年产960万吨连铸坯的全连铸转炉炼钢车间工艺设计
炼钢艺设计流程图

炼钢工艺流程1炼钢厂简介炼钢厂主要将铁水冶炼成钢水,再经连铸机浇铸成合格铸坯。
现有5座转炉,5台连铸机,年设计生产能力为500万吨,现年生产钢坯400万吨。
其中炼钢一分厂年生产能力到达240万吨;炼钢二厂年生产能力为160万吨。
2炼钢的根本任务钢是以Fe为基体并由C、Si、Mn、P、S等元素以及微量非金属夹杂物共同组成的合金。
炼钢的根本任务包括:脱碳、脱磷、脱硫、脱氧去除有害气体和夹杂,提高温度,调整成分,炼钢过程通过供氧造渣,加合金,搅拌升温等手段完成炼钢根本任务,"四脱两去两调整〞。
3氧气转炉吹炼过程氧气顶吹转炉的吹氧时间仅仅是十分钟,在这短短的时间内要完成造渣,脱碳、脱磷、脱硫、去气,去除非金属夹杂物及升温等根本任务。
由于使用的铁水成分和所炼钢种的不同,吹炼工艺也有所区别。
氧气顶吹转炉炼钢的吹炼过程,根据一炉钢吹炼过程中金属成分,炉渣成分,熔池温度的变化规律,吹炼过程大致可以分为以下3个阶段:〔1〕吹炼前期。
〔2〕吹炼中期。
〔3〕终点控制。
炼好钢必须抓住各阶段的关键,精心操作,才能到达优质、高产、低耗、长寿的目标。
3.1装入制度装入制度是保证转炉具有一定的金属熔池深度,确定合理的装入数量,适宜的铁水废钢比例。
装入量确实定装入量是指转炉冶炼中每炉次装入的金属料总重量,它主要包括铁水和废钢量。
目前国内外装入制度大体上有三种方式:〔1〕定深装入;〔2〕分阶段定量装入;〔3〕定量装入装入次序目前永钢的操作顺序为,钢水倒完后进展溅渣护炉溅渣完后装入废钢,然后兑入铁水。
为了维护炉衬,减少废钢对炉衬的冲击,装料次序也可以先兑铁水,后装废钢。
假设采用炉渣预热废钢,则先加废钢,再倒渣,然后兑铁水。
如果采用炉内留渣操作,则先加局部石灰,再装废钢,最后兑铁水。
3.2供氧制度制订供氧制度时应考虑喷头构造,供氧压力,供氧强度和氧枪高度控制等因素。
氧枪喷头转炉供氧的射流特征是通过氧枪喷头来实现的,因此,喷头构造的合理选择是转炉供氧的关键。
年产370万吨连铸坯的转炉炼钢车间工艺设计毕业设计论文
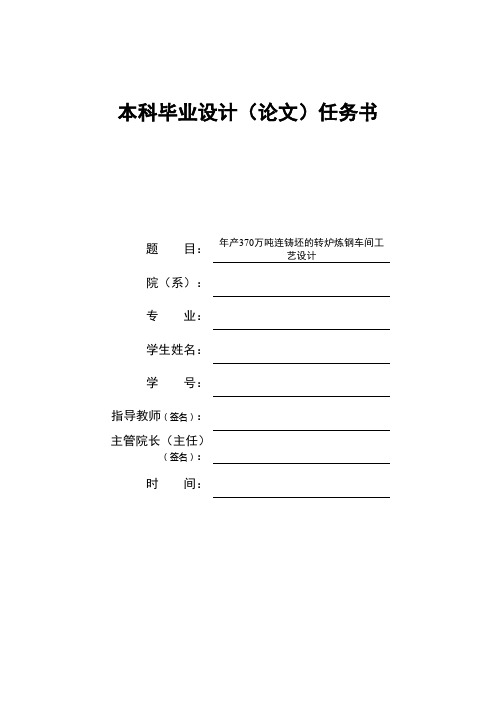
本科毕业设计(论文)任务书题目:年产370万吨连铸坯的转炉炼钢车间工艺设计院(系):专业:学生姓名:学号:指导教师(签名):主管院长(主任)(签名):时间:毕业设计(论文)原创性声明和使用授权说明原创性声明本人郑重承诺:所呈交的毕业设计(论文),是我个人在指导教师的指导下进行的研究工作及取得的成果。
尽我所知,除文中特别加以标注和致谢的地方外,不包含其他人或组织已经发表或公布过的研究成果,也不包含我为获得及其它教育机构的学位或学历而使用过的材料。
对本研究提供过帮助和做出过贡献的个人或集体,均已在文中作了明确的说明并表示了谢意。
作者签名:日期:指导教师签名:日期:使用授权说明本人完全了解大学关于收集、保存、使用毕业设计(论文)的规定,即:按照学校要求提交毕业设计(论文)的印刷本和电子版本;学校有权保存毕业设计(论文)的印刷本和电子版,并提供目录检索与阅览服务;学校可以采用影印、缩印、数字化或其它复制手段保存论文;在不以赢利为目的前提下,学校可以公布论文的部分或全部内容。
作者签名:日期:学位论文原创性声明本人郑重声明:所呈交的论文是本人在导师的指导下独立进行研究所取得的研究成果。
除了文中特别加以标注引用的内容外,本论文不包含任何其他个人或集体已经发表或撰写的成果作品。
对本文的研究做出重要贡献的个人和集体,均已在文中以明确方式标明。
本人完全意识到本声明的法律后果由本人承担。
作者签名:日期:年月日学位论文版权使用授权书本学位论文作者完全了解学校有关保留、使用学位论文的规定,同意学校保留并向国家有关部门或机构送交论文的复印件和电子版,允许论文被查阅和借阅。
本人授权大学可以将本学位论文的全部或部分内容编入有关数据库进行检索,可以采用影印、缩印或扫描等复制手段保存和汇编本学位论文。
涉密论文按学校规定处理。
作者签名:日期:年月日导师签名:日期:年月日注意事项1.设计(论文)的内容包括:1)封面(按教务处制定的标准封面格式制作)2)原创性声明3)中文摘要(300字左右)、关键词4)外文摘要、关键词5)目次页(附件不统一编入)6)论文主体部分:引言(或绪论)、正文、结论7)参考文献8)致谢9)附录(对论文支持必要时)2.论文字数要求:理工类设计(论文)正文字数不少于1万字(不包括图纸、程序清单等),文科类论文正文字数不少于1.2万字。
转炉车间设计
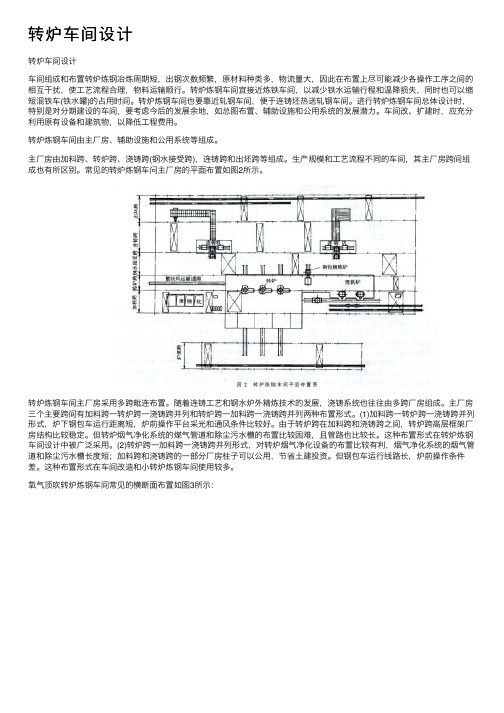
转炉车间设计转炉车间设计车间组成和布置转炉炼钢冶炼周期短,出钢次数频繁,原材料种类多,物流量⼤,因此在布置上尽可能减少各操作⼯序之间的相互⼲扰,使⼯艺流程合理,物料运输顺⾏。
转炉炼钢车间宜接近炼铁车间,以减少铁⽔运输⾏程和温降损失,同时也可以缩短混铁车(铁⽔罐)的占⽤时间。
转炉炼钢车间也要靠近轧钢车间,便于连铸坯热送轧钢车间。
进⾏转炉炼钢车间总体设计时,特别是对分期建设的车间,要考虑今后的发展余地,如总图布置、辅助设施和公⽤系统的发展潜⼒。
车间改、扩建时,应充分利⽤原有设备和建筑物,以降低⼯程费⽤。
转炉炼钢车间由主⼚房、辅助设施和公⽤系统等组成。
主⼚房由加料跨、转炉跨、浇铸跨(钢⽔接受跨),连铸跨和出坯跨等组成。
⽣产规模和⼯艺流程不同的车间,其主⼚房跨间组成也有所区别。
常见的转炉炼钢车问主⼚房的平⾯布置如图2所⽰。
转炉炼钢车间主⼚房采⽤多跨毗连布置。
随着连铸⼯艺和钢⽔炉外精炼技术的发展,浇铸系统也往往由多跨⼚房组成。
主⼚房三个主要跨间有加料跨⼀转炉跨⼀浇铸跨并列和转炉跨⼀加料跨⼀浇铸跨并列两种布置形式。
(1)加料跨⼀转炉跨⼀浇铸跨并列形式,炉下钢包车运⾏距离短,炉前操作平台采光和通风条件⽐较好。
由于转炉跨在加料跨和浇铸跨之间,转炉跨⾼层框架⼚房结构⽐较稳定。
但转炉烟⽓净化系统的煤⽓管道和除尘污⽔槽的布置⽐较困难,且管路也⽐较长。
这种布置形式在转炉炼钢车间设计中被⼴泛采⽤。
(2)转炉跨⼀加料跨⼀浇铸跨并列形式,对转炉烟⽓净化设备的布置⽐较有利,烟⽓净化系统的烟⽓管道和除尘污⽔槽长度短;加料跨和浇铸跨的⼀部分⼚房柱⼦可以公⽤,节省⼟建投资。
但钢包车运⾏线路长,炉前操作条件差。
这种布置形式在车间改造和⼩转炉炼钢车间使⽤较多。
氧⽓顶吹转炉炼钢车间常见的横断⾯布置如图3所⽰:加料跨转炉兑铁⽔、加废钢和炉前冶炼操作均在加料跨进⾏。
⼀般将转炉炼钢车间的铁⽔区和废钢区分别布置在加料跨的两端,中部为转炉炉前操作区。
年产100万吨合格不锈钢铸坯的电炉炼钢厂工艺设计

西安建筑科技大学本科毕业设计(论文)任务书题目:年产100万吨合格不锈钢铸坯的电炉炼钢厂工艺设计院(系):冶金工程学院专业:冶金工程学生姓名:学号:指导教师(签名):主管院长(主任)(签名):时间:2012年 2 月28 日设计总说明本文设计了一个年产100万吨合格不锈钢的电弧炉炼钢车间,通过产品大纲的确定、电弧炉炼钢的物料平衡与热平衡计算、超高功率电弧炉的炉型设计、连铸设备选择、车间工艺设计及车间总体布置,确定了一座150吨超高功率电弧炉、一台AOD精练炉、一台连铸机为主要生产设备。
并根据国内外炼钢技术的发展趋势、钢铁产品的发展方向,选择了先进且有较大发展余地的短流程工艺:废钢→超高功率电弧炉→AOD炉精炼→连铸。
设计方案以技术新、效益高为原则,充分体现了先进、灵活、多功能的特点,具备可持续发展性。
