整车制造厂各生产环节故障记录系统
汽车试验用的故障分析系统及故障分析方法与制作流程
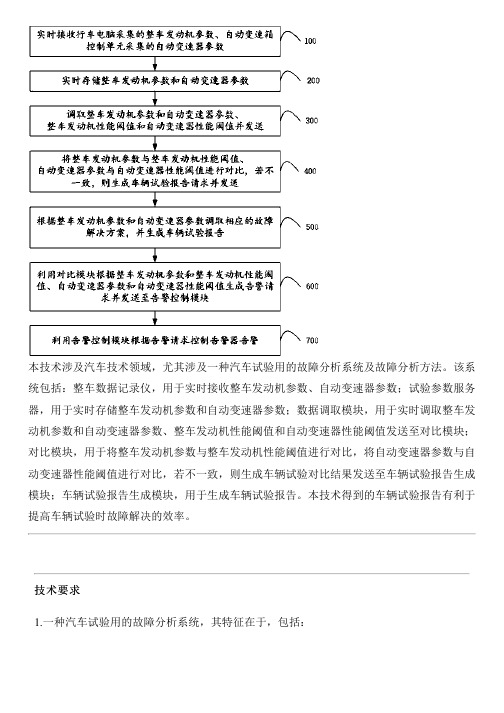
本技术涉及汽车技术领域,尤其涉及一种汽车试验用的故障分析系统及故障分析方法。
该系统包括:整车数据记录仪,用于实时接收整车发动机参数、自动变速器参数;试验参数服务器,用于实时存储整车发动机参数和自动变速器参数;数据调取模块,用于实时调取整车发动机参数和自动变速器参数、整车发动机性能阈值和自动变速器性能阈值发送至对比模块;对比模块,用于将整车发动机参数与整车发动机性能阈值进行对比,将自动变速器参数与自动变速器性能阈值进行对比,若不一致,则生成车辆试验对比结果发送至车辆试验报告生成模块;车辆试验报告生成模块,用于生成车辆试验报告。
本技术得到的车辆试验报告有利于提高车辆试验时故障解决的效率。
技术要求1.一种汽车试验用的故障分析系统,其特征在于,包括:整车数据记录仪,用于与分别电连接行车电脑和自动变速箱控制单元的车身CAN线电连接,通过车身CAN线实时接收行车电脑采集的整车发动机参数、自动变速箱控制单元采集的自动变速器参数,并发送至试验参数服务器;试验参数服务器,用于实时接收并存储整车发动机参数和自动变速器参数;数据调取模块,用于实时从试验参数服务器中调取整车发动机参数和自动变速器参数发送至对比模块;还用于实时从车辆性能数据库中调取整车发动机性能阈值和自动变速器性能阈值发送至对比模块;对比模块,用于实时将整车发动机参数与整车发动机性能阈值进行对比,若不一致,则根据整车发动机参数和整车发动机性能阈值生成车辆试验对比结果发送至车辆试验报告生成模块;还用于实时将自动变速器参数与自动变速器性能阈值进行对比,若不一致,则根据自动变速器参数和自动变速器性能阈值生成车辆试验对比结果发送至车辆试验报告生成模块;车辆试验报告生成模块,用于根据车辆试验对比结果中的整车发动机参数和自动变速器参数实时从车辆故障方案数据库中调取相应的故障解决方案,并根据车辆试验对比结果和故障解决方案生成车辆试验报告。
2.根据权利要求1所述的汽车试验用的故障分析系统,其特征在于,对比模块还用于根据整车发动机参数和整车发动机性能阈值生成告警请求发送至告警控制模块;还用于根据自动变速器参数和自动变速器性能阈值生成告警请求发送至告警控制模块;告警控制模块,用于根据接收的告警请求控制告警器告警。
汽车制造与装配技术《电子故障诊断系统任务工单》
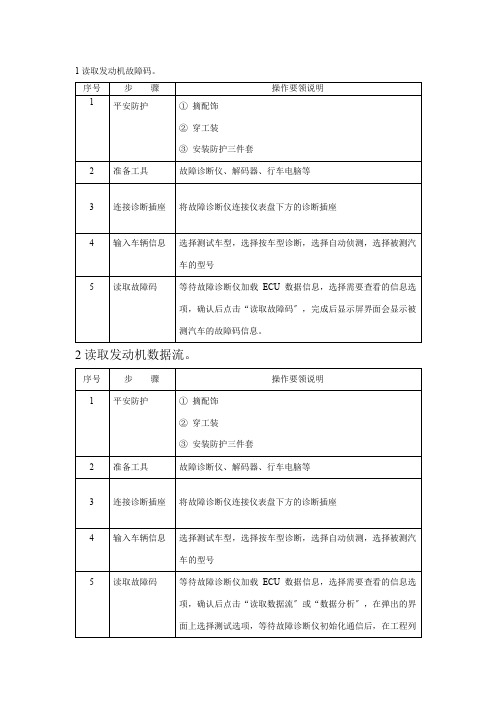
序号
步骤
操作要领说明
1
平安防护
①摘配饰
②穿工装
③安装防护三件套
2
准备工具
故障诊断仪、解码器、行车电脑等
3
连接诊断插座
将故障诊断仪连接仪表盘下方的诊断插座
4
输入车辆信息
选择测试车型,选择按车型诊断,选择自动侦测,选择被测汽车的型号
5
读取故障码
等待故障诊断仪加载ECU数据信息,选择需要查看的信息选项,确认后点击“读取数据流〞或“数据分析〞,在弹出的界面上选择测试选项,等待故障诊断仪初始化通信后,在工程列表的左栏依次点击发动机相关的数据流信息,每点击一次,右侧栏将显示被点击勾选的选项,故障诊断仪会以波形加动态数字的组合方式将发动机相关数据流显示出来
