR FOR INCIDENTAL OR CONSEQUENTIAL DAMAGES INCONNECTION WITH THE FURNISHING, PERFORMANCE OR USE OF THIS MATERIAL WHETHER BASED ON WARRANTY, CONTRACT, OR OTHER LEGAL THEORY.Hewlett-Packard assumes no responsibility for the use or reliability of its software on equipment that is not furnished by Hewlett-Packard. This document contains proprietary information which is protected by copyright. All rights are reserved. No part of this document may be photocopied, reproduced or translated to another language without the prior written consent of Hewlett-Packard Company.Restricted Rights LegendMicrosoft® and Microsoft Windows NT® are U.S. registered trademarks of Microsoft Corporation.UNIX® is a registered trademark in the United States and other countries, licensed exclusively through X/Open Company Limited.All other registered and unregistered trademarks mentioned within this paper are the sole property of their respective companies.ãCopyright 2002 Page 2 of 12Table of ContentsWarranty Information (2)Restricted Rights Legend (2)1Introduction (5)1.1Concept (5)1.2Comparison of ‘HP ITO Account/opc_op’ and local SYSTEM account (5)1.3Benefits (6)2Switching to the SYSTEM account (7)2.1Manual agent installation (8)3Restrictions (9)3.1Tools running as opc_op or ‘HP ITO account’ (9)3.2Policies using opc_op or ‘HP ITO account’ (9)3.3Accessing files with restricted Access Control List (10)3.4Agent on management server (10)3.4.1Message synchronization between two management servers (10)4Appendix (11)4.1SetMgmtServer Usage (11)ãCopyright 2002 Page 3 of 12Change RecordVersion Date Changes0.01 May 2002 First draft version for Operations for Windows 7.00.02 Added ACL section, added usage of SYSTEM asuser name, added comments about domainaccounts on DCs0.03 June 14, 2002 ISA references removedAdded comment that scheduled command policiescan also use ‘SYSTEM’ account1.00 July 2002 First version (released on channel web)SetMgmtServer Usage added, patch info addedãCopyright 2002 Page 4 of 121 IntroductionThis document describes how to setup and configure HP OpenView Operations 7.x for Windows so that the Operations agent (including all subagents like the embedded performance component and the discovery agent) on Windows systems uses the SYSTEM account.This is needed for customers which do not accept additional user accounts on the managed systems or which don’t want to worry about changing passwords of the opc_op and HP ITO Account.However, using the SYSTEM account has some impact on the functionality of OVO for Windows and might have some impact on Smart Plug-Ins (SPIs) or custom tools and policies. Therefore any restrictions are described in detail.Knowledge of Operations for Windows and Windows (2000 and NT) user administration is required to understand this document.The solution described herein is supported with Operations for Windows 7.x.Note: Patch OVOW_00001 is required for OVO 7.0 for Windows. This patch fixes a bug in ovpmpwutil and adds new options to the setmgmtserver tool (available from /patches).1.1 ConceptOVO for Windows allows you to change the user account, which will be used by all of the Windows agent processes, from ‘HP ITO Account’ to the local SYSTEM account. This change has to be made on the management server, using the setmgmtserver tool, before deploying the ‘Operations Agent’ package to a windows node. It affects all future package deployments until you decide to change the setting again, using setmgmtserver.The Operations agent and all registered subagents, such as the embedded performance component or the discovery agent will then run under the local SYSTEM account.1.2 Comparison of ‘HP ITO Account/opc_op’ and local SYSTEM accountThe default agent installation creates two local user accounts - the ‘HP ITO Account’ and the opc_op account. On domain controllers (DCs), which do not have local accounts, domain-accounts are created. The ‘HP ITO Account’ is a member of the local administrators group (domain-admin group on DCs) and is used for all agent processes. The opc_op account is a member of the Users group only and can be used for tools that should not be executed with administrative rights.ãCopyright 2002 Page 5 of 12The following table shows the differences between the accounts from an operating system perspective:opc_op HP ITO Account SYSTEM accountWhen created? During Operationsagent packageinstallation During Operationsagent packageinstallationDuring OSinstallation, existsalways.Member of administrators group No Yes, added duringOperations agentinstallationYes, by default, buthiddenMember of usersgroupYes Yes N/aPassword aging – password expires after a certain time and has to be changed Switched off bydefault. Can be turnedon.Switched off bydefault. Can be turnedon. (SHOULD NOT beturned on on DCs!1)No – SYSTEM accountdoes not have apasswordTypically used for Tools/programs thatshould run undernormal user account - All agent processes- Tools/programs thatshould run withadministratorprivilegesMost Windowsservices1.3 Benefits· No additional user accounts (both the ‘HP ITO Account’ and the ‘opc_op’ account will not be created)Thereforeo No conflict with password policieso No problem with domain policies that do not allow local accountso No problem with domain policies that remove necessary privileges or user rights1 On DCs, password aging SHOULD NOT be turned on and the password SHOULD NOT be changed, because all DCs share the same domain-user account and password. Passwords can only be changed when all necessary agents are installed on the DCs. Any new agent installation is only possible by deleting all existing agents on the DCs and reinstalling them again.ãCopyright 2002 Page 6 of 122 Switching to the SYSTEM accountThis change has to be made on the management server, using the setmgmtserver tool, before deploying the ‘Operations Agent’ package to a windows node.The Setmgmtserver tool can be found on the management server under <InstallDir>\bin. It has to be executed on the management server.Setmgmtserver can be used to configure the Operations agent to use the SYSTEM account. You always have to specify the Operations agent package as well.Call“%OvInstallDir%\bin\setmgmtserver” "%OvInstallDir%\Packages\Windows\OvEpMsgActAgt.FM" /system /onto switch to the SYSTEM account (Tip: The environment variable OvInstallDir points to the actual installation directory). Following you can find a typical output of this tool:Agent package 'C:\Program Files\HP OpenView\\packages\Windows\OvEpMsgActAgt.FM'Management Server name was updated from '' to''SYSTEM account installation: enabledThis will affect all future package deployments of the Operation Agent package. To update existing installations, use ‘All Tasks->Redeploy all’2 for systems where the Operations agent is already installed. If you want to switch to the ‘HP ITO Account’ again, call“%OvInstallDir%\bin\setmgmtserver” "%OvInstallDir%\Packages\Windows\OvEpMsgActAgt.FM" /system /offThe output should be similar to the following:Agent package 'C:\Program Files\HP OpenView\\packages\Windows\OvEpMsgActAgt.FM'Management Server name was updated from '' to''Again, this affects all future package deployments, so you have to re-deploy the agent to the managed node to make the change effective on the node.Note: If you don’t know your current setting (‘HP ITO Account’ or SYSTEM account) on the management server, call setmgmtserver /system.If you don’t know which user account is used on the managed node, check the services properties of the ‘HP ITO Agent’ service on the node.2 On DCs, ‘Redeploy all’ will not delete the domain user accounts (as they might still be needed by agents on other DCs). You can delete the domain user accounts manually when all agents on DCs are running using the SYSTEM account.ãCopyright 2002 Page 7 of 122.1 Manual agent installationThe manual agent installation package from the OVO for Windows standalone agents CD per default creates and uses the opc_op and HP ITO Account.If you would like to create your own manual agent installation package with an agent that uses the SYSTEM account, the following steps are required:1) Copy the ‘Windows’ subdirectory (including all files and subdirectories) from the CD to adirectory of your choice on the management server. Use either the Windows explorer or xcopye.g.mkdir c:\temp\Windowsxcopy D:\Windows c:\temp\Windows /E2) Call SetMgmtServer to switch to the SYSTEM account. Specify the OvEpMsgActAgt.FM in theWindows\program files\HP OpenView\packages\temp\Packages\Windows directory, e.g.