测量系统分析参考手册模板
测量系统分析作业指导书样本

测量系统分析作业指引书编制:审核:批准:本制度重要责任部门:生效日期:年月日一.目通过对量具重复性和再现性进行研究,对其浮现变差进行记录分析,来评估测量系统质量。
二.范畴在控制筹划中所提及测量系统。
三.职责3.1 质保部负责编制并更改本操作指引书;3.2质保部负责组织检查员对测量系统进行分析;四.定义4.1 测量系统误差模型:本作业指引书采用误差模型为S.W.I.P.E模型,该模型指出测量系统变差来源于如下几大方面:原则(Standard)、零件(Work)、仪器(I)、人员/程序(Person/Procedure)、环境(E)4.2测量系统:对测量单元进行量化或对被测特性进行评估,所使用仪器或量具、原则、操作、办法、夹具、软件、人员、环境及假设集合。
4.3辨别力:测量装置和原则测量解析度、刻度限制、或最小可检出单位。
与最小可读单位研究,即普通所说最小刻度值,但当仪器刻度较粗略时,容许将最小刻度值估读为本来一半作为仪器可视辨别力。
4.4 重复性:当测量条件已被拟定和定义——在拟定零件、仪器、原则、办法、操作者、环境和假设之下,测量系统内部变差。
4.5再现性:老式上将再现性称为“评价人之间”变差(AV)。
指是不同评价人使用相似仪器对同一产品上同一特性,进行测量所得平均值变差。
但对于操作者不是变差重要因素测量过程,上述说法是不对的。
ASTM定义为:再现性是指测量系统之间或条件之间平均值变差。
它不但涉及评价人变差,同步还也许涉及:量具、实验室及环境不同,除此之外,还涉及重复性。
4.6 偏倚:对相似零件上同一特性观测平均值与真值(参照值)差别。
4.7 线性:在测量设备预期工作(测量)量程内,偏倚值差别。
五.测量系统分析(一)分析原则a) 测量系统分析对象:■测量系统分析针对对象是控制筹划中提及测量系统。
■本作业指引书针对是非破坏性测量系统分析,关于破坏性测量系统分析见《测量系统分析》参照手册第三版。
b) 测量系统分析时机:当浮现如下状况时,应进行测量系统分析:■新品试生产时;■测量系统变更时,如新购量具替代控制筹划中规定量具、量具校准办法或测量程序发生变化等状况。
测量系统分析作业指导书
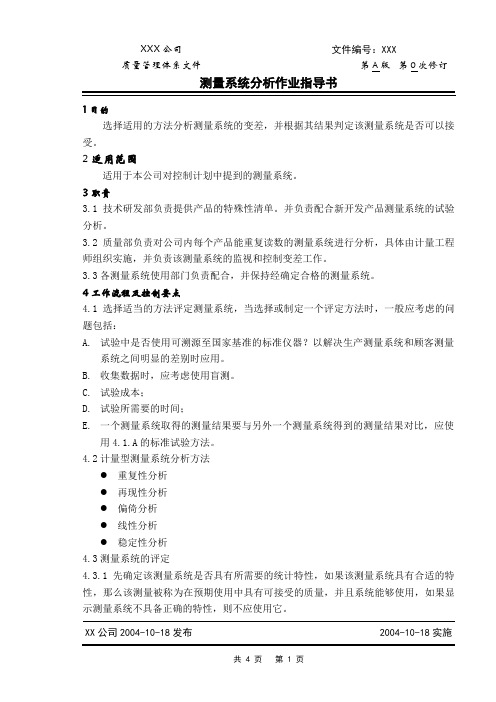
XXX公司文件编号:XXX质量管理体系文件第A版第0次修订测量系统分析作业指导书1目的选择适用的方法分析测量系统的变差,并根据其结果判定该测量系统是否可以接受。
2适用范围适用于本公司对控制计划中提到的测量系统。
3职责3.1技术研发部负责提供产品的特殊性清单。
并负责配合新开发产品测量系统的试验分析。
3.2质量部负责对公司内每个产品能重复读数的测量系统进行分析,具体由计量工程师组织实施,并负责该测量系统的监视和控制变差工作。
3.3各测量系统使用部门负责配合,并保持经确定合格的测量系统。
4工作流程及控制要点4.1选择适当的方法评定测量系统,当选择或制定一个评定方法时,一般应考虑的问题包括:A.试验中是否使用可溯源至国家基准的标准仪器?以解决生产测量系统和顾客测量系统之间明显的差别时应用。
B.收集数据时,应考虑使用盲测。
C.试验成本;D.试验所需要的时间;E.一个测量系统取得的测量结果要与另外一个测量系统得到的测量结果对比,应使用4.1.A的标准试验方法。
4.2计量型测量系统分析方法●重复性分析●再现性分析●偏倚分析●线性分析●稳定性分析4.3测量系统的评定4.3.1先确定该测量系统是否具有所需要的统计特性,如果该测量系统具有合适的特性,那么该测量被称为在预期使用中具有可接受的质量,并且系统能够使用,如果显示测量系统不具备正确的特性,则不应使用它。
XX公司2004-10-18发布2004-10-18实施4.3.2通过试验发现哪种环境因素对测量系统有显著影响。
应采取处理措施,例:如果试验表明环境温度对测量的质量有显著影响,那么,必须在恒温条件下才能测量。
4.3.3通过分析验证一个测量系统一旦被认为可行的,应持续具有恰当的统计特性。
4.3.4根据公司的情况,主要用重复性和再现性对测量系统进行分析,应重复性和再现性(R&R)对测量系统进行分析,具体步骤如下:1)选定测量系统中的产品10件,并按1至10给产品编号,使评价人不看到编号;2)确定测量系统中的评价人2名或3名;3)确定测量系统中的量具一件(经检定合格的);4)让评价人A以随机的顺序测量10个零件,观测人将结果记录在重复性和再现性分析报告上。
MSA手册_(新)

