冶炼烟气制酸转化工序余热的回收再利用(新版)
某铜冶炼厂余热利用系统简介
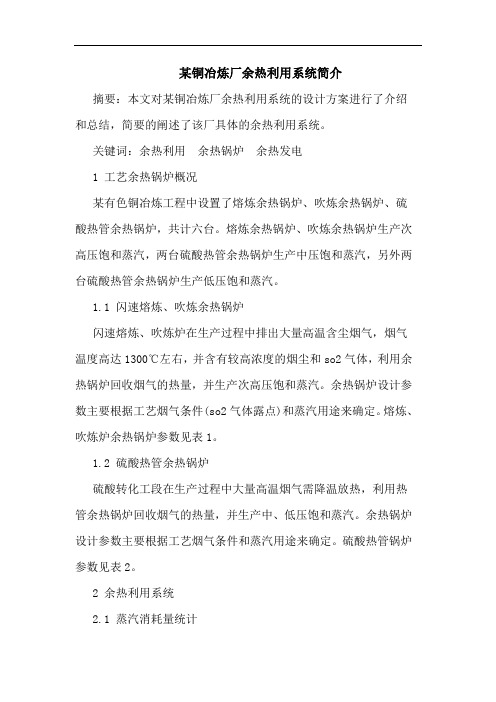
某铜冶炼厂余热利用系统简介摘要:本文对某铜冶炼厂余热利用系统的设计方案进行了介绍和总结,简要的阐述了该厂具体的余热利用系统。
关键词:余热利用余热锅炉余热发电1 工艺余热锅炉概况某有色铜冶炼工程中设置了熔炼余热锅炉、吹炼余热锅炉、硫酸热管余热锅炉,共计六台。
熔炼余热锅炉、吹炼余热锅炉生产次高压饱和蒸汽,两台硫酸热管余热锅炉生产中压饱和蒸汽,另外两台硫酸热管余热锅炉生产低压饱和蒸汽。
1.1 闪速熔炼、吹炼余热锅炉闪速熔炼、吹炼炉在生产过程中排出大量高温含尘烟气,烟气温度高达1300℃左右,并含有较高浓度的烟尘和so2气体,利用余热锅炉回收烟气的热量,并生产次高压饱和蒸汽。
余热锅炉设计参数主要根据工艺烟气条件(so2气体露点)和蒸汽用途来确定。
熔炼、吹炼炉余热锅炉参数见表1。
1.2 硫酸热管余热锅炉硫酸转化工段在生产过程中大量高温烟气需降温放热,利用热管余热锅炉回收烟气的热量,并生产中、低压饱和蒸汽。
余热锅炉设计参数主要根据工艺烟气条件和蒸汽用途来确定。
硫酸热管锅炉参数见表2。
2 余热利用系统2.1 蒸汽消耗量统计全厂蒸汽消耗主要有蒸汽干燥车间、电解车间、净液车间、布袋收尘器、制氧蒸汽加热器、制酸工段硫化钠设备、除氧器、浴室等,车间生产、生活用蒸汽消耗量表3。
考虑管网热损失、生产热负荷同时使用系数、生活热负荷同时使用系数,冬季计算最大用汽量123.8 t/h,夏季平均用汽量86.3 t/h。
2.2 蒸汽平衡蒸汽系统汽平衡见表4。
2.3 余热利用系统从全厂锅炉产汽和厂区蒸汽消耗参数来看,厂区蒸汽管网分为6.0mpa、2.5mpa、0.6mpa三个压力等级,其中厂区蒸汽消耗点分布在2.5mpa、0.6mpa两个压力等级。
对于每一种压力等级的多余饱和蒸汽可通过两种途径满足用户要求,一是通过减压后送入下一级蒸汽管网,另一种是利用蒸汽压差发电,排出的背压蒸汽送入下一级蒸汽管网使用。
由于第一种方案能源浪费很大,与当今能源发展政策不相符。
浅谈炼钢烟气余热资源的回收及利用

浅谈炼钢烟气余热资源的回收及利用作者:左建英来源:《中国科技博览》2013年第22期[摘要]炼钢生产过程在消耗能源的同时,也产生大量的余热余能,本文主要对炼钢烟气余热进行分析研究,文中把转炉和电炉放在同等重要位置上加以研究,以余热的回收和利用为主线,对炼钢烟气余热进行分析和说明,希望能与同行共同切磋。
[关键词]余热回收汽化冷却回收利用中图分类号:X757 文献标识码:X 文章编号:1009―914X(2013)22―0631―01引言转炉一直以来都是以汽化冷却的方式来回收这部分烟气余热。
而由于电炉烟气预热废钢技术存在初始投资较大、废钢预热温度低、温升不均匀、烟气的显热利用效率较低等问题,现在很多钢厂也开始采用汽化冷却法回收电炉烟气余热。
本文在对某炼钢系统深入调研的基础上,对转炉厂和电炉厂的余热回收和利用提出了一系列有效地改进措施。
一、转炉烟气余热回收的发展及现状分析1、转炉烟气余热回收的发展及现状分析最初的转炉烟气处理采用全燃法系统,利用显热效率低,大大增加了处理废气量,致使除尘系统庞大,投资费用和运行费用昂贵,同时也增加转炉炼钢的能耗,因此,该治理技术较早地被以后的“未燃法”转炉炼钢工艺所取代。
日本和其它发达国家推出的未燃法转炉炼钢先进工艺,被认为是回收能源、保护环境的最佳方案。
未燃法转炉烟气的处理方法,逐渐形成两大类。
一类是湿法处理,另一类是干法处理。
截至目前,各项技术主要围绕净化煤气的质量提高、减少或消除二次污染、减少投资、减少运行成本、提高操作性,以及提高经济效益、环境效益等方面一直在发展。
如湿法除尘从最早的“两文”的水平布置到“两文”竖向布置,二文喉口的改进、活动烟罩的微差压控制、设备改型,及对一文“半干法”改进等等;干法除尘中对关键的电除尘设备、燕发冷却器、输灰系统的不断改进,和使烟气在蒸发冷却器的稳定性的提高,以及系统设备材质的耐腐蚀性增强等,从而推进了转炉烟气除尘技术的发展和提高。
