乐天旋裁一体机说明书
旋切机说明书

Operating InstructionXINGTAI KEXINGYU MACHINERYMANUFACTURE CO.,LTDPrefaceThank you for using our products.This manual describes the function characteristic, this product installation debugging steps, operation etc.. Put forward by the accident may be caused by improper operation and common troubleshooting methods and matters needs attention.Before using this product, please read this manual carefully first, in order to achieve optimal use effect.Please keep this manual and read it with attention.XINGTAI KEXINGYU MACHINERY MANUFACTURE CO.,LTDA, product overview1.1、Main uses and characteristics of productsComputer numerical control spindle-less peeling machine is used to cut the logs which are made by human or spindle machine into veneers. Double roller of the device is fixed, the blade base move along the parallel guide way, through two feed screws while pushing the blade base seat in the horizontal direction. We use most advanced numerical control systems to get dynamic operation and current rotary cutting wood diameter, friction roller speed, the rotary cutting plate thickness and other parameters, calculate the feed speed, In order to achieve uniform thickness. At the same time, the blade base seat are fixed with the accessory that can adjust the distance between the blade and single roller (function of automatic adjustment of the blade gap).By adopting the structure above, our machine enjoys the merits as below:NC spindle-less system runs by intelligent microcomputer controller, inverter and displacement of NC spindle less rotary cutter sensor components, so it realizes numerical control operation, the true realization of automation. We the following characteristics:1、We use industrial grade control chip, and increase the number of software and hardware anti-jamming measures, the machine has extremely high reliability and stability.2、The use of large screen LCD display, full Chinese menu, the operation interface of Chinese character display working condition of the whole machine and convenient for the user simple and quick setting of the debugging and parameter.3.The core of high speed of calculation, the control model and the flexible patch thickness function, veneer precision up to 0.02mm.4、Configurability is strong, the factory can adjust the parameter according to the different types of rotary cutting machine, the user also can set the parameter according to their own needs.5、With the button fault detection function and parameter of intelligent, reliableself checking function.6、With restore factory default parameter function, users can simply be NC spindle less rotary cutter system restore to factory state.7、Additional powerful, with pieces of thick patch, menu management, error detection, debugging aid, veneer thickness compensation function.8、We use screw propulsion, high precision, small gap, not prone to abnormal sector; the blade gap automatic regulating function, single board to make the rotary cutting out the roughness increased greatly.9、A plate without transmission shaft design, easy to operate.10、Compact structure, stable performance, simple operation, high efficiency and other advantages of production.11、Perfect protection function, has phase lack, the function of overload protection, over current protection, overvoltage protection, so as to ensure the service life of electrical appliances.1.2、Product specifications, technical data(a), the total power: 23.5KW(1) single roller motor 7.5KW-4-B35 (2) 5.5KW-4-B5 double roller motor ,feedmotor (3) 7.5KW-4-B5,(4) the hob cutter motor 1.5KW-4-B5, (5) the transmission belt motor1.5KW-4-B5,(two), a rotary cutter:(1) specification (length * width * thickness) (mm): 1500 x 180 x 16.(2) edged arc length: flat grinding 22 degrees bevel 42-42.5 mm long.(three), the rotary cut wood:(1) the rotary cut wood specifications (diameter * length): the maximumopening 400mm, the longest rotary cutting 1300mm.(2) the small shaft diameter wood core diameter: 24mm.(four), log out board line speed: 45 m / min(five), equipment configuration installed total size (length * width * height): 4300 x 1600 x 1260mm(six), adapted to the voltage range of equipment: 3 phase 380V + 20%(other voltageand frequency according to the customer requirements can be customized).(seven) the work environment requirements:(1)the storage environment: -40 C and 60 C(2)the use of the environment temperature: -10 degrees C and 50 C(3)the maximum relative humidity: 90% relative humidity without condensation or water(4)the maximum operating altitude: 1000 meters below (beyond thisheight increases every100 meters, rated current fall 1%).TWO、Equipment, parts and accessories and working principle2.1、The main components of equipment diagram1, computer control box: the complete equipment of the entire control function.2, operation table: signal transmission to the control box control machine.3, automatic ramming wooden shaft rotary cutting device: after the completion of the remaining wood shaft from the knife to sew on tamping.4, automatic oiling pump: machine oil lubrication of all missing parts of automatic oiling.5, automatic tool setting seam arm frame: adjust the cutter slot arm support.6, automatic tool setting seam track: automatic track adjustment assistance, improving the precision.7, hob cutter motor: model YE90L-4, used to drive the speed reducer drivesthe hob cutting, rotation.8, hob cutting reducer: Type: GR47-Y1.5-4P-11.7-M1, drive motor power reduction partof hob cutter.9, transmission belt motor model: YE90L-4, used to drive the speed reducer to drivethe transmission belt to rotate.10, the transmission belt reducer: type GR47-Y1.5-4P-11.7-M1-B-180,transmission beltmotor powered deceleration section.11, double roller reducer model: GR87-Y7.5KW-4P-11.98-M1-1EC,drive and double rollermotor powered deceleration section.12, double roller motor: type Y2-132M-4, used to drive the speed reducer drives the double roller to rotate.13, a feed screw feed drive force, so that the overall: translation toolturret, completing the power supporting wood veneer when.14, double roll (phi 200): mechanical power transmission wood veneers used to dragthe timber rotation.15, single roller motor model: Y2-132S-4, used to drive the speed reducer, driving a single roll.16, single roller reducer model: GRF87-Y5.5-4P-11.98- phi 300-1FCdrive single roller motor powered deceleration section.17, the feed speed reducer: model GR87-Y7.5-4P-13.38-M1 feed drive motor powerreduction part.18, feed motor: Type: 7.5KW-4 used to drive reducer, driven by the rotationof the feed screw.19, automatic tool setting seam arm rack: used to fix the single roller drive assembly, and complete the regulation of blade gap function.20, automatic tool setting seam track: used to adjust the slope before and afterthe trip, to complete the wood in the rotary cutting diameter from big to small changes in response to the amount of automatic tool setting seam.21, lifting hook: equipment for transportation and hoisting wire rope used to remind. 2.2、Random accessories equipmentSingle roller motor and double roller motor drives the transmission system in each of the friction roller, respectively driven single and double friction roller in therotation, the wood in the middle of a single friction roller and the friction roller is composed of a single pair, friction roller and the friction roller is driven to rotate two together, at the same time, the computer control system is composed of testing friction roller speed encoder detection to the friction encoder roller speed and detection of wood diameter to detect the current rotary cutting wood diameter and user needs rotary cut veneer thickness, calculate out put speed feed motor to drive the feeding device, the turret and single friction roller continuous double friction roller to the direction of movement, thus completing the rotary cutting task.THREE、The rules for safe operation3.1、PrefaceIn this manual, section contains help you safe use of the device's advice about equipment installation, use and maintenance in the process of advice and further relevant information will be described in other chapters, the content is not included in the safety section.3.2、Safety signs and gradeWarning: pay attention to thecontent! The risk of electric shock.Warning: pay attention to the content! Hand squeeze risk.Don't try to in the operation of the equipment Repairs, adjustment, lubrication orcleaning machine.Warning: pay attentionto timing gas content.3.3、Equipment safety operation regulationWarning! The use of this equipment, must be absolutely obey safety basic matters, to prevent electric shock, personal injury and other accidents. Before use, please read the following safety operation specification carefully, after reading, please pay attention to the preservation.Equipment in most of the accidents are caused by failure to observe the safety rules of operation for the cause, but very important rule is the operation of equipment, maintenance of the machine, don't wipelubrication; failure outage in repair equipment, first stop; equipmentgrounding should always check. Safety devices keep equipment manufacturers to provide the isonly used to provide the most basic accident prevention, the work of the main responsibilities will still equipment owners and staff who are responsible for the operation ,maintenance and repairingEquipment owner must ensure that: the device associated with the personnel have been related to the rules of safe operation training safety operation rules posted in the relevant regional.Note: a comprehensive reading and pay attention to the following safety rulesThe operation of machine1, equipment maintenance must be trained healthy body, adapt to this work and can reliably complete staff bear.2, do not allow alcohol, take drugs or similar situation of personneloperation, maintenance and repair of the equipment.3, the equipment before the start, operators should check the safety facilities all is normal and check the equipment without obvious defects.4, if the device has any defect, especially relates to safety operationregulation aspect, the operator shall immediately report to the leadership responsiblefor repair or inform the personnel.5, if the crisis to the safe operation of equipment problems, the equipment mustbe immediately stopped, cut off the power supply, to make the warning signs on the equipment. 