● 分辨力(discrimination)、可读性(readability)、解 析度(resolution)
√ 别名:最小可读单位、测量解析度、最小刻度 极限、或探测的最小极限
√ 由设计所确定的固有特性 √ 一个测量仪器或输出的最小刻度单位 √ 通常被显示为测量单位 √ 10:1 的比例法则 ● 有效解析度(effective resolution) √ 特定应用条件下,一个测量系统对过程变差的
2010 年 6 月
1
MSA 第四版快速指南
测量系统类型 基本计量型
基本计数型 不可重复
(例如,破坏试验) 复杂计量型
复合的系统,量具 或试验标准 其他 其它
MSA 方法 级差,均值制图 信号探测法,假设试验分析法
控制图法
极差法,均值和极差法,方差分析(ANOVA)法, 偏倚,线性,控制图法
表征数据质量最通用的统计特性是测量系统的偏倚和方差。所谓偏倚的特性,是指数据相对 参考(基准)值的位置,而被称为变差的特性是指数据的分布宽度。
低质量数据最普通的原因之一是变差太大。一组数据中的变差多是由于测量系统及其环境相
4
互作用造成的。例如,一个用来测量一罐液体容积的测量系统,可能对该测量系统所处的环 境中的大气温度较敏感。在这种情况下,数据的变差可能是因为环境温度变化造成的。因此, 对测量的数据很难解释,因此,该测量系统不尽理想。
● 性能(performance)
√
长期读数的变化量
√
以总变差(total variation)为基础
● 不确定度(uncertainty)
√
有关被测值的数值估计范围,相信真值包括
在此范围内
测量系统分析MSA手册第四版-测量系统分析msa

对可重复测量系统推荐的实施方法 试验程序范例 计量型测量系统研究- 指南 用于确定稳定性的指南 确定偏倚的指南- 独立样本法 确定偏倚的指南- 控制图法 确定性的指南 确定重复性和再现性的指南 极差法 平均值和极差法 方差分析法(ANOVA)
计数型测量系统研究 风险分析法 信号检查(signal detection)方法 分析方法 其他测量概念和实践 不可重复的测量系统的实践 稳定性研究 变差研究 识别过大的零件内部变差的影响
3
MSA手册第四版
第 E 节 平均值和极差法—额外的处理 第 F 节 量具性能曲线 第 G 节 通过多次读值减少变差 第 H 节 聚焦标准差法计算 GRR 附录 附录 A 方差分析的概念 附录 B
GRR 对能力指数 Cp 的影响 公式 分析 图形分析 附录 C 附录 D 量具 R 研究 附录 E 用误差修正术语替代 PV 计算 附录 F P.I.S.M.O.E.A 误差模型 术语 参考文献 范例表格 索引
第 D 节 测量资源的开发 量具资源选择过程
第 E 节 测量问题 第 F 节 测量不确定度 第 G 节 测量问题分析 第二章 用于评估测量系统的基本概念 第 A 节 背景 第 B 节 选择/开发试验程序 第 C 节 测量系统研究的准备 第 D 节 结果分析
第三章 第A节 第B节
第C节
第四章 第A节 第B节 第C节 第D节
4
MSA手册第四版
第一章 测量系统总指南 第一章---第 A 节 引言、目的及术语
引言
测量数据的使用比以前更多更广泛了。例如,现在是否对制造过程进行调整的决定通常以测 量数据为基础,将测量数据或一些从它们所计算出的统计值,与这一过程的统计控制限 (statistical control limits)相比较,如果该比较过程已超出统计控制,则进行某种调整,否 则,该过程将被允许在没有调整的状态下运行。测量数据的另一个用处是确定在两个或更多 变量之间是否存在显著的相互关系。例如,如果怀疑一个模塑零件上的一个关键尺寸和注射 材料的温度有关。这种可能的关系可以通过采用所谓回归分析的统计方法来研究,即比较关 键尺寸的测量值和注射材料的温度测量值
MSA测量系统分析参考手册(doc 204页)

内部资料严禁翻印测量系统分析参考手册第三版1990年2月第一版1995年2月第一版;1998年6月第二次印刷2002年3月第三版©1990©1995©2002版权由戴姆勒克莱斯勒、福特和通用汽车公司所有测量系统分析参考手册第三版1990年2月第一版1995年2月第一版;1998年6月第二次印刷2002年3月第三版©1990©1995©2002版权由戴姆勒克莱斯勒、福特和通用汽车公司所有本参考手册是在美国质量协会(ASQ)及汽车工业行动集团(AIAG)主持下,由戴姆勒克莱斯勒、福特和通用汽车公司供方质量要求特别工作组认可的测量系统分析(MSA)工作组编写,负责第三版的工作组成员是David Benham(戴姆勒克莱斯勒)、Michael Down (通用)、Peter Cvetkovski(福特),以及Gregory Gruska(第三代公司)、Tripp Martin(FM 公司)、以及Steve Stahley(SRS技术服务)。
过去,克莱斯勒、福特和通用汽车公司各有其用于保证供方产品一致性的指南和格式。
这些指南的差异导致了对供方资源的额外要求。
为了改善这种状况,特别工作组被特许将克莱斯勒、福特和通用汽车公司所使用的参考手册、程序、报告格式有及技术术语进行标准化处理。
因此,克莱斯勒、福特和通用汽车公司同意在1990年编写并以通过AIAG分发MSA手册。
第一版发行后,供方反应良好,并根据实际应用经验,提出了一些修改建议,这些建议都已纳入第二版和第三版。
由克莱斯勒、福特和通用汽车公司批准并承认的本手册是QS-9000的补充参考文件。
本手册对测量系统分析进行了介绍,它并不限制与特殊生产过程或特殊商品相适应的分析方法的发展。
尽管这些指南非覆盖测量系统通常出现的情况,但可能还有一些问题没有考虑到。
这些问题应直接向顾客的供方质量质量保证(SQA)部门提出。
测量系统分析指导书MSA

