催化裂化装置用闸阀内腔表面喷涂工艺的分析与实施
江苏省人民政府关于印发江苏省大气污染防治行动计划实施方案的通知
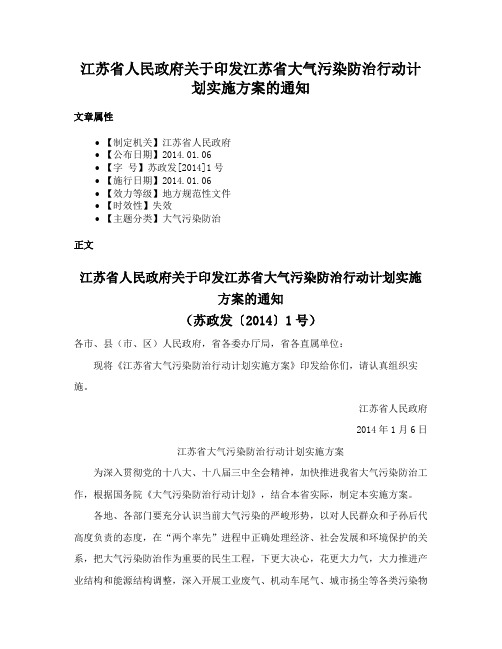
江苏省人民政府关于印发江苏省大气污染防治行动计划实施方案的通知文章属性•【制定机关】江苏省人民政府•【公布日期】2014.01.06•【字号】苏政发[2014]1号•【施行日期】2014.01.06•【效力等级】地方规范性文件•【时效性】失效•【主题分类】大气污染防治正文江苏省人民政府关于印发江苏省大气污染防治行动计划实施方案的通知(苏政发〔2014〕1号)各市、县(市、区)人民政府,省各委办厅局,省各直属单位:现将《江苏省大气污染防治行动计划实施方案》印发给你们,请认真组织实施。
江苏省人民政府2014年1月6日江苏省大气污染防治行动计划实施方案为深入贯彻党的十八大、十八届三中全会精神,加快推进我省大气污染防治工作,根据国务院《大气污染防治行动计划》,结合本省实际,制定本实施方案。
各地、各部门要充分认识当前大气污染的严峻形势,以对人民群众和子孙后代高度负责的态度,在“两个率先”进程中正确处理经济、社会发展和环境保护的关系,把大气污染防治作为重要的民生工程,下更大决心,花更大力气,大力推进产业结构和能源结构调整,深入开展工业废气、机动车尾气、城市扬尘等各类污染物的综合治理,严厉整治环境违法、违规行为,建立健全政府统领、企业施治、市场驱动、公众参与的大气污染防治联防联控新机制,凝聚全省之力改善空气质量,切实保障人民群众身体健康。
经过5年努力,全省空气质量明显好转,重污染天数控制在较低水平;到2017年,各省辖市细颗粒物(PM2.5)浓度比2012年下降20%左右。
一、深化产业结构调整,推进大气污染源头防治(一)加快淘汰落后产能。
提前完成钢铁、水泥等重点行业“十二五”落后产能淘汰任务。
2014年年底前,制定范围更广、标准更高的落后产能淘汰政策,完善淘汰落后产能公告制度和目标责任制,建立提前淘汰落后产能激励机制,鼓励企业加快生产技术装备更新换代,继续淘汰一批相对落后产能。
到2017年,再淘汰一批火电、钢铁、水泥等行业落后和低端产能。
催化裂化装置工艺流程及设备简图
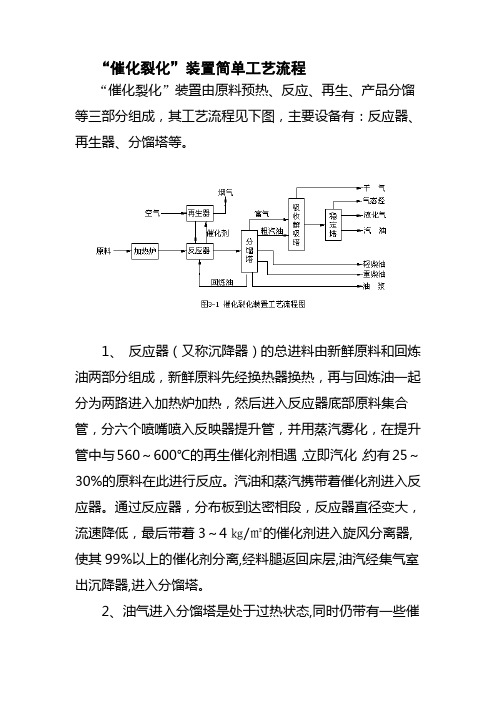
“催化裂化”装置简单工艺流程“催化裂化”装置由原料预热、反应、再生、产品分馏等三部分组成,其工艺流程见下图,主要设备有:反应器、再生器、分馏塔等。
1、反应器(又称沉降器)的总进料由新鲜原料和回炼油两部分组成,新鲜原料先经换热器换热,再与回炼油一起分为两路进入加热炉加热,然后进入反应器底部原料集合管,分六个喷嘴喷入反映器提升管,并用蒸汽雾化,在提升管中与560~600℃的再生催化剂相遇,立即汽化,约有25~30%的原料在此进行反应。
汽油和蒸汽携带着催化剂进入反应器。
通过反应器,分布板到达密相段,反应器直径变大,流速降低,最后带着3~4㎏/㎡的催化剂进入旋风分离器,使其99%以上的催化剂分离,经料腿返回床层,油汽经集气室出沉降器,进入分馏塔。
2、油气进入分馏塔是处于过热状态,同时仍带有一些催化剂粉末,为了回收热量,并洗去油汽中的催化剂,分馏塔入口上部设有挡板,用泵将塔底油浆抽出经换热及冷却到200~3000C,通过三通阀,自上层挡板打回分馏塔。
挡板以上为分馏段,将反应物根据生产要求分出气体、汽油、轻柴油、重柴油及渣油。
气体及汽油再进行稳定吸收,重柴油可作为产品,也可回炼,渣油从分馏塔底直接抽出。
3、反应生焦后的待生催化剂沿密相段四壁向下流入汽提段。
此处用过热蒸汽提出催化剂,颗粒间及表面吸附着的可汽提烃类,沿再生管道通过单动滑阀到再生器提升管,最后随增压风进入再生器。
在再生器下部的辅助燃烧室吹入烧焦用的空气,以保证床层处于流化状态。
再生过程中,生成的烟通过汽密相段进入稀相段。
再生催化剂不断从再生器进入溢流管,沿再生管经另一单动滑阀到沉降器提升管与原料油汽汇合。
4、由分馏塔顶油气分离出来的富气,经气压机增压,冷却后用凝缩油泵打入吸收脱吸塔,用汽油进行吸收,塔顶的贫气进入二级吸收塔用轻柴油再次吸收,二级吸收塔顶干气到管网,塔底吸收油压回分馏塔。
5、吸收脱吸塔底的油用稳定进料泵压入稳定塔,塔顶液态烃一部分作吸收剂,另一部分作稳定汽油产品。
催化裂化装置衬里施工与体会
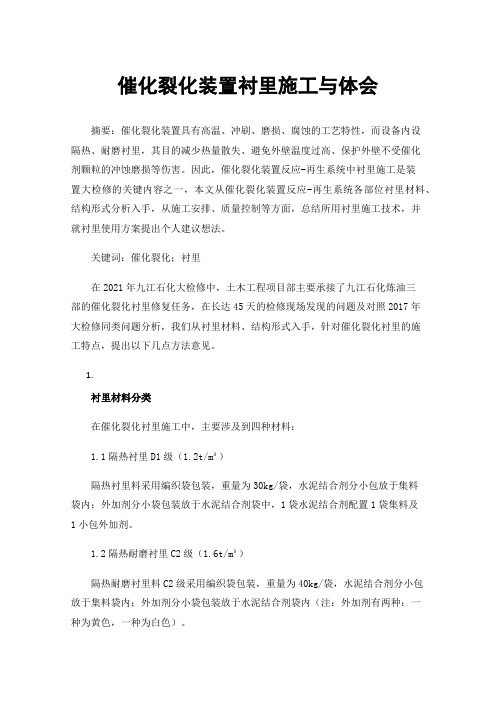
催化裂化装置衬里施工与体会摘要:催化裂化装置具有高温、冲刷、磨损、腐蚀的工艺特性,而设备内设隔热、耐磨衬里,其目的减少热量散失、避免外壁温度过高、保护外壁不受催化剂颗粒的冲蚀磨损等伤害。
因此,催化裂化装置反应-再生系统中衬里施工是装置大检修的关键内容之一,本文从催化裂化装置反应-再生系统各部位衬里材料、结构形式分析入手,从施工安排、质量控制等方面,总结所用衬里施工技术,并就衬里使用方案提出个人建议想法。
关键词:催化裂化;衬里在2021年九江石化大检修中,土木工程项目部主要承接了九江石化炼油三部的催化裂化衬里修复任务,在长达45天的检修现场发现的问题及对照2017年大检修同类问题分析,我们从衬里材料、结构形式入手,针对催化裂化衬里的施工特点,提出以下几点方法意见。
1.衬里材料分类在催化裂化衬里施工中,主要涉及到四种材料:1.1隔热衬里D1级(1.2t/m³)隔热衬里料采用编织袋包装,重量为30kg/袋,水泥结合剂分小包放于集料袋内:外加剂分小袋包装放于水泥结合剂袋中,1袋水泥结合剂配置1袋集料及1小包外加剂。