“%OvInstallDir%\bin\setmgmtserver” "C:\temp\Windows\program files\HPOpenView\packages\temp\Packages\Windows\OvEpMsgActAgt.FM" /system /onThe output should be similar to the following:Hostname: New hostname: Management Server for Message / Action Agent was unknownManagement Server for Message / Action Agent set to Authentication is turned Off3) Copy the ‘patched’ bits to the target system using FTP or another transport mechanism of yourchoice or create a new CD with the 'patched' bits: copy the complete Windows directory(including all files and subdirectories) to the CD.Then install the agent as usual by invoking setup.exe.ãCopyright 2002 Page 8 of 123 Restrictions3.1 Tools running as opc_op or ‘HP ITO account’OVO for Windows and some of the SPIs come with tools that are pre-configured to run using the'opc_op' or 'HP ITO account'. These are used because – in a default installation – these users exist on every node, so the tool can be run without asking for a login. If the agent runs under the SYSTEM account and if these users do not exist, then these tools cannot be started. You have to change the tool configuration by either specifying another user or by using the ‘allow operator to change login’ option, which leaves the choice to the operator.Note: Make sure that the specified user exists on every system you want to start the tool on. You might want to use a domain-user or ‘Administrator’ to accomplish this (Note: The Administrator account has a different name on some non-English Windows systems). You can also specify ‘SYSTEM’ as user with an empty password. In this special case the agent will detect that it is already running as ‘SYSTEM’ and will not try to switch to that user.OVO for Windows comes with a tool that allows you to switch the login and password for a certain user in every tool configuration. From the console tree, select Tools->OpenView Tools. In the Details pane, select the tool Modify Tools login/password. Start this tool and specify the old and new login name. This will launch OvUpdatePassword.exe (which can also be started from the command line).3.2 Policies using opc_op or ‘HP ITO account’Scheduled Task policiesOVO for Windows and some of the SPIs come with Scheduled Task policies that are pre-configured to run using the 'opc_op' or 'HP ITO account'. These are used because – in a default installation – these users exist on every node. If the agent runs under the SYSTEM account and if these users do not exist, then these policies cannot be processed. You have to change the policy configuration by specifying another user.Note: Make sure that the specified user exists on every system you want to deploy the policy on and that the user has all the rights necessary to run the scheduled command successfully. Again, you can also specify ‘SYSTEM’ as user (leave the password field empty). In this special case the agent will detect that it is already running as ‘SYSTEM’ and will not try to switch to that user.OVO for Windows comes with the tool ovpmpwutil that allows you to switch the login and password in every Scheduled task policy. It can be found on the management server under <InstallDir>\bin. It has to be executed on the management server. Call“%OvInstallDir%\bin\ovpmpwutil” /u "HP ITO Account” /n “Administrator” /p “”ãCopyright 2002 Page 9 of 12to change all Scheduled Task policies with the user “HP ITO account” to “Administrator”. You can specify a password, or you can leave the password blank.You can also use any other user or even the SYSTEM account. Call“%OvInstallDir%\bin\ovpmpwutil” /u "HP ITO Account” /n “SYSTEM” /p “”to change all Scheduled Task policies with the user “HP ITO account” to “SYSTEM”. In this case you must leave the password empty. The agent will detect that it’s already running using the SYSTEM account and will not attempt a user switch.This tool switches ALL Scheduled Task policies that currently use the specified user to a new user and creates a new policy version for each changed policy. Therefore already deployed policies have to be redeployed.3.3 Accessing files with restricted Access Control ListWindows offers the functionality to restrict file access based on Access Control Lists (ACLs). If any of the agent processes has to open such a file, for example a logfile (for read access) or a monitor script (for execute access), you have to make sure that the ACL of that file includes read respectively execute rights for the SYSTEM account.If tools or scheduled task policies are accessing such files, make sure that you specify a user with appropriate rights in the tool’s ‘user name’ field respectively in the scheduled task policy’s ‘Execute as user’ field.3.4 Agent on management serverThe Operations agent, which is installed automatically during the OVO management server installation, creates and uses the opc_op and HP ITO account on the management server. This cannot be changed. However, after the OVO server installation, it’s possible to switch the agent to the SYSTEM account: make the necessary changes to the agent package as described in 2 Switching to the SYSTEM account, select the management server system in the nodes tree and chose ‘All Tasks->Redeploy all’. This will remove the old Operations agent package and install it again, now using the SYSTEM account.3.4.1 Message synchronization between two management serversThe message synchronization of messages that have been forwarded from one OVO for Windows management server to another OVO for Windows management server (synchronization of‘acknowledge’, ‘own’) uses the HP ITO Account and pass-through authentication to access the Windows Management Instrumentation (WMI) of the other management server.This will not work if the agent is running under the SYSTEM account, which does not have access to WMI on the remote management server.ãCopyright 2002 Page 10 of 12Therefore, message synchronization is only supported if both agents are running under the default HP ITO Account.4 Appendix4.1 SetMgmtServer UsageUsage: SetMgmtServer.exe <pkg> \[-d] [-s|/system [/on|/off|/default]] [/auth [/on|/off|/default]]Updates the management server's name in the agent installation <pkg>.-d Removes the NetBIOS domainname from the fullqualified hostname in case it exists in there.-s Agents will be installed to run as SYSTEM account./system Shows the current status of the SYSTEM account switch./system /on Turns on SYSTEM account installation./system /off Turns off SYSTEM account installation./system /default Sets the SYSTEM account installation back to default./auth Shows the current status of authentication./auth /on Turns on authentication./auth /off Turns off authentication./auth /default Sets the authentication back to default.The settings of '/system' and '/auth' switches will be written into the registry and reused at the next usage of SetMgmtServer.The SYSTEM account switch controls if the Windows agent will be installed to run as the dedicated 'HP ITO account' user or as SYSTEM account.NOTE:The '-s' switch sets the SYSTEM account flag only once. If the registry was set to 'Off' once, this will overwrite future usage of the '-s' switch. This command line option will become obsolete soon.The authentication switch controls if the Windows agent requires a password for switching to a different user account when execute commands or tools. Authentication 'Off' means the user doesn't need to provide a password. Tools or Scheduled Task policies can be setup with an empty password. Authentication ‘On’ means that the Scheduled Task policy and tool definitions always have to contain a password or that the operator always has to provide a password when launching a tool.ãCopyright 2002 Page 11 of 12Publication Date: 07/2002 ãCopyright 2002。
Vincent Cheung VC 用户手册说明书

