电缆用模具的分类和设计
电线电缆挤出工艺
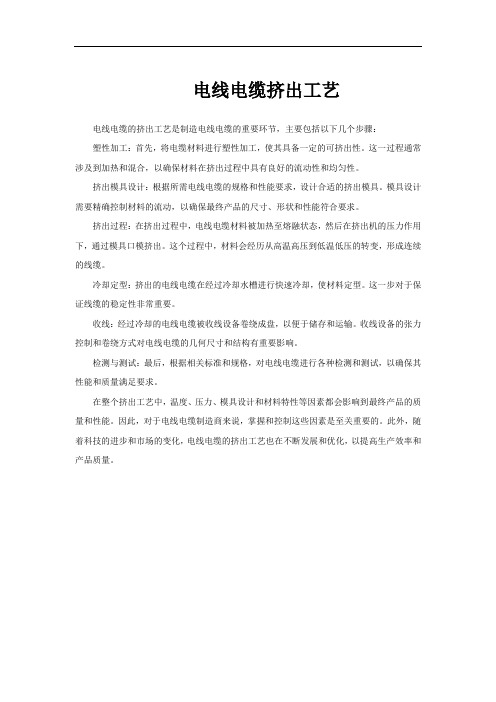
电线电缆挤出工艺
电线电缆的挤出工艺是制造电线电缆的重要环节,主要包括以下几个步骤:
塑性加工:首先,将电缆材料进行塑性加工,使其具备一定的可挤出性。
这一过程通常涉及到加热和混合,以确保材料在挤出过程中具有良好的流动性和均匀性。
挤出模具设计:根据所需电线电缆的规格和性能要求,设计合适的挤出模具。
模具设计需要精确控制材料的流动,以确保最终产品的尺寸、形状和性能符合要求。
挤出过程:在挤出过程中,电线电缆材料被加热至熔融状态,然后在挤出机的压力作用下,通过模具口模挤出。
这个过程中,材料会经历从高温高压到低温低压的转变,形成连续的线缆。
冷却定型:挤出的电线电缆在经过冷却水槽进行快速冷却,使材料定型。
这一步对于保证线缆的稳定性非常重要。
收线:经过冷却的电线电缆被收线设备卷绕成盘,以便于储存和运输。
收线设备的张力控制和卷绕方式对电线电缆的几何尺寸和结构有重要影响。
检测与测试:最后,根据相关标准和规格,对电线电缆进行各种检测和测试,以确保其性能和质量满足要求。
在整个挤出工艺中,温度、压力、模具设计和材料特性等因素都会影响到最终产品的质量和性能。
因此,对于电线电缆制造商来说,掌握和控制这些因素是至关重要的。
此外,随着科技的进步和市场的变化,电线电缆的挤出工艺也在不断发展和优化,以提高生产效率和产品质量。
电线电缆模具设计的要点

电线电缆模具设计的要点电线电缆模具设计的要点工艺配模配模是否合理,直接影响挤塑的质量和产量,故配模是重要操作技能之一。
由于塑料熔体离模后的变化,使得挤出线径并不等于模套的孔径,一方面由于牵引、冷却使制品挤包层截面收缩,外径减少;另一方面又由于离模后压力降至零,塑料弹性回复而胀大,离模后塑料层的形状尺寸的变化与物料性质、挤出温度及模具尺寸和挤出压力有关。
模具的具体尺寸是由制品的规格和挤塑工艺参数决定的,选配好适当的模具,是生产高质量、低消耗产品的关键。
1.模具的选配依据挤压式模具选配主要是依线芯选配模芯,依成品(挤包后)的外径选配模套,并根据塑料工艺特性,决定模芯和模套角度及角度差、定径区(即承线径)长度等模具的结构尺寸,使之配合得当、挤管式模具配模的依据主要是挤出速俩的拉伸比,所谓拉伸比就是塑料在模口处的圆环面积与包覆与电线电缆上的圆环面积之比,即模芯模套所形成的间隙截面积与制品标称厚度截面积之比值,拉伸比:K=(D-D)/(d-d)其中D――为模套孔径(mm);D ――为模芯出口处外径(mm);d ――为挤包后制品外径(mm);d ――为挤包前制品直径(mm)。
不同塑料的拉伸比K也不一样,如聚氯乙稀K=1.2~1.8、聚乙K=1.3~2.0,由此可确定模套孔径。
但此方法计算较为繁琐,一般多用经验公式配模。
2.模具的选配方法(1)测量半制品直径:对绝缘线芯,圆形导电线芯要测量直径,扇形或瓦形导电线芯要测量宽度;对护套缆芯,铠装电缆要测量缆芯的最大直径,对非铠装电缆要测量缆芯直径。
(2)检查修正模具:检查模芯、模套内外表面是否光滑、圆整,尤其是出线处(承线)有无裂纹、缺口、划痕、碰伤、凹凸等现象。
特别是模套的定径区和挤管式模芯的.管状长嘴要圆整光滑,发现粗糙时可以用细纱布圆周式摩擦,直到光滑为止。
(3)选配模具时,铠装电缆模具要大些,因为这里有钢带接头存在,模具太小,易造成模芯刮钢带,电缆会挤裂挤坏。
10KV架空绝缘电缆挤管式模具的设计要点

10KV垂直绝缘电缆挤压管模设计选择:挤出模头的质量直接影响塑料挤出的质量。
本文介绍了用于10KV 架空绝缘电缆的挤出管模的设计。
关键词:10KV架空绝缘电缆;挤出管模具模芯模具套设计0前言最终成型设备在塑料挤压过程中挤压模具时,其几何形状,结构和尺寸,温度,压力等直接决定电缆加工的成败。
在电线和电缆的生产中使用的挤压模具主要有三种类型:挤压,半挤压和管材挤压。
本文介绍了用于10kV架空绝缘电缆的挤出管模的设计。
1个挤出管芯1.1选材挤压管芯的结构特点是其尺寸为薄壁圆管,通常无法进行热处理。
因此,必须充分考虑所用材料的耐磨性。
因此,它通常由诸如38CrMoAl的耐磨合金制成,并被加工成具有一定余量的毛坯。
淬火和回火后,将其精炼以确保加工零件。
同心度。
1.2相关几何尺寸的设计和符号说明现在用φ90mm挤出机,挤出导体横截面为120mm2例如,挤出管芯结构如图1所示。
