磨削圆度不良 解决工艺
磨削缺陷分析与解决

磨削缺陷分析与解决1.产生原因及影响因素零件的磨削精度指零件在磨削加工后,其形状、尺寸及表面相互位置三方面与理想零件的符合程度。
一般说来,形状精度高于尺寸精度,而位置精度也应高于尺寸精度。
磨削加工中的误差主要来源与两方面。
一是磨床-夹具-砂轮组成的工艺系统本身误差;二是磨削过程中出现的载荷和各种干扰:包括力变形、热变形、振动、磨损等引起的误差。
而在磨削过程中,使砂轮与工件位置改变以降低磨削精度的主要原因有:⑴.由磨削力引起的磨床和工件弹性变形;⑵.磨床和工件的热变形;⑶.磨床和工件的振动;⑷.砂轮磨损后其形状、尺寸变化;⑸.工装、夹具的损坏或变形;⑹.导轨、轴承和轴等部件的非弹性变形。
其中磨削过程中的弹性变形是主要的影响因素,它会使砂轮的实际切入深度与输入切入深度不一致,这一变化是由“砂轮架—砂轮轴承-砂轮轴-工件-工件支承”的弹性系统刚性决定。
一般为消除这种原因带来的误差常在行程进给磨削后,停止相互间的进给,仅依靠弹性回复力维持磨削,即光磨阶段(又叫清火花磨削),从而消除残留余量。
当然造成磨削误差的其它因素液很多如:工件磨削形状误差,工件热变形,磨粒切刃引起的塑性变形,砂轮的磨损等。
2.对工件的影响:降低工件使用寿命;降低工件抗疲劳强度;特殊特性的尺寸精度误差易影响工件使用,如轴承孔尺寸的控制,尺寸过小,安装不到轴上;过大,易引起振动,影响轴承使用寿命等。
3.解决方法:增加系统刚性;减少上工序加工留量,以减小磨削厚度,从而减小磨削力降低残留应力;增加光磨时间;及时修整砂轮,及时检查工装、夹具、轴承完好性及电主轴的振动性等;精细的选择砂轮,如挑选细粒度,硬度较大,组织稍紧密的砂轮;选用导热性好的砂轮(如CBN 砂轮);采用冷却性能优良的磨削液以减少因热变形引起的误差。
二、工件表面粗糙度1.产生原因及影响因素表面粗糙度指加工表面具有较小间距和峰谷所组成微观几何形状特征。
它是大量磨粒在工件表面进行切削后留下的微观痕迹的集合。
工业金属砂轮真圆度丧失及研磨面不平整等问题,可采用空心陶瓷微珠改善

工业金属砂轮真圆度丧失及研磨面不平整等问题,可采用空心陶瓷微珠改善前言:工业金属砂轮在研磨过程中会有碎屑的产生,若砂轮的气孔不够大或气孔率较低,容易使碎屑填塞在气孔中,从而,进一步导致砂轮成为一个无锯齿的平面,失去切削力。
关键词:砂轮磨料结合剂空心陶瓷微珠薄壁微球如果砂轮有足够的容屑空间,砂轮的嵌入型堵塞就会大大减小,相应的砂轮的磨削力、效率也更好,砂轮的粘着型的和混合型的堵塞情况也减少,整个磨削过程处于一个良好循环之中自锐性。
砂轮又称固结磨具,砂轮是由结合剂将普通磨料固结成一定形状(多数为圆形,中央有通孔),并具有一定强度的固结磨具。
其一般由磨料、结合剂和气孔构成,这三部分常称为固结磨具的三要素。
砂轮是磨具中用量最大、使用面最广的一种,使用时高速旋转,可对金属或非金属工件的外圆、内圆、平面和各种型面等进行粗磨、半精磨和精磨以及开槽和切断等。
树脂砂轮广泛应用于工业生产活动中,以切割或磨削金属材料或精密部件。
随着高速摩削和超精密磨削技术的迅速发展,工业应用对金刚石砂轮提出了更高的要求。
为提高砂轮的性能,许多研究采取等静压烧结技术、真空热压烧结法、金属结合剂的预合金化、金刚石的表明镀覆、磨料的有序排列等新技术和新工艺,使金属结合剂金刚石砂轮的性价比得到很大的优化。
然而,传统的金属结合剂金刚石砂轮都为致密型,砂轮的自锐性较差,容易堵塞,因此,向金属结合剂中引入具有良好的空隙结构,空心陶瓷微珠提升砂轮的气孔率,从而改善砂轮等磨具的性能,具有非常实际的意义。
以往多孔金刚石砂,多是把水溶性粒子,或者中空材料混入流动的料浆内,形成“占位”情况,产生气孔。
水溶性粒子法,主要是通过将可形成孔的水溶性粒子加入到磨料层中“占位”。
中空材料法,则是通过添加中空的类球形的闭孔材料到砂轮中制造多孔结构。
早在1992年日本科研人员,尝试使用多孔陶瓷结构合剂砂轮的孔隙结构,引入金属结合剂砂轮,这为改善金属结合剂砂轮的性能指出了新的研究方向。
外圆磨削质量缺陷原因分析与排除措施

外圆磨削质量缺陷原因分析与排除措施摘要:在外圆磨削加工过程中,在工件表面经常会产生各种各样的表面缺陷,常见的如表面存在波纹、表面划伤、烧伤、鱼鳞状痕迹等。
为了保证磨削的质量,不仅要保证磨床有较高的加工精度,还要保证砂轮有较好的磨削性能。
我们从检查的角度对外圆磨削这些质量缺陷,进行分析并给出相应的解决措施。
