iso9001 WJ8.2.4-2过程检验规程
过程检验规程

过程检验规程1目的和适用范围1.1为确保各类产品加工过程的检验和试验符合产品标准的要求,明确规则过程检验和试验的项目.程序和方法,特制定本标准。
1.2本标准适用于本厂生产制造过程的各类毛坯.零部件的检验过程。
2引用标准GB/T1348-1988球墨铸铁件GB/T9437-1988耐热铸铁件GB/T9439-1988灰铸铁件JB/T5000.4-1998重型机械通用技术条件铸铁件JB/T5000.6-1998重型机械通用技术条件铸钢件JB/T5000.7-1998重型机械通用技术条件铸钢件补焊JB/T5000.9-1998重型机械通用技术条件切削加工件JB/T5000.10-1998重型机械通用技术条件装配JB/T6397-1992大型碳素结构钢铸件JB/T6404-1992大型高锰钢铸件3检验依据和总要求3.1在与顾客签订销售合同时,合同及技术协议中的各项技术要求均应成为过程检验和试验的依据。
3.2按合同规则的图样.技术标准应是过程检验和试验的依据。
3.3本标准第2章引用的各项标准均应成为过程检验和试验的依据。
3.4各类热加工毛坯.零部件.机械加工件.装配过程的检验和试验应按工艺流程和本标准规则的程序进行。
3.5检验人员应掌握各类过程产品的检测方法,按本标准的规则,对各项检验内容进行检验,并实施质量记录。
3.6各项检验所使用的量具.仪器.仪表等,必须经过计量部门校准合格后方可使用,并应根据规则定期检定。
4铸铁件的检验程序和要求4.1灰口铸铁件的检验我厂灰口铸铁件种类主要为HT200,HT300,HT350几种,检查员首先要对木模进行检验检验合格后才能造型,铸铁件检验有以下项目。
4.1.1铸件形状和尺寸检测:铸件在铸造过程及随后的冷却.落砂.清理.热处理和放置过程中会发生变形,使其实际尺寸与铸件图规则的基本尺寸不符。
为此,国家标准规则《铸件尺寸公差与机械加工余量》GB/T6414-1999,以此为依据来检验铸件的尺寸。
过程检验规程
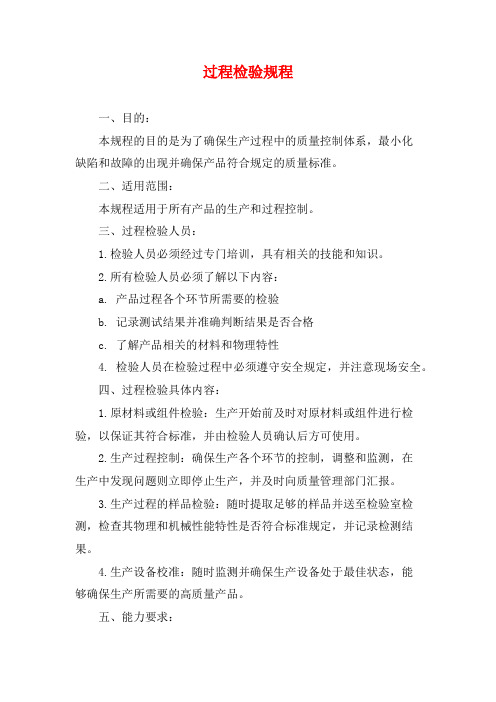
过程检验规程一、目的:本规程的目的是为了确保生产过程中的质量控制体系,最小化缺陷和故障的出现并确保产品符合规定的质量标准。
二、适用范围:本规程适用于所有产品的生产和过程控制。
三、过程检验人员:1.检验人员必须经过专门培训,具有相关的技能和知识。
2.所有检验人员必须了解以下内容:a. 产品过程各个环节所需要的检验b. 记录测试结果并准确判断结果是否合格c. 了解产品相关的材料和物理特性4. 检验人员在检验过程中必须遵守安全规定,并注意现场安全。
四、过程检验具体内容:1.原材料或组件检验:生产开始前及时对原材料或组件进行检验,以保证其符合标准,并由检验人员确认后方可使用。
2.生产过程控制:确保生产各个环节的控制,调整和监测,在生产中发现问题则立即停止生产,并及时向质量管理部门汇报。
3.生产过程的样品检验:随时提取足够的样品并送至检验室检测,检查其物理和机械性能特性是否符合标准规定,并记录检测结果。
4.生产设备校准:随时监测并确保生产设备处于最佳状态,能够确保生产所需要的高质量产品。
五、能力要求:1.检验人员必须对测试设备进行日常维护,以确保它们的准确性。
2.检验人员必须按时,按规定检查样品。
3.检验人员必须具备明确并准确地记录检测事件,包括所采取的行动和结果,以便数据能够用于持续改进工作。
4.检验人员必须了解管理系统的各种手册,并能够熟练操作。
5.检验人员必须定期参加培训和熟悉相关职业知识。
六、不符合检验规程的纪律1.如不符合检验规程,则不得继续进行生产过程。
