紧固螺栓开裂原因分析
螺栓断裂分析报告

螺栓断裂分析报告1. 引言螺栓是一种常见的连接元件,广泛应用于工程领域。
然而,在使用过程中,螺栓的断裂可能会导致严重的安全事故和设备损坏。
因此,对螺栓的断裂原因进行分析非常重要。
本文将介绍螺栓断裂的分析步骤,以帮助读者更好地了解螺栓断裂的原因,并提供相应的解决方案。
2. 分析步骤螺栓断裂分析通常可以按照以下步骤进行:2.1 收集断裂螺栓样本首先,需要收集断裂的螺栓样本。
这些样本应来自不同的工程项目,并涵盖不同的工作条件。
收集足够数量的样本有助于得出准确的结论。
2.2 观察断口形貌通过对断裂螺栓的断口形貌进行观察可以初步判断断裂的原因。
断口形貌可以分为韧性断口、脆性断口等。
韧性断口常常表明螺栓断裂是由于受到超负荷载荷所致,而脆性断口则意味着存在其他问题。
2.3 进行金相分析金相分析是一种常用的分析方法,通过对螺栓样本进行金相薄片制备和观察,可以获得螺栓的组织结构信息。
通过金相分析,可以检测到螺栓材料中的缺陷、夹杂物、氧化层等问题。
2.4 进行力学性能测试力学性能测试是评估螺栓质量的重要手段。
通过对螺栓样本进行拉伸试验、硬度测试等,可以了解螺栓的强度、韧性等性能参数。
与标准数值进行对比,可以判断螺栓是否达到设计要求。
2.5 考虑工况因素分析断裂螺栓时,还需要考虑螺栓所处的工作条件。
例如,工作温度、湿度、振动等因素都可能对螺栓的性能产生影响。
通过分析工况因素,可以找到与断裂相关的潜在问题。
2.6 结果分析与解决方案综合以上分析结果,可以得出螺栓断裂的原因。
根据不同的原因,提出相应的解决方案。
例如,如果断裂原因是由于材料质量问题,可以优化材料制备过程;如果是由于超负荷导致断裂,则需要对工作负荷进行合理评估等。
3. 结论螺栓断裂分析是一项复杂的工作,需要综合考虑多个因素。
通过对断裂螺栓样本的观察、金相分析、力学性能测试以及考虑工况因素,可以准确判断螺栓断裂的原因,并提出相应的解决方案。
对螺栓断裂问题的分析与解决不仅可以提高工程项目的安全性,还能为相关领域的研究提供参考。
螺栓断裂

螺栓断裂原因分析2010/10/28 17:22:07螺栓断裂分析的方法及程序在紧固件的失效分析中,螺栓的失效最多、也最为常见,而螺栓的断裂失效则占螺栓失效的80%左右,严重威胁着整个构件的安全。
因此,我们有必要、也必须对断裂螺栓进行分析。
由于螺栓的结构、形状和受力形式比较复杂,且在材料、工艺和使用状况等因素的影响下,经常发生各种形式的断裂失效。
由于螺栓种类多、用量大,普遍采用冷变形制造工艺,并依据各种不同性能要求而采用不同钢材和热处理工艺,同时进行严格的材料和工艺检查。
尽管如此,往往由于工艺管理和控制不善,构成了批量或频次较高的断裂失效,经常影响着正常生产和使用。
下面我们就谈谈紧固件断裂失效分析的方法。
紧固件断裂失效分析的方法一、系统方法系统方法,又称相关性方法,就是把失效分析类型、失效方式、断口特征形貌、工作条件、材质情况、制造工艺水平和过程、使用和维护情况等放在一个研究系统中,从总体上予以考虑的方法。
寻找失效原因应从设计、材质、制造、使用、维护等相关方面去考虑,并据此进行测试和分析,找出失效原因。
本方法的特点是:从一般到个别,从普遍到特殊,从单项分析到综合联系上找原因。
这就是尽可能地收集与全局有关的资料和测试信息,从而确定分析系统的范围。
该方法主要针对失效原因复杂的断裂螺栓。
二、抓主要矛盾方法在紧固件失效分析时要抓住失效中起主要作用的因素。
如在断裂失效中就一定要对断裂源、断裂形状及导致断裂的因素重点分析和研究。
这也是我们螺栓断裂失效分析中最常用的方法。
举例来说,当一个螺栓断裂件送到我们手上,我们发现该螺栓的支撑面的装配痕迹不对称(就是说一边有明显的装配痕迹而一边没有或者两边装配痕迹相差很大)。
我们都知道:力是造成痕迹的唯一原因,接下来我们就应对这一应力进行重点分析。
三、比较方法选择一个同批次,同服役状态而没有失效的螺栓与断裂螺栓一一对比,然后进行分析比较,从中找出差异,寻找出引起失效的原因。
紧固件螺栓断裂常见原因分析

紧固件螺栓断裂的原因有多种多样,归纳来说,一般螺栓的损坏由应力因数、疲劳、腐蚀和氢脆等原因形成。
1、应力因数超过常规应力(超应力)由剪切、拉伸、弯曲和压缩中的任一个或其组合而产生。
大多数设计人员首先考虑的是拉伸负荷、预紧力和附加实用载荷的组合。
预紧力基本是内部的和静态的,它使接合组件受压。
实用载荷是外部的,--般是施加在紧固件上的循环(往复)力。
拉伸负荷试图将接合组件抗开。
当这些负荷超过螺栓的屈服极限时,螺栓从弹性变形变为塑性区,导致螺栓永久变形,因此在外部负荷除去时不能再恢复原先的状态。
类似原因,如果螺栓上的外负荷超过其极限抗拉强度,螺栓将断裂。
螺栓拧紧是靠预紧力扭转得来的。
在安装时,过量的扭矩导致超扭矩,同时也使紧固件受到了超应力而降低了紧固件的轴向抗拉强度,即在连续扭转的螺栓与直接受张力拉伸的相同螺栓相比,屈服值比较低。
这样,螺栓有可能在不到相应标准的最小抗拉强度时就出现屈服。
扭转力矩大可以使螺栓预紧力增大.使接合松弛相应减少。
为了增加锁紧力,预紧力一般采取上限。
这样,除非屈服强度和极限抗拉强度之间差异数目很小,一般螺栓不会因扭转而出现屈服现象。
剪切负荷对螺栓纵轴方向施加一个垂直的力。
剪切应力分为单剪应力和双剪应力。
从经验数据来讲,极限单剪应力大约是极限抗拉应力的65%。
许多设计人员优选剪切负荷,因为它利用了螺栓的抗拉和抗剪强度,它主要起类似销钉的作用,使受剪切的紧固件形成相对简单的联接.缺点是剪切联接使用范围小而且剪切联接不能经常使用,因其要求更多的材料和空间。
我们]知道,材料的组成成分和精度也起一定的决定性。
但是,将抗拉应力转换成剪切负荷的材料数据往往却是得不到的。
紧固件预紧力影响剪切联接的整体性。
预紧力越低,在与螺栓接触时接合层越易滑动。
剪切负荷能力通过乘以橫平面数计算(一个剪切平面通称单剪,两个剪切平面通称双剪),这些平面应该是无螺纹螺栓的横截面。
我们不提倡设计通过螺纹的剪切,因为紧固件的剪切强度可在横截面变化时被应力集中克服。
螺栓断裂原因分析

