P1111生产不良报告
生产线质量问题报告
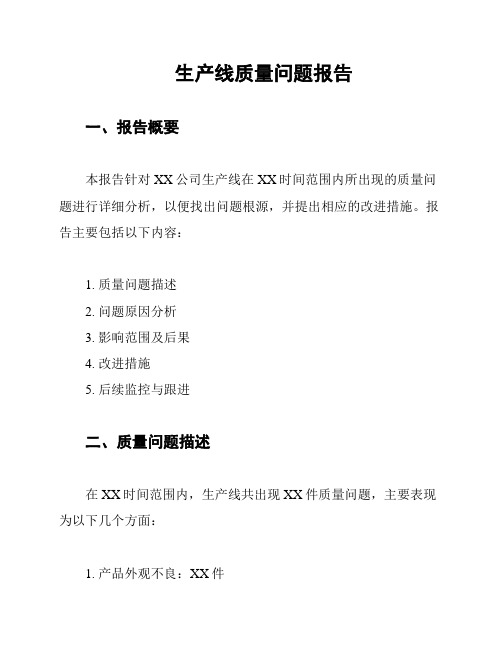
生产线质量问题报告一、报告概要本报告针对XX公司生产线在XX时间范围内所出现的质量问题进行详细分析,以便找出问题根源,并提出相应的改进措施。
报告主要包括以下内容:1. 质量问题描述2. 问题原因分析3. 影响范围及后果4. 改进措施5. 后续监控与跟进二、质量问题描述在XX时间范围内,生产线共出现XX件质量问题,主要表现为以下几个方面:1. 产品外观不良:XX件2. 功能异常:XX件3. 结构故障:XX件4. 性能不稳定:XX件三、问题原因分析针对上述质量问题,经过调查与分析,主要原因如下:1. 原材料质量问题:XX件2. 生产设备故障:XX件3. 操作人员技能不足:XX件4. 生产流程不合理:XX件5. 质量管理不到位:XX件四、影响范围及后果本次质量问题对公司的影响如下:1. 经济损失:XX元2. 客户满意度下降:XX%3. 品牌形象受损:XX%4. 市场份额下降:XX%五、改进措施针对问题原因,公司采取以下改进措施:1. 优化原材料采购流程,加强原材料质量检测:XX项2. 维修生产设备,确保设备正常运行:XX项3. 加强操作人员培训,提高技能水平:XX项4. 优化生产流程,提高生产效率:XX项5. 加强质量管理,严格执行质量制度:XX项六、后续监控与跟进为确保改进措施的有效实施,公司将继续加强以下监控与跟进工作:1. 定期检查原材料质量:XX次/月2. 每日检查生产设备运行状况:XX次/日3. 定期对操作人员进行技能培训与考核:XX次/月4. 跟踪生产流程执行情况:XX次/周5. 加强质量管理制度执行力度:XX次/月以上为生产线质量问题报告,请领导审阅,针对报告中存在的问题,我们将继续努力改进,提高产品质量,为公司创造更多价值。
生产质量管理异常报告

生产质量管理异常报告一、引言生产质量管理是企业运营的关键环节,直接关系到产品的质量和企业的声誉。
然而,在实际生产过程中,难免会出现各种质量异常情况。
本报告旨在对近期生产过程中出现的质量管理异常进行详细的分析和总结,以找出问题的根源,并提出相应的改进措施。
二、异常情况概述在最近的具体时间段内,我们的生产线上出现了以下几类质量异常情况:1、产品外观缺陷部分产品表面存在划痕、凹坑和色差等问题,严重影响了产品的外观质量。
经过调查,发现这主要是由于生产过程中操作不当,以及模具老化和维护不及时所致。
2、尺寸偏差一些产品的关键尺寸超出了设计公差范围,导致产品无法正常装配和使用。
经分析,尺寸偏差的原因主要是加工设备精度下降、工装夹具磨损以及操作人员未严格按照工艺要求进行操作。
3、性能不达标部分产品的性能指标未能达到相关标准和客户的要求,如强度、硬度、耐腐蚀性等。
深入研究发现,原材料质量不稳定、生产工艺参数控制不当以及检验环节存在漏洞是导致性能不达标问题的主要因素。
三、异常情况影响这些质量异常情况给企业带来了诸多不利影响,主要包括以下几个方面:1、客户满意度下降由于产品质量问题,客户对我们的信任度降低,部分客户甚至提出了退货和索赔的要求,这对企业的声誉和市场份额造成了严重的损害。
2、生产成本增加不合格产品的返工和报废导致了生产成本的大幅增加,同时也浪费了大量的人力、物力和时间资源。
3、生产进度延误质量异常问题的处理需要花费额外的时间和精力,导致生产进度受到延误,无法按时交付订单,影响了企业的交货信誉。
四、原因分析为了找出质量异常问题的根本原因,我们对生产过程中的各个环节进行了深入的调查和分析,具体情况如下:1、人员方面操作人员质量意识淡薄,对产品质量的重要性认识不足,在生产过程中未严格遵守操作规程和质量标准。
培训不到位,操作人员对新设备、新工艺的掌握程度不够,操作技能不熟练,导致生产过程中容易出现失误。
2、设备方面生产设备老化,精度下降,维护保养不及时,设备故障频繁发生,影响了产品的加工质量。
造成不良品分析报告

造成不良品分析报告1. 引言本报告旨在对公司生产中出现的不良品进行详细分析,并提供解决方案以减少不良品产生率,提高产品质量。
通过分析不良品的主要原因,我们能够更好地理解并控制生产过程中的问题,从而降低产品质量风险,提高客户满意度。
2. 背景公司一直致力于生产高质量的产品,但最近一段时间发现不良品产生率有所上升。
在此报告中,我们将重点分析不良品的主要原因,并提出一些建议和解决方案。
3. 不良品分析3.1 不良品定义我们首先需要明确不良品的定义。
在此报告中,不良品指的是生产过程中无法达到预期产品质量标准的产品。
3.2 不良品分类根据不良品的性质和原因,我们将不良品分为以下几个类别:1.外观缺陷:产品外观存在瑕疵、划痕、气泡等问题。
2.功能异常:产品在使用过程中出现缺陷,无法正常工作。
3.尺寸偏差:产品尺寸与设计要求不符合。
