凸凹模刃口尺讲义寸计算
凸、凹模刃口尺寸的计算
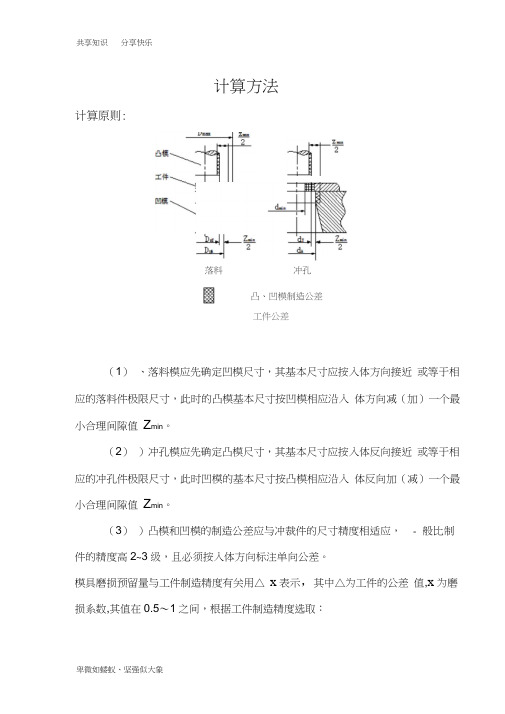
工件公差(1) 、落料模应先确定凹模尺寸,其基本尺寸应按入体方向接近 或等于相应的落料件极限尺寸,此时的凸模基本尺寸按凹模相应沿入 体方向减(加)一个最小合理间隙值 Z min 。
(2) )冲孔模应先确定凸模尺寸,其基本尺寸应按入体反向接近 或等于相应的冲孔件极限尺寸,此时凹模的基本尺寸按凸模相应沿入 体反向加(减)一个最小合理间隙值 Z min 。
(3) )凸模和凹模的制造公差应与冲裁件的尺寸精度相适应, - 般比制件的精度高2~3级,且必须按入体方向标注单向公差。
模具磨损预留量与工件制造精度有关用△ x 表示,其中△为工件的公差 值,x 为磨损系数,其值在0.5〜1之间,根据工件制造精度选取:计算原则:计算方法落料 冲孔凸、凹模制造公差工件精度IT10级以上X =1.0工件精度IT11〜13X =0.75工件精度IT14X =0.5规则形状冲裁模凸模、凹模制造偏差51、分别加工法§凸+ §凹W Z max- Z min落料D凹=(D max - X △0D凸=(D凹-Z min )二凸=(D max - X △Z min )」凸冲孔d凸=(d min + X △) 1凸d凹=(d凸+ Z min ) 0 = ( d min + X△Z min ) 0孔心距孔心距属于磨损后基本不变的尺寸,在同一工步中,在工件上冲出的孔距为L±2/2两个孔时,其凹模型孔心距L d可按下式确定。
L d =L+ —■-8:凸、「•凹一一凸、凹模制造公差,可按IT6〜IT7级来选取,或取、•凸W0.4 ( Z max- Z min ) , '•凹W0.6 ( Z max" Z min )2、单配加工法单配加工法是用凸模和凹模相互单配的方法来保证合理间隙的一种方法。
此方法只需计算基准件(冲孔时为凸模,落料时为凹模)基本尺寸及公差,另一件不需标注尺寸,仅注明“相应尺寸按凸模(或凹模)配做,保证双面间隙在Z max〜Z min之间”即可。
凸凹模(落料、拉深)尺寸计算
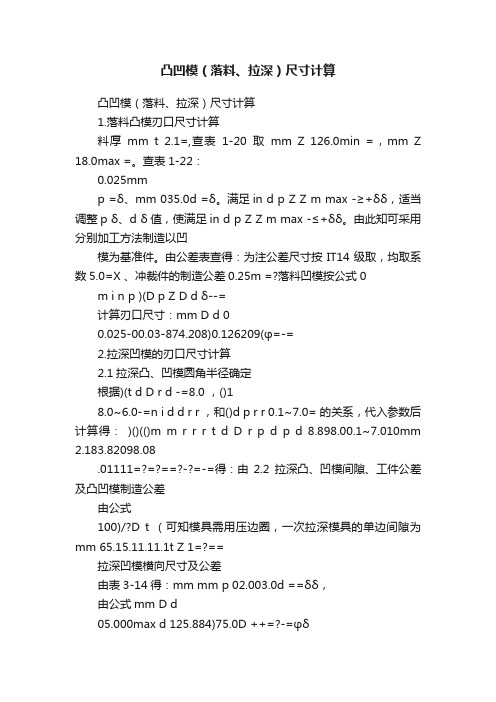
凸凹模(落料、拉深)尺寸计算凸凹模(落料、拉深)尺寸计算1.落料凸模刃口尺寸计算料厚mm t 2.1=,查表1-20取mm Z 126.0min =,mm Z 18.0max =。
查表1-22:0.025mmp =δ、mm 035.0d =δ。
满足in d p Z Z m max -≥+δδ,适当调整p δ、d δ值,使满足in d p Z Z m max -≤+δδ。
由此知可采用分别加工方法制造以凹模为基准件。
由公差表查得:为注公差尺寸按IT14级取,均取系数5.0=X 、冲裁件的制造公差0.25m =?落料凹模按公式0 m i n p )(D p Z D d δ--=计算刃口尺寸:mm D d 00.025-00.03-874.208)0.126209(φ=-=2.拉深凹模的刃口尺寸计算2.1拉深凸、凹模圆角半径确定根据)(t d D r d -=8.0 ,()18.0~6.0-=n i d d r r ,和()d p r r 0.1~7.0= 的关系,代入参数后计算得:)()(()m m r r r t d D r p d p d 8.898.00.1~7.010mm 2.183.82098.08.01111=?=?==?-?=-=得:由2.2拉深凸、凹模间隙、工件公差及凸凹模制造公差由公式100)/?D t (可知模具需用压边圈,一次拉深模具的单边间隙为mm 65.15.11.11.1t Z 1=?==拉深凹模横向尺寸及公差由表3-14得:mm mm p 02.003.0d ==δδ,由公式mm D d05.000max d 125.884)75.0D ++=?-=φδ3.1计算弹簧的预压力冲模冲裁的板料厚度t=1.2mm ,由表1-7得MPa b 350=σ,由表1-8得45.00=X K ,冲裁力:N Lt F b .22756293502.16.2656=??==σ ,所以卸料力:N F X .31124035.236211445.00=?=按标准选弹簧个数n=4,则每个弹簧的预压力为;N F F Y Y 5.731004/1.3124034/1===3.2初选弹簧规格估算弹簧的极限负荷.5N 62015.73100221=?==r j F F查标准GB/T 2089—94。
