等高切削
论述金刚石刀具超精密切削的机理丶条件和应用范围

金刚石刀具超精密切削的机理丶条件和应用范围
金刚石刀具是超精密切削中常用的刀具材料,其切削机理、条件和应用范围如下:
1.切削机理:
⏹金刚石刀具的切削刃非常锋利,在切削过程中能够实现“切入式切削”,
使切削力大大减小。
⏹金刚石的硬度极高,切削时不易被工件材料磨损,能够保持良好的切削刃
形状。
⏹金刚石的传热性能极佳,能够快速地将切削热量传递出去,从而降低切削
温度,减少热损伤。
1.切削条件:
⏹刀具刃口半径:为了实现超精密切削,需要将刀具的刃口半径减小到亚微
米级,以提高切削的精度和表面粗糙度。
⏹切削用量:为了减小切削力和热量,需要选择较小的切削深度和进给速度,
以提高切削效率。
⏹工件材料:金刚石刀具适用于加工各种硬材料,如淬火钢、硬质合金等。
但是,对于一些韧性较大的材料,需要进行预处理或选择其他刀具材料。
1.应用范围:
⏹金刚石刀具广泛应用于超精密切削领域,如光学零件、轴承、硬盘磁头、IC
芯片等高精度、高表面质量的零件加工。
⏹在加工过程中,金刚石刀具还可以用于制作各种微细结构,如微孔、微槽
等。
综上所述,金刚石刀具的超精密切削需要满足一定的条件,并具有广泛的应用范围。
加工中心切削参数表

加工中心切削参数表CNC加工切削刀具参数⑴一般大小的钢料开粗时尽量选用Φ30R5,较大型的钢料尽量选用Φ63R6;⑶铜公2D外形光刀,高度50mm以下选用M12刀具;高度在50-70mm 之间,选用M16刀具;高度在70-85mm之间,选用M20;高度在85-120mm 之间,选用M25;超过120mm以上用Φ25R0.8、Φ32R0.8飞刀把加工;⑷较平坦的曲面或较高的外形曲面尽量选用Φ20R4、Φ25R5、Φ40R6作为光刀刀具;5. 钢料开粗时,Z下刀量0.5-0.7mm。
铜料开粗时Z下刀量1.0-1.5mm(内部开粗1.0mm,基准边开粗1.5mm)6. 平行式精铣时,ma×imum stepover按“精加工平行式最佳等高参数表”来设定。
精铣前余留量尽量留小点,钢料0.10—0.2mm。
铜料0.2--0.5mm。
不要使用R刀精锣面积大的平面8. 快速下刀至3mm高度使用F速下刀(相对加工深度)正常下刀F 速一律300mm/m,有螺旋下刀和外部进刀的Z下刀F速一律是900 mm/ m,有踩刀地方的Z下刀F速一律150mm/m,内部快速移动F 速一律是6500mm/m(必须走G01)。
9. 使用Φ63R6、Φ40R6、Φ30R5飞刀开粗时,余量留单边0.8mm,不能出现踩刀现象,不能使用Φ63R6加工范围较小的内型框。
挖槽开完粗后,要使用同一把刀具,将较大的平面再加工,保证底部留0.2mm余量,方便下一把刀具可以直接精加工工件底部。
10. 精铣前必须先用较小直径的刀将角位的余量粗清角,无法清角的地方,必须做曲面挡住,避免精铣时角位余量过多导致刀具损坏2、在二次开组选用参考刀具易造成过切或撞刀" R; _, b2 g q0 ^& f解决方法﹕在选用参考刀具时我们应当设置参考的刀具S" w+ N: m$ h) g! 比实际上一把刀具的直径大2~~3MM 牛鼻刀9 @( k* |/ z# q0 L/ S的话也要比之前的R角设置大点。
高速切削技术研究
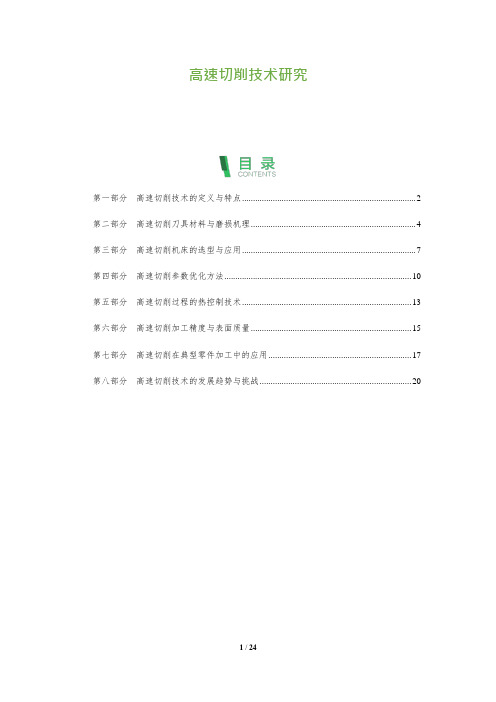
高速切削技术研究第一部分高速切削技术的定义与特点 (2)第二部分高速切削刀具材料与磨损机理 (4)第三部分高速切削机床的选型与应用 (7)第四部分高速切削参数优化方法 (10)第五部分高速切削过程的热控制技术 (13)第六部分高速切削加工精度与表面质量 (15)第七部分高速切削在典型零件加工中的应用 (17)第八部分高速切削技术的发展趋势与挑战 (20)第一部分高速切削技术的定义与特点高速切削技术是一种先进的制造工艺,它通过使用高转速的刀具和优化的切削参数来提高材料去除率、加工精度和表面质量。
该技术的核心在于实现高效率、高质量和高精度的加工过程。
在高速切削过程中,刀具以极高的速度旋转(通常超过每分钟数千转),同时进给速度也相应提高。
这种高速旋转产生的离心力有助于减小切削力和切削热,从而延长刀具寿命并减少工件的热变形。
此外,由于切削力的降低,高速切削还可以减少振动,进一步提高加工精度。
高速切削技术的优势主要体现在以下几个方面:1.高效率:与传统切削相比,高速切削可以显著提高材料去除率,缩短加工时间。
研究表明,高速切削可以提高生产效率达 30%至50%。
2.高精度:高速切削过程中的低切削力可以减少工件的振动,从而提高加工精度。
此外,由于切削热的影响较小,工件的热变形也得到了控制。
3.高质量表面:高速切削产生的切削热较低,这有助于减少工件的烧伤和裂纹,从而获得更好的表面质量。
4.刀具寿命延长:高速切削可以降低切削力,减少刀具磨损,从而延长刀具的使用寿命。
5.节能减排:高速切削技术可以实现更高的材料去除率,从而减少能源消耗和碳排放。
然而,高速切削技术也存在一些挑战,如刀具成本较高、对机床性能要求较高等。
因此,在实际应用中,需要根据具体加工需求和技术条件,合理选择切削参数和刀具,以确保高速切削技术的有效性和经济性。
总之,高速切削技术作为一种先进的制造工艺,具有高效率、高精度、高质量表面等优势,但在实际应用中需充分考虑其成本和设备要求。
高速加工技术

