(工艺技术)干膜光成像工艺规范
底片干膜工艺技术资料

底片干膜工艺技术资料一、底片干膜工艺概述底片干膜工艺是一种常用于光刻技术中的工艺方法。
在硅片制造过程中,光刻技术用于制造集成电路中的微细图案。
底片干膜工艺是光刻技术的一个重要环节,其主要作用是在硅片表面形成一层薄膜,用于保护或增强光刻图案。
二、底片干膜工艺流程底片干膜工艺流程包括以下几个步骤:1. 底片准备在进行底片干膜工艺之前,需要先准备好底片。
底片是一种透明平板,通常由玻璃或石英制成。
底片表面应保持干净无尘,以免影响后续的工艺步骤。
2. 底片清洁底片在使用前需要进行清洁处理,以去除底片表面的杂质和污染物。
清洁方法可以采用化学溶液浸泡或超声波清洗。
3. 干膜涂覆底片清洁完毕后,需要进行干膜涂覆的过程。
干膜是指一种特殊的聚合物材料,可以在底片表面形成一层均匀的薄膜。
干膜涂覆可以采用旋涂法或喷涂法,在涂布的过程中需要控制好涂布速度和涂布厚度,以保证干膜的质量。
4. 烘烤干膜涂覆完成后,需要进行烘烤处理。
烘烤的目的是将干膜固化,并使其与底片表面紧密结合。
烘烤的温度和时间根据具体的干膜材料而定,需要严格控制参数,以确保烘烤效果良好。
5. 剥膜经过烘烤后,干膜与底片表面形成了牢固的结合。
为了制作光刻图案,需要将部分干膜剥离,留下所需的图案。
剥膜的方法可以采用化学溶解或机械剥离,需要根据具体情况选择合适的方法。
6. 检验剥膜完成后,需要对底片进行检验,确保干膜工艺的质量符合要求。
检验的内容可以包括干膜的厚度、表面光洁度等指标。
三、底片干膜工艺的应用底片干膜工艺广泛应用于集成电路的制造过程中。
其主要作用有:1. 保护硅片表面底片干膜可以形成一层保护膜,用于保护硅片表面不被污染或损坏。
在后续的工艺步骤中,底片上的干膜可以起到保护的作用,确保光刻图案的准确传递。
2. 增强光刻图案对比度在光刻过程中,底片上的干膜可以增强光刻图案的对比度,使其更容易识别和处理。
干膜的颜色和透明度可以根据需求来选择,以提高图案的可见度。
干膜光成像工艺规范

个磨板系统是否正常,磨出来的板是否干燥洁净,有无污渍、水迹、氧化点,合格后方
可批量生产。
5.6.2 接板员工将检查合格的板先插架放置 3-6min,再叠板放置(0.6mm 以下的薄板可直接
叠板放置),为了防止板子放置时间太长、板面氧化导致贴膜不牢,原则上要求现磨现贴,
但积板数量不许超过 100 块且存板时间不可超过一小时。否则需重新磨板。
迹、氧化点。 5.5.2 磨痕试验:
取一块未经钻孔或已钻孔但未作图形的且与生产板同厚度的覆铜板作试板。 5.5.2.1 打开输送→放板入上(下)刷位置→关闭输送→调动磨刷进给压力到设定值→打
开上(下)刷喷啉并磨板 8-10 秒→关闭磨刷→打开输送→取出试板。 5.5.2.2 将板子传送出来,检查上(下)刷的磨痕是否均匀,宽度在 10-15mm 之间,过窄
干膜光成像工艺规范
目录
1.目的---------------------------------------------------------------------------------4 2.范围---------------------------------------------------------------------------------4 3.定义---------------------------------------------------------------------------------4 4.操作方法-------------------------------------------------------------------------4-5 5.磨板-------------------------------------------------------------------------------6-9 6.贴膜------------------------------------------------------------------------------9-11 7.曝光-----------------------------------------------------------------------------11-13 8.显影-----------------------------------------------------------------------------13-17 9.检查-----------------------------------------------------------------------------17-18 10. 故障与排除---------------------------------------------------------------------18-19
感光干膜法制造工艺

感光干膜法制造工艺感光干膜法制造工艺(1)贴膜制板工艺流程。
贴膜前处理一吹干或烘干一贴膜一对孔一定位一曝光一显影一晾干一修板。
1.)贴膜前处理。
在贴膜前将板材刷洗干净,去除氧化膜、油污等,以增加干膜与铜箔表面的结合力,否则将会引起干膜脱落与边缘起翘等。
刷洗一般用刷板机。
2)贴膜。
贴膜主要借助贴膜机进行。
贴膜温度对贴膜质量影响比较大。
温度过高,易使子膜流胶和发脆。
因此,要严格控制贴膜温度。
温度的选择与干膜性能、气候条件有关,一般为90-130℃,夏季要再低13 ---20℃。
选择适当的贴膜压力也是非常重要的。
压力过小,干膜与铜箔结合不牢,影响制板质量;反之,膜易变形起皱。
在生产过程中,要根据经验选择压力大卟。
贴膜速度太快,膜易起皱,无法制出合格图形;反之,会使贴膜不牢。
3)曝光。
曝光对印制电路板质量影响很大。
光源类型、曝光时间的长短、光源的强弱,对制成图形线条的粗细及精度产生直接影响。
若曝光过量,会造成显影困难,甚至细线条显不出影;反之,线条边缘发毛,会出现渗镀现象。
曝光时,应严格控制曝光量。
曝光量与光源的强弱、灯距的远近、曝光时间长短等有关。
在光源选定的情况下,决定曝光量的因素有灯距和时间。
若灯距远,曝光时间就要相应加长;反之,曝光时间要短。
但光源距离过近,会对干膜显影带来困难。
因此,光源的距离要合适,一般通过实验来确定。
4)显影。
显影一般在显影机里进行。
显影溶液采用无水碳酸钠,浓度为1% '--,20200操作程序是:曝光后的印制电路板去掉聚酯膜,放在显影机里进行显影,印制电路板首先进入喷淋2070稀碳酸钠溶液段中显影,然后进入水中冲洗干净,最后在盛有1%的碳酸钠溶液的容器中再次显影。
显影的时间不能太长,时间太长会造成过显,使边线不整齐;时间太短会使显影不彻底,密集线条部分显不出图像。
显影溶液的浓度要严格地控制,浓度太低,显影速度慢,不易显示出图像;浓度太高,显影速度过快,~易造成导绒边缘不整齐。
干膜光刻胶技术