螺栓断裂原因分析螺栓的抗拉强度比想象中强得多,以一只M20×80的8.8级高强螺栓为例,它的重量只有0.2公斤,而它的最小拉力载荷是20吨,高达它自身重量的十万倍,一般情况下,我们只会用它紧固几十公斤的部件,只使用它最大能力的千分之一。
即便是设备中其它力的作用,也不可能突破部件重量的千倍,因此螺栓的抗拉强度是足够的,不可能因为螺栓的强度不够而损坏。
很多螺栓断裂的最终分析认为是超过螺栓的疲劳强度而损坏,但是螺栓在横向振松实验中只需一百次即可松动,而在疲劳强度实验中需反复振动一百万次才会损坏。
换句话说,螺栓在使用其疲劳强度的万分之一时即松动了,我们只使用了螺栓能力的万分之一,所以说螺栓的损坏也不是因为螺栓疲劳强度。
静态紧固用螺栓很少会自行松动,也很少出现断裂情况。
但是在冲击,振动,变载荷情况下使用的螺栓就会出现松动和断裂的情况。
所以我认为螺栓损坏的真正原因是松动。
螺栓松动后,螺纹和连接件之间产生微小间隙,冲击和振动会产生巨大的动能mv^2,这种巨大的动能直接作用于螺栓,受轴向力作用的螺栓可能会被拉断。
受径向力作用的螺栓可能会被剪断。
因此设计时,对于关键的运动部位的连接紧固要注意防松设计。
自锁螺母尼龙锁紧螺母以上为两种形式的锁紧螺母。
对于弹簧垫片的放松效果,一直存在争议。
弹簧垫圈的放松原理是在把弹簧垫圈压平后,弹簧垫圈会产生一个持续的弹力,使螺母和螺栓连接副持续保持一个摩擦力,产生阻力矩,从而防止螺母松动。
同时弹簧垫圈开口处的尖角分别嵌入螺栓和被连接件的表面,从而防止螺栓相对于被连接件回转。
以M16螺栓连接为例,实验显示用约10N.m的螺栓预紧力矩就可以将16弹簧垫圈完全压平。
弹簧垫圈只能提供10N.m的弹力,而10N.m的弹力对于280N.m的螺栓预紧力矩来说可以忽略,其次,这么小的力,不足以使弹簧垫圈切口处的尖角嵌入螺栓和被连接件表面。
折卸后观察,螺栓和被连接件表面都没有明显的嵌痕。
所以,弹簧垫圈对螺栓的防松作用可以忽略。
螺栓受力检测及断螺栓分析

螺栓受力检测及断裂分析目录一、现场螺栓断裂问题描述二、螺栓断裂可能原因分析及测试依据三、测试系统介绍及标定四、现场机组螺栓测试五、数据分析六、现场螺栓测试时发现的问题及注意事项七、螺栓断裂分析注意事项及案例分享二、螺栓断裂可能原因分析及测试依据1、螺栓断裂可能原因1.1螺栓质量问题现场更换过多批次螺栓,且将部分螺栓送检过,未发现螺栓质量存在问题,故此种可能情况基本可以排除。
1.2螺栓脆性断裂1)氢脆断裂的典型特征是纤维性断口,且断口比较平整,见图1。
根据现场查看螺栓断口特征,机组断裂螺栓亦不符合氢脆断裂。
2)螺栓疲劳断裂的典型特征是存在贝纹状疲劳线,沿着疲劳弧线发展的逆向,可以找到裂纹源,见图2,现场机组断裂螺栓符合这一特征。
图1 纤维性断口图2 贝纹性断口2、螺栓测试依据螺栓疲劳断裂主要与螺栓连接受载时的应力幅值有关,所以此次螺栓测试主要测试螺栓的应力幅值的变化。
应力幅:Fmax:机组工作时螺栓受到的最大拉力;Fmin:机组工作时螺栓受到的最小拉力;As :螺纹公称应力截面积。
此次螺栓测试所携带设备,可将机组在工作时螺栓所受轴向拉力时时进行记录,从而得到机组工作时偏航轴承与底座联接螺栓的应力幅值。
通过螺栓频繁断裂机组螺栓应力幅值与未断裂机组螺栓应力幅值相比较,为后续仿真建模提供测试依据,找出螺栓断裂的真正原因。
1、测试系统组成(见图3)图3三、测试系统介绍及标定用户K值计算:用户K值计算的目的主要是确定力与应变间的对应关系。
HBM‐KMR拉力传感器灵敏度为1.7MV/V~2.3MV/V,取中间值为2mV/V,由于系统激励电压为2V,故该系统满量程为4mV。
1)满量程与电压对应关系:Ain=400KN/4mV=100KN/mV=0.1KN/μν。
2)无线应变节点的灵敏度F=1μν/με。
(注:无线应变节点可测量毫伏信号,但是显示的最小刻度值为με,而且系统给出了灵敏度F=1μν/με,所以需要转化为μν)3)此时传感器最小分辨电压能力为K0,K0=0.17481。
螺栓断裂分析报告

螺栓断裂分析报告一、引言螺栓是一种常见的连接元件,在机械设备和结构工程中得到广泛应用。
然而,螺栓在使用中可能会发生断裂,给机械设备和结构的安全运行带来隐患。
本报告旨在对螺栓断裂进行分析,并提供解决方案,以确保设备和结构的安全性。
二、螺栓断裂原因分析1.质量问题:螺栓断裂可能是由于螺栓本身存在质量问题所致,如材料强度不符合标准、制造工艺不良等。
为此,应关注螺栓的采购渠道和制造工艺,并严格按照相关标准进行选择和检测。
3.腐蚀问题:腐蚀是导致螺栓断裂的常见原因之一、在潮湿、酸性或碱性环境中,螺栓易受到腐蚀,使其材料的强度降低。
因此,在腐蚀环境中应选择抗腐蚀性能良好的螺栓材料,并进行定期维护保养。
4.紧固力不均匀:不正确的紧固力分布可能导致螺栓在负载过程中承受不均匀的力,从而引发断裂。
在安装过程中,应根据设备或结构的要求,采用正确的紧固力分布方案,并进行定期检查和调整。
三、螺栓断裂的解决方案1.优化选材:根据设备或结构的负荷、工作环境等要求,选择合适的螺栓材料。
关注材料的强度、韧性、抗腐蚀性等指标,并遵循标准进行选材。
2.合理设计螺栓连接:根据实际负荷情况和工作要求,合理选用螺栓的规格、数量和布置方式,并确保紧固力的均匀分布。
在设计过程中,可以借助有限元分析等工具来验证螺栓连接的安全性。
3.定期检查和维护:对于暴露在恶劣环境中的螺栓,应定期进行检查和维护,特别是针对腐蚀环境。
清洁螺栓表面,涂覆抗腐蚀涂层,必要时更换受损螺栓,以延长其使用寿命。
4.强化管理和培训:通过建立规范的螺栓管理制度和培训机制,提高操作人员的专业水平,加强螺栓使用和维护的知识宣传,以减少螺栓断裂的发生。
四、结论螺栓断裂是机械设备和结构工程中常见的问题,但可以通过合理选材、优化设计、定期维护和加强管理来减少其发生。
对于已经断裂的螺栓,应及时进行更换,并对其断裂原因进行调查分析,以避免类似问题再次发生。
通过以上措施的综合应用,能够提高螺栓连接的安全性和可靠性,保证设备和结构的正常运行。
关于螺栓产生的问题的短篇

