WM_第1章 汽车左右门板大型注塑模设计实例
汽车注塑模具设计全图解教程案例介绍(系统)
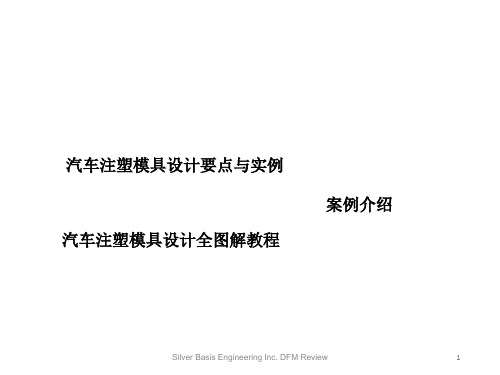
18
内分型核心技术
Silver Basis Engineering Inc. DFM Review
19
如上图所示,为汽车内分型保险杠二次变轨(又称双节变轨)运行轨迹图,共4种 运行轨迹,分别为a,b,c,d四种。下面详细分析4种二次变轨运动轨迹: 图a所示分为3段,分别为L1,L2,L3。 横向斜顶由运动导轨控制其运动,在L1这段距离内,横向斜顶保持不变。 在L2这段距离内,横向斜顶向内拉动制品变形,脱出定模倒扣。
用。
对于汽车保险杠塑件,一般有外分型与内分型两种分型方式。针对所有的汽车 保险杠两侧的大面积倒扣,即可以采用外分型也可以采用内分型。这两种分型方式 的选择主要取决于最终客户汽车主机厂对保险杠的要求,一般欧美汽车大多采用内 分型技术,日系汽车大多采用外分型。两种分型方式各有优缺点,外分型的保险杠 需要处理夹线,增加了加工工序,但外分型保险杠在模具成本与技术难度要低于内 分型保险杠。内分型的保险杠通过二次变轨轨道控制技术,一次性完美的将保险杠 注塑出来,从而保证了保险杠的外观质量,节省了塑件加工工序与加工成本。但缺
接着继续运行,横向斜顶保持不变,制品脱离大斜顶。在L3这段距离内,制品完成 脱模,接着机械手取件。
图b所示分为4段,分别为L1,L2,L3,L4。 1. 横向斜顶由运动导轨控制其运动,在L1这段距离内,横向斜顶保持不变。
2. 在L2这段距离内,横向斜顶在向内拉动制品变形,脱出定模倒扣。 3. 接着继续运行,横向斜顶保持不变,在L3这段距离内,制品脱离大斜顶。
Silver Basis Engineering Inc. DFM Review
图d所示分为4段,分别为L1,L2,L3,L4。
塑料注射模具设计与制造实例解析

根据调试结果,对模具进行修 正和调整,如修整浇口、调整
型芯位置等。
模具验收与交付
外观检查
检查模具外观是否无明显缺陷,各部分尺寸 是否符合设计要求。
文件资料
核对模具文件资料是否齐全,包括设计图纸 、装配图、调试记录等。
功能测试
对模具进行注射、冷却、开模等动作测试, 确认功能正常。
交付与培训
3
数控机床加工实例解析
以具体的数控机床加工实例说明其应用和效果。
其他制造工艺与实例解析
其他制造工艺简介
介绍其他模具制造工艺的原理和特点。
其他制造工艺流程
详细描述其他制造工艺的流程和步骤。
其他制造工艺实例解析
以具体的其他制造工艺实例说明其应用和效果。
03
模具装配与调试实例解析
模具装配流程与要点
准备工作
4. 实例效果:模具制造周期适中,注射成型效率 较高。制品表面质量较好,能满足使用要求。
实例三:多腔塑料注射模具设计与制造
1. 模具类型:多型腔模具
2. 设计特点:模具结构非常 复杂,但能进一步提高生产 效率。浇口设计在模具顶部 ,通过多个分流道将熔融塑 料注入各个型腔。制品为多 个相同的小盒子形,排列整 齐。
实例二:复杂塑料制品注射模具设计与制造
1. 模具类型:双型腔模具
3. 制造工艺:使用数控铣床和钻床进行加工,组 装时使用定位销和螺丝进行定位。浇口处使用拉 杆和顶杆组合顶出制品。
2. 设计特点:模具结构较复杂,但能提高生产效 率。浇口设计在模具侧面,适应复杂制品的结构 。制品为带有多个凸起的盒子形,表面结构复杂 。
3. 制造工艺:使用数控铣床 和钻床进行加工,组装时使 用定位销和螺丝进行定位。 浇口处使用顶杆和拉杆组合 顶出制品。
塑料注射模设计实例

第10页/共27页
二、模具结构方案设计
4、成型零件结构设计
(2)型芯:整体式?整体+局部镶入式?
➢型芯整体式
▪优点:曲面过渡圆滑;拼接痕迹少;冷却 系统易开设; ▪缺点:结构复杂、制造难度大,电火花加 工量大,加工时间长。
➢整体型芯+局部镶入式
▪既具有整体式的优点,又改善了局部制造 工艺(如圆形小型芯);但冷却系统开设 受一定限制。
➢薄壁深腔罩形件——推件板推出; ➢内部筋多、管形凸台多——推杆、推管推出;
➢螺纹部分——哈夫分型脱模;
➢综合考虑:推件板推出为主,高管形凸台采 用推管推出辅助。 ➢结论:推件板+推管联合推出
第13页/共27页
二、模具结构方案设计 6、侧向分型抽芯结构设计
➢开口端部外螺纹——矩形螺牙,螺距和牙尺寸较大,成型容易; ➢自动脱螺纹:螺纹成型精度高,但机构复杂,模具造价高 ➢斜滑块分型:导滑与推出机构设计难度较大,斜滑块冷却系统难以设置;推出 机构应改为推块推出才行。
▪注射容量:811cm3 锁模行程:1145mm
▪注射压力:150MPa 模板尺寸:840×840
▪注射行程:230
导柱间距:560×560
▪喷嘴半径:10mm
最小容模厚度:200mm
▪喷嘴孔径:3.5mm
最大容模厚度:640mm
▪定位圈直径:120mm 顶出力:73kN
Байду номын сангаас
▪锁模力:2500kN
顶出行程:125mm
第5页/共27页
细小 深槽
二、模具结构方案设计 1、分型面选择
➢选在塑件最大轮廓面上——可选A-A、B-B或C-C; ➢避免侧抽芯及长抽芯距——可选A-A或C-C; ➢便于充模排气——可选A-A或C-C ➢便于脱模——可选A-A;螺纹部分选B-B为好 ;
wgqsgm塑料注射模具制造与实例
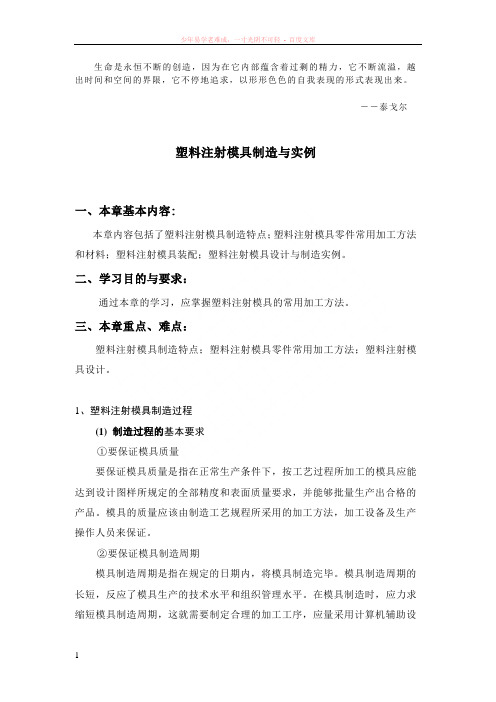
生命是永恒不断的创造,因为在它内部蕴含着过剩的精力,它不断流溢,越出时间和空间的界限,它不停地追求,以形形色色的自我表现的形式表现出来。
--泰戈尔塑料注射模具制造与实例一、本章基本内容:本章内容包括了塑料注射模具制造特点;塑料注射模具零件常用加工方法和材料;塑料注射模具装配;塑料注射模具设计与制造实例。
二、学习目的与要求:通过本章的学习,应掌握塑料注射模具的常用加工方法。