1读取发动机故障码。
序号
步骤操作要领说明1来自平安防护①摘配饰
②穿工装
③安装防护三件套
2
准备工具
故障诊断仪、解码器、行车电脑等
3
连接诊断插座
将故障诊断仪连接仪表盘下方的诊断插座
4
输入车辆信息
选择测试车型,选择按车型诊断,选择自动侦测,选择被测汽车的型号
5
读取故障码
等待故障诊断仪加载ECU数据信息,选择需要查看的信息选项,确认后点击“读取故障码〞,完成后显示屏界面会显示被测汽车的故障码信息。
汽车生产线故障管理系统

汽车生产线故障管理系统摘要:随着汽车产业信息化技术的高速发展,制造管理执行系统 MES在车间的应用变得尤为重要。
作为 MES 系统的一个模块,PMC 系统已经成为车间保全人员不可或缺的一套管理工具,而 PMC 系统的重中之重就是其报表功能。
一套完善的报表功能不仅能详细的罗列出生产线现场设备的数据,还能对这些数据进行统计和分析,并以更加直观化的图表形式呈现出来。
本文详细地介绍了某汽车厂焊装车间 PMC 项目的网络架构、数据流向以及报表功能的原理、数据存储的实现方式等,并系统地阐述了如何利用VB 高级编程语言与水晶报表来共同开发报表功能。
关键词:汽车;生产线;故障管理系统1系统网络规划为了便于车间管理人员对报警数据的统计、分析,焊装车间PMC 系统与ANDON 系统共用一台数据库服务器。
PMC 服务器通过 ISO 通讯协议与现场的 13个 PLC 进行通讯,将报警信息存储在PMC 服务器的分段数据库中;通过在 WINCC 编程环境下编写 VB应用程序,来实现将分段数据从 PMC 服务器到数据库服务器的转存;数据库 PMC 报表系统通过查询数据库服务器中的报警归档信息,来实现报表查询功能。
焊装车间网络架构简图如下。
2工具软件2.1 WINCC本项目中 PMC 数据采集服务器组态软件使用的是西门子上位组态软件 WinccV6.2。
WINCC具有良好的开放性和灵活性,为使用者提供了良好的图形界面开发平台;它提供了所有最重要的通讯通道,用于连接到 SIMATIC S5/S7/505 控制器(例如通过 S7 协议集)的通讯,以及如 PROFIBUS- DP/ FMS、DDE(动态数据交换)和 OPC(用于过程控制的 OLE),等非专用通道。
所有的控制器制造商都为其提供相应的 OPC 服务器,所以各种硬件均可连接到 WinCC。
2.2 SQL 2005 数据库使用当前应用较广的 SQL Server2005。
SQL Server 2005 包含了多个能显著提高开发者能力的新技术。
制造产线异常故障预警系统安灯Andon
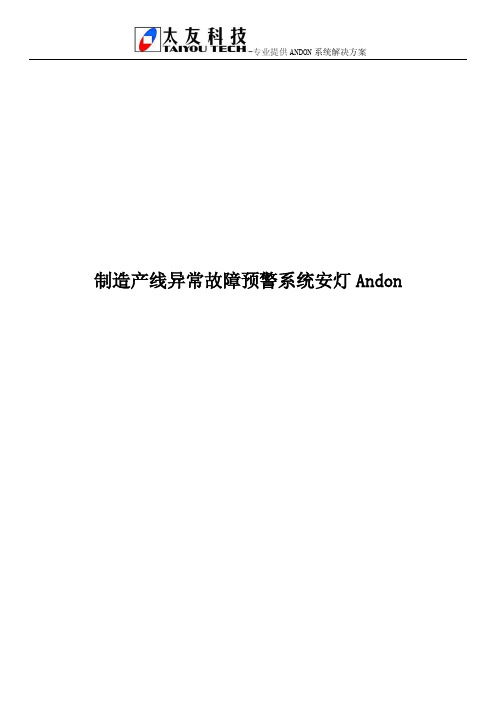
制造产线异常故障预警系统安灯Andon
摘要:在制造装配生产过程中,设备出现故障停机、物料短缺、工艺异常以及品质异常等问题会经常发生,如何在最短的时间内保证问题得到及时的处理,是当前企业非常关注的一个难题,因为这会直接影响到整个生产的效率。
