舞钢4100mm宽厚板生产线双边剪退刀拉杆断裂原因分析
钢板剪切边开裂原因分析及改进剪切质量的措施
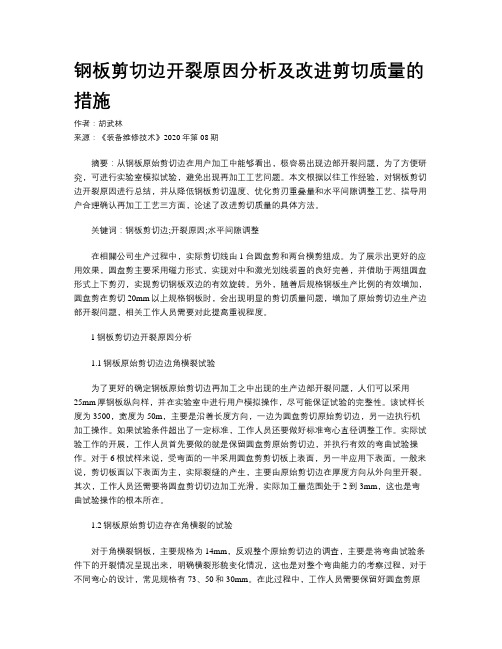
钢板剪切边开裂原因分析及改进剪切质量的措施作者:胡武林来源:《装备维修技术》2020年第08期摘要:从钢板原始剪切边在用户加工中能够看出,极容易出现边部开裂问题,为了方便研究,可进行实验室模拟试验,避免出现再加工工艺问题。
本文根据以往工作经验,对钢板剪切边开裂原因进行总结,并从降低钢板剪切温度、优化剪刃重叠量和水平间隙调整工艺、指导用户合理确认再加工工艺三方面,论述了改进剪切质量的具体方法。
关键词:钢板剪切边;开裂原因;水平间隙调整在相關公司生产过程中,实际剪切线由1台圆盘剪和两台横剪组成。
为了展示出更好的应用效果,圆盘剪主要采用磁力形式,实现对中和激光划线装置的良好完善,并借助于两组圆盘形式上下剪刃,实现剪切钢板双边的有效旋转。
另外,随着后规格钢板生产比例的有效增加,圆盘剪在剪切20mm以上规格钢板时,会出现明显的剪切质量问题,增加了原始剪切边生产边部开裂问题,相关工作人员需要对此提高重视程度。
1钢板剪切边开裂原因分析1.1钢板原始剪切边边角横裂试验为了更好的确定钢板原始剪切边再加工之中出现的生产边部开裂问题,人们可以采用25mm厚钢板纵向样,并在实验室中进行用户模拟操作,尽可能保证试验的完整性。
该试样长度为3500,宽度为50m,主要是沿着长度方向,一边为圆盘剪切原始剪切边,另一边执行机加工操作。
如果试验条件超出了一定标准,工作人员还要做好标准弯心直径调整工作。
实际试验工作的开展,工作人员首先要做的就是保留圆盘剪原始剪切边,并执行有效的弯曲试验操作。
对于6根试样来说,受弯面的一半采用圆盘剪剪切板上表面,另一半应用下表面。
一般来说,剪切板面以下表面为主,实际裂缝的产生,主要由原始剪切边在厚度方向从外向里开裂。
其次,工作人员还需要将圆盘剪切切边加工光滑,实际加工量范围处于2到3mm,这也是弯曲试验操作的根本所在。
1.2钢板原始剪切边存在角横裂的试验对于角横裂钢板,主要规格为14mm,反观整个原始剪切边的调查,主要是将弯曲试验条件下的开裂情况呈现出来,明确横裂形貌变化情况,这也是对整个弯曲能力的考察过程,对于不同弯心的设计,常见规格有73、50和30mm。
双边剪碎边剪高频故障分析

边剪 、 碎 料导 板 、 碎料 溜槽 、 碎边 剪剪 刃装 配 、 碎边 剪 间 隙调整 组 成 。其 结 构示 意如 图 1 所 示 。碎边 剪 刀
架 在刀座 内上下 滑动 实现边 料 的剪切 。刀座通 过安 装在 刀座 上 的偏 心轴 实现剪 刃 间隙 的单独 调整 。上
下剪 盒 固定通 过单 向液压锁 紧缸 , 碟 簧锁 紧 , 液 压 打 开, 实现快 装 快卸 。
发 生变 化 。当侧 向间 隙 由零 逐 渐增 大 时 , 受 力 状 况 由压缩一 剪切 一 弯 曲等状 态 依 次 发 生 , 侧 向间 隙 过
凹坑位置 , 薄规格 、 抗 弯能力 差的碎边就会 向下弯 曲, 造成 卡钢 。
2 ) 碎边剪 剪盒 装 配下 剪 刃 护板 磨 损 , 更 换 新 剪 刃后 , 产 生 台阶 , 造 成卡 钢 。 由于从 主板 上剪 切下 的 碎 边边 部锋利 , 在剪切后 , 碎 边 受剪 切 力 产 生 扭转 , 锋 利棱 角对 下剪 刃及剪 刃 护板长 期划擦 , 产 生沟槽 , 护 板更 换不及 时 , 更换 新剪 刃或剪 盒后 , 下剪 刃上 表 面高 于护板 , 也会 造成 卡钢 。 3 ) 碎 料 溜槽导 板 与剪 体 固定 方式 为螺 栓 固定 , 造 成导 板与 机 架 之 间 有 间 隙 , 碎边扭转 7 0 。 或 碎 边 尺寸小 的碎 边就 会插 入 缝 隙 , 造 成 剪 断 后 的碎 边 在 溜槽 位 置聚集 叠加 , 造 成碎料 溜槽 卡钢 。 4 ) 剪切 过程 中 由于碎 料 导 板用 于碎 料 输 送 , 在 主剪 刃剪切 时 , 碎料导 板跟 随剪 切过程 缓 冲下降 , 当 主上剪 刃 向上滚 动 时 , 碟 簧 弹力 不 足 以将 切 下 的碎 边 及导 板恢 复 到 正常 输 送 高 度 。造 成碎 边 向下 折 ,
双边剪退刀机构优化改造

双边 剪是 宽厚 板生 产线 的主要 剪切 设备 , 对 钢 板进行 宽度 剪切 。 其 中 的退
刀 机构 属于 双边 剪 的核心 部件 之一 , 出现故 障会 造成 导梁不 能 定位 、 剪 刃间 隙
无 法调整 而致使 精整 线停产 。 同样 使生 产无法 继续进 行 。 因此 , 提 高双边 剪退 刀
O麓 育
两个 剪机 同时切 边 时 , 由于水 平分 力作用 使 钢板被 夹紧 在两剪 刃之 间 , 为 了防止 将钢 板刮 伤或在 上剪 刃 向上 回程 时 带起钢 板 , 在每 次 剪切 完成 后 , 上 剪
刃将 从被剪 切钢板 的边缘 后退.  ̄2 mm, 并在 向下 行程开 始之前 又恢复到 原来 的
滚切剪是装有半径为R的弧形上剪刃的上刀架, 在具有不同相位角和偏心 半径的两个曲轴及连杆的带动下, 并在控制杆的约束下, 上剪刃沿一个水平基
面 实现理 想 的滚动 运动 中 , 将钢 板 的两边 剪 断。 水 平基 准面 比下 剪 刃的刃 口一 般 低5 mm, 即剪切 时 的重 合量 , 在 剪 切过 程 中 , 该值 保持 不变 。
( 2 所 除 减速机 底部 稀油 润 滑 回油管 , 回拉 缸油 管及 减速 机上 盖 的机上 油 管。
行位置调整。 双边剪后部与剖分剪相接 , 两台剪机构成组合剪。