关于螺栓产生的问题及分析
一、螺栓松动
问题描述:螺栓在紧固后,经过一段时间或振动后,出现松动现象,导致连接部位出现间隙或产生移位。
原因分析:
1. 螺栓与螺母之间的摩擦系数不够,导致自锁能力不足。
2. 紧固时未使用合适的工具或方法,导致预紧力不足或预紧力不均匀。
3. 螺栓与被连接件之间的振动或冲击,导致螺栓松动。
解决方案:
1. 使用摩擦系数较高的螺母或添加垫片来增加摩擦力。
2. 使用合适的工具进行紧固,确保预紧力均匀且足够大。
3. 在连接部位增加防松装置,如弹簧垫圈、止动垫圈等。
二、螺栓断裂
问题描述:螺栓在受力或振动后,发生断裂现象,导致连接失效。
原因分析:
1. 螺栓材料存在缺陷,如夹杂物、气孔等。
2. 螺栓制造工艺不当,如热处理不当、机械加工过度等。
3. 螺栓受力过大或疲劳损伤,导致应力集中部位发生断裂。
4. 螺栓装配时受到损坏或碰撞。
解决方案:
1. 使用合格的材料,确保材料质量符合要求。
2. 严格控制制造工艺,确保螺栓质量稳定可靠。
3. 根据受力情况选择合适的螺栓规格和材料。
4. 确保装配时螺栓不受损坏或碰撞。
5. 加强定期检查和维护,及时更换受损螺栓。
三、螺栓腐蚀
问题描述:螺栓在使用过程中受到腐蚀,导致连接部位失效或产生安全隐患。
原因分析:
1. 螺栓材料不耐腐蚀,如普通碳钢螺栓在潮湿环境中容易生锈。
紧固件断裂失效类型及原因分析

紧固件断裂失效类型及原因分析前言机器或钢结构件是由许多个零件和部件组成,这些零件和部件绝大部分是通过螺纹紧固件连接在一起的。
一旦紧固失效将造成机器失灵,严重者甚至出现人员伤亡事故。
由于紧固失效的常见性和潜在的严重性,所以我们应认真仔细地分析并找出紧固失效的原因,采取纠正措施,以杜绝紧固失效的发生。
紧固失效有两种,一种是螺栓断裂,被紧固零件瞬间分离,这种失效往往会造成严重的后果;还有一种是螺纹副松动和螺栓或螺母滑牙,被紧固零件出现一定范围的相互位移,造成机器部分功能失常。
人们发现,及时采取措施可以避免事故的发生。
如因未发现任其继续发展,螺栓和螺母终将分离,同样会引发重大安全事故。
紧固失效后直观现象是螺栓断裂或螺母与螺栓分离,因此人们一般认为螺栓断裂是螺栓质量有问题,螺母松动是螺母质量不好。
大家往往忽略了设计和安装中的问题。
一、剪切断裂剪切断裂出现在螺栓只受预紧力的连接中(见图1)。
剪切断口出现在螺栓杆部,位于两个被紧固零件的结合面处(见图1),断口有小面积的平整光亮剪切面。
出现剪切断裂有下列原因:图1 图21、设计原因⑴被紧固零件的结合面间摩擦系数太小或螺栓规格不够大造成预紧力F'不够,即:fF'<F ( f-结合面间的摩擦系数 )此时结合面间摩擦力小于横向工作载荷F,被紧固零件出现相对滑移,螺栓承受孔壁的挤压,当挤压力足够大时螺栓被剪切断。
在运动部件上因冲击力更大,所以出现的可能性也更大。
为了避免这种现象的发生,在设计上可以采用减载件和台阶来承受横向载荷,使螺栓仅起纯连接作用(见图2)。
⑵在振动工作环境下工作零件的紧固,未采用具有防松功能的紧固件。
在工作一段时间后,紧固件螺纹副出现松动,螺栓夹紧力(预紧力F')下降,此时也将发生上述同样的结果。
为了避免因松动而造成紧固失效,设计时应采用具有防松功能的紧固件,如美国施必牢防松螺母、有效力矩螺母。
2、装配原因装配时预紧扭矩过小,造成预紧力不够,即F'小,出现上述同样的结果。
螺栓断裂分析课件

7
2 分析与讨论
(1)螺栓断口无明显的宏观塑性变形,裂纹扩展区面积较大,且较平整, 有明显的疲劳弧线,瞬断区面积较小,结合35CrMo螺栓的工作状态可 以判断,该螺栓的断裂性质为低应力疲劳断裂。
(2)经裂纹宏观与微观形貌观察,发现几乎每个螺纹牙底都分布着细长的 热处理裂纹。裂纹开口端较宽,尾部细长曲折,呈沿晶断裂,为典型的热处 理裂纹形貌。
螺栓断裂分析
9
螺栓断裂分析
10
螺栓断裂分析
图7 螺栓心部的显微组织
6
另外在螺纹的表面也发现了如图8所示的不光滑起皮 现象,截取端面研磨后置于光学显微镜下观察,发现在如 图9中箭头所指处的螺纹表面存在大量 折叠缺陷。折叠缺 陷是由于螺纹表层在滚压过程中受到挤压力而产生的重叠 层。
图8 螺纹表面的起皮现象
纵剖面热处理裂纹的未侵蚀形貌
图6 沿晶热处理裂纹侵蚀后的形貌
螺栓断裂分析
5
1.3 显微组织及显微硬度检测
螺栓的热处理工艺为调质处理,显 微组织为正常的回火索氏体(图7), 符合调质处理的显微组织状态。回火索 氏体是马氏体的一种回火组织,是铁 素体与粒状碳化物的混合物,具有良好 的韧性和塑性,同时具有较高的强度和 硬度,具备良好的综合力学性能。对螺 栓心部进行维氏硬度检测,检测结果为 411HV,符合相关标准中硬度 > 318HV的要求。
(3)另外发现螺纹表面不光滑,主要是由于螺栓的滚压工艺不当,造成了 折叠、起皮等缺陷所致。
螺栓断裂分析
8
3 结论
35CrMo螺栓的断裂性质为低应力疲劳断裂。该螺栓在 制造过程中由于热处理及滚压工艺不当,造成了大量的裂纹和缺陷, 这些裂纹和缺陷存在很大的应力集中,成为疲劳裂纹源,在循环应 力的作用下裂纹逐渐扩展,最终发生了疲劳断裂。
2Cr13螺栓断裂原因分析