1.目的介绍测量系统质量评定的方法,确定测量系统的适用性、经济性、以确保本公司测量数据质量。
2.范围凡列在本公司产品控制计划上的量具均适用。
3.参考《测量系统分析》参考手册。
4.定义4.1 R&R:即“量具重复性和再现性”的缩写。
4.2 重复性:由一个评价人,采用一种测量仪器,多次测量同一零件的同一特性时,获得的测量量变差。
4.3 再现性:由不同评价人,采用相同的测量仪器,测量同一零件的同一特性时,测量平均值的变差。
4.4 偏倚:是测量结果的观察平均值与基准值的差值。
4.5 稳定性:是测量系统在某持续时间内测量同一基准或零件的单一特性时获得的测量总变差。
4.6 线性:是在量具预期的工作范围内,偏倚值的差值。
5.作业内容5.1 概述5.1.1 对测量数据最有影响的是测量系统的变差。
其主要因素有:量具的偏椅/重复性/再现性/稳定性/线性等。
这些都起因于量具的磨损、劣化、操作程序、操作环境、操作员等。
5.1.2 评价测量数据的信赖性时,上述5.1.1要素中,重复性和再现性对数据特别重要的影响,本指导书将予以重点介绍,与之同时对其余要素作一般介绍。
5.2 量具的重复性和再现性5.2.1 计量型测量系统评价方法—均值和极度差法。
使用记录《量具重复性和再现性数据表》。
5.2.1.1 数据的收集A.随机采取包含十个零件的一个样本,且样本中零件的规格及公差要求相同。
B.按1至10给零件编号,同时指定评价人A、B、C三名(要求熟悉或从事此类工作者),要求使评价人不能看到这些数字。
C.让评价人A以随机的顺序测量10个零件并让另一个观测人将结果记录在第一行对应列内,让评价人B和C测量10个零件且互相不看对方数据,然后将结果分别填入相应的记录单中。
D.使用不同的随机测量顺序重复C步骤操作过程,E.将所有的数据统一输入电脑,由系统自动计算结果及图表,同时打印报告。
5.2.1.2量具的重复性和再现性的判定基准如下:A.小于10%的误差(%R&R)—可接受的测系统;B. 10%~30%的误差—基于应用的重要性,测量装置的成本,维修成本等可能是可接受的;C.大于30% —认为是不可接受—应努力改良的测量系统。
测量系统分析作业指导书(含表格)

测量系统分析作业指导书(IATF16949 -2016)1、目的:通用应用适当的统计技术,对评价产品的测量系统进行分析,确保其能够对产品进行有效测量并提供质量保证。
2、适用范围:适用于汽车类产品控制计划中使用的检验量具、仪器。
3、职责:品管部:需要时拟定汽车类产品的测量系统分析计划并执行。
各部门:协助品管部搜集MSA数据,且MSA分析结果为不可接受时进行改善。
4、定义:4.1测量系统(Measurement system):用来对被测特性赋值的操作、程序、量具、设备、软件以及操作人员的集合,用来获得测量结果的整个过程。
4.2偏倚(Bias):指测量结果的观测平均值与基准值的差值。
4.3稳定性(Stability):指测量系统在某持续时间内测量同一基准或零件的单一特性时获得的测量平均值总变差,即偏倚随时间的变化。
4.4重复性(Repeatability):是指由同一位评价人,采用同一量具,多次测量同一产品的同一质量特性时获得的测量值的变差。
4.5再现性 (Reproducibility) :是指由不同评价人用同一量具,多次测量同一产品的同一质量特性时获得的测量平均值的变差。
4.6分辨力(Resolution):测量系统检出并如实指示被测特性中极小变化的能力。
4.7线性(Linearity):量具在预期工作范围内,偏移值的差值。
4.8盲测:指在实际测量环境中,操作者事先不知正在对该测量系统进行评价,也不知道所测为哪一只产品的条件下所获得的测量结果。
4.9计量型测量系统:测量系统的测量结果可用具体的连续的数值来表述,这样的测量系统称之为计量型测量系统;4.10计数型测量系统:测量系统的测量结果与某些指定限值相比较,如果满足限值则接受该零件否则拒收。
如用通过或不能通过塞规的方式来描述一只钢管直径尺寸,这样的测量系统称之为计数型测量系统。
5、作业内容:5.1测量系统分析条件:5.1.1测量作业必须标准化;5.1.2评价人必须是从日常熟练操作该仪器的人中挑选;5.1.3测量仪器必须是处于校验合格状态;5.1.4质量特性测量值可重复。
测量系统分析指导书