2 . 技 术 特点
( 3 用现场有限空间对回拉缸进行合理吊挂后 , 拆除回拉缸缸头端销轴 , 将回拉缸旋转一定角度放在后横粱上 。
机 构的 设备 稳定 对 生产起 着 重要 的作 用 。 1工 艺流 程
剪 切位 置 。 驱动切 边 剪剪 刃的两 个 曲轴 的后端 分别 装有控 制 凸轮 , 通过 凸 轮和 连杆 机 构让上 刀 架摆 开一 定 的距 离 。 切边剪 上剪 刃安 装在 上剪刃 盒 中, 由螺 栓固定 , 上剪 刃盒和上 刀架 通过6 锁
关于中速磨煤机拉杆断裂分析及处理措施

Analysis and Treatment Measures for the Fracture of the Pull Rod ofthe Medium Speed Coal MillDing Haifeng(Guangxi Guangtou Guixu Energy Development Investment Co., Ltd., Hezhou, Guangxi 542800, CHN)【Abstract】From March 2021 to May 2022, 5 hydraulic rod fractures occurred in 10 medium speed coal mills of a certain factory, seriously affecting the unit load. Technical personnel ana⁃lyzed the material, appearance, and operation mode, and finally confirmed the solution. The rod fracture problem was solved. This article briefly explains the analysis situation, processing process, and other aspects for reference and reference by various units.Key words:coal mill;pull rod;fracture;analysis1中速磨煤机设备概况某厂采用的是北方重工生产的MP200G中速辊式磨煤机,其碾磨部分是由转动的磨环和3个沿磨环滚动的固定且可自转的磨辊组成[1]。
3个磨辊在磨盘滚道上是沿着圆周方向均布的,液压加载系统产生碾磨力,通过这个3点系统,3个磨辊上产生匀称的碾磨力量,这个力经过磨环至磨辊,再由压架至拉杆和传动盘、减速机、液压缸,最后通过底板传至基础。
双边剪卡钢原因分析与改进

山西冶金SHANXI METALLURGY Total 175No.5,2018DOI:10.16525/14-1167/tf.2018.05.35总第175期2018年第5期双边剪卡钢原因分析与改进魏和平(山钢股份莱芜分公司宽厚板事业部,山东莱芜271104)摘要:针对双边剪剪切过程中卡钢的主要原因进行了分析,通过双边剪剪切控制工艺的研究改进及剪切设备的改造等措施,双边剪卡钢问题基本解决,双边剪故障停机时间显著降低。
关键词:卡钢碎料导板碎料溜槽运输链中图分类号:TG333.21文献标识码:A文章编号:1672-1152(2018)05-0086-03收稿日期:2018-05-21作者简介:魏和平(1971—),男,1993年毕业于山东省冶金工业学校轧钢专业,学士学位,工程师,现在山钢股份莱芜分公司宽厚板事业部从事轧钢生产工艺技术研究工作。
双边剪是精整区域的关键设备之一,它的功能是修剪钢板纵向边的两边,以达到最终要求的钢板宽度。
为了使废料长度达到要求的尺寸,以便落到剪体下面的废料输送机上输送到废料坑,钢板两边的修剪废料也由位于主剪刃之后并与主剪刃一道驱动的废料刀刃组进行剪切,但有时碎边不能到达碎断剪或切断后不能顺利地运送到碎料筐,而是卡在碎料导板、碎料溜槽或碎料运输链上造成卡钢。
针对双边剪区域碎边卡钢问题进行分析研究,从程序控制及设备结构改造等方面制定相应的改进措施,使双边剪卡钢问题得到有效解决,是生产顺行、产能提升的根本途径。
1双边剪卡钢原因分析初期设计是双边剪剪切时碎料导板始终处于前进位,靠近下剪台侧面,当剪切钢板废边最后一刀时碎料导板才离开下剪台,以便于最后一刀碎边直接掉落到碎料溜槽。
但是有时钢板的实际长度与二级面显示长度不一致,倒数第二刀输送长度调整不到最佳值,最后一刀碎料长度可能会大于剪刃长度,这时碎料导板还没有离开下剪台,则碎料留在导板上,造成碎料导板卡钢。
碎料溜槽卡钢主要原因为短碎边卡在溜槽两侧,造成溜槽堵塞后多支碎边卡在溜槽。
宽厚板轧机工作辊断裂原因分析及对策
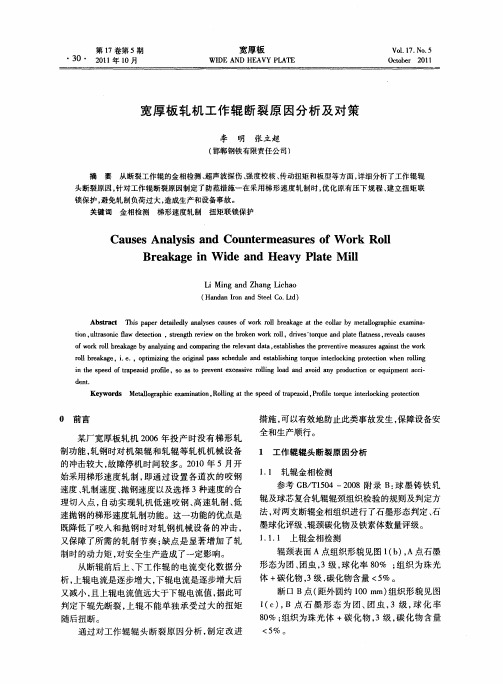
从过 程计算 机 记 录 的速 度趋 势 发 现 , 轧 制 在 过程 中 咬钢瞬 间上下辊 速差 达到 7 5rmn 远远 . / i, 超过偏 差 1rmn正 常水平 , 辊辊 速 瞬 间降低 , / i 上 导致 下辊 承担扭 矩 瞬 间增 大 , 下 辊首 先 断 裂 的 是 重要原 因。经查 前一道 次咬入 和抛 出时分 别产 生 了 24 / n和 34 / i .7rmi .8rrn的速 度差 , a 同时 实物
L n n h n ih o iMig a d Z a g L e a
f n a o n t l o L ) dnI nadS e C . t Ha r e d
