钢管加工工艺
长钢管的加工工艺流程
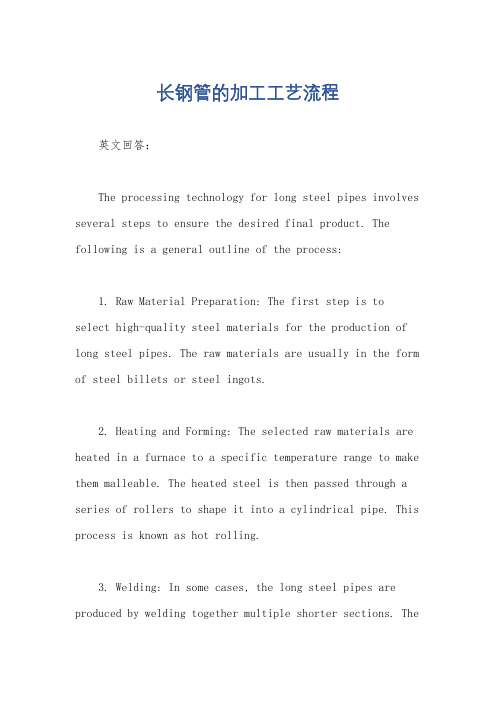
长钢管的加工工艺流程英文回答:The processing technology for long steel pipes involves several steps to ensure the desired final product. The following is a general outline of the process:1. Raw Material Preparation: The first step is to select high-quality steel materials for the production of long steel pipes. The raw materials are usually in the form of steel billets or steel ingots.2. Heating and Forming: The selected raw materials are heated in a furnace to a specific temperature range to make them malleable. The heated steel is then passed through a series of rollers to shape it into a cylindrical pipe. This process is known as hot rolling.3. Welding: In some cases, the long steel pipes are produced by welding together multiple shorter sections. Theends of the pipes are prepared by beveling or machining to create a suitable joint. The pipes are then welded together using various welding techniques such as arc welding or electric resistance welding.4. Sizing and Straightening: After the welding process, the long steel pipes undergo sizing and straightening operations. Sizing involves passing the pipes through a series of rollers to achieve the desired outer diameter and wall thickness. Straightening ensures that the pipes are perfectly straight and free from any deformations.5. Heat Treatment: Depending on the specificapplication and requirements, the long steel pipes may undergo heat treatment processes such as annealing, normalizing, or quenching and tempering. Heat treatment helps improve the mechanical properties and overall performance of the pipes.6. Surface Treatment: To protect the long steel pipes from corrosion and enhance their appearance, various surface treatments are applied. This may include processeslike shot blasting, pickling, galvanizing, or painting.7. Inspection and Testing: Before