高速加工技术一.起源1931年,德国切削物理学家萨洛蒙(Carl.J.Salomon)博士提出了一个假设,即同年申请了德国专利的所罗门原理:被加工材料都有一个临界切削速度V0,在切削速度达到临界速度之前,切削温度和刀具磨损随着切削速度增大而增大,当切削速度达到普通切削速度的5~6倍时,切削刃口的温度开始随切削速度增大而降低,刀具磨损随切削速度增大而减小。
切削塑性材料时,传统的加工方式为“重切削”,每一刀切削的排屑量都很大,即吃刀大,但进给速度低,切削力大。
实践证明随着切削速度的提高,切屑形态从带状、片状到碎屑状演化,所需单位切削力在初期呈上升趋势,而后急剧下降,这说明高速切削比常规切削轻快,两者的机理也不同。
通过长期的研究,从上世纪90年代中期起,高速加工进入实用化阶段。
用户可以享受高速加工的高效率,高精度和成本优势。
德国OPS-INGERSOLL公司是目前世界上最好的高速加工中心制造商之一。
二.高速加工的定义高速加工是指转速在30,000RPM以上,实际加工切削进给保持8-12m/min的恒定进给。
我们从定义中看出,高速加工的一个关键要素是高速恒定进给。
由于高速加工时,转速上万转,特别在加工高硬度材料时,瞬间产生大量热量,所以必须保持高速进给,使产生的85%以上的热量被铁屑带走。
但在模具加工过程中,硬度通常在HRC50以上,且为复杂的曲面或拐角,所以高速机床必须做到在加工曲面或拐角时仍能高速进给。
另外实际加工中,刀具都有一个最佳切削参数,如能保持恒定进给,对刀具寿命,切削精度和加工表面质量都有提高。
由此看出,高速加工不仅是高速主轴,而且也是机床伺服系统的综合。
事实上,高速切削技术是一个非常庞大而复杂的系统工程,它涵盖了机床材料的研究及选用技术,机床结构设计和制造技术,高性能C NC控制系统、通讯系统,高速、高效冷却、高精度和大功率主轴系统,高精度快速进给系统,高性能刀具夹持系统,高性能刀具材料、刀具结构设计和制造技术,高效高精度测试测量技术,高速切削机理,高速切削工艺,适合高速加工的编程软件与编程策略等等诸多相关的硬件和软件技术。
数控铣工技师理论知识资料
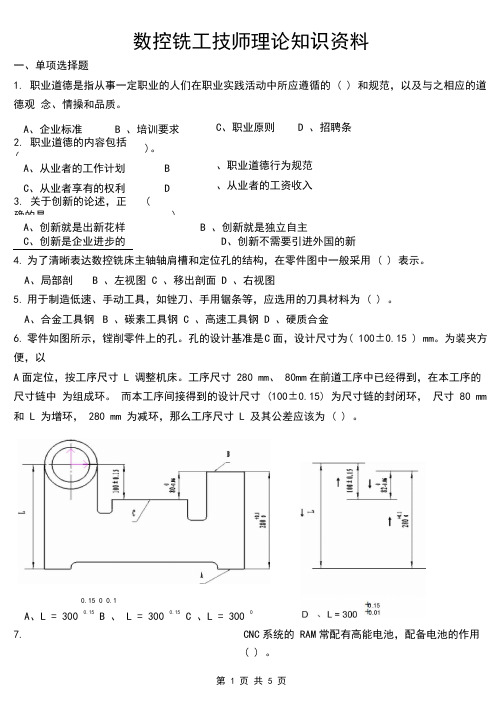
数控铣工技师理论知识资料一、单项选择题1. 职业道德是指从事一定职业的人们在职业实践活动中所应遵循的 ( ) 和规范,以及与之相应的道德观念、情操和品质。
A 、企业标准B 、培训要求C、职业原则 D 、招聘条件2. 职业道德的内容包括()。
A、从业者的工作计划 B 、职业道德行为规范C、从业者享有的权利 D 、从业者的工资收入3. 关于创新的论述,正确的是()A、创新就是出新花样 B 、创新就是独立自主C、创新是企业进步的灵魂D、创新不需要引进外国的新技术4.为了清晰表达数控铣床主轴轴肩槽和定位孔的结构,在零件图中一般采用 ( ) 表示。
A、局部剖 B 、左视图 C 、移出剖面 D 、右视图5.用于制造低速、手动工具,如锉刀、手用锯条等,应选用的刀具材料为 ( ) 。
A、合金工具钢 B 、碳素工具钢 C 、高速工具钢 D 、硬质合金6.零件如图所示,镗削零件上的孔。
孔的设计基准是C面,设计尺寸为( 100±0.15 ) mm。
为装夹方便,以A面定位,按工序尺寸 L 调整机床。
工序尺寸 280 mm、 80mm在前道工序中已经得到,在本工序的尺寸链中为组成环。
而本工序间接得到的设计尺寸 (100±0.15) 为尺寸链的封闭环,尺寸 80 mm 和 L 为增环, 280 mm 为减环,那么工序尺寸 L 及其公差应该为 ( ) 。
0.15 0 0.1A、L = 300 0.15 B 、 L = 300 0.15 C 、L = 300 0C系统的 RAM常配有高能电池,配备电池的作用( ) 。
A、保护 RAM不受损坏B、保护 CPU和 RAM之间传递信息不受干扰C、没有电池, RAM就不能工作D 、系统断电时,保护 RAM 中的信息不丢失8. 下列泵中,不能用作双向变量泵的是 ( ) 。
A 、径向柱塞泵 B 、轴向柱塞泵C 、齿轮泵 D、单作用式叶片泵C 系统软件是为实现 CNC 系统各项功能所编制的专用软件, 存放在计算机 ( )中。
精密加工课后习题答案
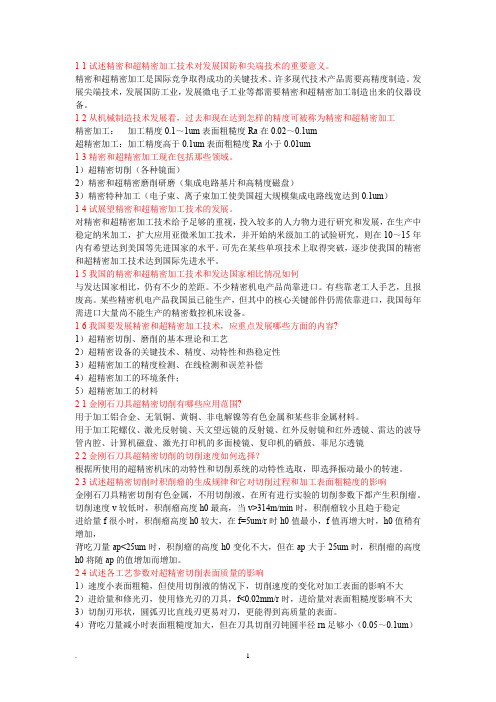
1-1试述精密和超精密加工技术对发展国防和尖端技术的重要意义。
精密和超精密加工是国际竞争取得成功的关键技术。
许多现代技术产品需要高精度制造。
发展尖端技术,发展国防工业,发展微电子工业等都需要精密和超精密加工制造出来的仪器设备。
1-2从机械制造技术发展看,过去和现在达到怎样的精度可被称为精密和超精密加工精密加工:加工精度0.1~1um表面粗糙度Ra在0.02~0.1um超精密加工:加工精度高于0.1um表面粗糙度Ra小于0.01um1-3精密和超精密加工现在包括那些领域。
1)超精密切削(各种镜面)2)精密和超精密磨削研磨(集成电路基片和高精度磁盘)3)精密特种加工(电子束、离子束加工使美国超大规模集成电路线宽达到0.1um)1-4试展望精密和超精密加工技术的发展。
对精密和超精密加工技术给予足够的重视,投入较多的人力物力进行研究和发展,在生产中稳定纳米加工,扩大应用亚微米加工技术,并开始纳米级加工的试验研究,则在10~15年内有希望达到美国等先进国家的水平。
可先在某些单项技术上取得突破,逐步使我国的精密和超精密加工技术达到国际先进水平。