干膜光刻胶技术一、介绍干膜光刻胶技术1.1 定义干膜光刻胶技术是一种常用于电子器件制造中的光刻工艺。
它是一种逐层涂覆光刻胶的过程,通过光刻胶的暴光和显影来实现对电路或器件的精确定义。
1.2 原理干膜光刻胶技术的基本原理是在待光刻的物体表面上涂覆一层光刻胶,并通过暴光和显影等步骤来实现对光刻胶的处理。
在光刻过程中,光刻胶会形成一个薄膜,保护待光刻物体的某些区域,其余区域则暴露出来以供后续处理。
二、干膜光刻胶的制备2.1 材料准备•光刻胶:选择适合的光刻胶,一般根据需要的分辨率和显影的要求来选择。
•基片:选择质量良好的基片材料。
2.2 胶液制备1.将光刻胶放入特定容器中。
2.按照比例向容器中加入相应的稀释剂。
3.严格按照工艺要求搅拌混合,直至光刻胶和稀释剂均匀混合。
2.3 胶液过滤1.准备一个过滤器。
2.将混合好的胶液通过过滤器,去除杂质和颗粒,以保证胶液的纯净度。
2.4 胶液涂覆1.准备好基片。
2.将过滤好的胶液均匀涂覆在基片表面。
3.使用旋涂机等设备,控制涂覆的厚度和均匀性。
三、干膜光刻胶的光刻步骤3.1 掩膜制备1.选择合适的掩膜材料。
2.利用曝光设备将掩膜图案转移到光刻胶上。
3.2 暴光1.使用光刻机将掩膜上的图案通过紫外线或激光照射到光刻胶上。
2.光刻胶中的光敏化剂会发生反应,产生化学变化。
3.3 烘烤1.将暴光过的光刻胶放入烘烤机中。
2.控制温度和时间,使光刻胶中的物质发生凝聚和固化的过程。
3.4 显影1.准备好显影液。
2.将烘烤后的光刻胶浸泡在显影液中,使显影液与未固化的光刻胶发生化学反应。
3.反应后,使用去离子水清洗光刻胶,去除显影液和剩余的光刻胶。
四、干膜光刻胶技术的应用领域4.1 电子器件制造干膜光刻胶技术广泛应用于电子器件制造过程中。
在集成电路制造中,通过干膜光刻胶技术可以实现对电路结构的精确定义,从而保证电路的正常工作。
4.2 晶体管制造在晶体管的制造过程中,干膜光刻胶技术可用于控制晶体管的栅极和源/漏极区域的尺寸和形状,从而影响晶体管的电性能。
干膜介绍及干膜工艺详解(40页)
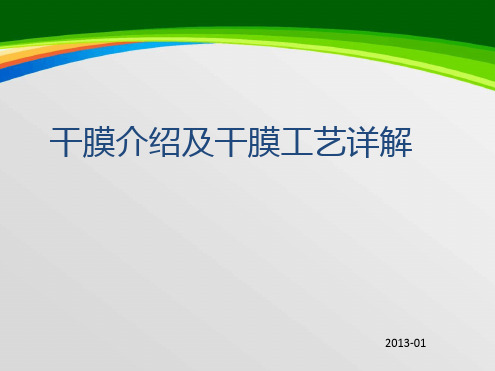
工序注意事项
? 曝曝光光能量均匀性≥ 90%;
每4H测定曝光能量; 抽真空时间不能太短,防止曝光不良; 曝光台面温度太高会造成底片变形; 板面、底片或曝光台面不能有脏点; 干膜、底片小心操作,防止划伤; 曝光机空气过滤芯定期清洁或更换。
?SES 工艺流程详显细影介:绍
全板电镀铜
基铜 玻璃纤维底料 曝光原件
曝光
干膜
显影
蚀板
电镀铜/锡或锡/铅
去膜
碱性蚀板 脱锡或锡/铅
2. 线路板图形制作工艺
?SES 流程基本工艺
贴膜 曝光
全板电镀铜
基铜 玻璃纤维底料 曝光原件
脱锡或锡/铅
显影
电镀铜+锡 或铜+锡/铅
碱性蚀板 去膜
?SES工艺流程详细介绍
前处理:
? 前处理的作用:去除铜表面的氧化 ,油污,清洁、 粗化铜面,以增大干膜在铜面上的附着力。
干膜介绍及干膜工艺详解
2013-01
主要内容安排:
1.干膜介绍及发展趋势 2.线路板图形制作工艺(以SES流程为例) 3.基本工艺要求 4.各工序注意事项 5.常见缺陷图片及成因 6.讨论
1. 干膜介绍及发展趋势
?干膜(Dry Film)的用途: 干膜是一种感光材料,是PCB生产中的重要 物料,用于线路板图形的转移制作。近几 年也开始广泛应用于选择性化金、电镀金 工艺。
曝光: 曝光的作用是曝光机的紫外线通过底片使干膜 上部分图形感光,从而使图形转移到铜面上。
底片 干膜 Cu
基材
?SES 工艺流程详细介绍
曝光反应机理
COOH
COOH
COOH
COOH
COOH COOH
底片干膜工艺技术资料

2024年8月15日星期四
电路图形转移材料的演变
电路图形转移材料的演变
v 印制电路图形的转移所使用的原材料,自出现印制电路 以来,原材料的研制与开发科学攻关工作从未停止过。 从原始阶段设计采用抗蚀油漆或虫胶漆手工描绘简单的 线路图形转移工艺技术的需要。但随着微电子技术的飞 速发展,大规模集成电路和超大规模集成电路的广泛应 用,要求印制电路板的制造技术,必须适应高密度、高 精度、细导线、窄间距及小孔径电路图形转移需要。几 十年来,研制与开发出新型的光致抗蚀剂与电路图形转 移技术: 如光致抗蚀干膜、湿法贴膜技术、电泳光致抗 蚀膜和直接成像技术,都逐步地被制造印制电路板商家 所采用,使电路图形的转移品质大幅度的提高。为叙述 简便,就印制电路板制造过程中,所采用的电路图形转 移原材料,按顺序加以简单论述:
v 以上两种工艺过过程概括如下:
v 印制蚀刻工艺流程:
v 下料→板面清洁处理→涂湿膜→曝光→显影(贴干膜→ 曝光→显影)→蚀刻→去膜→进入下工序
v 畋形电镀工艺过程概括如下:
v 下料→钻孔→孔金属化→预镀铜→板面清洁→涂湿膜→ 曝光→显影(贴干膜→曝光→显影)→形成负相图象 →图形镀铜→图形电镀金属抗蚀层→去膜→蚀刻→进入 下工序
v 6)热阻聚剂 在干膜的生产及应用过程中, 很多步骤需要接受热能, 为阻止 热能对干膜的聚合作用加入 热阻聚剂。如甲氧基酚、对苯二 酚等均可作为热阻聚剂。
v 7)色料 为使干膜呈现鲜艳的颜色, 便于修版和检查而添加色料。如 加入孔雀石绿、苏丹三等色料 使干膜呈现鲜艳的绿色、兰色 等。
v 8)溶剂 为溶解上述各组份必须使用溶剂。通常采用丙酮、酒精作溶 剂。 此外有些种类的干膜还加入光致变色剂, 使之在曝光后 增色或减色, 以鉴别是否曝光, 这 种干膜又叫变色于膜。
干膜光刻胶技术的应用与发展