the final product is released, the long steel pipes undergo rigorous inspection and testing. This ensures that the pipes meet the required specifications and quality standards. The tests may include dimensional checks, mechanical property testing, non-destructive testing, and hydrostatic testing.8. Packaging and Delivery: Once the long steel pipes pass all the quality checks, they are properly packaged to prevent damage during transportation. The pipes are typically bundled together and secured with steel straps or plastic wrapping. They are then loaded onto trucks or shipped to the customer's location.中文回答:长钢管的加工工艺流程包括以下几个步骤,以确保最终产品达到预期要求:1. 原材料准备,首先需要选择高质量的钢材作为长钢管的生产原料。
钢管生产工艺流程
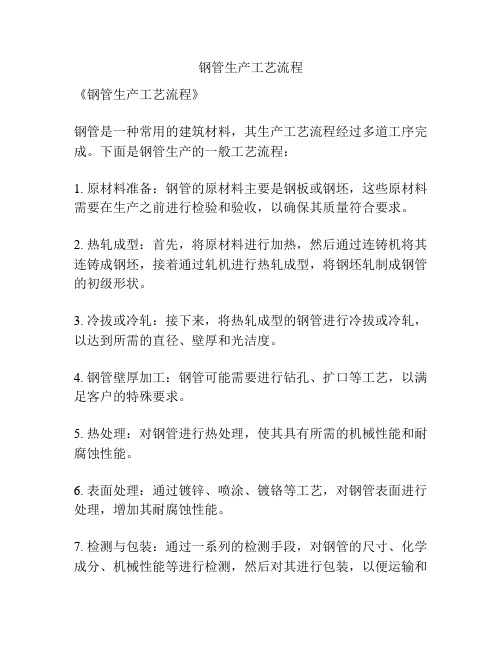
钢管生产工艺流程
《钢管生产工艺流程》
钢管是一种常用的建筑材料,其生产工艺流程经过多道工序完成。
下面是钢管生产的一般工艺流程:
1. 原材料准备:钢管的原材料主要是钢板或钢坯,这些原材料需要在生产之前进行检验和验收,以确保其质量符合要求。
2. 热轧成型:首先,将原材料进行加热,然后通过连铸机将其连铸成钢坯,接着通过轧机进行热轧成型,将钢坯轧制成钢管的初级形状。
3. 冷拔或冷轧:接下来,将热轧成型的钢管进行冷拔或冷轧,以达到所需的直径、壁厚和光洁度。
4. 钢管壁厚加工:钢管可能需要进行钻孔、扩口等工艺,以满足客户的特殊要求。
5. 热处理:对钢管进行热处理,使其具有所需的机械性能和耐腐蚀性能。
6. 表面处理:通过镀锌、喷涂、镀铬等工艺,对钢管表面进行处理,增加其耐腐蚀性能。
7. 检测与包装:通过一系列的检测手段,对钢管的尺寸、化学成分、机械性能等进行检测,然后对其进行包装,以便运输和
使用。
通过以上工艺流程,钢管的生产就完成了。
这些工艺流程的质量控制和技术创新,对于生产高品质的钢管具有重要意义。
钢管如何加工
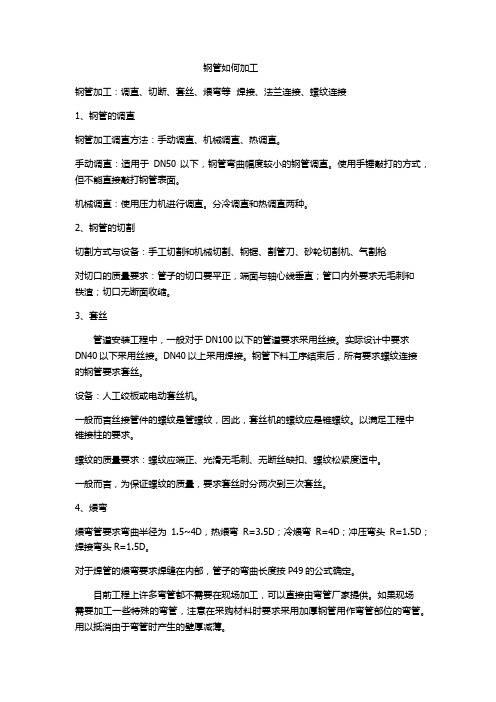
钢管如何加工钢管加工:调直、切断、套丝、煨弯等焊接、法兰连接、螺纹连接1、钢管的调直钢管加工调直方法:手动调直、机械调直、热调直。
手动调直:适用于DN50以下,钢管弯曲幅度较小的钢管调直。
使用手锤敲打的方式,但不能直接敲打钢管表面。
机械调直:使用压力机进行调直。
分冷调直和热调直两种。
2、钢管的切割切割方式与设备:手工切割和机械切割、钢锯、割管刀、砂轮切割机、气割枪对切口的质量要求:管子的切口要平正,端面与轴心线垂直;管口内外要求无毛刺和铁渣;切口无断面收缩。
3、套丝管道安装工程中,一般对于DN100以下的管道要求采用丝接。
实际设计中要求DN40以下采用丝接。
DN40以上采用焊接。
钢管下料工序结束后,所有要求螺纹连接的钢管要求套丝。
设备:人工绞板或电动套丝机。
一般而言丝接管件的螺纹是管螺纹,因此,套丝机的螺纹应是锥螺纹。
以满足工程中锥接柱的要求。
螺纹的质量要求:螺纹应端正、光滑无毛刺、无断丝缺扣、螺纹松紧度适中。
一般而言,为保证螺纹的质量,要求套丝时分两次到三次套丝。
4、煨弯煨弯管要求弯曲半径为1.5~4D,热煨弯R=3.5D;冷煨弯R=4D;冲压弯头R=1.5D;焊接弯头R=1.5D。
对于焊管的煨弯要求焊缝在内部,管子的弯曲长度按P49的公式确定。
目前工程上许多弯管都不需要在现场加工,可以直接由弯管厂家提供。
如果现场需要加工一些特殊的弯管,注意在采购材料时要求采用加厚钢管用作弯管部位的弯管。
用以抵消由于弯管时产生的壁厚减薄。
