汽车座椅制造工艺
汽车座椅工艺流程
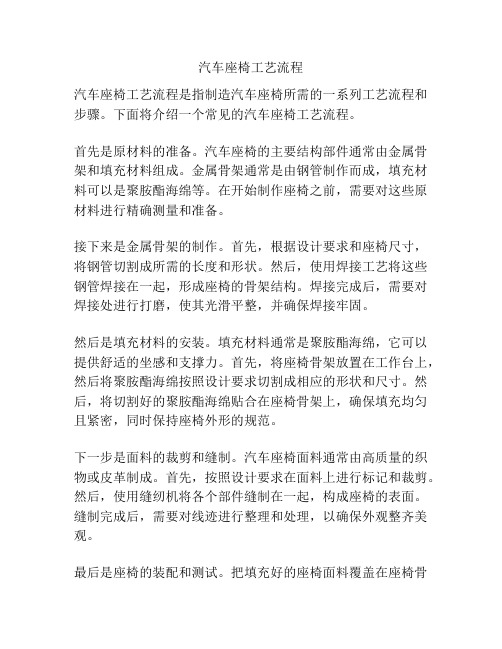
汽车座椅工艺流程汽车座椅工艺流程是指制造汽车座椅所需的一系列工艺流程和步骤。
下面将介绍一个常见的汽车座椅工艺流程。
首先是原材料的准备。
汽车座椅的主要结构部件通常由金属骨架和填充材料组成。
金属骨架通常是由钢管制作而成,填充材料可以是聚胺酯海绵等。
在开始制作座椅之前,需要对这些原材料进行精确测量和准备。
接下来是金属骨架的制作。
首先,根据设计要求和座椅尺寸,将钢管切割成所需的长度和形状。
然后,使用焊接工艺将这些钢管焊接在一起,形成座椅的骨架结构。
焊接完成后,需要对焊接处进行打磨,使其光滑平整,并确保焊接牢固。
然后是填充材料的安装。
填充材料通常是聚胺酯海绵,它可以提供舒适的坐感和支撑力。
首先,将座椅骨架放置在工作台上,然后将聚胺酯海绵按照设计要求切割成相应的形状和尺寸。
然后,将切割好的聚胺酯海绵贴合在座椅骨架上,确保填充均匀且紧密,同时保持座椅外形的规范。
下一步是面料的裁剪和缝制。
汽车座椅面料通常由高质量的织物或皮革制成。
首先,按照设计要求在面料上进行标记和裁剪。
然后,使用缝纫机将各个部件缝制在一起,构成座椅的表面。
缝制完成后,需要对线迹进行整理和处理,以确保外观整齐美观。
最后是座椅的装配和测试。
把填充好的座椅面料覆盖在座椅骨架上,并用固定装置将其固定在骨架上。
装配完成后,需要对座椅进行一系列的测试。
例如,测试坐垫和靠背的支撑力是否符合要求,调整可调部件是否灵活,以及确保座椅的稳定性和安全性等。
测试通过后,座椅便可以包装和运送到汽车制造厂,然后装配在汽车上。
总结起来,汽车座椅工艺流程包括原料准备、金属骨架制作、填充材料安装、面料裁剪和缝制、座椅装配和测试等一系列流程和步骤。
这些工艺流程需要严格的执行和控制,以确保生产的座椅质量和性能达到设计要求。
汽车座椅工艺流程
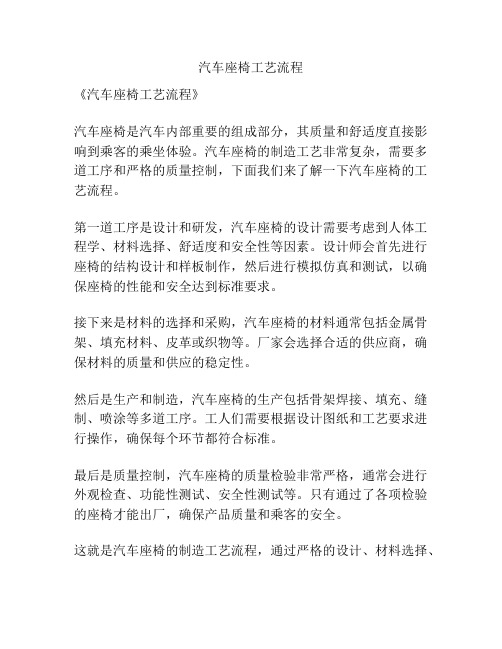
汽车座椅工艺流程
《汽车座椅工艺流程》
汽车座椅是汽车内部重要的组成部分,其质量和舒适度直接影响到乘客的乘坐体验。
汽车座椅的制造工艺非常复杂,需要多道工序和严格的质量控制,下面我们来了解一下汽车座椅的工艺流程。
第一道工序是设计和研发,汽车座椅的设计需要考虑到人体工程学、材料选择、舒适度和安全性等因素。
设计师会首先进行座椅的结构设计和样板制作,然后进行模拟仿真和测试,以确保座椅的性能和安全达到标准要求。
接下来是材料的选择和采购,汽车座椅的材料通常包括金属骨架、填充材料、皮革或织物等。
厂家会选择合适的供应商,确保材料的质量和供应的稳定性。
然后是生产和制造,汽车座椅的生产包括骨架焊接、填充、缝制、喷涂等多道工序。
工人们需要根据设计图纸和工艺要求进行操作,确保每个环节都符合标准。
最后是质量控制,汽车座椅的质量检验非常严格,通常会进行外观检查、功能性测试、安全性测试等。
只有通过了各项检验的座椅才能出厂,确保产品质量和乘客的安全。
这就是汽车座椅的制造工艺流程,通过严格的设计、材料选择、
生产制造和质量控制,汽车座椅才能保证品质和舒适度,为乘客带来良好的乘坐体验。
汽车座椅总成生产工艺
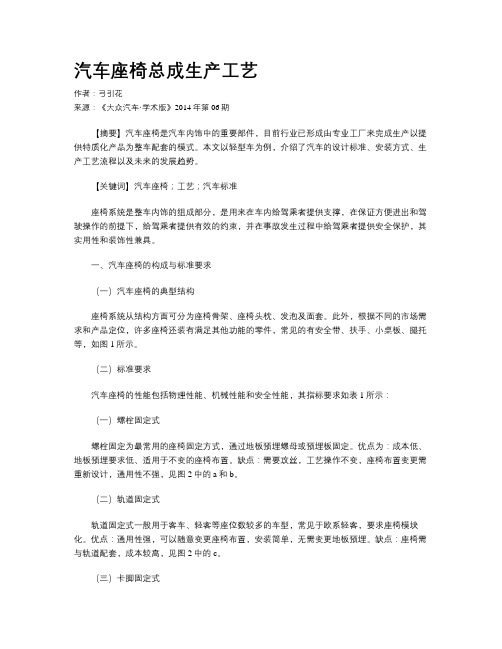
汽车座椅总成生产工艺作者:弓引花来源:《大众汽车·学术版》2014年第06期【摘要】汽车座椅是汽车内饰中的重要部件,目前行业已形成由专业工厂来完成生产以提供特质化产品为整车配套的模式。
本文以轻型车为例,介绍了汽车的设计标准、安装方式、生产工艺流程以及未来的发展趋势。
【关键词】汽车座椅;工艺;汽车标准座椅系统是整车内饰的组成部分,是用来在车内给驾乘者提供支撑,在保证方便进出和驾驶操作的前提下,给驾乘者提供有效的约束,并在事故发生过程中给驾乘者提供安全保护,其实用性和装饰性兼具。
一、汽车座椅的构成与标准要求(一)汽车座椅的典型结构座椅系统从结构方面可分为座椅骨架、座椅头枕、发泡及面套。
此外,根据不同的市场需求和产品定位,许多座椅还装有满足其他功能的零件,常见的有安全带、扶手、小桌板、腿托等,如图1所示。
