培训教材-9浪费-标准化课件ppt
合集下载
认识浪费与消除浪费PPT课件

一、认识浪费
精益管理的核心
彻底消除无效劳动与浪费
实施精益管理,必须从消除一切无效劳动与浪费开始。
(一)什么是无效劳动与浪费?
无效劳动与浪费:消耗了资源,增加了成本,但是没有 创造价值(或使附加值增加)的一切活动;也包括虽然创造 了价值,但耗费资源过高的工作。
浪费的表现
(二)无效劳动与浪费的表现
日本丰田汽车公司归纳为以下7种:
市场占有率(%)
冰箱
空调 洗衣机 产品
本企业 A企业 B企业
2004-2005年汽车销量对比 (单位:万辆)
1000
917
900 809
800 700
13.35% 643.2 681.8
600
471.9 487.2
500
400
6.00%
300
200
3.24%
100
0
通用
福特
戴克
809 747
16.00% 14.00% 12.00%
25
谢谢聆听
· 学习就是为了达到一定目的而努力去干, 是为一个目标去 战胜各种困难的过程,这个过程会充满压力、痛苦和挫折
Learning Is To Achieve A Certain Goal And Work Hard, Is A Process To Overcome Various Difficulties For A Goal
1、了解现状,找出问题 2、分析产生问题的原因 3、确定改善课题 4、制定改善方案(目标、措施、、费用、进度计划) 5、改善方案的优化、论证、审批 6、实施改善方案 7、评价改善效果,改善成果发表 8、巩固与标准化,奖励
写在最后
成功的基础在于好的学习习惯
精益管理的核心
彻底消除无效劳动与浪费
实施精益管理,必须从消除一切无效劳动与浪费开始。
(一)什么是无效劳动与浪费?
无效劳动与浪费:消耗了资源,增加了成本,但是没有 创造价值(或使附加值增加)的一切活动;也包括虽然创造 了价值,但耗费资源过高的工作。
浪费的表现
(二)无效劳动与浪费的表现
日本丰田汽车公司归纳为以下7种:
市场占有率(%)
冰箱
空调 洗衣机 产品
本企业 A企业 B企业
2004-2005年汽车销量对比 (单位:万辆)
1000
917
900 809
800 700
13.35% 643.2 681.8
600
471.9 487.2
500
400
6.00%
300
200
3.24%
100
0
通用
福特
戴克
809 747
16.00% 14.00% 12.00%
25
谢谢聆听
· 学习就是为了达到一定目的而努力去干, 是为一个目标去 战胜各种困难的过程,这个过程会充满压力、痛苦和挫折
Learning Is To Achieve A Certain Goal And Work Hard, Is A Process To Overcome Various Difficulties For A Goal
1、了解现状,找出问题 2、分析产生问题的原因 3、确定改善课题 4、制定改善方案(目标、措施、、费用、进度计划) 5、改善方案的优化、论证、审批 6、实施改善方案 7、评价改善效果,改善成果发表 8、巩固与标准化,奖励
写在最后
成功的基础在于好的学习习惯
标准化工作(PPT)
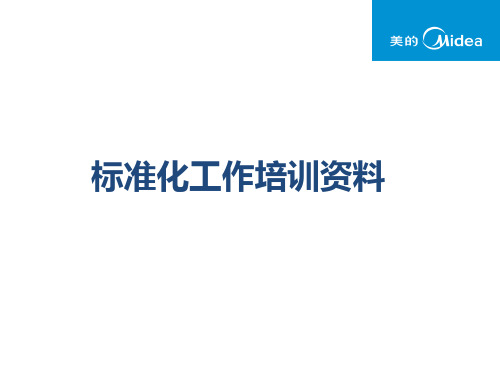
物料传递员角色是创建工作单元时需要考虑的关键因素
构建工作单元质量
目标
工作单元设计 主要概念 工作单元设计 步骤 构建工作单元 质量 工作单元设计的 必做与禁做事项
定义“poka-yoke防呆法”与“jidoka自働化”,并评议日常工 作示例 确定防错的四个级别 确定并评议错误的预防措施与探测示例 定义流程防错的7个步骤 讨论制定一个生产线停止支持计划的重要性 定义无法进行防错时的流程改善举措
防错
1 防呆法
日语短语,意思为“ 防错” 一种能够预防错误的 设计流程方法
2 自働化
还可以理解为“自働 化”,意思就是将人 工智能转移动流程中 流程可以探测异常情 况,并在探测到异常 情况时停止运作
3 示例
计算机磁盘只能以一种方向 装入驱动器中 自动保险带 自动关闭熨斗及其他家用电 器 公共洗手间中的自动冲洗水
单元布局中的单件流水线生产
单元工厂布局中的生产流
最终装配
显著减少了: • 运送 • 库存
检测
作业员
波峰焊接
• 等待时间 同时改善了: • 质量
包装
PC板装 配
• 交付
• 成本
客户 原材料
批量生产
库存
流水线生产
客 户
浪费
虚假流水线生产
客 户
为何是逆时针
单元流通常为逆时针方向
设计是用右手取用拉动,然后通过左手递交给下一个流程
动作的浪费
等待的浪费
过分加工的浪费
过量生产的浪费
缺陷的浪费
行为的浪费
工作单元设计
工作单元设计
工作单元设计这一科目的目标: 应用合理的工作单元设计原则与内容以实现你的业务目标
八大浪费培训ppt课件

4.搬运、堆积的浪費,管理工时的浪費
5.产品贬值
精选ppt课件
15
定义﹕由于生产原料供应中断、作业不平衡和生产计 划安排不当等原因造成的无事可做的等待, 被称为等待
的浪費.