在图中,D是纤芯外锥的最大直径; d模芯和头部的圆锥体的最小末端直径;1个d}是型芯内锥的最大内径;α是模芯的外锥角; d是型芯尺寸的内径; dノ是堆芯上浆区的外径;ι圆柱体长度是否超出芯子尺寸区域;ι1个圆柱体在堆芯尺寸确1个定区域中的长度;大号ˊ芯和模具的组合锥的长度; L是铁芯的总长度;αˊ它是模芯和机头组合锥的角度;δ堆芯尺寸区域的壁厚。
其中D,D,Lˊ,D}一切都1个取决于机头的尺寸。
图1挤压管芯结构(1)芯锥角α。
根据头部结构和塑性流动特性设计角度,α角度越小,流动通道越平滑,突变也越小,这有利于绝缘层的结构。
(2)模芯D的外锥的最大直径,锥D的最小端直径1个以及α1个角度和铁芯长度L。
这些尺寸由机头的模芯座的尺寸决定,并且必须严格按照机头的模芯座的尺寸,加工精度必须很高,并且表面必须抛光。
(3)内锥直径D1个。
尺寸主要由加工条件决定。
越大越好,越小,在确保壁厚的前提下加工就越困难。
在φ对于小于90mm的挤出机,螺纹用于模芯与模头之间的连接。
电缆头分类

浇注式电缆头:是用一个模具固定电缆头后,往里浇注环氧树脂,干燥后拆下模具就行拉,比较麻烦,不能在潮天浇注,以免受潮降低电缆头绝缘。
冷缩电缆头: 用热缩材料制作的主绝缘套管缩住,主绝缘套管外缩半导体管,再包金属屏蔽层,最后外护套管。
所用材料一般为硅橡胶或乙丙橡胶。
为中空的圆柱体,内孔壁是半导体层,半导体层外是主绝缘材料。
现在做电缆终端头一般都是用冷缩材料制作,操作方便简单。
一、电力电缆电力电缆头分为终端头和中间接头,按安装场所分有户内式和户外式;按电缆头制作安装材料分为干包式、环氧树脂浇注式和热缩式等三类.(1)干包式电力电缆头制作安装.干包式电力电缆头使用塑料带包缠电缆头制作安装不采用填充剂,也不用任何壳体,因而具有体积小、重量轻、成本低和施工方便等优点,但只适用于户内低压(≤1kv)全塑或橡皮绝缘电力电缆。
干包式电力电缆头分为户内终端头和户内中间接头,按电缆线芯截面大小,以“个”为计量单位计算。
定额中已包含了1个ST型手套,但终端盒、保护盒、铅套管和安装支架等项费用未包括,应另行计算。
对于全塑电缆和橡皮绝缘电力电缆,其干包电缆头也可以不装设终端盒,既属于“简包电缆头”制作安装。
(2)浇注式电力电缆头制作安装。
浇注式电力电缆头是由环氧树脂外壳和套管,配以出线金具,经组装后浇注环氧树脂复合物而成。
环氧树脂是一种优良的绝缘材料,特别是具有初始电性能好,机械强度高,成型容易,阻油能力强和粘接性优良等特点,因而获得广泛的使用。
主要用于油浸纸绝缘电缆,分户内式、户外式两类,并区分浇注式电缆终端头和浇注式电缆中间接头,分高压(≤10kv)和低压(≤1kv),按电缆线芯截面大小划分等级,以“个”为计量单位计算工程量,主材费应另计。
另外,浇注式电力电缆中间接头制作安装定额未包括保护盒、铅套管和支架的制作安装,浇注式电力电缆终端头制作安装定额中则未包括电缆终端盒和支架的制作安装,应另行计算。
(3)热缩式电力电缆头制作安装。
塑料电线电缆挤压式挤出模具的设计
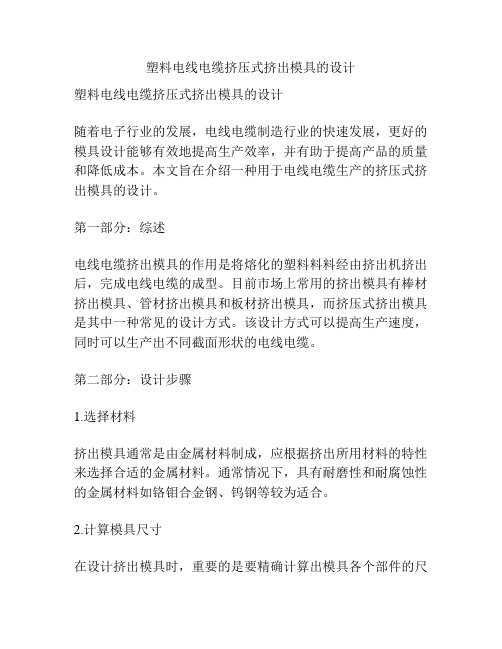
塑料电线电缆挤压式挤出模具的设计塑料电线电缆挤压式挤出模具的设计随着电子行业的发展,电线电缆制造行业的快速发展,更好的模具设计能够有效地提高生产效率,并有助于提高产品的质量和降低成本。
本文旨在介绍一种用于电线电缆生产的挤压式挤出模具的设计。
第一部分:综述电线电缆挤出模具的作用是将熔化的塑料料料经由挤出机挤出后,完成电线电缆的成型。
目前市场上常用的挤出模具有棒材挤出模具、管材挤出模具和板材挤出模具,而挤压式挤出模具是其中一种常见的设计方式。
该设计方式可以提高生产速度,同时可以生产出不同截面形状的电线电缆。
第二部分:设计步骤1.选择材料挤出模具通常是由金属材料制成,应根据挤出所用材料的特性来选择合适的金属材料。
通常情况下,具有耐磨性和耐腐蚀性的金属材料如铬钼合金钢、钨钢等较为适合。
2.计算模具尺寸在设计挤出模具时,重要的是要精确计算出模具各个部件的尺寸及其相对位置。
这需要根据所生产的电线电缆的要求来确定模具的截面形状、尺寸和材料厚度等参数,以保证电线电缆能够达到预期的性能指标。
3.模具设计在模具设计过程中,需要考虑到电线电缆挤出过程中塑料的熔化、流动和固化等工艺要素,并在此基础上设计合理的挤出模具结构。
一般来说,挤压式挤出模具应该包括进料区、形状调整区、定位区和出料区等部分,每个部分都有其独特的设计要求。