关键词:外圆磨削质量缺陷原因分析1.表面波纹缺陷在磨削加工的过程中,工件表面或多或少的都会留下一些加工波纹,表面的波纹是磨削加工过程中最常见的缺陷,形成表面波纹的原因是由于磨削过程中,磨床存在机械的振动,使砂轮在磨削工件时,与工件表面的接触力不能保证时刻一致,从而在工件的表面会留下不同的加工痕迹,由于振动的随机性,因此会产生不同的波纹。
常见的有直线的条纹、多边形波纹、鱼鳞斑纹和斜纹、螺纹线等。
(1)直线条纹产生原因及排除措施直线条纹的产生主要原因是由于磨削系统中存在的各种振动:①、由于砂轮的不平衡,在转动过程中产生的振动。
排除的方法:主要是在使用的过程中,保证砂轮的平衡质量,砂轮使用一段时间后,要对砂轮重新进行平衡性调整。
②、由于砂轮自身的硬度不均匀,在磨削的过程中引起振动。
排除方法:检查砂轮表面的硬度是否满足工艺的要求,如果硬度过高要更换硬度较软些的砂轮。
③、砂轮的修整量过大,或者是修整量不够。
排除的方法:对砂轮要进行合理的修整,修整量过大或不足同样会对工件的表面产生影响,根据要加工的工件进行合理的修整。
④、电机的振动引起的加工过程中砂轮的振动。
排除方法:电机要固定平衡,或者采用相应的隔振装置,如通过弹性零件吸收振动,消除电机的振动对磨削加工的影响。
⑤、砂轮的主轴与轴承这间的间隙过大,使砂轮在旋转时产生径向的跳动。
排除的方法:检查砂轮主轴与轴承间的间隙,按要求正确调整间隙。
(2)多边形波纹产生的原因及排除措施①、由于工件细长,在磨削过程中,工件由于刚性不足,产生振动。
排除的方法:在工件中间增加支撑架,提高支承的刚性,同时稍微降低进给量和进给速度。
常见的磨削缺陷及消除方法

工作台速度过高
适当改变
3
外圆工件有凸度,中间直径大两端小
工件磨削时朝离开砂轮方向弯
使用中心架磨削
使用中心架后支承块顶得太松或直径磨小后没及时调整支承块
重新调整支承块
砂轮在工件两端出刀太多
重新调整
停留床身工作台纵向导轨原始精度丧失
重新刮研
4
外圆工件有凹度,中间直径小两端大
中心架顶力大
调整支承块
常见的磨削缺陷及消除方法
序号
磨削缺陷
原因
消除方法
1
磨削表面有直波纹
机床以外的振动
消除或者隔离振源
砂轮主轴间隙过大
按规定重新调整(厂家调整)
砂轮没平衡好
重新平衡
砂轮太硬
换用较软的砂轮
砂轮变钝
重新修整
工件在两顶尖间顶得太松
调整尾架套筒的弹簧力
细长工件没有使用中心架或者数量太少或中心架的支承专人顶得太松或太紧
床身工作台纵向导轨原始精度丧失
重新刮研
两端磨削时间比中间部分短
增加砂轮在工件两端的出刀量或稍加停留
5
磨削表面划伤
冷却液不清洁
换新冷却液并精细过滤
砂轮与工件接触面间有脱落的磨粒
砂轮修整后将表面刷净或加大冷却液流量,增加其洗涤性能
6
磨削表面烧伤甚至有裂纹
砂轮过硬
换用较软的砂轮
进给量太大
调小
砂轮修整不够锋利或变钝
重研或消除污物
工件不平衡
降低工件转速或用附加的平衡重量,将工件平衡
工件回转不正常
检查各传动件找出原因或消除之
头架轴承孔或尾架顶尖套筒孔原始精度丧失
拆下修复或更换
重新修整或换新金刚刀
无心磨常见问题及处理方法计划
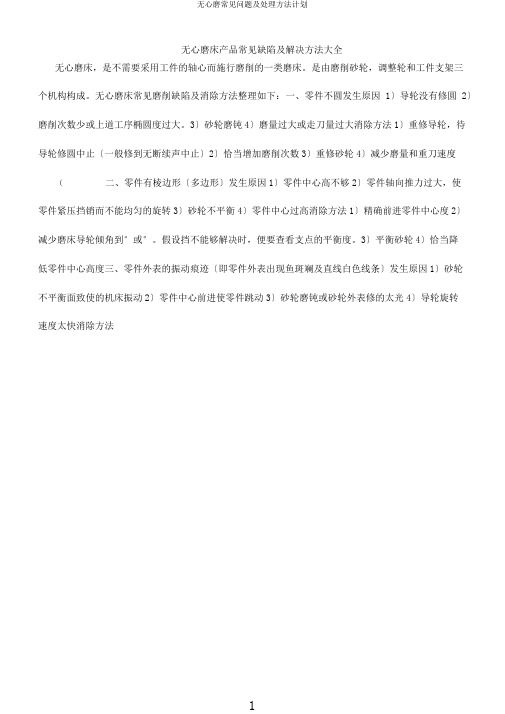
无心磨床产品常见缺陷及解决方法大全无心磨床,是不需要采用工件的轴心而施行磨削的一类磨床。
是由磨削砂轮,调整轮和工件支架三个机构构成。
无心磨床常见磨削缺陷及消除方法整理如下:一、零件不圆发生原因1〕导轮没有修圆2〕磨削次数少或上道工序椭圆度过大。
3〕砂轮磨钝4〕磨量过大或走刀量过大消除方法1〕重修导轮,待导轮修圆中止〔一般修到无断续声中止〕2〕恰当增加磨削次数3〕重修砂轮4〕减少磨量和重刀速度(二、零件有棱边形〔多边形〕发生原因1〕零件中心高不够2〕零件轴向推力过大,使零件紧压挡销而不能均匀的旋转3〕砂轮不平衡4〕零件中心过高消除方法1〕精确前进零件中心度2〕减少磨床导轮倾角到°或°。
假设挡不能够解决时,便要查看支点的平衡度。
3〕平衡砂轮4〕恰当降低零件中心高度三、零件外表的振动痕迹〔即零件外表出现鱼斑斓及直线白色线条〕发生原因1〕砂轮不平衡面致使的机床振动2〕零件中心前进使零件跳动3〕砂轮磨钝或砂轮外表修的太光4〕导轮旋转速度太快消除方法(1〕细心平衡砂轮2〕恰当降低零件中心3〕砂轮或恰当增加砂轮修整速度4〕恰当降低导速四、零件有锥度发生原因〔1〕由于前导板此导轮母线低的过多或前导板向导轮方向倾斜面致使零件前部小2〕由于后导板外表与导轮母线低或后导板向导轮方面倾斜而致使零件后部小3〕由于以下原因而致使零件前部或后部发生锥度①砂轮由修整不正确,本身便有锥度②砂轮与导轮外表已磨损消除方法1〕恰当的移进前导板及调整前导板与导轮母线平行2〕调整后导板的导向外表与导轮母线平行,并且在一条线上。