表现形式:
1. 生产线换线频繁;
2. 时常缺料而使人员﹑机器闲置;
3. 生产线未能取得平衡, 工序间经常发生等待;
4. 每天的工作量变动很大;
精选ppt课件
17
(一) 管理浪費的定义:
管理浪費指的是问题发生 以后, 管理人員才采取相 应的对策來进行补救而产 生的額外浪費; 包括生产 效率、成本、交期、时间、 资源利用等浪費;
精选ppt课件
18
(二) 浪費的产生: 管理能力:素质、执行力(速度/准度/精度); 技朮层次: 认知高度;把握度;(相对) 标准化: 可行度;推广度; 企業素质: 整体素质
如何消除过剩?
能否去除次零件的全部或部分;
能否把公差放宽;
能否改用通用件或标准件;
能否改善材料的回收率;
能否改变生产方法;
能否把检验省略掉;
供应商是否适当;
是否确实了解客戶的需求;
精选ppt课件
7
动作的浪费现象在生产线上随处可见,要达到
同样作业的目的,会有不同的动作,哪些动作是不
必要的呢?是不是要拿上、拿下如此频繁?有没有
合理化布局设计的要点:
1. 辅助生产线的终点,应尽量接近供给对象的主生 产产线工序;
2. 充分探讨供应各工序零部件的方法; 3. 研究空卡板﹑包裝箱﹑夹具的返回方法; 4. 沿生产线设置大小适当的零部件暫放场所; 5. 不要忘记在生产线中设置检查工序和修理工序; 6. 确保设备的保养与修理所需空间; 7. 生产线的形状受到产品和场地的制约,可从安裝﹑零部件供应﹑
精益生产之八大浪费培训教材(PPT 65页)
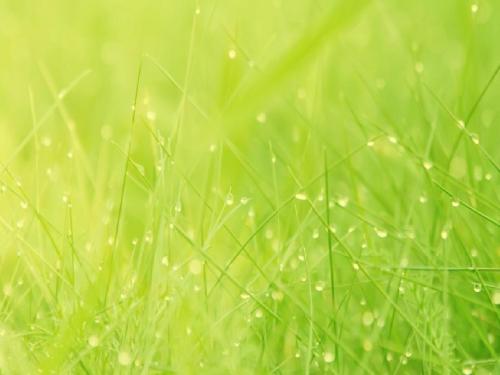
这类浪费具体包括:
★材料的损失
★设备、人员和工时的损失
★额外的修复、鉴别、追加
检查的损失
★有时需要降价处理产品
•29
不良修正的浪费
不良品是工厂中不可容忍的重大浪 费现象。我们客户需要的是合乎规范 要求的产品,客户不会负担不良品, 不仅仅是不良品这部分,随后可能引 起的下游延伸制品不良、检查、返工、 报废等损失都由企业自己承担。
•14
制造过多过早的浪费---内容、原因
内容:
原因:
生产过多 生产过早
信息不准,计划失当,信息 传递不准确,导致生产计划 作业进行盲目
妨碍生产流程
制造能力弱,品质差,换型
成品库存、半成品
时间长,为了弥补自身能力 不足,而提前过量生产
库存增加
各功能制造单位、制程产能
资金周转率低下
效率下降、增加WIP和库存、存货盘点;
3、延伸影响
推迟交期、增加营运压力;
•40
搬运浪费---产生原因 1、工厂布局及生产模式
设备集中的布局;制程不连续,前后制程 分离、路线迂回、曲折、混杂,孤岛作业, 非均衡化生产布置等;
2、生产批量
丰田生产方式提倡拉动系统设计缓冲存货 区域小量而频繁的搬运;
•41
当设备比较昂贵时,管理及财务人员有倾向提高 稼动率,生产过多的产品。
•16
制造过多过早的浪费---后果
被视为是最大的浪费:
1、它只是提早用掉了费用(材料费、人工费)而已, 并不能得到多少实在的好处
2、 它会把“等待的浪费”隐藏起来,使管理人员
漠 视等待的发生而使之永远存在下去。失去了
不断改善、进而增强企业“体质”的机会
(1)操作不经济(Handling)。 ①动作不精简; ②动作多余。 (2)设计不合理(Design)。 ①可同时完成但未同时; ②不必要但被增加; ③可同规格但不同; ④未考虑调整/转换/取放; ⑤物料需要翻找。
八大浪费培训PPT课件

第24页/共32页
6)动作的浪费
原则11. 器具/工具统合
改善前
改善后
原则12. 先入先出成为可能
改善前 取出部品 平均移动距离60㎝,先入先出很困 难
改善后
存放台改成有一定倾度的,利用Stopper使它 停滞。 移动距离是20㎝,取出部品时入口不再重叠, 所以取出方便
第25页/共32页
7)等待的浪费
不良品的浪费 4 Waste of defective products
加工的浪费 5 Waste of processing itself
动作的浪费 6 Waste of Motion
7 等待的浪费 Waste of waiting
管理的浪费 8 Waste of management
7/22
第6页/共32页
• 机器设备时常发生故障;
• 生产线未能取得平衡;
• 材料虽已备齐,但制造通知单没到
⑨
准⑩ 备维 工修 作等 等待 待
③ 返修
搬 运 等 待
③ ⑿搬 返运 修等 等待
产品仓库 ④⒀ 入出 库库 等等 待待
③ 搬 运 等
待
待
⑦
批
量
对不
等 待
起,请 少等会
还没
儿...