三、本章重点、难点:塑料注射模具制造特点;塑料注射模具零件常用加工方法;塑料注射模具设计。
1、塑料注射模具制造过程(1) 制造过程的基本要求①要保证模具质量要保证模具质量是指在正常生产条件下,按工艺过程所加工的模具应能达到设计图样所规定的全部精度和表面质量要求,并能够批量生产出合格的产品。
模具的质量应该由制造工艺规程所采用的加工方法,加工设备及生产操作人员来保证。
②要保证模具制造周期模具制造周期是指在规定的日期内,将模具制造完毕。
模具制造周期的长短,反应了模具生产的技术水平和组织管理水平。
在模具制造时,应力求缩短模具制造周期,这就需要制定合理的加工工序,应量采用计算机辅助设计(CAD)和计算机辅助制造(CAM)。
③要保证模具使用寿命模具的使用寿命是指模具在使用过程中的耐用程度,一般以模具生产出的合格制品的数量作为衡量标准。
高的使用寿命反应了模具加工制造水平,是模具生产质量的重要指标。
④要保证模具成本低廉模具成本是指模具的制造费用。
由于模具是单件生产,机械化、自动化程度不高,所以模具成本较高。
为降低模具的制造成本,应根据制品批量大小,合理选择模具材料,制定合理的加工规程,并设法提高劳动生产率。
⑤要提高模具的加工工艺水平模具的制造工艺要根据现有条件,尽量采用新工艺、新技术、新材料,以提高模具的生产效率,降低成本,使模具生产有较高的技术经济效益和水平。
⑥要保证良好的劳动条件模具的制造工艺过程要保证操作工人有良好的劳动条件,防止粉尘、噪音、有害气体等污染源产生。
注塑模具设计实例

注塑模具设计实例注塑模具是注塑成型过程中的重要工具,它决定了产品的形状、尺寸和质量。
下面将介绍一个注塑模具设计实例。
该注塑模具用于生产一个塑料小零件,产品尺寸为25mm × 10mm × 5mm。
根据客户要求,模具设计师需要考虑以下几个方面:1.产品结构设计:根据产品尺寸和功能要求,模具设计师需要确定模具中的产品结构。
在这个实例中,小零件是一个封闭的长方体,底部有一个孔。
设计师结合注塑工艺和产品功能要求,选择了一种单腔模具结构。
这个结构能够满足产品形状和尺寸的要求,同时保证注塑成型的稳定性。
2.模具材料选择:模具的材料选择直接影响着模具的使用寿命和成本。
根据产品的使用环境和注塑工艺要求,设计师选择了优质的冷作模具钢作为模具材料。
这种钢材具有良好的切削性能和耐磨性,可以满足长时间连续生产的需求。
3.注塑工艺参数:注塑模具的设计需要考虑注塑工艺的各个参数,如注塑温度、保压时间、保压压力等。
在这个实例中,设计师根据塑料材料的熔体温度和流动性选择了适当的注塑温度和保压时间。
同时,根据产品的厚度和尺寸,设计师设定了合适的保压压力,以确保产品的成型质量。
4.模具结构设计:模具结构的设计需要考虑产品的成型要求和模具的制造工艺。
在这个实例中,设计师在模具上设置了合适的冷却水道和顶针机构,以确保注塑成型过程中的温度控制和产品的尺寸稳定。
同时,设计师在模具上设置了合适的排气装置,以避免产品出现气泡和缺陷。
5.模具制造和组装:根据设计图纸,模具制造师使用数控机床进行模具加工。
首先进行粗加工,然后进行精细加工和装配。
在模具加工和组装过程中,需要进行严格的尺寸和工艺控制,以确保模具的精度和质量。
综上所述,注塑模具设计需要综合考虑产品结构、模具材料、注塑工艺、模具结构以及模具制造和组装等方面的因素。
通过合理设计和制造,注塑模具可以满足产品的形状、尺寸和质量要求,提高注塑成型的效率和稳定性。
注塑模具毕业设计例

塑件成型工艺分析塑件图塑件的视图如图1-1所示:塑件的工艺分析产品名称:衬套产品材料:球墨铸铁产品特点:球墨铸铁就是通过球化与孕育处理得到球状石墨,有效地提高了铸铁的机械性能,特别就是提高了塑性与韧性,从而得到比碳钢还高的强度。
塑件材料使用特性及用途球墨铸铁就是20世纪五十年代发展起来的一种高强度铸铁材料,其综合性能接近于钢,正就是基于其优异的性能,已成功地用于铸造一些受力复杂,强度、韧性、耐磨性要求较高的零件。
球墨铸铁已迅速发展为仅次于灰铸铁的、应用十分广泛的铸铁材料。
所谓“以铁代钢”,主要指球墨铸铁。
2拟定模具结构形式2、1 型腔数目的确定为了制模具与注射机的生产能力相匹配,提高生产效率与经济性,并保证塑件精度,模具设计时应确定型腔数目。
模具的型腔数可根据塑件的产量、精度高低、模具制造成本以及所选用注射机的最大注射量与锁模力大小等因素确定。
小批量生产,采用单型腔模具;大批量生产,宜采用多型腔模具。
但如果塑件尺寸较大时,型腔数将受所选用注塑机允许最大成型面积与注塑量的限制。
由于多型腔模的各个型腔的成型条件以及熔体到达各型腔的流程难以取得一致,所以塑件精度较高时,一般采用单型腔模具。
该塑件精度要求不高,又就是大批量生产,采用一模四件。
2、2 分型面的选择1) 分型面就是指分开模具能取出塑件与浇注系统凝料的可分离的接触表面。
合理地选择分型面对于塑件质量、模具制造、与使用性能都有着很大的影响,模具设计时应根据塑件的结构、尺寸精度来设计。
2) 不要设在塑件要求光亮平滑的表面或带圆弧的转角处,以免意料飞边、拼合痕迹影响塑件外观。
3) 开模时,尽量使塑件留在动模一边,一般在动模边设脱模机构较为方便。
4) 尽力保证塑件尺寸的精度要求。
5) 应有利于侧面分型与抽芯。
6) 尽量使分型面位于料流末端,以利于排气。
7) 尽量使模具加工方便。
由于本塑件的结构形状较为简单,只应在塑件最大轮廓处。
如图所示:注塑机型号的确定副模具都只能安装在与其相适应的注塑机上方能生产。
26347992_轿车左、右内扶手注塑模结构方案可行性分析与设计

作者简介:熊利军(1976-)男,高级工程师,本科,主要从事模具设计制造和管理工作。
收稿日期:2021-09-030 引言左、右内扶手是轿车的一种零部件,其注塑模的设计,首先必须进行左、右内扶手形体要素的可行性分析。
此次再要根据每项形体分析的要素制订出模具结构的方案,还需要对注塑模结构方案进行成型的左、右内扶手产生的缺陷进行预期分析,并需要将所有模具结构方案分析的结论进行协调。
