压铸产品切边模的设计
【设计规范_07】压铸产品相关设计要求

【设计规范_07】压铸产品相关设计要求导读压铸产品开始流行,都忘了是什么时候了,记得moto的刀锋系列就是镁合金压铸的,着实火了一把,现在的手机产品中压铸件使用也越来越多,今天我们就介绍下压铸产品设计的注意事项:1什么是压铸?压铸(英文:die casting)是一种金属铸造工艺,其特点是利用模具腔对融化的金属施加高压。
模具通常是用强度更高的合金加工而成的,这个过程有些类似注塑成型。
压铸设备和模具的造价高昂,因此好的产品结构更为重要,产品不但影响模具寿命,甚至对机台都会有影响;2压铸产品设计要求1.壁厚须力求平均2.孔径与深度关系3.肋与壁厚关系D≦4~5t 在此比例下应不会产生缩水痕,但非必要还是以力求壁厚平均为佳。
4.圆角当T1=T2时,若R2=R1+T1则 R1=T1 ,若R2=0则 R1=1~1.25T1当T2 > T1时,则R1=2/3( T1+T2) & R2=0~(R1+T2)当十字或Y型相接时:当Θ=90°时,则 R1= T1当Θ=45°时,则 R1= 0.7 T1 & R2= 1.5 T1当Θ=30°时,则 R1= 0.5 T1 & R2= 2.5 T15.拔模角3产品结构规避风险设计1.压铸产品进胶与塑胶产品不同,产品必需要有足够的进浇空间,且进浇位置尽量要平缓(不要有较大的高度落差),尽量让进浇平缓均匀,如下图说明:不合理:1.1 两边包胶燕尾槽分布较多,进浇无足够的空间1.2 内框太深,模具上形成高的钢位,阻挡了进浇的流向,且钢位易被冲击腐蚀;1.3外部料位有较大的断开,进浇需走高低差,压铸模不现实改进方式:1.1 取消部分燕尾槽,减少其分布密度1.2 内框深度做浅,其深度尽量控制在2.0MM以内1.3 断开处在装配要求允许的情况下尽量加胶连接起来2.产品进浇尽量避开正面冲击产品通孔,插穿扣位及较小的碰穿孔,如下说明:弊端:2.1.产品进浇正面冲击模具上通孔的碰穿柱,影响进浇的走向2.2.由于碰穿柱较小,正面冲击易致其断裂,压铸后产品通孔不通改进方式:2.1.减少通孔的分布数量,加大孔径,以加强此通孔模具上碰穿柱的强度2.2.此通孔拉胶位可做成沟槽的形式,模具强度较好3.产品内侧壁的厚度不要过于单薄弊端:3.1.由于壁厚过薄,会影响进浇的流动性,导致产品不易打满,影响产品的致密性及整体强度3.2.由于薄壁处强度较弱,产品脱模时易断裂改进方式:3.1.其厚度最小做到0.8MM左右3.2.条件允许下,可做些补丁形式的骨位,加强其强度,如右下效果图4.燕尾包胶槽的设计上图所示的两种燕尾槽形式,在产品压铸后都需冲模冲切成型,由于上左图所示的燕尾槽开口宽度尺寸较小,导致冲模冲头钢位较弱,而且模具加工困难,所冲出的产品精度不易控制,右图形式较为合理,具体如下:1.燕尾槽开口处的尺寸最小在1.8-2.5MM左右,冲模冲头钢位强度相对较理想2.此通孔式的燕尾槽压铸模易成型,有利于模具生产及产品的稳定。
压铸切边模具的设计及应用
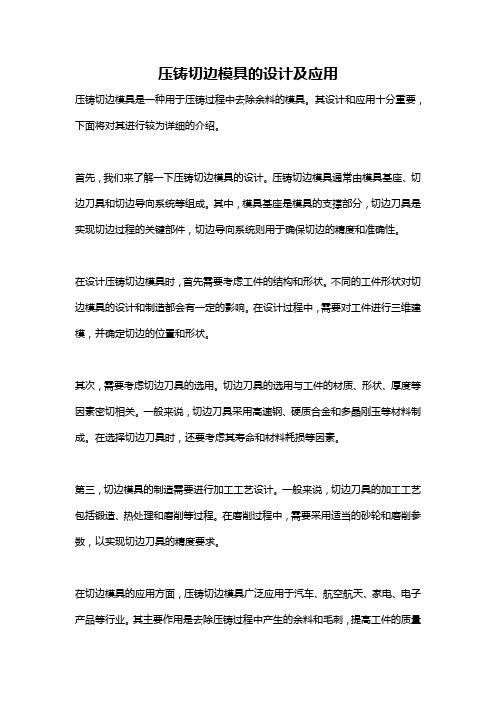
压铸切边模具的设计及应用压铸切边模具是一种用于压铸过程中去除余料的模具。
其设计和应用十分重要,下面将对其进行较为详细的介绍。
首先,我们来了解一下压铸切边模具的设计。
压铸切边模具通常由模具基座、切边刀具和切边导向系统等组成。
其中,模具基座是模具的支撑部分,切边刀具是实现切边过程的关键部件,切边导向系统则用于确保切边的精度和准确性。
在设计压铸切边模具时,首先需要考虑工件的结构和形状。
不同的工件形状对切边模具的设计和制造都会有一定的影响。
在设计过程中,需要对工件进行三维建模,并确定切边的位置和形状。
其次,需要考虑切边刀具的选用。
切边刀具的选用与工件的材质、形状、厚度等因素密切相关。
一般来说,切边刀具采用高速钢、硬质合金和多晶刚玉等材料制成。
在选择切边刀具时,还要考虑其寿命和材料耗损等因素。
第三,切边模具的制造需要进行加工工艺设计。
一般来说,切边刀具的加工工艺包括锻造、热处理和磨削等过程。
在磨削过程中,需要采用适当的砂轮和磨削参数,以实现切边刀具的精度要求。
在切边模具的应用方面,压铸切边模具广泛应用于汽车、航空航天、家电、电子产品等行业。
其主要作用是去除压铸过程中产生的余料和毛刺,提高工件的质量和外观。
在汽车行业中,压铸切边模具被广泛应用于汽车发动机缸体、变速器壳体等零部件的生产中。
通过使用切边模具,可以有效去除铸件表面的毛刺和余料,提高工件的装配精度和密封性能。
在电子产品行业中,压铸切边模具常用于手机、平板电脑、电视等产品的生产中。
通过使用切边模具,可以去除工件表面的毛刺和余料,提高产品的外观质量和用户体验。
在家电行业中,压铸切边模具常用于制造电冰箱、洗衣机、空调等产品的关键零部件。
切边模具的应用可以大幅度改善工件的质量和装配精度,提高产品的性能和可靠性。
总之,压铸切边模具是一种用于压铸过程中去除余料的重要工具。
其设计和应用对于提高工件质量和提高生产效率具有重要意义。
随着科技的不断发展,切边模具的设计和制造技术也在不断革新,将为各行业的生产带来更大的便利和效益。
压铸型(模)设计
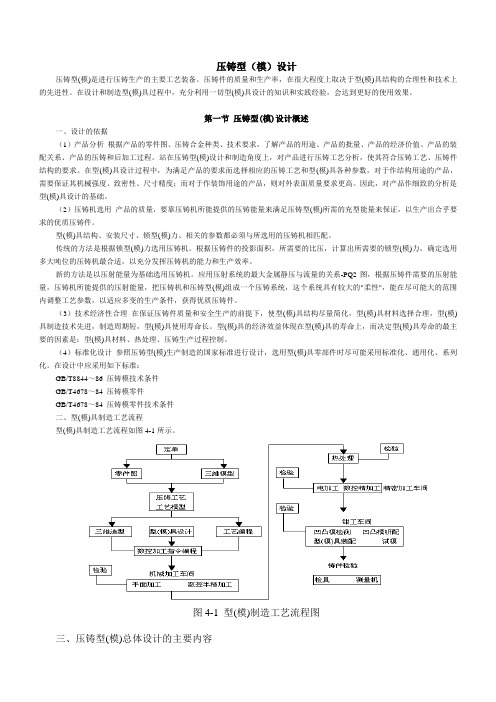
