PFMEA实例1
防松螺栓PFMEA分析实例

德信诚培训网
更多免费资料下载请进: 好好学习社区
潜在失效模式及后果分析
FMEA 编号: 防松螺栓04 (过程FMEA ) 编号:PFMEA-31 项目名称: 过程责任部门: 金工车间 编制者:
车型年/车辆类型: CA-153系列 关键过程: 01。
07。
15 FMEA 日期(编制) 0 1.06.24 .(修订) 主要参加人: 过程功能要 求 潜在的失效模式 潜在的 失效后果 严重度数 级别 潜在的失效原因/机理 频
度
数 现行过程控制
不易探测度数 风险顺序数RPN 建议的 措施 责任及目标完成日期
措施结果
采取的 措施
严重
度数
频度数 不易
探测
度数 风险 顺序数
RPN 滚丝过程
螺纹能通止
滚丝粗糙度达到要求
保证螺纹精度
螺纹不能通过
螺纹通不过,影响顾客装配
4
压力过小
4
首件检验 巡回检验, 4次/班 4只/次 3
48
无
螺纹止不住
螺纹止不住,抗拉强度达不到要求
10 压力过大 4 首件检验 巡回检验, 4次/班 4只/次 3 120
增加压力参数监视
金工车间 01.07.15 每班4次监视压力参数 10 2 3 60
螺纹中径高于工艺要求 不符合工艺要求,顾客难以装配
4 ◇
滚丝轮磨损严重
2 首件检验 巡回检验, 4次/班 4只/次
3 24
压力过小
4 首件检验 巡回检验, 4次/班 4只/次
3 48。
六步法pfmea案例
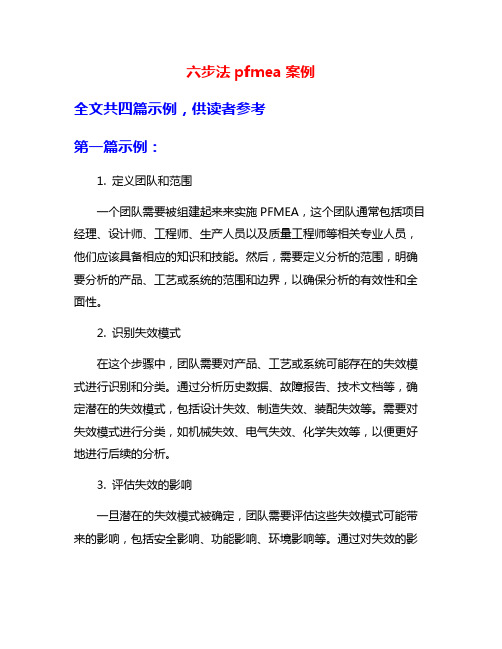
六步法pfmea案例全文共四篇示例,供读者参考第一篇示例:1. 定义团队和范围一个团队需要被组建起来来实施PFMEA,这个团队通常包括项目经理、设计师、工程师、生产人员以及质量工程师等相关专业人员,他们应该具备相应的知识和技能。
然后,需要定义分析的范围,明确要分析的产品、工艺或系统的范围和边界,以确保分析的有效性和全面性。
2. 识别失效模式在这个步骤中,团队需要对产品、工艺或系统可能存在的失效模式进行识别和分类。
通过分析历史数据、故障报告、技术文档等,确定潜在的失效模式,包括设计失效、制造失效、装配失效等。
需要对失效模式进行分类,如机械失效、电气失效、化学失效等,以便更好地进行后续的分析。
3. 评估失效的影响一旦潜在的失效模式被确定,团队需要评估这些失效模式可能带来的影响,包括安全影响、功能影响、环境影响等。
通过对失效的影响进行评估,可以确定关键的失效模式,并优先制定控制措施,以确保产品质量和可靠性。
4. 评估失效的频率和检测能力在这一步骤中,团队需要评估每个失效模式发生的频率和检测能力,即失效的可能性和检测的有效性。
通过对失效频率和检测能力的评估,可以确定高风险的失效模式,并制定相应的控制措施,以减少失效的发生和提高检测的有效性。
5. 制定和实施控制措施基于前面的分析,团队需要制定和实施相应的控制措施,以减少潜在的失效发生和影响。
这些控制措施可以包括设计改进、工艺优化、操作规程更新等,确保产品或系统在生产和使用过程中能够达到预期的性能和可靠性要求。
6. 监控和持续改进团队需要建立一个监控机制来跟踪控制措施的实施效果,并进行持续改进。
通过监控失效模式的发生和影响,可以及时调整和改进控制措施,以确保产品或系统的质量和可靠性得到持续改进。
通过六步法PFMEA的实施,可以帮助团队深入分析潜在失效模式,制定有效的控制措施,从而提高产品质量、减少生产成本和不良问题,提升企业的竞争力。
建议企业在产品设计和生产过程中广泛应用PFMEA方法,并不断优化和完善实施流程,以实现持续的质量改进和效率提升。
PFMEA案例
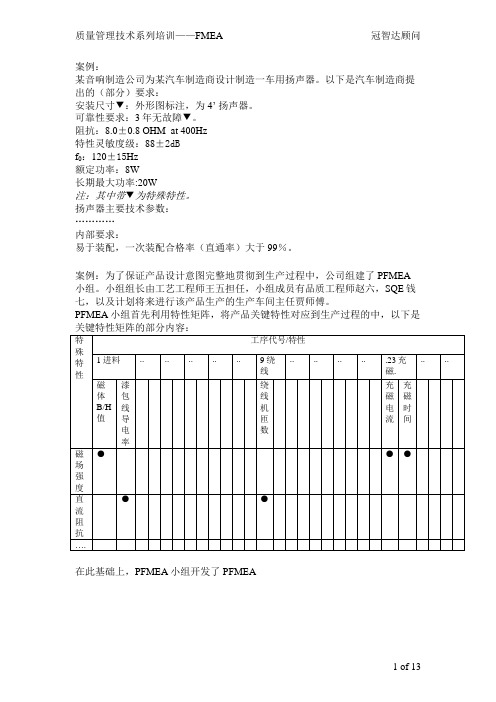
50个 每1000件
9
高:经常性失效
20个 每1000件
8
10个 每1000件
7
中等:偶然性失效
5个 每1000件
6
2个 每1000件
5
1个 每1000件
4
低:相对很少发生失效
0.5个 每1000件
3
0.1个 每1000件
2
级低:失效不太可能发生
≤0.01个 每1000件
1
推荐的PFMEA探测度评价准则
附录1:美国三大汽车评价严重度,频度数,探测度的准则
推荐的PFMEA严重度评价准则
后果
评定准则:后果的严重度
当潜在失效模式导致最终顾客和/或一个制造/装配厂产生缺陷时便得出相应的定级结果。最终顾客永远是要首先考虑的。如果两种可能都存在的,采用两个严重度值中的较高者。(顾客的后果)
评定准则:后果的严重度
扬声器主要技术参数:
…………
内部要求:
易于装配,一次装配合格率(直通率)大于99%。
案例:为了保证产品设计意图完整地贯彻到生产过程中,公司组建了PFMEA小组。小组组长由工艺工程师王五担任,小组成员有品质工程师赵六,SQE钱七,以及计划将来进行该产品生产的生产车间主任贾师傅。
PFMEA小组首先利用特性矩阵,将产品关键特性对应到生产过程的中,以下是关键特性矩阵的部分内容:
一个潜在的关键特性(启动PFMEA)
严重度=9,10
PFMEA小组关注
设计
YS
一个潜在的重要特性(启动PFMEA)
严重度=5~8,且频度数=4~10
PFMEA小组关注
设计
不是特殊特性
严重度=1~4
无
过程
完整实用的过程PFMEA实例(注塑企业)
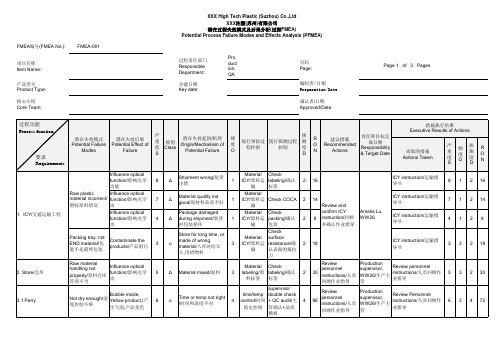
过程责任部门 Responsible Department:
Pro duct ion, QA
关键日期 Key date:
页码 Page:
编制者/日期 Preparation/Date
确认者/日期 Approved/Date
Page 1 of 3 Pages
பைடு நூலகம்
过程功能
Process function 要求
Imaging lens Dia.,