1.2隔热耐磨衬里C2级(1.6t/m³)隔热耐磨衬里料C2级采用编织袋包装,重量为40kg/袋,水泥结合剂分小包放于集料袋内;外加剂分小袋包装放于水泥结合剂袋内(注:外加剂有两种:一种为黄色,一种为白色)。
1.3耐磨衬里B1级(2.5t/m³)耐磨衬里料B1级采用编织袋包装,重量为50kg/袋,水泥结合剂分小包放于集料袋内;外加剂分小袋包装放于水泥结合剂袋内,1袋集料内配置1袋水泥结合剂及1小包外加剂。
1.4高温耐磨衬里A级(3.1t/m³)高温耐磨衬里料A级采用编织袋包装,重量为40kg/袋,水泥结合剂分小包放于集料袋内;外加剂分小袋包装放于水泥结合剂袋内。
1.结构形式2.1双层有龟甲网结构由12mm长的保温钉+龟甲网+端板+隔热层+耐磨层组成。
龟甲网隔热耐磨双层衬里,采用带端板的柱型锚固钉加龟甲网组成隔热耐磨双层衬里的骨架,先施工隔热层,隔热层衬里表面与柱型锚固钉的端板表面相平,待隔热层施工完后,再焊接龟甲网、施工耐磨衬里层,耐磨衬里层表面与龟甲网面在一个平面。
催化裂化装置工艺设计
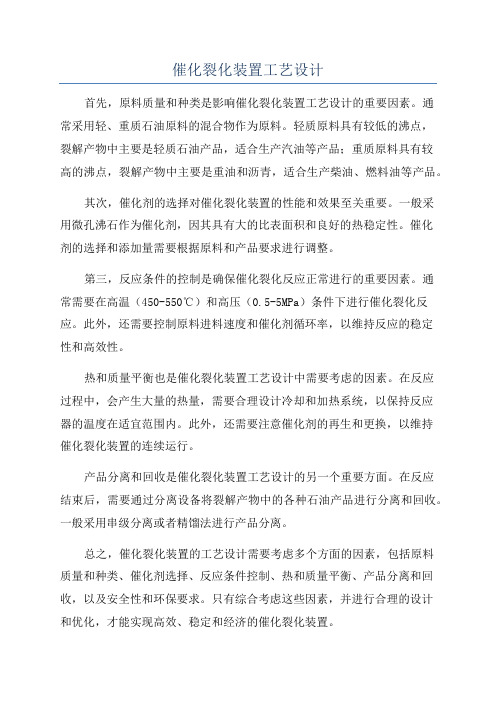
催化裂化装置工艺设计首先,原料质量和种类是影响催化裂化装置工艺设计的重要因素。
通常采用轻、重质石油原料的混合物作为原料。
轻质原料具有较低的沸点,裂解产物中主要是轻质石油产品,适合生产汽油等产品;重质原料具有较高的沸点,裂解产物中主要是重油和沥青,适合生产柴油、燃料油等产品。
其次,催化剂的选择对催化裂化装置的性能和效果至关重要。
一般采用微孔沸石作为催化剂,因其具有大的比表面积和良好的热稳定性。
催化剂的选择和添加量需要根据原料和产品要求进行调整。
第三,反应条件的控制是确保催化裂化反应正常进行的重要因素。
通常需要在高温(450-550℃)和高压(0.5-5MPa)条件下进行催化裂化反应。
此外,还需要控制原料进料速度和催化剂循环率,以维持反应的稳定性和高效性。
热和质量平衡也是催化裂化装置工艺设计中需要考虑的因素。
在反应过程中,会产生大量的热量,需要合理设计冷却和加热系统,以保持反应器的温度在适宜范围内。
此外,还需要注意催化剂的再生和更换,以维持催化裂化装置的连续运行。
产品分离和回收是催化裂化装置工艺设计的另一个重要方面。
在反应结束后,需要通过分离设备将裂解产物中的各种石油产品进行分离和回收。
一般采用串级分离或者精馏法进行产品分离。
总之,催化裂化装置的工艺设计需要考虑多个方面的因素,包括原料质量和种类、催化剂选择、反应条件控制、热和质量平衡、产品分离和回收,以及安全性和环保要求。
只有综合考虑这些因素,并进行合理的设计和优化,才能实现高效、稳定和经济的催化裂化装置。
催化裂化装置解读

催化裂化装置催化裂化是炼油工业重要的二次加工装置,是提高轻质油收率,生产高辛烷值汽油,同时又多产柴油的重要手段,随着重油催化工艺的实现,其地位更加倍增。
作为一项传统的重油加工工艺,催化裂化实现工业化已经有60年的历史,其总加工能力超过加氢裂化、焦化和减粘裂化之和,是目前最重要的重油轻质化工艺。
虽然曾多次受到加氢裂化工艺的竞争和清洁燃料标准的挑战,但由于催化裂化技术的进步,各种以催化裂化技术为核心的催化裂化“家族工艺”的不断出现,已经将催化裂化转变为“炼油-化工一体化”的主体装置,催化裂化仍然保持了其在石油化工行业中的重要地位。
我国的催化裂化技术与国际先进水平保持同步,进入21世纪以后,由于我国催化裂化装置在炼厂地位的特殊性,技术发展的势头更猛,目前为止,基本解决了由于产品升级换代给催化裂化工艺带来的各种问题,而且在应对产品质量问题的技术开发过程中,拓宽了催化裂化产品的品种和范围,为确保催化裂化技术在未来石油化工中的核心地位提供了技术保证。
催化裂化装置的工艺原理是在流化状态下的催化剂作用下,重质烃类在480--520 ℃及0.2-0.3MPa(a)的条件下进行反应。
主要包括:1).裂解反应:大分子烃类裂解为小分子,环烷烃进行断环或侧链断裂,单环芳烃的烷基侧链断裂。
2).异构化反应:正构烷烃变成异构烷烃,带侧链的环烃或烷烃变成环异烷,产品中异构烃含量增加。
3).芳构化反应:环己烷脱氢生成芳香烃,烯烃环化脱氢生成芳烃。
4).氢转移反应:多环芳烃逐渐缩合成大分子直至焦炭,同时一种氢原子转移到烯烃分子中,使烯烃饱和成烷烃。
催化裂化装置的规模近三十年来逐步发展到350万吨/年(加工1000万吨/年原油)。
加工的原料为常压蜡油、减压渣油以及蜡油加氢裂化尾油。
原料主要性质装置由反应再生、分馏、吸收稳定(包括产品精制)、烟气能量回收几个部分组成。
装置主要产品为液化气、汽油、重石脑油和轻柴油,副产部分干气和油浆。
液化气去气体分馏装置。
重油催化裂化装置主要工艺流程说明

重油催化裂化装置主要工艺流程说明重油催化裂化装置主要工艺流程说明一. 反再系统1.反应部分混合蜡油和常(减)压渣油分别由罐区原料罐送入装置内的静态混合器(D-214)混合均匀后,进入原料缓冲罐(D-203/1),然后用原料泵(P-201/1.2)抽出,经流量控制阀(8FIC-230)后与一中回流换热(E-212/1.2),再与油浆(E-201/1.2)换热至170~220℃,与回炼油一起进入静态混合器(D-213)混合均匀。
在注入钝化剂后分三路(三路设有流量控制)与雾化蒸汽一起经六个进料喷嘴进入提升管,与从二再来的高温再生催化剂接触并立即汽化,裂化成轻质产品(液化气、汽油、柴油)并生成油浆、干气及焦炭。