安灯系统作为生产管理系统中的一部分,主要应用于制造业生产车间的生产线上的实时呼叫,在异常故障出现后能及时把问题反馈到相关人员中,可以帮助生产线上的工人在一定生产节拍内、完成质量可靠的产品装配任务。
在生产过程中,一旦产线出现异常故障时,可由线上操作人员通过触摸屏选择对应的异常问题直接激活Andon系统,以下为Andon系统数据采集端界面,可直接通过触控方式进行操作,也可直接通过附带的键盘进行操作:
安灯系统被激活后就可以直接向生产环节管理者汇报产品质量问题、设备故障、物料缺失或其它请求帮助等等,并且通过LED大屏把异常信息显示出来,提醒相关人员尽快解决问题。
注:LED大屏
具体显示的内容可根据客户的需求制定。
安灯系统可以实时并准确地将异常信息反应在现场看板上,通过这些显示提示相关人员迅速作出反应,以最短时间解决相关问题,从而最终实现生产过程各种问题的准确传递和及时处理,可大幅度地减少工人问题求救的时间,从而提高产量,提高生产效率。
同时,Andon系统可实时记录呼叫的次数、停机时间等信息,并提供丰富多样的数据统计分析报表,通过分析后,就可以迅速得出潜在的质量、流程、人员等问题, 管理人员可以针对以上改进点进行改进,提高生产管理水平。
汽车生产线故障管理系统

~
进 各 种 各样 的 操作 时 , 用 的最 多 的就 是 数 据 查 询 。 使 S LC E E T语 句 的 完 整 句 法如 下 : S L C 目标 表 的列 名 或列 表 达 式序 列 F OM 基 本 表 和 ( ) EET R 或 视 图 序列 【 HE E行 条 件 表 达 式 】 R W R 【 OUP B 列 名 序 列 】 A l G 组 G Y 【 VN H
鞫 练 静
州
激 … 势
( 查 询 记 录 1 ) S LC E E T语 句 是 S QL查 询 的 基 本 语 句 , 当我 们在 对 一 个 数 据 库
;
、
— | ~ —. | 塑 0 = 嚣 镪 = \
I= … / 一
条 件 表 达 式】
【 DE Y列名【S DE C .】 OR R B A C l A 】・ . 2 工 具 软 件 21 W I C 本 项 目中 P . NC MC 数据 采 集 服 务 器 组 态 软 件 使 用 的 ② 插 入记 录 往 数 据库 的基 本表 中插 入 数 据 使 用 的是 IS R N E T语 句 ,采 用 元 是 西 门子 上 位 组 态软 件 W i cV .。 W I C n 62 c N C具 有 良好 的开 放 性 和 其 灵 活 性 , 使 用者 提 供 了 良好 的图 形 界 面 开 发平 台 ; 提供 了所 有 最 组 值 的插 入 方 式 , 句 法 如 下 : 为 它 I E T IT 基 本 表名 ( 表 名 ) A U S 元 组值 ) NS R N O 列 \ LE( , 重 要 的 通 讯 通 道 , 于 连 接 到 SMA I 5S ,O 用 I TC S /75 5控 制 器 ( 如 通 例 过 S 7协 议 集 ) 通 讯 , 及 如 P OFB S D /F 、 DE 动 态 数 的 以 R IU — P MS D ( ③ 删除记录 往 数 据 库 的基 本 表 中 删 除 数 据 使 用 的是 D L T E E E语 句 , 句 法 其 据 交换 ) OP ( 于 过 程 控 制 的 OL )等 非专 用通 道 。 