模具的整体结构布局概述
模具组成系统与结构介绍

模具组成系统与结构介绍引言模具是现代工业生产中不可或缺的重要工具,它的质量、可靠性和生产效率直接影响着产品的制造质量和成本。
在模具的设计与制造过程中,模具的组成系统和结构是至关重要的因素。
本文将对模具组成系统与结构进行详细介绍,包括模具的基本组成部分、模具结构设计的原则和常用结构形式。
模具的基本组成部分1.模具底板:模具底板是模具的主要支撑部分,承载着模具的各种组成部件。
它通常由高强度合金钢材料制成,具有足够的刚性和耐磨损性。
模具底板上还通常安装着定位销和定位孔,以确保模具的定位精度和互换性。
2.模具腔:模具腔是模具制造的核心部分,直接决定了产品形状和尺寸的精度。
模具腔通常由模具边缘、模具中板和模具芯构成,其中模具中板又包括上模板和下模板。
模具腔的制造通常采用数控机床精加工和电火花加工等工艺。
3.导向机构:导向机构用于保持模具腔的运动方向和相对位置,确保模具的准确定位和稳定运行。
常用的导向机构有滑块导向、柱销导向和楔块导向等形式。
4.驱动机构:驱动机构用于实现模具的开合和顶出动作。
常见的驱动机构有液压驱动、气动驱动和机械驱动等方式,具体选择根据模具的尺寸、复杂程度和生产需求决定。
5.排气机构:排气机构用于排除模具腔中积聚的气体,防止产品在注塑、压铸过程中产生气泡或缺陷。
排气机构通常采用通气孔、排气槽和排气筒等形式。
模具结构设计的原则1.适应生产要求:模具的结构设计需要满足产品的生产要求,包括产品的尺寸精度、外观质量、材料流动性等方面。
结构设计需要考虑产品的成型工艺和材料特性,确保模具能够准确而稳定地实现产品的成型。
2.提高生产效率:模具结构设计需要考虑生产效率的提高,包括模具的开合速度、顶出速度和换模时间等方面。
合理的结构设计可以减少模具的开合力和顶出力,降低能耗,提高生产效率。
3.保证模具的可靠性和稳定性:模具的结构设计需要保证模具的可靠性和稳定性,防止模具在使用中发生断裂、变形或失效。
结构设计需要考虑材料的选择、强度计算、疲劳寿命等因素,确保模具在长期使用过程中能够正常运行。
模具基本结构(3篇)

第1篇一、引言模具作为一种重要的加工工艺,广泛应用于机械制造、汽车、电子、塑料、包装等行业。
模具的基本结构是模具设计和制造的基础,了解模具的基本结构对于提高模具质量、降低生产成本具有重要意义。
本文将详细介绍模具的基本结构,包括模具的组成、各部分的作用以及模具的结构特点。
二、模具的组成1. 模具座模具座是模具的基础部分,用于固定模具各部分,保证模具的精度和稳定性。
模具座通常由以下几部分组成:(1)底板:底板是模具座的基础,用于固定模具各部件。
(2)支撑板:支撑板用于支撑模具的侧面,保证模具的垂直度。
(3)顶板:顶板位于模具顶部,用于固定模具的上模和下模。
2. 模具上模模具上模是模具的加工部分,负责对工件进行加工。
模具上模主要包括以下几部分:(1)模板:模板是模具上模的主体,用于固定模具的凸模、凹模等部件。
(2)凸模:凸模是模具上模的关键部件,负责对工件进行成型。
(3)导向装置:导向装置用于保证模具上模和下模的准确对位。
3. 模具下模模具下模是模具的加工部分,负责对工件进行加工。
模具下模主要包括以下几部分:(1)模板:模板是模具下模的主体,用于固定模具的凹模、凸模等部件。
(2)凹模:凹模是模具下模的关键部件,负责对工件进行成型。
(3)导向装置:导向装置用于保证模具上模和下模的准确对位。
4. 模具导向系统模具导向系统是保证模具加工精度的重要部分,主要包括以下几部分:(1)导柱:导柱用于引导模具上下移动,保证模具的垂直度。
(2)导套:导套用于固定导柱,保证导柱的稳定性和导向精度。
(3)导向板:导向板用于固定导套,保证模具的导向精度。
5. 模具加热冷却系统模具加热冷却系统是保证模具加工质量和提高生产效率的重要部分,主要包括以下几部分:(1)加热器:加热器用于加热模具,提高模具温度,改善加工性能。
(2)冷却器:冷却器用于冷却模具,降低模具温度,保证模具精度。
(3)热交换器:热交换器用于实现模具加热和冷却的循环。
模具结构设计方案

模具结构设计方案模具是工业生产中常用的工具之一,广泛应用于塑料、金属、陶瓷等制品的生产过程中。
模具的结构设计对产品的成型质量、生产效率以及模具寿命等都有着重要的影响。
下面将以塑料模具为例,详细介绍模具结构设计的几个方面。
首先是模具的整体结构设计。
模具一般由上、下两部分组成,上模和下模之间通过模具螺栓连接。
上模通常由进料口、固定板、移动板、顶针等部分组成,下模则由底板、定位销、导向板等部分组成。
在整体结构设计中,需要注意上、下模的对位准确、顶出机构的稳定性以及模具的可拆卸性等。
其次是注塑模具中的流道系统设计。
流道系统是塑料模具中最关键的部分,直接影响产品的成型质量。
在流道系统的设计中,需要考虑塑料的充填速度、压力和温度等因素,合理选择流道的截面形状和尺寸。
同时,还需要设计出合适的喷嘴和冷却系统,以确保塑料在流道中充分流动和冷却。
第三是模具的冷却系统设计。
冷却系统对于模具寿命和产品质量有着重要的影响。
在冷却系统的设计中,需要合理设置冷却通道,并确保冷却通道与模具表面的距离足够近,以提高冷却效果。
同时,还需要注意冷却通道的位置和布局,以保证整个模具受热均匀,避免产生应力集中和变形等问题。
另外还需要考虑模具的顶出机构设计。
顶出机构主要用于将成型的产品从模具中弹出,避免产品粘模。
在顶出机构的设计中,需要确保顶出机构的稳定性和可靠性,同时考虑到产品的形状、材料和尺寸等因素,设计合适的顶出机构形式和数量。
最后是模具材料的选择。