新增焦化蜡油流程:焦化蜡油进装后先进焦化蜡油缓冲罐(D-203/2),然后经焦化蜡油泵(P-201/3.4)提压至1.3MPa 后分为两路:一路经焦化蜡油进提升管控制阀(8FIC242)进入提升管反应器的回炼油喷嘴或油浆喷嘴,剩余的焦化蜡油经另一路通过D-203/2的液位控制阀(8LIC216)与进装蜡油混合后进入原料油缓冲罐(D-203/1)。
新增常压热渣油流程:为实现装置间的热联合,降低装置能耗,由南常减压装置分出一路热常渣(约350℃),经8FIQC530直接进入D-213(原料油与回炼油混合器)前,与原料混合均匀后进入提升管原料喷嘴。
反应油气、水蒸汽、催化剂经提升管出口快分器分离出大部分催化剂,反应油气经过沉降器稀相沉降,再经沉降器(C-101)内四组单级旋风分离器分离出绝大部分催化剂,反应油气、蒸汽、连同微量的催化剂细粉经大油气管线至分馏塔人档下部。
分馏塔底油浆固体含量控制<6g/L。
旋分器分出的催化剂通过料腿返回到汽提段,料腿装有翼阀并浸没在汽提段床层中,保证具有正压密封,防止气体短路,汽提蒸汽经环形分布器进入汽提段的上中下三个部位使催化剂不仅处于流化状态,并汽提掉催化剂夹带的烃油气,汽提后的催化剂通过待生滑阀进入一再催化剂分布器。
催化裂化装置MIP工艺

催化裂扮装置 MIP工艺MIP 工艺要求的主要设计参数项目数值平衡剂活性>60回炼比0~0.1提升管出口温度,℃其中:第一反响区出口温度, ℃515 第一反响区出口温度范围, ℃505~525其次反响区温度, ℃505其次反响区出口温度范围, ℃495~515 提升管反响停留时间, s其中:第一反响区反响时间, s 1.4第一反响区反响时间范围, s 1.2~1.4其次反响区空速(WHSV), h-120其次反响区空速范围(WHSV), h-115~30其次反响区反响时间, s ~5 第一反响区剂油比(对总进料), m/m 5~7雾化蒸汽用量(对总进料), m% 4~6原料预热温度, ℃200再生器密相温度, ℃690~700(≯710)MIP 主要工艺计算汇总1.反响沉降器局部工艺操作条件项目单位设计值1 沉降器压力〔绝〕MPa 0.342 第一反响区温度℃5153 其次反响区温度℃5054 颖原料量kg/h 1190485 原料油预热温度℃200~2306 回炼比0~0.05项目单位设计值7 催化剂循环量t/h 6748 剂油比〔对总进料〕 5.669 提升管第一反响区入口线速m/s 7.3910 提升管第一反响区出口线速m/s 13.2111 提升管第一反响区停留时间s 1.312 提升管其次反响区出口线速m/s 1.8413 提升管其次反响区停留时间s 5.8314 其次反响区重时空速h-115~3015 汽提蒸汽量〔总量〕kg/h 250016 原料雾化蒸汽量kg/h 600017 预提升干气量kg/h 300018 沉降器旋分器组数 219 沉降器旋分器入口线速m/s 19.02.再生局部工艺操作条件项目单位数据1 再生器压力〔绝〕MPa 0.342 密相温度℃6903 烧焦罐下部内径mm 51604 烧焦罐下部线速m/s 1.825 烧焦罐上部内径mm 57606 烧焦罐上部线速m/s 1.527 稀相管内径mm 24008 稀相管线速m/s 8.749 总主风量〔湿〕m3n/min 204010 催化剂循环量t/h 67411 稀相内径mm 836012 稀相线速m/s 0.7413 旋分组数 614 一级旋分器入口线速m/s 21.015 二级旋分器入口线速m/s 23.016 内取热负荷kW 446517 外取热负荷KW 28880项 目 数 据(MPa) 备 注推动力沉降器顶压〔绝〕 0.34 稀相静压 0.0007 汽提段静压 0.0633 待生斜管静压 0.0385 合 计 0.4425 阻力项目数 据(MPa)推动力压力平衡1. 再生线路压力平衡汇总2. 待生线路压力平衡汇总再生顶压〔绝〕 0.34 再生稀相静压 0.0028 再生一密相静压 0.0252 稀相管,T 型快分压降 0.017 待生滑阀压降 0.05748 合 计0.44253. 二反催化剂循环线路压力平衡汇总旋流头顶压力〔绝〕 0.345稀相静压 0.0002 预汽提段静压 0.0385 循环管料位静压0.0375项目 数 据(MPa) 备 注推动力再生顶压〔绝〕 再生稀相静压 再生密相静压 再生斜管静压 合 计 0.34 0.0028 0.007 0.09 0.4400 阻力沉降器顶压〔绝〕 提升管总压降〔含旋流头〕 旋流头后部压降 再生滑阀压降 合 计0.34 0.054 0.005 0.041 0.4400项 目数 据(MPa)4. 旋流快分至沉降器线路压力平衡汇总推动力数据旋流头顶压力〔绝〕 0.345稀相静压 0.0002 预汽提段静压 0.0385 待生斜管管料位静压 0.01合 计 0.3937阻力沉降器顶压力〔绝〕 0.34 稀相净压 0.0004 待生滑阀 II 压降 0.0533 合 计0.3937MIP 工艺的原料以及产品质量〔设计〕1. 原料性质项 目数 值 一般性质密度(20℃),g/cm 30.92 运动粘度,mm 2/s(100℃) 残炭,w % 元素组成,w %C H N S碱性氮,μg/g 四组分,w %饱和烃 芳烃胶质42 6.086.33 12.18 0.24 1.050.0431.68 18.04合 计 阻力旋流头顶压力〔绝〕 其次反响区总压力降其次反响区后催化剂输送压力降旋流头压力降 滑阀压降 0.4212 合 计0.345 0.0223 0.0065 0.005 0.04242 0.42122.