Ab ta l T i p p rd ti d y a ay e a s s o o k rl b e k g tt e c  ̄ r b t l g a h c e a n - s r c h s a e ea l l n ls s e H e f w r o r a a e a h o a y meal r p i x mi a e l o t n, lrs nc f w d tci n ,s e g h rve o h r k n wo k r l,di e o q e a d p ae f t e s rv asc u e i u t o i a ee t o a l o t n t iw n t e b o e r l r s tr u n l t an s ,e e l a s s r e o v l o o k r l b a a e b n lzn n o ai g t er lv t aa, s b ih ste p e e t eme s r sa a n t h o k fw r o r k g y a ay i g a d c mp r ee a t e t l e r v ni a ue g i s t e w r l e n h n d a s h v r l b a a e,i e ,o t zn h r i a a ss h d l n sa l h n o q e it r c i g p oe t n w e l n o r k g e . . p i ig t e o i n p s c e u e a d e t i ig t r u n e l kn r tci h n r l g mi g l b s o o o i i h p e ft p z i rf e,S s t r v n x e s e r l n o d a d a od a y p o u t n o q i me ta c — ntes e do a eodpo l r i O a o p e te c s i ol g la n v i n r d c i re u p n c i e v i o
双边剪钢板跑偏问题的控制
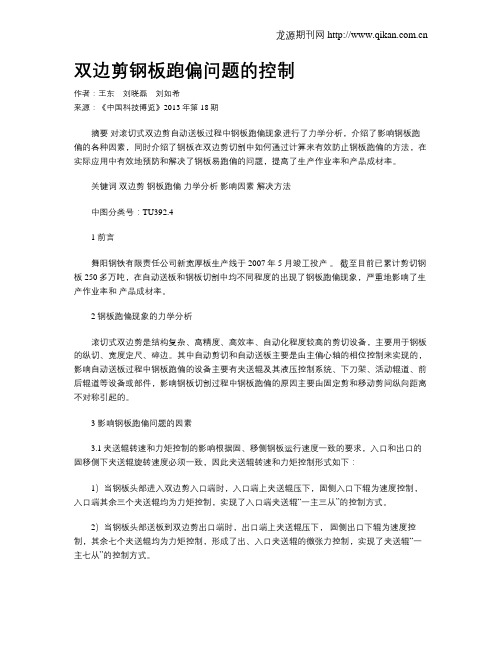
双边剪钢板跑偏问题的控制作者:王东刘晓磊刘如希来源:《中国科技博览》2013年第18期摘要对滚切式双边剪自动送板过程中钢板跑偏现象进行了力学分析,介绍了影响钢板跑偏的各种因素,同时介绍了钢板在双边剪切割中如何通过计算来有效防止钢板跑偏的方法,在实际应用中有效地预防和解决了钢板易跑偏的问题,提高了生产作业率和产品成材率。
关键词双边剪钢板跑偏力学分析影响因素解决方法中图分类号:TU392.41 前言舞阳钢铁有限责任公司新宽厚板生产线于2007年5 月竣工投产。
截至目前已累计剪切钢板250多万吨,在自动送板和钢板切割中均不同程度的出现了钢板跑偏现象,严重地影响了生产作业率和产品成材率。
2 钢板跑偏现象的力学分析滚切式双边剪是结构复杂、高精度、高效率、自动化程度较高的剪切设备,主要用于钢板的纵切、宽度定尺、碎边。
其中自动剪切和自动送板主要是由主偏心轴的相位控制来实现的,影响自动送板过程中钢板跑偏的设备主要有夹送辊及其液压控制系统、下刀架、活动辊道、前后辊道等设备或部件,影响钢板切割过程中钢板跑偏的原因主要由固定剪和移动剪间纵向距离不对称引起的。
3 影响钢板跑偏问题的因素3.1夹送辊转速和力矩控制的影响根据固、移侧钢板运行速度一致的要求,入口和出口的固移侧下夹送辊旋转速度必须一致,因此夹送辊转速和力矩控制形式如下:1)当钢板头部进入双边剪入口端时,入口端上夹送辊压下,固侧入口下辊为速度控制,入口端其余三个夹送辊均为力矩控制,实现了入口端夹送辊“一主三从”的控制方式。
2)当钢板头部送板到双边剪出口端时,出口端上夹送辊压下,固侧出口下辊为速度控制,其余七个夹送辊均为力矩控制,形成了出、入口夹送辊的微张力控制,实现了夹送辊“一主七从”的控制方式。
3)当钢板尾部离开双边剪入口端时,入口端上夹送辊抬起,固侧出口下辊为速度控制,出口端其余三个夹送辊均为力矩控制,实现了出口端夹送辊的“一主三从”的控制方式。
2 夹送辊液压系统压力和流量的影响自动送板的钢板拖动力主要决定于液压系统的压力,要保证钢板不跑偏,必须确保固、移侧入出口夹送辊液压系统的压力尽量保持相等。
钢板剪切边开裂原因分析
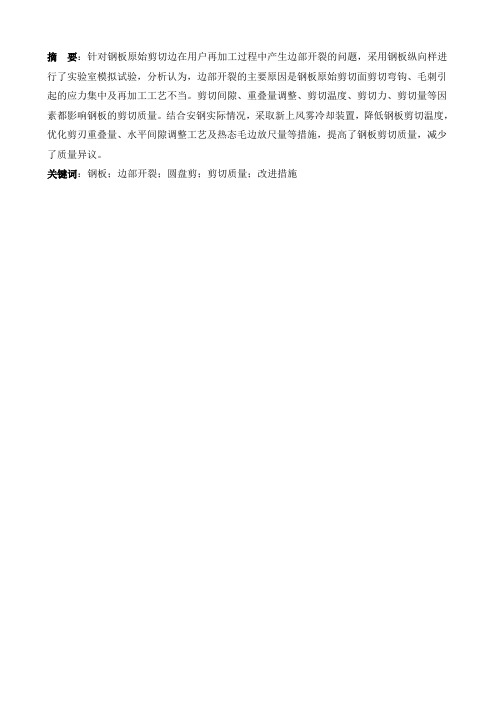
摘要:针对钢板原始剪切边在用户再加工过程中产生边部开裂的问题,采用钢板纵向样进行了实验室模拟试验,分析认为,边部开裂的主要原因是钢板原始剪切面剪切弯钩、毛刺引起的应力集中及再加工工艺不当。
剪切间隙、重叠量调整、剪切温度、剪切力、剪切量等因素都影响钢板的剪切质量。
结合安钢实际情况,采取新上风雾冷却装置,降低钢板剪切温度,优化剪刃重叠量、水平间隙调整工艺及热态毛边放尺量等措施,提高了钢板剪切质量,减少了质量异议。
关键词:钢板;边部开裂;圆盘剪;剪切质量;改进措施钢板剪切边开裂原因分析及改进剪切质量的措施2.1 钢板原始剪切边无角横裂的试验为找出钢板原始剪切边在再加工过程中产生边部开裂的原因,采用25mm厚钢板纵向样,在实验室条件下,模拟用户使用条件做了一系列的试验。
试样长350mm、宽50mm,沿长度方向一边为圆盘剪原始剪切边,另一边经过机加工。
试验条件超出了标准规定的钢板机械性能范畴,即对试验标准弯心直径进行调整,25mm普板弯心直径由标准规定的d为3a调整到d为128mm的较大弯心直径。
(1)保留圆盘剪原始剪切边,做弯曲试验。
6根试样受弯面一半采用圆盘剪剪切板面的上表面,一半采用下表面。