最后,才能是注塑模结构的设计和造型,只有这样才能避免造成注塑模结构设计的失误。
1 左、右内扶手的形体要素可行性分析左、右内扶手是轿车的一种零部件,那就应该是属于大批量生产的性质。
右内扶手形体要素分析,如图1(a )所示;右内扶手造型,如图1(b )所示;左内扶手与右内扶手对称。
材料为:PA6+GF30,收缩率为1.004%。
右内扶手形体要素分析如下:右内扶手形体存在着:Φ5.2 mm 、Φ5.2 mm 、2×Φ6.8 mm 、4×Φ6.8 mm 型孔要素与2 mm×6 mm×2×R 腰字型孔要素;2×2 mm×3 mm×5.5 mm 型槽要素[1];2×R1 mm 弓形高障碍体要素[2];还存在着正面外观要素及大批量要素[3];上述形体要素是决定注塑模结构的要素。
2 左、右内扶手注塑模结构方案可行性分析注塑模结构方案的制订,是根据注塑件的形体要素来制订的。
只要能找出上述每项形体要素的解决措施,就能制订出左、右内扶手注塑模结构方案,再要制订出该模具方案成型加工时预测左、右内扶手缺陷的处置措施。
左、右内扶手可同时在一副模具中成型,该模具为一模两腔。
对于左、右内扶手周边存在着R1 mm 弓形高障碍体要素,可以在沿弧面切点处设置分型面来避开对注塑件脱模的阻挡。
由于型孔要素的轴线平行开闭模方向,成型这些型孔的型芯可以镶嵌在定模型芯中,利用定、动的闭合实现型芯的复位,模具的开启实现型芯的抽芯。
汽车内外板模具设计

2 汽车内外板覆盖件拉延模模具2.1 拉延模具概述拉延模是保证制成合格覆盖件最主要的装备。
其作用是将平板状毛料经过拉延工序使之成型为立体空间工件。
拉延模有正装和倒装两种型式。
正装拉延模和凸模和压料圈在上,凹模在下,它使用双动压力机,凸模安装在内滑块上,压料圈安装在外滑块上,成型时外滑块首先下行,压料圈将毛料紧紧压在凹模面上,然后内滑块下行,凸模将毛料引伸到凹模腔内,毛料在凸模、凹模和压料圈的作用下进行大塑性变形。
倒装拉延模的凸模和压料圈在下,凹模在上,它使用单动压力机,凸模直接装在下工作台上,压料圈则使用压力机下面的顶出缸,通过顶杆获得所需的压料力。
倒装型式拉延模只有在顶出压力能够满足压料需要的情况下方可采用。
此次设计我所选的就是后面一种即倒装型式拉延模。
在设计的过程中,首先要明确拉延模模具的组成。
(1)成型零件——凸模、凹模(2)压边圈(3)导向装置(4)调压装置(5)气顶装置(6)模具起吊装置拉延模的导向分为内导向和外导向。
外导向是指压料圈和凹模之间的导向,内导向是指压料圈和凸模之间的导向。
而常用的导向零件有导向板、导向块、和背靠块三种。
由于导向装置是置于压边圈内侧,所以此次设计将采用内导向的导向板导向。
导向板结构尺寸如图2-1所示。
导向板材料为T8A,淬火硬度HRC53~57。
2.2 工艺性分析和初步确定方案2.2.1 工艺性分析工艺设计是在模具设计制造之前的技术准备工作,其主要内容有以下几项:1)根据生产纲领确定工艺方案;2)根据覆盖件结构形状,分析成型可能性和确定工序数及模具品种;3)根据装配要求确定覆盖件的验收标准;4)根据工厂条件决定模具使用的压床;5)根据制造要求确定协调方法;6)提出模具设计技术条件,其中包括结构要求、材料要求等。
工艺设计内容是贯彻执行生产纲领的具体要求和体现,是生产纲领和模具设计制造之间的桥梁和纽带。
工艺设计要求方案正确、内容可靠、符合实际和实施容易,不允许有任何大的漏洞。
汽车注塑模具设计全图解教程

经典模图-X01-结构分析
产品开模后顶针板带动整个行位一起顶出
6
经典模图-X01-结构分析
步骤1
步骤2
产品顶出一定高度后,油缸带动直顶块将产品从
行位镶件上强脱。
7
经典模图-X02
行位走斜顶
8
9
经典模图-X02-产品分析 此产品这几处的倒扣为特殊结构,不好出模
10
经典模图-X01-结构分析 前模斜顶
汽车注塑模具设计要点与实例 汽车注塑模具设计全图解教程
SilverBasisEngineeringInc.DFMReview 1 1 1
《汽车注塑模具设计全图解 教程》-预订会员赠送图档及
资料介绍
2
3
经典模图-X01
横向顶出
4
经典模图-X01-产品分析
产品此次倒扣常规行位无法出模,需利用行位顶 出,再油缸带动推块横向顶出产品 5
动,不会干涉。
29
经典模图-X106-结构分析 底板先开20,脱镶针,斜抽行位有运动空间
经典模图-X01-结构分析 ຫໍສະໝຸດ -B板开69,扣鸡限位,给斜抽预留空间
经典模图-05结构分析 托板与B板开65脱外侧行位,此时A-B板继续开模
经典模图-05结构分析 先合A-B板→再合外侧行位→合底板镶针回位
经典模图-X05-结构分析
步骤2
后模芯子继续脱开后, 为行位运动留开空间。
步骤3 行位向内侧运动脱扣 25
经典模图-X06
缩针—斜抽
26
27
经典模图-X06-产品分析
产品此处倒扣需斜抽,而后模镶针垂直出模,与 斜抽方向干涉,为本案例难点
28
经典模图-X06结构分析
汽车门板注塑工艺分析及其注射模设计

汽车门板注塑工艺分析及其注射模设计随着汽车制造技术水平的不断进步,人们对降低汽车能耗提出了越来越高的要求,这为塑料制件在汽车行业的推广应用提供了广阔的发展空间。
近些年来,塑料制件在汽车生产中的应用比例越来越大。
目前汽车的内外饰件已基本实现塑料化,为汽车减轻重量、节约成本和降低油耗发挥着重要作用。
塑料制件需要普及,并提高技术质量,模具作为工业母体必然要先行。
以下以某车型汽车门板为例,阐述其制造工艺及相关注射模具设计要点。
通常汽车拥有前、后两车门,按照门板包皮套分类可分为包皮套和不包皮套,按照门板外形特征,可分为喇叭网和无喇叭网门板。
其中包皮套门板的产品表面质量要求较低,而不包皮套门板的外观件质量要求很高,如产品表面不允许有熔接线、不允许顶白、强度要求高而且无毛刺等。