= %
总变差(TV)
TV
=
ndc=1.41(PV/GRR)
=1.41(/)
=
所有计算均基于预计5.15σ(正态分布曲线下99.0%的面积)。
表E3XXXXXXXX有限公司汽车齿轮总厂
零件名称:技术要求:日期:
工序号:量具名称:操作者:
检测项目:量具编号:
重复性极差控制图
UCLR=数据见测量系统分析报告之一
6.1计量仪器、带表检具及万能量具的GRR实施方法和结果评估。
6.1.1带表检具及万能量具由使用部门组织并确定三位测量者,并从过程中抽取有代表性的10个零件(选定的零件应考虑到零件加工过程中可能波及的范围),同时做好标记。每个测量者代号(A,B,C)测量10个零件三次,并分别记录在JJ/SQC-69“测量系统分析数据采集卡”输入电脑,电脑需计算的数据有:
5.2.6卡板的MSA,进行GRR分析。
5.3对在控制计划中出现的万能量具,由使用部门按控制计划组织MSA,对同一类万能量具用于同一大类的产品、同一工艺、同一精度允许只选取一种作为代表性的来做GRR分析分析方法,根据客户要求分为GRR和Cg。
5.4对带表检具全部实施MSA,但对一台多参数专用检具,允许只对最小公差的检测项进行MSA。分析方法根据客户要求分为GRR和Cg。周期为检具六个月。
6.3.2数据记录规定如下:如果测量结果合格记录“1”,测量不合格记录“0”
6.3.3专用量具计数型的评估原则,如果20个零件,三个测量者结果一致,那此量具为可接受的。
如果20个零件中,三个测量者有一个零件的测量结果不同,那需要从新选20个零件再做分析。
(注:凡在过程控制中,用于SPC控制点的量具需按周期做MSA分析。)
测量系统分析(MSA)作业指导书

力嘉精密有限公司 VIGOR PRECISION LTD.
ISO/TS16949:2002 工作指示(測量系統分析)
WI-DGQC-WK-02-01 标题
偏倚 i = ∑ 偏倚 i , j m
j =1
m
式中:i 为零件序; j 为测量次数的序号; Xi,j 表示第 i 个零件第 j 次的测量读数 ⑤ 在线性图上画出相对于参考值的每个偏倚及偏倚的平均值。 ⑥ 应用以下公式,计算并画出最适合的线(拟合直线)及该线的置信度区间,并 在线性图上画出来。 最适合的线(拟合直线)的方程为:y=aX+b 其中:a=
2007-7-17 3
力嘉精密有限公司 VIGOR PRECISION LTD.
ISO/TS16949:2002 工作指示(測量系統分析)
WI-DGQC-WK-02-01 标题
ø ø ø ø ø
仪器产生错误的尺寸。 仪器所测量的特性有误。 仪器没有经过适当的校准。对校准程序进行评审。 评价者使用仪器的方法不正确。对测量指导书进行评审。 仪器纠正的指令错误。 见图2 MSA Bias Report
(四)线性分析 1、图示法 ① 选择至少五个零件(g≥5) ,以覆盖被研究量具的整个工作量程。 ② 对每个零件进行全尺寸测量,以确定每个零件的参考值,并确定是否覆盖了被 研究量具的整个工作量程。 ③ 让经常使用该量具的操作者按正常程序测量每个零件至少 10 次(m≥10) 。 注:测量时,尽量随机选择零件,以提高分析的可信度。 ④ 计算零件每次测量的偏倚,以及每个零件的偏倚平均值。 偏倚 i,j=Xi,j -(参考值)i
WI-DGQC-WK-02-01 标题
一、目的 为公司各类简单的计量型、计数型量具的测量系统分析提供指导。 二、参考文件 测量系统分析参考手册 三、术语 1、 测量系统误差模型:本作业指导书采用的误差模型为 S.W.I.P.E 模型,该模型指 出测量系统变差来源于以下几大方面: 标准 (Standard) 、 零件 (Work) 、 仪器 (I) 、 人员/程序(Person/Procedure) 、环境(E) 2、 测量系统:对测量单元进行量化或对被测的特性进行评估,所使用的仪器或量 具、标准、操作、方法、夹具、软件、人员、环境及假设的集合。 3、 分辨力:测量装置和标准的测量分辨率、刻度限制、或最小可检出的单位。与 最小可读单位研究,即通常所说的最小刻度值,但当仪器刻度较粗略时,允许 将最小刻度值估读为原来的一半作为仪器的可视分辨力。 4、 重复性:当测量条件已被确定和定义——在确定的零件、仪器、标准、方法、 操作者、环境和假设之下,测量系统内部的变差。 5、 再现性:传统上将再现性称为“评价人之间”的变差(AV) 。指的是不同评价 人使用相同的仪器对同一产品上的同一特性,进行测量所得的平均值的变差。 但对于 操作者不是 变差的主要 原因 的测量过程,上述说法是不正确的。ASTM 的定义为:现现性是指测量的系统之间或条件之间的平均值变差。它不但包括 评价人的变差,同时还可能包括:量具、试验室及环境的不同,除此之外,还 包括重复性。 6、 偏倚:对相同零件上同一特性的观测平均值与真值(参考值)的差异。 7、 线性:在测量设备预期的工作(测量)量程内,偏倚值的差异。 四、测量系统分析 (一)分析的原则 1、测量系统分析的对象 测量系统分析针对的对象是控制计划中提及的测量系统。 本作业指导书针对的是非破坏性的测量系统分析, 关于破坏性的测量系统 的分析见《测量系统分析》参考手册第三版。 2、测量系统分析时机 当出现以下情况时,应进行测量系统分析: n 新汽车产品项目开发时或客户有要求时; n 测量系统变更时,如新购量具替换控制计划中规定的量具、量具的校 准方法或测量程序发生变化等情况。 3、计量型量具的分辨力
MSA测量系统分析手册范本