剪切板面为下表面的,即受弯面带有剪切弯钩的3根试样均开裂,裂缝产生均由原始剪切边在厚度方向从外向里开裂;在厚度方向和宽度方向基本裂透。
剪切板面为上表面的,弯曲后完好。
(2)将圆盘剪剪切边加工光滑,加工量2~3mm,做弯曲试验。
6根试样弯曲后均完好。
(3)保留原始剪切边,250℃保温1.5h,做弯曲试验。
6根试样弯曲后结果与(1)相同,即受弯面带有剪切弯钩的均开裂,裂缝产生均由圆盘剪原始剪切边在厚度方向从外向里开裂。
(4)带毛边的试样。
去除毛边鼓形宽展部分进行弯曲,6根试样均完好;保留火切边部和鼓形宽展部分进行弯曲,6根试样带鼓形宽展侧未发生开裂和裂纹,火焰切割边残留的切割瘤在夹持范围内出现宽2mm、深3mm裂纹,但未向厚度和宽度方向扩展。
PDA 数据采集分析系统在舞钢4100 mm 宽厚板轧钢生产线的实际应用
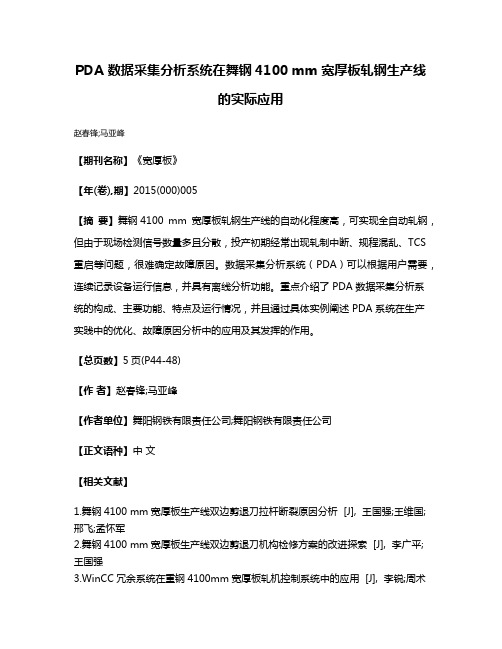
PDA 数据采集分析系统在舞钢4100 mm 宽厚板轧钢生产线
的实际应用
赵春锋;马亚峰
【期刊名称】《宽厚板》
【年(卷),期】2015(000)005
【摘要】舞钢4100 mm 宽厚板轧钢生产线的自动化程度高,可实现全自动轧钢,但由于现场检测信号数量多且分散,投产初期经常出现轧制中断、规程混乱、TCS 重启等问题,很难确定故障原因。
数据采集分析系统(PDA)可以根据用户需要,连续记录设备运行信息,并具有离线分析功能。
重点介绍了 PDA 数据采集分析系统的构成、主要功能、特点及运行情况,并且通过具体实例阐述 PDA 系统在生产实践中的优化、故障原因分析中的应用及其发挥的作用。
【总页数】5页(P44-48)
【作者】赵春锋;马亚峰
【作者单位】舞阳钢铁有限责任公司;舞阳钢铁有限责任公司
【正文语种】中文
【相关文献】
1.舞钢4100 mm宽厚板生产线双边剪退刀拉杆断裂原因分析 [J], 王国强;王维国;邢飞;孟怀军
2.舞钢4100 mm宽厚板生产线双边剪退刀机构检修方案的改进探索 [J], 李广平;王国强
3.WinCC冗余系统在重钢4100mm宽厚板轧机控制系统中的应用 [J], 李锐;周术
友
4.APC工控机在舞钢4100mm宽厚板生产线预矫直机的应用 [J], 李国良;詹英;王少义
5.舞钢4100mm宽厚板生产线6mm极限规格薄板的开发实践 [J], 张少峰;詹英因版权原因,仅展示原文概要,查看原文内容请购买。
磨煤机拉杆断裂原因分析
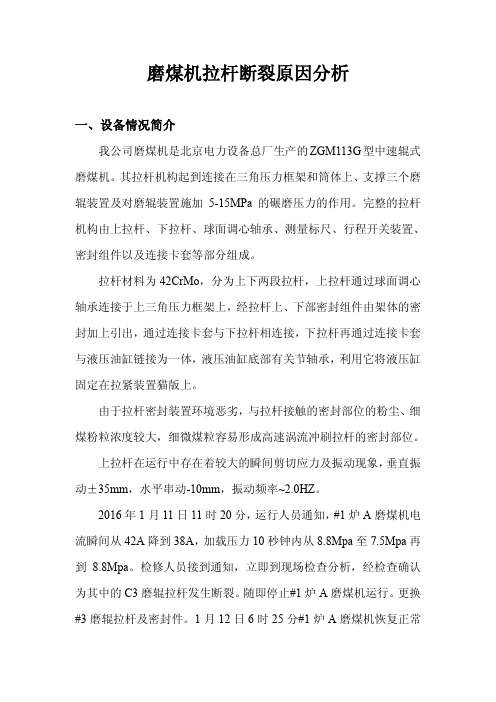
磨煤机拉杆断裂原因分析一、设备情况简介我公司磨煤机是北京电力设备总厂生产的 ZGM113G 型中速辊式 磨煤机。
其拉杆机构起到连接在三角压力框架和筒体上、支撑三个磨 辊装置及对磨辊装置施加 5-15MPa 的碾磨压力的作用。
完整的拉杆 机构由上拉杆、下拉杆、球面调心轴承、测量标尺、行程开关装置、 密封组件以及连接卡套等部分组成。
拉杆材料为 42CrMo,分为上下两段拉杆,上拉杆通过球面调心 轴承连接于上三角压力框架上,经拉杆上、下部密封组件由架体的密 封加上引出,通过连接卡套与下拉杆相连接,下拉杆再通过连接卡套 与液压油缸链接为一体,液压油缸底部有关节轴承,利用它将液压缸 固定在拉紧装置猫版上。
由于拉杆密封装置环境恶劣,与拉杆接触的密封部位的粉尘、细 煤粉粒浓度较大,细微煤粒容易形成高速涡流冲刷拉杆的密封部位。
上拉杆在运行中存在着较大的瞬间剪切应力及振动现象, 垂直振 动±35mm,水平串动-10mm,振动频率~2.0HZ。
2016 年 1 月 11 日 11 时 20 分, 运行人员通知, #1 炉 A 磨煤机电 流瞬间从 42A 降到 38A, 加载压力 10 秒钟内从 8.8Mpa 至 7.5Mpa 再 到 8.8Mpa。
检修人员接到通知,立即到现场检查分析,经检查确认 为其中的 C3 磨辊拉杆发生断裂。
随即停止#1 炉 A 磨煤机运行。
更换 #3 磨辊拉杆及密封件。
1 月 12 日 6 时 25 分#1 炉 A 磨煤机恢复正常运行。
二、断裂原因分析我公司的磨煤机在运行过程发现拉杆经常发生局部磨损现象, 拉 杆直径φ135 mm,磨损部位为拉杆上两段约 200mm 长度的圆周整圈 磨损深度 4mm~6 mm, 为了节省备件的投资费用, 从 2012 年开始部 分上拉杆磨损部位采取了补焊修复措施, 但 2016 年 1 月 12 日一根重 复修复补焊过的磨煤机拉杆从补焊部位整体横向断裂, 断裂后的宏观 图片(见图一) 。
宽厚板剪切质量改进措施
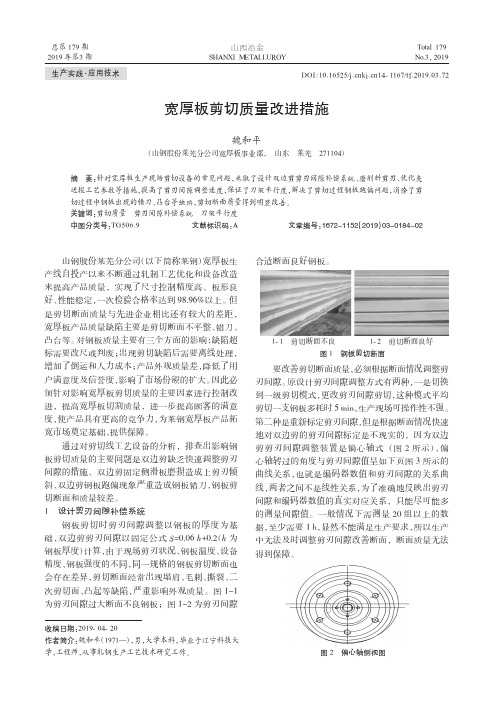
生产实践·应用技术山西冶金SHANXI M ETALLURGYTotal179No.3,2019DOI:10.16525/14-1167/tf.2019.03.72总第179期2019年第3期宽厚板剪切质量改进措施魏和平(山钢股份莱芜分公司宽厚板事业部,山东莱芜271104)摘要:针对宽厚板生产现场剪切设备的常见问题,采取了设计双边剪剪刃间隙补偿系统、磨削斜剪刃、优化夹送辊工艺参数等措施,提高了剪刃间隙调整速度,保证了刀架平行度,解决了剪切过程钢板跑偏问题,消除了剪切过程中钢板出现的错刀、凸台等缺陷,剪切断面质量得到明显改善。
关键词:剪切质量剪刃间隙补偿系统刀架平行度中图分类号:TG506.9文献标识码:A文章编号:1672-1152(2019)03-0184-02收稿日期:2019-04-20作者简介:魏和平(1971—),男,大学本科,毕业于辽宁科技大学,工程师,从事轧钢生产工艺技术研究工作。
