第七节 间歇精馏
间歇精馏流程
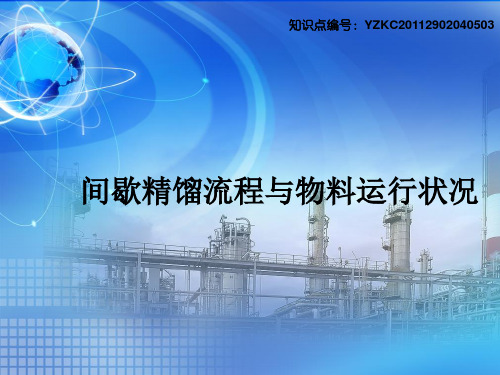
〖新课展开〗
图2 间歇精馏装置
一、间歇精馏流程
2.间歇精馏流程 图3所示为典型的间歇精馏装置 流程图。 问题5 简述间歇精馏操作过程。 回答——如图3所示,间歇精馏 时,原料液一次性投入蒸馏釜 (再沸器),逐步加热气化,待 釜中液体组成降至规定值后将其 一次排出,精馏操作即被停止。
图3 间歇精馏流程示图 1-精馏塔 2-再沸器 3-冷凝器 4-观察帽 5-贮槽
一、间歇精馏流程
3.间歇精馏的特点 问题7 间歇精馏塔有哪些特点? 回答——由间歇精馏操作可以归纳出间歇精馏过程具有如下特点。 (1)间歇精馏为非定态过程 在精馏过程中,釜中液体的组成随精馏的进行而不断降低,塔内操 作参数(如温度、浓度)也随时间而变化。若在操作时保持回流比 不变,则馏出液组成将随之下降;反之,为使馏出液组成保持不变, 则在精馏过程中应不断加大回流比。为达到预定的要求,实际操作 可以灵活多样。 例2 在操作初期可逐步加大回流比以维持馏出液组成大致恒定;但 回流比过大,在经济上并不合理。故在操作后期可保持回流比不变, 若所得的馏出液不符合要求,可将此部分产物并入下一批原料再次 精馏。
一、间歇精馏流程
3.间歇精馏的特点
(2)间歇精馏时全塔均为精馏段,没有提馏段。物料全部加到精 馏釜中,操作中没有进料、出料过程。 问题8 间歇精馏要得到与连续精馏相同的塔顶、塔底产品,消耗的 能量怎样? 回答——消耗的能量比连续精馏要多。 (3)间歇操作可以按以下两种方式进行。 ①保持馏出液浓度恒定,但相应不断改变回流比; ②保持回流比恒定,而馏出浓度逐渐降低。
二、间歇精馏操作物料运行状况
〖新课展开〗
问题11 间歇精馏塔内物料运行 状况怎样? 回答——如图3所示,从再沸器 中产生的蒸气进入精馏塔自下而 上沿塔上升,与回流液接触传质 后,进入冷凝器。一部分冷凝液 作为产品,一部分作为回流返回 塔顶。由于塔顶产品中易挥发组 分的浓度高,釜液中易挥发组分 的浓度不断下降。当降低到规定 浓度时,停止操作,釜液一次排 出。
2_间歇精馏和反应精馏

影响分离的主要因素
设备性能, 设备性能,如塔分离效率的高低 操作过程中的控制调节 主要因素: 主要因素:
物性参数(相对挥发度) 物性参数(相对挥发度) 设备参数(理论塔板数、持液量) 设备参数(理论塔板数、持液量) 操作参数(回流比、塔压、蒸发速率) 操作参数(回流比、塔压、蒸发速率)
物性参数
相对挥发度:反映混合物分离的难易程度的物理参数。 相对挥发度:反映混合物分离的难易程度的物理参数。 K y /x 对多组分混合物 α ij = i = i i K j yj / xj
确定xw和R的关系 确定 的关系
因操作开始时, 因操作开始时,釜液组成 为原料液组成, 为原料液组成,易挥发组 分含量较高, 分含量较高,故操作初期 可采用较小的回流比。 可采用较小的回流比。 若已知精馏过程某一时刻 下釜液组成xw1,对应的R 下釜液组成 对应的 可采用视察作图的方法求 即先假设一R, 得。即先假设一 ,然后在 x-y图上图解求理论板层数。 图上图解求理论板层数。 图上图解求理论板层数 若梯级数与给定的理论板 层数相等, 即为所求, 层数相等,则R即为所求, 即为所求 否则重设R值 否则重设 值,直到满足要 求为止。 求为止。
流程和操作
两种基本方式:精馏式(常用),提馏式 两种基本方式:精馏式(常用),提馏式 ),
产 过 品 渡 馏 分 1
产 品 2 产 中 品 间 提馏式 馏 分 1 2 品 产
,
精馏式
程: 精馏操作 程: 流) 和 ( 流) .