2.如有违规行为的人员,则必须立即通知生产经理或质量管理部门,让其采取适当措施。
七、适用的标准适用于ISO 9001标准八、检验记录检测员必须在检测文档中正确记录检测结果。
九、修订本规程将在生产过程中持续监测,以确保其始终符合生产需求,并进行适当的修订。
十、指示本规程将通过内部通知、通讯和培训落实至所有员工。
十一、一般条款1.本规程应成为生产过程控制规程的一部分,以支持ISO质量体系。
GM02过程检验规程

1目的规定过程检验的方式、标准,尽早发现过程中影响产品质量的系统因素,防止产品成批报废或将不合格产品转入下序。
2范围2.1适用于公司内部的所有生产过程。
2.2在对供应商进行管理和控制时,也适用本制度。
3定义3.1首件检验——是在生产开始时上班或换班或工序因素调整后,换人换料换活换工装调整设备等对制造的第1 件或前几件产品进行的检验。
包括操作工自检,操作工互检和检验员首件确认。
3.2巡回检验——是指检验员在生产现场按一定的时间间隔对有关工序的产品和生产条件进行监督检验。
3.3工序入库检验——是指对全部加工活动结束的零件进行的检验,工序入库检验的工作包括验证前面各工序的检验是否已完成,检验结果是否符合要求即对前面所有的检验数据进行复核。
4职责4.1品管部过程检验员按本指示要求对负责管辖范围内加工过程进行首检、巡检和产品完工后的完工检。
4.2制造部作业人员负责加工过程中自检、互检及提报首检。
5控制程序5.1图纸、工艺卡片及表单分发及悬挂:5.1.1车间班组长:将图纸或“工序卡片”及生产计划分发给操作工。
5.1.2操作工将图纸或“工序卡片”、“装配过程卡”放置在工位适当位置。
5.2操作工首检:5.2.1当批量大于20件时或单件价值高于500元且数量不少于5件的机加产品须填写“首件确认单”,并向品管部过程检验员交检。
5.2.2首次加工按图纸或“工序卡片”要求自检合格。
5.2.3将首件自检结果如实填写于“首件确认单”中,并在首件上作好标识。
5.2.4向过程检验员报首检,提交样件1~2件。
5.2.5首件未经检验合格不得继续加工或作业。
5.3检验员首检:5.3.1过程检验员按附表1“工序检验标准”要求进行首件检验。
5.3.2首件判定后,过程检验员应对首件合格件粘贴合格标识,以便作业参照,并保留到该批产品完工。
5.3.3个别装配难度大的零件或测量难度大的零件,首检按操作工→车间管理人员→过程检验三方确认原则执行。
ISO9001-2015制程检验程序
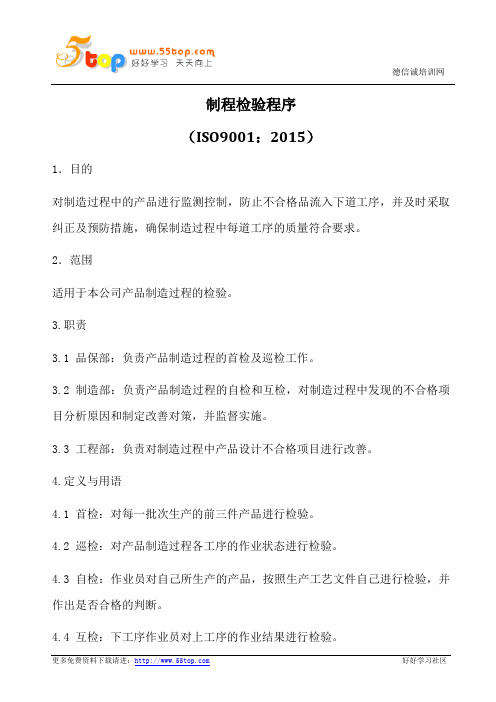
制程检验程序(ISO9001:2015)1.目的对制造过程中的产品进行监测控制,防止不合格品流入下道工序,并及时采取纠正及预防措施,确保制造过程中每道工序的质量符合要求。
2.范围适用于本公司产品制造过程的检验。
3.职责3.1 品保部:负责产品制造过程的首检及巡检工作。
3.2 制造部:负责产品制造过程的自检和互检,对制造过程中发现的不合格项目分析原因和制定改善对策,并监督实施。
3.3 工程部:负责对制造过程中产品设计不合格项目进行改善。
4.定义与用语4.1 首检:对每一批次生产的前三件产品进行检验。
4.2 巡检:对产品制造过程各工序的作业状态进行检验。
4.3 自检:作业员对自己所生产的产品,按照生产工艺文件自己进行检验,并作出是否合格的判断。
4.4 互检:下工序作业员对上工序的作业结果进行检验。
5.流程图见附件一6. 程序:6.1 首件检验6.1.1 每一生产批次的产品在生产时必须做首件检验,每批产品在投产时,各工序生产的符合生产工艺文件要求的前三件产品即为“首件”。