①根据零件锥度的方向,调整砂轮修改中的角度砂轮②砂轮与导轮【金属加工微信,内容不错,值得关注】五、零件中心大两头小发生原因1〕前后导板均匀向砂轮一边倾斜2〕砂轮修整成腰鼓形消除方法1〕调正前后导板2〕修改砂轮,每次修改余量不要过大六、零件外表有环形螺纹线发生原因1〕前后导板凸出导轮外表,使零件在出口处或入口对被导轮边缘所刮2〕支比太软,磨下的切削嵌在支比承面上构成凸出毛刺,在零件外表刻成螺纹线3〕冷却液不清洁,里面有切屑或砂粒4〕在出口处由于磨量较多,由砂轮边缘所刮磨成5〕零件中心低于砂轮中心笔直压力较大,使砂粒与切屑贴在支毛上6〕砂轮磨钝7〕一次磨下的余量过多或砂轮修的太粗,在另件外表发生极细的螺纹线消除方法(1〕调整前后导板2〕更换外表润滑而硬度较高的支毛3〕更换冷却液〔4〕将砂轮边打成圆角,最终使零件出口处的20mm支配不进行磨削5〕恰当前进零件中心高度6〕砂轮7〕恰当减少磨量及减慢修改速度七、零件前部切去一小块发生原因1〕前导板突出于导轮的外表2〕砂轮和导轮前端面不在一条直线上,并相差很大。
外圆磨床磨削圆跳动超差的原因分析及维修研究

外圆磨床磨削圆跳动超差的原因分析及维修研究摘要:数控外圆磨床是端面大轴类零件精密磨削加工中不可缺少的重要工具之一,其应用范围十分广泛,能够很好的确保零件的磨削效率及加工质量。
但是在长期运行使用后,却很容易出现磨削外圆表面跳动超差问题,这在一定程度上就会给零件加工带来较大困扰,进而无法保证最终的零件加工质量,因此,要想改善现状,就要寻找一条便捷有效的途径针对该故障问题进行解决和处理。
本文也会对外圆磨床磨削期间所产生的圆跳动超差故障进行着重研究,进而根据具体产生原因,提出科学合理的维修策略,以便相关人士参考借鉴。
关键词:外圆磨床;磨削圆跳动超差故障;原因分析;维修策略现今,数控外圆磨床在汽车发动机及其它行业中有着很高的利用率,其虽然可以很好地确保零件磨削加工质量,但是在运行使用过程中仍存有一定的缺陷和不足,尤其是在磨削期间,很容易出现圆跳动超差问题,进而影响到零件加工质量,因此,要想避免这种故障问题的发生,就要通过全面的检测和维修,来挖掘出故障问题的诱发因素,并制定针对性的防控措施,这样才能最大化发挥外圆磨床的应用性能,满足端面大轴类零件磨削加工需求。
1.故障产生的具体原因分析1.1初步分析与判断在故障初步分析阶段,相关工作人员考虑主要是由以下原因所致:第一,由于磨床车轴顶尖孔加工精度不达标所致;第二,磨床拨盘结构为三拨叉结构,但在实际操作时,操作人员只采用双拨叉,这样就会导致磨床在磨削加工时因拨叉不均匀而出现旋转摆动情况,从而诱发圆跳动超差故障的发生;第三,由于磨床后轴承间隙过大,从而使得磨床运行期间出现不规律的径向跳动,进而诱发圆跳动超差故障的发生[1]。
针对这些故障原因,工作人员进行了相应的调整,得出以下结论:首先,重新修正车轴顶尖孔后,发现磨削圆跳动超差现象依然存在;其次,调整拨盘结构后,发现磨床磨削精度略有改善,可以初步判断拨叉分布的不均匀是导致该故障发生的原因之一,但不是主因;最后,对磨床头架主轴拨盘装置进行拆卸,并在夹持状态下对其头架主轴顶尖径向跳动情况进行全面检测,发现千分表指针顶尖锥端和锥尾最大跳动值分别为0. 014 mm、0. 011 mm,随后又将顶尖拆除,发现工件头架主轴的内外锥面径向跳动及前端面旋转轴向跳动分别为0. 011 mm、0. 007 mm、0. 006mm,均已超出设备最大精度允差,所以可以初步判定,头架主轴的跳动是导致故障发生的主要原因。
常见磨削缺陷的产生原因及消除方法

产生原因
消除办法
直波形(多角型)
①砂轮磨钝滑及时修理;
②砂轮不平衡和修整不好;
③磨床主轴或轴承破损;
④砂轮园周速过大;
⑤砂轮硬度过大。
①及时修砂轮;
②平衡好砂轮;
③消除轴承与主轴配合间隙;
④调选主轴有轴向串动;
②砂轮轴心线和工件轴心线不垂直;
③砂轮修整表面凹凸不平;
①头架尾架中心线在垂直平面内不重合成一个角度;
②轧辊轴线没调整好,在垂直平面内成一个角度。
①校正头架与尾架,使中心线重合;
②调整好轧辊,使其轴线与顶针中心重合。
④减少砂轮与工件接触面;
⑤选择适当冷却液进行分冷却。
辊身呈锥形
①头架与尾架中心线在水平面上不合成一个角度;
②轧辊轴线没有调整好,与砂轮轴线不垂直;
③砂轮太软,使砂轮由工件端走到另一端时产生磨耗。
①用千分表校对头架和尾架,使中心重合;
②调整好轧辊,使其轴线与顶针中心线重合;