门板工艺性分析门板作为汽车的内饰件产品,根据车型的不同,尺寸大小有所不同。
图1所示为某车型汽车左前门装饰板,产品最大尺寸为835mm×520mm×90mm ,形状比较复杂,表面有皮纹,其中产品螺丝柱共21处,围绕产品周边一圈分布有7处倒扣,内部所有加强筋模具尺寸为小端0.8mm 、大端1.1mm 。
为防止产品飞边,喇叭网孔全部做在定模上,角度为8°。
图1 产品动模侧平面根据以上工艺性要求,本产品实际生产中材料选用PP-T20,缩水率为1.2%,平均壁厚2.5mm,采用1600t注塑机注射成形。
模流分析根据以上的产品结构及工艺性要求分析,模具设计为一模一穴式结构。
接下来我们采用MOLDFLOW对其注塑工艺性进行仿真分析,根据产品形状和注塑工艺,模具采用3点大水口设计,并配备搭接式侧浇口,流道尺寸直径为14mm,用调结阀控制进浇速度。
浇口详细位置如图2所示。
图2 热流道浇口位置在冷却系统方面,冷却水路(图3)采用直通和水塔式设计,水路直径设置为14mm、水塔为30mm,热嘴附近分布水路,以增强模具冷却效果并调节模具温度,因此极大地缩短了冷却时间和生产周期,提高了生产效率。
冲压模具设计和制造实例
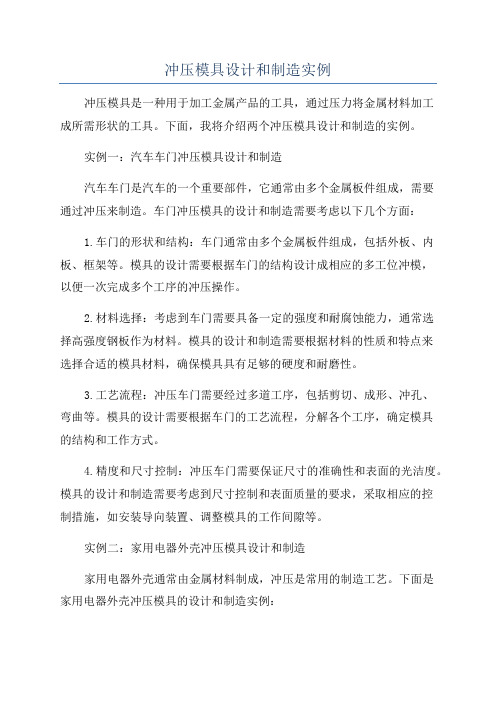
冲压模具设计和制造实例冲压模具是一种用于加工金属产品的工具,通过压力将金属材料加工成所需形状的工具。
下面,我将介绍两个冲压模具设计和制造的实例。
实例一:汽车车门冲压模具设计和制造汽车车门是汽车的一个重要部件,它通常由多个金属板件组成,需要通过冲压来制造。
车门冲压模具的设计和制造需要考虑以下几个方面:1.车门的形状和结构:车门通常由多个金属板件组成,包括外板、内板、框架等。
模具的设计需要根据车门的结构设计成相应的多工位冲模,以便一次完成多个工序的冲压操作。
2.材料选择:考虑到车门需要具备一定的强度和耐腐蚀能力,通常选择高强度钢板作为材料。
模具的设计和制造需要根据材料的性质和特点来选择合适的模具材料,确保模具具有足够的硬度和耐磨性。
3.工艺流程:冲压车门需要经过多道工序,包括剪切、成形、冲孔、弯曲等。
模具的设计需要根据车门的工艺流程,分解各个工序,确定模具的结构和工作方式。
4.精度和尺寸控制:冲压车门需要保证尺寸的准确性和表面的光洁度。
模具的设计和制造需要考虑到尺寸控制和表面质量的要求,采取相应的控制措施,如安装导向装置、调整模具的工作间隙等。
实例二:家用电器外壳冲压模具设计和制造家用电器外壳通常由金属材料制成,冲压是常用的制造工艺。
下面是家用电器外壳冲压模具的设计和制造实例:1.外壳结构和形状:家用电器外壳通常具有盒状结构,需要通过冲压来成形。
模具的设计需要根据外壳的尺寸和形状,设计成相应的单工位或多工位冲模。
2.材料选择:外壳通常采用不锈钢或者冷轧钢板作为材料,以保证外壳的强度和耐腐蚀能力。
模具的设计和制造需要选用适当的模具材料,以确保模具具有足够的硬度和耐磨性。
3.工艺流程:外壳冲压通常包括剪切、成形、冲孔、折弯等工序。
模具的设计需要分解各个工序,确定模具的结构和工作方式,以便一次完成所有工序。
4.精度和表面质量:外壳冲压需要保证尺寸的准确性和表面的光洁度。
模具的设计和制造需要考虑到尺寸控制和表面质量的要求,采取相应的控制措施,如安装导向装置、选用合适的冲头等。
汽车左右弯管注塑模设计毕业论文
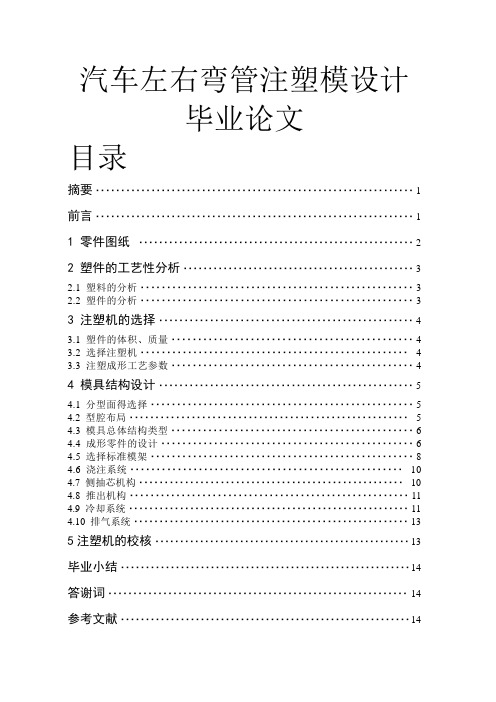
汽车左右弯管注塑模设计毕业论文目录摘要 (1)前言 (1)1零件图纸 (2)2塑件的工艺性分析 (3)2.1 塑料的分析 (3)2.2 塑件的分析 (3)3注塑机的选择 (4)3.1 塑件的体积、质量 (4)3.2 选择注塑机 (4)3.3 注塑成形工艺参数 (4)4模具结构设计 (5)4.1分型面得选择 (5)4.2型腔布局 (5)4.3模具总体结构类型 (6)4.4 成形零件的设计 (6)4.5选择标准模架 (8)4.6 浇注系统 (10)4.7 侧抽芯机构 (10)4.8 推出机构 (11)4.9 冷却系统 (11)4.10排气系统 (13)5注塑机的校核 (13)毕业小结 (14)答谢词 (14)参考文献 (14)1、零件图纸图1-1图1-2零件描述:汽车左/右弯管二维图如图1-1所示,三维图如图1-2所示。
1.1 塑件材料为ABS,收缩率为0.5%。
1.2 大批量生产,塑件表面不得有飞边毛刺、无银丝、无波浪、熔接痕最小、无缩痕、无气泡、无划伤和白斑等外观缺陷。
1.3 未注圆角为R21.4 表面粗糙度达到Ra1.61.5 未有尺寸按MT6级精度计算2、.塑件的工艺性2.1塑料品种:ABS颜色:白色基本特性:1、ABS是丙烯腈、丁二烯和苯乙烯的三元共聚物,A代表丙烯腈,B代表丁二烯,S代表苯乙烯。
ABS树脂是目前产量最大、应用最广泛的聚合物,它将PS、SAN、BS的各种性能有机地统一起来,兼具韧、硬、刚相均衡的优良力学性能。
ABS工程塑料一般是不透明的,外观呈浅象牙色、无毒、无味,兼有韧、硬、刚的特性,燃烧缓慢,火焰呈黄色,有黑烟,燃烧后塑料软化、烧焦,发出特殊的肉桂气味,但无熔融滴落现象。
2、ABS工程塑料具有优良的综合性能,有极好的冲击强度、尺寸稳定性好、电性能、耐磨性、抗化学药品性、染色性,成型加工和机械加工较好。
3、ABS树脂耐水、无机盐、碱和酸类,不溶于大部分醇类和烃类溶剂,而容易溶于醛、酮、酯和某些氯代烃中。
第一讲注塑模具设计实例

结论
1.熔融温度高且熔体粘度大,对于大于200g的塑件应用螺杆式 注射机成型,喷嘴宜用敞开式延伸喷嘴,并加热,严格控制模 具温度,一般在70~1200为宜,模具应用耐磨钢,并淬火; 2.水敏性强,加工前必须干燥处理,否则会出现银丝、气泡及 强度显著下降现象; 3.易产生应力集中,严格控制成型条件,塑件成型后需退火处 理,消除内应力;塑件壁不宜厚,避免有尖角、缺口和金属嵌 件造成应力集中,脱模斜度宜取20。
4.浇注系统方案设计