关键词:超高功率电弧炉,AOD精炼炉,炼钢Design DescriptionIn this paper, we have designed a electric arc furnace workshop which can produce 1000,000 tons of qualified stainless steel a year.Through the ascertained of the products outline, eaf material balance, thermal equilibrium calculation, ultra-high power electric arc furnace’s type design ,the workshop process design and workshop layout, we finaly identified a 1000,000 tons of qualified stainless steel smelting plant with which a 150 tons of ultra-high power electric arc furnace, a chastening AOD furnace and a caster is as the main production equipment.And according to the domestic and foreign steelmaking technology trends, the development direction of the steel product,we finally selected the short flow process,scrap steel →ultra-high power e lectric arc furnace→AOD furnace refineing→continuous casting, which is advanced and has a bigger development room.The Design scheme based new technology and high efficienc as the principle, fully embodies the advanced, flexible, multi-function characteristic and has the characteristics of sustainable development. Key Words:ultra-high power electric arc furnace,AOD refineing furnace, Steelmaking目录绪论 (1)1电弧炉炼钢车间的设计方案[1][2] (4)1.1电炉车间生产能力计算 (4)1.1.1 电炉容量和台数的确定 (4)1.1.2 电炉车间生产技术指标 (4)1.2电炉车间设计方案 (5)1.2.1主要冶炼钢种及产品方案 (5)1.2.2电炉炼钢车间设计与建设的基础材料 (5)1.2.3电炉炼钢车间的组成 (6)1.2.4 电炉各车间的布置情况 (6)2 电弧炉炉型设计[3] (7)2.1电弧炉炉型设计 (7)2.1.1 电弧炉炉型 (7)2.1.2 熔池的形状和尺寸 (7)2.1.3 熔化室的尺寸 (8)2.1.4 炉衬厚度δ的确定 (9)2.1.5 炉壳及厚度δz的确定 (9)2.1.6 工作门和出钢口 (10)2.2偏心底出钢箱的设计 (10)2.3电弧炉变压器功率和电参数的确定 (11)2.3.1确定变压器的功率 (11)2.3.2电极直径的确定 (12)2.3.3电极心圆的尺寸 (12)2.4水冷挂渣炉壁设计 (12)3电弧炉炼钢物料平衡和热平衡 (16)3.1物料平衡计算 (16)3.1.1 熔化期的物料平衡 (16)3.1.2 氧化期的物料平衡 (22)3.2热平衡计算 (25) (25)3.2.1 计算热收入QS (26)3.2.2 计算热支出QZ4 电弧炉炼钢车间工艺布置 (29)4.1原料跨 (29)4.1.1 原料跨的跨度 (30)4.1.2 原料跨总长度确定 (30)4.1.3 原料跨高度确定 (30)4.2炉子跨整体布置 (30)4.2.1 炉子跨工作平台高度 (30)4.2.2 炉子的变压器室和控制室 (31)4.2.3 电弧炉出渣和炉渣处理 (31)4.2.4 炉子跨的长度、跨度、高度 (31)4.3精炼跨 (31)4.3.1 整体布置 (31)4.3.2 AOD精炼炉的工艺布置 (32)4.4连铸跨 (32)4.4.1 总体布置 (32)4.4.2 连铸机操作平台的高度、长度、宽度 (32)4.4.3 连铸机总高和本跨吊车轨面标高 (33)4.4.4 连铸机总长度 (33)4.4.5 连铸跨跨度 (34)4.5出坯跨 (34)4.6备注 (34)5 电弧炉炼钢车间工艺设计 (36)5.1废钢 (36)5.2辅助料 (36)5.2.1 对辅助料的要求 (36)5.2.2 供应方案 (37)5.2.3 配料 (37)5.2.4 装料和补料 (38)5.2.5 电弧炉冶金工艺[3] (39)5.2.6 精炼工艺[4] (40)5.2.7 连铸操作工艺 (41)6 车间主要设备的选择 (43)6.1电弧炉主要设备选择 (43)6.1.1 校核年产量 (43)6.1.2 电极 (43)6.2精炼炉设备选择 (44)6.3连铸设备选型[5] (45)6.3.1 钢包允许的最大浇注时间 (45)6.3.2 拉坯速度 (45)6.3.3 连铸机的流数 (46)6.3.4 弧型半径 (46)6.4连铸机的生产能力的确定 (47)6.4.1 连铸浇注周期的计算 (47)6.4.2 连铸机作业率 (47)6.4.3 连铸坯收得率 (48)6.4.4 连铸机生产能力的计算 (48)6.5中间包及其运载设备 (49)6.5.1 中间包的形状和构造 (49)6.5.2 中间包的主要工艺参数 (49)6.5.3 中间包运载装置 (49)6.6结晶器及其振动装置 (49)6.6.1 结晶器的性能要求及其结构要求 (49)6.6.2 结晶器主要参数选择 (50)6.6.3 结晶器的振动装置 (50)6.7二次冷却装置 (51)6.7.1 二次冷却装置的基本结构 (51)6.7.2 二次冷却水冷喷嘴的布置 (51)6.7.3 二次冷却水量的计算 (51)6.8拉矫装置及引锭装置 (51)6.8.1 拉矫装置 (51)6.8.2 引锭装置 (51)6.9铸坯切割装置 (51)6.10盛钢桶的选择 (51)6.11渣罐及渣罐车的选择 (53)6.11.1 车间所需的渣罐数量 (53)6.11.2 车间所需渣罐车数量 (53)6.12起重机的选择 (53)6.13其它辅助设备的选择 (54)7 车间人员编制及主要经济技术指标 (55)7.1技术经济指标 (55)7.1.1 产量指标 (55)7.1.2 质量指标 (55)7.1.3 作业效率指标 (55)7.1.4 连铸生产技术指标 (55)7.2车间人员编制 (55)参考文献 (58)致谢 (59)专题............................................... 错误!未定义书签。
年产320万吨合格铸坯的转炉炼钢车间工艺设计毕业设计论文
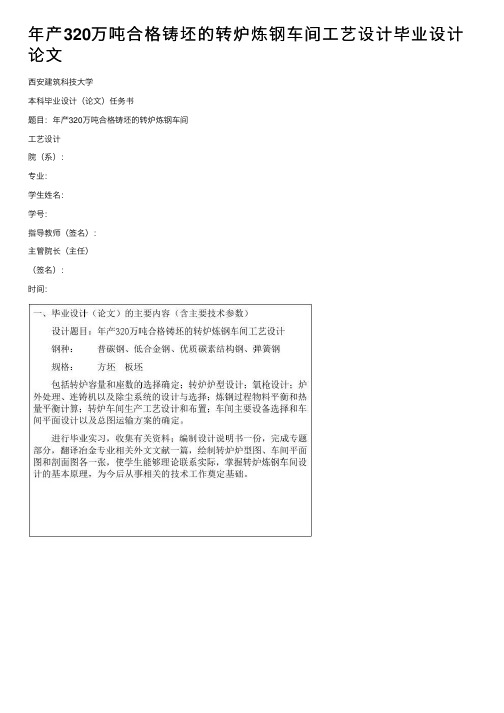
年产320万吨合格铸坯的转炉炼钢车间⼯艺设计毕业设计论⽂西安建筑科技⼤学本科毕业设计(论⽂)任务书题⽬:年产320万吨合格铸坯的转炉炼钢车间⼯艺设计院(系):专业:学⽣姓名:学号:指导教师(签名):主管院长(主任)(签名):时间:年产320万吨合格铸坯的转炉炼钢车间⼯艺设计设计总说明本设计根据设计任务书的要求,结合所学专业理论知识,对炼钢⼚从原料供给到炼钢过程,最后到连铸出坯等流程进⾏了全⾯的设计。
根据⽣产钢种及车间规模,选择的⼯艺流程是:BOF-LF-CC。
设计以炼钢车间为主体,并重点针对顶底复吹转炉。
在转炉物料平衡和热平衡计算的基础上,对炼钢车间的主要设备型号及参数进⾏了选择和设计,对车间⼈员编制及技术经济指标进⾏了计算,并且完成了主体设备选择、炼钢⼯艺设计、主⼚房⼯艺布置和设备布置⼯作。
编写说明书⼀份,绘制转炉炉型图、车间平⾯图和剖⾯图各⼀张,完成专题写作及外⽂翻译。
关键词:转炉炼钢车间;⼯艺设计;物料平衡及热平衡计算;炉外精炼;连铸Designing of the BOF Steelmaking Processing for the Annual Output of 3.2Million-ton SlabAccording to the design requirements of the mission statement,combined with the theoretical knowledge,from raw material supply to the steel making process,a slab continuous casting processing was designed. The processing is BOF-LF-CC. The steel-making plant is the main design project,the top and bottom blowing converter was selected. Based on the converter material balance and heat balance calculation,we completed the main equipment for steel-making plant selection and design parameters,and the completion of the main equipment selection,the design of steel-making