6.1.2 IPQC与PE根据《物料清单》(《订造机物料差异清单》)、《设计、工程变更通知单》、《生产工艺流程图》、《生产工艺通知单》对批次生产的前3件产品进行首件检验,确认合格后方可进行批量生产,并将检查结果记录在《首检记录报告》上。
6.1.3 如确认不合格,由品保部召集工程部、制造部三方检讨原因,制定对策,参照《纠正与预防措施管理程序》执行。
IPQC负责跟进处理结果直到异常解决转入正常生产。
6.2 巡回检验6.2.1 产品制造过程中制造部各生产线按照《生产工艺流程图》和《生产工艺通知单》要求进行自检和互检,以杜绝不良品流入下道工序。
发现不良品应依《产品标识与追溯管理程序》实施标识,对不良品依《不合格品控制程序》处理,当不良率>3%时应发出《异常处理单》至PE进行分析处理,设计不良的,发至工程部进行分析处理,材料不良由品保部进行分析处理。
产品过程检验规程
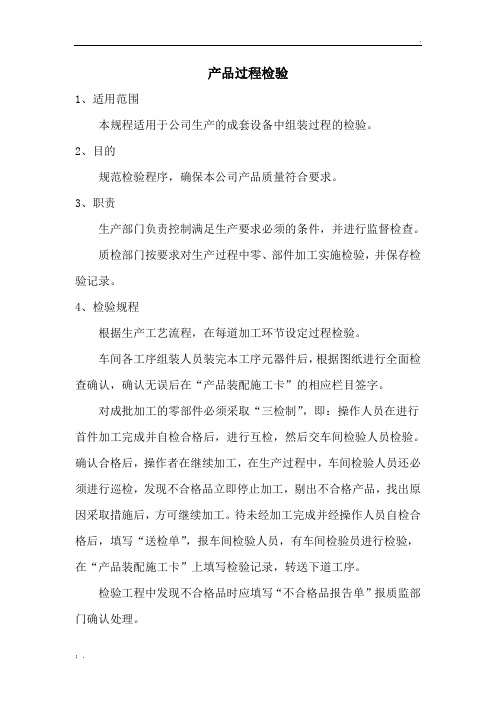
产品过程检验
1、适用范围
本规程适用于公司生产的成套设备中组装过程的检验。
2、目的
规范检验程序,确保本公司产品质量符合要求。
3、职责
生产部门负责控制满足生产要求必须的条件,并进行监督检查。
质检部门按要求对生产过程中零、部件加工实施检验,并保存检验记录。
4、检验规程
根据生产工艺流程,在每道加工环节设定过程检验。
车间各工序组装人员装完本工序元器件后,根据图纸进行全面检查确认,确认无误后在“产品装配施工卡”的相应栏目签字。
对成批加工的零部件必须采取“三检制”,即:操作人员在进行首件加工完成并自检合格后,进行互检,然后交车间检验人员检验。
确认合格后,操作者在继续加工,在生产过程中,车间检验人员还必须进行巡检,发现不合格品立即停止加工,剔出不合格产品,找出原因采取措施后,方可继续加工。
待未经加工完成并经操作人员自检合格后,填写“送检单”,报车间检验人员,有车间检验员进行检验,在“产品装配施工卡”上填写检验记录,转送下道工序。
检验工程中发现不合格品时应填写“不合格品报告单”报质监部门确认处理。
成品总装完成并经装配人员自检合格后,连同“产品装配施工卡”及该产品的其他图样一并送到质监部门,由质检部门进行最终全面检验。
检验人员根据检验结果(除巡检外),对被检产品还应进行“合格”或“不合格”的检验状态标识。
对检验过程中发现不合格产品均须及时作出明显的“不合格”标识,随后对不合格品按《不合格品控制程序》进行处理。
根据型式试验报现场生产产品要满足一致性的要求。
5、验项目、检验要求、检验方法。
品质手册ISO2000 8.2.4产品的监视和测量
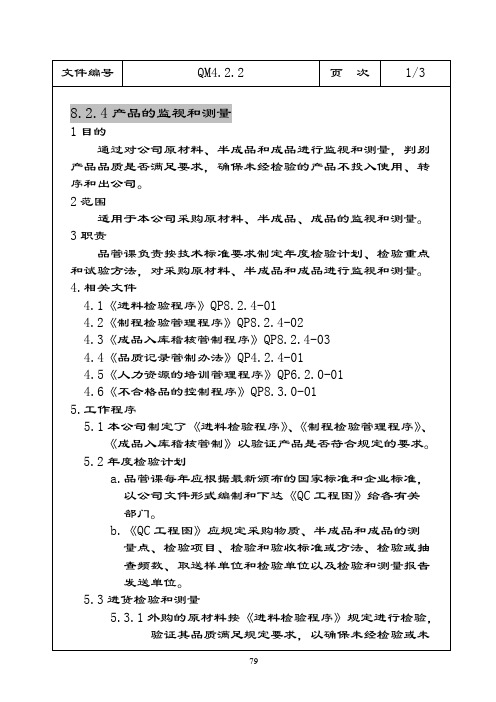
量(包括进货和过程)均已完成,且结果满足规
定的要求,数据、记录都得到审核认可后,产品
才能发货。
5.6监视和测量记录
5.6.1本公司建立并保存了表明采购原材料、生产过程
中的半成品和成品的检验记录或检验报告单,这
些记录和报告单都清楚地表明某种产品按规定的
文件编号
QM4.2.2
页次
1/3
-79-
8.2.4产品的监视和测量
1目的
通过对公司原材料、半成品和成品进转
序和出公司。
2范围
适用于本公司采购原材料、半成品、成品的监视和测量。
3职责
品管课负责按技术标准要求制定年度检验计划、检验重点
4.6《不合格品的控制程序》QP8.3.0-01
5.工作程序
5.1本公司制定了《进料检验程序》、《制程检验管理程序》、
《成品入库稽核管制》以验证产品是否符合规定的要求。
5.2年度检验计划
a.品管课每年应根据最新颁布的国家标准和企业标准,