好吗?.
第26页/共32页
顾 客
17/22
搬运浪费
○ 只考虑搬运合理化的一日一次搬运
= 供应系统是原因之一 ○ 不开箱就直接供应到LINE
高水平库存掩盖所有问题 “库存是万恶之源”
库存的浪费利用 库存回避工厂的许 多问题。在这种意 识下发生的。
计划有误 维修问题 效率问题 能力不平衡 质量问题 交货问题
九大浪费ppt课件

M u d a 五:加工的Muda
有时不适当的科技或设计,会衍生加工工 作本身的M u d a。机器加工作行程过长或 过份加工、冲床没有生产力的冲击时,以 及去毛边的动作,都是加工 M u d a的例子, 这都可以避免的。在每一道加工步骤时, 我们将价值加入被加工的工作物或信息, 然后送至下一个流程。在此,加工是指在 调制一个工作物或一条信息。
在许多实例中,加工 M u d a也是由于流程无 法同步所造成的。作业员经常把工作分得太精 细,超越了需要的程度,这也是加工Muda的另 一个例子。M ຫໍສະໝຸດ d a 六:等待的Muda
作业员的双手停滞不动时,就是等待 的 M u d a发生的时候。生产线不平衡、缺料、 机器故障,使得作业员停滞,或者机器在进行 附加价值的加工时,而作业员在旁监视,这些 都是等待的M u d a。这类的M u d a很容易看 得出来。较难以发现的,是当机器在加工或装 配工作时等待的 M u d a。纵使作业员很拼命 地工作,仍然存在着数秒、数分钟的M u d a, 以等待下一个工作物的到达。在此段时间内, 作业员仅能无所事事地望着机器
M u d a 三:不合格品重修的Muda
不合格品干扰了生产活动,也耗费昂贵的重修费用。 不合格品通常被丢掉,是资源及设备的最大浪费。在 今日大量生产的环境中,一部出差错的高速度性能自 动机器在问题被发现之前,就已吐出了巨量的不合格 品了。不合格品有时也可能伤害了昂贵的机器设备。 因此必须指派人员站在一旁监视这种高速度的机器, 一看到不正常的情况时,立即停止机器。为了拥有一 部高速度的机器,就必须指定专人为其服务。像这样 的设计,至少应装设有不合格品一旦产生时,就能立 即停止下来的机构。
M u d a 七:搬运的Muda
精益生产八大浪费PPT课件
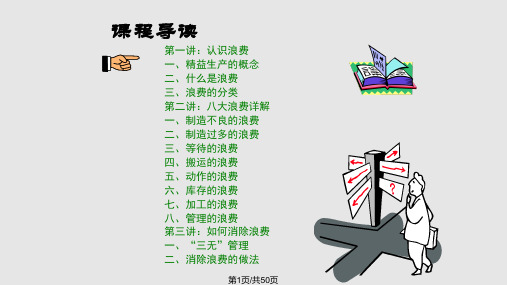
低成本地制造出满足市场 的产品
6
第6页/共50页
精益生产思想告诉我们
精益生产
如何增加经营利润 ——扩大生产规模 (高投资、高风险) ——提高价格 (破坏市场,降低竞争力) ——降低成本 (无需投资,回报率高)
成本降低10%,等于经营规模扩大一倍!!!
获得利润的手法: 之一:降低成本 之二:提高效率
7.做出不良的浪费
八大浪费
制造不良品所损失的浪费,越做损失越大
材料不良、加工不良、检查、市场不良、整修工件等
表现形式:
原因:
•因作业不熟练所造成的不良 •因不良而修整时所造成的浪费 •因不良造成人员及工程增多的浪费 •材料费增加
•标准作业欠缺 •过分要求品质 •人员技能欠缺
注意:
•品质控制点设定错误
表现形式:
•搬运距离很远的地方,小批量的运输 •主副线中的搬运 •出入库次数多的搬运 •破损、刮痕的发生
第22页/共50页
3.搬运的案例
整个冲压过程包括取产品、 冲压、放置产品,其中取产 品与排放产品占了50%的作 业时间,并且这些动作并不 产生价值。
八大浪费
2021/8/13
弯曲完的产品要先 放到工作桌上,再搬运 到冲压工作桌上,这一 过程是不是浪费呢?