浇口直径:经验值0.4~2mm;经验公式
d kc4 A
(A--型腔的表面积;C—壁厚系数,)视物料性质和制件重量而定。
点浇口圆柱孔长度: 0.5~1.2㎜。
剪切速率控制在
•
4qv R3
≥
105s-1
塑料模设计及制造实例
三、注射模的结构设计
5.浇注系统尺寸设计
流道尺寸理论计算目的:计算流道最小尺寸;保证熔体有适当的流动速 率和恰当的压力损失。
塑料模设计及制造实例
三、注射模的结构设计
3.型腔数目的确定及型腔的排列
由于该塑件采用的是一模一件成型,所以,型腔布 置在模具的中间。这样也有利于浇注系统的排列和模具 的平衡。
4.浇注系统方案设计
⑴主流道设计 根据手册查得xs-zy-250型注射机喷嘴的 有关尺寸: 喷嘴球面半径R0=18mm 喷嘴孔直径:d0=φ4mm 根据模具主流与喷嘴的关系: R=R0+(1~2)mm d=d0+0.5 mm
塑料模设计及制造实例
三、注射模的结构设计
2.分型面的选择
在选择分型面时,根据分型面的选择原则,考虑不影响 塑件的外观质量以及成型后能顺利取出塑件,有两种分型面 的选择方案。
基于CADCAE的汽车车门内饰板注塑模设计
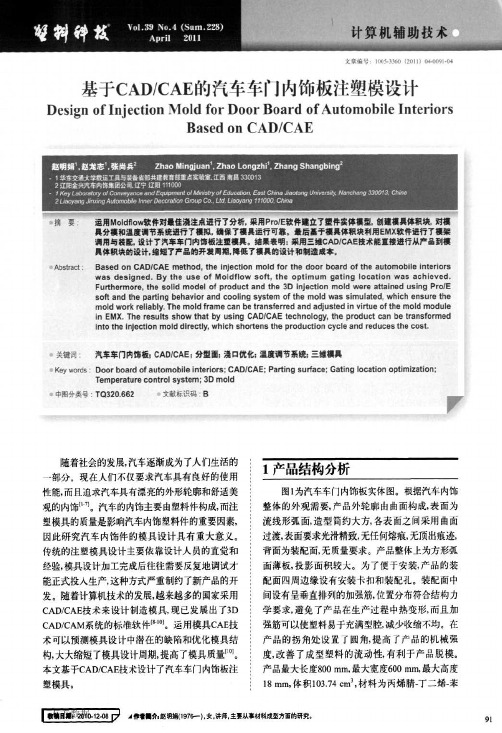
【6jIB自女#*月&^手册[Ul n京.机械In&《社2C10,5 【7]林*女ProtENGINGEER2001#AⅢ*[M】n束。清毕大学
口Kn
2003
【8]4j#Pro/ENGINGEER2001÷女%lm教S[Mj#i^
R∞自m《#2002
【9】驶毂科技Pto/ENGINGEER女料#^*计[M]]匕束=^B邮≈
3.3嵌具温度陶竹系统
模具温度是指模具型腔和型芯的表面盈度,注 人模具中的热塑性熔融树脂.必须在模具内冷却固 化才能成为塑件,所以模具温度必须低于注射八模 具型腔内的熔融树脂的温度。模具的冷却就是将 注塑成型过程中产生的、并传导给模具的热量.应 尽可能迅速、并最大程度地导出,以使塑件以较快 的速度冷却固化。因此,模具的冷却效果直接决定 着产品的表面质量、残余应力、注射效率和成本的
&m#2。。6
【1q IⅢMoldfl。W*A*折&用实倒【M】|匕京清华^学&Ⅲ
#a。05
科莱思近期推出MEVOPUR色母粒新产品
总部醴在瑞士的科莱恩公司日前推出MEVOPUR色母粒新产品。此奘色母粒与预着色塑料混配料属干科莱 科莱思近期推出了一系列用于聚丙烯,聚乙烯以厦其他材料的国际标准色彩。新型MEVOPUR色母粒与预 着色塑料混配料是科莱思全球通用的IS010993/USPVI标准色彩系列的新成员,是为聚醚嵌段酰胺以及聚乙烯与 聚丙烯材料量身定制的产品。
基于CAD/CAE的汽车车门内饰板注塑模设计
Design of
Injection
Mold for Door Board ofAutomobile Interiors
Based
on
CAD/CAE
#;
运用Moldflow辕件对●隹港建赢进行了分斩.果用Pro/E辕件一立了置件蜜体■量.翻t攥^伴瓤块,对曩 ^舒■和量度调节幕照进行了■担.一挥了曩^还行可●。■后基于羹鼻伴飘壤靳用EMX鞍件进行了曩纂
汽车大地板左右外侧梁汽车覆盖件冲压模具毕业设计说明书

XXXX大学毕业设计(论文)说明书课题名称某汽车覆盖件模具设计系别专业班级学号姓名指导教师年月日目录摘要第一章概述………………………………………………第一节冲压概念…………………………………………第二节冲压模具水平状况………………………………第三节冲压模具的发展重点与展望…………………第三节汽车覆盖件的定义………………………………第五节汽车覆盖件应满足的条件……………………第六节覆盖件模具的现状……………………………第七节覆盖件模具的发展方向………………………第三章工艺分析………………………………第一节零件结构特点……………………………………第二节材料性能的分析……………………………………第四章相关参数的计算与冲压设备的选择…………………………………………第一节相关工艺的计算…………………………(一)冲孔力的计算…………………………………(二)卸料力的计算………………………………(三)推件力的计算………………………………(四)顶件力的计算………………………………(五)切边力的计算………………………………(六)冲压工艺总力的计算…………………………第二节冲压设备的选择……………………………第五章切边冲孔复合模结构设计……………第一节模具工作运动方式………………………第二节凸模的结构设计…………………………第三节上模座结构设计…………………………第四节下模座结构设计…………………………第五节修边镶块的设计…………………………第六节废料刀的设计…………………………第七节压料芯的设计…………………………第八节限位机构……………………………第九节导向装置…………………………第十节起重方式的设计…………………第十一节压力槽………………………………第十二节安全平台……………………………第六章标准零件的设计与选用……………………第一节合模限位块的选用…………………………第二节安全螺钉的选用………………………………第三节凸模固定板……………………………………第四节导向标准零件的选用…………………………致谢……………………………………………总结………………………………………………参考文献…………………………………………摘要随着历史的车轮滚滚前进,中国工业不断地发展,模具行业在人类生活中起到举足轻重的作用。
汽车拉门装饰板注射模设计

6 2
工 程 塑 料 应用