压铸型(模)设计压铸型(模)是进行压铸生产的主要工艺装备。
压铸件的质量和生产率,在很大程度上取决于型(模)具结构的合理性和技术上的先进性。
在设计和制造型(模)具过程中,充分利用一切型(模)具设计的知识和实践经验,会达到更好的使用效果。
第一节压铸型(模)设计概述一、设计的依据(1)产品分析根据产品的零件图、压铸合金种类、技术要求,了解产品的用途、产品的批量、产品的经济价值、产品的装配关系、产品的压铸和后加工过程。
站在压铸型(模)设计和制造角度上,对产品进行压铸工艺分析,使其符合压铸工艺、压铸件结构的要求。
在型(模)具设计过程中,为满足产品的要求而选择相应的压铸工艺和型(模)具各种参数,对于作结构用途的产品,需要保证其机械强度、致密性、尺寸精度;而对于作装饰用途的产品,则对外表面质量要求更高。
因此,对产品作细致的分析是型(模)具设计的基础。
(2)压铸机选用产品的质量,要靠压铸机所能提供的压铸能量来满足压铸型(模)所需的充型能量来保证,以生产出合乎要求的优质压铸件。
型(模)具结构、安装尺寸、锁型(模)力、相关的参数都必须与所选用的压铸机相匹配。
传统的方法是根据锁型(模)力选用压铸机。
根据压铸件的投影面积,所需要的比压,计算出所需要的锁型(模)力,确定选用多大吨位的压铸机最合适,以充分发挥压铸机的能力和生产效率。
新的方法是以压射能量为基础选用压铸机。
应用压射系统的最大金属静压与流量的关系-PQ2图,根据压铸件需要的压射能量,压铸机所能提供的压射能量,把压铸机和压铸型(模)组成一个压铸系统,这个系统具有较大的"柔性",能在尽可能大的范围内调整工艺参数,以适应多变的生产条件,获得优质压铸件。
(3)技术经济性合理在保证压铸件质量和安全生产的前提下,使型(模)具结构尽量简化,型(模)具材料选择合理,型(模)具制造技术先进,制造周期短,型(模)具使用寿命长。
型(模)具的经济效益体现在型(模)具的寿命上,而决定型(模)具寿命的最主要的因素是:型(模)具材料、热处理、压铸生产过程控制。
压铸模具设计方案
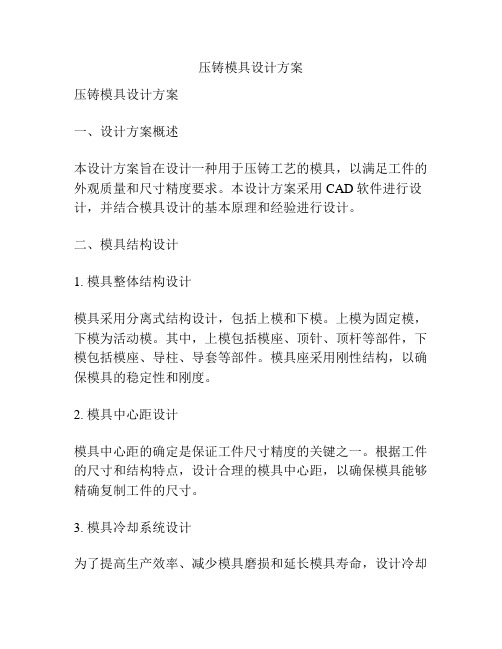
压铸模具设计方案压铸模具设计方案一、设计方案概述本设计方案旨在设计一种用于压铸工艺的模具,以满足工件的外观质量和尺寸精度要求。
本设计方案采用CAD软件进行设计,并结合模具设计的基本原理和经验进行设计。
二、模具结构设计1. 模具整体结构设计模具采用分离式结构设计,包括上模和下模。
上模为固定模,下模为活动模。
其中,上模包括模座、顶针、顶杆等部件,下模包括模座、导柱、导套等部件。
模具座采用刚性结构,以确保模具的稳定性和刚度。
2. 模具中心距设计模具中心距的确定是保证工件尺寸精度的关键之一。
根据工件的尺寸和结构特点,设计合理的模具中心距,以确保模具能够精确复制工件的尺寸。
3. 模具冷却系统设计为了提高生产效率、减少模具磨损和延长模具寿命,设计冷却系统对模具进行冷却。
冷却系统包括冷却孔和进水口,通过冷却水的流动,迅速冷却模具,以提高生产效率和模具寿命。
4. 模具材料选择模具的材料选择是保证模具寿命和使用效果的重要因素。
根据工件的材料和要求,选择适当的模具材料,保证模具具有良好的硬度和耐磨性。
三、模具生产工艺1. 加工工艺规程模具的加工工艺包括数控加工、外圆磨削等。
根据模具的具体结构和工艺要求,制定合理的加工工艺规程,以确保模具的加工质量。
2. 检测工艺模具加工完成后,进行检测以验证模具的质量。
检测工艺包括模具尺寸检测、表面质量检测等,通过合适的检测工艺,确保模具符合设计要求。
四、模具的维护、维修和更换为了保证模具的正常使用和延长其寿命,进行模具的定期维护、维修和更换。
维护工作包括清洁模具、添加润滑剂等,维修工作包括修复模具损伤、更换模具部件等,更换工作包括根据模具磨损程度,定期更换模具部件。
五、结论本设计方案是一种用于压铸工艺的模具设计方案,通过合理的结构设计、材料选择和加工工艺,可以满足工件的外观质量和尺寸精度要求。
同时,通过模具的定期维护、维修和更换,可以保证模具的正常使用和延长其寿命。
铝合金压铸工艺中的模具设计
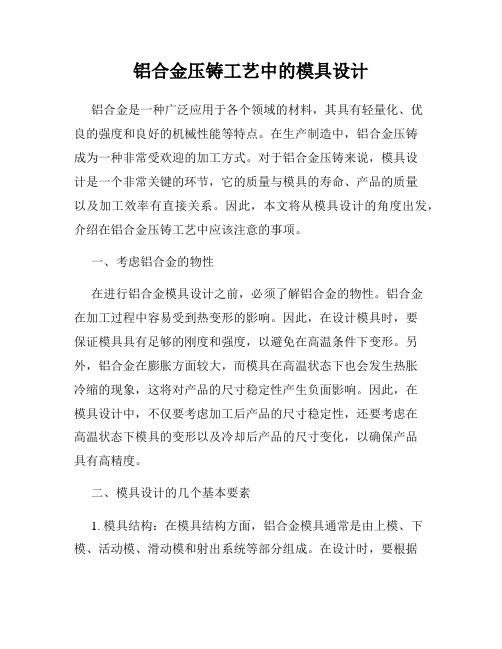
铝合金压铸工艺中的模具设计铝合金是一种广泛应用于各个领域的材料,其具有轻量化、优良的强度和良好的机械性能等特点。
在生产制造中,铝合金压铸成为一种非常受欢迎的加工方式。
对于铝合金压铸来说,模具设计是一个非常关键的环节,它的质量与模具的寿命、产品的质量以及加工效率有直接关系。
因此,本文将从模具设计的角度出发,介绍在铝合金压铸工艺中应该注意的事项。
一、考虑铝合金的物性在进行铝合金模具设计之前,必须了解铝合金的物性。
铝合金在加工过程中容易受到热变形的影响。
因此,在设计模具时,要保证模具具有足够的刚度和强度,以避免在高温条件下变形。
另外,铝合金在膨胀方面较大,而模具在高温状态下也会发生热胀冷缩的现象,这将对产品的尺寸稳定性产生负面影响。
因此,在模具设计中,不仅要考虑加工后产品的尺寸稳定性,还要考虑在高温状态下模具的变形以及冷却后产品的尺寸变化,以确保产品具有高精度。
二、模具设计的几个基本要素1. 模具结构:在模具结构方面,铝合金模具通常是由上模、下模、活动模、滑动模和射出系统等部分组成。