1-5我国的精密和超精密加工技术和发达国家相比情况如何与发达国家相比,仍有不少的差距。
不少精密机电产品尚靠进口。
有些靠老工人手艺,且报废高。
某些精密机电产品我国虽已能生产,但其中的核心关键部件仍需依靠进口,我国每年需进口大量尚不能生产的精密数控机床设备。
1-6我国要发展精密和超精密加工技术,应重点发展哪些方面的内容?1)超精密切削、磨削的基本理论和工艺2)超精密设备的关键技术、精度、动特性和热稳定性3)超精密加工的精度检测、在线检测和误差补偿4)超精密加工的环境条件;5)超精密加工的材料2-1金刚石刀具超精密切削有哪些应用范围?用于加工铝合金、无氧铜、黄铜、非电解镍等有色金属和某些非金属材料。
用于加工陀螺仪、激光反射镜、天文望远镜的反射镜、红外反射镜和红外透镜、雷达的波导管内腔、计算机磁盘、激光打印机的多面棱镜、复印机的硒鼓、菲尼尔透镜2-2金刚石刀具超精密切削的切削速度如何选择?根据所使用的超精密机床的动特性和切削系统的动特性选取,即选择振动最小的转速。
等高铣削加工技术

1.3 等高铣削分类
常见的等高铣削包含的加工类型有型腔铣、粗铣角、 精铣角和陡壁加工几种。具体介绍如下: 1. 型腔铣 2.粗铣角 3.精铣角 4.陡壁加工
2 型腔铣实例
本节以型芯为实例讲解型腔铣,如图7所示。型 芯外形为圆柱形,顶面为圆弧面,材料为718H。 毛坯为圆柱体尺寸为148×62。本节对型芯做粗 加工(不包含台阶脚)。
1.1 曲面铣削子类型
在曲面铣削(mill_contour)模板里面操作子类型一 共是21个,如图2所示。当鼠标停留在某个子类型上 时,就会出现相应的名称,每个子类型按照图2里面 的顺序排列,对应的英文图标翻译成中文如表1所示。
1.2 曲面铣削分类
每一个子类型都有它特定的加工对象和切削方法, 但是在实际操作中有些子类型是相似的,操作步骤 也基本相同。为了方便学习和工作,按照加工的对 象的不同可以归为3大类,具体内容如下所示。 等高铣削:型腔铣到精铣角。 曲面加工:固定轮廓铣到区域轮廓铣陡峭。 清根加工:从单刀清根到3D轮廓铣。 其他:曲面文字到铣削控制。
等高铣削加工技术
等高铣削是刀具逐层切削材料的一种加 工类型。它适用于大量切削材料的粗加 工以及陡壁的精加工,比如腔体、凸台、 角落的二轴半加工。因为切削区域的壁 可以不垂直刀轴,所以等高铣削的对象 包含曲面形状的零件,如图1所示。
1 曲面铣削模板
曲面铣削(mill_contour)模板是针对于模具制造, 复杂零件加工推出的一系列加工方法。编制的程序 可以是二轴半加工、三轴联动加工。特别是曲面铣 削中使用过程毛坯(In Process Workpiece简称IPW) 和参考刀具。可以有效地减少空刀数量,优化刀具 运动轨迹。
2.5 刀轨设置
cimatron it 12 环绕等高
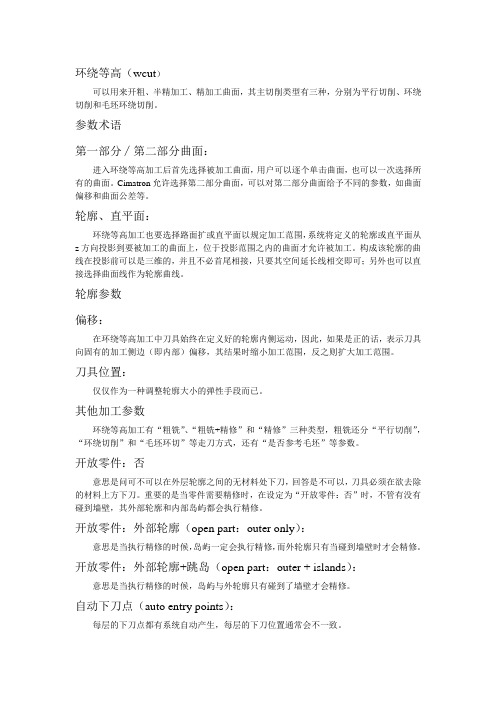
环绕等高(wcut)可以用来开粗、半精加工、精加工曲面,其主切削类型有三种,分别为平行切削、环绕切削和毛坯环绕切削。
参数术语第一部分∕第二部分曲面:进入环绕等高加工后首先选择被加工曲面,用户可以逐个单击曲面,也可以一次选择所有的曲面。
Cimatron允许选择第二部分曲面,可以对第二部分曲面给予不同的参数,如曲面偏移和曲面公差等。
轮廓、直平面:环绕等高加工也要选择路面扩或直平面以规定加工范围,系统将定义的轮廓或直平面从z方向投影到要被加工的曲面上,位于投影范围之内的曲面才允许被加工。
构成该轮廓的曲线在投影前可以是三维的,并且不必首尾相接,只要其空间延长线相交即可;另外也可以直接选择曲面线作为轮廓曲线。
轮廓参数偏移:在环绕等高加工中刀具始终在定义好的轮廓内侧运动,因此,如果是正的话,表示刀具向固有的加工侧边(即内部)偏移,其结果时缩小加工范围,反之则扩大加工范围。
刀具位置:仅仅作为一种调整轮廓大小的弹性手段而已。
其他加工参数环绕等高加工有“粗铣”、“粗铣+精修”和“精修”三种类型,粗铣还分“平行切削”,“环绕切削”和“毛坯环切”等走刀方式,还有“是否参考毛坯”等参数。
开放零件:否意思是问可不可以在外层轮廓之间的无材料处下刀,回答是不可以,刀具必须在欲去除的材料上方下刀。
重要的是当零件需要精修时,在设定为“开放零件:否”时,不管有没有碰到墙壁,其外部轮廓和内部岛屿都会执行精修。
开放零件:外部轮廓(open part:outer only):意思是当执行精修的时候,岛屿一定会执行精修,而外轮廓只有当碰到墙壁时才会精修。
开放零件:外部轮廓+跳岛(open part:outer + islands):意思是当执行精修的时候,岛屿与外轮廓只有碰到了墙壁才会精修。
自动下刀点(auto entry points):每层的下刀点都有系统自动产生,每层的下刀位置通常会不一致。
定义下刀点(defing entry points):由用户在图上指定一个点,每层的下刀都由该点开始运动到系统计算的自动下刀点,然后继续切削,此时可设定参数“建立进刀点:是”,以便在图上显示出该点与自动下刀点的关系。
高速铣削加工技术

模具高速铣削加工技术一、前言在现代模具生产中,随着对塑件的美观度及功能要求得越来越高,塑件内部结构设计得越来越复杂,模具的外形设计也日趋复杂,自由曲面所占比例不断增加,相应的模具结构也设计得越来越复杂。
这些都对模具加工技术提出了更高要求,不仅应保证高的制造精度和表面质量,而且要追求加工表面的美观。