(二)标准要求汽车座椅的性能包括物理性能、机械性能和安全性能,其指标要求如表1所示:(一)螺栓固定式螺栓固定为最常用的座椅固定方式,通过地板预埋螺母或预埋板固定。
优点为:成本低、地板预埋要求低、适用于不变的座椅布置。
缺点:需要攻丝,工艺操作不变,座椅布置变更需重新设计,通用性不强,见图2中的a和b。
(二)轨道固定式轨道固定式一般用于客车、轻客等座位数较多的车型,常见于欧系轻客,要求座椅模块化。
优点:通用性强,可以随意变更座椅布置,安装简单,无需变更地板预埋。
缺点:座椅需与轨道配套,成本较高,见图2中的c。
(三)卡脚固定式卡脚固定用于MPV、SUV等需要车内空间变换的车型。
座椅可以根据需求折叠、去除。
优点:通过卡扣固定座椅,灵活性高,可自行拆除座椅、安装座椅,不需借助工具。
缺点:座椅结构较多,卡扣强度较高,成本高,见图2中的d。
三、座椅的生产设备、模具及生产工艺(一)生产设备座椅总成需要的生产设备主要有焊接设备、液压机、缝纫设备、发泡设备、涂装设备等。
(二)模具模具按照材质可分为金属模具和树脂模具。
汽车座椅工艺流程
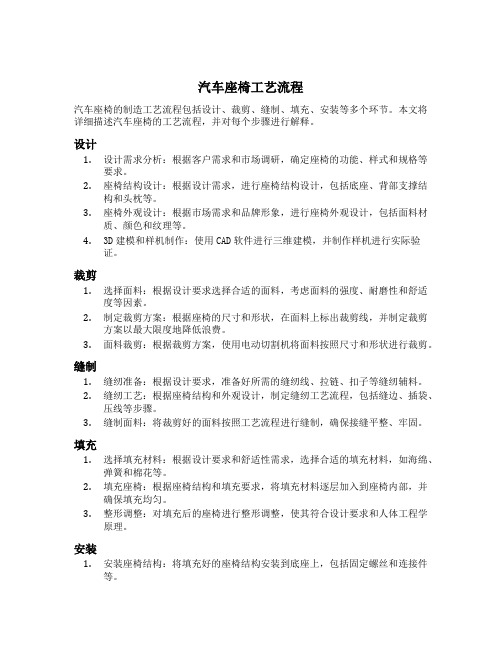
汽车座椅工艺流程汽车座椅的制造工艺流程包括设计、裁剪、缝制、填充、安装等多个环节。
本文将详细描述汽车座椅的工艺流程,并对每个步骤进行解释。
设计1.设计需求分析:根据客户需求和市场调研,确定座椅的功能、样式和规格等要求。
2.座椅结构设计:根据设计需求,进行座椅结构设计,包括底座、背部支撑结构和头枕等。
3.座椅外观设计:根据市场需求和品牌形象,进行座椅外观设计,包括面料材质、颜色和纹理等。
4.3D建模和样机制作:使用CAD软件进行三维建模,并制作样机进行实际验证。
裁剪1.选择面料:根据设计要求选择合适的面料,考虑面料的强度、耐磨性和舒适度等因素。
2.制定裁剪方案:根据座椅的尺寸和形状,在面料上标出裁剪线,并制定裁剪方案以最大限度地降低浪费。
3.面料裁剪:根据裁剪方案,使用电动切割机将面料按照尺寸和形状进行裁剪。
缝制1.缝纫准备:根据设计要求,准备好所需的缝纫线、拉链、扣子等缝纫辅料。
2.缝纫工艺:根据座椅结构和外观设计,制定缝纫工艺流程,包括缝边、插袋、压线等步骤。
3.缝制面料:将裁剪好的面料按照工艺流程进行缝制,确保接缝平整、牢固。
填充1.选择填充材料:根据设计要求和舒适性需求,选择合适的填充材料,如海绵、弹簧和棉花等。
2.填充座椅:根据座椅结构和填充要求,将填充材料逐层加入到座椅内部,并确保填充均匀。
3.整形调整:对填充后的座椅进行整形调整,使其符合设计要求和人体工程学原理。
安装1.安装座椅结构:将填充好的座椅结构安装到底座上,包括固定螺丝和连接件等。
2.安装面料:将缝制好的面料覆盖在座椅结构上,并使用夹子、针线等工具进行固定。
3.安装配件:根据设计要求,安装头枕、扶手和调节装置等配件。
4.质检和调试:对安装完成的座椅进行质量检查和功能调试,确保符合设计要求和产品标准。
包装1.清洁和整理:对座椅进行清洁和整理,去除污渍、折痕等,并确保外观完好。
2.包装材料准备:准备好适合的包装材料,如塑料薄膜、泡沫板和纸箱等。
汽车座椅制造工艺简介PPT课件

2.管焊工艺-焊接( CO2保护焊)
要获得性能优良的焊缝,必须设法保护焊接区,防止空气中的有害气体侵入 , CO2是一种比较稳 定的气体, 因此CO2保护焊就是我们常用的焊接方法,一般情况下,焊接过程的电流为90±10A, 气体流量12-18L/min,电压20±5V,根据员工的熟练程度,焊枪的行走速度可适当调大焊接电流。
翻边:是沿外形曲线周围将翻成侧 立短边的一种冲压工序。
2、管焊工艺
8
2、管焊工艺-弯管
①取件送料
②切割下料
③缩管
④弯管
⑤整形
⑥焊接
① ②:从长度一定的管材中取钢管放入切割机的料槽中(如下图),有人工送料和自动送料,下 料长度公差要求在±0.5mm 之内;
9
2、管焊工艺-弯管 ③缩管:缩管的目的是便于接口的装配和连接,增加焊接后的强度,缩管的长度一 般为14±1mm,如下图所示:
32