20 0 8年 , 3 第功能 外 , 在脱 模过 程 中还能 起 到 顶 出塑料 件 的作 用 , 即利 用 顶 出 机 构 的推 力 驱 动 斜 推杆运 动 , 在斜 推 杆 推 顶 塑 料 件使 其 脱 出 凸模 的 同时 , 成侧 向分 型 与抽 芯 动作 。其结 构 如 图 3 图 完 、 4所示 。斜推 杆 安 装 在 凸模 的斜 孑 中 , 上 端 连 接 L 其 着 侧 向型芯 ( 滑 块 ) 其 下 端 与 滑 块 连 接 , 块 可 斜 , 滑 在 滑槽 内左 右 移 动 。开 模 后 , 塑 机 顶 出装 置 通 过 注 推 板使 斜 推杆 和斜 滑块 向前 运动 , 由于斜 孑 的作用 , L 斜 滑块 向前 运 动 的 同时 向 内侧 移 动 , 而 在 推 出 塑 从
所 示
拉 门装饰 板 即是 其 中之 一 。该 塑 料 件结 构复 杂 、 尺
寸大 , 因而注射 模 的设 计 有 一 定 的难度 。根 据 拉 门 装饰 板 的结构 特 点 , 计 中采 用 了不 同 的侧 抽 芯机 设
构 , 着 重考 虑 了模 板 刚 度 、 注 系 统 流 动 比 、 却 并 浇 冷 系统 冷 却等 问题 。
收稿 日期 :0 80 —0 2 0 —31
图 1 汽 车 拉 门 装 饰 板
12 塑料件 材料 选 用 .
拉 门装饰 板 为 汽 车 内饰 件 , 材 料 必 须 具有 良 其
好 的耐 老化 性 、 冲 击 性 和 阻燃 性 。另外 塑料 件 尺 耐
维普资讯
2 模 具 设计
源消 耗 , 汽 车 减 重 , 来 汽 车 上 会 有更 多 的塑 料 使 未
件 。 目前 每 辆 汽 车 上 的 塑料 件 重 已 占汽 车 总 重 的 2 % 。汽 车上 的塑料 件 种类 繁多 , 2 结构 形式 多样 化 ,
汽车车门外板冲压模具设计
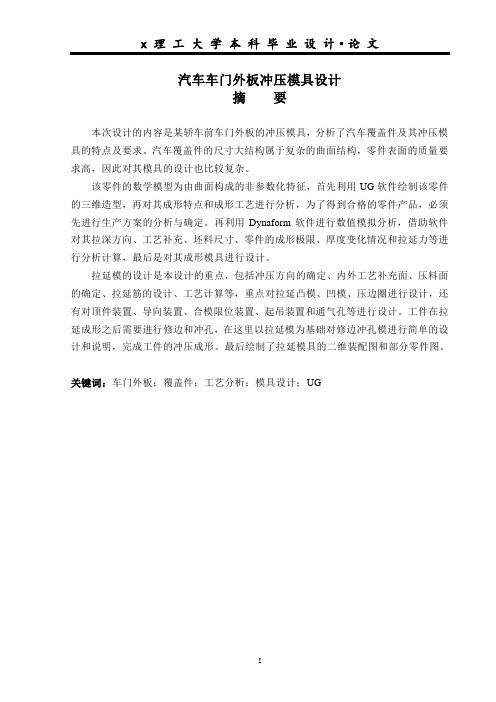
汽车车门外板冲压模具设计摘要本次设计的内容是某轿车前车门外板的冲压模具,分析了汽车覆盖件及其冲压模具的特点及要求。
汽车覆盖件的尺寸大结构属于复杂的曲面结构,零件表面的质量要求高,因此对其模具的设计也比较复杂。
该零件的数学模型为由曲面构成的非参数化特征,首先利用UG软件绘制该零件的三维造型,再对其成形特点和成形工艺进行分析,为了得到合格的零件产品,必须先进行生产方案的分析与确定。
再利用Dynaform软件进行数值模拟分析,借助软件对其拉深方向、工艺补充、坯料尺寸、零件的成形极限、厚度变化情况和拉延力等进行分析计算,最后是对其成形模具进行设计。
拉延模的设计是本设计的重点,包括冲压方向的确定、内外工艺补充面、压料面的确定、拉延筋的设计、工艺计算等,重点对拉延凸模、凹模、压边圈进行设计,还有对顶件装置、导向装置、合模限位装置、起吊装置和通气孔等进行设计。
工件在拉延成形之后需要进行修边和冲孔,在这里以拉延模为基础对修边冲孔模进行简单的设计和说明,完成工件的冲压成形。
最后绘制了拉延模具的二维装配图和部分零件图。
关键词:车门外板;覆盖件;工艺分析;模具设计;UGThe design of car door panels stamping dieAbstract: The content is designed for a car before the car door panel stamping dies, analyzes and stamping automotive panel characteristics and requirements. Large size structure of an automobile covering parts are complex surface structure, high quality requirements of the part surface, so the design of their molds more complicated.Mathematical model of the part of the grounds of non-parametric feature curved surface, the first use of UG software to draw three-dimensional modeling of the part, and then analyzed the characteristics shaping and forming processes, in order to get qualified parts products must be produced programs Analysis and determination. Reuse Dynaform numerical simulation analysis software, with the software to its drawing direction, forming limit addendum, blank size, part thickness changes and drawing force of analysis and calculation, and finally the design of its mold.Drawing die design is the focus of this design, including stamping direction is determined, both inside and outside addendum, binder determination drawbead design, process calculation, focusing on drawing punch, die, blankholder ring design, as well as for top pieces of equipment, guides, clamping stopper, lifting device and the vent, etc. design. After forming the workpiece drawing needed trimming and punching, drawing die in here with the basis for trimming punching die design and simple instructions to complete the stamping workpiece shape. Finally, draw the two-dimensional drawing die assembly drawing and some parts Fig.Key words:car door panels;cover;process pnalysis;mold design;UG目次摘要................................................ 错误!未定义书签。