工业余热的现状与利用

工业余热现状与利用姚**北京科技大学机械学院,100083摘要:工业余热指工业生产中各种热能装置所排出的气体、液体和固体物质所载有的热量。
余热属于二次能源,是燃料燃烧过程所发出的热量在完成某一工艺过程后所剩余的热量。
我国能源利用率相比发达国家较低,至少50%的工业耗能以各种形式的余热被直接废弃。
工业余热节能潜力巨大,近年来已经成为我国节能减排工作的重要组成部分。
关键字:工业余热节能减排热管0引言当前,我国能源利用仍然存在着利用效率低、经济效益差,生态环境压力大的主要问题。
节能减排、降低能耗、提高能源综合利用率作为能源发展战略规划的重要内容,是解决我国能源问题的根本途径,处于优先发展的地位。
实现节能减排、提高能源利用率的目标主要依靠工业领域。
处在工业化中后期阶段的中国,工业是主要的耗能领域,也是污染物的主要排放源。
我国工业领域能源消耗量约占全国能源消耗总量的70%,主要工业产品单位能耗平均比国际先进水平高出30%左右。
除了生产工艺相对落后、产业结构不合理的因素外,工业余热利用率低,能源没有得到充分综合利用是造成能耗高的重要原因。
我国能源利用率仅为33%左右,比发达国家低约10%。
至少50%的工业耗能以各种形式的余热被直接废弃。
因此从另一角度看,我国工业余热资源丰富,广泛存在于工业各行业生产过程中,余热资源约占其燃料消耗总量的17%~67%,其中可回收率达60%,余热利用率提升空间大,节能潜力巨大。
工业余热回收利用又被认为是一种“新能源”,近年来成为推进我国节能减排工作的重要内容。
[1]1工业余热资源工业余热来源于各种工业炉窑热能动力装置、热能利用设备、余热利用装置和各种有反应热产生的化工过程等。
目前,各行业的余热总资源约占其燃料消耗总量的17%~67%,可回收利用的余热资源约为余热总资源的60%。
合理充分利用工业余热可以降低单位产品能耗,取得可观的经济效益。
工业余热按其能量形态可以分为三大类,即可燃性余热、载热性余热和有压性余热。
烟气余热回收利用项目可行性研究报告

烟气余热回收利用项目可行性研究报告一、项目背景近年来,随着工业生产水平的提高,烟气余热的浪费日益严重。
大量的烟气余热未被有效回收利用,不仅导致企业额外的能源消耗,而且对环境造成了严重的污染。
因此,研究和开发烟气余热回收利用项目具有重要的意义。
二、项目概述本项目旨在通过对工业烟气的余热进行回收利用,提高能源利用效率,减少能源消耗,并降低环境污染。
项目计划在工业生产过程中,利用余热回收装置将烟气中的热量转化为电能或热能,用于企业的工业生产过程中或供热、供电。
三、项目优势1.节能减排:通过回收烟气中的余热,大大减少了能源的消耗,提高了能源的利用效率,从而达到节能减排的目的。
2.环保效益:有效利用烟气余热减少了废气的排放,降低了环境污染程度,增强了企业的环保形象。
3.经济效益:烟气余热回收利用可以降低企业的能源消耗,减少经营成本,提高企业竞争力。
四、项目实施方案1.确定烟气回收设备类型:根据具体工业生产过程中的烟气特点和需要回收利用的烟气余热的温度和压力要求,选择合适的烟气回收设备类型,如换热器、锅炉等。
2.设计安装烟气回收设备:根据工业生产过程中的烟气排放口和余热回收设备之间的距离以及烟气特点进行合理的设备设计和安装。
3.连接余热利用设备:将回收的烟气余热通过管道等方式连接到企业的工业生产设备或供热、供电设备,实现能源的回收利用。
五、预期效益1.节能减排效益:通过烟气余热回收利用,预计可使能源消耗减少20%,相应地减少废气排放量。
2.经济效益:根据企业的工业生产规模和能耗情况,预计每年可节省数百万元的能源成本。
3.环保效益:每年减少大量的二氧化碳、氮氧化物等大气污染物的排放,减少空气污染的程度。
4.政策扶持效益:符合国家节能减排政策,项目实施过程中可以享受相关优惠政策,加大项目的投资回报率。
六、项目风险1.技术风险:烟气余热回收利用技术相对较新,需要针对具体工业生产过程中的烟气特点进行技术研发和改进。
冶炼烟气余热回收利用的技术研究

张 晓
( 昆明冶金研究院