提馏式间歇精馏: 提馏式间歇精馏: 被分离物料存于与塔顶相连的贮罐中, 被分离物料存于与塔顶相连的贮罐中,塔顶冷凝液直接 流入贮料罐, 流入贮料罐,罐中液体由泵输送从塔顶以回流方式进入 塔内,产品从塔底采出。各组分的产品从高到低的顺序 塔内,产品从塔底采出。 逐一馏出。 逐一馏出。 适用于难挥发组分为目标产品或难挥发组分为热敏性物 质的情况。 质的情况。
6.12. 间歇精馏
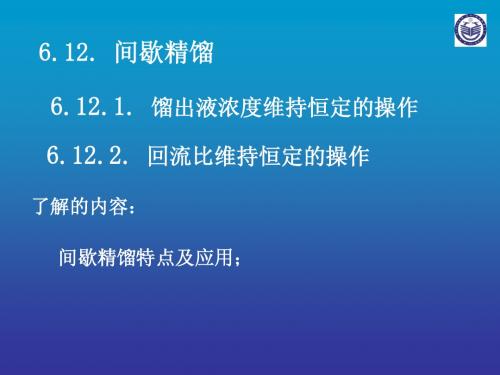
R (1.1 ~ 2) Rmin
实际上,以上两种操作方式常结合使用, 即采用分段保持恒定馏出液组成,而使回流比 逐级跃升的办法采进行操作。
y c1 c2 c3
x
图6-59 回流比不变的间歇精馏 End
图6-57 间歇精馏流程图
a
yWe1
y c1 c2 y c3
yWe2
We3
xWe1 xWe2
x
xWe3
图6-58 馏出液组成恒定的间歇精馏
6.12. 间歇精馏 6.12.1. 馏出液浓度维持恒定的操作 6.12.2. 回流比维持恒定的操作
了解的内容: 间歇精馏特点及应用;
6.12. 间歇精馏
适用范围: 反应产物的分离要求分批进行;
下列情况采用间歇精馏比用连续精馏更为合适: 欲分离的混合物种类或组成经常变动;
要求用一个塔把多组分混合物切割成为几个馏分; 欲处理的物料量很小;
特点:
(1)过程非定态是间歇过程。 间歇过程:一次加入材料,当塔釜组成达到一定 要求时,一次出塔底产品。 (2)塔底加料,无提馏段,只有精馏段; (3) 获得 xD, xW一定的产品,能耗大于连续精馏; (4)瞬间塔顶与塔底的组成呈平衡。
随操作方式的不同,有两种操作: 1)馏出液浓度维持恒定的操作 2)回流比维持恒定的操作
6.12.2. 回流比维持恒定的操作
塔板数一定,若回流比保持不变,则釜中 液体的浓度必随操作的进行而逐渐减小,同时 每一瞬间的组成亦将随之减小。 最小回流比Rmin,应根据xD1和xF计算,即: 回流比以开始的状态计算:
R min
x D1 - y Fe y yFe——与原料液xF相平衡的汽相浓度,摩尔 分数。 操作回流比可取为最小回流比的某一倍数,即:
间歇式甲醇精馏操作规程

间歇式甲醇精馏操作规程1. 引言本操作规程旨在规范间歇式甲醇精馏操作流程,确保生产过程的安全和稳定性。
本文档将具体描述操作步骤、注意事项和安全措施。
2. 设备准备在进行甲醇精馏操作之前,需要准备以下设备和材料: - 甲醇精馏塔 - 蒸馏设备(如蒸汽发生器) - 冷却设备(如冷却器) - 泵 - 管道连接件 - 安全设备(如安全阀、压力表) - 甲醇溶液3. 操作步骤3.1 准备工作1.检查甲醇精馏塔和相关设备是否处于良好状态。
2.检查管道连接是否紧固。
3.检查安全设备是否正常工作。
3.2 开启设备1.开启蒸汽发生器并调整温度,使其达到适宜的蒸汽发生温度。
2.开启冷却设备,确保甲醇精馏塔内温度控制在安全范围内。
3.启动泵,将甲醇溶液引入甲醇精馏塔。
3.3 调节操作条件1.根据需要,调节蒸汽发生器的温度和冷却设备的冷却效果,以控制甲醇精馏塔内的温度。
2.根据需要,调节泵的流量,以维持甲醇精馏塔内适宜的液位。
3.4 分离甲醇1.在甲醇精馏塔内,甲醇会向上升华并在顶部冷凝,然后被收集。
2.定期检查甲醇收集容器的液位,并及时更换。
3.5 结束操作1.当甲醇溶液消耗完毕或生产周期结束时,关闭泵。
2.关闭蒸汽发生器和冷却设备。
3.清洁设备和管道,确保设备处于良好状态。
4. 注意事项•操作人员应严格按照操作规程操作,并遵守安全规定。
•在操作过程中,应保持设备和管道的清洁。
•定期检查设备和安全设施,确保其正常工作。
•发现设备故障或异常情况时,应及时停机并报告维修。
•操作过程中出现泄漏或其他紧急情况时,应立即停止操作,采取紧急措施。
5. 安全措施•严禁操作人员单独操作,必须由经过培训的人员进行操作。
•操作人员应穿戴个人防护装备,包括安全帽、防护眼镜、防护服等。
•操作人员应经过必要的安全知识培训和操作规程培训。
•在操作过程中,应密切关注设备运行状态,如发现异常应及时报告。
•定期进行应急演练,提高操作人员的应急处理能力。
间歇精馏新研究进展

图2.3 中间罐间歇精馏塔
中间储罐间歇精馏塔的特点在于:
进料点位于塔中间的合适位置,再沸器的持液量要保持最 小
进料点处的持液被循环到中间储罐,因此中间储罐中的液 体浓度接近于进料处的液体浓度
产品或中间馏分可以同时从塔顶和塔底采出,缩短了操作 时间
适用于分离热敏性物料,该塔形吸收了提馏式间歇精馏塔 的特点,塔釜存料量少,物料只在蒸发中受热,而后存于 塔中段的储罐,存料温度低。
1.3间歇精馏的应用
由于间歇精馏具有设备简单、一塔多用、操作灵活的 优点,同时还能根据分离任务以满足高沸点、高纯度、高 凝固点和热敏物料等特殊过程的要求的特点,某些场合宜 采用间歇精馏操作。
例如:精馏的原料液是分批生产得到的,这是分离过 程也要分批进行;在实验室或科研室的精馏操作一般处理 量较少,且原料的品种、组成及分离程度经常变化,则采 用间歇精馏,更为灵活方便;多组分混合液的初步分离, 要求获得不同馏分(组成范围)的产品,这是也可采用间 歇精馏。
多罐间歇精馏塔与传统的间歇精馏塔相比,主要有以下2个特点:
多罐间歇精馏塔一般在全回流的条件进行操作,当所有罐 内的组分纯度都达到要求时,停止操作,所以整个过程操作 简单,不需要进行产品的切换
由于多罐间歇精馏塔操作的多效性,所需能量较少[7]
2.5等压串联双塔操作