⑷裁剪:在整片面料上裁剪出座椅面套所需要的不同形状的片件的过程。一般分为:手工裁剪和 自动裁剪。手工裁剪用电剪刀完成,而自动裁剪采用自动裁剪机完成。 注:裁剪过程,上下层必须对整齐,上下层片件尺偏差在±2mm以内;
自动裁剪
裁剪后的片件 33
⑤面罩缝制:此过程为片件缝制,将裁剪后的各种形状的片件按照尺寸要求缝合起来的过程。 注:1、剪口偏差≤5mm;2、缝边8mm,公差±1mm;3、面料针距10mm内2.5-3针;4、 起至回针长度≤10mm;5、内重逢补针50mm≤长度≤70mm。
修边后 修补后
5、缝纫工艺
31
⑴打版
⑵面料开卷
⑶铺布
⑷裁剪
⑴打版:针对座椅的尺寸定义,对所需要包装 面套的位置分片划分区域,每一个片件的尺寸 做模型的过程。(如右图1)
汽车座椅生产工艺

汽车座椅生产工艺
汽车座椅作为汽车重要的组成部分,其生产工艺也越来越讲究。
以下是汽车座椅的一般生产工艺:
1.设计与开发:根据汽车厂商的要求以及市场需求,汽车座椅
制造商进行座椅的设计与开发。
这包括确定座椅的外形、内部结构、材料选择等。
2.材料准备:根据设计要求,采购合适的座椅材料,如皮革、
织物、海绵等。
材料需要通过质量检测,并进行切割、处理等工艺。
3.座椅骨架制造:座椅骨架由金属或者塑料制成,根据设计要
求进行加工和焊接。
骨架需要经过表面处理,如喷涂或电镀,以提高骨架的耐用性和美观度。
4.座椅海绵制作:根据设计要求,把座椅的内部填充材料进行
切割和缝制,使其符合座椅外形,并且具有良好的支撑和舒适性。
5.面料缝制:将座椅外部面料进行切割和缝制,根据设计要求
进行加工,如装饰线的缝制、椅套的安装等。
同时,还要对面料进行检查,确保质量和规格的一致性。
6.装配和调试:根据座椅的构造,对各个部件进行装配和连接。
在装配过程中,要进行仔细的检查和调试,确保座椅的稳定性和功能的正常运行。
7.品质检验:对座椅进行全面的品质检验,包括外观检查、功能检测、安全性能检测等。
合格的座椅需要标识和包装,准备出货。
8.售后服务:汽车座椅厂商也需要提供售后服务,包括座椅安装指导、维修保养等,以确保用户的满意度和座椅的持久性。
以上是汽车座椅生产的一般工艺流程,不同厂商和不同类型的座椅可能会有一些差别。
随着科技的发展和用户需求的变化,汽车座椅的生产工艺也在不断革新和改进,以提供更安全、舒适和个性化的座椅产品。
汽车座椅的生产工艺

汽车座椅的生产工艺汽车座椅的生产工艺汽车座椅生产工艺是指汽车座椅从原材料到最终成品的加工过程。
汽车座椅作为汽车内部重要的功能部件,不仅要具备舒适性,还必须满足安全性和耐久性的要求。
下面将介绍汽车座椅的生产工艺。
一、原材料的选择和准备:汽车座椅的主要原材料有座椅骨架、填充物、面料等。
座椅骨架通常由金属材料制成,填充物可以是聚氨酯海绵或者记忆海绵,面料则通常采用皮革或者布料。
在生产过程中,需要根据座椅的设计要求,选择适当的原材料,并对原材料进行加工和处理,以保证最终产品的质量和性能。
二、骨架制造:座椅的骨架通常由金属材料制成,常用的材料有钢、铝合金等。
制造骨架的工艺包括材料切割、弯曲、焊接、抛光等。
在制造过程中,需要根据座椅的结构和设计要求,将金属材料进行切割和弯曲,然后通过焊接工艺将各个部件连接在一起,并进行抛光处理,以保证骨架的强度和外观。
三、填充物安装:填充物是为了增加座椅的舒适性和支撑力,通常采用聚氨酯海绵或者记忆海绵。
填充物的安装工艺包括剪裁、固定和压缩等。
在填充物安装的过程中,需要根据座椅的形状和设计要求,将填充物进行剪裁成适当的形状,然后固定在骨架上,并进行适当的压缩,以达到舒适和支撑的效果。
四、面料安装:面料是座椅的外表面,可以选择皮革或者布料。
面料的安装工艺包括剪裁、缝制和固定等。
在面料安装的过程中,需要根据座椅的形状和设计要求,将面料进行剪裁成适当的形状,然后通过缝制工艺将各个面料件缝制在一起,并固定在骨架上,以保证面料的平整和紧固度。
五、组装和质检:最后,将座椅的各个部件进行组装,并进行质量检验。
在组装过程中,需要将骨架、填充物和面料等部件进行组合和固定,通过螺栓、焊接或者胶水等工艺进行连接。
质量检验包括外观检查、功能检测和耐久性测试等,以确保座椅符合设计要求和产品标准。
