润滑油加氢装置的腐蚀影响及对策
加氢裂化装置的腐蚀问题及对策分析

加氢裂化装置的腐蚀问题及对策分析【摘要】在化工设备中,加氢裂化装置因为原油含量的增加而出现腐蚀加剧的情况,给安全生产带来了很大的隐患,这就需要从本质上对其腐蚀的原因进行分析,制定相应的防护措施。
本文主要是分析加氢裂化装置的腐蚀情况,包括氢损伤、硫化氢腐蚀、Cr-Mo钢的回火脆性、铵盐腐蚀、磨蚀、奥氏体不锈钢连多硫酸应力腐蚀开裂【关键词】加氢裂化腐蚀奥氏体在化工设备中,加氢裂化装置由于常常在高温、高压、临氧环境下工作,所以具有易燃易爆性等危险特性,安全的重要性在设备的运行的过程中越来越重视。
近年来,由于含硫化物在原油内含量的增多,导致对加氢裂化装置腐蚀情况加剧,这样影响设备的正常运转,使设备产生一定的安全隐患,日常工作中应该加强设备的防腐工作,防止因腐蚀造成的设备故障。
出现安全事故,。
本文主要分析了加氢裂化装置中发生腐蚀的情况进行,探讨相应的防腐措施。
1 氢损伤及其防护氢损伤主要有高温氢损伤、氢脆和奥氏体不锈钢堆焊层的氢致剥离。
高温氢腐蚀是氢在高温下侵入钢中和晶间的碳化物发生反应而产生甲烷导致内部脱碳。
即:Fe3C+2H2=CH4+3Fe。
CH4在非金属夹杂物部位和晶体空间具体而产生局部高压,形成的应力集中导致钢材发生裂纹等而降低了钢的强度和韧性,发生晶间断裂。
为避免发生高温氢腐蚀,工艺必须严格按要求进行,不能出现“飞温”,操作平稳,停工时的反应器温度不要在135℃以下。
氢脆主要是因氢在钢中表现出的脆化,一般在150℃以下是渗入氢导致,如果在某特定温度区间恒温一段时间就能将氢释放出来使钢的机械性能逐渐恢复。
扩大法兰密封槽底部转交半径可以实现氢脆的防护,避免在法兰密封槽底部出现裂缝。
在催化裂化装置的反应器开始工作的过程中,首先将温度升高到一定程度后在升压,如果停止工作,应当先降低压力后在降低温度,杜绝直接进行紧急停工的操作和非正常升温操作。
螺栓的上紧力需要严格控制,避免因上紧力的分布不均而导致法兰和螺栓过承压过大。
基于加氢裂化装置的腐蚀分析和防腐对策
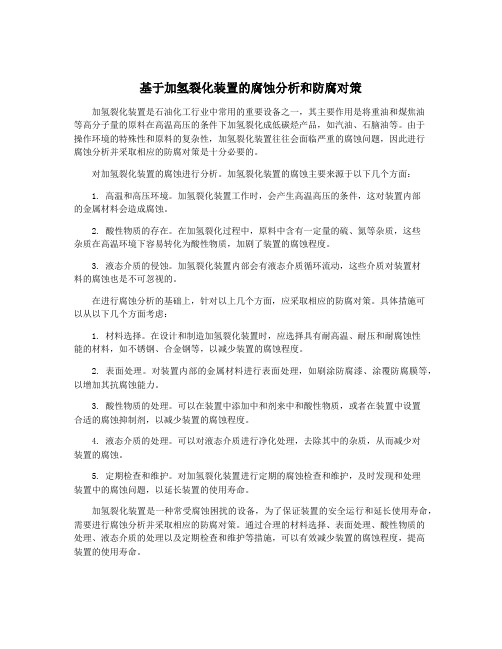
基于加氢裂化装置的腐蚀分析和防腐对策加氢裂化装置是石油化工行业中常用的重要设备之一,其主要作用是将重油和煤焦油等高分子量的原料在高温高压的条件下加氢裂化成低碳烃产品,如汽油、石脑油等。
由于操作环境的特殊性和原料的复杂性,加氢裂化装置往往会面临严重的腐蚀问题,因此进行腐蚀分析并采取相应的防腐对策是十分必要的。
对加氢裂化装置的腐蚀进行分析。
加氢裂化装置的腐蚀主要来源于以下几个方面:1. 高温和高压环境。
加氢裂化装置工作时,会产生高温高压的条件,这对装置内部的金属材料会造成腐蚀。
2. 酸性物质的存在。
在加氢裂化过程中,原料中含有一定量的硫、氮等杂质,这些杂质在高温环境下容易转化为酸性物质,加剧了装置的腐蚀程度。
3. 液态介质的侵蚀。
加氢裂化装置内部会有液态介质循环流动,这些介质对装置材料的腐蚀也是不可忽视的。
在进行腐蚀分析的基础上,针对以上几个方面,应采取相应的防腐对策。
具体措施可以从以下几个方面考虑:1. 材料选择。
在设计和制造加氢裂化装置时,应选择具有耐高温、耐压和耐腐蚀性能的材料,如不锈钢、合金钢等,以减少装置的腐蚀程度。
2. 表面处理。
对装置内部的金属材料进行表面处理,如刷涂防腐漆、涂覆防腐膜等,以增加其抗腐蚀能力。
3. 酸性物质的处理。
可以在装置中添加中和剂来中和酸性物质,或者在装置中设置合适的腐蚀抑制剂,以减少装置的腐蚀程度。
4. 液态介质的处理。
可以对液态介质进行净化处理,去除其中的杂质,从而减少对装置的腐蚀。
5. 定期检查和维护。
对加氢裂化装置进行定期的腐蚀检查和维护,及时发现和处理装置中的腐蚀问题,以延长装置的使用寿命。
加氢裂化装置是一种常受腐蚀困扰的设备,为了保证装置的安全运行和延长使用寿命,需要进行腐蚀分析并采取相应的防腐对策。
通过合理的材料选择、表面处理、酸性物质的处理、液态介质的处理以及定期检查和维护等措施,可以有效减少装置的腐蚀程度,提高装置的使用寿命。
加氢精制装置腐蚀检查及防腐措施
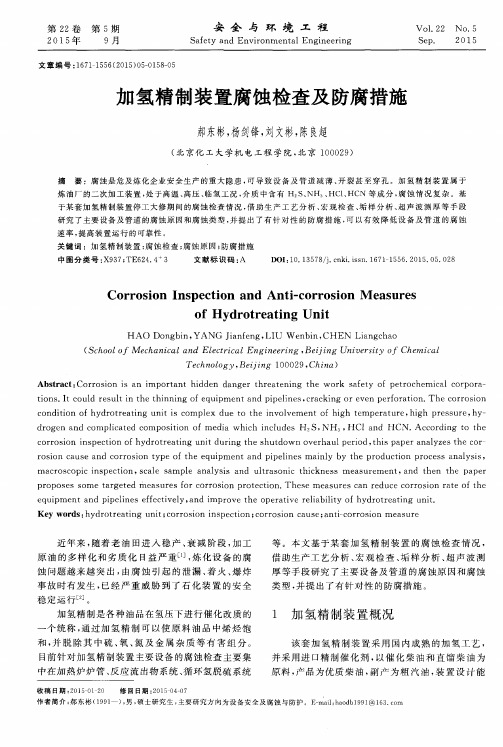
文章 编 号 : 1 6 7 1 1 5 5 6 ( 2 0 1 5 ) 0 5 — 0 1 5 8 — 0 5
安 全 与 环 境 工 程
Sa f e t y a nd Env i r o nm e n t a l Eng i ne e r i n g
Te c h n o l o g y, Be i j i n g 1 0 0 0 2 9 , Ch i n a)
Abs t r a c t : Cor r o s i on i s a n i mp or t a nt hi d de n da ng e r t hr e a t e ni ng t h e wo r k s a f e t y o f p e t r o c h e mi c a l c or p or a — t i o ns . I t c ou l d r e s u l t i n t he t h i nn i ng of e q ui p me nt a nd p i pe l i ne s , c r a c ki ng o r e v e n pe r f o r a t i o n. The c o r r o s i on c o nd i t i o n o f h yd r ot r e a t i n g un i t i s c o mp l e x d ue t o t he i n vo l v e me nt o f hi g h t e mpe r a t ur e, hi g h p r e s s ur e, hy —