云南昆明
6 5 0 0 3 1 )
广 / /
摘
节约材料 、 降低 成本方面具有独到的特点。 要: 近年来, 我 国的钢铁 工业飞速 的发展 , 钢铁产 \ 、 在热量 的刚收 、 现在进 行的烟气回收利用的形式大体上分为 三种 : 一种 是炯
L 、 \
关键词: 冶炼; 烟气余热; 余热回收; 节能
至 储水 箱 , 与 系 统互 补 后 送 至 热 用 户 。 2 . 2烟 气 余 热 回 收 利用 的解 决 方 法
随着工业的发展 , 能源 } 肖 耗量不 断地 增加 , 空气污染 日渐严
热 管式 换 热器 不仅 可 以降低 能 源 的消耗 还 能 降低排 炯 温
提高热能 的利用效 率 , 减少高 温炯气造成锅 炉壁的损坏 。使 重, 所 以当下减少能源 的消耗 , 合理利用 现有 能源 的二次 回收利 度 , 用热管式 的换热器 热阻极小 , 热 密度高 , 可 以克服 常规换热 器的 用是研究 的重要课题。烟气余热是二次能源 , 煤炭 、 石 油等不 可冉
烟气余 热虽然 热量很 高 , 得 到利 用 , 降低 了能 源的消耗 , 提高 了整体
另一方 面该 烟气余 热 回收装置能够把排 娴温度降低至 值, 但是烟气余 热回收利用的难度很高。因为若排烟温度低 , 锅炉 的经济性 , 6 0度 以下 , 有效地减少 了热污染 , 降低经济成本 。 尾部 受热面的烟气 和工 质的换热 温差 就会 减少 , 导致传热面积 的
耗 能 和 热 量 ,虽 然 在 节 能 方 面 我 国 也 在 努 力 并 且 取 得 了 一 些 效 下面设置落灰 斗, 这是 为了防止换热器工作时烟气 流速 下降时烟
火法冶炼铜及湿法冶炼铜工艺介绍

题,不利于贵金属等有价伴生元素的回收, 因此在工业上未得到广泛应用。
• 我国铜冶炼主要以火法冶炼为主,总产量占全 部铜产量约96%,我国也是采用铜冶炼工艺种 类最多的国家,国际上先进的铜冶炼技术在我 国大多已采用,且生产规模远大于其它国家, 同时仍存在大量采用落后生产工艺、污染严重 的中小型铜冶炼企业,根据《有色金属产业调 整和振兴规划》的要求,铜冶炼行业规划目标 是:按期淘汰落后产能,节能减排取得积极成 效,企业重组取得进展,创新能力明显增强, 资源保障能力进一步提高。
• 火法炼铜的原则流程如下,流程图见图
• 铜精矿(15~30%Cu)——造锍熔炼——冰 铜 (铜锍25~70%Cu)——吹炼——粗铜 (98~99%Cu)——火法精炼——阳极铜 (99%Cu)——电解精炼——电铜(99.9599.98%Cu)。
• 火法炼铜生产过程一般由以下几个工序组 成:备料、熔炼、吹炼、火法精炼、电解 精炼,最终产品为电解铜。配套工序:阳 极泥处理、余热回收、余热发电、烟气收 尘、烟气制酸、循环水系统等。
• 火法冶炼铜主要产物环节如下:
• 除火法工艺外,近20 年来湿法炼铜工艺也取 得了长足的进步,湿法工艺不仅可以处理一些 难选的氧化矿和表外矿、铜矿废石等,而且随 着细菌浸出和加压浸出的发展,亦可以处理硫 化铜矿石,并能获得较好的经济效益,从而大 大拓宽了铜资源综合利用范围。该法是在常温 常压或高压下,用溶剂浸出矿石或焙烧矿中的 铜,经过净液,使铜和杂质分离,而后用萃取 -电积法,将溶液中的铜提取出来。对氧化矿 和自然铜矿,大多数工厂用溶剂直接浸出;对 硫化矿,一般先经焙烧,而后浸出。
火法冶炼及湿法冶炼 铜工艺介绍
• 铜的冶炼工艺有火法冶炼和湿冶炼两种 方法。
重有色冶金炉窑余热回收利用技术规范
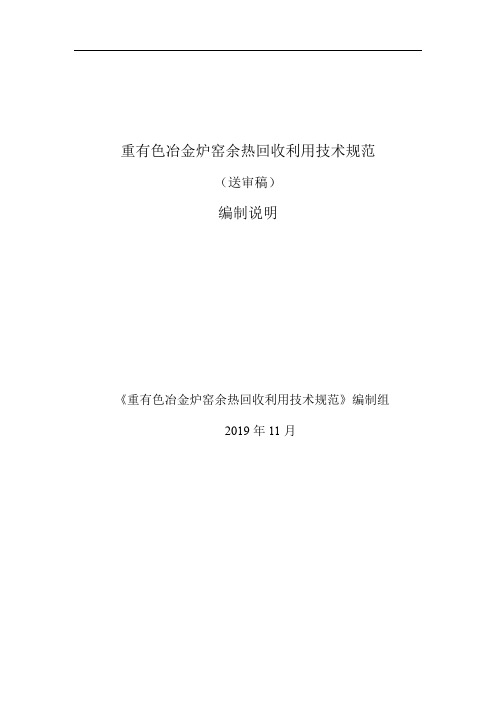
重有色冶金炉窑余热回收利用技术规范(送审稿)编制说明《重有色冶金炉窑余热回收利用技术规范》编制组2019年11月《重有色冶金炉窑余热回收利用技术规范》编制说明1.工作简况1.1重有色冶金可持续发展的需要随着社会的不断进步以及经济的快速发展,人们对有色金属的冶炼也提出了越来越高的要求。
其中,能源消耗大和环境保护要求高是有色冶炼行业中面临的主要问题。
为满足各项环保指标要求和降低能源消耗成本,开发针对有色金属冶炼系统中主要能耗设备冶金炉窑的预热回收技术至关重要。