冲裁——凸凹模刃口尺寸计算课件
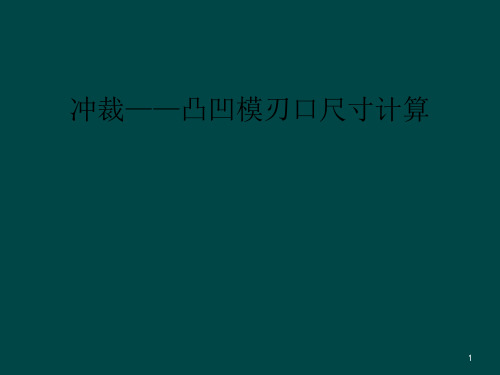
二、计算方法
1.凸凹模分开加工
具有互换性、制造周期短,但Zmin不易保
度,增加制造
形状的工件,必落须料满足
冲孔
适用于圆形或简单
(1)冲孔 (2)落料 (3)孔间距
落料
冲孔
IT10以上 x=1; IT11~13 x=0.75; IT14 x=0.5.
例1:冲制图示零件,材料为10钢, 料厚t=1.0mm。计算冲裁凸、凹模 刃口尺寸及公差。
凸模实际刃口尺寸与落料凹模配制,保证最小双面合理间隙值0.10mm
落料凸、凹模尺寸 a) 落料凹模尺寸 b) 落料凸模尺寸
图示连接板冲裁零件, 材料为10钢,厚度为2mm, 大批量生产,计算该零件 模具刃口尺寸。
谢谢!
19
x = 0.75。
落料凹模的刃口尺寸计算如下: 第一类尺寸:磨损后增大的尺寸
第二类尺寸:磨损后减小的尺寸
第三类尺寸:磨损后基本不变的尺寸
落料凸模的基本尺寸与凹模相同,分别是79.79mm, 39.75mm,34.75mm,22.07mm,14.94mm,不必标注公差,但 要在技术条件中注明:凸模实际刃口尺寸与落料凹模配制,保证 最小双面合理间隙值
d = 22±0.14mm
板料厚度t=1mm,材料为10号钢。 试计算冲裁件的凸模、凹模刃口尺寸及制造公差。 解:该冲裁件属落料件,选凹模为设计基准件,只需要计算落料 凹模刃口尺寸及制造公差,凸模刃口尺寸由凹模实际尺寸按间隙 要求配作。
由表查得:
由公差表查得: 尺寸80mm,选x = 0.5;尺寸15 mm,选x = 1;其余尺寸均选
了解:
精密冲裁和其它冲裁方法
§2.3冲裁凸凹模刃口尺寸的计算
一、尺寸计算原则
冲裁凸、凹模刃口尺寸计算

2.7.3 冲裁凸、凹模刃口尺寸计算
[例2-1] 用分开制造计算图2-72所示零件的凸凹模 刃口尺寸。
图2-72 零件图
解:1、确定基本工序 内形:冲孔。外形:落料 2、画磨损曲线
2.7.3 冲裁凸、凹模刃口尺寸计算
① 冲孔 画凸模刃口的磨损曲线如图2-73
② 落料 画凹模刃口的磨损曲线。如图2-74
按上(1)、(2)之法可得出: 冲孔磨后变大的公式
δ 凹 a凸 (a max x)0
(2-28) (2-29)
a凹 (a凸 Z min)0 δ 凸
落料磨后变小的公式
δ 凹 B凸 (B凹 Z min)0
(2-30) (2-31)
B凹 (Bmin x)0 δ 凸
0 0.52
2.7.3 冲裁凸、凹模刃口尺寸计算
尺寸Ⅳ、Ⅴ:25( )为落料磨后变大. Δ=0.52→IT14→X=0.5 A凹1 =(A1max-xΔ) =(25-0.5×0.52) =24.74 A凸1=( A凹1- Zmin) =(24.74-0.24) =24.5 尺寸Ⅵ: 7为落料单边磨后变大, Δ=0.2→IT13→X=0.75 A凹2=(A2max-xΔ) =(7-0.750.2)=6.85 A凸2=( A凸2 - )=(6.85-)=(6.85-0.12) =6.73
0.2 0
2.7.3 冲裁凸、凹模刃口尺寸计算
尺寸Ⅳ、Ⅴ:25( )为落料磨后变大. Δ=0.52→IT14→X=0.5 A凹1 =(A1max-xΔ) =(25-0.5×0.52) =24.74 A凸1=( A凹1- Zmin) =(24.74-0.24) =24.5 尺寸Ⅵ: 7为落料单边磨后变大, Δ=0.2→IT13→X=0.75 A凹2=(A2max-xΔ) =(7-0.750.2)=6.85 A凸2=( A凸2 - )=(6.85-)=(6.85-0.12) =6.73