实现多品种、小批量,低成本的生产
第3页/共50页
精益生产概念
精益生产
精益-LEAN
第4页/共50页
什么是精益生产方式
精益生产
精益生产(准时生产)其核心是消除一切无效劳动 和浪费,它把目标确定在尽善尽美上,通过不断地降低 成本、提高质量、增强生产灵活性、实现无废品和零库 存等手段确保企业在市场竞争中的优势。
原因:
•作业流程配置不当 •无教育训练 •设定的作业标准不合理
八大浪费培训讲座课件PPT模板(完整版)
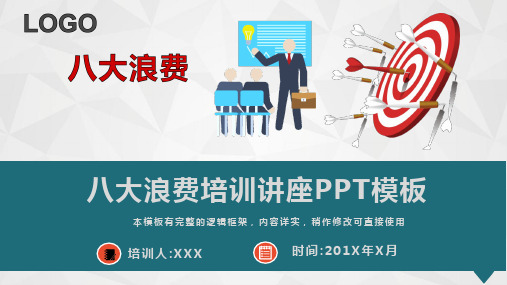
例子:
● 前工序在处理不良 ● 前工序慢,无来料 ● 工作量不平衡
八大浪费—等待浪费举例
问题:工站1每片需要1分钟,而工站2每 片需要30S, 工站二等待时间过长
改善后:工站二建立2个小时的结存 这样一来减少了等待浪费
八大浪费—过量生产浪费
定义:
产量大于需求
产生原因:
● 提前生产 ● 超额生产
例子:
八大浪费—智力浪费举例
问题:
对策:
1、现场作业员技能单一,机动性和灵活性 1、通过对作业员进行培训及考核,使其达
不高,不利于整体人力资源的协调;
到多技能的作业要求;
2、现场作业员有进行多技能学习和作业, 但其上岗认证未进行累加,需更直观的体 现;
2、符合多技能作业的员工采用新的上岗认 证更直观的体现;
改善后:按客户要求安排生产 计划,计算好出货计划。
八大浪费—动作浪费
定义:
多余和不必要的动作
产生原因:
● 工具/治具位置不合理 ● 产品/物料放置位置不合理 ● 工作桌子宽度/高度不合理
例子:
● 起身取高处治具 ● 弯腰操作点胶机
八大浪费—动作浪费举例
问题:001工站贴膜区域,产品放在 工作台左边,但空盘放置区却设在线 尾,每贴完一盘产品要将空盘从左边 拿到右边。 产生动作浪费,且增加作业员疲劳
改善后:将空盘放置区设在产品同一方向 (左边),避免作业员多余动作(从左手拿 给右手)。
减少作业员动作浪费,减少作业员疲劳。并 且收盘人员还可以在盘子满之前做其它的事.
八大浪费—等待浪费
定义:
人或机器的待工状态
产生原因:
● 上制程太慢,不能满足下制程 ● 上工站有异常 ● 工站人太多 ● 设备故障
● 前工序在处理不良 ● 前工序慢,无来料 ● 工作量不平衡
八大浪费—等待浪费举例
问题:工站1每片需要1分钟,而工站2每 片需要30S, 工站二等待时间过长
改善后:工站二建立2个小时的结存 这样一来减少了等待浪费
八大浪费—过量生产浪费
定义:
产量大于需求
产生原因:
● 提前生产 ● 超额生产
例子:
八大浪费—智力浪费举例
问题:
对策:
1、现场作业员技能单一,机动性和灵活性 1、通过对作业员进行培训及考核,使其达
不高,不利于整体人力资源的协调;
到多技能的作业要求;
2、现场作业员有进行多技能学习和作业, 但其上岗认证未进行累加,需更直观的体 现;
2、符合多技能作业的员工采用新的上岗认 证更直观的体现;
改善后:按客户要求安排生产 计划,计算好出货计划。
八大浪费—动作浪费
定义:
多余和不必要的动作
产生原因:
● 工具/治具位置不合理 ● 产品/物料放置位置不合理 ● 工作桌子宽度/高度不合理
例子:
● 起身取高处治具 ● 弯腰操作点胶机
八大浪费—动作浪费举例
问题:001工站贴膜区域,产品放在 工作台左边,但空盘放置区却设在线 尾,每贴完一盘产品要将空盘从左边 拿到右边。 产生动作浪费,且增加作业员疲劳
改善后:将空盘放置区设在产品同一方向 (左边),避免作业员多余动作(从左手拿 给右手)。
减少作业员动作浪费,减少作业员疲劳。并 且收盘人员还可以在盘子满之前做其它的事.
