过程失效模式及后果分析程序OK
过程失效模式和后果分析程序
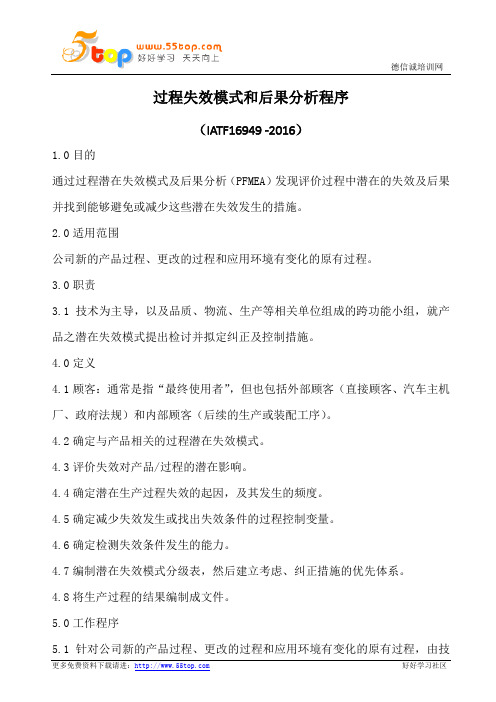
过程失效模式和后果分析程序(IATF16949 -2016)1.0目的通过过程潜在失效模式及后果分析(PFMEA)发现评价过程中潜在的失效及后果并找到能够避免或减少这些潜在失效发生的措施。
2.0适用范围公司新的产品过程、更改的过程和应用环境有变化的原有过程。
3.0职责3.1技术为主导,以及品质、物流、生产等相关单位组成的跨功能小组,就产品之潜在失效模式提出检讨并拟定纠正及控制措施。
4.0定义4.1顾客:通常是指“最终使用者”,但也包括外部顾客(直接顾客、汽车主机厂、政府法规)和内部顾客(后续的生产或装配工序)。
4.2确定与产品相关的过程潜在失效模式。
4.3评价失效对产品/过程的潜在影响。
4.4确定潜在生产过程失效的起因,及其发生的频度。
4.5确定减少失效发生或找出失效条件的过程控制变量。
4.6确定检测失效条件发生的能力。
4.7编制潜在失效模式分级表,然后建立考虑、纠正措施的优先体系。
4.8将生产过程的结果编制成文件。
5.0工作程序5.1针对公司新的产品过程、更改的过程和应用环境有变化的原有过程,由技术主动联络生产、物流、品质、采购等有关部门的相关人员组成PFMEA小组。
5.2PFMEA小组负责分析或重新确认过程流程图中各过程的风险程度,形成书面的过程流程图/风险评定表。
5.3PFMEA小组负责确定关键日期(初次FMEA预定完成日期,该日期不应超过计划开始生产的日期)和进行过程潜在失效模式及后果的分析,形成《PFMEA 表》,并按《技术文件和资料有效状态控制规定》进行编号。
5.4PFMEA分析管理如下:5.4.1列出被分析过程或工序并尽可能简单说明该过程或工序的目的。
5.4.2针对每一个过程或工序,列出每一个潜在的失效模式。
5.4.3列出每一个潜在的失效模式对顾客(包括最终使用者、外部顾客、内部顾客)产生的影响后果。
5.4.4按下述严重度评价准则确定每一个失效模式产生的影响后果的级别。
后果最终使用者外部顾客和内部顾客严重度级别无警告的危险当失效模式影响到车辆运行安全和/或牵连到违反政府法规时,无警告产生。
PFMEA过程失效模式及后果分析

PFMEA过程失效模式及后果分析PFMEA(Process Failure Mode and Effects Analysis)过程失效模式及后果分析是一种常用的质量管理工具,用于评估和改进产品制造过程中的潜在问题和风险。
它旨在预测和预防可能导致产品失效的过程步骤。
1.确定过程步骤:首先,识别和定义产品制造过程中的每个关键步骤,包括原材料采购、加工、装配、测试等。
2.确定失效模式:对于每个过程步骤,识别可能导致失效的模式。
失效模式可以是设备故障、人为错误、材料质量问题等。
3.评估失效后果:对于每个失效模式,评估其可能导致的后果和影响。
后果可以涉及到产品质量问题、安全风险、客户满意度等。
4.定义风险优先级:根据失效模式的严重性、发生频率和检测能力,为每个失效模式分配一个风险优先级。
这可以帮助制定合理的风险控制策略。
5.制定改进计划:对于评估出的高优先级失效模式,制定相应的改进计划和控制措施。
这可能包括优化生产工艺、提供培训和教育、改进设备维护等。
6.实施和监控措施:执行改进计划,并监控其有效性。
定期对PFMEA进行更新,以反映过程改进和新的风险评估。
通过实施PFMEA,可以有效地识别和消除潜在的制造过程问题,并降低产品质量问题的风险。
下面以汽车制造业为例,具体分析PFMEA的应用。
在汽车制造过程中,每个制造步骤都可能存在潜在的失效模式。
例如,原材料采购环节可能存在材料质量问题的风险,加工环节可能存在操作错误或设备故障的风险,装配环节可能存在组装错误或安装不良的风险,测试环节可能存在测试不准确或设备故障的风险。
针对这些潜在问题,可以使用PFMEA来识别并评估其风险。
例如,在加工环节,识别可能的失效模式可能包括不正确的参数设置、设备故障、操作错误等。
然后,评估这些失效模式可能导致的后果和影响,如产品偏差、生产延误、设备故障等。
根据评估结果,确定失效模式的风险优先级,以便制定相应的改进计划和控制措施。
例如,对于评估为高风险的加工失效模式,可以采取以下改进措施:加强对操作员的培训和教育,确保他们正确操作设备和设置参数;增加设备维护和保养频率,以减少设备故障的风险;实施过程监控和自动化控制,以确保稳定的生产环境。
过程失效模式及后果分析管理办法

过程失效模式及后果分析管理办法过程失效模式及后果分析(Process Failure Modes and Effects Analysis,简称PFMEA),是一种常用于管理过程风险和改进的工具。
PFMEA通过对过程中可能发生的失效模式及其后果进行分析,提前识别出潜在问题,并采取相应措施降低风险。
下面将介绍PFMEA的管理办法。
一、PFMEA的管理目标PFMEA的管理目标是识别和分析过程中的失效模式及其潜在后果,评估失效发生的概率和影响程度,并制定相应的预防控制措施,降低风险。
二、PFMEA的管理步骤1.选择适当的团队成员:PFMEA的分析需要跨越多个职能领域,因此需要选择适当的团队成员,包括具有相关专业知识和经验的人员。
