利用废塑料、废油或重油炼制燃料柴油的方法生产加工技术
废塑料催化裂解生成汽柴油中试工艺的研究
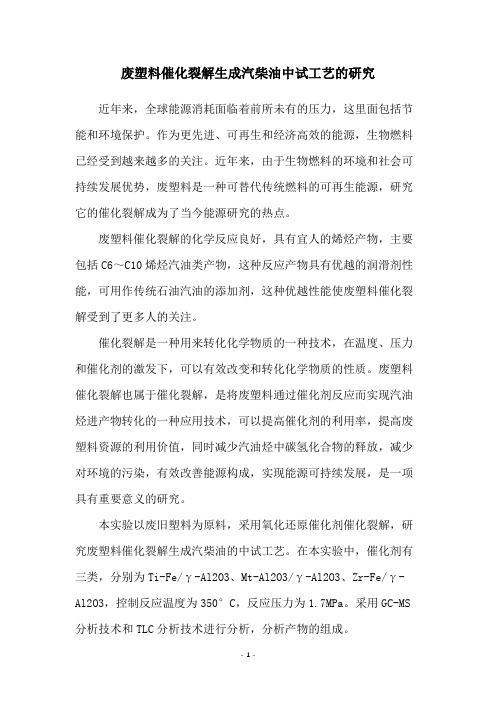
废塑料催化裂解生成汽柴油中试工艺的研究近年来,全球能源消耗面临着前所未有的压力,这里面包括节能和环境保护。
作为更先进、可再生和经济高效的能源,生物燃料已经受到越来越多的关注。
近年来,由于生物燃料的环境和社会可持续发展优势,废塑料是一种可替代传统燃料的可再生能源,研究它的催化裂解成为了当今能源研究的热点。
废塑料催化裂解的化学反应良好,具有宜人的烯烃产物,主要包括C6~C10烯烃汽油类产物,这种反应产物具有优越的润滑剂性能,可用作传统石油汽油的添加剂,这种优越性能使废塑料催化裂解受到了更多人的关注。
催化裂解是一种用来转化化学物质的一种技术,在温度、压力和催化剂的激发下,可以有效改变和转化化学物质的性质。
废塑料催化裂解也属于催化裂解,是将废塑料通过催化剂反应而实现汽油烃进产物转化的一种应用技术,可以提高催化剂的利用率,提高废塑料资源的利用价值,同时减少汽油烃中碳氢化合物的释放,减少对环境的污染,有效改善能源构成,实现能源可持续发展,是一项具有重要意义的研究。
本实验以废旧塑料为原料,采用氧化还原催化剂催化裂解,研究废塑料催化裂解生成汽柴油的中试工艺。
在本实验中,催化剂有三类,分别为Ti-Fe/γ-Al2O3、Mt-Al2O3/γ-Al2O3、Zr-Fe/γ-Al2O3,控制反应温度为350°C,反应压力为1.7MPa。
采用GC-MS 分析技术和TLC分析技术进行分析,分析产物的组成。
实验结果表明,三种催化剂均能有效的催化废塑料的裂解反应,在实验条件下反应期间产物组成较为稳定,且催化剂均可以有效的地利用废塑料资源,有效的生成C6-C10的烯烃汽油类组成,其中Mt-Al2O3/γ-Al2O3催化剂有最佳的活性与抗堵塞性,工艺反应稳定性高,也更能有效的抑制烯烃产物的沉淀,废塑料催化裂解生成汽柴油的中试工艺能够满足实际应用所需要的添加剂性能指标。
综上所述,废塑料催化裂解生成汽柴油的中试工艺的发展前景广阔。
废塑料催化裂解生成汽柴油中试工艺的研究

废塑料催化裂解生成汽柴油中试工艺的研究近年来,随着我国经济的快速发展和生活水平的提高,汽油的需求日益增加,同时,传统的汽柴油来源对环境的影响越来越大,因此搜索新的汽柴油来源变得尤为重要。
废塑料作为一种可再生的新能源,已被广泛应用于汽柴油的生产。
本文以“废塑料催化裂解生成汽柴油中试工艺的研究”为研究主题,旨在探讨废塑料催化裂解生成汽柴油中试工艺。
首先,本文对废塑料催化裂解生成汽柴油中试工艺的原理进行了探讨。
废塑料中含有大量的有机物,这些有机物可以通过高温催化裂解作用转化为汽柴油组分。
为了提高催化裂解效率,采用了多种高效催化剂,如有机酸和金属催化剂,在恒温的条件下进行催化反应,使废塑料中的有机物可以完全转化为汽柴油组分。
其次,本文进行了加速废塑料催化裂解生成汽柴油中试工艺的研究。
首先,采用磁控丝阀控制反应器中的温度,同时当温度达到设定值时,磁控丝阀将自动启动,以便调节温度使得催化处理效果更好;其次,研究了催化剂的应用,一般采用酸催化剂、金属催化剂和其他有机催化剂等,这些催化剂能够提高催化裂解的效率,使废塑料催化裂解生成汽柴油的效率更高;第三,为了提高废塑料催化裂解生成汽柴油的效率,研究了反应器外围装置,如添加热量保护装置、增加操作空间等,以便更好地控制反应过程,并尽可能提高废塑料催化裂解生成汽柴油的效率。
最后,本文对废塑料催化裂解生成汽柴油中试工艺的可行性进行了分析,结果表明,废塑料催化裂解生成汽柴油在实际操作中具有一定的可行性。
由于废塑料中含有大量有机物,经过催化裂解,可以提取出汽柴油组分,而且工艺操作简单,投资少,还可以减少石油的消耗,从而节约能源,减少对传统能源的依赖,减轻环境负担,可以说是一项非常有效的新能源利用技术。
综上所述,废塑料催化裂解生成汽柴油是一种可行的新能源利用技术,可以节约能源,减少环境负担。
本文分析了废塑料催化裂解生成汽柴油中试工艺的原理及加速技术,为进一步开发废塑料催化裂解生成汽柴油工艺提供了技术支持。
废塑料催化裂解生成汽柴油中试工艺的研究