本手册对测量系统分析进行了介绍,它并不限制与特殊生产过程或特殊商品相适应的分 析方法的发展。尽管这些指南非覆盖测量系统通常出现的情况,但可能还有一些问题没有考 虑到。这些问题应直接向顾客的供方质量质量保证(SQA)部门提出。如果不知如何与有 关的 SQA 部门联系,在顾客采购部的采购员可以提供帮助。
五
其它
White Papers 可在
http:
//www.,/publications/quality/msa3.html
中
查到
注:关于 GRR 标准差的使用
传统上,惯例是用 99%的分布代表测量误差的“全”分布,由系数 5.15 表示(此处, σGRR 乘以 5.15 用来表示全分布的 99%)。
MSA 工作组衷心感谢:戴姆勒克莱斯勒汽车公司副总裁 Tom Sidlik、福特汽车公司 Carlos Mazzorin,以及通用汽车公司 Bo Andersson 的指导和承诺;感谢 AIAG 在编写、 出版、分发手册中提供的帮助;感谢特别工作组负责人 Hank Gryn(戴姆勒克莱斯勒)、 Russ Hopkins(福特)、Joe Bransky(通用),Jackie Parkhurst(通用(作为代表与 ASQ 及美国试验与材料协会(国际 ASTM)的联系。编写这本手册以满足汽车工业界的特 殊需要。
级差,均值和极差,方差分析(ANOVA),偏倚,线性, 三
测量系统分析(MSA)作业指导书

测量系统分析(MSA)作业指导书1.目的:对所有量具、量测及试验设备实施统计分析,藉以了解量具系统之准确度与精确度。
2. 范围:所有控制计划(Control Plan)中包含的/或客户要求的各种量测系统均适用之.3.定义:3。
1 MSA:测量系统分析3.2 量具:是指任何用来获得测量结果的装置。
经常是用在工厂现场的装置,包括通/止规(go/no go device).3。
3 量测系统:是对测量单元进行量化或对被测的特性进行评估,其所使用的仪器或量具、标准、操作、方法、夹具、软件、人员、环境和假设的集合;也就是说,用来获得测量结果的整个过程。
3.4量具重复性(EV): 一个评价人多次使用一件测量仪器,对同一零件的某一特性进行多次测量下的变差。
3。
5 量具再现性(AV): 由不同的评价人使用相同的量具,测量一个零件的一个特性的测量平均值的变差。
3.6偏性:同一人使用同一量具在管制计划规划地点与在实验室量测同一产品之相同特性所得平均值与真值之间的差异。
3.7稳定性:指同一量具于不同时间量测同一零件之相同特性所得之变异。
3.8线性:指量具在预期内之偏性表现。
4.权责:4.1量测系统测试的排定、数据分析、仪器操作人员的选择: 品保部4。
2测试执行:各相关单位4.3 MSA操作人员的培训: 品保部5. 执行方法5.1 QA工程师人员依公司PCP文件建立《xx年MSA实施计划表》或客户要求,并依据计划表之排程进行对仪器做量测系统分析。
5。
2 取样方法:5.2.1计量型取样:从代表整个工作范围的过程中随机抽取10件样品,但所抽取的10件样品其数值必须涵盖该产品过程分布(也可用之前类似过程的过程能力或者过程标准差代表TV进行计算)。
5。
2.2计数型取样:取50PCS样品,其中包含临近值,不良品与合格品。
5.2。
3.测量过程中需要考虑盲测,由2或3个测量者随机抽取对每个产品各测量取一定数量样品.5.3计数型:5。
3.1被评价的零件的选定随机抽取50个零件,把零件编号,由研究小组给出该50个零件的标准,必须含合格,不合格,模糊品,条件允许的情况下最好各占1/3。
M S A手册

测量系统分析参考手册第三版1990年2月第一版1995年2月第一版;1998年6月第二次印刷2002年3月第三版©1990©1995©2002版权由戴姆勒克莱斯勒、福特和通用汽车公司所有前言本参考手册是在美国质量管理协会(ASQC)汽车部及汽车工业行动集团(AIAG)主持下,由克莱斯勒、福特和通用汽车公司供方质量要求特别工作组认可的测量系统分析(MSA)工作组编写,负责第二版的工作组成员是Ray Daugherty(克莱斯勒)、Victor Lowe,Jr.(福特)、Michael H.Down主席(通用),以及Gregory Gruska(第三代公司)。
过去,克莱斯勒、福特和通用汽车公司各有其用于保证供方产品一致性的指南和格式。
这些指南的差异导致了对供方资源的额外要求。
为了改善这种状况,特别工作组被特许将克莱斯勒、福特和通用汽车公司所使用的参考手册、程序、报告格式有及技术术语进行标准化处理。
因此,克莱斯勒、福特和通用汽车公司同意在1990年编写并以通过AIAG分发MSA 手册。
第一版发行后,供方反应良好,并根据实际应用经验,提出了一些修改建议,这些建议都已纳入第二版。
由克莱斯勒、福特和通用汽车公司批准并承认的本手册可由供方在制造过程和满足QS-9000要求中用来实现MSA技术。
本手册对测量系统分析进行了介绍,它并不限制与特殊生产过程或特殊商品相适应的分析方法的发展。
尽管这些指南非覆盖测量系统通常出现的情况,但可能还有一些问题没有考虑到。
这些问题应直接向顾客的供方质量质量保证(SQA)部门提出。
如果不知如何与有关的SQA部门联系,在顾客采购部的采购员可以提供帮助。
特别工作组衷心感谢:戴姆勒克莱斯勒汽车公司副总裁Thomas T.Stallkamp、福特汽车公司Norman F.Ehlers,以及通用汽车公司Harold R.Kutner的指导和参与;感谢AIAG 在编写、出版、分发手册中提供的帮助;感谢特别工作组负责人Russell Jacobs(克莱斯勒)、Stephen Walsh(福特)、Dan Reid(通用)的指导,以及ASQC给予的关心帮助。
测量系统分析指导书模板