6, to repair or other work in equipment, involving all staff will being formed, if the equipment must be the power supply, special care should be the power switch.7, the equipment can only be used for the design of the manufacturers use for rotary cutting wood, can not be used for other purposes.8, improve equipment technology will affect the operation of the equipment and the safety of people, must be authorized by the manufacturers or manufacturers of staff, otherwise manufacturers not by modifying the cause for the loss.9, if cannot guarantee the safety of the normal operation of equipment in theinstallation, maintenance or repair process, must be carried out byprofessional licensing professionals, these personnel must be guaranteed toprevent personnel injury and equipment damage.10, operators shall wear approved protective clothing canpreventaccidents. Work no rings, watches, jewelry, necklace, hanging looseticket clo thing, such as a tie, torn clothes, ordinary shoes, not buckled coat or not pullthe zipper to avoid machine rotating part, which caused the loss or damage, longhair should wear safety helmet.11, cleaning equipment, must stop power supply, pay attention to prevent cuts, and using appropriate methods to clean up.13, the equipment must have a good grounding! Do not let children get closeto the equipment, task irrelevant personnel must stay away from.12, pay attention to the usual refueling and maintenance equipment.3.4、The safety code for equipment before the start and operation.1, do not run the equipment in the equipment, indicating lights and sicksituation under control component fault.2, the equipment before the start, should ensure that all components are installed correctly, and no component damage, the various parts of the lubrication good short of oil, of the operating button functions clear ,all other objects in a machineindependent (cloth, tools, iron and other equipment) should take.3, the power supply voltage is higher or lower than the voltage range of the equipment requirements, do not give power transmission equipment, otherwise cause electricalparts damaged.4, the electric control system after the power is switched on, live electrical element is very dangerous, non professionals do not contact ,so as to avoid the risk of electric shock. 5, rotary cutting process, should first stop main engine, allowed to boot into the log. The process of the operation of 6, equipment, prohibited the use of repair tools and cleaning of utensils and other objects are dangerous operation, not just tothe equipment reached.7, in the rotation process, all rotating parts, lightly hand touch avoid,non operating personnel are prohibited from near, prohibit the removal or open the cover. 8, equipment lubrication, do not use hand directly touch device.9, wood rotary cut to the final application of wooden shaft or other objects to knock down the remaining wood shaft, should not be hand contact with wood shaft.10, equipment operation should be specifically responsible for, other personnel can notbe hands-on, avoid the miss operation danger. The operator must be in a stable and balanced work on the ground, must ensure good workplace lighting equipment.11, don't let the equipment run unattended.12, equipment operation, pay attention to whether there is abnormal sound, such as abnormal, should immediately stop the machine, cut off the power supply, must find out the cause of the malfunction and ruled out before test.13, found in normal running, promptly notify the maintenance person in charge. All repair and maintenance must be in accordance with safety procedures in thismanual operation in the accident prevention regulations.3.5、Restrictions on the use of time1, in the use of technology within the prescribed scope characteristics using the device. 2, can be used for purposes of design, do not used for other purposes, such as rotary cutting steel, rubber, plastic, because does not have the use of the design.3, do not use the device of rotary cutting technology in excess of the prescribed in this manual diameter wood.4, do not exceed the working load equipment calibration using the device.5, don't be equipment platform as storing tools, appliances, cloth etc .where objects. 6, do not use outdoors equipment or exposed to rain or humid environment.7, it must be used in the power supply voltage range of equipment within the requested. FOUR、Delivery, delivery, installation4.1、DeliveryEquipment in the factory has been in the factory inspection test, electrical system and moving parts are working properly. In the inspection process, with different diameters of logs were peeling test ,inspection reached the factory technical requirements.4.2、Equipment shippedAll components, including removing the components, packagingequipment in the prior to shipment are passed through the inventory and inspection. Receiving equipment, should check whether there is damaged during transport components. Unless otherwise requested, general equipment in the shipment, the rotary cutter is fixed on the blade base seat of the knife surface. The protective measures against the metal parts not painting, to prevent oxidation during the transportation andstorage.4.3、Hoisting equipmentResponsible for lifting personnel must be highly concentrated in the lifting process, avoid injury or damage to the goods. Equipment loading and unloading can be carried out and move with the forklift truck, or by crane or crane, the prohibition of the use of two or three hook hoisting!.Process equipment move in, try to keep your weight down, maximum limit maintain stability and visibility.4.4、Equipment installationEnsure that the equipment is fixed on the level and firm ground, to run when the machine smooth, no significant vibration principle. The ground must be capable of bearing the weight of equipment safety; equipment installation in the lighting good place. Equipment around to leave enough space, in order to facilitate the operation and future maintenance. Reservation and operation and minimum auxiliary space equipment installation locationAfter positioning the device, remove the friction roller and the guide, the sliding device protective paper, rust proof oil, clean the machine.4.5、The power supply connection note: the work mustbe completed by professionalsElectrical components list:1, the rotary cutting machine: 7.5KW special inverter2, 380V AC contactor3, the miniature circuit breaker4, terminal blocksOpen the electrical control cabinet, power lines willbe received aminiature circuit breaker.Note: well equipment grounding, always keepthe equipment good grounding.4.6、Replacement and cutter rotary cutting knife high adjustmentAfter the rotary cutting knife used for a period of time, the cutting edge wear appear, this time will affect the quality of rotary cut veneer, rotary cutter needs to be detached for edge grinding knife sharpener. After grinding according to the listed below measurement of rotary cutter heightRight angled corner ruler measurement tool (300mm) Straightedge rule (150mm)Methods of measurement:The first step (right angle corner ruler close double roller and double roller seat) The second step (when measuring ruler to vertical)Generally the height of the blade is 114-115 mm, if the veneer thickness below 1.5mm,the height of blade is 114mm, if the veneer thickness is more than 1.5mm,then the height of blade is 115mm, the gap of single roller (120mm diameter) and double roller (120mm diameter) is 32-34mm, if the veneer thickness below 1.5mm,the gap is 34mm, if the veneer thickness is 1.5-2.0mm,then the gap is 33mm. If the veneer thickness is 2.0-2.6mm,then the gap is 32mm If the veneer thickness is more than 2.6mm,pls ask us for the height of blade and the gap between single roller and double roller.Measurement of attention: 1, square and close, the friction roller.In 2, tighten the knife pressure plate, measuring rotary cutter when the installation is completed, whether the size of change.3, a rotary knife ends error cannot be more than 0.5mm.4, a rotary cutter and a blade base seat of the knife surface must clean, often of butter. 5, the replacement of rotary cutting knife, must cut off the power supply, also pay attention to prevent the blade.FIVE、Method of use5.1、Control panel1, equipment switch is switched on by the power supply, power indicatorlight and computer panel should be light, or electrical equipment systemfailure, should be carried out maintenance.2, equipment first sent electricity or power after re transmission, single roller and a knife bed back rewind to the maximum position, have rear limit switch stop. To complete the equipment data detection, rear can automatically boot.Note: the equipment after power failure, re energized, will perform this check, suchas travel switch used in damage, should be replaced promptly.To perform this check, the middle do not operate cross switch or fast forward rewind button. To perform this check, equipment can not be peeled wood; as a result of accidental power outage caused wood card inside the device ,manual will be to removethe rear wood equipment electricity.3, the manipulation of cross switch, make single friction roller left two frictionroller, starting friction roller motor, check the friction roller turnis consistent and below, such as compliance can be put into the wood ,for rotary cutting. If the steering as shown on the contrary can adjust the total power line cutting.Note: in case of emergency, the user can directly through the power switch off the power.5.2 Debugging operating system interfaceOperation panel for each key function introductionThe function keys are used mainly for various parameter switching interface settings. At the press of the button for 3 seconds can be parameters the next page interface to view and set, to see the other parameters interface can continue to press this function key.The function button is used to display the current parameter setting interface on a page. In need of machine tool position detection, press the function button for 3 seconds. The knife has no page table position nself page (see Figure 1-1): open the equipment of main engine start ,the knife bed will slowly forward, when touch stroke switch, automatically close the current knife bed position detection is completed.When you change or view the main parameters after