2.确定过程:明确要分析的过程范围和目标,包括过程流程、输入和输出等。
3.识别失效模式:团队成员通过头脑风暴和过程分析,识别可能导致过程失效的因素。
失效模式可以是物理性的、功能性的、行为性的等。
4.评估失效影响程度:对每个失效模式,评估其对过程和最终产品或服务的影响程度,包括安全性、质量、交付时间、成本等方面。
5.确定失效发生的概率:评估每个失效模式发生的概率,包括概率的频率、可能性等。
6.评估现有控制措施:评估当前过程中已存在的控制措施,对失效模式的控制程度,包括检验、测试等。
7.制定改进措施:根据评估结果,确定需要改进的控制措施,包括预防措施和检测措施,以降低失效发生的概率和影响程度。
8.实施改进措施:制定实施改进措施的计划,并跟踪监控改进效果。
9.更新PFMEA:根据实施改进措施的结果,修订和更新PFMEA,并确保团队成员了解改进措施的目标和具体要求。
三、PFMEA的管理原则1.整体团队参与:PFMEA需要全员参与,涉及到的问题通常跨越多个职能领域,需要充分调动团队的智慧和经验。
2.系统性分析:PFMEA需要从系统层面进行分析,识别可能的失效模式和其后果,并考虑多种因素对失效的影响。
过程潜在失效模式及后果分析程序(含表格)

文件制修订记录1.0目的:做好产前预防性工作,在设计与制造确定之前先探讨,并经由分析其中可能发生的错误、失效模式及失效模式对整体产品品质的影响,藉以早期找出失效原因与防止可预期性的错误发生,提高产品可靠度。
2.0范围:对公司生产汽车行业产品、军工类产品和客户有特殊要求的产品,以及超过了正常生产制作能力的产品。
3.0参考文件:3.1《文件控制程序》3.2《记录控制程序》3.3《纠正预防措施控制程序》4.0定义:4.1过程失效模式及后果分析(PFMEA:英文全称:Potential Failure Mode and Effects Analysis):由负责制造的工程师/工程师组为确保尽最大可能考虑并记录潜在失效模式和相关的原因/机理而使用的分析技术。
4.2控制计划(CP: 英文全称:Control Plan):是对用于控制生产零件和过程体系的文字描述。
由组织编写,陈述该产品重要特性和工程要求。
每个零件必须有一份控制计划,但是,在许多情况下可以对同一过程生产的一些零件应用“系列”控制计划。
在生产零件提交前要求客户认可控制计划。
4.3特殊产品的特性:特殊产品的特性(如关键、主要、重要、重点)是这样一种产品特性;对此合理地预测的变差,会明显影响产品安全性或政府标准或法规的一致性,或者会显著影响客户对产品的满意。
4.4特殊过程的特性:特殊过程的特性(如关键、主要、重要、重点)是这样一种过程特性;在制造和装配过程中,应保证特殊产品特性的变差保持在其目标值之内。
4.5 FMEA/CP多功能小组:由工艺工程师、工序主管、体系工程师、物理室主管、客服经理组成。
5.0职责权限:5.1体系部的职责:5.1.1负责参与FMEA、CP和WI一致性的评审。
负责FMEA正式版本的受控发行;5.2各部门:5.2.1 工艺部的职责:5.2.1.1负责作业指引和临时指引的编写修订;5.2.1.2 主导CP FMEA SPC的编写、修订控制和更新;5.2.1.3 负责修订文件或新岗位文件的培训和考核;5.2.1.4 依据顾客要求完成中英文版指引、控制计划、过程潜在失效模式及后果分析的编写、QC工程图等指导性文件的升级订本申请受控发行;5.2.2生产部的职责:5.2.2.1各个工序负责按照PFMEA的参数要求进行生产;5.2.2.2负责文件发行前的审核操作参数和保养频率的确认;5.2.2.3生产部各工序负责按照品质部的检验规范进行过程产品的自主检查和按照首板标准生产;5.2.2.4负责本生产部、生产工序的现用文件和资料使用及管理;5.2.3 FMEA/CP多功能小组的职责:每次FMEA/CP的更新前,由FMEA/CP多功能小组进行评审,从内部的需求,外部的需求,流程提醒的注意点等出发进行多方评审,保证FMEA、CP、工作指示一致性6.0程序:6.1工艺部针对新产品、新材料、新技术的要求,组织生产、工程、品质人员对本公司各生产工序在生产制造过程中存在的潜在失效模式及后果进行综合分析,并进行PFMEA活动。
过程失效模式及后果分析-教程
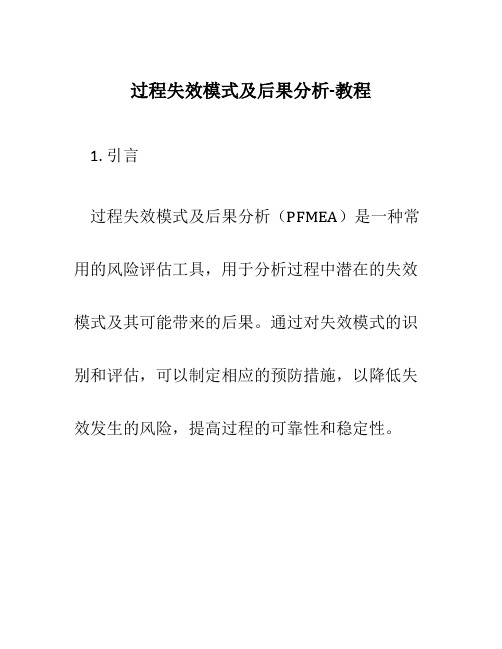
过程失效模式及后果分析-教程1. 引言过程失效模式及后果分析(PFMEA)是一种常用的风险评估工具,用于分析过程中潜在的失效模式及其可能带来的后果。
通过对失效模式的识别和评估,可以制定相应的预防措施,以降低失效发生的风险,提高过程的可靠性和稳定性。
本教程将介绍PFMEA的基本概念、步骤和应用方法,帮助读者了解如何进行过程失效模式及后果分析。
2. PFMEA的基本概念2.1 过程失效模式过程失效模式是指发生在特定过程中的潜在失效形式。
它可以是机械故障、工艺不稳定、材料质量问题等各种各样的问题,可能导致产品或服务无法达到预期的功能要求。
2.2 后果分析后果分析是对失效模式引起的后果进行评估和分析。
它包括两个方面的内容:失效后果的严重性评估和失效后果的概率评估。
严重性评估用于判断失效对产品或服务的影响程度,概率评估用于评估失效产生的频率或概率。
3. PFMEA的步骤PFMEA主要包括以下步骤:3.1 选择分析对象选择需要进行PFMEA分析的过程或系统,确定所要分析的范围和目标。