以公司文件形式编制和下达《QC工程图》给各有关
部门。
b.《QC工程图》应规定采购物质、半成品和成品的测
和试验方法,对采购原材料、半成品和成品进行监视和测量。
4.相关文件
4.1《进料检验程序》QP8.2.4-01
4.2《制程检验管理程序》QP8.2.4-02
4.3《成品入库稽核管制程序》QP8.2.4-03
4.4《品质记录管制办法》QP4.2.4-01
4.5《人力资源的培训管理程序》QP6.2.0-01
理程序》的要求,并进行专业培训上岗且取得相
应资格,以保证检验结果的准确性。
5.4.2各品质控制点在所要求的测量和监视完成或必须
ISO9001 WJ8.2.4-1进货检验规程

JB/T 5000.15-1998 重型机械通用技术条件 锻钢件无损探伤
3 检验依据
3.1 与顾客签订的销售合同以及技术协议中的各项技术要求均应成为进货检验和试验的依据。
3.2 按合同规定的图样以及相关技术标准应是进货检验和试验的依据。
4.1.2 检查员应将钢材质量证明书上记录的钢材的化学成分和力学性能参数与相应技术标准进行核对,验证是否合格。碳素结构钢应符合GB700标准的规定,低合金结构钢应符合GB1591标准的规定。
4.1.3 检查员应抽查钢材的外形尺寸,用卡尺测量钢板及型材的厚度,用钢卷尺测量钢板、型材等的尺寸。钢材的厚度和尺寸公差应符合相关的技术标准规定的要求。
4.1.4 检查员应目测钢材的外观质量,钢材的外表不得有疤痕、裂纹、凹坑、严重锈蚀和────────────────────────────────────── 编制:李志伟 日期: 2013-8-8 审批:肇军 日期:2013-8-8 1
3.3 本文件第2章引用的各项文件均应成为进货检验和试验的依据。
3.4 各项检验所使用的量具、仪器、仪表等,必须经过计量部门校准合格后方可使用,并应根据规定定期检定。
4 原材料的进货检验
4.1 钢材的验证
4.1.1 对于钢材,每批进货时应提供钢厂的质量证明书。检查员应核对质量证明书上的材料牌号与本公司要求的牌号是否一致,并验证钢材上的标识。
1.2 本文件适用于本公司为生产制造各类产品而采购的原材料、配套件和外协的毛坯、焊接结构件和机械加工件等产品的进 5000.1-1998 重型机械通用技术条件 产品检验
JB/T 5000.3-1998 重型机械通用技术条件 焊接件
ISO9001质量管理体系的审核
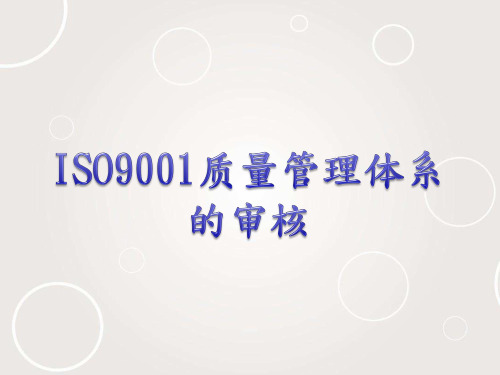
引导式的问题
• 这一类的问题会推论答案,并不是审核时使用的典型问题, 但可能有时候会需要用到
新建质量管理体系、质量管理体系发 生重大变化等情况时采用
一次审核几个部门或过程,但一个审 核周期内所有相关部门和过程均应得 到审核
重要的部门和过程可安排多次审核
适用于大、中型企业设有专门内审机 构或专职人员的情况
b.集中式年度审核计划—范例
• 冠智达顾问公司2005年度审核计划 1、目的 – 保证内部审核按计划实施,确保质量管理体系得以 有效实施和保持。 2、审核范围 – 公司汽车零件产品的设计、制造、服务所涉及的各 部门、场所、和过程。 3、审核依据 – ISO9001;/ 质量管理体系文件; – 适用的法律、法规等。 4、审核组 – 在每次审核前两周由管理者代表任命。
• "为什么你仅做一次设计评审?" "这些评审都是什么时候进行的?" "怎样控制评审过程?" "谁参加设计评审?" "这些评审的记录保存在哪里?"
封闭式的问题
• 以得到肯定或否定的回答为目的,一般只用于掌控交谈的 局面,适用于被审核者偏离审核主题时.