SPECIFICATIONSENSOR SPECIFICATIONSRELATIVE HUMIDITY (wTHP , wTHP2, wBTHP)Accuracy/Range : ±2% for 10 to 90%±3% for 5 to 10% and 90 to 95%±4% for 0 to 5% and 95 to 100%Hysteresis : ±1% RH Non-linearity : ±3%Repeatability : ±0.1%Resolution: 0.1%TEMPERATURE Accuracy/Range*:wTHP , wTHP2±0.5°C for 5 to 45°C (±0.9°F for 41 to 113°F); up to ±1.5°C for -40 to 5°C and 45 to 124°C (up to ±2.7°F for -40 to 41°F and 113 to 255°F)wTP1, wTP2±0.5°C for 10 to 85°C (±0.9°F for 50 to 185°F);±1°C for -40 to 10°C and 85 to 125°C (±1.8°F for -40 to 50°F and 185 to 257°F)wBTHP±0.5°C for 5 to 45°C (±0.9°F for 41 to 113°F); up to ±1.5°C for -40 to 5°C and 45 to 85°C (up to ±2.7°F for -40 to 41°F and 113 to 185°F)wBTP±0.8°C @ 25ºC (±1.5°F @ 77ºF)±4°C for -40 to 85°C (±7.2°F for -40 to 185ºF)*NOTE:extended temp range is for Probe only,the Controller’s operating temp is -10 to 55ºC Resolution : 0.1°CBAROMETRIC PRESSURE (wBTP , wBTHP)Accuracy/Range :±2 mbar for 300 to 1100 mbar @ 0 to 50ºC ±6 mbar for 300 to 1100 mbar @ -40 to 85ºC Resolution : 0.1 mbarANALOG VOLTAGE & CURRENT INPUT (wVI)Voltage Input:Differential; bipolar; ±100 mV, ±1 V, ±10 V Input Impedance: 38 K ohm for voltage Current Input:Differential; bipolar; ±20 mA (5 ohm load)Accuracy: ±0.1% Full Range @ 25ºCReading Rate : Periodic (1 sample/update) or continuous (3 samples/second)Resolution : 16 bitsTHERMOCOUPLE INPUT (wTC)Thermocouple Type (ITS 90):J, K, T , E, R, S, B, C, N, LReading Rate : Periodic (1 sample/update) or continuous (3 samples/second)METER SPECIFICATIONSSupported Protocols (Transmitter): TCP/IP ,UDP , ARP , ICMP , DHCP , HTTP and FTP Supported Protocols (VC):TCP/IP , UDP , HTTP , FTP , SMTP and T elnet WIRELESS COMMUNICATION Standard : IEEE 802.11 b/gFrequency: 2.4 GHz (2402~2483.5 MHz)Range: 60m (200') indoor line-of-site or more depending upon sensitivity, data rate, wireless access point and environmental considerationsRadio Power Output Level (Class 1):91.4 mW EIRP (19.6 dBm EIRP)Modulation:802.11b compatibility:DSSS (CCK-11,CCK-5.5, DQPSK-2, DBPSK-1);802.11g:OFDM (default)Channels:1 to 13; Channel 14 for Japan use only and is not certified.Channel Spacing (Bandwidth):20 MHz Transmission Rate (Over the Air):802.11b:1 to 11 Mbps for 802.11g:6 to 54 MbpsPOWER (wSERIES AC POWER)Power Input:5 VdcConsumption:0.7 W maxSafety Qualified AC Power Adapter (included):Nominal Output:*********Input: 100 to 240 Vac, 50/60 Hz Back-up Alkaline Battery:One AA 1.5 Vdc, supplied POWER (wSERIES-CCELL)Alkaline Battery:Two C-CELL 1.5 Vdc, supplied Lifetime:Estimate of 2.4 years (wTC/wVI) and 4.3 years (wTxxP/wBxxP) with frequency of 1reading per 1 minute Dimensions:96.5H x 146.3W x 50.8D mm (3.8 x 5.76 x 2"),not including connectors or antenna Operating Temperature:-10 to 55ºC (14 to 131ºF), 90% RH non-condensing AC Power Adapter: 0 to 40ºC (32 to 104ºF)b)Channel – This is the Wi-Fi channel on which the access point is accepts connections. If not sure what channel to use, simply select Auto.c)Authentication – This is the security method which the access point is using for connections. Choose thedesired security based on the present access point settings.Use WPA2-PSK for the most secure connection. No security can be used to conserve battery power. WPA2-PSK Enterprise is not supportedd)Passphrase – If the authentication is WPA2-PSK, then enter a passphrase here.•Passphrase restricted characters include “ ;•The minimum characters that can be used for Passphrase/WPA2 is 8, maximum is 63.e)Default Key – This is the password if authentication is WEP-128.•WEP KEY can only use the following characters:a b c d e f 0 1 2 3 4 5 6 7 8 9.•WEP KEY must be a length of 26 characters.f)DHCP – Check this option if the Transmitter will receive a Dynamic IP address from a DHCP server.For initial configuration, it is recommended to use DHCP for assigning IP Address to the Transmitter. The IP address can be made STATIC from the Virtual Coordinator after the Transmitter starts communicating with it.g)IP Address – Assign a STATIC IP address.h)Netmask – Assign a subnet mask associated with the STATIC IP address.i)Gateway Address – This could be the IP address of your access point or wireless router which the Transmitter is associating with.j)Virtual Coordinator IP – Assign the IP address of the PC on which the VC is installed.k)Communication Protocol – This is the protocol used to communicate with the VC. Either TCP or UDPprotocol can be selected. UDP is default and uses less battery power.l)Virtual Coordinator Port – Readings from the sensor (Transmitter) are sent to the VC using this port e the default UDP protocol and port 50002unless this port is already used on the VC. If TCP protocol is used change this port number to 50006.m)Update Period – Enter the Transmitter’s reading transmission frequency in seconds.n)Save and Reboot –Click “Save Changes”. Verify the settings and then click “Reboot”. The webpage should say that the Transmitter is rebooted.If your Transmitter has a display, you should now be able to see the sensor readings on the display.The Transmitter stays in AD-HOC mode for a few minutes and then goes to sleep toconserve battery. So the step to put the device into AD-HOC mode and to configure it using a web page needs to be done together.Also during this time, it is recommended to set the “Update Period” to the default (10 seconds). Once the Transmitter and the VC are communicating properly, the “Update Period” can be changed to the desired value.3.6.Getting the ReadingsIf the PC used to configure the Transmitter is the same as the one running the VC, then change its IP address to the STATIC IP address set for the VC. Start a new browser and enter http://<IP address of PC running virtual coordinator>If using a different PC, go to the PC running VC. Open up a web browser and enter http://<IP address of virtual coordinator>Click the button that says readings. Enter the user name as “user ” and the password as “12345678”. Y ou should be able to see the readings.SeriesSETUP GUIDEWireless TransmitterWi-Fi802.11b/g Wireless EthernetMQS5029/0918***********************Servicing North America:U.S.A. Omega Engineering, Inc.Headquarters: Toll-Free: 1-800-826-6342 (USA & Canada only)Customer Service: 1-800-622-2378 (USA & Canada only)Engineering Service: 1-800-872-9436 (USA & Canada only) Tel: (203) 359-1660 Fax: (203) 359-7700 e-mail:**************For Other Locations Visit /worldwideOMEGA’s policy is to make running changes, not model changes, whenever an improvement is possible. This affords ourcustomers the latest in technology and engineering.OMEGA is a trademark of OMEGA ENGINEERING, INC.© Copyright 2018 OMEGA ENGINEERING, INC. All rights reserved. This document may not be copied, photocopied, reproduced, translated, or reduced to any electronic medium or machine-readable form, in whole or in part, without the prior written consent of OMEGA ENGINEERING, INC.FOR WARRANTY RETURNS, please have thefollowing information available BEFORE contactingOMEGA:1. P urchase Order number under which the productwas PURCHASED,2. M odel and serial number of the product underwarranty, and3.Repair instructions and/or specific problemsrelative to the product.FOR NON-WARRANTY REPAIRS, consult OMEGA for current repair charges. Have the following information available BEFORE contacting OMEGA:1.Purchase Order number to cover the COST of the repair,2.Model and serial number of the product, and 3.Repair instructions and/or specific problems relative to the product.RETURN REQUESTS/INQUIRIESDirect all warranty and repair requests/inquiries to the OMEGA Customer Service Department. BEFORE RETURNING ANY PRODUCT(S) TO OMEGA, PURCHASER MUST OBTAIN AN AUTHORIZED RETURN (AR) NUMBER FROM OMEGA’S CUSTOMER SERVICE DEPARTMENT (IN ORDER TO AVOID PROCESSING DELAYS). The assigned AR number should then be marked on the outside of the return package and on any correspondence.The purchaser is responsible for shipping charges, freight, insurance and proper packaging to prevent breakage in transit.WARRANTY/DISCLAIMEROMEGA ENGINEERING, INC. warrants this unit to be free of defects in materials and workmanship for a period of 13 months from date of purchase. OMEGA’s WARRANTY adds an additional one (1) month grace period to the normal one (1) year product warranty to cover handling and shipping time. This ensures that OMEGA’s customers receive maximum coverage on each product.If the unit malfunctions, it must be returned to the factory for evaluation. OMEGA’s Customer Service Department will issue an Authorized Return (AR) number immediately upon phone or written request. Upon examination by OMEGA, if the unit is found to be defective, it will be repaired or replaced at no charge. OMEGA’s WARRANTY does not apply to defects resulting from any action of the purchaser, including but not limited to mishandling, improper interfacing, operation outside of design limits, improper repair, or unauthorized modification. This WARRANTY is VOID if the unit shows evidence of having been tampered with or shows evidence of having been damaged as a result of excessive corrosion; or current, heat, moisture or vibration; improper specification; misapplication; misuse or other operating conditions outside of OMEGA’s control. Components in which wear is not warranted, include but are not limited to contact points, fuses, and triacs.OMEGA is pleased to offer suggestions on the use of its various products. However, OMEGA neither assumes responsibility for any omissions or