模具材料的选择直接影响到模具的使用寿命和成本。
一般而言,模具材料要求具有较高的硬度、强度和耐磨性,同时还需具备一定的耐腐蚀性和导热性等特点。
在选择模具材料时,需要根据具体的生产需求和经济因素综合考虑,选择合适的模具材料。
综上所述,模具结构设计是一个复杂的工作,需要考虑多个方面的因素。
合理的模具结构设计可以提高产品的成型质量和生产效率,延长模具的使用寿命,减少生产成本。
因此,在进行模具结构设计时,需要充分考虑以上几个方面的原则和要点,以保证模具的性能和质量。
模具结构基础知识1
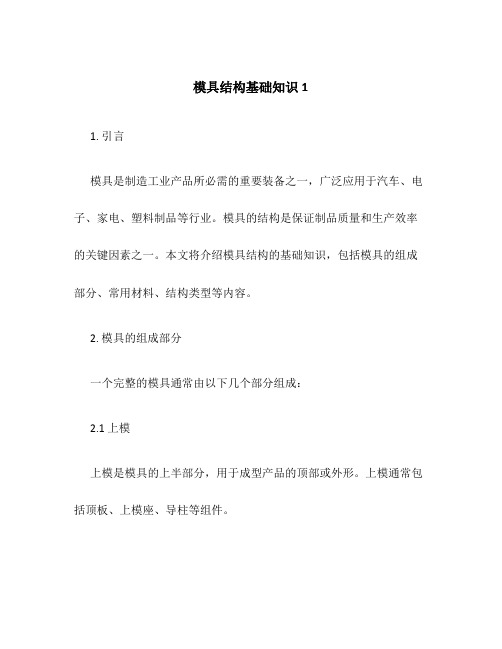
模具结构基础知识11. 引言模具是制造工业产品所必需的重要装备之一,广泛应用于汽车、电子、家电、塑料制品等行业。
模具的结构是保证制品质量和生产效率的关键因素之一。
本文将介绍模具结构的基础知识,包括模具的组成部分、常用材料、结构类型等内容。
2. 模具的组成部分一个完整的模具通常由以下几个部分组成:2.1 上模上模是模具的上半部分,用于成型产品的顶部或外形。
上模通常包括顶板、上模座、导柱等组件。
2.2 下模下模是模具的下半部分,用于成型产品的底部或内形。
下模通常包括下模座、下模板、导柱等组件。
2.3 滑块模滑块模也称为副模或侧模,用于成型产品的侧面或突起部分。
滑块模通常包括滑块、导柱套和定位销等组件。
2.4 斜顶模斜顶模用于成型带有斜侧面的产品。
斜顶模通常包括斜顶、导柱套、斜顶片等组件。
2.5 拉伸模拉伸模用于成型带有拉伸形状的产品。
拉伸模通常包括拉伸块、导柱、拉伸销等组件。
模具材料的选择直接影响到模具的使用寿命和成品质量。
常用的模具材料包括:3.1 铝合金铝合金具有良好的热传导性能和机械性能,适用于制作小型模具和大批量生产的模具。
3.2 铜合金铜合金因其良好的导热性和耐磨性被广泛应用于模具制造,尤其适用于高速冲压模具和大体积模具。
3.3 铁合金铁合金包括低碳钢、合金钢、工具钢等。
它们具有高硬度、高强度和耐磨性,适用于制作高精度模具和耐用性要求较高的模具。
塑料模具材料包括PVC、PE、PP等。
它们具有良好的耐腐蚀性和可塑性,适用于制作塑料制品模具。
4. 模具结构类型模具结构的选择取决于产品的形状、尺寸和材料等因素。
常见的模具结构类型包括:4.1 单模结构单模结构是最简单的模具结构,适用于产品形状简单、工艺要求低的情况。
4.2 组合模结构组合模结构由多个模块组合而成,适用于产品形状复杂、工艺要求高的情况。
4.3 多腔模结构多腔模结构是指在一个模具中设置多个腔室,可以同时成型多个产品。
多腔模结构适用于批量生产相同产品的情况。
模具的结构组成及各部分结构的作用

模具的结构组成及各部分结构的作用说到模具,很多人可能觉得这是个非常专业、复杂的东西。
其实,模具就像是我们在做菜时用的锅、碗、瓢、盆一样,虽然不起眼,但每一个部分都有其独特的作用。
如果你在想要了解模具的秘密,那就跟我一块儿揭开这神秘面纱吧!1. 模具的基本结构模具的基本结构可以说是模具的“骨架”,每一个部分都有自己的小秘密。
一般来说,模具的结构包括了模具的型腔、型芯、模具基板、导向装置和排气系统。
这些部分就像是一部精密的机器,每一部分都发挥着至关重要的作用。
1.1 型腔和型芯:模具的“心脏”首先,咱们得聊聊模具的型腔和型芯。
这两者就像是模具的“心脏”——如果没有它们,整个模具就会失去活力。
型腔是模具的内部空腔,它决定了最终产品的形状和尺寸。
可以想象成是一个蛋糕的模具,蛋糕的形状完全取决于这个模具的形状。
而型芯则是用来填充型腔的部分,它们就像是个“填料”,确保蛋糕的中心部分也能完美无瑕。
这两个部分通常是分开的,模具在工作时,型芯和型腔会互相配合,形成一个完整的模具结构。
它们的结合是如此密切,以至于当它们分开时,就像是一对好朋友告别,心里总有些不舍。
1.2 模具基板:模具的“底盘”接着说说模具基板,它可是模具的“底盘”,就像车的底盘一样,稳固又重要。
基板是模具的支撑结构,承载了整个模具的重量和压力。
模具基板上的孔、凹槽、定位装置都是为了确保模具能够在工作时稳定地固定在机器上。
基板的设计不仅要考虑强度,还要兼顾加工精度和装配方便。
如果基板不稳,整个模具就像在打高空弹跳,一不小心就会出问题。
因此,基板的设计可是个细致活儿,稍有差池,就会影响到整个模具的工作效果。
2. 导向装置:模具的“导航员”导向装置是模具的“导航员”,它确保了模具在打开和关闭时能够顺利进行。
这些装置包括了导柱、导套和定位销等。
它们的作用就像汽车上的导航系统,帮助模具精准定位,避免了模具在工作时的晃动或错位。
导向装置的好坏直接关系到模具的使用寿命和生产效率。
模具的结构组成及各部分结构的作用

模具的结构组成及各部分结构的作用大家好,我今天要给大家讲解一下模具的结构组成及各部分结构的作用。
首先我们来了解一下什么是模具,模具是用来生产各种零部件的工具,它可以使原材料经过加工后得到我们需要的产品。
模具在工业生产中有着非常重要的地位,它的质量和性能直接影响到产品的质量和性能。
那么模具到底是由哪些部分组成的呢?它们各自又有什么样的作用呢?接下来我将从以下几个方面给大家详细介绍。
一、模具的基本结构1.1 上模上模,也叫顶针板,是模具的上部结构。
它的主要作用是与下模板配合,使原材料顺利地进入模具型腔,同时在成型过程中起到导向作用。
上模通常采用钢材制作,具有较高的强度和耐磨性。
为了保证上模与下模板的配合精度,上模的表面通常需要进行精加工。
1.2 下模板下模板,也叫凹模,是模具的下部结构。
它的主要作用是固定上模板,使其与原材料接触,并在成型过程中起到支撑作用。