所 有 的控 制 和 C用 E, D LT R W R 。 器 制造 商 都 为 其 提 供 相 应 的 OP C服 务 器 ,所 以 各 种 硬 件 均 可连 接 如 下 : E E E F OM 基 本 表名 【 HE E条件 表 达 式l 删 除语 句 实 际 上 是 “ E E T * R S LC F OM 基 本 表 名 【 HE E 条 件 W R 到 W iCC。 n 表 达 式】和 DE E E操 作 的 结 合 , 找 到 一 个 元 组 , 把 它 删 除 。 此 ” LT 每 就 22 QL 2 0 数 据 库 使 用 当 前 应 用 较 广 的 S ev r - S 0 5 QL S re DE E E语 句 只 能 从 一 个 基 本 表 中删 除 元组 , HE E子 句 中条 W R 2 0 。 S ev r2 0 包 含 了 多 个 能 显 著 提 高 开 发 者 能 力 的 新 外 , L T 05 QL S re 0 5 也 技 术 。从 支 持 . T Fa wok 到 和 Vs a S u i 紧 密集 成 , NE rme r iu l tdo的 这 件 可 以嵌 套 , 可 以 是来 自几 个 基 本 表 的复 合 条 件 。 些 新特 性 使 开 发人 员 能够 以更 低 的 成 本 , 容 易 地创 建安 全 、 大 的 更 强 ④ 修 改记 录 需 要修 改基 本 表 中元 组 的列 值 时 ,可 以用 U D T P A E语 句 实 现 , 数 据库 应 用 程序 。
生产线故障维修记录

生产线故障维修记录尊敬的维修团队:日期:XXXX年XX月XX日地点:生产线工厂故障维修记录问题描述:在生产线工作过程中,我们遇到了一系列故障和问题,现将其记录如下:1. 设备编号:E001故障描述:机器出现电源故障,无法正常启动。
维修过程:- 检查电源线是否连接正常。
- 使用测试设备检测电源是否稳定。
- 发现电源开关损坏,更换新开关。
- 启动机器,并进行测试,故障完全解决。
2. 设备编号:E002故障描述:机器传送带运行缓慢,导致生产效率下降。
维修过程:- 检查传送带运行是否受阻。
- 清理传送带上的杂物并润滑机器。
- 调整传送带张力,确保其正常运行。
- 进行测试,故障得以解决。
3. 设备编号:E003故障描述:机器出现频繁断电,影响生产流程。
维修过程:- 检查电源线连接是否松动。
- 更换新的电源插头和插座。
- 检查设备是否过载,调整设备负荷。
- 故障修复后进行测试,确保问题解决。
4. 设备编号:E004故障描述:机器传感器失灵,无法正常检测产品。
维修过程:- 检查传感器连接是否良好。
- 清理传感器表面的灰尘和杂质。
- 校准传感器的灵敏度和精确性。