dr o g e n a nd c o mp l i c a t e d c o mp os i t i on of me di a w hi c h i n c l ud e s H 2 S, NH 3 , H C1 a n d H CN . Ac c or d i ng t o t h e
加氢装置设备常见腐蚀分析及防护措施

加氢装 置 中 的设 备不 可避 免地 要处 于氢 的环 境 中 , 分子 既 小 又 活 泼 , 加 上 高 温 高 压 的操 作 条 氢 再
件, 因此氢很 容 易渗 入 钢 中并 于 钢 中 的成 分 发 生 反
应 。氢 的腐 蚀可 以分 为两类 : 高温氢 腐蚀 和氢 脆 。 ( )高 温氢 腐蚀 。 表 现 为两 种 形 式 : 是 表 面 1 一 脱碳 , 二是 内部脱 碳 和开裂 。以后一 种 的影 响较大 。
关键词 加 氢装 置 腐蚀 防护措 施
Co r so nd Pr v n i n o d 0 e a i n Pl n r o i n a e e to fHy r g n t0 a t
S nS ua g u hj n i
( N C D l n P t c e Mo r q ime t e t ,D l n L ann 1 6 3 ) C P ai er h m t up n p. a a , io ig 0 2 a o oE D i 1
K e r s h d o e ai n pln ,c ro i n,p e e tv a u e y wo d y r g n to a t o so r v n ie me s r s
1 前 言
加氢 是 当今石 油化 工领 域 中处理 高硫 油 的主要 途径 和方 式 。随着 国 内炼油 企业 炼制 进 口高硫油 的 比例越来 越大 , 建 的加 氢 装 置 也 随之 增 多 。各 类 新 加氢 装置 中尤 以加 氢裂 化和 渣油 加氢装 置 的操作 条 件最 为苛 刻 , 应 器 操 作 压 力 近 2 a 反 应 温 度 反 0 Mp , 也在 4 0c 以上 。 因此 要 搞好 设 备 管 理 , 须 对 加 0 = 【 必
润滑油加氢补充精制装置腐蚀分析及防护措施
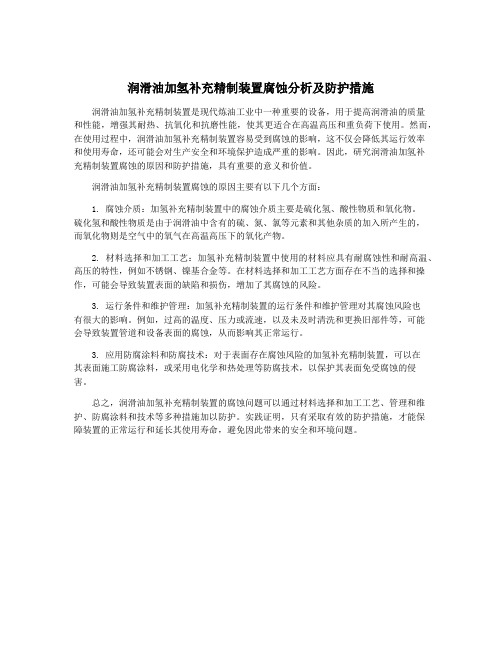
润滑油加氢补充精制装置腐蚀分析及防护措施润滑油加氢补充精制装置是现代炼油工业中一种重要的设备,用于提高润滑油的质量和性能,增强其耐热、抗氧化和抗磨性能,使其更适合在高温高压和重负荷下使用。
然而,在使用过程中,润滑油加氢补充精制装置容易受到腐蚀的影响,这不仅会降低其运行效率和使用寿命,还可能会对生产安全和环境保护造成严重的影响。
因此,研究润滑油加氢补充精制装置腐蚀的原因和防护措施,具有重要的意义和价值。
润滑油加氢补充精制装置腐蚀的原因主要有以下几个方面:1. 腐蚀介质:加氢补充精制装置中的腐蚀介质主要是硫化氢、酸性物质和氧化物。
硫化氢和酸性物质是由于润滑油中含有的硫、氮、氯等元素和其他杂质的加入所产生的,而氧化物则是空气中的氧气在高温高压下的氧化产物。
2. 材料选择和加工工艺:加氢补充精制装置中使用的材料应具有耐腐蚀性和耐高温、高压的特性,例如不锈钢、镍基合金等。
在材料选择和加工工艺方面存在不当的选择和操作,可能会导致装置表面的缺陷和损伤,增加了其腐蚀的风险。
3. 运行条件和维护管理:加氢补充精制装置的运行条件和维护管理对其腐蚀风险也有很大的影响。
例如,过高的温度、压力或流速,以及未及时清洗和更换旧部件等,可能会导致装置管道和设备表面的腐蚀,从而影响其正常运行。
3. 应用防腐涂料和防腐技术:对于表面存在腐蚀风险的加氢补充精制装置,可以在其表面施工防腐涂料,或采用电化学和热处理等防腐技术,以保护其表面免受腐蚀的侵害。
总之,润滑油加氢补充精制装置的腐蚀问题可以通过材料选择和加工工艺、管理和维护、防腐涂料和技术等多种措施加以防护。
实践证明,只有采取有效的防护措施,才能保障装置的正常运行和延长其使用寿命,避免因此带来的安全和环境问题。
润滑油加氢补充精制装置腐蚀分析及防护措施

润滑油加氢补充精制装置腐蚀分析及防护措施润滑油加氢补充精制装置是石油炼制工艺中的关键装置,主要用于提取润滑油中的硫、氮等杂质以及重质烃,以改善其性能。
由于润滑油加氢补充精制装置操作条件的特殊性,容易引起腐蚀问题。
本文将分析腐蚀原因并提出相应的防护措施。
腐蚀原因分析:1. 高温和高压:润滑油加氢补充精制装置在工艺过程中,需要在高温高压的环境下进行操作,这会引起金属的应力腐蚀和高温氧化腐蚀。
2. 强酸性物质:在加氢过程中,加入的氢气和催化剂会产生酸性物质,如硫酸、氮酸等,这些物质对金属设备具有腐蚀性。
3. 液体流动:润滑油加氢补充精制装置中液体的流动速度较快,会引起冲刷腐蚀。
防护措施:1. 选择耐腐蚀材料:在设计润滑油加氢补充精制装置时,应选择耐腐蚀的材料,如不锈钢、合金钢等,以提高设备的抗腐蚀性能。
2. 加强设备表面保护:在设备表面涂覆一层耐腐蚀涂料,以防止液体流动时对设备的冲蚀。