八大浪费—等待浪费
定义:
人或机器的待工状态
产生原因:
● 上制程太慢,不能满足下制程 ● 上工站有异常 ● 工站人太多 ● 设备故障
培训教材-9浪费-标准化课件ppt
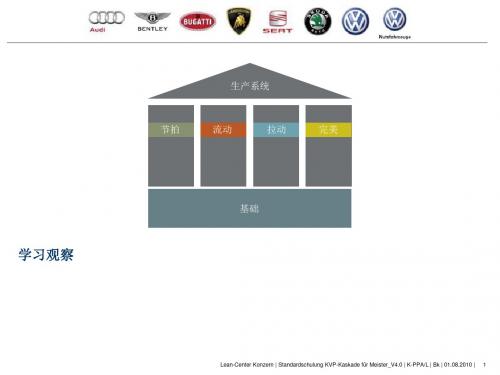
Lean-Center Konzern | Standardschulung KVP-Kaskade für Meister_V4.0 | K-PPA/L | Bk | 01.08.2010 | 2
基础
工作内容基本分为三类:
价值的创造
• 产品增值 • 顾客愿意付费 • 例如,钻孔、焊接、铆接、
定位焊
Hale Waihona Puke 现象示例针对性措施示例
物料摆放占用物流通道 零部件/半成品落满灰尘或长期堆放 查找零件和文件费时费力 生产区域占地面积需求大,办公区域空
间需求大
运输路程长 较高的组织发配需求
多层仓库
平顺化 采用一件流/一套流生产方式 固定的客户节拍 增加上料频次 标示最小-最大缓冲区库存量或料架托
8. 沟通不充分造成的浪费
沟通起到信息交换及技能交换的作用。在日常工 作中,沟通是必须的。过多和过少的信息都是浪 费。
现象示例
工位缺乏信息 信息获取过晚 只收集信息,不利用 由于缺乏信息造成的工作失误 信息重复 过时的文件 不转发信息 重复询问 会谈时间过长
针对性措施示例
按计划完整供料
Lean-Center Konzern | Standardschulung KVP-Kaskade für Meister_V4.0 | K-PPA/L | Bk | 01.08.2010 | 17
7. 不必要的流程造成的浪费
不必要的流程造成的浪费可理解为在工作中出 现的所有问题及相应的后果。
在安装前一刻预装轮罩 定义1级“成品库存”
Lean-Center Konzern | Standardschulung KVP-Kaskade für Meister_V4.0 | K-PPA/L | Bk | 01.08.2010 | 7
九大浪费ppt课件

M u d a 四:动作的Muda 任何人体的动作,若是没有直接产生附加价值,就 是没有生产力。例如,人在走路时,他并没有增加价 值。特别是,如提起或持着一个重物,需用到作业员 身体一部分的特别体力的动作,应予以避免。这不只 是因为工作困难,也是因为这代表着 M u d a。可以 借由工作地点的重新安排,来剔除作业员手持重物走 路的动作,仅花了数秒而已。其余的动作代表着没有 附加价值,例如拿起或放下工作物。经常可看到同一 件工作物,先由右手拿起然后再由左手持着。举例来 说,操作缝衣机的作业员,先从供料箱中拿出几块衣 料,然后放在机器上,最后才取一件衣料放进缝衣机 缝制,这就是动作的 M u d a。供料箱应重新摆置, 使作业员能拿起一块衣料,直接放进缝衣机缝制。要 认定动作的 M u d a,需详细观察作业员手脚使用的 方式。然后,必须重新安排物料放置的方式以及开发 适当的工具及夹具。
M u d a 五:加工的Muda
有时不适当的科技或设计,会衍生加工工 作本身的M u d a。机器加工作行程过长或 过份加工、冲床没有生产力的冲击时,以 及去毛边的动作,都是加工 M u d a的例子, 这都可以避免的。在每一道加工步骤时, 我们将价值加入被加工的工作物或信息, 然后送至下一个流程。在此,加工是指在 调制一个工作物或一条信息。
任何没有产生附加价值的事,就是 M u d a,所以M u d a的种类可以无限地补充。在佳能公司里,将 M u d a依类别区分为如表 6 - 1所示。法国改善顾问协会 的董事司奇· 李贝利( S e rge LeBerre),有次告诉我 说,应当还要再加一项“工程的 M u d a”。因为在工 程的设计上,可以看到许多M u d a。例如,工程师 纵使已有现成简单的解决方法,仍然倾向于设计一个 复杂的结构来解决问题。工程师偏好寻找能应用最新 科技的机会于其设计上,而不是去寻求最简单的方式, 以符合目的的需求。这样的心态违反了现场的需求, 更不用说能满足顾客的需求。李贝利说,今日的工程 师,总是在寻求更复杂及更精巧的东西,他们应当改 变,以寻找削减浪费才对。
八大浪费的培训PPT课件
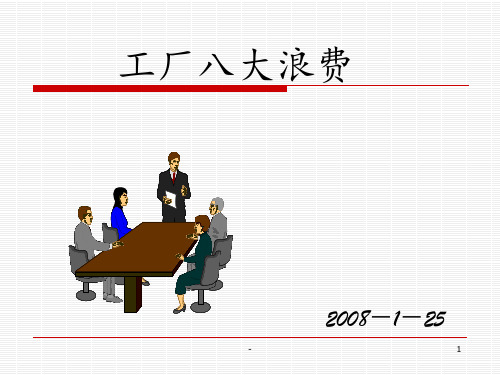
工厂八大浪费
2008-1-25
-
1
课程介绍
▽ JIT的定义
▽ 浪费的定义
▽ 修理不良品的浪费
▽ 加工的浪费
▽ 动作的浪费
▽ 搬运的浪费
▽ 库存的浪费
▽ 制造过多的浪费
▽ 等待的浪费
▽ 管理的浪费
-
2
JIT的定义:
JIT生产方式的是“ 只在需要时,按需要的量, 生产所需的产品”(英文含义:Just in time )。
JIT生产方式的引入,正是帮助企业解决工厂 常见的八大浪费;提高企业的经济效率和生产效 率,为企业的发展打造良好的基础。