废塑料催化裂解生成汽柴油中试工艺的研究近年来,全球能源发展迅速,传统石油资源的消耗量不断增加。
此外,由于地球温室气体的排放,全球气候变暖已成为全球关注的焦点。
因此,寻找新型能源已成为一项重要的任务。
近年来,业界开始关注废塑料,并相信它可能成为一种完全新的能源替代选择。
废塑料是通过热集成而制成的。
能够在裂解条件下,还原裂解产物,要求废塑料必须具有良好的稳定性和可控性。
催化裂解是一种有效的利用废塑料的方法,它可以把废塑料分解成优质汽油、柴油和其他化学品。
本研究以废塑料的催化裂解生成汽柴油为目标,以金属氧化物(MnO2)和金属硫化物(MoS2为催化剂,以三支碳苯和乙醇为溶剂,以温度在250℃、压力0.1MPa条件下催化裂解废塑料,对催化剂MnO2和MoS2的运行状态、裂解产物和汽柴油性能进行了研究。
研究表明,MnO2和MoS2的运行状态和活性均较差,随着催化时间的增加,催化剂的活性和运行状态有所提高,催化剂的运行状态仍然是不稳定的,但其可控性好于MoS2。
研究还表明,溶剂对催化剂的运行状态具有积极的影响,当温度较低时,催化剂活性较好;结果表明,汽柴油的性能良好,粘度变化率较小,所产汽柴油符合国家(GB/T511 - 2003)标准。
因此,本研究表明,利用金属氧化物(MnO2)和金属硫化物(MoS2)作为催化剂,以三支碳和乙醇为溶剂,在250℃、压力0.1MPa条件下,使用废塑料可以生产高品质汽柴油。
本研究为废塑料催化裂解生成汽柴油提供了新的技术选择。
综上所述,近年来,全球能源发展迅速,传统石油资源的消耗量不断增加。
废塑料已成为一种完全新的能源替代选择。
本研究表明,利用金属氧化物(MnO2)和金属硫化物(MoS2)作为催化剂,以三支碳和乙醇为溶剂,在250℃、压力0.1MPa条件下,废塑料可以催化裂解生成汽柴油,汽柴油的性能良好,符合国家标准。
本研究为废塑料催化裂解生成汽柴油提供了可能性,对于未来利用废塑料具有重要的意义。
废物炼制柴油
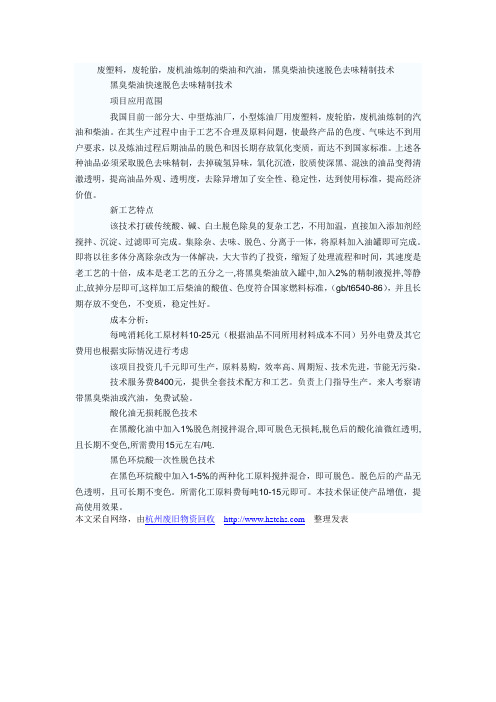
废塑料,废轮胎,废机油炼制的柴油和汽油,黑臭柴油快速脱色去味精制技术黑臭柴油快速脱色去味精制技术项目应用范围我国目前一部分大、中型炼油厂,小型炼油厂用废塑料,废轮胎,废机油炼制的汽油和柴油。
在其生产过程中由于工艺不合理及原料问题,使最终产品的色度、气味达不到用户要求,以及炼油过程后期油品的脱色和因长期存放氧化变质,而达不到国家标准。
上述各种油品必须采取脱色去味精制,去掉硫氢异味,氧化沉渣,胶质使深黑、混浊的油品变得清澈透明,提高油品外观、透明度,去除异增加了安全性、稳定性,达到使用标准,提高经济价值。
新工艺特点该技术打破传统酸、碱、白土脱色除臭的复杂工艺,不用加温,直接加入添加剂经搅拌、沉淀、过滤即可完成。
集除杂、去味、脱色、分离于一体,将原料加入油罐即可完成。
即将以往多体分离除杂改为一体解决,大大节约了投资,缩短了处理流程和时间,其速度是老工艺的十倍,成本是老工艺的五分之一,将黑臭柴油放入罐中,加入2%的精制液搅拌,等静止,放掉分层即可,这样加工后柴油的酸值、色度符合国家燃料标准,(gb/t6540-86),并且长期存放不变色,不变质,稳定性好。
成本分析:每吨消耗化工原材料10-25元(根据油品不同所用材料成本不同)另外电费及其它费用也根据实际情况进行考虑该项目投资几千元即可生产,原料易购,效率高、周期短、技术先进,节能无污染。
技术服务费8400元,提供全套技术配方和工艺。
负责上门指导生产。
来人考察请带黑臭柴油或汽油,免费试验。
酸化油无损耗脱色技术在黑酸化油中加入1%脱色剂搅拌混合,即可脱色无损耗,脱色后的酸化油微红透明,且长期不变色,所需费用15元左右/吨.黑色环烷酸一次性脱色技术在黑色环烷酸中加入1-5%的两种化工原料搅拌混合,即可脱色。
脱色后的产品无色透明,且可长期不变色。
所需化工原料费每吨10-15元即可。
本技术保证使产品增值,提高使用效果。
本文采自网络,由杭州废旧物资回收整理发表。
废塑料催化裂解生成汽柴油中试工艺的研究
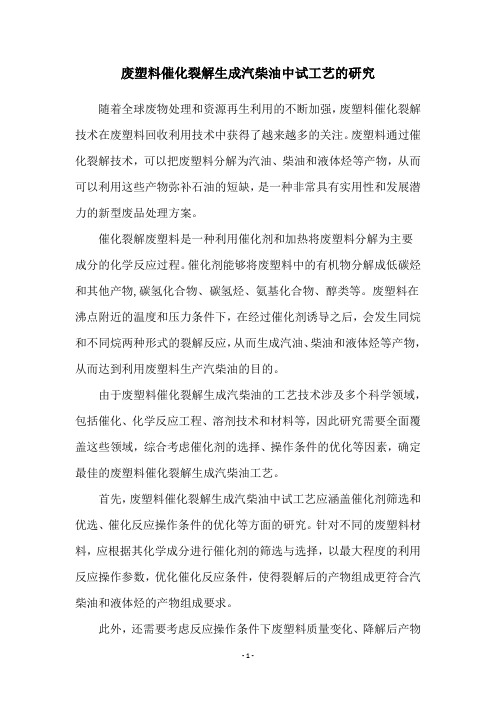