进料区:该部分应该具有良好的熔融流动性,容易使熔体堆积并形成压缩力以便推动塑料料料向模具内部流动。
形状调整区:在翻转和拉伸过程中,该部分应对挤出物的截面尺寸、圆度等进行调整。
在此过程中,应使用可调整的辊轮和成型板等工具。
定位区:该部分主要用于保持挤出物的固定位置,以确保产品尺寸的稳定性。
在设计中,应该考虑挤出物的流动特性,以便为其提供适当的压紧力,来保持其位置。
出料区:在该部分,挤出物经过剪切、冷却和质检等处理后即可完成。
4.模具制造模具制造需要使用CNC加工设备,以确保模具的精度和质量。
在制造过程中,还需要定期检查和调整模具尺寸,以确保其能够满足生产要求。
电缆模具计算公式
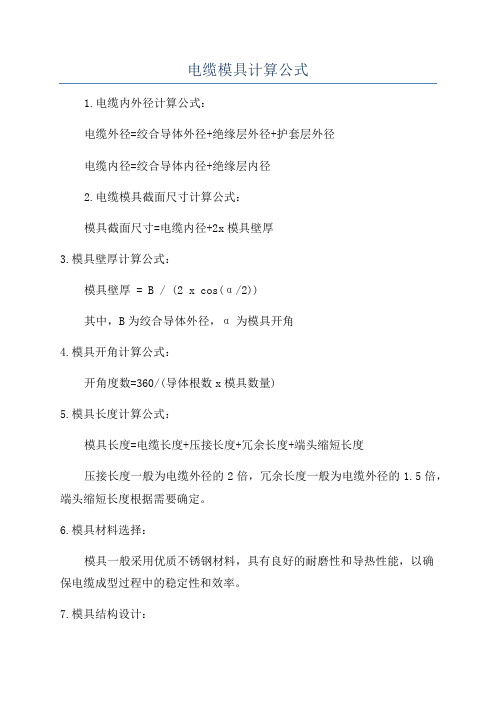
电缆模具计算公式
1.电缆内外径计算公式:
电缆外径=绞合导体外径+绝缘层外径+护套层外径
电缆内径=绞合导体内径+绝缘层内径
2.电缆模具截面尺寸计算公式:
模具截面尺寸=电缆内径+2x模具壁厚
3.模具壁厚计算公式:
模具壁厚= B / (2 x cos(α/2))
其中,B为绞合导体外径,α为模具开角
4.模具开角计算公式:
开角度数=360/(导体根数x模具数量)
5.模具长度计算公式:
模具长度=电缆长度+压接长度+冗余长度+端头缩短长度
压接长度一般为电缆外径的2倍,冗余长度一般为电缆外径的1.5倍,端头缩短长度根据需要确定。
6.模具材料选择:
模具一般采用优质不锈钢材料,具有良好的耐磨性和导热性能,以确
保电缆成型过程中的稳定性和效率。
7.模具结构设计:
模具结构要合理,能够满足电缆的成型要求,并考虑到模具的拆装和维护操作便利性。
总结:电缆模具计算需要根据具体的电缆尺寸和形状要求,进行综合计算和设计,以确保电缆成型的准确性和质量。
以上是一些常用的电缆模具计算公式,但实际设计时还需要结合具体情况进行调整和优化。
电缆厂模具管理制度

第一章总则第一条为加强电缆厂模具管理,提高模具使用效率,确保产品质量,降低生产成本,特制定本制度。
第二条本制度适用于电缆厂所有模具的管理和使用。
第三条模具管理应遵循“统一领导、分级管理、责任到人、维护保养”的原则。
第二章模具的分类与编号第四条模具按用途、结构、材质等分为以下几类:1. 成型模具:包括挤压模具、拉拔模具、绞合模具等。
2. 焊接模具:包括焊接模具、压接模具等。
3. 附件模具:包括绝缘子、接头等附件模具。
第五条模具应统一编号,编号格式为“厂名+模具类别+顺序号”。
第三章模具的采购与验收第六条模具采购应严格按照生产计划和设计要求进行,确保模具质量符合国家标准和行业标准。
第七条模具采购后,应由采购部门组织验收,验收内容包括:1. 模具型号、规格、数量是否与采购单相符;2. 模具外观是否有损伤;3. 模具尺寸、精度是否符合要求;4. 模具材质是否符合设计要求。
第八条验收合格的模具应填写验收报告,并由相关部门负责人签字确认。
第四章模具的入库与保管第九条新购模具或经维修、改造后的模具应进行入库登记,包括模具编号、名称、规格、数量、采购日期、验收日期等信息。
第十条模具应按照分类、规格、材质等进行分区存放,存放环境应干燥、通风、防尘、防锈。
第十一条模具应定期进行检查和维护,发现异常情况应及时处理。
第五章模具的使用与维护第十二条模具使用前应进行试模,确认模具性能符合生产要求。
第十三条模具使用过程中应严格按照操作规程进行,避免操作不当导致模具损坏。
第十四条模具使用后应及时清理,防止模具表面粘附异物。
第十五条模具应定期进行维护保养,包括润滑、清洁、检查等。
第六章模具的维修与改造第十六条模具出现故障或磨损严重时,应及时进行维修或改造。
第十七条模具维修或改造应由专业人员进行,确保维修或改造质量。
第十八条维修或改造后的模具应重新进行验收,合格后方可投入使用。
第七章模具的报废与回收第十九条模具达到使用寿命或损坏严重无法修复时,应予以报废。
电线电缆挤塑模具装配的注意事项

电线电缆挤塑模具装配的注意事项(1)安装说明,在安装时应该注意。
支撑架的锚固件必须牢固地埋在水泥层中;沟渠两侧的支撑面必须平坦且牢固。
(2)建议选择标准尺寸进行设计和施工。
(3)扁钢方向为承重(支撑)方向,扁钢长度根据沟(井)宽度确定。
(4)根据沟槽(井)长度排版,取符合加工模数的标准板宽,板与板之间留有间隙;长度小于1米的沟(井)剩余部分按模数确定尺寸;根据沟(井)宽和承重要求,选择钢格栅板型号。
