总装线工位布局资料
Ford总装车间布置简图

底盘线2线底盘的安装
座椅物流区域
后桥分线,装发动机和后桥
涂装
内外饰,电气物流区域
拆门,装拉索,铺电线,装地
)内饰板,仪表板ห้องสมุดไป่ตู้,粘玻璃。
位)车身调整紧固,部分检查
车门上附件和内外饰板的安装
轮的安装
底盘装上车身(工 装上顶) 发动机分装线 后桥分线,装发动机和后桥 前桥分装线
约260米
约135米
问题车存放返修 区
内饰线1(22工位)拆门,装拉索,铺电线,装地
内饰线2(22工位)内饰板,仪表板等,粘玻璃。
完成线2(28工位)车身调整紧固,部分检查
检 检 测 测 线 线 1 2
检 测 线 3
门分装线(28工位)4车门上附件和内外饰板的安装
完成线1(20工位)4轮的安装
内饰线3座椅等安装。
底盘线1线
预装.总装工位布局图2

23
2 6 12
2
电
测
包装
试
2
机动/返 修
2
导线送 料工
物料送 料工
2
Total 28
Security Classification
Competency Descriptor
E11 ENG Position Diagram
返工架
S1
S2
S3
S4
F/A-1
双面转板
波纹管架
P
Inspection
ALRO
A-CELL
B-CELL
C-CELL
D-CELL
E-CELL
F-CELL
KIT13
F/A-1 F/A-16
F/A-2 F/A-15
F/A-3 F/A-14
F/A-4 F/A-13
F/A-5 F/A-12
F/A-6 F/A-11
F/A-7 F/A-10
F/A-8 F/A-9
返工架 Security Classification
13.1
பைடு நூலகம்
10 H
131
2
4
4
16
10 H
16
2
4
4
16
10 H
16
2
4
4
18.7
10 H
187
2
4
4
14.3
10 H
143
2
4
4
16.5
10 H
165
2
4
4
13.1
10 H
131
2
4
4
16
10 H
16
汽车总装工序排布方法及原则

汽车四大工艺中,总装作为整车最后一道工艺,肩负着装配、调整和检测主要工作任务。
合理的工序编排才能造出高质量、高效率的汽车。
本文从前期汽车工序排布问题及编排工序因素进行阐述。
汽车工艺工序编排整车工艺工序流程为冲压→焊装→涂装→总装。
总装生产线的组成及基本生产流程如图所示。
具体生产环节如图所示前期工序排布在车型投产批量前期,规划部门对工序进行规划排布,新车型的工序初步排版主要是参考同类平台车型进行试制生产。
在后期生产过程中,出现如下问题:(1)人员装配物料量不均,工时节拍不平衡,导致员工抱怨大。
(2)人员左右跑动装配,装配过重件时无设备协助,劳动强度大。
(3)某些装配件被其他装配件覆盖,过程检验人员无法确认。
工序编排原则1. 装配先后顺序在编排过程中按照先后顺序,由内到外,进行逐层覆盖性装配。
在过程中,对于工段内装配覆盖件,必须要考虑过程检验员对覆盖件的检验方便程度,确保每个件能检查到位。
不会因为出现覆盖件查不到而放到后道工序,进而带来质量隐患。
在整个工序编排中,要做到装配顺序合理,不影响下道工序装配作业。
2. 同系统零件集中装配同系统的零件在同一组(生产线)装配,对整车物料分成几十个系统,例如安全带系统、标牌系统等,将系统零件安排在同一地点装配,在装配过程中不容易引起错漏装发生。
在新车型试制培训过程中,便于集中培训,减少培训时间。
在装配过程中便于质量要点控制,在检查过程中,方便检查系统的功能。
3. 同种零件集中紧固带复紧对于一个点螺栓的紧固、复紧工作,应放在同一工位进行,以便发现错误立即反馈给工人,避免总装错误。