process. Furthermore,the technical economy parameters was calculated,the main process plant layout and equipment layout were designed. Prepared a manual,drawing a converter furnace map,areal workshop and section plane blueprint .Translated a English paper into Chinese.Key words: BOF steel-making workshop;processing designing;converter material balance and heat balance calculation;Secondary refining;casting⽬录1炼钢车间设计⽅案 (1)1.1主要钢种及产品⽅案 (1)1.2⼯艺流程 (1)1.3转炉车间组成及⽣产能⼒的确定 (2) 1.3.1车间组成 (2)1.3.2转炉车间⽣产能⼒的确定 (2)1.4主⼚房⼯艺布置 (3)1.4.1原料跨间布置 (3)1.4.2炉⼦跨的布置 (3)1.4.3精炼跨的布置 (3)1.4.4浇注跨的布置 (3)1.5原材料⽅案设计 (4)1.5.1⾦属料 (4)1.5.2散状材料 (5)2物料平衡与热平衡 (5)2.1物料平衡 (5)2.1.1计算原始数据 (5)2.1.2物料平衡基本项⽬ (7)2.1.3计算步骤 (7)2.2热平衡计算 (15)2.2.1计算原始数据 (15)2.2.2计算步骤 (16)3顶底复吹转炉设计 (20)3.1炉型设计 (20)3.1.1炉型选择 (20)3.1.2主要参数的确定。
年产万吨钢坯电炉炼钢车间初步设计
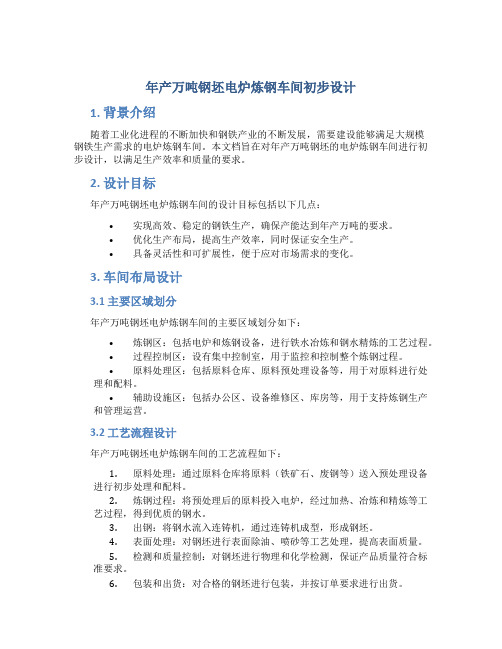
年产万吨钢坯电炉炼钢车间初步设计1. 背景介绍随着工业化进程的不断加快和钢铁产业的不断发展,需要建设能够满足大规模钢铁生产需求的电炉炼钢车间。
本文档旨在对年产万吨钢坯的电炉炼钢车间进行初步设计,以满足生产效率和质量的要求。
2. 设计目标年产万吨钢坯电炉炼钢车间的设计目标包括以下几点:•实现高效、稳定的钢铁生产,确保产能达到年产万吨的要求。
•优化生产布局,提高生产效率,同时保证安全生产。
•具备灵活性和可扩展性,便于应对市场需求的变化。
3. 车间布局设计3.1 主要区域划分年产万吨钢坯电炉炼钢车间的主要区域划分如下:•炼钢区:包括电炉和炼钢设备,进行铁水冶炼和钢水精炼的工艺过程。
•过程控制区:设有集中控制室,用于监控和控制整个炼钢过程。
•原料处理区:包括原料仓库、原料预处理设备等,用于对原料进行处理和配料。
•辅助设施区:包括办公区、设备维修区、库房等,用于支持炼钢生产和管理运营。
3.2 工艺流程设计年产万吨钢坯电炉炼钢车间的工艺流程如下:1.原料处理:通过原料仓库将原料(铁矿石、废钢等)送入预处理设备进行初步处理和配料。
2.炼钢过程:将预处理后的原料投入电炉,经过加热、冶炼和精炼等工艺过程,得到优质的钢水。
3.出钢:将钢水流入连铸机,通过连铸机成型,形成钢坯。
4.表面处理:对钢坯进行表面除油、喷砂等工艺处理,提高表面质量。
5.检测和质量控制:对钢坯进行物理和化学检测,保证产品质量符合标准要求。
6.包装和出货:对合格的钢坯进行包装,并按订单要求进行出货。
4. 设备选型和布置4.1 电炉选型年产万吨钢坯电炉炼钢车间的主要设备之一是电炉。
根据生产需求和技术要求,选用适当容量和高效率的电炉。
4.2 其他设备选型根据车间的实际情况,选用适当的设备,如炉盖起重机、原料处理设备、连铸机等。
选型时需要考虑设备的性能、稳定性、能耗和维护等因素。
4.3 设备布置根据车间布局和工艺流程,合理布置设备,保证生产流程的顺畅和安全。
转炉炼钢的总体工艺设计

转炉炼钢的总体工艺设计1、转炉炼钢车间设计应根据产品大纲,确定转炉公称容量、转炉座数和炉外精炼的配置。
2、转炉炼钢车间内转炉座数宜配置2座或3座,不宜大于4座,不应设置备用炉座。
多于3座转炉的车间,转炉宜分组分开布置。
3、转炉的公称容量应为炉役期的平均出钢量,最大出钢量应为公称容量的1.05倍~1.10倍,转炉生产宜采用分阶段定量法操作。
4、转炉吹炼炉座的年生产能力应按下列公式计算:式中:Q——每一吹炼炉座年产合格钢水量(t/a);G——转炉炉役期内每炉平均出钢量(t/炉);T——每炉钢平均冶炼周期(min/炉);N——转炉的年有效作业天数(d/a);n1——年修炉天数(d/a);n2——年日常计划检修天数(d/a);n3——年车间集中检修天数(d/a);n4——年生产耽误天数(d/a)。
5、转炉炼钢车间的组成宜符合下列规定:(1)主要生产系统宜包括主厂房、铁水预处理站、废钢配料间、炉渣间、烟气净化及煤气回收设施、余热蒸汽回收设施;(2)辅助生产系统宜包括铁合金贮运设施、散状原料贮运设施、快速分析室、空压站、车间变配电所、水处理设施、除尘设施、生活福利设施;(3)设计可根据生产规模、原材料供应情况等具体条件确定车间实际组成。
6、铁水中含有可利用的铌、钒、钛等合金元素时,应采用合理的冶炼工艺予以回收。
7、新建转炉的冶炼控制,宜采用以副枪检测系统和(或)炉气成分连续分析系统作为实时信号反馈的动态闭环过程控制。
8、转炉的各种工艺过程和能源介质的工作参数,均应配置检测仪表,所有被检测参数应输入到基础自动化控制系统。
冶炼试样应采用快速分析系统,数据应传输到过程控制计算机系统。
9、转炉炼钢使用的气体介质、燃料、冷却水及其管道,应符合下列规定:(1)氧气、氩气、氮气、蒸汽、压缩空气和燃料的供应能力应按设计规定的工作制度配备,并应按吨钢耗量和转炉车间的小时生产率计算;(2)贮气罐容积应满足车间高峰用量,同时能适应用量的波动和当供应源因事故停供时,贮气罐的贮备量至少应能满足一炉钢冶炼的需要;(3)车间分期建设时,各种介质的主管道宜按最终规模一次建成,而相关公用设施可视具体条件,或在总图上预留发展面积,也可在厂房内预留增建机组的条件。
设计年产395万吨合格连铸坯的转炉炼钢车间毕业设计

设计年产395万吨合格连铸坯的转炉炼钢车间毕业设计目录摘要............................................... 错误!未定义书签。
Abstract ........................................... 错误!未定义书签。
目录 (I)绪论 (1)1 设计方案的确定与论证 (2)1.1 产品大纲的制定 (2)1.1.1 产品大纲制定的原则及方法 (2)1.1.2 产品大纲 (2)1.1.3 典型钢种(IF钢)的介绍 (3)1.1.4 E36船板钢 (4)1.1.5 Q235结构钢 (5)1.1.6 X80管线钢 (6)1.1.7 耐候钢 (6)1.2 方案的选择与论证 (7)1.2.1 炉容量与座数的确定 (7)1.2.2 冶炼与精炼方法的选择与论证 (8)1.2.3 连铸机的选择 (13)2 物料平衡和热平衡计算 (15)2.1原始数据 (15)2.1.1铁水成分及温度 (15)2.1.2原材料成分 (15)2.1.3冶炼钢种成分 (16)2.1.4平均比热 (16)2.1.5反应热效率(认为25℃与炼铁温度下两者数值近似) (16)2.1.6有关参数的选用 (17)2.2 物料平衡计算 (17)2.2.1炉渣量及炉渣成分的计算 (17)2.2.2 矿石及烟尘中的铁量和氧量的计算 (22)2.2.3 炉气成分及重量的计算见表2-14 (22)2.2.4 未加废钢时氧气的消耗量的计算见表2-15 (23)2.2.5 钢水量计算 (24)2.2.6 未加废钢时的物料平衡表见表2-16 (24)2.3 热平衡计算(取冷料为25℃) (25)2.3.1 热收入项 (25)2.3.2 热支出项 (25)2.3.3 热平衡表见表2-17 (27)2.4 加入废钢后的物料平衡计算 (28)2.4.1 加入废钢的物料平衡计算 (28)3 车间主体设备的设计 (30)3.1 转炉炉型的设计 (30)3.1.1 原始数据 (30)3.1.2 炉容比 (30)3.1.3 熔池尺寸的计算 (30)3.1.4 炉帽尺寸的确定 (32)3.1.5 炉身尺寸的确定 (32)3.1.6 出钢口尺寸确定 (32)3.1.7 炉衬厚度确定 (33)3.1.8 炉壳厚度确定 (33)3.1.9 验算高宽比 (33)3.1.10 转炉主要参数 (33)3.2 喷头及氧枪的设计计算 (34)3.2.1 喷头参数的选择 (34)3.2.2 氧枪枪身设计 (35)3.3 