随着对高速加工技术研究的不断深入,尤其在加工机床、数控系统、刀具系统、CAD/CAM软件等相关技术不断发展的推动下,高速加工技术已越来越多地应用于模具型腔的加工与制造中。
数控高速切削加工作为模具制造中最为重要的一项先进制造技术,是集高效、优质、低耗于一身的先进制造技术。
相对于传统的切削加工,其切削速度、进给速度有了很大的提高,而且切削机理也不相同。
高速切削使切削加工发生了本质性的飞跃,其单位功率的金属切除率提高了30%~40%,切削力降低了30%,刀具的切削寿命提高了70%,留于工件的切削热大幅度降低,低阶切削振动几乎消失。
随着切削速度的提高,单位时间毛坯材料的去除率增加了,切削时间减少了,加工效率提高了,从而缩短了产品的制造周期,提高了产品的市场竞争力。
同时,高速加工的小量快进使切削力减少了,切屑的高速排出减少了工件的切削力和热应力变形,提高了刚性差和薄壁零件切削加工的可能性。
由于切削力的降低,转速的提高使切削系统的工作频率远离机床的低阶固有频率,而工件的表面粗糙度对低阶频率最为敏感,由此降低了表面粗糙度。
在模具的高淬硬钢件(HRC45~HRC65)的加工过程中,采用高速切削可以取代电加工和磨削抛光的工序,从而避免了电极的制造和费时的电加工,大幅度减少了钳工的打磨与抛光量。
对于一些市场上越来越需要的薄壁模具工件,高速铣削也可顺利完成,而且在高速铣削CNC加工中心上,模具一次装夹可完成多工步加工。
高速加工技术对模具加工工艺产生了巨大影响,改变了传统模具加工采用的“退火→铣削加工→热处理→磨削”或“电火花加工→手工打磨、抛光”等复杂冗长的工艺流程,甚至可用高速切削加工替代原来的全部工序。
磨削加工技术
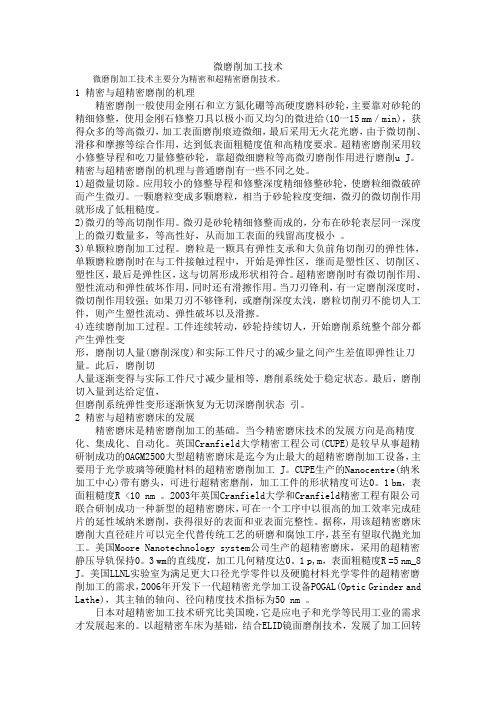
微磨削加工技术微磨削加工技术主要分为精密和超精密磨削技术。
1 精密与超精密磨削的机理精密磨削一般使用金刚石和立方氮化硼等高硬度磨料砂轮,主要靠对砂轮的精细修整,使用金刚石修整刀具以极小而又均匀的微进给(1O一15 mm/min),获得众多的等高微刃,加工表面磨削痕迹微细,最后采用无火花光磨,由于微切削、滑移和摩擦等综合作用,达到低表面粗糙度值和高精度要求。
超精密磨削采用较小修整导程和吃刀量修整砂轮,靠超微细磨粒等高微刃磨削作用进行磨削u J。
精密与超精密磨削的机理与普通磨削有一些不同之处。
1)超微量切除。
应用较小的修整导程和修整深度精细修整砂轮,使磨粒细微破碎而产生微刃。
一颗磨粒变成多颗磨粒,相当于砂轮粒度变细,微刃的微切削作用就形成了低粗糙度。
2)微刃的等高切削作用。
微刃是砂轮精细修整而成的,分布在砂轮表层同一深度上的微刃数量多,等高性好,从而加工表面的残留高度极小。
3)单颗粒磨削加工过程。
磨粒是一颗具有弹性支承和大负前角切削刃的弹性体,单颗磨粒磨削时在与工件接触过程中,开始是弹性区,继而是塑性区、切削区、塑性区,最后是弹性区,这与切屑形成形状相符合。
超精密磨削时有微切削作用、塑性流动和弹性破坏作用,同时还有滑擦作用。
当刀刃锋利,有一定磨削深度时,微切削作用较强;如果刀刃不够锋利,或磨削深度太浅,磨粒切削刃不能切人工件,则产生塑性流动、弹性破坏以及滑擦。
4)连续磨削加工过程。
工件连续转动,砂轮持续切人,开始磨削系统整个部分都产生弹性变形,磨削切人量(磨削深度)和实际工件尺寸的减少量之间产生差值即弹性让刀量。
此后,磨削切人量逐渐变得与实际工件尺寸减少量相等,磨削系统处于稳定状态。
最后,磨削切入量到达给定值,但磨削系统弹性变形逐渐恢复为无切深磨削状态引。
2 精密与超精密磨床的发展精密磨床是精密磨削加工的基础。
当今精密磨床技术的发展方向是高精度化、集成化、自动化。
英国Cranfield大学精密工程公司(CUPE)是较早从事超精研制成功的OAGM2500大型超精密磨床是迄今为止最大的超精密磨削加工设备,主要用于光学玻璃等硬脆材料的超精密磨削加工 J。
常用切削速度计算公式
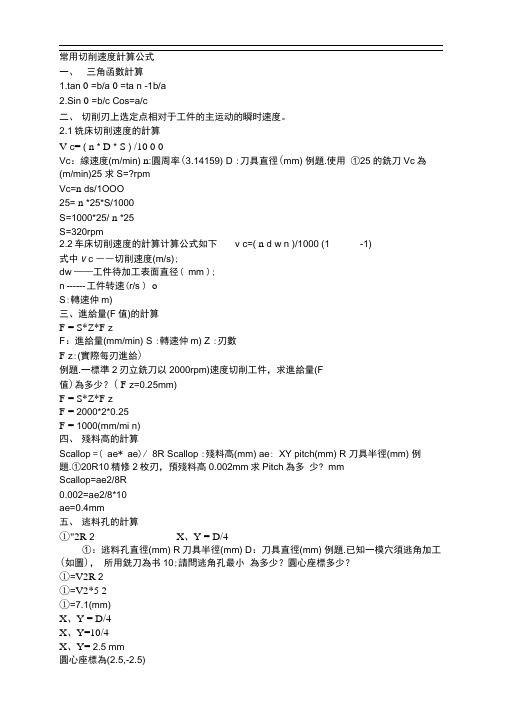
常用切削速度計算公式一、三角函數計算1.tan 0 =b/a 0 =ta n -1b/a2.Sin 0 =b/c Cos=a/c二、切削刃上选定点相对于工件的主运动的瞬时速度。
2.1铣床切削速度的計算V c= ( n * D * S ) /10 0 0Vc:線速度(m/min) n:圓周率(3.14159) D :刀具直徑(mm) 例題.使用①25的銑刀Vc為(m/min)25 求S=?rpmVc=n ds/1OOO25= n *25*S/1000S=1000*25/ n *25S=320rpm2.2车床切削速度的計算计算公式如下v c=( n d w n )/1000 (1 -1)式中v c ――切削速度(m/s);dw ——工件待加工表面直径( mm );n ------ 工件转速(r/s ) oS:轉速仲m)三、進給量(F值)的計算F = S*Z*F zF:進給量(mm/min) S :轉速仲m) Z :刃數F z:(實際每刃進給)例題.一標準2刃立銑刀以2000rpm)速度切削工件,求進給量(F值)為多少?(F z=0.25mm)F = S*Z*F zF = 2000*2*0.25F = 1000(mm/mi n)四、殘料高的計算Scallop =( ae* ae)/ 8R Scallop :殘料高(mm) ae: XY pitch(mm) R 刀具半徑(mm) 例題.