4. 零部件分装模块化整车装配应尽力使用模块化进行装车,汽车可实现的模块有:仪表板模块、动力总成模块、后桥模块和四门分装模块。
模块尽可能将可在主生产线外装配总成剥离出工序,减少主生产线装配零件数量,增加主线员工装配的空间,降低主生产线作业工时和减少主线人员作业量。
5. 工位比例及工位工艺高度(1)合理分析装配零件数量,均衡工位设置的比例。
总装部总体工艺布置简介教学文案

总装线平面布置
蒙派克底部装配线:总共20个工位,也是由两条线组成的, 主要用于承载式车身的底部装配,一线与二线之间采用自 行转线葫芦。蒙派克车身底部装配完毕后转到综合线进行 车门装配、液体加注等。蒙派克底部装配1线的南侧为副车 架分装、后悬分装、发动机分装线,在蒙派克底部装配线 的西侧是其车门分装线。 欧马可落厢线:在总装厂房的西南角,厂房长120米,宽96 米。欧马可车辆的前束调整、前后轮制动磨合台、均设置 在落厢线的前面。落厢线是一条与地面相平的双板链,中 间、两侧均设有地沟。落厢线的北面是货箱及附件的存储 区域,中间的2跨(约48米)是车辆的返修调整区域;南面 是欧马可车辆的检测线,检测线与返修区用墙隔开。
段段 一二
班
班 班班 班班班班理班
班班
班
8
生产组织方式及重点变更的作业内容
• 生产线节拍2.5分钟,比现在的节拍快了半分钟 • 两条底盘线供应一条综合线,但只配备一条线的作业人
员,底盘线人员需倒线作业,要求既会装配欧马可奥铃 底盘,同时也必须会装蒙派克底盘; • 员工单一作业内容向多作业内容转变或单一工位作业向 多工位转变,要求员工素质提高; • 零部件上线方式发生变化,由领料制改为物流配送制; • 新增蒙派克、P201下线直接上检测线的作业方式; • 内饰和综合增加了P201货箱装配内容; • 落厢线增加了前后轮动态磨合、前束调整、测漏等作业 内容; • 增加了蒙派克和P201产品的调试作业内容; • 各生产线之间的转序方式发生了较大变化。
3
总装线平面布置 车辆底部防锈线:设置在整车报交区域,厂房长60米,宽 18米,设置两条底部防锈喷漆线,能够适应小轴距和大轴 距的车辆底部防锈喷漆。 总装部车辆生产工 身
P
精选区
预装.总装工位布局图

安全性
确保工位布局符合人机工 程学原理,降低操作过程 中的安全隐患。
布局目标
提高生产效率
通过合理的工位布局,减 少生产过程中的等待和搬 运时间,提高整体生产效 率。
优化资源配置
根据生产需求和工艺特点, 合理配置设备和人力资源, 实现资源利用的最大化。
提升产品质量
通过合理的工位布局,减 少操作过程中的误差和不 良品率,提高产品质量。
不足
流水线设计可能导致员工工作单调乏味,降低工作积极性 和技能提升空间。此外,生产线的调整和扩展较为困难。
行业最佳实践分享
综合型布局
采用模块化与流水线相结合的布局方式,既考虑了生产效率和灵活 性,又兼顾了员工的工作体验和技能提升。
人机工程学应用
根据员工的作业姿势、视野范围和工作强度等因素,合理安排工位 布局,降低员工疲劳度。
作业环境设计
人员配置与培训
创造良好的作业环境,包括照明、温度、 湿度、清洁度等方面,确保产品质量和操 作人员的舒适度。
根据总装工位的工艺特点和设备操作要求 ,合理配置操作人员,并进行必要的培训 和技能提升。
总装工位优化
工艺流程优化
通过对工艺流程的持续改进 和优化,提高生产效率和质 量。
设备更新与改造
布局考虑因素
工艺流程
根据产品制造的工艺流程,确 定各工位的顺序和位置,确保
生产流程的顺畅。
设备特点
考虑设备的大小、形状和功能 ,合理安排工位的位置和空间 大小,以满足生产需求。
人员操作习惯
考虑员工的操作习惯和舒适度 ,合理安排工位布局,提高员 工工作效率。
环境因素