• 1. 一般情况下不用 例如: “你们有一个不合格品控制程序吗?”“是的。” “这个程序是经过批准的吗?”“是的。” “这个程序包括软件吗?” “不包括。”
ISO9001质量检验程序(含表格)

ISO9001质量检验程序※※※※※※※※※此文件未经批准﹐不准复印※※※※※※※※※※1 目的对产品实现的必须的过程进行测量和监控,以确保满足顾客的要求;对产品特性进行测量和监控,以验证产品要求得到满足。
2 范围适用于对产品实现过程持续满足其预定目的的能力进行确认;对生产所用原材料,生产的半成品和成品进行测量和监控。
3 职责品质部负责对过程和产品的测量和监控。
4 程序4.1 过程的测量和监控4.1.1 生产中心负责识别需要进行测量和监控的实现过程,它包括产品实现过程,也包括公司根据产品特点策划的各过程和子过程,特别是生产和服务运作的全过程。
4.1.2 过程持续满足预定目的的能力,是指过程实现产品并使其满足要求的本领。
4.1.3 与质量相关的各过程应根据组织总目标进行分解,转化为本过程具体的质量目标,如生产中心的工序产品合格率、设计开发部的设计输出文件失误率、供应部采购产品的合格率、营销部的销售指标及顾客服务满意率等。
为保证目标的顺利完成,需进行相应的测量监控:a)品质部负责使用控制图,对质量形成的关键过程进行测量,对图形数据分布趋势分析,明确过程质量和过程实际能力之间的关系,以确定需要采取纠正或预防措施的时机;b)当过程产品合格率接近或低于控制下限时,品质部应及时发出《纠正和预防措施处理单》,定出责任部门,对其从人员、设备、原材料、各类规程、生产环境及检验等方面分析原因并采取相应的措施;当需要采取改进措施时,品质部制定相应的改进计划,经管理代表审核,总经理批准后,交责任部门实施,品质部负责跟踪验证实施效果。
4.2 产品的测量和监控4.2.1 品质部负责编制各类检测规程,明确检测点、检测频率、抽样方案、检测项目、检测方法、叛别依据、使用的检测设备等。
4.2.2 进货验证4.2.2.1 对生产购进物资,仓库保管员核对送货单,确认物料品名、规格、数量等无误、包装无损后,置于待检区,填写《进货验证记录》交给检验员。
过程检验规程

过程检验规程过程检验规程文稿归稿存档编号:[KKUY-KKIO69-OTM243-OLUI129-G00I-FDQS58-过程检验规程1.目的:规定过程检验的方式、标准,确保生产过程中产品质量能够及时控制,防止不合格产品转入下道工序。
2.范围:适用于本公司过程加工的产品3.职责:工序操作工: 加工过程中自检.过程检验员: 按本指示要求对加工过程进行首检、巡检和产品完工后的成品检.4. 定义:首件检验:是在生产开始时上班或换班或工序因素调整后,换人换料换活换工装调整设备等对制造的第1 件或前几件产品进行的检验.包括操作工自检,操作工互检和检验员首件确认。
巡回检验:是指检验员在生产现场按一定的时间间隔对有关工序的产品和生产条件进行监督检验.半成品检:是指对全部加工活动结束的半成品零件进行的检验,半成品检验的工作包括验证前面各工序的检验是否已完成,检验结果是否符合要求即对前面所有的检验数据进行复核。
5. 运行程序:5.1操作工首检:5.1.1首次加工按图纸要求自检合格。
5.1.2向过程检验员报首检结果,提交样件最少2件。
5.1.3首件未经检验合格不得继续加工或作业。
5.3检验员首检:5.3.1过程检验员对首次加工样件,按《工序检验标准》要求作首件检验。
5.3.2首件判定后,过程检验员应对首件合格件打上确认标识,以便作业参照,并保留到该批产品完工.5.3.3首检记录:首检过程如实记录于【生产过程首检、巡检质量记录表】中.5.4操作工自检:5.1.6首检合格,过程加工可正式量产作业,操作工应在量产中保持一定频次的自检 (每0.5小时一次自检),以保证质量的稳定。
5.5个别装配难度大的零件或测量难度大的零件,首检按操作工→车间管理人员→检验员,三方确认原则执行5.6巡检:5.6.1过程检验员应对量产过程进行巡检作业,检验频次:2小时至少巡检1趟,每个机位产品最少抽样3-5件,检验标准参见《工序检验标准》,根据实际情况对关键特性、重要特性、工艺上有特殊要求对下道工序的加工装配有重大影响的和内外部质量信息反馈中出现质量问题多的薄弱环节加强巡检频次。
过程检验规范(已打印)

标题
过程检验规范
文件编号
WI-QC-017
版次
A1
页次
第1页,共1页
编写日期
2010/10/08
编制
审核
批准/日期
1.0抽样方案:尺寸按照GB2828-87,特殊抽样水平S-3,AQL=1.0抽样;外观按GB2828-87,一般抽样水平I,AQL=1.5抽样。