凸、凹模刃口尺寸计算
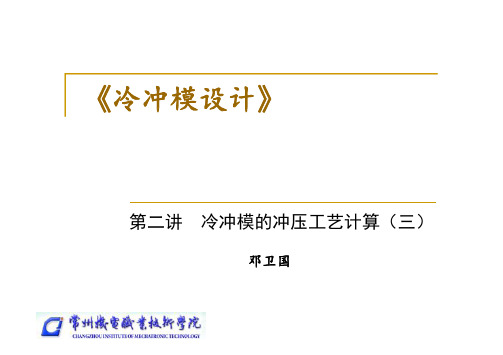
《冷冲模设计》第二讲冷冲模的冲压工艺计算(三)邓卫国第二讲冷冲模的冲压工艺计算(三)第三部分凸、凹模刃口尺寸的确定凹模与凸模的刃口尺寸计算定义:什么叫刃口尺寸:刃口尺寸指在凹模和凸模零件图上分别标注尺寸及公差值,这个值与冲压产品尺寸精度有关。
⏹学习目标☐掌握凸、凹模刃口计算作用☐掌握凸、凹模刃口尺寸计算的依据和原则☐掌握凸、凹模刃口尺寸计算的方法二、冲裁模凸、凹模刃口尺寸的确定1、冲裁模凸、凹模刃口计算的作用冲裁件的尺寸精度主要取决于凸、凹模的刃口部分尺寸。
并且合理的冲裁间隙也靠凸、凹模刃口尺寸保证。
凸模刃口尺寸示意图所以冲裁模刃口设计是冲裁模设计的重点。
凹模刃口尺寸示意图二、冲裁模凸、凹模刃口的确定2、凸、凹模刃口尺寸计算的依据在生产实践中发现:a.由于凸凹模之间存在间隙,冲裁件断面都带有锥度。
依据:①光亮带是冲压件测量和使用部位;②落料件的光亮带,是因凹模刃口挤切材料产生的;③冲孔件的光亮带,是因凸模刃口挤切材料产生的;④落料件的大端(光亮带)尺寸等于凹模尺寸;⑤冲孔件的小端(光亮带)尺寸等于凸模尺寸。
b.凸模轮廓越磨越小,凹模轮廓越磨越大,结果使间隙越用越大。
结论:在计算冲裁模刃口尺寸时,应按落料、冲孔两种情况分别进行计算。
二、冲裁模凸、凹模刃口尺寸确定3、冲裁模凸、凹模刃口计算的原则(一)(1)设计落料模先确定凹模刃口尺寸以凹模为基准,间隙取在凸模上,即冲裁间隙通过减小凸模刃口尺寸来取得;设计冲孔模先确定凸模刃口尺寸以凸模为基准,间隙取在凹模上,冲裁间隙通过增大凹模刃口尺寸来取得。
二、冲裁模凸、凹模刃口尺寸的确定4、冲裁模凸、凹模刃口计算的原则(二)(2)根据冲模在使用过程中的磨损规律:设计落料模时:凹模基本尺寸应取接近或等于零件的最小极限尺寸;设计冲孔模时:凸模基本尺寸则取接近或等于冲件孔的最大极限尺寸。
理由:凸、凹模在磨损到一定程度时,仍能冲出合格的零件。
二、冲裁模凸、凹模刃口尺寸确定5、冲裁模凸、凹模刃口计算的原则(三)(3)凹模和凸模制造公差主要与冲裁件的精度有关①一般冲模精度较零件精度高3~4级;②形状简单的圆形、方形刃口,其制造偏差值可按IT6~IT7级来选取,或查表;③形状复杂的刃口制造偏差可按零件相应部位公差值的1/4来选取;④刃口尺寸磨损后无变化的制造偏差值可取冲件相应部位公差值的l/8并冠(±);⑤若零件没有标注公差,则可按IT14级取值。
【最新资料】凸、凹模刃口尺寸的计算
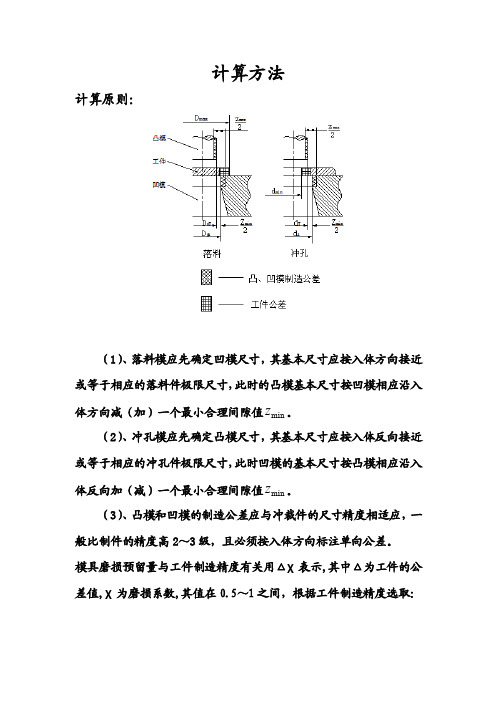
计算方法计算原则:(1)、落料模应先确定凹模尺寸,其基本尺寸应按入体方向接近或等于相应的落料件极限尺寸,此时的凸模基本尺寸按凹模相应沿入z。
体方向减(加)一个最小合理间隙值min(2)、冲孔模应先确定凸模尺寸,其基本尺寸应按入体反向接近或等于相应的冲孔件极限尺寸,此时凹模的基本尺寸按凸模相应沿入z。
体反向加(减)一个最小合理间隙值min(3)、凸模和凹模的制造公差应与冲裁件的尺寸精度相适应,一般比制件的精度高2~3级,且必须按入体方向标注单向公差。
模具磨损预留量与工件制造精度有关用△χ表示,其中△为工件的公差值,χ为磨损系数,其值在0.5~1之间,根据工件制造精度选取:工件精度IT10级以上χ=1.0工件精度IT11~13 χ=0.75工件精度IT14 χ=0.5规则形状冲裁模凸模、凹模制造偏差δ凸模和凹模分别加工时间隙变动范围1、 分别加工法凸δ+凹δ≤max Z -min Z 落料凹D =(max D -χ△)凹δ+0凸D =(凹D -min Z )0凸δ-=(max D -χ△-minZ )0凸δ- 冲孔凸d =(min d +χ△)0凸δ-凹d =(凸d +min Z )凹δ+0=(min d +χ△+min Z )凹δ+0孔心距孔心距属于磨损后基本不变的尺寸,在同一工步中,在工件上冲出的孔距为L ±Δ/2两个孔时,其凹模型孔心距d L 可按下式确定。