考虑车间内的环境因素,如噪 音、照明、温度等,合理安排 工位布局,提高工作环境质量
总装部简介及流程

1.安装前风窗玻璃总成 2.安装后风挡玻璃总成 3.安装中平台本体总成 4.安装后暖风机总成
蒙派克整车装配工艺流程图
NS18
DZ01
1.安装供油管路 2.安装离合器、制动油管总成 3.安装上摆臂总成 4.安装双头螺栓
FZ0201
1.压装轮毂轴承 2.安装后制动器总成
FZ0202
1.安装后制动鼓 2.主减速器总成加油
FZ0204
1.连接等速驱动半轴总 成与后制动器 2.安装后制动油管总成
DZ04
1.安装后桥分装合件
发动机二级质量 门及在线返修
DZ09
1.连接前制动软管总成 2.复紧扭杆总成 3.安装消声器隔热板
DZ08
1.复紧关键点力矩 2.安装备胎支架焊合总成 3.安装后悬横向稳定杆
DZ07
1.安装下摆臂总成 2.安装前盘式制动器带转向节总成 3.安装前横向稳定杆 4.安装推力杆
蒙派克整车装配工艺流程图
车身吊接
NS01
1.登记上线车辆信息 2.安装发动机罩撑竿总成 3.安装地板胶堵 4.安装扭杆调节螺栓
NS02
1.拆卸侧滑门 2.安装顶棚线束总成 3.安装后门线束总成 4.安装车门助力撑杆
NS03
1.安装发动机仓线束总成 2.打印车身VIN号 3.安装后背门锁 4.安装前围隔热垫
(1)蒙派克工艺流程介绍
蒙派克整车装配工艺流程(见后页),工艺流程中的各工序指的是各工 序的开始,并不是说一个工序结束后方可进行下道工序,有些工序 可以交叉进行,而有些工序的前后顺序可以调换,应根据实际情况 确定客车的总装装配工艺。蒙派克与迷迪生产线工艺流程就是在按 照蒙派克与迷迪车型及生产线实际作业条件进行编排的。 蒙派克与迷迪工艺流程相关说明: 1.蒙派克与迷迪整车装配工艺流程图中符号含义: NS—内饰线; DZ—吊装线; ZH—综合线; 分装线:FZ01—发动机分装;FZ02—后桥分装;FZ03—车门分装。 (取汉语拼音的首位大写字母组合而成) 其他的分装如:燃油箱分装、燃油制动管路分装、仪表板分装未在 此流程中体现。 2.流程中同时列出了生产线上车间一级、二级质量门的工艺流程。 3.流程中只列出了每个车位的主要操作内容部分,具体的作业内容 和要求还需要初学者现场实习才能了解。
总装车间布置经验

第 14 页
三、一汽-大众汽车总装车间简介
3.2 总装车间主要数据
Jetta轿车:
年设计纲领15万辆,采用二班工作制生产,生产节拍1.5分钟,整车单台装配总工时为15小
时,年设计纲领总劳动量225万小时。达产时设计工作人员总数为1580人。总装车间工艺投 资总数为2409万马克及6754万人民币。设备总台数221台(条),其中国外引进设备48台套。 Jetta轿车总装、分装、调试、返修所占面积37200m2。 所需非标准专用工装、夹具、吊具及工位器具68种2248台(套),所需专用工具98种670把 (件)。均为国内设计制造。 所需国内标准工具100种6687件,投产前一次性引进国外工具约30种386件。
空调、加速制动踏板等重要的零部件。一般情况下,这些部件都由不同的供应商提供。
第4页
一、总装车间的布置
1.2 动力总成工段
发动机是汽车的心脏,而动力总成则囊括了发动机、离合器、变速箱、前后桥以及悬架等 汽车底部重要的零部件。由于动力总成的组成零部件比较多,一般整车厂会将其设置为独 立的一条“副线”,工人们在副线上完成动力总成的装配,再由推车把此模块送到总装
3.2 总装车间主要数据
