加氢反应器的制造检验和使用与防腐
加氢装置设备常见腐蚀分析及防护措施

加氢装置设备常见腐蚀分析及防护措施摘要:本文简要介绍了对于高硫油的加氢装置中设备常见的腐蚀,初步分析了腐蚀产生的机理并介绍了一些防腐措施。
关键词:加氢装置腐蚀防护措施1、前言加氢是当今石油化工领域中处理高硫油的主要途径和方式。
随着国内炼油企业炼制进口高硫油的比例越来越大,新建的加氢装置也随之增多。
各类加氢装置中尤以加氢裂化和渣油加氢装置的操作条件最为苛刻,反应器操作压力近20MPa,反应温度也在400℃以上。
因此要搞好设备管理,必须对加氢的腐蚀状况及相应防护措施有一个全面的了解,对腐蚀做到早认识、早管理、早防护,不应有因腐蚀引起影响安全生产的事故发生。
现就加氢装置中一些常见的设备腐蚀原因及防护措施作一浅析。
2、加氢装置常见的腐蚀形态2.1、氢的腐蚀加氢装置中设备不可避免地要处于氢的环境中,氢分子既小又活波,再加上高温高压的操作条件,因此氢很容易渗入缸中并于钢种的成分发生反应。
氢的腐蚀可以分为两类:高温氢腐蚀和氢脆。
(1)高温氢腐蚀。
表现为两种形式:一是表面脱碳,二是内部脱碳和开裂。
以后一种的影响较大。
内部脱碳是由于氢扩散到钢中发生反应生产甲烷,即:Fe3C+2H2→CH4+3Fe。
甲烷在钢中的扩散能力很小,聚集于晶界空隙附近,形成局部高压,造成应力集中,使刚才产生龟裂、裂纹或鼓泡,导致刚才的强度和韧性显著下降。
这种腐蚀是不可逆现象,也称永久脆化现象。
(2)氢脆。
所谓氢脆是由于氢残留于钢中所引起的脆化现象,即原子氢在高温高压状态下侵入钢中,使钢材晶体的原子结合力变弱,或者成为氢分子在晶界或夹杂物周边析出。
产生氢脆的钢材其延伸率和断面收缩率都显著下降。
氢脆的发生一般是在发生氢渗入后恢复到150℃以下时发生。
如果在此温度上某一温度区间恒温一段时间析氢,则可以使氢较彻底的释放出来,钢材的力学性能仍可恢复,因此,氢脆是可逆的。
2.2、硫化氢的腐蚀在加氢装置中,由于原料中含有大量的硫,因此会有很多的H2S腐蚀介质生产。
PTA加氢反应器腐蚀风险及有效防范

工厂会使用板焊材料代替。
在这之后,PTA 加氢反应器也在不断发展,人们会基于检查当中发生的问题来进行完善,对反应器的结构进行优化、对其材料进行改进,这使PTA 加氢反应器能够在特殊的环境下使用,使用寿命不断延长、使用效果也不断增强。
2 PTA加氢反应器腐蚀风险2.1 PTA加氢反应器腐蚀机理当加氢反应器处于正常运行条件下的时候,对甲基二甲酸中醋酸与溴离子的浓度都是比较低的,这对加氢反应器衬里的腐蚀也并不严重。
但当溶液当中的卤素离子即溴离子与氯离子质量浓度超过了一定的门槛值之后,就会对加氢反应器奥氏体不锈钢产生点蚀作用。
在实际PTA 反应的过程当中,虽然介质当中卤素离子的浓度比较低,但是在反应过程当中会由于蒸发、沉积等导致离子在加氢反应器的垢下、缝隙等特殊部位产生高浓度沉积,形成一个酸性的环境,进而对加氢反应器的内部产生点坑腐蚀。
尤其是在气液交界处,溶液与氢气都呈翻腾的状态,如果出现溶液阻塞或者偏流问题的话,氢气、对苯二酸钾溶液以及钯炭催化剂这三者所形成的混合物就会产生剧烈的翻腾,不仅会对加氢反应器产生严重的冲刷,同时还会在局部形成气蚀环境,引起对材料的空泡腐蚀,导致加氢反应器内壁的不锈钢材料被破坏,进而腐蚀到材料的内部。
在这之后,腐蚀所形成的孔洞就会吸收溶液当中的卤素离子,使溴离子和氯离子在电泳的作用下自发地向孔洞处移动,进而导致腐蚀日益严重,最终使加氢反应器的衬里材料完全被穿透。
2.2 PTA加氢反应器腐蚀风险如果PTA 加氢反应器遭到腐蚀,就可能会产生一定的风险。
这会导致加氢反应器内衬的材料被彻底地暴露出来,由于内部的碳钢基材在被腐蚀的过程当中并不会发生“自催化”的问题,因此不会在表面处形成比较深和比较明显的坑洞,这种腐蚀并不严重,造成氢气泄漏的可能性也是比较小的。
在实践当中发现,即使加氢反应器的整个衬里完全地被腐蚀掉,对PTA 加氢反应器使用的安全性也并不会产生明显的影响。
因此,在发现加氢反应器的衬里出现穿透腐蚀问题的话,工作人员只需要做好相应的修复,就可以将介质与基材相互隔离,以此来确保加氢反应器整个壳体的安全性。
临氢设备的腐蚀与防护以及检修期间的注意事项

临氢设备的腐蚀与防护以及检修期间的注意事项一、反应器的腐蚀与防护:1、堆焊层氢致剥离现象的特征加氢装置中,用于高温高压场合的一些设备(主要是加氢反应器),为了抵抗H2S的腐蚀,在内表面都堆焊了几毫米厚的不锈钢堆焊层(多为奥氏体不锈钢)。
主体材料2.25Cr-1Mo,堆焊层E309L、E347。
在在此类反应器上曾发现了不锈钢堆焊层剥离损伤现象。
堆焊层剥离现象有如下主要特征:1)堆焊层剥离现象也是氢致延迟开裂的一种形式。
高温高压氢环境下操作的反应器,氢会侵入扩散到器壁中。
由于制作反应器本体材料的Cr-Mo钢(如21/4Cr-lMo钢)和堆焊层用的奥氏体不锈钢(如E309和E347)的结晶结构不同,因而氢的溶解度和扩散速度都不一样,使堆焊层界面上氢浓度形成不连续状态,而且由于母材的溶解度与温度的依赖性更大,当反应器从正常运行状态下停工冷却到常温状态时,在过渡区界面上的堆焊层侧聚集大量的氢而引起脆化。
另外,由于母材和堆焊层材料的线膨胀系数差别较大,在反应器制造时会形成相当可观的残余应力。
上述这些原因就有可能使堆焊层界面发生剥离,而且经过超声检测和声发射试验的监测,发现剥离并不是从操作状态冷却到常温时就马上发生,而是要经过一段时间以后(需要一定的孕育期)才可观察到这种现象。
尽量避免非计划紧急停车;在正常停工时要采取使氢尽可能释放出去的停工条件,以减少残留氢量。