d L =L+∆81凸δ、凹δ——凸、凹模制造公差,可按IT6~IT7级来选取,或取 凸δ≤0.4(max Z -min Z ) , 凹δ≤0.6(max Z -min Z )2、 单配加工法单配加工法是用凸模和凹模相互单配的方法来保证合理间隙的一种方法。
此方法只需计算基准件(冲孔时为凸模,落料时为凹模)基本尺寸及公差,另一件不需标注尺寸,仅注明“相应尺寸按凸模(或凹模)配做,保证双面间隙在max Z ~min Z 之间”即可。
在制件上,会同时有三类不同性质的尺寸,需要区别对待, 第一类:凸模(冲孔件)或凹模(落料件)磨损后增大的尺寸;第一类基准尺寸=(冲裁件上该尺寸的最大极限-χ△)4/0∆+第二类:凸模(冲孔件)或凹模(落料件)磨损后减小的尺寸;第二类基准尺寸=(冲裁件上该尺寸的最小极限+χ△)04/∆- 第三类:凸模(冲孔件)或凹模(落料件)磨损后基本不变的尺寸。
第二章冲裁三.凸、凹模刃口尺寸的计算
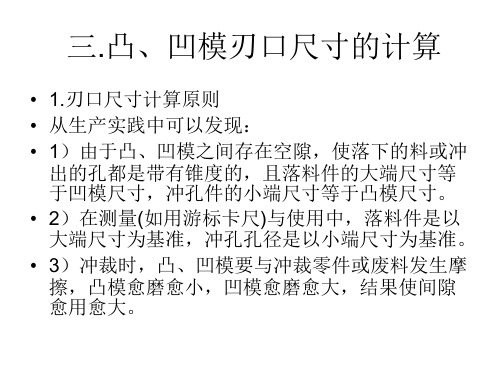
• 3)确定冲裁刃口制造公差时,应考虑制件 的精度Δ要求。如果对刃口精度δ要求过 高(即制造公差δ过小),会使模具制造 困难,增加成本,延长生产周期;如刃口 精度δ要求过低(即制造公差δ过大), 则生产出来的零件可能不合格,或使模具 的寿命降低。零件精度Δ与模具制造精度 δ的关系见表2.1(P11)。若零件没有标 注公差(P17)……
2.刃口尺寸计算方法
• (1)凸、凹模分开加工(圆形 或方形工件,且满足不等式) • ①已知落料件的尺寸与公差如 右图,其尺寸由凹模刃口确定。 先求凹模:因凹模刃口使用磨 损后会变大,所以名义尺寸预先比 D取小一些(- ∆ )。另外“孔”取正公差: Dd=(D-xΔ)0+δd (2.3) 式中x∆代表磨损量,取孔的偏小值,0.5<x≤1,系数x 查P18表2.7。 再求凸模:Dp=(Dd-Zmin)0 –δp =(D-xΔ-Zmin)0 –δp 凸模相当于“轴”取负公差。 公差δd和δp查P18表2.6。
(2)凸、凹模配合加工(复 杂形状工件) ①落料件的模具刃口尺寸 右图为落料工件和基准件凹 模。先求凹模,再配制凸 模。 a.先分析凹模刃口磨损后尺 寸的变化得出三种规律(用 虚线沿外围画出轮廓线后 再比较各尺寸的变化): 磨损后尺寸变大的A类(相 当于“孔”); 磨损后尺寸变小的B类(相 当于“轴”); 磨损后尺寸不变的C类。
• ②已知冲孔件的尺寸与公差如右图。 孔的尺寸由凸模刃口决定,先求 凸模(因为凸模使用磨损后会变小,所 以名义尺寸预先取大一些(+Δ)。且凸 模相当于“轴”取负公差。 凸模:dp=(d+xΔ)0-δp (2.1) 再求凹模:凹模相当于“孔”,取负公差。 dd=(dp+Zmin)0+δd=(d+xΔ+Zmin)0+δd (2.2) X、δp、δd同落料时一样查表。 • ③关于工件制造公差Δ的表示方法 若工件孔的尺寸最初是以d± Δ’的不规范形式表示, 则使用公式前应先变换为: d±Δ’=(d+Δ’)0-2Δ’落料=(d-Δ’)0+2 Δ’冲孔
凸、凹模刃口尺寸的计算
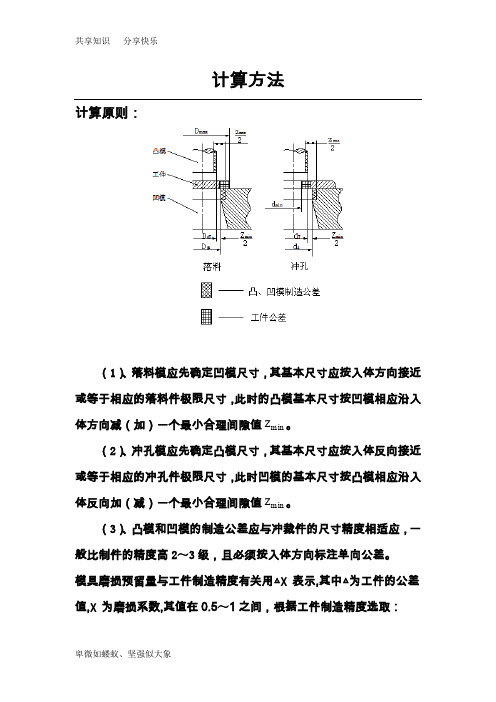
计算方法计算原则:(1)、落料模应先确定凹模尺寸,其基本尺寸应按入体方向接近或等于相应的落料件极限尺寸,此时的凸模基本尺寸按凹模相应沿入z。
体方向减(加)一个最小合理间隙值m in(2)、冲孔模应先确定凸模尺寸,其基本尺寸应按入体反向接近或等于相应的冲孔件极限尺寸,此时凹模的基本尺寸按凸模相应沿入z。
体反向加(减)一个最小合理间隙值m in(3)、凸模和凹模的制造公差应与冲裁件的尺寸精度相适应,一般比制件的精度高2~3级,且必须按入体方向标注单向公差。