在设计时,要根据铝合金的物性和加工要求来确定模具结构和形状,以达到高效生产的目的。
2. 模具材料:在模具材料的选择方面,应根据铝合金的物性进行选择。
通常,适合用于铝合金模具的材料应具有高强度、高耐磨性和高温耐受性等特点。
目前,常用的模具材料有SKD61、H13和CRM等。
3. 考虑注塑工艺:在进行模具设计时,必须考虑到注塑工艺。
这意味着必须根据注塑工艺的参数来设计模具。
例如,应根据化学成分和温度参数来确定注塑机的射出系统和出口形状,以确保正常的注塑过程。
三、注塑机的选择在进行铝合金压铸加工时,注塑机的选择是非常关键的环节。
不同的注塑机具有不同的投影面积和射程,这会对产品的尺寸稳定性、成型速度和加工效率产生直接影响。
因此,在选择注塑机时,不仅要考虑加工数量和生产周期,还要考虑产品的几何形状、尺寸和质量要求。
四、模具维护模具在长期使用过程中,需要进行定期维护和保养。
切边模的设计
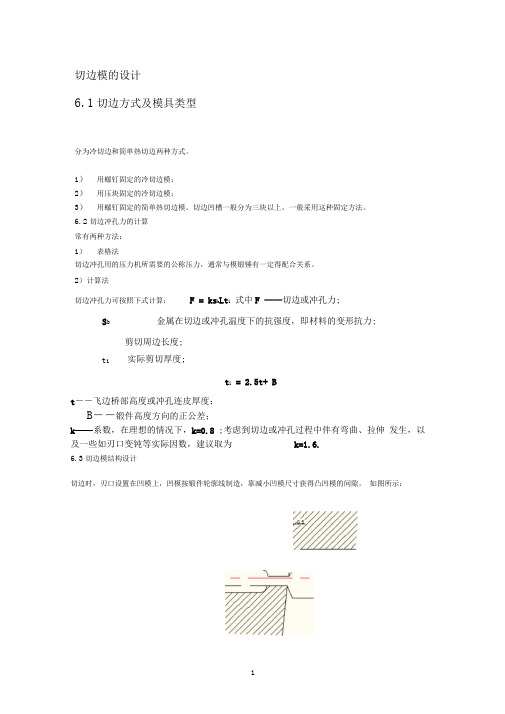
切边模的设计6.1切边方式及模具类型分为冷切边和简单热切边两种方式。
1) 用螺钉固定的冷切边模; 2) 用压块固定的冷切边模;3) 用螺钉固定的简单热切边模。
切边凹槽一般分为三块以上,一般采用这种固定方法。
6.2切边冲孔力的计算常有两种方法:1) 表格法切边冲孔用的压力机所需要的公称压力,通常与模锻锤有一定得配合关系。
2) 计算法切边冲孔力可按照下式计算:F = ks b Lt 1 式中F ——切边或冲孔力;金属在切边或冲孔温度下的抗强度,即材料的变形抗力;剪切周边长度;t 1 = 2.5t+ Bt ――飞边桥部高度或冲孔连皮厚度;B ――锻件高度方向的正公差;k ——系数,在理想的情况下,k=0.8 ;考虑到切边或冲孔过程中伴有弯曲、拉伸 发生,以及一些如刃口变钝等实际因数,建议取为k=1.6.6.3切边模结构设计切边时,刃口设置在凹模上,凹模按锻件轮廓线制造,靠减小凹模尺寸获得凸凹模的间隙。
如图所示:S b t i实际剪切厚度;tana宽度:对小型锻件,b=1.5-2.5mm ;对中型锻件,b=2-3mm 对大型锻件,b=3-5mra 如果锻件各部分的间隙不同,应按最小间隙作为整个凸凹模的间隙。
切边凹模有整体式、和组合式两种,前者用于中小型锻件,特别是形状简单具有 对称性的锻件;后者则用于大型锻件或形状复杂的锻件。
由于油箱盖是对称性的, 故选用整体式。
(1)切边凹模刃口设计切边凹模刃口轮廓形状按锻件在分模面上投影轮廓形状设计。
切边凹模刃口形式 有直刃口,斜刃口和局部斜刃口。
根据分析,可采用局部斜刃口,与斜刃口相比 较,减少了刃口切削加工量,便于制造。
是一种比较经济的形式。
如图所示:切边凹模尺寸飞边桥部高度H■ I minht 1t .Lmin备注<1.6 50 1035 30 1000kN 切边压力机 2~3 55 12 40 35 3150kN 切边压力机 >4601550503150kN 切边压力机)切边凹模其他部分尺寸的确定图中间隙均取d= 0.5mm ,$二彳3-O'0",同时应保证凸模削平后 b 值有一定得350mm ,最长应控制在 (2 )切边凹模的分块 切边凹模的分块原则:1) 分块处便于对位,又不易产生毛刺,而且能保证切边锻件质量,两端分块为好。
压铸工艺流程中的模具设计要点

压铸工艺流程中的模具设计要点压铸是一种常用的金属加工工艺,通过将熔融金属注入模具中,并在固化后取出成型件。
模具设计是整个压铸工艺中的关键环节,决定了成型件的质量和生产效率。
本文将从模具结构设计、材料选择和加工工艺三个方面讨论压铸工艺流程中的模具设计要点。
一、模具结构设计要点1. 合理选择模具结构模具结构的设计应根据产品的形状、尺寸和压铸工艺要求进行合理选择。
一般常见的模具结构包括单腔、多腔、合模和分模等。
对于形状复杂的产品,可以采用多腔结构来提高生产效率。
对于尺寸较大的产品,可以考虑采用合模结构来减少模具成本。
2. 考虑产品的冷却和顶针装置在模具设计中,需要考虑产品的冷却和顶针装置。
冷却系统的设计应能够有效地排除熔融金属的热量,以确保成型件的质量。
顶针装置的设计应满足产品的要求,并保证顶针在压铸过程中的精确位置。
3. 设计合理的浇口和溢流槽浇口和溢流槽是模具设计中的重要组成部分。
设计浇口时应考虑熔融金属的流动性和冷却速度,并确保浇口与产品的结合处处于合适的位置。
溢流槽的设计应考虑金属液体的顺利流动,以避免产生气体和杂质。
二、材料选择要点1. 选择耐磨耐热的材料模具在压铸过程中需要承受高温和高压的作用,因此材料的选择至关重要。
一般采用耐磨耐热的工具钢或合金钢作为模具材料,以保证模具的使用寿命和成型件的质量。
此外,还应考虑材料的加工性能和可靠性。
2. 考虑材料的强度和刚性模具的结构设计需要兼顾材料的强度和刚性。
材料的强度直接影响到模具的承载能力,而刚性则影响到模具的稳定性和精度。
因此,在模具设计中应根据产品的要求选择合适的材料,并进行合理的加工和热处理,以提高模具的性能。
三、加工工艺要点1. 精确计算和控制成型参数在压铸工艺中,成型参数的精确计算和控制是保证成型件质量和加工效率的关键。
成型参数包括注射速度、压力、温度和冷却时间等。