errors nor assumes liability for any damages that result from the use of its products in accordance with information provided by OMEGA, either verbal or written. OMEGA warrants only that the parts manufactured by the company will be as specified and free of defects. OMEGA MAKES NO OTHER WARRANTIES OR REPRESENTATIONS OF ANY KIND WHATSOEVER, EXPRESSED OR IMPLIED, EXCEPT THAT OF TITLE, AND ALL IMPLIED WARRANTIES INCLUDING ANY WARRANTY OF MERCHANTABILITY AND FITNESS FOR A PARTICULAR PURPOSE ARE HEREBY DISCLAIMED. LIMITATION OF LIABILITY: The remedies of purchaser set forth herein are exclusive, and the total liability of OMEGA with respect to this order, whether based on contract, warranty, negligence, indemnification, strict liability or otherwise, shall not exceed the purchase price of the component upon which liability is based. In no event shall OMEGA be liable for consequential, incidental or special damages.CONDITIONS: Equipment sold by OMEGA is not intended to be used, nor shall it be used: (1) as a “Basic Component” under 10 CFR 21 (NRC), used in or with any nuclear installation or activity; or (2) in medical applications or used on humans. Should any Product(s) be used in or with any nuclear installation or activity, medical application, used on humans, or misused in any way, OMEGA assumes no responsibility as set forth in our basic WARRANTY /DISCLAIMER language, and, additionally, purchaser will indemnify OMEGA and hold OMEGA harmless from any liability or damage whatsoever arising out of the use of the Product(s) in such a manner.™CONFIGURATION1.Configuring the computer running Virtual CoordinatorSoftware (VC)1.1.Disable Power Safe Options:The computer running VC software needs to be runningcontinuously. T o do that:a)Go to Control Panel>System and Security>Power Options.Choose the Power Plan>Change Plan Settings>ChangeAdvanced Settings. Then choose the Hard Disk>Turn Off HardDisk Option. Reduce this number from 20 to 0(Never).Save the settings.b)These settings may be different on Windows XP.Choose the Option to Never Turn Off Hard Disks and Never Putthe System to Standby.1.2.Java Runtime Environment:This PC needs to have the latest Java Runtime Environment(JRE) installed. First check the JRE installed.Go to Control Panel and look for the icon named Java. Clickingthat will start the Java Control Panel. Go to the Java tab and clickon View button.Note the Version number. It should be something like 1.6.0.x. If theversion number is anything less than 1.6 then go to ,download and install the latest version of JRE.1.3.Firewall Exception:This computer may have a firewall running which will block thereadings sent from the sensor (transmitter) to the VC Software.Configure the firewall to allow this data to go through. Refer toAppendix K and L in Operators Manual to configure the firewall.1.4.IP Address:If this computer is used to run the VC only and not to configure theTransmitter, then set a desired STATIC IP address.If this PC is used for configuring the Transmitter then set up aSTATIC IP address of 169.254.1.2for AD-HOC.It is recommended to have the computer running VChard-wired to the access point/wireless router.For initial setup it is recommended to place theTransmitter and the VC close to the wireless accesspoint/wireless router. Once the configuration is done theTransmitter can be mounted to the desired location.This configuration applies to Windows PC. For Linux, visitour website or read the instructions in the CD.One can also use a mobile device with a wireless (Wi-Fi)to configure the Transmitter.2.Installing Virtual Coordinator SoftwareFind the setup.exe in the accompanying CD or on the web.Double click that to install it.The setup process is typical to any Windows program and asks youto choose the installation path and whether it is a new installation oran upgrade Y ou must have the Administration Rights to the PCwhen installing the VC.Now go to Start>All Programs>Newport>Virtual CoordinatorManager. Click on Install Services twice and wait until it promptsyou to reboot the PC. Reboot the PC to start all the services ofVirtual Coordinator. Once the PC reboots, open up a web browserlike Internet Explorer, type in your PC’s IP Address and a VirtualCoordinator web page should show up. This means that the VirtualCoordinator web-server is running.This Quick Start Reference provides information on setting upyour instrument for basic operation. The latest wSeries manualcan be found at /manuals and the latestsoftware, including the “Virtual Coordinator” can be found at/softwareBEFORE YOU BEGINOVERVIEWwSeries wireless Transmitters take readings from the attachedsensors, and transmit data on a wireless Ethernet 802.11b/g networkcommonly referred to as “Wi-Fi.” These Transmitters are not“stand-alone” devices, they transmit data to the Virtual Coordinator.The wSeries wireless sensor system provides Web-based monitoringof Analog Current and Voltage, T emperature, Humidity, andBarometric Pressure.As with all Wi-Fi devices, the wSeries “Transmitters” are assignedunique IP addresses and connect to the LAN through a WirelessAccess Point/Router.T o conserve battery power, the Transmitters wake up, take readings,transmit data and quickly go back to sleep. The user can select thefrequency of transmissions. Less frequent transmissions result inlonger battery life. In applications where battery life is not an issue,the wSeries device can transmit continuously, up to three sensorreadings per second.The wireless transmitter mount discretely on the wall in clean rooms,laboratories, museums, computer server rooms, warehouses, andany remote facility.THE VIRTUAL COORDINATOR “VC” WEB SERVERThe “Virtual Coordinator” is a data logging software applicationrunning on a Windows or Linux computer somewhere on thenetwork. The “VC” logs/collects data from the wireless Transmitters.The VC includes a Java-based Web server that can displayreadings, charts, and record data sent by the transmitters.The readings, data, and charts are viewed from a Web browser.The browser accessing the VC Web server, can be the samecomputer on which the VC is installed-- or any other device with Webbrowsing capabilities on the local network or the Internet(a computer, tablet or smart phone).For Windows PC’sThe VC runs as a “Service” in the background, rather than a“Program”. As long as the computer and its network connection isfunctioning correctly, the VC will collect data from the transmittersand serve it to Web browsing clients as requested. The VC can alsoprovide data to popular Data Acquisition and Process Controlprograms running elsewhere on the network. Meanwhile, thecomputer running the VC server can be used for other tasks.Chart scales are fully adjustable on the fly. For example, the chartcan display one minute, one hour, one day, one week, one month orone year. T emperature and humidity can be charted across the fullspan (-40 to 125°C, and 0 to 100% RH) or within any narrow rangesuch as (20 to 30°C).The OPC Server software makes it easy to integrate the wSerieswireless sensor system with many popular Data Acquisition andAutomation programs offered by Omega, Wonderware, iConics,Intellution, Rockwell Automation, and National Instruments,among others.Parts Included:•Transmitter•Antenna•Batteries and/or AC adapter•Sensor (for models with anincluded digital sensor)•CD with Virtual CoordinatorSoftware, check our websitefor latest version.Hardware/System Requirements:Y ou will need a computer, tablet, orsmart phone that has Wi-Fiinfrastructure and is Ad hoc capable.System Requirements: WindowsXP, Vista, Windows 7 32/64-bit,Windows Server 2008 32/64-bit,Java 32-bit version 1.6 and above,Processor: 1GHz, RAM: 2GB,Browser: IE9 or Mozilla FirefoxAccess Point/Wireless Connection:You will need an Access Point /Wireless Router.You will need the followinginformation to ensure your deviceworks correctly:•Wireless Access Point SSID•Passphrase/Security Settings•IP Address (for transmitter)•Netmask•Gateway Address•IP Address of computer thatwill run the “VirtualCoordinator” service.Figure 1Firmware Version:: “X.XX”Reboot device with saved settings and go to run mode.After click on the Reboot button, please wait few secondsAccess Point SSIDMode (UDP Only)Initial Configuration802.11 ConfigurationSave Changes ResetRebootWireless Network ConnectionCurrently connected to:Figure 6 - iPhoneWi-Fi Settings。
DCFS快速操作手册及部分疑难解答V1.7-20100715