氧枪的升降机构与更换装置 (38)3.3.1 氧枪的升降机构 (39)3.3.2 升降卷扬机变速方式 (39)3.3.3 升降小车和固定导轨 (40)3.3.4 安全装置 (40)3.3.5 氧枪更换装置 (40)3.4 连铸机的主要设计参数 (40)3.4.1 钢包允许浇铸时间 (40)3.4.2 铸坯断面的选择 (41)3.4.3 理论拉速与工作拉速的确定 (41)3.4.4 冶金长度的计算 (42)3.4.5 连铸机圆弧(外弧)半径的计算R (43)3.4.6 连铸机的流数的计算 (44)3.4.7 连铸机生产能力的计算 (45)3.5 盛钢桶的计算 (47)3.5.1盛钢桶容积计算 (47)3.5.2 钢包需要量计算 (49)3.5.3 钢包质量计算 (50)3.6 RH精炼 (51)3.6.1 处理容量 (51)3.6.2 处理时间 (51)3.6.3 循环因数 (52)3.6.4 循环流量 (52)3.6.5 真空度 (53)3.6.6 真空泵的抽气能力 (53)3.7 钢包回转台 (54)3.7.1 直臂式钢包回转台 (54)3.7.1 双臂式钢包回转台 (55)3.8 中间包的主要设计参数 (55)3.8.1 中间包的作用 (55)3.8.2 中间包的形状与构造 (56)3.8.3 中间包小车 (59)3.9 结晶器的主要设计参数 (59)3.9.1 结晶器结构型 (59)3.9.2 结晶器结构参数的确定 (59)3.9.3 结晶器的振动与振动装置 (60)3.10 二次冷却系统的设计 (61)3.10.1 二次冷却装置 (61)3.10.2 喷水冷却系统。
设计一座年产万吨良坯的转炉炼钢车间

设计一座年产万吨良坯的转炉炼钢车间背景介绍转炉炼钢车间是钢铁企业中重要的设施之一,用于将生铁和废钢进行冶炼和炼制,生产出良好品质的钢坯。
本文将介绍如何设计一座年产万吨良坯的转炉炼钢车间,以满足钢铁企业的生产需求。
工艺流程转炉炼钢车间的工艺流程通常包括以下几个步骤:1.废钢预处理:废钢经过分选、压块等工艺处理,以满足后续冶炼的要求;2.转炉冶炼:将生铁和废钢投入转炉中进行冶炼,通过吹氧、搅拌等控制参数,使炉内的成分达到预定要求;3.过程控制:对冶炼过程中的温度、压力、氧气吹入量等参数进行监控和调整,确保炉内的化学反应进行顺利;4.出钢操作:炼钢完成后,将炼钢渣和钢水分离,通过倾吊等工艺操作,将钢水倾入连铸机进行连铸;5.连铸过程:将钢水铸造成连续的坯料,在连铸机上进行拉伸、切割等操作,生产出相应规格的钢坯;6.冷却处理:将连铸坯料进行冷却处理,使其达到适合后续轧制加工的温度。
设备配置为了实现年产万吨良坯的转炉炼钢车间,需要合理配置以下关键设备:•转炉:根据产量要求选择适当规模的转炉,确保能够满足炼钢工艺的要求;•除尘设备:通过布袋除尘器等设备,对炼钢过程中产生的烟尘进行有效处理,减少对环境的影响;•吹氧设备:提供足够的氧气供应,在转炉冶炼过程中,通过吹氧操作促进化学反应的进行;•连铸机:选择合适规格的连铸机,能够实现稳定连铸生产,并保证坯料的质量;•冷却设备:通过冷却设备对连铸坯料进行快速冷却处理,确保其达到后续轧制工艺要求。
设施布局为了实现高效的运行和生产,转炉炼钢车间的设施布局应该合理设计,包括以下几个方面的考虑:1.原料区:合理划分废钢和生铁的存放区域,确保按需调配原料,并提供合适的设备进行前处理;2.转炉区:转炉应位于中心位置,便于对转炉冶炼过程进行监控和操作,同时设备之间的距离要合理,便于人员操作;3.出钢区:炼钢完成后,需要有足够的空间进行钢渣和钢水的分离操作,并能顺利将钢水倾入连铸机;4.连铸区:连铸机应根据产量设定合理数量,并合理布置连铸机的进出坯口位置,便于钢坯的连续生产;5.冷却区:钢坯在连铸后需要进行冷却处理,确保其达到后续轧制加工的要求,冷却区应根据产量和冷却时间合理设置。
炼钢车间设计
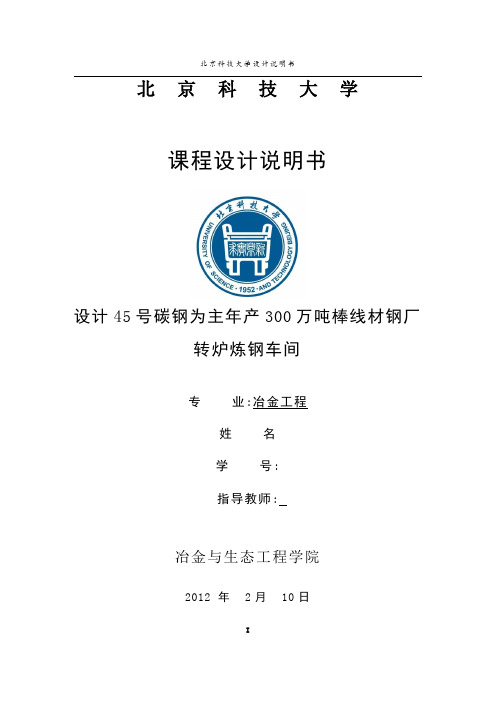
北京科技大学设计说明书
1.转炉计算 „„„„„„„„„„„„„„„„„„„„„„„„„„ 31 1.1 炉型设计及计算,划出炉型纵剖面图„„„„„„„„„„„„ 31 1.2 炉衬材质选定及其钢板的选定„„„„„„„„„„„„„„„ 33 1.3 校核转炉的高径比„„„„„„„„„„„„„„„„„„„„ 34
3.连铸机设计 „„„„„„„„„„„„„„„„„„„„„„„„„ 37 3.1 连铸坯断面„„„„„„„„„„„„„„„„„„„„„„„ 37 3.2 连铸机主要工艺参数的确定„„„„„„„„„„„„„„„„ 37 3.3 连铸机生产能力„„„„„„„„„„„„„„„„„„„„„ 39 3.4 结晶器选型及主要参数的选定„„„„„„„„„„„„„„„ 40 3.5 二冷系统的支撑和冷却方式及主要参数的选定„„ „„„„„„40 3.6 拉坯矫直装置的选定„„„„„„„„„„„„„„„„„„„ 42 3.7 铸坯切割设备及切割区长度的选定„„„„„„„„„„„„„ 42
送入小方坯连铸机保护浇注,出坯后热装热送。
表 1-2 45 号钢国标化学成分
元素
%C
%Si
%Mn
%P
%S
成分范围
0.42-0.50 0.17-0.37 0.50-0.80 ≤0.035 ≤0.035
45 钢 属 中 碳 钢 ,碳 是 影 响 其 性 能 的 关 键 元 素 ,也 是 炉 前 控 制 的 难 点 。
2.浇注系统设备及其计算 „„„„„„„„„„„„„„„„„„„„ 46 2.1 钢包容量、数量和钢包车的选定„„„„„„„„„„„„„„ 46 2.2 钢包载运装置的选定„„„„„„„„„„„„„„„„„„„ 46 2.3 中间包型式、配置及主要工艺参数的确定„„„„„„„„„„ 47
年产350万吨连铸坯的转炉炼钢车间工艺设计毕业论文

年产350万吨连铸坯的转炉炼钢车间工艺设计毕业论文目录1 绪论 (1)1.1 转炉冶炼原理简介 (1)1.2 氧气转炉炼钢的特点 (2)1.3设计原则和指导思想 (2)1.4 产品方案 (3)2 氧气转炉炼钢车间 (5)2.1 初始条件 (5)2.2 公称容量选择 (5)2.3 转炉座数的确定 (5)2.4根据生产规模和产品方案计算出年需钢水量。
(6)2.5 根据生产规模和产品方案计算出年需钢水量 (6)3 转炉物料平衡和热平衡计算 (8)3.1 氧气顶底复吹转炉的物料平衡和热平衡 (8)3.2热平衡计算 (20)3.2.1热平衡计算所需数据 (20)3.2.2计算步骤 (21)4 氧气转炉及相关设备设计 (25)4.1 炉型设计 (25)4.1.1炉型选择 (25)4.1.2 主要参数的确定 (25)4.2 炉衬设计 (27)4.3 炉底供气构件的设计 (28)4.4 转炉炉体金属构件设计 (28)4.5 倾动机构 (29)4.6 氧枪喷头设计 (29)4.6.1喷头设计 (29)4.6.2 氧枪枪身设计 (31)4.6.3氧枪升降和更换机构 (34)4.6.4 副枪设计 (34)4.6.5 副枪的功能和要求 (35)4.7 底部供气元件设计 (36)4.7.1底气种类 (36)4.7.2供气构件的选择 (36)4.7.3喷嘴数量及布置 (36)5 转炉车间烟气净化和回收 (37)5.1 烟气量的计算 (37)5.2 烟气净化系统类型的选择 (38)5.3 烟气净化系统主要设备的选择 (39)5.4 含尘污水处理 (40)6 转炉炼钢的生产制度 (41)6.1主要原材料的技术要求 (41)6.1.1金属料 (41)6.1.2造渣材料 (42)6.1.3氧化剂 (43)6.2装料制度 (44)6.3供氧制度 (45)6.3.1供氧制度主要工艺参数 (45)6.3.2氧枪操作 (45)6.4造渣制度 (46)6.4.1采用单双渣操作 (47)6.4.2各种渣料用量计算及加 (47)6.4.3炉渣调整 (48)6.5 温度制度 (49)6.6 终点控制与出钢 (50)6.7 脱氧合金化 (51)6.7.1脱氧合金化操作 (51)6.7.2 影响合金元素吸收率的因素 (52)6.8 精炼与连铸 (52)7 连铸车间的设计 (54)7.1 连铸机机型的选择 (54)7.2 连铸机的主要工艺参数 (54)7.2.1 钢包允许的最大浇注时间 (54)7.2.2 铸坯断面 (54)7.2.3 拉坯速度 (54)7.2.4 连铸机的流数 (56)7.2.5 铸坯的液相深度和冶金长度 (56)7.2.6 弧形半径 (56)7.3 连铸机生产能力的确定 (57)7.3.1 理论小时产量 (57)7.3.2 连铸机的平均年产量 (57)7.3.3 连铸机台数的确定 (57)7.4 结晶器的设计 (58)7.4.1 结晶器的长度 (58)7.4.2 结晶器断面尺寸 (58)7.4.3 结晶器铜壁厚度 (58)7.4.4 结晶器锥度 (58)7.4.5 结晶器拉坯阻力 (59)7.5 二次冷却装置 (59)7.6 拉坯矫直装置及引锭装置 (59)7.7 钢包 (60)7.8 中间包 (62)8 炼钢车间其它设备的选择与计算 (63)8.1渣罐车 (63)8.1.1渣罐车型号的选取 (63)8.1.2渣罐车数量的确定 (63)8.2 混铁车 (63)8.3 铁水罐 (64)8.4 废钢供应系统 (64)8.4.1转炉车间昼夜所需废钢量 (64)8.4.2废钢贮仓容积或堆放场地所需面积计算 (64)8.4.3废钢料斗容量及数量 (65)8.5 散装材料供应系统 (65)8.5.1 地面料仓容积和数量的确定 (65)8.5.2 上料方式的选择 (66)8.5.3 高位料仓容积和数量的确定 (66)8.6 钢包的其他工艺参数 (67)8.7起重机的选用 (68)9 转炉车间的组成、类型和主厂房尺寸 (69)9.1 车间组成 (69)9.2主厂房主要尺寸的确定 (69)9.2.1加料跨 (69)9.2.2炉子跨 (71)9.2.3 浇铸跨 (75)10 炼钢车间人员编制 (78)11 炼钢车间经济指标 (82)参考文献 (83)致谢 (84)1 绪论1.1 转炉冶炼原理简介[1]转炉炼钢是把氧气鼓入熔融的生铁里,使杂质硅、锰等氧化。
推荐-年产350万吨连铸坯的转炉炼钢车间工艺设计-毕业论文

西安建筑科技大学华清学院本科毕业设计(论文)任务书题目:年产350万吨连铸坯的转炉炼钢车间工艺设计院(系):专业:冶金工程学生姓名:学号:指导教师(签名):主管院长(主任)(签名):时间:2013 年 2月 25 日年产350万吨全连铸坯的转炉炼钢车间设计专业:冶金工程姓名:指导老师:设计总说明当前的炼钢工艺中,较为普遍的是以高炉铁水为原料的转炉炼钢工艺和以预还原球团矿或高质量的工业废钢为原料的电弧(炉)工艺。
本设计为具有代表性的氧气顶底复吹工艺,预计年生产能力为350万吨良坯钢。
车间设有公称容量为150吨的转炉两座,LF精炼炉2座、板坯连铸机1台和方坯连铸机1台。
转炉的冶炼周期38分钟,吹氧时间16分钟。
根据国内外转炉炼钢技术的发展趋势,结合设计任务书中普碳钢和普碳钢的品种需要,选择了LF炉外精炼设备,进行全连铸生产。
最终确定如下的的工艺流程:铁水预处理→转炉炼钢→LF精炼→连铸。
本次设计在对转炉物料平衡和热平衡计算的基础上,对炼钢车间的主要设备参数进行了设计、选型,完成了主体设备选择、炼钢工艺设计、主厂房工艺布置和设备布置。
编制说明书一份,绘制转炉炉型图、车间平面图、剖面图各一张,并完成题目为炼钢节能技术思路与对策的专题。
关键词:炼钢,顶底复吹,工艺流程,精炼,连铸,Design DescriptionAt present, there are two main steel-making processes: converter steelmaking process with blast furnace hot metal and steel scrap as the raw materials and the arc (furnace) process with pre-reduction pellets or high-quality industrial steel scrap as raw materials. In this paper, the representative process combined-blowing oxygen converter process with a scale of 3.7×106 continuous casting billet annual is designed.. In the workshop, main equipments including 2×150t converters and its auxiliary equipments with 2 LF refining furnaces, 2 sets of slab continuous casting machines and a set of billet continuous casting machine are designed. The Smelting period is set for 38 minuter in which the actual oxygen blowing time is only 16 minutes.Depending on the development trend of steel-making process and the quality requirement of carbon steel and pressure vessel steel, LF refining is selected to fulfill continuous casting. Finally,the following process flow is choosed: Pretreatment→Converter→LF→CC.On the base of the material and heat equilibrim calculation,the size of steel-making plant workshop span and device assign, personnel placement is made .A project instruction is redacted ,furnace size graphic, a ground plane and a sectional view of the workshop are also submitted. And finally, the monograph which is about non-metallic inclusions in steel and its damagement is also finished.Key words:steel making, combined-blown, process, refining, continuous casting目录1 绪论 (1)1.1 转炉冶炼原理简介 (1)1.2 氧气转炉炼钢的特点 (2)1.3设计原则和指导思想 (2)1.4 产品方案 (3)2 氧气转炉炼钢车间 (5)2.1 初始条件 (5)2.2 公称容量选择 (5)2.3 转炉座数的确定 (5)2.4根据生产规模和产品方案计算出年需钢水量。
年产200万吨转炉炼钢厂毕业设计说明书
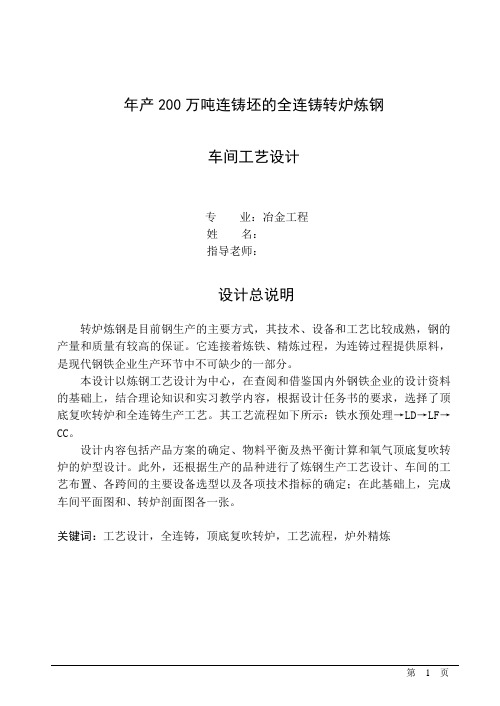
年产200万吨连铸坯的全连铸转炉炼钢车间工艺设计专业:冶金工程姓名:指导老师:设计总说明转炉炼钢是目前钢生产的主要方式,其技术、设备和工艺比较成熟,钢的产量和质量有较高的保证。
它连接着炼铁、精炼过程,为连铸过程提供原料,是现代钢铁企业生产环节中不可缺少的一部分。
本设计以炼钢工艺设计为中心,在查阅和借鉴国内外钢铁企业的设计资料的基础上,结合理论知识和实习教学内容,根据设计任务书的要求,选择了顶底复吹转炉和全连铸生产工艺。
其工艺流程如下所示:铁水预处理→LD→LF→CC。
设计内容包括产品方案的确定、物料平衡及热平衡计算和氧气顶底复吹转炉的炉型设计。
此外,还根据生产的品种进行了炼钢生产工艺设计、车间的工艺布置、各跨间的主要设备选型以及各项技术指标的确定;在此基础上,完成车间平面图和、转炉剖面图各一张。