测量系统分析指导书1目的本规定具体明确进行“测量系统分析”的方法,以确定测量系统是否具有恰当的统计特性,并根据对研究结果的分析来评估所使用的量具或设备的测量能力是否能达到预期的要求。
2 适用范围:本规定适用于由控制计划规定的量具或测试设备并指出其相对应的关键特性。
3 术语或缩语3.1 重复性Repeatability :是用一个评价人,使用相同测量仪器,对同一零件上的同一特性进行多次测量所得到的测量变差。
3.2 再现性Reproducibility :是用不同的评价人,使用相同的测量仪器,对同一零件上的同一特性进行测量所得的平均值的变差。
3.3 重复性和再现性(GRR ):测量系统重复性和再现性联合估计值。
3.4 Cg :检具能力指数。
4 程序4.1流程图4.2 职责4.2.1 质量保证部负责对本工作规定的建立,保持和归口管理。
4.2.2 使用部门按控制计划要求,编制测量系统分析计划,上报质量保证部批准,使用部门准备样件,实施,提供报告。
质量保证部负责结果评价。
4.2.3 人力资源部负责人员培训。
4.2.4 量具使用部门归档保存相应记录。
5 测量系统分析:5.1 根据客户的要求来确定MSA,现场使用的计量器具,用于大众产品用Cg值来评估,用于通用的产品的用GRR来评估,其余的产品根据客户要求来定,客户无要求的采用GRR分析。
5.2 计量仪器的MSA,采用GRR来分析。
测量仪器按对应的测量产品来做评估,但对同一大类的产品,同一种工艺允许只选取一种零件作为代表性的来做GRR分析。
5.2.1 CMM的MSA,可从控制计划中选取具有代表性的零件进行,项目包括位置尺寸、几何尺寸进行GRR 分析。
5.2.2 齿轮测量中心的MSA,可根据齿轮加工特性,选取对最终的齿轮精度有影响加工工艺(如插齿、剃齿、珩齿、磨齿、成品)进行GRR分析。
项目选取:周节累积误差、相邻齿距误差、平均齿向角度误差、平均齿形角度误差。
测量系统分析(MSA)指导书

测量系统分析(MSA)指导书1、目的通过MSA,了解测量变差的来源,测量系统能否被接受,测量系统的主要问题在哪里,并针对问题适时采取纠正措施。
2、适用范围适用于公司产品质量控制计划中列出的测量系统。
3、职责3.1 质量部计量室负责编制MSA计划并组织实施。
3.2 各相关部门配合做好MSA工作。
4、工作程序4.1 测量系统分析(MSA)的时机4.1.1初次分析应在试生产中且在正式提交PPAP之前进行。
4.1.2一般每间隔一年要实施一次MSA。
4.1.3在出现以下情况时,应适时增加分析频次和重新分析:(1)量具进行了较大的维修;(2)量具失准时;(3)顾客需要时;(4)重新提交PPAP时;(5)测量系统发生变化时。
4.2 测量系统分析(MSA)的准备要求4.2.1制定MSA计划,包括以下内容:(1)确定需分析的测量系统;(2)确定用于分析的待测参数/尺寸或质量特性;(3)确定分析方法:对计量型测量系统,可采用极差法和均值极差法;对计数型测量系统,可采用小样法;(4)确定测试环境:应尽可能与测量系统实际使用的环境条件相一致;(5)对于破坏性测量,由于不能进行重复测量,可采用模拟的方法并尽可能使其接近真实分析(如不可行,可不作MSA分析);(6)确定分析人员和测量人员;(7)确定样品数量和重复读数次数。
4.2.2量具准备(1)应针对具体尺寸/特性选择有关作业指导书指定的量具,如有关作业指导书未明确规定某种编号的量具,则应根据实际情况对现场使用的一个或多个量具作MSA分析;(2)确保要分析的量具是经校准合格的;(3)起的分辨力i一般应小于被测参数允许查T的1/10,即i<T/10。
在仪器读数中,如有可能,读数应取值最小刻度的一半。
4.2.3测试操作人员和分析人员的选择(1)在MSA分析时,测试操作人员和分析人员不能是同一个人,测试操作(2)人员实施测量并读数,分析人员作记录并完成随后的分析工作;应优先选择通常情况下实际使用所选定的量具实施测试的操作工/检验员作为测试操作人员,以确保测试方法和测试结果与日后的正式生产或过程更改的实际情况相符;(3)应选择熟悉测试和MSA分析方法的人员作为分析人员。
MSA手册(第三版)