- 进行测试,确保传感器功能正常。
5. 设备编号:E005故障描述:机器出现异常噪音,影响工作环境。
维修过程:- 检查机器内部是否有异物。
- 调整机器部件的位置,消除摩擦导致的噪音。
- 润滑机器,减少摩擦产生的噪音。
- 进行测试,噪音问题得到解决。
总结:通过维修团队的努力和合作,我们成功地解决了生产线中出现的各种故障和问题。
我们采取了及时有效的维修措施,确保了生产线的正常运行。
同时,我们记录了每个设备的故障情况和维修过程,以备将来参考和分析。
我们将持续关注设备运行状态,确保生产线的稳定运行,提高生产效率。
维修人员签名:___________日期:XXXX年XX月XX日。
企业故障报告、分析和纠正措施系统(FRACAS系统)实施方案

纠正措施制定
针对每个故障,FRACAS系统应制定相应的纠正措施计划。
02
纠正措施实施
根据纠正措施计划,FRACAS系统应监督和管理纠正措施的实施过程
。
应对纠正措施的效果进行评估,以便
确定是否达到了预期效果。
07
FRACAS系统实施效果评估
评估指标和方法
实施时间表和里程碑
• 第一阶段(1-3个月) • 完成系统需求分析和设计; • 确定系统实施范围和功能模块; • 制定详细实施计划。 • 第二阶段(4-6个月) • 完成系统开发和测试; • 确定系统运行环境和配置;
需要配合的部门和人员
生产部门
提供生产过程中的故障数据和信息;
技术部门
负责系统的技术实现和开发;
FRACAS系统的工作流程
01
02
03
04
05
FRACAS系统的工作流程包 括以下几个步骤
1. 故障报告:当设备发生 故障时,相关人员需要及 时记录故障信息,包括故 障时间、故障现象、影响 范围等,并通过FRACAS系 统上报。
2. 故障分析:专业人员对 故障信息进行深入分析, 明确故障原因,评估故障 对设备性能和安全的影响 ,并确定相应的纠正措施 。
企业故障报告、分析和纠正 措施系统(FRACAS系统) 实施方案
目 录
• 引言 • FRACAS系统基本原理 • 实施FRACAS系统的必要性 • FRACAS系统实施计划 • FRACAS系统实施步骤 • FRACAS系统应用举例 • FRACAS系统实施效果评估 • FRACAS系统实施总结与展望
故障分析实例
故障分类和分析
根据故障类型,FRACAS系统应对故障进行分类和分析。
汽车维修记录管理系统方案
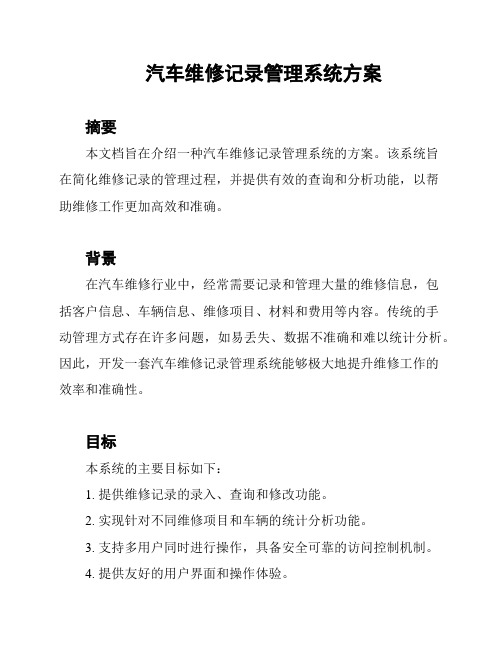
汽车维修记录管理系统方案摘要本文档旨在介绍一种汽车维修记录管理系统的方案。
该系统旨在简化维修记录的管理过程,并提供有效的查询和分析功能,以帮助维修工作更加高效和准确。
背景在汽车维修行业中,经常需要记录和管理大量的维修信息,包括客户信息、车辆信息、维修项目、材料和费用等内容。
传统的手动管理方式存在许多问题,如易丢失、数据不准确和难以统计分析。
因此,开发一套汽车维修记录管理系统能够极大地提升维修工作的效率和准确性。
目标本系统的主要目标如下:1. 提供维修记录的录入、查询和修改功能。