2Cr13螺栓断裂原因分析2Cr13钢属于马氏体不锈钢,淬火后经高温回火处理,该钢具有良好的抗弱腐蚀介质能力和综合力学性能,因而被广泛应用于航空、航天以及船舶等各领域,其中也应用于航天紧固件产品。
开槽圆柱头螺栓,材料牌号为2Cr13,在成检前发现5件杆部存在轴向裂纹,此批螺栓共计366件,现对其中1件开裂螺栓进行原因分析。
该批零件由规格为φ20mm的2Cr13棒材加工制造,其生产工艺流程为:车→铣→钳→热处理→磨→滚丝→清洗→表面处理→试验→成检。
1.试验过程与结果(1)宏观检查开槽圆柱头螺栓开裂宏观形貌如图1所示,可见螺栓表面裂纹沿轴向分布,较平直,裂纹从头部台阶处到螺纹端头,总长约35.1mm,肉眼观察,裂纹深度较浅,螺栓外表面未见明显机械损伤。
图1 开槽圆柱头螺栓开裂宏观形貌(2)金相检查由于螺栓较长,分段截取进行镶嵌试样。
截取开裂螺栓杆部纵截面、横截面进行金相检查,宏观形貌如图2所示。
根据GB/T10561试验方法,对开裂螺栓杆部纵截面进行非金属夹杂评级,A类0.5级,B类2级,C类0级,D类0级,DS0级。
经4 %硝酸酒精水溶液腐蚀后,螺栓头部发现尺寸约(长4.9mm×宽0.6mm)的条带区域(见图2),沿轴向分布,内部为晶粒清晰的等轴晶(见图3),明显区别于基体,且对应于开裂位置的延伸线。
横向截取开裂螺栓螺纹处腐蚀后,开裂位置未见脱碳现象(见图4),条带区深约0.3mm。
基体组织为回火索氏体组织(见图5)。
图2 开裂螺栓杆部截面宏观形貌图3 开裂螺栓纵截面形貌图4 开裂螺栓横截面形貌图5 螺栓正常位置组织(3)能谱分析分别对图3中基体和条带区域进行能谱成分分析(EDS),表1为两区域能谱成分的半定量分析数据。
表1 螺栓基体及条带区域能谱成分(重量百分比)结果(%)位置Fe Cr Mn Si C基体84.2713.700.500.34 1.19条带区域97.05 1.290.470.10 1.09可以看出,基体主要成分为Fe(84.27%)、Cr(13.70%)、Si等元素,主要成分符合Cr13型不锈钢要求。
螺栓断裂分析

螺栓断裂(螺栓头根部断裂,如果是单件估讣是应力集中的原因,断裂批量应是材料或热处理问题。
)
1.拧紧力矩过大(8.8级M8螺栓的介理拧紧力矩在18~23N.m)
2.螺栓根部设计不合理导致了应力集中
3.热处理没有达到要求,,导致硬度过髙,发生脆性断裂。
是否有回火脆性?螺纹处是否有
脱碳组织?
4.材料问题(8.8级螺栓的材质应该是40MnB或者是35CrMOA
5.电镀时如处理不当,容易导致氢的侵蚀,导致氢脆:氢脆断口的特征为:微观准解理面、微孔及韧性的
发丝。
(判断是否为氢脆有个最简单的办法:把样品表而水和油污淸洗干净,
烘干,倒一烧杯石蜡.加热到没有气泡冒出为止.然后把样品放入石蜡中,如果有气泡冒出就说明氢含址高)
6.枪未调好扭距,有冲击,岀现瞬间过载。
7.材料本身就有缺陷(螺栓头杆结合处有微裂纹。
螺栓断裂分析报告

螺栓断裂分析报告摘要:本报告针对螺栓断裂现象进行了详细的分析和研究。
通过对螺栓断裂的原因、影响以及防止措施的探讨,为相关行业的螺栓使用提供了重要的参考。
本报告基于理论分析与实际案例,对螺栓断裂的破坏机理进行了深入剖析,为预防螺栓断裂提供了有益的建议。
1. 引言螺栓断裂是制造行业普遍存在的问题,对设备和生产过程的正常运行产生了严重的影响。
因此,了解螺栓断裂的原因和预防方法对确保设备和工业机械的长期运行至关重要。
2. 螺栓断裂的原因螺栓断裂的主要原因可以归结为以下几点:2.1 载荷过大:超过螺栓设计承载能力的载荷会加剧螺栓的应力,导致螺栓断裂。
2.2 腐蚀和疲劳:螺栓在潮湿或酸碱环境中易受到腐蚀,长期使用和重复加载会引起螺栓疲劳,最终导致断裂。
2.3 不合适的材料选择:选择低强度或不符合工作环境需求的材料使用螺栓,容易导致断裂。
2.4 不当的安装和紧固:螺栓的安装和紧固过程如果不正确,会影响其承载能力,增加螺栓断裂的风险。
3. 螺栓断裂的影响3.1 安全问题:螺栓断裂可能导致设备或机械的故障,对人员和生产环境造成潜在的安全隐患。
3.2 生产中断:螺栓断裂会导致设备停机和生产中断,给企业带来经济损失和生产延误。
3.3 维修和更换成本:螺栓断裂需要进行维修和更换,企业需要承担额外的成本。
4. 螺栓断裂的预防措施4.1 正确的设计和选择:根据工作环境和载荷要求,合理设计和选择螺栓材料和规格。
4.2 适当的安装和紧固:严格按照安装规范进行螺栓的安装和紧固,确保螺栓能够承受设计载荷。
4.3 定期检测和维护:定期检查螺栓的状态,及时发现问题并采取措施修复或更换。
4.4 使用防腐措施:在潮湿或有腐蚀环境的场所使用螺栓时,应采取防腐措施,延长螺栓的使用寿命。
5. 结论通过对螺栓断裂现象进行分析和探讨,我们可以得出以下结论:5.1 正确的设计和选择对于防止螺栓断裂至关重要。
5.2 安装和紧固过程必须按照规范进行,以确保螺栓可以承受设计载荷。
螺纹紧固件失效分析案例(第5部分)

13. 网架螺栓断裂原因分析对一个M39×131的网架螺栓在服役中发生断裂的原因进行分析。
螺栓由40Cr钢制造,并经调质热处理。
一、 外观螺栓断裂处位于杆部的第二个螺扣牙根处。
螺栓断裂部位未见塑性变形,断口有部分锈蚀。
二、 断口图1为螺栓断口的宏观照片。
图1 断口宏观形貌断口可明显分成三个区。
Ⅰ区为无明显花样的光滑区;Ⅱ区为呈海滩花样的条带区;Ⅲ区为最后断裂区——瞬断区,该区平面与螺栓轴线大体呈45°角,属于剪切断裂区。
由断口特征可以判断,螺栓断裂属于弯曲疲劳断裂。
为了更清晰的观察断口三个区的形貌,将三个区进行局部放大观察(图2)Ⅰ区 Ⅱ区(其中白道为滑伤)Ⅲ区图2 断口三个特征区的局部放大形貌8×由照片可见,Ⅰ区为疲劳裂纹萌生及缓慢扩展区。
螺纹在螺纹根部高应力集中区首先诱发裂纹,在周期交变应力的作用下,螺纹反复张合,产生摩擦挤压,因而形成光滑断面。
在该区裂纹起始部位(图中箭头所指),可见大量细小台阶,说明疲劳裂纹的产生是多源的,此系在缺口应力集中时疲劳裂纹产生的典型形貌特征。
Ⅱ区为疲劳裂纹快速扩展区,其形貌特征为有明显的且平行的海滩状前沿线,此系裂纹扩展时周期性伸展与停歇而留下的痕迹。
该区约占断口总面积的2/3。
Ⅲ区为最后断裂区,断口粗糙灰暗。
该区的形成为裂纹扩展至一定程度后(Ⅱ阶段结束),剩余断面不堪承受外力作用,瞬时被拉断的结果。
Ⅰ区和Ⅱ区占整个断口面积的90%以上。
三、 低倍、金相组织1.夹杂图3为螺栓材料中的非金属夹杂物,主要为球状不变形氧化物,评定为3级(GB 10561-1989)。
图3 夹杂物100×2.金相组织螺栓材料的金相组织为调质索氏体+部分断续网状铁素体和针状铁素体(魏氏组织)(图4)。
100× 500×图4 螺栓材料金相组织四、 初步分析意见1.螺栓的断裂属于弯曲疲劳断裂。
螺栓在服役过程中承受了单向弯曲交变应力(或者说双向弯曲交变应力,但其中一侧的应力远大于另一侧)。
螺栓断裂原因及处理方案