下模板通常采用钢板制作,具有较高的强度和耐磨性。
为了保证下模板与上模板的配合精度,下模板的表面通常需要进行精加工。
1.3 导柱、导套导柱、导套是模具的导向结构。
它们分别安装在上下模板的两侧,用于引导原材料流向正确的方向。
导柱、导套通常采用铜合金或硬质合金制成,具有较高的耐磨性和抗拉强度。
它们的设置可以有效地提高模具的使用寿命和生产效率。
二、模具的其他结构2.1 限位柱、限位环限位柱、限位环是模具的安全保护结构。
它们分别安装在上下模板的内侧,用于限制原材料在进料过程中的行程范围。
当原材料超出设定的范围时,限位柱、限位环会自动弹起,防止模具受损或安全事故的发生。
限位柱、限位环通常采用硬质合金制成,具有较高的耐磨性和抗冲击性。
2.2 冷却系统冷却系统是模具的重要辅助结构。
它通过循环流动的冷却液,有效地降低模具的工作温度,延长模具的使用寿命。
冷却系统的设置可以根据不同的生产工艺要求进行调整,以满足不同的生产需求。
常见的冷却方式有水冷和气冷两种。
三、总结通过对模具的结构组成及各部分结构的介绍,我们可以了解到模具是一个复杂的机械系统,它涉及到多个学科的知识。
模具结构和基本原理简单介绍

Adobe Acrobat 7.0 Document
14
五 * 1,组立图 ,
• 决定模具大的结构包括水路的排放,滑 块的安排,分型面的决定
Adobe Acrobat 7.0 Document
Adobe Acrobat 7.0 Document
15
五 * 2 带滑块的组立图
Adobe Acrobat 7.0 Document
首页
模具结构和基本原理简单介绍
Date : 2007-01-05 Venue : BOD room - TPV Suzhou
Prepared by : Red Ma
1
一, 模具的基本结构
模架:注塑模具的骨架,由模班板、紧固件和导向零件组成。 模架 成型零件:直接与产品接触或部分接触并决定产品形状及尺寸的部分。 成型零件 就是我们常说的模仁部分。 浇注系统: 浇注系统 是熔融塑料从注塑机喷嘴进入模具型腔所流经的通道。一 般由主流道、分流道、浇口和冷料穴几个部分组成。 脱模系统:主要作用是将冷却的产品从模具型腔中推出(包括顶针、 脱模系统 顶板、斜抽芯机构,复位机构等)。 导向系统:导向系统主要用于保证在注塑生产时,模具的动、定模开 导向系统 合时位置正确(有导柱和导套,零度束块)。 控温系统:包括水路、铍铜、热流道、模温加热系统等。 控温系统 侧向分型抽芯机构:用于成型产品上与开模方向不同的结构(例如滑 侧向分型抽芯机构 块、斜销等)。 排气系统:当熔融的塑料以高压力,高速度冲入型腔时,如果型腔里 排气系统 的气体不能快速排出就会被包在塑料中造成气泡,或者是产生高温 将塑胶产品烧焦。一般模具都会有排气系统(排气槽,排气块和镶 针排气)。
Adobe Acrobat 7.0 Document
模具结构概述.pptx
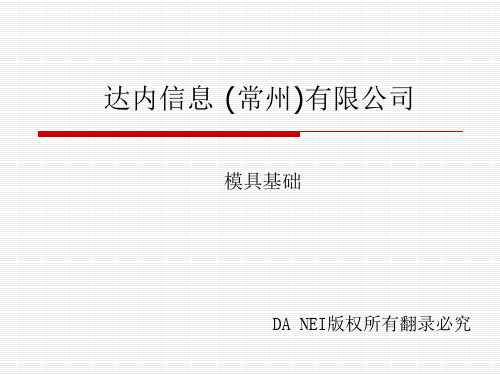
12、越是无能的人,越喜欢挑剔别人的错儿。08:18:0408:18:0408:18Monday, January 11, 2021
13、志不立,天下无可成之事。21.1.1121.1.1108:18:0408:18:04January 11, 2021
• 14、Thank you very much for taking me with you on that splendid outing to London. It was the first time that I had seen the Tower or any of the other fa mous sights. If I'd gone alone, I couldn't have seen nearly as much, because I wouldn't have known my way about.
公模进浇系统(一) 三板模
公模进浇系统(二)两板模
型式
优点
缺点
备
注
二板模 1.模具构造简单,加工容易 1.成型问题较不具可修正性
2.价格较具优势
2.
优 三板模 1.
劣
比
1.成型周期较短
较 热浇道 2.节省塑料成本
表
3.成型条件易于控制
1.模具构造复杂,故成本较 高,加工较难
2.成型周期较长,且塑料残 料过多,故成本高
T H E E N D 17、一个人如果不到最高峰,他就没有片刻的安宁,他也就不会感到生命的恬静和光荣。上午8时18分4秒上午8时18分08:18:0421.1.11
达内信息 (常州)有限公司
模具基础
DA NEI版权所有翻录必究
模具基础知识设计基本结构和使用注意事项
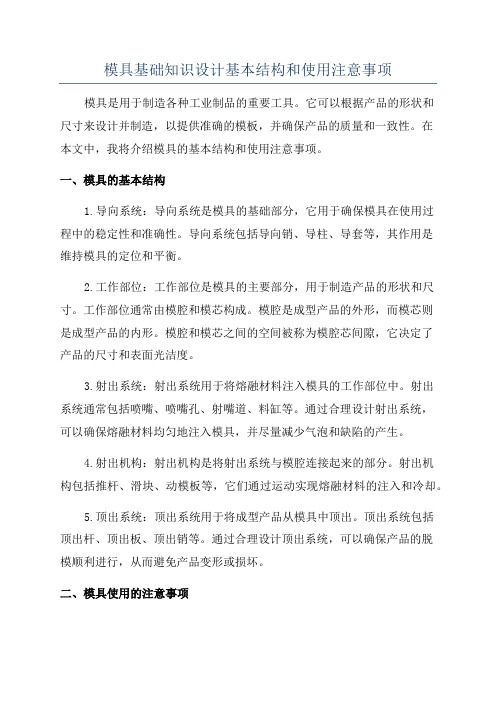
模具基础知识设计基本结构和使用注意事项模具是用于制造各种工业制品的重要工具。
它可以根据产品的形状和尺寸来设计并制造,以提供准确的模板,并确保产品的质量和一致性。
在本文中,我将介绍模具的基本结构和使用注意事项。
一、模具的基本结构1.导向系统:导向系统是模具的基础部分,它用于确保模具在使用过程中的稳定性和准确性。
导向系统包括导向销、导柱、导套等,其作用是维持模具的定位和平衡。
2.工作部位:工作部位是模具的主要部分,用于制造产品的形状和尺寸。
工作部位通常由模腔和模芯构成。
模腔是成型产品的外形,而模芯则是成型产品的内形。
模腔和模芯之间的空间被称为模腔芯间隙,它决定了产品的尺寸和表面光洁度。
3.射出系统:射出系统用于将熔融材料注入模具的工作部位中。
射出系统通常包括喷嘴、喷嘴孔、射嘴道、料缸等。