厂房及公用工程: 设在厂房屋顶上南北各一排的通风机房共装有40台送风机组,其送风管路系统沿厂房屋架 上的最上层敷设,并沿厂房柱子向下延伸到3.5m高度均匀分布,共设有360个送风口,上述 系统的采用使车间内的总送风量达2.4×l06m3/h,夏季每小时换气次数3次,冬季新鲜空气 补充量9.2×l06m3/h,每小时换气次数一次。厂房内冬季设计采暖温度为16℃。该系统的实
总装车间布1、认识和了解整车总装生产线布置方式 2、探讨总装车间布置优缺点。
第1页
总装工艺布局规划方案
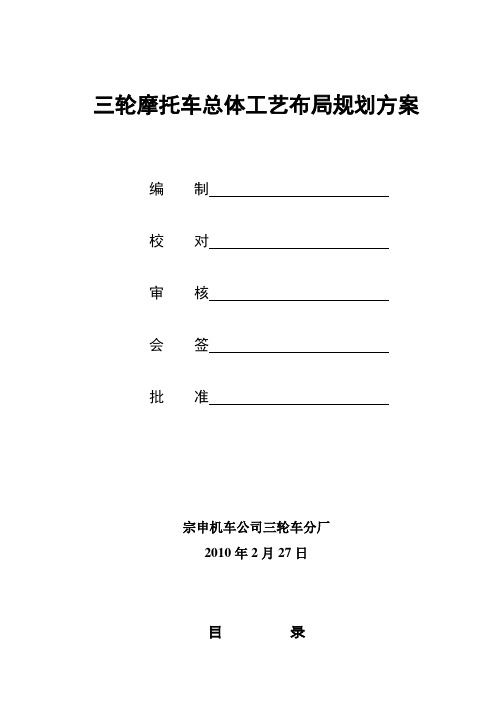
三轮摩托车总体工艺布局规划方案编制校对审核会签批准宗申机车公司三轮车分厂2010年2月27日目录一、项目方案设计概况 (3)二、装配检测线工艺方案 (3)三、包装线工艺方案 (4)四、物流方案 (6)五、装备配置方案 (7)六、项目实施建议 (10)七、结束语 (11)附图:装配检测工艺流程图装配检测线工艺布局图包装线工艺布局图(含工艺流程)总装车间工艺布置图一、项目概述根据集团的发展规划和统一部署,三轮车业务将作为摩托车业务的有力补充,为公司创造经济效益。
为此公司成立了专门的三轮车项目组开展相关工作。
依据项目的初步设想,首先建立总装生产基地,随后完善焊接、涂装等配套生产项目。
现就本项目总装工艺布局进行规划如下。
二、基本指导原则1、不做简单效仿,要具有宗申特色的差异化;2、遵照总体规划设计,分步实施的的指导原则开展项目工作;3、尽可能利用现有的厂房场地、装备等资源,以减少新增投入费用,降低投资风险。
三、主要生产类型1、总装生产:三轮摩托车的装配、检测、发运;2、发动机生产:三轮摩托车用发动机的生产;3、冲焊生产:三轮摩托车的车架、车厢等结构件的生产;4、涂装生产:三轮摩托车的车架、车厢、外观件的涂装生产;5、线束生产:三轮摩托车的线束生产;6、座垫生产:三轮摩托车的座垫、靠背的生产;7、其它零部件生产。
四、生产场地1、总装生产:利用机车公司联合厂房总装车间现有2跨空余场地(含厂房及公用工程等基础设施)进行三轮摩托车的配货、装配、检测、暂存、发运等生产。
2、发动机生产:利用发动机公司现有资源,承担各型三轮摩托车的发动机的生产。
3、冲焊件生产:先期外协配套,逐步利用集团现有冲焊工厂资源扩展各型三轮摩托车的车架、车厢等结构件的生产,同时以外协配套为辅助。
4、涂装生产:先期外协配套,逐步利用现有联合厂房涂装工厂扩展各型三轮摩托车的车架、车厢、外观件的涂装生产,同时以外协配套为辅助。
5、线束生产:利用联合厂房现有线束生产线资源扩展三轮车品种,承担三轮车线束生产任务。
THA总装车间设备分布剖析

BA2
BA2工段以平板输 送车体,制造商为 DURR
5
N
底盘预装线(PA线)
虚线框为有玻璃门区域 电动葫芦 电柜 组合式高精枪
连续工位 检测平台 升降机
升降机
后桥拧紧机械手
01
02
03
04
05
06
07 08 09 10 11 12 13 14 15
16
17
18
行车方向
动力总成线(TS线)
16 17 18 19 20 21 22 23
宁波总装车间设备分布图
宁波TFH项目
1
总装车间布局图
三区
四区
MQ5
BA6 返修 前束转毂 门预装线
BA7
BA5 前围预装线 BA4 一区 BA2 BA0 BA1 仪表板预装线
贴膜
ZT8
雨淋
注:空余部分为车间物流周转区 因车间安全要求,高层输送区域及地坑平板 输送区域未能进入,输送路线按照工位顺序 排列
地毯
A柱内饰
加液
制动杆
落水槽板
方向盘对中 行李箱盖板
踏板检测
雨刮器
手制动调整
QRK
加汽油
门盖调整
外部电源
UPS
Q-Gate
QRK
前轮定位 灯光调整 合格出车
转鼓试验
LEP
道路试验
门预装线
QRK
ZP8检查
雨淋
BA6
QRK
三角玻璃涂胶
车门装配
气囊
方向盘安装
前座椅
后座椅
中央通道