干气和液化石油气组成项目数值H -C ,w%2 2H 3.42H S213.1CH 29.54C H2 627.8C H2 426.2总计100.0C -C , w%3 4C H3 86.9C H30.03 6i-C H18.24 10n-C H 4.54 10C H -14 8i-C H4 8 t-C H -24 8c-C H -24 86.412.8 10.8 10.4沥青质0.24重金属,μg/gFe V Cu Na Ni7.6380.1~0.4 10馏程,℃初馏点10% 50% 90%235 385 528 5833. 汽油性质4. 轻柴油性质催化剂和化学药剂消耗序号 名 称 型号或规格年用量t 一次装入量t 预期 寿命备 注1催化剂1400180项 目密度〔20℃〕,g/cm3十六烷值 凝点,℃ 硫含量,ppm 馏程,℃ 初馏点 10% 30% 50% 70% 90% 干点数 值 ~0.93 ~20 <0195 219 250 281 317 353 360项 目密度〔20℃〕,g/cm 3诱导期,min 硫含量,ppm 烯烃,v% 芳烃,v% 辛烷值 RON MON馏程,℃初馏点 10% 30% 50% 70% 90% 干点数 值 ~0.72 >500 850 ~27 ~21 ~93.0 ~81.040 55 75 98 136 170 195总计100.02 CO 助燃剂Pt:0.05% 5.63 磷酸三钠98w% 3.364 阻垢剂135 金属钝化剂含锑25%406 硫转移剂70.5公用工程消耗序号工程单位数据备注1 颖水t/h 102 循环水t/h 38003 除盐水t/h 624 电kW -250 输出3.5MPa t/h -15 输出5 蒸汽 1.0MPa0.6MPa t/ht/h-19/输出6 净化压缩空气m3n/h 15457 非净化压缩空气m3n/h 12808 氮气m3n/h 300MIP 工艺技术简介该工艺技术设置两个反响区,承受串联式提升管反响器和适宜的工艺条件,在不同的反响区实现裂化、氢转移、异构化及芳构化反响以到达降低汽油烯烃含量的目的。
催化裂化装置工艺流程

催化裂化装置工艺流程
《催化裂化装置工艺流程》
催化裂化装置是石油化工行业中常见的一种重要装置,主要用于将重质石油原料加工成轻质高值产品,如汽油、柴油和航空燃料。
在催化裂化装置中,石油原料通过加热和催化剂的作用,发生分子内部的饱和碳链裂解,生成较轻的烃类产品,并产生丰富的芳烃和液化石油气。
催化裂化装置的工艺流程通常包括以下几个主要步骤:
1. 原料加热:首先,将经过预处理的重质石油原料送入加热炉中进行加热,使其达到裂化反应的最佳温度。
2. 催化裂化:加热后的石油原料进入裂化反应器,与催化剂接触,发生裂化反应。
在裂化过程中,重质烃分子会发生碳链裂解,生成较轻的烃类产品,包括汽油、柴油和液化石油气。
3. 分离和净化:裂化反应产物进入分馏塔,通过精馏、冷却和净化等步骤,将不同碳数的烃类产品进行分离,以得到所需的轻质产品。
4. 再生催化剂:随着反应的进行,催化剂会逐渐失活,需要通过再生来恢复其活性。
再生催化剂的过程包括焙烧和再活化,以保持催化剂的活性和稳定性。
以上便是催化裂化装置的基本工艺流程。
该装置能够将重质石
油原料转化为高附加值的轻质产品,对于提高石油炼制的产出和质量具有重要意义。
同时,催化裂化装置的工艺流程也在不断优化和改进,以适应不断变化的市场需求和环保要求。
催化裂化装置操作工(初级)复习题
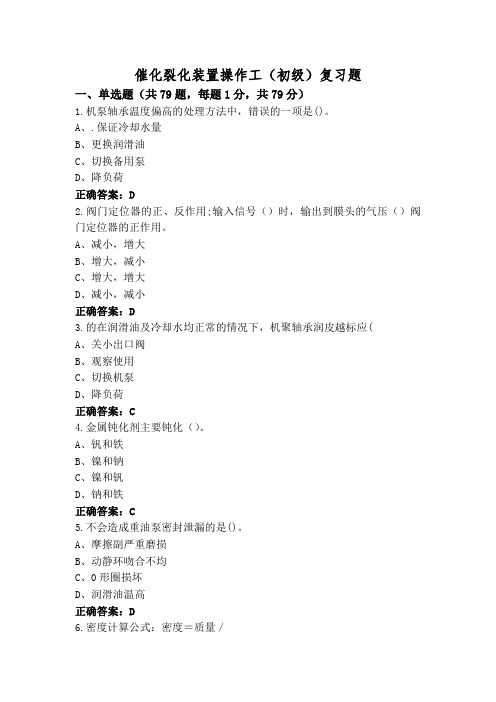
催化裂化装置操作工(初级)复习题一、单选题(共79题,每题1分,共79分)1.机泵轴承温度偏高的处理方法中,错误的一项是()。
A、.保证冷却水量B、更换润滑油C、切换备用泵D、降负荷正确答案:D2.阀门定位器的正、反作用;输入信号()时,输出到膜头的气压()阀门定位器的正作用。
A、减小,增大B、增大,减小C、增大,增大D、减小,减小正确答案:D3.的在润滑油及冷却水均正常的情况下,机聚轴承润皮越标应(A、关小出口阀B、观察使用C、切换机泵D、降负荷正确答案:C4.金属钝化剂主要钝化()。
A、钒和铁B、镍和钠C、镍和钒D、钠和铁正确答案:C5.不会造成重油泵密封泄漏的是()。
A、摩擦副严重磨损B、动静环吻合不均C、0形圈损坏D、润滑油温高正确答案:D6.密度计算公式:密度=质量/B、直径C、表面积D、半径正确答案:A7.干粉灭火器主要有磷酸铵盐、碳酸氢钠、氯化钾等。
A、氯化钠B、氢氧化钠C、碳酸氢钾D、磷酸钠正确答案:A8.金属钝化剂热稳定性较差,使用时一般要求进料温度控制在()左右。
A、200℃B、150℃C、300℃D、250℃正确答案:D9.不属于管壳式换热器优点的是()。
A、清洗方便B、金属消耗量大C、生产成本低D、选材范围广正确答案:B10.下列选项中,关于热油泵不预热所产生后果,错误的是()A、导致泵内零件因热胀系数不同而胀死B、导致启动时发生汽蚀C、.造成启动时产生振动D、造成启动时流量小正确答案:B11.反应一再生循环过程中,催化剂不断经历()过程,所以,要求钝化剂有较好的热稳定性,以保证较高的有效组分沉积率。