查手册,选螺栓
No. 4
金风科技
1、螺栓连接受力形式及预紧力控制
1.3螺栓受力分析
2) 紧联接 (1)只受预紧力F’的紧联接
外载荷FR——对螺栓为横向力——靠摩擦力传递
a. FR作用下,板不滑移:FR≤Ff,而Ff—→F’。 b. 按F’计算: F’为螺栓轴向负荷—→拉应力 c. 拧紧过程中,在T1作用下螺栓受扭—→产生τ T
3/17/2015
No. 14
金风科技
3/17/2015
Mechanical Laod test
3/17/2015
No. 15
金风科技
螺栓断裂原因:机组运行时,螺栓应力幅值过大,现场更换螺栓时未按 要求进行“十”字交叉紧固,造成法兰面间存在间隙。
3/17/2015
Mechanical Laod test
3/17/2015
No. 9
金风科技
3、螺栓断裂原因及案例分析
案例二
某项目现场叶片与轮毂连接螺栓频繁发生断裂,现场检查时发现该位置螺 栓有松动迹象。
3/17/2015
No. 5
金风科技
1、螺栓连接受力形式及预紧力控制
3/17/2015
Mechanical Laod test
3/17/2015
No. 6
金风科技
1、螺栓连接受力形式及预紧力控制
3/17/2015
Mechanical Laod test
3/17/2015
No. 7
金风科技
2、螺栓断裂分析时注意事项
杂、间隙等。 5) 登机检查时注意断裂螺栓位置法兰与螺杆是否存在干涉的情况。 6) 关注同批次多颗螺栓断裂的问题。
3/17/2015
螺丝柱断裂分析报告
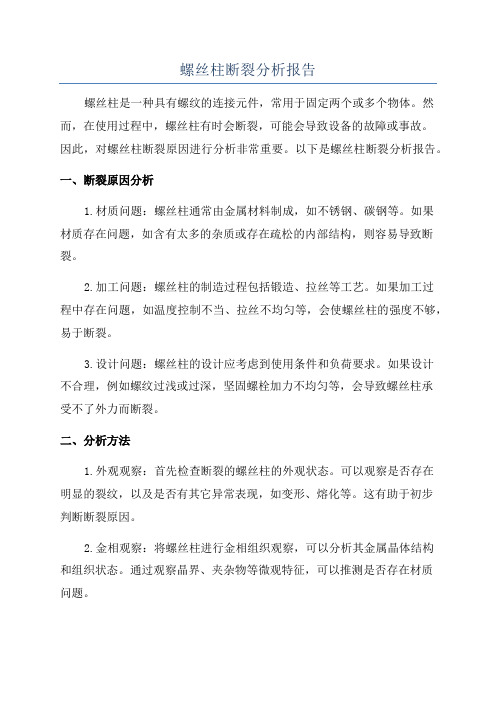
螺丝柱断裂分析报告螺丝柱是一种具有螺纹的连接元件,常用于固定两个或多个物体。
然而,在使用过程中,螺丝柱有时会断裂,可能会导致设备的故障或事故。
因此,对螺丝柱断裂原因进行分析非常重要。
以下是螺丝柱断裂分析报告。
一、断裂原因分析1.材质问题:螺丝柱通常由金属材料制成,如不锈钢、碳钢等。
如果材质存在问题,如含有太多的杂质或存在疏松的内部结构,则容易导致断裂。
2.加工问题:螺丝柱的制造过程包括锻造、拉丝等工艺。
如果加工过程中存在问题,如温度控制不当、拉丝不均匀等,会使螺丝柱的强度不够,易于断裂。
3.设计问题:螺丝柱的设计应考虑到使用条件和负荷要求。
如果设计不合理,例如螺纹过浅或过深,坚固螺栓加力不均匀等,会导致螺丝柱承受不了外力而断裂。
二、分析方法1.外观观察:首先检查断裂的螺丝柱的外观状态。
可以观察是否存在明显的裂纹,以及是否有其它异常表现,如变形、熔化等。
这有助于初步判断断裂原因。
2.金相观察:将螺丝柱进行金相组织观察,可以分析其金属晶体结构和组织状态。
通过观察晶界、夹杂物等微观特征,可以推测是否存在材质问题。
3.化学分析:利用化学分析方法,可以检测螺丝柱的化学成分。
如果发现成分与标准不符,说明可能存在供应商选材问题或杂质引入问题。
4.扫描电镜观察:使用扫描电镜对断裂面进行观察,可观察到断裂面的微观形貌和细节特征。
该方法能够提供螺丝柱断裂的形态和特征,为原因分析提供更精确的依据。
5.扭矩测试:通过在正常使用条件下进行扭矩测试,可以检测螺丝柱的扭矩性能。
如果在测试中发现明显的扭矩异常,可以判断设计或加工问题。
三、预防措施1.材料选择:选择质量可靠,合格标准的螺丝柱材料。
避免采用质量不过关的低价螺丝柱材料。
2.加工控制:确保螺丝柱的制造过程控制到位,温度、拉丝等工艺参数符合标准要求。
3.设计合理:根据实际使用需求,合理设计螺丝柱的尺寸、螺纹参数等。
确保其能够承受正常负荷下的工作要求。
4.检测监控:建立螺丝柱断裂的检测监控机制,定期检查螺丝柱的状态和使用情况,发现异常及时处理。
螺栓断裂原因分析及预防