2. 实现针对不同维修项目和车辆的统计分析功能。
3. 支持多用户同时进行操作,具备安全可靠的访问控制机制。
4. 提供友好的用户界面和操作体验。
功能和模块本系统将包含以下功能和模块:1. 用户管理模块- 支持管理员和普通用户的注册和登录。
- 提供用户角色管理功能,分别设置不同角色的权限。
2. 维修记录模块- 支持录入和管理维修记录,包括客户信息、车辆信息、维修项目、材料和费用等。
- 提供维修记录的查询、修改和删除功能。
3. 统计分析模块- 根据维修项目或车辆进行统计分析,如总维修次数、平均费用等。
- 提供图表展示和导出功能,方便用户进行数据分析。
4. 安全和权限模块- 实现用户访问控制机制,保证数据安全性。
- 管理员具备对用户和权限的管理能力。
技术实现本系统的技术实现将采用以下技术:- 后端开发:使用Java语言和Spring框架进行开发,保证系统的稳定性和安全性。
- 数据库:使用关系型数据库进行数据存储和管理。
实施计划本系统的实施计划如下:1. 需求分析和系统设计阶段:预计持续2周,确定系统的功能和规格。
2. 开发阶段:预计持续4周,实现系统的各个功能模块。
3. 测试和调试阶段:预计持续1周,确保系统的稳定性和准确性。
4. 部署和上线阶段:预计持续1周,将系统部署到生产环境并上线使用。
总结汽车维修记录管理系统的开发将提高维修工作的效率和准确性,简化维修记录的管理过程,并提供有效的查询和分析功能。
整车行业车辆故障报告

整车行业车辆故障报告摘要:本文旨在对整车行业中车辆故障进行全面的分析和报告,通过详细描述各类故障并提供解决方案,以帮助行业内的相关人员更好地应对和解决这些问题。
引言:整车行业作为汽车产业链中的重要组成部分,负责汽车的设计、制造和销售。
然而,在车辆的使用过程中,难免会出现各种故障,给用户带来诸多不便。
因此,在整车行业中及时准确地报告和解决车辆故障问题变得尤为重要。
本报告将详细分析整车行业中常见的车辆故障,并提出相应的解决方案,旨在为整车行业提供参考和借鉴。
一、发动机故障发动机作为汽车的心脏,随着使用时间的增长,常常出现各种故障。
最常见的发动机故障包括点火系统故障、供油系统故障以及冷却系统故障等。
针对这些问题,解决方案可以包括定期保养和检查,及时更换磨损部件以及提高生产制造工艺等。
二、制动系统故障制动系统是车辆行驶中的关键系统之一,直接关系到行车安全。
常见的制动系统故障包括制动片磨损、刹车液泄漏以及制动失灵等。
解决这些问题的方法包括定期检查制动片磨损情况、保持刹车液的充足和定期更换刹车油等。
三、电气系统故障电气系统问题通常涉及到电池、线路和传感器等方面。
常见的故障包括电池电量不足、线路接触不良以及传感器故障等。
解决这些问题的办法可以包括定期检查电池电量、及时清洁电路接头以及更换故障传感器等。
四、悬挂系统故障悬挂系统对车辆的操控性和驾驶舒适性有着重要影响。
常见的悬挂系统故障包括减震器损坏、悬挂弹簧断裂以及悬挂系统噪音等。
解决这些问题的方法包括定期更换减震器、保持悬挂弹簧的弹性以及及时检查悬挂系统的紧固件等。