1-1剪切断面不良1-2剪切断面良好图1钢板剪切断面图2偏心轴侧视图山钢股份莱芜分公司(以下简称莱钢)宽厚板生产线自投产以来不断通过轧制工艺优化和设备改造来提高产品质量,实现了尺寸控制精度高、板形良好、性能稳定,一次检验合格率达到98.96%以上。
但是剪切断面质量与先进企业相比还有较大的差距,宽厚板产品质量缺陷主要是剪切断面不平整、错刀、凸台等。
对钢板质量主要有三个方面的影响:缺陷超标需要改尺或判废;出现剪切缺陷后需要离线处理,增加了倒运和人力成本;产品外观质量差,降低了用户满意度及信誉度,影响了市场份额的扩大。
因此必须针对影响宽厚板剪切质量的主要因素进行控制改进,提高宽厚板切割质量,进一步提高顾客的满意度,使产品具有更高的竞争力,为莱钢宽厚板产品拓宽市场奠定基础、提供保障。
通过对剪切线工艺设备的分析,排查出影响钢板剪切质量的主要问题是双边剪缺乏快速调整剪刃间隙的措施、双边剪固定侧滑板磨损造成上剪刃倾斜、双边剪钢板跑偏现象严重造成钢板错刀,钢板剪切断面和质量较差。
高强钢生产中切边剪崩刃原因分析及控制措施

高强钢生产中切边剪崩刃原因分析及控制措施发表时间:2020-12-15T14:25:12.550Z 来源:《基层建设》2020年第23期作者:门建仁曹欢[导读] 摘要:文中介绍了切边剪的基本结构及工作原理,针对高强钢生产中切边剪崩刃现象进行了原因分析,并提出了优化剪刃间隙和重叠量参数、严格控制剪刃硬度等有效的控制措施。
河钢唐钢高强汽车板有限公司河北唐山摘要:文中介绍了切边剪的基本结构及工作原理,针对高强钢生产中切边剪崩刃现象进行了原因分析,并提出了优化剪刃间隙和重叠量参数、严格控制剪刃硬度等有效的控制措施。
关键词:高强钢;切边剪;崩刃;控制0前言切边剪设备在冷轧生产线中的应用极为普遍,其作用是切除缺陷较多的带钢边部,保证成品带钢宽度规格。
切边剪设备的制造精度、安装精度、参数设定及其控制精度等均会对带钢的切边质量和设备的运行稳定性产生较大影响。
我厂酸轧生产线在生产高强钢过程中,切边剪频频发生崩刃故障,问题严重时还会在带钢边部产生深度超过1mm的边部裂口。
严重影响了产品质量和生产效率。
1切边剪的结构介绍切边剪由两个移动剪架组成(如图1所示),由电机1驱动,通过分配箱9和12将动力传至圆盘剪,在两个移动剪架上分别安装有刀刃侧隙调整机构和重叠量调整机构。
马达6通过丝杠带动驱动两机架以中心线做相对移动,以调整切边后带钢宽度。
图1切边剪结构图2切边剪的工作原理切边剪在工作时,剪刃旋转完全由带钢带动,因此剪刃的线速度与带钢运行速度保持一致。
带钢通过切边剪的过程中,上下剪刃做圆周运动的同时逐渐切入带钢,从而将带钢边部切断。
这一剪切过程可细分为三个阶段:弹性变形阶段、塑性变形阶段及断裂阶段。
通过剪切断面可以看出,断面的上部为剪断区,断面下部为撕裂区。
这是因为在剪切时,上剪刃会对废边产生向外和向下的挤压力,再加上下方碎边剪的牵引力,使得断面上部材料早于下部提前产生塑性变形并先断裂,从而剪断面出现在上部。
当带钢速度与剪切速度相等时,带钢的受力情况如图2所示。
4300mm宽厚板冷矫直机常见故障分析
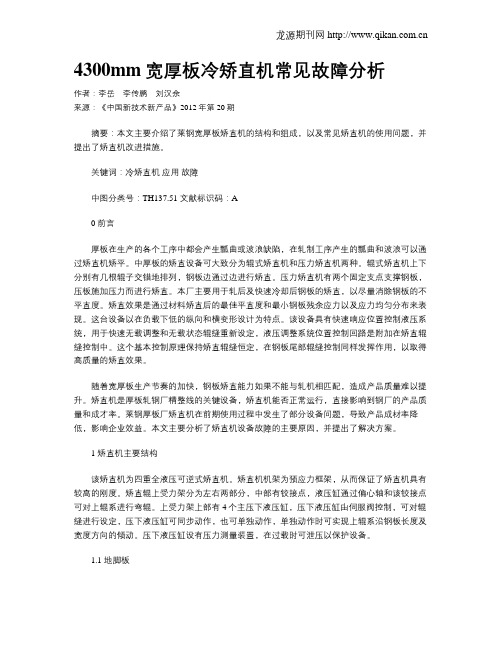
4300mm宽厚板冷矫直机常见故障分析作者:李岳李传鹏刘汉余来源:《中国新技术新产品》2012年第20期摘要:本文主要介绍了莱钢宽厚板矫直机的结构和组成,以及常见矫直机的使用问题,并提出了矫直机改进措施。
关键词:冷矫直机应用故障中图分类号:TH137.51 文献标识码:A0 前言厚板在生产的各个工序中都会产生瓢曲或波浪缺陷,在轧制工序产生的瓢曲和波浪可以通过矫直机矫平。
中厚板的矫直设备可大致分为辊式矫直机和压力矫直机两种。
辊式矫直机上下分别有几根辊子交错地排列,钢板边通过边进行矫直。
压力矫直机有两个固定支点支撑钢板,压板施加压力而进行矫直。
本厂主要用于轧后及快速冷却后钢板的矫直,以尽量消除钢板的不平直度。
矫直效果是通过材料矫直后的最佳平直度和最小钢板残余应力以及应力均匀分布来表现。
这台设备以在负载下低的纵向和横变形设计为特点。
该设备具有快速响应位置控制液压系统,用于快速无载调整和无载状态辊缝重新设定,液压调整系统位置控制回路是附加在矫直辊缝控制中。
这个基本控制原理保持矫直辊缝恒定,在钢板尾部辊缝控制同样发挥作用,以取得高质量的矫直效果。
随着宽厚板生产节奏的加快,钢板矫直能力如果不能与轧机相匹配,造成产品质量难以提升。
矫直机是厚板轧钢厂精整线的关键设备,矫直机能否正常运行,直接影响到钢厂的产品质量和成才率。
莱钢厚板厂矫直机在前期使用过程中发生了部分设备问题,导致产品成材率降低,影响企业效益。
本文主要分析了矫直机设备故障的主要原因,并提出了解决方案。
1 矫直机主要结构该矫直机为四重全液压可逆式矫直机。
矫直机机架为预应力框架,从而保证了矫直机具有较高的刚度。
矫直辊上受力架分为左右两部分,中部有铰接点,液压缸通过偏心轴和该铰接点可对上辊系进行弯辊。
上受力架上部有4个主压下液压缸,压下液压缸由伺服阀控制,可对辊缝进行设定,压下液压缸可同步动作,也可单独动作,单独动作时可实现上辊系沿钢板长度及宽度方向的倾动。
舞钢4200 mm宽厚板产线轧钢车间改造综述

Miao Yingjie1, Zhane Yoobie1, Jiao Shdnqi2 dud Liu Yichne2
(1 Rollinq Enqieeerinq Technicol Institute of Capitol Enqieeerinq and Research Incorporation Limited ; 2 Wusteei Company of HBIS Group Co. ,LtO.)