快速操作手册及部分疑难解答目录1. 建立地址组 (2)2. 快速拦截P2P应用 (3)3. 限制P2P应用的流量 (5)4. 观察每个用户的实时连接状况 (8)5. 限制IP地址段中每个IP的带宽 (9)6. 什么情况下使用二级带宽策略 (12)7. 如何让一些特殊权限的地址快速通过 (13)8. 未知应用过大怎么办 (14)9. 如何限制每个用户的会话数 (15)10. 如何限制MSN的使用 (18)11. 配合DCBI认证快速操作指南 (20)12. 配合DCSM的Portal认证计费快速操作指南 (23)12.1. DCFS Portal认证--DCSM管理端配置 (23)12.1.1. 登录WEB管理端 (24)12.1.2. 管理端首页 (24)12.1.3. 创建服务或套餐 (25)12.1.4. 创建账户组 (26)12.1.5. 创建关联用户或用户组的策略 (28)12.1.6. 创建用户组,并关联相应的安全策略 (29)12.1.7. 创建用户并启用该用户的订单 (30)12.1.7.1. 管理员开户 (30)12.1.7.2. 管理端运营管理相关检查 (32)12.1.7.3. 批量导入开户 (33)12.2. 添加DCFS设备 (34)12.3. DCFS WebPortal认证---DCFS配置 (35)12.4. 接口IP、路由配置(省略) (35)12.5. 配置认证门户 (35)12.6. 配置认证策略 (35)12.7. 设置预置安全策略,定义放行、认证的各项参数 (37)12.8. DCFS Portal认证—用户浏览器认证 (40)12.8.1. 用户打开一个外部网站,将得到认证提示页面 (40)12.8.2. 认证成功页面 (41)12.9. DCFS在线认证用户查看 (43)13. 配合DCSM的客户端认证计费快速配置指南 (43)14. 附录一:协议名称的简单说明 (44)1.建立地址组建立地址组有两种方法,对于有确定掩码段不分散的地址,可以使用“地址对象管理”,添加一个地址对象。
ICP DAS M-7002 数据采集模块快速入门指南说明书

M-70024-channel AI, 5-channel DI and 4-channels Relay OutputData Acquisition ModuleQuick Start GuideProduct Website:https:///m_7002.html/dcon_utility_pro.html1. IntroductionThe M-7002 is a 16-bit, 4-channel differential analog inputs 5-channel digital inputs and 4-channels for relay output. All of its channels are Form A type relay module that provides programmable input range on all analog channels (+/-150 mV, +/-500 mV, +/-1 V, +/-5 V, +/-10 V, +/-20 mA, 0 ~ 20 mA and 4 ~ 20 mA) and digital output can be set alarm output with shortcircuit protection and overload protection. Each analog channel is allowed to configure an individual range and has 240 Vrms high overvoltage protection. Jumper selectable for voltage or current input. The sampling rate of M-7002 is changeable; there are fast mode and normal mode for your consideration. M-7002 also has qualification for 4 kV ESD protection as well as 2500 VDC intra-module isolation.2. Terminal AssignmentM-7002 - 4-ch AI, 5-ch DI and 4-ch Relay Output DAQ Module - QuickStart (Jun/2018)M-7002 - 4-ch AI, 5-ch DI and 4-ch Relay Output DAQ Module - QuickStart (Jun/2018)3. Block/ Wiring Diagram4. Default SettingsDefault settings for the M-7005 modules are as follows:▫ Protocol: Modbus RTU ▫ Module Address: 01 ▫ Thermistor Type: Type 60, PreCon Type III, -30°F to 240°F ▫ Baud Rate: 9600 bps ▫ Temperature Scale: Celsius (the M-7005 also supports Fahrenheit for DCON protocol)5. ConfigurationTo install the module, follow the steps below:1. Connect the thermistor analog input.2. Connect the module to the RS-485 network using the DATA+ and DATA- terminals. If the host is only equipped with an RS-232 interface, then an RS-232 to RS-485 converter will be required.3. Connect the module to the power supply using the +Vs and GND terminals. Note that the voltage supplied should be in the range of +10 to +30V DC.M-7002 - 4-ch AI, 5-ch DI and 4-ch Relay Output DAQ Module - QuickStart (Jun/2018)4. Open DCON utility proclick on COM port(first icon).It can select multi-options such as Baud Rate, Protocol, Checksum, and Format to search module. The default settings for the module can be found in Section 3. Click OK after selecting the COM port setting.M-7002 - 4-ch AI, 5-ch DI and 4-ch Relay Output DAQ Module - QuickStart (Jun/2018)5. DCON utility pro will search for the selected COM port according the setting previously set. DCON Utility Pro supports DCON and Modbus protocol for all ICPDAS and the others modules.6. Configuration I/O module setting on PCM-7002 - 4-ch AI, 5-ch DI and 4-ch Relay Output DAQ Module - QuickStart (Jun/2018)7. For M-7000 modules, DCON utility pro terminal can send command to the module. See user manual Sections 2 for details command.Configure the module: sending the %AANNTTCCFF command. See Section 2.1 for details. To configure the M-7005, the $AA7CiRrr command must also be sent. See user manual Section 2.12 for details. For M-7000 modules using the Modbus RTU protocol, configure the module using the following functions.-Sub-function 04h of Function 46h, see user manual Section 3.6.2-Sub-function 06h of Function 46h, see user manual Section 3.6.4-Sub-function 08h of Function 46h, see user manual Section 3.6.6Read data from the input channels: send either the #AA or #AAN commands to the module. See user manual Sections 2.3 and 2.4 for details. For M-7000 modules using the Modbus RTU protocol, use Function 04h to read the data from the input channels. See user manual Section 3.3 for details.M-7002 - 4-ch AI, 5-ch DI and 4-ch Relay Output DAQ Module - QuickStart (Jun/2018)8. If user doesn’t know command, user can select Address and ID, it will show some refer commands as below. User can select necessary command to test or debug modules.M-7002 - 4-ch AI, 5-ch DI and 4-ch Relay Output DAQ Module - QuickStart (Jun/2018)。
LaCie d2 Network 网络文件服务器说明书
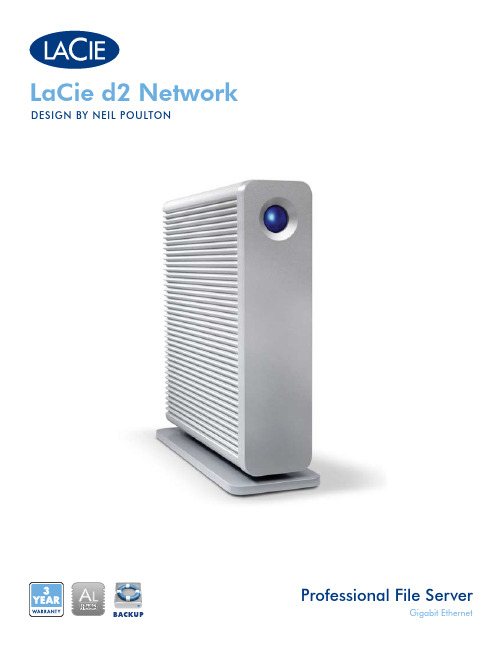
LaCie d2 NetworkGigabit EthernetProfessional File ServerDESIGN BY NEIL POULTONEssential Networking SolutionThe LaCie d2 Network offers professional, reliable, central storage for instantly storing, sharing, and backing up from any PC or Mac ® on your network. Manage your home or small office network easily with this full-featured file server, recommended for networks with up to 50 users (15 at once). With the LaCie d2 Network, you can share files amongWindows ®, Mac, and Linux users thanks to its SMB and AFP protocols support, or connect remotely through FTP , HTTP , and HTTPS file systems.Back Up Your NAS ContentGet extra security and increase data portability by backing up your LaCie d2 Network— on your own schedule— to an external hard drive through its USB ports using the built-in backup system. The LaCie d2 Network comes also with Genie Backup Manager Pro™ for Windows and Intego Backup Manager Pro™ for Mac to install on each PC/Mac for client backups to the NAS. This software lets you reliably and efficiently back up your documents, emails, settings, or other digital assets; it supports compressed, encrypted, or image backups and initiates a computer recovery program in case of general crash.Multimedia Server CapabilitiesWith the LaCie d2 Network, it’s easy to stream multimedia content to your television. Y ou can play your media on any UPnP AV-compatible Digital Media Adapter (DMA), such as a PS3 or Xbox, without needing a computer—you can store the information directly on the LaCie d2 Network. In fact, the d2 Network has been developed to be compatible with any DLNA multimedia device, and also works with iT unes ®. Y ou can also download torrent files automatically with the LaCie d2 Network without even having to turn on your PC.Access d2 Networkfrom iTunesGame ConsoleStereoQuick AccessControlling access is simple; you can assign various security levelsto shares, groups, user profiles, and public access. With Windows ADS domain support, there’s no need to recreate existing user and group accounts of your Windows domain, making it easy to manage for IT Administrators. Thanks to the Wake-on-LAN feature, the LaCie d2 Network can be switched back to operating mode from the client side.Avant-Garde By DesignDesigned exclusively for LaCie by the world-renowneddesigner Neil Poulton, the LaCie d2 Network was engineered to maximize reliability and longevity. Its sturdy aluminum body with a unique fanless heat sink design offers natural heat dissipation by providing 60% more surface area. Designed to stay cool without a fan, the LaCie d2 Network works both efficiently and quietly, helping it stand out from thecompetition. With space-saving versatility, it can stand upright on your desk or lie vertically or be rackmounted with other drives to save space. For added security, there’s a Kensington lock-compatible slot on the back.A Multiprotocol SolutionApple ® Time Machine CompatibleThe LaCie d2 Network is compatible with Mac OS X v10.5 Leopard, including Time Machine,making it an ideal partner for your Mac. Time Machine automatically backs up your Mac’s system files, applications, accounts, preferences, music, photos, movies, and documents to an external hard drive and you can easily go back in time to recover anything.Easy to UseWith its intuitive Web interface, administration is easy, convenient, and secure. Thanks to the LaCie d2 Network’s DHCP andAutomatic IP support, network configuration is fast and automatic. The LaCie d2 Network also comes with the LaCie NetworkAssistant, an easy-to-use program available for Windows, Mac, and Linux users. The LaCie d2 Network keeps its administrator informed with email notifications for backup and downloads, as well as high temperatures and disk damage.eSATAExpansion Port USB Expansion Port Gigabit EthernetPower connectorLock SlotOff/Auto/OnEXCLUSIVE D2 HEAT SINK DESIGN*EN 1TB (T erabyte) = 1000GB. 1GB = 1,000,000,000 bytes. T otal accessible capacity varies depending upon operating environment (typically 10–15% less).