合理选择和控制这些参数,可以避免产生缺陷和变形,提高成型件的精度和表面质量。
压铸工艺及压铸模具设计
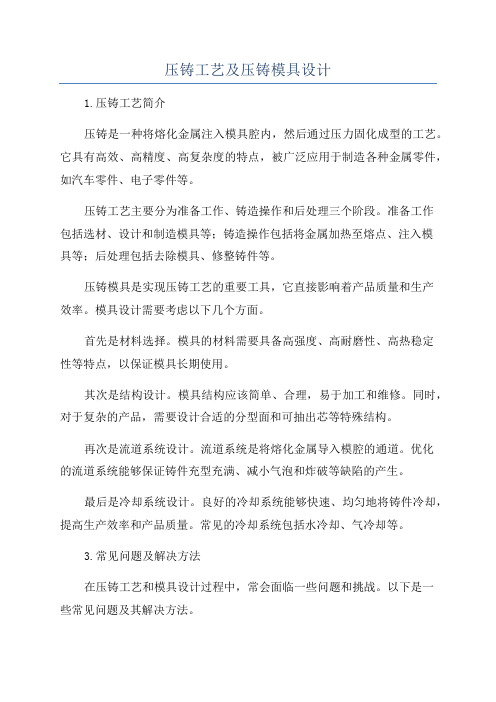
压铸工艺及压铸模具设计1.压铸工艺简介压铸是一种将熔化金属注入模具腔内,然后通过压力固化成型的工艺。
它具有高效、高精度、高复杂度的特点,被广泛应用于制造各种金属零件,如汽车零件、电子零件等。
压铸工艺主要分为准备工作、铸造操作和后处理三个阶段。
准备工作包括选材、设计和制造模具等;铸造操作包括将金属加热至熔点、注入模具等;后处理包括去除模具、修整铸件等。
压铸模具是实现压铸工艺的重要工具,它直接影响着产品质量和生产效率。
模具设计需要考虑以下几个方面。
首先是材料选择。
模具的材料需要具备高强度、高耐磨性、高热稳定性等特点,以保证模具长期使用。
其次是结构设计。
模具结构应该简单、合理,易于加工和维修。
同时,对于复杂的产品,需要设计合适的分型面和可抽出芯等特殊结构。
再次是流道系统设计。
流道系统是将熔化金属导入模腔的通道。
优化的流道系统能够保证铸件充型充满、减小气泡和炸破等缺陷的产生。
最后是冷却系统设计。
良好的冷却系统能够快速、均匀地将铸件冷却,提高生产效率和产品质量。
常见的冷却系统包括水冷却、气冷却等。
3.常见问题及解决方法在压铸工艺和模具设计过程中,常会面临一些问题和挑战。
以下是一些常见问题及其解决方法。
首先是翘曲和变形问题。
由于金属在冷却过程中会有收缩和变形,容易导致铸件产生翘曲和变形。
解决方法可以是增加冷却系统,控制金属温度等。
其次是气孔和缺陷问题。
气孔和缺陷是常见的铸件质量问题,可能是由于金属中的气体未能完全排出或模具内部有不完全填充的区域导致。
解决方法可以是优化流道和冷却系统,增加压力等。
最后是模具使用寿命问题。
模具在使用过程中会受到磨损、冲击和热应力等的影响,容易损坏。
解决方法可以是选用高耐磨材料、增加模具表面硬度等。
4.发展趋势随着科技的发展和需求的变化,压铸工艺和模具设计也在不断发展和改进。
未来的发展趋势主要包括以下几个方面。
首先是数字化和智能化。
通过数字化技术和智能化设备,可以实现对压铸工艺和模具设计的更精确和高效的控制。
压铸模具设计规范,总结了好多天的精品资料

压铸模具设计规范,总结了好多天的精品资料模具设计规范一.模仁的设计1. 模仁最低面处厚度不小于35mm,产品边距模仁边不小于45mm,如制件较大时应相应相应加大。
(具体见附表一和附表二)2. 模仁上如有高的筋或凹槽时,为了制造与维修的方便,应尽可能将模仁做成镶嵌式.3. 为保证顺利脱模,产品内表面就尽可能置于动模,如无明显内表面,应将产品大部分表面置于动模.4. 模仁硬度规定为:HRC:48±1º。
附表一附表二二.模框的设计1. 为防止重复顶出在顶板上形成凹坑,顶板的硬度需保持在HRC48左右.2. 为防止顶板变形以及模架强度,要求每套模架底部加一块底板及支撑柱(EGP),针板导柱(EGP),限位柱(STB) (如下图)喜欢的话关注小编哦3. 顶出限位时需加上限位块,以保护顶针,动模四个角上需做撬模槽(撬模槽深度为8mm),以及动定模框需做四个撬模孔(∮20-30mm 通孔),以方便拆模。
4. 导柱孔的位置应三个相同,其余一个特别向内1~2mm,以防止模具装配时,动定模方向倒置.5. 为方便安装,模具四侧均应开设吊环螺纹孔,同时需考虑平衡问题. 螺纹孔使用M20、M24、M30、M36等规格(需要考虑模具总重量)6. 150吨以下(含150吨)锁模槽尺寸为25*25,150吨以上锁模槽尺寸为30*30.7. 模架材质要求为:AB板材质为S50C,顶出板材质为P20,硬度要求为HRC28º,回位销、导柱导套材质为模架厂标准材质。
8. 模框侧边强度设计及导柱导套,回位梢规范(见附表三)附表三三.滑块的设计1. 滑块的材质应保证一定的强度与硬度(HRC:48±1º),滑块底部需加耐磨板,压条,背部耐磨块。
(附图)喜欢的话关注小编哦2. 为防止承受压力而产生变形,滑块锁紧块要保证足够的强度(HRC:48±1º)。
3. 滑块与抽芯在开模方向上需完全定位。
压铸产品切边模的设计

压铸产品切边模的设计Last revision on 21 December 2020切边模的设计该零件是采用的是一模两件的结构方式,分型面不是在产品的同一个平面上,孔的公差要求不高,唯一的难点就在于一模两件的产品结构在压铸生产过程中是存在变形的, 那么我们如何去设计这一切边模才能满足产品的要求既然产品存在变形,那么产品的固有的工艺参数下,产品的变形是存在一定规律性,我们只有通过一系列生产跟踪和试验摸索,才能找到了这一变形的规律,只要该产品的变形规律确定,那么这一套切边模设计和制作将不存在任何的问题.从以上的产品的要求我们最终确认切边和冲孔由一套模具完成,并且产品的两个件都必须有独立的模腔,只有这样才方便我们在后期根据产品的变形量对每一模腔进行调整,以满足产品的要求(如图所示2).a) 通常的情况下,铸件的飞边都是在冷态下进行,因此要求切边模的材料应有较高的综合机械性能,良好的耐磨性和耐疲劳性.热处理硬度的硬度推荐为HRC56-60b) 切边模凸凹模间隙选择是非常重要的,如果间隙选择过大,那么会造成切边后的产品浇口余根过高,飞边过高,无法满足客户的要求; 如果间隙选择过小,那么会导致飞边卡的模具上,难于退料,影响模具的使用寿命.为了利于凸凹模为准和产品的要求,我们一般的凸凹模单边间隙应该在之间.切边过程中的工艺影响产品在切边每个循环中,我们一定要严格按照切边工艺执行,主要影响的工艺有:首先,模具内有残留的飞边,会造成产品表面有压痕,所以每一循环我们都对模具进行清理,可以使用自动吹气系统和手动气枪将模具表面的飞边吹干净。