3.2 建立团队建立一个跨部门的团队,包括相关的设计、生产和质量控制人员。
团队成员应具备相关的知识和经验,以能够准确地分析和评估失效模式及其后果。
3.3 列出过程步骤对所选过程进行详细的步骤分解,将整个过程拆分为多个子过程或操作步骤。
3.4 识别失效模式对每个步骤识别可能存在的失效模式,包括机械失效、材料问题、环境因素等。
3.5 评估失效后果对每个失效模式评估其可能带来的后果,包括严重性和概率评估。
根据经验和数据进行评估,各团队成员提供专业意见。
3.6 优先级排序根据失效后果的严重性和概率进行排序,确定重要性较高的失效模式。
3.7 制定预防措施对于重要性较高的失效模式,制定相应的预防措施,包括改进设计、改变工艺、提高操作规范等。
3.8 实施并跟踪将制定的预防措施实施到实际生产过程中,并定期进行跟踪和评估,以确保措施的有效性和可操作性。
过程失效模式及后果分析
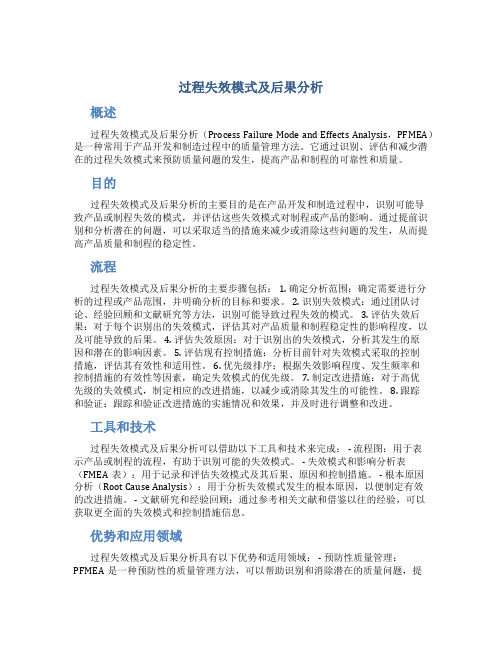
过程失效模式及后果分析概述过程失效模式及后果分析(Process Failure Mode and Effects Analysis,PFMEA)是一种常用于产品开发和制造过程中的质量管理方法。
它通过识别、评估和减少潜在的过程失效模式来预防质量问题的发生,提高产品和制程的可靠性和质量。
目的过程失效模式及后果分析的主要目的是在产品开发和制造过程中,识别可能导致产品或制程失效的模式,并评估这些失效模式对制程或产品的影响。
通过提前识别和分析潜在的问题,可以采取适当的措施来减少或消除这些问题的发生,从而提高产品质量和制程的稳定性。
流程过程失效模式及后果分析的主要步骤包括: 1. 确定分析范围:确定需要进行分析的过程或产品范围,并明确分析的目标和要求。
2. 识别失效模式:通过团队讨论、经验回顾和文献研究等方法,识别可能导致过程失效的模式。
3. 评估失效后果:对于每个识别出的失效模式,评估其对产品质量和制程稳定性的影响程度,以及可能导致的后果。
4. 评估失效原因:对于识别出的失效模式,分析其发生的原因和潜在的影响因素。
5. 评估现有控制措施:分析目前针对失效模式采取的控制措施,评估其有效性和适用性。
6. 优先级排序:根据失效影响程度、发生频率和控制措施的有效性等因素,确定失效模式的优先级。
7. 制定改进措施:对于高优先级的失效模式,制定相应的改进措施,以减少或消除其发生的可能性。
8. 跟踪和验证:跟踪和验证改进措施的实施情况和效果,并及时进行调整和改进。
工具和技术过程失效模式及后果分析可以借助以下工具和技术来完成: - 流程图:用于表示产品或制程的流程,有助于识别可能的失效模式。
- 失效模式和影响分析表(FMEA表):用于记录和评估失效模式及其后果、原因和控制措施。
- 根本原因分析(Root Cause Analysis):用于分析失效模式发生的根本原因,以便制定有效的改进措施。
- 文献研究和经验回顾:通过参考相关文献和借鉴以往的经验,可以获取更全面的失效模式和控制措施信息。
过程失效模式及后果分析(PFMEA)
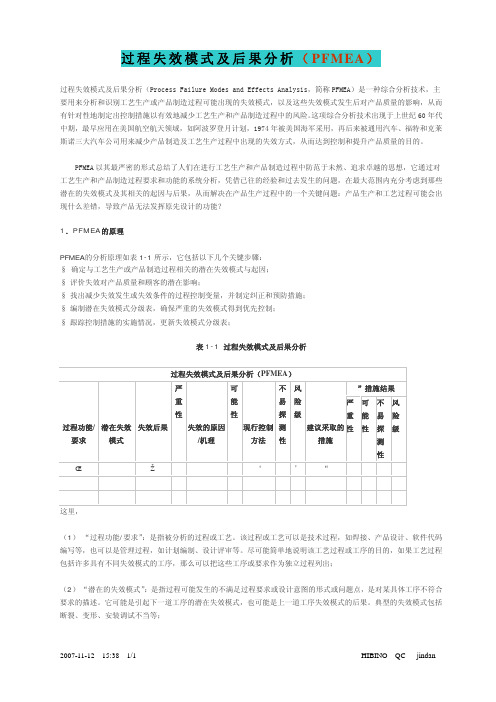
过程失效模式及后果分析(PFMEA)过程失效模式及后果分析(Process Failure Modes and Effects Analysis,简称PFMEA)是一种综合分析技术,主要用来分析和识别工艺生产或产品制造过程可能出现的失效模式,以及这些失效模式发生后对产品质量的影响,从而有针对性地制定出控制措施以有效地减少工艺生产和产品制造过程中的风险。
这项综合分析技术出现于上世纪60年代中期,最早应用在美国航空航天领域,如阿波罗登月计划,1974年被美国海军采用,再后来被通用汽车、福特和克莱斯诺三大汽车公司用来减少产品制造及工艺生产过程中出现的失效方式,从而达到控制和提升产品质量的目的。
PFMEA以其最严密的形式总结了人们在进行工艺生产和产品制造过程中防范于未然、追求卓越的思想,它通过对工艺生产和产品制造过程要求和功能的系统分析,凭借已往的经验和过去发生的问题,在最大范围内充分考虑到那些潜在的失效模式及其相关的起因与后果,从而解决在产品生产过程中的一个关键问题:产品生产和工艺过程可能会出现什么差错,导致产品无法发挥原先设计的功能?1.PFMEA的原理PFMEA的分析原理如表1-1所示,它包括以下几个关键步骤:§确定与工艺生产或产品制造过程相关的潜在失效模式与起因;§评价失效对产品质量和顾客的潜在影响;§找出减少失效发生或失效条件的过程控制变量,并制定纠正和预防措施;§编制潜在失效模式分级表,确保严重的失效模式得到优先控制;§跟踪控制措施的实施情况,更新失效模式分级表;表1-1 过程失效模式及后果分析过程失效模式及后果分析(PFMEA)”措施结果过程功能/要求潜在失效模式失效后果严重性失效的原因/机理可能性现行控制方法不易探测性风险级建议采取的措施严重性可能性不易探测性风险级ŒŽ‘ ’“这里,(1)“过程功能/要求”:是指被分析的过程或工艺。
该过程或工艺可以是技术过程,如焊接、产品设计、软件代码编写等,也可以是管理过程,如计划编制、设计评审等。
失效模式及后果分析