3. 优化工艺条件:合理控制加氢过程中的温度和压力,避免过高的温度和压力对设备造成腐蚀。
4. 引入中和剂:在加氢反应器中引入中和剂,如钠碱、石灰等,以中和酸性物质,防止对设备的腐蚀。
5. 定期检查和维护:定期对润滑油加氢补充精制装置进行检查和维护,及时清除设备表面的腐蚀产物,并修复设备中出现的腐蚀问题。
润滑油加氢补充精制装置的腐蚀问题主要是由于高温高压、酸性物质和液体流动等原因导致的。
为了解决这些问题,可以选择耐腐蚀材料、加强设备表面保护、优化工艺条件、引入中和剂以及定期检查和维护设备。
这些防护措施能够有效提高润滑油加氢补充精制装置的抗腐蚀能力,延长设备的使用寿命。
加氢裂化装置腐蚀问题及应对策略研究

加氢裂化装置腐蚀问题及应对策略研究加氢裂化装置作为炼油、化工等行业中不可或缺的设备,具有高效能、低能耗、生产成本低等优点。
然而,在长期的使用过程中,加氢裂化装置也面临着腐蚀等问题,严重影响设备的使用寿命和生产效率。
因此,本文将就加氢裂化装置腐蚀问题及应对策略进行探讨。
加氢裂化装置的腐蚀问题主要表现在两个方面:首先是设备表面的材质损伤,其次是设备内部液体或气体的腐蚀。
以不锈钢为例,不锈钢的表面上可能会产生微小的锈蚀点,长时间使用容易导致腐蚀,使不锈钢失去原有的耐蚀性。
针对这些问题,需要采取措施加以解决。
应对措施主要有以下几点:首先,选择合适的材质。
根据加氢裂解装置的使用环境和工艺要求,选择符合设备使用要求的耐腐蚀材料。
例如,使用有特殊抗腐蚀性能的合金材料等,提高设备本身的耐腐蚀性能。
其次,加强设备的防腐措施。
加强设备的防腐涂层,以保护设备表面不被腐蚀。
实施防腐措施的同时也要加强设备的日常维护,对设备的腐蚀情况进行监测和管理,及时处理设备表面腐蚀点,保持设备表面的完整性,及时清洗管道等设备内部管路,保持设备内干净卫生。
再次,改善工艺流程。
合理的生产工艺设计能减少设备使用条件下的各种不利影响,尽可能减少设备表面和内部材料的腐蚀,减缓腐蚀速率。
例如,保持设备内部物料的PH值在一定范围内,避免氯气的使用,设备在危险的作业条件下进行停机等。
最后,加强科技创新,发展新型防腐材料和加氢裂化装置。
科技的发展为加氢裂化装置的防腐提供了新的思路和方向。
例如,利用纳米技术制备高性能复合材料、开发新型涂层材料等,防止设备表面的腐蚀,提高设备的耐腐蚀性能。
总之,加氢裂化装置的腐蚀问题需要采取科学有效的应对措施。
针对加氢裂化装置的特有性质进行合理处理才能保证设备的正常运行,提高设备使用寿命和生产效率。
同时,加强科技创新和完善管理手段,也能为加氢裂化装置的防腐工作提供更多的新思路和新技术。
润滑油加氢补充精制装置腐蚀分析及防护措施

润滑油加氢补充精制装置腐蚀分析及防护措施润滑油加氢补充精制装置常见的腐蚀形式包括:材料腐蚀、热腐蚀、腐蚀疲劳、应力腐蚀等。
这些腐蚀形式的发生会导致装置的性能下降、设备寿命减短、甚至发生渗漏、事故等严重后果,给生产带来不利影响。
材料腐蚀是润滑油加氢补充精制装置中常见的腐蚀形式之一。
在加氢过程中,装置内氢气中的杂质、有机酸、硫、水等物质与管道、容器等设备材料反应,形成酸性物质,对设备材料造成腐蚀损伤。
热腐蚀通常是在高温高压下,设备材料表面被水蒸汽等腐蚀介质湿润,使得原有保护层破坏,材料表面出现裂纹、氧化、可脱落等现象。
腐蚀疲劳是一种具有时间依赖性的腐蚀形式,与设备的使用寿命有关。
在高温高压下,设备材料表面因周期性工作负载或应力变化而受到损伤,疲劳裂纹随着时间的推移逐渐扩大,最终导致设备失效。
应力腐蚀则是在材料表面存在应力影响下,与腐蚀介质反应产生的化学、电化学、物理化学作用,导致设备表面发生腐蚀和破损的一种形式。
一、选择高品质耐腐蚀的材料,如铬合金钢、钼合金钢、不锈钢等,能尽量减少设备受腐蚀的程度。
二、选用高性能耐腐蚀涂层,如环氧、氟碳等,能压制住液体腐蚀剂的腐蚀作用,提高设备的使用寿命。
三、对氢气纯度、含杂质量等指标进行完全控制,降低腐蚀剂的含量,使其避免与设备材料发生反应。
四、优化加氢工艺条件,降低装置的运行温度和压力,从而减少设备表面对腐蚀介质的接触时间和接触面积。
五、加强设备维护,及时清除设备内的水和杂质,保持设备表面的清洁,及时发现和处理设备的腐蚀情况。
六、加强安全防护,提高设备的安全管理级别,以及加强人员技能培训和操作规范化,降低运行风险。
总之,对润滑油加氢补充精制装置的腐蚀问题,应采取综合措施,积极避免腐蚀的发生,确保设备功能正常,生产质量稳定。
基于加氢裂化装置的腐蚀分析和防腐对策

基于加氢裂化装置的腐蚀分析和防腐对策加氢裂化装置是炼油厂中主要的加工装置之一,其作用是将高分子烃分解为低分子烃,并通过加氢使得分解产物氢化生成更高品质的燃料。
但是,在加氢裂化装置运行过程中,由于反应高温、高压、酸性环境等因素的影响,设备常常会出现腐蚀现象,从而影响设备寿命、安全性和生产效率。
因此,加氢裂化装置腐蚀分析和防腐对策显得尤为重要。
1. 酸性环境下的腐蚀加氢裂化反应涉及到催化剂的使用,催化剂通常是酸性催化剂,如氢氟酸、磷酸、硫酸等,这些催化剂容易在高温、高压、酸性环境下与金属材料发生化学反应,从而导致设备腐蚀。
如催化剂与设备中的铁元素反应,会产生FeF3、FeCl3等产物,使设备表面发生严重腐蚀。
2. 氢气在高温高压下的腐蚀在加氢裂化装置中,氢气是必不可少的媒介,但是氢气在高温高压下容易与金属材料发生化学反应,形成氢化金属和氢脆,导致设备出现裂纹和疲劳等问题。