总之,汽车座椅的生产工艺涉及多个环节,包括原材料选择和准备、骨架制造、填充物安装、面料安装、组装和质检等。
每个环节都需要精细的加工和处理,以保证汽车座椅的质量和性能。
汽车座椅的生产工艺
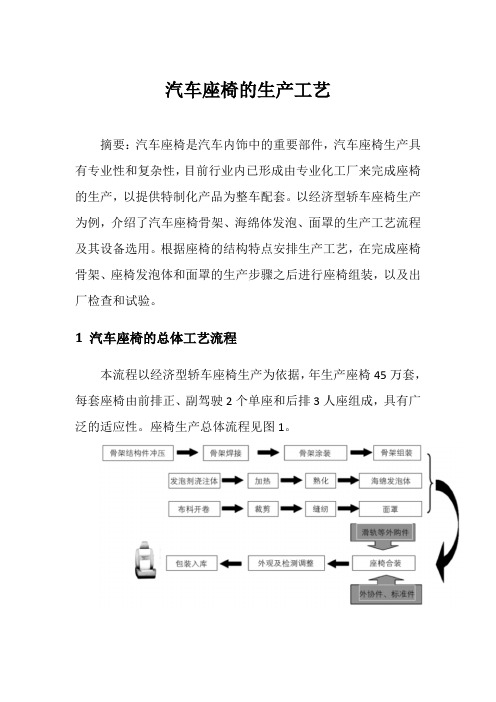
汽车座椅的生产工艺摘要:汽车座椅是汽车内饰中的重要部件,汽车座椅生产具有专业性和复杂性,目前行业内已形成由专业化工厂来完成座椅的生产,以提供特制化产品为整车配套。
以经济型轿车座椅生产为例,介绍了汽车座椅骨架、海绵体发泡、面罩的生产工艺流程及其设备选用。
根据座椅的结构特点安排生产工艺,在完成座椅骨架、座椅发泡体和面罩的生产步骤之后进行座椅组装,以及出厂检查和试验。
1 汽车座椅的总体工艺流程本流程以经济型轿车座椅生产为依据,年生产座椅45万套,每套座椅由前排正、副驾驶2个单座和后排3人座组成,具有广泛的适应性。
座椅生产总体流程见图1。
2 汽车座椅生产流程及设备选用2.1 骨架生产工艺2.1.1 冲压工艺座椅骨架常用轧制型材制成或用钢板焊接而成,并用螺钉直接固定或通过座椅调节机构固定在车身上。
冲压工序主要完成板材、管材的原材料备料,以及板材成形工作。
(1)典型零件的工艺过程板材冲压工艺流程见图2。
卷材冲压工艺流程见图3。
(2)主要工艺设备的选用冷轧钢板选用液压剪板机下料。
钢管采用管材切割机下料,利用压力机压扁端头。
钢丝采用线材切割机下料。
冲压成形采用的7条冲压生产线如下。
a.座盆全自动生产线1条:由4台闭式双点机械压力机、1台自动开卷剪切机、输送装置组成。
主要生产座盆和分体式后靠板。
b.大件冲压生产线1条:主要生产整体式后靠板。
由5台闭式双点机械压力机、1套简易上料装置和3套压力机间输送装置组成。
采用人工上、下料。
c.小件全自动生产线3条:每条线由1台开式双点机械压力机、1套卷料开卷剪切装置和1套步进模具组成。
主要生产形状比较复杂的小型冲压件。
d.其它件冲压生产线2条:其中,1条线由6台2 000~2 500 kN闭式单点机械压力机、1套简易上料装置和5套压力机间输送装置组成。
人工上、下料,主要生产较大冲压件。
另1条线由3台1 600 kN以下闭式单点机械压力机组成。
人工上、下料,主要生产较小冲压件。
汽车座椅生产工艺流程

汽车座椅生产工艺流程一、设计和研发阶段在汽车座椅生产工艺的第一阶段,设计师和工程师们首先进行座椅的设计和研发工作。
他们根据汽车厂商的要求和市场需求,设计出符合人体工程学和舒适性要求的座椅结构和外形。
二、原材料采购在座椅生产的第二阶段,需要进行原材料的采购工作。
座椅的主要原材料包括钢材、泡沫材料、皮革或织物等。
厂商会选择优质的原材料供应商,确保座椅的品质。
三、座椅骨架制作座椅骨架是座椅的基本结构,通常由钢材制成。
在制作座椅骨架时,首先需要根据设计图纸进行剪裁和弯曲,然后进行焊接和磨光,最后进行喷涂等表面处理。
四、泡沫垫料制作座椅的垫料主要由泡沫材料制成。
在制作座椅垫料时,首先需要根据设计要求进行剪裁和粘合,然后进行成型和压缩,最后进行修整和质检。
五、座椅面料制作座椅的面料可以选择皮革或织物等材料。
在制作座椅面料时,首先需要进行剪裁和缝制,然后进行填充和压花等加工工艺,最后进行熨烫和质检。
六、座椅装配在座椅装配阶段,将座椅骨架、垫料和面料等组件进行组装。
座椅装配需要进行固定和调整,确保座椅的稳固性和舒适性。
七、质量检测在座椅生产的最后阶段,需要进行质量检测以确保产品的合格性。
质量检测包括外观检查、功能检测和耐久性测试等,以确保座椅符合相关标准和要求。
八、包装和出厂在座椅生产完成后,需要进行包装工作。
根据客户要求和运输方式的不同,座椅可以采用纸箱包装或塑料薄膜包装等。
最后,座椅被打包完毕后,可以出厂交付给汽车厂商或销售商。
总结:汽车座椅生产工艺流程包括设计和研发、原材料采购、座椅骨架制作、泡沫垫料制作、座椅面料制作、座椅装配、质量检测以及包装和出厂等环节。
每个环节都需要严格控制和执行,以确保座椅的质量和性能符合要求。
通过精细的生产工艺流程,汽车座椅得以高效生产和交付,为汽车使用者提供舒适和安全的乘坐体验。
汽车座椅是如何制造的?