finished, press this button to return to the initial host page. Press and hold for 3 seconds after the current page knife table position shows yet self-study page. Open the equipment of main engine start, deviceautomatically opened, quickly back to the knife bed opening the maximum position, the device host to start, with the cutting knife and knife bed forward. Automatic cut wide, until the wood veneer finish.In the initial interface press this function keys can be on the plate rotary cutting thickness increase adjustment, each time, increased by 0.01mm.In the initial interface press this function keys can be on the plate rotary cutting thickness is reduced to adjust, press each time, reduce the 0.01mm.In the initial interface press this function keys can be on the plate rotary cutting width increase adjustment, each time the increase of 0.1 mm.In the initial interface press this function keys can be on the plate rotary cutting width decreases adjustment, each time, reduce the 0.1 mm.The first interface system (limit setting program) parameter adjustmentIn the initial main interface of the stationary state, hold for three seconds, the interface, according to the following steps of adjusting the parameters setting.1. Wood core diameter to press the required changes.2. Change the equipment within the permissible range of the largest diameter can be rotary cut wood. Can not exceed the scope of changing this parameter. General Factory maximum opening diameter of 400 mm.Second system interface (width thickness calibration procedure)parameter adjustmentIn the last operation interface adjustment or view is completed, press again once, this interface, follow the steps of the adjustment settings.1.First measured actual current slab width size rotary cutting machine cut, and then the real size measurement by pressing the two function keys to the actual width of the size of the input.2.First measured the actual thickness of slab size current rotary cuttingmachine cut, and then the real size measurement by pressing the two function keys to the actual thickness of the size of the input.Third system interface (tail cutter calibration procedure) parameter adjustmentIn the last operation interface adjustment or view is completed, press again once, this interface, follow the steps of the adjustment settings.1. To measure the real width the last piece of skin current rotary cutting machine cut off, and then the real size measurement by pressing thetwo function keys to the actual width of the size of the input2. By pressing the two function keys to adjust the tail cutter correction coefficient, the adjustment range: 0 - 5. In general do not need this parameter is adjusted, default is3. (debugging experience: this parameter is set smaller rotary cutting thickness is uniform, but will cause the length differences in size the last piece of skin becomes large. If the parameter is set larger, uneven will lead to skin rotary cutting thickness, but can ensure the length differences in size the last piece of skin becomes small.)System interface (fourth stop setting program) parameter adjustmentIn the last operation interface adjustment or view is completed, press again once, this interface, follow the steps of the adjustment settings.Press the edit machine tool rotary cutting back automatically stop and continue to cycle after the completion of the position. Debugging experience: most wood such as rotary cutting diameter were within 120 mm, then it can be modified automatically back position is 150 mm ,which can improve the work efficiency.Click to change the selection procedure of circulatory function is open, the general default settings for the open state.System interface (sixth back automatically set the parameters of the adjustment of parameters)In an operation interface adjustment or view is completed, press again once, this interface, follow the steps of the adjustment settings.Press the adjustment of wood veneer finish in the automatic withdrawal process in the driving motor open position of single and double drum. If this parameter is changed to 0, then the single and double roller drive motor will be in the running state. Debugging experience: This is the consequence of a wood core won't last hanging in the blade and the tail plate thickness is thin.。
全自动衬衫冷折装袋机使用说明书

全自动衬衫冷折装袋机Automatic Shirt Pocket Setter (MB1002B -1-S7300A-603P)使用说明书Instruction Manual常州智谷机电科技有限公司CHANGZHOU WISDOM &VALLEY ELECTRICAL TECHNOLOGY CO.,LTD在使用本设备之前请先阅读本使用说明书Please read the operation manual of the touch screen interface before using the device 请将本使用说明书放在便于查阅的地方保管Please keep this operation manual of touch screen interface in convenient placeforreference2020.03版本信息/Version感谢购买IMB工业用缝纫机。
在使用此机器之前,请仔细阅读以下的说明,这样可以更好地帮到您了解此机器的相关操作。
这些说明是根据现行的条例明确阐述了正确的工作方法。
Thank you for purchasing this industrial sewing machine from IMBBefore using this automatic unit,please read the following instructions,which will help you tounderstand how the machine operates.These instructions illustrate the correct working methods to comply with current regulations.在没有得到IMB授权许可的前提下,此说明书的任何部分是不可以被复制或者转录的。
说明书的内容可能被修改,而不需预先通知。
LECA6 最新官方中文操作手册
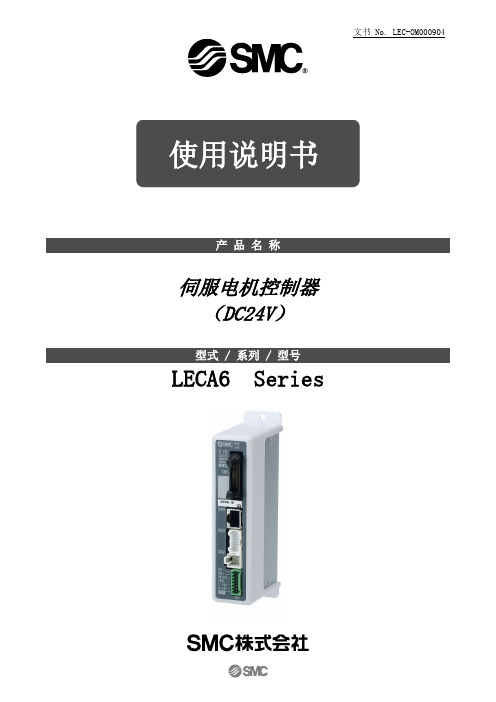
14.1. 设计注意事项 ..................................... 54 14.2.安装 ............................................. 55 14.3. 使用注意事项 ..................................... 56 14.4. 使用环境 ......................................... 57 14.5. 维护检查的注意事项 ............................... 58 14.6. 带锁执行器的注意事项 ............................. 58
目录
1. 安全注意事项 ............................. 4
2. 产品概要 ................................. 6
2.1. 产品特点 ............................................ 6 2.2.型号表示方法 ......................................... 7 2.3 产品构成 ............................................. 8 2.4 步骤(直到执行器动作为止) ............................. 9
(1) 推压动作成功时 .................................. 35 (2) 推压动作失败时(空振) ............................ 35 (3) 推压动作结束后工件移动的场合 .................... 35 8.4 对于控制器的输入信号的响应时间 ...................... 36 8.5 关于运行中的中断方法 ................................ 36
多功能洗涤机操作手册说明书

CONTENTSPage Product information . . . . . . . . . . . . . . . . . . . . . . . . . . . . . . . . . . . .3• Important safety advice . . . . . . . . . . . . . . . . . . . . . . . . . . . . . . . . . . . . . . .3• Guidelines for the operator . . . . . . . . . . . . . . . . . . . . . . . . . . . . . . . . . . . . .3• Working principle . . . . . . . . . . . . . . . . . . . . . . . . . . . . . . . . . . . . . . . . . . . .3• Know your machine . . . . . . . . . . . . . . . . . . . . . . . . . . . . . . . . . . . . . . . . . .4 Preparing for use . . . . . . . . . . . . . . . . . . . . . . . . . . . . . . . . . . . . . . . .5• Assembly . . . . . . . . . . . . . . . . . . . . . . . . . . . . . . . . . . . . . . . . . . . . . . . . . . .5• Brush selection guide . . . . . . . . . . . . . . . . . . . . . . . . . . . . . . . . . . . . . . . . .6• Brush identification . . . . . . . . . . . . . . . . . . . . . . . . . . . . . . . . . . . . . . . . . .6 Controls . . . . . . . . . . . . . . . . . . . . . . . . . . . . . . . . . . . . . . . . . . . . . . . . . .7 Operating machine . . . . . . . . . . . . . . . . . . . . . . . . . . . . . . . . . . . . . .8 Care of the machine . . . . . . . . . . . . . . . . . . . . . . . . . . . . . . . . . . . .9 Maintenance . . . . . . . . . . . . . . . . . . . . . . . . . . . . . . . . . . . . . . . . . . . . .9 Accessories . . . . . . . . . . . . . . . . . . . . . . . . . . . . . . . . . . . . . . . . . . . . .10 After sales service . . . . . . . . . . . . . . . . . . . . . . . . . . . . . . . . . . . . .10 Technical specifications . . . . . . . . . . . . . . . . . . . . . . . . . . . . . . .11This symbol is used in this manual to identify particularareas that are essential for your safety . Please pass all safety instructions on to other persons operating this machine . Powr-Flite floor cleaning machines are designed for useon smooth, even floors in indoor areas . They can be used on most floor surfaces including short pile carpet, wood, rubber and stone . They should not be used on rough uneven surfaces . We are confident the machines will give years of trouble free service, coupled with ease of use and minimum maintenance . Equipment must be operated, serviced and maintained in accordance with the manufacturer’s instructions . If in doubt, contact the supplier of your machine .The following instructions contain important information about the machine and safety advice for the operator .• The machine must be unpacked and assembled in accordance with these instructions before connecting to the electrical supply .• This machine should always be connected to a fully grounded power supply of the right voltage and frequency .• Keep the power supply cord away from moving parts . During operation, hazard may occur when running machine over the power cord .• The machine must be disconnected from the power outlet (by pulling the plug out) before changing the brushes, cleaning the machine or performing routine maintenance .• Warning! Only use brushes/accessories as per the instruction manual . Usage of any other brushes/accessories can cause safety problems .• Periodically inspect the cord for possible damage . A damaged cord must be replaced with the proper cord available from the manufacturer or an authorized service agent .• DO NOT leave the machine connected to the power supply when not in use; always remove the plug from the power outlet .• DO NOT use where hazardous dust is present .• DO NOT use machine near flammable liquids .• DO NOT use in an explosive atmosphere .• DO NOT use on a gradient or slopes .GUIDELINES FOR THE OPERATOR •Operators must be fully trained in accordance with theseinstructions, able to perform routine upkeep of the machineand correct selection of brushes .• Operators should be physically capable to maneuver,transport and operate the machine .• DO NOT run the machine dry, as this could damage thefloor surface or the machine itself .• Take adequate care to hold the machine firmly whileinstalling and removing the brushes .• Never use excessive foaming or highly corrosive cleaningsolutions .• While operating on a flooded floor, always ensure that thewater level does not exceed 1/4" or 6 mm .•DO NOT operate this machine on rough uneven surfacese .g . industrial concrete floors .• DO NOT clean the machine using pressure washers orsteam cleaners .