Dim 1: 5.78±0.03 Influence out of spec./镜头 assembly/影响装配
3
直径尺寸超规
Review PM mould
Order start
Production personnel instruction,
o
Wrong insert/嵌入错误
Contaminate the products/产品脏污
3
2. Store/仓库
Raw material handling not properly/原料仓库 管理不当
Influence optical function/影响光学 功
5
3.1 Perry
Not dry enough/湿 度控制不够
1
release
Dim check/尺
plan/订单开 寸确认
2
6
PM mould /点检 磨具
supervisor, incoming inspection WW26/生产主 optical inserts/人员回顾
时包装损坏
输
包装
并确认作业指导
ICY instruction/运输指 导书
ICY instruction/运输指 导书
六步法pfmea案例

六步法pfmea案例全文共四篇示例,供读者参考第一篇示例:案例背景:某家汽车零部件制造公司在生产过程中发现了一个频繁出现的问题:某零部件的尺寸偏差过大,导致装配时无法完全契合,进而影响产品的性能和质量。
为了解决这一问题,公司决定使用六步法PFMEA 进行分析和改进。
步骤一:确定分析范围团队确定了分析的范围为某零部件的生产工艺。
他们明确了问题的具体表现,以及对产品性能和质量的影响。
团队还确定了分析的目的是为了找出可能引起零部件尺寸偏差的潜在故障模式,并制定相应的控制措施。
步骤二:收集相关信息团队开始收集相关信息,包括零部件的设计图纸、生产工艺流程、设备参数、材料性质等。
他们还对生产现场进行实地考察,观察生产过程中的关键环节,并与相关工程师和操作人员进行沟通交流,了解他们对问题的认识和看法。
步骤三:识别潜在故障模式通过分析收集到的信息,团队识别出了可能导致零部件尺寸偏差的潜在故障模式。
包括:材料供应质量不稳定、设备操作不规范、工艺参数设置不当等。
每个故障模式都被赋予一个风险等级,以确定其重要性和优先级。
步骤四:确定故障影响团队分析每个故障模式的影响范围,包括对产品性能、质量、交付时间等方面的影响。
他们还评估了每个故障模式的可能性和频率,以确定其潜在风险。
步骤五:制定改进控制措施基于对故障模式和影响的分析,团队制定了一系列改进控制措施,以降低潜在风险。
加强材料供应商管理、优化生产工艺流程、规范设备操作规程等。
每个控制措施都被赋予一个责任人和执行时间表,以确保实施和落实。
步骤六:跟踪和持续改进团队制定了一个跟踪和持续改进计划,以监控改进控制措施的执行情况和效果。
他们定期对实施情况进行评估和审查,继续识别和解决可能存在的风险和问题,确保质量和性能的持续提升。
通过六步法PFMEA的分析和改进,该汽车零部件制造公司成功解决了零部件尺寸偏差的问题,提高了产品的质量和性能,降低了生产过程中的风险和损失,进一步提升了企业的竞争力和市场地位。
最新PFMEA经典案例
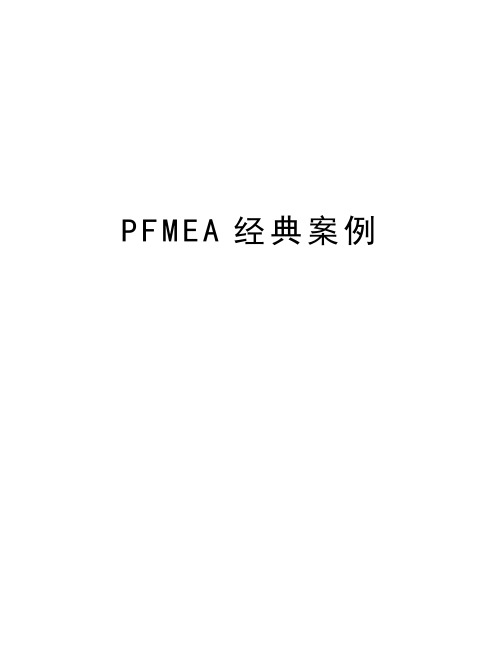
潜在失效模式及后果分析
过程FMEA
FMEA编号:1450 (1)
页码:第1页共1页
项目名称:左前门/H8HX–000–A (2)过程责任部门:车身工程师/装配部(3)编制者:J. Ford–X6512–装配部门(4)
车型年度/车辆类型:199X/狮牌4门/旅行车(5)关键日期:9X.03.01 9X 08 26工序#1(6)FMEA日期:(编制)9X.05.17 (修订)9X.11.06 (7)
每小时进行目测检查,每班检查一次喷膜厚度(深度计)和范围
按作业说明书进行抽样(每班10个门)检查重要部分喷蜡范围570无来自7喷蜡时间不足
8
每小时进行目测检查,每班检查一次喷膜厚度(深度计)和范围
按作业说明书进行抽样(每班10个门)检查重要部分喷蜡范围
7
392
安装喷蜡定时器
维修部门
9X,09,15
安装了自动喷蜡定时器,控制打开喷头,定时器控制关闭。控制图显示过程已受控Cpk=2.05
每小时进行目测检查,每班检查一次喷膜厚度(深度计)和范围
按作业说明书进行抽样(每班10个门)检查重要部分喷蜡范围
5
175
使用设计试验确定粘度、温度和压力
制造工程9X,10,01
确定温度和压力限值,并安装限值控制器。控制图显示过程已受控制。Cpk=1.85
7
1
5
35
7
因撞击使喷头变形
2
依预防维护程序维护喷头
7
1
7
49
按作业说明书进行抽样(每班10个门)检查重要部分喷蜡范围
5
280
给喷蜡枪加装深度限位器
制造工程
9X,10,15
注塑pfmea实例

潜在失效模式
潜在失效后果
Potential Failure Potential Effect of
Modes
Failure
严 级别 重 Class
潜在失效起因/机理
度 S
(★, Δ,o)
Origin/Mechanism of Potential Failure
频 度 O
探
现行预防过 现行探测过程 测
过程责任部门 Responsible Department:
Pro duct ion, QA
关键日期 Key date:
页码 Page:
编制者/日期 Prepartion/Date
确认者/日期 Approved/Date
Page 1 of 3 Pages
过程功能 Process function
要求 Requirements
6 5 2 60 6 5 2 60 6 5 2 60
3.2 Moulding
Distance, Dim.9: 1.60±0.05 out of Impact TOP spec.