当前,冶金炉窑的余热回收目前在国内外已有多种成熟的技术,各类技术不尽相同,缺少对该技术的技术性指导文件。
因此,通过制定《重有色冶金炉窑余热回收利用技术规范》来对冶金炉窑的余热回收规范化管理,有利于技术的标准化和规范化,同时将为贯彻执行相关法律法规及产业政策起到纽带作用。
我国有色金属工业单位产品能耗(标煤)约为 4.76t,约占全国能源消费量的3.5%以上。
其中铜、铝、铅、锌冶炼能耗占有色金属工业总能耗90%以上。
余热利用率低是造成能耗高的重要原因之一。
从另一角度看,我国工业余热资源丰富,广泛存在于工业各行业生产过程中,余热资源约占其燃料消耗总量的17%~67%,其中可回收率达60%,余热利用率提升空间大,节能潜力巨大。
工业余热回收利用被认为是一种“新能源”,近年来成为推进我国节能减排工作的重要内容。
有色金属工业作为高能耗行业,生产集中度小,但能耗高。
随着当今社会经济水平的不断提高以及现代工业的快速发展,有色金属的冶炼作为工业生产过程中的重要环节,其能源消耗情况以及资源回收利用水平不仅会对企业自身效益产生极其重要的直接影响,还会对社会经济、节能环保等方面产生间接影响。
伴随工业产业的不断发展以及能源消耗总量的不断增加,资源短缺也成为了未来一个时期人类发展所面对的一项重要问题,而烟气余热的回收和利用正是应对该问题的一个有效解决方案。
未来,余热回收在节能工作中仍占有极为重要的地位。
年产40万吨铜冶炼烟气制酸系统转化工艺恒算设计
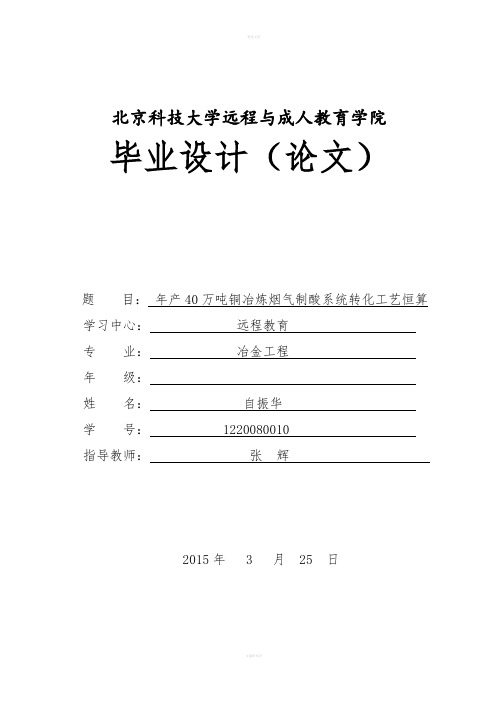
北京科技大学远程与成人教育学院毕业设计(论文)题目:年产40万吨铜冶炼烟气制酸系统转化工艺恒算学习中心:远程教育专业:冶金工程年级:姓名:自振华学号: 1220080010 指导教师:张辉2015年 3 月 25 日目录摘要: (1)ABSTRACT: (1)第一章文献综述 (2)第二章工艺说明书 (4)2.1概述 (4)2.1.1产品规模和规格 (4)2.1.2工艺方案叙述 (4)2.2 装置设计说明 (4)2.1.1 工艺原理 (4)2.2.2 工艺流程说明 (5)2.2.3 主要设备选型说明 (5)2.2.4 化工原材料规格及用量 (5)第三章转化工序物料衡算与热量衡算 (6)3.1转化工序流程示意图及简要说明 (6)3.2 确定各段进口温度及转化率 (6)3.2.1温度与平衡转化率的关系 (6)3.2.2最适宜温度与转化率的关系 (7)3.2.3确定操作线 (7)3.2.4各段进口温度及转化率 (8)3.3 转化工序物料衡算 (9)3.3.1进转化器一段气体量及成分 (10)3.3.2出一段气体量及成分 (10)3.3.3 出二段气体量及成分 (10)3.3.4出三段气体量及成分 (10)3.3.5出四段气体量及成分 (10)3.4 转化器各段的热量衡算 (12)3.4.1转化一段反应热量和出口温度 (12)3.4.2转化二段反应热量和出口温度 (14)3.4.3转化三段反应热量和出口温度 (16)3.4.4转化四段反应热量和出口温度 (17)第四章安全备忘录 (21)4.1概述 (21)4.2二氧化硫和硫酸的危害 (21)4.3二氧化硫和硫酸运输、使用等应注意的事项以及如何防护 (22)第五章环境保护与治理建议 (23)5.1 三废主要来源 (23)5.1.1 废气 (23)5.1.2 废水 (23)5.1.3 矿渣 (23)5.2 三废处理方案 (23)5.2.1 废气 (23)5.2.2 废水 (23)5.2.3 废渣 (24)设计小结 (25)参考文献 (26)致谢 (27)摘要:本设计是进行400Kt/铜冶炼烟气制酸转化系统工艺设计,首先,通过制定两转两吸接触法作为主工艺路线,画出工艺流程图,再绘制X-T平衡曲线和最适温度曲线,根据转化入口原料气的组成,平衡曲线和最适温度曲线以及催化剂的起燃温度、使用温度,大致估计四段转化过程的操作线,根据操作线来进行物料衡算和热量衡算,完成工艺说明书,安全备忘录,即完成课程设计说明书。
锌冶炼工艺简介.