• Ensure all parts are fitted properly before operation .ELECTRICAL CONNECTIONSBefore connecting the machine to the power supply, check thatyour supply voltage corresponds with that marked on the ratinglabel on the body of the machine .IMPORTANT!READ THESE INSTRUCTIONS AND RETAIN FOR FUTURE REFERENCE1 . Cleaning liquid, in the solution tank, is applied to the floor byspray jet .2 . The contra rotating brushes scrub the floor and also throw thedirty water on the conveyor drum . The front brush does mostof the scrubbing and drying . The rear brush completes thescrubbing and collects the remaining water off the floor .3 . A blade fitted to the dirty water tank wipes the drum andcollects the dirty water .THE WORKING PRINCIPLE(4)(1)(2)(3)(10)(9)(8)(5)(1) Top handle(2) Solution control handle (3) Solution tank (4) Bottom handle (5) Dirty water tank (6) Inline solution filter(7) Component housing (8) Conveyor drum (9) Brush(10) Handle release p edal(5)(6)(7)PREPARING FOR USE(4)(1)(2)(3)(5)(6)(7)(8)(9)(10)(11)(12)1 . The Powr-Flite Multiwash XL ships with the handle dismantled . To assemble, verify that all of the parts listed are included .2 . Remove the black band, which holds the bottom handle with the machine body, while holding the bottom handle .Warning! Since the bottom handle is spring loaded, care must be taken when removing the hook to avoid sudden springing back, leading to possible injury to personnel .UNPACKASSEMBLY1 . Insert the two tubular handles into the bottom handle and secure them using handle knobs (12) by tightening lightly . Verify that the handles are assembled according to their marked position and the cable holding hooks are pointing towards the rear .2 . Slide the electric cable retainer into the top portion of RH handle .3 . Fit the top handle over the tubular handles and secure them with a washer and screw (2 sets) . Ensure that the label on the top handle is facing the front of the machine . Now firmly tighten both the knobs and screws alternately . Insert the dummy caps provided to cover the screws (2) in the top handle .4 . Pass the free end of the pull cable through the plastic guide in RH Handle . Press and twist clock-wise to firmly secure the cable end to the fitting in the component housing .5 . Fix the solution tank firmly into the bottom handle by holding the top handle .6 . Rotate the knobs to hold the solution tank .7 . The brushes are only loosely packed in the machine for transit . The brush shafts must be fitted before operating the machine . Push the shafts through the brushes from the side of the machine . To remove brushes, push the brush shaft out from the side of the machine and remove the shaft . Normally the standard brush will be supplied with the machine . Brushes should be selected ac-cording to the type of floor surface to be cleaned and the type of dirt to be removed . Please refer Brush Selection Guide . 8 . The machine is now ready for use .RIGHT BOTTOM REAR LEFT BOTTOM REARThis is applicable when the customer has more than one set of brushes of same type . Array Distinct color coding make it easy to separate tools into their correct areas of use .Restroom brushes are kept in the restroom, kitchen brushes are kept in the kitchen -reducing bacteria cross-contamination between high and low-risk areas . RED, BLUE, WHITEand YELLOW brush buttons are packed with the machine . Simply plug the buttons into thehole in the brush as shown .Clear identification, by color coding, helps to prevent cross contamination .(a) Hole provided for plugging button .(b) Brush with button plugged .Release the pedal handle lightly with your foot (1), pull back the handle (2) to start the motor . The brushes and the drum starts rotating . Pulling the handle further without pressing the pedal, lowers the machine and engages the rotating brushes onto the floor . To stop working, take the handle to the vertical position .On/Off ControlInsert the free end of solution cable into the valve body fitted in the solution tank . Press and twist clock-wise to secure the cable end . Similarly, press and twist counter-clockwise to disconnect the cable end .Slide this knob to TOP position (Working Mode) to operate the machine . Slide this knob to BOTTOM position to move the machine and park the machine .Warning! Keeping the knob in the top position (working mode) and moving the machine will damage the brushes .Brush contact with the floor is adjustable in 4 steps, contact is MINIMUM when the knob is fully down and MAXIMUM when it is fully raised . This helps you to compensate for the wear of brushes and also to con-trol the scrubbing effect . If the machine does not move when the handle is lowered, slide the transport/working mode knob up one step .By pulling the solution control handle up, the cleaning solution is dispensed on the floor . The solution stops once the solution control handle is released .In the event of motor getting overloaded due to improper power supply or unexpected obstruction to the brush/drum rotation, the circuit breaker trips and protects the motor from damage . If this happens, identify the cause, correct it and, reset the breaker after minimum of 30 seconds from tripping by pressing the circuit breaker button manually and continue working .(a)(b)(a)(b)(a)(b)(Iv)(a) Recommended pattern for small rooms(b) Recommended pattern for large hallsWarning! Avoid touching the sharp edge of dirty water tank . It may cause injury to hands .1 . Move the Transport / Working mode control knob to BOTTOM (Transport) position (Fig-viii) .2 . Disconnect the power supply by unplugging the electrical plug and wind the cable over cable holders in the handle .3 . Pull out the dirty water tank and wash it completely .4 . To prevent possible clogging of filter, drain cleaning liquid and keep the fresh water tank clean .5 . Remove the brushes by pushing the brush shaft out (Fig-ix) .6 . Wash the brushes either by dipping in a bucket/sink or in running water (Fig-x) .7 . Turn the machine sideways and wipe clean the conveyor and machine body with a dampcloth (Fig-xi) .8 . Re-install the brushes after washing . It is easier to push the brush shaft from the right hand side (identified by the electrical cable) .9 . Store the machine in a dry indoor area only .MAINTENANCE• Power cordRegularly inspect power cord, plug and strain relief for damage or loose connection .• BrushesFor maximum life, wash the brushes regularly . Ensure machine is in Transport mode when not in use . Store additionalbrushes in a vertical position to avoid bending of bristles . Check for permanent bending of bristles in a particular direction . This may occur if the machine is operated for several days without removing the brushes, which is not recommended . If this occurs, reverse the brush so that the bent bristles are automatically straightened .• Wiper BladeAfter years of use the wiper blade may wear . If this occurs the water collection performance will decrease . It should be replaced by an authorized service agent .• Solution tank filterThe filter prevents clogging of the drip holes in the tank . Periodically clean the filter to ensure uniform discharge of liquid . In case of non uniform discharge from the drip holes, back flush the tank in running water . Clean the drip holes using wire or a blunt pin .The transport cart provides for ease of movement when transporting the machine .Transport CartUsing the transport cart1 . With the machine handle in the upright position place the cart centrally alongside the machine .2 . By holding the machine firmly, tilt the handle away from your body . Slide the cart base under the machine and strap it to the machine with the velcro .3 . Ensure that the velcro strap is securely wrapped around the bottom handle .4 . Now the cart is ready to use . The machine can then be maneuvered easily while holding the top handle .Side BrushTo clean up to walls, the side brush may be used . Switch off and unplug the machine before fitting the side brush .Fitting the side brush1 . Remove the front brush and brush shaft .2 . Fix the shield assembly on the side plate .3 . Insert the side brush through the shield and main brush .Using the side brush1 . Tilt the machine at an angle, move forward . This way, the dirty waterthrown by the side brush will be collected by the rear brush .2 . Use side brush only for washing the edges*TheoreticalNote:1 . Noise levels measured at a distance of 3 .28 feet from machine and 5 .25 feet above floor, when washing a hard floor . Measurements recorded using a hand held meter .2 . Handle vibration does not exceed 2 .5 m/s2, when operating on a smooth hard surface .3 . Above dimensions are approx . Since the company’s policy is to continuously improve the product, there could be changes without prior notice .11。
FC300操作说明书

" 快速设置 .................................................................. 36 " 参数列表 .................................................................. 38 " 参数选择 .................................................................. 39
! 安全说明和一般警告 ...................................................... 7
" 处理说明 .................................................................. 7 " 软件版本 .................................................................. 7 " 高压警告 .................................................................. 8 " 安全说明 .................................................................. 8 " 避免意外启动 .............................................................. 9 " FC 302 的安全停止 .......................................................... 9 " IT 主电源 ................................................................. 9
花样机5770-1306HA2使用说明书(中文全)V2.2

Amada EM-K3106 控制面板操作介绍