废塑料催化裂解生成汽柴油中试工艺的研究随着全球废物处理和资源再生利用的不断加强,废塑料催化裂解技术在废塑料回收利用技术中获得了越来越多的关注。
废塑料通过催化裂解技术,可以把废塑料分解为汽油、柴油和液体烃等产物,从而可以利用这些产物弥补石油的短缺,是一种非常具有实用性和发展潜力的新型废品处理方案。
催化裂解废塑料是一种利用催化剂和加热将废塑料分解为主要成分的化学反应过程。
催化剂能够将废塑料中的有机物分解成低碳烃和其他产物,碳氢化合物、碳氢烃、氨基化合物、醇类等。
废塑料在沸点附近的温度和压力条件下,在经过催化剂诱导之后,会发生同烷和不同烷两种形式的裂解反应,从而生成汽油、柴油和液体烃等产物,从而达到利用废塑料生产汽柴油的目的。
由于废塑料催化裂解生成汽柴油的工艺技术涉及多个科学领域,包括催化、化学反应工程、溶剂技术和材料等,因此研究需要全面覆盖这些领域,综合考虑催化剂的选择、操作条件的优化等因素,确定最佳的废塑料催化裂解生成汽柴油工艺。
首先,废塑料催化裂解生成汽柴油中试工艺应涵盖催化剂筛选和优选、催化反应操作条件的优化等方面的研究。
针对不同的废塑料材料,应根据其化学成分进行催化剂的筛选与选择,以最大程度的利用反应操作参数,优化催化反应条件,使得裂解后的产物组成更符合汽柴油和液体烃的产物组成要求。
此外,还需要考虑反应操作条件下废塑料质量变化、降解后产物组成变化以及催化剂使用寿命等方面,并对催化剂在多次使用后的反应活性进行考察,综合考虑反应过程中产物的物理化学性质,找到最有效的废塑料催化裂解生成汽柴油中试工艺。
最后,研究也应设计并研制一套完整的废塑料催化裂解生成汽柴油的实验流程,以进一步验证催化剂和反应操作条件的优选结果,确保催化剂和反应操作条件在实际生产过程中的正常操作性能,确保最终生产出的汽柴油达到技术标准和环保标准。
综上所述,废塑料催化裂解生成汽柴油中试工艺的研究将使废塑料分解技术得到进一步发展,有助于利用废塑料生产石油替代燃料,解决石油资源短缺和环境污染问题,是一种可行价值的解决方案。
废塑料与废机油共催化裂解-催化改质制取汽、柴油新技术
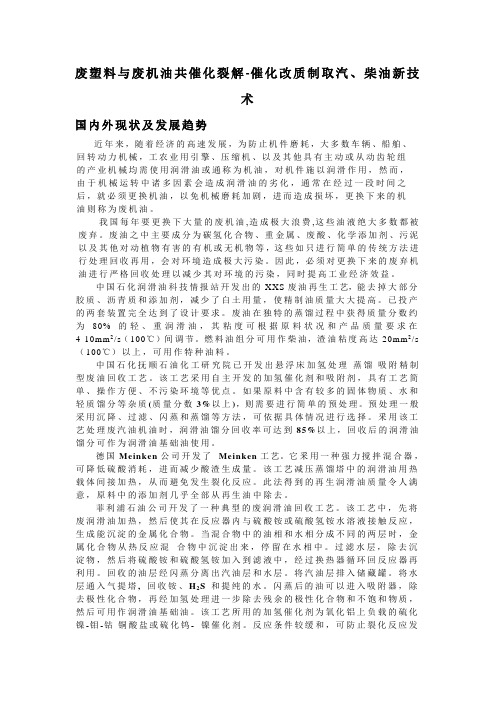
废塑料与废机油共催化裂解-催化改质制取汽、柴油新技术国内外现状及发展趋势近年来,随着经济的高速发展,为防止机件磨耗,大多数车辆、船舶、回转动力机械,工农业用引擎、压缩机、以及其他具有主动或从动齿轮组的产业机械均需使用润滑油或通称为机油,对机件施以润滑作用,然而,由于机械运转中诸多因素会造成润滑油的劣化,通常在经过一段时间之后,就必须更换机油,以免机械磨耗加剧,进而造成损坏,更换下来的机油则称为废机油。
我国每年要更换下大量的废机油,造成极大浪费,这些油液绝大多数都被废弃。
废油之中主要成分为碳氢化合物、重金属、废酸、化学添加剂、污泥以及其他对动植物有害的有机或无机物等,这些如只进行简单的传统方法进行处理回收再用,会对环境造成极大污染。
因此,必须对更换下来的废弃机油进行严格回收处理以减少其对环境的污染,同时提高工业经济效益。
中国石化润滑油科技情报站幵发出的X XS废油再生工艺,能去掉大部分胶质、沥青质和添加剂,减少了白土用量,使精制油质量大大提高。
已投产的两套装置完全达到了设计要求。
废油在独特的蒸馏过程中获得质量分数约为80% 的轻、重润滑油,其粘度可根据原料状况和产品质量要求在4-10mm2/s(100℃)间调节。
燃料油组分可用作柴油,渣油粘度高达20mm2/s (100℃)以上,可用作特种油料。
中国石化抚顺石油化工研究院已开发出悬浮床加氢处理-蒸馏-吸附精制型废油回收工艺。
该工艺采用自主开发的加氢催化剂和吸附剂,具有工艺简单、操作方便、不污染环境等优点。
如果原料中含有较多的固体物质、水和轻质馏分等杂质(质量分数3%以上),则需要进行简单的预处理。
预处理一般采用沉降、过滤、闪蒸和蒸馏等方法,可依据具体情况进行选择。
釆用该工艺处理废汽油机油时,润滑油馏分回收率可达到85%以上,回收后的润滑油馏分可作为润滑油基础油使用。
德国Me ink e n公司开发了Me ink e n工艺。
它釆用一种强力搅拌混合器,可降低硫酸消耗,进而减少酸渣生成量。
一种利用废塑料生产燃料油方法