模具磨损预留量与工件制造精度有关用△χ表示,其中△为工件的公差值,χ为磨损系数,其值在0.5~1之间,根据工件制造精度选取:工件精度IT10级以上χ=1.0工件精度IT11~13 χ=0.75工件精度IT14 χ=0.5规则形状冲裁模凸模、凹模制造偏差δ凸模和凹模分别加工时间隙变动范围1、 分别加工法凸δ+凹δ≤max Z -min Z 落料凹D =(max D -χ△)凹δ+0凸D =(凹D -min Z )0凸δ-=(max D -χ△-min Z )0凸δ-冲孔凸d =(min d +χ△)0凸δ-凹d =(凸d +min Z )凹δ+0=(min d +χ△+min Z )凹δ+0孔心距孔心距属于磨损后基本不变的尺寸,在同一工步中,在工件上冲出的孔距为L ±Δ/2两个孔时,其凹模型孔心距d L 可按下式确定。
d L =L+∆81凸δ、凹δ——凸、凹模制造公差,可按IT6~IT7级来选取,或取 凸δ≤0.4(max Z -min Z ) , 凹δ≤0.6(max Z -min Z )2、 单配加工法单配加工法是用凸模和凹模相互单配的方法来保证合理间隙的一种方法。
此方法只需计算基准件(冲孔时为凸模,落料时为凹模)基本尺寸及公差,另一件不需标注尺寸,仅注明“相应尺寸按凸模(或凹模)配做,保证双面间隙在max Z ~min Z 之间”即可。
凸模与凹模刃口尺寸的计算

冲压工艺与模具设计冲裁模凸模与凹模刃口尺寸的计算主讲人:陈德平落料件大端尺寸冲孔件小端尺寸1、 基准件的确定 落料件尺寸由凹模尺寸决定,以凹模为基准,间隙取在凸模上; 冲孔件尺寸由凸模尺寸决定;以凸模为基准, 间隙取在凹模上。
2.3.1 凸模、凹模刃口尺寸计算的依据和原则2、考虑冲模的磨损规律 落料模:凹模基本尺寸应取落料件公差范围的较小尺寸; 冲孔模:凸模基本尺寸应取冲孔件公差范围的较大尺寸。
冲裁间隙采用最小合理间隙值3、制件和冲模刃口尺寸偏差应按“入体”原则标注“入体”原则:向材料实体方向单向标注落料件和凸模上偏差为零,下偏差为负;冲孔件和凹模上偏差为正,下偏差为零。
2.3.2 凸、凹模刃口尺寸的计算方法图 2.3.1冲模的制造公差与冲裁间隙之间关系图 a)落料;b)冲孔 1、凸模与凹模分别加工计算模具刃口尺寸分开加工:是指凸模和凹模分别按图纸标注的尺寸和公差进行加工特点:制造周期短,互换性好,但是间隙受模具制造影响,适合于简单形状的冲压件。
冲模的制造公差与冲裁间隙之间应满足:∣δp∣+ ∣δd∣≤2c max-2c minδp ——凸模下偏差;δd——凹模上偏差。
若:∣δp∣+ ∣δd∣>2c max-2c min取δp = 0.4(2c max-2c min) ;δd = 0.6(2c max-2c min)(1)落料(以凹模为基准,先确定凹模尺寸)落料凹模的尺寸:D d=(D max-xΔ)0+ δd落料凸模的尺寸:D p=(D d- 2c min)0-δp(2)冲孔(以凸模为基准,先确定凸模尺寸)冲孔凸模的尺寸:d p=(d min+ xΔ)0-δp冲孔凹模的尺寸:d d=(d p+2c min)0+ δd(3)凹模型孔中心距:L d=(L min+0.5Δ)±0.125Δ2、凸模和凹模配制加工计算刃口尺寸按尺寸和公差制造出凹模或凸模其中一个(基准件),然后依此为基准再按最小合理间隙配作另一件。
计算凸、凹模刃口尺寸及公差xiugai
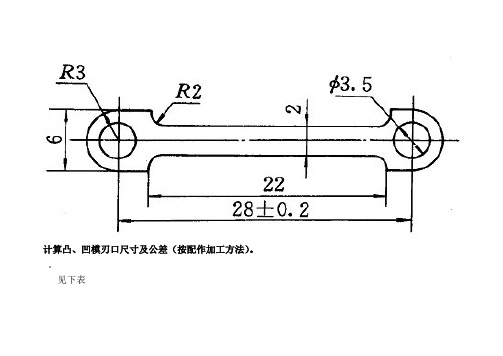
R2
22+0.52
R2+0.25
B凸= (Bmax+x⊿)-⊿/4
0.5
0.5
22.26-0.13
2.13-0.063
随基本刃口磨损而变小(凸模尺寸),
∮3.5
∮3.5+0.3
0.5
与凸模实际刃口配做
3.65-0.075
C类:随基本刃口磨损而不变(凸模的位置尺寸),
28
28+0.2
C凹=C+⊿/8
零件尺寸性质
尺寸分类
公差标注
计算公式
X值取定
凸模刃口
B类,零件尺寸随基本(凸模)刃口磨损而变小
∮3.5
∮3.5+0.3
B凸= (Bmax+x⊿)-⊿/4
0.5
3.65-0.பைடு நூலகம்75