概况·····················4-3基本操作···················4-3文字、数值的输入··············4-3滚动条···················4-3光标的移动·················4-3基本画面构成··················4-4 菜单选择按钮················4-4加工状态显示区域················4-9 加工状况显示················4-9执行程序名显示··············4-10运行状态显示···············4-10信息按钮·················4-10NC状态显示···············4-10操作面板按钮···············4-11操作面板A················4-12操作面板B················4-16当前值··················4-17画面说明···················4-18准备(后台)画面··············4-18加工状态显示区域·············4-18操作面板按钮···············4-18数据编辑区域···············4-19传送作业按钮···············4-30菜单按钮·················4-31(接下页)任务列表画面·················4-32 加工状态显示区域1············4-33 加工状态显示区域2 ············4-33 操作面板按钮···············4-33 数据编辑区域···············4-33 运行状态切换按钮·············4-33 程序画面···················4-34 加工状态显示区域1············4-35 加工状态显示区域2 ············4-35 操作面板按钮···············4-35 数据编辑区域···············4-35 运行状态切换按钮·············4-35 显示切换按钮···············4-35 结果画面···················4-36 常用指令画面·················4-38 报警发生画面·················4-40 加工条件画面·················4-41 M码编辑画面···············4-41 引导输入画面···············4-43 模具信息画面···············4-43 时间段设定画面··············4-44 维护画面···················4-45 用户设定画面···············4-45 应用(程序)设定画面···········4-51 数据输出入画面··············4-52 冲切数管理画面··············4-54 CNC维护画面··············4-56 邮件通知功能画面·············4-61 检查设定画面···············4-65 备用程序机画面··············4-67 外部输出入设定画面············4-70概况在此对机械接通电源、NC装置起动、原点复归之后,液晶显示屏显示的各个画面进行说明。
裁剪设备的图片及其使用说明
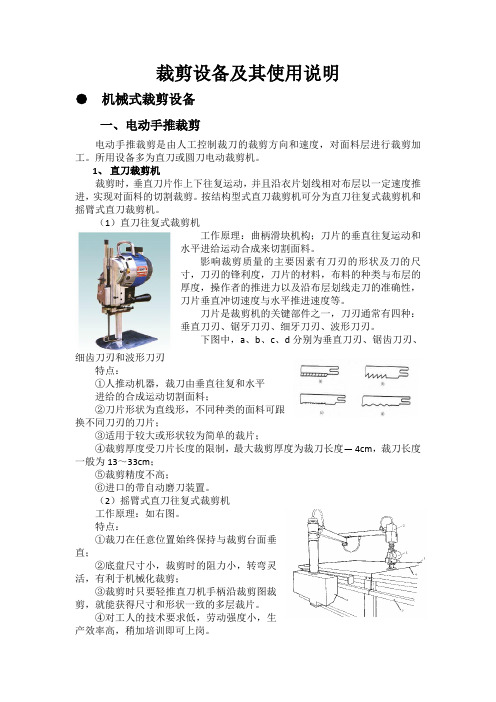
裁剪设备及其使用说明●机械式裁剪设备一、电动手推裁剪电动手推裁剪是由人工控制裁刀的裁剪方向和速度,对面料层进行裁剪加工。
所用设备多为直刀或圆刀电动裁剪机。
1、直刀裁剪机裁剪时,垂直刀片作上下往复运动,并且沿衣片划线相对布层以一定速度推进,实现对面料的切割裁剪。
按结构型式直刀裁剪机可分为直刀往复式裁剪机和摇臂式直刀裁剪机。
(1)直刀往复式裁剪机工作原理:曲柄滑块机构;刀片的垂直往复运动和水平进给运动合成来切割面料。
影响裁剪质量的主要因素有刀刃的形状及刀的尺寸,刀刃的锋利度,刀片的材料,布料的种类与布层的厚度,操作者的推进力以及沿布层划线走刀的准确性,刀片垂直冲切速度与水平推进速度等。
刀片是裁剪机的关键部件之一,刀刃通常有四种:垂直刀刃、锯牙刀刃、细牙刀刃、波形刀刃。
下图中,a、b、c、d分别为垂直刀刃、锯齿刀刃、细齿刀刃和波形刀刃特点:①人推动机器,裁刀由垂直往复和水平进给的合成运动切割面料;②刀片形状为直线形,不同种类的面料可跟换不同刀刃的刀片;③适用于较大或形状较为简单的裁片;④裁剪厚度受刀片长度的限制,最大裁剪厚度为裁刀长度— 4cm,裁刀长度一般为13~33cm;⑤裁剪精度不高;⑥进口的带自动磨刀装置。
(2)摇臂式直刀往复式裁剪机工作原理:如右图。
特点:①裁刀在任意位置始终保持与裁剪台面垂直;②底盘尺寸小,裁剪时的阻力小,转弯灵活,有利于机械化裁剪;③裁剪时只要轻推直刀机手柄沿裁剪图裁剪,就能获得尺寸和形状一致的多层裁片。
④对工人的技术要求低,劳动强度小,生产效率高,稍加培训即可上岗。
小结:直刀裁剪机的使用和选择:①面大而广,服装厂一般都配备②通常有四种:1500r/min、1800r/min、2800r/min、3600r/min③选择带有自动刃磨装置的裁剪机④选用摇臂式自动刃磨直刀式裁剪机时,要注意裁床和裁剪机的配套2、圆刀式裁剪机工作原理:圆刀裁剪机由电机经过一对圆锥齿轮传动使圆刀转动,裁剪时,操作者推电剪在裁剪台上移动切布。
DynaQuip电动旋转机械臂说明书

26AutomationDynaQuip Controls offers two series of electric rotary actuators with output torques from 150 to 31,000 inch pounds. Our DE and MA Series actuators are available in AC and DC voltages and provide some of the most compact, high-output designs available anywhere. DynaQuip electric actuators provide a solid foundation for automating almost any quarter-turn application. Electric actuators are used where plant air andcompressors are not available. They are the actuators of choice in cold temperatures,corrosive environments, and are easilyintegrated into distributed control systems. Automating ball, butterfly, and plug valves are the primary application of most end users. DynaQuip electric actuators can also be used to operate quarter-turn louver anddamper mechanisms.Electric Actuator Options•Auxiliary Limit SwitchesAdditional dry contact limit switches within the control housing to indicate various valve positions remotely, or to stop the valve at intermediate positions, or to control other pieces of equipment, such as pumps.•NEMA 4, 4X, 7, and 9Various NEMA ratings available to meet specific environmental requirements:watertight, corrosion resistant, or explosion proof. Special housings for high-pressure wash down also available.•TimerAdjustable time intervals and length of time open and/or closed.•Modulating ControlsAccepts a 4 - 20 mA , 0 - 5 VDC, or 0-10 VDC control signal to position the valve at various degrees of open/close.•Continuous Position IndicationGives a continuous remote indication of the degrees or percent of opening based on either a resistance output of 0 - 1000 ohms or a current output of 4 - 20 mA. Other options available.•Fail-Safe BackupBattery backup system that allows normal operation of actuator with 120 volt AC but converts battery DC to AC upon incoming AC power failure.•Spring-Return Fail-SafeFail-safe spring backup system within the electric actuator takes over upon loss of AC power.DynaQuip Controls can provide actuators and hardware to automate existing valves of otherbrands and manufacturers. Contact DynaQuip Controls Customer Service, or your local Dynaquip distributor, and allow us to help solve your automation problems.The following options may require a custom quote from Customer Service team.27800-545-3636Electric Actuators•Heavy Duty Heat Treated Pinion Gearing -Lubricated for Life •Manual Override-Local Position Indication•Die Cast Aluminum•Epoxy Polyurethane Paint •Stainless Steel Fasteners•Two (2) 1/2" NPT Conduit Entries•Self-Locking, High-Alloy Steel Gear Train •Lubricated for Life•Plated Steel Output Shaft •30% Duty Rated Long LifePH1 and 12 to 24 VDCSuffix “E” for 24 VDC Suffix “F” for 230 volt, PH3Suffix “G” for 460 volt, PH3。
FC300 操作说明书(MG33A143)
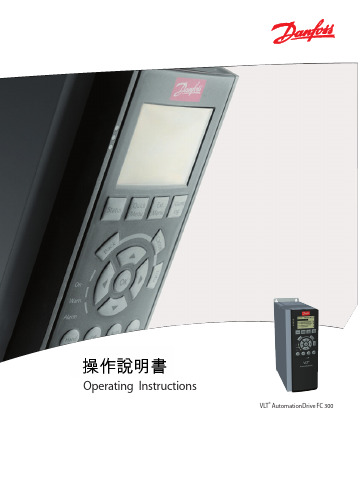
VLT® AutomationDrive FC 300
FC 300 操作說明書
目錄
如何閱讀操作說明 ........................................................ 3
認可 ...................................................................... 4 符號 ...................................................................... 5 縮寫 ...................................................................... 5
供透過 DeviceNet Fieldbus 控制、監控和規劃傳動裝置的必要資訊。 - VLT AutomationDrive FC 300 MCT 10 Operating Instructions (VLT AutomationDrive FC 300 MCT 10 作業說明) 提供在電
腦上安裝和使用軟體的資訊。 Danfoss Drives 技術文獻也可在 /drives 網站上找到。 認可
「疑難排解」的分頁符號。
FC 300 300 Operating Instructions (VLT AutomationDrive FC 300 作業說明) 提供啟動和運轉
傳動裝置的必要資訊。 - VLT AutomationDrive FC 300 Design Guide (VLT AutomationDrive FC 300 設計指南) 詳細說明關於傳動裝置及客戶
乐天壁挂炉说明书

乐天壁挂炉说明书尊敬的用户:感谢您选择乐天壁挂炉。
为了确保您能安全、正确地使用本产品,充分发挥其性能,请您在安装和使用前仔细阅读本说明书,并妥善保存,以备日后查阅。
一、产品概述乐天壁挂炉是一种高效、节能、环保的采暖设备,它采用先进的燃烧技术和智能控制系统,能够为您的家庭提供稳定、舒适的采暖和生活热水。
本壁挂炉具有外观美观、体积小巧、安装方便等优点,适用于各种住宅类型。
二、技术参数1、型号:_____2、额定热输入:_____kW3、额定热输出:_____kW4、采暖温度调节范围:_____℃_____℃5、生活热水温度调节范围:_____℃_____℃6、燃气种类:_____7、电源:_____V/_____Hz8、防护等级:_____三、安装说明1、安装位置选择应选择通风良好、干燥、无易燃、易爆物品的地方。
避免安装在阳光直射、雨淋、潮湿或温度过低的环境中。
安装位置应便于操作和维修,且与燃气管道、电源插座、采暖系统管道和生活热水管道的连接应方便。
2、安装步骤首先,根据安装图纸确定壁挂炉的安装位置,并在墙上打孔,安装固定支架。
将壁挂炉挂在固定支架上,并确保其水平安装。
连接燃气管道,应使用专用的燃气管道和阀门,并确保连接牢固、无泄漏。
连接采暖系统管道,包括进水管道和回水管道,应使用符合标准的管道和连接件,并确保管道无泄漏。
连接生活热水管道,应使用符合标准的管道和连接件,并确保管道无泄漏。
连接电源插座,应使用符合标准的电源插座,并确保电源接地良好。
3、安装注意事项安装应由专业人员进行,严格按照安装说明书和相关标准进行操作。
安装完成后,应进行燃气泄漏检测和系统压力测试,确保系统安全可靠。
在安装过程中,应注意保护壁挂炉的外观和内部部件,避免碰撞和损坏。
四、使用说明1、开机前准备检查燃气阀门是否打开,燃气压力是否正常。
检查采暖系统和生活热水系统的阀门是否打开,系统是否充满水。
检查电源插座是否连接正常,电源是否接通。
三乐天旋切机调板技术表
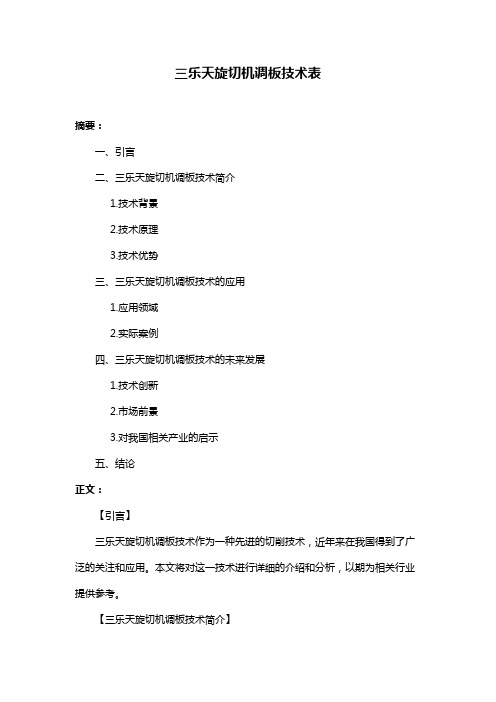
三乐天旋切机调板技术表摘要:一、引言二、三乐天旋切机调板技术简介1.技术背景2.技术原理3.技术优势三、三乐天旋切机调板技术的应用1.应用领域2.实际案例四、三乐天旋切机调板技术的未来发展1.技术创新2.市场前景3.对我国相关产业的启示五、结论正文:【引言】三乐天旋切机调板技术作为一种先进的切削技术,近年来在我国得到了广泛的关注和应用。
本文将对这一技术进行详细的介绍和分析,以期为相关行业提供参考。
【三乐天旋切机调板技术简介】三乐天旋切机调板技术,是指利用三乐天旋切机对板材进行高速、高精度的切削。
该技术具有以下特点:1.技术背景:随着我国制造业的不断发展,对于板材加工精度和效率的要求越来越高,三乐天旋切机调板技术应运而生。
2.技术原理:通过高速旋转的刀具对板材进行切削,同时通过计算机控制系统实现刀具的精准定位和控制。
3.技术优势:相比传统切削技术,三乐天旋切机调板技术具有切削速度快、精度高、材料损耗小等优点。
【三乐天旋切机调板技术的应用】1.应用领域:三乐天旋切机调板技术广泛应用于家具制造、建筑装饰、汽车制造等行业。
2.实际案例:在家具制造行业,三乐天旋切机调板技术可以实现家具板材的快速、精准切割,提高生产效率和产品质量;在建筑装饰行业,该技术可以用于石材、木材等材料的加工,满足建筑装饰的高精度需求。
【三乐天旋切机调板技术的未来发展】1.技术创新:随着科技的不断发展,三乐天旋切机调板技术仍有很大的创新空间,如提高切削速度、降低生产成本等。
2.市场前景:在当前制造业转型升级的大背景下,三乐天旋切机调板技术有着广阔的市场前景。
3.对我国相关产业的启示:我国相关产业应加大对先进切削技术的研发和应用力度,提高产品质量和市场竞争力。
【结论】总之,三乐天旋切机调板技术作为一种先进的切削技术,具有广泛的应用前景和重要的现实意义。
多功能裁缝机说明书

EPA and California ARB Emissions Certified for All 50 StatesExclusiveTwin Blades ConfigurationAnd CapabilityBlade Safety Flywheel Flywheel Flywheel Flywheel Flywheel Roto-Stop® Flywheel Flywheel Roto-Stop® Roto-Stop® Roto-Stop® Systembrake brake brake brake brake BSS brake brake BSS BSS BSSTransmission Push Push Hydrostatic Hydrostatic Control Cruise Control Cruise Control Starter Recoil Recoil Recoil Recoil Electric/Recoil Recoil Recoil Electric/Recoil Recoil Recoil Electric/Recoil Wheels8" Poly8" Poly8" Poly8" Poly8" Poly8" Poly9" Poly9" Poly9" Poly9" Poly9” Poly# of Wheel Positions 6 6 7 7 7 7 7 7 7 7 7 Cutting Height 11⁄8"- 4"11⁄8"- 4"1"- 4"1"- 4"1"- 4"1"- 4"3⁄4"- 4"3⁄4"- 4"3⁄4"- 4"3⁄4"- 4"3⁄4”- 4”Handle HeightQuick Release Quick Release Quick Release Quick Release Quick Release Quick Release Quick Release Quick Release Quick Release Quick Release Quick ReleasePositions 2-Position 2-Position 2-Position 2-Position 2-Position 2-Position 3-Position 3-Position 3-Position 3-Position 3-Position Honda Honda Honda Honda Honda Honda Honda Honda Honda Honda Honda GCV200GCV160 GCV160 GCV170 GCV170 GCV170 GCV170 GCV200 GCV200 GCV200 GCV200 Self Charging Engine w/Auto Choke w/Auto Choke w/Auto Choke w/Auto Choke Self Charging w/ACS and w/Auto Choke Self Charging w/ACS and w/ACS and Electric w/ACSSystem (ACS) System (ACS) System (ACS) System (ACS) Electric adj. throttle System (ACS) Electric adj. throttle adj. throttle and adj.w/ACS control w/ACS control control throttle control Deck Material Steel 16 ga Steel 16 ga Steel 16 ga Steel 16 ga Steel 16 ga Steel 16 ga Ground SpeedN/A0 to 4 mphN/A0 to 4 mph0 to 4 mph0 to 4 mph0 to 4 mph0 to 4 mph0 to 4 mph0 to 4 mph0 to 4 mphBag Capacity (bu.) N/A N/A 1.9 1.9 1.9 1.9 2.5 2.5 2.5 2.5 2.5 Emissions Warranty* 36 mo. 36 mo. 36 mo. 36 mo. 36 mo. 36 mo. 60 mo. 60 mo. 60 mo. 60 mo. 60 mo. Deck Warranty* 36 mo. 36 mo. 36 mo. 36 mo. 36 mo. 36 mo. Lifetime** Lifetime** Lifetime** Lifetime** Lifetime** Engine Warranty* 36 mo. 36 mo. 36 mo. 36 mo. 36 mo. 36 mo. 60 mo. 60 mo. 60 mo. 60 mo. 60 mo. WarrantyCommercial/RentalOptionalMicroCut® Twin Blade System3-in-1 System with Clip Director® — No tools or attachments. Mulch/Bag/Discharge 2-in-1 Mulch/Discharge 4-in-1 Versamow System with Clip Director® —No tools or attachments. Mulch/Bag/Leaf Shred/DischargeInfinitely Variable Speed Select Drive ™Adjustable,Variable Speed Smart Drive Adjustable,Variable Speed Smart Drive Adjustable,Variable Speed Smart Drive 3 mo.3 mo.3 mo.3 mo.3 mo.3 mo.3 mo.3 mo.3 mo.3 mo.3 mo.Adjustable,Variable SpeedSmart Drive InfinitelyVariable Speed Select Drive ™ NeXite® with Lifetime Warranty**Infinitely Variable Speed Select Drive ™Move Up with HondaChoose the model features you need to simplify your lawn mowing and Move Up to the Honda lawn mower with the best combination of innovative features to meet your needs.* Warranty, Deck Warranty and Engine Warranty apply to non-commercial use only. Visit for details. ** L ifetime Deck Warranty applies to any new HRX Series mower. Deck warranty is valid for the original purchaserand non-commercial use only.For additional warranty details, see your local Honda Power Equipment Dealer or visit our website at .。
SCHUNK RM 50-310旋转模块集装箱操作手册说明书
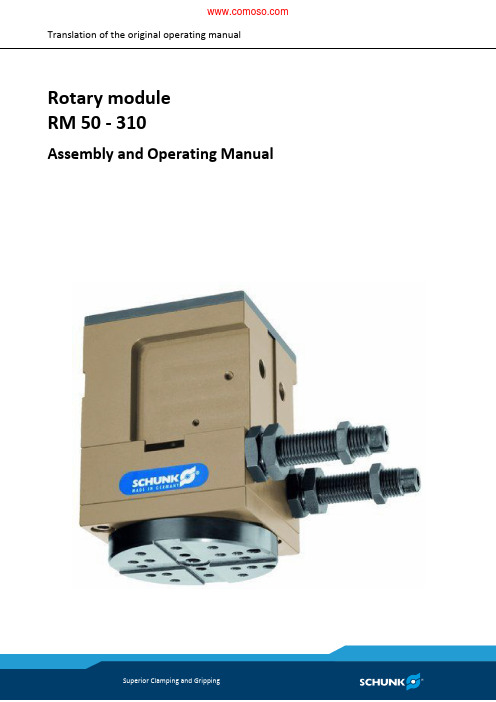