Molding process or 7 ★ mold dim. Or mould
temp.
1 IPQC
Dim 2, 3, 4
Origin/Mechanism of Potential Failure
频 度 O
探
现行预防过 现行探测过程 测
程控制
控制
度
D
R P N
建议措施 Recommended
3 o Wrong insert
1
Order start release plan
Dim check
2 6 PM mould
PFMEA的例子
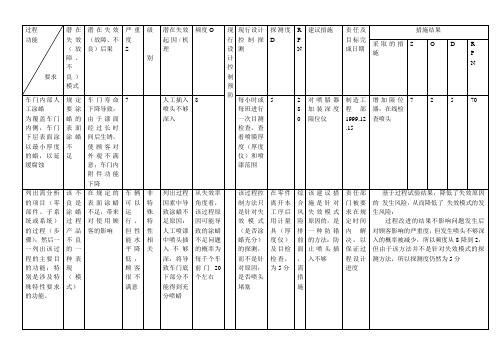
在规定的表面涂蜡不足,带来对使用顾客的影响
车辆可以运行,但性能水平降低,顾客很不满意
非特殊特性相关
列出过程因素中导致涂蜡不足原因:人工喷漆中喷头插入不够深,将导致车门底下部分不能得到充分喷蜡
从失效率角度看,该过程原因可能导致的涂蜡不足问题的概率为每千个车前门20个左右
RPN
建议措施
责任及目标完成日期
措施结果
采取的措施
S
O
D
R
P
N
车门内部人工涂蜡
为覆盖车门内侧,车门下层表面涂以最小厚度的蜡,以延缓腐蚀
规定要涂蜡的表面涂蜡不足
车门寿命下降导致:由于漆面经过长时间后生锈,使顾客对外观不满意;车门内附件功能下降
7
人工插入喷头不够深入
8
每小时或每班进行一次目测检查,查看厚度(厚度仪)和喷漆范围
7
人工插入喷头不够深入
8
每小时或每班进行一次目测检查,查看喷膜厚度(厚度仪)和喷漆范围
5
280
对喷腊器加装深度限位仪
制造工程部1999.12.15
增加限位器,在线检查喷头
7
2
5
70
列出需分析的项目(零部件、子系统或系统)的过程(步骤);然后一一列出该过程的主要目的功能;特别是涉及特殊特性要求的功能。
过程改进的结果不影响问题发生后对顾客影响的严重度,但发生喷头堵塞的概率被减少,所有频度从5降到1(完全不会发生),但由于该方法并不是针对失效模式的探测方法,所有探测度仍然为5分。
ቤተ መጻሕፍቲ ባይዱ过程
功能
要求
潜在失效(故障、不良)模式
潜在失效(故障、不良)后果
严重度
5、PFMEA实例1

FMEA 编号Number:页码Page:准备人Prepared By:关键日期Key Date: 2009.09.07车型年/车辆类潜在的失效模式及效应分析表POTENTIAL FAILURE MODE AND EFFECTS ANALYSIS(过程PROCESS FMEA)过程责任部门Process Responsibility: 质量部 QA Dept.项目名称 Item:工FMEA 编号Number:页码Page:准备人Prepared By:关键日期Key Date: 2009.09.07车型年/车辆类潜在的失效模式及效应分析表POTENTIAL FAILURE MODE AND EFFECTS ANALYSIS(过程PROCESS FMEA)过程责任部门Process Responsibility: 质量部 QA Dept.项目名称 Item:工FMEA 编号Number:页码Page:准备人Prepared By:关键日期Key Date: 2009.09.07车型年/车辆类潜在的失效模式及效应分析表POTENTIAL FAILURE MODE AND EFFECTS ANALYSIS(过程PROCESS FMEA)过程责任部门Process Responsibility: 质量部 QA Dept.项目名称 Item:工FMEA 编号Number:页码Page:准备人Prepared By:关键日期Key Date: 2009.09.07车型年/车辆类潜在的失效模式及效应分析表POTENTIAL FAILURE MODE AND EFFECTS ANALYSIS(过程PROCESS FMEA)过程责任部门Process Responsibility: 质量部 QA Dept.项目名称 Item:工FMEA 编号Number:页码Page:准备人Prepared By:关键日期Key Date: 2009.09.07车型年/车辆类潜在的失效模式及效应分析表POTENTIAL FAILURE MODE AND EFFECTS ANALYSIS(过程PROCESS FMEA)过程责任部门Process Responsibility: 质量部 QA Dept.项目名称 Item:工machiningFMEA 编号Number:页码Page:准备人Prepared By:关键日期Key Date: 2009.09.07车型年/车辆类潜在的失效模式及效应分析表POTENTIAL FAILURE MODE AND EFFECTS ANALYSIS(过程PROCESS FMEA)过程责任部门Process Responsibility: 质量部 QA Dept.项目名称 Item:工FMEA 编号Number:页码Page:准备人Prepared By:关键日期Key Date: 2009.09.07车型年/车辆类潜在的失效模式及效应分析表POTENTIAL FAILURE MODE AND EFFECTS ANALYSIS(过程PROCESS FMEA)过程责任部门Process Responsibility: 质量部 QA Dept.