-
3
浪费的定义:
在JIT生产方式中,浪费的含意与社会 上通常所说的浪费有所区别。
对于JIT来讲,凡是超出增加产品价值 所绝对必须的最少量的物料,设备,人力, 场地和时间的部分都是浪费。
管理浪费是由于事先管理不到位而导致的问题, 科学的管理应该是具有相当的预见性,有合理的规 划,并在事情的推进过程中加强管理,控制和反馈, 这样就可以在很大程度上减少管理浪费现象的发生。
-
16
减少浪费,降低成本; 提升品质,增创效益。
-
17
-
7
不明技巧; 伸背动作; 弯腰动作; 重复及不必要的动作
上述动作的浪费造成了 时间和体力上的不必要消 耗。
-
8
搬运的 浪费
从JIT的角度来看,搬运是一种不产生附加价值 的动作,而不产生价值的工作都属于浪费。
搬运的浪费具体表现为放置,堆积,移动,整列 等动作浪费,有此而带来物品移动所需空间的浪费, 时间的浪费和人力工具的占用等不良后果。
-
14
等待的 浪费
2008-1-25
-
1
课程介绍
▽ JIT的定义
▽ 浪费的定义
▽ 修理不良品的浪费
▽ 加工的浪费
▽ 动作的浪费
▽ 搬运的浪费
▽ 库存的浪费
▽ 制造过多的浪费
▽ 等待的浪费
▽ 管理的浪费
-
2
JIT的定义:
JIT生产方式的是“ 只在需要时,按需要的量, 生产所需的产品”(英文含义:Just in time )。
JIT生产方式的引入,正是帮助企业解决工厂 常见的八大浪费;提高企业的经济效率和生产效 率,为企业的发展打造良好的基础。
-
3
浪费的定义:
在JIT生产方式中,浪费的含意与社会 上通常所说的浪费有所区别。
对于JIT来讲,凡是超出增加产品价值 所绝对必须的最少量的物料,设备,人力, 场地和时间的部分都是浪费。
管理浪费是由于事先管理不到位而导致的问题, 科学的管理应该是具有相当的预见性,有合理的规 划,并在事情的推进过程中加强管理,控制和反馈, 这样就可以在很大程度上减少管理浪费现象的发生。
-
16
减少浪费,降低成本; 提升品质,增创效益。
-
17
-
7
不明技巧; 伸背动作; 弯腰动作; 重复及不必要的动作
上述动作的浪费造成了 时间和体力上的不必要消 耗。
-
8
搬运的 浪费
从JIT的角度来看,搬运是一种不产生附加价值 的动作,而不产生价值的工作都属于浪费。
搬运的浪费具体表现为放置,堆积,移动,整列 等动作浪费,有此而带来物品移动所需空间的浪费, 时间的浪费和人力工具的占用等不良后果。
-
14
等待的 浪费
- 1、下载文档前请自行甄别文档内容的完整性,平台不提供额外的编辑、内容补充、找答案等附加服务。
- 2、"仅部分预览"的文档,不可在线预览部分如存在完整性等问题,可反馈申请退款(可完整预览的文档不适用该条件!)。
- 3、如文档侵犯您的权益,请联系客服反馈,我们会尽快为您处理(人工客服工作时间:9:00-18:30)。
Lean-Center Konzern | Standardschulung KVP-Kaskade für Meister_V4.0 | K-PPA/L | Bk | 01.08.2010 | 10
示例- 等待时间 车身: 在焊接设备上放置零件
改进前
Foto
改进后
Foto
设备的门关着,员工需等待设备加工过程结束 设备的门开着,员工在设备上放置零件
Lean-Center Konzern | Standardschulung KVP-Kaskade für Meister_V4.0 | K-PPA/L | Bk | 01.08.2010 | 3
概览- 9种浪费
生产过剩 不必要的移动/动作
在制品/库存 违反人机工程
等待时间 运输
不必要的过程
欠缺沟通
架
看板管理 快速换型 过程稳定
Lean-Center Konzern | Standardschulung KVP-Kaskade für Meister_V4.0 | K-PPA/L | Bk | 01.08.2010 | 8
示例- 在制品/ 库存 发动机装配: 缸盖零件仓库
改进前
Foto
Lean-Center Konzern | Standardschulung KVP-Kaskade für Meister_V4.0 | K-PPA/L | Bk | 01.08.2010 | 6
示例- 生产过剩 总装: 车轮轮罩预装
改进前
Foto
改进后
Foto
预装轮罩储备起来,并多次拿取放置 在生产区域的占地面积需求大
Lean-Center Konzern | Standardschulung KVP-Kaskade für Meister_V4.0 | K-PPA/L | Bk | 01.08.2010 | 2
基础
工作内容基本分为三类:
价值的创造
• 产品增值 • 顾客愿意付费 • 例如,钻孔、焊接、铆接、
定位焊
缺陷/返修