干膜光刻胶技术的应用与发展干膜光刻胶技术的应用与发展1. 引言在现代科技的快速发展中,干膜光刻胶技术作为一种重要的微电子制造工艺,发挥着越来越重要的作用。
本文将从基本原理、应用领域、发展趋势等方面深入探讨干膜光刻胶技术。
2. 基本原理干膜光刻胶技术是一种通过光敏感材料形成图案,实现微细结构制备的方法。
该技术主要包括以下几个步骤:(1)干膜涂布:将光刻胶均匀涂布于待加工的基片上;(2)热压:将干膜与基片通过热压粘附在一起;(3)曝光和显影:使用紫外光对所需图案进行曝光,然后通过显影去除未曝光的区域,形成所需图案。
3. 应用领域干膜光刻胶技术在多个领域有着广泛的应用,下面重点介绍其中几个主要领域:(1)微电子制造:干膜光刻胶技术在集成电路、光电子器件等微电子制造中应用广泛。
通过该技术可以实现微细、高精度的图案制备,满足现代电子器件对结构精度的要求。
(2)光学器件制备:干膜光刻胶技术在光学器件的制备中也得到了广泛的应用。
在光通信领域,可以利用该技术制备光波导器件、光耦合器等光学器件。
(3)生物芯片制备:生物芯片作为生物学与微电子学相结合的产物,干膜光刻胶技术在其制备中具有重要的应用。
通过该技术可以在芯片上制备出微细的通道和微井,实现基因分析、蛋白质分析等生物实验。
4. 发展趋势干膜光刻胶技术在不断发展壮大的也面临着一些挑战。
下面将就其发展趋势进行探讨:(1)高分辨率:随着微电子技术和纳米技术的不断进步,对于高分辨率的需求也越来越大。
干膜光刻胶技术在未来将继续提高其分辨率,以满足更加精细的微细结构制备需求。
(2)新材料开发:目前干膜光刻胶技术主要采用光敏剂与树脂的组合,而新材料的开发将为该技术带来更多的可能性。
利用纳米材料、功能高分子等新材料,可以进一步提高干膜光刻胶技术在微电子等领域的应用性能。
(3)工艺改进:干膜光刻胶技术在涂布、热压等环节仍存在一些难点和缺陷,需要通过工艺改进来解决。
提高涂布均匀性、降低热压温度等,都是未来该技术需要解决的问题。
干膜的技术性能要求

干膜的技术性能要求
2008-9-23作者:来源::
干膜光致抗蚀剂的技术条件
外观
使用干膜时,首先应进行外观检查。质量好的干膜必须无气泡、颗粒、杂质;抗蚀膜厚度均匀;颜色均匀一致;无胶层流动。如果干膜存在上述要求中的缺陷,就会增加图像转移后的修版量,严重者根本无法使用。膜卷必须卷绕紧密、整齐,层间对准误差应小于1mm,这是为了防止在贴膜时因卷绕误差而弄脏热压辊,也不会因卷绕不紧而出现连续贴膜的故障。聚酯薄膜应尽可能薄,聚酯膜太厚会造成曝光时光线严重散射,而使图像失真,降低干膜分辨率。聚酯薄膜必须透明度高,否则会增加曝光时间。聚乙烯保护膜厚度应均匀,如厚度不均匀将造成光致抗蚀层胶层流动,严重影响干膜的质量。干膜外观具体技术指标如表7—1所述:
◎其它性能
在生产操作过程中为避免漏曝光和重曝光,干膜在曝光前后颜色应有明显的变化,这就是干膜的变色性能。当使用于膜作为掩孔蚀刻时,要求干膜具有足够的柔韧性,以能够承受显影过程、蚀刻过程液体压力的冲击而不破裂,这就是干膜的掩蔽性能。
◎光谱特性
在紫外——可见光自动记录分光光度计上制作光谱吸收曲线(揭去聚乙烯保护膜,以聚酯薄膜作参比,光谱波长为横坐标,吸收率即光密度D作纵坐标),确定光谱吸收区域波长及安全光区域。技术要求规定,干膜光谱吸收区域波长为310~440毫微M(nm),安全光区域波长为≥460毫微M(nm)。
高压汞灯及卤化物灯在近紫外区附近辐射强度较大,均可作为干膜曝光的光源。低压钠灯主要幅射能量在波长为589.0~589.6nm的范围,且单色性好,所发出的黄光对人眼睛较敏感、明亮,便于操作。故可选用低压钠灯作为干膜操作的安全光。
干膜生产工艺

干膜生产工艺干膜生产工艺是一种在电子工业中广泛应用的技术,用于制作薄膜电路板和其他电子产品。
下面是一个关于干膜生产工艺的700字的介绍。
干膜生产工艺是一种先进的制造技术,它可以用于制作高品质的电路板。
干膜是一种特殊的光敏胶片,它可以与印刷电路板表面紧密结合,在光的作用下形成图形。
与传统的湿膜工艺相比,干膜工艺具有更高的精度和稳定性。
干膜生产工艺的主要步骤包括准备基板、涂敷干膜、曝光、显影、蚀刻和清洗。
首先,需要准备好需要制作电路的基板。
基板的材料可以是FR4、铜或其他导电材料。
然后,在基板表面涂敷一层干膜。
干膜有多种类型,可以根据需要选择不同的干膜来实现不同的功能。
涂敷干膜后,需要将其暴露在紫外光下,以形成所需的电路图案。
曝光的过程中,光线会通过掩膜上的图案,然后照射到干膜上。
只有暴露在光下的部分会发生化学反应,形成稳定的图案结构。
完成曝光后,接下来是显影的步骤。
显影是指将不需要的部分从干膜上去除的过程。
显影液会分解暴露在光下的部分干膜,使其变得可溶于溶剂。
而未暴露在光下的部分干膜则保持不变。
通过显影,可以形成所需的电路图案。
在显影完成后,接下来是蚀刻的步骤。
蚀刻是指将基板表面的铜或其他导电材料去除,从而形成所需的电路图案。
蚀刻液会溶解掉没有被干膜保护的铜层,使电路图案明确可见。
最后一步是清洗。
清洗的目的是去除干膜残留物和其他杂质,以保证电路板的质量和可靠性。
清洗过程通常使用酒精或其他溶剂进行。
干膜生产工艺具有许多优点。
首先,它可以实现高精度的电路图案,使电路板具有更好的性能和可靠性。
其次,与传统的湿膜工艺相比,干膜工艺更加环保,能够节约更多的水资源和能源。
此外,干膜工艺操作简单,工艺周期短,能够大大提高生产效率。
总之,干膜生产工艺是一种先进的制造技术,适用于电子行业中的薄膜电路板制造。
它具有高精度、稳定性和环保等优点,能够提高电路板的性能和可靠性,同时还能提高生产效率。
随着电子行业的快速发展,干膜生产工艺将继续在电子制造领域发挥重要作用。
干膜工艺流程