3. 金属材料的腐蚀常见的加氢裂化装置材料如碳钢、不锈钢、镍合金等,其中碳钢容易发生点蚀和晶间腐蚀,不锈钢在含氯介质中容易出现应力腐蚀开裂,镍合金则可能发生点蚀和应力腐蚀。
采用耐酸性材质,如耐酸不锈钢、耐酸玻璃钢等。
对于金属材料,可以进行表面处理,如喷涂耐酸涂层。
采用合适的材料,如具有高抗氢脆性的合金材料。
此外,加氢裂化装置中氢气的压力和流量也需要控制在合理范围内,避免形成局部高压和高速流动状态,从而减轻氢气的腐蚀作用。
3. 表面防护对设备的表面进行防护处理,如电镀、喷涂、涂层等。
这些防护措施可以有效减轻设备表面的腐蚀作用,提高设备抗腐蚀能力。
4. 清洗防腐定期对加氢裂化装置进行清洗,清除因反应产物沉积而引起的腐蚀。
同时,加强设备运行和维护管理,及时发现和处理设备腐蚀问题,保证设备安全运行。
综上所述,加氢裂化装置腐蚀分析和防腐对策对设备的安全生产和长期稳定运行至关重要。
通过采取合理的防腐措施,可以延长设备寿命、提高生产效率、降低运行成本,并确保设备在安全稳定的状态下运行。
提高炼油加氢装置设备防腐蚀的管控能力
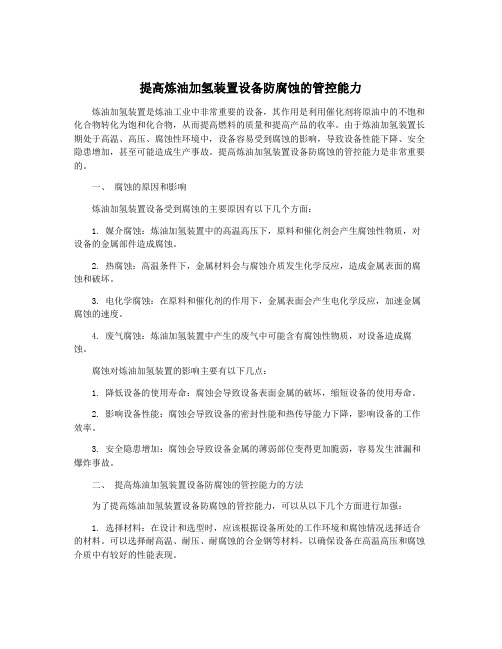
提高炼油加氢装置设备防腐蚀的管控能力炼油加氢装置是炼油工业中非常重要的设备,其作用是利用催化剂将原油中的不饱和化合物转化为饱和化合物,从而提高燃料的质量和提高产品的收率。
由于炼油加氢装置长期处于高温、高压、腐蚀性环境中,设备容易受到腐蚀的影响,导致设备性能下降、安全隐患增加,甚至可能造成生产事故。
提高炼油加氢装置设备防腐蚀的管控能力是非常重要的。
一、腐蚀的原因和影响炼油加氢装置设备受到腐蚀的主要原因有以下几个方面:1. 媒介腐蚀:炼油加氢装置中的高温高压下,原料和催化剂会产生腐蚀性物质,对设备的金属部件造成腐蚀。
2. 热腐蚀:高温条件下,金属材料会与腐蚀介质发生化学反应,造成金属表面的腐蚀和破坏。
3. 电化学腐蚀:在原料和催化剂的作用下,金属表面会产生电化学反应,加速金属腐蚀的速度。
4. 废气腐蚀:炼油加氢装置中产生的废气中可能含有腐蚀性物质,对设备造成腐蚀。
腐蚀对炼油加氢装置的影响主要有以下几点:1. 降低设备的使用寿命:腐蚀会导致设备表面金属的破坏,缩短设备的使用寿命。
2. 影响设备性能:腐蚀会导致设备的密封性能和热传导能力下降,影响设备的工作效率。
3. 安全隐患增加:腐蚀会导致设备金属的薄弱部位变得更加脆弱,容易发生泄漏和爆炸事故。
二、提高炼油加氢装置设备防腐蚀的管控能力的方法为了提高炼油加氢装置设备防腐蚀的管控能力,可以从以下几个方面进行加强:1. 选择材料:在设计和选型时,应该根据设备所处的工作环境和腐蚀情况选择适合的材料。
可以选择耐高温、耐压、耐腐蚀的合金钢等材料,以确保设备在高温高压和腐蚀介质中有较好的性能表现。
2. 设备设计:在设计炼油加氢装置时,应该合理设计设备结构和排布,尽量减少腐蚀介质对设备的侵蚀,降低腐蚀的速度。
可以采取防腐蚀涂层、防腐蚀合金材料等措施。
3. 检测和监控:定期对炼油加氢装置进行检测和监控,及时发现腐蚀情况。
可以采用无损检测、震动监测等技术手段,及时发现设备的腐蚀情况,提前进行维护和修复。
润滑油加氢补充精制装置腐蚀分析及防护措施

润滑油加氢补充精制装置腐蚀分析及防护措施润滑油加氢补充精制装置是石油化工行业中常见的装置之一,用于对润滑油进行精细加工,提高其品质和性能。
长期运行中,该装置可能受到腐蚀的影响,导致设备的寿命缩短和工艺效果的下降。
进行腐蚀分析并采取相应的防护措施非常重要。
腐蚀分析是确定腐蚀原因和对设备的影响程度的过程。
常见的润滑油加氢补充精制装置腐蚀类型有以下几种:1. 酸性腐蚀:主要是由于金属表面与酸性物质接触而引起的腐蚀。
这种腐蚀往往与酸性催化剂的存在有关。
某些润滑油和添加剂中的酸性组分可能在高温和高压的环境下释放出酸性物质,导致设备腐蚀。
防护措施:选择耐腐蚀材质的设备部件,如不锈钢、镍合金等。
可通过控制工艺参数和酸性成分的含量来减少酸性腐蚀。
3. 硫化物应力腐蚀开裂(SSC):是一种由于应力、硫化物和环境共同作用导致的金属开裂现象。
润滑油中的硫化物在高温和高压的条件下会释放出硫化氢,与金属表面反应,引起腐蚀开裂。
防护措施:采用合适的金属材料,并对设备进行应力分析,以减少应力集中的程度。
可以使用阻挡剂或添加剂来控制润滑油中的硫化物含量。
4. 氢腐蚀:是由于润滑油加氢过程中产生的氢与金属表面反应而引起的腐蚀。
氢在高温和高压条件下会渗入金属晶粒中,导致金属变脆。
防护措施:选择耐氢腐蚀的金属材料。
控制润滑油中氢的含量和加氢工艺参数,以减少氢腐蚀的风险。
为了防止润滑油加氢补充精制装置的腐蚀问题,除了以上所提到的防护措施外,还可以采取以下措施:1. 定期进行设备的维护和检修,清洗设备内部,以减少腐蚀物质的积累和对设备的侵蚀。
2. 加强设备的管道和阀门的防腐保温措施,减少温差对金属表面的腐蚀影响。
3. 严格控制润滑油中的杂质和酸性物质的含量,选择优质的润滑油和添加剂。
4. 根据设备的实际使用情况和工艺参数,对设备进行合理的设计和布局,减少腐蚀物质的生成和对设备的腐蚀。
润滑油加氢补充精制装置的腐蚀分析及防护措施对设备的正常运行和寿命的延长至关重要。
解决加氢装置腐蚀问题

解决加氢装置腐蚀问题
设备腐蚀加氢装置高温、高压、临氢、系统内存在H
2S、NH
3
,因此,加氢装置的