①20R10精修2枚刃,預殘料高0.002mm求Pitch為多少? mmScallop=ae2/8R0.002=ae2/8*10ae=0.4mm五、逃料孔的計算①"2R 2 X、Y = D/4①:逃料孔直徑(mm) R刀具半徑(mm) D:刀具直徑(mm) 例題.已知一模穴須逃角加工(如圖),所用銑刀為书10;請問逃角孔最小為多少?圓心座標多少?①=V2R 2①=V2*5 2①=7.1(mm)X、Y = D/4X、Y=10/4X、Y= 2.5 mm圓心座標為(2.5,-2.5)六、取料量的計算Q=( ae* ap*F)/10 0 0Q: 取料量(cm3/min) ae:XY pitch(mm) ap : Z pitch(mm)例題.已知一模仁須cavity等高加工,①35R5的刀XY pitch是刀具的60%每層切1.5mm進給量為2000mm/min求此刀具的取料量為多少?Q=( ae* ap*F)/1000Q= 35*0.6*1.5*2000 /1000Q = 63 cm3/min七、每刃進給量的計算F z =h m * V ( D/ ap )F z:實施每刃進給量h m 理論每刃進給量ap : Z pitch(mm)D:刀片直徑(mm)例題(前提depo XY pitch 是刀具的60%)depo①35R5的刀,切削NAK80材料h m為0.15mm Z軸切深1.5mm 求每刃進給量為多少?F z =h m * V ( D/ ap )F z = 0.2* V 10/1.5F z= 0.5mm沖模刀口加工方法刀口加工深度=板厚—刀口高+鉆尖(0.3D)D表示刀徑鑽頭鑽孔時間公式T(min)=L(min)/N(rpm)*f(mm/rev) =nDL/1000vfL:鑽孔全長N:回轉數f:進刀量系數D:鑽頭直徑v:切削速度如圖孔深1 鑽頭孔全長L 則L=l+D/3T=L/Nf=nDL/1000vf系數表f 直徑mm 進刀mm/rev1.6~3.2 0.025~0.0753.2~6.4 0.05~0.156.4~12.8 0.10~0.2512.8~25 0.175~0.37525 以上0.376~0.6251英寸=25.4mm=8分25.4/牙數二牙距管牙計算公式例如25.4/18 = 1.414 牙距為5/16絲攻馬力(槍鑽)W=Md*N/97.410W:所要動力(KW)Md:扭矩(kg — cm)N:回轉數(r . p . m)扭矩計算公式如下:Md=1/20*f*ps*f為進給量mm/rev系數r為鑽頭半徑賽(mm)a:切削抵抗比值ps.在小進給時,一般鋼為5 0 0 kg/mtf; 一般鑄鐵為300kg/mtf; B1-400K立式升降台铣床主要参数介绍项目单位XA5032 B1-400K 工作面积宽*长mm 320*1250 400*1600工作台承载重量kg 500 800 T型槽数目个 3 3T型槽宽度mm 18 18T型槽间距mm 70 90X向(工作台纵向)手动/机动mm 700/680 900/880行程Y向(滑座横向)手动/机动mm 255/240 315/300 Z向(升降台垂向)手动/机动mm 370/350 385/365 最大回转角度deg ±45 ±45转速r/min 30-1500 300-1500转速级数Step 18 18锥孔ISO7 : 24 NO.50 ISO7 : 24 NO.50 主轴轴向移动距离mm 85 85 主轴端面至工作台距离最小/最大mm 45/415 30/500 主轴中心线至床身垂直导轨面距离mm 350 450切削进给速度mm/minX , Y : 23.5-1180, Z:8-394 X : 19-950 Y : 12.6-634 Z:6.3-317进给快速移动进给速度mm/min X, Y: 2300, Z: 770 X, Y: 2300, Z: 770 进给级数Step 18 18电动主轴电机功率KW 7.5 11机进给电机功率KW 1.5 3其他机床外形尺寸(长*宽*高)mm 2272*1770*2094 2556*2159*2298 机床净重(约)kg 2800 4250。
机械制造基础教材试题及答案
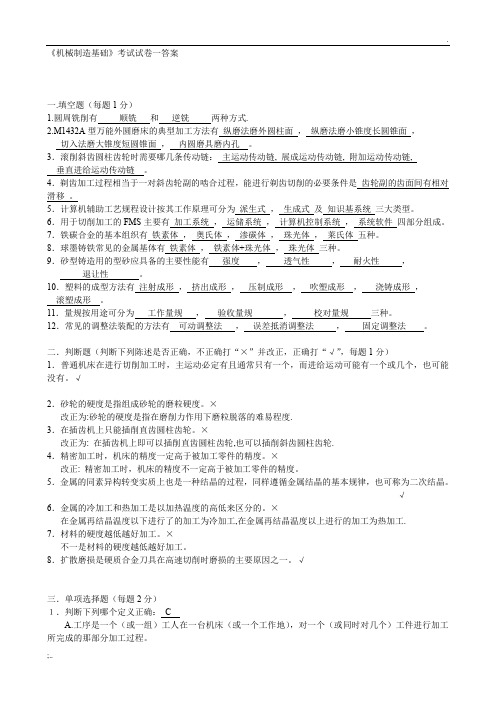
《机械制造基础》考试试卷一答案一.填空题(每题1分)1.圆周铣削有顺铣和逆铣两种方式.2.M1432A型万能外圆磨床的典型加工方法有纵磨法磨外圆柱面,纵磨法磨小锥度长圆锥面,切入法磨大锥度短圆锥面,内圆磨具磨内孔。
3.滚削斜齿圆柱齿轮时需要哪几条传动链:主运动传动链, 展成运动传动链, 附加运动传动链,垂直进给运动传动链。
4.剃齿加工过程相当于一对斜齿轮副的啮合过程,能进行剃齿切削的必要条件是齿轮副的齿面间有相对滑移。
5.计算机辅助工艺规程设计按其工作原理可分为派生式,生成式及知识基系统三大类型。
6.用于切削加工的FMS主要有加工系统,运储系统,计算机控制系统,系统软件四部分组成。
7.铁碳合金的基本组织有铁素体,奥氏体,渗碳体,珠光体,莱氏体五种。
8.球墨铸铁常见的金属基体有铁素体,铁素体+珠光体,珠光体三种。
9.砂型铸造用的型砂应具备的主要性能有强度,透气性,耐火性,退让性。
10.塑料的成型方法有注射成形,挤出成形,压制成形,吹塑成形,浇铸成形,滚塑成形。