干膜工艺流程干膜工艺流程是一种常用于电子产品制造过程中的技术,主要用于保护电路板和其他电子设备的表面。
下面是一篇关于干膜工艺流程的700字文章。
干膜工艺流程是一种常用于电子产品制造过程中的技术,主要用于保护电路板和其他电子设备的表面。
它采用了干式光敏材料,能够提供高度的保护和可靠的性能。
干膜工艺流程通常分为以下几个步骤。
首先,我们需要准备一个电路板,它通常由导电材料制成,如铜。
然后,我们将电路板放在一个清洁的环境中,以确保没有任何污垢或杂质附着在表面上。
接下来,我们需要对电路板进行化学处理,以去除表面的氧化物和其它不洁物,以增强粘附力。
完成化学处理后,我们需要在电路板上涂覆一层干膜光敏材料。
这种材料的一个主要特点是在紫外线照射下会发生化学反应,使其变得可溶于特定的溶剂。
涂覆干膜光敏材料的方法通常有两种:一是手工刷涂,二是使用涂布机自动涂覆。
无论使用哪种方法,都需要确保膜厚均匀,以保证光敏材料的耐用性和可靠性。
涂覆完成后,电路板需要被烘干,以使光敏材料完全固化。
通常使用烘箱进行烘干,温度和时间的控制非常重要,以确保膜层完全干燥和固化。
烘干后,接下来就是曝光,即将电路板暴露在紫外线照射下。
这一步是干膜工艺流程的关键步骤。
通过使用掩膜,我们可以通过滤光的方式选择性地曝光光敏材料。
在曝光过程中,未被曝光的区域仍然保持可溶性,而曝光区域的光敏材料则发生化学反应并变为不可溶性。
曝光完成后,我们需要对电路板进行显影处理。
这一步骤的目的是将未曝光的光敏材料溶解掉,留下仅有曝光区域的膜层。
通过控制显影过程中的时间和温度,我们可以确保对电路板进行精确和可靠的处理。
最后的步骤是对电路板进行烘干和固化。
这样,电路板上的干膜光敏材料就可以达到最佳的保护效果。
烘干和固化的温度通常较高,以确保材料的耐久性和可靠性。
干膜工艺流程在电子产品制造中起着至关重要的作用。
它能够为电路板和其他电子设备提供高度的保护和可靠的性能。
通过严谨的操作和精确的控制,干膜工艺能够确保电子产品在各种恶劣条件下的稳定工作。
干膜介绍及干膜工艺详解

干膜介绍及干膜工艺详解干膜是一种常用的覆盖材料,用于保护电子元件表面免受污染、腐蚀和机械损伤。
它由聚酰胺树脂制成,具有优异的耐温性、耐化学性和机械强度。
干膜广泛应用于电子工业、半导体制造业、汽车制造业等领域。
本文将详细介绍干膜的工艺及应用。
干膜工艺主要分为涂布、曝光、显影和固化四个步骤。
首先,将干膜涂布在待保护的基板表面,然后通过热压或UV曝光使干膜与基板紧密结合。
曝光是将覆盖了光掩膜的基板和干膜放置在紫外线曝光机中,通过控制曝光时间和光强来实现显影效果。
显影是将经过曝光的基板和干膜放入化学液中,使未曝光部分的干膜溶解,从而揭露出基板的表面。
最后,通过热固化或UV固化使干膜与基板牢固结合,形成保护层。
干膜具有许多优越的特性。
首先,干膜具有出色的耐化学性,能够抵抗酸、碱和溶剂的侵蚀,保护电子元件不受腐蚀。
其次,干膜具有良好的耐温性,能够在高温环境下保持稳定性,适用于高温焊接和其他高温工艺。
此外,干膜具有优秀的机械强度,能够抵御机械冲击和摩擦,确保元件表面的完整性。
最重要的是,干膜具有良好的电绝缘性能,能够有效隔离电子元件,保证电路的正常运行。
干膜广泛应用于各种电子元件的保护和焊接过程中。
在印制电路板(PCB)制造过程中,干膜可以作为覆盖材料,保护线路图案在酸碱腐蚀、高温焊接和表面处理中不受损坏。
在集成电路制造中,干膜可用作衬底保护层,保护器件免受机械和化学损伤。
此外,干膜还可以用于电子元件的封装和封装,提高元件的可靠性和稳定性。
总之,干膜作为一种常用的保护材料,具有优越的性能和广泛的应用领域。
通过涂布、曝光、显影和固化等工艺步骤,可以将干膜均匀附着在基板表面,形成坚固耐用的保护层。
干膜能够有效保护电子元件免受污染、腐蚀和机械损伤,提高元件的可靠性和稳定性。
在电子工业、半导体制造业和汽车制造业等领域发挥着重要作用。
干膜作为一种常用的保护材料,具有许多优越的特性,因此在各个领域得到广泛应用。
下面将进一步介绍干膜的应用以及其在电子工业、半导体制造业和汽车制造业中的具体应用。
干膜光刻胶技术

干膜光刻胶技术干膜光刻胶技术是一种高精度微细加工技术,适用于微电子、半导体、光电、 MEMS 等领域。
该技术利用光刻胶遮光和腐蚀等特性,在平板上制备各种微细图形和结构。
干膜光刻胶技术具有成本低、加工速度快、加工精度高等优点,因此在微电子工业中得到了广泛应用。
干膜光刻胶技术的原理是在硅片表面和光刻胶之间贴上一层薄膜,使光刻胶与硅片分离,然后通过光刻制程对胶膜进行加工。
光刻制程通常包括以下步骤:(1)洗净,将硅片表面脱脂、清洗干净。
(2)光刻胶涂覆,将光刻胶均匀地涂覆在硅片上,形成厚度为 2-4μm 的光刻胶膜。
其中,光刻胶的选择对加工精度、分辨率和加工速度等方面均有影响。
(3)加热,利用高温热板或热板和光刻炉对光刻胶进行加热,控制光刻胶的光安息点和曝光时的光子剂量。
(4)曝光,通过主曝光机或光掩膜对光刻胶进行暴露,形成所需的微细图形和结构。
(5)显影,利用显影液除去暴露于光下的光刻胶,使暴露的硅片区域裸露出来。
(6)腐蚀,通过湿法或干法腐蚀来加工出所需结构。
与传统湿法光刻相比,干膜光刻胶技术具有显著优点。
首先,干膜光刻胶不需要洗涤处理,不会对环境造成污染。
其次,干膜光刻胶技术可以减少加工时间和成本,并提高了加工效率。
此外,干膜光刻胶技术的加工精度和分辨率也得到了极大的提高。
干膜光刻胶技术近年来越来越受到研究人员和工业界的高度重视。
然而,干膜光刻胶技术也面临着一些挑战。
例如,制备高材料质量的干膜光刻胶仍然是一个难题。
此外,干膜光刻胶在加工过程中容易受到机械力和热膨胀等因素的影响,这也限制了其加工精度和分辨率。
综上所述,干膜光刻胶技术是一种高精度微细加工技术,具有成本低、加工速度快、加工精度高等优点。
该技术在微电子、半导体、光电、MEMS等领域得到了广泛应用。
虽然干膜光刻胶技术面临一些挑战,但相信在不久的将来,通过不断的研究和创新,干膜光刻胶技术将会带来更大的突破和进步。
干膜曝光工艺