其次,产品没有完全放置在切边模,就已经启动切边按钮,造成产品切伤。
最后,我们要对产品进行100%的自检,特别是切边涉及到的浇口、集渣包的部位、孔内以及相关的位置,都是特别要关注的地方。
自检在切边工序中是非常重要的,因为及时发现了问题,才能针对出现的问题提出解决方案,否则将会造成批量事故。
压铸模具设计参考
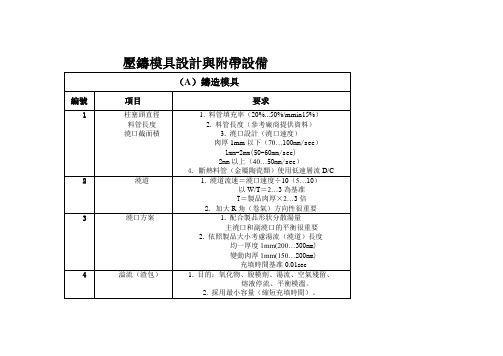
3.降低鑄造壓力。
4.考慮脫械劑的類型。
5. 機械頂出平衡。
(A)鑄造模具
編號
項目
要求
14
起泡、氣孔
1.開模時模溫高(冷卻時間、模具冷卻、湯溫)。
2.低速射出太快、太短(卷氣)。
3.高速射料位置優化(例:在模腔1/3處起高速)。
4.溶液中含氣量過多。
5.澆口方案改進。
6.須有氣孔和縮孔的分辯對策。
3.模溫分佈。
4.表面處理(長中子抽出斜度0.5度以下)。
5.抽出傾斜凸1.5度以上、凹1.0度以上。澆口部壁2.0度以上、分流錐部3度以上。
6.自動噴霧A:中子內側,中子進入噴霧(沒壓中子)模具內安裝噴霧嘴(注意中子行程)。B:噴霧液與毛邊的清掃,中子滑動部位加抽水孔。
7.脫械劑的類型。
13
變形
1.加大頂針尺寸和數量。
壓鑄模具設計與附帶設備
(A)鑄造模具
編號
項目
要求
1
柱塞頭直徑
料管長度
澆口截面積
1.料管填充率(20%...50%/mmin15%)
2.料管長度(參考廠商提供資料)
3.澆口設計(澆口速度)
肉厚1mm以下(70…100mm/sec)
1mm-2mm(50-60mm/sec)
2mm以上(40…50mm/sec)
1.搭配足夠熔解能力的熔解爐。
2.溶液氣化少(爐體構造、燃燒器的選擇、隔熱)。
3.材料成份變化少。
4.溶液處理容易。
5.爐內容易清理。
6.節省能源。
6
保溫爐
1.溶液溫度穩定(在設定溫度的±5度為基准)。
2.溶液氧化少。
7
水冷卻系統
压铸模具结构及设计

压铸模具结构及设计压铸模具结构设计压铸模具结构设计目录1.压铸模具的结构2.压铸模具结构设计应注意事项3.内模4.外模5.模脚6.导柱与导套7.回位销8.拔模力计算9.顶出销10.角销11.压铸模具材料12.附录1 压铸模具的结构压铸模具一般的结构如图1.导柱2.固定外模(母模) 3分流子镶套 4.分流子5固定内模6角销7滑块挡片8滑块9.可动内模10.可动外模(公模) 11.模脚12.顶出板13.顶出销承板14.回位销15.导套2.压铸模具结构设计应注意事项(1)模具应有足够的刚性,在承受压铸机锁模力的情况下不会变形。
(2)模具不宜过于笨重,以方便装卸修理和搬运,并减轻压铸机负荷。
(3)模穴的压力中心应尽可能接近压铸机合模力的中心,以防压铸机受力不均,造成锁模不密,铸件产生毛边。
(4)模具的外形要考虑到与压铸机的规格的配合:(a)模具的长度不要与系杆干涉。
(b)模具的总厚度不要太厚或太薄,超出压铸机可夹持的范围。
(c)注意与料管(冷室机)或喷嘴(热室机)之配合。
(d)当使用拉回杆拉回顶出出机构时,注意拉回杆之尺寸与位置之配合。
(5)为便于模具的搬运和装配,在固定模和可动模上方及两侧应钻螺孔,以便可旋入环首螺栓。
3 内模(母模模仁)(1)内模壁厚内模壁厚基本上不必计算其强度,起壁厚大小决定于是否可容纳冷却水管通过,安排溢流井,及是否有足够的深度可攻螺纹,以便将内模固定于外模。
由于冷却水管一般直径约10mm,距离模穴约25mm,因此内模壁厚至少要50mm。
内模壁厚的参考值如下表。
(2)内模与外模的配合内模的高度应该比外模高出0.05-0.1mm,以便模面可确实密合,并使空气可顺利排出。
其与外模的配合精度可用H8配h7,如下图所示。
(3)内模与分流子的配合分流子的功用是将熔汤由压铸机导至模穴内,因此其高度视固定模的厚度而定。
分流子的底部与内模相接,使流道不会接触外模,如下图,内模与分流子的配合可用H7配h6。
压铸模模具设计(一)

压铸模模具设计(一)由物理学原理:我们知道:SV,有最大值;如果大于这个最大值,则会产生overflow的问题;而VL<300mps,当然,我们要求越多的溢料口,对成型有利,但是太多的溢料口,其弊端可想而知.每次开模后,注意要使用离型剂进行清除,我设计的溢料口要确保有足够的逃气截面积,计算时要注意一些回馈信息.Qm=(Mρ Mο)/S ╳ TF ( Mο≒1/3Mρ)其中:TF (经验值)≒S∕100CX: S=1.5mm. ∴TF=0.015s对TF值的部分¸影响因素很多。