Lean-Center Konzern | Standardschulung KVP-Kaskade für Meister_V4.0 | K-PPA/L | Bk | 01.08.2010 | 4
生产系统
节拍
流动
拉动
完美
基础
9种浪费 – 示例
Lean-Center Konzern | Standardschulung KVP-Kaskade für Meister_V4.0 | K-PPA/L | Bk | 01.08.2010 | 5
学习观察
生产系统
节拍
流动
拉动
完美
基础
Lean-Center Konzern | Standardschulung KVP-Kaskade für Meister_V4.0 | K-PPA/L | Bk | 01.08.2010 | 1
坚决杜绝各种浪费是持续改进过程的驱动力
原则
以创造价值为导向的同步型 生产系统
节拍原理
流动原理
以客户需求 为节拍
减少流程时间
拉动原理
拉动式 生产流程
完美原则
零缺陷 质量标准
效率
工作组织
生产平顺化 坚决杜绝各种浪费
标准化
环境保护
框架要素
合作的原则
• 领导与沟通 • 流程控制
标准化
• 流程的 • 产品的 • 工装设备的 • 基础设施的 • 组织结构的
学习性的组织
• 员工发展 • 问题解决流程 • 持续改进过程 • 知识管理 • 供应商管理 • 整体性组织发展
改进后
Foto
较高的缸盖库存量
减少后的库存量
Lean-Center Konzern | Standardschulung KVP-Kaskade für Meister_V4.0 | K-PPA/L | Bk | 01.08.2010 | 9
3. 等待时间造成的浪费
等待时间是由人员或机器受既定工作过程或工作环 境所限无法工作造成的。 模式:例如,人等人,人等设备
现象示例
针对/半成品落满灰尘或长期堆放 查找零件和文件费时费力 生产区域占地面积需求大,办公区域空
间需求大
运输路程长 较高的组织发配需求
多层仓库
平顺化 采用一件流/一套流生产方式 固定的客户节拍 增加上料频次 标示最小-最大缓冲区库存量或料架托
现象示例
等待前一道工艺步骤完成 等待设备维修或换型 等待人员共同工作 等待上料 等待信息
针对性措施示例
与工位节拍相适应的固定客户节拍 通过采用一件流生产方式使等待时间显
露出来 通过”停顿”进行目视化管理 (例如,
装配线节拍器) 用可拆分的或不受期限约束的工作来填
补等待时间 多设备操作
1. 生产过剩造成的浪费
HANDOUT
生产过剩造成的浪费,是指相对于当前内部或外部 的客户需求来说,过早,过快,过多地准备了产品、 服务和信息。
现象示例
针对性措施示例
提前生产或预生产 成品堆积如山 缓冲区满载 零部件/半成品落满灰尘或长期堆放 报废/降价处理
规定缓冲库存量的最小值-最大值 采用一件流生产方式 灵活的人员安排 快速换型 达到规定的标准缓冲量后即暂停生产
Lean-Center Konzern | Standardschulung KVP-Kaskade für Meister_V4.0 | K-PPA/L | Bk | 01.08.2010 | 11
目标: 最大化
手持钻机,放置于钻 孔处
员工工作
隐含的浪费
• 不增值 • 对于增值工作来说是必要的 • 例如,运输、零件放置、取料路线、
工具更换
目标: 最小化
因磨损或任务切换而 更换钻头
明显的浪费
• 不增值 • 对于增值工作来说是不必要的 • 例如,返工,拆包装,检测
目标: 消除
从一堆未分类的钻头 中挑选出正确的钻头
在安装前一刻预装轮罩 定义1级“成品库存”
Lean-Center Konzern | Standardschulung KVP-Kaskade für Meister_V4.0 | K-PPA/L | Bk | 01.08.2010 | 7
2. 在制品/ 库存造成的浪费
生产过剩、较大的额定批量生产、岛国意识以 及自我保护意识造成了物料及半成品库存,掩 盖了各种其他形式的浪费。
示例- 等待时间 车身: 在焊接设备上放置零件
改进前
Foto
改进后
Foto
设备的门关着,员工需等待设备加工过程结束 设备的门开着,员工在设备上放置零件
Lean-Center Konzern | Standardschulung KVP-Kaskade für Meister_V4.0 | K-PPA/L | Bk | 01.08.2010 | 3
概览- 9种浪费
生产过剩 不必要的移动/动作
在制品/库存 违反人机工程
等待时间 运输
不必要的过程
欠缺沟通
架
看板管理 快速换型 过程稳定
Lean-Center Konzern | Standardschulung KVP-Kaskade für Meister_V4.0 | K-PPA/L | Bk | 01.08.2010 | 8
示例- 在制品/ 库存 发动机装配: 缸盖零件仓库