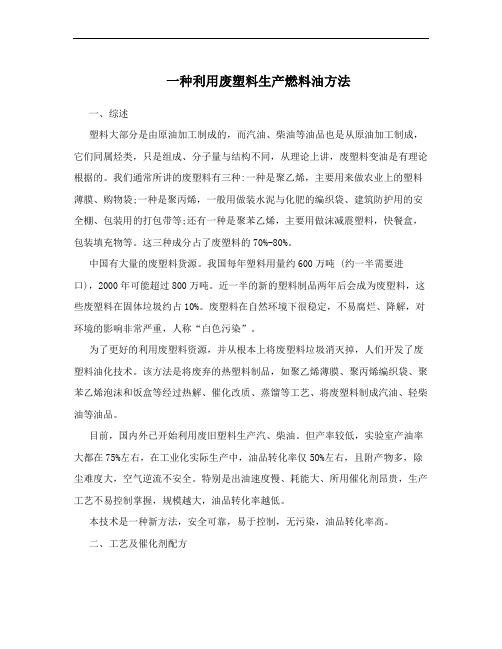
一种利用废塑料生产燃料油方法一、综述塑料大部分是由原油加工制成的,而汽油、柴油等油品也是从原油加工制成,它们同属烃类,只是组成、分子量与结构不同,从理论上讲,废塑料变油是有理论根据的。
我们通常所讲的废塑料有三种:一种是聚乙烯,主要用来做农业上的塑料薄膜、购物袋;一种是聚丙烯,一般用做装水泥与化肥的编织袋、建筑防护用的安全棚、包装用的打包带等;还有一种是聚苯乙烯,主要用做沫减震塑料,快餐盒,包装填充物等。
这三种成分占了废塑料的70%-80%。
中国有大量的废塑料货源。
我国每年塑料用量约600万吨 (约一半需要进口),2000年可能超过800万吨。
近一半的新的塑料制品两年后会成为废塑料,这些废塑料在固体垃圾约占10%。
废塑料在自然环境下很稳定,不易腐烂、降解,对环境的影响非常严重,人称“白色污染”。
为了更好的利用废塑料资源,并从根本上将废塑料垃圾消灭掉,人们开发了废塑料油化技术。
该方法是将废弃的热塑料制品,如聚乙烯薄膜、聚丙烯编织袋、聚苯乙烯泡沫和饭盒等经过热解、催化改质、蒸馏等工艺、将废塑料制成汽油、轻柴油等油品。
目前,国内外已开始利用废旧塑料生产汽、柴油。
但产率较低,实验室产油率大都在75%左右,在工业化实际生产中,油品转化率仅5O%左右,且附产物多,除尘难度大,空气逆流不安全。
特别是出油速度慢、耗能大、所用催化剂昂贵,生产工艺不易控制掌握,规模越大,油品转化率越低。
本技术是一种新方法,安全可靠,易于控制,无污染,油品转化率高。
二、工艺及催化剂配方将废塑料置于气热裂解炉内,炉温控制在180-500?,同时将水蒸汽送入气热裂解炉内;将气热裂解炉内生成的石蜡蒸汽和燃料油混合汽引入催化裂解炉,炉温180-480?,经炉内AL203分子筛进一步裂解重整;将催化裂解炉内充分裂解重整后的燃油汽引入精馏塔蒸馏出汽油和柴油。
将废塑料置于气热裂解炉内裂解时,是通过伸入气热裂解炉底部的蒸汽管将水蒸汽送入气热裂解炉内,还通过从气热裂解炉上部引出而与上述蒸汽管相通,且带控制阀的气管在停止蒸汽管送汽的情况下,使水蒸汽在气热裂解炉内循环。
废塑料制油操作方法

废塑料制油操作方法废塑料制油是一种将废弃塑料经过加热、裂解、蒸馏等工艺转化为可再生能源的方法。
该技术具有环保、节能和经济的优势,可以有效地解决塑料垃圾带来的环境问题。
下面将详细介绍废塑料制油的操作方法。
一、废塑料制油的原理废塑料制油的原理是通过热解或催化热解的方式将废塑料转化为液体燃料油。
废塑料经过加热和压力处理后,在高温下分解为气体、液体和残渣等三种组分。
其中,液体组分就是可再生能源的油品,可以被用作柴油、汽油等燃料的替代品。
二、废塑料制油的操作步骤1. 废塑料的预处理:将废塑料进行清洗、切碎和分类。
清洗可以去除塑料表面的污物和杂质,切碎有利于后续的加热和加压处理,分类则是为了分离不同类型的塑料,以便根据其特性进行不同的处理。
2. 加热和加压处理:将经过预处理的废塑料进入反应装置,通过加热和加压使其发生热解反应。
加热的温度通常在300-450摄氏度之间,加压则是为了提高反应的效率和产率。
3. 液体油品的分离:经过加热和加压处理后,废塑料开始发生热解反应,产生气体、液体和残渣等三种组分。
在此步骤中,需要对液体油品进行分离。
一般通过减压和冷却等措施,使液体油品冷凝成液态,方便后续的提纯和利用。
4. 油品的提纯和净化:从热解反应产出的液体油品中,常常还含有杂质和不同碳链长度的烃类混合物。
为了使得提取的油品能符合商业化销售的标准,需要进行提纯和净化的处理。
常用的方法是通过蒸馏、溶剂洗涤和催化加氢等步骤,去除杂质和调整烃类的组分和结构。
5. 油品的利用和回收:提纯净化后的油品可以直接用作柴油、汽油或工业燃料的替代品,同时还可以用于化工行业的原料和能源供应。
此外,还可以通过进一步处理和改性,将其应用于塑料制品的生产过程中,实现资源的循环利用。
三、废塑料制油的注意事项1. 安全操作:废塑料制油过程中要注意安全,避免发生爆炸、火灾等事故。
需要严格控制反应温度和压力,防止过高的温度和压力造成设备损坏和人员伤害。
废弃塑料制备燃料油的技术研究