通过合理设计射出系统,可以确保熔融材料均匀地注入模具,并尽量减少气泡和缺陷的产生。
4.射出机构:射出机构是将射出系统与模腔连接起来的部分。
射出机构包括推杆、滑块、动模板等,它们通过运动实现熔融材料的注入和冷却。
5.顶出系统:顶出系统用于将成型产品从模具中顶出。
顶出系统包括顶出杆、顶出板、顶出销等。
通过合理设计顶出系统,可以确保产品的脱模顺利进行,从而避免产品变形或损坏。
二、模具使用的注意事项1.合理使用模具:在使用模具时,应根据产品的特点和要求,选择合适的模具。
同时,还应遵循模具的使用规范和操作流程,确保安全使用。
2.定期维护模具:模具在使用过程中,会受到磨损和变形的影响。
因此,定期维护模具是非常重要的。
维护包括清洁模具、修复模具、更换模具零件等,以确保模具的正常工作。
3.善于保养模具:除了定期维护模具外,还应善于保养模具。
保养包括防锈、润滑、正确存储等,以延长模具的使用寿命。
4.注意模具的温度:模具在使用过程中,会发生高温和低温的变化。
因此,在使用模具时,应注意模具的温度,避免过热或过冷,以免影响产品的质量。
5.善于解决故障:在使用模具时,可能会遇到一些故障,如堵塞、变形、磨损等。
塑料模具基本结构介绍

塑料模具基本结构介绍塑料模具是塑料制品的关键部件,它的质量直接关系到塑料制品的质量和生产效率。
而塑料模具的基本结构则是决定塑料制品形状和品质的关键。
一、模具结构种类模具结构分为单面模和双面模两种,单面模具只有一面模具,双面模具则有两面模具。
1.单面模具单面模具结构简单,价格也相应较低,适用于简单的塑料制品的生产。
2.双面模具双面模具一般由顶模和底模组成。
底模具在模具架主体内,顶模在模柄上,可以升降和倾斜。
顶模和底模一起合模形成塑料制品的外观和内部结构,使用起来更加灵活方便。
二、模具结构详解塑料模具的基本结构可以分为以下几个部分:模具架、导向柱、活动板、托架、顶模、底模、滑块、成型部件和冷却系统。
1.模具架模具架是支撑模具的主体结构,通常采用的材料有钢铁、铝合金等,也有采用不锈钢的。
模具框架架构牢固,耐用性好,对模具的制作有很大的影响。
2.导向柱导向柱是模具架上支撑模具的结构,在模具的加工中起到了稳定作用。
导向柱一般采用冷拉钢制作,表面加工滑动层,以防止摩擦磨损。
3.活动板模具在成型过程中需要进行开闭模,活动板与顶模或底模相连,通过开关模座,实现开闭模,同时保证模具的定位。
4.托架托架是承载模具的结构,一般采用铝合金或钢质制作。
托架的稳定性和牢固性保证了模具运转过程的稳定性。
5.顶模和底模顶模和底模是塑料模具的核心部件,直接影响塑料制品的质量和生产效率。
(1)底模:底模是根据塑料制品实际要求设计的,并根据塑料制品的特性调整制品毛坯的数量和质量。
底模可以分为定位模版和成型模板之间的大模座和小模座。
(2)顶模:顶模的设计也必须合理,以保证模具整体结构的牢固性和稳定性。
常见的顶模有拉杆式和顶套式,拉杆式顶模适用于大型产品或复杂造型,顶套式顶模适用于小型或简单塑料制品的制造。
6.滑块塑料模具的滑动结构一般称为滑块,其作用是形成复杂的内部结构。
滑块的设计必须满足了模具的复杂性和精度要求。
7.成型部件成型部件是模具的关键部分,其数量和质量直接影响了塑料制品的质量和性能。
浅析模具的整体结构布局

浅析模具的整体结构布局模具是用来制造制品的工具。
模具的设计和制造对于制品的质量、成本和效率都起着重要的作用。
模具的整体结构布局是模具设计中的一个关键环节。
正确的整体结构布局可以提高模具的使用寿命、提高生产效率、降低制品的成本。
一、模具整体结构布局的意义模具整体结构布局是指模具设计中对整体结构的各个部分进行逐一分析、计算、设计和组合的一个过程。
模具结构布局直接影响模具的质量、寿命、成本等方面。
模具结构的优化,对于制品的质量和生产效率有着重要的作用。
二、模具整体结构布局的原则模具整体结构布局的原则有四个方面,分别是:1、简洁明了模具整体结构应该简洁明了。
在模具的布局设计中,结构应该尽量简化,同时明确各个部分的功能和作用。
2、合理实用模具整体结构设计应根据制品的特性和生产过程的需要,选择适当的结构形式。
在保证结构强度和刚性的前提下,尽量降低模具重量,减少生产过程中的动能消耗。
3、稳定可靠模具整体结构设计应该保证结构的稳定和可靠。
在设计时应考虑各部分的相互作用和长期使用的可能引起的变形和痕迹,尽可能减少疲劳等方面的损伤。
4、易于加工和维护模具整体结构设计应该考虑到模具的加工和维修的方便。
在设计中应尽量考虑到加工、修理结构的复杂程度,保证模具可以快速修复。
三、模具整体结构布局的步骤模具整体结构布局的步骤分五个方面,分别是:1、确定模具尺寸根据制品的尺寸和生产过程的需要,确定模具的尺寸和格式。
以保证模具的结构强度和稳定性。
2、设计模具型式根据制品的特点和生产过程的需要,设计适当的模具型式。
在模具型式设计中应充分考虑到成本的控制、效率的提高等因素。
3、分析每一部分分析模具的整体结构的各个部分,如模具底座、卡板、导向机构等。
对于每一部分设计应充分分析结构强度、刚性、稳定性、可靠性等方面要求。
4、结构的合理组合在模具结构设计过程中,应考虑各部分的组合,使各个部分的功能最大限度地发挥出来。
另外在设计组合时,应合理地使用充分的技能和经验。
经典模具结构讲解

经典模具结构讲解经典模具结构是指在模具制造和使用过程中应用最广泛、被广泛认可和使用的模具结构设计形式。
它包括以下几个部分:1. 上模座:上模座是模具的固定部分,通常由座板和上模芯组成。
上模芯可以嵌入到座板中,以便固定模具。
上模座通常安装在机床的固定床身上。