干膜曝光工艺干膜曝光工艺是一种常用于制作印制电路板(PCB)的工艺。
干膜曝光是利用光敏干膜和紫外光源将图形图案转移到PCB基板上的过程。
首先,为了进行干膜曝光,需要先将光敏干膜粘贴在PCB基板上。
干膜是由光敏物质和聚酯薄膜构成的一种材料,它能够在紫外光的作用下发生化学反应,并固化在PCB基板上。
在将干膜粘贴在基板上后,需要将图形图案传输到干膜上。
这一步骤通常使用曝光机进行,曝光机会利用紫外光源照射干膜,将图形图案暴露在上面。
暴露后的干膜在紫外光的作用下会发生化学反应,使得未暴露的部分保持柔软,而已经暴露的部分则变得硬化。
接下来,需要进行干膜的显影。
显影过程中,会使用一种化学溶液将未曝光的部分从干膜上洗掉,只留下已经曝光固化的部分。
这一步骤十分关键,因为它能够确保将图形图案准确地转移到PCB基板上。
最后,通过去除干膜,就可以得到最终的PCB板。
通常会使用酸性溶液或碱性溶液将干膜从PCB基板上去除,同时保持已固化的部分不受影响。
干膜曝光工艺相对于其他印制电路板制作工艺具有许多优点。
首先,它能够实现高精度的图形图案转移,可以制作出细线宽和小间距的电路。
其次,干膜曝光工艺具有较高的生产效率,能够快速完成大量的PCB制作任务。
此外,干膜曝光工艺还具有较低的成本和良好的可重复性。
总的来说,干膜曝光工艺是一种重要的PCB制作工艺,它能够实现高精度和高效率的图形图案转移。
随着技术的发展,干膜曝光工艺在PCB行业中的应用将会更加广泛。
干膜曝光工艺是印制电路板(PCB)制造过程中至关重要的一环。
它不仅能够实现高精度的图形图案转移,还能够提高生产效率,降低成本,以及保证制造的可重复性。
在干膜曝光工艺中,光敏干膜是关键的材料之一。
光敏干膜是由聚酯薄膜和光敏物质组成的,在曝光过程中会发生化学反应。
干膜有很好的粘附性,可以牢固地贴在PCB基板上,提供稳定的工作平台。
在进行干膜曝光之前,需要进行图形设计和制作。
设备通常使用计算机辅助设计(CAD)软件来完成PCB的图形设计。
底片干膜工艺技术资料

感谢您的观看
汇报人:
底片的质量检测:检查底片是否符合工艺要求,包括曝光、显影、定影等环节
底片的清洁处理:使用专业的清洁剂和工具对底片进行清洁,去除表面的污渍和尘埃
底片的烘干处理:将清洁后的底片进行烘干,以避免潮湿对底片的影响 底片的存储与保管:将烘干后的底片按照规定的方式进行存储和保管,以避免损坏和污染
底片干膜工艺参数 与控制
添加标题
添加标题
添加标题
添加标题
平整度要求:确保底片表面平整, 无气泡、皱褶等缺陷
底片张力与平整度的检测方法:通 过观察、测量等方法对底片进行检 查,确保符合工艺要求
温度控制:确保底片干膜在适宜的温度下进行固化 压力控制:通过调整压力,确保底片干膜与基材紧密贴合 时间控制:确定底片干膜的固化时间,确保其完全固化 设备维护:定期对设备进行检查和维护,确保工艺参数的稳定性和准确性
干膜的组成:由聚合物、感 光剂和溶剂等组成
干膜的固化程度:可以通过控 制曝光时间和光源波长来调节
干膜的固化特点:具有较高 的耐热性和耐化学腐蚀性
底片表面处理:底片表面进行粗化处理,使其表面不平整,增加附着力 干膜材料:采用高分子材料,具有较好的粘附性和化学稳定性 附着原理:干膜与底片之间通过化学键合、物理吸附等作用力产生附着 烘烤固化:在高温下进行烘烤,使干膜固化附着在底片表面
形项正文
其他领域
此处输入你的智能图 形项正文
案例一:某电子制 造公司的应用
案例二:某汽车零 部件公司的应用
案例三:某航空航 天公司的应用
案例四:某医疗设 备公司的应用
案例一:某公司采用底片干膜 工艺提高产品质量
案例二:某工厂利用底片干膜 工艺降低生产成本
案例三:某项目采用底片干膜 工艺解决技术难题
光成像

入职工艺知识培训讲义
3.主要设备、物料
贴 曝 显 蚀 退 膜 光 影 刻 膜
点光源 曝光机 平行光 激光(LDI)
RD-CM-WI01S1A
注意事项: (1)清洁频率:每做一块板使用粘尘辘清洁板面、菲林、麦拉; 每生产5块板使用无尘布蘸菲林水清洁一次菲林,并使用5倍放大镜检查菲林是否偏位。 (2)先用手辅助赶气,然后用擦气板擦气;保证抽真空的效果。
第10页
入职工艺知识培训讲义
2.工序原理、主要参数及控制点
前处理 贴 膜 曝 光 显 影 蚀 刻 退 膜 工艺流程
RD-CM-WI01S1A
曝光即在紫外光/激光照射下,光引发剂吸收了光能分解成游离基, 游离基再引发光聚合单体进行聚合交联反应,反应后形成不溶于稀 碱溶液的体型大分子结构。
曝光前
曝光后
第22页
入职工艺知识培训讲义
4.常见问题
RD-CM-WI01S1A
第23页
入职工艺知识培训讲义
4.常见问题
RD-CM-WI01S1A
第24页
入职工艺知识培训讲义
5.环境要求
RD-CM-WI01S1A
贴膜、曝光等动作主要在净化房进行。 净化房的要求为:
(1)灯光:黄光;此种颜色灯光下,干膜与之反应的速度最慢。 (2)温度:21+/-2℃; (3)湿度:55+/-5%; (4)洁净度:1千级;具体理解为单位体积(平方英寸)内5UM尘埃颗粒的个 数不超过1000个,50μm尘埃颗粒的个数不超过7个。
更换蚀刻过滤碳芯 蚀刻 清洗蚀刻段过滤网膜 检查蚀刻及补偿蚀刻段温度 检查蚀刻段各喷淋压力 清倒退膜段干膜收集桶 清洗退膜段过滤网膜 检查退膜段温度 退膜 检查退膜段压力 退膜液自动添加检查 更换退膜缸 检查退膜后清洁风干段的过滤芯并清洁,风刀有堵塞用气吹或高压水冲洗 退膜段排水30S钟,以防堵塞排水管路ຫໍສະໝຸດ RD-CM-WI01S1A
PCB光成像工艺知识