Translation of the original operating manualRotary moduleRM 50 - 310Assembly and Operating ManualSuperior Clamping and GrippingImprint2ImprintCopyright:This manual remains the copyrighted property of SCHUNK GmbH & Co. KG. It is solely supplied to our customers and operators of our products and forms part of the product. This documentation may not be duplicated or made accessible to third parties, in particu-lar competitive companies,without our prior permission.Technical changes:We reserve the right to make alterations for the purpose of technical improvement. Document number: 0389388Edition: 05.00 |25/07/2013|en© SCHUNK GmbH & Co. KGAll rights reserved.Dear customer,congratulations on choosing a SCHUNK product. By choosing SCHUNK, you have opted for the highest precision, top quality and best service.You are going to increase the process reliability of your production and achieve best machining results – to the customer's complete satisfaction.SCHUNK products are inspiring.Our detailed assembly and operation manual will support you.Do you have further questions? You may contact us at any time – even after purchase.Kindest Regards Yours SCHUNK GmbH & Co. KGSpann- und GreiftechnikBahnhofstr. 106 – 134D-74348 Lauffen/NeckarTel. +49-7133-103-0Fax +49-7133-103-2399**************.comTable of contents05.00|RM 50 - 310 |en 3Table of contents1 About this manual (5)1.1 Warnings (5)1.1.1 Key words (5)1.1.2 Symbols (5)1.2 Applicable documents (5)2 Basic safety notes (6)2.1 Intended use (6)2.2 Not intended use (6)2.3 Environmental and operating conditions (6)2.4 Product safety (7)2.4.1 Protective equipment (7)2.4.2 Constructional changes, attachments, or modifications (7)2.5 Personnel qualification (7)2.6 Using personal protective equipment (7)2.7 Notes on particular risks (8)3 Warranty (9)4 Scope of delivery (9)5 Accessories (10)5.1 Sensors (10)6 Technical data (11)7 Assembly and settings (12)7.1 Mechanical connection (12)7.2 Air connections (13)7.3 Adjusting the end positions (14)7.3.1 Angle of rotation fine adjustment (15)7.3.2 Dampening adjustment (15)7.4 End position monitoring (16)8 Start-up (17)9 Troubleshooting (18)9.1 Modul does not move? (18)9.2 Does the module not travel through the rotating angle? (18)9.3 End position signal not present? (18)9.4 Is torque dropping? (19)9.5 Does the module rotate abruptly? (19)9.6 Does the module move hard against the end positions? (19)Table of contents410 Maintenance and care (20)10.1 Shock absorber (20)10.2 Maintenance and lubrication intervals (20)10.3 Lubricants/Lubrication points (basic lubrication) (21)10.4 Dismantling the module (21)10.5 Assembling the module (22)11 Spare parts (22)11.1 Sealing kit (22)12 Assembly drawing (23)13 Translation of original declaration of incorporation (24)About this manual05.00|RM 50 - 310 |en 5About this manualThis instruction is an integral part of the product and contains impor-tant information for a safe and proper assembly, commissioning, op-eration, maintenance and help for easier trouble shooting.Before using the product, read and note the instructions, especial-ly the chapter "Basic safety notes".WarningsThe following key words and symbols are used to highlight dangers.Key wordsSymbolsApplicable documents• General terms of business• SCHUNK catalog Modular Assembly Automation• Assembly and Operating Manuals of the accessories • "Gemotec Toolbox Rotation" programThe documents listed up here, can be download on our homepage 1 1.1 1.1.1 1.1.2 1.2 Basic safety notes6Basic safety notesIntended useThe module was designed to swivel permissible attachments or workpieces.The module is intended for installation in a machine/system. The requirements of the applicable guidelines must be observed and complied with.The module may be used only in the context of its defined applica-tion parameters (☞ 6, Page 11).To use this unit as intended, it is also essential to observe the technical data and installation and operation notes in this manual and to comply with the maintenance intervals.Not intended useIt is not an intended use if the module is used, for example, as a pressing tool, stamping tool, lifting gear, guide for tools, cutting tool, clamping device or a drilling tool.Environmental and operating conditions• The module may be used only within its defined application pa-rameters.• Ensure that the environment is clean. Observe the lubrication intervals (☞ 10.2, Page 20).• Ensure that the environment is free of splashing water and va-pors, and also of abrasive dust and process dust. This does not apply to modules designed especially for unclean environ-ments.• Do not subject the module to excessive vibrations and/or me-chanical shocks.• Strong magnetic fields can impair the function of the module. If the product is to be used in strong magnetic fields, contact your SCHUNK partner.2 2.1 2.2 2.3 Basic safety notes05.00|RM 50 - 310 |en 7Product safetyDangers arise from the module, if:• the module is not used in accordance with its intended purpose. • the module is not installed or maintained properly.• the safety and installation notes are not observed.Avoid any manner of working that may interfere with the function and operational safety of the module.Wear protective equipment. NOTEMore information are contained in the relevant chapters.Protective equipmentProvide protective equipment per EC Machinery Directive.Constructional changes, attachments, or modificationsAdditional drill holes, threads, or attachments that are not offered as accessories by SCHUNK may be attached only with permission of SCHUNK.Personnel qualificationThe assembly, initial commissioning, maintenance, and repair of the module may be performed only by trained specialist person-nel. Every person called upon by the operator to work on the module must have read and understood the complete assembly and operating manual, especially the chapter "Basic safety notes" ( 2, Page 6). This applies particularly to personnel only used oc-casionally, such as maintenance personnel.Using personal protective equipmentWhen using this product, observe the relevant industrial safety regulations and use the personal protective equipment (PPE) re-quired!• Use protective gloves, safety shoes and safety goggles. • Observe safe distances.• Minimal safety requirements for the use of equipment. 2.4 2.4.1 2.4.2 2.5 2.6 Basic safety notes8 05.00|RM 50 - 310 |enNotes on particular risksGenerally valid:• Remove the energy supplies before installation, modification, maintenance, or adjustment work.• Make sure, that no residual energy remains in the system. • Do not move parts by hand when the energy supply is con-nected.• Do not reach into the open mechanism or the movement area of the module.• Perform maintenance, modifications, and additions outside the danger zone.• For all work, secure the unit against accidental operation. • Take a precautionary approach by maintenance and disassem-bly.• Only specially trained staff should disassemble the module.2.7 Scope of delivery05.00|RM 50 - 310 |en 9WarrantyThe warranty is valid for 24 months from the delivery date to the production facility under the following conditions:• Intended use in 1-shift operation• Observe the mandatory maintenance and lubrication intervals • Observe the environmental and operating conditionsParts touching the work piece and wear parts are not part of the warranty.Scope of deliveryThe scope of delivery includes:• Rotary Actuator RM in the ordered model.• Exhaust air throttles• Accessory pack3 4 Accessories10AccessoriesThe following accessories that are required for the module must be ordered seperately:• End-position monitoring• SensorsFor information about which accessories can be used with the ap-propriate product version ☞ catalog.SensorsOverview of the compatible sensors• Exact type designation of the compatible sensors see ☞ catalog • If you require further information on sensor operation, contact your SCHUNK contact person or download information from our homepage.5 5.1 Technical data Technical data6Further technical data can be found in the catalog data sheet.The most recent version applies.Assembly and settings12Assembly and settingsAssembly measures•When mounting loads, do not allow impermissible forces andmoments to be exerted (see catalog data).•Select the suitable screw tightening torque when assemblingthe module or loads at the module in accordance with thegenerally accepted guidelines for screw connections.•Secure all screws using a suitable chemical screw lock.Mechanical connectionThe values relate to the entire bolting surface.Requirements for levelness of the bolting surface (Dimensions in mm)The connection geometries are above, below and at the side of therotary module.Dimensions for the position and size of the connection geometries,☞ Catalog data sheet.NOTE•When mounting the module from the rear or on the side,mount the module using the fixing bores provided.•Mount the modules using the fixing bores provided.77.1Check the evennessof the bolting surfaceMountingAssembly and settings 7.2Air connectionsPressure medium:The unit must not under any circumstances be operated withoiled air before operation with unoiled air (washing out of factory lubrication).Observe the requirements for the air supply.( 6, Page 11) "Technical Data"Use connecting wires with the same or a larger cross-section asthe connection thread.See the catalog for precise information about the position and size of the connection geometries.Assembly and settings14Adjusting the end positionsThe parts listed below are included within the scope of delivery of every rotary module for angle of rotation fine adjustment and ad-justment of the end position dampening to the mass moment of inertia occurring in operation.•Counter nut (10)•Stop coupling (13)•Rod (14)•Shock absorber (22)•Counter nut (23)Fig. 1 Adjusting the end positions7.3Assembly and settingsAngle of rotation fine adjustment1 Release counter nut (10).2 By twisting the stop coupling (13) with the rod (14) and shock absorber (22) that are integrated in it, the angle of rotation in both end positions can be set by ±5° from the nominal angle of rotation. The nominal rotation angle has to be specified for the order and can be selected without steps between 5° and 180°. Standard angles are 90° and 180°.3 Tighten the stop coupling again with the counter nut.Dampening adjustmentUse the shock absorber!Operation without the shock absorber included within the scope of delivery is not permitted.• Observe the maximum mass moment of inertia (☞ catalog da-ta).• Adjust the dampening at the mass moment of inertia.