关键词:工艺设计,全连铸,顶底复吹转炉,工艺流程,炉外精炼目录1 绪论 (5)2 炼钢厂总体设计方案 (6)2.1年生产能力的确定 (6)2.1.1 初始条件 (6)2.1.2转炉坐数及公称容量选择 (6)2.2炼钢生产流程 (7)2.3原材料方案 (7)2.3.1 铁水的供应与预处理 (7)2.3.2废钢的供应 (7)2.3.3 散状料供应 (7)2.3.4 铁合金料供应 (7)2.3.5 氧气的供应 (7)2.4车间布置方案 (8)3转炉炉型及氧枪设计 (8)3.1转炉炉型设计 (8)3.1.1 炉型及炉容比确定 (8)3.1.2 转炉参数设计 (8)3.1.3 支承结构 (11)3.1.4 倾动机构 (12)3.2氧枪喷头设计 (12)3.2.1氧枪喷头设计 (12)3.2.2 氧枪枪身设计 (13)3.3底部供气元件设计 (14)3.3.1 底气种类 (14)3.3.2 供气构件的选择 (14)3.3.3 喷嘴数量及布置 (14)4转炉炼钢的生产工艺设计 (15)4.1主要原材料的技术要求 (15)4.1.1 金属料 (15)4.1.2 造渣材料 (15)4.1.3 氧化剂 (16)4.2装料制度 (16)4.3供气制度 (17)4.3.1供氧制度 (17)4.3.2底部供气制度 (17)4.4造渣制度 (17)4.5温度控制 (19)4.6终点控制和出钢 (20)4.7脱氧合金化 (20)4.8精炼和连铸 (21)5车间主体设备选型 (22)5.1铁水供应设备 (22)5.2废钢工段 (23)5.3连铸机的设计及选型 (24)5.5.1 连铸机的主要工艺参数 (24)5.5.2连铸机生产能力的确定 (25)5.7中间包及其载运设备 (27)5.7.1中间包容量的确定 (27)5.7.2 中间包参数的确定 (28)5.7.3中间包车 (28)5.8结晶器的设计和选用 (29)5.9二次冷却装置 (30)5.10引锭装置 (30)5.11切割装置 (30)6炼钢车间生产工艺布置 (30)6.1主厂房的工艺布置 (30)6.2原料跨间的布置 (31)6.3转炉跨间的布置 (32)6.3.1炉子跨的高度布置 (32)6.3.2炉子跨的纵向布置 (35)6.3.3炉子跨的横向布置 (35)6.4出钢跨和精炼跨的布置 (36)6.5浇注跨间的布置 (36)7 转炉车间环境保护系统设计 (38)7.1转炉烟气净化系统设计 (38)7.1.1转炉烟气净化方法的选择 (38)7.1.2转炉烟气净化工艺设计 (38)7.1.3烟气净化系统的主要设备 (39)7.2资源综合利用 (39)7.2.1资源再利用 (39)7.2.2转炉固体废弃物的再利用 (39)7.2.3转炉气体废弃物的再利用 (40)8生产组织与人员编制 (40)9车间主要技术经济指标 (44)致谢 (44)1 绪论顶底复合吹炼法是在考虑顶吹和底吹方法的优点之上提出的。
年产500万吨合格铸坯炼钢厂转炉炼钢系统设计方案

年产500万吨合格铸坯炼钢厂转炉炼钢系统设计方案第一章文献综述1.1 国内外钢铁产业的发展情况钢铁产业是国民经济的重要支柱产业,涉及面广、产业关联度高、消费拉动大,在经济建设、社会发展、财政税收、国防建设以及稳定就业等方面发挥着重要作用。
为应对国际金融危机的影响,落实党中央、国务院保增长、扩内需、调结构的总体要求,确保钢铁产业平稳运行,加快结构调整,推动产业升级,特编制本规划,作为钢铁产业综合性应对措施的行动方案。
2008年下半年以来,随着国际金融危机的扩散和蔓延,我国钢铁产业受到严重冲击,出现了产需陡势下滑、价格急剧下跌、企业经营困难、全行业亏损的局面,钢铁产业稳定发展面临着前所未有的挑战。
应当看到,钢铁产业在经历了长期粗放型扩张后,必然要进行一次大的调整。
现阶段,我国城镇化、工业化任务依然繁重,内需潜力巨大,钢铁产业发展的基本面没有改变。
必须抓住机遇,制定实施钢铁产业结构调整和振兴规划,促进钢铁产业平稳运行、健康发展。
按照规划目标:力争在2009年遏制钢铁产业下滑势头,保持总体稳定。
据2010年初统计,2009年粗钢产量超过1000万吨的钢铁企业共有11家。
钢铁产业粗放发展方式得到明显转变,技术水平、创新能力再上新台阶,综合竞争力显著提高,支柱产业地位得到巩固和加强,步入良性发展的轨道。
(1)总量恢复到合理水平。
2009年我国粗钢产量5.6亿吨,同比下降8%;表观消费量维持在5.3亿吨左右,同比下降5%。
到2011年,粗钢产量控制在5亿吨左右,表观消费量4.5亿吨左右,工业增加值占GDP的比重维持在4%的水平。
(2)淘汰落后产能有新突破。
按期淘汰300立方米及以下高炉产能和20吨及以下转炉、电炉产能。
提高淘汰落后产能的标准,力争三年内再淘汰落后炼铁能力7200万吨、炼钢能力2500万吨。
(3)联合重组取得重大进展。
形成若干个具有较强自主创新能力和国际竞争力的特大型企业,国内排名前5位钢铁企业的产能占全国产能的比例达到45%以上,沿海沿江钢铁企业产能占全国产能的比例达到40%以上,产业布局明显优化,重点中心城市钢铁企业污染明显减少。
转炉炼钢工艺简介
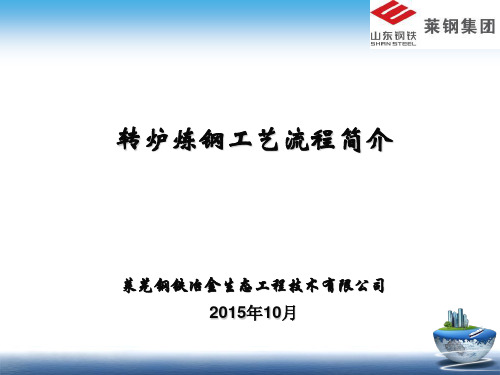
6、连铸
连续铸钢是将高温钢水连 续不断的浇到一个或几个用强 制水冷带有活底的铜模内(结
晶器),钢水在结晶器内凝固
成有一定厚度的坯壳后,连续 不断的从水冷结晶器被拉出,
在二次冷却区继续喷水冷却,
直至完全凝固为止。
2、混铁炉
混铁炉是高炉和转炉之 间的炼钢辅助设备,它主要 用于调节和均衡高炉和转炉 之间铁水供求的设备,保证 不间断地供给转炉需要的铁 水,铁水在混铁炉中储存和 混匀铁水成份及均匀温度, 它对转炉炼钢非常有利。
3、转炉
转炉炼钢是以铁水、 废钢、铁合金为主要原料, 不借助外加能源,靠铁液 本身的物理热和铁液组分 间化学反应产生热量而在 转炉中完成炼钢过程。 氧气顶吹和顶底复吹 转炉由于其生产速度快、 产量大,单炉产量高、成 本低、投资少,为目前使 用最普遍的炼钢设备。
转炉炼钢工艺流程简介
莱芜钢铁冶金生态工程技术有限公司 2015年10月
内容提纲
1 2 3
工艺流程 炼钢厂工艺装备概述 主要装备简介
一、工艺流程
渣 料 铁 合 金 LF 炉
铁 水 包
脱 硫 站
混 铁 炉
铁 水 包
转 炉
钢 包
连 铸
废 钢
吹 氩
二、炼钢厂工艺装备概述
以年产100万吨合格连铸坯炼钢系统为例,主要 产品为螺纹、普碳系列钢种的转炉炼钢厂工艺装备包 括: 由1套双工位的脱硫装置、 1座600吨混铁炉、1
4、钢包吹氩
钢包吹氩搅拌是最基本也是最普通的炉外处理工艺。 钢包吹氩搅拌的作用是: (1)均匀钢水温度。从炼钢炉流到钢包的钢水,在钢包内的温度分布是不均匀 的。钢包吹氩搅拌促使钢包钢水温度均匀,并且能使钢水向包衬的传热进入稳 定态,这样连铸过程钢水温度稳定均匀,有利于提高铸坯内部质量,使结晶器 内坯壳生长均匀,避免开浇水口冻钢断流。 (2)均匀钢水成分。出钢时在钢包内加入大量的铁合金,成分不均匀,吹氩搅 拌可使钢水成分均匀。在吹氩搅拌过程中可根据快速分析提供的钢水成分而进 行成分微调,以使钢的成分控制范围更窄,以确保钢材性能均匀。
年产100万吨连铸坯的电弧炉 炼钢车间工艺设计

目录1 电弧炉炼钢技术现状及发展 (1)1.1电弧炉炼钢发展概况 (1)1.2国内外电炉炼钢技术的发展趋势 (1)2 电弧炉炼钢车间的设计方案 (3)2.1电炉车间生产能力计算 (3)2.1.1电炉容量和台数的确定 (3)2.1.2 电炉车间生产技术指标 (3)2.2电炉车间设计方案 (4)2.2.1 电炉炼钢车间设计与建设的基础材料 (4)2.2.2 产品大纲 (4)2.2.3 电炉炼钢车间的组成 (4)2.2.4 电炉车间各跨的布置情况 (5)3 电弧炉炉型设计 (6)3.1电弧炉炉型 (6)3.1.1 炉缸 (6)3.1.2 熔化室 (7)3.1.3 电极分布 (8)3.1.4 工作门和出钢口 (8)3.1.5 炉衬厚度 (8)3.2电弧炉变压器容量选择 (9)3.3水冷炉壁与水冷炉盖 (9)3.3.1 水冷炉盖的设计 (9)3.3.2 水冷炉盖的安装 (10)3.4偏心底出钢的设计 (11)3.4.1 EBT电炉的炉壳 (11)3.4.2 EBT电炉的炉底 (12)3.4.3 出钢口 (12)3.4.4 机械装置 (13)3.4.5 偏心底出钢箱的设计 (13)3.5水冷挂渣炉壁的设计 (14)3.5.1 电弧炉炉壁的热流 (14)3.5.2 冷却水流量 (14)3.5.3 水冷炉壁水速的确定 (15)3.5.4 管径的确定 (15)3.5.5 平衡挂渣厚度 (15)3.5.6 综合传热系数 (16)3.5.7 临界热流量与最大热流量 (16)4 电弧炉炼钢过程中的物料平衡与热平衡计算 (17)4.1物料平衡计算 (17)4.1.1熔化期计算 (19)4.1.2 氧化期计算 (23)4.2热平衡的计算 (27)4.2.1 计算热收入Qs 。
(27)4.2.2 计算热支出Qz 。