凸凹模刃口尺寸配做,要求保证双面间隙0.05—0.07 mm。
合并以上计算:凹模、凸模图纸尺寸标注尺寸;凸凹模不标注尺寸,只注明配作关系及配作间隙。
计算凸、凹模刃口尺寸及公差(按配作加工方法)。
。
见下表
落料凹模:外形落料,尺寸公差等级皆为IT14级:
零件尺寸性质
尺寸分类
公差标注
计算公式
X值取定
凹模刃口
A类,零件尺寸随基本(凹模)刃口磨损而变大
6
2
R3
6--0.3
2--0.25
A凹= (Amax--x⊿)+⊿/4
0.75
0.75
5.8+0.075
28+0.5
1.81+0.063
2.9+0.038
B类,零件尺寸随基本(凹模)刃口磨损而变小
第三节凸模与凹模刃口尺寸的确定

+δ A min 0
)
0 −δ T
d
+∆ 0
+δ A min 0
= (d min + x∆ + Z
)
第三章 冲裁工艺与冲裁模设计 (3)孔心距
∆ ∆ Ld = Lmin + ± 2 8
x
δT
查表3-7
δA
查表3-6
第三章 冲裁工艺与冲裁模设计 例 t=0.5mm Q235钢. 计算冲 裁凸、 凹模刃 口尺寸 及公差。
1落料模:以凹模为基准,间隙凸模上 冲孔模:以凸模为基准,间隙凹模上 2落料模:凹模基本=工件较小极限尺寸; 凸模基本=凹模-Zmin 冲孔模:凸模尺寸=工件孔较大极限尺寸 凹模基本=凸模+Zmin。
第三章 冲裁工艺与冲裁模设计
一、凸、凹模刃口尺寸计算原则 计算原则:
3 模具刃口制造公差时,考虑工件精度与 模具精度的关系 高2-3级 4.工件尺寸公差与冲模 制造偏差 “入体” 单向公差。
第三章 冲裁工艺与冲裁模设计 作业:如图 所示垫圈, Q235 t=2mm,采 用分别加工 试确定凸模 凹模的刃口 尺寸及公差。
第三章 冲裁工艺与冲裁模设计
二、凸、凹模刃口尺寸的计算方法
2.配合加工法
基准件(凸模或凹模),然后根据基 准件的实际尺寸再按最小合理间隙配制另一件。 特点: 模具的间隙由配制保证,不必校核δ T + δ A ≤ Z max − Z min
e
第三章 冲裁工艺与冲裁模设计
第三章 冲裁工艺与冲裁模设计
第三章 冲裁工艺与冲裁模设计
第三章 冲裁工艺与冲裁模设计
第三章 冲裁工艺与冲裁模设计
第三章 冲裁工艺与冲裁模设计
凸凹模刃口尺寸计算课件
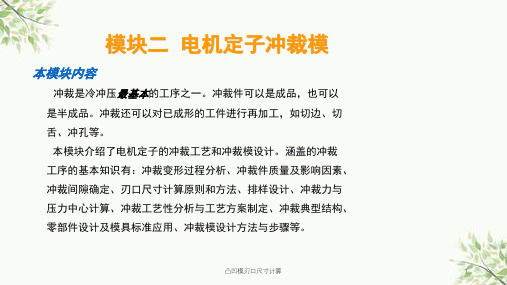
凸凹模刃口尺寸计算
23
A.根据磨损后轮廓变化情况,正确判断出模具刃口尺 寸类型:即:磨损后变大,变小还是不变。
B.根据尺寸类型,采用不同计算公式。 磨损后变大的尺寸,采用分开加工时的落料凹模尺寸计算 公式。 磨损后变小的尺寸,采用分开加工时的冲孔凸模尺寸计算 公式。 磨损后不变的尺寸,采用分开加工时的孔心距尺寸计算公 式。
设计时,基准模的刃口尺寸及制造公差应详细标注,而配 制件上只标注公称尺寸,不注公差,但在图纸技术要求上注 明:“凸(凹)模刃口按凹(凸)模实际刃口尺寸配制,保证
双面合理间隙值 Zmin~Zmax”。
特点: 模具的间隙由配制保证,工艺比较简单,不必校核 T A ≤ ZmaxZmin的条件,并且还可放大基准件的制造公差, 使制造容易。
凸凹模刃口尺寸计算
8
B.模具间隙的影响
间隙小,出现二次剪裂,产生第二光亮带 间隙大,出现二次拉裂,产生二个斜度
C.模具刃口状态的影响 当凸模刃口磨钝时,则会在落料件上端产生毛刺; 当凹模刃口磨钝时,则会在冲孔件的孔口下端产生毛刺; 当凸、凹模刃口同时磨钝时,则冲裁件上、下端都会产 生毛刺。
凸凹模刃口尺寸计算
Z m a Z m x i(0 n .0 0 6 .0 )m 4 0 m .0 m 2m
凸凹模刃口尺寸计算
20
例2-1(续)
由公差表查得:2600.12mm 为IT12级,取x = 0.75; 3600.62mm 为IT14级,取x = 0.5;
设凸、凹模分别按IT6和IT7级加工制造,则
冲孔:d T d m x in 0 T ( 6 0 . 7 0 . 1 5 ) 0 0 . 0 2 0 6 . 0 8 0 0 . 0 9 08