2. 下模座:下模座是模具的移动部分,通常由下模块和下模芯组成。
下模块可以通过导柱和导套与上模座连接,以便于上下模具之间的移动。
下模座通常安装在机床的可移动工作台上。
3. 塑料料斗:塑料料斗是模具的原料进入口,通常位于模具的上部,与注塑机连接。
塑料料斗通过喂料装置将塑料颗粒送入模具中进行成型。
4. 出料口:出料口是模具中制品的出口,通常位于模具的下部。
通过打开出料口,成型制品可以从模具中取出。
5. 合模装置:合模装置用于使上下模具之间完成闭合,以便进行注塑成型过程。
合模装置通常包括模具开闭机构、导向机构和锁紧机构。
6. 冷却系统:冷却系统用于控制模具中的温度,防止模具在注塑过程中过热。
冷却系统通常由冷却水管和冷却水箱组成,冷却水通过水管流经模具,带走模具中的热量。
7. 弹簧机构:弹簧机构用于保持模具的闭合状态,并在成型过程中起到缓冲作用。
弹簧机构通常安装在模具的合模装置中。
8. 引导机构:引导机构用于确保上下模具的准确定位,防止模具在闭合过程中产生错位。
引导机构通常安装在模具的合模装置中。
经典模具结构的设计旨在提高模具的加工精度、提高生产效率、保证产品质量,并具有良好的实用性和通用性。
不同的模具结构适用于不同的注塑产品,具体结构设计应根据具体产品要求和操作习惯进行调整。
模具结构概述

灌嘴
三板(sānbǎn)模图面
脱料板 锁模块
母模仁 公模仁 小拉杆
导套
第八页,共38页。
上固定 (gùdìng)板 导套
母模板
开闭器 公模板 (múbǎn) 大拉杆
模角板 上顶出板 下顶出板 下固定板
大拉杆 (lāgān) 小拉杆 (lāgān)
开闭器
第九页,共38页。
锁模块
母模板 (múbǎn) 脱料板
第二十页,共38页。
公模滑塊
斜撑销
滑块束块
公模滑 块
挡块
第二十一页,共38页。
母模滑塊
第二十二页,共38页。
滑块拨杆 挡块
母模滑块
內滑塊
滑块 拨杆 挡块
内滑块
第二十三页,共38页。
特殊(tèshū)滑塊(油壓缸滑塊)
滑块束块
滑块
挡块
第二十四页,共38公模斜销 2.母模斜销
胶系统 料方式
制作难度高
2.成型周期最长
第十七页,共38页。
一 滑块 二 斜销 三 顶出系统(xìtǒng)
第十八页,共38页。
1.公模滑块 2.母模滑块 3.内滑块 4.特殊(tèshū)滑块(油压缸滑块)
第十九页,共38页。
滑块形式(xíngshì)
滑块是为了(wèi le)解决倒勾 (undercut) 而发展的模具机构,其基本原 理是将模具开闭的垂直运动,转向成水平运动.而为了(wèi le)配合倒勾位 置在公模或者是母模,而变化出不同的机构形式.滑块机构为下列几项基本 机构加以组合而成
RP
上顶出板 下顶出板
下固定 (gùdìng)板
热浇道系统(xìtǒng)
热流(rèliú) 道板
模具的整体结构布局概述

模具的整体结构布局概述1.成品的收缩率1.1它是成品冷却后的收缩量与冷却前在模型内之尺寸的比值.这个比值是经常会发生变化的,能够产生收缩率有所浮动的因素有:原料品种,成型保压时间,模具温度,室内温度……,因此设计人员在设计模具型腔的具体尺寸时,应搞清正常条件下的原料收缩率是最最重要的,否则,当收缩率取错,基本上将要重新更换模仁,那幺,收缩率在设计的过程如何应用呢?最要紧的还是利用收缩率来计算.模具型腔的尺寸,即: 模具尺寸=成品尺寸*(1+收缩率)而另外一种算法应用极少,即: 模具尺寸=成品尺寸/(1-收缩率) 而各类原料的收缩率请参考第八章“成型部分”附表1.2长条形成品的收缩率如何确定:长条形成品在扣收缩率时,在宽度方向与长度方向是确信有出入的,即可能是宽度尺寸收缩率放5%0,而长度方向则为 3.5%0,这样的例子.但毕竟如何面对这些不定因素,我们还需要从实际积存经验,从现实的角度考虑,在此无法论证抱歉.2.一模多腔如何布置:在现行的模具设计过程中,由于客户对成品的品质及精度要求日益增高,因此,司之内).由于从理论出发,因此,在常用的多穴布置时,穴.如图1中.(1*2与1*4)简单的背后,位,另一个不到位.侧模腔填充较满.衡.如按键的进浇系统,绕远一点,已有圆弧流道之成功的实例.3.模具的模仁尺寸确定:一个例子说明,如图2.图中母仁之形式取值是绝对不可取的.而公仁COR部分,也要根据实际情况计算模仁的最佳尺寸,那幺如何对模仁的边界进行尺寸取值呢?须注意下列几点:3.1考虑成品的总体高度若成品高度尺寸不是太大,则母仁CA V部分的边缘厚度尺寸只须达到封闭熔体塑料即可.通常为15~30mm.查表定值,当然,这一尺寸还要考虑水路布置及螺钉部分.若成品那幺,这两种方法如何相辅相承地灵活应用呢?要现场所决定,建议第二种方法行事.在模仁的宽度确定了,能够试比较的方法来选择不一致的模架,基本上当CA V或者COR,并同模仁压块之最大投影宽度在顶出板的宽度范围就能够了.若要跑滑块或者所遇母模型腔特别深之特殊情况,能够据实追加模架宽度.另外,模架高度方面要紧是母模与公模本体板及枕板部分的厚度,母模本板厚度要紧考虑加工时不变形就能够了.假如母模板中模仁穴过深,通常情况下,母模板底部厚度为30~80mm即可.公模本体板厚度能够为公模仁PL面下列高度的3倍.公模仁的PL面下列厚度与本体板底部厚度比值为1/2关系.枕板高度,视成品的需要顶出量而定,其它无影响因素.还有一点要注意,许多人对简易三板模与标准三板模的应用场合还不是特别明确,在此简单说明.简易三板模比标准三板模的结构上少了四根GP导柱,简易三板模的公,母模之间的合模导向完全是通过LP(即前板导柱)操纵,而LP 通常相当长.