行政部门员工生产工艺学习指南紫金有色金属有限公司二0一一年四月目录公司简介 (1)10万吨/年锌冶炼整体生产网 (2)焙烧制酸生产工艺简介 (3)浸出生产工艺简介 (7)净化生产工艺简介 (12)电解生产工艺简介 (14)锌粉生产工艺简介 (16)熔铸生产工艺简介 (16)综合回收生产工艺简介 (17)水汽车间生产工艺简介 (21)紫金有色金属有限公司是紫金矿业集团控股子公司,公司成立于2004年10月,注册资本3.75亿元,现有总资产27.6亿元,员工2500余人。
地处工业园区,是国内大型有色金属冶炼企业,自治区重点工业企业,自治区循环经济发展示范企业,也是首批通过国家工业和信息化部全国《铅锌行业准入条件》审核的8户铅锌企业之一。
公司的20万吨/年锌冶炼工艺采用热酸浸出—低污染沉矾除铁湿法炼锌工艺,目前公司已具备年产锌锭22万吨、硫酸40万吨的产能,年产值可达40亿元以上。
控股公司紫金矿业集团股份有限公司(A+H)是一家以黄金及基本金属矿产资源勘查和开发为主的高新技术效益型特大国际矿业集团,是中国最大的黄金生产企业和中国控制金属矿产资源最多的企业之一。
(H股票代码:2899,A 股票代码:601899)。
公司积极开展矿产资源整合和风险勘探工作,目前紫金在当地控股矿山一座,参股矿山一座,控制锌资源金属量300多万吨,原料自给率可达50%以上;现有矿权17个,矿权面积1000余平方公里。
公司始终将科学管理、安全环保、节能减排和发展循环经济作为企业可持续发展及构建和谐企业的核心来抓,成立了技术研发中心,已对伴生的铜、镉、钴、铅银等有价金属全部实现了综合回收利用,对饱和蒸汽实施了余热发电项目,建成了水污染和尾气在线监控系统,在国内首次成功应用离子液尾气吸收技术,使公司尾气排放在达到国家一级排放标准的基础上再减少了2/3的尾气排放量,成为内蒙古自治区循环经济示范企业,公司技术研发中心被认定为自治区级技术中心,巴彦淖尔市“环境友好型企业”,公司先后荣获“科技进步一等奖”、自治区“科技进步三等奖”。
稀贵金属综合回收项目冶炼烟气余热利用研究
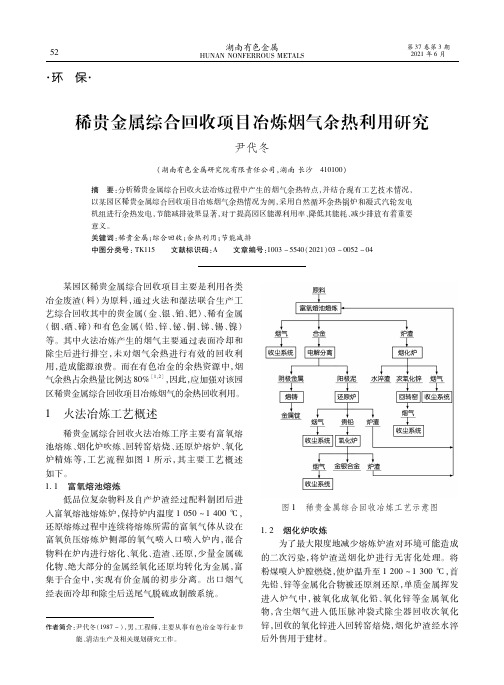
湖南有色金属HUNANNONFERROUSMETALS第37卷第3期2021年6月作者简介:尹代冬(1987-),男,工程师,主要从事有色冶金等行业节能、清洁生产及相关规划研究工作。
·环 保·稀贵金属综合回收项目冶炼烟气余热利用研究尹代冬(湖南有色金属研究院有限责任公司,湖南长沙 410100)摘 要:分析稀贵金属综合回收火法冶炼过程中产生的烟气余热特点,并结合现有工艺技术情况,以某园区稀贵金属综合回收项目冶炼烟气余热情况为例,采用自然循环余热锅炉和凝式汽轮发电机组进行余热发电,节能减排效果显著,对于提高园区能源利用率、降低其能耗、减少排放有着重要意义。
关键词:稀贵金属;综合回收;余热利用;节能减排中图分类号:TK115 文献标识码:A 文章编号:1003-5540(2021)03-0052-04 某园区稀贵金属综合回收项目主要是利用各类冶金废渣(料)为原料,通过火法和湿法联合生产工艺综合回收其中的贵金属(金、银、铂、钯)、稀有金属(铟、硒、碲)和有色金属(铅、锌、铋、铜、锑、锡、镍)等。
其中火法冶炼产生的烟气主要通过表面冷却和除尘后进行排空,未对烟气余热进行有效的回收利用,造成能源浪费。
而在有色冶金的余热资源中,烟气余热占余热量比例达80%[1,2],因此,应加强对该园区稀贵金属综合回收项目冶炼烟气的余热回收利用。
1 火法冶炼工艺概述稀贵金属综合回收火法冶炼工序主要有富氧熔池熔炼、烟化炉吹炼、回转窑焙烧、还原炉熔炉、氧化炉精炼等,工艺流程如图1所示,其主要工艺概述如下。
1 1 富氧熔池熔炼低品位复杂物料及自产炉渣经过配料制团后进入富氧熔池熔炼炉,保持炉内温度1050~1400℃,还原熔炼过程中连续将熔炼所需的富氧气体从设在富氧负压熔炼炉侧部的氧气喷入口喷入炉内,混合物料在炉内进行熔化、氧化、造渣、还原,少量金属硫化物、绝大部分的金属经氧化还原均转化为金属,富集于合金中,实现有价金属的初步分离。
冶炼炉渣干法粒化余热回收技术
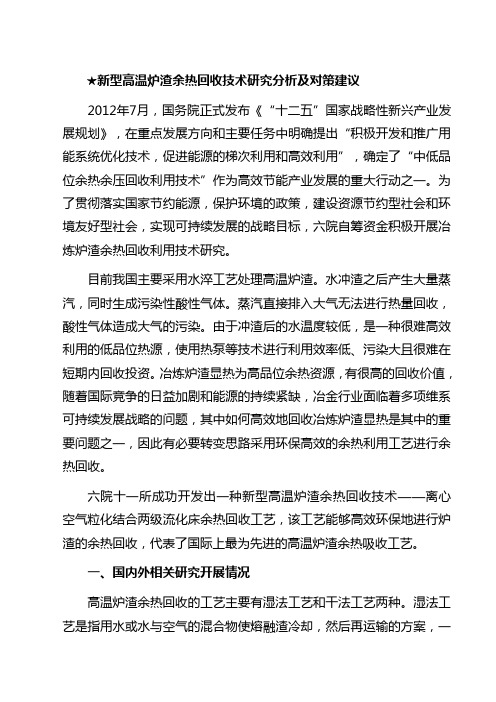
★新型高温炉渣余热回收技术研究分析及对策建议2012年7月,国务院正式发布《“十二五”国家战略性新兴产业发展规划》,在重点发展方向和主要任务中明确提出“积极开发和推广用能系统优化技术,促进能源的梯次利用和高效利用”,确定了“中低品位余热余压回收利用技术”作为高效节能产业发展的重大行动之一。
为了贯彻落实国家节约能源,保护环境的政策,建设资源节约型社会和环境友好型社会,实现可持续发展的战略目标,六院自筹资金积极开展冶炼炉渣余热回收利用技术研究。
目前我国主要采用水淬工艺处理高温炉渣。
水冲渣之后产生大量蒸汽,同时生成污染性酸性气体。
蒸汽直接排入大气无法进行热量回收,酸性气体造成大气的污染。
由于冲渣后的水温度较低,是一种很难高效利用的低品位热源,使用热泵等技术进行利用效率低、污染大且很难在短期内回收投资。
冶炼炉渣显热为高品位余热资源,有很高的回收价值,随着国际竞争的日益加剧和能源的持续紧缺,冶金行业面临着多项维系可持续发展战略的问题,其中如何高效地回收冶炼炉渣显热是其中的重要问题之一,因此有必要转变思路采用环保高效的余热利用工艺进行余热回收。
六院十一所成功开发出一种新型高温炉渣余热回收技术——离心空气粒化结合两级流化床余热回收工艺,该工艺能够高效环保地进行炉渣的余热回收,代表了国际上最为先进的高温炉渣余热吸收工艺。
一、国内外相关研究开展情况高温炉渣余热回收的工艺主要有湿法工艺和干法工艺两种。
湿法工艺是指用水或水与空气的混合物使熔融渣冷却,然后再运输的方案,一般也称为水淬工艺。
干法工艺即依靠高压空气或其他方法实现熔融金属冷却、粒化的工艺。
湿法处理工艺是将高炉渣作为一种材料来加以利用,并没有对其余热量进行充分的利用。
从节能和环保的角度来看,湿法工艺都无法避免处理渣耗水量大的问题。
干式粒化工艺是在不消耗新水的情况下,利用高炉渣与传热介质直接或间接接触进行的高炉渣粒化和显热回收的工艺,几乎没有有害气体排出,是一种环境友好的新式处理工艺。
热管余热锅炉效率下降分析及处理