凸凹模刃口尺寸计算
刃口尺寸计算2.3
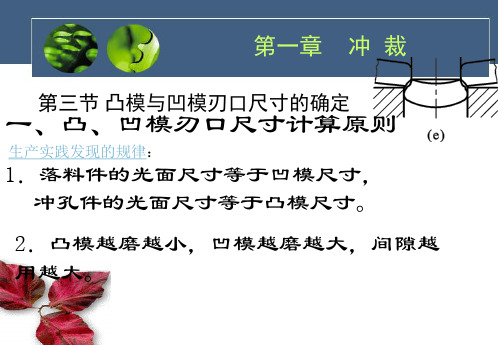
查冲裁初始合理间隙表得:Zmin=0.1 技术要求中说明:凸模刃口尺寸按凹模实际配做,保证最小双面合理 间隙Zmin(0.1mm)
第一章 冲 裁
第一章 冲 裁
= (6.09 + 0.04 )0
+0.012
+ = 6.13 0 0.012
校核: 校核:
δ T + δ A ≤ Z max − Z min
工件精 度IT10 以上 X=1 工件 精度 IT11~ IT13 X=0.75 工件 精度 IT14 X=0.5 也可查 表获得
第一章
冲 裁
第一章 冲 裁
凸、凹模制造公差,可按 取,也可
) − Z min )
IT6~IT7级来选
查表选取,
第一章
冲 裁
第一章
冲 裁
例 t=0.5mm Q235钢. 计算冲 裁凸、 凹模刃 口尺寸 及公差。
第一章 冲 裁
冲制如图所示零件,材料为Q235 钢,料厚t=0.5mm。计算冲裁凸、 凹模刃口尺寸及公差。 解:由图可知,该零件属于无特 殊要求的一般冲孔、落料。
0
校核: 校核: 因此, 因此,可取:
0.016 + 0.025 = 0.04 f 0.02
δ T = 0.4 ⋅ (Z max − Z min ) = 0.4 × 0.02 = 0.008
δ A = 0.6 ⋅ (Z max − Z min ) = 0.6 × 0.02 = 0.012
故:
+ D A = 35.69 0 0.012 mm
a = 80
0 − 0 . 42
mm
b = 40
0 − 0 . 34
mm
c = 35
- 1、下载文档前请自行甄别文档内容的完整性,平台不提供额外的编辑、内容补充、找答案等附加服务。
- 2、"仅部分预览"的文档,不可在线预览部分如存在完整性等问题,可反馈申请退款(可完整预览的文档不适用该条件!)。
- 3、如文档侵犯您的权益,请联系客服反馈,我们会尽快为您处理(人工客服工作时间:9:00-18:30)。
精品
本模块重点
1.冲裁变形规律及冲裁件质量影响因素; 2.刃口尺寸计算原则和方法; 3.冲裁工艺性分析与工艺方案制定; 4.冲裁模典型结构及特点; 5.冲裁模结构设计及模具标准应用; 6.冲裁工艺与冲裁模设计的方法和步骤。
本模块难点
1.冲裁变形规律及冲裁件质量影响因素; 2.刃口尺寸计算原则和方法; 3.模具结构设计及模具标准应用; 4.冲裁工艺与冲裁模设计的方法和步骤。
图纸规定 的公差范 围内
外形满足图纸 要求;表面平 直,即拱弯小
二 冲裁变形过程
3.冲裁件质量及其影响因素 (1)冲裁件断面质量及其影响因素
A.断面组成
圆角带a: 刃口附近的材料产生弯曲和伸长变形。 光亮带b: 塑性剪切变形。质量最好的区域。
通常占全断面1/3─ 1/2 。
断裂带c: 裂纹形成及扩展。 毛刺区d:间隙存在,裂纹产生不在刃尖,毛刺不可避免。
(2)冲裁件尺寸精度及其影响因素 冲裁件的尺寸精度:
指冲裁件的实际尺寸与图纸上基本尺寸之差。 该差值包括两方面的偏差:
一是冲裁件相对于凸模或凹模尺寸的偏差; 二是模具本身的制造偏差。
影响因素: (1)冲模的制造精度(零件加工和装配) (2)材料的性质 (3)冲裁间隙
(3)冲裁件形状误差及其影响因素 冲裁件的形状误差:指翘曲、扭曲、变形等缺陷。
T ≤ 0.4Zma xZmin A ≤ 0.6Zma xZmin
例2-1
如图所示零件,材料Q235钢,料厚 t=0.5mm。计算冲裁凸、凹模刃口尺寸及 公差。
B.冲孔
dTdmi nx0 T
d A d T Z m 0 A i n d m x i n Z m 0 A in
C.孔心距
Ld
=L± 1
8
为了保证可能的初始间隙不超过Zmax,即
T A +Zmin≤Zmax,选取必须满足以下条件:
T A ≤ ZmaxZmin 凸、凹模的制造公差,可按IT6~IT7级来选取。 但需校核。或取
(3)冲裁(设计)间隙一般选用最小合理间隙值(Zmin)。