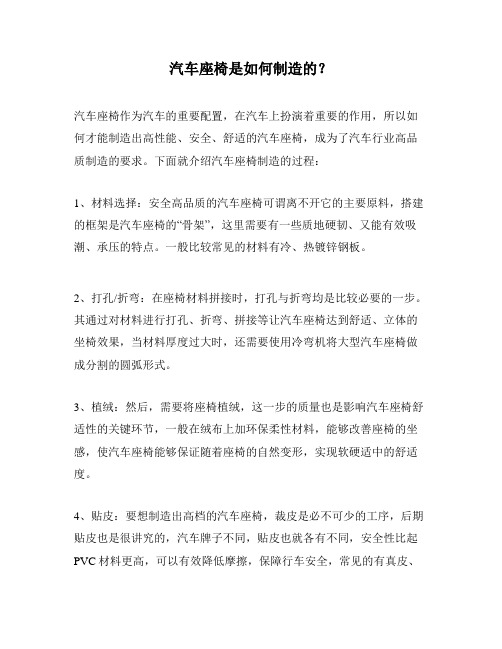
汽车座椅是如何制造的?
汽车座椅作为汽车的重要配置,在汽车上扮演着重要的作用,所以如何才能制造出高性能、安全、舒适的汽车座椅,成为了汽车行业高品质制造的要求。
下面就介绍汽车座椅制造的过程:
1、材料选择:安全高品质的汽车座椅可谓离不开它的主要原料,搭建的框架是汽车座椅的“骨架”,这里需要有一些质地硬韧、又能有效吸潮、承压的特点。
一般比较常见的材料有冷、热镀锌钢板。
2、打孔/折弯:在座椅材料拼接时,打孔与折弯均是比较必要的一步。
其通过对材料进行打孔、折弯、拼接等让汽车座椅达到舒适、立体的坐椅效果,当材料厚度过大时,还需要使用冷弯机将大型汽车座椅做成分割的圆弧形式。
3、植绒:然后,需要将座椅植绒,这一步的质量也是影响汽车座椅舒适性的关键环节,一般在绒布上加环保柔性材料,能够改善座椅的坐感,使汽车座椅能够保证随着座椅的自然变形,实现软硬适中的舒适度。
4、贴皮:要想制造出高档的汽车座椅,裁皮是必不可少的工序,后期贴皮也是很讲究的,汽车牌子不同,贴皮也就各有不同,安全性比起PVC材料更高,可以有效降低摩擦,保障行车安全,常见的有真皮、
PU、PVC等。
5、拉丝:最后一步是拉丝,良好的拉丝能让座椅更实用,细节上也更考究,不同材质的拉丝,做出不同的视觉效果,除了尖角拉丝外,还有打蜡、上蜡的细节处理,让皮革有上层更高的防护效果,从而确保汽车座椅的耐久性与耐磨性。
通过以上介绍,我们能够领略到汽车座椅制造的细致入微,所需精细的流程细节,每一个环节对座椅安全性、舒适性都有着不可磨灭的贡献,从而为汽车行业的发展贡献自身的力量。
轿车座椅生产流程
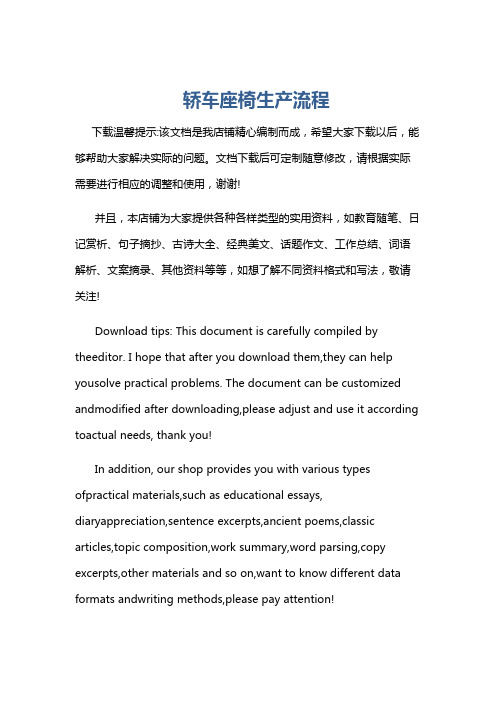
轿车座椅生产流程下载温馨提示:该文档是我店铺精心编制而成,希望大家下载以后,能够帮助大家解决实际的问题。
文档下载后可定制随意修改,请根据实际需要进行相应的调整和使用,谢谢!并且,本店铺为大家提供各种各样类型的实用资料,如教育随笔、日记赏析、句子摘抄、古诗大全、经典美文、话题作文、工作总结、词语解析、文案摘录、其他资料等等,如想了解不同资料格式和写法,敬请关注!Download tips: This document is carefully compiled by theeditor. I hope that after you download them,they can help yousolve practical problems. The document can be customized andmodified after downloading,please adjust and use it according toactual needs, thank you!In addition, our shop provides you with various types ofpractical materials,such as educational essays, diaryappreciation,sentence excerpts,ancient poems,classic articles,topic composition,work summary,word parsing,copy excerpts,other materials and so on,want to know different data formats andwriting methods,please pay attention!轿车座椅生产流程随着汽车的普及,轿车座椅的生产也成为了一个重要的行业。
汽车座椅按摩生产工艺流程
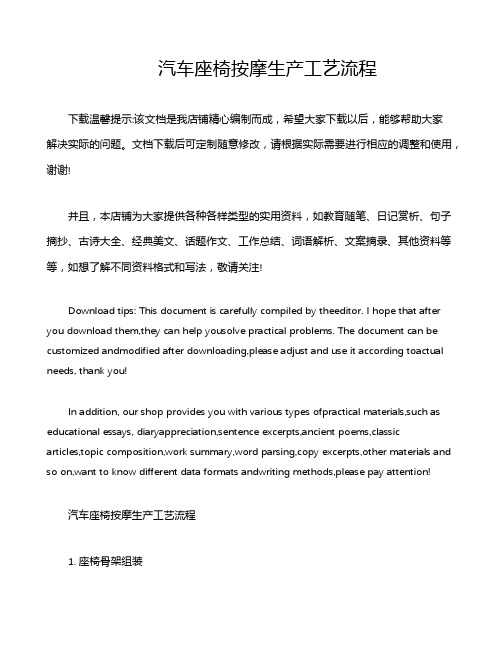
汽车座椅按摩生产工艺流程下载温馨提示:该文档是我店铺精心编制而成,希望大家下载以后,能够帮助大家解决实际的问题。
文档下载后可定制随意修改,请根据实际需要进行相应的调整和使用,谢谢!并且,本店铺为大家提供各种各样类型的实用资料,如教育随笔、日记赏析、句子摘抄、古诗大全、经典美文、话题作文、工作总结、词语解析、文案摘录、其他资料等等,如想了解不同资料格式和写法,敬请关注!Download tips: This document is carefully compiled by theeditor. I hope that after you download them,they can help yousolve practical problems. The document can be customized andmodified after downloading,please adjust and use it according toactual