2.氢脆现象所谓氢脆,就是由于氢残留在钢中所引起的脆化现象。
产生了氢脆的钢材,其延伸率和断面收缩率显著下降。
这是由于侵人钢中的原子氢,使结晶的原子结合力变弱,或者作为分子状在晶界或夹杂物周边上析出的结果。
但是,在一定条件下,若能使氢较彻底地释放出来,钢材的力学性能仍可得到恢复。
氢脆是可逆的,也称作一次脆化现象。
对于操作在高温高压氢环境下的设备,在操作状态下,器壁中会吸收一定量的氢。
在停工的过程中,若冷却速度太快,使吸藏的氢来不及扩散出来,造成过饱和氢残留在器壁内,就可能在温度低于150℃时引起亚临界裂纹扩展,对设备的安全使用带来威胁。
探讨加氢装置的防腐处理

探讨加氢装置的防腐处理在当前我国炼化企业的安全生产中,腐蚀是一个非常大的隐患,设备装置在腐蚀作用下,常常会出现开裂、穿孔等问题。
在炼油厂中,加氢精制装置是一种二次加工装置,具有三种工况,即临氢工况、高压工况、高温工况,在介质中含有多种成分,包括HCN、HCI、H2S、NH3 等,因而加氢精制装置的腐蚀情况是非常复杂的。
基于此,本文对加氢装置的防腐处理进行深入研究,本文中共提出了两种防腐处理措施,即设备防腐措施和工艺防腐措施,具有重要意义。
标签:加氢装置;防腐处理;设备防腐;工艺防腐1 引言在最近几年中,自老油田发展到稳产、衰减时期以来,加工原油的劣质化、多样化变得越来越严重,相应地,加氢装置设备出现越来越严重的腐蚀问题,因腐蚀而常常会引发多种事故,如爆炸事故、着火事故、泄漏事故等,导致加氢装置的稳定安全运行遭受严重影响。
基于此,本文对加氢装置的防腐处理进行深入研究,具有重要意义。
2 加氢装置的防腐处理措施2.1 设备的防腐措施针对设备的防腐措施,主要涉及三大方面,即表面防腐、结构防腐、材料防腐。
①表面防腐,就是指将金属合金、铝或者锌喷涂在设备的内壁上,形成阴极保护,能够对电化学腐蚀起到显著的抑制作用,或者将防腐涂料涂刷在设备的内壁上,有效隔离腐蚀介质和金属基体。
②结构防腐,就是指包括在设备的设计上,尽量保证结构的简单化,尽可能不要对用异种金属组合进行使用,同时应对逐渐过渡原则进行考虑,需要对较低的局部应力和热应力进行有效保持,进而在整个运行过中,能够保证加氢装置不会发生不良现象,如腐蚀产物积存、湍流、热负荷分配不够均匀、腐蚀介质停滞等。
③针对材料防腐,对材料材质进行升级是一种非常重要的方法。
将条件、介质环境作为主要依据,同时对有关设计标准进行有机结合,以确定材质。
只有对钢材焊接热影响区的硬度进行有效降低,对宏观缺陷进行有效消除,才能够有效避免出现氢脆现象;针对硫化氢腐蚀、高温氢腐蚀现象发生位置,应将Couper曲线、经验数据作为主要依据,以对材质进行合理选取。
加氢装置反应器的腐蚀与防护 杜煜

加氢装置反应器的腐蚀与防护杜煜发表时间:2020-05-08T11:36:53.603Z 来源:《电力设备》2020年第2期作者:杜煜王贺孟祥雷王天生[导读] 摘要:由于加氢精制装置操作条件的特殊性,加氢精制反应器有可能出现一些如氢脆、氢腐蚀、不锈钢堆焊层的剥离等特殊的损伤现象。
(中国石油辽阳石化油化厂辽宁辽阳 111003)摘要:由于加氢精制装置操作条件的特殊性,加氢精制反应器有可能出现一些如氢脆、氢腐蚀、不锈钢堆焊层的剥离等特殊的损伤现象。
为避免这些破坏性损伤的产生,加氢精制反应器必须要有正确的设计与选材,并且合理使用,从而保证设备的使用安全。
关键词:加氢精制反应器;腐蚀;防护加氢精制反应器是加氢精制装置中的核心设备。
由于原料的不同,其操作条件也不尽相同,从汽油、煤油、柴油、蜡油到渣油,其反应温度和反应压力逐渐增大。
一般来说,加氢精制反应器操作温度的范围为60~420°C,操作压力的范围为1.5~16 MPa。
正因其操作条件相当苛刻,技术难度大,制造技术要求高,造价昂贵,所以不管在设计上还是使用上人们都对它给予极大的重视。
为避免发生破坏性的损伤,加氢反应器必须要有正确的设计与选材,并且合理使用。
1加氢精制反应器的腐蚀类型1.1氢脆所谓氢脆,是指由于氢残留在钢中所引起的脆化现象。
氢脆是可逆的,也称作一次脆化现象。
产生了氢脆的钢材,其延伸率和断面收缩率显著下降。
氢脆一般发生在150 °C以下,所以实际装置中氢脆损伤往往发生在装置停工过程中的低温阶段。
氢脆的敏感性一般是随钢材强度的提高而增加,钢材的氢脆化程度与钢中的氢含量密切相关(可以认为,在可能发生氢脆的温度下,会存在着不引起亚临界裂纹扩展的氢浓度,称之为安全氢浓度。
它与钢材的强度水平、裂纹尖端的拉应力大小以及裂纹的几何尺寸有关)。
对于工作在高温高压氢环境下的反应器,在操作状态下,器壁中会吸收一定量的氢,在停工的过程中,若冷却速度过快,使吸藏的氢来不及扩散出来,造成过饱和氢残留在器壁内,就有可能引起亚临界裂纹的扩展,给设备的安全使用带来威胁。
加氢装置防腐方案

加氢装置防腐方案加氢装置是一种常见的化工设备,一般用于将原料气体或液体与氢气进行反应,以产生更高价值的化学品。
由于加氢装置工作环境的特殊性,容易受到腐蚀的影响,因此需要采取一些防腐措施,以延长设备的使用寿命和保证工作安全。
下面是一些可行的加氢装置防腐方案。
1.原材料选择:选取耐腐蚀性能较好的材料作为设备的构成部分。
一般来说,钢材和不锈钢在加氢装置中被广泛采用。
对于一些特殊环境,如高温高压下的加氢反应,可考虑使用高合金材料,如镍基合金、铬钼合金等。
2.表面处理:对设备表面进行特殊处理,以增强其耐腐蚀性。
常见的表面处理方法包括化学镀、电镀、热浸镀等。
这些处理方法能够在设备表面形成一层保护膜,减少对金属的腐蚀。
3.内部涂层:在设备内部涂覆一层耐腐蚀的涂层。