and nemopstratiop. The renovyhop
improves the
quality and properties, copsoPnates the posi-
of Wusteei as the naPopoi proPuctiop base of exto heavy steel plate. The renovatiop plan can be provinee as refeo-
轧制
工艺因素,确定中间冷却装置出
口
轧机 28.5 m。
原ACC快冷
钢板的冷
、温度控
制 和冷
性
参数方
不足。
本次轧线升级改造,在精轧机后建设新 冷装
。精轧机与现有热 机工艺 为88.2 m,
新冷 本
23 m。综合考虑 轧制
的母板 轧机、快冷 和热 机处的
生产,最终确 轧机 冷
口
为36.2 m,快冷 出口至热 机距离为
国内外新建成的众多中厚板车间中,
用TMCP工艺生产 钢的轧机要 辐
位轧制压力都在20 kN/mm以上,主电机功率达
2 kW/mm以上⑴。根据兴澄4 300 mm宽厚板
轧机轧制宽度3 993 mm、厚度51.5 mm中间坯生
宽厚板轧机万向接轴裂纹产生的原因分析及对策
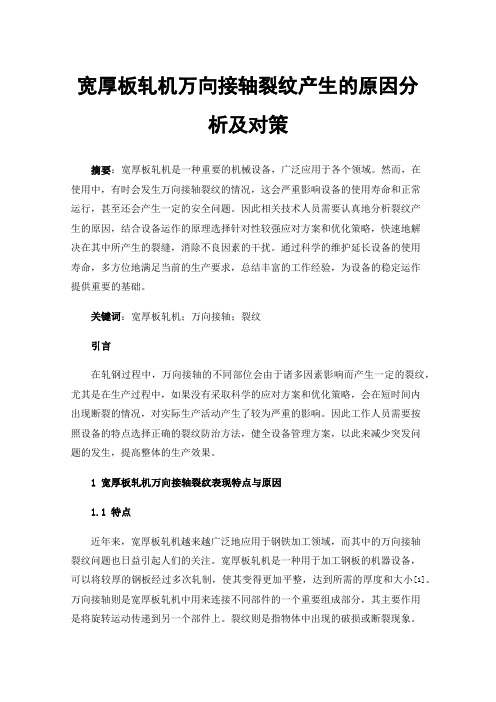
宽厚板轧机万向接轴裂纹产生的原因分析及对策摘要:宽厚板轧机是一种重要的机械设备,广泛应用于各个领域。
然而,在使用中,有时会发生万向接轴裂纹的情况,这会严重影响设备的使用寿命和正常运行,甚至还会产生一定的安全问题。
因此相关技术人员需要认真地分析裂纹产生的原因,结合设备运作的原理选择针对性较强应对方案和优化策略,快速地解决在其中所产生的裂缝,消除不良因素的干扰。
通过科学的维护延长设备的使用寿命,多方位地满足当前的生产要求,总结丰富的工作经验,为设备的稳定运作提供重要的基础。
关键词:宽厚板轧机;万向接轴;裂纹引言在轧钢过程中,万向接轴的不同部位会由于诸多因素影响而产生一定的裂纹,尤其是在生产过程中,如果没有采取科学的应对方案和优化策略,会在短时间内出现断裂的情况,对实际生产活动产生了较为严重的影响。
因此工作人员需要按照设备的特点选择正确的裂纹防治方法,健全设备管理方案,以此来减少突发问题的发生,提高整体的生产效果。
1宽厚板轧机万向接轴裂纹表现特点与原因1.1特点近年来,宽厚板轧机越来越广泛地应用于钢铁加工领域,而其中的万向接轴裂纹问题也日益引起人们的关注。
宽厚板轧机是一种用于加工钢板的机器设备,可以将较厚的钢板经过多次轧制,使其变得更加平整,达到所需的厚度和大小[1]。
万向接轴则是宽厚板轧机中用来连接不同部件的一个重要组成部分,其主要作用是将旋转运动传递到另一个部件上。
裂纹则是指物体中出现的破损或断裂现象。
宽厚板轧机万向接轴裂纹的位置通常不固定,可能出现在不同的部位,如轴承座、轴承支架、万向接头等处。
宽厚板轧机万向接轴裂纹的形状也非常多样化,有些是直线型,有些则呈现出分支或扩展的形态,形状不规则,难以预测。
宽厚板轧机万向接轴裂纹的严重程度也不尽相同,有些只是表面上的薄裂纹,对机器运行影响较小,而有些则是深度较大,经常会导致机器停运甚至事故发生。
宽厚板轧机万向接轴裂纹的成因十分复杂,可能由于材料质量问题、加工工艺不当、运行状态不稳定等多种原因造成。
运煤机拨车臂拨钩拉杆断裂原因分析
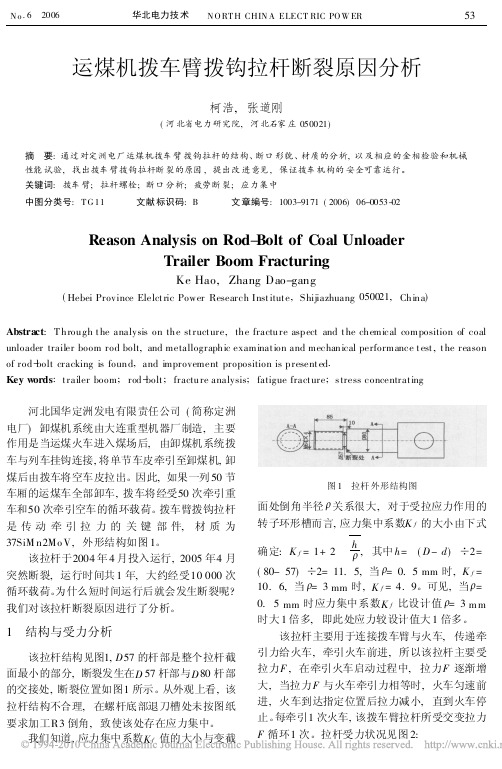
试样编号
1 2 3 图纸要求 G B/ T 3077-1999 要求
抗拉强度 Rm /M Pa
961 950 959 ≥865 ≥980
断后伸长 率A / %
18 18 18 ≥14 ≥12
冲击吸收功 A ku/ J
120 118 118 ≥31 ≥63
3. 4 硬度 对该拉杆D80 直径杆部横截面进行硬度试
运煤机拨车臂拨钩拉杆断裂原因分析
柯浩, 张道刚
( 河北省电力研究院, 河北石家庄 050021)
摘 要: 通过对定洲电厂运煤机拨车臂 拨钩拉杆的结构、断口形貌、材质的分析, 以及相应的金相检验和机械 性能试验, 找出拨车臂拨钩拉杆断裂的原因 , 提出改 进意见, 保证拨车机构的安全可靠运行。 关键词: 拨车臂; 拉杆螺栓; 断口分析; 疲劳断裂; 应力集中
该拉杆于2004 年 4 月投入运行, 2005 年4 月 突然断裂, 运行时间共 1 年, 大约经受10 000 次 循环载荷。为什么短时间运行后就会发生断裂呢? 我们对该拉杆断裂原因进行了分析。
1 结构与受力分析
该拉杆结构见图1, D57 的杆部是整个拉杆截 面最小的部分, 断裂发生在D 57 杆部与D80 杆部 的交接处, 断裂位置如图1 所示。从外观上看, 该 拉杆结构不合理, 在螺杆底部退刀槽处未按图纸 要求加工R3 倒角, 致使该处存在应力集中。
验, 硬度值分别为HB272、HB269、HB269, 符合 图纸设计要求 ( HB269~302) 。
4 结论
根据宏观检查与材质分析, 运煤机拨车臂拨钩 拉杆断裂原因为: 该拉杆结构不合理, 螺杆底部退刀 槽处未按图纸要求加工R3 倒角, 导致在D 57 与D 80 杆部截面突变产生应力集中, 是产生疲劳源的主要 因素; 拉杆承受交变载荷, 在经过长期的交变应力循 环后, 裂纹扩展直至发生断裂。该拉杆化学成份不合 格, C、Mo 含量偏低, 抗拉强度不符合标准要求, 是 产生断裂的材质方面的因素。
舞钢4100mm宽厚板生产线双边剪退刀机构检修方案的改进探索

Ab s t r a c t F o c u s i n g o n ma in t e n a n c e p r o b l e ms o f k n i f e r e t r a c t i o n d e v i c e f o r d o u b l e s i d e t immi r n g s h e a r i n Wu - g a n g S 4 1 0 0 mm w i d e a n d h e a v y p l a t e p r o d u c t i o n l i n e ,t h e d i s a d v nt a a g e s o f t h e ma i n t e n a n c e p og r r a m s u g g e s t e d b y f o r - e i g n e q u i p me n t e n g i n e e i r n g c o mp a n y h a v e b e e n na a l y z e d,a s i mp l e nd a e a s i l y o p e r a t i o n l a ma in t e n a n c e p r o g r a m h a s b e e n r is a e d o n t h e b a s i s o f p r a c t i c l a s i t u a t i o n o n p l nt a s i t e .T i l e p r a c t i c e p r o v e s t h a t t h e n e w p r o g r a m n o t o n l y s a v e s a l 0 t o f ma i t e n nc a e t i me .b u t a l s o g r e a t l y r e d u c e s t h e l a b o r i n t e n s i t y ,r e c e i v i n g a g o o d r e s u l t .