③合理选择砂轮。
辊身呈细腰形
③砂轮粒度号过大,组织紧密,磨削时砂轮堵塞;
④砂轮与工件接触面过大或接触弧过长,砂轮易堵塞;
⑤工件本身材料导热性差,导热系数小;
⑥冷却方法不良,冷却液不足,热量排不出。
①相应提高轧辊圆周速度,减小切削深度;
②正确选择砂轮。散热条件差时,应选择硬度低、粒度号小的砂轮;
③及时检查砂轮,使其具有良好的切削能力;
④纵向进给量太大。
①消除砂轮主轴轴向串动;
②调好砂轮轴心线与工件轴心线平衡;
③修整好砂轮;
④纵向进给量适当。
划伤和划痕
①磨粒脱落在砂轮与工作台之间;②冷却液过滤不清洁。
①消除砂轮;
常见磨削缺陷的产生原因及消除方法
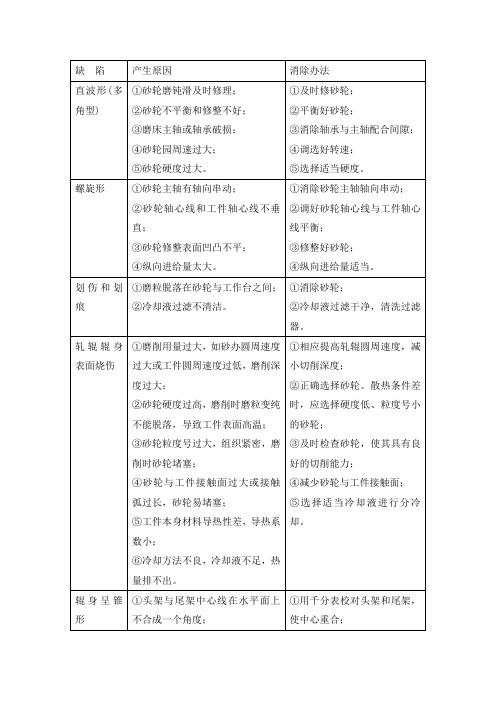
⑤选择适当冷却液进行分冷却。
辊身呈锥形
①头架与尾架中心线在水平面上不合成一个角度;
②轧辊轴线没有调整好,与砂轮轴线不垂直;
③砂轮太软,使砂轮由工件端走到另一端时产生磨耗。
①用千分表校对头架和尾架,使中心重合;
②调整好轧辊,使其轴线与顶针中心线重合;
③合理选择砂轮。
辊身呈细腰形
①头架尾架中心线在垂直平面内不重合成一个角度;
②轧辊轴线没调整好,在垂直平面内成一个角度。
①校正头架与尾架,使中心线重合;
②调整好轧辊,使其轴线与顶针中心重合。
外圆磨削中常见的缺陷及防止措施
缺陷
产生原因
消除办法
直波纹振痕
砂轮不平衡
砂轮进行精细平衡
砂轮磨钝,阻塞引起自振
及时修整砂轮
砂轮主轴或头架主轴跳动
缺陷
产生原因
消除办法
直波形(多角型)
①砂轮磨钝滑及时修理;
②砂轮不平衡和修整不好;
③磨床主轴或轴承破损;
④砂轮园周速过大;
⑤砂轮硬度过大。
①及时修砂轮;
②平衡好砂轮;
③消除轴承与主轴配合间隙;
④调选好转速;
⑤选择适当硬度。
螺旋形
①砂轮主轴有轴向串动;
②砂轮轴心线和工件轴心线不垂直;
③砂轮修整表面凹凸不平;
③砂轮粒度号过大,组织紧密,磨削时砂轮堵塞;
④砂轮与工件接触面过大或接触弧过长,砂轮易堵塞;
⑤工件本身材料导热性差,导热系数小;
⑥冷却方法不良,冷却液不足,热量排不出。
①相应提高轧辊圆周速度,减小切削深度;
②正确选择砂轮。散热条件差时,应选择硬度低、粒度号小的砂轮;
③及时检查砂轮,使其具有良好的切削能力;
平面磨床的加工误差分析与改善

平面磨床的加工误差分析与改善摘要本文对平面磨床的加工误差进行了详细分析,并提出了相应的改善措施。
首先,介绍了平面磨床的工作原理及其应用范围;然后,分析了加工误差的来源和影响因素;接着,针对不同的误差类型,详细介绍了相应的改善方法;最后,通过实例分析验证了改善措施的有效性。
本文旨在帮助读者更好地理解和掌握平面磨床的加工误差分析与改善方法,提高加工质量和效率。
1. 引言平面磨床是一种常见的工具机械,广泛应用于金属加工行业。
其主要功能是通过研磨磨料,将工件表面的粗糙度降低,尺寸精度提高,以满足工件的加工要求。
然而,由于加工误差的存在,平面磨床加工的工件往往无法达到理想的精度要求。
因此,对加工误差进行准确的分析和改善是提高平面磨床加工质量和效率的关键。
2. 加工误差的来源和影响因素加工误差是由于多种因素的综合作用而产生的。
常见的加工误差来源包括机床本身的精度、加工刀具的质量、磨料的选择和使用、工件材料的性质以及操作人员的技术水平等。
这些因素相互影响,从而导致加工误差的产生和累积。
2.1 机床本身的精度平面磨床的机床本身精度是影响加工误差的一个关键因素。
机床的机械结构和控制系统的设计都会对加工精度产生影响。
例如,导轨滑块的精度、主轴的定位精度、磨头的运动平稳性等都会影响加工误差的大小。
因此,选购和维护优质的机床设备是减小加工误差的重要手段。
2.2 加工刀具的质量加工刀具是平面磨床加工的关键工具,其质量直接影响加工精度。
加工刀具的刃磨精度和刃口形状的精度对加工结果具有较大的影响。
刃口磨损严重、刃口形状不规则或者刃口的刃磨精度不高都会导致加工误差的增大。
因此,定期检查和更换加工刀具,保证其质量和精度,是减小加工误差的重要措施。
2.3 磨料的选择和使用磨料的选择和使用也是影响加工误差的重要因素之一。
不同类型的磨料对加工结果产生的影响是不同的。
一般情况下,细砂磨料可以降低磨削力和热影响,有利于提高加工精度;而粗砂磨料则容易产生较大的划痕和磨损,加工精度会受到一定的影响。
轧辊磨削中的常见问题及其处理
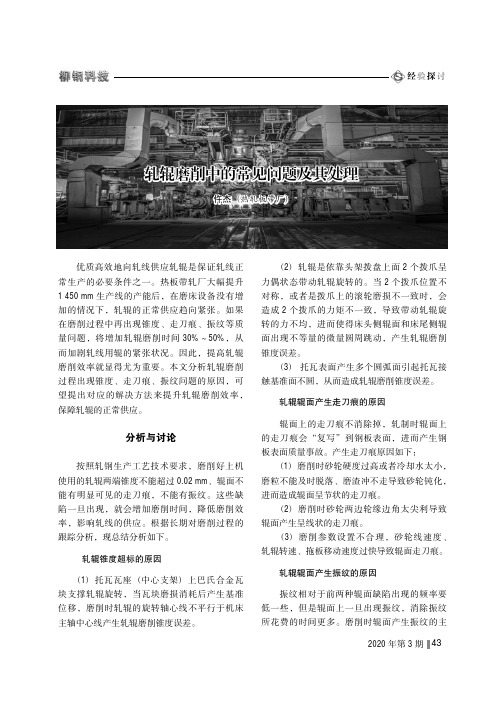
2020年第3期优质高效地向轧线供应轧辊是保证轧线正常生产的必要条件之一。