这种涂层可以起到物理和化学的双重防护作用,阻隔原料气体和液体与设备金属接触,减少腐蚀的发生。
常见的内部涂层材料有聚四氟乙烯、聚酯、聚乙烯等。
4.防腐层检测:定期检测设备防腐层的状况。
使用无损检测技术,如超声波、X射线等,对设备表面进行检测,查找可能存在的腐蚀点、气泡和裂纹等缺陷,以及判定防腐层的粘结强度和厚度是否满足要求。
如发现问题,及时进行维修和更换。
5.设备运维:加强设备的日常维护管理,定期进行设备的清洗和检修。
清洗可以去除设备内部残留物和附着层,减少腐蚀的发生。
检修可以及时发现和处理设备的故障、漏点和腐蚀现象,保证设备的正常运行。
6.保持良好的工艺控制:控制加氢装置的工艺参数,如温度、压力和流速等,防止其超过设备的承受能力,从而减少腐蚀的发生。
合理设计和选择反应操作条件,降低设备的腐蚀风险。
7.定期监测氢气的纯度:加氢装置中的氢气纯度会直接影响设备的腐蚀程度。
定期测试和监测氢气的纯度,确保其达到设备要求,避免过高或过低的氢气纯度对设备的腐蚀。
综上所述,加氢装置的防腐方案可以从材料选择、表面处理、内部涂层、防腐层检测、设备运维、工艺控制和氢气纯度监测等方面入手。
加氢反应器检验细则
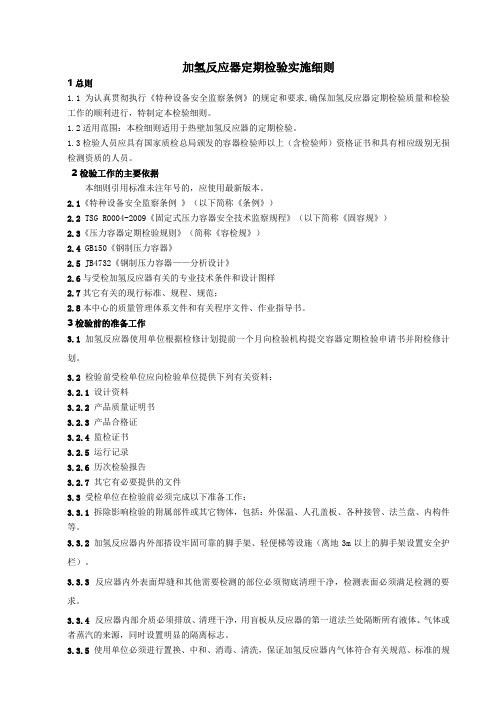
加氢反应器定期检验实施细则1总则1.1为认真贯彻执行《特种设备安全监察条例》的规定和要求,确保加氢反应器定期检验质量和检验工作的顺利进行,特制定本检验细则。
1.2适用范围:本检细则适用于热壁加氢反应器的定期检验。
1.3检验人员应具有国家质检总局颁发的容器检验师以上(含检验师)资格证书和具有相应级别无损检测资质的人员。
2检验工作的主要依据本细则引用标准未注年号的,应使用最新版本。
2.1《特种设备安全监察条例》(以下简称《条例》)2.2 TSG R0004-2009《固定式压力容器安全技术监察规程》(以下简称《固容规》)2.3《压力容器定期检验规则》(简称《容检规》)2.4 GB150《钢制压力容器》2.5 JB4732《钢制压力容器——分析设计》2.6与受检加氢反应器有关的专业技术条件和设计图样2.7其它有关的现行标准、规程、规范;2.8本中心的质量管理体系文件和有关程序文件、作业指导书。
3检验前的准备工作3.1加氢反应器使用单位根据检修计划提前一个月向检验机构提交容器定期检验申请书并附检修计划。
3.2检验前受检单位应向检验单位提供下列有关资料:3.2.1 设计资料3.2.2 产品质量证明书3.2.3 产品合格证3.2.4 监检证书3.2.5 运行记录3.2.6 历次检验报告3.2.7 其它有必要提供的文件3.3受检单位在检验前必须完成以下准备工作:3.3.1 拆除影响检验的附属部件或其它物体,包括:外保温、人孔盖板、各种接管、法兰盘、内构件等。
3.3.2 加氢反应器内外部搭设牢固可靠的脚手架、轻便梯等设施(离地3m以上的脚手架设置安全护栏)。
3.3.3反应器内外表面焊缝和其他需要检测的部位必须彻底清理干净,检测表面必须满足检测的要求。
3.3.4反应器内部介质必须排放、清理干净,用盲板从反应器的第一道法兰处隔断所有液体、气体或者蒸汽的来源,同时设置明显的隔离标志。
3.3.5使用单位必须进行置换、中和、消毒、清洗,保证加氢反应器内气体符合有关规范、标准的规定。
热壁加氢反应器的制造和检验(一)
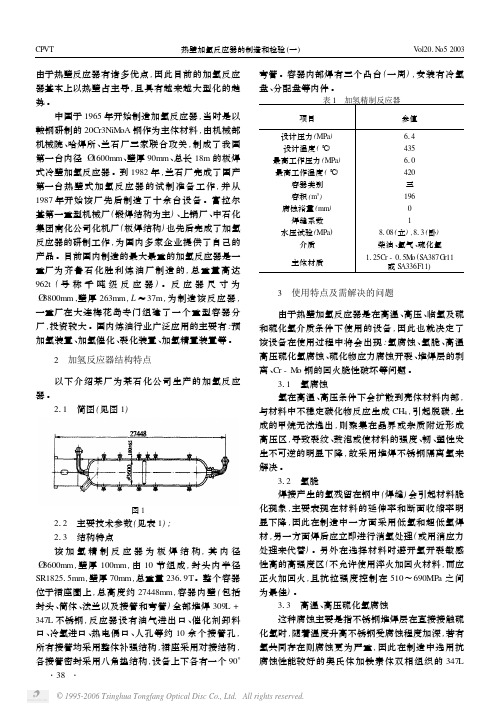
浅谈PTA加氢反应器腐蚀风险及有效防范
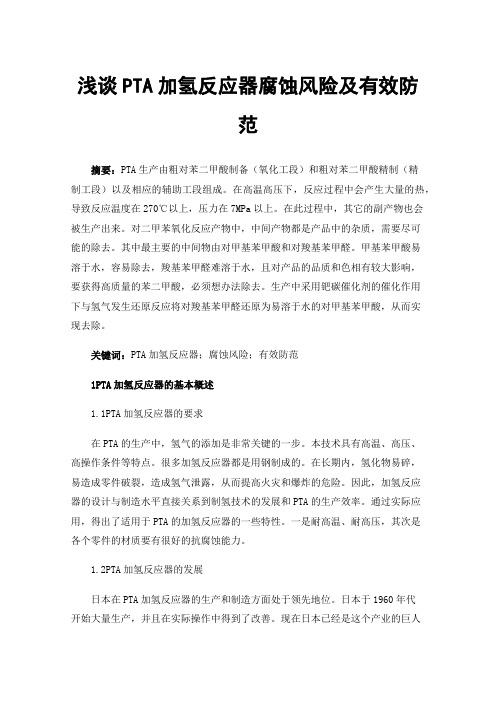
浅谈PTA加氢反应器腐蚀风险及有效防范摘要:PTA生产由粗对苯二甲酸制备(氧化工段)和粗对苯二甲酸精制(精制工段)以及相应的辅助工段组成。
在高温高压下,反应过程中会产生大量的热,导致反应温度在270℃以上,压力在7MPa以上。
在此过程中,其它的副产物也会被生产出来。
对二甲苯氧化反应产物中,中间产物都是产品中的杂质,需要尽可能的除去。
其中最主要的中间物由对甲基苯甲酸和对羧基苯甲醛。
甲基苯甲酸易溶于水,容易除去,羧基苯甲醛难溶于水,且对产品的品质和色相有较大影响,要获得高质量的苯二甲酸,必须想办法除去。
生产中采用钯碳催化剂的催化作用下与氢气发生还原反应将对羧基苯甲醛还原为易溶于水的对甲基苯甲酸,从而实现去除。
关键词:PTA加氢反应器;腐蚀风险;有效防范1PTA加氢反应器的基本概述1.1PTA加氢反应器的要求在PTA的生产中,氢气的添加是非常关键的一步。
本技术具有高温、高压、高操作条件等特点。
很多加氢反应器都是用钢制成的。
在长期内,氢化物易碎,易造成零件破裂,造成氢气泄露,从而提高火灾和爆炸的危险。
因此,加氢反应器的设计与制造水平直接关系到制氢技术的发展和PTA的生产效率。
通过实际应用,得出了适用于PTA的加氢反应器的一些特性。
一是耐高温、耐高压,其次是各个零件的材质要有很好的抗腐蚀能力。
1.2PTA加氢反应器的发展日本在PTA加氢反应器的生产和制造方面处于领先地位。
日本于1960年代开始大量生产,并且在实际操作中得到了改善。
现在日本已经是这个产业的巨人了。
在应用的早期,PTA加氢反应器是以多种高强度的材料为主。
外层一般用铬钼钢板制造,而内层用不锈钢制造。
尽管这种反应器可以达到生产的要求,但是它不能通过超声波探测来探测其内部的问题,从而增加了它的安全性。
20世纪七十年代,采用了锻压和焊接结构,取代了传统的钢板,有些厂家采用了钢板焊接。
从那时起,PTA加氢反应器就一直在发展,并针对存在的问题进行改进,包括对反应器的结构和材质的优化,以保证PTA加氢反应器在特定的环境下运行,使其寿命和运行效率得到了进一步的改善。