失效模式及后果分析失效模式及后果分析(Failure Mode and Effects Analysis,简称FMEA)是一种用于确定系统、产品或过程中潜在失效模式及其潜在后果的方法。
该分析方法可以帮助组织确定潜在的失败模式,并采取措施来减轻或消除潜在的后果。
以下是对失效模式及其后果的分析,具体内容如下。
一、失效模式失效模式指系统、产品或过程中可能出现的失效形态。
通过分析失效模式,可以确定其潜在的后果,并制定相应的应对措施。
1.机械失效模式机械失效模式是指由于机械部件的失效引起的系统故障。
例如,机械零件的磨损、断裂、腐蚀等都可能导致机械失效。
机械失效的后果可能包括系统停机、故障扩大和安全隐患等。
2.电气失效模式电气失效模式是指由电气元件或电路的失效引起的系统故障。
例如,电路板上元件的烧毁、电路的短路、电源的故障等都可能导致电气失效。
电气失效的后果可能包括系统损坏、数据丢失和火灾等。
3.人为失效模式人为失效模式是指由于人为操作不当或疏忽引起的系统故障。
例如,错误的设置参数、操作错误、机械部件的未经授权更换等都可能导致人为失效。
人为失效的后果可能包括生产线停机、产品质量问题和安全事故等。
4.材料失效模式材料失效模式是指由于材料的质量问题或老化引起的系统故障。
例如,材料的抗拉强度下降、一些材料易受腐蚀等都可能导致材料失效。
材料失效的后果可能包括产品不合格、系统寿命降低和安全隐患等。
5.环境失效模式环境失效模式是指由于环境条件的变化引起的系统故障。
例如,温度变化、湿度变化、气压变化等都可能导致环境失效。
环境失效的后果可能包括元件老化、系统性能下降和产品失效等。
二、失效后果失效后果指在系统、产品或过程中出现失效模式后可能带来的结果。
失效后果可以是直接的,也可以是间接的。
1.经济影响失效模式可能导致产品停产或停机,造成生产停顿和损失。
此外,产品的质量问题也可能导致产品召回和赔偿等经济影响。
2.安全隐患一些失效模式可能会给人员的生命安全和身体健康带来威胁。
过程失效模式及后果分析控制程序IATF16949

过程失效模式及后果分析控制程序IATF169491.目的确定与产品和过程相关的潜在的失效模式和潜在制造或装配过程失效的机理/起因,评价潜在失效对顾客产生的后果和影响,采取控制来降低失效产生频度或失效条件探测度的过程变量和能够避免或减少这些潜在失效发生的措施。
2.范围适用于公司用于汽车零组件的所有新产品/过程或修改过的产品/过程及应用或环境发生变更的原有产品/过程的样品试制和批量生产。
3.定义3.1失效:在规定条件下(环境、操作、时间),不能完成既定功能或产品参数值和不能维持在规定的上下限之间,以及在工作范围内导致零组件的破裂卡死等损坏现象。
3.2严重度(S):指一给定失效模式最严重的影响后果的级别,是单一的FMEA范围内的相对定级结果。
严重度数值的降低只有通过设计更改或重新设计才能够实现。
3.3频度(O):指某一特定的起因/机理发生的可能发生,描述出现的可能性的级别数具有相对意义,但不是绝对的。
3.4探测度(D):指在零部件离开制造工序或装配之前,利用第二种现行过程控制方法找出失效起因/机理过程缺陷或后序发生的失效模式的可能性的评价指标;或者用第三种过程控制方法找出后序发生的失效模式的可能性的评价指标。
3.5风险优先数(RPN):指严重度数(S)和频度数(O)及不易探测度数(D)三项数字之乘积。
3.6 CFT:多功能小组4.职责CFT:负责过程失效模式及后果分析(PFMEA)的制定与管理。
5.工作流程5.1 FMEA策划5.1.1新产品进入试生产之前,要使用PFMEA分析;5.1.2现有的产品出现质量故障时,要使用PFMEA去分析;5.2 组建CFT,根据需要,小组成员可包括制造、采购、质量、工程、和顾客方面的代表;5.3收集FMEA所需的信息5.3.1零部件生产过程流程图;5.3.2过程有关的产品质量特性;5.3.3制造和装配的要求;5.3.4与成熟产品相近的产品过程质量情况等信息。
5.4失效模式确认5.4.1 FMEA小组分析产品的功能失效模式;5.4.2可以使用鱼骨图,从人、机、料、法、环五方面分析失效模式的每一个起因或机理;5.4.3确定潜在的失效模式;5.5 严重度评价5.5.1分析潜在失效的后果,根据严重度评价准则进行严重度评定;5.6频度评价5.6.1对失效模式的起因或机理,根据频度评价准则进行频度评价;5.7探测度评价5.7.1选择现行的控制方法,根据探测度评价准则进行探测度评价;5.8确定风险顺序数5.8.1根据严重度、频度、探测度的评定,计算出风险顺序数(RPN);5.9制定改正措施5.9.1CFT列出RPN值先后次序表,首先对级数高、严重度高或最关键的项目要制定改正。
失效模式及后果分析控制程序(含表格)

失效模式及后果分析控制程序(IATF16949-2016/ISO9001-2015)1.0目的:本规则介绍了本公司的制品在工程FMEA的实施阶段的运用程序及有关规定,其主要目的是:1)确定与产品相关的过程潜在的实效模式;2)评价失效时对顾客的潜在影响;3)确定潜在制造或装配过程失效的起因,确定减少失效发生或找出失效条件的过程控制变量;4)编制潜在失效模式等级表,然后建立考虑纠正措施的顺序。