needs, thank you!In addition, our shop provides you with various types ofpractical materials,such as educational essays, diaryappreciation,sentence excerpts,ancient poems,classicarticles,topic composition,work summary,word parsing,copy excerpts,other materials and so on,want to know different data formats andwriting methods,please pay attention!汽车座椅按摩生产工艺流程1. 座椅骨架组装将座椅骨架支架、靠背架、坐垫架等部件组装在一起,形成座椅的基本框架。
汽车座椅生产工艺
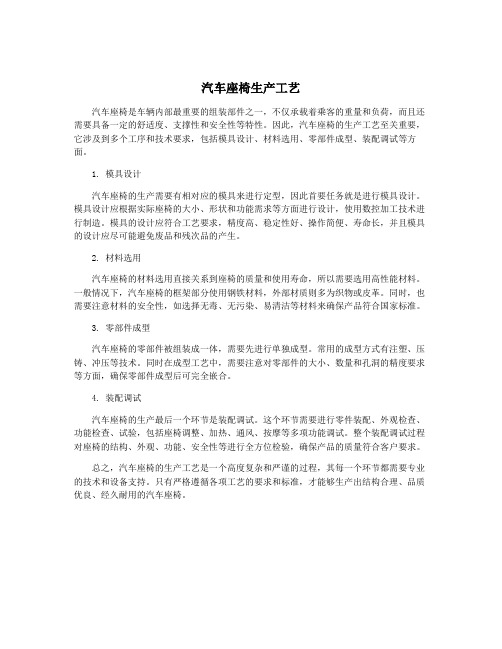
汽车座椅生产工艺汽车座椅是车辆内部最重要的组装部件之一,不仅承载着乘客的重量和负荷,而且还需要具备一定的舒适度、支撑性和安全性等特性。
因此,汽车座椅的生产工艺至关重要,它涉及到多个工序和技术要求,包括模具设计、材料选用、零部件成型、装配调试等方面。
1. 模具设计汽车座椅的生产需要有相对应的模具来进行定型,因此首要任务就是进行模具设计。
模具设计应根据实际座椅的大小、形状和功能需求等方面进行设计,使用数控加工技术进行制造。
模具的设计应符合工艺要求,精度高、稳定性好、操作简便、寿命长,并且模具的设计应尽可能避免废品和残次品的产生。
2. 材料选用汽车座椅的材料选用直接关系到座椅的质量和使用寿命,所以需要选用高性能材料。
一般情况下,汽车座椅的框架部分使用钢铁材料,外部材质则多为织物或皮革。
同时,也需要注意材料的安全性,如选择无毒、无污染、易清洁等材料来确保产品符合国家标准。
3. 零部件成型汽车座椅的零部件被组装成一体,需要先进行单独成型。
常用的成型方式有注塑、压铸、冲压等技术。
同时在成型工艺中,需要注意对零部件的大小、数量和孔洞的精度要求等方面,确保零部件成型后可完全嵌合。
4. 装配调试汽车座椅的生产最后一个环节是装配调试。
这个环节需要进行零件装配、外观检查、功能检查、试验,包括座椅调整、加热、通风、按摩等多项功能调试。
整个装配调试过程对座椅的结构、外观、功能、安全性等进行全方位检验,确保产品的质量符合客户要求。
总之,汽车座椅的生产工艺是一个高度复杂和严谨的过程,其每一个环节都需要专业的技术和设备支持。
只有严格遵循各项工艺的要求和标准,才能够生产出结构合理、品质优良、经久耐用的汽车座椅。
汽车座椅的生产工艺
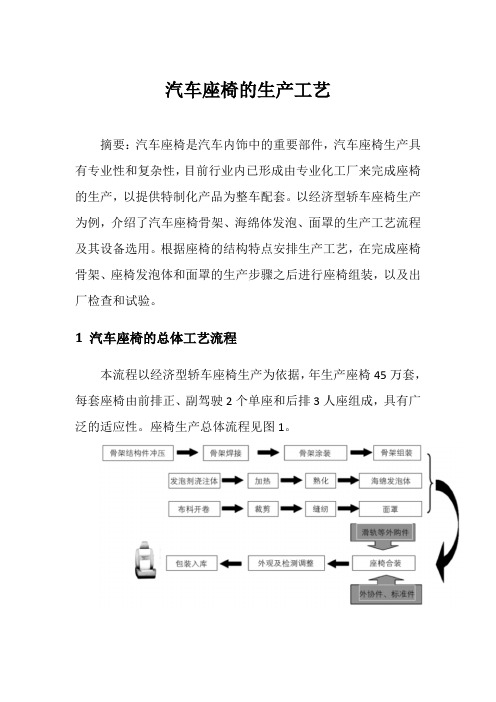
汽车座椅的生产工艺摘要:汽车座椅是汽车内饰中的重要部件,汽车座椅生产具有专业性和复杂性,目前行业内已形成由专业化工厂来完成座椅的生产,以提供特制化产品为整车配套。
以经济型轿车座椅生产为例,介绍了汽车座椅骨架、海绵体发泡、面罩的生产工艺流程及其设备选用。
根据座椅的结构特点安排生产工艺,在完成座椅骨架、座椅发泡体和面罩的生产步骤之后进行座椅组装,以及出厂检查和试验。
1 汽车座椅的总体工艺流程本流程以经济型轿车座椅生产为依据,年生产座椅45万套,每套座椅由前排正、副驾驶2个单座和后排3人座组成,具有广泛的适应性。
座椅生产总体流程见图1。
2 汽车座椅生产流程及设备选用2.1 骨架生产工艺2.1.1 冲压工艺座椅骨架常用轧制型材制成或用钢板焊接而成,并用螺钉直接固定或通过座椅调节机构固定在车身上。
冲压工序主要完成板材、管材的原材料备料,以及板材成形工作。
(1)典型零件的工艺过程板材冲压工艺流程见图2。
卷材冲压工艺流程见图3。
(2)主要工艺设备的选用冷轧钢板选用液压剪板机下料。
钢管采用管材切割机下料,利用压力机压扁端头。
钢丝采用线材切割机下料。
冲压成形采用的7条冲压生产线如下。
a.座盆全自动生产线1条:由4台闭式双点机械压力机、1台自动开卷剪切机、输送装置组成。
主要生产座盆和分体式后靠板。
b.大件冲压生产线1条:主要生产整体式后靠板。
由5台闭式双点机械压力机、1套简易上料装置和3套压力机间输送装置组成。
采用人工上、下料。
c.小件全自动生产线3条:每条线由1台开式双点机械压力机、1套卷料开卷剪切装置和1套步进模具组成。
主要生产形状比较复杂的小型冲压件。
d.其它件冲压生产线2条:其中,1条线由6台2 000~2 500 kN闭式单点机械压力机、1套简易上料装置和5套压力机间输送装置组成。
人工上、下料,主要生产较大冲压件。
另1条线由3台1 600 kN以下闭式单点机械压力机组成。
人工上、下料,主要生产较小冲压件。