(29)5 电弧炉炼钢车间工艺设计 (33)5.1.1 废钢 (33)5.1.2 辅助料 (33)5.2电弧炉冶炼工艺 (34)5.3精整工艺 (35)5.4连铸操作工艺 (36)6 电弧炉炼钢车间工艺布置 (38)6.1原料跨 (38)6.1.1 原料跨的宽度 (39)6.1.2 原料跨的烘烤间 (39)6.1.3 原料跨总长度确定 (40)6.2炉子跨整体布置 (40)6.2.1 炉子跨工作平台高度 (40)6.2.3 炉子的变压器室和控制室 (40)6.2.4 电弧炉出渣和炉渣处理 (40)6.2.5 精炼炉的工艺布置 (40)6.2.6 炉子跨的长度、跨度、高度 (40)6.3连铸跨 (41)6.3.1 总体布置 (41)6.3.2 钢包回转台的布置 (41)6.3.3 连铸机操作平台的高度、长度、宽度 (41)6.3.4 连铸机总高和本跨吊车轨面标高 (42)6.3.5 连铸机总长度 (42)6.3.6 其它布置 (43)6.4精整跨 (43)7 车间主要设备的选择和配置 (45)7.1电弧炉主体设备选择 (45)7.1.1 校核年产量 (45)7.1.2 电极 (45)7.2精炼炉设备选择 (45)7.2.1 LF钢包炉的参数确定 (45)7.2.2 LF钢包炉的工艺确定 (46)7.3连铸设备选择 (46)7.3.1 钢包允许的最大浇注时间 (46)7.3.2 铸坯断面 (47)7.3.3 拉坯速度 (47)7.3.4 连铸机的流数 (48)7.3.5 铸坯的液相深度和冶金长度 (48)7.3.6 弧型半径 (49)7.4连铸机的生产能力的确定 (49)7.4.1 连铸浇注周期的计算 (49)7.4.2 连铸机作业率 (50)7.4.3 连铸坯收得率 (50)7.4.4 连铸机生产能力的计算 (51)7.4.5 最高日浇注炉数 (51)7.4.6 最高日产量 (52)7.5中间包及其运载设备 (52)7.5.1 中间包的形状和构造 (52)7.5.2 中间包的主要工艺参数 (52)7.6结晶器及其振动装置 (53)7.6.1 结晶器的性能要求及其结构要求 (53)7.6.2 结晶器主要参数选择 (53)7.6.3 结晶器的振动装置 (55)7.7二次冷却装置 (55)7.7.1 二冷装置的基本结构 (55)7.7.2 二次冷却水冷喷嘴的布置 (55)7.7.3 二次冷却水量的计算 (55)7.8拉矫装置及引锭装置 (56)7.9铸坯切割装置 (56)7.10盛钢桶的选择 (56)7.10.1 型号选择 (56)7.10.2 容纳钢水量 (56)7.10.3 盛钢桶内渣量 (57)7.10.4 盛钢桶容积 (57)7.10.5 盛钢桶壁砖衬厚度 (57)7.10.6 盛钢桶外壳 (57)7.10.7 盛钢桶的质量 (58)7.10.8 钢包需用量 (58)7.11渣罐及渣罐车的选择 (59)7.11.1 车间所需的渣罐数量 (59)7.11.2 车间所需渣罐车数量 (59)7.12起重机和电动平车的选择 (59)7.13其它辅助设备的选择 (60)8.1技术经济指标 (61)8.2车间人员编制 (61)9参考文献 (64)10 专题........................................... 错误!未定义书签。
年产500万吨合格铸坯炼钢厂转炉炼钢系统设计方案

年产500万吨合格铸坯炼钢厂转炉炼钢系统设计方案第一章文献综述1.1 国内外钢铁产业的发展情况钢铁产业是国民经济的重要支柱产业,涉及面广、产业关联度高、消费拉动大,在经济建设、社会发展、财政税收、国防建设以及稳定就业等方面发挥着重要作用。
为应对国际金融危机的影响,落实党中央、国务院保增长、扩内需、调结构的总体要求,确保钢铁产业平稳运行,加快结构调整,推动产业升级,特编制本规划,作为钢铁产业综合性应对措施的行动方案。
2008年下半年以来,随着国际金融危机的扩散和蔓延,我国钢铁产业受到严重冲击,出现了产需陡势下滑、价格急剧下跌、企业经营困难、全行业亏损的局面,钢铁产业稳定发展面临着前所未有的挑战。
应当看到,钢铁产业在经历了长期粗放型扩张后,必然要进行一次大的调整。
现阶段,我国城镇化、工业化任务依然繁重,内需潜力巨大,钢铁产业发展的基本面没有改变。
必须抓住机遇,制定实施钢铁产业结构调整和振兴规划,促进钢铁产业平稳运行、健康发展。
按照规划目标:力争在2009年遏制钢铁产业下滑势头,保持总体稳定。
据2010年初统计,2009年粗钢产量超过1000万吨的钢铁企业共有11家。
钢铁产业粗放发展方式得到明显转变,技术水平、创新能力再上新台阶,综合竞争力显著提高,支柱产业地位得到巩固和加强,步入良性发展的轨道。
(1)总量恢复到合理水平。
2009年我国粗钢产量5.6亿吨,同比下降8%;表观消费量维持在5.3亿吨左右,同比下降5%。
到2011年,粗钢产量控制在5亿吨左右,表观消费量4.5亿吨左右,工业增加值占GDP的比重维持在4%的水平。
(2)淘汰落后产能有新突破。
按期淘汰300立方米及以下高炉产能和20吨及以下转炉、电炉产能。
提高淘汰落后产能的标准,力争三年内再淘汰落后炼铁能力7200万吨、炼钢能力2500万吨。
(3)联合重组取得重大进展。
形成若干个具有较强自主创新能力和国际竞争力的特大型企业,国内排名前5位钢铁企业的产能占全国产能的比例达到45%以上,沿海沿江钢铁企业产能占全国产能的比例达到40%以上,产业布局明显优化,重点中心城市钢铁企业污染明显减少。
转炉炼钢车间
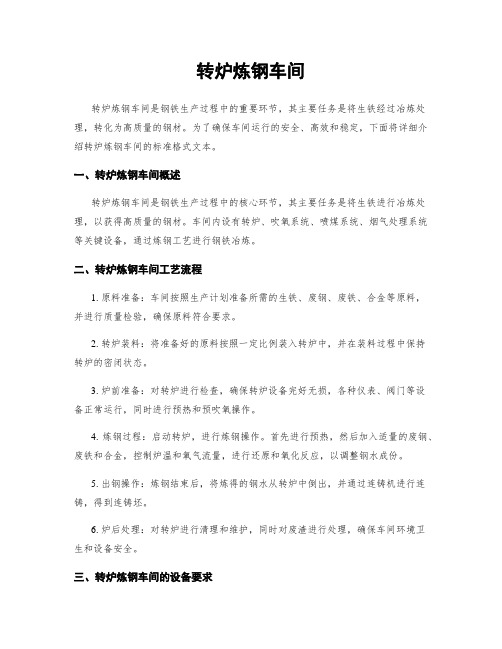
转炉炼钢车间转炉炼钢车间是钢铁生产过程中的重要环节,其主要任务是将生铁经过冶炼处理,转化为高质量的钢材。
为了确保车间运行的安全、高效和稳定,下面将详细介绍转炉炼钢车间的标准格式文本。
一、转炉炼钢车间概述转炉炼钢车间是钢铁生产过程中的核心环节,其主要任务是将生铁进行冶炼处理,以获得高质量的钢材。
车间内设有转炉、吹氧系统、喷煤系统、烟气处理系统等关键设备,通过炼钢工艺进行钢铁冶炼。
二、转炉炼钢车间工艺流程1. 原料准备:车间按照生产计划准备所需的生铁、废钢、废铁、合金等原料,并进行质量检验,确保原料符合要求。
2. 转炉装料:将准备好的原料按照一定比例装入转炉中,并在装料过程中保持转炉的密闭状态。
3. 炉前准备:对转炉进行检查,确保转炉设备完好无损,各种仪表、阀门等设备正常运行,同时进行预热和预吹氧操作。
4. 炼钢过程:启动转炉,进行炼钢操作。
首先进行预热,然后加入适量的废钢、废铁和合金,控制炉温和氧气流量,进行还原和氧化反应,以调整钢水成份。
5. 出钢操作:炼钢结束后,将炼得的钢水从转炉中倒出,并通过连铸机进行连铸,得到连铸坯。
6. 炉后处理:对转炉进行清理和维护,同时对废渣进行处理,确保车间环境卫生和设备安全。
三、转炉炼钢车间的设备要求1. 转炉:车间内设有转炉,转炉要求具备一定的容量和冶炼能力,同时要求设备结构坚固、密闭性好,能够承受高温和高压的工作环境。
2. 吹氧系统:车间内设有吹氧系统,用于向转炉中注入氧气,以促进燃烧和还原反应,提高炼钢效果。
3. 喷煤系统:车间内设有喷煤系统,用于向转炉中喷入煤粉,提供燃料和还原剂,以维持炉内的高温和还原条件。
4. 烟气处理系统:车间内设有烟气处理系统,用于处理转炉炼钢过程中产生的烟尘和废气,以达到环保要求。
5. 电气控制系统:车间内设有完善的电气控制系统,用于控制转炉和其他设备的运行,实现自动化生产。
四、转炉炼钢车间的安全要求1. 安全设施:车间内设有灭火器、消防栓、疏散通道等安全设施,以应对突发火灾等紧急情况。
- 1、下载文档前请自行甄别文档内容的完整性,平台不提供额外的编辑、内容补充、找答案等附加服务。
- 2、"仅部分预览"的文档,不可在线预览部分如存在完整性等问题,可反馈申请退款(可完整预览的文档不适用该条件!)。
- 3、如文档侵犯您的权益,请联系客服反馈,我们会尽快为您处理(人工客服工作时间:9:00-18:30)。
专业编制可行性研究报告了解更多详情..咨询公司网址年产960万吨连铸坯的全连铸转炉炼钢车间工艺设计摘要:本说明书在实习和参考文献的基础上,对所学知识进行综合利用。
讲述了设计一转炉车间的方法和步骤,说明书中对车间主要系统例如铁水供应系统,废钢供应系统,散装料供应系统,铁合金供应系统,除尘系统等进行了充分论证和比较确定出一套最佳设计方案。
并确定了车间的工艺布置,对跨数及相对位置进行设计,简述了其工艺流程,并在此基础上进行设备计算,包括转炉炉型计算,转炉炉衬计算及金属构件计算,氧枪设计,净化系统设备计算,然后进行车间计算和所用设备的规格和数量的设计,在此基础上进行车间尺寸计算,确定各层平台标高。
最后对转炉车间设计得环境和安全要求进行说明。
为了更加详细说明转炉车间设计中的一些工艺及设备结构,本设计穿插了图形,为能够明确、直观的介绍了转炉炼钢车间的工艺布置。