2.0范围:2.1生产部在新产品投入时,依据关联规程《产品质量先期策划控制程序》,在生产可行性评价阶段或之前,进行潜在的失效模式及后果分析(PFMEA);2.2 PFMEA是一种动态文件,在新产品的制造策划阶段、对新过程或修改的过程进行早期评价和分析能够促进预测、解决或监控潜在过程问题。
应包括工场内所有可能影响到制造和装配操作的过程,它应始终反映过程设计的最新状态,以及最新的相关措施。
3.0定义:3.1FMEA:潜在的失效模式及后果分析(Potential Failure Mode and Effects Analysis简称FMEA)。
是在制品/工程等的策划设计阶段,对构成制品的各种部品,对构成工程的各个程序逐一进行分析,找出潜在的失效模式,分析其可能的后果,苹果其风险,从而预先采取措施,减少失效模式的严重程度,降低其可能发生的概率,以有效地提高质量与可靠性,确保顾客满意的一系列活动。
3.2 DFMEA和PFMEA:设计FMEA和工程FMEA(Design FMEA和Process FMEA)。
3.3FMEA的顾客:不仅是指最终顾客、也可以是下一道工序或组立工程及服务等。
3.4其它(如:严重度、频度等)的定义在后述5项中说明。
4.0职责:4.1PFMEA应由CFT(Cross-Functional Team部门横向协调小组)小组来开发和维护。
4.2CFT小组的成员应包括:技术、生产、生产管理、品质管理;必要时包括采购、品证、供应商、后续装配领域等人员。
失效模式及后果分析控制程序(IATF16949)
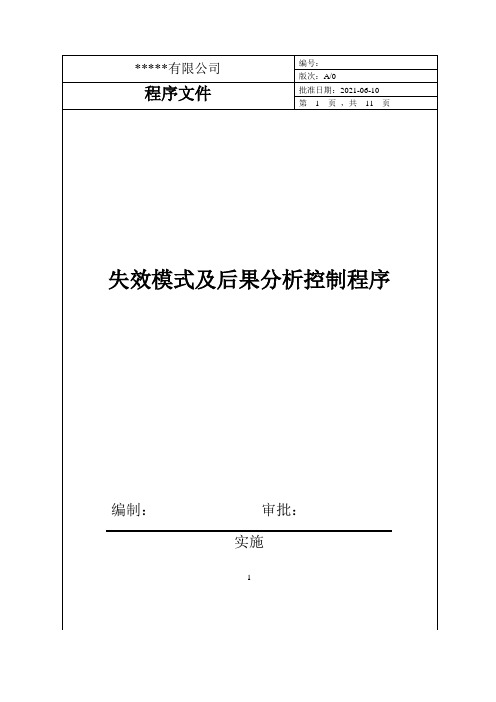
修改记录1.目的规范FMEA活动,评价和发现产品在设计中和工艺过程开发中存在的潜在失效及其后果, 并将能够避免减少这些潜在失效产生的措施正式书面文件化,对产品质量前期进行缺陷预防,以确保产品质量。
2.范围适用于本公司所有的新产品的开发与工艺过程开发,以及量产后提出改进措施。
3.术语和定义:DFMEA: 设计失效模式分析,应采用多方论证方法,在新产品开发立项前启动,最终配方和产品规范定稿时结束。
PFMEA:过程失效模式分析,应采用多方论证方法,在新产品过程开发、工装开发前启动,最终设备和工装完工前结束。
失效:在规定条件下(环境、操作、时间),不能完成既定功能或产品参数值和不能维持在规定的上下限之间,以及在工作范围内导致零组件的破裂卡死等损坏现象。
4.职责:APQP小组负责失效模式及后果分析(FMEA)的制定与管理。
5 流程图无6 内容6.1 FMEA的三情形:情形1—新设计、新技术或新过程。
FMEA的范围是全部设计、技术或过程。
情形2—对现有设计或过程的修改(假设已有FMEA)。
FMEA的范围应集中于对设计或过程的修改、由于修改可能产生的相互影响。
情形3—将现有的设计或过程用于新的环境、场所或应用(假设已有FMEA)。
FMEA的范围是新环境或场所对现有设计或过程的影响。
6.2 DFMEA由负责产品设计的工程师制定和实施,技术部接到销售部转来的顾客产品资料,经过评审后应开始启动DFMEA,在产品开发的各个阶段,发生更改或获得更多的信息时,持续予以更新,在产品加工配方完工之前全部完成。
6.3 DFMEA的评审应包括制造、设计、品质及销售人员,必要时可包括顾客代表,小组成员应由经验丰富的工程师参加。
对该产品设计过程中存在的潜在失效模式及后果进行综合分析评估预测,以减小或消除产品设计不合格或导致产品设计报废的机会。
6.4 对DFMEA开发的失效模式、后果和原因及机理进行严重度(S)、频度(O)及探测度(D),6.5 对于DFMEA的中RPN排序,分数高的项目及严重度(S)特别高和项目,如大于8以上时,应优先考虑提出措施,以降低其RPN和S值。
过程失效模式与影响分析程序
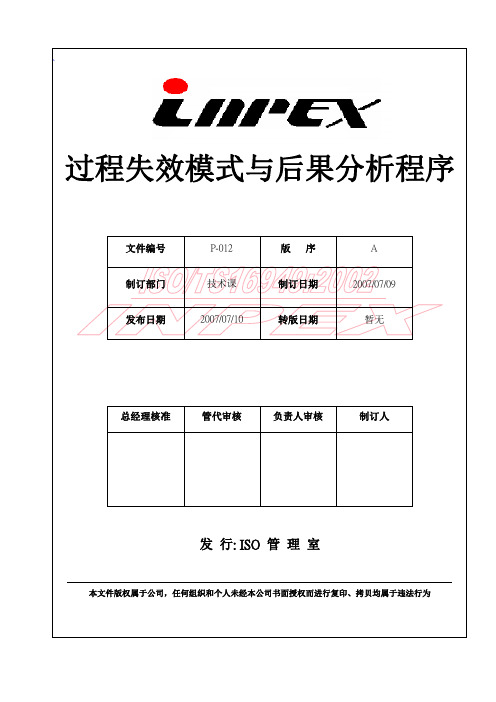
`过程失效模式与后果分析程序文件编号P-012 版序 A制订部门技术课制订日期2007/07/09发布日期2007/07/10 转版日期暂无总经理核准管代审核负责人审核制订人发行: ISO 管理室本文件版权属于公司,任何组织和个人未经本公司书面授权而进行复印、拷贝均属于违法行为变更履历表文件编号:P-012 Page:1文件名称:过程失效模式与后果分析程序提出部门提出人变更版序变更页次变更内容修订日期1 目的确定与产品和过程相关的潜在的失效模式和潜在制造或装配过程失效的机理/起因,评价潜在失效对顾客产生的后果和影响,采取控制来降低失效产生频度或失效条件探测度的过程变量和能够避免或减少这些潜在失效发生的措施。
2 范围适用于公司用于汽车零组件的所有新产品/过程或修改过的产品/过程及应用或环境发生变更的原有产品/过程的样品试制和批量生产。
3 职责APQP小组负责过程失效模式及后果分析(PFMEA)的制定与管理,并尽可能将客户归入此项目团队。
4 术语和定义PFMEA:指Process Failure Mode and Effects Analysis(过程失效模式及后果分析)的英文简称。
由负责制造/装配的工程师/小组主要采用的一种分析技术,用以最大限度地保证各种潜在的失效模式及其相关的起因/机理已得到充分的考虑和论述。
失效:在规定条件下(环境、操作、时间),不能完成既定功能或产品参数值和不能维持在规定的上下限之间,以及在工作范围内导致零组件的破裂卡死等损坏现象。
严重度(S):指一给定失效模式最严重的影响后果的级别,是单一的FMEA范围内的相对定级结果。