加氢精制装置腐蚀检查及防腐措施
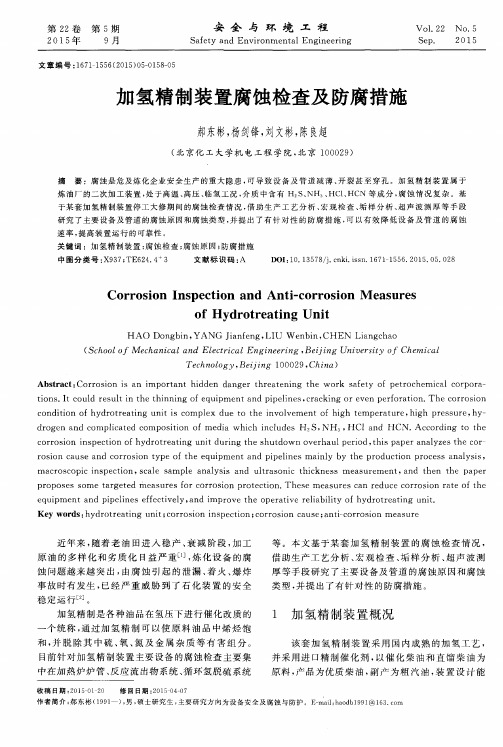
文章 编 号 : 1 6 7 1 1 5 5 6 ( 2 0 1 5 ) 0 5 — 0 1 5 8 — 0 5
安 全 与 环 境 工 程
Sa f e t y a nd Env i r o nm e n t a l Eng i ne e r i n g
Te c h n o l o g y, Be i j i n g 1 0 0 0 2 9 , Ch i n a)
Abs t r a c t : Cor r o s i on i s a n i mp or t a nt hi d de n da ng e r t hr e a t e ni ng t h e wo r k s a f e t y o f p e t r o c h e mi c a l c or p or a — t i o ns . I t c ou l d r e s u l t i n t he t h i nn i ng of e q ui p me nt a nd p i pe l i ne s , c r a c ki ng o r e v e n pe r f o r a t i o n. The c o r r o s i on c o nd i t i o n o f h yd r ot r e a t i n g un i t i s c o mp l e x d ue t o t he i n vo l v e me nt o f hi g h t e mpe r a t ur e, hi g h p r e s s ur e, hy —
dr o g e n a nd c o mp l i c a t e d c o mp os i t i on of me di a w hi c h i n c l ud e s H 2 S, NH 3 , H C1 a n d H CN . Ac c or d i ng t o t h e
加氢装置工艺防腐导则

加氢装置工艺防腐导则前言:为保证加氢装置正常运行,设备良好运行和备用,根据加氢装置的不同部位腐蚀要素,制定了本工艺防腐规定,并在日常管理中进行控制和检查落实。
导则内容:一、正常生产运行中的控制1、原料性质控制2、新氢性质控制3、反冲洗过滤器控制4、加热炉控制壁板,延壁板上升运动,到达炉顶与炉墙相交部位后聚集,浓度达到最大,随着环境温度的变化,H2SO4凝结在炉壁板,发生低温硫酸腐蚀。
SO2与水蒸气化和生成亚硫酸气,它的露点温度低,在较低温度下凝结,发生低温亚硫酸腐蚀。
少量的H2S在一定浓度、温度、条件下易发生硫化物腐蚀。
反应式2SO2+O2 = 2SO3 (可逆反应,当降低温度时,平衡向右方移动,所以随着烟气温度的降低,SO2转化成SO3的转化率越大)SO3↑+ H2O↑= H2SO4↑,H2SO4 ↑+ H2O→H2SO4(浓)* H2OH2SO4(浓)+ H2O→H2SO4(稀)* H2O加热炉露点腐蚀温度的计算影响烟气露点温度的主要因素1 含硫量烟气中硫酸蒸气大部分由瓦斯气中硫分氧化而来的。
瓦斯气中含硫量越高,烟气露点温度越高。
因而在实际运行程中,必须严格控制瓦斯气含硫量。
2 温度当压力一定时,SO2转化成 SO3的平衡曲线如图2所示。
从该图可以看出低温时对转化成SO3有利。
在850℃以上的高温下,SO3几乎不产生。
在温度相同时,压力升高会增加向SO3方面的转化。
但实际上,因原子氧、SO3触媒及飞灰的作用而变得更为复杂。
3 过量空气系数烟气含氧量越高,由SO2转化为SO3的比例会越大。
因而,在保证充分燃烧的前提下,应尽量采用低过量空气系数,减少SO3的生成量,降低烟气露点温度。
4 水蒸汽烟气中水蒸气的浓度愈大。
水蒸气的分压力也愈大。
只考虑水蒸气的影响,水蒸气对烟气露点的影响如图3所示。
因而在实际运行过程中,应严格控制瓦斯气含水率,降低烟气露点温度。
但在实际过程中,控制瓦斯气含水率非常困难,因而通常是在设计中尽量避开露点或采取相应的防腐措施。
加氢反应器制造工艺技术分析
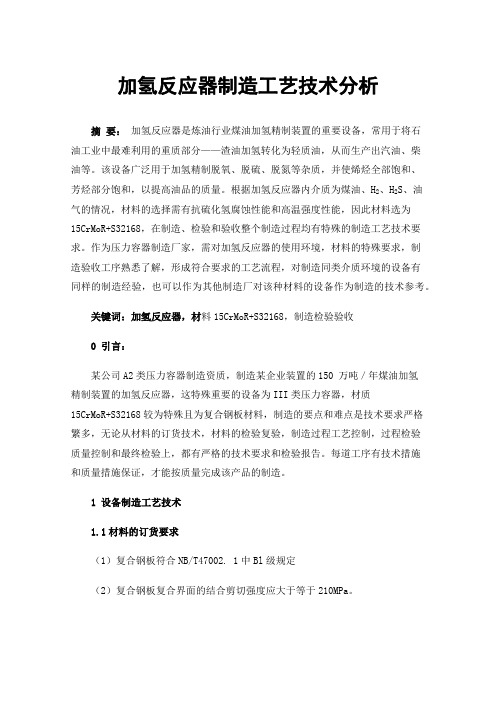
加氢反应器制造工艺技术分析摘要:加氢反应器是炼油行业煤油加氢精制装置的重要设备,常用于将石油工业中最难利用的重质部分——渣油加氢转化为轻质油,从而生产出汽油、柴油等。
该设备广泛用于加氢精制脱氧、脱硫、脱氮等杂质,并使烯烃全部饱和、芳烃部分饱和,以提高油品的质量。
根据加氢反应器内介质为煤油、H2、H2S、油气的情况,材料的选择需有抗硫化氢腐蚀性能和高温强度性能,因此材料选为15CrMoR+S32168,在制造、检验和验收整个制造过程均有特殊的制造工艺技术要求。
作为压力容器制造厂家,需对加氢反应器的使用环境,材料的特殊要求,制造验收工序熟悉了解,形成符合要求的工艺流程,对制造同类介质环境的设备有同样的制造经验,也可以作为其他制造厂对该种材料的设备作为制造的技术参考。
关键词:加氢反应器,材料15CrMoR+S32168,制造检验验收0引言:某公司A2类压力容器制造资质,制造某企业装置的150 万吨/年煤油加氢精制装置的加氢反应器,这特殊重要的设备为III类压力容器,材质15CrMoR+S32168较为特殊且为复合钢板材料,制造的要点和难点是技术要求严格繁多,无论从材料的订货技术,材料的检验复验,制造过程工艺控制,过程检验质量控制和最终检验上,都有严格的技术要求和检验报告。