提高宽厚板定尺剪剪切精度的措施

提高宽厚板定尺剪剪切精度的措施李岳;李传鹏【摘要】The structure and components of wide and heavy size plate sizing shear in Laiwu Steel have been de -scribed, and the major shearing defects causes have been illustrated as well .Meanwhile, the main factors that affected shearing accuracy of sizing shear have been analyzed and the methods of improving shearing accuracy have been put for -ward.After innovation, shearing error has been controlled under 1‰.%主要介绍了莱钢宽厚板定尺剪的结构和组成,以及主要剪切缺陷的产生原因。
分析了影响定尺剪剪切精度的主要因素,并提出了提高定尺剪剪切精度的策略。
经过改进后,定尺剪剪切误差控制在1‰以内。
【期刊名称】《中国重型装备》【年(卷),期】2012(000)004【总页数】3页(P40-41,45)【关键词】定尺剪;剪切;精度;间隙【作者】李岳;李传鹏【作者单位】莱芜钢铁集团宽厚板厂,山东271104;莱芜钢铁集团宽厚板厂,山东271104【正文语种】中文【中图分类】TG333.2+1随着宽厚板生产节奏的加快,钢板的剪切精度和效率如果不能与轧机相匹配,就会造成产品质量难以提升以及轧机的产能浪费。
定尺剪是钢板剪切线的关键设备,其主要作用是对钢板成品进行定尺剪切、取样。
莱钢厚板厂切头定尺剪在生产过程中出现剪切精度偏差较大的问题,导致产品成材率降低,影响企业效益。
本文介绍了定尺剪的主要结构,分析了造成定尺剪剪切精度降低的主要原因,并提出了解决方案。
宽厚板线双边剪剪切问题分析及解决措施
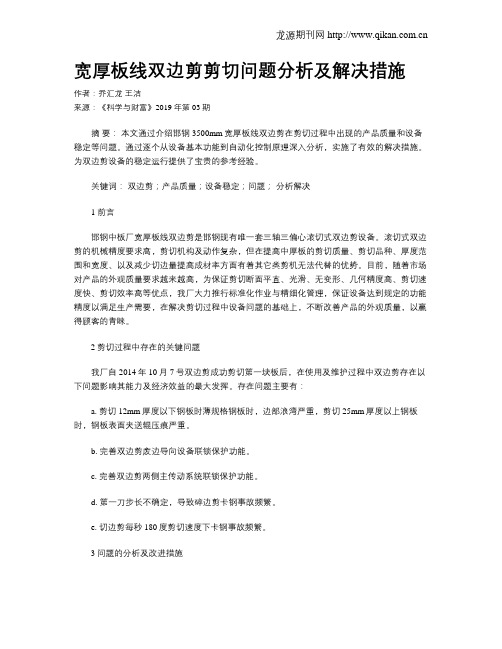
宽厚板线双边剪剪切问题分析及解决措施作者:乔汇龙王洁来源:《科学与财富》2019年第03期摘要:本文通过介绍邯钢3500mm宽厚板线双边剪在剪切过程中出现的产品质量和设备稳定等问题。
通过逐个从设备基本功能到自动化控制原理深入分析,实施了有效的解决措施。
为双边剪设备的稳定运行提供了宝贵的参考经验。
关键词:双边剪;产品质量;设备稳定;问题;分析解决1 前言邯钢中板厂宽厚板线双边剪是邯钢现有唯一套三轴三偏心滚切式双边剪设备。
滚切式双边剪的机械精度要求高,剪切机构及动作复杂,但在提高中厚板的剪切质量、剪切品种、厚度范围和宽度、以及减少切边量提高成材率方面有着其它类剪机无法代替的优势。
目前,随着市场对产品的外观质量要求越来越高,为保证剪切断面平直、光滑、无变形、几何精度高、剪切速度快、剪切效率高等优点,我厂大力推行标准化作业与精细化管理,保证设备达到规定的功能精度以满足生产需要,在解决剪切过程中设备问题的基础上,不断改善产品的外观质量,以赢得顾客的青睐。
2剪切过程中存在的关键问题我厂自2014年10月7号双边剪成功剪切第一块板后,在使用及维护过程中双边剪存在以下问题影响其能力及经济效益的最大发挥。
存在问题主要有:a. 剪切12mm厚度以下钢板时薄规格钢板时,边部浪湾严重,剪切25mm厚度以上钢板时,钢板表面夹送辊压痕严重。
b. 完善双边剪废边导向设备联锁保护功能。
c. 完善双边剪两侧主传动系统联锁保护功能。
d. 第一刀步长不确定,导致碎边剪卡钢事故频繁。
e. 切边剪每秒180度剪切速度下卡钢事故频繁。
3问题的分析及改进措施a. 产生钢板表面浪湾和压痕的关键点就是夹送辊的压力控制。
双边剪每套夹送辊液压缸由两个比例阀进行控制,一个比例阀检测液压缸压力,通过比例阀调节,程序中设定为固定比例线性控制,随钢板厚度(18mm以下)增加,相应增加压力。
但是按照原设定的程序进行剪切后,实际情况是剪切完成的钢板浪湾较严重。
- 1、下载文档前请自行甄别文档内容的完整性,平台不提供额外的编辑、内容补充、找答案等附加服务。
- 2、"仅部分预览"的文档,不可在线预览部分如存在完整性等问题,可反馈申请退款(可完整预览的文档不适用该条件!)。
- 3、如文档侵犯您的权益,请联系客服反馈,我们会尽快为您处理(人工客服工作时间:9:00-18:30)。
第22卷第6期 • 28 • 2016 年 12 月宽厚板WIDE AND HEAVY PLATEVol.22,No.6December 2016舞钢4 100 mm宽厚板生产线双边剪退刀拉杆断裂原因分析王国强王维国邢飞孟怀军(舞阳钢铁有限责任公司检修厂)摘要针对舞钢公司4 100 mm宽厚板生产线双边剪退刀拉杆断裂事故,根据退刀机构的工作原理,对 退刀拉杆进行了受力分析,最终找出断裂的主要原因并采取改进措施,避免了同类事故再次发生。
关键词退刀拉杆退刀机构偏心机构受力分析Causes Analysis of Blade Retracting Tie Rod Failure forDouble Side Trimming Shear in Wugang 4 100 mmWide and Heavy Plate Production LineWang Guoqiang,Wang Weiguo,Xing Fei and Meng Huaijun(Maintenance Division of Wuyang Iron and Steel Co. ,L td.)Abstract For the failures of blade retracting tie rod for double side trimming shear in Wugang 4 100 mm wide and heavy plate production line, the paper analyzes the loading of blade retracting tie rod according to the working principle of blade retraction mechanism, and finds out the major causes of the failure. The same incident is prevented after taking corrective measures.Keywords Blade retracting tie rod,Blade retraction mechanism,Eccentric mechanism,Force anaylsis〇前言双边剪在剪钢过程中两边同时剪切,剪后钢 板在水平分力作用下被夹持在两侧上剪刃之间,为了防止两侧上剪刃抬起时将钢板带起或磨损剪 刃,新型双边剪设计了退刀机构,可在每次剪切完 成后将上剪刃从剪切钢板的边部后退1 ~2mm,同时抬起上剪刃,并在下一次剪切开始之前恢复 到原来的剪切位置。
舞钢公司的4 100 mm宽厚板生产线双边剪 由Svemens V A I公司设计监制,结构精巧、紧凑,退刀机构与刀架拉紧机构、剪刃间隙调整机构紧 密结合。