等压串联双塔间歇精馏是由两个等压的间歇精馏塔串联集 成的操作过程[13],能获得相当于两个塔理论板数相加的 分离效率,但各塔塔釜的压力却与串联前一样,均保持串 联以前的值,因而对于难分离物系,特别是沸点差较小的 热敏性物料分离具有独特的优越性。装置见图2.5
9-6 间歇、恒沸、萃取精馏及多组分精馏
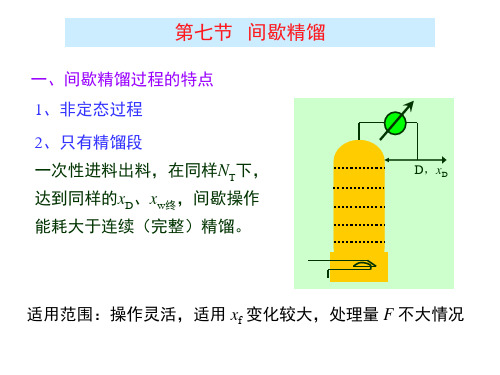
(2) 全回流近似法 假定:实际部分回流时,各组分在塔顶、塔底产品中的摩 尔分数与全回流时的相同 芬斯克方程:任意组分i和重关键组分h
xDi xDh log = N min log α ih + log xWi xWh
xDi = k log α ih + b 也可写成 log xWi
或
log
Di = k log α ih + b Wi
(1) 若N T、xf 、xw 相同,xD = xD,则操作能耗:xD 为分离的逆过程,能耗大。 (2)实际操作而言, xD恒定需R不断 增大,但操作不方便,且后期R过大, R 如右图;R恒定虽操作方便,但总 蒸汽量 V 较大,塔径 D↑,热耗↑, 不经济。故应将两者优势互补: xW R
恒
< R恒
理解:R恒定操作得 xD ,实质是将不同浓度产品混合,
∫
xf
xw
R +1 dx ( xD − x) 2
xw
xf
这里R是变量,因NT不变,x与R有对应关系 采用数值积分求出
∫
xf
xw
R +1 dx (阴影面积) 2 ( xD − x)
三、保持回流比恒定的间歇精馏 1、确定 NT
NT 及R不变,xw、xD同时下降 设计以操作初态为基准 : xD始 ~ x f 求出 Rmin = xD始 − y f yf − xf
yj αij xi = n ⇒ yi = αij xi = n xj xj ∑(αij xi ) ∑(αij xi ) yj 1
i =1 i =1
5、露点温度计算 、 同求泡点 温度(yi、P已知)归一条件∑xi=1 6、多组分物系的平衡蒸馏(闪蒸) 、多组分物系的平衡蒸馏(闪蒸) 物衡: F=D+W FxFi = Dyi + Wxi xfi=(1-q)yi+qxi 例9-12
制药分离工程-第七章精馏技术

加热
加 热 板
轻分子 重分子
冷 冷凝 凝 板
重组分
轻组分
分子蒸馏
3.分离因子 分离因子是衡量液相分子蒸发后进入气相以 及气液表面捕捉气相分子能力的参数,其主 要影响因素为温度和被分离物质的分子量。
分子蒸馏过程及其特点
冷凝面
蒸发面
1.分子蒸馏过程 分子由液相主体至冷凝面 上冷凝的过程需经历四个步骤: 内扩散→自由蒸发→飞射→冷凝
x B1 B1 dxB ln xB 0 x x B0 D B
双组分恒回流比操作的计算
任一时间下,xD与xB和塔板数N有关,可用图确 定。取若干组xB~ x 1 x 值进行图解积分,可得xB 与釜中量B的关系。
D B
N=1的理想溶液,积分得:
B1 1 xB1 1 xB 0 ln [ln ln ] B0 1 xB 0 1 xB1
2.萃取精馏
萃取精馏:在精馏过程中,从塔上部加入萃取 剂,以增加原溶液中组分间的相对挥发度,从而 实现分离。 在加入第三组分(萃取剂 )于溶液中,使组 分间的活度系数和相对挥发度发生变化,由热力 学原理得: (r / r )
12s
1
2
s
( r1 / r2 )
12
萃取精馏流程以乙二醇为萃取剂分离乙醇~水 溶液为例。
水蒸汽蒸馏
水蒸汽蒸馏有饱和水蒸汽蒸馏和过热蒸汽蒸馏 两种形式。 当系统中有水相和A的液相同时存在时,系统 的沸腾温度为该系统压力下的最低值tf。外压一 定,则温度就确定。在常压下,水蒸汽蒸馏在 100oC以下进行。 若用过热蒸汽蒸馏时,待分离组分的沸点为, 釜内只有A的液相存在,随着水蒸汽量的增加,A 组分的分压减少,系统沸点不断下降。
间歇精馏数学模型

4.计算实例
谢谢!
为简化起见,通常假设以下几条成立: 1)塔内各级为平衡级,理论板,板效率为 100%; 2)忽略塔内各级和塔顶持汽量; 3)塔身绝热操作; 4)忽略由于塔内流体力学引起的滞后,塔板上的液体全 混和; 5)塔釜相当于一个平衡级。 在不考虑塔内的持液类型情况下,对上图间歇精馏塔模型 的数学描述如下: 将塔分为冷凝器、中间级和塔釜三部分分别描述,各部分 的描述方程式均包括总物料衡算式,组分物料衡算式和焓 衡算式。
(3)求解流程 合理的求解流程同样能提高模拟的准确性和稳定性
2.间歇精馏过程的模型
间歇精馏塔比较常见的模型 如图 2-1 所示。中间级塔板 数目为N ,塔底再沸器为第 N +1块塔板。为使其具有 普适性,每个平衡级均包含 有汽、液相侧线采出和进料, 塔顶为全凝器。
2.1 模型的数学描述
间歇精馏数学模 型及计算
丁瑞
简介
间歇精馏又称分批精馏,间歇精馏操作开始 时,全部物料加入精馏釜中,再逐渐加热气 化,自塔顶引出的蒸汽经冷凝后,一部分作 为馏出液产品,另一部分作为回流送回塔内, 待釜液组成降到规定值后,将其一次排出, 然后进行下一批的精馏操作。
① ② ③
间歇精馏与连续精馏相比,具有以下特点:
模型适用条件: 本模型中引入恒体积持液的假设与工业实际情况比较接近, 因而可以用来更严格的模拟塔内操作压力不太高,汽相持料 可忽略的间歇精馏过程。
3.间歇精馏恒体积持液模型的数值解法
求解描述间歇精馏的微分和代数方程组时,求得非线性微 分方程组的解析解是不可能的,为此必须采用数值积分方 法,数值积分方法有许多种,计算过程的繁简程度互异, 计算的结果的精度和数值计算的稳定性也各不相同,这里 就有必要讨论数值积分方法的截断误差、稳定性和收敛性 的问题。 对于一阶常微分初值问题:
蒸馏-7

(2)物料衡算关系复杂 )
y in +1
y i ( n +1)
xiD R = xin + R +1 R +1
有m-1个方程
L + qF W = xi ( n ) − xiW L + qF − W L + qF − W
(3)流程方案的选定比较复杂 )
▲ 需要的塔多
若要将一混合物完全分离成纯组份产品的分离称 之为锐分离 锐分离,需多塔操作。采用简单塔操作时M 锐分离 组份,需M-1个塔。 ▲ 流程方案多 确定原则: ①保证产品质量原则:
分离要求规定: 分离要求规定:通过规定关键组分的分离要求, 对塔的分离结果进行控制。 ◆规定轻关键组份在塔顶的组成和重关键组分在塔底 的组成 ◆规定轻关键组分在塔顶组成及回收率 ◆规定重关键组分在塔底组成及轻关键组分在塔顶的 回收率 (2)非关键组份在两端产品中的分配 ) 作为设计型计算,求N,欲知qnD, qnW,必需知 xwi和xDi, 但xwi 、 xDi 又和N有关,故需试差。
式中:
Ki =
∑α
α ih
ih x i
= α ih K h
④ 逐板计算求解理论塔板数
当关键组份居中时,可分别从塔顶和塔底计算理论板数。
xl x h
xl x h
xl xl ≥ ≥ x x n −1 h q h n
N min
q nDl xl ( )D = xh q nDh
q nWl xl ( )w = xh q nWh
N min
q nD q nW l l log q nD h q nW h = log α l , h
间歇精馏
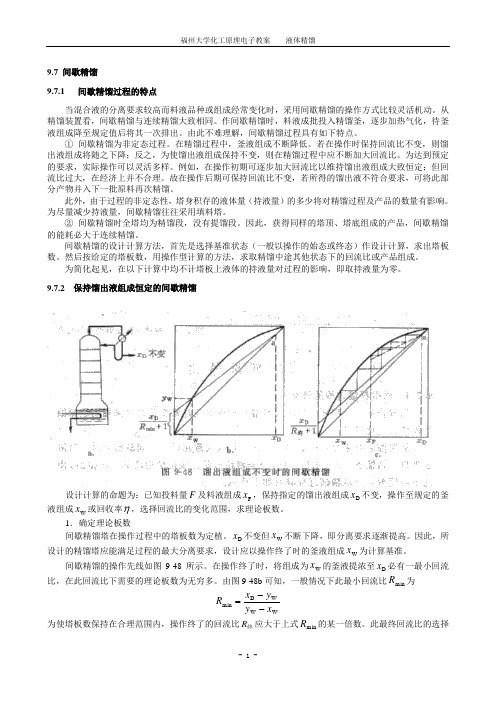
9.7 间歇精馏9.7.1 间歇精馏过程的特点当混合液的分离要求较高而料液品种或组成经常变化时,采用间歇精馏的操作方式比较灵活机动。
从精馏装置看,间歇精馏与连续精馏大致相同。
作间歇精馏时,料液成批投入精馏釜,逐步加热气化,待釜液组成降至规定值后将其一次排出。
由此不难理解,间歇精馏过程具有如下特点。
① 间歇精馏为非定态过程。
在精馏过程中,釜液组成不断降低。
若在操作时保持回流比不变,则馏出液组成将随之下降;反之,为使馏出液组成保持不变,则在精馏过程中应不断加大回流比。
为达到预定的要求,实际操作可以灵活多样。
例如,在操作初期可逐步加大回流比以维持馏出液组成大致恒定;但回流比过大,在经济上并不合理。
故在操作后期可保持回流比不变,若所得的馏出液不符合要求,可将此部分产物并入下一批原料再次精馏。
此外,由于过程的非定态性,塔身积存的液体量(持液量)的多少将对精馏过程及产品的数量有影响。
为尽量减少持液量,间歇精馏往往采用填料塔。
② 间歇精馏时全塔均为精馏段,没有提馏段。
因此,获得同样的塔顶、塔底组成的产品,间歇精馏的能耗必大于连续精馏。
间歇精馏的设计计算方法,首先是选择基准状态(一般以操作的始态或终态)作设计计算,求出塔板数。
然后按给定的塔板数,用操作型计算的方法,求取精馏中途其他状态下的回流比或产品组成。
为简化起见,在以下计算中均不计塔板上液体的持液量对过程的影响,即取持液量为零。
9.7.2 保持馏出液组成恒定的间歇精馏设计计算的命题为:已知投料量F 及料液组成F x ,保持指定的馏出液组成D x 不变,操作至规定的釜液组成W x 或回收率η,选择回流比的变化范围,求理论板数。
1.确定理论板数间歇精馏塔在操作过程中的塔板数为定植。
D x 不变但W x 不断下降,即分离要求逐渐提高。
因此,所设计的精馏塔应能满足过程的最大分离要求,设计应以操作终了时的釜液组成W x 为计算基准。
间歇精馏的操作先线如图9-48所示。
间歇精馏讲解

间歇精馏讲解
间歇精馏是一种常见的分离和纯化有机化合物的方法。
它主要适
用于不同沸点的化合物,通过温度的变化使它们分别蒸发、凝结,最
终得到纯净的化合物。
在间歇精馏过程中,需要一个精细的装置。
通常采用双颈烧瓶,
烧瓶装有导管和热交换器,可以用来控制温度和压力。
还需要连接一
个冷凝水管,以便冷却蒸气并使其转化成液体。
此外,还需要使用温
度计、计时器和其他辅助设备来精确控制操作。
在进行间歇精馏时,首先将混合物放入烧瓶中,并加热至混合物
开始汽化。
这时,蒸汽通过导管进入热交换器,在那里它与冷却水接
触并冷却,逐渐转变为液体。
得到的液体收集在另一个烧瓶中,在此
过程中,可以通过温度的变化来控制分离的化合物。
间歇精馏可以广泛应用于有机化合物的分离,如酯、醇、酚、醛、酮、酸等。
它不仅可用于合成工艺中的分离和提纯,还可用于从天然
中提取组分,如植物和动物油脂。
此外,间歇精馏还可以协助分离和测量化合物的揮发度和沸点,
以及用于分析和确定它们的纯度,从而确定适合于不同的应用的最佳
条件。
总之,间歇精馏是一种广泛使用的有效分离方法,它的技术要求
较高,需要精密设备和技能操作。
但是,通过对间歇精馏的逐步理解
和掌握,你将能够通过精确的温度控制和操作技巧,成功分离和纯化你的化合物。
9-7间歇精馏

返回
西北大学化工原理电子课件 大学化工原理电子课件
三,回流比保持恒定的间歇精馏
设计命题为:
x (馏出液的平均 已知: F,xf,xw(最终的釜液组成), D
组成),选择合适的R. 求: N 计算以操作初态为基准,假设一最初的馏出液浓度xD始,则:
k min 始 =
x d始 y f yf xf
R适宜 = ARmin 求 N →
xD R终 + 1
应
的直线.根据最终的XW求理论板数.