热板带轧厂大幅提升1450mm 生产线的产能后,在磨床设备没有增加的情况下,轧辊的正常供应趋向紧张。
如果在磨削过程中再出现锥度、走刀痕、振纹等质量问题,将增加轧辊磨削时间30%~50%,从而加剧轧线用辊的紧张状况。
因此,提高轧辊磨削效率就显得尤为重要。
本文分析轧辊磨削过程出现锥度、走刀痕、振纹问题的原因,可望提出对应的解决方法来提升轧辊磨削效率,保障轧辊的正常供应。
分析与讨论按照轧钢生产工艺技术要求,磨削好上机使用的轧辊两端锥度不能超过0.02mm 、辊面不能有明显可见的走刀痕,不能有振纹。
这些缺陷一旦出现,就会增加磨削时间,降低磨削效率,影响轧线的供应。
根据长期对磨削过程的跟踪分析,现总结分析如下。
轧辊锥度超标的原因(1)托瓦瓦座(中心支架)上巴氏合金瓦块支撑轧辊旋转,当瓦块磨损消耗后产生基准位移,磨削时轧辊的旋转轴心线不平行于机床主轴中心线产生轧辊磨削锥度误差。
(2)轧辊是依靠头架拨盘上面2个拨爪呈力偶状态带动轧辊旋转的。
当2个拨爪位置不对称,或者是拨爪上的滚轮磨损不一致时,会造成2个拨爪的力矩不一致,导致带动轧辊旋转的力不均,进而使得床头侧辊面和床尾侧辊面出现不等量的微量圆周跳动,产生轧辊磨削锥度误差。
(3)托瓦表面产生多个圆弧面引起托瓦接触基准面不圆,从而造成轧辊磨削锥度误差。
轧辊辊面产生走刀痕的原因辊面上的走刀痕不消除掉,轧制时辊面上的走刀痕会“复写”到钢板表面,进而产生钢板表面质量事故。
产生走刀痕原因如下:(1)磨削时砂轮硬度过高或者冷却水太小,磨粒不能及时脱落、磨渣冲不走导致砂轮钝化,进而造成辊面呈节状的走刀痕。
(2)磨削时砂轮两边轮缘边角太尖利导致辊面产生呈线状的走刀痕。
(3)磨削参数设置不合理,砂轮线速度、轧辊转速、拖板移动速度过快导致辊面走刀痕。
轧辊辊面产生振纹的原因振纹相对于前两种辊面缺陷出现的频率要低一些,但是辊面上一旦出现振纹,消除振纹所花费的时间更多。
QC小组活动(轴承内圈无心磨圆度不良调整)

水
平
度
, 避免产生共振
利用水平尺, 紧固机床螺丝
杨东坡
13.12.7
3 车削品磨削余量大
减小车削品磨削 控制单次切削量
余量
切削量 ,粗 磨 : ≤ 0.15增加磨削次数 精磨:≤0.05
机床 操作者
每次磨削
4 工件心高不合适
调整合适心高
心高 H=14mm
制作支板及 垫板
姚春锋
13.7.2
秦皇岛恩彼碧轴承有限公司
作成部门
页
轴承工场
9/10
附表 1
QC 小组活动课题注册登记表
小组名称
端面探索组
登记号
ZC-13-07
组长
姚春峰
课题名称
大物外径圆度不良调整
部门
轴承工场端面研磨班
小组人数
10
成立日期
2013 年 5 月 4 日
登记日期
姓名
班组
姓名
班组
魏怀峰
端面研磨班
武亚强
轴承工场总务
小 杨海峰
组 成
赵宏亮
员 郭守正
圆
4.机床没有水平放置,电机运转产生共振 11.磨削时切削量过大
度
5.导轮皮带过松,速度不均匀
不
良
6.砂轮导轮主轴和轴承配合间隙大
12.车削品圆度大 13.车削品磨削余量大
㈡.磨削液
14.工件心高不合适
7.磨削液水量小
15.工件支板磨损
16.工件转动不好
秦皇岛恩彼碧轴承有限公司
编号
ZC-13-07
QC 小 组 课 题 名 称
大物外径圆度不良调整(端面探索组)
作成部门
页
常见的磨削缺陷、原因及消除方法

砂轮修整器重新修整砂轮
5
由于工件局部发热引起烧伤痕或裂痕
砂轮太硬或太细
使用软和较粗砂轮
增加工作台速度
减少砂轮圆周速度
砂轮钝了或阻塞
修整砂轮使粗化且切得好
切除率太大
减少进给
减少横进给
适量减少立柱与拖板结合面镶条间隙
立柱与拖板结合面缺油
润滑油量调整
立柱与拖板结合面润滑油太多
润滑油量调整
7
拖板移动式磨床磨头横向进出火花不一致
一些火花不能放出
调节地脚螺栓重调机床、并用酒精水平仪检查
丝杆无润滑油或润滑油少
润滑油量调整
十字拖板导轨无润滑油或润滑油少
润滑油量调整
十字拖板导轨两导轨油量大小严重不均衡
砂轮掉屑
清洗砂轮罩内部
更换合适的砂轮
4
工件表面呈波纹状
主轴承磨损,造成间隙过大而产生波纹
重新调整主轴轴承间隙,要求主轴与轴承间隙小于0.04mm
砂轮及组件不平衡,使主轴振动而产生波纹
重新对砂轮组件进行静平衡
磨头的垂直进刀量和横向进刀量选择不当,从而使磨削工件表面出现波纹
适当减少磨头垂直进刀深度,减少横向进刀量
润滑油量调整
8
横向进刀不均匀
磨头导轨镶条调得过紧
将磨头导轨镶条放松一点
导轨无润滑油或润滑油少
调大或人工加润滑油