- 1、下载文档前请自行甄别文档内容的完整性,平台不提供额外的编辑、内容补充、找答案等附加服务。
- 2、"仅部分预览"的文档,不可在线预览部分如存在完整性等问题,可反馈申请退款(可完整预览的文档不适用该条件!)。
- 3、如文档侵犯您的权益,请联系客服反馈,我们会尽快为您处理(人工客服工作时间:9:00-18:30)。
人工 浇注
机械手 浇注
26
合模方式:合模机合模、轨道合模。
合模机合模
合模机 合模
合模完 毕
合模前
合模后 27
⑸熟化成型:当模温机持续加温,使模腔 内的温度达到45-60℃ 时,持续220-300秒,使发泡熟化成型的 过程。
⑹取件:是把发泡件与模具分离的一个操作过 程。 注:若模腔内有模舌,模具打开后,双手挤压 海绵四周,使海绵与上模分开,然后将海绵与 模舌掀离下模后取出海绵
缝纫机缝制
34
6、总装工艺
35
⑴分装
⑵骨架连接
⑶护板装配
⑷整形熨烫
⑴分装:将焊接完成的骨架分总成 与相应的发泡、面套连接的过程。 (如右图所示)
36
靠背分装
⑵骨架连接:按照结构不同,将座椅滑道、分装完成的坐垫和靠背通过连 接螺栓结合起来的过程。
滑轨连接
坐垫连接 37
⑶护板装配:将座椅上的塑料件(内外护板、塑料手柄、头枕套管等)通过螺钉或卡扣连 接到座椅指定的位置上。 ⑷熨烫整形:对以上装配完成的座椅总成进行外观整形,保证缝线整齐,包覆良好,无褶 皱。
25
⑷浇注:将两种材料不同的A料和B料,或称黑白料,根据产品硬度要求,按一定比列
混合后注入到模具内的一种操作。分人工浇注和机械手浇注。
注:通常的发泡线分干、湿两部分,根据干部的不同分别有:环形线(一般有24工位、
32工位、48工位的较多)、转盘线。根据生产工艺规划的不同,同一条发泡线可布置
1或2个浇注工位。
⑵-⑼工 序,均在喷 淋式前处理 箱中完成, 如右图所示:
19
⑽水份烘干:将工件表面的水分去除,在限定的悬挂链速度,烘箱温度为:120~140℃。 注:工件经过前处理除掉冷轧钢板表面的油污和灰尘后才能喷涂粉末,同时在工件表面形成一层 锌系磷化膜以增强喷粉后的附着力。前处理后的工件必须完全烘干水分并且充分冷却到35℃以下 才能保证喷粉后工件的理化性能和外观质量。
汽车事业部培训教材
座椅制造工艺简介
一、座椅结构简介 二.六大工艺介绍 三. 产品开发与工艺设计的关系
2
一、座椅结构简介
3
座椅结构简介
1、骨架:根据座椅强度要求,中低档座椅骨架一般采用 φ20~φ30的管材、厚度为1mm~2mm的板材,有些高 端座椅为了减轻骨架重量,采用合金材料; 2、头枕:机械式的一般分为两向和四向; 3、靠背:按结构分为钢板结构、S簧结构和钢丝结构。 4、坐垫:按结构分为坐盆结构、S簧结构; 5、蒙皮:分为针织绒布、仿皮、真皮; 6、弹性元件:海绵; 7、调节机构:靠背调节、坐垫调节(前后、上下); 8、装饰件:有左右护板、解锁手柄、靠背后护盖、螺栓 堵盖等(一般为塑料件)。
⑶放钢丝:将型号、数量正确的钢丝件,按照要 求放入模具凹槽的一种操作。钢丝是靠模腔凹槽 中的吸铁和卡簧固定的。 注:若操作者未按要求操作,钢丝件固定不良, 将导致钢丝漂移,造成成品发泡总成中的镶嵌的 钢丝不在规定位置上,偏浅(钢丝受力时脱落或 者凸出发泡表面)或偏深(与面套连接后在座椅 A面出现凹坑。
包括粉末固化工序,均用天然气烘干箱进行加温。如下图所示:
风机 20
燃烧箱
⑾粉末喷涂:静电发生器通过喷枪枪口的电极针向工件方向的空间释放高压静电(负极),该高压静电使 从.喷枪口喷出的粉末和压缩空气的混合物以及电极周围空气电离(带负电荷)。工件经过挂具通过输送 链接地(接地极),这样就在喷枪和工件之间形成一个电场占粉末在电场力和压缩空气压力的双重推动下 到达工件表面,依靠静电吸引在工件表面形成一层均匀的涂层,涂层厚度要求50~70um。
因此,此连接的设计不合理,可采用减少焊点(单边焊接),满焊的连接方式。
41
翻边:是沿外形曲线周围将翻成侧 立短边的一种冲压工序。
2、管焊工艺
8
2、管焊工艺-弯管
①取件送料
②切割下料
③缩管
④弯管
⑤整形
⑥焊接
① ②:从长度一定的管材中取钢管放入切割机的料槽中(如下图),有人工送料和自动送料,下 料长度公差要求在±0.5mm 之内;
9
2、管焊工艺-弯管 ③缩管:缩管的目的是便于接口的装配和连接,增加焊接后的强度,缩管的长度一 般为14±1mm,如下图所示:
16
3、涂装工艺
17
3.涂装工艺-工序介绍
⑴上件
⑵预脱脂
⑶脱脂
⑷水洗1 ⑸水洗2
⑹表调
⑺磷化
⒀下挂
⑿粉末固化
⑾粉末喷涂
⑽水份烘干
⑼水洗4
⑻水洗3
⑴上件:根据零件尺寸选择挂具类型及挂具间距,按照流水线喷涂的座椅零部件,一般挂具 的间距为400mm和右。
18