2,每批料液的操作时间
F 每批料液的投料量 Kmol D 馏出液量 Kmol 其值随精馏时间而变. x 釜液组成,由Xf或Xw V 蒸馏釜的汽化能力 kmol s 在操作中可保持为某异常数 汽化量 Vd τ = ( R + 1) d D
xD = Fx f wxw F w = Fx f wxw D
当此 xD 等于或稍大于规定的值时,计算有效. 处理一批料液塔釜的总蒸发量为G=(R+1)D.由此可 计算再沸器热耗.
返回
�
返回
西北大学化工原理电子课件 大学化工原理电子课件
1, xD始的验算
设:W——瞬间的釜液量,操作时由投料量F降为残液量. X——瞬间的釜液组成,由Xf降为Xw. 和简单蒸馏的物料衡算式相同,有
xf F dx ln = ∫ w xw x D x
xD x
因为N和R为定值,故X和XD有一一对应的关系, 通过数值积分可得W.
返回
西北大学化工原理电子课件 大学化工原理电子课件 某一瞬间之前馏出 的液体量为:
V R +1 = D xf x D=F xD x f Rx
xf x D = F x x D xf x dD = F d (xD x )2 X ∴Vd τ = (R + 1)F F τ= V F = V =
间歇精馏常见的操作模式

间歇精馏常见的操作模式
间歇精馏是一种常见的分离技术,被广泛用于液体和蒸气混合物的分离,可以将任意混合物分别提取出组分。
它可以在较短时间内多次进
行操作,这是其最大优势之一。
首先,要使用间歇精馏进行操作,必须准备好适当的容器。
经常选择
一个圆形管道,其形状能够增加精馏的效率。
另外,还必须准备好充
分的液体供给,以及用来加热或冷却的装置。
其次,将混合物倒入容器中,然后尽可能地加热它。
加热的方式可以
采用电加热或水加热等。
这步操作可使各成分之间的极性不同,低极
性物质容易上升,高极性物质容易下降。
接着,就要开始精馏操作了。
首先,根据所需分离的物质,确定相应
的温度。
然后,将混合物放置在设置好的温度中,并使其进行内部结
构的转化,也就是间歇的蒸发精馏操作,它不但能够将组分分离开来,还能有效地消除其中的某些成分,从而获得更高的纯度。
最后,精馏实验中经常会产生很多残渣,如果不及时清理,则会影响
下一次操作的效果。
从而需要定期清理容器,并将渣滓物质抛弃掉。
总之,间歇精馏常见的操作模式主要包括准备工作、加温结构转化、
精馏操作和维护清理等几个步骤。
将混合物加热,调节到所需温度,
使其发生相变,从而让组分分离出来。
最后,定期清理容器和渣滓,
以保证操作的可靠性和精确度。
间歇精馏的工艺原理
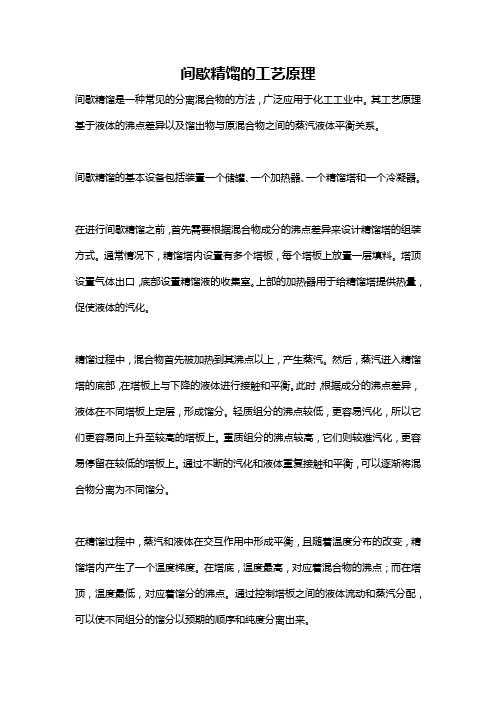
间歇精馏的工艺原理间歇精馏是一种常见的分离混合物的方法,广泛应用于化工工业中。
其工艺原理基于液体的沸点差异以及馏出物与原混合物之间的蒸汽液体平衡关系。
间歇精馏的基本设备包括装置一个储罐、一个加热器、一个精馏塔和一个冷凝器。
在进行间歇精馏之前,首先需要根据混合物成分的沸点差异来设计精馏塔的组装方式。
通常情况下,精馏塔内设置有多个塔板,每个塔板上放置一层填料。
塔顶设置气体出口,底部设置精馏液的收集室。
上部的加热器用于给精馏塔提供热量,促使液体的汽化。
精馏过程中,混合物首先被加热到其沸点以上,产生蒸汽。
然后,蒸汽进入精馏塔的底部,在塔板上与下降的液体进行接触和平衡。
此时,根据成分的沸点差异,液体在不同塔板上定层,形成馏分。
轻质组分的沸点较低,更容易汽化,所以它们更容易向上升至较高的塔板上。
重质组分的沸点较高,它们则较难汽化,更容易停留在较低的塔板上。
通过不断的汽化和液体重复接触和平衡,可以逐渐将混合物分离为不同馏分。
在精馏过程中,蒸汽和液体在交互作用中形成平衡,且随着温度分布的改变,精馏塔内产生了一个温度梯度。
在塔底,温度最高,对应着混合物的沸点;而在塔顶,温度最低,对应着馏分的沸点。
通过控制塔板之间的液体流动和蒸汽分配,可以使不同组分的馏分以预期的顺序和纯度分离出来。
最后,蒸汽通过塔顶的气体出口进入冷凝器,冷凝为液体馏分。
这些液体馏分被收集到不同的容器中,可以进一步进行加工和利用。
间歇精馏的优势之一是可以分离出纯度较高、品质较好的馏分。
另外,间歇精馏的设备相对简单,操作容易掌握,适用于不同规模的生产。
总而言之,间歇精馏是一种利用混合物的沸点差异和蒸汽液体平衡来实现分离的方法。
通过控制加热、冷凝和液体流动,可以将原混合物逐渐分离为各种纯度不同的馏分。