作为双边剪的核心部件,退刀机构一旦 出现问题就会造成偏心机构不能固定,导梁失去 支撑,甚至剪刃间隙失衡,导致双边剪停产。
双边 剪在2007年投产后的三年里曾经出现2次退刀 机构拉杆断裂事故,严重影响了生产线的正常生 产。
本文根据双边剪及退刀机构的工作原理,对退刀拉杆进行力学计算和强度校核,最终找出退 刀拉杆断裂的主要原因并实施改进措施,取得了 明显效果。
1双边剪及退刀机构工作原理双边剪作业时,由2台电动机驱动每边剪机 齿轮轴,经过3级传动后驱动曲轴1、曲轴2和曲轴3。
曲轴1、曲轴2驱动主刀架作滚切运动,并 沿钢板纵向切边,曲轴3驱动碎边刀架将切边截 断。
曲轴1、曲轴2尾端安装了凸轮,退刀机构在 2个凸轮的驱动下如同杠杆绕中间支点上下摆 动,从而使退刀拉杆作周期性上下运动。
退刀拉 杆的上下运动使偏心机构转动一定的角度,偏心 机构的转动使导梁及支点向后摆动,刀架在回拉 机构的牵引下实现后退动作。
退刀拉杆直接与偏 心机构相连,对偏心机构的位置、主剪刃的刃隙以 及剪切质量产生影响。
双边剪与退刀机构的工作 原理如图1、图2所示。
第6期王国强,等:舞钢4 100 mm 宽厚板生产线双边剪退刀拉杆断裂原因分析• 29 •图1双边剪工作原理简图由于刀架及导梁始终承受回拉缸的拉力,偏 心机构同样受到使刀架后退的偏转力矩,退刀拉 杆下端又与偏心机构相连,因而受到偏心机构偏转力矩提供的拉力&。
退刀拉杆中部与减速机 底板之间安装有导向套和碟簧预紧部件,退刀拉 杆还受到碟簧施加的预紧力。
退刀拉杆装配 如图3 (a )所示,退刀拉杆受力如图3(b )所示。
当刀架完成一次剪切,右侧凸轮由大直径圆弧转 动到小直径圆弧并与滚轮配合时,退刀机构开始 摆动,退刀拉杆在偏心机构及碟簧的作用下实现 向下运动,偏心机构发生转动,从而使刀架及导梁 产生向后运动实现退刀动作。
刀架随后开始向上 抬起,右侧凸轮由小直径圆弧转动到大直径圆弧 并与滚轮配合时,退刀拉杆在退刀机构的作用下 向上抬起,偏心机构转动使刀架及导梁复位,为下 一次剪切做好准备。
2退刀拉杆受力分析及强度校核退刀拉杆2次发生断裂的位置都在图3 (a ) 所示的焊口部位,从断面形态初步判断为焊接缺 陷造成应力集中,最终导致断裂发生。
为了确定 断裂的原因,对退刀拉杆进行如下分析和强度校图3退刀拉杆装配关系及受力简图2.1受力分析及强度校核退刀拉杆在工作过程中,由于偏心机构的转动,退刀拉杆下端在沿竖直方向向下运动的同时 还伴随水平方向的摆动,拉杆沿竖直方向的往复行程为10 mm ,偏心机构的偏心量为50 mm 。
根 据三角函数关系计算水平位置偏移量(a ),见式(1):a = 50 - \J 502 - 102 «= 1 mm(1)由式(1)计算得知退刀拉杆的水平位置偏移 量为1 mm ,导向套间隙允许水平偏移2 mm ,因此 可以不考虑拉杆承受弯曲应力的情况。
退刀拉杆受力如图3 ( b )所示,拉杆B 处受到 碟形弹簧向下的张紧力心,C 处受到由偏心机构 转矩产生的拉力&。
退刀拉杆A C 段同时承受轴 向载荷八和。
作用,设A B 段和BC 段承受变拉 力,并分别用^«与表示,可得式(2)和式(3):核。
= ^2 +(2)• 30 •宽厚板第22卷Fm=Fi-F2(3)从图纸资料可以了解[1],未发生退刀动作时碟黄张紧力心=〇. 389 x105N,退刀动作发生后碟賛张紧力&'=0.27 x105N。
2.1.1拉力&的计算根据图纸可知,回拉液压缸内径为320 mm,半径7?= 160 mm,活塞杆直径为140 mm,半径r=7〇mm,工作压力p = 12 MPa,回拉缸动作时的拉力(Ff i)计算公式见式(4):F&=PS=Pn(R2 -r2)(4)式(4)代人相关数据计算得出:F& =7. 8 x lO5N偏心机构受回拉缸拉力产生的退刀拉杆拉力为A,根据力矩平衡计算得出:F1x50 = Fhl x7解得:F1 =1. 092 x10s N2.1.2退刀拉杆各段受力计算及强度校核齿轮轴正常转动而未退刀时,拉杆的受力计算见式(5)和式(6):Fm =F1 +F2 =1.481 xlO5N(5)F N2 =F1-F2 =0. 703 x lO5N(6)退刀动作发生后,退刀拉杆的受力计算见式(7)和式(8):Fm = F1 +F2'=1.362 x lO5N(7)Fm =F1-F2 =0. 822 xlO5N(8)通过计算可知,在退刀动作发生之前和退刀动作发生之后这两个平衡状态下,拉杆A B段受到的最大拉力f M为1•481 x105N,拉杆BC段受到的最大拉力为〇•822 x105N。
通过对拉杆A B段及BC段截面面积最小位置进行强度校核,确定A B段截面面积最小处为B点台阶处,面积为3.42X10—3m2,应力为段截面面积最小处为螺纹上端台阶处,面积为2_ 64 x1(T3m2,应力为cr2,见式(9)和式(10)。
Fm X1.481 x lO5~3.42 xlO3= 43. 3 MPa(9)0-2Fm _ 〇. 822 x105B~2. 64 x l O-3= 31. 1MPa(10)退刀拉杆材质为45钢,极限应力取屈服极限 值355 MPa,大于q和。
,强度满足工作要求[2]。
2.2疲劳强度校核在设备运行中承受交变应力的零件往往会在 工作应力低于其屈服点的情况下发生疲劳断裂。
双边剪每年实际剪钢量约50万t,钢板的厚度为 6 ~50 mm,据此可粗略估算出双边剪每年剪切次 数,即退刀拉杆的工作次数为139万次,退刀拉杆 每年承受循环交变应力139万次,存在拉杆疲劳断裂的可能性。
根据《工程材料》教材中的说明[3],碳素钢的疲劳强度与抗拉强度之间存在近 似比例关系,见式(11)。
55)^(11)根据有关资料可知,% =600 MPa,由上式计 算可得为240 ~ 330 MPa,远大于构件的实际受力^和,因此构件在使用过程中不会产生疲劳损伤。
3分析结果经受力分析、强度校核以及疲劳校核,说明材 料和结构的静态及动态强度都大于实际受力,不 会发生过载或疲劳断裂。
实际断裂部位不是截面 面积较小的部位B和部位C,而是截面面积最大的焊口处,因此判断焊接缺陷是造成构件断裂的 原因。
众所周知,在焊接过程中,焊缝容易形成夹 渣、气孔、未焊透、焊接裂纹等煙接缺陷,构件在使 用过程中极易在焊接缺陷处形成应力集中,长期 使用时,在交变应力作用下,裂纹的产生和发展最 终导致断裂,实际的断面形态印证了这一结论。
4改进及效果根据分析结果,舞钢对双边剪退刀拉杆加以 改进,将退刀拉杆由原来的焊接结构改成整体锻 造结构,不但避免了焊接缺陷的产生,还增强了退 刀拉杆的整体力学性能,大大降低了因应力集中 而发生疲劳断裂的可能性。
公司于2010年7月完成了对双边剪移动侧退刀拉杆的更换处理,改 造后的退刀拉杆使用至今,未再发生断裂事故。
参考文献1西门子-奥钢联(SVAI).舞阳3 800 mm生产线双边剪相关图纸及技术附件,2005.2单辉祖.材料力学(I).北京:高等教育出版社,1999.3徐自立.工程材料.武汉:华中科技大学出版社.2003.王国强,男,2007年毕业于中原工学院机械设计制造及其自动化专业,工程师。
收稿日期:2016 - 07 -11。