腐蚀问题也应引起重视,解决加氢装置腐蚀问题的主要方法是合理选材,在使用时加强监视与检测。
1、高温氢腐蚀
氢气在常温下对普通碳钢没有腐蚀,但是在高温、高压下则会产生腐蚀,使材料的机械强度和塑性降低。
高温氢腐蚀的机理为氢气与材料中的碳反应生成甲烷,使材料的机械强度和塑性降低,形成的甲烷在钢材的晶间积聚,使材料产生很大的内应力或产生鼓泡、裂纹。
至于在什么条件下产生腐蚀,则根据Nels。
n曲线确定。
为避免高温氢腐蚀,加氢装置高温、高压、临氢部分的设备、管线多采用合金钢或不锈钢。
2、氢脆
氢原子渗入钢材后,使钢材晶粒中原子结合力降低,造成材料的延展性、韧性下降,这种现象称为氢脆。
这种氢脆是可逆的,当氢气从材料中溢出后,材料的力学性能就能恢复。
氢脆的危害主要出现在加氢装置的停工阶段,装置停工阶段,系统温度、压力下降,氢气在材料中的溶解度下降,由于氢气溢出的速度很慢,这时材料中的氢气处于过饱和状态,当温度冷却到150℃时,大量的过饱和氢气会聚积到材料的缺陷处,如裂纹的前端,引起裂纹扩展。
所以加氢装置停工时降温、降压的速度应进行适当的控制,进行脱氢处理。
3、高温H2S腐蚀
高温H
2S腐蚀主要发生在反应系统高温部分,高温H
2
S腐蚀表现为与H
2
共同作用,
氢气的存在加强了H
2S的腐蚀作用,同时,H
2
S的存在也加强了氢气的腐蚀作用。
该种腐蚀的防治方法是选择抗H
2
S腐蚀材质。
基于加氢裂化装置的腐蚀分析和防腐对策

基于加氢裂化装置的腐蚀分析和防腐对策加氢裂化装置是石油化工行业的重要设备之一。
由于它长期承受高温、高压、高腐蚀等恶劣工况,因此其腐蚀问题一直是生产过程中需要关注和解决的难点之一。
本文从腐蚀机理出发,对加氢裂化装置的腐蚀问题进行了分析,并提出了相应的防腐对策。
加氢裂化装置是将高沸点石油馏分加氢裂解为低沸点烷烃和芳烃的设备。
该装置在操作中需要承受高温高压、反应物质的腐蚀以及可能产生的腐蚀产物等多方面的影响。
其中,主要的腐蚀机理有以下几种:1. 高温氧化腐蚀加氢裂化反应需要高温高压下进行,这对设备的材质和防腐措施提出了较高要求。
在反应过程中,反应器内部的金属表面会与氧气发生反应,产生氧化物,这种腐蚀称为高温氧化腐蚀。
这种腐蚀会导致反应器内部材料的表面失去原有的保护层,从而使材料更容易被腐蚀。
此外,高温氧化腐蚀还会导致反应器壁厚度变薄,从而影响设备的使用寿命。
2. 酸性腐蚀加氢裂化反应中使用的氢气和反应物质可能会产生一些有害酸性物质,如硫酸、盐酸等,这些物质会与金属表面发生酸性反应,从而引起腐蚀。
酸性腐蚀通常是在设备内壁表面形成一个物理或化学吸附的液膜,导致金属表面无法得到足够的氧气进行氧化而使腐蚀继续发生,增加了设备的维护难度和成本。
3. 废弃物腐蚀加氢裂化过程会产生类似金属间化合物、环氧和硫化物等难以溶解的废弃物,长期滤于设备内,会形成化学反应并产生腐蚀。
这种腐蚀多表现为腐蚀凸出或凹陷等等,影响设备性能和寿命。
基于以上腐蚀机理,合理的防腐措施对于加氢裂化装置的运行至关重要。
以下是一些常见的防腐对策:1. 选择耐腐蚀合金加氢裂化反应器内部材质的选择至关重要。
尽可能选择优质的耐腐蚀合金材料,以增加反应器的寿命和使用周期。
常用的耐腐蚀材料包括不锈钢、钛合金、镍合金等等。
2. 采取防护措施为了保护设备内表面免于腐蚀,可以对内表面进行防护处理。
常用的防护措施包括涂层、电镀等。
涂层可以采用耐高温、耐腐蚀的涂层材料,例如:镍基合金、钢玉陶瓷、不锈钢、耐酸玻璃等。
润滑油加氢补充精制装置腐蚀分析及防护措施
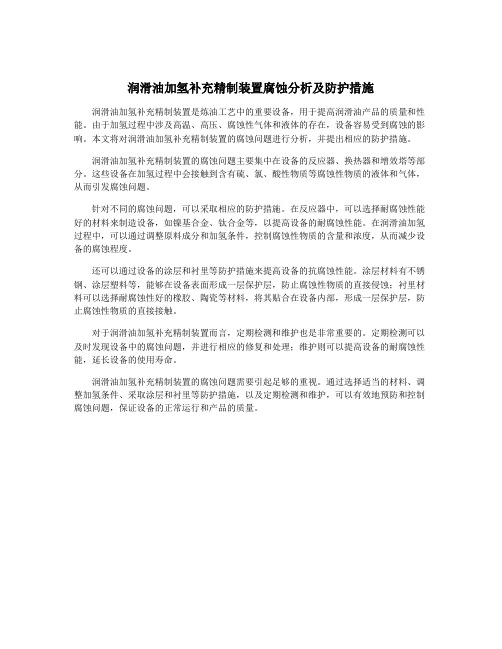
润滑油加氢补充精制装置腐蚀分析及防护措施
润滑油加氢补充精制装置是炼油工艺中的重要设备,用于提高润滑油产品的质量和性能。
由于加氢过程中涉及高温、高压、腐蚀性气体和液体的存在,设备容易受到腐蚀的影响。
本文将对润滑油加氢补充精制装置的腐蚀问题进行分析,并提出相应的防护措施。
润滑油加氢补充精制装置的腐蚀问题主要集中在设备的反应器、换热器和增效塔等部分。
这些设备在加氢过程中会接触到含有硫、氯、酸性物质等腐蚀性物质的液体和气体,从而引发腐蚀问题。
针对不同的腐蚀问题,可以采取相应的防护措施。
在反应器中,可以选择耐腐蚀性能好的材料来制造设备,如镍基合金、钛合金等,以提高设备的耐腐蚀性能。
在润滑油加氢过程中,可以通过调整原料成分和加氢条件,控制腐蚀性物质的含量和浓度,从而减少设备的腐蚀程度。
还可以通过设备的涂层和衬里等防护措施来提高设备的抗腐蚀性能。
涂层材料有不锈钢、涂层塑料等,能够在设备表面形成一层保护层,防止腐蚀性物质的直接侵蚀;衬里材料可以选择耐腐蚀性好的橡胶、陶瓷等材料,将其贴合在设备内部,形成一层保护层,防止腐蚀性物质的直接接触。
对于润滑油加氢补充精制装置而言,定期检测和维护也是非常重要的。
定期检测可以及时发现设备中的腐蚀问题,并进行相应的修复和处理;维护则可以提高设备的耐腐蚀性能,延长设备的使用寿命。
润滑油加氢补充精制装置的腐蚀问题需要引起足够的重视。
通过选择适当的材料、调整加氢条件、采取涂层和衬里等防护措施,以及定期检测和维护,可以有效地预防和控制腐蚀问题,保证设备的正常运行和产品的质量。
润滑油加氢补充精制装置腐蚀分析及防护措施
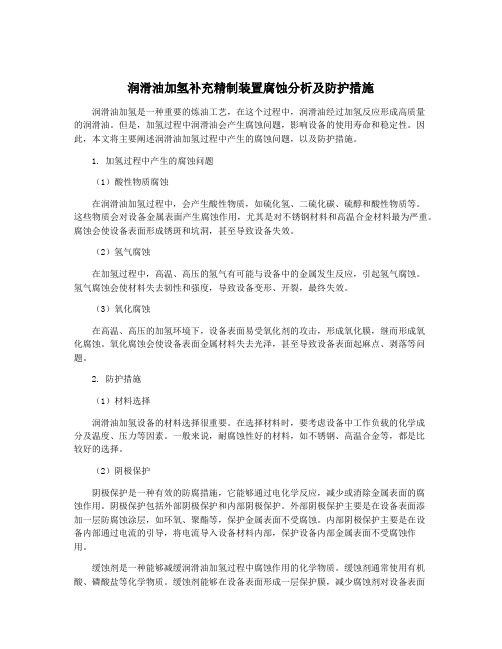
润滑油加氢补充精制装置腐蚀分析及防护措施润滑油加氢是一种重要的炼油工艺,在这个过程中,润滑油经过加氢反应形成高质量的润滑油。