电缆槽模具有着先进的科技发展历史,电缆槽模具具有易脱模、韧性强、使用寿命长等特点。
一般生产能力大的模具制造都要使用高性能材料,不仅可以将模具的耐久性提高到一个新的水平,还可以对这类模具材料进行低真空表面强化处理。
模具要求精度高,、形状复杂,模具制造周期较长,模具材料本身的成本远小于加工费的成本。
最后是模具的高强度,是否有能力穿、,耐热、,耐压,只有强度符合标准的产品才能经得起市场的考验。
在我国模具吸引住了中国的顾客,现阶段,从的宏观经济政策、制造行业发展趋势、国际性和中国的市场需求看,大中型高精密繁杂电缆槽模具的国际性、中国的市厂侈大,中国铝压铸模具商品早已深受店家认同。
电缆槽模具的原料一般有塑胶注塑工艺与钣金件钢模具成形二种,预制件塑胶模具选用聚丙烯塑料颗粒历经塑料机高温解决引入事先提前准备好的预制件模芯之中,待历经制冷解决以后成形预制件模具;预制件钢模具以3-8mm的不锈钢板历经打卷,裁切,造型设计,结构加固,电焊焊接,组装,打磨抛光等多道办理手续制作而成。
电缆槽钢模具的制要亲身经历好几个工艺流程。
最先要以3-8mm厚钢板为原材料,历经弯折、裁切、外观设计、结构加固、电焊焊接、拼装、打磨抛光等多道加工工艺生产制造而成的。
其本身是用于生产混凝土电缆槽的板金钢模具,其生产出的制成品适用范围是在铁路和公路的电缆槽,并且在生产的全过程中不用设备抑制,只必须用混凝土、水泥砂浆等原材料与一套振动台来做相互配合即就行。
电缆挤塑模具配模及分析计算软件

电缆挤塑模具配模及分析计算软件电缆挤塑模具配模是指根据电缆挤塑工艺要求,选择合适的模具尺寸,使得电缆在挤塑过程中能够顺利通过模具并获得理想的挤塑效果。
电缆挤塑模具配模是一个非常重要的环节,它直接影响到电缆产品的质量和生产效率。
因此,一个好的模具配模工具是必不可少的。
电缆挤塑模具配模及分析计算软件可以提供多种配模方法和算法,根据工程师输入的电缆尺寸和挤塑工艺参数,自动生成最佳的模具尺寸和结构。
同时,软件还可以进行电缆挤塑过程的模拟计算,包括挤塑力、温度分布、应变分布等工艺参数的计算。
工程师可以通过分析计算结果,调整模具设计参数,进一步优化模具结构,实现更好的挤塑效果。
1.模具尺寸和结构设计:根据输入的电缆尺寸和挤塑工艺参数,自动生成最佳的模具尺寸和结构。
软件可以考虑多种模具设计因素,如模具芯棒尺寸、挤塑力分布等。
2.分析计算功能:进行电缆挤塑过程的模拟计算,包括挤塑力、温度分布、应变分布等工艺参数的计算。
软件可以提供多种计算方法和算法,帮助工程师全面了解电缆挤塑过程。
3.优化设计功能:根据分析计算结果,对模具结构进行优化设计。
软件可以根据工程师的优化要求,自动调整模具设计参数,实现更好的挤塑效果。
4.数据管理和共享:软件可以保存和管理设计计算过程中产生的数据,方便工程师进行后续的分析和共享。
电缆挤塑模具配模及分析计算软件的使用可以大大提高电缆挤塑模具设计和分析计算的效率和准确性,降低模具设计成本,改善电缆产品质量。
与传统的手工设计方法相比,这种软件具有更高的自动化程度和智能化水平,减少了人为因素的干预,提高了工作效率。
电缆模具管理制度

电缆模具管理制度第一章绪论一、背景和意义电缆模具是电缆生产中不可或缺的重要工具,在生产过程中起到了至关重要的作用。
电缆模具管理制度是为了规范电缆模具的使用和管理,确保电缆生产的质量和效率,保护电缆模具的安全,降低生产成本,提高生产效率而制定的管理规范。
电缆模具管理制度对于企业的发展和生产都具有重要的意义。
二、制度依据本制度的制定依据是中华人民共和国相关法律法规和国家标准,以及企业的相关规定和要求。
第二章电缆模具管理的基本要求一、模具管理的目标电缆模具管理的目标是保证电缆生产的正常进行,降低电缆生产成本,提高电缆生产效率,确保电缆质量。
二、模具管理的原则1.全员参与:所有员工都要参与电缆模具管理工作,共同维护模具的完好和安全。
2.分类管理:根据模具的不同特点和用途进行分类管理,确保模具的有效利用和管理。
3.合理使用:员工要善于使用模具,并根据模具的要求进行正确操作,避免模具损坏。
4.定期检查:定期对模具进行检查和维护,及时发现问题并加以解决。
5.安全第一:模具管理过程中要始终把安全放在首位,确保员工的人身安全。
第三章电缆模具管理的组织架构一、责任部门公司将设立专门的模具管理部门,负责电缆模具的采购、使用、维护和报废等工作。