项目名称 Item:工FMEA 编号Number:页码Page:准备人Prepared By:关键日期Key Date: 2009.09.07车型年/车辆类潜在的失效模式及效应分析表POTENTIAL FAILURE MODE AND EFFECTS ANALYSIS(过程PROCESS FMEA)过程责任部门Process Responsibility: 质量部 QA Dept.项目名称 Item:工FMEA 编号Number:页码Page:准备人Prepared By:关键日期Key Date: 2009.09.07车型年/车辆类潜在的失效模式及效应分析表POTENTIAL FAILURE MODE AND EFFECTS ANALYSIS(过程PROCESS FMEA)过程责任部门Process Responsibility: 质量部 QA Dept.项目名称 Item:工FMEA 编号Number:页码Page:准备人Prepared By:关键日期Key Date: 2009.09.07车型年/车辆类潜在的失效模式及效应分析表POTENTIAL FAILURE MODE AND EFFECTS ANALYSIS(过程PROCESS FMEA)过程责任部门Process Responsibility: 质量部 QA Dept.项目名称 Item:工。
PFMEA分析范例
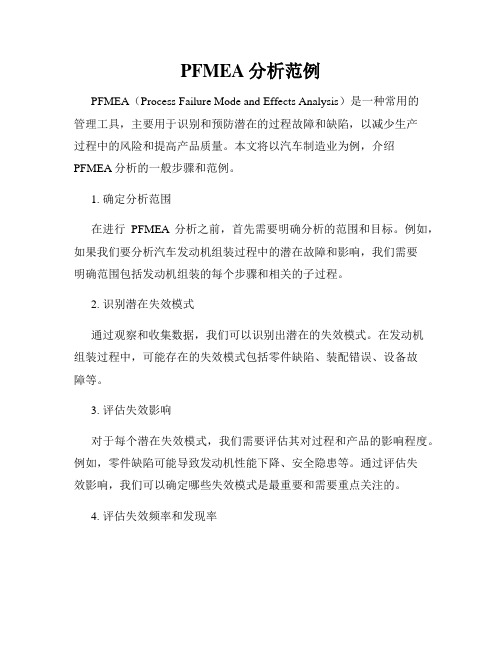
PFMEA分析范例PFMEA(Process Failure Mode and Effects Analysis)是一种常用的管理工具,主要用于识别和预防潜在的过程故障和缺陷,以减少生产过程中的风险和提高产品质量。
本文将以汽车制造业为例,介绍PFMEA分析的一般步骤和范例。
1. 确定分析范围在进行PFMEA分析之前,首先需要明确分析的范围和目标。
例如,如果我们要分析汽车发动机组装过程中的潜在故障和影响,我们需要明确范围包括发动机组装的每个步骤和相关的子过程。
2. 识别潜在失效模式通过观察和收集数据,我们可以识别出潜在的失效模式。
在发动机组装过程中,可能存在的失效模式包括零件缺陷、装配错误、设备故障等。
3. 评估失效影响对于每个潜在失效模式,我们需要评估其对过程和产品的影响程度。
例如,零件缺陷可能导致发动机性能下降、安全隐患等。
通过评估失效影响,我们可以确定哪些失效模式是最重要和需要重点关注的。
4. 评估失效频率和发现率在这一步骤中,我们需要评估潜在失效的频率和发现率。
频率指的是该失效模式在特定时间段内发生的次数,发现率指的是我们能在生产过程中或产品出厂之前检测到该失效模式的概率。
5. 确定风险优先级通过综合考虑失效影响、频率和发现率,我们可以确定每个失效模式的风险优先级。
通常采用风险优先数(RPN)计算方法,RPN = 失效影响 ×频率 ×发现率。
风险优先级高的失效模式意味着需要优先采取预防和纠正措施。
6. 制定预防和纠正措施根据风险优先级,我们可以制定相应的预防和纠正措施来降低潜在失效的风险。
例如,对于零件缺陷,我们可以建立更严格的质量控制流程,提高零件的检验和筛选标准。
7. 实施和监控措施制定好措施后,需要将其实施到实际生产过程中,并进行监控和评估。
通过不断追踪和更新PFMEA表格,我们可以及时发现并纠正新的失效模式,不断提升生产过程的稳定性和产品质量。
总结:本文以汽车制造业为例,介绍了PFMEA分析的一般步骤和范例。
aiag vda pfmea例子
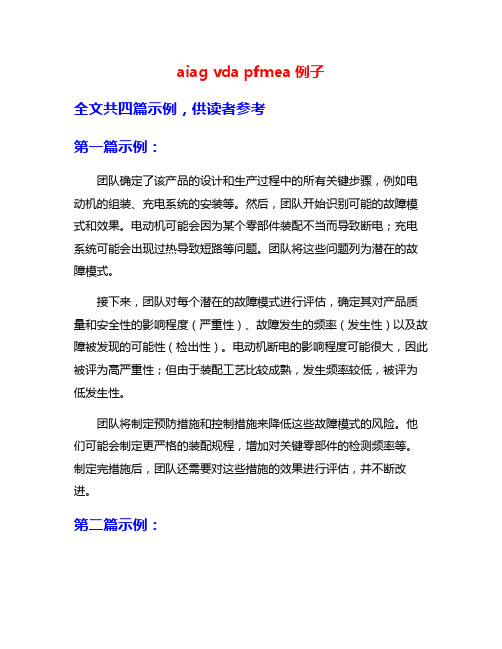
aiag vda pfmea例子全文共四篇示例,供读者参考第一篇示例:团队确定了该产品的设计和生产过程中的所有关键步骤,例如电动机的组装、充电系统的安装等。
然后,团队开始识别可能的故障模式和效果。
电动机可能会因为某个零部件装配不当而导致断电;充电系统可能会出现过热导致短路等问题。
团队将这些问题列为潜在的故障模式。
接下来,团队对每个潜在的故障模式进行评估,确定其对产品质量和安全性的影响程度(严重性)、故障发生的频率(发生性)以及故障被发现的可能性(检出性)。
电动机断电的影响程度可能很大,因此被评为高严重性;但由于装配工艺比较成熟,发生频率较低,被评为低发生性。
团队将制定预防措施和控制措施来降低这些故障模式的风险。
他们可能会制定更严格的装配规程,增加对关键零部件的检测频率等。
制定完措施后,团队还需要对这些措施的效果进行评估,并不断改进。
第二篇示例:AIAG VDA PFMEA是指根据国际汽车行业标准组织(AIAG)和德国汽车工程师协会(VDA)共同制定的一种过程失效模式及影响分析方法。
这种方法是为了帮助汽车行业的供应链伙伴在产品设计和生产过程中识别和解决潜在的故障模式,从而提高产品质量和可靠性。
在本文中,我们将以实际案例为例,介绍AIAG VDA PFMEA的具体应用及其重要性。
故障模式及影响分析(FMEA)是一种常见的质量管理工具,其目的是通过系统性地识别和排除产品和过程中的潜在故障模式,以确保产品的质量和可靠性。
在汽车行业,产品设计和生产过程中存在着各种各样的潜在故障模式,如设计错误、工艺不当、零部件失效等,这些故障模式可能会导致产品的功能失效、安全性降低,甚至对用户造成伤害。