11.量规按用途可分为工作量规,验收量规,校对量规三种。
12.常见的调整法装配的方法有可动调整法,误差抵消调整法,固定调整法。
二.判断题(判断下列陈述是否正确,不正确打“×”并改正,正确打“√”,每题1分)1.普通机床在进行切削加工时,主运动必定有且通常只有一个,而进给运动可能有一个或几个,也可能没有。
√2.砂轮的硬度是指组成砂轮的磨粒硬度。
×改正为:砂轮的硬度是指在磨削力作用下磨粒脱落的难易程度.3.在插齿机上只能插削直齿圆柱齿轮。
×改正为: 在插齿机上即可以插削直齿圆柱齿轮,也可以插削斜齿圆柱齿轮.4.精密加工时,机床的精度一定高于被加工零件的精度。
×改正: 精密加工时,机床的精度不一定高于被加工零件的精度。
5.金属的同素异构转变实质上也是一种结晶的过程,同样遵循金属结晶的基本规律,也可称为二次结晶。
精密加工与特种加工

第一阶段测试卷考试科目:《精密加工与特种加工》第一章至第三章(总分100分)时间:90分钟__________学习中心(教学点)批次:层次:专业:学号:身份证号:姓名:得分:一、填空题(每空1分,共10分)1、超精密加工对机床的基本要求是:、高刚度、、高自动化。
2、微量切削加工中,由于材料晶粒的机械性能不同产生的的影响,使得材料纯度越高加工质量越好。
3、精密切削时被挤压的材料在刀具移过之后,工件加工表面形成隆起,称之为。
4、精密加工对环境条件的要求主要有、、空气洁净。
5、超硬磨料砂轮的修整包括和两个过程。
6、金刚石晶体主要的晶面指数有(100)晶面、、。
二、判断题(正确的打√,错误的打×,每小题1分,共10分)1、金刚石刀具尖刃安装方便,磨损后需要立即重磨。
()2、超硬磨料砂轮可以磨削陶瓷但不能磨削铁类黑色金属。
()3、金刚石刀具常用来加工陶瓷、玻璃等硬脆材料。
()4、金刚石刀具方向选择不当,在切削力作用下,刀具可能产生解理劈开。
()5、金刚石刀具切削加工进给量对表面质量的影响很大程度上取决于刀具的几何形状。
()6、一般常用金刚石刀具加工硬质合金、铸铁等材料。
()7、金刚石刀具精密切削时,为获得高质量表面,一定要采用高的加工速度。
()8、多面镜可以用金刚石刀具进行车削。
()9、微量切削时,由于晶界段差的影响,晶粒越细工件表面质量越好。
()10、切削深度的分辨率是指切削厚度的稳定性。
()三、单项选择题(从以下选项中选出1个正确答案,每小题1分,共15分)1、下列哪种方法不是金刚石晶体的定向方法。
A、人工目测B、激光定向C、X射线定向D、离心法2、下列四个选项中,属于超硬磨料的是。
A、白刚玉B、棕刚玉C、立方氮化硼D、碳化硼3、下列哪个选项不是精密超精密机床上采用的导轨的结构形式。
A、空气静压导轨B、液体静压导轨C、气浮导轨D、滑动导轨4、下列精度不属于当前精密加工精度范围的是。
A、1-0.1umB、0.01mmC、Ra0.01umD、Rmax0.2um5、由于金刚石刀具材料很高,所以对机床动态精度及抗振性要求高。
高速切削对数控编程的具体要求

高速切削对数控编程的具体要求
1. 切削参数要求,高速切削对数控编程要求合理选择切削速度、进给速度和切削深度等参数。
切削速度要保持在合适的范围内,以
确保切削效率和刀具寿命的平衡。
进给速度要根据材料的硬度、切
削力和刀具的性能等因素进行调整,以实现高效的切削。
切削深度
要根据工件的要求和刀具的稳定性来确定。
2. 刀具选择要求,高速切削要求选择合适的刀具。
刀具的材料、刃数、刃角、刃长等参数需要根据切削材料、切削条件和加工要求
进行选择。
高速切削一般需要使用硬质合金刀具或涂层刀具,以提
高切削速度和刀具寿命。
3. 编程技巧要求,高速切削对数控编程的要求包括合理的刀具
路径规划、平滑的切削轨迹和精确的切削参数控制。
刀具路径要避
免多余的刀具运动,减少空程时间,提高切削效率。
切削轨迹要尽
量平滑,避免急剧的变化和过大的加速度,以减少振动和刀具的应力。
切削参数的控制要准确,包括切削速度、进给速度、切削深度、切削角度等,以保证加工质量和刀具寿命。
4. 程序调试要求,高速切削对数控编程的程序调试要求严格。
需要对程序进行充分的模拟和验证,确保刀具路径和切削参数的准确性。
同时,还需要进行切削试验和切削力的监测,以调整和优化切削参数,提高切削效率和加工质量。
综上所述,高速切削对数控编程的具体要求包括合理选择切削参数、选择合适的刀具、掌握编程技巧和进行程序调试等方面。
这些要求的达成可以提高加工效率、降低成本和提高产品质量。
钨钢铣刀的使用技巧

30°螺旋角 2刃 30°螺旋角 4刃 45°螺旋角 3刃
3刃立铣刀下记理由使它的形状能抑制振颤与刚性同时兼有、侧面加工和槽加工同时可对应 第一:不同于偶数刃,切削刃没有处在对角线上,具有振颤不易发生的特点 第二:衡量刚性的指标有刃径的芯厚与维持刚性的形状等. 30°平刀芯厚占65%;45°平刀芯厚占70%; 15°的芯厚以上的随形状可实现刚性
●螺旋角的选定
不锈钢的热传导率低,对刀尖的影响大的难削材的切削、使用大 螺旋角的立铣刀对刀具的寿命是有利的。高硬度的被削材,随着 硬度的增加,切削抵抗将加大,大螺旋角的立铣刀对刀具寿命有 利. 另一方面,选择大螺旋角的刀具易造成切削抵抗的增大.右螺旋 的刀具,作用在刀具上的切削抵抗向下,使得刀具容易脱落,所以, 采用刚性高的刀柄的对策有必要. 即便确保了刀具的刚性、对于薄板加工等工件刚性低的情况,有 时采用小螺旋角的立铣刀.