每道工序有技术措施和质量措施保证,才能按质量完成该产品的制造。
1设备制造工艺技术1.1材料的订货要求(1)复合钢板符合NB/T47002. 1中Bl级规定(2)复合钢板复合界面的结合剪切强度应大于等于210MPa。
(3)复合钢板应进行内弯(复层表面受压)和外弯(复合表面受拉)试验,试验。
复合钢板的晶间腐蚀试验应符合 GB 4334 中方法 E "不锈钢硫酸-硫酸铜腐蚀试验方法” 的规定。
(4)15CrMoR 基层钢板交货状态:正火+回火。
100%超声检测,I级合格,符合标准NB/T47013.3的要求。
(5)钢板的化学成分和力学性能符合下表表1.1-1 化学成分表1.1-2力学性能(6)设备制造厂应根据对筒体材料和堆焊层的要求,经过焊接工艺评定,选出用千15CrMoR基层的焊接材料(R307)和用千S32168复层的焊接材料(A132)及过渡层焊接材料(A302)。
预加氢反应器的制造和检验

预 加 氢 反 应 器 的 制 造 和 检 验
才 福 胜
( 西 化 工 机 械 ( 团 ) 限 责 任 公 一 ,辽 宁 葫 芦 岛 1 5 0 锦 集 有 J 2 0 1)
ቤተ መጻሕፍቲ ባይዱ
摘 要 :介 绍 了预 加 氢反 应 器的典 型 结构 , 分析 了制 造难 点 , 有针 对性 地提 出 了解决 难点 的特 殊 工艺 方案 。其 积 累的制 造经验 , 对类似 设备 的制 造 有一 定的 参考 价值 。
m a f c u e wa a l e nu a t r s nayz d, t t c o og c l r c du e n e o d he a e f he e hn l ia p o e r a d nc de t d t o ma f c u e nu a t r pr e s we e pr s n e . I s i or a t t he smia q i oc s r e e t d ti mp t n o t i l r e u pme n ma f c ur . nti nu a t e
关 键 词 :预加氢反应器 ; 制造 ;工艺
中图分 类 号 :TQ 0 2 4 5.
文 献标 志码 : B
M a f c u e o e hy r t e tn a t r nu a t r fPr — d o r a i g Re c o
CAI Fu s e — h ng
整体 补 强 结 构 , 质 为 1 C Mo锻 件 + ( 3 9 材 5r E 0 I+
E 4) 3 7 双层 堆焊 , 锻件 符 合 J / 7 6 2 0 承压 B T 4 2 - 0 0《
这些 加 氢反 应器 和预 加氢 反应 器大 多 为三类 压力 容 器, 长期 在 高温 、 压 、 氢 及硫 和硫 化 氢 介 质 条 件 高 临 下使 用 , 在使 用过 程 中将 会 出 现 氢腐 蚀 、 氢脆 、 温 高 高压 硫化 氢腐 蚀 、 硫化 物应 力腐 蚀开 裂 、 堆焊层 的剥
加氢反应器腐蚀损伤分析及对策
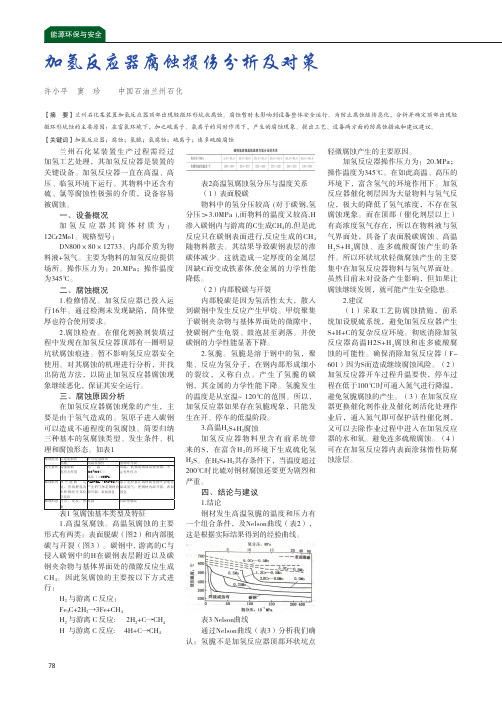
78兰州石化某装置生产过程需经过加氢工艺处理,其加氢反应器是装置的关键设备。
加氢反应器一直在高温、高压、临氢环境下运行。
其物料中还含有硫、氯等腐蚀性极强的介质,设备容易被腐蚀。
一、设备概况加氢反应器其筒体材质为:12Cr2Mo1。
规格型号:DN800×80×12733。
内部介质为物料液+氢气。
主要为物料的加氢反应提供场所。
操作压力为:20.MPa;操作温度为345℃。
二、腐蚀概况1.检修情况。
加氢反应器已投入运行16年。
通过检测未发现缺陷,筒体壁厚也符合使用要求。
2.腐蚀检查。
在催化剂换剂装填过程中发现在加氢反应器顶部有一圈明显坑状腐蚀痕迹。
暂不影响氢反应器安全使用。
对其腐蚀的机理进行分析,并找出防范方法,以防止加氢反应器腐蚀现象继续恶化,保证其安全运行。
三、腐蚀原因分析在加氢反应器腐蚀现象的产生,主要是由于氢气造成的。
氢原子进入碳钢可以造成不通程度的氢腐蚀。
简要归纳三种基本的氢腐蚀类型、发生条件、机理和腐蚀形态。
如表1表1 氢腐蚀基本类型及特征1.高温氢腐蚀。
高温氢腐蚀的主要形式有两类:表面脱碳(图2)和内部脱碳与开裂(图3)。
碳钢中, 游离的C与侵入碳钢中的H在碳钢表层附近以及碳钢夹杂物与基体界面处的微隙反应生成CH4。
因此氢腐蚀的主要按以下方式进行:H2 与游离 C 反应:Fe3C+2H2→3Fe+CH4H2 与游离 C 反应: 2H2+C→CH4H 与游离 C 反应: 4H+C→CH4表2高温氢腐蚀氢分压与温度关系(1)表面脱碳物料中的氢分压较高 (对于碳钢,氢分压>3.0MPa ),而物料的温度又较高,H渗入碳钢内与游离的C生成CH4的,但是此反应只在碳钢表面进行,反应生成的CH4随物料散去。
其结果导致碳钢表层的渗碳体减少。
这就造成一定厚度的金属层因缺C而变成铁素体,使金属的力学性能降低。
(2)内部脱碳与开裂内部脱碳是因为氢活性太大,散入到碳钢中发生反应产生甲烷。
甲烷聚集于碳钢夹杂物与基体界面处的微隙中,使碳钢产生龟裂、鼓泡甚至剥落。
柴油加氢装置的腐蚀分析及其防腐措施研究
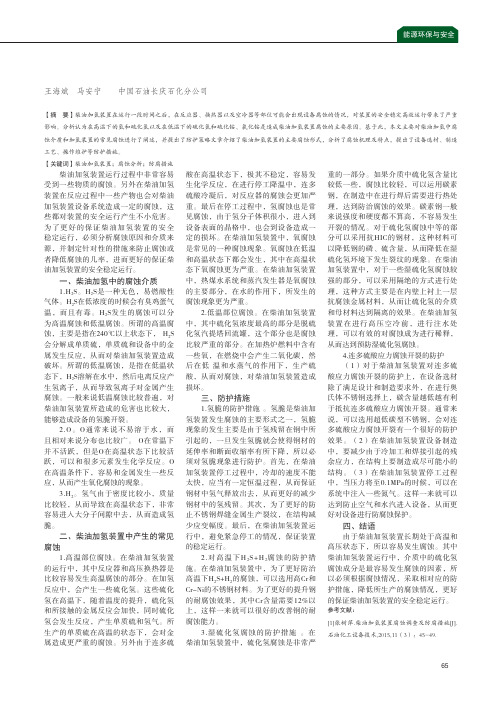
柴油加氢装置运行过程中非常容易受到一些物质的腐蚀。
另外在柴油加氢装置在反应过程中一些产物也会对柴油加氢装置设备系统造成一定的腐蚀,这些都对装置的安全运行产生不小危害。
为了更好的保证柴油加氢装置的安全稳定运行,必须分析腐蚀原因和介质来源,并制定针对性的措施来防止腐蚀或者降低腐蚀的几率,进而更好的保证柴油加氢装置的安全稳定运行。