AIAG VDA PFMEA是结合了AIAG和VDA两个国际汽车行业标准组织的最佳实践而制定的一种FMEA方法。
它强调了全面性和系统性,要求参与方从产品设计、制造、测试、维修等全过程来考虑潜在故障模式,并评估其可能的影响程度和频率。
第五版过程PFMEA标准实例
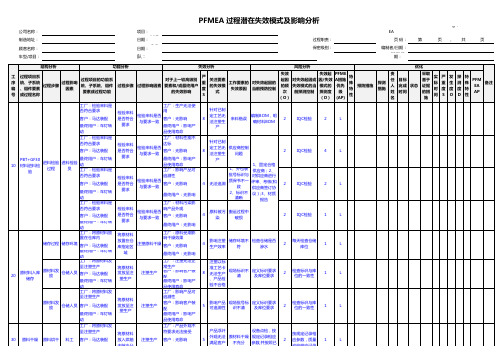
项PF目M:EA开始 日PF期M:EA修订 日跨期职:能团 队:
PFMEA 过程潜在失效模式及影响分析
过程职责: 保密级别:
PM EA
页 码:
第
编制者批/准日/期日: 期:
版本 号:
页, 共
页
结构分析
功能分析
失效分析
风险分析
优化
工 过程项目系
失效
失效起 PFME
最终用户:无影响
4
原料被污 搬运过程中
染
破损
2
IQC检验
1
L
工厂:将原材料放 将原材料
工厂:原料受潮影
置在仓库内 储存过程 储存环境 客户:马达装配
放置在仓 库指定区
响干燥效果 注塑原料干燥 客户:无影响
4
影响注塑 储存环境不 检查仓储是否
生产效率
符
渗水
2
每天检查仓储 库位
1
L
最终用户:车灯转
域
动
最终用户:无影响
检验来料 是否符合
要求
达标 检验来料是否 客户:无影响
与要求一致 最终用户:影响产
品使用寿命
工厂:影响产品可
针对已制
8
定工艺无 供应商控制 法注塑生 问题
产
1、固定合格 1、外包装 供应商;2、
2
IQC检验
4
L
否符合要求
客户:马达装配
最终用户:车灯转 动 工厂:检验来料是
检验来料 是否符合
要求
追溯性 检验来料是否
2
注塑机台
注塑生产
、模具、 注塑成型
客户:马达装配
工艺
PFMEA案例

30
检查与评估现有的操纵方法
生产部
7﹑
装扣钩
漏装扣钩/扣钩装的位置不正确
线束装入车辆时困难或者安装失败
6
操作员未依规定操作
3
培训操作人员并重点标注图面要求
依照图面规定操作/100%外观检验
2
54
检查与评估现有的操纵方法
生产部
6
扣钩插入的深度不充分
2
培训操作人员并重点标注图面要求
依照图面规定操作/100%外观检验
装线盆入线不正确
3
用正确的装线盆/架
操作员检验
3
36
绝缘破皮,导线断线
端子铆线困难/导通测试不良
4
*裁线机故障/刀片设置太低/刀片用旧;*短路或者开路
5
保护保养/点检
100%检查
2
40
2﹑
压端子
端子变形
铆线端子插入壳仔困难
6
送料爪的变化导致端子经导流板时不正确
2
加大清洁/润滑端子机活动部门的频次
PQC每小时巡检/操作员自检
3
பைடு நூலகம்36
检查与评估现有的操纵方法
工程部
铆线端子插入壳仔后不合格
6
端子在导流板卡住而被硬拉出铆线
2
加大清洁/润滑端子机活动部位的频次
PQC每小时巡检/操作员自检
3
36
检查与评估现有的操纵方法
工程部/品管部/生产部
拉力不够
端子铆线不正确
8
▲
模座/刀座松动
2
保护保养/操纵正确的C/H
每小时拉力测试;巡检
3
48
灯炮装配线束时困难
5
检查图面脏污或者褪色未及时更换
六步法pfmea案例
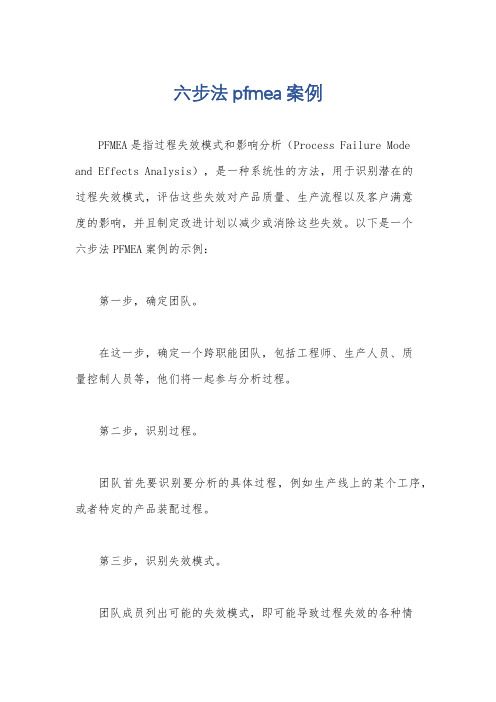
六步法pfmea案例
PFMEA是指过程失效模式和影响分析(Process Failure Mode and Effects Analysis),是一种系统性的方法,用于识别潜在的
过程失效模式,评估这些失效对产品质量、生产流程以及客户满意
度的影响,并且制定改进计划以减少或消除这些失效。
以下是一个
六步法PFMEA案例的示例:
第一步,确定团队。
在这一步,确定一个跨职能团队,包括工程师、生产人员、质
量控制人员等,他们将一起参与分析过程。
第二步,识别过程。
团队首先要识别要分析的具体过程,例如生产线上的某个工序,或者特定的产品装配过程。
第三步,识别失效模式。
团队成员列出可能的失效模式,即可能导致过程失效的各种情
况,例如机器故障、操作失误、材料缺陷等。
第四步,确定失效影响。
团队评估每种失效模式对产品质量、生产流程以及客户满意度的影响程度,确定其严重性。
第五步,确定改进措施。
针对每种失效模式,团队制定相应的改进措施,例如改进工艺流程、提高操作技能、加强设备维护等。
第六步,实施改进并监控。
团队将改进措施付诸实施,并持续监控过程,确保改进效果符合预期,必要时对改进措施进行调整。
通过这六个步骤,团队可以全面地分析潜在的失效模式,并采取相应的措施来提高产品质量和生产效率。
PFMEA案例的实施可以帮助企业减少质量问题和生产故障,提高客户满意度,从而提升竞争力。
PFMEA分析范例
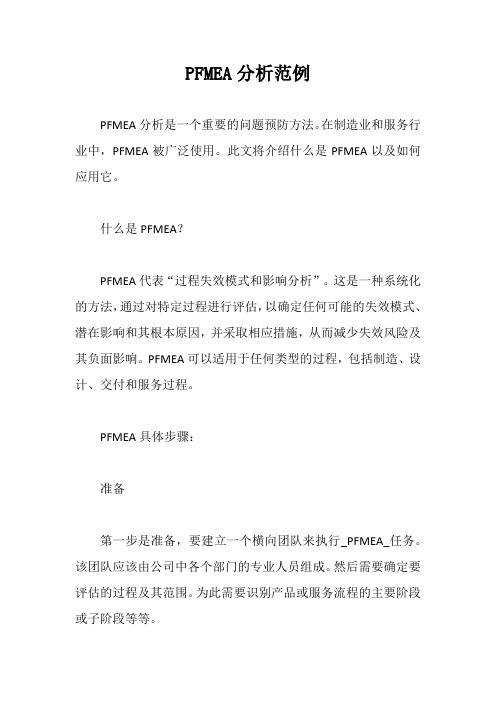
PFMEA分析范例PFMEA分析是一个重要的问题预防方法。
在制造业和服务行业中,PFMEA被广泛使用。
此文将介绍什么是PFMEA以及如何应用它。
什么是PFMEA?PFMEA代表“过程失效模式和影响分析”。
这是一种系统化的方法,通过对特定过程进行评估,以确定任何可能的失效模式、潜在影响和其根本原因,并采取相应措施,从而减少失效风险及其负面影响。