改进前
Foto
Lean-Center Konzern | Standardschulung KVP-Kaskade für Meister_V4.0 | K-PPA/L | Bk | 01.08.2010 | 6
示例- 生产过剩 总装: 车轮轮罩预装
改进前
Foto
改进后
Foto
预装轮罩储备起来,并多次拿取放置 在生产区域的占地面积需求大
Lean-Center Konzern | Standardschulung KVP-Kaskade für Meister_V4.0 | K-PPA/L | Bk | 01.08.2010 | 2
基础
工作内容基本分为三类:
价值的创造
• 产品增值 • 顾客愿意付费 • 例如,钻孔、焊接、铆接、
定位焊
缺陷/返修
Lean-Center Konzern | Standardschulung KVP-Kaskade für Meister_V4.0 | K-PPA/L | Bk | 01.08.2010 | 4
生产系统
节拍
流动
拉动
完美
基础
9种浪费 – 示例
Lean-Center Konzern | Standardschulung KVP-Kaskade für Meister_V4.0 | K-PPA/L | Bk | 01.08.2010 | 5
学习观察
生产系统
节拍
流动
拉动
完美
基础
Lean-Center Konzern | Standardschulung KVP-Kaskade für Meister_V4.0 | K-PPA/L | Bk | 01.08.2010 | 1
坚决杜绝各种浪费是持续改进过程的驱动力
原则
以创造价值为导向的同步型 生产系统
节拍原理
流动原理
以客户需求 为节拍
减少流程时间
拉动原理
拉动式 生产流程
完美原则
零缺陷 质量标准
效率
工作组织
生产平顺化 坚决杜绝各种浪费
标准化
环境保护
框架要素
合作的原则
• 领导与沟通 • 流程控制
标准化
• 流程的 • 产品的 • 工装设备的 • 基础设施的 • 组织结构的
学习性的组织
• 员工发展 • 问题解决流程 • 持续改进过程 • 知识管理 • 供应商管理 • 整体性组织发展
改进后
Foto
较高的缸盖库存量
减少后的库存量
Lean-Center Konzern | Standardschulung KVP-Kaskade für Meister_V4.0 | K-PPA/L | Bk | 01.08.2010 | 9
3. 等待时间造成的浪费
等待时间是由人员或机器受既定工作过程或工作环 境所限无法工作造成的。 模式:例如,人等人,人等设备
现象示例
针对/半成品落满灰尘或长期堆放 查找零件和文件费时费力 生产区域占地面积需求大,办公区域空
间需求大
运输路程长 较高的组织发配需求
多层仓库
平顺化 采用一件流/一套流生产方式 固定的客户节拍 增加上料频次 标示最小-最大缓冲区库存量或料架托
现象示例
等待前一道工艺步骤完成 等待设备维修或换型 等待人员共同工作 等待上料 等待信息
针对性措施示例
与工位节拍相适应的固定客户节拍 通过采用一件流生产方式使等待时间显
露出来 通过”停顿”进行目视化管理 (例如,
装配线节拍器) 用可拆分的或不受期限约束的工作来填
补等待时间 多设备操作
1. 生产过剩造成的浪费
HANDOUT
生产过剩造成的浪费,是指相对于当前内部或外部 的客户需求来说,过早,过快,过多地准备了产品、 服务和信息。
现象示例
针对性措施示例
提前生产或预生产 成品堆积如山 缓冲区满载 零部件/半成品落满灰尘或长期堆放 报废/降价处理
规定缓冲库存量的最小值-最大值 采用一件流生产方式 灵活的人员安排 快速换型 达到规定的标准缓冲量后即暂停生产
Lean-Center Konzern | Standardschulung KVP-Kaskade für Meister_V4.0 | K-PPA/L | Bk | 01.08.2010 | 11
目标: 最大化
手持钻机,放置于钻 孔处
员工工作
隐含的浪费
• 不增值 • 对于增值工作来说是必要的 • 例如,运输、零件放置、取料路线、
工具更换
目标: 最小化
因磨损或任务切换而 更换钻头
明显的浪费
• 不增值 • 对于增值工作来说是不必要的 • 例如,返工,拆包装,检测
目标: 消除
从一堆未分类的钻头 中挑选出正确的钻头
在安装前一刻预装轮罩 定义1级“成品库存”
Lean-Center Konzern | Standardschulung KVP-Kaskade für Meister_V4.0 | K-PPA/L | Bk | 01.08.2010 | 7
2. 在制品/ 库存造成的浪费
生产过剩、较大的额定批量生产、岛国意识以 及自我保护意识造成了物料及半成品库存,掩 盖了各种其他形式的浪费。