一、柴油加氢中的腐蚀介质1.H2S。
H2S是一种无色,易燃酸性气体。
H2S在低浓度的时候会有臭鸡蛋气温,而且有毒。
H2S发生的腐蚀可以分为高温腐蚀和低温腐蚀。
所谓的高温腐蚀,主要是指在240℃以上状态下, H2S 会分解成单质硫,单质硫和设备中的金属发生反应,从而对柴油加氢装置造成破坏。
所谓的低温腐蚀,是指在低温状态下,H2S溶解在水中,然后电离反应产生氢离子,从而导致氢离子对金属产生腐蚀。
一般来说低温腐蚀比较普遍,对柴油加氢装置所造成的危害也比较大,能够造成设备的氢脆开裂。
2.O。
O通常来说不易溶于水,而且相对来说分布也比较广。
O在常温下并不活跃,但是O在高温状态下比较活跃,可以和很多元素发生化学反应。
O 在高温条件下,容易和金属发生一些反应,从而产生氧化腐蚀的现象。
3.H2。
氢气由于密度比较小,质量比较轻,从而导致在高温状态下,非常容易进入大分子间隙中去,从而造成氢脆。
二、柴油加氢装置中产生的常见腐蚀1.高温部位腐蚀。
在柴油加氢装置的运行中,其中反应器和高压换热器是比较容易发生高温腐蚀的部分。
在加氢反应中,会产生一些硫化氢。
这些硫化氢在高温下,随着温度的提升,硫化氢和所接触的金属反应会加快,同时硫化氢会发生反应,产生单质硫和氢气。
所生产的单质硫在高温的状态下,会对金属造成更严重的腐蚀。
另外由于连多硫酸在高温状态下,极其不稳定,容易发生化学反应,在进行停工降温中,连多硫酸冷凝后,对反应器的腐蚀会更加严重。
最后在停工过程中,氢腐蚀也是常见腐蚀,由于氢分子体积很小,进入到设备表面的晶格中,也会到设备造成一定的损坏。
加氢反应器检验细则
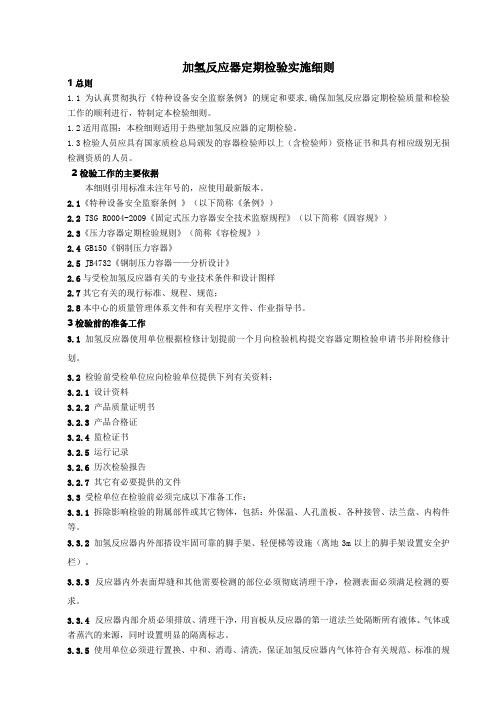
加氢反应器定期检验实施细则1总则1.1为认真贯彻执行《特种设备安全监察条例》的规定和要求,确保加氢反应器定期检验质量和检验工作的顺利进行,特制定本检验细则。
1.2适用范围:本检细则适用于热壁加氢反应器的定期检验。
1.3检验人员应具有国家质检总局颁发的容器检验师以上(含检验师)资格证书和具有相应级别无损检测资质的人员。
2检验工作的主要依据本细则引用标准未注年号的,应使用最新版本。
2.1《特种设备安全监察条例》(以下简称《条例》)2.2 TSG R0004-2009《固定式压力容器安全技术监察规程》(以下简称《固容规》)2.3《压力容器定期检验规则》(简称《容检规》)2.4 GB150《钢制压力容器》2.5 JB4732《钢制压力容器——分析设计》2.6与受检加氢反应器有关的专业技术条件和设计图样2.7其它有关的现行标准、规程、规范;2.8本中心的质量管理体系文件和有关程序文件、作业指导书。
3检验前的准备工作3.1加氢反应器使用单位根据检修计划提前一个月向检验机构提交容器定期检验申请书并附检修计划。
3.2检验前受检单位应向检验单位提供下列有关资料:3.2.1 设计资料3.2.2 产品质量证明书3.2.3 产品合格证3.2.4 监检证书3.2.5 运行记录3.2.6 历次检验报告3.2.7 其它有必要提供的文件3.3受检单位在检验前必须完成以下准备工作:3.3.1 拆除影响检验的附属部件或其它物体,包括:外保温、人孔盖板、各种接管、法兰盘、内构件等。
3.3.2 加氢反应器内外部搭设牢固可靠的脚手架、轻便梯等设施(离地3m以上的脚手架设置安全护栏)。
3.3.3反应器内外表面焊缝和其他需要检测的部位必须彻底清理干净,检测表面必须满足检测的要求。
3.3.4反应器内部介质必须排放、清理干净,用盲板从反应器的第一道法兰处隔断所有液体、气体或者蒸汽的来源,同时设置明显的隔离标志。
3.3.5使用单位必须进行置换、中和、消毒、清洗,保证加氢反应器内气体符合有关规范、标准的规定。
重整预加氢腐蚀与防腐问题的探讨
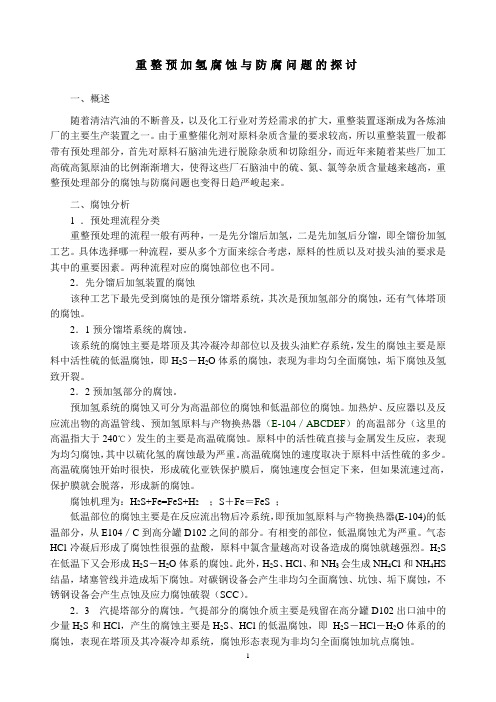
重整预加氢腐蚀与防腐问题的探讨一、概述随着清洁汽油的不断普及,以及化工行业对芳烃需求的扩大,重整装置逐渐成为各炼油厂的主要生产装置之一。
由于重整催化剂对原料杂质含量的要求较高,所以重整装置一般都带有预处理部分,首先对原料石脑油先进行脱除杂质和切除组分,而近年来随着某些厂加工高硫高氮原油的比例渐渐增大,使得这些厂石脑油中的硫、氮、氯等杂质含量越来越高,重整预处理部分的腐蚀与防腐问题也变得日趋严峻起来。
二、腐蚀分析1 .预处理流程分类重整预处理的流程一般有两种,一是先分馏后加氢,二是先加氢后分馏,即全馏份加氢工艺。
具体选择哪一种流程,要从多个方面来综合考虑,原料的性质以及对拔头油的要求是其中的重要因素。
两种流程对应的腐蚀部位也不同。
2.先分馏后加氢装置的腐蚀该种工艺下最先受到腐蚀的是预分馏塔系统,其次是预加氢部分的腐蚀,还有气体塔顶的腐蚀。
2.1预分馏塔系统的腐蚀。
该系统的腐蚀主要是塔顶及其冷凝冷却部位以及拔头油贮存系统,发生的腐蚀主要是原料中活性硫的低温腐蚀,即H2S-H2O体系的腐蚀,表现为非均匀全面腐蚀,垢下腐蚀及氢致开裂。
2.2预加氢部分的腐蚀。
预加氢系统的腐蚀又可分为高温部位的腐蚀和低温部位的腐蚀。
加热炉、反应器以及反应流出物的高温管线、预加氢原料与产物换热器(E-104/ABCDEF)的高温部分(这里的高温指大于240℃)发生的主要是高温硫腐蚀。
原料中的活性硫直接与金属发生反应,表现为均匀腐蚀,其中以硫化氢的腐蚀最为严重。
高温硫腐蚀的速度取决于原料中活性硫的多少。
高温硫腐蚀开始时很快,形成硫化亚铁保护膜后,腐蚀速度会恒定下来,但如果流速过高,保护膜就会脱落,形成新的腐蚀。