这种工艺原理在化工工业中有着广泛的应用,例如石油炼制、化学品生产等领域。
间歇精馏新研究进展-PPT精品文档
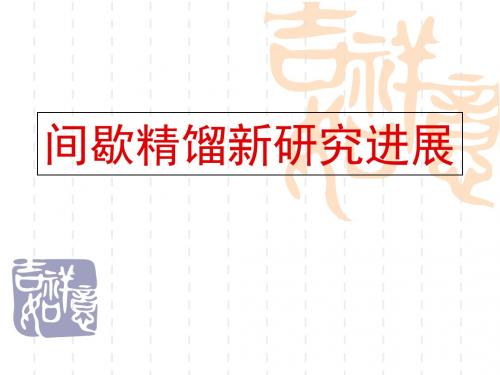
一、前言
1.1间歇精馏 1.2间歇精馏的特点 1.3间歇精馏的应用
1.1间歇精馏
间歇精馏又称为分批 精馏。间歇精馏操作开始 时,全部物料加入精馏釜 中,再逐渐加热汽化,自 塔顶引出的蒸气经冷凝后, 一部分作为流出液产品, 另一部分作为回流送回塔 内,待塔釜组成降到规定 值后,将其一次排出,然 后进行下一批的精馏操作。
根据回流比可以将间歇精馏分为部分回流间歇精馏过程和全回 流间歇精馏过程:
部分回流间歇精馏过程 现在在工业间歇精馏塔和实验室装置中广泛应用的是 部分回流间歇精馏,它是间歇精馏的最基本模式。它又可 以分为恒定回流比操作和恒定塔顶浓度操作。 全回流间歇精馏过程 全回流间歇精馏过程通常是在精馏塔顶设置一个回流 存料罐,进行全回流操作,直到回流罐内料液浓度达到或 接近平衡后放出的操作过程。
二、新型操作方式
间歇精馏这些年来新发展起来的操作方式主要有:动 态累积间歇精馏塔操作、反向间歇精馏塔操作、中间罐间 歇精馏塔操作、多罐间歇精馏塔操作、提馏式间歇精馏塔 操作、等压串联双塔操作、带塔底储罐的间歇精馏塔操作 以及双再沸器间歇精馏塔操作
2.1动态累积间歇精馏塔的操作
动态累积间歇精馏是在塔顶累积全回流操作的基础 上发展起来的。塔顶累积全回流操作最早由Barb等人和 Block于1967年提出的,装置见图2.1。这种操作方式主 要分为3个阶段:(1)充液阶段;(2)全回流阶段;(3)放液 阶段。
间歇精馏塔
1.2间歇精馏的特点
间歇精馏与连续精馏相比,具有以下特点: 间歇精馏为非稳态过程 即塔内操作参数(如温度、组 成)不仅随位置变化,也随时间变化。
间歇精馏塔只有精馏段。
单塔可以完成多个组分的分离 允许进料组分浓度在较大的范围内变化,操作弹性大。 特别适合于原料处理量小、组分数多的批量生产。
精细化工过程与设备 第七课 精馏

精细化工工程与设备教材:《精细化工过程与设备》 主编: 杨春晖 郭亚军主讲:赵 平混合物的分离净化原料 纯化产物混合物分离为单一产物非均相混合物:气-液、气-固、液-气、液-液、液-固等; 分离手段:非均相混合物一般可用沉降、过滤等。
均相混合物:气-气、液-液、固-固等; 分离手段:一般用传质过程单元操作解决。
传质过程以及单元操作传质过程:物质借助扩散作用由一相转移到另一相的过程称为传质过程。
单元操作:单元操作1吸收2解吸3蒸馏4萃取5结晶6吸附7浸取8离子交换适用体系 气体混合物(氨-空气分离体系)液体混合物(吸收逆过程) 液体混合物 液体混合物液体混合物(溶液结晶分离)气体混合物、液体混合物 固体混合物(中药有效成分的分离) 液体混合物(水的软化)传质方向 气→液 液→气 气↔液 液→液 液→固 气→固 液→固 固→液液→固Chapter 7 蒸馏与精馏本章主要内容:概述 蒸馏和精馏的操作流程操作流程 特殊精馏塔设备1. 概 述蒸馏与蒸发的区别蒸馏:溶质和溶剂都具有挥发性; 塔顶和塔底都有可能是产品。
蒸发:溶剂挥发,溶质不挥发; 蒸发产品是被浓缩了的溶液。
互溶液体混合物的分离方法很多,其中常用的方法是蒸馏和精馏。
分类:1、按操作方式分类简单蒸馏:一次部分汽化冷凝 精馏: 多次部分汽化冷凝 特殊精馏:恒沸精馏、萃取精馏、2、根据原料的组分数目分类双组分精馏 多组分精馏3、操作流程的不同分类间歇精馏 连续精馏4、按操作压力分类常压精馏 减压精馏 加压精馏双组分的常 压连续精馏2. 蒸馏和精馏的操作流程蒸馏的基本原理液体混合物挥发度易挥发(低沸点、轻组分)组分 难挥发(高沸点、重组分)组分简单蒸馏流程简单蒸馏特点非定态,用于初步分离精馏原理(一)D, yDF, xFt 3’2’ 1’12 3W, xWxWxFyD多次部分汽化和部分冷凝可分别得到较纯的轻重组分;重复单级操作,流程复杂,能耗大,中间产品多,产品收率低。
第七节 间歇精馏

第七节间歇精馏§6.7.1 间歇精馏过程的特点间歇精馏是将料液成批投入蒸馏釜,逐步加热汽化,待釜液组成降至规定值后一次性排出的操作,其特点有二:1.间歇精馏为非定态过程,在精馏过程中,釜液组成不断降低,若在操作时保持回流比不变(R不变),则xD 随时下降;反之,若xD保持不变,则在精馏过程中不断提高(增大)R。
特点:①非定态过程,为了达到预期分离要求,实际操作可灵活多样,例如在操作初期可逐步加大回流比使xD不变,但R过大,经济上不合理。