再利用其头部导向公,母模合模,必定容易失稳,在模具型腔内部,若靠破,斜破或者合模时滑动的组件或者部位较多时,容易碰伤.因此,就务必利用标准三板模的GP(4*)来对公,母模的合模进行导向.当然,所有GP的高度不用过高,只需GP头部高出公模仁最高点1.5倍的GP直径就能够了.目的是为让公仁部进入母仁内腔之前就开始导向合模.GP的导套,在过分厚的模板中是不需要从上通到下的,实际起到作用的只有2/3的板厚即可.如图2所示.5.直束子与斜束子的区别:往常,许多说法认为直束子没有斜束子的定位精度高,这从现在的角度出发,是不完全也是不根本的讲法,由于光用斜束子的模具比起光用直束子的模具而言,在插破处易产生毛边的依旧有毛边.那幺,现在如何正确选用这两种束子呢?5.1直束子:它是一对束块保持垂直面束紧关系的装置, 垂直面的配合高度就决定了定位作用的长度,即运用了直束子的模具在合模合紧之前就产生了一段距离的公,母模相对定位,完全不可能使模腔内插破角度小(0.5°)的斜面切伤.因此,据以上情况,直束子并不是只能够运用在公,母面无滑块机构的情况下,而是被应用在所有有较多插破关系成型的各类机构模具中,要紧是内部结构成品模具中.8.1模具的进浇口邻近,特别是肓形浇口的邻近,由于有许多的上,下盖,及掀盖,在使用肓形浇口进浇口产生了溢料,浇口邻近注射压力太大.8.2靠破,插破面的正下方,一定要有支撑柱SUP8.3热流道系统模具中,母模板背后偷空部分亦应多布置SUP对分流板及母模板进行支撑,由于此处注射压力极高,变形可能性极大.8.4在公模侧枕板之间务必要尽量有针对性的布置SUP,且保证公模的底部各个部位都有所支撑.8.5在模具比较小的情况下,布置大的SUP要注意不能够减弱顶出板的强度,防止顶了, 板由于SUP的偷孔太大太多而被损坏.9.入子拆法:9.1拆入子的目的.割成几个模块进行同步加工.如图10所示,那幺如何对其进行分割呢,考虑方面如下.✧总体成型型腔区域的高度,将其有界分开备料不可能浪费.比如说“入子1”的整个成型区域象“山区”.而“入子3”的成型区域象平原,海拔相差很大,如今则能够无条件分割,而且对水路的操纵较有益.不可能由于水路离成型面太远而力不能及.✧成型型腔有较深的筋,从易加工性出发,也务必将筋处模仁分割,比如: “入子6”上有许多排加强筋,若作为自然模后,务必以较慢速度的放电加工,而拆成入子则能够单独取出,以较快的磨床加工为工艺,绝对事半功倍.再比如: “入子2”与“入子3”之间有一根较深的加强筋,自然模仁加工时须放电,且电极需要很大一块料(板),费用极高,而拆成两块入子,则能够用侧面铣削加工的方法很快做成.综上所述,分割模仁的基本考虑点应是根据成型面与区筋.注意点:确.积误差.(4)那幺,然,事置宜,请参照图11.另外,如图11中(b),该图标为先端走纸面的筋,在这些筋的端部由于要有走纸作用,因此在成品的表面要求上不可有任何段差,入子线,毛边等成品缺陷.但由于这些走纸面的筋在模具上务必要拆入子才能更顺利地加工出来,成型中拆入子也能更好地排气,不至短射,因此,应务必考虑另外一种特别的入子拆法,如图11(b).保证入子的一侧尖角处留有0.5mm的平面台阶,作强度保证.(5)拆入子的典例(图12)工方法上就有别于贴拆入子之形式,即一个以线割加工,另一个以放电加工,因此,为了选择最富有经济效益的加工,才是设计人员真正考虑的.如图149.4圆入子的防转:在圆入子的头部成型部分为非绝对回转体时,或者入子成型部分为非圆柱形,或者入子成型顶部为斜面等类似的情况,圆入子都务必做成防转性质,这是非常有必要,且容易造成疏忽的方面,如图14中的两个常见的圆入子防转形式.10.模具设计中的注意点10.1当模具的定位环安装在前板,而注道衬套被安装在母模板时,前板与母模板须在模架加工阶段追加定位梢,以保证定位环与注道衬套的对中性.10.2当模具的注道衬套被沉入模具中过深时,须考虑注机之喷嘴能否抵住注道衬套的顶部球面.10.3热流道系统中为保证整个系统安装不损坏,设计人员须在模个的前板,前枕板,母模板之间插入导柱,导套以起安装导向作用;导柱,导套的规格比GP,GB能够小一个规格型号,但不可太小.10.4三板模中,前板与后板厚度须保持一致,以便上机安装,因此通常都需偷肉前板10.5直筒式导套在模具设计时,侧面要有无头螺钉抵紧防滑10.6公,母模板的吊模孔选择时,是建立在起吊整组模具的基础上的而其它各模板上的吊模孔设计只须考虑模板自己重量,另外,在相拼模仁的模具中,设计人员一定要设置各块大模仁的吊模作业孔,包含滑块顶部10.7模具中装有油压缸,并凸出了模具整个外形,须考虑在油压缸四周设计保护杆四根,以防止油缸在作业及运输中损坏.10.8模具设计的总体理念首先:所有的设计安排务必以最终的成型注射为宗旨,保证在最短的成型周期注塑最佳的成品其次:以加工的实际条件出发,考虑零件的可加工性,并尽可能优先使用传统机械加工,有必要时,作回转体零件,这样能够方便其固定部分的钻孔加工.10.9单个零件的尺寸标注,一定要标明:PL面,基准角,入子位置,甚至是加工工艺安排.。
模具基本结构图解

8.在凸出模仁排布頂針需注意其模仁強度之限制.
頂針防轉方式
板與公模板分開.分開到設定距離時停止不動.
3.在脊桿地推動下,頂出板帶動頂出機構(頂針,頂桿,斜稍etc)
開始頂出運動,將成品頂出(自動落下或由機械手取走)
合模過程:當頂出板上有拉回機構時,在合模前,頂出板被注塑機 強制拉回. (1)在注塑機地推動下,公模側向母模側運動,若頂出板沒有 被預先拉回,RP最先接觸母模板,在反作用力下,頂出板在RP 的帶動下回位. (2)公模板壓向母模板和剝料板,最後完全合緊,注塑機上的 噴嘴與模具上的注口襯套密合,開始注塑.