螺栓断裂原因分析及预防摘要:本文通过对失效螺栓及同批次的零件进行理化分析和无损检测。
对断裂件进行了宏观、微观断口观察、金相组织检查、硬度、化学成分、破坏拉力等一系列试验,经分析找出螺栓失效原因,并提出预防措施。
关键词:螺栓断裂回火脆化螺栓作为飞机上重要的紧固件,其发生断裂危害较大。
我厂修理过程中使用的螺栓主要为M4、M5、M6、M8和M10等规格,然而在某产品装配和停放过程中,某批次30CrMnSiA M8的螺栓先后发生脆性断裂。
引起工厂高度重视,因为螺栓发生脆断,不论是氢脆断裂,还是热处理造成的脆性断裂大都与“批次性”问题有关,涉及数量多,危害大,组织专业人员对螺栓在装配过程中及装配一段时间后发生断裂的原因进行了分析,并对后续的预防工作,提出了建议和方案。
1 宏观、微观检查对断裂螺栓进行宏观观察:发现断裂位置接近于第一扣螺纹处见(图1)。
断裂处螺纹表面未发现有明显的机械接触痕迹,如压坑、啃刀、划伤等表面缺陷,也未发现热处理表面烧蚀痕迹、螺纹变形等现象,没有局部麻点、剥蚀等缺陷。
断裂螺栓螺纹牙底呈线性起源,放射棱线粗大,断口附近无明显宏观塑性变形,断口齐平,呈暗灰色,断面粗糙,具有金属光泽(图2)。
图1断裂螺栓图2螺栓断口图3 螺栓整体形貌对裂纹断口进行观察,断口特征呈现以沿晶为主+韧窝的混合断裂形貌,且断口源区未见冶金和加工等产生的缺陷。
对同批次的螺栓抽样进行了磁粉检测,在螺纹的根部没有发现表面或近表面裂纹,对螺栓进行X射线检测,也没有发现内部缺陷。
同批螺栓见图3。
2 材质检验2.1成份分析抽取同批次的螺栓去掉镀层后制取化学粉末,采用碳、硫联合测定仪对碳、硫含量进行了检测,利用QSN750光谱仪对其它元素进行了检测,结果见(表1),螺栓的化学成分符合技术要求,但含碳量较高。
表1 化学成份检测结果表2.2 金相分析在靠近断口位置切取金相试样,镶嵌、磨抛、腐蚀后,显微镜对试样进行组织观察,螺栓显微组织为较粗大的回火马氏体(图4)。
螺栓断裂的原因分析及预防措施
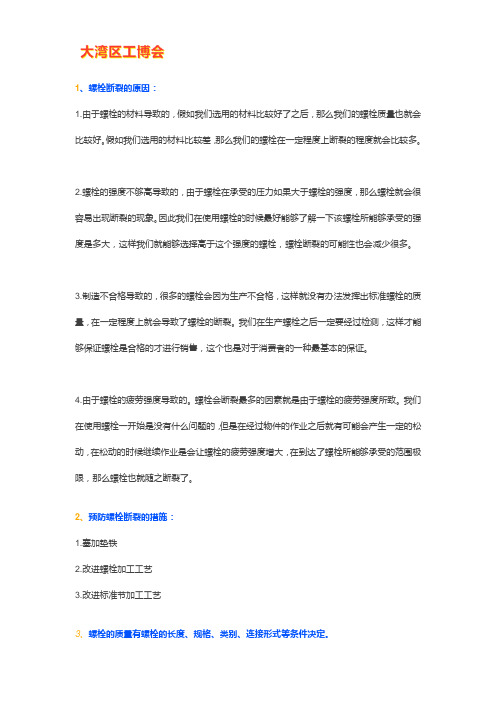
1、螺栓断裂的原因:1.由于螺栓的材料导致的,假如我们选用的材料比较好了之后,那么我们的螺栓质量也就会比较好。
假如我们选用的材料比较差,那么我们的螺栓在一定程度上断裂的程度就会比较多。
2.螺栓的强度不够高导致的,由于螺栓在承受的压力如果大于螺栓的强度,那么螺栓就会很容易出现断裂的现象。
因此我们在使用螺栓的时候最好能够了解一下该螺栓所能够承受的强度是多大,这样我们就能够选择高于这个强度的螺栓,螺栓断裂的可能性也会减少很多。
3.制造不合格导致的,很多的螺栓会因为生产不合格,这样就没有办法发挥出标准螺栓的质量,在一定程度上就会导致了螺栓的断裂。
我们在生产螺栓之后一定要经过检测,这样才能够保证螺栓是合格的才进行销售,这个也是对于消费者的一种最基本的保证。
4.由于螺栓的疲劳强度导致的。
螺栓会断裂最多的因素就是由于螺栓的疲劳强度所致。
我们在使用螺栓一开始是没有什么问题的,但是在经过物件的作业之后就有可能会产生一定的松动,在松动的时候继续作业是会让螺栓的疲劳强度增大,在到达了螺栓所能够承受的范围极限,那么螺栓也就随之断裂了。
2、预防螺栓断裂的措施:1.塞加垫铁2.改进螺栓加工工艺3.改进标准节加工工艺3、螺栓的质量有螺栓的长度、规格、类别、连接形式等条件决定。
4、螺栓的预紧力矩使得螺栓受到拉应力、剪应力两种力,而预紧力的控制是为了保证法兰连接系统紧密不漏、安全可靠地长周期运行,垫片表面必须有足够的密封比压,特别在高温工况下垫片会产生老化、蠕变松弛,法兰和螺栓产生热变形,因此高温连接系统的密封比常温困难得多,此时螺栓预紧力的施加与控制就显得十分重要,过大或过小的预紧力都会对密封产生不利影响。
螺栓预紧力过大,密封垫片会被压死而失去弹性,甚至会将螺栓拧断;过小的螺栓预紧力又使受压后垫片表面的残余压紧应力达不到工作密封比压,从而导致连接系统泄漏。
因此如何控制螺栓预紧力是生产实际中必须重视的问题。
5、螺栓的抗拉强度和屈服强度决定了螺栓的强度,强度越大,通常寿命越大。
螺栓断裂文档

螺栓断裂引言螺栓是一种常用的紧固件,广泛应用于各个领域,如机械制造、建筑工程、汽车制造等。
然而,螺栓的断裂是一种常见的故障,会导致设备的停工和安全隐患。
本文将探讨螺栓断裂的原因、预防措施以及处理方法,以期提高螺栓的可靠性和安全性。
螺栓断裂的原因螺栓断裂的原因复杂多样,主要包括以下几个方面:1. 过载当螺栓承受超过其承载能力的载荷时,会发生断裂现象。
这可能是由于设计不合理、材料不符合要求或者使用过程中的意外超载造成的。
因此,在设计和使用过程中,需要对螺栓进行充分的强度计算和载荷分析,合理选择螺栓材料和尺寸,以避免超载断裂。
2. 疲劳螺栓在长时间的工作循环中,受到的循环载荷会引起疲劳断裂。
循环载荷包括振动、冲击、震动等,这些载荷会在螺栓表面产生应力集中,从而导致疲劳裂纹的形成和扩展。
为了预防螺栓的疲劳断裂,需要选择高强度的材料、合理的表面处理和正确的安装方法。
3. 材料质量螺栓的材料质量直接影响其断裂的风险。
低质量的材料可能存在成分不合格、缺陷、夹杂物等问题,这些缺陷会降低螺栓的强度和抗疲劳性能,增加断裂的风险。
因此,在购买和使用螺栓时,应选择信誉好的供应商,并进行材料质量检测。
4. 安装错误错误的安装方法也会导致螺栓断裂。
例如,过紧或过松的拧紧力矩都会对螺栓产生不良影响,造成松动或者断裂。
正确的安装方法包括合理的拧紧力矩、均匀的力分布和正确的工具使用等。
螺栓断裂的预防措施为了避免螺栓断裂,可以采取以下预防措施:1. 合理设计在设计上,应充分考虑螺栓的承载能力和工作环境,选择合适的材料、尺寸和标准。
合理的力学计算和工程分析可以保证螺栓的强度和可靠性。
2. 材料检测在采购螺栓时,应选择信誉好的供应商,并进行材料质量检测。
对于重要的工程项目,可以采用无损检测等方法来检测螺栓的材料质量和缺陷情况。
3. 正确安装正确的安装方法是避免螺栓断裂的关键。
在安装过程中,应遵循螺栓的安装规范,包括拧紧力矩、工具使用、力分布等。
螺栓断裂原因分析及预防