**Calculations are based on 2.5MB/3-minute song, 1GB/200 office presentations, and 1GB/movie (encoded in MPEG-4 or equivalent codec).*** AFP required for full compatibility with Mac OS.© 2009, LaCie. The LaCie logo is a trademark of LaCie. Other products and brand names mentioned herein may be trademarks or registered trademarks of their respective owners. Specifications and appearance are given as guidelines and may change without notice. 090312Box Content• LaCie d2 Network • Ethernet cable• External power supply• Drive stand for upright use• Utilities CD-ROM with software and User Manual • Quick Install GuideSystem Requirements• PC or Mac equipped with a network adapter• Windows 2000, Windows XP (SP1 and SP2), Windows Vista ™ / Mac OS 10.2 or higher / Linux 2.4 or higher •Ethernet switch or router• Minimum free local disk space: 600MB recommended • 500MHz processor or greater • Minimum 512MB of RAM• Web browsers: Internet Explorer, 6.0 or higher, Safari 2.0 or higher, or Firefox 1.5 or higherFeatures• Cross-platform (Windows/Mac/Linux)• Auto IP configuration access• New Web-based administration page• Assign shares, groups, user profiles, public, and guest access • Active Directory support• Scheduled incremental backup using local ports • 1-click data import/backup • Multimedia server • iTunes-compatible• Download Machine: BitT orrent download• Email alert in case of failures• Wake-on-LAN: turn on/off from the network • USB 2.0 and eSATA expansion ports • Aluminum d2 heat sink design • Fanless• Genie and Intego Backup Manager Pro software for Windows and MacPremium 3-Year WarrantyThe LaCie d2 Network comes with a 3 Year Limited Warranty. For superior service, it also comes with an optional Advance Care Option, which can be purchased separately online within 30 days of the purchase date. Under the Advance Care Option, LaCie will immediately swap out the product without it needing to be returned first for minimal interruption of your workflow. LaCie covers all freight costs. Availability depends on the sales area. See for details.ADVANCECARE OPTION。
toyota 7 inch Basic AVX使用者手冊说明书
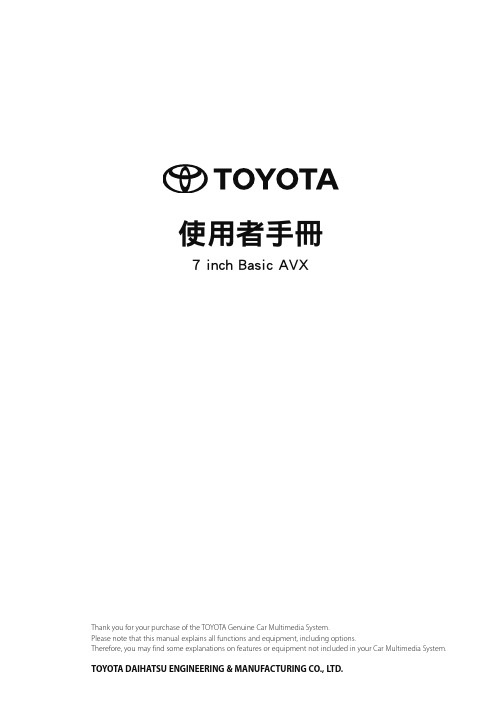
Article 3 (Terms of License)1.I n assigning this product, User may not retain the original copy of the embedded Licensed Software (including associated literature, updates and upgrades) and any duplicates and associated literature with regard tothe license to use Licensed Software. User may transfer Licensed Software only to the condition of binding the assignee to abide by the terms of this Software License Agreement.2.U ser may not reverse-engineer, disassemble, decompile or otherwise analyze the source code of Licensed Software.Article 4 (Rights to Licensed Software)All rights to Licensed Software and the associated literature, including copyrights, shall reside with Licensor orthe original right holder who has granted the Right of Use and right to sublicense to Licensor (hereinafter referred to as “Original Right Holder”), and User does not have any rights other than Right of Use granted hereunder with regard to Licensed Software and the associated literature. Article 5 (Exemption Granted to Licensor)1.L icensor and Original Right Holder do not assume any responsibility for damages caused to User or third parties resulting from the exercise by User of the license granted hereunder, unless otherwise provided by any law to the contrary.2.L icensor does not warrant Licensed Software to be merchantable, compatible and fit for specific purposes.Article 6 (Responsibility for Third Parties)If disputes over the infringement of third parties’intellectual property rights, such as copyrights and patent rights, arise out of the use of Licensed Software by User, User shall resolve these disputes at User’s own expenses while keep Licensor and Original Right Holder harmless.Article 7 (Secrecy Obligation)User shall keep confidential Licensed Software provided hereunder, information contained in the associated literature or the like and those provisions of this agreement not yet in public knowledge and may not disclose or leak these to third parties without prior written consent from Licensor.Article 8 (Cancellation of the Agreement) Licensor reserves the right to cancel thisagreement forthwith and claim compensation from User for the damages caused by such cancellation when User:(1)B reaches any of the provisions of thisagreement, or(2)H as received a petition for seizure, provisionalseizure, provisional disposition or any otherkind of compulsory execution.Article 9 (Destruction of Licensed Software)If this agreement is terminated under the provision of the foregoing paragraph, User shall destroy Licensed Software, along with all associated literature and its duplicates, within two (2) weeks from the date of termination. Article 10 (Copyright Protection)1.C opyrights and all other intellectual property rights relating to Licensed Software shall reside with Licensor and Original Right Holder and in no circumstances with User.2.U ser shall abide by the laws relating to copyrights and intellectual property rights in using Licensed Software.Article 11 (Export Control)1.L icensed Software and the associated literature or the like may not be exportedto places outside the Country (including transmission outside the Country over the Internet or the like).2.U ser agrees that Licensed Software is subjectto export controls imposed by the Country and the United States of America.3.U ser agrees to comply with all the international and domestic laws that applyto this software (U.S. Export Administration Regulations and regulations established bythe U.S., the Country and their governmental agencies regarding usage by end users and export destinations).Article 12 (Miscellaneous)1.E ven if this agreement is invalidated in part by law, all other provisions shall remain in effect.2. L icensor and User shall consult each other in good faith to resolve any matters not provided for in this agreement or questions arising from the interpretation of this agreement.3.L icensor and User agree that this agreementis governed by the law of Japan and that all disputes involving claims and obligations that may arise out of this agreement will be settled by arbitration at the Tokyo District Court asthe court of first instance.ii基本操作6基本操作前面板按鈕功能57 12346右手驅動機型1237 564左手驅動機型注意• 本指南中的面板是用作清晰說明操作的範例。
Royal Alpha-9170用户编程指南说明书

To Program Manager Passwords ...................................................................... 20 To Use Manager Passwords .......................................................................... 20 DATE ••••••••••••••••••••••••••••••••••••••••••.•••••••••••••••••••••.•••••••••••••••••••.••.•••••••••• 21 TIME •••••.•.•.•..•.•...•••••.•...•••••••.••..•••••••..•••••••.•.•.••••••••••••••••••.•••.••...•••••••• 21 MACHINE NUMBER •••.•••••••••• ; ••••.••••••••.•••••••••••••••••.••.••••••••••••.••••.••••.•..•••.•.•••. 21 TAX RATES • • • • • • • • • • . . . . • . . • • . • • . • • • • • • • • • • • • • • • • • • • • • . • • . • • • . • • • • • • • • • • . • • • • • • . . • . • . • • • • . • • • • • • • • .• 22-24 To Set Type of Tax Being Used ........................................................................... 22 FIxed Tax Rate . . . . . . . . . . . . . . . . . . . . . . . . . . . . . . . . . . . . . . . . . . . . . . . . . . . . . . . . . . . . . . . . . . . . . . . . . . . . . . . . . . . . 22 Tax Table Rate. . . . . . . . . . . . . . . . . . . . . . . . . . . . . . . . . . . . . . . . . . . . . . . . . . . . . . . . . . . . . . . . . . . . . . . . . . . . . . . .. 23-24 DEPARTMENT PROGRAMMING . • • • • . • • • • • • • • . • • • • • • . • • • • . • • . • • • • . • • • • • • • • . • • • • • • • • • • • • • • • • . • • . • • • • • • • • •• 25-28 COUPON DISCOUNT •••.••.•••••••.••••••••••••••••••.••••••.•••••••••••••••••.•.••••••••.•.•.•••••••• 29-30 MINUS PERCENTAGE DISCOUNT (-%) •••••••••••.•••..•.••..•.•...••••••.•.•••..••..•.••.••..•....•.••..• 31-32 PLUS PERCENTAGE (+%) ............................................................•.....•........... 33-34 PRICE LOOK-UP (PLU) •.•.••..••..•.•.•••••..•••.•••••••..•••..• : • • • • • • • . • • • . • • • . • • . • • • • . • . • . • . • • • . . • .• 35-36 TRAINING MODE .••.••..••...•••••••..•.••••.•.•..•••••••••••••.•.••••••••.•••.••.•••••..•.•••...•••••.• 37 GRAND TOTAL PRESET ••.••••.•..•.••••.••.•••••••••••••••••.•..•••••.••••••.••••.•••••••••••••••••••••.• 38 TRANSACTION NUMBER PRESET •••••••••.•••••••••••••••••••••..••••••••.•••••••••..••••.•••••.••••••••••• 39 Xl and X2 COUNTER PRESET ..••.•.••••.•.••••.••...••••..••....•.•..••...•••..•.•.••••...••.•.•..••••••.• 40 Zl and Z2 COUNTER PRESET ...•.••••••••••.••.•......•.•..•.•••.....•...•.••..••.....•....•.•.••••.••.•.. 41 PROGRAMMING ALPHANUMERIC DESCRIPTIONS. • . • • . • . • • • . • . • . . • • . . . • • • • • • . • • • • . • • • • . • . • • . . . . . . • • . . . . . . .. 42-47 FLAG OPTIONS. • • . . . • • . • • • • • • • • • • • • • • . • • • • • • . • . • . . • . • . . . • • • • • • • . • • . • . • • • . • • . • • • • • . . • • . . . • . . • . . • • • • • •. 48-61 PROGRAM CONFIRMATION REPORTS ....•.•.•••...•...••••••.•.••••.•.••••••.•••..••••••...••.•..•..•.••.•• 62 Program Confirmation Report - Main Printout ................................................................ 62 Confirmation Report of Tax Rate Programming ............................................................... 63 Program Confirmation Report of Clerk 10 Numbers, Clerk Confirmation and Department ...... . . . . . . . . . . . . . . . . . . . . . .. 64-6S PLU Confirmation Report ................................................................................ 66