A、还原B、化合C、氧化-还原正确答案:C12.暂时硬度是指水中钙、镁的()含量。
A、硫酸盐B、硅酸盐C、氯化物D、碳酸盐正确答案:D13.不属于主风机出口单向阀检查内容的是()。
A、检查单向阀的安装方向是否正确B、检查阀体外表面腐蚀情况C、检查紧固件是否均匀坚固D、检查单向阀温度情况正确答案:D14.下列不属于变频器优点的是()。
催化裂化装置区工艺管道施工技术要求

催化裂化装置区改造工程施工技术要求1.1施工技术准备1.1.1开工之前由设计代表对施工单位技术人员进行施工图纸交底并由施工单位技术人员对所有参加施工人员进行技术交底,以便施工人员了解工程概况、工期、质量及安全要求,施工难点及技术要求。
1.1.2机具检查,对施工所需要的机具进行清点核实,查看施工机具是否完好,是否满足施工的要求。
1.1.3材料检验,主要检查材料的外观质量,质量保证书和合格证。
管材、管件表面不得有裂纹、缩孔、折皱、重皮以及严重锈蚀和过大的机械损伤。
所有阀门都必须按要求进行水压强度和严密性试验。
1.1.4特殊工种作业人员资格需检查是否符合要求并办理上岗证,焊接工艺评定需报检。
1.2管道预制1.2.1材料的领用:根据设计图纸的要求,领用所需的材料,核对其规格、型号、数量、材质,以免误领,而用于预制的材料需经过喷沙除锈和底漆防腐处理。
1.2.2管道组对1. 道用火焰切割,要清除管口附近的毛刺、熔渣、氧化物、铁屑等。
2. 管壁厚度为3--9mm 时,坡口形式按下图3. 管道组对时应检查组对的平直度。
1. 管子、管件组对应对坡口及其内外表面50mm 范围内的油、漆、锈、毛刺等污物进行清理,清理合格后及时焊接。
5.部分大口径管道因条件限制可采用火焰加工坡口,坡口示意图然后用角向磨光机将火焰切割的热影响区打磨干净,相邻的两道焊缝之间的最小距离不得小于100mm。
对于SHA级管道应采用机械加工破口。
6. 法兰连接时应保持平行,其偏差不得大于法兰外径的1.5‰且不大于2mm。
法兰连接应保持与管道同心,并应保证螺栓自由穿入。
1.2.3管道预制1. 工艺管道的预制在指定预制场完成,在进行预制时应按单线图(进行,若设计未给出单线图的则需先按平面布置图绘制出单线图用于施工。
2. 在管道预制前,应对单线图进行焊口编号并报项目组审核,在经确认后用于施工。
3. 所有预制焊口的详细信息(包括焊口号、焊工号、焊接日期及管线号等)需被及时记录并在输入到计算机上相关焊接数据库以便追踪检查。
催化裂化装置工作总结

催化裂化装置工作总结
催化裂化装置是炼油厂中非常重要的设备,它能够将重质石油馏分转化为高附加值的产品,如汽油和柴油。
在催化裂化装置的工作过程中,通过催化剂的作用,将长链烃分子裂解成短链烃分子,从而提高产品的产率和质量。
在这篇文章中,我们将对催化裂化装置的工作原理和关键技术进行总结。
首先,催化裂化装置的工作原理是通过将重质石油馏分在高温和高压下与催化剂接触,从而裂解成轻质产品。
催化剂通常是一种特殊的固体材料,它能够在裂化过程中促进化学反应的进行,从而提高产品的产率和质量。
催化裂化装置通常包括反应器、再生器、分离装置和催化剂循环系统等部分,通过这些部分的协同作用,实现了重质石油馏分的裂解和产品的分离。
其次,催化裂化装置的工作需要依靠一系列的关键技术来保证其稳定和高效运行。
首先是催化剂的选择和再生技术,不同类型的催化剂对产品的选择和产率有着重要的影响,而催化剂的再生技术则能够延长催化剂的使用寿命。
其次是温度和压力的控制技术,裂化过程需要在高温和高压下进行,因此需要精确控制反应器的温度和压力,以保证裂化反应的进行。
最后是产品分离技术,裂化反应产生的产品需要经过分离装置进行分离,以得到纯净的汽油和柴油等产品。
总的来说,催化裂化装置是炼油厂中非常重要的设备,它能够将重质石油馏分转化为高附加值的产品,通过对其工作原理和关键技术的总结,我们能够更好地理解催化裂化装置的工作过程,从而保证其稳定和高效运行。
催化裂化的装置简介及工艺流程-11页word资料
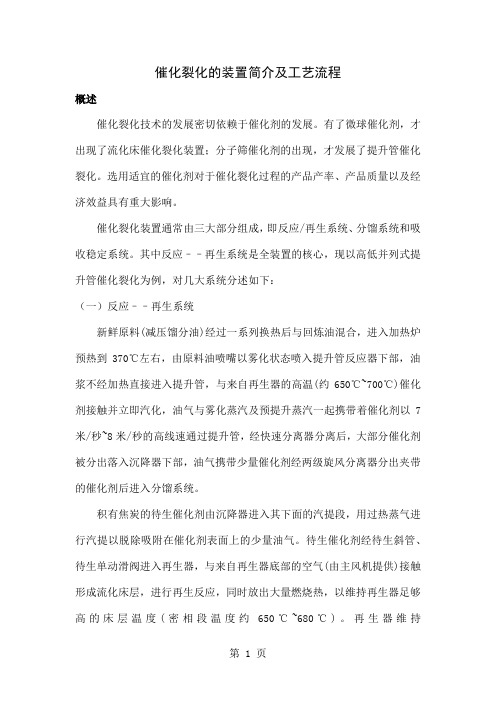
催化裂化的装置简介及工艺流程概述催化裂化技术的发展密切依赖于催化剂的发展。
有了微球催化剂,才出现了流化床催化裂化装置;分子筛催化剂的出现,才发展了提升管催化裂化。
选用适宜的催化剂对于催化裂化过程的产品产率、产品质量以及经济效益具有重大影响。
催化裂化装置通常由三大部分组成,即反应/再生系统、分馏系统和吸收稳定系统。
其中反应––再生系统是全装置的核心,现以高低并列式提升管催化裂化为例,对几大系统分述如下:(一)反应––再生系统新鲜原料(减压馏分油)经过一系列换热后与回炼油混合,进入加热炉预热到370℃左右,由原料油喷嘴以雾化状态喷入提升管反应器下部,油浆不经加热直接进入提升管,与来自再生器的高温(约650℃~700℃)催化剂接触并立即汽化,油气与雾化蒸汽及预提升蒸汽一起携带着催化剂以7米/秒~8米/秒的高线速通过提升管,经快速分离器分离后,大部分催化剂被分出落入沉降器下部,油气携带少量催化剂经两级旋风分离器分出夹带的催化剂后进入分馏系统。
积有焦炭的待生催化剂由沉降器进入其下面的汽提段,用过热蒸气进行汽提以脱除吸附在催化剂表面上的少量油气。
待生催化剂经待生斜管、待生单动滑阀进入再生器,与来自再生器底部的空气(由主风机提供)接触形成流化床层,进行再生反应,同时放出大量燃烧热,以维持再生器足够高的床层温度(密相段温度约650℃~680℃)。