(4)选择模具刃口制造公差时,要考虑工件精度与模具精 度的关系,即要保证工件的精度要求,又要保证有合理的间 隙值。
(5)工件尺寸公差与冲模刃口尺寸的制造偏差原则上都应 按“标注双向偏差。
(2)表格法(表2.3) (3)经验公式法
四 凸模和凹模的刃口尺寸计算
刃口尺寸计算的作用:
凸模和凹模的刃口尺寸和公差,直接影响冲裁件的尺寸大 小。模具的合理间隙值也靠凸、凹模刃口尺寸及其公差来 保证。
1.凸、凹模刃口尺寸计算原则
(1)设计落料模先确定凹模刃口尺寸。以凹模为基准, 间隙取在凸模上,即冲裁间隙通过减小凸模刃口尺寸来取 得。
此外,间隙不正常、刃口不锋利,还会加大毛刺。
B.模具间隙的影响
B.模具间隙的影响
间隙小,出现二次剪裂,产生第二光亮带 间隙大,出现二次拉裂,产生二个斜度
C.模具刃口状态的影响 当凸模刃口磨钝时,则会在落料件上端产生毛刺; 当凹模刃口磨钝时,则会在冲孔件的孔口下端产生毛刺; 当凸、凹模刃口同时磨钝时,则冲裁件上、下端都会产 生毛刺。
设计冲孔模先确定凸模刃口尺寸。以凸模为基准,间 隙取在凹模上,冲裁间隙通过增大凹模刃口尺寸来取得。
(2)由于凸模在使用中越磨越大,凹模在使用中则越磨越 小,因此在设计落料模时,凹模基本尺寸应取接近或等于工 件的最小极限尺寸;设计冲孔模时,凸模基本尺寸则取接近 或等于工件孔的最大极限尺寸。 模具磨损预留量与工件制造 精度有关。
二 冲裁变形过程
1.冲裁变形时板料变形区力态分析
四对力 凸、凹模间隙存在,
产生弯矩。
1-凸模 2-板材 3-凹模
二 冲裁变形过程
2.冲裁变形过程
(1)弹性变形阶段 (2)塑性变形阶段 (3)断裂分离阶段
二 冲裁变形过程
3.冲裁件质量及其影响因素
指断面状况、尺寸精度和形状误差。
垂直、 光洁、 毛刺小
翘曲:冲裁件呈曲面不平现象。它是由于间隙过大、弯矩
增大、变形拉伸和弯曲成分增多而造成的,另外材 料的各向异性和卷料未矫正也会产生翘曲。
扭曲:冲裁件呈扭歪现象。它是由于材料的不平、间隙不
均匀、凹模后角对材料摩擦不均匀等造成的。
变形:由于坯料的边缘冲孔或孔距太小等原因,因胀形而产
生的。
三 冲裁间隙
Z=DA—dT
命,在保证冲裁件质量的前提下适当采用较大的间隙值是十
分必要的。
2.冲裁模间隙值的确定
主要根据冲裁件断面质量、尺寸精度和模具寿命这三个因 素综合考虑,给间隙规定一个范围值。考虑到在生产过程中的 磨损使间隙变大,故设计与制造新模具时应采用最小合理间隙
Zmin。
(1)理论法确定法
Z2th0tan2t1ht0tan
2.凸、凹模刃口尺寸计算方法
(1)分开加工
具有互换性、制造周期短,但Zmin不易保证,需提高加 工精度,增加制造难度。
(2)配合加工
Zmin易保证,无互换性、制造周期长。
(3)凸模与凹模分开加工
A.落料
D AD ma x x0 A
D T D A Z m 0 T i nD m x a x Z m 0 T in
课题一 冲裁模基础
一 落料与冲孔
冲裁:利用模具使板料沿着一定的轮廓形状产生分离的一种冲压工序。 包括落料、冲孔、切断、修边、切舌、剖切等。 分类:普通冲裁、精密冲裁。
落料冲孔件
落料:若使材料沿封闭曲线相互分离,封闭曲线以内的部分作为冲裁件时, 称为落料;落料工序中使用的模具叫落料模。工件的尺寸由冲裁凹模尺 寸决定。 冲孔:若使材料沿封闭曲线相互分离,封闭曲线以外的部分作为冲裁件时, 则称为冲孔。 冲孔工序中使用的模具叫冲孔模。工件的尺寸由冲孔凸模 尺寸决定。
1.冲裁间隙对冲裁工艺的影响
(1)间隙对冲裁件质量的影响:间隙是影响冲裁件质量的 主要 因素。
(2)间隙对冲裁力的影响:随间隙的增大冲裁力有一定程 度的降低,但影响不是很大。 间隙对卸料力、推件力的影 响比较显著。随间隙增大,卸料力和推件力都将减小。
(3)间隙对模具寿命的影响:小间隙将使磨损增加,甚至 使模具与材料之间产生粘结现象,并引起崩刃、凹模胀裂、 小凸模折断、凸凹模相互啃刃等异常损坏。为了延长模具寿