The same part, but the gate location is difference:图: A-6SFLOW1>SFLOW2TF1Temperature of the mold is higher; The value of TF is shorter.SFLOW is longer, TF is shorter.以一成品为例:图: A-7这一成型品共有7个overflow:每个overflow的重量是5 g设Mρ=150 g:∴ Qm = MA/1.75×TF=150 7×5/(1.75×0.015)= 7050cm3/s∵Qm= VMA×SA∴SA= Qm/ VMAVMA 的值一般由经验得出:其常见值为40~80 m/s.以一般经验来考虑:图1的VMA值可大一些;而途图2的VMA值须小一些.现取值为50 m/s;∴SA=Qm/VMA=7050/50=141mm*mm以上就是我们所求的浇口截面积大小¸通常我们按具体情况决定具体的参数值:SO we decideSA=141=10×14.1=1×141=0.5×282……分成许许多多种类 :The following is design of the overflow:图: A-8压铸模具结构设计类似于塑模但由于压铸模必须承受较大之冲力及变形.因此,结构设计上强度大于塑模.以下列出压铸模异于塑模之要点.(一).模仁结构设计:成品边缘距模仁至少60mm.(见图A-9)公母模板的确定:模仁外边到模板外缘宽度(B)至少90mm厚度,为2倍之模仁厚. (见图A-9)模脚内侧进入模仁外缘垂直线至少20mm. (见图A-9)A板隔热板(材料S40000),厚度约12mm. (见图A-9)下固定板至少50mm.夹模厚50MM四边夹模,直接用螺丝锁,不用压板.上下顶出板厚分别为30`35mm,尽量减少宽度,从而增大模脚而使公模板变形减少.公母模仁表面均需出模板面0.1mm,切不可太大.否则,产生毛边镁通汤溅出,将极其危险.模仁尽量避免有尖锐之角点,尖点将导致应力集中.压铸时使模仁爆裂,模仁内水孔末端拐角也应有R 角.图A-9(二).RP设计可选用偏小径φ18~φ20mm,位置于模仁内. (见图A-10) EGP设计应注意:不可插入公模板,至少留1mm间隙. (见图A-9) 顶板顶出时不可靠在公模板上,至少留5mm间隙.STP可用10个左右数量,比塑模多.从下固定板锁公模板之螺丝S-1,在连接处加上圆环,插入板内定位.(如图A-11)GP应倒装在母模侧. (见图A-10)水平方向需装入0度定位块. (见图A-10)KO孔位置请见压铸机上顶杆位置,切不可用注塑成型机位置.料管中心与压铸机中心距为0~250mm,50MM为一级.图 A-10图 A-11拆模(3D)设计注意要点:所有地方除PL线外¸均至少应做R0.2圆角。
压铸模具设计
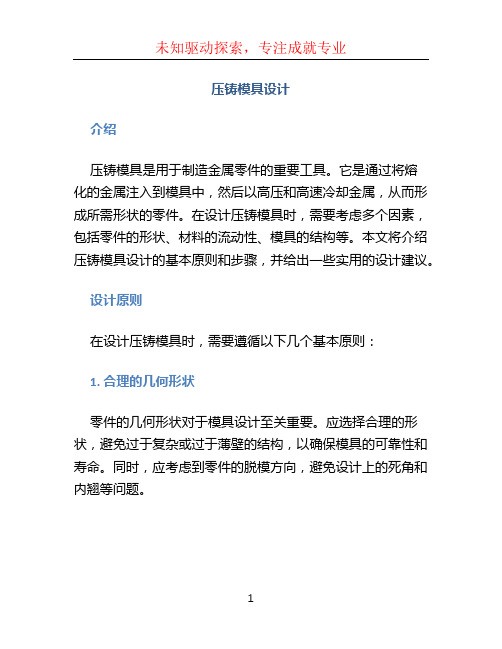
压铸模具设计介绍压铸模具是用于制造金属零件的重要工具。
它是通过将熔化的金属注入到模具中,然后以高压和高速冷却金属,从而形成所需形状的零件。
在设计压铸模具时,需要考虑多个因素,包括零件的形状、材料的流动性、模具的结构等。
本文将介绍压铸模具设计的基本原则和步骤,并给出一些实用的设计建议。
设计原则在设计压铸模具时,需要遵循以下几个基本原则:1. 合理的几何形状零件的几何形状对于模具设计至关重要。
应选择合理的形状,避免过于复杂或过于薄壁的结构,以确保模具的可靠性和寿命。
同时,应考虑到零件的脱模方向,避免设计上的死角和内翘等问题。
2. 流线型设计在注入熔融金属时,要确保金属流动的顺畅和均匀。
因此,模具的设计应尽量避免死角和锐角,采用流线型的设计,以提高金属的流动性和充填性。
3. 强度和稳定性模具需要承受高压和高温的工作环境,因此需要具备足够的强度和稳定性。
结构设计应合理,考虑到模具的受力情况和热膨胀等因素,以确保模具在工作过程中不会出现变形和损坏。
4. 易于制造和维修模具的制造和维修是一个复杂的过程,因此设计时应考虑到制造和维修的可行性。
模具的结构应尽量简化,并采用易于加工和替换的零部件,以便在需要时进行维修和更换。
设计步骤1. 零件分析在进行压铸模具设计之前,首先需要对待生产的零件进行全面的分析。
分析包括材料的性质、几何形状和尺寸、工艺要求等方面的内容。
通过这些分析,可以初步确定模具的类型和结构。
2. 模具类型选择根据零件的性质和生产要求,选择合适的模具类型。
常见的模具类型包括单腔模、多腔模和滑动模等。
选择模具类型时,需要综合考虑生产效率、成本和质量等因素。
3. 模具结构设计根据选择的模具类型,进行具体的模具结构设计。
设计包括模具的核心和型腔结构、冷却系统、进气系统等。
设计时应考虑到零件的几何形状、材料的流动性和冷却要求等因素,以提高生产效率和零件质量。
4. 模具材料选择模具的材料需要具备一定的硬度、强度和耐磨性。
压铸模设计第11章压铸模设计步骤及图例[补充new]
![压铸模设计第11章压铸模设计步骤及图例[补充new]](https://img.taocdn.com/s3/m/f3fededf7c1cfad6195fa745.png)
(2)校核压室容量
查手册,可知J116型压铸机,其压室直径为40mm时, 压室内铝合金浇入量为0.7kg。经计算(计算从略),压 铸件、浇注系统及排溢系统总重量小于0.7kg,故J116型 压铸机能满足要求。
据此,初步确定选用J116型卧式冷式压铸机.