故操作后期可保持R不变,若所得的馏出液不符合要求,可将此部分产物并入下一批原料再次精馏。
间歇精馏往往采用填料塔。
这样可尽量减小持液量(塔身积存的液体量)。
持液量将影响间歇精馏过程及产品的数量。
2.间歇精馏时全塔均为精馏段,无提馏段。
因此获得同样的塔底、塔顶组成的产品,间歇精馏的能耗必大于连续精馏。
间歇精馏一般用于混合液的分离要求较高而料液品种或组成经常变化的情况。
间歇精馏的设计计算方法,首先是选择基准状态(一般为操作的始态和末态)作设计计算,求出塔板数,然后按给定的塔板数,用操作型计算的方法,求取精馏中途其它状态下的回流比及产品组成。
为简化起见,在以下介绍的计算中均不计塔板上液体的持液量对过程的影响,即取持液量为零。
§6.7.2 保持馏出液组成恒定的间歇精馏 设计计算的命题为:已知投料量F 及料液组成x f ,x D 不变,操作至规定的釜液组成x w 或回收率η,选择回流比的变化范围,求理论板数。
一. 确定理论板数1. 计算基准:间歇精馏塔在操作过程中的塔板数是定值。
x D 不变但x w 不断下降,即分离要求逐渐提高。
因此所涉及的精馏塔应满足过程的最大分离要求,设计应以操作终了时的釜液组成x w 为计算基准。
2. 最小回流比的确定在操作终了时,将组成为x w 的釜液增浓至x D 必有一最小回流比R min 在此回流比下需要的理论板数为无穷多。
间歇精馏操作切割原理
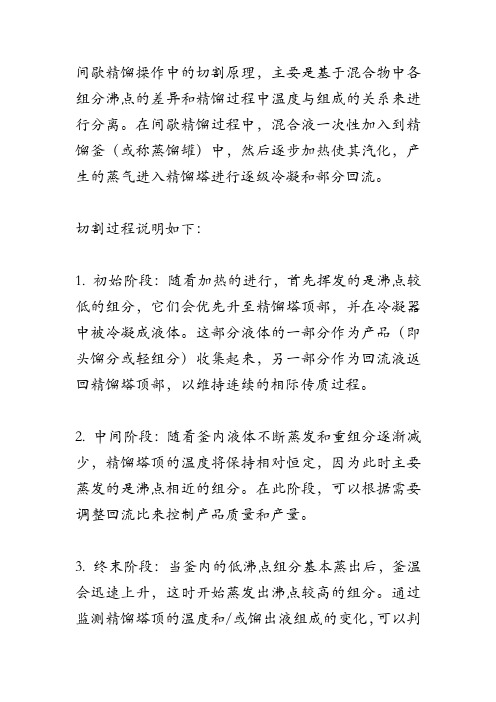
间歇精馏操作中的切割原理,主要是基于混合物中各组分沸点的差异和精馏过程中温度与组成的关系来进行分离。
在间歇精馏过程中,混合液一次性加入到精馏釜(或称蒸馏罐)中,然后逐步加热使其汽化,产生的蒸气进入精馏塔进行逐级冷凝和部分回流。
切割过程说明如下:
1. 初始阶段:随着加热的进行,首先挥发的是沸点较低的组分,它们会优先升至精馏塔顶部,并在冷凝器中被冷凝成液体。
这部分液体的一部分作为产品(即头馏分或轻组分)收集起来,另一部分作为回流液返回精馏塔顶部,以维持连续的相际传质过程。
2. 中间阶段:随着釜内液体不断蒸发和重组分逐渐减少,精馏塔顶的温度将保持相对恒定,因为此时主要蒸发的是沸点相近的组分。
在此阶段,可以根据需要调整回流比来控制产品质量和产量。
3. 终末阶段:当釜内的低沸点组分基本蒸出后,釜温会迅速上升,这时开始蒸发出沸点较高的组分。
通过监测精馏塔顶的温度和/或馏出液组成的变化,可以判
断何时开始切换收集第二馏分(重组分),这就是所谓的“切割”操作。
4. 结束操作:当达到预定的产品纯度或者釜液中目标组分含量极低时,停止加热并排出剩余釜液(残渣或残留物),完成一批次的精馏操作。
总之,在间歇精馏过程中,通过实时监控和调节精馏塔的操作参数,如温度、压力以及回流比等,可以精确地在不同时间点切割出不同沸点范围的产品馏分,实现混合物的有效分离。
间歇精馏
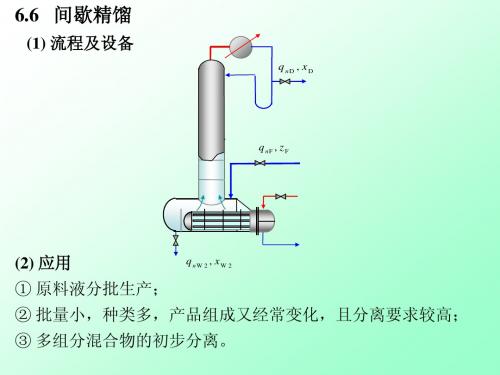
∑n
Di
nVT = ( R + 1)n D
说明: 说明:由总上升蒸汽量可计算加热蒸汽消耗量。 间歇精馏过程时间为: 间歇精馏过程时间为:
( R + 1)n D τ= q nVi
6.6.2 恒定产品组成的间歇精馏
特点: 特点:保持馏出液组成不变,连续加大回流比。 增大回流比的途径: 增大回流比的途径:① 提高上升蒸汽量; 回流比的途径 (1) 理论板数确定 ) ② 减小采出量qnD。
xD
在dτ 时间内,对系统作物料衡算,则有:
ln
nWi nWe
xwi
=
∫
xwe
dx w xD xw
令:
ln
nW i nWe
=λ
则:
nW i nWe
=e
λ
初始工况时: nWi = n F 则由物料衡算有:
xWi = z F
n D = n F nWe = n F (1 e λ )
计算平均组成:
′ xD =
6.6.1. 恒定回流比的间歇精馏 恒定回流比 回流比的间歇精馏
特点:塔顶产品组成不断降低; 特点: 釜液中组成也不断降低。
(1)理论塔板数的确定 ) 已知: q nF 已知 选取:R 选取 求 :N 计算思路:假定xD1,确定Rmin, 计算思路 假定是否合适,以 x D = 确定R,求N
zF
xWe
若x wj < x we,则回流比不必再增大
③ 操作时间 τ 通过建立dτ时间内的物料衡算方程,导得操作时间 τ 计算式:
nF τ= (xD z F ) q nV
∫
zF
xW e
R +1 dx ( x D x)