✓ The desired angle of rotation has been set (☞ 7.3.1, Page 15). 1 Release counter nut (23).2 By turning the shock absorber (22) in and out, the stroke of the shock absorber (and therefore the shock absorber charac-teristic curve) can be adjusted to the mass moment of inertia occurring in operation. The previously adjusted angle of rota-tion is not influenced by this.3 Tighten the absorber again with the counter nut.7.3.1 7.3.2Assembly and settings16End position monitoringTo monitor the end positions, standardized monitoring sets for di-rect installation are available.The stop level that is integrated in the rotary module is directlymonitored.Proximity switch monitoring: GMNS-...Scope of delivery of the monitoring set:•1 x retaining plate•1 x Proximity switch•1 x connection cableFig. 2Position of the proximity switches1 Undo the attachment screw.2 Set the sensor via the retainer plate.3 Fix the sensor via the attachment screw.7.4Setting themonitoringStart-up Start-up8•Check the technical specifications (☞ 6, Page 11).•Check the permissible loading specifications (see catalog).•Do not use the module until trouble-free operation has beenchecked taking all permissible operating parameters into ac-count.•Set the speed of the movement in such a way that the permit-ted swiveling time is not exceeded. Use the "Gemotec Toolbox"program for calculation ().•The movement speed is ideally regulated via throttle checkvalves (☞ 7.2, Page 13). The speed is always set so that it starts at a low speed and increases to a higher speed until the desired operating speed has been reached.•Operate the device in such a way that the permissible cyclenumber per minute is not exceeded. Use the "Gemotec Tool-box" program for calculation ().Troubleshooting1805.00|RM 50 - 310 |enTroubleshootingModul does not move?Does the module not travel through the rotating angle?End position signal not present?9 9.1 9.2 9.3TroubleshootingIs torque dropping?Does the module rotate abruptly?Does the module move hard against the end positions?9.4 9.5 9.6Maintenance and care20Maintenance and careShock absorberSerious mechanical damage due to failure of the shock absor-bers.The shock absorbers have a limited service life span. A shock ab-sorber failure can lead to serious mechanical damage; for thisreason, they must be checked regularly for proper function. Theshock absorber is working correctly if the device reaches its endposition swiftly without any mechanical impact.Overloading of the unit or exceeding the permitted swivel speed can lead to drastic reduction of the service life.•Determine the swiveling times and the permitted stroke fre-quency with "Gemotec Toolbox".•Regularly check the shock absorber.•Observe the recommended maintenance intervals.Maintenance and lubrication intervalsAt ambient tempertature above 60°C the lubricanscure out faster•Interval decrease accordingly.1010.110.2Maintenance and careLubricants/Lubrication points (basic lubrication)• All module bearings are life-time lubricated and do not need to be re-lubricated. • When disassembling the module for repairs, all bearings have to be cleaned and re-lubricated.We recommend the lubricants listed.During maintenance, treat all greased areas with lubricant. Thinly apply lubricant with a lint-free cloth.Greasing areas, grease* Only after disassembling the module for repairsDismantling the moduleNOTICEA high degree of expertise is required for the disassembly and assembly of the module, (☞ 2.5, Page 7).The repair or elimination of defects by the customer on the mod-ule results in the termination of the warranty and liability for all resulting warranty and subsequent damage.• It is recommended to have SCHUNK repair damaged and de-fective modules.• Disassemble the module as shown in the "Assembly drawings", (☞ 12, Page 23). • Only disassemble the rotation module for repair purposes.10.3 10.4Maintenance and care22Assembling the module•Clean all parts thoroughly and check for damage and wear.•Treat all grease areas with lubricant.( 10.3, Page 21)•Oil or grease bare outside steel parts.Assembly takes place in the opposite order to disassembly. Ob-serve the following:•Unless otherwise specified, secure all screws and nuts with Loc-tite no. 243 and tighten with the appropriate tightening torque.Select suitable tightening torques for screws when assemblingthe module in accordance with generally accepted guidelinesfor screw connections.Spare partsSealing kitID.-No. of the seal kit10.5MaintenanceAssembly1111.1Assembly drawingAssembly drawing12The following figure is an example image.It serves for illustration and assignment of the spare parts.Variations are possible depending on size and variant.Fig. 3 Assembly of RM 06Translation of original declaration of incorporation2405.00|RM 50 - 310 |enTranslation of original declaration of incorporationmeets the applicable basic requirements of the Machinery Directive (2006/42/EC). The incomplete machine may not be put into operation until conformity of the machine into which the incomplete machine is to be installed with the provisions of the MachineryDirective (2006/42/EC) is confirmed.The manufacturer agrees to forward on demand the special technical documents for the incomplete machine to state offices.The special technical documents according to Annex VII, Part B, belonging to the incom-plete machine have been created.Person responsible for documentation: Mr. Robert Leuthner, Address: see address of the manufacturerRalf Winkler;Business Unit ManagerR & D Mechanical Gripping Systems13。
VIPROS-2510C-(操作手册)

伺服系统保护: 如果探测到伺服系统出现不正常的情况,比如伺服马达过载,机床将停机。
脱膜失败探测: 如果脱膜失败或者脱膜延时,机床停机。
夹钳/压料缸保护: 如果夹钳进入危险区(妨碍冲切的区域),机床将停机。如果在板材再定位时,夹钳-压料 缸出现碰撞危险,机床也将停机。夹钳打开时,机床停机。
Ⅶ-2 Ⅶ-4 Ⅶ-4 Ⅶ-5 Ⅶ-5 Ⅶ-8 Ⅶ-10 Ⅶ-12 Ⅶ-14 Ⅶ-15 Ⅶ-16 Ⅶ-18
模具
转塔盘的排放 34工位的转塔 模具类型
A工位(1/2 " ) B工位(1 1/4 " ) C工位(2 " ) D工位(3 1/2 " ) 拆装上下模具 转塔内圈A工位 转塔外圈A、B、C、D工位 自动分度模具 转塔工位及模具的键与键槽 模具的键与键槽 转塔工位的键与键槽 上下模具的维护 拆装上模(A、B工位) 拆装上模冲头(C、D工位) 研磨上下模 调整上下模高度 润滑 检查上下模 检查板材 上下模的间隙 冲压能力 最小孔的直径
数控转塔冲床
VIPROS-2510C
操作手册
AMADA
前言 仔细阅读本操作说明书,可以对机床的安装、 操作、维护等方面有系统的认识。安装本操作说明书 所述正确的操作机床,可以避免人员的伤害和机床的 损害。不要凭想像操作机床。把本操作说明书放在附 近,当你出现不能确认的操作步骤时请参阅它。
目录
安全规则&安全功能
C)不要在操作机床期间,穿宽松的衣服、领带或者围巾。如果他们中任意部分被 机床刮住,将会给操作者带来巨大伤害。
D)遵守下述冲切规章。如果你不确定将要冲切的板材能否冲切,请咨询AMADA 工程师。
不要冲切超过机床压力允许范围的板材。
YARDMAX YG1650 21英寸三合一电动裁缸推车裁草机说明书
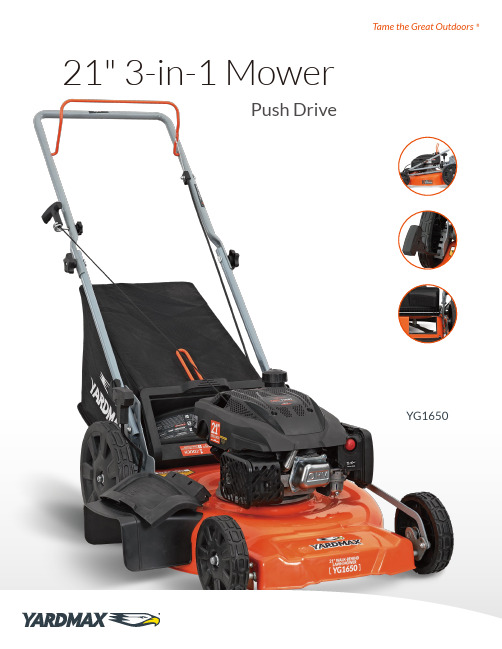
Tame the Great Outdoors®21" 3-in-1 MowerPush DriveYG1650*Specs are preliminary and subject to changeMake that a three-peat.The YARDMAX 21” 3-in-1 push mower is perfect for the homeowner that wants a mower with all the features and is easy to use, but doesn’t mind pushing. The 170cc OHV Yardmax engine delivers maximum performance in this class of mower.FEATURES & BENEFITSSingle-lever deck adjustment for quickly setting your mow heightSeven cutting heights from 1.25” to 3.75”Double-ball-bearing wheels for easy, smooth mowing with less pushing effortMAXFlow™ Deck Technology – volute spiral deck design for better airfow and mulching Heavy-duty, 16-guage stamped steel deck Durable, one-piece seamless steel deck reduces vibration21" cutting blade lets you cut a wide area of lawn with each pass Large rear bag capacity Folds for space-saving storageChoose side discharge, mulching, or rear bagging 7" front & 11" rear wheels for stability and control Adjustable, durable 3-position handle height••••••••••••consistently get the job done right, at the right price.YARDMAX outdoor power equipment delivers the perfect combination of practicality and performance, offering durable and affordable product lines engineered to Tame the Great Outdoors ®844-YARDMAX (847-327-0566)|****************|/mowers。
Sakura Finetek Accu-Cut SRM 300 LT 手动旋转微摘机说明书
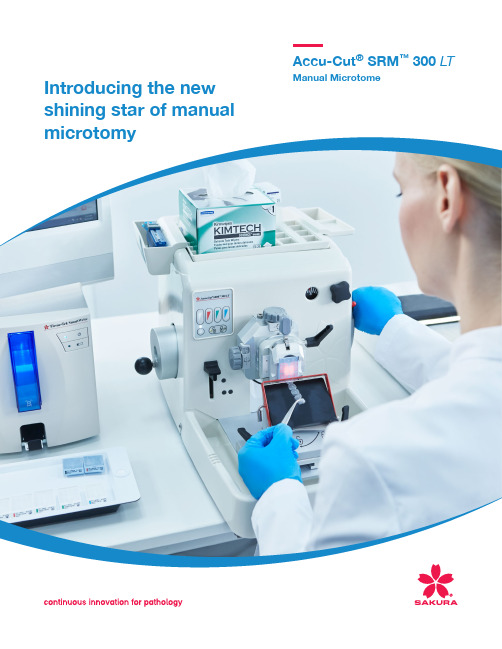
Introducing the new shining star of manual microtomy Accu-Cut® SRM™ 300 LT Manual Microtome23The Accu-Cut ® SRM ™ 300 LT is the first and only manual rotary microtome with a patented LED backlit chuck to illuminate paraffin embedded tissue samples making themmuch easier to see and safer to section.Two models are available, with and without specimen retraction.The course hand wheel is user-selectable for either clockwise or counter clockwise rotation.The Accu-Cut SRM 300 LT comes with a space saving Tool Organizer that fits on top of the microtome to store tools anddry slides before staining.Sakura Finetek microtomes combined with the Accu-Edge ®microtome blades provide a full range of cutting edge solutions for daily microtomy.Manual microtomy is nowsophisticatedAccu-Cut ® SRM ™ 300 LTAccu-Cut SRM 300 LT – shining a new light on manual microtomyLED backlit chuck for improved visualization of the specimen in the blockThe Accu-Cut SRM 300 LT is the first and only manual microtome with a LED backlit chuck that increases the contrast between specimens and paraffin without warming the block. Users can now be confident in seeing exactly where the tissue is located to prevent cutting through a small biopsy or previously sectioned block.• 4 user selectable LED color options: white, red, green and blue• Independent adjustable intensity for each color• Ability to create any color by mixing the color intensities to contrast the specimen against cassette and paraffin• Electronic LED backlight can be turned on and off Built-in safety features to protect users from microtomy injuriesThe Accu-Cut SRM 300 LT includes many exclusive features that reduce the risk of accidental injuries associated with blade exposure.• The first and only brake lock indicator provides users with peace-of-mind by displaying that the chuck is locked and will not move while the user interacts with the microtome • The universal blade holder can be moved laterally on its base to allow full utilization of the blade edge without having to change the clamping pressure on the blade or touch it until it is completely used• The red blade guard can be set in the UP position to protect the user from accidental exposure to the blade edge while sectioning• The exclusive sliding dispense and Pilot Pin features of the Low Profile Accu-Edge blade cartridges enable the user to safely insert a blade into the blade holder without touching itPrecision orientation for precise block alignment The Accu-Cut SRM 300 LT features a 3D Precision Chuck for accurate alignment of the block face to the blade, which is crucial for recuts.