弯管的工艺有冷弯和热弯;有芯弯和无芯弯。
主要根据现场设备情况决定。
5、焊接工程上一般在使用普通焊接钢管时,DN40以上一般采用焊接。
采用焊接连接的方式其优点在于:1>、接口牢固严密,焊缝强度一般达到母材的85%以上。
2>、管段之间直接连接,构造简单,管路美观整齐,节省大量管件。
3>、焊接口不用填料,减少漏水的可能,亦减少了维修工作量。
4>、施工速度快,劳动强度小。
ep、ba、ap、mp管道管的加工工艺

ep、ba、ap、mp管道管的加工工艺
EP、BA、AP、MP是四种不同的管道加工工艺,具体如下:
EP(电解抛光):利用阳极处理的方式,借由电化学的原理适当地调整电压、电流、酸液组成以及抛光时间,对管道进行抛光处理。
这种工艺可以有效地提高管道的光洁度,同时去除管道表面的氧化层和微小杂质。
BA(光亮退火):钢管在制造过程中,为了避免油脂残留在钢管中,在退火时利用高温以氩气充当炉内气氛。
借由氩气与钢管表面的碳氧结合燃烧,进一步清洁钢管的表面以产生亮面效果。
这种利用纯氩气退火加热并快速冷却以亮化光面的方式叫做光亮退火。
虽然利用此种方式来亮化表面可保钢管充分干净无任何外来污染,但这种表面的明亮度若与其他抛光方式相较(如机械抛光),会显得稍暗,有雾面的感觉。
AP(酸洗处理):利用硝酸与亚氟酸等酸性溶液来除去钢管的氧化层,使管道表面更加光滑、干净。
这种工艺可以有效地去除管道表面的锈蚀和氧化物,提高管道的质量和耐腐蚀性。
MP(机械抛光):抛光轮或抛光带借助抛光剂中的磨料对不锈钢管表面进行抛磨加工,以促使不锈钢管面达到平滑抛光效果。
其亮度与效果则取决于加工方式的种类。
另外,虽然机械抛光后的钢管较美观,但其抗蚀性会降低,因此当用在腐蚀环境下需再经过钝化处理。
而且,钢管表面常有抛光材料残留。
这四种加工工艺各有特点,可以根据具体需求和管道材质选择合适的工艺。
热轧钢管生产工艺

热轧钢管生产工艺
热轧钢管是将钢坯通过加热至高温状态后,在轧机中进行轧制加工而成的管材。
热轧钢管生产工艺包括以下几个步骤:
1. 钢坯准备:选用适合的钢坯作为原料,一般为钢坯长条状,需要经过切割、锯断等工艺进行处理。
2. 坯料加热:将钢坯加热至适当的温度,一般为1100℃以上,以便在轧制过程中使钢坯达到塑性变形的要求。
3. 轧制加工:将加热至高温状态的钢坯送入轧机中,经过多道次的轧制,逐步压制出所需尺寸和形状的钢管。
4. 缩径:为了获得更加精确的直径尺寸,制造高精度的钢管,需要通过缩径工艺进行处理。
该工艺是在钢管的一端注入高压液体,使钢管内部受到液体的压力作用,从而缩小钢管的直径。
5. 冷却:在轧制完毕后,将钢管进行快速冷却,以提高钢管的物理性能和机械性能。
6. 修边:通过修边工艺,去除热轧钢管两侧的毛刺,使钢管的两侧光滑整齐。
7. 检测:对热轧钢管进行各项检测,包括尺寸、化学成分和力学性能等方面的检测,以确保热轧钢管的质量和安全性。
8. 成品:经过检测合格的热轧钢管,根据不同的要求,可以进
行颜色标识、喷涂和打包等工艺,最终成为成品,供应给用户使用。
总结:热轧钢管生产工艺主要包括钢坯准备、坯料加热、轧制加工、缩径、冷却、修边、检测和成品处理等过程。
每个步骤都非常关键,对于最终的钢管质量和性能有着重要影响,因此需要严格控制和管理。
钢管生产工艺

3.3无缝钢管工艺流程图
四、焊管生产工艺
4.1焊接钢管
定义
• ◆焊接钢管即有缝钢管,其生产是将管坯(钢板和钢带)用各种
成型方法弯卷成要求的横断面形状和尺寸的管筒,再用不同的焊 接方法将焊缝焊合而得到钢管的过程
特点 • 产品精度高,尤其是壁厚精度 • 主题设备简单,占地小 • 生产上可以连续化作业 • 生产灵活、机组的产品范围宽
4.2.1直缝高频焊管(ERW)
将热轧卷板经过成型机成型后,利用 高频电流的集肤效应和邻近效应,使管坯 边缘加热熔化,在挤压辊的作用下进行 压力焊接来实现生产的
பைடு நூலகம்
4.2.2高频焊管工艺流程图
4.3.1螺旋钢管生产工艺
1、螺旋钢管原材料即带钢卷、焊丝、焊剂。 2、成型前带钢经过矫平、剪边、刨边,表面清 理输送和予弯边处理。 3、采用焊缝间隙控制装置来保证焊缝间隙满足 焊接要求,管径、错边量和焊缝间隙都得到严 格的控制。 4、切成单根钢管后,每批钢管头三根要进行严 格的首检制度,检查焊缝的力学性能,化学成 份,溶合状况,钢管表面质量以及经过无损探 伤检验,确保制管工艺合格后,才能正式投入 生产。