说明: 说明:实际生产过程中,为两种操作方式的结合。
- 1、下载文档前请自行甄别文档内容的完整性,平台不提供额外的编辑、内容补充、找答案等附加服务。
- 2、"仅部分预览"的文档,不可在线预览部分如存在完整性等问题,可反馈申请退款(可完整预览的文档不适用该条件!)。
- 3、如文档侵犯您的权益,请联系客服反馈,我们会尽快为您处理(人工客服工作时间:9:00-18:30)。
第七节间歇精馏
§6.7.1 间歇精馏过程的特点
间歇精馏是将料液成批投入蒸馏釜,逐步加热汽化,待釜液组成降至规定值后一次性排出的操作,其特点有二:
1.间歇精馏为非定态过程,在精馏过程中,釜液组成不断降低,若在操作时保
持回流比不变(R不变),则x
D 随时下降;反之,若x
D
保持不变,则在精馏过程
中不断提高(增大)R。
特点:
①非定态过程,
为了达到预期分离要求,实际操作可
灵活多样,例如在操作初期可逐步加
大回流比使x
D
不变,但R过大,经济
上不合理。
故操作后期可
保持R不变,若所得的馏出液不符合要求,可将此部分产物并入下一批原料再次精馏。
间歇精馏往往采用填料塔。
这样可尽量减小持液量(塔身积存的液体量)。
持液量将影响间歇精馏过程及产品的数量。
2.间歇精馏时全塔均为精馏段,无提馏段。
因此获得同样的塔底、塔顶组成的产品,间歇精馏的能耗必大于连续精馏。
间歇精馏一般用于混合液的分离要求较高而料液品种或组成经常变化的情况。
间歇精馏的设计计算方法,首先是选择基准状态(一般为操作的始态和末态)作设计计算,求出塔板数,然后按给定的塔板数,用操作型计算的方法,求取精馏中途其它状态下的回流比及产品组成。
为简化起见,在以下介绍的计算中均不计塔板上液体的持液量对过程的影响,即取持液量为零。
§6.7.2 保持馏出液组成恒定的间歇精馏 设计计算的命题为:
已知投料量F 及料液组成x f ,x D 不变,操作至规定的釜液组成x w 或回收率η,选择回流比的变化范围,求理论板数。
一. 确定理论板数
1. 计算基准:间歇精馏塔在操作过程中的塔板数是定值。
x D 不变但x w 不断下降,即分离要求逐渐提高。
因此所涉及的精馏塔应满足过程的最大分离要求,设计应以操作终了时的釜液组成x w 为计算基准。
2. 最小回流比的确定
在操作终了时,将组成为x w 的釜液增浓至x D 必有一最小回流比R min 在此回流比下需要的理论板数为无穷多。
一般R
终是R
min
的某一倍数,R
终
的选择由经济因素决定。
一旦R
终
选定后,即可从
(b)图中a点出发,以为截距做出操作终了的操作线求出理论板数。
在操作初期可采用较小的回流比,此时的操作线如上图虚线所示。
二.每批料液的操作时间
设F——每批料液的投料量,kmol
D——馏出液量(kmol),其值随精馏时间而变
X——釜液组成(摩尔分率),其值在操作中由x
f 降为x
w
V——蒸馏釜的汽化解力(kmol/s),在操作中可保持以某常数在
d
τ是自由的汽化量为Vdτ,其等于(R+1)dD,即
Vdε=(R+1)Dd
任一瞬间之前已馏出的液体量D由物料衡算式确定,即
∴
积分得:
在操作过程中因塔板数不变,每一釜液组成必对应一回流比,可用数值积分从上式求出每批料液的精馏时间。
§6.7.3回流比保持恒定的间歇精馏
因塔板数及R不变,故在精馏过程中釜液组成x与馏出液组成x
D
同时降低,自此只有使操作初期的馏出液组成适当提高,馏出液的平均浓度才能符合产品的质量要求。
设计计算的命题:已知料液量F及x
f ,x
w
,馏出液的平均组成,选择适宜的回
流比R,求理论板数。
1.计算基准:操作初态
2.R
min 假设最初的馏出液浓度x
D始
,根据设计的x
D始
与釜液组成x
f
,求出所需的
最小回流比R
min。
然后,选择适宜的回流比R
opt ,计算理论板数N
T。
二. x
D始
的验算
设定x
D始
是否合适,应以令精馏过程所得到的馏出液平均组成满足分离要求为准。
设W——某时刻的釜液量,投料量为F,残液量为W;
X——某时刻的釜液组成,由x
f 降为x
w
;
与简单蒸馏相同,对微元时间dε作物料衡算
因为N
T 一定,R亦一定,所以x必与x
D
一一对应,见上面右图,作平衡线(R一
定),并以N
T =4试差作x与x
D
的对应值来。
于是可用数值积分上式求得残液量
W。
而馏出液平均组成:
若
则x
D始
假设合理,上述计算有效。
否则重新假定再计算。
又:处理一批料液塔釜的总蒸发量为:
由此计算加热蒸汽的消耗量。