严重度数值的降低只有通过设计更改或重新设计才能够实现。
频度(O):指某一特定的起因/机理发生的可能性,描述出现的可能性的级别数具有相对意义,但不是绝对的。
探测度(D):指在零部件离开制造工序或装配之前,利用第二种现行过程控制方法找出失效起因/机理过程缺陷或后序发生的失效模式的可能性的评价指标;或者用第三种过程控制方法找出后序发生的失效模式的可能性的评价指标。
过程失效模式及后果分析(PFMEA)
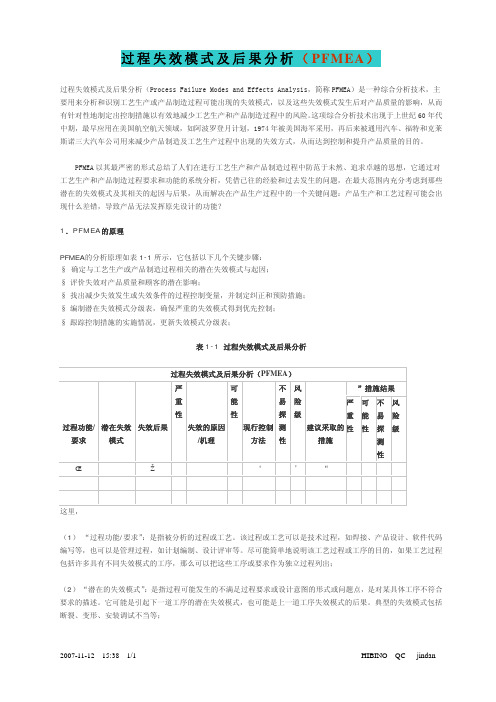
过程失效模式及后果分析(PFMEA)过程失效模式及后果分析(Process Failure Modes and Effects Analysis,简称PFMEA)是一种综合分析技术,主要用来分析和识别工艺生产或产品制造过程可能出现的失效模式,以及这些失效模式发生后对产品质量的影响,从而有针对性地制定出控制措施以有效地减少工艺生产和产品制造过程中的风险。
这项综合分析技术出现于上世纪60年代中期,最早应用在美国航空航天领域,如阿波罗登月计划,1974年被美国海军采用,再后来被通用汽车、福特和克莱斯诺三大汽车公司用来减少产品制造及工艺生产过程中出现的失效方式,从而达到控制和提升产品质量的目的。
PFMEA以其最严密的形式总结了人们在进行工艺生产和产品制造过程中防范于未然、追求卓越的思想,它通过对工艺生产和产品制造过程要求和功能的系统分析,凭借已往的经验和过去发生的问题,在最大范围内充分考虑到那些潜在的失效模式及其相关的起因与后果,从而解决在产品生产过程中的一个关键问题:产品生产和工艺过程可能会出现什么差错,导致产品无法发挥原先设计的功能?1.PFMEA的原理PFMEA的分析原理如表1-1所示,它包括以下几个关键步骤:§确定与工艺生产或产品制造过程相关的潜在失效模式与起因;§评价失效对产品质量和顾客的潜在影响;§找出减少失效发生或失效条件的过程控制变量,并制定纠正和预防措施;§编制潜在失效模式分级表,确保严重的失效模式得到优先控制;§跟踪控制措施的实施情况,更新失效模式分级表;表1-1 过程失效模式及后果分析过程失效模式及后果分析(PFMEA)”措施结果过程功能/要求潜在失效模式失效后果严重性失效的原因/机理可能性现行控制方法不易探测性风险级建议采取的措施严重性可能性不易探测性风险级ŒŽ‘ ’“这里,(1)“过程功能/要求”:是指被分析的过程或工艺。
该过程或工艺可以是技术过程,如焊接、产品设计、软件代码编写等,也可以是管理过程,如计划编制、设计评审等。
过程潜在失效模式与后果分析管理程序
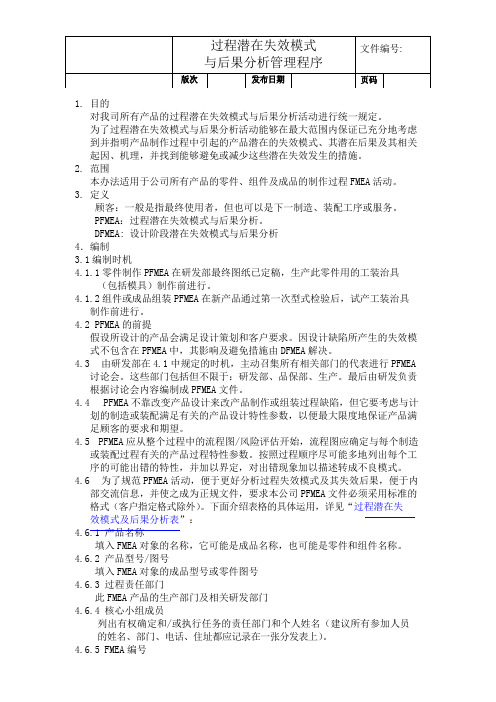
1.目的对我司所有产品的过程潜在失效模式与后果分析活动进行统一规定。
为了过程潜在失效模式与后果分析活动能够在最大范围内保证已充分地考虑到并指明产品制作过程中引起的产品潜在的失效模式、其潜在后果及其相关起因、机理,并找到能够避免或减少这些潜在失效发生的措施。
2.范围本办法适用于公司所有产品的零件、组件及成品的制作过程FMEA活动。
3.定义顾客:一般是指最终使用者,但也可以是下一制造、装配工序或服务。
PFMEA:过程潜在失效模式与后果分析。
DFMEA:设计阶段潜在失效模式与后果分析4.编制3.1编制时机4.1.1零件制作PFMEA在研发部最终图纸已定稿,生产此零件用的工装治具(包括模具)制作前进行。
4.1.2组件或成品组装PFMEA在新产品通过第一次型式检验后,试产工装治具制作前进行。
4.2PFMEA的前提假设所设计的产品会满足设计策划和客户要求。
因设计缺陷所产生的失效模式不包含在PFMEA中,其影响及避免措施由DFMEA解决。
4.3由研发部在4.1中规定的时机,主动召集所有相关部门的代表进行PFMEA讨论会。
这些部门包括但不限于:研发部、品保部、生产。
最后由研发负责根据讨论会内容编制成PFMEA文件。
4.4PFMEA不靠改变产品设计来改产品制作或组装过程缺陷,但它要考虑与计划的制造或装配满足有关的产品设计特性参数,以便最大限度地保证产品满足顾客的要求和期望。
4.5PFMEA应从整个过程中的流程图/风险评估开始,流程图应确定与每个制造或装配过程有关的产品过程特性参数。
按照过程顺序尽可能多地列出每个工序的可能出错的特性,并加以界定,对出错现象加以描述转成不良模式。
4.6为了规范PFMEA活动,便于更好分析过程失效模式及其失效后果,便于内部交流信息,并使之成为正规文件,要求本公司PFMEA文件必须采用标准的格式(客户指定格式除外)。
下面介绍表格的具体运用,详见“过程潜在失效模式及后果分析表”:4.6.1产品名称填入FMEA对象的名称,它可能是成品名称,也可能是零件和组件名称。
过程失效模式及后果分析–过程控制计划
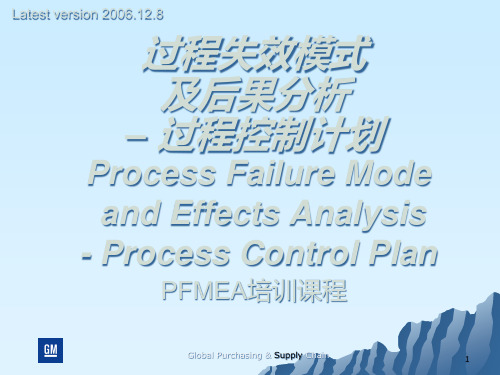
QSB WORKSHOP REV. 091304
Global Purchasing & Supply Chain
13
13
FMEA的类型
• 根据在APQP中的不同阶段,FMEA主要有DFMEA和 PFMEA两种,即设计FMEA和过程FMEA;
数 预防 探测 度 P
(O)
(D) N
建议措施
負責人和 完成日期
此流程描述 作业特性的 要求是什么?