4.4.2.1UOE直缝埋弧焊管成型工艺
UOE直缝埋弧焊钢管成型工艺的三大主成形工序包括: 钢板预弯边、U 成型及O 成型。各工序分别采用专用的成 型压力机,依次完成钢板边部预弯、U成型及O成型三道工 序,将钢板变形成为圆形管筒。如图:
4.4.2.2JCOE直缝埋弧焊管成型工艺
成型:在JC0 成型机上经过多次步进冲压,首先将钢板的一半压 成“J,,形,再将钢板的另一半压成“J”开,形成 C”形, 最后从中部加压从而形成开口的“0”形管坯。如图:
4.4.3直缝埋弧焊钢管生产工艺流程图
钢管加工工序

4.5.1.2、钢管加工:钢管构件集中在场外租用设置的钢构件组合场地加工,该场地配备15t/20m龙门吊1台。
为提高加工质量,除配备一般加工设备外,还配有自动割枪、自动焊机、喷砂除锈、喷漆、漆膜厚度测定仪等设备。
施工工艺流程:原材料矫正→放样、号料→下料(剪切或气割)→焊接加工→成品检验。
钢管在厂内制作设计长度的钢管,焊缝外观检查不得有裂纹,局部连续咬边累计长小于等于100mm。
制成品钢管经无抽探伤、煤油渗透和水压试验验收合格后,即可发往组装工地。
4.5.1.3、钢制管道防腐:各钢制管道在涂刷防腐涂料前均需对钢制管道表面涂锈处理,保证管道表面干燥、无水迹、无焊渣、无油迹。
管内壁防腐:表面清理合格后,刷钢管专用防腐涂料PHA106底漆一遍,然后再刷PHA106面漆二遍,要求固化后的漆膜厚度为90-100μm。
管外壁防腐分下面几种情况:A、明露管道:表面清理合格后,刷钢管专用防腐涂料PHA106二遍,然后再刷加强型抗紫外光PHA106面漆二遍,要求固化后的漆膜不小于100μm。
B、埋地管道:表面清理合格后,刷钢管专用防腐涂料PHA106底漆二遍,然后再刷PHA106面漆一遍,要求防腐层厚度不小于150μm。
以上防腐涂料其具体操作方法、验收标准和安全注意事项详见采购产品的说明书。
4.5.1.4、各管道间的焊接处均要进行补口,补口部位的表面处理及底漆、面漆的涂饰要求同前,咬边不小于100mm,各管道在安装过程中被损伤和涂层如未漏出金属表面,只需补涂面漆,并用与管体防腐结构相同的防腐材料与施工方法补伤,如已漏出金属表面,必须先进行表面处理然后再做防腐工程。
4.5.1.5、螺栓及螺母:除特殊说明外,机械装置的所有螺栓螺母、垫片及小轴杆的材质一般采用碳钢Q235,当与污水存在接触的可能性时应采用不锈钢。
装配时把用聚酰胺垫片隔开的垫片放到螺钉头或螺母下方(不能用防松垫圈代替垫片)。
任何情况下,都可在螺栓与金属部件之间放一个聚酰胺垫圈。
无缝钢管的工艺
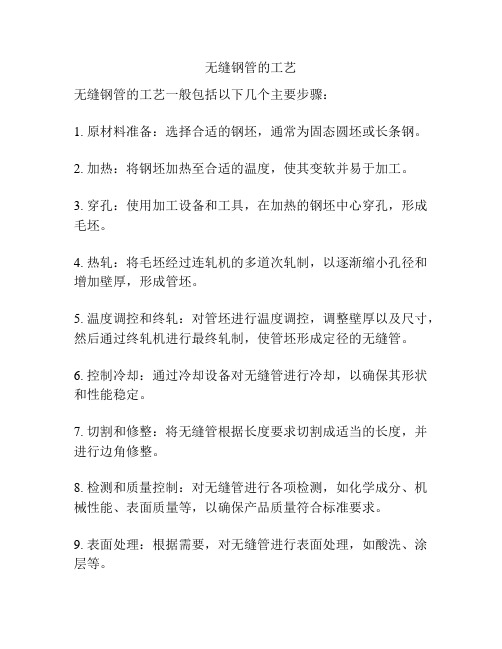
无缝钢管的工艺
无缝钢管的工艺一般包括以下几个主要步骤:
1. 原材料准备:选择合适的钢坯,通常为固态圆坯或长条钢。
2. 加热:将钢坯加热至合适的温度,使其变软并易于加工。
3. 穿孔:使用加工设备和工具,在加热的钢坯中心穿孔,形成毛坯。
4. 热轧:将毛坯经过连轧机的多道次轧制,以逐渐缩小孔径和增加壁厚,形成管坯。
5. 温度调控和终轧:对管坯进行温度调控,调整壁厚以及尺寸,然后通过终轧机进行最终轧制,使管坯形成定径的无缝管。
6. 控制冷却:通过冷却设备对无缝管进行冷却,以确保其形状和性能稳定。
7. 切割和修整:将无缝管根据长度要求切割成适当的长度,并进行边角修整。
8. 检测和质量控制:对无缝管进行各项检测,如化学成分、机械性能、表面质量等,以确保产品质量符合标准要求。
9. 表面处理:根据需要,对无缝管进行表面处理,如酸洗、涂层等。
10. 包装和运输:将无缝管进行包装并标记好相关信息,以方便运输和保护产品质量。
这是一般无缝钢管的生产工艺,不同的管材种类和用途可能会有一些不同的工艺步骤和要求。
钢管的铸造和锻造工艺
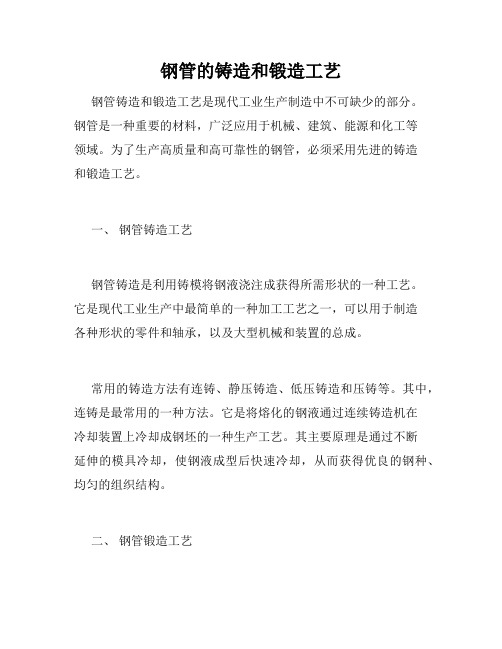
钢管的铸造和锻造工艺钢管铸造和锻造工艺是现代工业生产制造中不可缺少的部分。
钢管是一种重要的材料,广泛应用于机械、建筑、能源和化工等领域。
为了生产高质量和高可靠性的钢管,必须采用先进的铸造和锻造工艺。
一、钢管铸造工艺钢管铸造是利用铸模将钢液浇注成获得所需形状的一种工艺。
它是现代工业生产中最简单的一种加工工艺之一,可以用于制造各种形状的零件和轴承,以及大型机械和装置的总成。
常用的铸造方法有连铸、静压铸造、低压铸造和压铸等。