4.材料问题:产品使用的材料存在质量问题。
3.3 不良品原因分析通过对不良品的进一步分析,我们得出以下主要原因:1.工艺不稳定:生产过程中存在工艺参数不稳定的情况,导致产品质量波动较大。
2.操作不当:操作人员在生产过程中未按照标准操作规程进行操作,导致产品质量下降。
3.设备故障:生产设备存在故障或老化现象,导致产品质量无法保证。
4.材料质量问题:供应商提供的材料存在质量问题,影响了产品的质量。
5.质检失误:质检部门未能及时发现不良品,导致不良品流入市场。
3.4 解决方案为了降低不良品产生率,我们提出以下解决方案:1.工艺优化:通过优化生产工艺参数和流程,确保生产过程的稳定性和一致性,减少不良品的产生。
2.培训与培养操作人员:加强对操作人员的培训,提高其操作技能和质量意识,确保按照规程进行操作。
3.设备维护与更新:定期对生产设备进行维护保养,及时更换老化设备,确保设备正常运行,降低故障率。
4.严格供应商管理:加强对材料供应商的质量管理,确保材料的质量符合要求。
5.强化质检控制:加强对质检工作的监管和管理,提高质检员的质量意识和技术水平,确保不良品能够及时发现并进行处理。
产品不良原因分析报告模板

产品不良原因分析报告模板1. 背景产品不良是指产品在生产、运输、储存或使用过程中出现的质量问题,不仅会导致客户投诉和损失,还会影响企业声誉和市场竞争力。
因此,对产品不良进行及时、有效的原因分析至关重要。
2. 报告目的本报告旨在对产品不良原因进行系统分析,找出根本问题,为企业改进生产和质量管理提供参考依据,提升产品质量和客户满意度。
3. 分析方法通过对产品不良案例进行调查和分析,采用常用的质量管理工具和方法,如因果分析、故障模式与效果分析(FMEA)、5W1H分析等,结合生产过程和质量管理体系开展深入研究。
4. 分析报告详述4.1 不良现象描述描述发生不良的具体情况,包括不良类型、频次、影响范围等,对不良问题进行准确定义。
4.2 不良原因分析•产生原因:对所涉及的环节、流程、材料进行分析,确定不良的根本产生原因。
•影响因素:分析可能导致产品不良的各种因素,包括人、机、料、法、环境等,在不同尺度上进行详细考察。
•关键环节:确定影响产品质量的关键环节,寻找在这些环节上的不良原因,并提出改进措施。
4.3 改进建议•技术改进:对发现的技术问题提出改进方案,包括工艺优化、设备更新等。
•管理改进:对不良管理流程进行梳理,完善管理制度,加强对员工培训和监管。
•供应链管理:加强对原材料和零部件的质量管理,建立供应商质量评估体系。
5. 实施计划针对以上提出的改进建议,制定详细的实施计划和时间表,明确责任人及监督执行机制,确保改进措施的有效实施。
6. 结语产品不良原因分析是企业质量管理的基础工作,只有通过深入分析和不断改进,才能提高产品质量和客户满意度。
希望本报告能为企业提供有益的参考,引领企业不断提升管理水平,为提供更优质的产品和服务奠定基础。
不良品分析报告

不良品分析报告随着社会的发展,人们对产品的质量要求也越来越高。
然而,尽管企业在生产过程中投入了大量的时间和资源,不可避免地还是会出现不良品的情况。
针对不良品的存在,本文将进行一份分析报告,从不良品的原因、影响和解决方法三个方面进行探讨。
一、不良品的原因不良品产生的原因是多种多样的,其中包括工艺问题、设备故障、材料质量、人为失误等。
首先,工艺问题是导致不良品的主要原因之一。
在生产过程中,工艺步骤的操作不当或者流程设计不合理可能导致产品的质量问题。
其次,设备故障也是不良品产生的重要原因。
设备在长时间运行时可能出现损坏或故障,导致生产出的产品质量不合格。
再次,材料质量是影响产品质量的另一个关键因素。
材料的质量不过关可能导致产品的性能不稳定,从而产生不良品。
此外,人为失误也是不良品产生的重要原因之一。
工人在生产过程中粗心大意或者操作不规范可能引发产品质量问题。
二、不良品的影响不良品对企业和消费者都带来了一定的影响。
首先,不良品的存在会导致企业的声誉受损。
不良品一旦流入市场,可能会引发消费者的不满和投诉,进而影响企业的形象和口碑。
其次,不良品还会给企业带来经济损失。
企业需要承担产品的退换货、售后维修等费用,不仅浪费了大量的人力物力,还影响了企业的盈利能力。
此外,不良品对消费者也有一定的影响。
消费者购买到不良品后可能会对产品失去信心,并对企业产生怀疑,甚至会对整个行业产生负面影响。
三、不良品的解决方法针对不良品问题,企业可以采取一系列的解决方法,以确保产品质量的稳定和提升。
首先,企业应加强工艺管理,规范操作流程,确保每一个生产环节都符合标准要求。
其次,企业要注意设备的维护和保养,及时检查设备运行状态,减少设备故障对产品质量的影响。
此外,企业还应加强供应链管理,确保原材料的质量可靠。
通过与供应商建立长期合作关系,企业能够更好地控制供应链的质量。