但是,加氢过程中润滑油会产生腐蚀问题,影响设备的使用寿命和稳定性。
因此,本文将主要阐述润滑油加氢过程中产生的腐蚀问题,以及防护措施。
1. 加氢过程中产生的腐蚀问题(1)酸性物质腐蚀在润滑油加氢过程中,会产生酸性物质,如硫化氢、二硫化碳、硫醇和酸性物质等。
这些物质会对设备金属表面产生腐蚀作用,尤其是对不锈钢材料和高温合金材料最为严重。
腐蚀会使设备表面形成锈斑和坑洞,甚至导致设备失效。
(2)氢气腐蚀在加氢过程中,高温、高压的氢气有可能与设备中的金属发生反应,引起氢气腐蚀。
氢气腐蚀会使材料失去韧性和强度,导致设备变形、开裂,最终失效。
(3)氧化腐蚀在高温、高压的加氢环境下,设备表面易受氧化剂的攻击,形成氧化膜,继而形成氧化腐蚀。
氧化腐蚀会使设备表面金属材料失去光泽,甚至导致设备表面起麻点、剥落等问题。
2. 防护措施(1)材料选择润滑油加氢设备的材料选择很重要。
在选择材料时,要考虑设备中工作负载的化学成分及温度、压力等因素。
一般来说,耐腐蚀性好的材料,如不锈钢、高温合金等,都是比较好的选择。
(2)阴极保护阴极保护是一种有效的防腐措施,它能够通过电化学反应,减少或消除金属表面的腐蚀作用。
阴极保护包括外部阴极保护和内部阴极保护。
外部阴极保护主要是在设备表面添加一层防腐蚀涂层,如环氧、聚酯等,保护金属表面不受腐蚀。
内部阴极保护主要是在设备内部通过电流的引导,将电流导入设备材料内部,保护设备内部金属表面不受腐蚀作用。
缓蚀剂是一种能够减缓润滑油加氢过程中腐蚀作用的化学物质。
缓蚀剂通常使用有机酸、磷酸盐等化学物质。
缓蚀剂能够在设备表面形成一层保护膜,减少腐蚀剂对设备表面的腐蚀作用。
但需要注意的是,缓蚀剂的使用要控制在一定的浓度范围内,否则会对设备的运行产生负面影响。
总之,润滑油加氢的防腐措施是非常重要的。
润滑油加氢补充精制装置腐蚀分析及防护措施
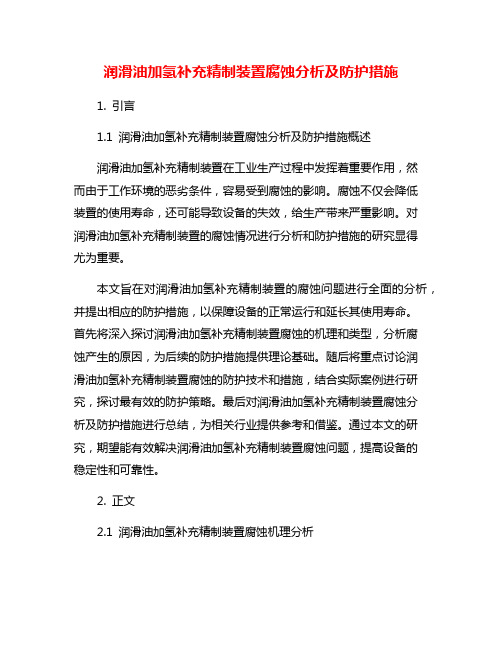
润滑油加氢补充精制装置腐蚀分析及防护措施1. 引言1.1 润滑油加氢补充精制装置腐蚀分析及防护措施概述润滑油加氢补充精制装置在工业生产过程中发挥着重要作用,然而由于工作环境的恶劣条件,容易受到腐蚀的影响。
腐蚀不仅会降低装置的使用寿命,还可能导致设备的失效,给生产带来严重影响。
对润滑油加氢补充精制装置的腐蚀情况进行分析和防护措施的研究显得尤为重要。
本文旨在对润滑油加氢补充精制装置的腐蚀问题进行全面的分析,并提出相应的防护措施,以保障设备的正常运行和延长其使用寿命。
首先将深入探讨润滑油加氢补充精制装置腐蚀的机理和类型,分析腐蚀产生的原因,为后续的防护措施提供理论基础。
随后将重点讨论润滑油加氢补充精制装置腐蚀的防护技术和措施,结合实际案例进行研究,探讨最有效的防护策略。
最后对润滑油加氢补充精制装置腐蚀分析及防护措施进行总结,为相关行业提供参考和借鉴。
通过本文的研究,期望能有效解决润滑油加氢补充精制装置腐蚀问题,提高设备的稳定性和可靠性。
2. 正文2.1 润滑油加氢补充精制装置腐蚀机理分析润滑油加氢补充精制装置在运行过程中,经常会受到腐蚀的影响,而了解其腐蚀机理是有效预防和防护的关键。
润滑油加氢补充精制装置腐蚀的主要机理包括化学腐蚀、电化学腐蚀和微生物腐蚀。
化学腐蚀是由原料油、加热介质和催化剂中的酸性物质造成的,这些酸性物质与金属表面发生反应导致金属失去电子,产生金属离子而发生腐蚀。
电化学腐蚀则是由金属表面与介质中的离子发生电化学反应引起的,包括阳极腐蚀和阴极腐蚀。
微生物腐蚀是由微生物在介质中繁殖生长并产生酸性物质,进而导致金属表面腐蚀。
了解润滑油加氢补充精制装置腐蚀的机理有助于我们选择合适的防护措施和技术,有效预防和延缓腐蚀的发生和发展。
在设计和运行过程中,必须重视腐蚀机理的分析,以确保装置的安全稳定运行。
2.2 润滑油加氢补充精制装置腐蚀类型及原因润滑油加氢补充精制装置在运行过程中容易出现腐蚀问题,主要的腐蚀类型包括晶间腐蚀、点蚀腐蚀、磁滋蚀、热蚀等。
基于加氢裂化装置的腐蚀分析和防腐对策

基于加氢裂化装置的腐蚀分析和防腐对策加氢裂化装置是石油化工行业中常见的重要装置之一,其主要用于将重质原油分解为较轻的产品,如汽油、煤油和润滑油等。
由于加氢裂化装置在工作过程中接触到高温、高压和腐蚀性物质,因此会产生腐蚀问题。
本文将对加氢裂化装置的腐蚀进行分析,并提出相应的防腐对策。
加氢裂化装置中的主要腐蚀类型包括:金属腐蚀、酸性腐蚀和高温腐蚀等。
金属腐蚀是因为装置内部金属材料与化学反应物接触而产生的腐蚀现象。
这种腐蚀主要是由于装置内存在酸性物质,如硫酸和盐酸等,而金属的腐蚀速度取决于腐蚀介质的酸碱性和温度等因素。
酸性腐蚀是因为装置内酸性介质的存在而引起的腐蚀现象。
酸性物质会对金属表面产生腐蚀,如金属的表面被腐蚀掉一层,从而影响装置的结构和性能。
高温腐蚀是由于装置在高温条件下运行时,金属材料与高温气体发生反应而产生的腐蚀现象。
高温腐蚀会导致金属材料的失效,使装置的寿命大大降低。
为了防止加氢裂化装置的腐蚀问题,可以采取以下防腐对策:1. 选择适合的材料。
在装置设计和制造过程中,应选择抗腐蚀性能良好的材料,如不锈钢、耐酸钢和镍基合金等。
2. 表面涂层。
可以对装置内部金属表面进行涂层处理,如喷涂耐酸性涂料或涂覆陶瓷材料,以提高金属的抗腐蚀性能。
3. 控制介质的酸碱性。