随车工具
轮胎装配
3
N
升降机 EM S座椅
升降机
右后 门密 封机
轿车总装检测线及返修区工艺流程设计与布置

车辆工程技术13车辆技术轿车总装检测线及返修区工艺流程设计与布置刘 科,刁世磊(神龙汽车有限公司,成都 610100)摘 要:进入21世纪以来,汽车电气化、智能化水平越来越高,越来越多的车辆集成了驾驶辅助系统(ADAS)、更好的信息娱乐系统,与之对应的各大整车厂对车辆各项功能的检测也提出了越来越高的要求,同时日益增长的实际销售需求导致的多车型混线生产对检测线的柔性化也要求更高。
基于此本文研究了新的行业背景下,实现绩效更好的总装检测线及返修区工艺流程设计,更优的总装检测线设备布置,更优的,功能更全面的跑道布置,更紧凑的商业线及返修区布置。
关键词:检测线工艺;检测线布置;返修区布置0 引言 检测线是乘用车总装车间内的最后环节,对整车预计零部件功能进行综合检测,用于确认整车是否满足产品技术要求[1]。
本文在进行乘用车总装检测线与返修区的工艺设计过程中,根据紧凑、高效的工位设计原则,模块式、集中化进行设备布置和区域规划,既考虑集约化生产要求,又保证工艺路线的顺畅连贯和车流的有序、便捷。
1 总装检测线及返修区工艺流程设计 总装检测线工艺流程设计方案在基于整车厂已有生产工序流程和生产边界的基础上,笔者的思路是区域内整体工艺流向按照“Π”型设计,同时在检测线设备区域和商业线中间集中布置返修区,可以保证返修车流和生产车流的交叉和相对独立。
具体工艺流程为:符合性检查→前束大灯调整→侧滑检测→制动及车速检测→ADAS 功能标定及调整→跑道路试→排放检测→底盘检查→淋雨密封检测→电器检查→商业化。
符合性检查工位设计,在考虑整车厂车型功能越来越齐备尤其是先进技术大量应用的实际,笔者认为应增加设置必要的检查岗位,具体应包含如下工艺流程: 外观检查→调整→内饰功能→行李箱功能→外饰→符合性→下线转运。
2 总装检测线设备布置 笔者认为检测线设备区域布置应考虑增大设备之间间距,增加车辆检测等待工位,避免高节拍下的车辆拥堵,保证车流顺畅。
总装部总体工艺布置简介

日韩质量水平
国内郑州日产、江铃皮卡、海外丰田、五十铃
VAN
蒙派克
(4790-5230)×1825×1950
5200X1800X2230
国内中高端MPV
江淮瑞风
CUV
4630x1785x1710
4630x1785x1710
日原产质量水平
*
总装线平面布置
底盘线:总共有39个有效工位,由两条地拖组成,底盘一线20个,底盘2线19个,底盘一线到底盘二线采用底盘转线自行葫芦。在底盘1线与底盘2线之间设有发动机分装线、前、后桥分装台(对于前后桥的装配设计上做了两种准备,一种是在线上直接装配前后桥,不进行分装;另一种是先分装再上线装配。)在两条底盘线中间设置了很多分装台,如储气筒分装、散热器分装、副水箱分装等。
总装线平面布置
01
02
总装线平面布置
PBS线:即车身存储线,涂装好的车身经过滑橇输送系统被送到总装的车身存储区域,存储区域总共可存储车身166台(单排),车身均被放置在滑橇上,车身带着滑橇被转运到内饰线上,待内饰装配完毕后空橇通过返回系统再回到空橇存储区。滑橇总共280个,长橇140个和短橇140个,空橇存储区在空中分上下两层,上面一层存储短橇,下面一层存储长橇。
多功能工厂总装部总共有7条生产线,分别为PBS线(在空中)、内饰线、底盘线、综合线、蒙派克底部装配线、落箱线、整车底部防锈线。其中落箱线、整车底部防锈线与其它5条线不在同一厂房内。另外在欧马可返修调试车间设置3个并排的补漆室。 总装线厂房共计6.24万平米,长400米,宽156米。总装线分2期建设,其中一期建设总装线占用厂房东西长约209米,南北宽约115米,除此以外在总装厂房的西南侧建有一条蒙派克、P/U201的整车检测线和报交线。总装车间内剩余的面积为二期工程预留。