其中,连铸是最常用的一种方法。
它是将熔化的钢液通过连续铸造机在冷却装置上冷却成钢坯的一种生产工艺。
其主要原理是通过不断延伸的模具冷却,使钢液成型后快速冷却,从而获得优良的钢种、均匀的组织结构。
二、钢管锻造工艺钢管锻造是通过应用压力、力和温度等制造所需的形状的一种工艺。
这种工艺可以改变钢的物理和化学性质,从而提高其机械性能和耐磨性。
常用的锻造方法有自由锻、轧制锻造、环轧锻造、坯锻造和模锻等。
其中,自由锻造是最古老的锻造方法之一,也是最常用的一种方法。
它是将钢坯放在锻造装置上,并利用偏置、锤头等力量将钢坯加工成所需的形状。
三、钢管铸造与锻造工艺的比较钢管铸造和锻造工艺各自都有其优点和不足。
铸造工艺可以生产大量的产品,并能够制造复杂的零件和轴承。
而锻造工艺可以提高钢的机械性能,并能够生产更加精确的产品。
铸造工艺的缺点是其所生产的产品易受缺陷和杂质等因素的影响。
而锻造工艺的缺点则是其所生产的产品往往较小和比较难制造。
综上所述,钢管铸造和锻造工艺在现代工业生产中都扮演着重要的角色。
它们各自具有其独特的优点和不足,可以根据生产需要进行选择和应用。
无论是铸造还是锻造,都需要采用先进的工艺和设备,以确保生产出质量稳定,性能优良的钢管产品。
无缝钢管生产工艺流程
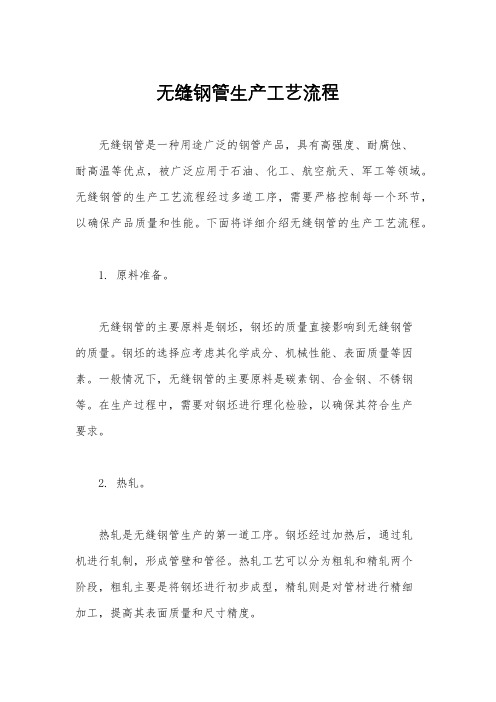
无缝钢管生产工艺流程无缝钢管是一种用途广泛的钢管产品,具有高强度、耐腐蚀、耐高温等优点,被广泛应用于石油、化工、航空航天、军工等领域。
无缝钢管的生产工艺流程经过多道工序,需要严格控制每一个环节,以确保产品质量和性能。
下面将详细介绍无缝钢管的生产工艺流程。
1. 原料准备。
无缝钢管的主要原料是钢坯,钢坯的质量直接影响到无缝钢管的质量。
钢坯的选择应考虑其化学成分、机械性能、表面质量等因素。
一般情况下,无缝钢管的主要原料是碳素钢、合金钢、不锈钢等。
在生产过程中,需要对钢坯进行理化检验,以确保其符合生产要求。
2. 热轧。
热轧是无缝钢管生产的第一道工序。
钢坯经过加热后,通过轧机进行轧制,形成管壁和管径。
热轧工艺可以分为粗轧和精轧两个阶段,粗轧主要是将钢坯进行初步成型,精轧则是对管材进行精细加工,提高其表面质量和尺寸精度。
3. 穿孔。
经过热轧后的钢坯需要进行穿孔,形成无缝钢管的管壁。
穿孔工艺是将加热后的钢坯放入穿孔机中,通过旋转锥形工具对钢坯进行穿孔,形成管状结构。
4. 酸洗。
酸洗是为了去除无缝钢管表面的氧化铁皮和锈蚀物,提高管材的表面质量。
酸洗工艺一般采用盐酸或硫酸进行酸洗,去除表面氧化物,然后经过清洗和中和处理,最终得到清洁的钢管表面。
5. 冷拔。
冷拔是为了提高无缝钢管的尺寸精度和表面质量。
经过酸洗的钢管通过冷拔机进行拉拔,使得管材的尺寸精度更高,表面质量更好。
6. 热处理。
热处理是为了改善无缝钢管的组织结构和性能。
经过冷拔后的钢管需要进行退火或正火处理,以消除加工硬化和应力,提高钢管的塑性和韧性。
7. 直径校直。
直径校直是为了保证无缝钢管的尺寸精度和表面质量。
经过热处理的钢管通过校直机进行校直,使得管材的直径误差和偏心率达到生产要求。
8. 检测。
无缝钢管生产的最后一个环节是对产品进行检测。
检测项目包括外观质量、尺寸精度、化学成分、机械性能等多个方面。
合格的产品才能够出厂销售。
通过以上工艺流程,钢坯经过一系列的加工和处理,最终形成优质的无缝钢管产品。
钢管的工艺流程

钢管的工艺流程
《钢管的生产工艺流程》
钢管是一种常见的金属制品,广泛应用于建筑、机械制造、石油化工等领域。
钢管的生产工艺流程通常包括钢板开卷、成型、焊接、热处理、表面处理等多个步骤。
首先是钢板开卷。
生产钢管的起始材料通常是钢板或钢带,这些原材料需要经过开卷机进行开卷,以便后续的成型加工。
接着是成型。
经过开卷后的钢板进入成型机,在成型机的作用下,钢板被弯折和卷曲成钢管的形状。
成型机可分为冷轧机和热轧机,冷轧机适用于薄壁钢管的生产,而热轧机适用于厚壁钢管的生产。
然后是焊接。
成型完成后的钢管需进行焊接工艺,将卷板焊接成一整根钢管。
焊接工艺有多种方法,包括埋弧焊、高频焊、电阻焊等。
不同种类的钢管使用不同的焊接工艺。
接下来是热处理。
经过焊接的钢管需要进行热处理,以消除内部应力和改善钢管的力学性能。
热处理过程包括退火、正火、淬火等,根据不同的要求选择不同的热处理工艺。
最后是表面处理。