通过调整加氢裂化装置内介质的酸碱性,使其处于适宜的范围内,可以减少金属与酸性物质的接触,从而降低腐蚀速度。
4. 控制温度和压力。
合理控制装置的工作温度和压力,使其在安全范围内运行,减少高温和高压对金属的腐蚀作用。
5. 定期检查和维护。
定期对装置进行检查和维护,及时发现和修复装置内部的腐蚀问题,以延长装置的使用寿命。
通过以上防腐对策的实施,可以有效减少加氢裂化装置的腐蚀问题,提高装置的安全性和稳定性,并延长装置的使用寿命。
提高炼油加氢装置设备防腐蚀的管控能力
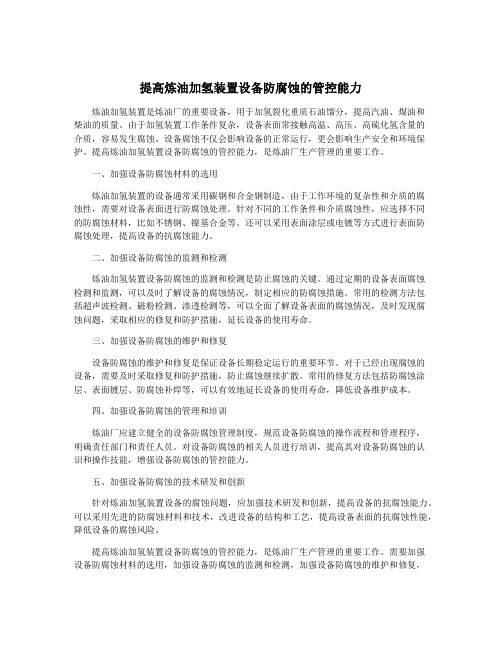
提高炼油加氢装置设备防腐蚀的管控能力炼油加氢装置是炼油厂的重要设备,用于加氢裂化重质石油馏分,提高汽油、煤油和柴油的质量。
由于加氢装置工作条件复杂,设备表面常接触高温、高压、高硫化氢含量的介质,容易发生腐蚀。
设备腐蚀不仅会影响设备的正常运行,更会影响生产安全和环境保护。
提高炼油加氢装置设备防腐蚀的管控能力,是炼油厂生产管理的重要工作。
一、加强设备防腐蚀材料的选用炼油加氢装置的设备通常采用碳钢和合金钢制造,由于工作环境的复杂性和介质的腐蚀性,需要对设备表面进行防腐蚀处理。
针对不同的工作条件和介质腐蚀性,应选择不同的防腐蚀材料,比如不锈钢、镍基合金等。
还可以采用表面涂层或电镀等方式进行表面防腐蚀处理,提高设备的抗腐蚀能力。
二、加强设备防腐蚀的监测和检测炼油加氢装置设备防腐蚀的监测和检测是防止腐蚀的关键。
通过定期的设备表面腐蚀检测和监测,可以及时了解设备的腐蚀情况,制定相应的防腐蚀措施。
常用的检测方法包括超声波检测、磁粉检测、渗透检测等,可以全面了解设备表面的腐蚀情况,及时发现腐蚀问题,采取相应的修复和防护措施,延长设备的使用寿命。
三、加强设备防腐蚀的维护和修复设备防腐蚀的维护和修复是保证设备长期稳定运行的重要环节。
对于已经出现腐蚀的设备,需要及时采取修复和防护措施,防止腐蚀继续扩散。
常用的修复方法包括防腐蚀涂层、表面镀层、防腐蚀补焊等,可以有效地延长设备的使用寿命,降低设备维护成本。
四、加强设备防腐蚀的管理和培训炼油厂应建立健全的设备防腐蚀管理制度,规范设备防腐蚀的操作流程和管理程序,明确责任部门和责任人员。
对设备防腐蚀的相关人员进行培训,提高其对设备防腐蚀的认识和操作技能,增强设备防腐蚀的管控能力。
五、加强设备防腐蚀的技术研发和创新针对炼油加氢装置设备的腐蚀问题,应加强技术研发和创新,提高设备的抗腐蚀能力。
可以采用先进的防腐蚀材料和技术,改进设备的结构和工艺,提高设备表面的抗腐蚀性能,降低设备的腐蚀风险。
加氢裂化装置的腐蚀与防护

加氢裂化装置的腐蚀与防护加氢裂化是炼油厂重要的二次加工手段,可以获得高质量的轻质燃料油。
其特点是对原料适应性强,可加工直镭重柴油、催化裂化循环油、焦化镭出油,甚至可以用脱沥青重残油生产汽油、航煤、和低凝点柴油。
其次,生产方案灵活,可根据不同的季节改变生产方案,并且产品质量好,产品收率高。
加氢裂化操作条件:温度380-450°C,操作压力8-20Mpa,采用的催化剂含有Pt、Pd、W、Mo、Ni、Co等金属氧化物作为加氢组分,以硅酸铝、氟化氧化铝或结晶硅铝酸盐为载体。
原料油经加氢、裂化、异构化等反应转化为轻油产品,收率一般可达100%(体积),可以获得优质重整原料、高辛烷值汽油、航煤、和低凝点柴油,同时产品含硫、氮、烯坯低,安定性好。
加工含酸、高酸原油主要对原料油进料系统有严重影响,加氢反应器也应选择防护措施。
6.1腐蚀形态6.1.1氢损伤高温高压条件下扩散在钢中的氢与钢中不稳定的碳反应生成甲烷,可引起钢的内部脱碳,甲烷不能从钢中逸出,聚集在晶界及其附近的空隙、夹杂物等不连续处,压力不断升高,形成微小裂纹和鼓泡,钢材的延展性、韧性等显著降低,随之变成较大的裂纹,致使钢最终破坏。
因为路铝钢具有良好的高温力学性能和抗氢损伤性能,近年来加氢反应器大多选用2.25CrlMo 钢制造。
6.1.2堆焊层氢致开裂在高温高压的氢气氛中,氢气扩散侵入钢材,当反应器停工冷却过程中,温度降至150°C以下时,由于氢气来不及向外释放,钢中吸藏了一定量的氢,这样在一定条件下就有可能发生开裂。
裂纹的产生和钢中的氢气含量有很大关系,曾经有实验证明,停工7个月后的加氢反应器,堆焊层仍有29ppm的氢含量,在堆焊层上取样进行弯曲实验,弯曲角度在19-750范围内试样就发生了开裂,取试样进行脱氢处理后,试样中氢含量降到1.2ppm,试样弯曲到1800也没有发生开裂。
实验证明了氢脆的危害性,同时也证明了氢脆是可逆的。
- 1、下载文档前请自行甄别文档内容的完整性,平台不提供额外的编辑、内容补充、找答案等附加服务。
- 2、"仅部分预览"的文档,不可在线预览部分如存在完整性等问题,可反馈申请退款(可完整预览的文档不适用该条件!)。
- 3、如文档侵犯您的权益,请联系客服反馈,我们会尽快为您处理(人工客服工作时间:9:00-18:30)。
润滑油加氢装置的腐蚀影响及对策
第33卷第4期石油与天然气化工259
润滑油力口氢装置帕腐蚀影响及对策
田晓龙黄坤
(兰州石化公司炼油厂)
摘要润滑油加氢装置由于原料性质的变化,不仅设备腐蚀问题严重导致非计划停工时间增加,
而且影响到产品质量.简要阐述了润滑油加氢装置的腐蚀机理,并针对腐蚀问题,采取在塔顶挥发线,
回流罐等易腐蚀部位增注缓蚀剂,完善化学防腐设施,优化脱H2S汽提塔工艺条件,提高H2S脱除率等
措施.经过生产验证,效果比较明显,达到了缓解装置腐蚀的目的.