喷涂附着力、涂膜硬度、涂膜柔韧性、光泽按GB2828-87,特殊抽样水平S-1,AQL=2.5抽样。
备注
1
外观
按照《喷涂件质量检验分级标准》进行
目测
2
涂膜厚度
按照《喷涂件质量检验分级标准》进行
用测厚仪直接测量
3
膜层附着力
划格后的膜层划格交错处用粘合性高的胶布拉表面,膜层无脱皮或剥落为合格
用刀片采取划格法
4
色差
按照《喷涂件质量检验分级标准》进行
色板、色差仪
5
涂膜硬度
2H中华铅笔于产品表面推过无明显刮痕或露底材为合格
2H中华铅笔
6
涂膜柔韧性
8折弯棒折弯180度无脱漆或明显痕纹
8折弯棒
7
光泽度
同一平面测3点,取平均值,范围≥85%为合格
光泽仪
根据客户要求
喷涂涂膜厚度、色差、外观按GB2828-87,特殊抽样水平S-4,AQL=2.5抽样。
2.0检验标准
2.1钣金件检验标准
序号
检验项目
检验标准
检验方法及工具
备注
1
尺寸
依据工艺卡片中的检验卡要求进行检验
游标卡尺及相关检具
2
外观
依据工艺卡片中的检验卡要求
目测
ISO9001仪器校验程序(含表格)

ISO9001仪器校验程序※※※※※※※※※此文件未经批准﹐不准复印※※※※※※※※※※1 目的对用于确保产品符合规定要求的测量和监控设备进行控制,确保测量和监控结果的有效性。
2 范围适用于对产品和过程进行测量监控用的设备、软件等。
3 职责品质部a)负责对测量、监控设备的校准;根据需要编制内部校准规程;b)负责对偏离校准状态的测量、监控设备的追踪处理;c)负责对测量和监控设备操作人员的培训、考核。
4 程序4.1 测量和监控设备的采购及验收根据所需测量能力和测量要求配置测量和监控设备,对其的采购和验收,执行《设备工装管理程序》中对生产设备采购的管理规定。
4.2 测量和监控设备的初次校准a)经验收合格的测量和监控设备,由品质部负责送国家计量部门检定或自行校准,合格后方能发放使用。
对合格品应贴上表明其状态唯一性标识;品质部负责对该设备编号,建立《测量监控设备履历卡》,记录设备的编号、名称、规格型号、精度等级、生产厂家、校准周期、校准日期、放置地点等;并填写《测量监控设备一览表》;b)对于没有国家标准的设备,应记录用于校准的依据;c)品质部负责测量、监控设备的发放。
4.3 测量、监控设备的周期校准4.3.1 每年十二月品质部编制下年度《计量校准计划》,根据计划执行周期校准。
a)对需外校的设备,由品质部负责联系国家法定计量部门进行校准,并出具校准报告;b)对需进行内部校准的设备,品质部应编制相应的《内部校准规程》,规定校准的方法、使用设备、验收标准及周期等内容,经品质部经理批准,由品质部实施并填写《内部记录表》。
4.3.2 校准合格的设备,由校准人员贴《合格标签》,并标明有效期;部分功能或量程校准合格的,贴《限用标签》,标明限用有范围;校准不合格的,贴“不合格标签”,修理后重新校准;对不便粘贴标签的设备,可将标签贴在包装盒上,或由使用者妥善保管。
4.3.3 对于测量、监控用的软件,在使用前应进行自校准,填写相应的校准记录。
- 1、下载文档前请自行甄别文档内容的完整性,平台不提供额外的编辑、内容补充、找答案等附加服务。
- 2、"仅部分预览"的文档,不可在线预览部分如存在完整性等问题,可反馈申请退款(可完整预览的文档不适用该条件!)。
- 3、如文档侵犯您的权益,请联系客服反馈,我们会尽快为您处理(人工客服工作时间:9:00-18:30)。
过程检验规程1 目的和适用范围1.1 为确保各类产品加工过程的检验和试验符合产品标准的要求,明确规定过程检验和试验的项目、程序和方法,特制定本标准。
1.2 本标准适用于本厂生产制造过程的各类毛坯、零部件的检验过程。
2 引用标准GB/T 1348-1988 球墨铸铁件GB/T 9437-1988 耐热铸铁件GB/T 9439-1988 灰铸铁件JB/T 5000.4-1998 重型机械通用技术条件铸铁件JB/T 5000.6-1998 重型机械通用技术条件铸钢件JB/T 5000.7-1998 重型机械通用技术条件铸钢件补焊JB/T 5000.9-1998 重型机械通用技术条件切削加工件JB/T 5000.10-1998 重型机械通用技术条件装配JB/T 6397-1992 大型碳素结构钢铸件JB/T 6404-1992 大型高锰钢铸件3 检验依据和总要求3.1 在与顾客签订销售合同时,合同及技术协议中的各项技术要求均应成为过程检验和试验的依据。
3.2 按合同规定的图样、技术标准应是过程检验和试验的依据。
3.3 本标准第2章引用的各项标准均应成为过程检验和试验的依据。