最后一道工艺是对钢管进行表面处理,包括除锈、喷漆、热镀锌等,以提高钢管的耐腐蚀性能和美观度。
以上就是钢管的生产工艺流程,每个步骤都需要严格控制,以确保生产出高质量的钢管产品。
无缝钢管工艺
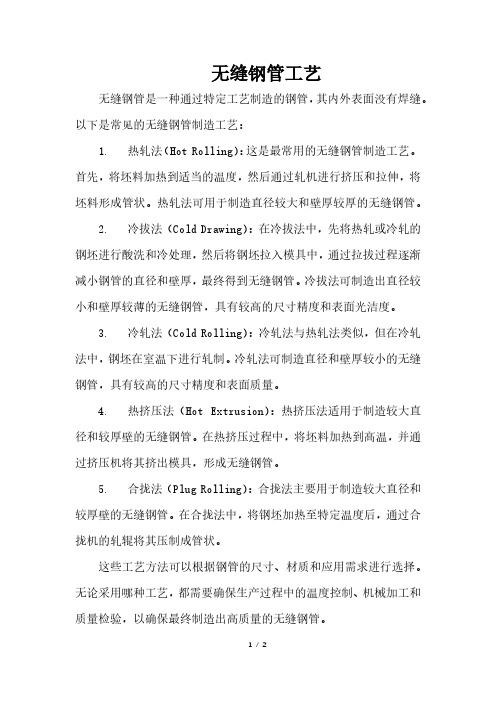
无缝钢管工艺
无缝钢管是一种通过特定工艺制造的钢管,其内外表面没有焊缝。
以下是常见的无缝钢管制造工艺:
1. 热轧法(Hot Rolling):这是最常用的无缝钢管制造工艺。
首先,将坯料加热到适当的温度,然后通过轧机进行挤压和拉伸,将坯料形成管状。
热轧法可用于制造直径较大和壁厚较厚的无缝钢管。
2. 冷拔法(Cold Drawing):在冷拔法中,先将热轧或冷轧的钢坯进行酸洗和冷处理,然后将钢坯拉入模具中,通过拉拔过程逐渐减小钢管的直径和壁厚,最终得到无缝钢管。
冷拔法可制造出直径较小和壁厚较薄的无缝钢管,具有较高的尺寸精度和表面光洁度。
3. 冷轧法(Cold Rolling):冷轧法与热轧法类似,但在冷轧法中,钢坯在室温下进行轧制。
冷轧法可制造直径和壁厚较小的无缝钢管,具有较高的尺寸精度和表面质量。
4. 热挤压法(Hot Extrusion):热挤压法适用于制造较大直径和较厚壁的无缝钢管。
在热挤压过程中,将坯料加热到高温,并通过挤压机将其挤出模具,形成无缝钢管。
5. 合拢法(Plug Rolling):合拢法主要用于制造较大直径和较厚壁的无缝钢管。
在合拢法中,将钢坯加热至特定温度后,通过合拢机的轧辊将其压制成管状。
这些工艺方法可以根据钢管的尺寸、材质和应用需求进行选择。
无论采用哪种工艺,都需要确保生产过程中的温度控制、机械加工和质量检验,以确保最终制造出高质量的无缝钢管。
钢管生产工艺及流程

钢管生产工艺及流程
原材料准备:
钢管的原材料通常是钢板或钢带,一般采用低碳钢、中碳钢或合金钢。
在生产之前,需要对原材料进行检验,确保其质量符合要求。
钢管制造:
1.切割原材料:将钢板或钢带按照规定的大小和厚度进行切割。
2.弯曲和卷制:通过专用设备将钢板或钢带弯曲成合适的形状,并将
其卷制成管状。
3.焊接:将钢板或钢带的两端进行焊接,形成一段无缝或有缝的钢管。
4.热处理:对钢管进行热处理,提高其物理性能,如强度和硬度。
钢管加工:
1.钢管精整:通过校直机和轧辊机等设备对钢管进行进一步加工,提
高其几何形状的精度和表面的光滑度。
2.钢管涂层:对钢管进行表面处理,如热镀锌、喷涂防腐等,以提高
其耐腐蚀性能。
质量检验:
1.外观检验:对钢管的外观进行检查,包括表面缺陷、几何形状等。
2.物理性能测试:对钢管的物理性能进行测试,如拉伸强度、抗弯强
度等。
3.化学成分分析:对钢管的化学成分进行分析,确保其合格。
包装:
在生产完成后,将钢管进行包装,以确保其在运输和储存过程中不受损坏。
常见的包装方式包括裸装、塑料薄膜包装等。
总结:
以上就是钢管生产的工艺及流程,整个生产过程需要严格控制每个环节的质量,以确保生产出的钢管能够满足各种要求。
钢管生产工艺的不断创新和改进,使得钢管的品质和应用范围不断提高。
钢管的生产工艺
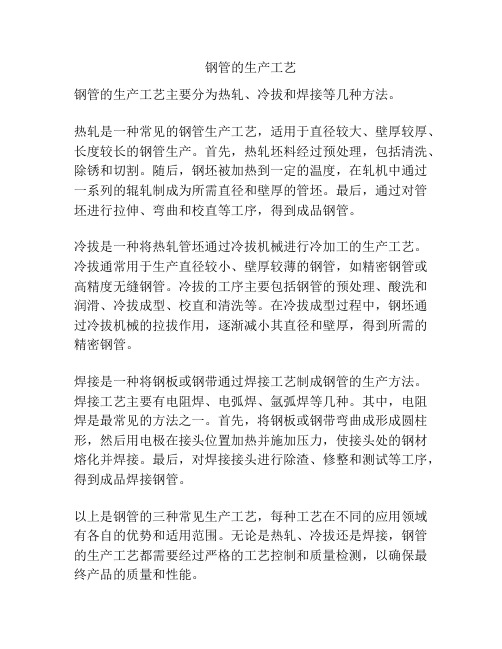
钢管的生产工艺
钢管的生产工艺主要分为热轧、冷拔和焊接等几种方法。
热轧是一种常见的钢管生产工艺,适用于直径较大、壁厚较厚、长度较长的钢管生产。
首先,热轧坯料经过预处理,包括清洗、除锈和切割。
随后,钢坯被加热到一定的温度,在轧机中通过一系列的辊轧制成为所需直径和壁厚的管坯。
最后,通过对管坯进行拉伸、弯曲和校直等工序,得到成品钢管。
冷拔是一种将热轧管坯通过冷拔机械进行冷加工的生产工艺。
冷拔通常用于生产直径较小、壁厚较薄的钢管,如精密钢管或高精度无缝钢管。
冷拔的工序主要包括钢管的预处理、酸洗和润滑、冷拔成型、校直和清洗等。
在冷拔成型过程中,钢坯通过冷拔机械的拉拔作用,逐渐减小其直径和壁厚,得到所需的精密钢管。
焊接是一种将钢板或钢带通过焊接工艺制成钢管的生产方法。
焊接工艺主要有电阻焊、电弧焊、氩弧焊等几种。
其中,电阻焊是最常见的方法之一。
首先,将钢板或钢带弯曲成形成圆柱形,然后用电极在接头位置加热并施加压力,使接头处的钢材熔化并焊接。
最后,对焊接接头进行除渣、修整和测试等工序,得到成品焊接钢管。
以上是钢管的三种常见生产工艺,每种工艺在不同的应用领域有各自的优势和适用范围。