第十一章 压铸模设计步骤及图例
• 由于压铸件的品种繁多,模具的结构特征和要求各不 相同,而且不同的设计者和加工单位也有各自的特点 和习惯,因此压铸模设计程序也会有些差异。不过,
基本的设计程序应该是相同的。
• §1 压铸模设计步骤 • §2 压铸模设计举例 • §3 压铸模结构图例
§1 压铸模设计步骤
• 压铸模设计步骤一般包括以下几个方面: 1.取得必要的资料和数据
设计前,设计者必须向模具用户取得如下资料和数据: (1) 压铸件的零件图。图中零件的尺寸、尺寸公差、形位
公差、表面粗糙度、材质、热处理要求以及其他技术要求 等应该齐全。 (2) 压铸件的生产数量及交货期限。 (3) 压铸件生产单位的设备情况(即压铸机的型号)。 (4) 模具加工单位的加工能力和设备条件。 (5) 用户的其他要求。
5.参数的计算与校核
模具结构形式确定后应对有关参数进行计算或校核。
1)成型零件成型尺寸计算。
成型零件尺寸分为:型腔径向尺寸、型芯径向尺寸、型
腔深度尺寸、型芯高度尺寸及中心距尺寸或位置尺寸。
按第7章的规定和图纸要求,零件尺寸公差为IT12级,这
些尺寸可用式7-5、6、7等计算。
零件最大外形尺寸为80mm,标上公差后为800-0.30mm,
§1 压铸模设计步骤
2.分析压铸件的结构、合金材料的性能及技术要求 (1) 分析压铸件的结构能否保证铸件质量及有利成型。如压铸件的壁厚是
关于压铸模具设计制作技术标准要求

关于压铸模具设计制作技术标准要求ADC-03-版本A0 实施日期2020-1-1编制人更改记录标记处数更改依据更改人更改日期审核人批准人1、目的标准化压铸模具,达到提高模具寿命,减少装拆模浪费,提高产品质量,降低产品制造成本。
2、适用范围公司所用压铸模具。
3、内容3.1 产品孔由压铸模具保证,切边冲孔后无后处理工序的要求:对不需要后续加工直接压铸成型,经过切边冲孔就直接交货的产品,压铸模具设计时,孔内销子孔分型面尽量选择在孔的中间段,两边销子在分型面留隔皮间隙0.1-0.2mm。
目的是防止单边销子,隔皮在孔口,切边毛刺不净或蹦口,需要后续补充加工来保证,增加了制造成本。
如下图示例。
3.2 模芯材料:模芯材料用国际知名品牌材料的优质模具钢,保证量产过程中模具质量稳定,减少反复修模造成浪费。
3.3模具浇注系统设计:合适的浇注口大小影响模具型腔注满的时间和压射力大小、速度高低、填充时间。
A、流道设计应符合流体力学原理,尽量各分流道做到铝液能同时到达各内浇口。
B、流道截面积从料柄分出到内浇口应逐步收紧变小,不可突然变大,造成喷射卷气。
C、流道不能小90°突然转急弯。
如因条件限制必须急弯,应采用大圆弧过渡,以减低压铸铸造压力和速度,避免压力速度过大产生飞边、涨模。
D、料筒选择:填充率30-50%.3.4 模具冷却系统:A、模具冷却主要是控制模具温度高低,同时使模具温度均匀,不均匀的模具温度将影响:产品有严重的缺陷,如开裂、冷隔、变形、压铸气孔、缩孔等。
温度过低,铸件冷隔,温度过高,铸件缩孔。
B、模具冷却水管要做成拔插式快换接头。
C、模具冷却水管理进水、出水管要有颜色区分,进水管蓝色,出水管红色。
D、模具定模侧上方集水器高度必须小于250mm,以避免与喷雾机干涉。
E、从模具内部接出来的水管要与图纸一致的编号标识,以利于根据模具温度要求调整冷却水的流量大小(开关开度)。
3.5 模具顶出系统:A、顶杆位置布置应使顶出力量均匀、平衡,防止因顶出力量不平衡,造成顶出变形。
压铸产品切边模的设计

切边模的设计该零件是采用的是一模两件的结构方式,分型面不是在产品的同一个平面上,孔的公差要求不高,唯一的难点就在于一模两件的产品结构在压铸生产过程中是存在变形的, 那么我们如何去设计这一切边模才能满足产品的要求既然产品存在变形,那么产品的固有的工艺参数下,产品的变形是存在一定规律性,我们只有通过一系列生产跟踪和试验摸索,才能找到了这一变形的规律,只要该产品的变形规律确定,那么这一套切边模设计和制作将不存在任何的问题.从以上的产品的要求我们最终确认切边和冲孔由一套模具完成,并且产品的两个件都必须有独立的模腔,只有这样才方便我们在后期根据产品的变形量对每一模腔进行调整,以满足产品的要求如图所示2.a 通常的情况下,铸件的飞边都是在冷态下进行,因此要求切边模的材料应有较高的综合机械性能,良好的耐磨性和耐疲劳性.热处理硬度的硬度推荐为HRC56-60b 切边模凸凹模间隙选择是非常重要的,如果间隙选择过大,那么会造成切边后的产品浇口余根过高,飞边过高,无法满足客户的要求; 如果间隙选择过小,那么会导致飞边卡的模具上,难于退料,影响模具的使用寿命.为了利于凸凹模为准和产品的要求,我们一般的凸凹模单边间隙应该在之间.切边过程中的工艺影响产品在切边每个循环中,我们一定要严格按照切边工艺执行,主要影响的工艺有:首先,模具内有残留的飞边,会造成产品表面有压痕,所以每一循环我们都对模具进行清理,可以使用自动吹气系统和手动气枪将模具表面的飞边吹干净;其次,产品没有完全放置在切边模,就已经启动切边按钮,造成产品切伤;最后,我们要对产品进行100%的自检,特别是切边涉及到的浇口、集渣包的部位、孔内以及相关的位置,都是特别要关注的地方;自检在切边工序中是非常重要的,因为及时发现了问题,才能针对出现的问题提出解决方案,否则将会造成批量事故;我们不但要做好本工序的工作,还要为下一道工序做好服务,只有这样,才能对产品质量进行有效地控制;。