( ux S ee , inx C p e o o t n G i ,i gi 34 4 C ia G i m lr J gi o pr r r i , u iJ nx 3 5 2 , hn ) i t a C p ao x a
Ab ta t s r c :Gux met ru e e tpp s e trc v r e h oo y i cd ma ig w t me t g g s c n e so rc s o h iis l s d h a i ewa t h a e o ey t c n l g n a i kn ih s l n a o v rin p o e sfr t e e e i i ti f s t .A tr2 y a so e ain,t eh a x h n e e ce c f s e tpp olrwa e r a e . G i iS l r s mma ie n r me f e r p rt e o h e te c a g f in y o t h a i e b i sd c e sd i wa e e u x met u e r dad z a ay e h e o ;t e h a x h n e e ce c e u t n Wa a s d b h o —c n e s b e g s a d i cu t t mp e n e n— n lz d te r a n h e t c a g f i n y r d ci s c u e y te n n s e i o o d n a l a n r s n n a ,i lme t d o
Ke r s h a ie;b i r f c e c ;n n—c n e s l a ;ic u t g e ar g y wo d : e t p p o l ;e in y o e i o d n a e g s n r s n ;rp i n b i i
锌冶炼烟气净化污酸治理与综合利用的工艺研究

锌冶炼烟气净化污酸治理与综合利用的工艺研究张富兵【摘要】介绍了锌冶炼烟气制酸净化过程中净化污酸的产生机理以及净化污酸治理的方法,提出了控制并减少污酸生成量的措施,探讨了净化污酸在浸渣酸浸工序的综合回收利用方法,对100 kt/a电锌系统污酸处理和综合回收利用的改进措施提出了建议.【期刊名称】《硫酸工业》【年(卷),期】2016(000)005【总页数】3页(P27-29)【关键词】锌冶炼;硫酸生产;烟气净化;污酸处理;综合利用【作者】张富兵【作者单位】河南豫光锌业有限公司,河南济源454650【正文语种】中文【中图分类】X703现代锌冶炼生产工艺主要分为湿法炼锌、火法炼锌和直接炼锌等几类。
豫光锌业有限公司(以下简称豫光锌业)200 kt/a电锌系统采用传统湿法炼锌工艺,在锌精矿焙烧过程中会产生大量的含SO2烟气。
该烟气经余热锅炉、旋风除尘器和电除尘器降温除尘后,再采用逆喷式高效洗涤塔洗涤,去除其中少量的烟尘和SO3气体;再经二转二吸工艺制取浓硫酸。
冶炼烟气在净化工序冷却洗涤时产生含有F-、Cl-以及重金属等杂质的稀硫酸(称污酸),该污酸无法直接回收利用,需经复杂的工艺进行无害化处理。
目前各锌冶炼企业处理污酸主要采用化学沉淀法、电絮凝法、生物制剂法等[1],这些工艺均存在一些问题。
豫光锌业利用现有的生产条件进行了多次探索性的试验研究和工业应用性试验,开发了锌冶炼烟气净化污酸综合治理和回收利用的新方法,特别是污酸综合利用方法,操作简单,能耗低,有价金属回收率高,不产生二次污染。
1.1 污酸产生的机理豫光锌业200 kt/a电锌系统采用常规的湿法炼锌工艺。
将锌精矿送入焙烧炉进行脱硫氧化焙烧,产出的焙砂去下道工序浸出,冶炼烟气经降温除尘后送制酸系统。
在稀酸洗涤净化过程中产生大量的污酸。
锌冶炼焙烧工艺流程见图1。
锌精矿在氧化焙烧过程中,产生大量含尘烟气,其中具有催化作用的铁、铝、锰、钒等氧化物存在,使烟气中含有一定量的SO3气体。
炼钢烟气余热资源的回收及利用

日 期:
学位论文版权使用授权书
本学位论文作者和指导教师完全了解东北大学有关保留、使用学位论 文的规定:即学校有权保留并向国家有关部门或机构送交论文的复印件和 磁盘,允许论文被查阅和借阅。本人同意东北大学可以将学位论文的全部 或部分内容编入有关数据库进行检索、交流。
(如作者和导师不同意网上交流,请在下方签名;否则视为同意。)
随着炼钢烟气余热回收技术的发展以及炼钢饱和蒸汽不连续、不等量特性的客观存 在,现在的钢铁企业考虑得更多的是如何更好的利用炼钢饱和蒸汽。本文重点介绍了炼 钢饱和蒸汽用于真空炉汽源和直接发电两种利用方式,并对两者的能源利用率、节能量 和经济效益进行对比,企业可以根据自身情况选择适合的炼钢饱和蒸汽的利用方式。
As steel-making flue gas residual-heat recovery technology development and that the steel-making saturated vapour is discontinuous and not identical size exists objectively. Now the steel enterprises,consider more that is how to make better use of steel-making saturated vapour. This article introduces the steel-making saturated vapour using on vapour source of vacuum firing furnace and direct generate electricity, and compare two kinds of modes’ vapour utilization efficiency,energy-saving quantity and economic benefits,and steel enterprises can choose saturated vapour utilization mode depending on their situation.