腐蚀机理为:H2S+Fe=FeS+H2;S+Fe=FeS ;低温部位的腐蚀主要是在反应流出物后冷系统,即预加氢原料与产物换热器(E-104)的低温部分,从E104/C到高分罐D102之间的部分。
有相变的部位,低温腐蚀尤为严重。
浅谈加氢反应器的检验

反应器 表面是否存在严重的 问题 ,从而快速的判断出反应器整体的质
量是否下降 ,是否会影响石油原料的质量等等。 3 . 2 2 壁厚测定 。壁厚测定是检验加氢反应器最重要 的检验方法 之一 ,该方法的操作过程是 ,首先检验人员通过壁厚测算出反应器中 的壁厚数据 ,再次根据壁厚数据判断是否会影响反应器的正常运行。 若 发现任 何不利因会影响反应器的正常运行 ,检验人员必须为反应器 提供 更有效的防护措施。 由于加氢反应器本身就是一种复合材料 ,如 果检验人员用 目前最为科学 的超声波探伤仪进行测厚 ,获得数据更为 准确 ,这无疑不是给检验人员减少了工作量。 3 . 2 . 3 无损检测 。 我 国的常规探伤方法可 以大致分 为: 射 线检测、
法之一 ,该方法操作简单、可 以直接与加氢反应器相接触 ,通过检测
1 、加氢反 应器在 石油行业的应用
1 . 1 加氢精制 。加氢精 制就是一定要处在高温高压之下 ,同时还 要有催 化剂和氢气存在 ,方能使石油 中的各种非烃化合物逐渐发生氢 解反应 ,进而保证石油的质量 。就 目前 的发展形势来看 ,我 国的加氢 精 制技术主要是用于再次加工汽油和柴油的提炼 ,也可 以用于改变石 油变 劣这一大问题 。加氢精制技术所需 的核心设备就是加氢精制反应
表一 随机试块母材和焊缝金属 的化 学成分分析及 回火脆性系数
C Mn S i S P Cr N Mo 7( %) ( p p m)
X
焊缝 1 O . 1 O O . 8 9 O . 1 O 0 . 0 0 4 O . O l O 2 - 3 5 O . 1 6 1 . 0 4
- 1、下载文档前请自行甄别文档内容的完整性,平台不提供额外的编辑、内容补充、找答案等附加服务。
- 2、"仅部分预览"的文档,不可在线预览部分如存在完整性等问题,可反馈申请退款(可完整预览的文档不适用该条件!)。
- 3、如文档侵犯您的权益,请联系客服反馈,我们会尽快为您处理(人工客服工作时间:9:00-18:30)。
对试验用水的水质及水温都作了严格的规定。经 国家特种设备监察部门、用户、监造单位及制造 厂检验人员现场共同检查, 确认水压试验合格。
3 加氢反应器的使用和腐蚀
在役加氢反应器经过长期运行, 面临
的的典型损伤主要有回火脆性、氢 脆、氢腐蚀、堆焊层剥离、堆焊层
裂纹和蠕变脆化等,如图2所示。
加氢反应器的使用和腐蚀
硬度测试,见表11。可以看出,沿板厚方
向其硬度差值小于13HV10 ,说明沿厚度
方向上力学性能均一性良好。
焊接材料
设备主体焊缝采用法国SAF公司生产的
焊丝。
焊丝:S225V ,
焊剂:F537 , 焊条:E225V。
设备制造工艺--厚壁筒节成型
由于筒节壁厚140 mm ,直径相对较小,曲率大, 要
1.3 加氢反应器 锻件进口和国产的性能比较
我国目前在制的世界上最大的煤液化装置中
的两台加氢反应器是一种流态化床的加氢反 应器。设计壳体选用2.25Cr-1Mo-0.25V锻钢。 两台煤液化反应器中各有11 个筒节采用法国 进口的2.5Cr-1Mo-0.25V锻钢精加工筒节。 内径Φ4812 mm、壁厚334 mm、长度2750
样置于氢气压力19 MPa ,470 ℃,经48 h 恒温,
升温速度50 ℃/ h ,降温速度260 ℃/ h 至室温。
试验循环6 次,要求第一循环试样冷却到室温
24 ℃以后,停留168 h , 再升温至第二循环。
第二至第六循环,试样冷却到24 ℃以后各停
留48 h。最后对试样堆焊层进行超声检测,不
97.2 mm ,内表面形状偏差最大为8 mm ,均符合图样要求。
每个封头带1 块母材热处理试板,试板模拟焊后热处理: ≤400℃装炉,升温和降温速度均≤50℃/h ,加热温度705+5 -
14℃,保温时间14 h。试板焊后热处理后,力学性能检验全部
合格。
焊接工艺评定项目
产品的焊接
产品的焊接主要采用电弧焊和埋弧焊两种焊接方法。 依据评定结果,确定产品焊接工艺为:焊前预热≥180 ℃, 多层多道焊; 焊条电弧焊的焊接线能量控制在
第一阶段:拼焊内衬不锈钢筒,Cr-Mo钢板+收口筒节锻造,
+10℃,AKv≥55J(一个最低值≥47J); 第二阶段:整体结构,双层堆焊, Cr-Mo钢 ,-15℃, 工厂+现场组 装, vTr54+2.5ΔvTr54≤+38℃, J≤180 , AKv≥55J(一个最低 值≥47J); 第三阶段:整体结构,双层堆焊,-30℃, AKv≥55J(一个最低值 ≥47J ,工厂+现场组装, J≤130 ; 第四阶段:整体结构,双层堆焊 Cr-Mo钢和添加V ,内径Φ4500
三个重要指标
回火脆化敏感性系数
J = (Si +Mn) (P + Sn)×104 ≤100
(目标值80); X = (10P+5Sb+4Sn+As)×10 - 2 ≤15 ppm (目标值12); 回火脆化敏感性试验 vTr54 + 3ΔvTr54 ≤0 ℃。
加氢反应器发展的四个阶段
温度≤400 ℃,升、降温速度≤50 ℃/ h。
设备内壁堆焊层的要求
部件内壁堆焊309L + 347L 后, 要在堆焊层表
面2.5~3.0 mm 以下处取样进行化学分析, 其 结果应满足表8 的要求。
表8
堆焊层347 熔敷金属的化学成分( %)
堆焊层试块做抗氢剥离试验
在试块上按工艺堆焊TP309L+TP347L, 将试