压铸模设计实例
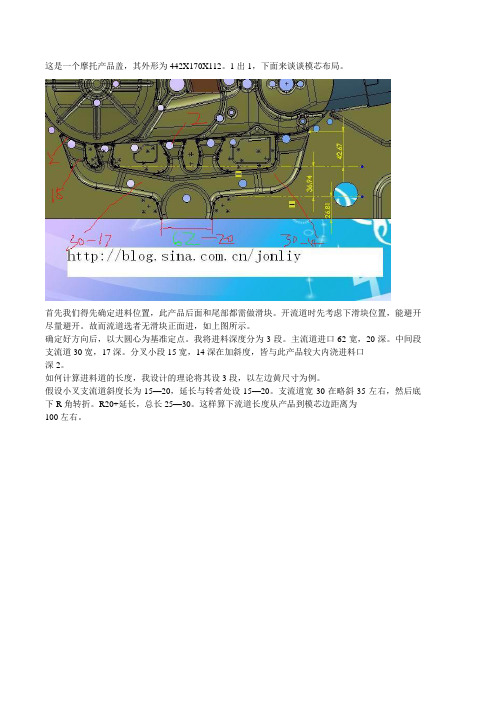
这是一个摩托产品盖,其外形为442X170X112。
1出1,下面来谈谈模芯布局。
首先我们得先确定进料位置,此产品后面和尾部都需做滑块。
开流道时先考虑下滑块位置,能避开尽量避开。
故而流道选者无滑块正面进,如上图所示。
确定好方向后,以大圆心为基准定点。
我将进料深度分为3段。
主流道进口62宽,20深。
中间段支流道30宽,17深。
分叉小段15宽,14深在加斜度,皆与此产品较大内浇进料口深2。
如何计算进料道的长度,我设计的理论将其设3段,以左边黄尺寸为例。
假设小叉支流道斜度长为15—20,延长与转者处设15—20。
支流道宽30在略斜35左右,然后底下R角转折。
R20+延长,总长25—30。
这样算下流道长度从产品到模芯边距离为100左右。
渣包尺寸为30宽以上,长40以上,距离足够的话。
深度13—15,出模度数8—10度,底下R3—5过度。
假设渣包宽35,进料边口为5,预设渣包后留25。
那么产品到模芯边为60余量。
如有滑块得根据抽出距离另行计算或者加宽余量边,祥见以下图所示。
对于有滑块面的余量放置,假设模内抽芯距离为70,那么后面的距离为70+余量,使之滑块滑出绝对距离后始终在模芯内,余量15—20最起码。
另外边也同样的道理,这样我们可以计算出模芯的大小,然后去小归整。
设计好大小后,然后来设计模芯的厚度。
厚度的设计准则以模芯最低出开始算余量50以上。
因为底下通10水管,水管位置离产品模芯底面下来20—25距离,底下留余量为25—30,然后以分型面为定点基准,凑整数。
绿色为水管,红色,蓝色为点冷却。
一般模芯不是很厚的,如果中间没有孔位,可以直通,或环绕试。
如果无法通水管,那就采取点冷却。
一般在型腔的镶快出,凸起出,热聚处。
其深度离腔体最深出低20—30左右。
滑块的设计,皆如此产品的滑芯不是很大。
宽度方面一般滑座比滑芯大5一边,然后凑整数。
滑块高度的设计,首先确定此滑块是用油泵。
如油泵接头最大处为32,那我设置尾座面比接头高4,底下留9,这样尾座高度为45。
- 1、下载文档前请自行甄别文档内容的完整性,平台不提供额外的编辑、内容补充、找答案等附加服务。
- 2、"仅部分预览"的文档,不可在线预览部分如存在完整性等问题,可反馈申请退款(可完整预览的文档不适用该条件!)。
- 3、如文档侵犯您的权益,请联系客服反馈,我们会尽快为您处理(人工客服工作时间:9:00-18:30)。
切边模的设计
该零件是采用的是一模两件的结构方式,分型面不是在产品的同一个平面上,孔的公差要求不高,唯一的难点就在于一模两件的产品结构在压铸生产过程中是存在变形的, 那么我们如何去设计这一切边模才能满足产品的要求?
既然产品存在变形,那么产品的固有的工艺参数下,产品的变形是存在一定规律性,我们只有通过一系列生产跟踪和试验摸索,才能找到了这一变形的规律,只要该产品的变形规律确定,那么这一套切边模设计和制作将不存在任何的问题.从以上的产品的要求我们最终确认切边和冲孔由一套模具完成,并且产品的两个件都必须有独立的模腔,只有这样才方便我们在后期根据产品的变形量对每一模腔进行调整,以满足产品的要求(如图所示2).
a) 通常的情况下,铸件的飞边都是在冷态下进行,因此要求切边模的材
料应有较高的综合机械性能,良好的耐磨性和耐疲劳性.热处理硬度的硬
度推荐为HRC56-60
b) 切边模凸凹模间隙选择是非常重要的,如果间隙选择过大,那么会造
成切边后的产品浇口余根过高,飞边过高,无法满足客户的要求; 如果间
隙选择过小,那么会导致飞边卡的模具上,难于退料,影响模具的使用寿命.
为了利于凸凹模为准和产品的要求,我们一般的凸凹模单边间隙应该在
0.2-0.4mm之间.
切边过程中的工艺影响
产品在切边每个循环中,我们一定要严格按照切边工艺执行,主要影响的工艺有:首先,模具内有残留的飞边,会造成产品表面有压痕,所以每一循环我们都对模具进行清理,可以使用自动吹气系统和手动气枪将模具表面的飞边吹干净。
其次,产品没有完全放置在切边模,就已经启动切边按钮,造成产品切伤。
最后,我们要对产品进行100%的自检,特别是切边涉及到的浇口、集渣包的部位、孔内以及相关的位置,都是特别要关注的地方。
自检在切边工序中是非常重要的,因为及时发现了问题,才能针对出现的问题提出解
决方案,否则将会造成批量事故。
我们不但要做好本工序的工作,还要为下一道工序做好服务,只有这样,才能对产品质量进行有效地控制。