磨板的控制
五、无尘房的控制
无尘房需控制的条件
温度 湿度 压力 空气中尘粒含量 光线
温度控制
a. 温度过高,干膜容易融边,而且干膜 溶剂挥发影响贴膜效果。
b. 菲林尺寸稳定性会受温度的影响。 *温度对黄菲林影响:(10-20)*10-6 / 0C例如长度为24” 的菲林,温度升高10C,长度约增加 24*1000*(10~20)*10-6=0.24~0.48mil/0C
传送速度决定。
附表(生产时以传送速度作为参考)
压力 速度
3bar
1m/min 0.72sec.
2m/min 0.36sec.
3m/min 0.24sec.
4bar
0.82Sec. 0.41Sec. 0.27பைடு நூலகம்ec.
5bar
0.91Sec. 0.45Sec. 0.30Sec.
贴膜辘对贴膜效果的影响
贴膜辘对良率的影响
效果的决定因素
a.真空框的密封性 b.抽真时间 c.真空泵工作收况 d.擦真空好坏决定
赶气与偏位
1、刚刚合上框架,抽真空时,赶气力度不 可过大。以免菲林与偏移 2、厚板由于麦拉膜的真空时的变形会引起 菲林的移动,所以单面曝光较合适
牛顿环判断真空效果(有牛顿环出现,且不移动)
1、牛顿环出 现,当不再移 动,表示气体 已经不在流动 且接近真空。
磨痕类型
磨板的控制
E、磨板后质量检查
a.目检板面是否有氧化、水迹、污物. 板面清洁度 。 b.水膜测试 测试方法:取板面清洁处理后的板,用水浸湿板面并垂直放置,用秒 表测量水腊膜破裂的时间, c.板面粗糙度:经磨板后的板面粗糙程度(2.0µ m左右).
* 行业界人员定义一些参数衡量粗糙度如 Ra;表面取样长度内基准线上所有距离绝对值 的算术平均值;一般0.2-0.4µ m.Rt;表面取样长度内最高峰顶和最低谷度之间的距离 1.5-3.0µ m一般用目视法估计,较少用科学仪器检测。粗糙度由:磨刷材料,磨料粒度, 磨板时的功率等共同决定。
干膜曝光工艺(一)
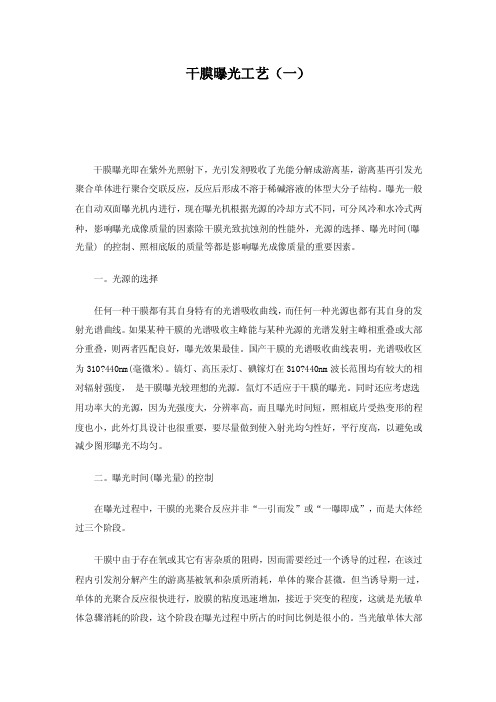
干膜曝光工艺(一)干膜曝光即在紫外光照射下,光引发剂吸收了光能分解成游离基,游离基再引发光聚合单体进行聚合交联反应,反应后形成不溶于稀碱溶液的体型大分子结构。
曝光一般在自动双面曝光机内进行,现在曝光机根据光源的冷却方式不同,可分风冷和水冷式两种,影响曝光成像质量的因素除干膜光致抗蚀剂的性能外,光源的选择、曝光时间(曝光量) 的控制、照相底版的质量等都是影响曝光成像质量的重要因素。
一。
光源的选择任何一种干膜都有其自身特有的光谱吸收曲线,而任何一种光源也都有其自身的发射光谱曲线。
如果某种干膜的光谱吸收主峰能与某种光源的光谱发射主峰相重叠或大部分重叠,则两者匹配良好,曝光效果最佳。
国产干膜的光谱吸收曲线表明,光谱吸收区为310?440nm(毫微米)。
镐灯、高压汞灯、碘镓灯在310?440nm波长范围均有较大的相对辐射强度,是干膜曝光较理想的光源。
氙灯不适应于干膜的曝光。
同时还应考虑选用功率大的光源,因为光强度大,分辨率高,而且曝光时间短,照相底片受热变形的程度也小,此外灯具设计也很重要,要尽量做到使入射光均匀性好,平行度高,以避免或减少图形曝光不均匀。
二。
曝光时间(曝光量)的控制在曝光过程中,干膜的光聚合反应并非“一引而发”或“一曝即成”,而是大体经过三个阶段。
干膜中由于存在氧或其它有害杂质的阻碍,因而需要经过一个诱导的过程,在该过程内引发剂分解产生的游离基被氧和杂质所消耗,单体的聚合甚微。
但当诱导期一过,单体的光聚合反应很快进行,胶膜的粘度迅速增加,接近于突变的程度,这就是光敏单体急骤消耗的阶段,这个阶段在曝光过程中所占的时间比例是很小的。
当光敏单体大部分消耗完时,就进入了单体耗尽区,此时光聚合反应已经完成。
该过程类似于原子弹爆炸的过程。
正确控制曝光时间是得到优良的干膜抗蚀图像非常重要的因素。
当曝光不足时,由于单体聚合的不彻底,在显影过程中,胶膜溶涨变软,线条不清晰,色泽暗淡,甚至脱胶,在电镀前处理或电镀过程中,膜起翘、渗镀、甚至脱落。
线路板干膜流程
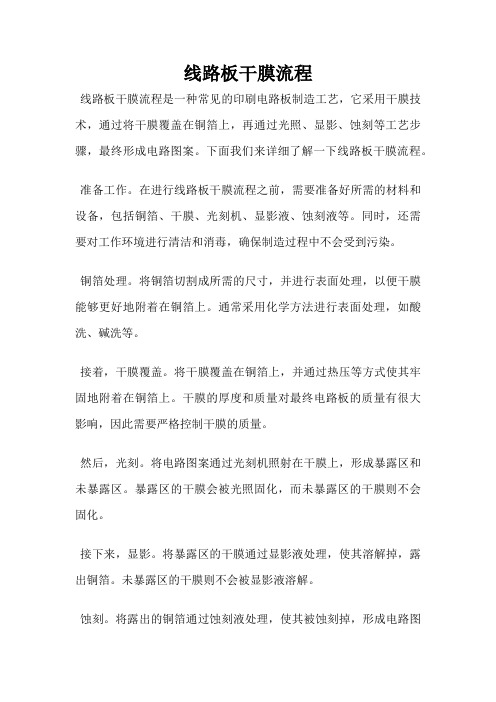
线路板干膜流程
线路板干膜流程是一种常见的印刷电路板制造工艺,它采用干膜技术,通过将干膜覆盖在铜箔上,再通过光照、显影、蚀刻等工艺步骤,最终形成电路图案。
下面我们来详细了解一下线路板干膜流程。
准备工作。
在进行线路板干膜流程之前,需要准备好所需的材料和设备,包括铜箔、干膜、光刻机、显影液、蚀刻液等。
同时,还需要对工作环境进行清洁和消毒,确保制造过程中不会受到污染。
铜箔处理。
将铜箔切割成所需的尺寸,并进行表面处理,以便干膜能够更好地附着在铜箔上。
通常采用化学方法进行表面处理,如酸洗、碱洗等。
接着,干膜覆盖。
将干膜覆盖在铜箔上,并通过热压等方式使其牢固地附着在铜箔上。
干膜的厚度和质量对最终电路板的质量有很大影响,因此需要严格控制干膜的质量。
然后,光刻。
将电路图案通过光刻机照射在干膜上,形成暴露区和未暴露区。
暴露区的干膜会被光照固化,而未暴露区的干膜则不会固化。
接下来,显影。
将暴露区的干膜通过显影液处理,使其溶解掉,露出铜箔。
未暴露区的干膜则不会被显影液溶解。
蚀刻。
将露出的铜箔通过蚀刻液处理,使其被蚀刻掉,形成电路图
案。
未被蚀刻的铜箔则保留下来,成为电路板的导线。
以上就是线路板干膜流程的主要步骤。
通过这种工艺制造出来的电路板质量稳定、精度高,广泛应用于电子产品制造领域。