再生器维持0.15MPa~0.25MPa(表)的顶部压力,床层线速约0.7米/秒~1.0米/秒。
再生后的催化剂经淹流管,再生斜管及再生单动滑阀返回提升管反应器循环使用。
烧焦产生的再生烟气,经再生器稀相段进入旋风分离器,经两级旋风分离器分出携带的大部分催化剂,烟气经集气室和双动滑阀排入烟囱。
再生烟气温度很高而且含有约5%~10%CO,为了利用其热量,不少装置设有CO 锅炉,利用再生烟气产生水蒸汽。
对于操作压力较高的装置,常设有烟气能量回收系统,利用再生烟气的热能和压力作功,驱动主风机以节约电能。
催化裂化装置技术手册
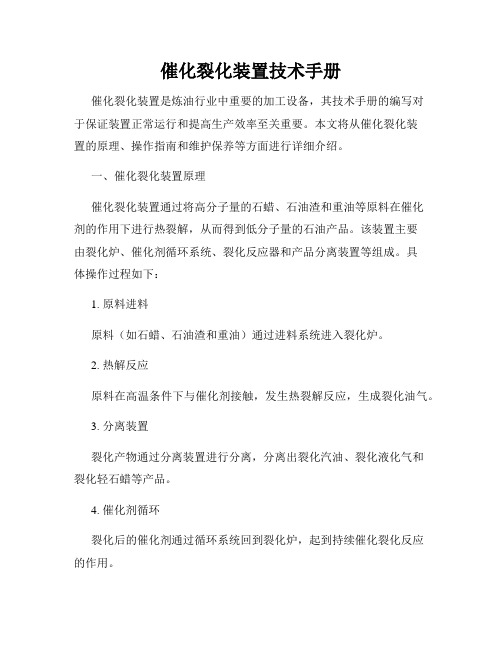
催化裂化装置技术手册催化裂化装置是炼油行业中重要的加工设备,其技术手册的编写对于保证装置正常运行和提高生产效率至关重要。
本文将从催化裂化装置的原理、操作指南和维护保养等方面进行详细介绍。
一、催化裂化装置原理催化裂化装置通过将高分子量的石蜡、石油渣和重油等原料在催化剂的作用下进行热裂解,从而得到低分子量的石油产品。
该装置主要由裂化炉、催化剂循环系统、裂化反应器和产品分离装置等组成。
具体操作过程如下:1. 原料进料原料(如石蜡、石油渣和重油)通过进料系统进入裂化炉。
2. 热解反应原料在高温条件下与催化剂接触,发生热裂解反应,生成裂化油气。
3. 分离装置裂化产物通过分离装置进行分离,分离出裂化汽油、裂化液化气和裂化轻石蜡等产品。
4. 催化剂循环裂化后的催化剂通过循环系统回到裂化炉,起到持续催化裂化反应的作用。
二、催化裂化装置操作指南1. 温度控制裂化炉温度是影响裂化反应效果的关键参数。
在操作中,应根据不同原料的特性和所需产品质量,合理控制催化裂化温度,避免温度过高导致催化剂失活或温度过低影响反应速率。
2. 原料选择不同原料的性质对裂化反应的影响有所差异。
应根据目标产品质量和市场需求,合理选择原料,并进行合适的预处理,如脱蜡、脱硫等,以提高裂化效果和产品品质。
3. 催化剂活性管理催化剂是催化裂化装置中最关键的组成部分。
为保证装置的正常运行,应定期检测催化剂的活性,并进行必要的处理,如焙烧、再生等,以延长催化剂的使用寿命。
4. 安全操作在操作催化裂化装置时,应严格遵守操作规程,保证操作人员的人身安全和设备的正常运行。
同时,应加强对催化裂化装置的检测和维护,及时发现和处理潜在的安全隐患。
三、催化裂化装置维护保养1. 清洗与清理定期对催化裂化装置进行清洗和清理,去除附着物、沉积物和焦炭,以保证装置的畅通和正常运行。
2. 检修和更换定期进行设备的检修和更换,如检修泵、阀门等关键设备,更换老化和磨损的零部件,以确保催化裂化装置的长期稳定运行。
催化裂化装置工艺流程
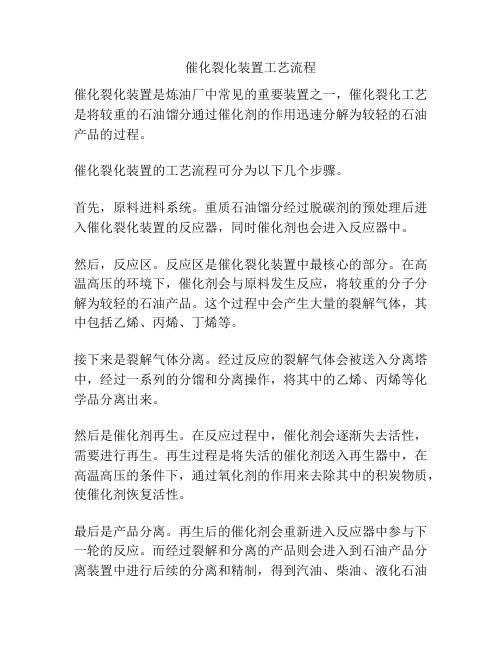
催化裂化装置工艺流程催化裂化装置是炼油厂中常见的重要装置之一,催化裂化工艺是将较重的石油馏分通过催化剂的作用迅速分解为较轻的石油产品的过程。
催化裂化装置的工艺流程可分为以下几个步骤。
首先,原料进料系统。
重质石油馏分经过脱碳剂的预处理后进入催化裂化装置的反应器,同时催化剂也会进入反应器中。
然后,反应区。
反应区是催化裂化装置中最核心的部分。
在高温高压的环境下,催化剂会与原料发生反应,将较重的分子分解为较轻的石油产品。
这个过程中会产生大量的裂解气体,其中包括乙烯、丙烯、丁烯等。
接下来是裂解气体分离。
经过反应的裂解气体会被送入分离塔中,经过一系列的分馏和分离操作,将其中的乙烯、丙烯等化学品分离出来。
然后是催化剂再生。
在反应过程中,催化剂会逐渐失去活性,需要进行再生。
再生过程是将失活的催化剂送入再生器中,在高温高压的条件下,通过氧化剂的作用来去除其中的积炭物质,使催化剂恢复活性。
最后是产品分离。
再生后的催化剂会重新进入反应器中参与下一轮的反应。
而经过裂解和分离的产品则会进入到石油产品分离装置中进行后续的分离和精制,得到汽油、柴油、液化石油气等多种石油产品。
整个催化裂化装置的工艺流程需要严格控制各个环节的工艺参数,以确保裂化气体的质量和产品的纯度。
同时,催化剂的性能和使用寿命也是需要重点关注的问题,原料的质量和稳定性也会直接影响到整个工艺的效果。
催化裂化装置的工艺流程通过高效的催化剂和合理的工艺操作来实现重质石油馏分的转化,不仅提高了石油资源的利用率,还为石油产品提供了丰富的选择。
然而,由于催化裂化装置操作条件的复杂性和催化剂的高成本,装置的优化和经济性也是需要进一步研究和探索的方向。
催化裂化装置分馏系统工艺分析
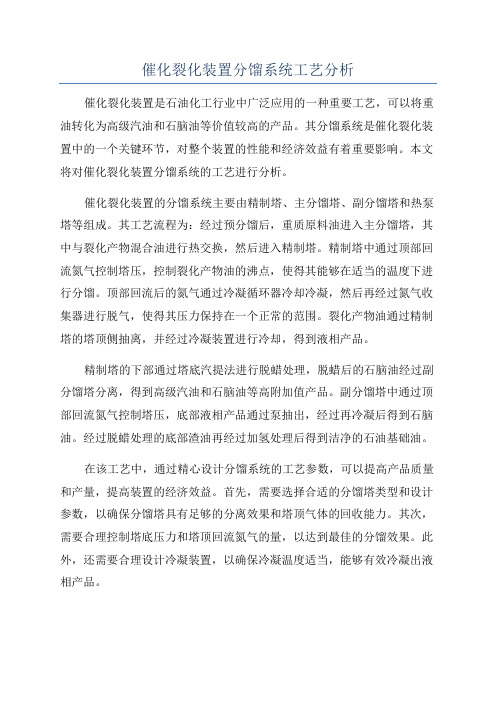
催化裂化装置分馏系统工艺分析催化裂化装置是石油化工行业中广泛应用的一种重要工艺,可以将重油转化为高级汽油和石脑油等价值较高的产品。
其分馏系统是催化裂化装置中的一个关键环节,对整个装置的性能和经济效益有着重要影响。
本文将对催化裂化装置分馏系统的工艺进行分析。
催化裂化装置的分馏系统主要由精制塔、主分馏塔、副分馏塔和热泵塔等组成。
其工艺流程为:经过预分馏后,重质原料油进入主分馏塔,其中与裂化产物混合油进行热交换,然后进入精制塔。
精制塔中通过顶部回流氮气控制塔压,控制裂化产物油的沸点,使得其能够在适当的温度下进行分馏。
顶部回流后的氮气通过冷凝循环器冷却冷凝,然后再经过氮气收集器进行脱气,使得其压力保持在一个正常的范围。