内部资料严禁翻印测量系统分析参考手册第三版1990年2月第一版1995年2月第一版;1998年6月第二次印刷2002年3月第三版©1990©1995©2002版权由戴姆勒克莱斯勒、福特和通用汽车公司所有本参考手册是在美国质量协会(ASQ)及汽车工业行动集团(AIAG)主持下,由戴姆勒克莱斯勒、福特和通用汽车公司供方质量要求特别工作组认可的测量系统分析(MSA)工作组编写,负责第三版的工作组成员是David Benham(戴姆勒克莱斯勒)、Michael Down (通用)、Peter Cvetkovski(福特),以及Gregory Gruska(第三代公司)、Tripp Martin(FM 公司)、以及Steve Stahley(SRS技术服务)。
过去,克莱斯勒、福特和通用汽车公司各有其用于保证供方产品一致性的指南和格式。
这些指南的差异导致了对供方资源的额外要求。
为了改善这种状况,特别工作组被特许将克莱斯勒、福特和通用汽车公司所使用的参考手册、程序、报告格式有及技术术语进行标准化处理。
因此,克莱斯勒、福特和通用汽车公司同意在1990年编写并以通过AIAG分发MSA手册。
第一版发行后,供方反应良好,并根据实际应用经验,提出了一些修改建议,这些建议都已纳入第二版和第三版。
由克莱斯勒、福特和通用汽车公司批准并承认的本手册是QS-9000的补充参考文件。
本手册对测量系统分析进行了介绍,它并不限制与特殊生产过程或特殊商品相适应的分析方法的发展。
尽管这些指南非覆盖测量系统通常出现的情况,但可能还有一些问题没有考虑到。
这些问题应直接向顾客的供方质量质量保证(SQA)部门提出。
如果不知如何与有关的SQA部门联系,在顾客采购部的采购员可以提供帮助。
MSA工作组衷心感谢:戴姆勒克莱斯勒汽车公司副总裁Tom Sidlik、福特汽车公司Carlos Mazzorin,以及通用汽车公司Bo Andersson的指导和承诺;感谢AIAG在编写、出版、分发手册中提供的帮助;感谢特别工作组负责人Hank Gryn(戴姆勒克莱斯勒)、Russ Hopkins (福特)、Joe Bransky(通用),Jackie Parkhurst(通用(作为代表与ASQ及美国试验与材料协会(国际ASTM)的联系。
测量系统分析工作指导书
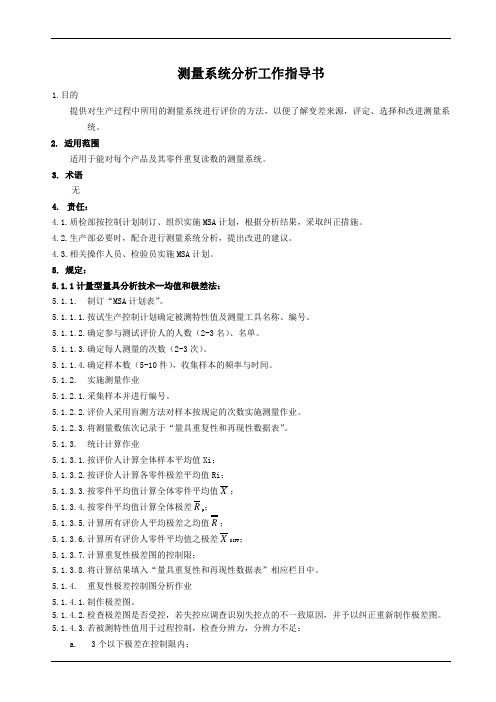
测量系统分析工作指导书1.目的提供对生产过程中所用的测量系统进行评价的方法,以便了解变差来源,评定、选择和改进测量系统。
2. 适用范围适用于能对每个产品及其零件重复读数的测量系统。
3. 术语无4.责任:4.1.质检部按控制计划制订、组织实施MSA计划,根据分析结果,采取纠正措施。
4.2.生产部必要时,配合进行测量系统分析,提出改进的建议。
4.3.相关操作人员、检验员实施MSA计划。
5. 规定:5.1.1计量型量具分析技术--均值和极差法:5.1.1. 制订“MSA计划表”。
5.1.1.1.按试生产控制计划确定被测特性值及测量工具名称、编号。
5.1.1.2.确定参与测试评价人的人数(2-3名)、名单。
5.1.1.3.确定每人测量的次数(2-3次)。
5.1.1.4.确定样本数(5-10件),收集样本的频率与时间。
5.1.2. 实施测量作业5.1.2.1.采集样本并进行编号。
5.1.2.2.评价人采用盲测方法对样本按规定的次数实施测量作业。
5.1.2.3.将测量数依次记录于“量具重复性和再现性数据表”。
5.1.3. 统计计算作业5.1.3.1.按评价人计算全体样本平均值Xi;5.1.3.2.按评价人计算各零件极差平均值Ri;5.1.3.3.按零件平均值计算全体零件平均值X;5.1.3.4.按零件平均值计算全体极差R p;5.1.3.5.计算所有评价人平均极差之均值R;5.1.3.6.计算所有评价人零件平均值之极差X DIFF;5.1.3.7.计算重复性极差图的控制限;5.1.3.8.将计算结果填入“量具重复性和再现性数据表”相应栏目中。
5.1.4. 重复性极差控制图分析作业5.1.4.1.制作极差图。
5.1.4.2.检查极差图是否受控,若失控应调查识别失控点的不一致原因,并予以纠正重新制作极差图。
5.1.4.3.若被测特性值用于过程控制,检查分辨力,分辨力不足:a. 3个以下极差在控制限内;4个以下极差在控制限内,且1/4的极差为零;5.1.4.4.若分辨力不足应更换测量工具。
测量系统分析参考手册(PDF 161页)