WARN 1700 Utility Winch 产品说明书

WARNING signals a hazard that CAUTION signals a hazard thatMOVING PARTS ENTANGLEMENT HAZARDFailure to observe these instructions could lead to severe injury or death.keep hands clear of wire rope, hook loop, hook and fairlead opening during installation, operation and whenFALLING OR CRUSHING HAZARDFailure to observe these instructions could lead to severe injury or death.Safety Precautions - continuedCAUTIONMOVING PARTS ENTANGLEMENT HAZARDFailure to observe these instructions could lead to minor to moderate injury.General Safety:• Always Know Your Winch: Take time to fully read and understand the included Installation and Operations guide, and Basic Guide to Winching Techniques, in order to understand your winch and the winching operation.• Never operate this winch if you are under 16 years of age.• Never operate this winch when under the influence of drugs, alcohol or medication.• Never exceed winch or wire rope rated capacity. Double line using a snatch block to reduce winch load.Installation Safety:• Always choose a mounting location that is sufficiently strong to withstand the maximum pulling capacity of your winch.• Always use factory approved switches, remote controls, accessories and installation components.• Always use grade 5 or better hardware, never weld bolts and never use longer bolts than those supplied from factory.• Always complete winch mounting and attachment of hook to hook loop before wiring winch during installation. • Always position fairlead with WARNING label on top.• Always spool the wire rope onto the drum as indicated by the drum rotation label on the winch.Required for automatic brake to work (if winch is so equipped) and for correct installation orientation.• Always prestretch wire rope and respool under load before use. Tightly wound wire rope reduces chances of "binding", which is wire rope working it's way down into a loosely wound wire rope layer, and catching or damaging itself.Winching Safety:• Always inspect winch installation and wire rope and hook condition before operating winch. Frayed, kinked or damaged wire rope must be replaced immediately. Loose or damaged winch installation must be corrected immediately.• Never hook wire rope back onto itself. This damages the wire rope. Always use a choker chain, wire choker rope or tree trunk protector on the anchor.• Always prior to winching, remove any element that may interfere with safe winch operation.• Always take your time when rigging for a winch pull.• Always be certain the anchor you select will withstand the load, and the strap or chain will not slip.• Never engage or disengage clutch if winch is under load, wire rope is in tension or wire rope drum is moving• Always unspool as much wire rope as possible when rigging. Double line or pick distant anchor point.• Never winch with less than 5 wraps of wire rope around the drum, the wire rope could come loose from the drum. • Always stand clear of wire rope and load during operation.• Never touch wire rope or hook while in tension or under load.• Never touch wire rope or hook while someone else is at the control switch or during winching operation.• Never touch wire rope or hook while remote control is plugged into winch.• Always stand clear of wire rope and load and keep others away while winching.• Always require operator and bystanders to be aware of stability during winching of vehicle and/or load.• Always keep remote control lead clear of the drum, wire rope and rigging. Inspect for cracks, pinches, frayed wires or loose connections. Replace if damaged.Failure to observe these instructions could lead to minor to moderate injury. To avoid injury to hands and fingers:wear heavy leather gloves when handling a wire rope.let wire rope slip through your hands.be aware of possible hot surface at winch motor, drum or wire rope during or after winch use.CAUTIONNeverNeverWinch Failure HazardShock & Fire HazardMoving Parts Entanglement HazardOperating Instructions - continuedSPOOLING IN UNDER LOAD❑The wire rope must always spool onto the bottom of the drum as indicated by decal on the winch.❑Power in the wire rope evenly and tightly on the drum. This prevents the outer wire wraps from drawing into the inner wraps, binding and damaging the wire rope.❑Avoid shock loads when spooling, by using the control switch intermittently to take up wire rope slack. Shock loads can momentarily far exceed the winch and wire rope ratings.❑To prolong the life of the winch, use a snatch block and a double-line rigging technique. This is especially important when pulling heavy loads.SPOOLING IN UNDER NO LOAD❑Assisted: Have your assistant hold the hook with the hook strap putting as much constant tension on the wire rope as possible. While keeping tension, the assistant should walk toward the winchwhile you operate the control switch spooling in the wire rope. Release the switch when the hook isa minimum of 4 ft (1.2m) from the fairlead opening. Spool in the remainder for storage.❑Unassisted: Arrange the wire rope to be spooled so it will not kink or tangle when spooled. Be sure any wire rope on the drum is tightly and evenly layered. Spool enough wire rope to complete thenext full layer on the drum. Tighten and straighten the layer. Repeat process until the hook is aminimum of 4ft (1.2m) from the fairlead. Spool in the remainder for storage.SPOOLING REMAINDER FOR STORAGEKeep hands clear of the wire rope, hook and fairlead opening. Always use the hook strap to hold hook when spooling under no load. Carefully power in the remaining wire rope, jogging the control switch to take up the last of the slack. Secure the hook to a suitable anchor point near the winch. Be careful not to over tighten or damage may occur to the wire rope or anchor point.RIGGING❑Always spool out as much wire rope as possible when preparing rigging. Pick an anchor as far away as is practical; this provides the winch with its greatest pulling power.❑Rigging a double line with a snatch block will reduce the load on the winch to half without significant loss of spooling speed.❑Natural anchors such as trees, stumps and rocks are the handiest when available. Attach the choker chain, wire choker rope or tree trunk protector on the anchor as low as possible to avoid pulling the anchor down. If several possible anchors are available but they are not strong enough individually, it may be practical to attach a wire or chain choker around several anchors to form a strong collective anchor point.。
GPSFox 快速指南说明书

Communication indicator : Symbol
Description COM Port disconnection Data transmission ,COM port busy No data transmission ,COM port idle
If you perform a Hot/Cold Start command, the information of TTFF(Time To First Fix) will display on the TTFF panel.
Fix Mode not Fix 2D 3D
Description Fix not available 2D (<4 SVs used) 3D (>3 SVs used)
Function Bar
Select the COM port with the property baud rate which is connected to GPS receiver Connect/Disconnect with the GPS receiver Perform a hot start command To restore all navigation parameters back to the factory defaults and perform a cold start command
3. Click “Connect to GPS”
and then the NMEA output messages will display in the NMEA View.
The GPSFox is an easy-to-use utility which can display graphically specific NMEA 0183 message received from GPS receiver. There are five information areas, two function bars and some status indicators in the main form.