PFMEA可以适用于任何类型的过程,包括制造、设计、交付和服务过程。
PFMEA具体步骤:准备第一步是准备,要建立一个横向团队来执行_PFMEA_任务。
该团队应该由公司中各个部门的专业人员组成。
然后需要确定要评估的过程及其范围。
为此需要识别产品或服务流程的主要阶段或子阶段等等。
评估下一步是评估,评估的目的是按照每个步骤分别分析该步骤中存在的所有失效模式、可能导致这些失效模式的根本原因,评估排除或减轻这些失效的现有控制措施,并放置必要的预防措施。
步骤1:清单采取行动第一步是收集有关过程的所有基本信息。
这包括产品或服务流程图、工艺/操作说明、过程流程图等等。
同时,还需要列出与这个过程相关的所有可能的失效模式。
这些失效模式可以通过历史数据来确定、文献资料、讨论等等。
步骤2:规定过程变量和流程参数在此步骤中定义影响特定过程的所有变量和参数。
例如,所用在特定生产线的材料、设备和人员等等,都必须如实记录。
步骤3:识别失效模式然后,针对每个可能存在的失效模式进行归纳整理,以确定其概率和严重性。
促使这些失效模式的原因也需要被认清。
步骤4:剖析并改进已经存在的控制措施下一步是检查任何现有的防范措施,并判断它们是否足够有效,如果不是,则需要加强或更新现有的控制措施。
步骤5:评估新的控制措施该团队应该定期回顾每个部门的PFMEA工作表,并随时注意重新评估过程以确保没有新的失效模式、变量或参数被漏掉,以及对失效控制所采取的所有行动都是正确和充分的。
注意-评估必须包括所有可能导致失败的原因和根本原因,而不仅仅是现有的故障。
PFMEA分析范例

PFMEA分析范例PFMEA(流程故障模式及影响分析,Process Failure Mode and Effects Analysis)是一种常用的质量管理工具,旨在通过识别和评估潜在的流程故障模式及其可能的影响,以及制定相应的预防控制措施。
下面将针对PFMEA分析进行详细介绍,包括其基本原理、步骤和实施方法。
一、基本原理PFMEA分析的基本原理是通过提前分析和评估流程中可能发生的故障模式及其潜在影响,以及制定相应的控制和预防措施,从而最大程度地减少产品或服务质量问题的发生。
它能够帮助组织识别和解决潜在的质量问题,提高产品或服务的质量可靠性和可用性。
二、步骤1.确定分析范围首先,确定需要进行PFMEA分析的具体流程范围。
该范围应该明确、具体,并确保涵盖了可能影响产品或服务质量的关键环节。
2.建立团队组建一个多学科的团队来执行PFMEA分析工作。
团队成员应包括质量工程师、生产工程师、设计工程师和操作人员等。
3.识别潜在故障模式对于确定的流程范围,团队成员需要开展头脑风暴和讨论,以识别可能的故障模式。
这些故障模式可能包括材料问题、操作失误、设备故障等。
4.评估故障影响对于每个已识别的故障模式,团队成员需要评估其潜在的影响。
影响可以包括产品质量下降、客户投诉增加、安全事故发生等。
通过评估故障影响,确定需要特别关注的故障模式。
5.确定控制措施为了减少故障模式的发生和减轻其影响,团队成员需要制定相应的控制措施。
这些控制措施可以包括质量检查、培训、设备维护等方面的改进。
6.优先级排序根据每个故障模式的潜在影响和控制措施的成本和可行性,对故障模式进行优先级排序。
这有助于组织合理分配资源,以最大限度地提高质量管理的效果。
7.实施控制措施根据优先级排序的结果,组织需要实施确定的控制措施。
这包括在流程中增加质量检查点、开展操作培训、改进设备维护计划等。
8.监控和改进完成控制措施的实施后,需要定期监控其效果,并根据实际情况对措施进行调整和改进。
PFMEA案例(7.2)
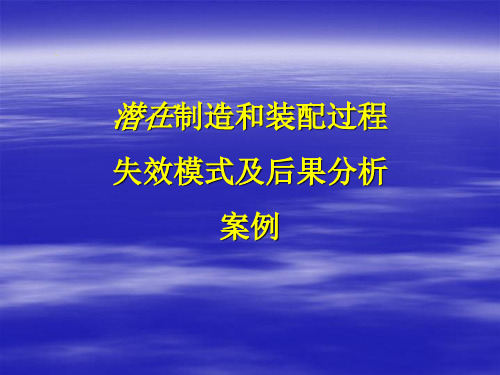
失效模式及后果分析
案例
do
something
案例一、导气筒PFMEA分析
表1:导气筒《工艺潜在失效模式及后果(PFMEA)分析表》
案例一、导气筒PFMEA分析
表1:导气筒《工艺潜在失效模式及后果(PFMEA)分析表》
案例一、导气筒PFMEA分析
表1:导气筒《工艺潜在失效模式及后果(PFMEA)分析表》
案例六
表1:导气筒《工艺潜在失效模式及后果(PFMEA)分析表》
感谢阅读
感谢阅读
案例六
表1:导气筒《工艺潜在失效模式及后果(PFMEA)分析表》
案例六
表1:导气筒《工艺潜在失效模式及后果(PFMEA)分析表》
案例六
表1:导气筒《工艺潜在失效模式及后果(PFMEA)分析表》
案例六
表1:导气筒《工艺潜在失效模式及后果(PFMEA)分析表》
案例六
表1:导气筒《工艺潜在失效模式及后果(PFMEA)分析表》
案例二、摇架工艺 PFMEA分析
表1:导气筒《工艺潜在失效模式及后果(PFMEA)分析表》
案例三、摇架工艺 PFMEA分析
表1:导气筒《工艺潜在失效模式及后果(PFMEA)分析表》
案例四、排壳排链器PFMEA分析
表1:导气筒《工艺潜在失效模式及后果(PFMEA)分析表》
案例五、排壳排链器PFMEA分析
表1:导气筒《工艺潜在失效模式及后果(PFMEA)分析表》
案例六
表1:导气筒《工艺潜在失效模式及后果(PFMEA)分析表》
案例六
表1:导气筒《工艺潜在失效模式及后果(PFMEA)分析表》
案例六
表1:导气筒《工艺潜在失效模式及后果(PFMEA)分析表》