- 1、下载文档前请自行甄别文档内容的完整性,平台不提供额外的编辑、内容补充、找答案等附加服务。
- 2、"仅部分预览"的文档,不可在线预览部分如存在完整性等问题,可反馈申请退款(可完整预览的文档不适用该条件!)。
- 3、如文档侵犯您的权益,请联系客服反馈,我们会尽快为您处理(人工客服工作时间:9:00-18:30)。
汽车左右门板大型注塑模设计汽车门板是汽车内饰件的重要组成部分,位于汽车车门的内侧,有前后左右之分,根据车系的不同而不同,通常为两门与四门,这些零件统称门板系列,左右门板本体,为叙述方便,统称为门板。
本章以汽车左右门板为案例进行分析,总结门板模具的设计要点与经验,门板零件特征如图1与图2所示:02.4图1 汽车左右门板零件图1扣1BA图2 汽车左右门板零件图21 塑件外观要求与结构分析图1所示为某品牌汽车门板零件图,材料为PP+EPDM,收缩率一般取1.011,其中EPDM 能够提高门板的弹性,模具型腔数为1+1。
外表面皮纹,塑件为外观件,表面要求高。
塑件尺寸为:804.8*721.3*102.4mm。
塑件特点如下:(1)外观面要求高,塑件外观面需皮纹,塑件外观面不允许有斑点,浇口痕迹,更不允许有收缩凹陷.熔接痕.飞边等缺陷。
(2)塑件为皮纹件,塑件外观面(A面)脱模斜度设计要合理(一般至少设计5度以上)。
(3)塑件外形复杂,曲面光洁度高,塑件内外侧面共有6个倒扣,倒扣多且成型困难。
2 模具结构分析根据门板塑件的结构特点,模具优先采用热流道注塑模结构,采用2点针阀式顺序阀热流道+冷流道+扇形浇口进胶。
图1所示塑件内外侧面共有6个倒扣,倒扣1.2.3.4.5均采用“斜导柱+滑块”抽芯结构。
倒扣6面积大,在本模具中采用斜推块结构。
本模具外形尺寸为:2050*1610*995(mm),总重量约20吨,属于大型注塑模具。
详细结构见图3-图9。
图3 汽车左右门板注塑模具结构图1非操作侧图4 汽车左右门板注塑模具结构图273图5 汽车左右门板注塑模具结构图图6 汽车左右门板注塑模具结构图4484950525354 图7 汽车左右门板注塑模具结构图5444345D-D图8 汽车左右门板注塑模具结构图64746F-F394142图9 汽车左右门板注塑模具结构图72.1成型零件设计本模具定动模采用一体式,常用材料为:P20/738。
模具AB板采用四面围边的设计方式,在门板模具设计中,斜推块与推块的设计是门板的核心结构,斜推块的设计要防止塑件粘斜推块,以及拉伤塑件。
对于门板零件一般都有网孔,因而网孔的设计也是门板模具的难点。
2.1浇注系统设计本模具浇注系统采用热流道进胶,采用2点顺序阀热流道+冷流道+扇形浇口的进胶方式,塑件材料为PP+EPDM.由于塑件为PP+EPDM料,料流动性好,在设计流道时流道设计范围广些,但热嘴至塑件边缘的流道长度尽量设计在60mm以内,如果实在不行也尽量控制在100mm以内,避免冷流道过长与避免压力损失大。
门板为外观件,表面不允许有熔接痕,注塑成型时必须把熔接痕赶到非外观面或消除熔接痕,这是本模具设计的重点和难点之一。
传统的同步多点进浇,虽然能使熔体充满整个型腔,但是由于熔接痕的存在,很难使产品质量达到理想的要求。
为此本模具采用了2点顺序阀热流道浇口控制技术,它通过油缸的驱动来控制2个热射嘴的开启和关闭,由此达到了塑件表面无熔接痕的理想效果。
门板注塑模热流道浇口位置见图10,图中G1-G2为热嘴位置。
图10 2点顺序阀热流道控制系统2.2 侧向抽芯机构设计侧向抽芯机构是本模具最重要的结构之一。
针对塑件外侧的5处倒扣,模具采用了“滑块+斜导柱+弹簧”的抽芯机构,倒扣6倒扣面积大,在产品内侧,本模具采用斜推块抽芯机构。
抽芯方向见图2.图3。
2.3温度控制系统设计汽车门板为汽车最重要的内饰件之一,也是外观要求很高的塑件之一,因此温度控制系统设计的好坏对模具的成型周期与产品成型质量影响很大。
冷却水道设计原则之一是距离型腔面要大致相等,以达到模具型腔各处温度大致均衡。
本模具的温度控制系统采用了“直通式水管+水井”的组合形式(见图11和图12),设计此种组合形式虽然冷却效果有所下降,但会节约模具制造成本。
其优点是塑件冷却均匀,成型周期较短,成型质量较高,适用于较高要求与外观性能要求较高的模具。
图11(a)定模冷却系统非操作侧图12(b)动模冷却系统本模具定动模温度控制系统为:定模设计了10组水路,动模设计了8组水路,模具冷却水路设计做到了与料流方向一致,本模具冷却系统采用:“直通式水管+水井”的设计形式,进出水距离做到了水路长度大致相等,因而使塑件得到了良好的冷却效果与外观质量。
本模具温度控制系统设计时还做到了以下几点。
(1)水道之间的间距保证在50~60mm之间,冷却水道距型腔面在20~25mm之间。
本模具的定模.动模与斜推块结构较为复杂,热量又较为集中,因此进行了重点冷却,斜推块上设计了冷却水。
(2)考虑到加工问题,本模具的冷却水道与推杆、推块等推件孔保持了至少8mm的距离,这样设计是为了避免加工误差,造成钻咀偏心。
(3)冷却水道长短做到了大致相等,保证了冷却水出入口温差大致相等,从而保证了模具温度大致均衡。