- 1、下载文档前请自行甄别文档内容的完整性,平台不提供额外的编辑、内容补充、找答案等附加服务。
- 2、"仅部分预览"的文档,不可在线预览部分如存在完整性等问题,可反馈申请退款(可完整预览的文档不适用该条件!)。
- 3、如文档侵犯您的权益,请联系客服反馈,我们会尽快为您处理(人工客服工作时间:9:00-18:30)。
# npx0 npy0 npz0 2 4
# N_MSG_SIZE 0
BLOCK_COMPACT_Z BLOCK_COMPACT_Y OCFD_Barrier 5 5 Iperiodic(1:3) 1 SLz 3.14159265358979d0 Pr
4
0
# Iflag_grid(1),Iflag_grid(2),Iflag_grid(3) 0 # SLx, 1 SLy 0
kstep_show Kstep_save 10000
save_file read_file 0 0
0.003d0 # name of '', '' , 0
savefile, name of initial data file , Init_stat
# Scheme_x+ NL NR 107 0 0
1 11
2 3 4-6
13
1
15
2 3 1 2 3 4 5 6 7
Prandtl 数 Schemit 数 (包含被动标量计算时有效)
Iflag_Amu 粘性系数的计算方法。 0 采用 Satherland 公式计算;1 保持常 数。 T_Ref Isplit: 参考温度。 供 Satherland 公式计算粘性时用,是计算无量纲 化时采用的特征温度。通常采用来流温度。 Volume_Forcex: x 方向的流场外加体积力。 多数情况下为 0。 Force_flag: > 0 表示定流量。 <0 表示定体 积力。 Flux_target: 流量的目标值 Mass_target: 总质量的目标值。 这几个量目前只有“时间 发展的槽道湍流”算例使 用。目的是通过外加体积 力防止湍流衰减。 只有 IBC (41 行第 1 列) 设定为 101 时有效。其他 算例可忽略。
运行本软件需要如下个文件: 文件类型 文件名 1 执行程序 opencfd-1.7.2.out 2 控制文件 opencfd.in 3 网格文件 ocfd-grid.dat 4 5
备注
对于均匀网格不需要网格文件 (见控制文件的说明) 初值文件 由控制文件指定 默认为 opencfd.dat 用 户 自 定 义 数 由控制文件和用户自 用户自定义的程序需要的文件
# Scheme_z0 NL NR 204 # IBC 101 # nk 1 # N_ana 1 #Ian1 Kstep_ana1 nk nr 110 100 1 0 IF_Statistics_init 1 nr 0 nk 0 0 nr 1 0 Tw 1.d0
Turb_model ! RANS & LES modeling 0
行 1 2 3 4 5 6 7 8 9 10 11 12 13 14
文件内容
# OpenCFD 1.7.2/1.7.1 input file #IFLAG_Equation (0 NS, 1 Euler),IFLAG_G,IFLAG_Coordinate (0 Car, 1 Por, 2 Spher) 0 # nx 128 0 ny 161 0 nz 128 LAP 4 4
# Scheme_y- NL NR 108 3 4
104 106 2 3 4 203
401 201 Nx 401
# Scheme_y0 NL NR 204 4 4
Nx-1 Nx-2 Nx-3 201 202 203
201 202
# Scheme_z+ NL NR 107 0 0
# Scheme_z- NL NR 108 0 0
# Scheme_x- NL NR 108 0 0
# Scheme_x0 NL NR 204 0 0 i=1 402 i=1 402 i=1 402 2 3 4 105 Nx Nx-1 Nx-2
# Scheme_y+ NL NR 107 4 3
201 103 2 3
401 103 105 Nx Nx-1 Nx-2 Nx-3 104 106
Mass_target
12000.d0 288.15
16 17 18 19 20 21 22 23 24 25 26 27 28 29 30 31 32 33 34 35 36 37 38 39 40 41 42 43 44 45
# dt
end_time NUM_Time_Advance 10000.d0 3 10
2
第一章 软件 Hoam-OpenCFD 简介
1.1 简介 “复杂流动的直接数值模拟” (Hoam-OpenCFD)软件是在本课题组已有数 值方法及程序基础上进行整理、 综合及并行化而形成的一套并行计算流体力学软 件。该软件的核心是可压缩 Navier-Stokes 方程差分求解器。 本软件的求解器可以求解直角坐标、柱坐标、轴对称旋转体坐标及曲线坐标 的可压缩 Navier-Stokes 方程。其差分库包括目前流行的各类差分格式及本课题 组构造的多种差分方法。 本软件包括两部分:三维计算软件 OpenCFD 和二维计算软件 OpenCFD2d。 目前的最新版本是 OpenCFD ver1.7.2 和 OpenCFD2d ver1.5.1。 1.2 软件安装 本软件需要 Fortran 编译器及 MPI 库。 在 Linux 及 Windows 环境下均可编译。 在 Linux 下安装方法如下: 1) 建立一个子目录,将软件的源程序拷贝入该子目录。 2) 键 入 make 进 行 编 译 即 可 得 到 可 执 行 文 件 。 三 维 求 解 器 为 opencfd-1.7.2.out; 二维求解器为 pencfd2d-1.5.1.out。 3) 将可执行文件拷贝到工作目录中即可完成安装。 本软件同时支持单精度及双精度计算,默认为双精度计算。如果用户使用单 精度计算,需要将 OpenCFD.h (或 OpenCFD2d.h) 中 integer,parameter::OCFD_REAL_KIND=8, OCFD_DATA_TYPE=MPI_DOUBLE_PRECISION 改为: integer,parameter::OCFD_REAL_KIND=4, OCFD_DATA_TYPE=MPI_REAL 即可。 makefile 文件中的编译选项默认编译器为 Intel Fortran 编译器, 如用于采 用其他编译器编译,请根据该编译器的特点修改 makefile 中的编译选项,以提 高计算效率。 1.3 软件的运行方法
复杂流动直接数值模拟软件 Hoam-OpenCFD V1.7.2
使用手册
李新亮 中国科学院力学研究所
第一章:软件简介 1.1 简介 1.2 软件的安装 1.3 软件的运行 第二章:三维计算软件 OpenCFD 使用说明 2.1 简介 2.2 控制文件 opencfd.in 2.3 差分格式的选取 2.3 网格文件 2.4 初值文件 2.5 OpenCFD 的运行和输出 第三章 二维计算软件 OpenCFD2d 使用说明 3.1 简介 3.2 控制文件 opencfd2d.in 3.3 网格及初值文件 3.4 算例 附录: OpenCFD 应用算例
表 2.2 行 3 列 1 2 3
opencfd.in 中各数据的含义
5
7
1 2 3 1 2 3 4
含义 方程类型: 0 为 N-S 方程, 1 为 Euler 方程 是否计算被动标量方程: 0 不含被动标量,1 含被动标量 坐标系: 0 直角坐标系; 1 柱坐标;2 球坐标系 (目前版本不 支持) ; 3 曲线坐标系 (目前版本只支持二维变换) ; 99 旋转 体专用求解器 I -方向的网格数 (nx) (总计算网格数为 nx*ny*nz) J -方向的网格数 (ny) K-方向的网格数 (nz) i- 方向的并行分割块数 注: 本软件采用区域分解法进行并行计 j- 方向的并行分割块数 算,延 3 个方向分别分割成 npx0,npy0 总共为 npx0*npy0*npz0 块。 k- 方向的并行分割块数 和 npz0 块, LAP: 并行处理的交叠区的长度,详见上篇:理论手册。 该长度与数值方法有关,具体选取见表 3 。 通常采用 5,6 阶 格式时 LAP=3; 采用 7,8 阶格式时 LAP=4; 采用更高阶格式时 LAP=5。 设置的 LAP 过小会导致结果错误 ; 设置的 LAP 过 大会造成计算效率下降。
0Hale Waihona Puke 16.28318530717958d0 2.d0 # Re Ama gamma
Sc
Iflag_Amu (0: Sutherland, 1
constant) 15
T_Ref Isplit 6.d0 0
Volume_Forcex 1.4d0 0.0006
Force_flag Flux_target 0.7d0 1.d0 1.d0 2.d0 0 2.d0
N_MSG_SIZE MPI 并行通信方式。 0 默认方式; 使用 MPI_SENDRECV()函数一次完成发送/接收。 -1 将二维数组切割成一维发送/接收 -2 以“用户自定义 MPI 数据类型”完成发送/接收 -3 以“用户自定义 MPI 数据类型” ,且切割成一维完成发送/接收。 > 0 的数据。 把 MPI 消息切割成 N_MSG_SIZE 大小进行传输。
3
据文件
定义模块决定
建立一个子目录,将这些文件拷贝到这个目录,在并行计算机上提交作业即 可 运 行 。 不 同 计 算 机 上 提 交 作 业 的 方 法 不 同 , 例 如 mpirun -np 32 ./opencfd-1.7.2.out, 或 bsub -n 32 "mpijob ./opencfd-1.7.2.out" 等。 具体作 业提交方法可查阅该计算机系统的使用手册。
5
表 2.1 给出了其中一个算例的控制文件 opencfd.in。 该算例计算时间发展槽道 湍流的直接数值模拟。为了下文解释方便,表中左侧一列显示了控制文件的行号 控制文件的内容在表中右侧一栏显示。 控制文件包含了注释行 (即本例子中以“#”号开头的行)和数据行。软 件根据控制文件中的位置读取数据,因此各行的含义固定,不能随意移动。 本软件根据 opencfd.in 文件的数据决定计算采用的方程类型,边界条件,数 值方法及计算参数等。各参数的含义见