最后,企业应加强对员工的培训和教育,提高员工的操作技能和质量意识,减少人为失误对产品质量的影响。
生产质量管理异常报告

生产质量管理异常报告一、背景随着市场竞争的日益激烈,产品质量已成为企业生存和发展的关键。
为了确保产品质量稳定,提高客户满意度,我们必须对生产过程中的质量管理异常情况进行及时、准确的报告和处理。
本次报告旨在对近期生产过程中出现的质量管理异常情况进行详细的分析和总结,并提出相应的改进措施。
二、异常情况概述1、原材料质量问题在最近一批原材料采购中,发现部分原材料的规格不符合要求,导致生产过程中出现产品尺寸偏差较大的情况。
经过检验,发现不合格原材料的比例达到了 5%,严重影响了生产进度和产品质量。
2、生产工艺执行不到位在生产过程中,部分操作人员未严格按照生产工艺要求进行操作,例如温度控制不当、加工时间不足等,导致产品的性能指标未能达到标准要求。
3、设备故障生产设备在运行过程中出现了多次故障,如模具磨损、传动部件损坏等,影响了生产的连续性和产品质量的稳定性。
4、检验环节疏漏在产品检验过程中,存在检验标准不明确、检验人员责任心不强等问题,导致一些不合格产品流入市场,给企业形象造成了不良影响。
三、异常情况原因分析1、原材料供应商管理不善对原材料供应商的评估和筛选不够严格,缺乏有效的监督和管理机制,导致供应商提供的原材料质量不稳定。
2、员工培训不足部分员工对生产工艺和质量要求的理解不够深入,操作技能不熟练,导致在生产过程中不能严格执行工艺要求。
3、设备维护保养不及时设备维护保养计划执行不到位,缺乏定期的检查和维修,导致设备故障频发。
4、检验管理体系不完善检验标准和流程不够清晰明确,检验人员的培训和考核机制不健全,导致检验环节存在漏洞。
四、异常情况影响评估1、经济损失由于原材料质量问题和产品不合格,导致了原材料的浪费和产品的返工、报废,给企业造成了直接的经济损失。
2、客户满意度下降不合格产品流入市场,影响了客户的使用体验,导致客户投诉增加,客户满意度下降,可能会影响企业的市场份额和长期发展。
3、企业声誉受损产品质量问题的曝光,对企业的声誉造成了负面影响,降低了企业在市场上的信誉度和竞争力。
生产异常事件报告范文

生产异常事件报告范文尊敬的领导:我在此向您汇报一起生产异常事件的情况,以便能够及时采取措施解决问题。
在过去的几天里,我们的生产线发生了一起异常情况,导致了生产计划的延误和产品质量的下降。
以下是详细的情况描述:事件发生在上周五的下午,当时我们正在生产一批新产品。
在生产过程中,我们的设备突然出现了故障,导致生产线停止运行。
经过工程师的检查,发现是供电系统出现了问题,导致设备无法正常运转。
由于供电系统故障,我们不得不停止生产线,等待维修人员的到来。
这期间,我们无法继续生产,导致了计划的延误。
此外,由于设备在停机期间无法正常运行,已经生产出来的产品也存在质量问题,需要重新进行检验和修复。
经过维修人员的紧急处理,供电系统在周末得到了修复。
然而,由于停机时间较长,我们无法在短时间内追赶上生产计划。
为了保证产品质量,我们决定对已经生产出来的产品进行全面检验,并重新进行必要的修复和调整。
尽管我们已经尽力处理这次生产异常事件,但仍然无法避免对公司造成的损失。
首先,由于延误了生产计划,我们可能无法按时交付客户订单,给公司声誉和利润带来了负面影响。
其次,重新检验和修复已经生产出来的产品,将增加额外的人力和物力成本。
为了避免类似的事件再次发生,我们已经采取了以下措施:首先,对供电系统进行了全面检修,确保其正常运行。
其次,加强了设备的维护和保养工作,确保其长期稳定运行。
同时,我们也对生产计划进行了优化,以应对突发事件的发生。
请您对此次事件给予关注,并指导我们采取进一步的措施来避免类似问题的再次发生。
我们将竭尽全力恢复生产计划,并确保产品质量的稳定和可靠。
谢谢您的关注与支持!此致。
生产异常分析报告模板范文

生产异常分析报告模板范文1. 引言本报告旨在分析公司生产中的异常情况,并提供相应的解决方案以改进生产流程。
异常情况对生产效率和产品质量产生负面影响,因此需要及时发现和解决问题,以保证顺利的生产运营。
2. 异常情况概述在过去一个月的生产过程中,我们发现了以下几种异常情况:2.1 原材料损耗率上升自前一个月以来,我们注意到原材料损耗率有明显增加。
在分析生产数据和进行现场调查后,我们发现主要原因是操作工人对生产设备的操作不熟悉导致的操作不当。
这导致了原材料的浪费和不必要的损耗。
2.2 生产设备故障频繁在过去一个月中,各个生产线的设备故障频繁发生。
经过检查,我们发现主要原因是设备维护保养工作不到位,导致设备使用寿命提前消耗。
此外,缺乏预防性维护和准时维修也是故障频繁发生的原因。
2.3 品质异常率升高品质异常率在过去一个月中有所上升。
通过对生产数据和产品抽样检验的分析,发现这主要是由于员工加工技术不熟练、操作不规范以及质量控制不严格所致。