模具基本結構簡介 之三板模
三板模(小水口 DC type)結構形式
三板模(小水口 DC type)運動過程
典型的三板模(小水口 DC type)運動過程:
開模過程:三板模有兩次分型,第一次在剝料板與母模板之間,第 二次在母模板與公模板之間 1.當公模側起初受到注塑機的拉力時,公母模板之間由於裝有開 閉器,而剝料板與母模板之間沒有任何連結和阻礙,(多數情
4.每一套模具頂針直徑尺寸不宜太多種,否則加工時
需頻頻換刀既浪費時間及易出錯
5.頂針孔配合公差模仁孔為(ψXX.XX +0.02,+0.01) ,XY方
向位置度±0.1內即可(見附圖頂管 X.Y 方向位置度公差需在
±0.02-- ±0.05內. 6.頂針在配置時需考慮頂出時力量分佈是否平均成品深度是 否一致若不一致需考慮增方梢在側面咬花或局部增加頂出 7.在排氣不良場所可考慮加頂針以利排氣。例如:十字肋下方
1.拉料梢的作用a.将料头从母模板中脱离;b.在第一次开模时, 拉料梢之倒勾形成上固定板与剥料板分开的阻力 2.设计要点a.在进胶点上方,排布拉拉梢;b.对于料头长或有曲 线变化时,每隔一段距离式在转弯处增加拉料梢
模具结构

进料口 Gate
• 侧进料口 Edge gate
• 直接进料口 Direct gate
• 盘形进料口 Disk gate
• 分流式进料口 Subsprue gate
• 轮辐式进料口 Spoke gate
• 爪形进料口 Clawed gate
点状进料口 Pin-point gate
1.定模板 fixed mould plate; 2.型芯 core; 3.推料板 stripper plate; 4.拉料杆 sprue puller pin; 5.导套 sprue bush; 6.定模固定板 fixed mould clamping plate; 7.顶杆 ejector pin; 8.限位钉 stop pin
保证塑件外观 Assure plastic part's appearance
有利于排气 Parting line to facilitate venting
尽量使塑件留在动模一侧 Parting line to facilitate demolding
保证塑件精度 Parting line to assure plastic part accuracy
模具类型 Mould type
斜导柱抽芯 斜推杆抽芯 高光无痕注塑 螺纹抽芯 定模脱模 热流道系统 叠层模具 双色模具 气体辅助成型模具 Angle pin core-pulling Slanted lifer core-pulling Weldless plastic injection Mould with unscrewing unit
分流道 Runner 平衡式分流道 Balanced runner
• 辐射式 Radiate
模具基本结构及分类
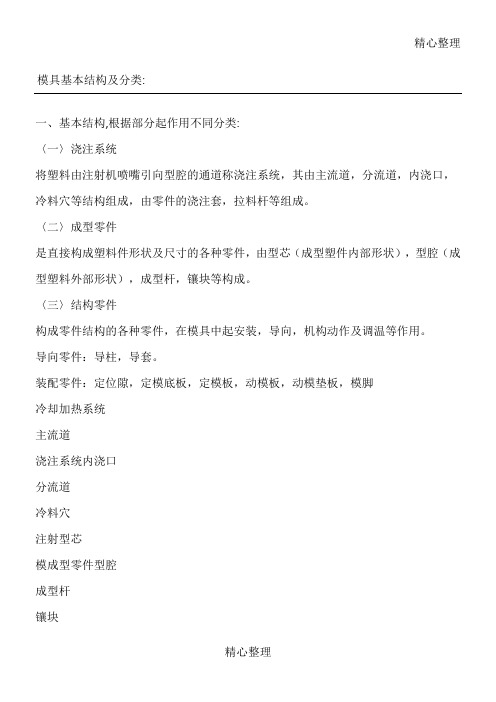
它是指构成模具结构的各种零件,包括:导向、脱模、抽芯以及分型的各种零件。如前后夹板、前后扣模板、承压板、承压柱、导向柱、脱模板、脱模杆及回程杆等。
1.导向部件
为了确保动模和定模在合模时能准确对中,在模具中必须设置导向部件。在注塑模中通常采用四组导柱与导套来组成导向不见,有时还需在动模和定模上分别设置互相吻合的内、外锥面来辅助定位。
4.浇口
它是接通主流道(或分流道)与型腔的通道。通道的截面积可以与主流道(或分流道)相等,但通常都是缩小的。所以它是整个流道系统中截面积最小的部分。浇口的形状和尺寸对制品质量影响很大。
浇口的作用是:
A、控制料流速度:.
B、在注射中可因存于这部分的熔料早凝而防止倒流:
C、使通过的熔料受到较强的剪切而升高温度,从而降低表观粘度以提高流动性:
浇注系统是指塑料从射嘴进入型腔前的流道部分,包括主流道、冷料穴、分流道和浇口等。成型零件是指构成制品形状的各种零件,包括动模、定模和型腔、型芯、成型杆以及排气口等。典型塑模结构如图示。
一.浇注系统
浇注系统又称流道系统,它是将塑料熔体由注射机喷嘴引向型腔的一组进料通道,通常由主流道、分流道、浇口和冷料穴组成。它直接关系到塑料制品的成型质量和生产效率。
2.推出机构
在开模过程中,需要有推出机构将塑料制品及其在流道内的凝料推出或拉出。推出固定板和推板用以夹持推杆。在推杆中一般还固定有复位杆,复位杆在动、定模合模时使推板复位。
3.侧抽芯机构
有些带有侧凹或侧孔地塑料制品,在被推出以前必须先进行侧向分型,抽出侧向型芯后方能顺利脱模,此时需要在模具中设置侧抽芯机构。
2、点浇口脱出模具(三板式模具)
3、带横向轴芯的分型模具
4、自动卸螺纹注射成型模具
- 1、下载文档前请自行甄别文档内容的完整性,平台不提供额外的编辑、内容补充、找答案等附加服务。
- 2、"仅部分预览"的文档,不可在线预览部分如存在完整性等问题,可反馈申请退款(可完整预览的文档不适用该条件!)。
- 3、如文档侵犯您的权益,请联系客服反馈,我们会尽快为您处理(人工客服工作时间:9:00-18:30)。
第二节模具的整体结构布局
1.成品的收缩率
1.1它是成品冷却后的收缩量与冷却前在模型内之尺寸的比值.这个比值是经常会发生变化的,可以产生收缩率有所浮动的因素有:原料品种,成型保压时间,模具温度,室内温度……,所以设计人员在设计模具型腔的具体尺寸时,应搞清正常条件下的原料收缩率是最最重要的,否则,当收缩率取错,基本上将要重新更改模仁,那幺,收缩率在设计的过程如何应用呢?最主要的还是利用收缩率来计算.
模具型腔的尺寸,即: 模具尺寸=成品尺寸*(1+收缩率)
而另外一种算法应用极少,即: 模具尺寸=成品尺寸/(1-收缩率) 而各种原料的收缩率请参考第八章 “成型部分”附表
1.2长条形成品的收缩率如何确定:长条形成品在扣收缩率时,在宽度方向和长度方向是肯定有出入的,即可能是宽度尺寸收缩率放5%0,而长度方向则为 3.5%0,这样的例子.但究竟如何面对这些不定因素,我们还需要从实际积累经验,从现实的角度考虑,在此无法论证抱歉.
2.一模多腔如何布置:
在现行的模具设计过程中,由于客户对成品的品质及精度要求日益增高,所以,大批量生产如一模十穴,
内).因为从理论出发,在常用的多穴布置时,图1中.(1*2和1*4)的背后,一个不到位.填充较满.
按键的进浇系统,一点,圆弧流道之成功的实例.
3.模具的模仁尺寸确定:
子说明,如图2.图中母仁CA V
取值是绝对不可取的.而公仁COR部分,也要根据实际情况计算模仁的最佳尺寸,那幺如何对模仁的边界进行尺寸取值呢?须注意以下几点:
3.1考虑成品的总体高度若成品高度尺寸不是太大,则母仁CA V部分
的边缘厚度尺寸只须达到封闭熔体塑料即可.一般为15~30mm.