二、职责分工1.模具管理部门负责电缆模具的采购、存放和管理工作。
2.生产部门负责模具的使用和操作工作。
3.质量部门负责对模具的质量进行监督检查。
4.安全保卫部门负责模具使用过程中的安全管理工作。
5.员工要根据工作职责做好模具管理工作。
第四章电缆模具的管理流程一、采购管理1.模具管理部门根据生产需要制定模具采购计划。
2.根据采购计划选择合适的模具供应商进行采购。
3.采购完成后,模具管理部门负责对模具进行入库登记和分类存放。
二、使用管理1.生产部门要根据生产计划合理安排模具的使用。
2.员工要对模具进行正确操作,杜绝不当操作导致模具损坏。
3.使用过程中发现模具有损坏应立即上报并停止使用。
电缆公司模具管理制度

第一章总则第一条为确保电缆公司模具的安全、高效、经济运行,提高产品质量,降低生产成本,特制定本制度。
第二条本制度适用于公司所有模具的采购、使用、维护、保养、报废等各个环节。
第三条公司各部门应严格遵守本制度,确保模具管理工作的规范化和标准化。
第二章模具采购管理第四条模具采购应遵循以下原则:1. 经济性:在保证模具质量的前提下,选择性价比高的供应商。
2. 合理性:根据生产需求,合理选择模具的规格、型号和数量。
3. 先进性:选用技术先进、性能优良的模具,提高生产效率。
第五条模具采购流程:1. 需求部门提出模具采购申请,填写《模具采购申请单》。
2. 采购部门对申请进行审核,确定模具采购方案。
3. 采购部门与供应商进行洽谈,签订采购合同。
4. 采购部门验收模具,确保模具质量符合要求。
第三章模具使用管理第六条模具使用前,操作人员应接受专业培训,了解模具的结构、性能、操作方法及注意事项。
第七条模具使用过程中,操作人员应遵守以下规定:1. 严格按照操作规程进行操作,确保模具安全运行。
2. 注意观察模具运行状态,发现问题及时上报。
3. 定期检查模具,发现异常情况立即停机检查。
4. 避免人为损坏模具,延长模具使用寿命。
第八条模具使用过程中,严禁以下行为:1. 擅自调整模具结构。
2. 使用损坏或变形的模具。
3. 在模具上刻划、涂鸦。
第四章模具维护保养第九条模具维护保养应遵循以下原则:1. 定期保养:根据模具使用频率和运行状况,制定合理的保养计划。
2. 预防为主:在模具出现故障前进行预防性保养。
3. 保养内容:包括模具表面清洁、润滑、紧固等。
第十条模具维护保养流程:1. 操作人员每天进行日常保养。
2. 模具维修人员每月进行一次全面保养。
3. 发现模具故障,及时上报并安排维修。
第五章模具报废管理第十一条模具达到以下情况之一,应予以报废:1. 模具磨损严重,无法修复或修复成本过高。
2. 模具结构损坏,无法保证产品质量。
3. 模具技术落后,无法满足生产需求。
07室内光缆生产中的模具设计

附件7室内光缆生产中的模具设计李然山一光缆护套的挤出1 光缆护套挤出光缆护套是光缆中最重要的结构部件之一,它关系到光缆在各种敷设条件下对环境的适应性及其在使用寿命期内光缆传输性能的长期稳定性。
因此,光缆护套的塑料挤出及成型是光缆生产中非常重要的工艺,在室内光缆的生产中尤其重要。
下面对光缆护套挤出及成型工艺做一简单介绍。
通常塑料挤出机常用的全螺纹螺杆如图1-1所示。
输送沟深度螺杆直径螺杆翼距计量沟深度图1-1 全螺纹螺杆螺杆分三个区段:馈料区、塑化区及混练计量区。
在料斗口到馈料区一段的料筒内有纵向沟槽,因而从料斗进馈料区的塑料被螺杆轴向推进,而无切向摩擦。
在馈料区的塑料基本上应是固体粒状塑料,但为了进入压缩塑化区时及时塑化,因此需受热而处于熔化初期的状态。
所以馈料区的温度控制是相当重要的工艺条件。
通常为了除去塑料粒子可能因受潮而凝结在料粒表面的水分,在加热干燥料斗中加温鼓风而使这些水分和料粒周围的空气一起通过加热漏斗被排出。
料粒干燥加热的温度必须严格控制。
温度太低,干燥效果差,料温过高,塑料软化,影响料粒在馈送区的推进。
鉴于同一理由,加料斗部的温度不能太高。
为防止从料筒传过来的热量的影响,加热口需同冷水冷却,以保证入料通畅。
在塑化压缩段,料粒从固体向熔融态过渡,螺杆的螺纹深度减小,以增加对塑料的挤压剪切力,加热温度也相应提高。
常用的全螺线杆对塑化的均匀熔化能力有先天不足,其原因可作如下说明:料粒的熔化起始于塑料与金属的交界面处,如图1-2所示。
通过料筒传送的热量,使与料筒邻接的固体料粒的表面熔融,形成薄的熔融膜。