横进丝杆无油
调大或人工加润滑油
常见的磨削缺陷、原因及消除方法
序号
缺陷
原因
消除方法
1
分布于整个工件表面上小块振纹
起重机或建筑物行车等
改善基础
打磨不良改善方案

打磨不良改善方案概述打磨是一种常见的加工工艺,在许多制造业领域都被广泛应用。
然而,由于操作技巧不当、设备不合适等原因,打磨过程中常常会出现不良情况,如表面粗糙、划痕、裂纹等问题。
针对打磨不良问题,本文将探讨一些改善方案,以提高打磨的质量和效率。
问题分析在深入讨论改善方案之前,我们首先需要了解打磨不良的主要原因。
根据经验和研究,以下是一些常见的打磨不良原因:1.设备不合适:打磨设备选择不当,如磨料不匹配、转速不合理等。
2.操作技巧不当:操作人员对打磨技术了解不够,无法正确控制打磨力度、速度等参数。
3.研磨材料不佳:使用质量差的研磨材料,如砂纸磨损严重、砂粒不均匀等。
4.工件材料问题:工件材料硬度、形状等方面与打磨工艺不匹配。
改善方案针对以上问题,我们可以采取一些措施来改善打磨质量和效率。
以下是一些值得尝试的方案:1. 设备优化选用合适的打磨设备是保证打磨质量的关键。
首先,需要根据具体要求选择合适的打磨设备,确保其能提供所需的转速、力度等参数。
其次,注意设备的维护和保养,确保设备始终处于良好状态。
2. 技术培训对打磨操作人员进行技术培训是提高打磨质量的有效手段。
培训内容主要包括打磨技巧、安全操作规范等。
通过培训,操作人员能够更好地理解和掌握打磨过程中的关键步骤和技术要点。
3. 研磨材料留样检验选用质量较好的研磨材料对打磨质量至关重要。
为了确保选用的研磨材料符合技术要求,可以对研磨材料进行留样检验。
留样检验包括检测砂粒分布均匀性、砂纸磨损率等指标,只有通过留样检验合格的研磨材料才能使用。
4. 工艺参数优化工艺参数优化是提高打磨质量和效率的关键环节。
根据具体情况,可以调整打磨速度、力度、研磨材料的选用等参数,以优化打磨过程。
此外,还可以通过引入自动化设备、机器人等手段来提高打磨的精度和稳定性。
5. 工件材料选择正确选择工件材料也是提高打磨质量的重要因素。
不同材料对打磨工艺的要求不同,因此需要根据具体材料的硬度、形状等特点选择合适的打磨工艺。
石墨材料零件外圆磨削难点及解决方法
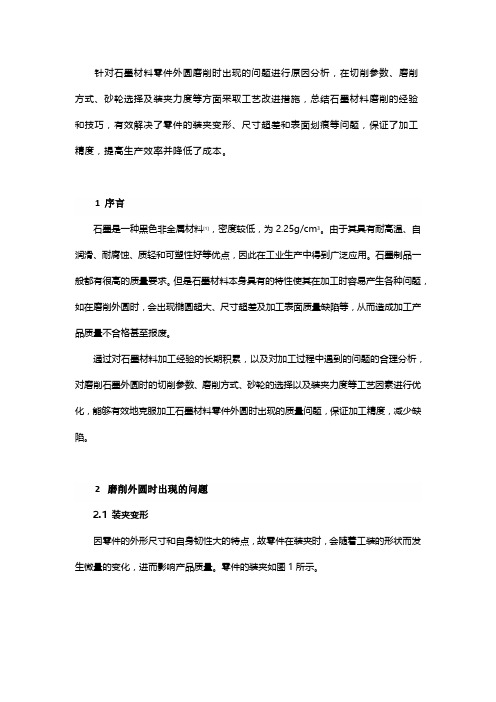
针对石墨材料零件外圆磨削时出现的问题进行原因分析,在切削参数、磨削方式、砂轮选择及装夹力度等方面采取工艺改进措施,总结石墨材料磨削的经验和技巧,有效解决了零件的装夹变形、尺寸超差和表面划痕等问题,保证了加工精度,提高生产效率并降低了成本。
1 序言石墨是一种黑色非金属材料[1],密度较低,为2.25g/cm3。
由于其具有耐高温、自润滑、耐腐蚀、质轻和可塑性好等优点,因此在工业生产中得到广泛应用。
石墨制品一般都有很高的质量要求。
但是石墨材料本身具有的特性使其在加工时容易产生各种问题,如在磨削外圆时,会出现椭圆超大、尺寸超差及加工表面质量缺陷等,从而造成加工产品质量不合格甚至报废。
通过对石墨材料加工经验的长期积累,以及对加工过程中遇到的问题的合理分析,对磨削石墨外圆时的切削参数、磨削方式、砂轮的选择以及装夹力度等工艺因素进行优化,能够有效地克服加工石墨材料零件外圆时出现的质量问题,保证加工精度,减少缺陷。
2 磨削外圆时出现的问题2.1 装夹变形因零件的外形尺寸和自身韧性大的特点,故零件在装夹时,会随着工装的形状而发生微量的变化,进而影响产品质量。
零件的装夹如图1所示。
图1 零件的装夹(1)影响零件的圆度和同轴度同轴度的两个加工基准是内孔与心轴,零件内孔与小锥度心轴过盈配合,心轴的磨损或顶尖与中心孔接触不良可能会引起跳动超差。
上一道工序的内孔采用车床加工,有装夹变形的情况发生,可能造成内孔呈椭圆状,从而影响外圆的加工精度。
(2)影响零件的尺寸石墨材料具有很大的韧性,当石墨零件装夹在心轴上时,由于心轴有锥度,因此零件会被心轴撑大,从而产生变形,进而使零件实际尺寸偏小,造成超差。
2.2 零件表面产生各种缺陷石墨材料零件在磨削过程中,由于质地较软[2],会受到砂轮颗粒和磨削方式等因素的影响,使零件表面产生各种缺陷:①多角形缺陷。
在零件表面沿轴线方向存在一条条等距的直线痕迹。
②螺旋形缺陷。
磨削表面呈现一条螺旋痕迹。
外圆磨削加工的质量缺陷分析与控制

外圆磨削加工的质量缺陷分析与控制作者:张光普焦禹萃张艳兵来源:《科技资讯》 2014年第27期张光普焦禹萃张艳兵(郑州工业应用技术学院河南郑州 451100)摘要:目前,外圆磨削技术已广泛应用于各种零件的加工中,但在磨削过程中经常出现一些有质量缺陷的零件,如加工过的零件常常会出现表面烧伤、划伤等现象。