五、变速器故障变速器是整车行业中另一个容易出现故障的系统。
常见的变速器故障包括换挡不顺畅、变速箱漏油以及换挡冲击等。
解决这些问题的方法可以包括定期更换变速箱油、检查传动链条的紧固程度以及及时维护和保养变速器等。
六、安全气囊故障安全气囊作为车辆中重要的 pass事故保护系统,随着使用时间的增长也容易出现故障。
设备故障记录

设备故障记录2019年10月15日设备类型:生产线机器设备编号:PLM-001故障描述:设备无法启动,显示屏出现错误代码404。
故障发生时间:2019年10月14日,下午3点。
故障修复时间:2019年10月15日,上午10点。
修复人员:技术员李明故障原因:连接电源线松动导致供电中断。
修复过程:故障发生后,我立即调取了设备的故障代码手册,发现错误代码404表示设备供电中断。
首先,我检查了设备的电源线连接情况,发现电源线插头松动,导致供电中断。
我立即重新插好电源线,并确保插头牢固。
随后,我重新启动设备,设备顺利启动,显示屏无错误代码显示。
为了确保修复的有效性,我在设备运行了一段时间后进行了多次测试,确认设备故障已完全修复。
根因分析:此次设备故障是由于电源线连接不稳引起的。
经过分析,可能是在设备运行过程中,由于设备震动或其他外力造成了电源线插头脱落。
我们将进一步加强设备的维护和保养工作,并定期检查设备连接情况,确保设备正常运行。
预防措施:为了避免类似的设备故障再次发生,我们制定了以下预防措施:1. 设备巡检:定期对设备进行巡检,检查电源线及其他重要部件是否安全可靠。
2. 维护计划:建立设备维护计划,包括定期清洁、润滑和检查设备各部件的功能。
3. 培训和意识提高:加强员工对设备故障预防和检修的培训,提高他们对设备维护的重视。
4. 备品备件:加强备件管理,确保紧急情况下能够及时更换关键部件。
结论:通过本次设备故障记录和修复分析,我们找到了故障的根本原因,并采取了相应的措施进行修复和预防。
同时,我们也意识到设备维护的重要性,将进一步加强设备的保养和巡检工作,确保生产线的顺利运行。
以上是对本次生产线机器故障的详细记录和修复过程。
我们将持续关注设备运行情况,并不断优化维护措施,确保设备的安全和稳定运行。
注:此记录仅用于内部故障分析和修复参考,不得泄露给外部人员。
机械运行故障记录
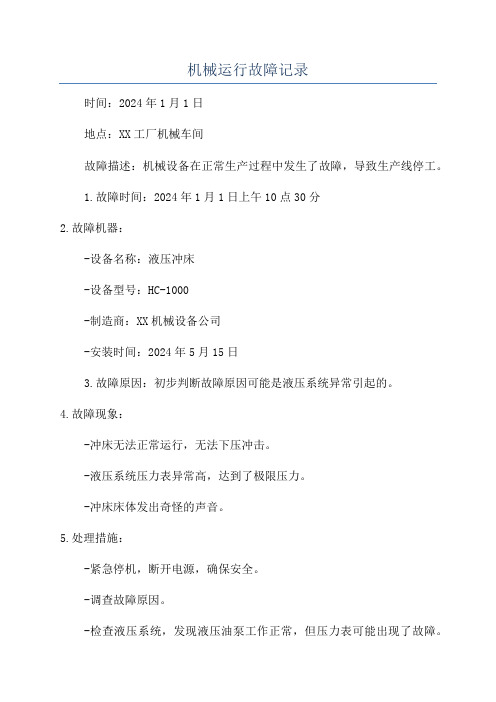
机械运行故障记录时间:2024年1月1日地点:XX工厂机械车间故障描述:机械设备在正常生产过程中发生了故障,导致生产线停工。
1.故障时间:2024年1月1日上午10点30分2.故障机器:-设备名称:液压冲床-设备型号:HC-1000-制造商:XX机械设备公司-安装时间:2024年5月15日3.故障原因:初步判断故障原因可能是液压系统异常引起的。
4.故障现象:-冲床无法正常运行,无法下压冲击。
-液压系统压力表异常高,达到了极限压力。
-冲床床体发出奇怪的声音。
5.处理措施:-紧急停机,断开电源,确保安全。
-调查故障原因。
-检查液压系统,发现液压油泵工作正常,但压力表可能出现了故障。