PFMEA分析范例

PFMEA分析范例引言:产品质量是企业发展的基础,但在产品制造过程中,常常会伴随着一些潜在的风险和问题。
为了提前识别并解决这些问题,降低产品质量风险,PFMEA(Process Failure Mode and Effects Analysis,流程失效模式与影响分析)成为了一种常用的工具。
本文将以PFMEA分析为例,介绍其应用和流程,以及如何编制PFMEA表。
一、PFMEA概述PFMEA是一种系统性的分析方法,用于识别可能导致流程失效的潜在原因及其潜在影响,以制定预防和控制措施,提高产品质量。
它主要用于以下三个方面的分析:1. 识别潜在的流程故障模式;2. 评估故障模式对产品质量和客户满意度的影响;3. 制定相应的改进和预防措施。
二、PFMEA流程1. 确定分析范围:明确要分析的流程和子过程,定义分析的上下文和目标。
2. 组织团队:由多个跨职能的专家组成团队,以确保全面性和准确性。
3. 构建流程图:绘制出要分析的流程图,包括输入、输出、关键操作和关键检查点。
4. 识别潜在失效模式:团队成员根据各自专业知识和经验,逐一列出可能出现的失效模式。
5. 评估失效后果:对每个失效模式进行评估和排名,考虑其对产品质量、安全性和客户满意度的影响程度。
6. 识别潜在原因:为每个失效模式找出潜在原因,考虑可能导致该失效模式发生的所有因素。
7. 评估当前控制措施:对现有的控制措施进行评估,看是否足以防止失效模式的发生或降低影响。
8. 制定改进措施:针对每个失效模式和潜在原因,制定相应的改进措施,包括预防和控制措施。
9. 实施改进措施:将制定的改进措施转化为具体的行动计划,并跟踪执行情况。
10. 更新PFMEA表:将分析结果和改进措施记录在PFMEA表中,以便后续追踪和参考。
三、PFMEA表编制PFMEA表是记录PFMEA分析结果的重要工具,其一般包含以下几个方面的信息:1. 流程步骤:按照流程图中的顺序,列出每个步骤的简要描述。
pfmea例子
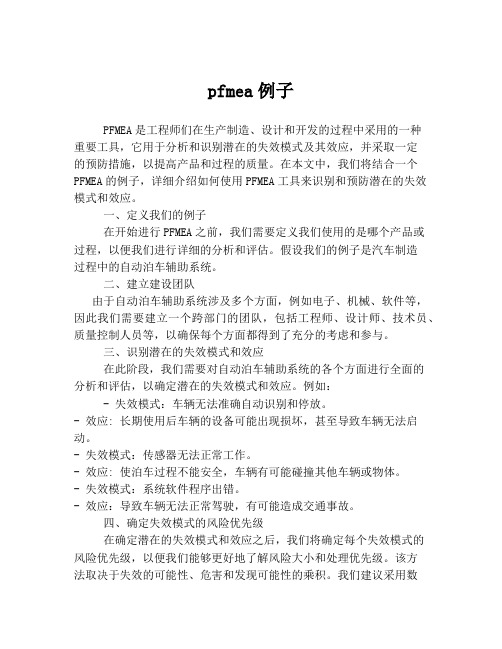
pfmea例子PFMEA是工程师们在生产制造、设计和开发的过程中采用的一种重要工具,它用于分析和识别潜在的失效模式及其效应,并采取一定的预防措施,以提高产品和过程的质量。
在本文中,我们将结合一个PFMEA的例子,详细介绍如何使用PFMEA工具来识别和预防潜在的失效模式和效应。
一、定义我们的例子在开始进行PFMEA之前,我们需要定义我们使用的是哪个产品或过程,以便我们进行详细的分析和评估。
假设我们的例子是汽车制造过程中的自动泊车辅助系统。
二、建立建设团队由于自动泊车辅助系统涉及多个方面,例如电子、机械、软件等,因此我们需要建立一个跨部门的团队,包括工程师、设计师、技术员、质量控制人员等,以确保每个方面都得到了充分的考虑和参与。
三、识别潜在的失效模式和效应在此阶段,我们需要对自动泊车辅助系统的各个方面进行全面的分析和评估,以确定潜在的失效模式和效应。
例如:- 失效模式:车辆无法准确自动识别和停放。
- 效应: 长期使用后车辆的设备可能出现损坏,甚至导致车辆无法启动。
- 失效模式:传感器无法正常工作。
- 效应: 使泊车过程不能安全,车辆有可能碰撞其他车辆或物体。
- 失效模式:系统软件程序出错。
- 效应:导致车辆无法正常驾驶,有可能造成交通事故。
四、确定失效模式的风险优先级在确定潜在的失效模式和效应之后,我们将确定每个失效模式的风险优先级,以便我们能够更好地了解风险大小和处理优先级。
该方法取决于失效的可能性、危害和发现可能性的乘积。
我们建议采用数字大小为1到10,数字越高则表示失效的严重性越高。
五、建立控制措施在确定失效模式和风险优先级之后,我们需要建立相应的控制措施,以减轻或避免失效的效应。
例如:- 采用多个传感器以提高准确性并减少失效的可能性。
- 建立合适的故障检测与纠正系统,在操作系统出错时的同时修复它。
- 明确系统的软件设计和开发的标准,以保证其正确性和适应性。
六、建立检测和监测措施在建立了相应的控制措施之后,我们需要建立检测和监测措施,以确保实施有效并及时告知需要采取改进措施的数据。
- 1、下载文档前请自行甄别文档内容的完整性,平台不提供额外的编辑、内容补充、找答案等附加服务。
- 2、"仅部分预览"的文档,不可在线预览部分如存在完整性等问题,可反馈申请退款(可完整预览的文档不适用该条件!)。
- 3、如文档侵犯您的权益,请联系客服反馈,我们会尽快为您处理(人工客服工作时间:9:00-18:30)。
FM EA
编
号
Nu
mb er:页
码
Pag
e:
准备人Pre par ed By:
潜在的失效模式及效应分析表POTENTIAL FAILURE MODE AND EFFECTS ANALYSIS
(过程PROCESS FMEA)
项目名称 Item: 过程责任部门Process Responsibility: 质量部 QA Dept.
车型年/车辆类 关键日期Key Date: 2009.09.07
工
FM EA
编
号
Nu
mb er:页
码
Pag
e:
准备人Pre par ed By:
潜在的失效模式及效应分析表POTENTIAL FAILURE MODE AND EFFECTS ANALYSIS