- 1、下载文档前请自行甄别文档内容的完整性,平台不提供额外的编辑、内容补充、找答案等附加服务。
- 2、"仅部分预览"的文档,不可在线预览部分如存在完整性等问题,可反馈申请退款(可完整预览的文档不适用该条件!)。
- 3、如文档侵犯您的权益,请联系客服反馈,我们会尽快为您处理(人工客服工作时间:9:00-18:30)。
干膜光成像工艺规范目录1.目的---------------------------------------------------------------------------------42.范围---------------------------------------------------------------------------------43.定义---------------------------------------------------------------------------------44.操作方法-------------------------------------------------------------------------4-5 5.磨板-------------------------------------------------------------------------------6-9 6.贴膜------------------------------------------------------------------------------9-11 7.曝光-----------------------------------------------------------------------------11-13 8.显影-----------------------------------------------------------------------------13-17 9.检查-----------------------------------------------------------------------------17-1810.故障与排除---------------------------------------------------------------------18-19注意:以下所有数据建议参考,与你公司如有相同实属巧合。
1.目的:本文旨在建立干膜光成像工艺之操作规范及工艺控制要求、设备之日常维护方法和要求。
2.范围: 适用于线路板光成像工艺过程之干膜、曝光、显影工序。
3.定义:光成像——指将底片的线路图像移到覆铜板上,形成一种抗蚀或抗电镀的掩膜图像。
4.操作方法4.1安全。
4.1.1化学溶液加入槽中时,应戴橡胶手套,必要时戴上安全眼镜,眼睛和皮肤避免与其接触,如果化学溶液溅到皮肤上,需立即用自来水进行冲洗, 并报告领班。
4.1.2溅到地上的化学药品须立即擦净。
4.1.3操作时不要观看紫外光源。
4.1.5酒精、丙酮等易燃品使用完后应盖好盖子。
4.2主要设备4.3主要物品4.4制程能力4.5工艺流程图4.5.1双面板制作过程4.5.2内层板制作过程:内层底片铆合4.6 工艺环境及要求4.6.1 生产前对所有设备和周围环境进行约30分钟的擦拭或吸尘等清洁工作,所有工作区域都必须保持干净整洁。
4.6.2 贴膜、曝光间属四级空调区,环境要求:温度21±2℃,湿度55+8-5%,该区照明灯为安全黄光灯,室内不得漏白光。
4.6.3 进入贴膜、曝光间必须穿防静电服(防尘服),并经风淋门风淋10秒以上,风淋时应将两侧门关紧,将风淋嘴对准防静电服全身风淋。
4.6.4 防静电服的着装方法:先戴帽,将头发置于帽内,再穿衣、以裤束紧上衣,以袜束紧裤脚,防静电服只能在指定范围内穿着,并要保持整洁。
4.6.5 风淋门不允许开着或半掩着,不允许两道门同时是开启状态,否则有过量的灰尘和污物进入,不许将有灰尘的物品(如纸箱)带入工作区域内。
风淋门前面的过道每天必须进行清洁。
4.6.6 除了对位、曝光人员不戴手套取放板子外,工序的其它工位(磨板、贴膜、显影、检板)取放、接收板子的人员一律要戴洁净干燥的白细纱手套取放板子,磨板接板贴膜放板人员戴指套操作。
并要做到轻拿轻放,手指不得触及线路图形,板角不得碰伤其它板的铜面或干膜线路。
5. 磨板5.1目的:保证贴膜前的板面干燥清洁无氧化、胶渍等污物。
5.1.1 物料:硫酸(工业)、尼龙磨刷(第1对为320目,第2对为500目)。
5.1.2 工具:吸管、胶手套、无毛白纱手套。
5.2工序流程:5.3 工艺条件5.4操作方法5.4.1开机:依次打开下列开关。
5.4.2配制药水5.4.2.1先放掉旧药水、清洗缸内残渣。
5.4.2.2加入100升自来水,用虹吸管吸取2升硫酸,缓缓加入水中。
5.4.2.3开机循环3-5min即可投入使用,一般要求每班要换一次药水。
5.4.3关机:依开机的相反顺序进行。
5.5检测判断方法5.5.1一般通过磨痕试验和水膜破裂试验来检测磨板效果,要求磨出来的板干燥洁净,无污迹、氧化点。
5.5.2磨痕试验:取一块未经钻孔或已钻孔但未作图形的且与生产板同厚度的覆铜板作试板。
5.5.2.1打开输送→放板入上(下)刷位置→关闭输送→调动磨刷进给压力到设定值→打开上(下)刷喷啉并磨板8-10秒→关闭磨刷→打开输送→取出试板。