• Quick and precise fine angle adjustments on all 3 axes (XYZ)• Chuck retains its position when locked or unlocked• Dial indicators display the angle position of the chuck (± 8°)• Quickly and accurately return to a zero position• Universal cassette clamp accommodates most common cassettesErgonomic design for comfortable sectioningThe compact and ergonomic design of the Accu-Cut SRM 300 LT helps to minimize cumulative stress on the user and increases both efficiency and productivity.• A smooth-running, conveniently positioned hand wheel reduces fatigue• An optional ergonomic oblong handle is available for even more comfortable sectioning• The course hand wheel is optimally sized and positioned for comfortable trimming in either clockwise or counter clockwise rotation, switchable by the user• The trimming lever can be engaged to advance the chuck 10 or 40 microns to reduce the number of hand wheel rotations for quick trimming• Immediate response to hand wheel movements require less user effort to move the chuck Spacious, easy to clean waste tray• The Accu-Cut SRM 300 LT features a large andcomfortably shaped waste tray for efficient removal ofparaffin waste.• The waste tray easily snaps in and out for quick removaland cleaning• Two integrated forceps cleaners are available on the rightand left sides of the tray• The waste tray has an exclusive built-in slot and wastebag attachment system for convenient waste collectionand disposal• Disposable plastic waste bags help to keep themicrotome area cleanConvenient accessoriesThe Accu-Cut SRM 300 LT is the first and only microtomewith a space-saving Tool Organizer giving back preciousbench space. The Tool Organizer sits on top of themicrotome and holds Kimwipes®, blade cartridges, brushes,forceps, teasing needles, pencils and has 40 slots to air-dryslides, all in one central location.Accu-Cut® SRM™ 300 LT54SpecificationsProduct names Accu-Cut® SRM™ 300 LT Manual Microtome, RetractingAccu-Cut® SRM™ 300 LT Manual Microtome, Non-RetractingProduct codes13001300NApplication Sectioning of paraffin-embedded specimens for routine and research histopathologyDimensions16.4 (W) x 20.7 (D) x 11.8 (H) inches41.6 (W) x 52.5 (D) x 30 (H) cmWeight156.5 lbs (71.0 kg)Section thickness 1 to 40 microns total1 to 10 microns: in 1 micron increments 10 to 20 microns: in2 micron increments 20 to 40 microns: in 5 micron incrementsTrimming thickness lever10 or 40 micronsRetraction distance No retraction or 20 microns (factory set) Vertical stroke60 mmHorizontal stroke25.4 mmCoarse feed advance User switchable: clockwise or counter clockwiseSpecimen orientation using the 3D Precision Chuck ±8° (XYZ axes)Dial indicators show the exact angle of the chuckLED backlit chuck 4 color electronic LED backlight (white, red, green and blue) with user-adjustableintensity for each color, on-off optionRated voltage and currentfor LED light90-264 VAC, 50/60 Hz, 0.3ABlade angle0 to 10°Blade holder base:North/south (vertical direction) East/west (horizontal direction)25 mm 60 mmUser interface display Key pad to control the electronic LED backlightBrake light indicatorCertifications UL61010-1:2012 Ed. 3, UL61010-2-101:2015 Ed. 2, CSA C22.2 61010-1:2012 Ed. 3, CSA C22.2 61010-2-101:2015 Ed. 2, IEC61010-1:2012 Ed. 3, IEC61010-2-101:2015 Ed. 2, IEC 61326-1, IEC61326-2-6Regulatory status IVD, FDA Class I Product code Product name and quantity1302Accu-Cut® SRM™ Universal Cassette Clamp with LED backlight;1 unit1303Accu-Cut® SRM™ Tool Organizer; 1 unit1304Accu-Cut® SRM™ Waste Tray; 1 unit1305Accu-Cut® SRM™ Maintenance Kit; 1 unit4650Tissue-Tek® Cold Plate; 25 x 10 x 3 cm; 24/case4658Waste Collection Bags; 250/case4685Accu-Edge® High-Profile Disposable Blades; 500/case4689Accu-Edge® Low-Profile Disposable Blades; 500/case4980Tissue-Tek® Feather® A35 Durable Low-Profile Blades; 500/case6216Tissue-Tek® Cryo3® Flex Ergonomic Handle, Oblong; 1 unit7089Tissue-Tek® Feather® Low-Profile Blades; 500/case Accessories and consumablesFeather is a registered trademark of Feather Safety Razor Co. and is used with permissionKimwipes is a registered trademark of Kimberly-Clark Corp.Accu-Cut® SRM™ 300 LT76Please visit our website Sakura Finetek USA, Inc., 1750 West 214th Street Torrance, CA 90501 U.S.A.0008195-01 R e v .AKnown for best-in-class automation and reliability Sakura Finetekremains a privately-held company in business for over 160 years. Sakura Finetek has achieved its success and solidified its reputation by providing timely, ingenious solutions to the real challenges laboratories face on a day-to-day basis.Our rich history has given us athorough understanding of technology, quality, reliability, value for money and our customers’ requirements. We use this knowledge to passionately develop products that anticipate developments in both technology and market needs.Sakura Finetek USA, Inc. (SFA) isbased in Torrance, California. Functions covered at this facility include sales and marketing, service and technical support, R&D, and manufacturing.SFA is an ISO 13485 certifiedmanufacturer and supplier. As one of the two global manufacturing and R&D sites, SFA develops instruments and reagents into system solutions and secures our innovation with a steady stream of patents.In addition to supporting the U.S. marketplace, SFA is also responsible for Canada, Mexico, Central and SouthAmerica and serves these markets with a network of local distributors.With the worldwide headquarters in Japan and regional offices in Japan, The Netherlands and the U.S.A., the global strategy of worldwide representation has been fulfilled to guarantee our customers the best service and support.Our organization is developing, professionalizing and growingcontinuously, and thus maintaining its position as a trustworthy and valuable partner in histopathology.A long tradition of excellence。
- 1、下载文档前请自行甄别文档内容的完整性,平台不提供额外的编辑、内容补充、找答案等附加服务。
- 2、"仅部分预览"的文档,不可在线预览部分如存在完整性等问题,可反馈申请退款(可完整预览的文档不适用该条件!)。
- 3、如文档侵犯您的权益,请联系客服反馈,我们会尽快为您处理(人工客服工作时间:9:00-18:30)。
SLXC系列变频数控无卡旋切裁板一体机使用说明书【触摸屏用】出厂编号:河北大华宇机械制造有限公司目录一、机床的主要用途----------------------------------------------------------3二、机床的外观图-------------------------------------------------------------3三、机床的规格和技术参数------------------------------------------------4四、机床的构成及主要部件概述------------------------------------------4五、电气系统-------------------------------------------------------------------41、电气原理图--------------------------------------------------------52、电器元件明细表--------------------------------------------------63、常见电器故障---------------------------------------------------74 数控系统操作指南----------------------------------------------8六、机床搬运、安装及调试----------------------------------------------19七、常用调整-----------------------------------------------------------------20八、旋切单板常见问题指导-----------------------------------------------22九、正确使用和维护-------------------------------------------------------23十、合格证明书--------------------------------------------------------------24十一、装箱单--------------------------------------------------------------25十二、产品质量意见书--------------------------------------------------27一、机床的主要用途该机床是人造胶合板生产线上的重要设备,主要用于小径级原木或有卡旋切机剩余木轴的单板旋切。
旋切长度分为1400mm、2200mm、2700mm;旋切直径分为φ300mm以下和φ400mm以下两种;旋切单板厚度从任意选择。
.本机床采用旋切裁板一体的形式,裁板长度可自行设定,从而大大提高了生产率,降低了人工成本。
二、机床的外观图(图一)1——双辊动力2——进刀丝杠3——进刀丝杠母4——进刀伞轮箱5——进刀动力6——输送带7——进刀传动轴8——裁板动力9——单辊动力10——控制系统11——单辊箱12——单排辊13——双排辊筒14——双辊箱15——机架16——旋切刀17——压刀板18——滑道19——刀台20——输送辊121——砧辊22——输送辊223——裁板刀24——单箱转板三、机床的规格和技术参数注:技术参数仅供参考,如有变更,恕不另行通知。
四、机床的构成及主要部件概述1、机床的构成该机床制造精度及各方面配合要求极高,主要由一次加工成型的框架机架,单、双箱;单、双排辊筒及动力系统;胶辊、裁刀、输送带组成的裁板系统;变频电机进给系统;刀台;单箱转板、斜滑道组成的自动调刀缝系统;数控电器柜等组成。
2、各组件概述本机床机架、单双箱部分均为钢板焊接件,双排辊筒与双支架安装于双辊箱上,单辊单箱装于刀台之上,刀台为全焊件,整体加工,通过两端侧滑道运动于机架上。
伺服电机通过减速机伞轮、后传动轴、丝杠、丝母实现进给、快进和快退。
单双辊动力传动系统保证辊筒转速一致。
旋切刀通过压刀板固定在刀台之上,通过调整丝可调整刀刃高度和刀缝大小。
五、电气系统1、电气原理图2、电气元件明细表续表V DF-VE变频器显示屏显示字符说明:4. 旋切裁板一体机数控裁切部分操作指南重要提示:在所有界面当中,用户一般只需调整旋切厚度和裁板宽度;其它参数出厂时已设定好,用户在不了解的情况下,千万注意不要随意更改;主要靠调整机械部分如:刀高、刀缝、单辊压力来达到板厚、板宽的要求。
----------首先调整厚度,以设定厚度与实际厚度相符为准,然后再调整板宽度。
一体机显示界面速查表:(以做厚,裁板宽度650mm为例,仅供参考。
)、开机上电,屏幕上出现界面一,点击【简体中文】进入界面二(界面一)(界面二)如果[界面二]左下角出现[ PLC运行]说明PLC没有运行,机器不能工作。
按[ PLC运行]键开始运行;如果PLC运行正常,[界面二]左下角显示[日期]。
、下面以设定单板厚度,裁切宽度650mm,举例说明:在【界面二】时,点击屏幕上面[厚度设定]进入【界面三】(界面三)、在【界面三】时,可改变[厚度设定]数值,以达到加工各种厚度单板;具体操作按界面详细提示进行。
在此界面中,可实时监测到设定的【厚度设定】以及【圆木直径】和【运行频率】的变化值即设备工作状态。
【刀盒换向阀夹紧】和【刀盒换向阀松开】是液压夹刀功能,为选配。
、如果板子厚度不准确,均匀度不好等问题可以在界面三时点击[补偿参数],然后输密码8个2即,可以进入界面四。
(界面四)【1 厚度校正】此功能是用来改变单板厚度校正值,从而校正设定厚度与实际厚度不符的现象,来使实际厚度与设定厚度吻合。
【2 人工补偿厚度】此功能是指:在木头不圆时,人为增加单板厚度,做一些较为厚的单板。
此功能要配合操作台上的[人工补偿]按钮使用,在木头不圆时按下[人工补偿]按钮,设备按实际厚度加上[人工补偿厚度]值旋切,在木头刚好找完圆时松开[人工补偿]按钮,此时按设定值正常旋切,此值可根据需要设定。
【3 直径补偿】此功能是改变单板前面厚后面薄或前面薄后面厚,操作如下:单板前面厚后面薄补偿改为负数(-1或-2、-3等),前面薄后面厚改为正数(+1、+2、+3等),出厂值是“0”。
【4 旋切补偿长度】是根据刚开始旋切时单板虚尖长度而设定。
【5 旋切补偿厚度】是根据刚开始旋切时的单板厚度而定,一开始板子厚度薄多少就补多少,如果达不到厚度可继续增加。
【6 尾部补偿长度】是指在木轴旋切结束点以前的长度,也就是单板从后向前厚度有偏差的长度。
【7 尾部补偿厚度】是根据单板尾部厚度偏差值而设定,可加可减,从而达到要求的厚度。
【8 尾部补偿结束直径】是指剩余木芯直径,可更改。
【9 旋切补偿选择】是配合【1 厚度校正】和【3 直径补偿】来用的,也就是说改变1、3的值后一定要点击【旋切补偿选择】,否则1、3值程序不执行,选择此按钮后,按钮界面变为绿色。
【10 尾部补偿选择】是配合【6 尾部补偿长度】和【7 尾部补偿厚度】来用的,也就是说改变6、7 的值确定后一定要点击【尾部补偿选择】,否则程序不执行,选择此按钮后,按钮界面变为绿色。
【11 前补开关选择】是配合【4 旋切补偿长度】和【5 旋切补偿厚度】来用的,也就是说改变4、5的值确定后一定要点击【前补开关选择】,否则程序不执行,选择此按钮后,按钮界面变为绿色。
、在【主界面三】时,点击【参数设定】,输入密码8个2,Enter键进入界面五:(界面五)★在界面五中:可改变快进快退的显示数值,从而改变快进快退速度,此值可在20--150Hz之间调整,建议值为50Hz。
【2 上行限位设定】即木头剩余最小直径,可随意改变,此范围为25--100mm,建议值为35mm。
【3 下行限位设定】即木头的最大直径,可随意改变,一般根据木材直径设定,最大值不要超过300或400mm(视机型而定)。
★否则会撞车,造成设备永久损坏(为防止程序故障,本设备装有下行极限硬件开关,出厂已调试好勿动)。
【4 尾部频率限制直径】是指:旋切到此直径时进给频率锁死不再提升,此功能配合【尾部频率限制选择】按钮使用,(此功能基本上不用)。
、在【界面五】时,点击【下一页】,进入界面六:(界面六)【1 气动打轴延迟时间】是指木轴最小时,单双辊停止并开始退车到打木轴气缸开始动作的时间,时间长短可以调整。
此时间应小于【压辊停止时间】。
【2 气动打轴时间】是指打木轴气缸工作时间的长短,时间长短可以调整。
此时间应小于【压辊停止时间】。
【3 压辊停止时间】是指单双辊停止转动到重新启动的间隔时间,时间长短可以调整。
【4 收板延迟时间】和【5 收板时间】暂不选用。
【6 气动打轴使用选择】有打木轴机构的设备才选用,选用时点击【气动打轴使用选择】按钮,按钮变为绿色为选用。
、在【界面五】时,点击【屏幕左上角】,进入界面七:(界面七)输入密码:,点击Ennter键进入界面八:(界面八)【1 界面八】中的参数如:【丝杠螺距】、【压辊直径】、【压辊中心距】、【压辊转速】、【旋切减速比】、【旋切编码器线数】,出厂时已设定好,不要随意更改,否则会造成系统瘫痪。
以上界面中的数值仅供参考,以实际为准(机型不同,参数可能不同)。
【1 原点距离】的数值,不同机数值可能不同,在配电箱右侧,“重点提示”铭牌中查找。
【原点距离】出厂时已设定好,它是整个系统正常工作的关键技术参数,不要随意更改。
【2 圆木直径】数值随张口大小而即时变化。
【3 水平距离】数值随张口大小而即时变化。
【水平距离】示意图;★当【原点距离】接近开关(见整机结构图三)不慎挪动后,或单板均匀度差时,就需要矫正原点距离。
首先将【原点距离】接近开关紧固好,开关端面距检测铁板之间距离不能超过5mm。
如上图所示,测出双排辊筒切面到刀刃的直线距离A,再加上辊筒半径R,(现有辊筒直径为¢99mm、¢110mm、¢103mm,半径R分别为:、55mm、。
不同机型辊筒直径、半径不一样。
)这样A﹢R=【水平距离】测出【水平距离】后,与显示屏显示的【水平距离】数值相比较。
举例:以¢99mm辊筒为例,实测【水平距离】值比显示值大10mm,就在【原点距离】显示值上加10mm,确认后-----【圆木直径】、【水平距离】的数值会自行校正。
若实测值比显示值小10mm,就在【原点距离】显示值上减去10mm,确认后-----【圆木直径】、【水平距离】的数值会自行校正。
、在【界面八】时,点击【下一页】,进入界面九:(界面九)、在【界面二】时,点击【裁板设定】,进入界面十:(界面十)【1 裁切长度】是指设定单板宽度。