因此,为了保证磨削后的产品的质量,在加工时就要有足够高的加工精度的磨床。
该文将从外圆磨削加工的质量缺陷分析以及控制方法进行阐述。
关键词:磨削加工质量缺陷分析控制中图分类号:TG581 文献标识码:A 文章编号:1672-3791(2014)09(c)-0049-01Quality defects analysis and controlling of grindingZhang Guangpu Jiao Yucui Zhang Yanbing(The Industrial Applied Technology College of Zhengzhou,Zhengzhou Henan,451100 China)Abstract:at present, the external cylindrical grinding technology has been widely used in various kinds of parts processing, but often appear some quality defects in the process of grinding parts, such as processed parts often appear burns, scratches and other surface phenomenon. Therefore, in order to guarantee the quality of the products after grinding, during processing need to be high enough to machining precision grinding machine. This article will from external circular grinding quality defects analysis and elaborates the control approach.Key Words:Grinding;Analysis of Quality Defects;Control磨削是指用磨料、磨具等工具来加工比较精确零件的加工方法。
无心磨削改善轴承外径棱圆度误差的方法

无心磨削改善轴承外径棱圆度误差的方法李延杰,关艳敏,姜 明(哈尔滨轴承集团公司 推力轴承分厂,黑龙江 哈尔滨 150036)摘 要:通过对无心磨削机床的参数调整和计算分析,结合生产实际,找出了外径棱圆度的影响因素并加以 控制,确保了产品质量。
关键词:轴承外径;外径磨削;棱圆度;圆形偏差 中图分类号:TG 581+.3 文献标识码:B文章编码:1672-4582(2013)01-0037-02Method of improving prismatic roundness error of bearingouter diameter with centerless grindingLi Y anjie, Guan Y anmin, Jiang Ming( Thrust Bearing Factory, Harbin Bearing Group Corporation, Harbin 150036,China )Abstract: By the parameter adjustment and calculation analysis of centerless grinding machine, and relations with the actual production, the influencing factors of prismatic roundness of the outer diameter were found and controled, the quality was ensured.Key words: bearing outer diameter; grinding of outside diameter; prismatic roundness; roundness deviation1 前言是圆形偏差中的一种。
在无心外圆磨床(如 M1080、M1081等)磨削过程中,套圈放置于机 床的砂轮与导轮之间,工件的下面由托板托住。
M250磨床磨削圆度超差的原因分析及维修
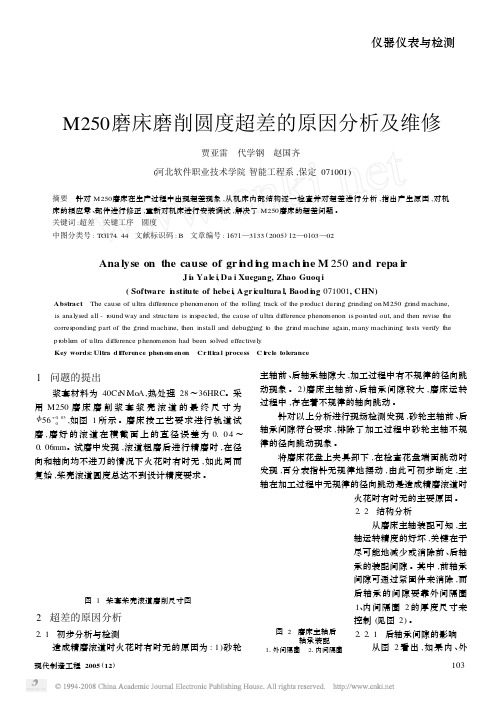