裂化产物油通过精制塔的塔顶侧抽离,并经过冷凝装置进行冷却,得到液相产品。
精制塔的下部通过塔底汽提法进行脱蜡处理,脱蜡后的石脑油经过副分馏塔分离,得到高级汽油和石脑油等高附加值产品。
副分馏塔中通过顶部回流氮气控制塔压,底部液相产品通过泵抽出,经过再冷凝后得到石脑油。
经过脱蜡处理的底部渣油再经过加氢处理后得到洁净的石油基础油。
在该工艺中,通过精心设计分馏系统的工艺参数,可以提高产品质量和产量,提高装置的经济效益。
首先,需要选择合适的分馏塔类型和设计参数,以确保分馏塔具有足够的分离效果和塔顶气体的回收能力。
其次,需要合理控制塔底压力和塔顶回流氮气的量,以达到最佳的分馏效果。
此外,还需要合理设计冷凝装置,以确保冷凝温度适当,能够有效冷凝出液相产品。
此外,还需要注意操作控制的安全性和稳定性。
对于分馏系统来说,要注意控制好分馏温度和压力的变动,以防止分馏塔内发生过热、过压等异常情况。
在日常操作中,要注意监控分馏系统的各个关键参数,及时发现问题并进行调整和处理。
综上所述,催化裂化装置分馏系统是催化裂化装置中一个重要的工艺环节。
通过合理设计和精心操作,可以提高产品的质量和产量,提高装置的经济效益。
但需要注意操作的安全性和稳定性,及时处理和解决问题。
石油加工生产技术:催化裂化反应原理及工艺流程精选PPT
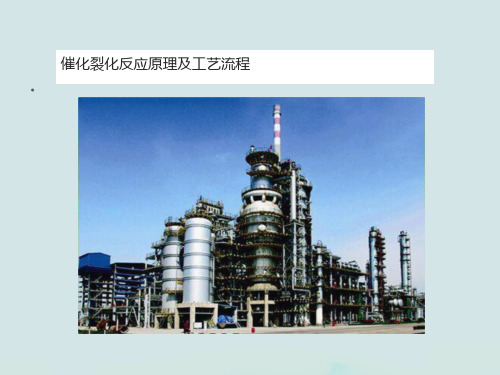
提升管催化裂化的反应-再生系统有多种形式,
双动滑阀是一种两块阀板双向动作的超灵敏调节阀,安装在再生器出口管线上
塞阀比滑阀具有以下优点:
其作用是:正常操作时用来调节催化剂在两器间的循环量,出现重大事故时用
470~510℃2~4s
双塔流程由于单塔流程,可同时满足高吸收率和高
解析率的要求。
吸收C3、C4和 部分C2
7~8m/s 汽提
再生催化剂 650~700℃
200~250 ℃ 高低并列反应再生系统
二、分馏系统
过热油气 460~480℃
为了取走分馏塔的过剩热量,设有塔顶循环回流、一 个至两个中段回流以及塔底油浆循环
三、吸收解吸系统有两种流程:
活性,同时提供裂化反应所需
双塔流程由于单塔流程,可同时满足高吸收率和高
催化裂化反应原理及工艺流程
●
催化裂化催化工艺流程
催化裂化装置一般由四大系统构成
反应-再生系统、分馏系统、 吸收-稳定系统、烟气能量回收系统
一、反应—再生系统
提升管催化裂化的反应-再生系统有多种形式, 如高低并列式、同轴式、同高并列式、两段提 升管催化裂化等
470~510℃2~4s 待生催化剂
二级旋风分离器 13~20m/s
(一)三器——提升管反应器、沉降器及再生器
提升管反应器
预提升:由提升 管底部吹入水蒸 气(称预提升蒸 汽),使出再生 斜管的再生催化 剂加速,以保证 催化剂与原料油 相遇时均匀接触。
沉降器
沉降器是用碳 钢焊制成的圆筒 形设备,上段为 沉降段,下段是 汽提段。
再生器
再生器的作用 是为催化剂再 生提供场所和 条件。
2、三阀
单动滑阀用于床层反应器催化裂化和高低并列式提升管催化裂化装置。 其作用是:正常操作时用来调节催化剂在两器间的循环量,出现重大事故时用 以切断再生器与反应沉降器之间的联系,以防造成更大事故。
催化裂化工艺技术手册

催化裂化工艺技术手册第一章催化裂化工艺概述1.1 催化裂化的定义和作用催化裂化是一种重要的炼油工艺,主要用于将重质石油原料分解为轻质燃料和高附加值的化工产品。
通过催化剂的作用,在高温下将长链烃分子裂解成短链烃分子,以提高产品质量和产率。
1.2 催化裂化工艺的发展历程催化裂化工艺的应用可以追溯到20世纪初。
随着石油行业的不断发展,催化裂化技术也得到了广泛应用。
从传统催化裂化到流化床催化裂化,再到现代的超轻质催化裂化,工艺不断创新和改进,以满足市场需求。
1.3 催化裂化的工艺流程和原理催化裂化的工艺流程包括加热炉和裂解器两个主要部分。
在加热炉中,通过加热将石油原料加热至适宜的温度,然后送入裂解器进行裂解反应。
裂解反应在催化剂的作用下进行,在高温和压力下,长链烃被裂解成短链烃。
第二章催化剂的选择和性能2.1 催化剂的种类和特点常用的催化剂包括酸性催化剂和贵金属催化剂。
酸性催化剂主要是用来促进分子内结构重排和骨架碳裂解反应,贵金属催化剂则用于催化氢化反应,减少不饱和化合物。
2.2 催化剂的性能参数选择合适的催化剂对于提高催化裂化的效果至关重要。
催化剂的性能参数包括比表面积、孔径分布、酸性、稳定性等。
这些参数直接影响到催化反应的速率和选择性。
第三章催化裂化装置的设计和运行3.1 催化裂化装置的主要设备催化裂化装置主要包括加热炉、裂解器、分馏塔等组成。
加热炉用于将石油原料加热至裂解温度,裂解器是催化裂化反应的主要场所,分馏塔用于分离裂解产物。
3.2 催化裂化装置的操作注意事项催化裂化装置的正常运行需要注意以下几个方面:保持适宜的反应温度和压力,注意催化剂的再生和投料,控制氢气和催化剂的用量,合理处理废气和废水。
第四章催化裂化产品的特性和应用4.1 轻质燃料的生产和应用催化裂化可以将重质石油原料转化为轻质燃料,如汽油、柴油和液化石油气。
这些轻质燃料在交通运输、工业生产和日常生活中广泛应用。
4.2 高附加值化工产品的生产和应用除了轻质燃料,催化裂化还可以生产一系列高附加值的化工产品,如石蜡、石油焦等。
催化裂化工艺流程及主要设备通用课件
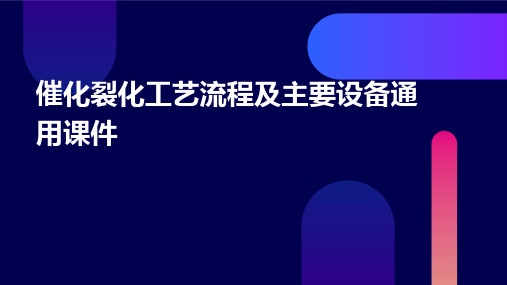