硫铁矿和冶炼烟气制酸配套低温余热回收系统技术总结

硫铁矿和冶炼烟气制酸配套低温余热回收系统技术总结孙正东【摘要】介绍了硫铁矿和冶炼烟气制酸配套的DWHS系统工艺原理、技术特点以及与硫磺制酸配套DWHS系统的区别.DWHS系统的关键是解决水平衡,充分利用外串酸回路上的热量;根据实际情况来确定是否采用酸酸换热器和锅炉给水预热器,总阻力降大约在5~6 kPa;影响产汽量的因素较多,需根据不同装置的运行参数确定产汽量大小.【期刊名称】《硫酸工业》【年(卷),期】2017(000)003【总页数】7页(P20-26)【关键词】硫铁矿;冶炼烟气;硫酸生产;低温余热回收系统;特点;比较【作者】孙正东【作者单位】上海奥格利环保工程有限公司,上海201702【正文语种】中文【中图分类】TQ111.16在各种含硫原料制取硫酸生产过程中,含硫原料的燃烧、SO2的氧化及SO3的吸收3个主要过程均伴有大量的化学能释放出来。
含硫原料的燃烧及SO2的氧化过程中产生的高、中温位余热利用均已有较为成熟的回收工艺。
在硫酸装置干燥和吸收过程中,伴有大量的反应热、冷凝热和稀释热产生,这部分热量的利用由于高温浓硫酸的强腐蚀性而受到了很大的限制。
随着硫磺制酸配套低温位余热回收技术的推广运用,大量硫磺制酸装置的低温位热能已能得到充分回收利用,但目前除了极少量硫铁矿制酸和冶炼烟气制酸装置配套了低温余热回收系统,绝大部分这类装置还是用循环冷却水将热量移走而白白浪费。
利用硫酸装置低温位热能产生蒸汽,是热能利用的理想方法,但必须提高吸收循环酸的温度。
在传统的吸收酸浓度范围内,硫酸的腐蚀性随着其温度的上升而加剧,现有的耐浓硫酸腐蚀的不锈钢和合金似乎都不能适应如此高的酸温。
研究发现:当硫酸w(H2SO4)接近100%时,某些合金的耐腐蚀能力便会增强。
因此,上海奥格利环保工程有限公司(以下简称奥格利公司)和宣达实业集团有限公司(以下简称宣达集团)一方面研发了耐高温硫酸〗腐蚀的XDS系列特种合金材料,另一方面对不同浓度和温度下的硫酸腐蚀特性进行了研究。
住房和城乡建设部公告第203号――关于发布国家标准《冶炼烟气制酸工艺设计规范》的公告

住房和城乡建设部公告第203号――关于发布国家标准《冶炼烟气制酸工艺设计规范》的公告
文章属性
•【制定机关】住房和城乡建设部
•【公布日期】2013.11.01
•【文号】住房和城乡建设部公告第203号
•【施行日期】2014.06.01
•【效力等级】部门规范性文件
•【时效性】现行有效
•【主题分类】标准定额
正文
住房和城乡建设部公告
(第203号)
关于发布国家标准《冶炼烟气制酸工艺设计规范》的公告现批准《冶炼烟气制酸工艺设计规范》为国家标准,编号为GB50880-2013,自2014年6月1日起实施。
其中,第3.2.6、3.7.3、6.4.3、7.2.7、7.4.5、
7.4.8、7.4.10、8.7.3条为强制性条文,必须严格执行。
本规范由我部标准定额研究所组织中国计划出版社出版发行。
住房城乡建设部
2013年11月1日。
- 1、下载文档前请自行甄别文档内容的完整性,平台不提供额外的编辑、内容补充、找答案等附加服务。
- 2、"仅部分预览"的文档,不可在线预览部分如存在完整性等问题,可反馈申请退款(可完整预览的文档不适用该条件!)。
- 3、如文档侵犯您的权益,请联系客服反馈,我们会尽快为您处理(人工客服工作时间:9:00-18:30)。
( 安全管理 )
单位:_________________________
姓名:_________________________
日期:_________________________
精品文档 / Word文档 / 文字可改
冶炼烟气制酸转化工序余热的
回收再利用(新版)
Safety management is an important part of production management. Safety and production are in
the implementation process
冶炼烟气制酸转化工序余热的回收再利用
(新版)
某冶炼厂原有一系列、二系列制酸系统是利用冶炼工段的闪速炉和转炉烟气,经余热锅炉和电收尘,再经净化、转化和吸收工序进行制酸。
烟气转化后的多余热量通过SO3冷却后排入大气,烟气中的余热不但没有回收加以利用,反而还消耗大量能源,既增加了生产成本,又浪费了能源。
另一方面,该企业原有的冶炼工艺过程需消耗大量的低压蒸汽,厂区的蒸汽90%由燃煤锅炉提供,在能源供应十分紧缺的今天,对低温烟气的余热回收及利用显得极为重要。
在众多形式的余热锅炉中,热管技术在低温烟气余热回收中的应用显示出其显著的特点和优势。
一、热管特点
1、热管简介及工作原理
热管是一种具有特高导热性能的新颖传热元件。
热管起源于二十世纪六十年代的美国,1967年一根不锈钢——水热管首次被送入地球卫星轨道并运行成功,热管理论一经提出就得到了各国科学家的高度重视,并展开了大量的研究工作,使得热管技术得以很快发展。