图1-2 塑化区螺槽中塑料熔融的性状图1-3 屏障式螺杆的工作原理另外通过料粒与料筒的剪切发热,固体料粒继续熔融,使沟内底和侧部形成熔融塑料池。
熔融的塑料部分不再受到摩擦和剪切,并继续被加热。
而被熔融部分包围的固体料粒既不能与料筒剪切,又因塑料本身是不良热导体的特性,在高出料率的情况下不可能通过热传导而熔化均匀。
电缆工业设计中的挤塑模具设计、配模关键环节探讨

抽取芯线真空方式来补偿加工中的配模误差问题。
图1挤压式模芯示意图图2挤压式模套示意图部门提供,并协助实验,对本文有所贡献,在此鸣谢。
电缆企业兼职见习生。
Science&Technology Vision科技视界注意的问题:图3挤管式模芯示意图挤管式模芯的结构尺寸,除定径区外,其余外形尺寸与挤压式模芯设计基本相同。
a.模芯内径3-1:模芯内孔直径,设计时应该选用适中模芯壁厚度,材料则选择的耐磨性强的合金钢材质。
依据产品工艺规定线芯(缆芯)尺寸大小,及塑料材质等要求设计。
设计模芯内径的原则为:线芯尺寸较小为宜,线芯直径+(1~2)mm;缆芯直径+(3~8) mm,通常将模芯内孔径设计加工取整数为宜,b.模芯外圆柱直径3-2:模芯定径区外圆柱直径,决定了模芯定径尺寸及其壁厚。
壁厚的选择,既要考虑模芯使用的寿命,又得参考塑料的拉伸比特性,及保证线缆绝缘或护套层的挤包松紧程度。
通常的设计原则为:模芯内径+2(1.0~2.5)mm,即模芯嘴壁厚为1.5~ 2.5mm。
选择的数值不能太大,拉伸比过大,按工艺选择的绝缘料层,在加工时拉伸强度过大,而后的热延伸率,;图4如图C所示,半挤管式模具,在线的另一种模具形式。
有管状承径部分,比较短。
内模承端面的挤出方式为半挤管式。
这另一种过渡形式,通过对调模另一种方便实用挤出方式。
取了挤压式模具不易调偏芯的缺格的绞合线绝缘,和要求挤包柔软性较差的线芯或缆芯呈现出会产生偏芯等现象出现。
绝缘、护套挤出的工艺配模科技视界Science &Technology VisionScience &Technology Vision 科技视界(2)在加工生产选铠装电缆时,模芯模套的选择,要十分关注铠装电缆有钢带接头的存在,模芯模套选择过小,容易造成模芯刮坏钢带,破坏电缆的绝缘塑料层。
反之,模芯模套选择过大,绝缘护套过松,严重影响线缆的内在参数和外观质量。
(3)选配模具要依据工艺文件为准,模芯模套选配原则上要按工艺文件的配模表为准,实际生产中,线芯或缆芯的最大直径加放大值;模套按模芯直径加塑料层标称厚度加放大值。
- 1、下载文档前请自行甄别文档内容的完整性,平台不提供额外的编辑、内容补充、找答案等附加服务。
- 2、"仅部分预览"的文档,不可在线预览部分如存在完整性等问题,可反馈申请退款(可完整预览的文档不适用该条件!)。
- 3、如文档侵犯您的权益,请联系客服反馈,我们会尽快为您处理(人工客服工作时间:9:00-18:30)。
浙江三科线缆有限公司模具有关知识1模具的分类此类模具一般称为线模,可分圆模和型模,常用线模材料有钻石模、硬质合金模、聚晶模等。
a钻石模:钻石模也称金刚石,具有最高的硬度,耐磨,但价格较贵。
在拉丝中,一般用在拉小规格单丝,如Φ0.40mm及以下规格。
b硬质合金模:在拉伸生产中,过去使用的钨钢模全为硬质合金模所代替的。
因为硬质合金模拉伸模与钢模相比具有:耐磨性较好,抛光性好、对被加工金属的粘附性小,摩擦系数小,导热系数高和具有很高的耐腐蚀性。
c 聚晶模:也称人造钻石,是目前最常用的模丝模,它具有耐磨性,但也有不足之处就是生产出产品表面不光滑。
d 钨钢模:目前常用于铝拉,且使用寿命较短,一般用于过桥模,钨钢模耐磨性一般、价格低廉,其强度不适合于铜拉,拉制线芯表面不光滑。
2模孔结构2.1入口区:一般有圆弧,便于拉制线材进入工作区,不被模孔边缘所损伤;润滑液储蓄、并起到润滑拉制线材作用,在拉伸模孔中靠这部分来加大工作区的高一般为模坯总高H的25%,角度为60度。
2.2工作区:是整个模孔的重要部分,金属拉伸塑性变形是该区进行的就是金属材料通过此区由尺寸的截面。
此区的选择主要是高度和锥角,高度的选择原则是:a)拉制软金属线材应拉制硬金属线材为短,b)拉制小直径线材应拉制较大直径线材为短,c)湿法拉伸应干式润滑拉伸为短,d)一般为定径区d的1~1.4倍。
工作锥角根据下列原则选择:a)压缩率越小,工作锥角越小,b)拉制材料越硬,工作锥角越小,c)拉制小直径的材料的材料为小,一般有金属及其合金拉伸时,角度为16~26°,一般拉铜线圆锥角为16~18°,拉铝线时圆锥角为20~24°。