这些因素导致了生产过程中质量不稳定和产品不合格率上升。
3. 异常分析与解决方案3.1 原材料损耗率上升的解决方案为了减少原材料损耗,我们建议采取以下措施:•提供操作工人培训计划,提高其对生产设备操作的技能和知识水平;•建立操作规程和工作指导书,明确生产过程中的操作要求和注意事项;•加强现场管理和监督,确保操作工人按照规定的操作要求进行操作;•设置原材料测量和控制系统,确保原材料用量准确,并避免浪费和不必要的损耗。
3.2 生产设备故障频繁的解决方案为了解决设备故障频繁发生的问题,我们建议采取以下措施:•制定设备维护保养计划,明确维护保养的内容和时间节点;•培训设备操作人员,提高其对设备故障排查和维修的能力;•定期进行设备巡检和检修,及时发现潜在问题并进行修复;•引入设备故障预测技术,通过数据分析和预测来预防设备故障的发生。
3.3 品质异常率升高的解决方案为了降低品质异常率,我们建议采取以下措施:•组织员工参加技术培训和技能提升课程,提高其加工技术和操作规范性;•加强质量控制和检验过程,建立完善的质量管理体系;•建立员工激励制度,鼓励员工对产品质量的关注和持续改进;•加强管理人员对生产过程的监督和指导,确保各环节符合质量要求。
生产运行异常总结汇报材料

生产运行异常总结汇报材料尊敬的领导、同事们:大家好!我是生产部门的XX,今天非常荣幸向大家汇报我们最近生产运行异常的情况。
接下来,我将详细介绍问题的具体情况、可能的原因以及我们拟定的解决方案。
一、问题描述在过去的一段时间里,我们生产过程中出现了一些异常情况。
首先,我们发现产品生产过程中的质量问题增多,导致了不少产品无法达到客户的要求。
其次,我们的生产线也遭遇了不少故障,导致生产效率下降以及交货时间延误。
最后,我们还意识到员工的工作积极性和团队凝聚力也有所下降。
二、可能的原因针对问题的分析,我们初步认为以下几个方面可能导致了这些异常情况的发生:1. 设备老化或者维护不及时,导致了生产线故障频繁发生;2. 工艺流程不合理或者操作规范不够严格,导致产品质量下降;3. 员工培训不足,导致出现错误操作或疏忽;4. 员工积极性和工作动力缺乏,导致工作效率下降。
三、解决方案为了解决上述问题,我们制定了一系列的解决方案,以期能够提升我们的生产效率和产品质量,同时提高员工的工作积极性和团队凝聚力。
具体如下:1. 设备维护与更新:建立设备维护计划,确保设备的正常运行。
同时,鼓励部门购置新设备以提高生产效率。
2. 工艺流程优化:对现有工艺流程进行评估和优化,确保每道工序都能正确、规范地执行。
加强工艺技术培训,提高员工工艺操作水平。
3.员工培训与激励:建立员工培训计划,加强员工技能的培养和提升,并定期组织技能竞赛活动,激发员工的工作热情和积极性。
4.团队建设与沟通:加强团队协作,通过定期部门会议、团队建设活动等方式,促进员工之间的交流和互动,增强团队凝聚力。
四、预期效果通过以上方案的实施,我们预期能够达到以下效果:1. 技术和设备方面,通过设备维护和更新,降低故障发生率,提高生产线稳定性和效率。
2. 工艺和质量方面,通过工艺流程优化和员工培训,提高产品质量水平,减少不合格品的产生。
3. 员工方面,通过培训与激励,提高员工技能和团队凝聚力,提高生产效率和员工积极性。
线束车间不良品处理报表

线束车间不良品处理报表摘要:一、引言二、线束车间不良品处理流程1.不良品分类2.不良品原因分析3.不良品处理方法三、不良品处理报表内容1.报表基本信息2.不良品数量统计3.不良品原因分析4.处理措施及效果四、不良品处理报表的作用1.提高生产质量2.降低生产成本3.优化生产流程五、结论正文:一、引言在我国的制造业中,线束车间的生产过程尤为重要。
然而,由于各种原因,不良品的出现是难以避免的。
为了提高生产质量、降低生产成本以及优化生产流程,对线束车间的不良品进行有效处理是至关重要的。
本文将重点介绍线束车间不良品处理报表的相关内容。
二、线束车间不良品处理流程1.不良品分类线束车间的不良品可以根据不同的标准进行分类,如:性能不良、外观不良、结构不良等。
2.不良品原因分析对于分类后的不良品,需要进行详细的原因分析。
这包括生产过程中的各种因素,如原材料、设备、操作人员等。
3.不良品处理方法针对不同原因的不良品,采取相应的处理措施。
如:修复、重新加工、报废等。
三、不良品处理报表内容1.报表基本信息不良品处理报表的基本信息包括:报表编号、报表日期、报表部门等。
2.不良品数量统计对各类不良品进行数量统计,以便了解不良品的情况。
3.不良品原因分析详细分析各类不良品产生的原因,为制定预防措施提供依据。
4.处理措施及效果记录不良品的处理措施及效果,为优化生产流程提供参考。
四、不良品处理报表的作用1.提高生产质量通过不良品处理报表,可以及时发现生产过程中的问题,从而采取措施提高生产质量。