无论是热轧、冷拔还是焊接,钢管的生产工艺都需要经过严格的工艺控制和质量检测,以确保最终产品的质量和性能。
钢管的生产工艺和加工技术

钢管的生产工艺和加工技术钢管是一种广泛应用于工业、建筑和交通等领域的基础材料,无论是作为支撑结构还是输送介质,都具有不可替代的重要作用。
钢管生产工艺和加工技术的发展,对于提高钢管的质量、降低生产成本和开发新型钢管具有至关重要的意义。
一、钢管的生产工艺钢管的生产工艺主要分为两种:热轧和冷拔。
热轧是通过加热钢坯至一定温度,然后通过轧制机器将钢坯压制成所需的形状和尺寸;冷拔则是通过将钢坯在室温下进行拉拔,使其逐渐变细并成形。
这两种工艺各有优缺点,选择哪种工艺取决于所需钢管的用途、材质和性能要求。
在热轧工艺中,钢坯首先被送入加热炉加热,为轧制做好准备。
然后通过各种钢压机将钢坯逐渐压制成所需形状和尺寸,最后通过切割机进行切割。
热轧工艺能够生产各种厚度和尺寸的钢管,但其表面粗糙度较高,需要经过表面处理才能够达到要求。
冷拔工艺中,则需要采用钢坯拉拔机,将加热过的钢坯拉拔成为所需的尺寸和形状。
由于冷拔工艺不需要加热,因此能够生产出表面光滑、尺寸精确、耐腐蚀性好的钢管,但其生产成本较高。
二、钢管的加工技术除了生产工艺之外,钢管的加工技术也是很关键的。
钢管经过了热轧或冷拔后,虽然已经变成所需的尺寸和形状,但是还需要进行进一步的加工才能够满足各种要求。
例如,在建筑行业中,钢管常常需要进行焊接、涂漆、绝缘等处理,以提高其使用寿命和安全性能。
以下是几种常见的钢管加工技术:1. 焊接:在钢管的两端进行焊接处理,可以将若干根钢管连接起来,形成一个更长的管道或结构,常用于输送液体或气体。
2. 内外涂层:将钢管进行内外涂层,可以提高其抗腐蚀性能,延长使用寿命。
通常使用的涂层材料包括环氧树脂、聚氨酯、煤沥青等。
3. 绝缘:在钢管表面涂覆一层绝缘材料或进行绝缘处理,可以减少电气设备的损失和泄漏,提高电气安全性能。
常用的绝缘材料包括聚氨酯泡沫、玻璃纤维、硅酸盐等。
4. 机加工:通过钻孔、切割、镗孔等机械加工方法,可以在钢管表面上开不同形状的孔或者进行孔的加工处理。
冷拔钢管工艺流程

冷拔钢管工艺流程
《冷拔钢管工艺流程》
冷拔钢管是一种常见的钢管加工工艺,通过特定的加工流程可以得到高精度、光洁度好的钢管产品。
下面将介绍冷拔钢管的工艺流程。
1.原材料准备
首先是选材。
通常情况下,冷拔钢管的原材料是无缝钢管。
在选材时,需要考虑钢管的成分和性能要求,确保选用合适的原材料。
然后进行物理和化学性能的检测,以确保符合生产要求。
2.预处理
原材料经过预处理,主要是采用钢管的清洗、除锈和表面处理等工艺,以确保原材料的表面质量和成分符合要求。
3.坯料加热
将预处理后的原材料进行加热处理,使其达到一定的热加工温度。
一般来说,加热温度要根据不同的钢种和成分而定,确保钢管在后续的冷拔过程中能够保持较好的韧性和塑性。
4.冷拔
在加热后的原材料进入冷拔机进行冷拔加工。
冷拔是通过将钢管在一定的温度下通过模具拉拔成各种规格和形状的工艺。
在冷拔过程中,钢管的外径和壁厚会得到相应的变化,同时也能够提高钢管的表面质量和机械性能。
5.光亮处理
冷拔完成后的钢管需要进行光洁处理,以提高其表面质量。
光亮处理通常包括酸洗、光亮热处理等工艺,最终使得钢管表面光洁度达到要求。
6.成品检验
最后,需要对冷拔完成的钢管进行质量检验。
主要包括外径、壁厚、长度、表面光滑度、化学成分、物理性能等各项指标的检测,确保产品符合技术要求。
通过以上工艺流程,可以生产出高质量的冷拔钢管产品。
随着钢管在工业领域的应用不断增加,冷拔钢管工艺也在不断完善和发展,成为了现代工业制造中不可或缺的一部分。
直缝钢管的加工工艺过程

直缝钢管的加工工艺过程一、原材料准备直缝钢管的原材料一般是热轧卷板或冷轧卷板。
在加工之前,需要对原材料进行检查和准备工作。
首先,对卷板进行外观检查,检查是否有划痕、裂纹等表面缺陷。
然后,对卷板进行尺寸检查,包括厚度、宽度等参数。
最后,对卷板进行切割,将其切成适当的长度。
二、板材矫直在直缝钢管的加工过程中,需要将卷板进行矫直,以保证加工后的钢管具有良好的直线度。
矫直是通过机械力的作用,对卷板进行拉伸和弯曲,使其恢复到平直状态。
矫直过程中,需要注意控制力度和速度,以免对板材造成损伤。
三、板材切割矫直后的卷板需要进行切割,将其切割成相应的宽度。
切割可以采用剪切机、切割机等设备进行。
在切割过程中,需要控制切割机的刀具,使得切割线条平直、垂直,并且不产生毛刺。