废弃塑料制备燃料油的技术研究第一章:引言废弃塑料的处理和利用已经成为当前环保领域的研究热点。
废弃塑料作为一种可再生、易处理的资源,可以在不增加二氧化碳排放和减少传统石化原料的使用的情况下,制备出多种高附加值的产品,其中包括燃料油。
本文对现有的废弃塑料制备燃料油技术进行了研究,探讨了其制备过程、工艺优化、产品提纯等方面的问题。
第二章:废弃塑料的分解废弃塑料分解是制备燃料油的第一步。
目前常用的分解方法有热解和催化裂解两种。
其中热解是通过高温将废弃塑料直接分解成液体烃类,不需要添加任何催化剂。
但热解法的主要问题是产物组分复杂,难以进行进一步加工提纯。
催化裂解则是通过在适当的反应条件下,在催化剂的作用下将废弃塑料分解为油气混合物,其优点在于可以得到较为单一的产品,且所需催化剂的用量较少。
但催化裂解也存在一些问题,如催化剂选择、反应温度、反应时间等方面需要进行优化。
第三章:燃料油制备的工艺优化在废弃塑料分解后得到的油气混合物中,燃料油只是其中的一种组分。
为了获得更高的燃料油产率和更高的燃料质量,需要对制备工艺进行优化。
其中包括反应温度、催化剂用量、反应时间、氢气压力等参数的优化。
同时,为了降低产品中杂质的含量,还需要考虑净化工艺的优化。
这些优化措施可以有效提高制备效率和燃料质量。
第四章:燃料油的提纯生产过程中获得的燃料油仍然含有一定量的杂质和残留催化剂。
为了获得更高纯度的燃料油,需要进行进一步提纯。
提纯包括溶剂抽提、蒸馏、热解等方法。
其中,溶剂抽提和蒸馏是较为常见的方法。
溶剂抽提法通过有机溶剂将油中的杂质分离出来,提高燃料油的纯度。
蒸馏法则是通过不同沸点的油组分之间的分离达到提纯的目的。
第五章:燃料油的性能测试在燃料油制备过程中,需要对产品的性能进行测试。
常见的性能测试包括密度、粘度、含硫量、含氧量、馏程等。
这些测试结果可以反映出产品的质量和可用性,为后续的产品使用和出售提供可靠的数据依据。
第六章:结论废弃塑料制备燃料油是一种有效的资源利用方式,具有环保、经济、社会价值。
专利名称:一种用废塑料和,或重油生产汽油柴油的方法和设备

专利名称:一种用废塑料和,或重油生产汽油柴油的方法和设
备
佚名
【期刊名称】《广东塑料》
【年(卷),期】2004(000)011
【摘要】本发明公开了一种用废塑料和/或重油生产汽油柴油的方法和设备。
具体地,将同一原料进行两级两种不同温度下的热裂解和催化裂解,进料和排渣连续化,排出的残渣是无机物,产品收率高,生产连续化;它是由裂解反应釜、带螺旋的管式反应器和烃油收集装置等组成。
【总页数】1页(P55)
【正文语种】中文
【中图分类】TE626.2
【相关文献】
1.废塑料生产汽油,柴油最佳生产工艺及设备 [J], 常玉宏
2.废塑料生产汽油,柴油生产工艺及设备 [J], 常玉宏
3.废塑料生产汽油,柴油的生产工艺及设备 [J], 薛福连
4.废塑料生产汽油,柴油最佳生产工艺及设备 [J], 常玉宏
5.废塑料生产汽油,柴油生产工艺设备 [J], 薛福连
因版权原因,仅展示原文概要,查看原文内容请购买。
利用废旧塑料生产汽油、柴油

利用废旧塑料生产汽油、柴油
佚名
【期刊名称】《农学学报》
【年(卷),期】1997(000)006
【摘要】一、简介:随着社会步入二十世纪,塑料及其制品已成为人民生活中不可缺少的物质。
以石油、煤、天然气为原料的合成高分子材料——塑料,产量及发展速度逐日增长,预计到本世纪末,塑料将占世界石化产品的
【总页数】3页(P21-23)
【正文语种】中文
【中图分类】X783.2
【相关文献】
1.利用废旧塑料生产汽油、柴油 [J],
2.利用废旧塑料生产汽柴油的研究 [J], 方永奎;邱安娥;贡学刚
3.关于加强利用废塑料生产汽油、柴油管理有关问题的通知 [J],
4.废旧塑料生产汽油、柴油的技术问题 [J], 陈煜超
5.利用废旧塑料生产汽油柴油技术 [J],
因版权原因,仅展示原文概要,查看原文内容请购买。
- 1、下载文档前请自行甄别文档内容的完整性,平台不提供额外的编辑、内容补充、找答案等附加服务。
- 2、"仅部分预览"的文档,不可在线预览部分如存在完整性等问题,可反馈申请退款(可完整预览的文档不适用该条件!)。