重卡装配线工艺布局
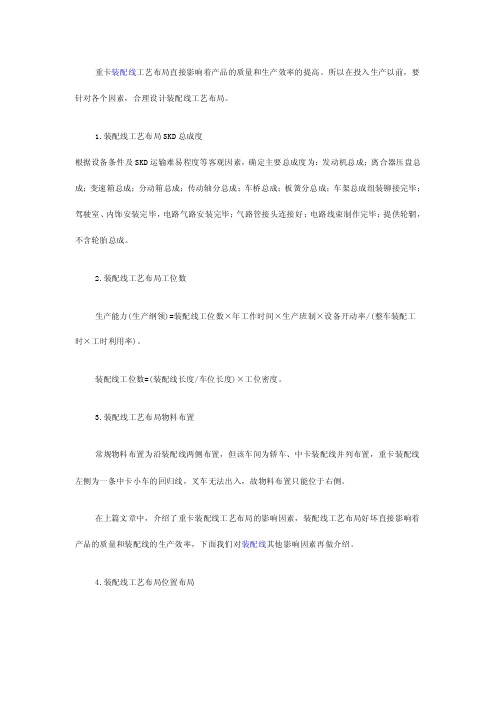
重卡装配线工艺布局直接影响着产品的质量和生产效率的提高。
所以在投入生产以前,要针对各个因素,合理设计装配线工艺布局。
1.装配线工艺布局SKD总成度根据设备条件及SKD运输难易程度等客观因素,确定主要总成度为:发动机总成;离合器压盘总成;变速箱总成;分动箱总成;传动轴分总成;车桥总成;板簧分总成;车架总成组装铆接完毕;驾驶室、内饰安装完毕,电路气路安装完毕;气路管接头连接好;电路线束制作完毕;提供轮辋,不含轮胎总成。
2.装配线工艺布局工位数生产能力(生产纲领)=装配线工位数×年工作时间×生产班制×设备开动率/(整车装配工时×工时利用率)。
装配线工位数=(装配线长度/车位长度)×工位密度。
3.装配线工艺布局物料布置常规物料布置为沿装配线两侧布置,但该车间为轿车、中卡装配线并列布置,重卡装配线左侧为一条中卡小车的回归线,叉车无法出入,故物料布置只能位于右侧。
在上篇文章中,介绍了重卡装配线工艺布局的影响因素,装配线工艺布局好坏直接影响着产品的质量和装配线的生产效率,下面我们对装配线其他影响因素再做介绍。
4.装配线工艺布局位置布局一工位:平衡轴、前后悬装配、车架翻身;二工位:车桥、传动轴、转向机装配;三工位:蓄电池装配;四工位:线束、管路装配;五工位:发离变装配;六工位:冷却系、排气系装配;七工位:油箱、驾驶室悬置装配;八工位:驾驶室、备胎架装配;九工位:轮胎装配,整车加油;十工位:装配保险杠、调整及整车下线。
为保证装配车辆的整体流水操作,装配线工艺布局与检测线布置于同一条直线上,车辆从装配线行驶下线直接进入检测线。
5.装配线工艺布局较重零件跨线方案由于物料布置只能位于装配线右侧,故对左侧装配的较重零件必须有合理的跨线方案。
(1) 左侧轮胎。
轮胎位于装配线末端,用手推小车从轮胎分装区送至装配地点的左右侧。
(2) 蓄电池箱体。
布局于三工位,借用天车从空中将蓄电池箱体从右侧运输到左侧。
总装门线项目工艺设计及布局规划简介

总装门线项目工艺设计及布局规划简介1 项目简介1.1 项目目标宝骏总装自2021年11月投产以来,陆续生产GP50、M150、CN112等车型,按60JPH的生产节拍年产能输出达到40万辆;随着日益增长的市场需求,2021年在满足以上车型的基础上,生产线新增GP50HB、CN200两种车型。
通过一段时间的运行,多种车型共用一条生产线的模式可以最大程度的满足客户对各类车型的精准需求,但是同时也逐渐显露出影响车间生产效率的一些问题,如内饰人员密集度高、下线车辆划伤比率高及线旁物料空间不足等。
因此针对这些问题制定一些目标:1.1.1 提升車间生产效率通过四门的拆分,把与车门相关的的装配内容分离主线,减轻了主线的负荷、减少了四门存在而产生的非增值时间浪费、解决部分的瓶颈工位、提升装配质量,将有效改善当前的运行状况。
1.1.2 为员工创建一个安全、方便的环境在进行设计的时候,充分考虑人机工程学,如合适的操作空间、充分的光线,合理的布置休息区域,为员工创建一个安全、方便的环境。
1.1.3 确保布局具备一定的柔性考虑到陆续会有GP60、GP30等新车型上线,可能需要对生产线进行扩产,因此进行设计时,需预留有一定的空间。
2 工艺设计2.1 门线操作流程设计首先确认车门的各个装配零件的工艺要求。
2.1.1测算每个零件的实际装配时间,车间统一的TT(单件操作时间)为55s,每一个工位总的操作时间不应大于55s。
2.1.2各零件的安装顺序按下图所示装配,否则可能会出现操作工艺干涉问题。