关键词:炼钢,复吹转炉,连铸,方坯,板坯,物料平衡,热平衡,炉型设计专业编制可行性研究报告了解更多详情..咨询公司网址目录1 文献综述 (1)1.1国外炼钢技术的发展 (1)1.2钢铁工业在国民经济中的地位和作用 (1)1.3现代转炉炼钢工艺流程 (2)1.4 我国氧气转炉炼钢技术展望 (2)1.4.1 转炉大型化和流程优化 (3)1.4.2 转炉高效化 (3)1.4.3 钢水洁净化 (3)1.4.4 控制模型化 (3)1.4.5 资源综合利用化 (4)1.5 现代转炉炼钢技术存在的问题 (4)2 转炉炼钢厂设计方案 (5)2.1 转炉车间组成 (5)2.2 转炉座数、容量和车间生产能力的确定 (5)2.2.1 转炉座数 (5)2.2.2 车间生产能力的确定 (5)2.3 主要钢种的选择 (6)2.4 工艺流程 (7)2.5 原料方案 (7)2.5.1 铁水的供应 (7)2.5.2 废钢的供应 (7)2.5.3 散装料的供应 (8)2.5.4 铁合金的供应 (8)2.6 主厂房工艺布置 (8)2.6.1 原料跨的布置 (8)2.6.2 炉子跨的布置 (9)2.6.3 精炼跨的布置 (9)专业编制可行性研究报告了解更多详情..咨询公司网址3.1 物料平衡 (10)3.1.1计算所需原始数据 (10)3.1.2物料平衡基本项目 (11)3.1.3计算步骤 (11)3.2 热平衡计算 (19)3.2.1计算所需原始数据 (19)3.2.2计算步骤 (20)4 顶底复吹转炉炉型设计 (24)4.1 炉型选择 (24)4.2 原始条件 (24)4.3 主要参数的确定 (24)4.4 炉衬各层填充材料选择 (28)5 生产工艺设计 (29)5.1炼钢原料 (29)5.1.1铁水 (29)5.1.2废钢 (29)5.1.3铁合金 (29)5.1.4石灰 (29)5.1.5萤石 (30)5.1.6生白云石 (30)5.1.7其他 (30)5.2装料制度 (30)5.3供氧制度 (30)5.3.1转炉炉膛内氧气射流的特性 (30)5.3.2氧气射流对转炉熔池的作用 (31)5.3.3顶吹氧气转炉的氧枪操作 (31)5.4造渣制度 (31)5.4.1炉渣碱度的控制与石灰加入量的确定 (31)5.4.2影响石灰熔解速度的因素 (32)5.4.3炉渣粘度的控制 (32)5.4.4炉渣氧化性的控制 (33)5.4.5泡沫渣及其控制 (33)5.4.6放渣及留渣操作 (34)5.5温度制度 (34)5.5.1出钢温度的确定 (34)5.5.2冷却剂及其加入量的确定 (35)5.6终点控制和出钢 (36)专业编制可行性研究报告了解更多详情..咨询公司网址5.7.1顶吹氧气转炉炼钢的脱氧方法 (36)5.7.2合金化的一般原理 (37)6 转炉炉体金属构件设计 (38)6.1炉壳设计 (38)6.2支撑装置设计 (38)6.3倾动机构的设计 (39)7 氧气转炉供氧系统设计 (40)7.1氧气的供应 (40)7.1.1转炉炼钢车间需氧量计算 (40)7.1.2制氧机能力的选择 (40)7.2氧枪设计 (41)7.2.1喷头类型与选择 (41)7.2.2喷头设计 (41)7.3氧枪枪身设计 (42)7.3.1枪身各层尺寸的确定 (42)7.3.2氧枪长度的确定 (44)7.4转炉底部供气构件设计 (44)7.4.1底气种类 (44)7.4.2底气用量 (44)7.4.3供气构件 (44)7.4.4底吹元件布置 (44)8 转炉车间烟气净化与回收 (45)8.1转炉烟气与烟尘 (45)8.1.1烟气的特征 (45)8.1.2烟尘的特征 (45)8.2烟气净化方案选择 (45)8.2.1炉口附近烟气处理方法 (45)8.2.2转炉烟气净化方法 (46)8.3烟气净化系统 (46)8.4烟气净化回收系统主要设备 (46)8.4.1烟罩 (46)8.4.2静电除尘器 (47)8.4.3煤气柜 (47)车间主要设备的选择 (48)9.1原料跨 (48)9.1.1混铁车的设计 (48)9.1.2废钢料斗的计算 (49)专业编制可行性研究报告了解更多详情..咨询公司网址9.2.1钢包 (49)9.2.2渣罐数量的确定 (50)9.3精炼跨 (50)9.4连铸跨 (51)9.4.1板坯的生产:(尺寸为170mm×1500mm) (52)9.4.2方坯的生产:(尺寸为150mm×150mm) (54)9.4.3其它工艺参数的确定 (55)9.4.4中间包主要工艺参数的确定 (55)9.4.5结晶器的有关参数 (56)9.4.6车间起重机的选择 (56)10 主厂房工艺布置 (58)10.1 原料跨间的布置 (58)10.2 转炉跨间的布置 (60)10.2.1炉子跨的布置 (60)10.2.2转炉跨各平台的确定 (62)10.3 连铸设备的布置 (65)11 总劳动定员表 (67)1 炼钢工序 (67)2 连铸工序 (68)3 燃气 (69)4 给排水 (70)5 热力 (70)6 通风 (70)7 电气 (70)8 精炼工序 (71)9 机修 (71)10 检化室 (71)12 主要技术经济指标 (72)致谢 (73)专业编制可行性研究报告了解更多详情..咨询公司网址1 文献综述1.1国外炼钢技术的发展世界近代炼钢工业首先诞生于欧洲,机器的大量发明和广泛应用,是炼钢成为最基本的工业材料,对钢铁的数量和质量的需求越来越高。
首先公布转炉炼钢法的是英国发明家亨利·贝塞麦,1965年,亨利·贝塞麦在英国科学协会发表演讲,宣布其发明了底吹酸性空气转炉炼钢法,也因此此法生产率高、成本低的炼钢方法,成为冶金史上的一大创举,从此开创了大规模炼钢的新时代。
回顾氧气转炉炼钢的发展,可分为以下三个时期。
(1)转炉大型化时期(1950~1970):以转炉大型化技术为核心,逐步完善了转炉炼钢工艺和设备。
先后开发出大型化转炉设计技术、OG法除尘与煤气回收技术、计算机静态与副枪动态控制技术、镁碳砖综合砌筑与喷补挂渣等护炉工艺技术。
(2)转炉复合吹炼时期(1970~1990):这一时期,由于连铸技术的迅速发展,出现了全连铸的炼钢车间。
对转炉炼钢的稳定性和终点控制的准确性提出了更高的要求。
为了改善转炉吹炼后期钢-渣反应远离平衡,实现稳定吹炼的目标,综合顶吹、底吹转炉的优点,研究开发出各种顶低复合吹炼工艺技术,在世界上迅速推广。
(3)转炉综合优化时期(1990年以后):在这一时期,由于社会对纯净钢的生产需求日益增加。
迫切需要建立起一种全新的、能大规模廉价生产纯净钢的生产体制。
围绕纯净钢生产,研究开发出铁水“三脱”预处理、高效转炉生产、全自动吹炼控制与溅渣护炉等重大新工艺技术。
降低了生产成本、大幅提高了生产效率。
1.2钢铁工业在国民经济中的地位和作用钢铁工业是国民经济的支柱产业,是国民经济中的主导产业。
而钢铁材料是用途最广泛的金属材料,人类使用的金属中,钢铁占90%以上。
人们生活离不开钢铁,人们从事生产或其他活动所用的工具和设施也都要使用钢铁材料。
钢铁产量往往是衡量一个国家工业化水平和生产能力的重要标志,钢铁的质量和品种对国民经济的其他工业部门产品的质量,都有着极大的影响。
世界经济发展到今天,钢铁作为最重要的基础材料之一的地位依然未受到专业编制可行性研究报告了解更多详情..咨询公司网址 材料的进步而消弱。
纵观世界主要发达国家的经济发展史,不难看出钢铁材料工业的发展在美国、前苏联、日本、英国、德国、法国等国家的经济发展中都起到了决定性作用。
这些国家和地区钢铁工业的迅速发展和壮大对于推动其汽车、造船、机械、电器等工业的发展和经济的腾飞都发挥了至关重要的作用。
美国钢铁工业曾在20世纪70-80年代遭到来自日本为主的国外进口材料的冲击而受到重创,钢铁产品生产能力急剧下降,但经过十几年的改造和重建,终于在20世纪90年代中期恢复到其原有的钢铁生产规模,为其维持世界强国地位继续发挥着重要作用。
由此可见钢铁工业在国民经济的重要作用,并且钢铁工业在整个国家的发展中都起着举足轻重的作用。
1.3现代转炉炼钢工艺流程现在钢铁联合企业是一个庞大而复杂的综合生产部门。
在这个钢铁联合企业中,钢铁材料的生产包括采矿、选矿、烧结(球团)、焦化、炼铁、炼钢和各种轧钢等过程。
由于各种钢材质量主要决定于炼钢工艺过程和设备,所以炼钢成为钢铁工业生产流程中的中心环节。
目前主要的炼钢方式是转炉炼钢,我国现在转炉钢占总钢产量的比例已经超过80%,并接近90%。
过去钢铁冶炼的工艺流程基本是铁水→炼钢炉(转炉、电炉、平炉)→浇铸(模铸、连铸)→轧钢的模式,这样的模式由于缺少铁水的预处理、炉外精炼工艺,只能冶炼普通钢种,难以冶炼优质特种高性能钢材,平炉由于其炉渣碱度低,脱磷、脱硫效果差,限制了钢材质量的提高,随着工业和科学技术的发展,对钢材质量和性能提出了更高的要求,迫使人们开发冶炼更多品种的钢材,从而推动了炼钢技术的不断发展。
转炉冶炼采用铁水预处理、炉外精炼工艺后,钢的质量大大提高,转炉钢品种增加,转炉不仅能冶炼普通钢种,而且能冶炼高级优质钢种,甚至能冶炼包括不锈钢在内的特种钢,这为转炉炼钢的发展提供了广阔的空间。
传统的钢水浇铸一直以模铸为主,不仅生产效率低、工人劳动强度大、车间环境恶劣,而且金属损失大、回收率低、难以浇铸大型钢锭。
采用连铸后,情况大为改观,生产效率和金属回收率大为提高,工人劳动强度降低,实现了浇铸过程的完全自动化,近十年中炼钢连铸比不断提高,许多大型钢铁企业均已实现了全连铸。
高炉→铁水预处理→转炉顶低复合吹炼→炉外精炼→连铸连轧,已成为大型现代化钢铁企业钢铁生产模式。
而高炉→铁水预处理→转炉顶低复合吹炼→RH真空精炼→连铸连轧→铸坯热送→直接轧制,则是现在转炉炼钢生产的最佳工艺流程。