热管技术开始主要用于航天航空领域,我国自二十世纪70年代开始对热管进行研究,自80年代以来相继开发了热管气-气换热器、热管气-水换热器、热管余热锅炉、热管蒸汽发生器、热管热风炉等各类热管产品,使得热管在建材工业、冶金工业、化工及石油化工、动力工程、纺织工业、玻璃工业、电子电器工程等领域内得到广泛的应用。
图1热管结构
热管结构如图1所示。
由管壳、封头、吸液芯、工质等组成。
管内有工质,工质被吸附在多孔的毛细吸液芯内,一般为气、液两相共存,并处于饱和状态。
对应于某一个环境温度,管内有一个与之相应的饱和蒸汽压力。
热管与外部热源相接触的一端,称为蒸发
段;与被加热体相接触的一端,称为冷凝段。
热管从外部热源吸热,蒸发段吸液芯中工质蒸发,局部空间的蒸汽压力升高,管子两端形成压差,蒸汽在压差作用下被驱送到冷凝段,其热量通过热管表面传输给被热体,热管内工质冷凝后又返回蒸发段,形成一个闭式循环,包括三个过程:
吸热段液相工质吸热蒸发;
被蒸发的工质在放热段放热冷凝;
冷凝的工质又返回吸热段再蒸发。
因热管的热力循环是在一个封闭的管内实现的,对外界环境而言,热管自高温热源处吸收热量,在低温段放出热量。
热管仅是热量传输的工具,工质则是热量传输的载体,驱动工质循环的动力是管两端的温差。
2、热管的优点
1)超强的导热性:导热速度快、强度大、效率高,导热速度可达到音速。
2)良好的等温性:良好的等温性使热管在很小的温差下,传递
很大的热通量,传热阻力小。
3)热流密度可变性:热管可以独立改变蒸发段或冷却段的加热面积,即以较小的加热面积输入热量,而以较大的冷却面积输出热量,或者热管可以较大的传热面积输入热量,而以较小的冷却面积输出热量。
4)安全可靠性:不存在管内超压,不怕干烧。
液体工质汽化后,热管的内压不随温度的变化而变化。
5)环境的适应性:不受环境的限制,热管可根据环境的需要而单独设计。
6)应用领域广。
超导热管形状具有更大的灵活性,更广泛的应用领域,能适应各种恶劣的工作环境
3、热管系统的基本特点
1)热量从高温介质转移到低温介质,完全由热管元件完成,低温介质被间接加热。
2)系统中热管元件间相互独立,单根或数根热管失效不影响整个装置的运行。
3)由于热管的单向导热性,热量的传输只能由受热段传至放热段。
4)热管外壁采用高频焊翅片,强化传热,传热效率高,热侧阻力小,设备结构紧凑。
5)热量的传输过程不需要任何外界动力,运行管理简单。
6)热侧换热面积可调,可以在一定范围内调节换热管管壁温度,有效防止低温露点腐蚀。
二、热管余热锅炉(热管蒸发器)
热管式余热锅炉(热管蒸发器)是由若干组热管联箱同其外壳组装而成。
其中每组热管联箱又由若干根热管组成的,为增大传热面积,其加热外表面一般都焊有若干片高频焊环形翅片,各热管之间彼此独立,构成各自独立封闭传热系统,其典型结构如图2所示。
图2热管余热锅炉结构示意图(分体式)
由于上述结构的特点,使其具有以下优点:
1)热管由于外壁带有螺旋翅片,增加了传热面积,单根传热强度大(相对光管);
2)工作介质玄幻是依靠地球重力和压差作用,无需外加动力,无机械运行部件,增加了设备的可靠性,也极大的减少了运行费用。
3)由于其冷、热两端热阻方便可调,便于控制管壁温度,从而有效地解决了设备的露点腐蚀。
4)根据工艺要求,可以进行顺、逆流混合布置,适应较宽的温度范围。
5)热交换系统由众多热管组装而成,各热管之间相互独立,一根或几根热管损坏或失效不影响整个系统的安全运行,只是余热锅炉整体效率会略有降低而已。
6)由于采用上升管、下降管连接汽包结构,使设备水侧能承受较高的压力范围。
7)外壳为钢板连续焊制,设有密封检查门,便于设备清灰。
三、热管余热锅炉(热管蒸发器)的应用
1、烟气参数
该企业原有制酸系统转化烟气参数见表1所示:
表1制酸系统转化烟气参数
从表1可以看出来转化烟气具有以下特点:
1)烟气温度低;
2)几乎不含尘、不含水;
3)SO3浓度高;
4)烟气连续但波动量大;
5)烟气可利用的温差小。
2、热管余热锅炉参数
为了充分回收一系列、二系列制酸系统的中、低温烟气余热,共设置3台热管余热锅炉,取代原系统中的热交换器、SO3冷却器和SO3冷却风机,在满足制酸工艺要求的同时,利用烟气余热生产饱和蒸汽。
热管余热锅炉技术参数见表2。
表2热管余热锅炉技术参数
四、改造后节能效益
自3台热管余热锅炉正式投运至今,均达到设计的额定产汽量,可产1.27MPa饱和蒸汽180000吨/年,,可节约标煤20300吨/年,
同时可节约电耗1383000KW.h/年,相当于节约标煤526吨/年。
热管余热锅炉投产后可减少烟气排放量290×104Nm3/年,减少烟尘排放量868吨/年,减少SO2排放量303吨/年,在很大程度上减少了污染物的排放,改善了厂区环境。
云博创意设计
MzYunBo Creative Design Co., Ltd.。