按照此两点要求,可初步确定门线的操作流程(如图1所示)。
另外还有需要注意的地方,编排工艺时考虑工位零件物料的存放空间,保证在新车型上线时有足够的空间使用;工具方面如电池枪每工位应不超过2把,电池枪过多不方便员工区分,有用错的风险,增加装配工艺的复杂性。
2.2 门线装车单设计在设计门线之前,主线装车单上目视有图1 车门分装流程图整车的零件种类、型号等信息,用一张A3纸打印后贴在发盖上,内容包括车门装配零件,而采用门线之后,门线的零件信息较少,包括线束、玻璃、后视镜等,因此考虑将门线的零件信息单独整合成一张装车单,用A4纸打印。
模块化汽车总装生产线布局研究

模块化汽车总装生产线布局研究摘要:目前,随着车型更新换代的加速,平台车型的增多,以及各种产品的混线生产。
不同的产品,装配工时也会有差别,目前产线生产中的问题是:1)在现有生产线引入装配工时比现有产线装配工时高的产品混线生产,新产品溢出工时需要通过改造生产线,增加工位、新增装配员工或降低目前产线的运转节拍来完成;(2)增加工位,装配工人在完成高工时的产品装配后,产线在生产低工时的产品时,不仅造成了场地和人员的浪费,而且造成了大量的资源浪费;(3)传统生产线结构刚度有限、线材布局单一、产线柔性较低、产品兼容性较差、后期改造费用较高。
针对以上问题,本论文针对装配车间进行了模块化生产线的设计,以提升生产线的灵活性,以达到模块化、个性化的生产要求,同时优化生产线的人员配备,增强企业的竞争力。
关键词:汽车总装生产线;布局;模块化;自动化;MES;SPS物流;一、汽车总装生产概述汽车组成一般分为四部分,即发动机、底盘、车身以及电器与电子设备。
其中每部分又涉及到多个系统,每个系统涵盖多个总成,每个总成又由多个零部件组成。
对于一般轿车总装生产线而言,需要将数以千计的零部件与总成会按照产品及工艺要求进行联结,最后形成一辆完整的汽车,进而完成整个生产过程。
汽车总装的特点主要有:首先,汽车总装的联结方式具有多样性;其次,汽车总装的装配的零件种类多、数量大;最后,汽车总装生产具有规模较大。
对于汽车生产的纲领,其主要是指工程建设的预期年产量,对于不同品种的汽车,其年产量应做成表格,并以此进行生产活动。
产品及其生产纲领明确规定了汽车制造厂产品生产的范围与能力,即对汽车制造厂的建设规模做出了要求。
二、汽车总装生产线技术参数的计算与确定在汽车装配过程中,汽车总装是一个非常重要的环节,它可以起到至关重要的作用,因此,必须要对装配过程进行科学的设计,以保证装配过程的科学性,从而达到更好地满足目前的市场需求,因此,本文对整车装配过程中的各个环节进行了详细的分析:2.1总装式车辆参数总装车辆是汽车装配过程中的一个主要工作对象,它的外型和特性要真正地把握。
一汽公共总装车间人员优化配置方案设计

一汽公共总装车间人员优化配置方案设计第3章一汽-公共总装车间人员配置方案设计总装车间概况一汽-公共总装车间共有五条整车流水装配线,八条分装流水装配线,六条检测线,车间外部配有公共集团标准路谱的试车场,装配进程中所有的信息利用生产控制系统进行控制,关键零部件实行准时化供货,生产中采用了国际上汽车生产厂最先进的模块装配技术,利用激光测量技术、电子控制技术使装配质量达到国际先进水平。
总装车间主要装配捷达、宝来、奥迪A6(A4)、高尔夫轿车。
总装车间的生产任务和生产能力一、面积:建筑面积近9万平方米;二、流水线:共有三条整车流水线,七条分装流水线、两条检测线,车间外部配有国际标准路谱的试车场;3、产品品种:奥迪A六、奥迪A4、宝来、高尔夫、捷达;4、工位数:捷达/宝来线153个装配车位、奥迪70个装配车位、新产品试制线26个装配车位;五、日产辆:现日生产948辆轿车,其中捷达/宝来线日产798辆、奥迪线日产150辆,奥迪A4及高尔夫处于SKD装配阶段,尚未达到规模生产;六、工艺装备水平:装配进程中所有的信息利用网络系统(SAP—R3)进行控制,大量采用先进的机械人、机械手、电动扳手进行装配,并利用激光、电子技术使装配质量达到国际先进水平。