- 3、如文档侵犯您的权益,请联系客服反馈,我们会尽快为您处理(人工客服工作时间:9:00-18:30)。
利用废塑料、废油或重油和炼制燃料柴油的方法技术领域本发明涉及一种工艺方法,具体涉及一种采用废塑料、废油或重油和水在超临界状态下制造燃料柴油的工艺方法。
背景技术柴油是一种重要的动力燃料,在现有的燃料结构中已占有较高的份额。
当今社会经济的迅速发展,特别是交通运输工具的柴油化规模的不断扩大,也对柴油的需求量日益增大。
现在普遍使用的柴油源于石油,而全世界的石油资源是宝贵而有限的,随着现代工业的发展对石油需求也越来越大,能源紧缺的问题也日益突出,节约能源并寻找新型的替代型能源已是当今世界的面临的主要问题之一。
利用废旧物质回收循环再使用是现今节约能源的重要举措。
目前大量的废旧塑料已造成严重的环境污染问题,如何更好的回收利用废旧塑料是普遍关注的社会问题。
同样大量废弃的废机油、地沟油能否重复炼制成燃料油也是能源界所关注的。
目前所见所知的采用废塑料、废油或重油的油化还原技术普遍存在问题是排渣难、反应釜易结焦,导致生产不连续不稳定,也无法大批量的工业化生产。
而且大多数炼制工艺只要采用间断排渣法,且渣中含有大量的烃油,使得产品收率低。
如申请号00121207.9的《用废塑料裂解石油产品的方法》的发明专利申请公开说明书中所公开的用废塑料裂解石油产品的方法同样存在上述问题。
该方法包括将准备好的废旧塑料和裂解催化剂投入反应釜内,然后将反应釜升温至100℃~110℃进行裂解反应,当反应釜继续升温至380 ℃开始产生石油;将所述石油送至蒸馏釜内,加入抗氧化剂静置60分钟,蒸馏釜升温至180℃,保持60分钟,分馏出汽油,然后继续升温到380℃分馏出柴油,在分馏出的汽油中,按5~8%的重量比加入甲醇。
发明内容本发明所要解决的技术问题是提供一种生产稳定流动性好、产品收率高,且没有废渣、废气、废水排放,在超临界状态下采用废塑料、废油或重油和水制造燃料柴油的工艺方法。
为解决上述技术问题本发明实现的技术方案是:一种利用废塑料、废油或重油和水在超临界状态下炼制燃料柴油的方法,包括以下步骤:1、重油或废油从废油罐流出并由换热器加热,然后输送到挤塑机入料口内带动入料口内所加入的被破碎的废塑料进入挤塑机内,所述挤塑机入料口内同时还加入有废塑料用解聚剂和硅酸铝。
2、重油或废油以及塑料通过挤塑机进入溶解釜,在溶解釜内以常压、高温200℃~250℃条件下溶解成熔融状塑料混合油;3、溶解釜出油口排出的塑料混合油连同蒸汽通过输送泵输送到汽化炉,汽化炉的工作压力范围是0.2~0.3Mpa,温度控制在400℃~500℃之间,使得汽化炉中的水为超临界水,使废塑料混合油在高温、短时、快速分解,在汽化管里反应约1-2分钟。
4、废塑料混合油在汽化炉内被加热汽化成气相进入催化塔中进行催化、分解、重组。
5、催化塔塔顶轻组份经过换热器冷却后液化进入油水分离器,油水分离器上层的所得燃料柴油。
本发明相比现有技术具有以下显著效果:本发明采用重油或废油与废塑料混合和水一同在超临界状态下裂解的方法改善了过程的传热和传质条件,提高生产效率和产品质量。
本发明方法避免了现有采用废塑料油化过程中所存在的导热性差,流动性差且容易产生大量残渣和结焦的问题。
本发明方法不但解决的残渣和结焦的问题,而且工艺过程环保,安全避免了三废污染问题。
从汽化炉出来的高温烟气并不是直接排出而是通过多级回收达到能量的最大利用,通过除尘室把少量的微尘粒子收集,从烟道排出的仅仅是二氧化碳气体;催化塔塔底的排出的废渣通过循环系统的送到溶解釜燃烧,故没有废渣等固体物质排出;而从催化塔塔顶出来的轻组份冷却后大部分液化成燃料柴油,少量没有液化的低碳氢化合物也返回到溶解釜燃烧。
附图说明图1是本发明工艺流程示意图。
具体实施方式下面附图通过具体实施例对本发明的其制备方法进行详述:炼制成燃料柴油的原料包括废塑料、重油或废弃的机油、地沟油等废油。
重油资源丰富、价格低廉容易获取,废油可以通过回收得到。
重油或废油放置在废油罐1中待用,废油罐出油口101通过管道连接有加热器901,加热器与蒸汽炉9011连接。
加热器把废油罐中排出的重油或废油加热后通过循环泵 401打入盘管,盘管303焊接在溶解釜3外周,盘管下部入口与循环泵出口管道连接,盘管上部出口连接至挤塑机入料口内。