2.降低生产成本对不良品进行有效处理,可以减少原材料的浪费,降低生产成本。
3.优化生产流程通过分析不良品产生的原因,可以找出生产流程中的瓶颈,进而优化生产流程。
五、结论线束车间不良品处理报表是生产质量管理的重要组成部分。
通过有效地利用不良品处理报表,可以提高生产质量、降低生产成本以及优化生产流程。
生产质量管理异常报告

生产质量管理异常报告一、背景在生产过程中,质量管理是确保产品质量和企业声誉的关键环节。
然而,近期我们在生产过程中发现了一系列的质量异常情况,这些异常不仅影响了产品的质量和交付,也给企业带来了一定的经济损失和声誉风险。
为了及时解决这些问题,提高生产质量管理水平,特编写此报告。
二、异常情况描述1、原材料质量问题在最近一批原材料采购中,发现部分原材料的规格和质量与合同要求不符。
例如,_____供应商提供的钢材强度未达到标准,导致在加工过程中出现断裂现象,影响了产品的整体性能。
2、生产工艺执行不严格在生产过程中,部分操作人员未严格按照既定的生产工艺进行操作。
如在焊接工序中,焊接电流和焊接时间未按照工艺要求进行调整,导致焊缝质量不稳定,存在气孔和夹渣等缺陷。
3、设备故障生产设备在运行过程中出现了多次故障,影响了生产的正常进行。
例如,_____生产线的数控机床出现了精度偏差,导致加工出来的零件尺寸不符合要求,需要进行返工处理。
4、检验环节疏漏在产品检验过程中,存在检验标准不明确、检验方法不科学以及检验人员责任心不强等问题。
例如,对于一些外观缺陷的判定标准不够清晰,导致部分不合格产品流入了下一道工序。
三、异常原因分析1、供应商管理不善对原材料供应商的评估和监管不到位,未能及时发现供应商在原材料质量控制方面存在的问题,也没有采取有效的措施督促供应商改进。
2、员工培训不足操作人员对生产工艺和质量要求的理解不够深入,企业在员工培训方面投入不足,导致员工在实际操作中不能严格按照工艺要求进行生产。
3、设备维护保养不到位没有建立完善的设备维护保养制度,设备的日常巡检和定期维护工作没有落实到位,导致设备故障频发。
4、检验制度不完善检验标准和检验流程不够完善,检验人员的业务能力和责任心有待提高,缺乏有效的质量监督和考核机制。
四、异常影响评估1、产品质量下降由于上述质量异常情况的存在,导致部分产品出现了质量问题,如性能不稳定、外观缺陷等,降低了产品的整体质量水平。
不良品纠正和预防措施报告范文

不良品纠正和预防措施报告范文一、不良品情况概述。
1.1 不良品的发现。
咱在生产过程或者产品检验的时候啊,就突然发现了不良品。
这不良品就像一颗老鼠屎坏了一锅粥啊,好好的产品里突然冒出来这些个不合格的,真让人头疼。
比如说啊,有次在生产电子产品的时候,发现有一批产品的屏幕显示有问题,不是这儿闪屏就是那儿有坏点,这可咋整呢?1.2 不良品带来的影响。
这不良品的影响可不小呢。
首先就是对咱公司的声誉有损害啊,就像一个人脸上抹黑似的。
客户要是收到了不良品,那不得觉得咱们公司不靠谱嘛。
再者呢,这也造成了成本的增加,那些个不良品的材料啊、人工啊,都打了水漂,就像把钱扔到大海里一样,连个响都听不到。
二、纠正措施。
2.1 对不良品的处理。
咱得赶紧对不良品进行处理啊。
对于那些还能挽救的,就像医生治病救人一样,能修的就修。
像刚刚说的电子产品屏幕有问题,要是小毛病,就安排技术人员去调整修复。
要是那些实在没救的,就只能报废处理了,可不能让这些不良品混到好产品里去,那可就是自欺欺人了。
2.2 查找产生不良品的直接原因。
这得好好查一查为啥会产生这些不良品呢。
咱不能稀里糊涂的啊。
就拿那屏幕显示有问题来说,是不是原材料本身就有毛病呢?还是在生产过程中,设备的参数设置错了呢?经过一番调查啊,发现原来是设备的某个零件老化了,导致屏幕显示参数不稳定,才出现了这些问题。
这就好比车胎破了,车肯定跑不稳当了。
2.3 改进措施的实施。
知道原因了就得赶紧改啊。
把那个老化的设备零件换了,就像给病人换了个新器官一样。
然后呢,还得对设备进行全面的检查和维护,不能让其他零件也出问题。
而且啊,在生产过程中要增加检验的频次,就像站岗的士兵一样,多检查几遍,这样才能把不良品扼杀在摇篮里。
三、预防措施。
3.1 建立预防机制。
咱不能总是等不良品出现了才去处理啊,得建立一个预防机制。
这就好比盖房子要打地基一样,基础得打好。
比如说,建立原材料的严格检验标准,不能让不合格的原材料进入生产线。
生产产品出现问题报告
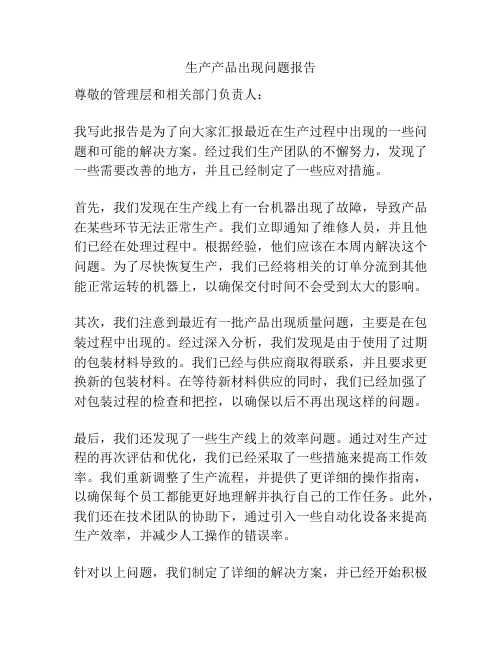
生产产品出现问题报告尊敬的管理层和相关部门负责人:我写此报告是为了向大家汇报最近在生产过程中出现的一些问题和可能的解决方案。
经过我们生产团队的不懈努力,发现了一些需要改善的地方,并且已经制定了一些应对措施。
首先,我们发现在生产线上有一台机器出现了故障,导致产品在某些环节无法正常生产。