2.3定径区:它的作用是使制品得到最终尺寸,其高度的选择原则是:a)拉制软金属材料较拉制金属材料要短,b )拉制大直径材料应较拉制小直径的炎短,c )湿式拉伸较之干式润滑拉伸的为短,一般选择h=0.5~1.0d。
2.4出口区:出口区是拉制材料离开模孔的最后一部分,它能保护定径区不致于崩裂,出口锥角可避免金属线材被定径的出口处损伤和停机时线倒退被括伤,一般为45°。
金属的强度极限与拉伸应力之比称为拉伸的安全系数。
它的制范围:1.4~2.0。
电缆行业紧压成型类模具最常见的是异型压轮,适用于多芯电缆线芯的压制。
按其用途及角度主要分:180°两芯电缆用、120°三芯电缆用、90°四芯或3+1芯电缆及3+2或4+1芯电缆用。
也有将3+1芯、3+2芯及4+1芯电缆用紧压成型模具细分为:90°、100°等。
圆形线芯经异型压轮紧压后,可获得我们设计给定的形状,从而较小电缆的外径,节省材料。
压轮的设计面积S与线芯计算面积S1的关系为:S=S1/kk—填充系数,等于紧压系数k1×延伸系数k2。
根据线芯截面大小,一般:70mm2及以下,k1取0.84,k2取1.03;120 mm2~185 mm2,k1取0.83,k2取1.03;240 mm2及以上,k1取0.85,k2取1.02。
以上均为全国标线芯的经验值,供大家可以参考,针对目前导体多元化的情形,k值一定需经验证后才能知晓。
影响S值的关键因素有大圆弧半径R及扇高H。
因R、H值的计算公式较为烦琐,在此我就不详细说明,大家可以参考电线电缆手册第一册P1133页相关资料。
此类模具(图1)的设计主要是根据成缆模架的装配尺寸决定成缆压模的外形尺寸,其孔径根据我们成缆缆芯的外径来决定。
注意的是,在模具的两端有圆弧过渡,在进线端需取一个较大圆弧来保护线芯,其主要计算方法可以采用下列方法(本方法是实践总结得出,仅供大家参考):图11、测出成缆绞笼的最大外径D1,测出绞笼至压模架的距离L,利用三角形计算出角度α,见图2。
图22、将α角引入到成缆模具中,从B点作α角线段BA与端面交于A点,作AB垂直平分线CO,作BO线与中心线垂直并相交CO线与O点,得到∠COB=α,设计时根据模架尺寸给定成缆压模的总长L1,设计给定成缆模定径区长度L2,出线区长度等于圆弧半径(一般R1取5或10),通过求三角函数关系得到我们需要的大圆弧半径R=OB(见图3):图3cosα=(L1-L2-L3)/ABsinα=(0.5×AB)/ OB通过以上公式,可以计算得到大圆弧半径R=OB。
模具是产品定型的装置,是塑料挤出全过程中最后热压作用装置,其几何形状、结构形式和尺寸,温度高低、压力大小等直接决定电缆加工的成败,因此任何挤塑产品模具的设计、选配及其保温措施都受到高度重视。
在用塑料挤出机挤制电线电缆的绝缘层和护套层时,模具是控制塑料挤包层厚度的关键。
一般挤出模具按挤出方式可分为:挤压式、挤管式、半挤管(挤压)式三种。
其配合方式见图:挤压式模具挤管式模具半挤管式模具挤压式模具:模芯与模套定径区内侧有一定的距离,利用压力实现产品最后定型的,塑料通过挤压,直接挤包在线芯或缆芯上,挤出紧密结实、表面平整光滑。
但其易偏心,使用寿命不长,配模要求较高,挤出线芯弯曲性能不好。
适合用于小规格线芯的挤出;挤包要求紧密、外表要求圆整、均匀的线芯;以及塑料拉伸比较小者等。
挤管式模具:模芯有“长嘴”,配合时一般将模芯嘴与模套口持平,这样就组成挤管式模具。
其是利用塑料的可拉伸性,与挤压式模具相比,具有高效率、易调偏、挤出线芯的弯曲性能好、使用寿命长、配模互换性强等优点,但在挤出致密性、挤出质量等方面不如挤压式模具。
半挤管式模具:又称半挤压式模具,模芯有“短嘴”,一般模芯模嘴在模套定径区的1/2处。
半挤管式模具与挤管式模具大体相同,只是模嘴长度比挤管式短,模套定径区长度也比挤管式稍短,其吸取了挤管式和挤压式的优点,改善了上面两种方式模具的缺点,适用性较广,但线芯柔软性较差或线芯弯曲时,不宜采用此类模具挤出。
1模芯1)模芯外锥最大外径ΦD1:该尺寸是由模芯座的尺寸决定的,要求严格吻合,不得出现“前台”,也不可出现“后台”,否则会造成存胶死角,直接影响塑料组织和挤出表面质量。
2)内锥最大外径ΦD2:该尺寸决定于加工条件及模芯螺纹壁厚,在保证螺纹壁厚的前提下,ΦD2越大越好,便于穿线,也便于加工。