-检查底座和床体之间的连接,未发现异常。
-检查液压油管路,未发现泄漏。
6.故障排除:-将压力表更换为备用压力表。
-重新启动冲床,发现冲床可以正常下压冲击。
-测试运行15分钟,冲床运行正常,无异常声音。
7.结论:按照故障现象和排除过程来看,故障可能是压力表损坏导致的,更换压力表后冲床恢复正常运行。
8.预防措施:-定期检查液压系统压力表的工作状态,确保正常使用。
-加强设备维护保养工作,定期更换易损件。
9.故障记录者:XXX-职位:机械车间主任-签名:_____________________10.备注:-该故障记录仅作为参考,具体原因需要技术人员进一步检查确认。
-若类似故障再次发生,请立即报告相关人员进行处理。
以上为机械运行故障的记录,详细描述了故障发生的时间、地点、机器信息、故障现象、处理措施、故障排除过程、故障原因初步判断等内容,并提出了预防措施和备注。
这样的记录可以帮助团队了解故障发生的情况,追踪故障处理过程,并指导今后的预防工作。
生产线故障排查记录

生产线故障排查记录一、问题描述在本次生产线运行中,发现了故障现象。
具体描述如下:生产线在运行过程中,出现了频繁的停机现象,导致生产效率下降明显。
二、故障排查过程1. 观察故障现象经过仔细观察,发现停机现象发生在特定的工作站,每次停机时间约为5分钟左右。
而在停机期间,其他工作站的运行正常。
2. 检查设备状态针对出现停机现象的工作站,我们对设备进行了状态检查。
发现此工作站的设备在停机时,显示出异常的灯光闪烁,同时发出了异常的噪音。
3. 分析设备故障原因根据设备的异常现象,我们初步判断故障可能是由于设备的电源或者电路出现了问题。
为了进一步确定故障原因,我们进行了以下操作:a. 检查电源我们检查了设备的电源线路,发现电源线路连接良好,没有出现断裂或接触不良的情况。
b. 检查电路板我们拆开设备,检查了电路板的状态。
在检查过程中,发现一块电容出现凸起的迹象,初步判断此电容可能已经损坏。
c. 更换电容鉴于上述情况,我们决定更换故障的电容。
在更换过程中,我们使用了合适的工具,确保了更换的准确性。
4. 故障处理结果验证更换电容后,我们重新启动了生产线,并观察了一段时间。
经过验证,发现生产线的停机现象已经消失,设备运行正常,生产效率恢复到正常水平。
三、故障原因总结根据以上的故障排查过程和处理结果,我们可以推测故障的原因是电路板上的电容损坏,导致设备出现异常现象,进而引发停机问题。
通过及时更换故障电容,成功解决了问题,恢复了生产线的正常运行。
四、故障排查的启示本次故障排查过程中,我们从观察故障现象、检查设备状态、分析故障原因、故障处理结果验证等环节逐步进行,最终成功排查并解决了故障问题。
这次故障排查过程给我们带来了以下启示:1. 观察故障现象的重要性及时观察故障现象,有助于我们缩小故障范围、尽快定位问题,从而提高排查效率。
2. 设备维护的重要性定期对设备进行维护和检查,可以及时发现潜在问题并进行处理,避免故障发生。
3. 故障排查的系统性故障排查需要按照一定的步骤和流程进行,尤其是在处理复杂故障时更为重要。