我们立即通知了维修人员,并且他们已经在处理过程中。
根据经验,他们应该在本周内解决这个问题。
为了尽快恢复生产,我们已经将相关的订单分流到其他能正常运转的机器上,以确保交付时间不会受到太大的影响。
其次,我们注意到最近有一批产品出现质量问题,主要是在包装过程中出现的。
经过深入分析,我们发现是由于使用了过期的包装材料导致的。
我们已经与供应商取得联系,并且要求更换新的包装材料。
在等待新材料供应的同时,我们已经加强了对包装过程的检查和把控,以确保以后不再出现这样的问题。
最后,我们还发现了一些生产线上的效率问题。
通过对生产过程的再次评估和优化,我们已经采取了一些措施来提高工作效率。
我们重新调整了生产流程,并提供了更详细的操作指南,以确保每个员工都能更好地理解并执行自己的工作任务。
此外,我们还在技术团队的协助下,通过引入一些自动化设备来提高生产效率,并减少人工操作的错误率。
针对以上问题,我们制定了详细的解决方案,并已经开始积极实施。
我们相信通过这些措施的改进,我们能够更好地应对生产中出现的问题,并不断提高产品的质量和效率。
我们将密切关注并监控这些改进措施的实施情况,并及时向大家汇报进展情况。
同时,我们也欢迎各位管理层和部门负责人提出任何改进和建议,以更好地解决生产中的问题。
最后,我们衷心感谢大家一直以来对我们工作的支持和关注。
我们相信只有通过共同努力和密切合作,我们才能不断提升产品的质量和效率。
谢谢!此致敬礼。
关于不良产品的处理报告_概述说明

关于不良产品的处理报告概述说明1. 引言1.1 概述不良产品是指在制造、生产或流通环节中存在质量问题,无法满足预期用途或标准要求的产品。
这些产品可能会对消费者的健康、安全和权益造成潜在危害。
因此,对不良产品进行及时有效的处理至关重要,以保护消费者的权益和维护市场秩序。
本篇文章旨在探讨不良产品的处理方法与政策,并提出改进与加强处理措施的建议。
首先,我们将介绍不良产品的定义和分类,以便更好地理解其特点和影响。
接着,我们将了解相关的法律法规和政策支持,以及政府部门对于不良产品处理所采取的监管措施。
此外,我们还将阐述消费者权益保护机制和渠道。
随后,文章将详细介绍不良产品处理的步骤和流程。
包括如何发现不良产品并进行报告,如何鉴定其问题并评估风险等级,以及处理措施如何选择,例如召回、修复或销毁等方案。
最后,在结论与建议部分中,我们将总结目前不良产品处理的现状,并分析存在的问题。
同时,我们将提出改进和加强不良产品处理的建议,以期在未来能够更好地管理和监管不良产品。
通过本文的阐述,我们希望能够对不良产品处理有一个深入的了解,并为相关政府部门、企业和消费者提供借鉴和参考,以共同维护市场秩序、保障消费者权益。
2. 不良产品的定义和分类:2.1 不良产品的概念:不良产品是指在生产制造、销售过程中存在安全缺陷或者不符合相关质量标准,可能对消费者的生命、健康或财产造成危害的产品。
不良产品包括但不限于存在设计缺陷、制造瑕疵或标识误导等问题的商品。
2.2 不良产品的分类标准:根据不良产品引起的危害程度和性质,可以将不良产品分为以下几类:a) 安全隐患类:具有安全风险,可能导致人员伤亡、重大财产损失或危及公共利益。
例如,劣质电子电器可能引发火灾,儿童玩具存在窒息风险等。
b) 质量缺陷类:这些产品虽然无直接安全隐患,但存在一定质量问题,影响使用效果和持久性。
例如,易损坏、易变形或易老化的家居用品。
c) 虚假宣传类:这些产品通过虚假广告或欺骗手段向消费者传递错误信息。
SMT生产不良改善报告

Two-proportions P-Value = 0.03 <0.05 Two-proportions P-Value = 0.038 <0.05 Two-proportions P-Value = 0.04 <0.05 Two-proportions P-Value = 0.021 <0.05 Two-proportions P-Value = 0.031 <0.05 Two-proportions P-Value = 0.043 <0.05
主要改善对象
KPI
Stretch Goal 现 况 竞争社
Combo 1,123
TDR Target
4,00
Break Through IDEA • MD生产供应商问题点追踪
COMBO 作业不良降 (Main) 作业不良 低 为什么要做(背景)? 内/外部环境 外部 •客户要求逐渐提高,品质保证 成为市场重点。
2006.05.10
Great Company Great People
Background Output
D
M
A
I
C
通过4月份工程不良数据分析发现作业不良占比率高,特选定作业不良为活动主题.
4月不良细部分析( PPM )
作业不良改善
TDR改善中
生产规模的迅速扩大,品质控制的
力度相对不足.