每辆装配后的整车采用目前国际上最先进的检测设备进行性能、相关参数的检测及调整。
7、车间平面布局:详见下图3-1。
轿车总装配车间必需配置的人员结构为保证生产的正常运行,一汽-公共总车间必需拥有生产制造人员、技术管理人员、行政管理人员、生产保障与支持人员,随着产能的不断提升,各类人员的总量也逐年爬升,员工总量已达:2510人。
其中:专业技术管理人员28人、生产操作服务人员2482人。
在用工形式上,自进行人力资源优化配置以来已发生明显转变,劳务用工、第三方人员已占员工总量的三分之一以上;其员工的平均受教育年限也由原来的年上升到年。
合理的人员配置结构、高素质的员工队伍打造了中国的知名品牌轿车,为一汽的战略进展作出了突出奉献。
- 1、下载文档前请自行甄别文档内容的完整性,平台不提供额外的编辑、内容补充、找答案等附加服务。
- 2、"仅部分预览"的文档,不可在线预览部分如存在完整性等问题,可反馈申请退款(可完整预览的文档不适用该条件!)。
- 3、如文档侵犯您的权益,请联系客服反馈,我们会尽快为您处理(人工客服工作时间:9:00-18:30)。
• 交作业时间:2013年4月15号
20
“沒有最好,只有更好”
具竟争力的团队 持续不断改善
改善
更上一层楼 改善
“精”
改善
21
欢
迎
提
问
22
■代表最好、最容易与最安全的工作方法; ■提供了保存技巧和专业技术的最佳方法;
■提供了衡量绩效的方法;
■表现出因果之间的基础; ■提供维持及改善的基础; ■作为目标及训练目的与基础; ■建立成为稽查或论断的基础; ■防止错误再发生及变异最小化的方法;
15
标准化操作
■完成工作所必须的操作;
■已经知道的最佳的操作顺序;
整体培训
之
《工位布局》
作成:张家明
1
课程:
一.现状分析 二.布局重点 三.应用练习
2
一.现状(1)
1).对人员技术状况/操作习 惯/质素状况未完全掌握,在工作 分配上不能完全做到量才而用; 2).未仔细对产品的物料状 况对场地要求进行全面评估; 3).换线时,作业员多数状 况是把大量的物料摆在工位旁,造 成生产线物料大量堆积,影响流线 生产与环境卫生
3
一.现状(2)
4).工位的布局未按产品性/ 体积进行仔细排列,导致工位与工位 之间间距不适宜; 5).工位布局未与流水线速度 相配合,造成作业员操作节拍失去平 衡; 6).作业区的非当批物料未及 时的清退,造成阻碍;
4
二.布局重点(1)
工件摆放不符合动作经济原则
5
二.布局重点(2)
码放不合理,半成品/物料不超过1.5米
■最能够保证PQCDSM的工作方法。
16
设施布置
传统方法 - 部门专业化
17
设施布置
精益组织方法 – 产品为中心
18
均衡化生产
▓ 每小时的工作量基本相等,避免较大的波动 ▓ 每小时內的工作量全部保质保量完成 ▓ 人员不用非正常加班,也不用应对过大的短 时工作强度
19
三.应用练习
• • • • 应用练习题: A线人员:M1316 B线人员:M1429 夏 课 长:M6105
6
二.布局重点(3)
工位制造过多
7
二.布局重点(4)
频繁搬运
8
二.布局重点(5)
造成等待
9
二.布局重点(6)
流程不平衡
1
10
二.布局重点(7)
运输储存过远
11
二.布局重点(8)
找出方法进行改善
12
二.布局重点(9)
自然而又自动的方法
13
二.布局重点(10)
制定标准布局
14
标准的主要特征