3.4 各类热加工毛坯、零部件、机械加工件、装配过程的检验和试验应按工艺流程和本标准规定的程序进行。
3.5 检验人员应掌握各类过程产品的检测方法,按本标准的规定,对各项检验内容进行检验,并实施质量记录。
3.6 各项检验所使用的量具、仪器、仪表等,必须经过计量部门校准合格后方可使用,并应根据规定定期检定。
4 铸铁件的检验程序和要求4.1灰口铸铁件的检验我厂灰口铸铁件种类主要为HT200,HT300,HT350几种,检查员首先要对木模进行检验检验合格后才能造型,铸铁件检验有以下项目4.1.1铸件形状和尺寸检测:铸件在铸造过程及随后的冷却、落砂、清理、热处理和放置过程中会发生变形,使其实际尺寸与铸件图规定的基本尺寸不符。
为此,国家标准规定《铸件尺寸公差与机械加工余量>>GB/T6414-1999,以此为依据来检验铸件的尺寸,4.1.2铸件表面粗糙度的评定:铸件的铸造表面粗糙度是衡量毛坯铸件表面质量的重要指标。
铸造表面粗糙级别用全国铸造标准化技术委员会监制的铸造表面粗糙度比较样块进行评定。
《表面粗糙度比较样块铸造表面>>GB/T6060.14.1.3铸件表面和近表面缺陷的目视检验:用肉眼或借助于低倍放大镜检查暴露在铸件表面的宏观缺陷,同时检查铸件的生产标记是否正确齐全。
检查时应判定铸件对于检查项目是否合格,区分合格品、返修品和废品。
目视外观检验可检查的缺陷项目有:飞翅、毛刺、抬型、胀砂、冲砂、掉砂、外渗物、冷隔、浇注断流、表面裂纹(包括热裂、冷裂和热处理裂纹)、鼠尾、沟槽、夹砂结疤、粘砂、表面粗糙、皱皮、缩陷、浇不到、未浇满、跑火、型漏、机械损伤、错型、错芯、偏芯、铸件变形翘曲、冷豆,以及暴露在铸件表面的夹杂物、气孔、缩孔、渣气孔、渣缩孔、砂眼等。
检查前,铸件生产厂应事先制定或与用户商定检查项目的合格品标准。
目视外观检验分为工序检查和终端检查两种。
工序检查一般在落砂或清理后进行;终端检查在清理后或热处理后,铸件入库或交付前进行。
单件或小批生产的铸件应检查全部铸件,成批或大量生产的铸件可按批或按周期抽样检查样本铸件。
4.1.4、铸件力学性能检验:灰口铸铁的力学性能,硬度应符合GB/T9439标准规定化学成分不做验收依据4.2球墨铸铁件的检验4.2.1球墨铸铁件的检验方法与灰口铸铁基本相同,但是在检验木模尺寸时应注意,球墨铸铁的手收缩率与灰口铸铁不同,球墨铸铁件的尺寸公差应符合GB/T6414-1999,以此为依据来检验铸件的尺寸4.2.2铸件表面粗糙度的评定:铸件的铸造表面粗糙度是衡量毛坯铸件表面质量的重要指标。
铸造表面粗糙级别用全国铸造标准化技术委员会监制的铸造表面粗糙度比较样块进行评定。
《表面粗糙度比较样块铸造表面>>GB/T6060.14.2.3铸件表面和近表面缺陷的目视检验:用肉眼或借助于低倍放大镜检查暴露在铸件表面的宏观缺陷,同时检查铸件的生产标记是否正确齐全。
检查时应判定铸件对于检查项目是否合格,区分合格品、返修品和废品。
目视外观检验可检查的缺陷项目有:飞翅、毛刺、抬型、胀砂、冲砂、掉砂、外渗物、冷隔、浇注断流、表面裂纹(包括热裂、冷裂和热处理裂纹)、鼠尾、沟槽、夹砂结疤、粘砂、表面粗糙、皱皮、缩陷、浇不到、未浇满、跑火、型漏、机械损伤、错型、错芯、偏芯、铸件变形翘曲、冷豆,以及暴露在铸件表面的夹杂物、气孔、缩孔、渣气孔、渣缩孔、砂眼等。
检查前,铸件生产厂应事先制定或与用户商定检查项目的合格品标准。
目视外观检验分为工序检查和终端检查两种。
工序检查一般在落砂或清理后进行;终端检查在清理后或热处理后,铸件入库或交付前进行。
单件或小批生产的铸件应检查全部铸件,成批或大量生产的铸件可按批或按周期抽样检查样本铸件。
4.2.4球墨铸铁件的内在质量的检验:机械性能应符合GB/T1348-1988标准的规定,金像组织检验应遵循GB/T9441规定执行,球化率要低于4级其他金像组织与用户协商定,化学成分不做为普通球墨铸铁验收依据5 铸钢件的检验程序和要求5.1铸钢件的尺寸公差应符合GB/T6414-1999,以此为依据来检验铸件的尺寸5.2铸钢件表面粗糙度的评定:铸件的铸造表面粗糙度是衡量毛坯铸件表面质量的重要指标。
铸造表面粗糙级别用全国铸造标准化技术委员会监制的铸造表面粗糙度比较样块进行评定。
《表面粗糙度比较样块铸造表面>>GB/T6060.15.3一般工程用铸造碳钢依据GB/T11352-1989进行检验5.4低合金铸件依据JB/T6402或JB/T5000.6标准进行验收5.5大型耐热钢铸件依据JB/T6403-1992标准进行验收5.6大型不锈钢铸件依据JB/T6405-1992标准进行验收5.7煤机铸件根据三一提供标准进行检验5.8水电,核电铸件根据其提供的标准进行检验6 热处理件的检验程序和要求6.1检查员应对热处理工艺曲线要彻底了解并对热处理温度实施监控6.2对硬度的检测时要把试件氧化皮及脱碳层去除干净多取几点测试6.3对热处理产生的缺陷要注意检查及时及时反馈及时扑救7 机械加工零部件的检验程序和要求7.1 零部件的外观检验7.1.1 检查员应目测加工后的零部件,不得有锈蚀、毛刺,除非图样或工艺文件有特殊要求,加工后的零件不得有尖棱和尖角。