螺栓断裂原因分析及预防
一般情况下,分析螺栓断裂从以下四个方面着手:螺栓的质量,螺栓的预紧力矩,螺栓的强度,螺栓的疲劳强度。
1、实际上,螺栓断裂绝大多数情况都是因为松动而断裂的,是由于松动而被打坏的。
因为螺栓松动打断的情况和疲劳断裂的情况大体相同,我们总能从疲劳强度上找到原因。
实际上,疲劳强度大得我们无法想象,螺栓在使用过程中根本用不到疲劳强度。
2、螺纹紧固件的松动不是由于螺栓的疲劳强度:
螺纹紧固件在横向振松实验中只需一百次即可松动,而在疲劳强度实验中需反复振动一百万次。
换句话说,螺纹紧固件在使用其疲劳强度的万分之一时即松动了,我们只使用了它大能力的万分之一,所以说螺纹紧固件的松动也不是因为螺栓疲劳强度。
3、螺纹紧固件损坏的真正原因是松动:
螺纹紧固件松动后,产生巨大的动能mv2,这种巨大的动能直接作用于紧固件及设备,致使紧固件损坏,紧固件损坏后,设备无法在正常的状态下工作,进一步导致设备损坏。
受轴向力作用的紧固件,螺纹被破坏,螺栓被拉断。
受径向力作用的紧固件,螺栓被剪断,螺栓孔被打成橢圆。
综上所述:选用防松效果优异的螺纹防松方式是解决问题的根本所在。
紧固螺栓开裂原因分析