⑵预脱脂、 ⑶脱脂:预脱脂指把零件表面的杂质、油污去除,一般能除去表面80%-90%的杂质和油污, 经过脱脂工序后基本能清洁零件表面。 ⑷水洗1、 ⑸水洗2:经过两次水洗,基本可将附着于工件表面的脱脂液 、颗粒去除干净。 ⑹表调:对工件表面进行活化,调节PH值,保证总碱度在1.5-4.0内。 ⑺磷化:调节磷化槽的PH值呈酸性,保证工件表面均匀、细小、致密,无黄锈缺陷 ,增强其表面附着力。 ⑻水洗3、⑼水洗4:去除工件表面的磷化残渣、磷化夜和杂质,保证清洁。
10
2、管焊工艺-弯管 1、工件的弯管长度(包括每一段的管件),误差不得超过0.5mm;2、角度误差在±2度;3、总成 件的平面度误差不能超过1mm。 注:1.对于靠背钢管和座垫钢管总成,须有整形工序,以保证工件总成的平面度,否则,将导致骨架 总成的装配困难,并造成前排靠背恢复力小(或后靠背解锁不同步);2.弯管过程中,根据弯曲角度 对角度进行补偿也是很重要的,钢管自身有一定的回弹力,在完成弯管后,比较容易回弹,造成骨 架总成的开档尺寸超差,很可能对座椅滑道造成影响,致使滑动发涩。
采用手动喷枪 进行局部喷涂, 喷涂面为锁盒 及靠背下横杆 左右外露端 (化圈处)
工作人员正在用手动喷枪喷 涂。喷枪距离:150-300mm
21
采用自动喷 枪进行全面 喷涂,对支 脚折页喷涂 死角部位在 粉末固化后 采用补漆处 理
⑿粉末固化:固化时工件在烘干箱中约20min,温度为190±5℃ ,待温度冷却后,便完成 了整个喷涂过程。 注:1、在喷涂前,若考虑管材的除锈,须增加酸洗或者抛丸工序,以除去管材上的黄锈, 增加粉末喷涂后的附着力;2、喷粉后的工件,须保证色泽均匀,无明显色差,满足涂膜中 性盐雾试验≥96h。
冲孔( punching ):是将废料沿封闭 轮廓从材料或工序件上分离的一种冲压工 序,在材料或工件上获得需要的孔。
穿孔(piercing):是将废料从材料或 工序件上分离的一种冲压工序,在成形后 的材料或工件上获得需要的孔。
成形(forming):是将落料或冲孔 后的工序件,改变工序件形状和尺寸, 获得所需要形状的一种冲压工序。
28
⑺破泡:是指将熟化成型后的发泡内的空气 通过一定的挤压进行排气的过程。分真空破 泡和机械破泡(必要时人工破泡)。 注:1.海绵从模具中取出后,停留时间不能 过长,应控制在60秒内进行破泡。2.机械破 泡时,压棉厚度为40mm,因此,若海绵中 如有包裹空心金属件、嵌件多且复杂或者海 绵底部装有弹簧之类的金属件,必须使用真 空破泡。
吹气清理 24
⑷浇注 ⑸熟化成型
铲废料
⑵喷脱模剂:脱模剂是一种具有润滑性质的液体辅 助材料,均匀喷涂在模具上,待发泡成形熟化后, 能较容易地将发泡总成和模具分离。 注:根据不同的模具形状,将脱模剂均匀地喷涂到 模腔内(一般会制定喷涂轨迹),调节喷枪使脱模 剂呈雾化状态,喷枪压力在1-2Kg,喷枪距离模具 距离在20-30cm范围内。
32
⑷裁剪:在整片面料上裁剪出座椅面套所需要的不同形状的片件的过程。一般分为:手工裁剪和 自动裁剪。手工裁剪用电剪刀完成,而自动裁剪采用自动裁剪机完成。 注:裁剪过程,上下层必须对整齐,上下层片件尺偏差在±2mm以内;
自动裁剪
裁剪后的片件 33
⑤面罩缝制:此过程为片件缝制,将裁剪后的各种形状的片件按照尺寸要求缝合起来的过程。 注:1、剪口偏差≤5mm;2、缝边8mm,公差±1mm;3、面料针距10mm内2.5-3针;4、 起至回针长度≤10mm;5、内重逢补针50mm≤长度≤70mm。
修边后 修补后
5、缝纫工艺
31
⑴打版
⑵面料开卷
⑶铺布
⑷裁剪
⑴打版:针对座椅的尺寸定义,对所需要包装 面套的位置分片划分区域,每一个片件的尺寸 做模型的过程。(如右图1)
⑵面料开卷、 ⑶铺布:将成卷包装的面料开 卷的过程。方向正面朝上,一般面料的层数 为≤30.(如图2、3)
⑤面罩缝制
图1
图2
图3
手工焊接
机器人焊接
15
2.管焊工艺-焊接(凸焊)
优点:凸焊点的位置比点焊焊点的位置更精确,而且由于凸点大小均匀,所以凸焊焊点的质量更为 稳定; 缺点:在用同一电极同时焊数个焊点时,工件的对准和凸点的尺寸(尤其时高度)必须保持高精度 公差 。
如右图: 将件②放到件 ①上, 凸焊后成为总成件 ③
1
③
2
护板装配
熨烫整形 38
三. 产品开发与工艺设计的关系
39
产品设计与工艺设计: 在满足法规要求的基础上,须保证工艺可行性和质量一致性。
40
举例:汽车前座椅防下潜结构设计。 此设计装车可通过强度试验,但是,制作工艺要求的对称焊接无法实现,并且经常出现内支撑
钢管与防下潜焊接点脱焊。 分析: 1、工艺设计不合理:由于防下潜半坐盆骨架内侧空间较小,常用的焊枪和机械手无操作空间,可 行性较低,并且影响效率; 2、质量一致性较差:虽然内外8个焊点,在焊接合格的情况下,能满足强度要求,但是由于防下 潜坐盆材料厚度仅为1.5mm,若焊接熔深不够,容易造成脱焊,若熔深较强,则容易焊穿。
11