催化剂在使用过程中会逐渐失去 活性,需要经过再生处理恢复活 性,同时烧去积碳,延长催化剂 使用寿命。
产品处理与分离
产品处理
裂化产物经过一系列的分离和加工处 理,得到不同规格的气体、汽油、柴 油等产品。
分离过程
包括粗汽油分离、轻柴油分离、重柴 油分离、气体分离等,以得到高纯度 、高质量的产品。
沉降器的操作和维护对于保持工艺的稳定性和产品的 质量至关重要。
分馏塔
分馏塔是用于对催化裂化工艺产生的油气产品进行分离和提纯的设备。
分馏塔内部通常装有塔板、加热器和冷凝器等设备,油气产品在分馏塔内经过多次加热和冷 凝,根据不同组分的沸点差异实现分离和提纯。
分馏塔的操作和维护对于保证产品的质量和产量至关重要。
。
沉降器
沉降器内部通常装有过滤网和集油箱等设备,油气产 品经过过滤网去除催化剂颗粒后进入集油箱,再通过 管道输送到分馏塔进行进一步处理。
单击此处添加正文,文字是您思想的提一一二三四五 六七八九一二三四五六七八九一二三四五六七八九文 ,单击此处添加正文,文字是您思想的提炼,为了最 终呈现发布的良好效果单击此4*25}
余热回收系统
余热回收
催化裂化过程中会产生大量的余热,余热回收系统将这些余热回收并利用,提 高能源利用效率。
回收方式
包括余热锅炉回收、蒸汽轮机回收等,将余热转化为有用的热能或电能。
03
主要设备介绍
反应器
反应器是催化裂化工艺中的核心设备,用于实现原料油在催化剂的作用 下的裂化反应。
反应器通常采用管式反应器或流化床反应器,其中管式反应器由许多垂 直的管束组成,原料油在管内经过催化剂裂化;流化床反应器则是催化
全阀等,以防止事故发生。
人员安全
催化裂化装置操作安全技术范文

催化裂化装置操作安全技术范文一、背景介绍催化裂化装置是石油炼制工艺中重要的装置之一,其主要功能是将长链烃通过催化反应转化为短链烃,增加汽油和石脑油的产量。
然而,催化裂化装置的操作安全性一直备受关注。
为了确保操作人员和设备的安全,必须严格遵守操作规程,并采取一系列的安全措施。
二、操作安全技术措施1. 操作前的准备工作在操作催化裂化装置之前,应对操作人员进行专门的培训,使其熟悉设备的工作原理、操作规程和安全要求。
同时,需要指定专门的操作人员,并对其进行资格审定。
在确保操作人员具备必要的知识和技能后,方可进行装置的操作。
2. 压力容器的安全保护催化裂化装置中常涉及到高温高压操作,因此压力容器的安全阀和爆破片是非常重要的安全设备。
在操作中,必须及时检查和维护安全阀和爆破片的正常工作,定期检验和校准,确保其可靠性。
同时,需要监测和记录压力容器的工作压力,一旦超过安全限制,应立即停止操作并排除故障。
3. 防止爆炸和火灾的安全措施催化裂化装置中常存在易燃和爆炸的危险,因此需要采取一系列的措施来确保操作的安全。
首先,必须定期检查和维护设备及管道的防爆措施,如隔爆器、爆炸检测器和火焰探测器等设备的工作状态。
其次,要确保操作区域的通风和疏散通道的畅通,以便及时排除有害气体。
另外,要禁止在催化裂化装置周围吸烟、使用明火和进行焊接、切割等高温作业。
4. 废气处理和环境保护催化裂化装置的废气中常含有大量有害物质和污染物,因此需要进行有效的处理和排放。
在操作中,必须定期检查和维护废气处理设备,确保其正常工作。
同时,要注意控制气体的流速和排放温度,以避免对环境造成污染。
此外,还应制定相应的废气处理方案,并进行相关的监测和记录。
5. 事故应急预案和演练催化裂化装置在操作中可能发生各种事故,如泄漏、爆炸和火灾等。
为了应对各种突发情况,必须制定详细的事故应急预案,并进行定期的演练。
在演练中,要模拟真实的事故场景,并测试应急设备和人员的反应能力。
催化裂化工艺主要操作条件分析

(一)反应温度
✓ 一方面,反应温度高则反应速度增大。当反应温度升高时, 热裂化反应的速度提高比较快,当温度高于500℃时,热 裂化趋于重要,产品中出现热裂化产品的特征(气体中C1、 C2多,产品的不饱和度上升)。但是,即使这样高的温度, 催化裂化的反应仍占主导地位。
✓ 另一方面,反应温度可以通过对各类反应速率大小来影响 产品的分布和质量。温度升高汽油的辛烷值上升,但汽油 产率下降,气体产率上升,产品的产量和质量对温度的要 求产生矛盾,必须适当选取温度。
1/ 空速
空速倒数不是真正的反应时间,只是相对的反映反应时
间的长短,故称为假反应时间
假反应时间越长,则反应时间越长 对提升管反应器:
停留时间
提升管反应器的体积VR 油气对数平均体积流量V对
V对
V出 V进 ln(V出 / V进 )
二、影响催化裂化反应速度的主 要因素
• (1)反应温度 • (2) 原料性质 • (3)反应压力 • (4) 剂油比(C/O)
•
15、一年之计,莫如树谷;十年之计 ,莫如 树木; 终身之 计,莫 如树人 。2021年6月上 午12时 3分21.6.2800:03June 28, 2021
•
16、提出一个问题往往比解决一个更 重要。 因为解 决问题 也许仅 是一个 数学上 或实验 上的技 能而已 ,而提 出新的 问题, 却需要 有创造 性的想 像力, 而且标 志着科 学的真 正进步 。2021年6月28日星期 一12时 3分39秒00:03:3928 June 2021
✓ 应当指出,催化裂化装置的操作压力主要不是由
•
9、要学生做的事,教职员躬亲共做; 要学生 学的知 识,教 职员躬 亲共学 ;要学 生守的 规则, 教职员 躬亲共 守。21.6.2821.6.28M onday, June 28, 2021