5.5.2.2将板子传送出来,检查上(下)刷的磨痕是否均匀,宽度在10-15mm之间,过窄则顺时针方向旋转调压手柄调大进给压力,过宽则逆时针方向旋转调压手柄减少进给压力,直到磨痕宽度在要求范围内,同时查相应的电表头指示值是否正确,并要求工作员工在试板上作记录(时间、板子厚度、磨刷压力,磨痕宽度)。
5.5.3水膜破裂试验将刚磨出来的板,浸入干净的水中,然后取出竖直放置,若水膜能保持15秒以上,说明此板合格,否则重新调试直到符合要求为止。
5.6安全生产5.6.1当调整好磨板各参数后,先做磨痕试验和水膜破裂试验,然后试刷3-5块板,检查整个磨板系统是否正常,磨出来的板是否干燥洁净,有无污渍、水迹、氧化点,合格后方可批量生产。
5.6.2接板员工将检查合格的板先插架放置3-6min,再叠板放置(0.6mm以下的薄板可直接叠板放置),为了防止板子放置时间太长、板面氧化导致贴膜不牢,原则上要求现磨现贴,但积板数量不许超过100块且存板时间不可超过一小时。
否则需重新磨板。
5.6.3为了防止磨刷不均匀磨损成腰鼓形,批量磨板时,放板要左右均匀放置,通常每个月用80目砂纸将磨刷整平一次。
5.6.4磨刷使用寿命每道磨刷通过板子的长度累积达4万至5万米,要求更换该道磨刷,并作相关的运行记录。
5.6.5吸水辊应以清水充分润湿,不许让吸水辊干燥工作,一般要求2个月换一次吸水辊。
5.7注意事项:5.7.1取硫酸时,需戴手套,用吸管吸取,以免发生意外。
5.7.2为防止磨板时叠板,放板时要求板与板的间距约10mm。
5.8维护与保养5.8.1日保养5.8.2周保养,除日保养以外,每周周末进行一次大保养。
5.8.3月保养:除日保养、周保养以外,由维修负责人负责安排人员每月月底进行一次大保养。
a.将各输送轮、压轮、吸水辊、过滤网、风刀、喷管、喷咀,拆出进行全面保养,整机大清洁,同时保养课安排人员对机器作全面检修,并作维护记录。
b.清洗方法:3%-5%的NaOH溶液浸泡约30的H2SO4洗20-30分钟→清水冲洗干净(除风刀和钢制压辊外)。
c.风刀和钢制压辊,先用吸尘器吸风刀口内的灰尘杂物,再用清水冲洗干净。
d.各喷咀保持畅通,有堵塞现象的用牙签穿透,以确保喷出的水呈扇形,且与磨刷轴向平行,同时磨刷处之喷淋必须均匀喷在磨刷上。
e.保养完毕、安装后要先试运转,试磨一块废板,合格后方可生产。
6.贴膜6.1目的:通过热压方式将干膜抗蚀剂贴附在清洁的铜面上。
6.2工具:介膜刀片、刮胶擦、框架。
6.2.1物料:干膜、无毛白纱手套、指套、压辘。
6.3流程:6.4工艺条件:6.4.1压辘(上/下)温度:100-120℃,最佳范围:110±5℃6.4.2气压:40-55psi一般金板:45-50psi,喷锡板:40-50psi6.4.3速度:1.0-1.5m/min,最佳1.1-1.3m/min。
一般大压辘机2.0-2.7格,最佳2.5格,小压辘机4.5-6格,最佳5格,用秒表测出一块已知长度的板经过压辘所需的时间再用已知长度(m)与所需时间(min)的比值即为速度。
6.4.4贴膜出板表面温度:40-65℃,最佳50±5℃(一般用接触式电子测温仪轻轻接触板面即可测得)6.5操作规程6.5.1开机:依次打开下列开关6.5.2打开机后先预热15min左右。
6.5.3戴指套对板面进行检查,必须保证压膜前的板面干燥清洁无氧化、无污渍、磨痕均匀。
6.5.4待机器进入正常待压干膜状态,将板子平放在上、下两压辘的输送口间,后试压膜一块。
6.5.5检查试压膜的板,若板面无气泡、无起皱、无干膜碎、无流胶、颜色均匀,且单边露铜不大于3-5mm,则可批量生产。
6.5.6贴膜合格的板不允许平叠,要求先插架冷却之后,再竖直叠板放置于专用架子上,静置15min后再转下工序。
6.5.7关机:依开机的相反顺序进行。
6.5.8换干膜:6.5.8.1根据所要生产的板来选择对应尺寸的干膜,一般生产板的大小和干膜大小基本一致或略小于板宽4-6mm最佳,但单边露铜不能超过5mm。
6.5.8.2关掉转动开关,去掉剩的旧干膜(不允许超过三英尺即91.5cm)。
6.5.8.3用刮胶擦或酒精擦洗压辘上的干膜碎等杂物。
6.5.8.4装上新干膜,将上、下两卷干膜对齐调试合格后方可生产。
6.5.8.5换干膜后的左视图如下:1,4表示上、下压辘2,5表示干膜3,6表示保护膜6.6安全、注意事项:6.6.1为了防止贴膜起皱、起泡,要求气压保持充足,不低于40psi,上、下压辘轴向平行、贴紧无空隙,均速运转。
6.6.2为了防止板边干膜碎介膜不净,引起开短路,通常要求磨板前的板子均须磨斜边。
6.6.3不允许用刀片、指甲或硬的工具清理压辘,以防划伤、损坏压辘,通常压辘无划痕、凹坑则不需要换。
贴膜人员要注意手或衣袖不要距压辘太近,以防卷入。
6.6.4控制好压辘的温度、气压、速度,随时观察是否在控制范围之内,若有异常现象,按急停开关,及时向领班或课长汇报。
6.6.5贴膜放板时,要求板与板之间距离保持5±2mm,防止板子重叠损坏压辘,距离过大则浪费干膜,造成不必要的损失。
6.6.6介膜时不允许刀片伤及板面,如聚酯膜被拉起或破裂,并经常检查压辘是否清洁。
6.6.7贴膜后合格的板最好在48小时之内完成曝光。
6.6.8为了追溯品质问题,每次将干膜拆箱后要求将商标贴在干膜卷桶内。
6.7维护与保养6.7.1日保养6.7.2每班一次由当班领班负责用测温仪检测压辘实际温度,若有异常及时通知保养课人员及时校正或修理。