2 螺栓开裂原因分析
2. 1 螺栓受力分析 螺栓在安装过程中 ,安装力矩克服的主要是螺
旋副产生的摩擦力矩 、螺旋副正压力分力产生的分
力矩和螺栓头底面产生的摩擦力矩[5] 。螺栓在一定
拧紧力矩作用下所产生的轴向拉力 P0 可通过下式 计算[6 ] :
P0
= d2
2M
tan (α+β)
+
2μ( D3 3 ( ຫໍສະໝຸດ 2 -Key words : bolt ; overload f ract ure ; f rictio n coefficient
0 引 言
某紧固螺栓材料为 30CrMnSiA 钢 ,表面镀镉 , 经调质 和除 氢处 理 , 其 抗拉 强 度 要 求 在 1 050 ~ 1 200 M Pa范围内 。该螺栓采用 150 N ·m 的定力 扳手进行紧固 ,安装前需在螺纹孔表面涂覆 TB0629 锌黄丙烯酸聚氨酯底漆 。
试样 检测位置
1#
中心
边缘
2#
中心
边缘
显微硬度/ HV0. 2
352. 8 352. 2 339. 5 346. 6
354. 4 353. 3 346. 1 353. 2
355. 6 360. 6 353. 8 361. 2
抗拉强度 / MPa 1 152 1 155 1 126 1 152
( a) 宏观特征
1. 5 结果分析 由以上的结果可知 ,两螺栓原始裂纹断口微观
形貌均为韧窝断裂特征 ,且也无陈旧性裂纹断口 ,可 以判断螺栓开裂性质为过载开裂 。螺栓的过载开裂 主要与两方面因素有关[4] :材质和应力水平 。试验 结果表明 ,螺栓显微组织和显微硬度正常 ,由硬度值 换算的抗拉强度值也在规定的范围值之内 ,且断口 上也未见夹杂等冶金缺陷 ,由此可知 ,螺栓的开裂与 材质无关 ,而与受到较大的应力有关 。
- 1、下载文档前请自行甄别文档内容的完整性,平台不提供额外的编辑、内容补充、找答案等附加服务。
- 2、"仅部分预览"的文档,不可在线预览部分如存在完整性等问题,可反馈申请退款(可完整预览的文档不适用该条件!)。
- 3、如文档侵犯您的权益,请联系客服反馈,我们会尽快为您处理(人工客服工作时间:9:00-18:30)。
刘昌奎 , 等 :紧固螺栓开裂原因分析
色区域 , 能谱检测结果表明为 T B06-9 底漆 ;原始裂 纹断口微观特征为等轴韧窝(图 2b)。可以推断 , 断 口上的底漆是装配时螺栓开裂后渗入造成的 。
表 1 显微硬度检测及抗拉强度换算结果 Tab .1 Results of microhardness testing and tensile strength
图 1 2 #螺栓裂纹宏观形貌 Fig.1 The morphol ogy of cracks
1 .2 断口形貌 用 S600 型扫描电镜(SEM)对裂纹打断后的断
口进行观察 。 两原始裂纹断口微观特征基本相同 , 裂纹均起源于螺纹牙底 , 裂纹源区未见夹杂等冶金 缺陷 。2 #螺栓原始裂纹断口上 存在面积较大的黄
oil and TB06-9 lacquer
2 .4 螺栓受力有限元分析 根据上面提到的螺栓轴向拉力计算公式 , 扭矩
选取 150 N ·m , 摩擦因数 f 设定为 0 .15 , 其他参数 不变 , 计算螺栓所受轴向拉力为 P0 =59 940 N 。 在 该条件下采用 ANSYS 软件对螺栓的受力状态进行 有限元分析 , 结果见图 6 。 可见 , 在轴向 拉力 P0 = 59 940 N 条件 下 , 螺栓在装配过程中 , 其内外螺纹 旋合部位头四牙的螺纹牙底 , 存在局部塑性变形 , 第 一和第二牙较为明显 , 并且在螺栓光杆下未旋合的 头三牙的螺纹牙底也有小部分存在塑性变形 。
表 2 摩擦因数测定结果 Tab.2 The results of friction coeff icient testing
压力 /N
30 60 90
干摩擦
0 .22 0 .21 0 .24
蓖麻油 润滑
0 .13 0 .12 0 .11
底漆润滑 蓖麻油+
体积比 体积比 体积比 底漆润滑 5∶95 13 .6 ∶86.4 20 ∶80
0.27 0 .32
0 .14
0 .06
0.27 0 .33
0 .12
0 .03
0.33 0 .28
0 .12
0 .12
图 4 底漆和润滑油对轴向拉力的影响 Fig .4 The relation between logni tudinal loading of bol t and castor
摘 要 :某螺栓在安装过程中有两个在螺纹牙底开裂 。通过对螺栓裂纹及裂纹断口的宏观微观 观察 、显微组织和显微硬度检测 , 确定了裂纹性质 ;通过对螺栓在安装过程中的受力分析 、扭拉试 验 、摩擦因数测定以及有限元数值模拟分析 , 确定了螺栓开裂原因 。结果表明 :螺栓裂纹性质为过 载开裂 , 其主要原因是由于螺栓孔内残留的蓖麻油和 T B06-9 底漆使得螺纹旋合摩擦因数大大降 低 , 螺栓在一定的扭矩下承受的轴向拉应力显著增加 , 从而导致螺栓开裂 。
观察 , 结果均为回火索氏体组织 , 未见异常 , 见图 3 。
图 3 螺栓显微组织 Fig .3 The microstructure of bolts
1 .4 显微硬度 用 WOLP ERT 401MVD 型显微硬度仪对两螺
栓进行显 微硬度 测定 , 并 根据 GB/ T 1172 -1999 《黑色金属硬度及强度换算值》将所测硬度值换算为 抗拉强度值 , 检测及换算结果见表 1 。结果表明 , 两 螺栓心部和表面硬度基本相当 , 换算所得的抗拉强 度值均在 1 050 ~ 1 200 M Pa 范围内 。
第 32 卷 第 4 期 2008 年 4 月
机 械 工 程 材 料
M ate rials f or M echanical Eng ineering
V ol .32 N o .4 A pr .2008
紧固螺栓开裂原因分析
Байду номын сангаас
刘昌奎 , 李运菊 , 陶春虎 , 张 兵 (北京航空材料研究院中国航空工业失效分析中心 , 北京 100095)
2 螺栓开裂原因分析
2 .1 螺栓受力分析 螺栓在安装过程中 , 安装力矩克服的主要是螺
旋副产生的摩擦力矩 、螺旋副正压力分力产生的分 力矩和螺栓头底面产生的摩擦力矩[ 5] 。 螺栓在一定 拧紧力矩作用下所产生的轴向拉力 P0 可通过下式 计算[ 6] :
P0 = d2
2M t an(α+β)+32(μD(D2 -3 -d2d)3d)2
式中 :M 为拧紧力矩 , N · mm ;P0 为轴向拉力 , N ;d
为螺纹外径 , m m ;d2 为螺纹平均 直径 , m m ;α为螺
纹上升角 , t anα=s/ πd2 , s 为螺距 ;β 为螺纹摩擦角 ,
t anβ =f , f 为螺栓与螺帽间的摩擦因数 ;D 为六角
螺栓外接圆直径 ;μ为螺母与其支撑面之间的摩擦
试样 检测位置
1#
中心
边缘
2#
中心
边缘
显微硬度/ HV 0 .2
352 .8 352 .2 339 .5 346 .6
354 .4 353 .3 346 .1 353 .2
355 .6 360 .6 353 .8 361 .2
抗拉强度 / MPa
1 152 1 155 1 126 1 152
(a) 宏观特征
因数 。
对于开裂的螺栓而言 , d =14 m m 、d2 =13 .026
mm 、α=2 .1°、s =1 .5 mm 、D =19 .8 m m 、μ=0 .15 ,
均为定值 。而 M 为施加在螺栓上的拧紧力矩 , t gβ
=f 则与实际的摩擦条件有关 。
从螺栓的安装条件来看 , 在装螺栓前 , 需在对应
关键词 :螺栓 ;过载开裂 ;摩擦因数
中图分类号 :TG 11 文献标识码 :A 文章编号 :1000-3738(2008)04-0070-04
Failure Analysis of Fractured Bolts
LIU Chang-kui , LI Yun-ju , TAO Chun-hu , ZHANG Bing (Bei jing Insti tute of Aeronaut ical M at erials , Beijing 100095 , China)
2 .2 不同条件下的扭拉试验
为得出不同润滑条件对螺栓所受轴向拉力的影 响 , 对螺栓在不同润滑条件和扭力水平下进行扭拉 试验 。扭拉试验设备为瑞格尔 RNJ-500 型拉扭 试 验机 。选取四种试验条件 , 分别为干摩擦 、蓖麻油润 滑 、底漆润滑(底漆与稀释剂体积比为 1 ∶4)、蓖麻 油 +底漆润滑 。选取从 80 N · m 到 150 N · m 的 10 的整数倍共 8 个扭力水平 。每种条件下的 每一 应力水平分别做 5 组试验 , 试验结果见图 4(5 组试 验结果平均值)。可见 , 采用不同的润滑条件 , 螺栓 在相同的力矩下所受的轴向拉力 会出现较大的 差 异 。 其中 , 蓖麻油 +底漆共同作用下 , 在相同的力矩 下 , 螺栓所受轴向拉力明显偏大 。 并且在试验中 , 出 现了两组异常数据 , 均是在蓖麻油 +底漆润滑条件 下产生的 , 当扭矩达到 110 N · m 左右 , 出现了螺栓 所受轴向拉力明显增大 , 当扭矩为 150 N · m 时 , 螺 栓所受轴向拉力达到 110 kN , 见图 5 。
1 .5 结果分析 由以上的结果可知 , 两螺栓原始裂纹断口微观
形貌均为韧窝断裂特征 , 且也无陈旧性裂纹断口 , 可 以判断螺栓开裂性质为过载开裂 。螺栓的过载开裂 主要与两方面因素有关[ 4] :材质和应力水平 。 试验 结果表明 , 螺栓显微组织和显微硬度正常 , 由硬度值 换算的抗拉强度值也在规定的范围值之内 , 且断口 上也未见夹杂等冶金缺陷 , 由此可知 , 螺栓的开裂与 材质无关 , 而与受到较大的应力有关 。
1 理化检验与结果
1 .1 宏观检查
收稿日期 :2007-05-18 ;修订日期 :2007-08-03 作者简介 :刘昌奎(1976 -), 男 , 四川内江人 , 工程师 , 博士研究生 。 导师 :陶春虎研究员
· 70 ·
两螺栓的裂纹分布基本相同 , 均出现在第 1 ~ 第 4 螺纹牙底 , 其中 2#螺栓裂纹开口较大 , 见图 1 。 对螺纹用 H I-scope KH-2700 型体视显微镜进行高 倍检查 , 未发现明显的加工缺陷 。
为 0 .03 和 0 .12 , 相差 4 倍 。 其他条件下摩擦因数 都较稳定 , 变化不大 。 蓖麻油 +底漆润滑条件下摩 擦因数的波动与试验中蓖麻油和底漆实际的混合比
例有关 。 如果将蓖麻油 +底漆润滑的条件下所测定 的摩擦因数和力矩 150 N ·m 带入上面所提到的轴 向拉力计算公式中 , 则螺栓轴向拉力波动范围达到 22 .2 kN ;如果将各种试验条件 下所测得的最大和 最小摩擦因数值(分别为 0 .03 和 0 .33)带入计算 , 则螺栓轴向拉力波动范围达到 46 .75 kN 。由表 2 还可见 , 体积比为 20 ∶80 的底漆润滑和蓖麻油润滑 条件下的摩擦因数大致相当 , 说明在相同的扭矩作 用下 , 两种润滑条件下螺栓所受轴向拉力水平应大 致相当 。 而这一试验结果正好与扭拉试验中两种相 同条件下的试验结果相吻合 。
Abstract :T wo bolts fr actur ed in the process of installatio n.Based on macr o-observ ation , micr o-observ ation ,
micro structure te sting and micr ohardness testing , the fracture mechanism w as confirmed .And based o n loading analysis , ring-draw ex amination , frictio n co efficient te sting and finite element analy sis , the f racture cause w as found .T he fracture w as caused by over lo ad.U nder the co-effect of casto r oil and T B06-9 lacque r , the f rictio n co efficient reduced gr eatly .A s a result , the lo gnitudinal stress of bolts increased remar kably unde r a ce rtain moment of to rsion .T he n the bolts f ractured.