失效模式 的后果是 什么?
作业特性的失 效会有哪些形 式
影 響 程 度 有 多 嚴 重 ?
失效模 式的原 因是什 么?
其 發 生 的 機 率 有 多 少 ?
• 设计FMEA即DFMEA: 针对产品与规范本身,是产品设计开发的分析技术。 主要是设计工程师和其多功能小组应用。 -- 主要驱动力:消除失效并通过稳健的设计减低严重度 实现产品零缺陷的目标
• 过程FMEA即PFMEA: 针对产品的制造过程,是过程设计开发的分析技术。
主要是过程(制造)工程师和其多功能小组应用。 -- 主要驱动力:通过对所有潜在失效的识别了解过程, 目的在于制定消除潜在失效起因的建议措施。
• 检验或检测只能是最后的选择。
QSB WORKSHOP REV. 091304
Global Purchasing & Supply Chain
11
11
什么是FMEA
FMEA 是先期质量策划中评价潜在失效模式及其起因 与后果的一种分析工具,用来识别并帮助消除产品/过程 的潜在失效模式。
• 一项系统结构化的分析工具,意在:
TS16949—过程潜在失效模式及后果分析程序
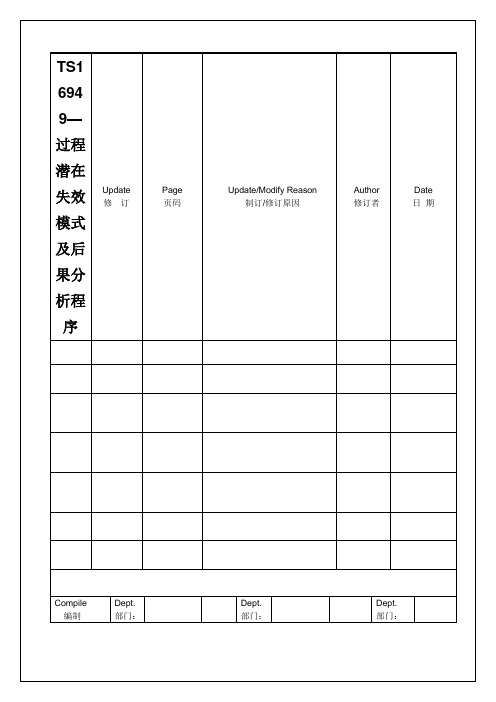
中上
操纵有较多机会可探测出
×
×
在工位上的误差控测,或者在作业准备时进行测量与首件检查(仅适用于作业准备的原因)
4
高
操纵有较多机会可探测出
×
×
在工位上的误差探 测,或者利用多层验收在后续工序上进行误差探测:供应、选择、安装、确认。不能同意有差异零件。
3
很高
操纵几乎确信能探测出
×
×
在工位上的误差探测(自动测量并自动停机)。不能通过有差异的零件。
2
无
无可辨识的影响。
或者对操作或者操作者而言有轻微的不方便或者无影响。
1
附件3: 潜在失效模式频度评价表
失效发生可能性
可能的失效率
频度
很高:持续性失效
≥100个 每1000个
10
50个 每1000个
9
高:经常性失效
20个 每1000个
8
10个 每1000个
7
中等:偶然性失效
5个 每1000个
6
2个 每1000个
严重度数
后果的严重度(内部用户)
无警告的严重危害
可能危害机器或者装配操作者。潜在失效模式严重影响车辆安全运行与/或者包含不符合政府法规项,严重程度很高。失效发生时无警告。
10
对下道工序或者内部用户会造成安全问题,生产中断。
有警告的严重危害
可能危害机器或者装配操作者。潜在失效模式严重影响车辆安全与/或者包含不符合政府法规项,严重程度很高。失效发生时有警告。
附件1:FMEA制作步骤
附件2:潜在失效后果严重程度评价表
附件3:潜在失效模式频度评价表
附件4:潜在失效模式不易探测度评价表
附件5:推荐的不易探测度(D)评价准则
电镀厂过程失效模式及后果分析管理程序

过程失效模式及后果分析管理程序制作日期2021/01/21审核日期2021/01/21批准日期2021/01/21修订记录1.0目的根据客户的要求,通过对产品生产过程中的潜在失效模式及后果进行预见性的分析,将产品过程中存在的失效风险降至最低。
2.0范围适用于产品生产中的过程潜在失效模式及后果分析。
3.0职责3.1多方论证小组:负责制订PFMEA的各项内容及相关改进措施,建立纠正措施优先体系;当有新的失效模式出现时及时更改PFMEA。
3.2工程部:主导多方论证小组分析并制订所有潜在失效模式及后果。
3.3各部门:参与PFMEA的制订和评估,相关纠正和预防措施的执行。
4.0定义4.1PFMEA:(Process Failure Mode& Effects Analysis)过程失效模式及后果分析.4.2顾客:顾客对PFMEA而言通常指“终端顾客”,但顾客也可能是后续或下游制造或装配作业、服务操作或法规4.3MSA:Measurement System Analysis(测量系统分析)包括准确性、线性、重复性、再现性、稳定性。
5.0流程无6.0内容6.1PFMEA制订说明:6.1.1工程部主导成立多方论证小组(即APQP策划小组),并确定PFMEA的实施项目。
多方论证小组根据客户的要求和生产加工情况,在APQP总进度中明确PFMEA项目的实施进度要求。
6.1.2多方论证小组组织品管部、工程部、生产部等相关部门的人员对整个生产流程进行评定。
6.1.3工程部针对过程失效模式和后果分析,确定相关过程的“严重度(S)”、“频度(O)”、“探测度(D)”,并通过S、O、D值的排列组合“措施优先级(AP)”,进行改进,编制PFMEA。
6.2在针对措施优先级(AP)行动时,需考虑以下因素:6.2.1严重度数高的(≥9)必须实施;6.2.2措施优先级(AP)为高(H)的优先实施;6.2.3措施优先级(AP)为中(M),但是易于实施,成本投入少的,优先实施。
- 1、下载文档前请自行甄别文档内容的完整性,平台不提供额外的编辑、内容补充、找答案等附加服务。
- 2、"仅部分预览"的文档,不可在线预览部分如存在完整性等问题,可反馈申请退款(可完整预览的文档不适用该条件!)。
- 3、如文档侵犯您的权益,请联系客服反馈,我们会尽快为您处理(人工客服工作时间:9:00-18:30)。
1.目的
1.1确定与产品相关的过程潜在失效模式。
1.2确定制造或装配过程中失效的起因,确定减少失效发生或找出失效条件的过程控制变量。
1.3编制潜在失效模式分析表,为制造部及技术部等部门采取纠正和预防措施提供对策。
2.适用范围
适用于新产品、产品变更及应用环境发生变更时的样品试作、批量生产。
3.定义