也就是加热后的重油或废油被输送到挤塑机入料口201。
本发明的循环泵采用压力控制器控制循环泵的正常工作,当循环泵工作压力大于压力控制器所设定的工作压力时,循环泵将自动停止工作,这样可以避免循环泵出现事故。
挤塑机2入料口内同时也加入已被破碎的废塑料,废塑料可以是聚乙烯、聚丙烯、聚丁烯、聚苯乙烯等制品的废弃物。
废油罐中可以是重油,也可以是废油,废塑料与重油或者废油的重量比控制在1∶0.9~1.1左右,废塑料和重油或废油的混合原料来炼制可以提高整个工艺的传热效率,避免结焦同时增加炼制工艺的流动性和稳定性。
为了有利于废塑料的熔融分解,在入料口内还设置有小型螺杆机来向入料口内投放废塑料用解聚剂,解聚剂为氢氧化锌、碳酸镍、硅酸铝、及活性白土的混合物,解聚剂各组份的重量百分比含量是氢氧化锌为1.5~10%、碳酸镍1~5%、硅酸铝5~20%、其余为活性白土,解聚剂的加入量为废塑料总重量的5-20%。
进入入料口的被加热的重油或废油带动废塑料进入挤塑机中,并由挤塑机带动输送到溶解釜上部的入口301。
溶解釜底部设有燃烧器,用于对溶解釜加热。
溶解釜中心设置有搅拌器,搅拌器使得废油或重油废塑料充分融解。
溶解釜上还设置有检测溶解釜内压力和温度的压力表和温度表。
溶解釜内压力保持为常压,温度范围是200℃~250℃。
重油或废油以及塑料在溶解釜内溶解成熔融状塑料混合油。
为了方便把沉淀于溶解釜底的残渣排出溶解釜,在溶解釜底设置有排渣阀门,排渣阀门通过管道连接到排渣罐304,排渣罐中会残留一些塑料油。
为此排渣罐内接出的废油被也通过循环泵回送到挤塑机入料口再次利用,从而提高了物料的利用率。
溶解釜出油口302连接到输送泵402管道中,输送泵管道中与蒸汽管道连同,输送泵将塑料混合油连同蒸汽一起输送到汽化炉5中。
输送泵采用液位感应控制器和压力控制器检测的双重安全保险控制,当液位高于设定的液面时,输送泵停止工作;相反,即工作;或者压力大于设定值时,输送泵停止工作,相反,即工作。
这样可以避免输送泵出现事故。
汽化炉用于把塑料混合油由液态加热汽化成气态。
汽化炉上设有燃烧器,此燃烧器采用温度控制及气相压力控制,当汽化炉内的温度高于设定值时,燃烧器停止工作,相反,即工作;或气相压力大于设定值时,即燃烧器停止工作,相反,即工作。
这样保证了汽化炉的安全正常工作。
汽化炉的工作压力范围是0.2~0.3Mpa,温度控制在400℃~500℃之间。
在超临界状态下,塑料混合油与水在汽化管里进行高温、短时、快速反应,将塑料分解成油分,加上超临界水的存在抑制了缩重合反应的发生,焦化得到控制,故残渣减少而油品的回收率提高。
本发明采用超临界水作为介质,可以使得废塑料分解更加充分。
因温度在374℃以上的超临界水和常温常压的水有完全不同的性质。
在374℃下,通过控制水的压力变化,水的密度由气相向液相变化,同时导电率和离子积亦呈连续变化。
当压力提高到接近液态密度下,亦和常温水一样对离子性质有较高的溶解力。
离子积很大程度随密度提高而增加。
故高密度的超临界水具有离子质溶媒的性质,可作为离子反应场利用。
相反,在同一温度下,由于低密度而接近气相状态时则可提供自由基反应场,故可以通过密度或温度的控制,使反应气氛从离子反应向自由基间变化。
为此,在常温常压下不溶解的无极性有机化合物则易溶于超临界水,加上高温条件,难分解性化合物变为易分解。
催化塔6底层放瓷环,中间层放颗粒活性白土,顶层放4A和5A分子筛。
催化塔内温度控制在320℃,压力是常压或高于常压。
催化塔6塔顶轻组份通过冷凝器903后液化进入油水分离器7,在油水分离器上层流出的就得到燃料油。
在超临界状态下排出的油气中的重组份被催化塔下层的瓷环拦截后,掉进催化塔下的分离器,收集排出作燃料使用、从而保证了油质的清洁达标。
本发明采用的炼制方法,把炼制过程的副产品或废物料都充分回收利用,大大提高了工艺的减排、节能、环保性。
汽化炉中燃烧产生的烟气通过催化塔、由烟气管道806输送到溶解釜和废油罐中回收热量,然后由引风机403 送入除尘器804,除尘后的产生的尾气由烟道805排出。
为了提高安全性在烟气管道中还安装烟道温度过热总控制器,用于预防管道破裂漏气后烟道温度过高时自动关闭整个汽化炉的电源,从而保证了整个汽化炉生产过程的安全性。