关键词腐蚀H2s化学防腐脱除率硫含量
兰州石化公司炼油厂润滑油加氢装置是采用临氢
转化工艺生产高质量润滑油基础油的高压加氢装置.
1997年建成投产后,受各种因素影响造成装置非计划
停工时有发生.例如,1999年装置全年开工4464h,非
计划停工821h,其中设备腐蚀问题造成的停工时间达
到536h.经过技术攻关,车间采取在减压塔,产品汽
提塔顶等易发生腐蚀的部位,注入SF一121B缓蚀剂,
完善装置防腐设施;同时优化脱H,s汽提塔工艺条件,
提高H2s脱除率,降低分馏塔原料硫含量等措施,来解
决设备腐蚀问题.经过近几年来的生产运行可认为,
效果明显,达到了预期目的,确保了高质量润滑油基础
油的生产,装置技术优势得以发挥.
1装置腐蚀机理及现状
1.1腐蚀机理
润滑油加氢装置腐蚀的原因,主要是高含硫原料
中各类含硫化合物生成的H2s和各类盐水解生成的HCI.在加热过程中,H,S和HCI随原料中的轻组分和
水蒸汽一起上升至塔顶并馏出.当进一步挥发冷凝,
H2s和HCI聚集在蒸馏装置顶部轻油活动区的低温部位,特别是在气一液两相转变的地方.因S和HCI
溶于冷凝水,只要相对含量达到100×10-6(∞)左右,
pH值会下降到2~3,形成强烈的电化学腐蚀.如不
采取措施,碳钢的腐蚀程度可高达20mm/a.由于润
滑油加氢过程能产生大量的H2S,原料中也含有含Cl一的有害杂质,所以极易产生化学腐蚀.
即使FeS在钢铁表面形成具有保护作用的硫化
膜,但是在高流速的介质冲刷和环烷酸存在的情况下, 硫化膜就会被破坏,生成环烷酸铁,造成进一步的腐
蚀,反应方程式为:
Fe+H,S—FeS+
2R—COOH+FeS"-*Fe(R—coo)2+H2S
1.2装置腐蚀现状
目前装置脱H2s汽提塔顶,常压塔顶注缓蚀剂sF
一
121B,取得了良好的防腐效果.减顶冷却器和产品
汽提塔顶冷凝器等设备没有注入缓蚀剂.1999年初
开工过程中,发现减压塔顶水冷器E205A/B,E207,
E208和产品汽提塔顶水冷器E304,E305腐蚀均十分
严重,腐蚀物经化验分析为FeS,其中E304,E305,E208 三台水冷器被迫更换管束,减压塔抽空器喉管(锡青
铜)也腐蚀穿透,检修费用高达15万元.我们结合脱
H2S汽提塔顶,常压塔顶注缓蚀剂SF一121B的经验, 提出在减压塔顶及产品汽提塔顶注缓蚀剂以减缓腐蚀
速率.
2装置化学防腐措施
由于装置设计原料是以北疆油为主的新疆混合原
油,而随着近年来我厂进厂原油的变化,南疆油比例已经大大高于北疆油,硫含量随之大幅度提高,目前原料与设计原料硫含量对比见表1.
表1原料硫含量设计值与实际值
项目设计值实际值
原料LVGoHVGoDA0IlVGO}n,GODA0
S,∞,%0.080.100.220.380.330.28
从表1中可以看出,原料中硫含量均高于设计值.
以LVGO为例,平均是设计值的3.6倍,最高达5倍.
原设计中正常生产需补充CS2以维持循环氢中H2S浓度保持800×10I6(∞)左右.由于原料中硫含量大大
高于设计值,在正常生产中未进行过补硫.另外,由于
硫含量严重超标,循环氢中H,s浓度达(3000~7500)
260润滑油加氢装置腐蚀影响及对策
×10I6(叫),使得H2S含量在整个产品中都有明显增加,在粗石脑油与汽油中表现得尤为明显,有关数据见表2.
表2设计,实际值对比
从表2中可看出,循环氢中H2S浓度在脱H2S汽
提塔C101进料中增大l3倍,在汽油中增大24~108 倍,由此可推断常压塔进料中H2s含量大幅度增加,进而造成减压塔及产品汽提塔进料中H2S浓度增加.这与水冷器E205A/B,E207,E208,E304,E305腐蚀严重
和减顶抽空器喉管(锡青铜)腐蚀穿透相吻合.1999
年初开工减压产品的平均硫含量分布见表3.
表3减压产品硫含量分布
在原设计中,减一,二,三线,减底硫含量应小于
20×10I6().根据表3可知,目前减压产品硫含量
均比设计值大2~3倍,设备腐蚀必然更为严重.如果本装置腐蚀问题不解决,水冷器腐蚀穿透,油气串人循环水,会给下游装置带来极大危害,发生安全事故.同
时加氢装置处于高温,高压,临氢状态操作,减压部分
如果发生腐蚀穿透,空气倒窜人塔,其后果不堪设想. 由于润滑油加氢装置原料硫含量比设计值高3~5倍, 原设计仅在脱H2S汽提塔C101,常压塔C201顶增注缓蚀剂.因此,在目前状况下,应给C204顶,C301,
C302顶增设配套防腐设备,完成装置多点化学防腐, 多点注人工作.根据常压塔顶,脱H2S汽提塔顶防腐
经验,确定缓蚀剂仍采用SF一121B,完成对新增缓蚀剂贮罐和计量泵选型及施工.
在检修中同时发现已经注入缓蚀剂的汽提塔顶空冷,回流罐及常压塔顶水冷器,空冷,回流罐未发生明
显腐蚀,这正是通过采用化学防腐注缓蚀剂进行保护而取得的效果.
3优化脱H2s汽提塔C101工艺条件
3.1C101存在的问题
C101承担着装置H2S汽提脱除的主要任务,脱
H2S效果的好坏将直接关系到后续工段进料中硫含量的高低,而且将影响到后续工段的设备腐蚀.由于原
料硫含量增高,车间曾组织技术攻关,对该塔进行改造,将精馏段6层塔盘全部更换为50号矩鞍环填料, 把提馏段塔盘浮伐由8个改为l6个,希望提高H2S脱除率.但是C101改造之后,一直沿用原操作参数,在
生产中不能完全适应要求,因此需要摸索新的工艺条
件.
3.2优化C101工艺条件
由于C101的进料温度,塔顶压力,汽提量对汽提
塔脱除H,S效果有较大影响,因此根据技术分析和实
际操作经验,决定按照不同的操作参数进行试验,以确
定最佳的工艺条件,操作参数见表4.
表4操作参数表
按照确定的参数,进行了严格的正交试验,得出三
个参数对H2S脱除率的影响顺序为汽提量影响最大,
塔顶压力次之,进料温度最小.并得到最佳的工艺条
件:塔进料温度180~(2,塔顶压力0.1MPa,汽提量150
kg/h.装置进行实施后,脱硫效果明显改善,在各馏分
中硫含量明显下降,优化前减底油硫含量55×10I6
(),优化后硫含量达到35×10I6()比优化前下降
了20×10一().
4结论
(1)化学防腐设施完善后,装置实现了多点注剂,
减压塔C204顶,产品汽提塔C301顶腐蚀减缓,1999年
后未发生一起因上述设备腐蚀造成的停工.
(2)设备检修周期由2次/年延长至1次/年,可
节约检修费用15万元.
(3)提高装置生产的安全系数,最大程度地消除
事故隐患.
作者简介
田晓龙:工程师,1995年毕业于华东石油大学炼制系石油加工专业.现在兰州石化公司炼油厂工作.
收稿日期:2O04—02—27
编辑:杨兰。