查表定值,当然,这一尺寸还要考虑水路布置及螺钉部分.若成品
这两种方法如何相辅相承地灵活应用呢?要现场所决定,建议第二种
方法行事.
在模仁的宽度确定了,可以试比较的方法来选择不同的模架,基本上当CA V或COR,并同模仁压块之最大投影宽度在顶出板的宽度范围就可以了.若要跑滑块或所遇母模型腔特别深之特殊情况,可以据实追加模架宽度.
另外,模架高度方面主要是母模和公模本体板及枕板部分的厚度,母模本板厚度主要考虑加工时不变形就可以了.如果母模板中模仁穴过深,一般情况下,母模板底部厚度为30~80mm即可.公模本体板厚度可以为公模仁PL面以下高度的3倍.公模仁的PL面以下厚度与本体板底部厚度比值为1/2关系.
枕板高度,视成品的需要顶出量而定,其它无影响因素.
还有一点要注意,许多人对简易三板模和规范三板模的应用场合还不是特别明确,在此简单说明.
简易三板模比规范三板模的结构上少了四根GP导柱,简易三板模的公,母模之间的合模导向完全是通过LP(即前板导柱)控制,而LP一般相当长.再利用其头部导向公,母模合模,必然容易失稳,在模具型腔内部,若靠破,斜破或合模时滑动的组件或部位较多时,容易碰伤.所以,就必须利用规范三板模的GP(4*)来对公,母模的合模进行导向.当然,所有GP的高度不用过高,只需GP头部高出公模仁最高点1.5倍的GP直径就可以了.目的是为让公仁部进入母仁内腔之前就开始导向合模.GP的导套,在过分厚的模板中是不需要从上通到下的,实际起到作用的只有2/3的板厚即可.如图2所示.
5.直束子与斜束子的区别:
以前,许多说法认为直束子没有斜束子的定位精度高,这从现在的角度出发,是不完全也是不根本的讲法,因为光用斜束子的模具比起光用直束子的模具而言,在插破处易产生毛边的依旧有毛边.那幺,现在如何正确选用这两种束子呢?
5.1直束子:它是一对束块保持垂直面束紧关系的装置, 垂直面的配
合高度就决定了定位作用的长度,即运用了直束子的模具在合模合紧之前就产生了一段距离的公,母模相对定位,完全不会使模腔内插破角度小(0.5°)的斜面切伤.所以,据以上情况,直束子并不是只可以运用在公,母面无滑块机构的情况下,而是被应用在所有有较多插破关系成型的各类机构模具中,主要是内部结构成品模具中.
盖,及掀盖,在采用肓形浇口进浇口产生了溢料,浇口附近注射压力太大.
8.2靠破,插破面的正下方,一定要有支撑柱SUP
8.3热流道系统模具中,母模板背后偷空部分亦应多布置SUP对分流
板及母模板进行支撑,因为此处注射压力极高,变形可能性极大.
8.4在公模侧枕板之间必须要尽量有针对性的布置SUP,且保证公模
的底部各个部位都有所支撑.
8.5在模具比较小的情况下,布置大的SUP要注意不可以减弱顶出板
的强度,防止顶了, 板由于SUP的偷孔太大太多而被损坏.
9.入子拆法:
9.1拆入子的目的.
✧ 总体成型型腔区域的高度,将其有界分开备料不会
浪费.比如说 “入子1”的整个成型区域象 “山
区”.而 “入子3”的成型区域象平原,海拔相差很
大,此时则可以无条件分割,而且对水路的控制较有
益.不会因为水路离成型面太远而力不能及.
✧ 成型型腔有较深的筋,从易加工性出发,也必须将筋
处模仁分割,比如: “入子6”上有许多排加强筋,
若作为自然模后,必须以较慢速度的放电加工,而拆
成入子则可以单独取出,以较快的磨床加工为工艺,
绝对事半功倍.再比如: “入子2”和 “入子3”之
间有一根较深的加强筋,自然模仁加工时须放电,且
电极需要很大一块料(板),费用极高,而拆成两块入
子,则可以用侧面铣削加工的方法很快做成.
综上所述,分割模仁的基本考虑点应是根据成型面和区
指筋.
注意点:确.积误差.
(4) 那幺,然,事置宜,请参照图11.
另外,如图11中(b),该图标为先端走纸面的筋,在这
些筋的端部因为要有走纸作用,所以在成品的表面要
求上不可有任何段差,入子线,毛边等成品缺陷.但由
于这些走纸面的筋在模具上必须要拆入子才能更顺利
地加工出来,成型中拆入子也能更好地排气,不至短射,所以,应必须考虑另外一种特别的入子拆法,如图
11(b).保证入子的一侧尖角处留有0.5mm的平面台阶,作强度保证.
(5)拆入子的典例(图12)
入子之形式,即一个以线割加工,另一个以放电加工,所以,为了选择最富有经济效益的加工,才是设计人员真正考虑的.如图
14
9.4圆入子的防转:
在圆入子的头部成型部分为非绝对回转体时,或入子成型部分为非圆柱形,或入子成型顶部为斜面等类似的情况,圆入子都必须做成防转性质,这是非常有必要,且容易造成疏忽的方面,如图14中的两个常见的圆入子防转形式.
10.模具设计中的注意点
10.1当模具的定位环安装在前板,而注道衬套被安装在母模板时,前
板与母模板须在模架加工阶段追加定位梢,以保证定位环与注道衬套的对中性.
10.2当模具的注道衬套被沉入模具中过深时,须考虑注机之喷嘴能否
抵住注道衬套的顶部球面.
10.3热流道系统中为保证整个系统安装不损坏,设计人员须在模个的
前板,前枕板,母模板之间插入导柱,导套以起安装导向作用。
导柱,导套的规格比GP,GB可以小一个规格型号,但不可太小. 10.4三板模中,前板与后板厚度须保持一致,以便上机安装,所以一般都需偷肉前板
10.5直筒式导套在模具设计时,侧面要有无头螺钉抵紧防滑
10.6公,母模板的吊模孔选择时,是建立在起吊整组模具的基础上的
而其它各模板上的吊模孔设计只须考虑模板自己重量,另外,在相拼模仁的模具中,设计人员一定要设置各块大模仁的吊模作业孔,包括滑块顶部
10.7模具中装有油压缸,并凸出了模具整个外形,须考虑在油压缸四
周设计保护杆四根,以防止油缸在作业及运输中损坏.
10.8模具设计的总体理念
首先:所有的设计安排必须以最终的成型注射为宗旨,保证在最短的成型周期注塑最佳的成品
其次:以加工的实际条件出发,考虑零件的可加工性,并尽可能优先采用传统机械加工,有必要时,作回转体零件,这样可以方便其固定部分的钻孔加工.
10.9单个零件的尺寸标注,一定要标明:PL面,基准角,入子位置,甚至
是加工工艺安排.。