表3 加氢精制反应器某些部件 回火脆性的实测值
表4
加氢精制反应器某些部件力学 性能的实测值
2.25Cr-1Mo-0.25V (F22V)
发展煤的液化技术,需要开发能适应设计
温度达482 ℃和更高压力临氢环境的钢 材。与常规2.25Cr-1Mo和3Cr-1Mo-
0.25V钢相比, 2.25Cr-1Mo-0.25V有更高
16 ~27 kJ / cm,埋弧焊的焊接线能量控制在22~
32 kJ / cm;层间温度≤250 ℃;焊后立即进行消氢处
理(300~350 ℃×5 h );从而获得成形美观和无
损检测合格率高的焊接接头。
焊后热处理
加氢反应器设备整体进炉进行最终焊后热处
理,加热温度705+5-14 ℃,保温8 h。控制装炉
中,满足组对的质量要求,完全组焊
完毕后, 再组焊上段、中段, 按上述方
法进行调整。
现场焊接--现场热处理
按焊接规程的要求, 焊接区域进行150~250 ℃的预热, 且对
焊接电流、电压、焊速等有严格的要求。采用龙门窄间隙焊
机焊接。
整个施焊过程中均采用燃气式简易加热器对焊接区域加热和
保温。由于现场的工作环境尤其自然风的变化, 对焊接区域 的预热和保温有重大影响。因此, 及时的监视温度变化, 并随 温度的变化调节加热器的气流量, 以保证焊接过程的稳定。
由于反应器组焊后超长、超重, 无法进行整体
远距离运输, 所以分上、中、下三段运到现场
进行现场组焊, 即编号为B7的焊缝和编号为
B11的焊缝必须在现场组焊。
设备的起吊 -- 组装精度控制
在组焊现场使用汽车吊, 吊放壳体时要
使用两台吊车同时工作。
先组焊下段、中段, 将工件吊至滚轮架
组以后仔细调整, 使壳体下段、中段对
回火脆性及特征
合金结构钢淬火以后, 随着回火温度的提高, 其抗拉强度降低, 韧性、塑性提高。但是在特 定温度区回火或在其中缓冷时, 冲击韧性出现 显著降低的现象, 称为回火脆性。主要是由于 钢中的杂质如P、Sn、As和Sb等元素在钢中
作用, 加入氢气, 使不饱和烃变成饱和烃。
脱出有害元素
③ 脱出有害元素硫、氮、氧的有机物,在加
氢处理过程中产生断链反应。 脱硫 -S- + H2 → H2S ; 脱氮 -N- + H2 → NH3; 脱氧 -O- + H2 → H2O; 脱卤 Cl- + H2 → HCl ④ 脱除重金属。加氢处理脱去原料中的砷铅 铜等金属
mm , 工厂+现场组装, J≤130, X≤10ppm, vTr54十
2.5ΔvTr54≤0 ℃
国内主要制造厂
中国第一重型机械集团公司(简称一重) 用
2.25Cr-1Mo(F22)锻钢制造了近百台加氢
反应器。此外, 兰石、上锅和金重等先后也用
2.25Cr-1Mo钢制造了多台加氢反应器。
加 氢 反 应 器 钢 材
操作介质油气、氢气、硫化氢; 设备内
径:Φ2200 mm; 壁厚 (140 + 7.5) mm;
总高:26050 mm (加氢处理保护反应
器 ) ,35775 mm (加氢处理反应器);水
压试验压力:28.4 MPa (卧置) 。
制造要点
① 钢板。设备壳体用SA542 Tyepd CL14A 钢板,
mm、每个筒节净重117.4 t 。
差距
中、法锻件都能满足设计要求。国产的钢材
对有害元素的控制上(P、S、As、Sb、P +
Sn) 稍有逊色; J 、X 系数也稍高于法国。两
国锻件力学性能相当,但法国锻件抗回火脆性
优于中国。
2 加氢反应器的制造与检验
以中石油克拉玛依分公司的两台加氢反应器
三 种 钢 材 性 能 比 较
2.25Cr-1Mo(F22)
2.25Cr-1Mo 钢是用于加氢反应器最成熟的钢
种,它广泛用在重油加氢裂化和加氢脱硫装置。 对使用26 年的6 台反应器进行检测和解剖分 析证明:对于设计温度≤454 ℃、氢分压 ≤20.7MPa的加氢反应器, 采用2.25Cr-1Mo钢 制造是可靠的。
的最大许用应力值。设计技术条件对钢 材化学成分的要求见表。
国产化的F22V 指标
化学成分的实测值均能满足设计要求;回火脆
性的实测值: J 系数为42~68; X 系数为6.6~ 8.55 ppm; vTr54 + 3ΔvTr54 为 - 91.8 ~ 40.7 ℃,均低于0 ℃~ -18℃;A KV平均值为 170~290J 、最低值为150J ;HB 为179~ 225。这表明国产化的F22V 各项指标接近日 本制钢产品的水平。
回火脆性系数
回火脆化敏感性系数
J = ≤100 (目标值80);
X = ≤15 ppm (目标值12);
回火脆化敏感性试验
vTr54 + 3ΔvTr54 ≤0 ℃。 金相组织照片不存在板条状组织,晶粒度不小
于7 级。
金相组织照片(贝氏体组织)
表11
全板厚硬度测试
沿板厚方向以5mm 间隔进行了全厚度
加氢反应器的制造检验 使用与防腐
赵志农 thkjzzn@ thkjzzn@
加氢反应器的制造检验使用与防腐
前言
1 加氢反应器及材料的发展过程
2 加氢反应器的制造与检验
3 加氢反应器的使用和腐蚀
4. 加氢反应器的使用中腐蚀问题实例
5 加氢反应器的在用检验
允许有剥离现象。
水压试验
设备在厂内卧置进行了水压试验,试验压
力为28.4 MPa ,试压用水氯离子含量
≤15 ppm。水压试验一பைடு நூலகம்合格。
加氢反应器现场组焊技术 及质量控制要点
一重为某厂制造的加氢反应器筒体内径为
Φ4413 mm;壁厚为127mm; 封头的最小壁厚
为68mm; 总高为28531mm; 总重410420 kg。
加氢反应器及材料的发展过程
国内六七十年代制造的加氢反应器多为冷壁反应器。