3)连接螺纹M1:该尺寸必须与模芯座的螺纹尺寸一致,保证螺纹连接紧密。
4)模芯孔径Φd1:此尺寸是影响挤出质量最大的结构尺寸,按线芯结构特性及其几何尺寸设计。
一般情况下,单线取d1=线芯直径+(0.05~0.15)mm;绞合线芯取d1=线芯外径+(0.3~1.3)mm,具体根据线芯大小而定。
5)模芯外锥最小外径Φd2:实际上是模芯出线端口厚度的尺寸,端口厚度Δ=1/2(d2-d1)不能太薄,否则影响模具使用寿命;也不宜太厚,否则塑料不能直接流到线芯上,且在结合处容易形成涡流区,引起挤出压力的波动,挤出质量不稳定,一般壁厚控制在0.5~1mm为宜。
6)模芯定径区长度l1:l1决定了线芯通过模芯的稳定性,不能设计的太长,否则造成加工困难,工艺要求的必要性也不大,一般取l1=(0.5~1.5)d1。
但同时必须考虑加工制造的因素,太短或太长,都会引起加工困难,在设计时需综合考虑,根据模芯总长度取一个合适的值。
7)模芯外锥角度β:这是设计给出的参考尺寸,从图6中不难看出,tgβ/2=(D1-d2)/[2*(L1-l2)],即(L1-l2)=(D1-d2)/[2*tg(β/2)]。
所以,模芯外锥部分长度可以依据上述决定的尺寸确定,经计算如果太长或太短,与机头内部结构配合不当,可回过头来修正锥角β,然后在计算外锥长度,直至合适。
设计时,一般模芯外锥角度β应不大于45°,与模套内锥角度γ的角度差应控制在3~10°,具体应根据机头实际结构尺寸及挤出材料的不同,选择一个合理角度。
2模套1)模套最大外径ΦD3:根据模套座(或机头内筒直径)设计,一般小于筒径2~3mm,此间隙工艺调整偏心、确保同心度的必须。
2)内锥最大直径ΦD4:这是模套设计的精密尺寸之一。
其尺寸必须严格与模套座(或机头内锥)末端内径一致,否则装配后将产生阶梯死角,这是工艺设计不允许的。
3)模套定径区直径Φd3:这也是模套设计的精密尺寸之一。
要根据产品外径、考虑挤出各工艺参数及塑料特性严格设计。
一般d3=成品标称直径+(0.1~0.3)mm,根据材料的不同,有时则设计为d3=成品标称外径-(0.1~0.3)mm。
4)模套内锥角γ:角γ是由ΦD4、Φd3及模套长度制约的,角γ同时又受到与其配套的模芯的外锥角的制约,需控制模套内锥角γ-模芯外锥角β=3~10°。
若角度差过小,保证不了挤出压力;角度差也不能太大,太大则挤出压力过大,减少挤出量,影响生产效率,可能会引起生产时厚度不能满足我们的工艺要求。
5)模套定径区长度l3:一般取l3=(0.5~1)d3为宜,定径区长些对成型有利,但越长阻力越大,影响产量。
所以当模套孔径d3较大时,不能取上限。
6)模套压座厚度l4:按模套座深度(或机头内筒出口处深度)设计,一般要大0.5~1mm。
7)模套总长L2:这是设计给出的参考尺寸,由模套内锥角γ、模套内锥最大外径ΦD4及模套定径区长度l3来决定。
但还应考虑到,设计的模套在装配时,模套最外端伸出机头部分的长度不宜过长,太长会影响传热效果,导致模套口塑料的温度受到影响,从而影响挤出质量。
1挤管式模芯其结构设计除定径区部分外,其余外形尺寸与挤压式模芯基本相同,现对挤管式模芯定径部分的尺寸设计进行说明。
1)模芯定径区内径Φd1:又叫模芯孔径。
该尺寸根据选用材料的耐磨性、半制品(线芯或缆芯)尺寸的大小及其材质与外径规整程度等进行设计,一般设计为:绝缘时,d1=d线芯+(2~3)mm;护套时,d1=d线芯+(3~7)mm。
通常,在设计模具规格时,应考虑系列化,将模具尺寸调整成整数。
2)模芯定径区外圆柱直径Φd2:从图8中,我们可以看出d2决定于d1及其壁厚δ,即d2=d1+2δ ,这个壁厚的设计既要考虑到模芯的寿命,又要考虑塑料的拉伸特性及挤包紧密程度等因素,一般都设计为d2=d1+2(0.5~1.5)mm,即模芯壁厚为0.5~1.5mm。
3)模芯定径区外圆柱长度l1:该尺寸依照尺寸d1考虑挤出塑料成型特性设计,一般设计为l1=(0.5~1)d1+(1~2)mm。
4)定径区内圆柱长度l2:该尺寸由加工条件及半制品结构特性所决定。
无论如何l2都必须比l1长2~4mm,主要是保证模芯模嘴部分的强度。
2挤管式模套挤管式模套的结构型式与挤压式模套基本相同,如图7所示。
所不同之处是其结构尺寸中的模套定径区的直径d3及其长度l3,必须按与其配合的挤管式模芯来设计1)模套定径区直径d3:该尺寸按挤管式模芯模嘴外圆直径d2、线芯或缆芯外径、挤包塑料厚度等因素来设计。