(过程PROCESS FMEA)
项目名称 Item: 过程责任部门Process Responsibility: 质量部 QA Dept.
车型年/车辆类 关键日期Key Date: 2009.09.07
工
FM EA
编
号
Nu
mb er:页
码
Pag
e:
准备人Pre par ed By:
潜在的失效模式及效应分析表POTENTIAL FAILURE MODE AND EFFECTS ANALYSIS
(过程PROCESS FMEA)
项目名称 Item: 过程责任部门Process Responsibility: 质量部 QA Dept.
车型年/车辆类 关键日期Key Date: 2009.09.07
工
FM EA
编
号
Nu
mb er:页
码
Pag
e:
准备人Pre par ed By:
潜在的失效模式及效应分析表POTENTIAL FAILURE MODE AND EFFECTS ANALYSIS
(过程PROCESS FMEA)
项目名称 Item: 过程责任部门Process Responsibility: 质量部 QA Dept.
车型年/车辆类 关键日期Key Date: 2009.09.07
工
FM EA
编
号
Nu
mb er:页
码
Pag
e:
准备人Pre par ed By:
潜在的失效模式及效应分析表POTENTIAL FAILURE MODE AND EFFECTS ANALYSIS
(过程PROCESS FMEA)
项目名称 Item: 过程责任部门Process Responsibility: 质量部 QA Dept.
车型年/车辆类 关键日期Key Date: 2009.09.07
工
FM EA
编
号
Nu
mb er:页
码
Pag
e:
准备人Pre par ed By:
潜在的失效模式及效应分析表POTENTIAL FAILURE MODE AND EFFECTS ANALYSIS
(过程PROCESS FMEA)
项目名称 Item: 过程责任部门Process Responsibility: 质量部 QA Dept.
车型年/车辆类
关键日期Key Date: 2009.09.07
工
machining
FM EA
编
号
Nu
mb er:页
码
Pag
e:
准备人Pre par ed By:
潜在的失效模式及效应分析表POTENTIAL FAILURE MODE AND EFFECTS ANALYSIS
(过程PROCESS FMEA)
项目名称 Item: 过程责任部门Process Responsibility: 质量部 QA Dept.
车型年/车辆类 关键日期Key Date: 2009.09.07
工
FM EA
编
号
Nu
mb er:页
码
Pag
e:
准备人Pre par ed By:
潜在的失效模式及效应分析表POTENTIAL FAILURE MODE AND EFFECTS ANALYSIS
(过程PROCESS FMEA)
项目名称 Item: 过程责任部门Process Responsibility: 质量部 QA Dept.
车型年/车辆类 关键日期Key Date: 2009.09.07
工
FM EA
编
号
Nu
mb er:页
码
Pag
e:
准备人Pre par ed By:
潜在的失效模式及效应分析表POTENTIAL FAILURE MODE AND EFFECTS ANALYSIS
(过程PROCESS FMEA)
项目名称 Item: 过程责任部门Process Responsibility: 质量部 QA Dept.
车型年/车辆类 关键日期Key Date: 2009.09.07
工
FM EA
编
号
Nu
mb er:页
码
Pag
e:
准备人Pre par ed By:
潜在的失效模式及效应分析表POTENTIAL FAILURE MODE AND EFFECTS ANALYSIS
(过程PROCESS FMEA)
项目名称 Item: 过程责任部门Process Responsibility: 质量部 QA Dept.
车型年/车辆类 关键日期Key Date: 2009.09.07
工
FM EA
编
号
Nu
mb er:页
码
Pag
e:
准备人Pre par ed By:
潜在的失效模式及效应分析表POTENTIAL FAILURE MODE AND EFFECTS ANALYSIS
(过程PROCESS FMEA)
项目名称 Item: 过程责任部门Process Responsibility: 质量部 QA Dept.
车型年/车辆类 关键日期Key Date: 2009.09.07
工
FM EA
编
号
Nu
mb er:页
码
Pag
e:
准备人Pre par ed By:
潜在的失效模式及效应分析表POTENTIAL FAILURE MODE AND EFFECTS ANALYSIS
(过程PROCESS FMEA)
项目名称 Item: 过程责任部门Process Responsibility: 质量部 QA Dept.
车型年/车辆类 关键日期Key Date: 2009.09.07
工。