1236
P r o p o r t io n
0 .0 0 1 5
_ P = 0.001243
0 .0 0 1 0
0 .0 0 0 5
L C L = 0.000056
0 .0 0 0 0 1 2 3 4 5 6 7 样 本 T e s ts p e r fo r m e d w ith u n e q u a l s a m p le s iz e s 8 9 10 11 12 13
生产线不良问题点分析---装配线
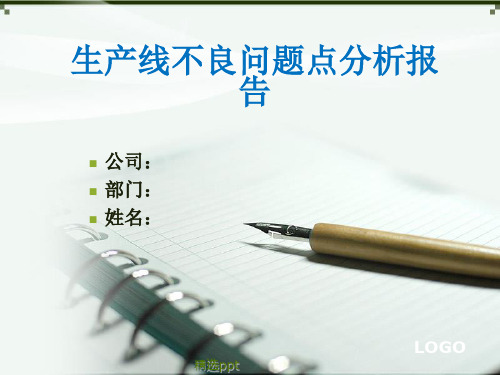
磕伤 不到
不良
印不 不转 不转 丝红
裂痕 位
良
精选ppt
按照过程将问题点分类如下:
来料错误 冲压错误 焊接错误 搬运错误 安装错误 紧固错误 检验错误
精选ppt
按照过程分类计算出不良问题点如下
通过六月份装配线不良统计看得出结论, 安装不良是所有不良中所占比重最大的一项, 占精不选p良pt 总数的57%。
精选ppt
四.改善 对策
1. 操作不规范无次序打钉
漏钉
2.注意力不集中 3. 打钉数量过多,产生疲惫疏忽 4.不再同一平面操作,多面打钉
5.老员工操作麻痹大意 1.制定工艺规范,督导工人按照打钉顺序操作 2.改善工作环境,加强督导防止工人走神 3.规范出标准打钉数量,不超过打定上线 4.尽量安排工人 在同一平面内操作 5. 加强线上宣导,防止老员工麻痹心理出现
精选ppt
四:改善 对策
1.打钉时风枪操作不规范划伤
2.零件在搬运的过程中划伤
划伤不良 3. 带有锐角的零件无规则摆放导致划伤
4.零件在包装容器中往生产线上料途中划伤
5.零件在装配过程中划伤
1.加强培训,规定持枪动作及打钉顺序规范 2.制定搬运规范,加强巡检防止不规范搬运发生 3.带锐角的零件用专用料箱,制定摆放标准 4.加强督导,制定特殊零件搬运规范 5.注意轻拿轻放,规则摆放,避免装配 时产生划伤
跟踪调查分析原因----生产1线
1 确认安装是不良问题的主要原因后7月15日-7月31日现场跟踪生产 线的实际生产
情况。得出结果如下:
精选ppt
跟踪调查分析原因----生产2线
确认安装是不良问题的主要原因后7月15日-7月31日现场跟踪生产2线的
11月份生产物料异常反馈分析报告(1)

11月份生产部物料异常反馈分析报告一、为了对计划交付部物料进度追踪结果进行跟踪落实,确保物料按时到货,设备按时发货,生产部物料小组制定了物料异常反馈回复信息汇总表、物料到货信息汇总表,以此跟计划交付部形成更完善的链接,做到有异常及时告知并反馈。
为了更方便准确的录入异常合同及具体物料,我们会以周为单位分析,然后月底汇总,以下是十一月份物料异常反馈情况见底端附件1-2 查看详情通过对附件分析汇总得;由下表及折线图可知,11月份物料异常反馈回复及时率波动较大,不稳定,在第二周达到最低谷,;准确率趋于平衡。
由此建议,采购员填写采购回复信息积极性有待提高。
周异常反馈回复汇总周次异常不及时数不准确数周排产周及时率周准确率第一周 5 2 11 54.5% 81.8%第二周10 2 13 23.1% 84.6%第三周 6 2 11 45.5% 81.8%第四周周异常反馈回复折线图二、为了深入研究及追踪物料情况,从本月开始,生产将结合物料到货与否情况给予一定的数据分析,同时这也是对采购员工作的一种提醒与督促,整体上,从第一周到第三周,人均到货率逐渐提高,但具体到个人,仍存在到货不及时情况,本月物料到货不及时情况张磊尤为突出,主要是机械加工件像激光器箱、机柜、激光器固定板等物料基本上到料不及时,11月份物料到料、缺料合同记录等情况如下(详情参照附件1-2);周个人到货及时率责任人周次到货不及时明细第一周第二周第三周个数及时率个数及时率个数及时率石进645.5%469.2%281.8%余海峰463.6%469.2%372.7%姚秀芳372.7%561.5%190.9%余同勋372.7%284.6%281.8%毕朝阳463.6%192.3%190.9%张磊736.4%930.8%818.2%周人均到货率59.1%67.9%72.7%周个人到货及时率周次责任人石进余海峰姚秀芳余同勋毕朝阳张磊第一周45.5%63.6%72.7%72.7%63.6%36.4%第二周69.2%69.2%61.5%84.6%92.3%30.8%第三周81.8%72.7%90.9%81.8%90.9%18.2%11月份周个人到货及时率柱形图三、根据生产各班组缺料情况分析总结得,合同设备缺料较为严重的班组为机械,其次总调。