切削路径对刀具的影响 ●高速加工首选等高切削
等高切削
仿形切削
为了得到最长的刀具寿命,在铣削过程中应使切削刃尽可能长时间地保持连续切削, 最好是顺铣.在这方面采用等高线铣削是最好方法,它能让刀具始终沿着一个方向切削, 受力变化是最小的. 而仿形铣削路径常常是逆铣和顺铣的混合(之字形),这意味切削中会频繁地吃刀和 退刀,切削刃和切削过程便更容易受到工作负载和方向改变的不利影响,工作负载和方 向的变会引起切削力和刀具弯曲的变化,使刀具产生崩刃或异刚性刀具切削刃部的退让可以抑制.短刃长、大直径、多刃数是保持高刚性 的刀具
多段加工的有效性
短刃刀具具有高刚性,侧面加工时柄部易发生干涉.为了避免干涉,(避空)比刀具刃 径小、设定颈长的细长刀具使用是非常有必要的. 若有这类刀具,Z方向的多段加工成为可能.同时切削速度、进给速度可以实现高速, 实现加工时间缩短.
mastercam曲面等高螺旋限制

一、介绍mastercam软件mastercam是一款广泛应用于机械制造和数控加工领域的CAD/CAM 软件,其功能强大,易于使用。
mastercam可以帮助用户进行零件的建模、工艺规划、数控编程等工作,广泛应用于模具制造、航空航天、汽车零部件等行业。
二、mastercam曲面等高螺旋限制的概念曲面等高螺旋限制是mastercam软件中的一种加工限制,主要用于在曲面上进行等高螺旋切削加工。
在实际操作中,曲面雕铣通常采用等高螺旋加工,能够提高加工效率、表面质量和工件寿命。
使用曲面等高螺旋限制可以实现更加精准的加工,提高工件的质量和精度。
三、曲面等高螺旋限制的应用1. 曲面等高螺旋限制在模具制造中的应用在模具制造中,常常需要对复杂曲面进行加工,采用曲面等高螺旋限制能够实现高效、精确的加工,提高模具的质量和生产效率。
2. 曲面等高螺旋限制在航空航天领域的应用航空航天零部件通常具有复杂的曲面结构,采用曲面等高螺旋限制可以实现对零件的高精度加工,确保零部件的质量和性能。
3. 曲面等高螺旋限制在汽车零部件加工中的应用汽车零部件的加工通常需要对曲面进行高精度的切削,采用曲面等高螺旋限制可以提高加工效率、降低成本,同时确保零部件的质量和稳定性。
四、mastercam曲面等高螺旋限制的特点1. 简单易操作mastercam软件具有友好的用户界面和丰富的操作指南,使得曲面等高螺旋限制的操作变得简单易懂,即使对于初学者也能够迅速上手。
2. 灵活多样mastercam软件支持丰富的处理方式和加工策略,用户可以根据不同的加工需求选择合适的曲面等高螺旋限制方式,在满足加工质量的前提下,实现加工效率的最大化。
3. 精度高mastercam软件对曲面等高螺旋限制的实现,能够保证加工精度和表面质量,满足高精度加工的需求。
5、mastercam曲面等高螺旋限制的操作步骤1. 打开mastercam软件,选择相应的加工工艺和零件模型。
等高块的加工方法
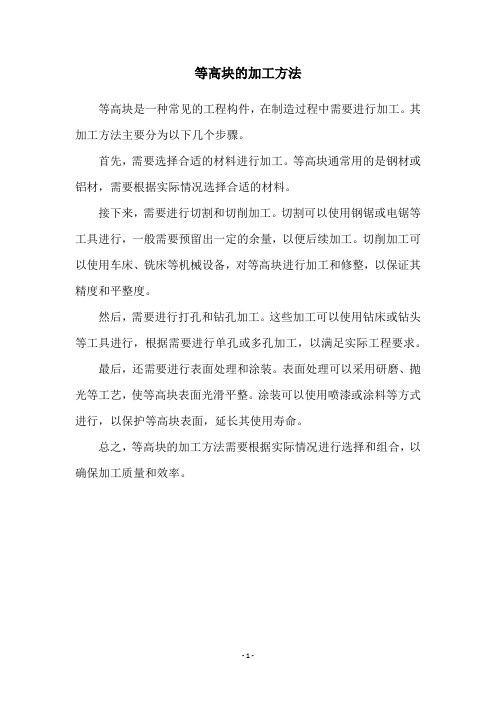
等高块的加工方法
等高块是一种常见的工程构件,在制造过程中需要进行加工。
其加工方法主要分为以下几个步骤。
首先,需要选择合适的材料进行加工。
等高块通常用的是钢材或铝材,需要根据实际情况选择合适的材料。
接下来,需要进行切割和切削加工。
切割可以使用钢锯或电锯等工具进行,一般需要预留出一定的余量,以便后续加工。
切削加工可以使用车床、铣床等机械设备,对等高块进行加工和修整,以保证其精度和平整度。
然后,需要进行打孔和钻孔加工。
这些加工可以使用钻床或钻头等工具进行,根据需要进行单孔或多孔加工,以满足实际工程要求。
最后,还需要进行表面处理和涂装。
表面处理可以采用研磨、抛光等工艺,使等高块表面光滑平整。
涂装可以使用喷漆或涂料等方式进行,以保护等高块表面,延长其使用寿命。
总之,等高块的加工方法需要根据实际情况进行选择和组合,以确保加工质量和效率。
- 1 -。
中望3D之CAM加工全体验

中望3D之CAM加工全体验出处:天空软件作者:佚名日期:2010-12-30关键字:中望3D是一款CAD/CAM一体化的高端三维设计软件,拥有非常强大的CAM功能,能支持2-5轴联动加工,同时也是国内唯一一款拥有全球自主知识产权的三维CAD软件。
作为一名CAD设计师,一直都非常希望能实地感受一下中望3D的CAM功能。
最近终于找到了机会,进行了实际的机床操作。
接下来,我就和大家分享一下中望3D之CAM加工的体验和心得。
首先我想和大家分享一下中望3D这款软件的一些特点。
与其他的软件的CAM模块相比,中望3D有一些非常显著的优点:进给速度控制比较好,同一刀路有变速控制(如下图),在默认情况下是采用倾斜角进刀方式,保护了工件表面质量。
面向业内熟练者,提供非常多的速度控制,可以让高手把加工速度更上一层楼。
其默认参数合理,足以让初学者应付常见问题的解决。
如果能根据材质和刀具自动给出其默认参数,个人认为会更加震撼。
Z轴转角半径控制。
在进刀时在Z轴以圆弧方式切入工件,该功能独特(别的软件没有)。
快速切削功能:省略了很多参数的设置,默认参数的提供减轻了设置时的繁琐。
过多的参数控制有时会让不熟悉软件的使用者茫然,无从下手。
加工方式比较齐全。
接下来我想谈谈在实际操作过程中的一些加工技巧。
从产品设计到加工制造,是一项繁琐而精细的事务。
在整个流程中,我们需要理解各步骤的关键地方和要诀,避免出现安全事故,以下列举一些原则和方法。