热嘴区域由于温度较高,必须在热嘴区域要设计冷却水。
(4)本模具定动模设计了网孔镶件,网孔镶件要单独设计一组冷却水冷却。
网孔镶件为避免困气,需要采用透气钢材料。
透气钢材料一般都很贵,如果采用S136钢料,需要在网孔镶件上设计排气针或者镶针,网孔镶件底部还要设计排气槽,方便气体排出。
2.4导向定位系统设计在汽车注塑模具设计中,由于模具大,塑件外观要求高,尺寸精度要求也高,因此对模具的导向定位设计非常严格,导向定位系统设计的好坏直接影响成型塑件的精度和模具的寿命。
本模具在4个角上各设计了1支方导柱与1支圆导柱,以及4个1 °精定位,详见图3和图4。
其中4支圆导柱尺寸为∅80×300mm(导柱最长做到10倍直径),安装在定模侧,由于塑件开模后留在动模侧,这样就不会影响塑件取出。
同时4支导柱还起到翻模时可作为支撑脚用,方便FIT模,如图13所示。
导柱的长度必须做到:无滑块的模具导柱要高出定动模最高点30mm,有滑块的模具要在斜导柱插入滑块前20mm插入导套,否则在模具的制造和生产中会带来很大的麻烦,严重时会损坏模具。
37图13 汽车左右门板模具导向定位系统2.5脱模系统设计本模具为推杆+斜推块+油缸推出结构,模具在定.动模开模后,依靠推件推出塑件与流道,推件固定板由注塑机通过油缸推动和在4支复位杆的作用下复位。
在设计脱模系统时要注意以下几点:1.大型模具(长宽方向超过1400mmX700mm)需设计6支复位杆与6支推杆板导柱,所有汽车模具复位杆上要设计一比复位杆大一级的回复块,回复块一般选45#(S50C)氮化处理。
推杆板导柱要布置在推出力大的推出元件附近(如油缸.复位杆等)。
2.所有汽车模具需要设计限位柱,限位柱要优先布置在KO孔上方或附近。
推杆要排布在靠近R处的受力位置,布置在包紧力大的位置,推杆设计要大,推杆布置要多些,设计推杆尽量设计成同一规格,不要设计很多种规格,这样可以避免频繁更换钻嘴,节省加工时间与加工成本。
3 模具工作过程熔体通过注塑机喷嘴,经热嘴16进入模具型腔,熔体充满型腔后,经保压、冷却和固化,至足够刚性后,注塑机拉动模具的动模固定板8,模具从分型面PLⅠ处开模。
开模500mm 后,注塑机油缸推动推件固定板6,进而推动所有推件将成型塑件推离动模。
塑件取出后,注塑机油缸拉动推件及其固定板复位,接着注塑机推动动模合模,模具开始下一次注射成型。
4 模具强度与分型面管位设计在模具设计中,根据一个塑件的尺寸大小与结构来设计模具,首先让设计者迷惑的是模具强度是否足够?分型面管位的大小.位置.强度是否合理?又该如何来解决这些问题?在进行模具设计时首先要考虑的是模具强度与模具成本问题。
一个有丰富经验的设计师与一般的设计师所设计的模具在模具成本上要节省很多。
合理的模具设计是:模具强度既合理又不乱费,就地取材,模具强度与成本兼顾,选取最优的设计方案与加工工艺。
对于模具强度太强显得乱费,太弱则影响模具使用寿命。
本模具分型面管位设计在定动模,定动模四面围边四周做5度斜度,四周做耐磨块,此种四面围边的设计方法在汽车门板与挡泥板等模具上应用广泛。
图14所示A.B两尺寸的计算方法是:首先从塑件最大边缘加50mm封胶位(在汽车模具设计中,小型模具(5050以内)30mm封胶,中型模具(5050-1010)40mm封胶,大型模具(1010以上)50mm封胶。
),再加50-70mm避空位(在汽车模具设计中,只有封胶位配合,其余全部避空,减少FIT模工作量。
避空位也是保证模具强度的区域。
),然后再加上模胚处分型面承压板的尺寸就是A.B的尺寸,这样就设计出既符合客户模具强度要求又节省成本的模具。
C处尺寸不同塑件数值会不一样,最少C处尺寸定模要保证塑件最高胶位面有80mm以上距离,动模由于承受注塑压力大,需相应加厚,最低设计100mm以上。
用来保证模具强度。
总之,在日常设计中依据不同的客户与工厂灵活运用,设计出既符合客户需求又节省成本的模具。
B-B图14 汽车左右门板模具强度参考5 模具排气系统设计在汽车模具设计中,排气系统的设计相当重要。
如果排气设计不合理,会严重影响塑件的品质。
会出现填充不满.困气.脱模不顺等注塑缺陷,严重困气时会烧焦产品。
汽车左右门板属于内饰件,塑件外观要求严格,合理设计排气至为重要,在设计模具排气系统时要注意以下几点:1.排气要优先开设在料流末端与塑件转角位置。
2.靠近镶件或壁厚最薄处,因为这里最容易形成熔接线。
3.最好开设在分型面上,因为分型面上产生溢料最容易清除。
本模具排气主要开设在定模,还有网孔区域的排气。
6 结果与讨论本模具采用“推杆+斜推块+油缸推出”的脱模系统以及“直通式水管+水井”的温度控制系统。
前者文中已有详细论述,下面重点讨论一下本模具的温度控制系统。
温度控制系统在汽车模具设计中至关重要,对塑件的成型周期与成型质量影响很大,合理的温度控制,对提高塑件质量与缩短成型周期影响深远。
对于大型汽车模具冷却系统设计要遵循以下几点:1.三米原则,汽车大型模具的直通式冷却管一般设计在¢15,门板定动模冷却水如果设计成随形(随塑件形状),要设计成两端钻孔,冷却水路总长度不能超过3米,因为超过3米,深孔钻将无法加工,钻嘴长度不够。
2.手掌效应。
设计大型汽车塑料件模具水路设计,布置水路向一个方向流动,间隔排布有如手掌,水道之间距离控制在50-60mm 之间。
3.水路流程不能太长,避免模具开模了冷却水还没走出来。
在汽车模具温度控制系统设计中,主要有以下两种组合形式:(1)第一种组合形式:直通式水管+倾斜式水管+水井;(2)第二种组合形式:直通式水管+水井+倾斜式水管。
此两种形式的区别在于:在倾斜式水管和水井之间,前者是优先采用倾斜式水管,而后者是优先采用水井。
此两种组合侧重点不同,因而效果也不同。
第一种形式的优点是型腔各处冷却均匀,成形周期短,塑件质量高,适用于高要求与外观性能要求高的模具,如汽车前、后保险杠,汽车上、下仪表板本体和汽车左、右门板等内外饰注塑模具。