产品不良报告格式
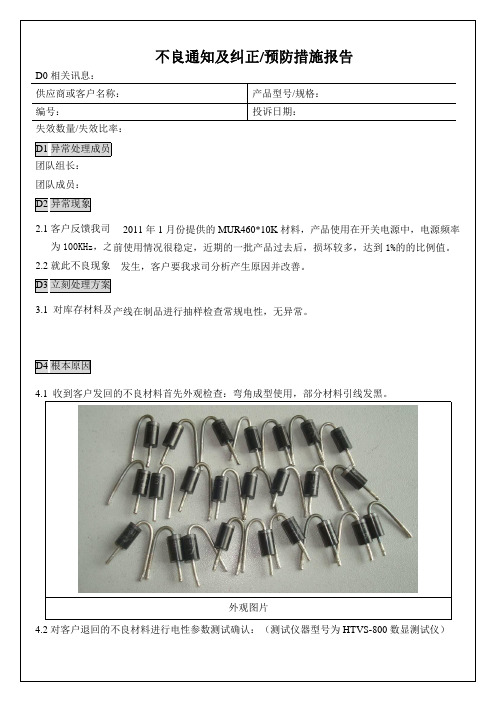
异常处理成员
D1 不良通知及纠正/预防措施报告
D0 相关讯息: 供应商或客户名称: 产品型号/规格: 编号:
投诉日期:
失效数量/失效比率:
团队组长:团队成员:
2011 年 1 月份提供的 MUR460*10K 材料,产品使用在开关电源中,电源频率前使用情况很稳定,近期的一批产品过去后,损坏较多,达到 1%的的比例值。
发生,客户要我求司分析产生原因并改善。
产线在制品进行抽样检查常规电性,无异常。
4.1 收到客户发回的不良材料首先外观检查:弯角成型使用,部分材料引线发黑。
4.2 对客户退回的不良材料进行电性参数测试确认:(测试仪器型号为 HTVS-800 数显测试仪)
外观图片
D2 异常现象
2.1
客户反馈我司于
为 100KHz ,之 2.2 就此不良现象的 D3 立刻处理方案
3.1
对库存材料及 D4 根本原因。
生产质量问题综合分析报告
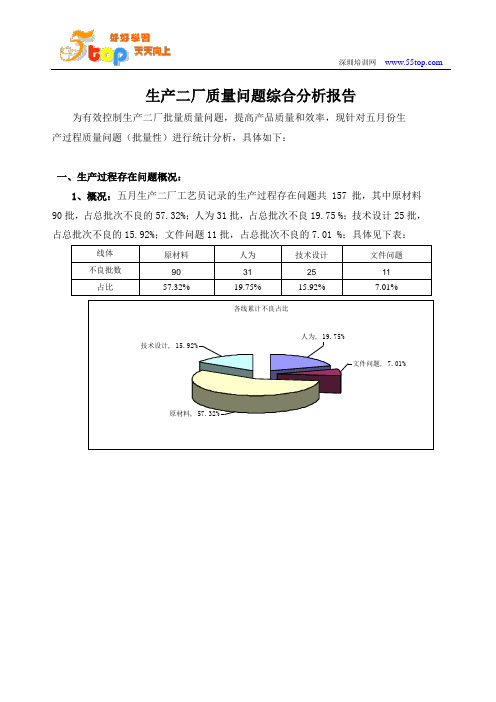
生产二厂质量问题综合分析报告为有效控制生产二厂批量质量问题,提高产品质量和效率,现针对五月份生产过程质量问题(批量性)进行统计分析,具体如下:一、生产过程存在问题概况:1、概况:五月生产二厂工艺员记录的生产过程存在问题共157批,其中原材料90批,占总批次不良的57.32%;人为31批,占总批次不良19.75 %;技术设计25批,占总批次不良的15.92%;文件问题11批,占总批次不良的7.01 %;具体见下表:2、人为不良方面:生产中心批量质量问题共157批次,生产二厂人为批量质量问题31批次,其中总装13批/次、预装5批/次、领料4批/次。
生产三厂预焊问题9批/次.具体见下表:个批次,占30.77%;条形码打印错误有1个批次,占7.69%。
通过上述表格可以发现,塑料厂、纸箱厂与电子公司、诚丰、东丽不良批次占了整个原材料不良批次的79.31%,其中塑料厂问题主要为底座、中框不良,纸箱厂问题主要为纸箱印刷不良,电子公司问题主要为遥控器混送(出现4批)、电控板不良等,诚丰、东丽问题主要为底座、面板不良。
4、设计开发文件方面:设计开发不良共13批次,其中订单BOM:8个批次,对照表4个批次。
具体如下:5、原材料问题点分布1216台。
具体如下表所示:通过上述表格可以发现底座不良达612台占总和的50.33%,中框不良达189台占总和的15.54%,面板不良达133块占总和的10.94%通过上述表格看出纸箱不良达1928台占总和的44.33%,电加热绝缘座不良达1000台占总和的22.99%,遥控器不良达809台占总和的18.60%6、质量工艺反馈方面:05月份生产二厂共提交外部门质量反馈61份,其中《工艺/质量问题反馈单》16份,《原材料质量问题反馈单》45份,反馈单整改情况如下:从以上反馈单整改统计来看,原材料质量反馈单整改完成率仅20%,仍有80%的问题未得到及时整改,其中因散点问题(不合格比例未达到5%,不符合批量问题定义)驳回占28.89%,不整改比例为13.33%,未处理比例为37.78%。
- 1、下载文档前请自行甄别文档内容的完整性,平台不提供额外的编辑、内容补充、找答案等附加服务。
- 2、"仅部分预览"的文档,不可在线预览部分如存在完整性等问题,可反馈申请退款(可完整预览的文档不适用该条件!)。
- 3、如文档侵犯您的权益,请联系客服反馈,我们会尽快为您处理(人工客服工作时间:9:00-18:30)。
P1111生产不良报告
2016年4月9日星期六生产产品P1111时,发现夹色白点,前面生产品种为E0119-1为纯黑色有轻微夹色现象,生产前为水清更换螺杆的方法清机,为最高级别的清机,后再次更换螺杆一次,反复水清设备多次,仍然夹色,后经过验证发现按原有工艺生产此类纯黑产品皆有不同程度的夹色,验证产品为
P21132/P35517,初步判断为此类产品当中某一类原料无法在现有工艺条件下充分分散和融容,后经调整螺杆转速和抬高挤出温度后正常生产,共计耽搁生成时间24小时以上,2016年4月11日星期一再次生产时,由于生技提出按原有温度进行生产再次出现夹色白点,后再次提高温度恢复正常,已经充分验证了此次问题是由于原料不稳定造成的,希望公司加强原料的检验,确保原料的稳定性,以免生产时造成产品品质问题和不必要的人力物力的损失。
生产部
2016年4月11日星期一。