开粗的意义:在机床载荷承受范围内,在加工绝大部分的情况下,尽可能的采用大的刀具,尽可能大的进给,尽可能快的进刀量,达到快速高效的去掉切削胚料,为后面的半精和精加工创造有力的条件。
选刀的原则:根据产品的二维角与三维弧的曲率半径来选择,稍微小一点。
钻孔的方法:一般在钻孔前,都要用中心钻钻一个小孔,再钻孔。
在工厂一般采用螺旋下刀的方式,省略了这一步。
加工步骤:一般分三步进行:开粗(多次开粗),半精加工,精加工。
- 1、下载文档前请自行甄别文档内容的完整性,平台不提供额外的编辑、内容补充、找答案等附加服务。
- 2、"仅部分预览"的文档,不可在线预览部分如存在完整性等问题,可反馈申请退款(可完整预览的文档不适用该条件!)。
- 3、如文档侵犯您的权益,请联系客服反馈,我们会尽快为您处理(人工客服工作时间:9:00-18:30)。
(8)在个别加工曲面上,可以设定不同的加工预留量
在模具设计中,由于成品几何形状的规范,往往需要定义不同的壁厚、合模面、靠破面及一般成品面。为了方便NC程序设计师在单一CAD模型上设定NC程序,UG让NC设计师在个别加工曲面上设定不同的预留量(正值及负值),以提高NC程式的设计效率。
加工素材及成品体的运作,让使用者在不修改CAD模型的情形下,能便利地进行等高粗加工及精加工的计算。对于模具电极及滑块的NC程序制作非常方便。
D资料,经常是上游所提供的IGES档案。因此加工用的CAD模型的曲面之间常会有间隙及重叠的情形。UG提供允差切削功能,在使用者设定的公差范围内能自动处理曲面间的间隙及重叠,从而产生良好的刀具路径。
(5)在不同高度区域设定不同切削深度
为了在加工后能留下均匀的毛坯,同时又不耗费不必要的加工时间,UG可提供使用者按加工工件的形状特性,在不同的高度区域中设定不同的切削深度。在完成多层沿面中加工时,在陡峭区域可设定较大的切削深度,在平缓区域设定较小切削深度。
(6)具有加工素材及成品体的观念
等高切削
等高切削在模具加工上,主要用于需要刀具受力均匀的加工条件下。应用等高切削可以完成数控加工中80%的工作量。例如粗加工时,一般刀具受力极大,因此等高切削能以控制切深的方式,将刀具受力限制在一个范围内。此外,在中加工或精加工时,如果加工部位太陡、太深、需要延长加长刀刃的情形,由于刀具太长,加工时偏摆太大,往往也需要用等高切削的方式来减少刀具受力。目前最流行的高速切削机床,也是等高切削的使用者。
模具是目前应用CAD/CAM最普遍和最先进的行业之一。在模具加工中,为了使数据能够在数控加工机床上应用,必然要用到CAM编程。目前比较流行的CAM软件有UG,Cimatron,MasterCAM,DELCAM powerMILL,EDGECAM,HZS space-E等。
在UG的发展过程中,CAM一直是加工业者最可靠的工作伙伴。它不仅提供可靠、精确的刀具路径,更让NC程序设计师可以随心所欲地设计出心目中最有效的加工程序。CIMdata的调查报告指出,EDS UG被视为所有CAM软体供应商中最强大的竞争者。
(2)自动探测undercut区域
UG能自动探测加工范围内的undercut区域,并自动计算出最佳的刀具路径。用T型刀铣切时,若刀柄与加工面不发生干涉,UG尽可能作最完整的切削。由于用平刀切削,因此在undercut区域,UG产生的刀具路径以刀具不碰到加工面为原则。
(3)提供多样化的刀具路径型式
UG的等高切削功能不仅提供多样化的加工方式,同时允许刀具在整个加工过程中能在均匀的受力状态下实现最快、最好的切削。以下是UG等高切削的特性。
(1)刀具使用没有限制
NC程序设计师可以依照加工机床的性能、毛坯材质、夹持方式以及对切削效率的考虑,自由选用平刀、球刀、圆鼻刀、T型刀等刀具进行等高切削。在计算上,UG利用所选用的刀具,分层沿等加工面计算,所以能产生准确的刀具路径。
UG等高切削提供住复式切削、单向切削、螺旋切削、沿边切削及多层沿边切削。其中多层沿边切削可提供高效率的粗毛坯加工路径,也是深陡加工面精加工的良好选择。高速切削机床可利用此功能生成良好的加工路径。多层沿边切削的刀具路径的每一深度上产生3道刀具路径,第一道离成品面3mm,第二道离成品面1mm,第三道则加工在成品面上。
(9)提供多种进/退刀方式
UG等高切削提供直线、折线、圆弧等多种进/退刀方式,来满足实际加工的需要。使用者同时能在不同深度区域或加工区域设定不同的预钻孔位置及钻孔深度。UG在进刀时亦能依加工几何形状及刀具定义,自动决定由预钻孔进刀或斜向进刀,以符合实际加工要求。
(4)产生刀具受力均匀的加工路径
模具加工时,NC程序设计师或机床操作员往往为了避免NC程序中刀具局部受力过大而造成刀具严重损耗的情形,不得不降低整体路径的进给速率,从而影响了整个加工效率。UG提供多样的进给速率设定方式来解决这个问题。使用者可以设定刀具局部受力的进给率(如第一刀切削,刀具路径往复时刀具路径转角时)。
(5)提供完整的刀具库及加工参数库管理功能,使新进人员能充分利用资深人员的经验,设计优良的刀具路径。
(6)提供泛用型后处理功能,产生各NC加工机床适用的NC程式。
UG CAM包含二轴到五轴铣削、线切割、大型刀具库管理、实体模拟切削及泛用型后处理器等功能。本文将介绍三轴铣削中等高切削在模具加工上的应用。
UG CAM有下列几个特点:
(1)提供可靠、精确的刀具路径。
(2)能直接在曲面及实体上加工。
(3)良好的使用者界面,允许使用者能依工作上的需要,定制使用者界面,不仅能提高作业效率,同时能有效使用及保存公司的Know-How。
(4)提供多样性的加工方式,方便NC程序设计师设计各种高效率的刀具路径。