替代的方法 白皮书---可上网查询,网址
章节 三
三 四
三、四
三、四
五
注:关于 GRR 标准差的使用
2
目录
第一章 测量系统总指南 第 A 节 引言、目的及术语
引言 目的 术语 第 B 节 测量过程 测量系统 测量系统变差的影响 第 C 节 测量策划和计划
本手册的目的是为评定测量系统的质量提供指南。尽管这些指南足以用于任何测量系统,但 主要用于工业界的测量系统。本手册不打算作为所有测量系统的一种分析总览,而是主要用 于那些注每个零件能重复读数的测量系统。许多分析对于其它形式的测量系统也是很有用的, 并且该手册的确包含了参考意见和建议,但对更复杂的或不常用的方法在此没有讨论,建议 使用者参考适宜的统计资源。本手册也不涵盖顾客对测量系统分析方法所要求的批准。
对可重复测量系统推荐的实施方法 试验程序范例 计量型测量系统研究- 指南 用于确定稳定性的指南 确定偏倚的指南- 独立样本法 确定偏倚的指南- 控制图法 确定性的指南 确定重复性和再现性的指南 极差法 平均值和极差法 方差分析法(ANOVA) 计数型测量系统研究 风险分析法 信号检查(signal detection)方法 分析方法 其他测量概念和实践 不可重复的测量系统的实践 稳定性研究 变差研究 识别过大的零件内部变差的影响
2010 年 6 月
1
MSA 第四版快速指南
测量系统类型 基本计量型
基本计数型 不可重复
(例如,破坏试验) 复杂计量型
复合的系统,量具 或试验标准 其他 其它
MSA 方法 级差,均值和极差,方差分析(ANOVA),偏倚,线
性,控制图 信号探测法,假设试验分析法
- 1、下载文档前请自行甄别文档内容的完整性,平台不提供额外的编辑、内容补充、找答案等附加服务。
- 2、"仅部分预览"的文档,不可在线预览部分如存在完整性等问题,可反馈申请退款(可完整预览的文档不适用该条件!)。
- 3、如文档侵犯您的权益,请联系客服反馈,我们会尽快为您处理(人工客服工作时间:9:00-18:30)。
测量系统分析参考
手册模板
内部资料严禁翻印
测量系统分析
参考手册
第三版
1990年2月第一版
1995年2月第一版; 1998年6月第二次印刷
3月第三版
©1990©1995© 权
由戴姆勒克莱斯勒、福特和通用汽车公司所有
测量系统分析
参考手册
第三版
1990年2月第一版
1995年2月第一版; 1998年6月第二次印刷
3月第三版
©1990©1995© 权
由戴姆勒克莱斯勒、福特和通用汽车公司所有
前言
本参考手册是在美国质量协会( ASQ) 及汽车工业行动集团( AIAG) 主持下, 由戴姆勒克莱斯勒、福特和通用汽车公司供方质量要求特别工作组认可的测量系统分析( MSA) 工作组编写, 负责第三版的工作组成员是David Benham( 戴姆勒克莱斯勒) 、Michael Down( 通用) 、Peter Cvetkovski( 福特) , 以及Gregory Gruska( 第三代公司) 、Tripp Martin( FM公司) 、以及Steve Stahley( SRS技术服务) 。
过去, 克莱斯勒、福特和通用汽车公司各有其用于保证供方产品一致性的指南和格式。
这些指南的差异导致了对供方资源的额外要求。
为了改进这种状况, 特别工作组被特许将克莱斯勒、福特和通用汽车公司所使用的参考手册、程序、报告格式有及技术术语进行标准化处理。
因此, 克莱斯勒、福特和通用汽车公司同意在1990年编写并以经过AIAG分发MSA手册。
第一版发行后, 供方反应良好, 并根据实际应用经验, 提出了一些修改建议, 这些建议都已纳入第二版和第三版。
由克莱斯勒、福特和通用汽车公司批准并承认的本手册是QS-9000的补充参考文件。
本手册对测量系统分析进行了介绍, 它并不限制与特殊生产过程或特殊商品相适应的分析方法的发展。
尽管这些指南非覆盖测量
系统一般出现的情况, 但可能还有一些问题没有考虑到。
这些问题应直接向顾客的供方质量质量保证( SQA) 部门提出。
如果不知如何与有关的SQA部门联系, 在顾客采购部的采购员能够提供帮助。
MSA工作组衷心感谢: 戴姆勒克莱斯勒汽车公司副总裁Tom Sidlik、福特汽车公司Carlos Mazzorin, 以及通用汽车公司Bo Andersson的指导和承诺; 感谢AIAG在编写、出版、分发手册中提供的帮助; 感谢特别工作组负责人Hank Gryn( 戴姆勒克莱斯勒) 、Russ Hopkins( 福特) 、Joe Bransky( 通用) , Jackie Parkhurst( 通用( 作为代表与ASQ及美国试验与材料协会( 国际ASTM) 的联系。
编写这本手册以满足汽车工业界的特殊需要。
戴姆勒克莱斯勒、福特和通用汽车公司于后取得了本手册的版权和所有权。
如果需要, 可向AIAG订购更多的本手册, 和/或在得到AIAG的许可下, 复制本手册的部分内容, 在各供方组织内使用。
( AIAG联系电话: 248-358-3570) 。
3月
前言
本参考手册是在美国质量管理协会( ASQC) 汽车部及汽车工业行动集团( AIAG) 主持下, 由克莱斯勒、福特和通用汽车公司供方质量要求特别工作组认可的测量系统分析( MSA) 工作组编写, 负责第二版的工作组成员是Ray Daugherty( 克莱斯勒) 、Victor Lowe, Jr.(福特)、Michael H.Down主席( 通用) , 以及Gregory Gruska( 第三代公司) 。
过去,克莱斯勒、福特和通用汽车公司各有其用于保证供方产品一致性的指南和格式。
这些指南的差异导致了对供方资源的额外要求。
为了改进这种状况, 特别工作组被特许将克莱斯勒、福特和通用汽车公司所使用的参考手册、程序、报告格式有及技术术语进行标准化处理。
因此, 克莱斯勒、福特和通用汽车公司同意在1990年编写并以经过AIAG分发MSA手册。
第一版发行后, 供方反应良好, 并根据实际应用经验, 提出了一些修改建议, 这些建议都已纳入第二版。
由克莱斯勒、福特和通用汽车公司批准并承认的本手册可由供方在制造过程和满足QS-9000要求中用来实现MSA技术。
本手册对测量系统分析进行了介绍, 它并不限制与特殊生产过程或特殊商品相适应的分析方法的发展。
尽管这些指南非覆盖测量系统一般出现的情况, 但可能还有一些问题没有考虑到。
这些。