7.1.2 最终工序热处理后的零件,表面不应有氧化皮。
经过精加工的配合面,不应有退火、发蓝、变色的现象。
7.2 零件的尺寸检验7.2.1 检查员应根据检验项目的需要,使用适合的检测量具对加工后的零件尺寸进行检测,并依据规定的公差验证零件的加工尺寸是否合格。
7.2.2 图样上规定了公差的,尺寸偏差不得大于图样规定的公差范围。
7.2.3 图样上未注公差的,切削表面之间的尺寸偏差不得大于表1规定的数值。
对于毛坯表面和切削表面之间的尺寸,如图样中未注公差,则采用毛坯尺寸的未注公差之半加上表1中的未注公差。
7.2.4 检查员应用卡尺或样板检测零部件的倒圆、倒角。
7.2.4.1 零件各加工面接合而形成的台阶根部或棱边的倒圆、倒角应符合图样的要求,零件的倒圆和倒角无配合关系时,倒圆半径和倒角高度尺寸的极限偏差应符合表2的规定;有配合关系时,凸圆和凸角的极限偏差应取表2中的正值,凹圆和凹角的极限偏差应取表2中的负值。
7.2.4.2 图样未注明倒圆、倒角尺寸,又无清根要求时,应根据台阶的高度或零件的尺寸进行倒圆、倒角。
未注明倒圆半径应符合表3规定的数值,未注倒角角度应为45°,倒角尺寸应符合表4规定的数值。
7.3 零件的角度检验7.3.1 检查员应根据检验项目的需要,使用适合的角度尺等量具对加工后的零件尺寸进行检测,并依据规定的公差验证零件的加工角度是否合格。
7.3.2 图样上规定了角度公差的,角度偏差不得大于图样规定的公差范围。
7.3.3 图样未注角度公差时,零件的角度偏差不得大于表5规定的数值。
角度偏差值按角度短边的长度确定,对圆锥角按圆锥素线长度确定。
7.4 形位公差的检验7.4.1 检查员应根据检验项目的需要,使用适合的检测量具对加工后的零件几何形状、几何要素的相互位置进行检测,并依据规定的形位公差验证零件是否合格。
7.4.2 图样上规定了形位公差的,零件的形状和位置偏差不得大于图样规定的数值。
7.4.3 零件的未注直线度和平面度,应符合表6的规定。
7.4.4 零件的圆度和圆柱度的未注公差值,应不大于其未注尺寸公差值。
7.4.5 零件的平行度的未注公差值等于给出的尺寸公差值或是直线度和平面度未注公差值中的较大者,应取两要素中的较长者作为基准。
7.4.6 零件的未注垂直度应符合表7的规定。
7.4.7 零件的同轴度和对称度应符合表8的规定。
7.4.8 零件的圆跳动和全跳动的公差值应不大于该要素的形状和位置未注公差的综合值。
7.4.9 其它项目如线轮廓度、面轮廓度、倾斜度、位置度和全跳动均应由各要素的注出或未注线性尺寸公差或角度公差控制。
7.4.10 键槽的对称度应符合表9规定的数值。
7.4.11 螺纹孔与螺栓孔未注位置度公差应符合表10的规定。
7.5 螺纹的检验7.5.1 检查员应对加工的螺纹进行检验。
7.5.2 螺纹表面不得有黑皮、磕碰、乱扣和毛刺等缺陷。
7.5.3 内外螺纹旋入侧在加工螺纹前必须倒角,外螺纹为45°,内螺纹为60°,倒角深度等于螺栓端部倒角深度。
7.6 表面粗糙度的检验7.6.1 检查员应根据检验项目的需要,检测加工面的表面粗糙度,并对照样板、样块验证零件是否合格。
7.6.2 图样上规定了表面粗糙度的,零件的表面粗糙度不得大于图样规定的公差范围。
7.6.3 螺纹通孔、长孔、麻花钻或尖头钻加工的孔表面Ra值不得大于25μm。
7.6.4 加工中出现的退刀槽、润滑槽、螺纹、螺纹退刀槽、楔键和平键槽的Ra值不得大于3.2μm。
7.6.5 内倒圆(倒角)的表面粗糙度应与同它相连的精表面相同,外倒圆(倒角)的表面粗糙度与同它相连的粗表面相同。
8 装配的检验和试验8.1 装配准备8.1.1 对进入装配的零部件进行外观检验,零部件应清理干净,不得有毛刺、飞边、氧化皮、锈蚀、油污、着色剂、灰尘等。
零部件外表油漆应干燥,不得带有型砂、切屑等杂物。
8.1.2 对零部件的主要配合尺寸,特别是过盈配合尺寸及相关精度进行复检。
8.1.3 对机座、机身等装配基础件的水平度或垂直度进行检测,结构简单、精度低的产品不低于0.2/1000,结构复杂、精度高的产品不低于0.1/1000。
8.2 装配连接的检验8.2.1 螺钉、螺栓连接的检验a)螺钉、螺栓连接应均匀拧紧。