3.1 PFMEA:由负责制造的工程师/小组为确保尽最大可能考虑并记录潜在的失效模式和相关
的原因/机理而使用的分析技术。
3.2过程流程图:指对某一产品预期的制造过程的早期描述。
3.3控制计划(QC工程表):是对控制零件和过程的系统的书面描述。
3.4在失效分析中,首先要明确产品的失效是什么,否则产品的数据分析和可靠度评估结果
将不一样,一般而言,失效是指:
3.4.1在规定条件下(环境、操作、时间)不能完成既定功能。
3.4.2在规定条件下,产品参数值不能维持在规定的上下限之间。
3.4.3产品在工作范围内,导致零组件的破裂、断裂、卡死等损坏现象。
3.5客户:一般是指“最终使用者”,但也可以是后续的或下一制造装配工序,以及服务工作。
4.职责
4.1 PFMEA制订:产品开发课
4.2 PFMEA审查:APQP小组
4.3 PFMEA核准:技术部经理/管理者代表
5.作业程序
6.相关文件
6.1记录管制程序 FT-QP-003
6.2产品品质先期策划程序 FT-EP-012
6.3文件与资料管制程序 FT-QP-001
7.使用表单
7.1潜在失效模式及后果分析TR-014-02-A0
7.2过程流程图TR-014-03-A0
8.附件
1、FMEA编号
编号方法如下:
××××─×××
流水号
年份
2、项目名称
依据5.1中所确定的分析项目填入该过程(工序)、名称、编号。
3、过程责任部门
填入产品制造部门和生产线。
4、编制者
填入负责编制FMEA的人员姓名、电话及所在部门名称。
5、产品型号
填入将要分析的产品和/或零部件型号。
6、关键日期
填入初次FMEA预定完成的日期,该日期不应超过计划开始生产的日期。
7、FMEA日期
填入编制FMEA初稿的日期及最新修订的日期。
8、主要参加人
列出参与或执行此项工作的各部门负责人姓名。
9、过程功能/要求
简单描述被分析的过程或工序,说明该工序过程或工序的目的,工序过程包括多个具有不同失效模式的工序,应把这些工序作为独立过程列出处理。
10、潜在失效模式:指过程中可能发生的不符过程要求和/或设计意图的形式,是对其具体工
序不符合要求的描述,它可能是引起下道工序的潜在失效模式,也可能是上一道工序潜
在失效的后果。
在过程FMEA准备中,应假定提供的附件、毛坯是合格的。
11、潜在失效后果:是指失效模式对客户的影响,客户可以是下一道工序、后续工序或工位、
代理商、最终用户,当评价潜在失效后果时,应依据客户可能注意到的或经历的情况来
描述失效后果,对最终用户来说失效的后果应一律用产品(或系统)的性能来描述(如
噪音大、漏油、卡死、侵蚀等)若客户是下一道工序或后续工序/工位,失效的后果应
用工艺/工序性能来描述(如无法装配、危害操作者、工艺基准误差大等)。
12、严重度:是潜在失效模式对客户的影响后果的严重程序的评价指标。
严重度仅适用于失
效的后果,分为1∽10级,其严重程序按下表予以评价选定:
13
对需要附加过程控制的零部件、半成品或成品的一些特殊过程的特性进行分级(如关键、主要、重要、重点等)。
若过程FMEA中确定了某一分级,应通知技术部开发生技负责设计的工程技术人员,以便制订相应的工程文件及控制项目的标识。
应将产品的特殊性符号在此栏目中予以明确标识。
14、潜在失效起因/机理:指失效是怎么发生的,并依据易于纠正或控制的方式来描述。
应尽
可能在更广、更深的范围内列出所能想象到的所有原因,以便采取针对性的纠正措施。
15、频率
指具体的失效起因/机理发生的频率,分为1∽10级,其大小按下表评价选取。
评价准则
16、现行过程控制:是对尽可能防止失效模式的发生,或探测将发生失效模式的控制方法的描述,有三
种控制方法予以考虑:
16.1预防失效原因或失效模式/后果的发生或降低发生比率
16.2查明起因/机理并找到纠正措施
16.3查明失效模式:较好的方法是首先使用16.1其次16.2,最后使用16.3。
17、不易探测度:是指零部件(半成品、成品)在制造或在装配过程中,利用16.2的控制方
法找出失效起因/机理过程缺陷的可能性的评价指示,或利用16.3控制方法找出后序发生的失效模式的可能性的评价指标,分为1∽10级,不易探测度数的大小按下表评价选取:
不易探测度评价准则表
风险顺序(RPN)是严重度数(S)、频度(O)和不易探测度数(D)乘积。
RPN=(S)×(O)×(D)
对过程中所有担心事项可以以RPN值来排序,RPN取值于1∽1000范围内。
18.1RPN≥100(或依客户要求),应采取后续改进措施。
18.2(S)>8时,应采取后续改进措施或依客户要求。
19、建议措施
当失效模式依RPN值排列风险顺序时,应首先对最高等级的关键项目提出改进措施,任何
措施的目的都是为了减少严重度、频度、和/或不易探测度的数值,可考虑下列措施,但不限于此:
19.1修改工艺过程和/或设计,以降低失效发生的可能性
19.2修改工艺过程和/或设计,以降低失效的严重度数
19.3修改工艺过程和/或设计,以降低失效的不易探测度
19.4从更积极的意义上讲,应制订永久性的改进措施,以及采用统计过程控制(SPC)方法
制订预防缺陷发生的措施。
20、责任及目标完成日期
填入建议措施的部门(个人)和预订完成的日期。
21、采取的措施
当实施一项措施后,简要记载具体的执行情况,并记下生效日期。
22、措施结果
改进措施实施后,应估算并记录改进后失效以发生的频度、严重度和不易控测度数,计算并记录改进后RPN值,所有改进后的RPN值都应复查,而且有必要考虑进一步措施,还应重复19∽20的步骤。