进入油水分离器7的未液化的气体从油水分离器顶部排出通过阻火器 801,缓冲罐802经真空泵405由排废气管803输送到溶解釜燃烧再用;在油水分离器底部排出的废水可作循环水用,位于催化塔下的分离器底部的比重较重的碳氢化合物经排渣管排出经冷却器902冷却后用螺杆泵404送回溶解釜燃烧再用。
实施例1采用0.9吨的废塑料和1.1吨的重油以及废油混合加入到挤塑机内。
同时在入料口内加入18公斤的解聚剂,其中解聚剂是按照氢氧化锌为1.5~10%、碳酸镍1~5%、硅酸铝5~20%、其余为活性白土混合而成的。
适量的解聚剂连同原料一起进入挤塑机,挤塑机混合后的原料进入溶解釜,在溶解釜内以釜内温度控制在210℃左右使得上述原料溶解成熔融状塑料油;溶解釜出油口排出的塑料油连同蒸汽通过输送泵输送到汽化炉,汽化炉的工作压力范围是0.2Mpa,温度控制在430℃左右。
在汽化炉内被加热汽化成气相进入催化塔内进行催化反应;催化塔内加入的磁环是30公斤、颗粒活性白土30公斤、 4A和5A分子筛30公斤,催化塔塔顶轻组份经过换热器冷却后液化进入油水分离器,油水分离器上层的所得燃料柴油。
实施例2采用1.2吨的废塑料和0.8吨的重油以及废油混合加入到挤塑机内。
同时在入料口内加入20公斤的解聚剂,其中解聚剂是按照氢氧化锌为1.5~10%、碳酸镍1~5%、硅酸铝5~20%、其余为活性白土混合而成的。
所述解聚剂连同原料一起进入挤塑机,挤塑机混合后的原料进入溶解釜,在溶解釜内以釜内温度控制在240℃左右使得上述原料溶解成熔融状塑料油;溶解釜出油口排出的塑料混合油连同蒸汽通过输送泵输送到汽化炉,汽化炉的工作压力范围是0.3Mpa,温度控制在480℃左右。
在汽化炉内被加热汽化成气相进入催化塔内进行催化反应;催化塔内加入的磁环是32公斤、颗粒活性白土33公斤、 4A和5A分子筛32公斤,催化塔塔顶轻组份经过换热器冷却后液化进入油水分离器,油水分离器上层的所得燃料柴油。
CN91104875.8 C08J11/10 用废塑料制造汽油柴油的方法及装置CN94106337.2 C08J11/04 废塑料制汽油和柴油CN94110379.X C10G1/00 废塑料两段联合裂解制液化气、汽油、柴油和润滑油基础油的原料油CN95106412.6 C10G1/00 废塑料制汽柴油的方法与装置CN99107968.X C10G1/00 用废塑料和或重油生产汽油柴油的方法和设备CN00120728.8 C10G1/00 利用废塑料生产汽油、柴油和液化气的工艺方法及设备CN00110034.3 C10G1/00 利用废塑料炼制汽柴油的设备及其方法CN01100486.X C10G1/10 用废塑料、废轮胎常压制作汽油、柴油的设备CN01113811.4 C10G1/00 一种利用煤炭和废塑料制取代用柴油的配方及其制取方法CN01120570.9 C10G1/00 一种用废塑料和/或重油生产汽油柴油的方法和设备CN00819355.X C10G1/10 由废塑料连续地制备汽油、煤油和柴油的方法和系统CN03119082.0 C10G1/00 用废塑料炼制汽、柴油的方法CN03156958.7 C10G1/00 利用废塑料生产汽油、柴油装置CN03134661.8 C10G1/00 工业化用废塑料生产汽油、柴油的方法CN200510001750.1 C10G1/00 能长周期满负荷运行的废塑料裂解制汽油柴油装置CN200510093794.1 C10G1/00(2006.01) 废塑料热裂解制取柴油的设备和工艺方法CN200810026555.8 C10G1/00(2006.01) 利用废塑料、废油或重油和炼制燃料柴油的方法CN200810225614.4 C10G1/06(2006.01)I 一种废塑料裂解油生产优质柴油调和组分的方法CN201120236078.5 C10G1/00(2006.01)I 废塑料、橡胶、废油一次性产汽柴油天然气电脑控制设备CN93234583.2 C08J11/12 用废塑料、废油、废植物油脚提取汽、柴油用的解聚釜CN94208345.8 C10G9/00 用废塑料提炼汽油、柴油的裂解釜。