四、板材预弯直缝钢管的加工工艺中,板材预弯是为了使钢管在后续的焊接过程中更容易形成圆形。
预弯是通过机械设备对板材进行弯曲,使其呈现出一定的曲率。
预弯的程度和曲率需要根据钢管的尺寸和要求进行调整。
五、板材焊接板材焊接是直缝钢管加工过程中最关键的一步。
焊接可以采用电弧焊、埋弧焊、高频焊等不同的焊接方法。
在焊接过程中,需要控制焊接电流、电压和焊接速度,以保证焊缝的质量。
焊接完成后,需要对焊缝进行除渣和平整处理。
六、管坯成型焊接完成后的钢管需要进行成型,使其呈现出圆形。
成型可以采用多辊成型机进行,通过多个辊轮的作用,将钢管进行挤压和拉伸,使其逐渐形成圆形。
成型过程中,需要控制辊轮的间距和速度,以保证钢管的尺寸和表面质量。
七、管坯校直管坯成型后,需要对钢管进行校直,以保证其直线度和外观质量。
校直可以采用校直机进行,通过机械力的作用,对钢管进行拉伸和弯曲,使其恢复到平直状态。
校直过程中,需要注意控制力度和速度,以免对钢管造成损伤。
八、管坯切割对校直后的钢管进行切割,将其切割成所需的长度。
切割可以采用锯床、切割机等设备进行。
在切割过程中,需要控制切割机的刀具,使得切割线条平直、垂直,并且不产生毛刺。
钢管生产工艺流程

钢管生产工艺流程钢管是指由钢坯经过加热、穿孔、成型、焊接、脱鳞、校直、切割、除锈等工艺加工而成的管材。
以下是钢管生产的工艺流程:第一步:材料准备钢管的制造过程以钢坯作为原材料。
钢坯可以是热轧钢板、冷轧钢板、热轧带钢或冷轧带钢等。
钢坯经过切割和检验后,进入下一步的加工准备阶段。
第二步:加热钢坯需要通过炉加热来提高其可塑性,以便后续的加工操作。
加热可采用火焰加热、电阻加热或电磁感应加热等方式。
第三步:穿孔加热后的钢坯被送入穿孔机,通过圆锥工具的旋转和下压,形成一个中空的管状形状。
穿孔可以分为冷轧穿孔和热轧穿孔两种方法。
第四步:成型穿孔后的钢坯进入成型机,通过连续滚轧或循环滚轧,使其成为长条状的管材。
这个过程将会通过一系列的传送辊和辊轧将钢坯变形成圆形。
第五步:焊接成型后的圆管经过焊接机焊接,形成钢管。
焊接可以采用多种方法,如电阻焊、气焊、电弧焊等。
第六步:脱鳞焊接后的钢管表面上会形成一层氧化皮和焊渣,需要经过脱鳞工艺进行清除。
脱鳞可以采用化学脱鳞、机械脱鳞或水压脱鳞等方法。
第七步:校直脱鳞后的钢管需要经过校直机进行校直,以保证钢管的外形尺寸及内外表面质量。
第八步:切割校直后的钢管被送入切割机,根据需求进行切割成不同的长度。
第九步:除锈切割后的钢管进行除锈处理,以去除表面的铁锈和污垢。
除锈可以采用酸洗、机械刷洗等方法进行。
以上就是钢管生产的主要工艺流程。
钢管生产过程中需要严格的控制各道工序的操作参数,确保钢管的质量和性能。
随着技术的进步,钢管生产工艺不断改进,以提高钢管的质量和效率。
钢管加工工艺

(2)狄舍尔穿孔机
特点:
① 主动导盘的圆周线速度(2.1~2.3m/s)大于毛管的出口速度(1.1~1.2m/s), 使其生产效率提高了(从0.7提高到0.8以上);
② 在送进角 (原始位置α=13°,可在8~13°内调节) α<15°的范围内, 金属的可穿性可提高20%以上;
③ 轧辊上下布置并采用双传动机构,较好的解决了大送进角穿孔机的主传动 布置问题,使万向接轴始终在小倾角条件下工作,既运动平稳又不易磨损;
③ 轧制中旋转横锻效应大附加变形严重,能 耗大;
④ 受电机驱动条件限制,送进角较小(α< 13°,故轧制速度不快)。
送进角:轧辊轴线与轧制线在包含轧制线的垂直平面上投影之 间的夹角。
曼乃斯曼穿孔机的布置
图4-15 100穿孔机设备布置简图 1.受料槽;2.气动进料机;3.齿轮联轴节;4.主电机;5.减速齿轮座; 6.万向连接轴;7.扣瓦装置;8.穿孔机工作机座;9.翻料沟;10.顶杆小 车;11.至挡架;12.定心装置;13.升降辊;14.顶头;15穿孔机轧辊
π
总
F p
F 0
π
D2
D2 4p π (D
2S
)2
4 4 p
0
0
式中: LP:管坯长度;
D2
D2
p
p
4D S 4S 2 4(D S )S
00
0
0
0
0
FP:管坯横断面; n:热轧管的倍尺数(根); D0,S0:成品管外径、壁厚;
L0:成品管长;
4(L L) (D S ) S
管坯技术标准按国家或企业的技术标准执行,包括化学 成分、断面形状、几何尺寸、内部组织、机械性能等因素。