M250磨床磨削圆度超差的原因分析及维修贾亚雷 代学钢 赵国齐(河北软件职业技术学院智能工程系,保定071001)摘要 针对M250磨床在生产过程中出现超差现象,从机床内部结构逐一检查并对超差进行分析,指出产生原因,对机床的相应零、部件进行修正,重新对机床进行安装调试,解决了M250磨床的超差问题。
关键词:超差 关键工序 圆度中图分类号:TG174.44 文献标识码:B 文章编号:1671—3133(2005)12—0103—02Ana lyse on the cause of gr i n d i n g mach i n e M250and repa i rJ i a Ya le i,Da i Xuegang,Zhao Guoq i(Software i n stitute of hebe i,Agr i cultura l,Baod i n g071001,CHN) Abstract The cause of ultra difference phenomenon of the r olling track of the p r oduct during grinding on M250grind machine, is analysed all-r ound way and structure is ins pected,the cause of ultra difference phenomenon is pointed out,and then revise the corres ponding part of the grind machine,then install and debugging t o the grind machine again,many machining tests verify the p r oblem of ultra difference phenomenon had been s olved effectively.Key words:Ultra d i fference pheno m enon Cr iti ca l process C i rcle tolerance1 问题的提出浆套材料为40Cr N i M oA,热处理28~36HRC。
外圆磨床圆度超差分析

外圆磨床磨削工件圆度超差的解决办法
1、若工件中心孔不合格时研磨工件中心孔至准确的角度
且其圆度误差达到要求
2、头架尾架的顶尖与轴锥孔的配合接触不良,工作时引起
晃动,则应卸下顶尖检查接触面上是否有毛刺用刮刀修去
3、头架尾架顶尖磨损时应修磨顶尖以校正顶尖角度,最好
采用硬质合金顶尖
4、工件两端中心孔轴心线同轴度超差时应重研工件中心
孔
5、工件顶得过紧或过松,要重新调整尾座的位置
6、磨削液不够充分容易使工件发生热变形要注意加大磨
削液
7、磨细长的工件时为防止中心架使用不当应注意调整中
心托架
8、工件中心孔太浅时应重钻中心孔
9、头架主轴旋转精度
10、尾架主轴旋转精度
11、砂轮主轴旋转精度。
外圆磨削中常见缺陷的产生原因及消除方法

工件有鼓形
1、工件刚性差,磨削时产 生弹性弯曲变形。
2、中主架调整不适当。
1、减少工件的弹性变形
(1)减速少背吃刀量,最的多 作“光磨”行程
(2)及时修整砂轮,使其经常 保持良好的切削性能
(3)工件很长时,应使用适当 数量的中心架
3、调整砂轮架位置
台阶轴各外 圆表面有同 轴度误差
1、与圆度误差原因1〜5相同
2、磨削用量过大及“光磨” 时间不够
3、磨削步骤安排不当
4、用卡盘装夹磨削时,工 件找不正不对,或头架主 轴径向圆跳动太大
1、与消除圆度误差的方法院~5相同
2、精磨时减小背吃刀量并多作“光 磨”和程式
3、同轴度要求高的表面应分清粗 磨、精磨,同时尽可能在一次装夹 中精磨完毕。
2、正确调整停留时间
轴肩端面有
跳动
1、进给量过大,退刀过快。
2、切削液不充分
3、工件顶得过紧或过松
4、砂轮主轴有轴向窜动。
5、头架主轴推力轴承间隙 过大
6、用卡盘装夹磨削端面 时,头架主轴轴向窜动过 大。
1、进给地纵向摇动工作台要慢而均 匀,“光磨”时间要充分
2、加大切削液
3、调节尾座顶尖压力
4、检修机庆
而背吃刀量过大。
2、纵向进给量太大
3、砂轮磨损,素线不直
4、金刚石在修整器中未夹 紧或金刚石在刀杆上焊接 不牢,有松动现象,使修 出的砂轮凸凹不平
5、切削液太少或太淡
6、工作台导轨润滑油浮力 过大使工作漂起,在运动 中产生摆动。
7、工作台运行时有爬行现 象
&砂轮主轴有轴向窜动
适当减小背吃刀量