模具4-1斜顶机构
模具4-1斜顶机构
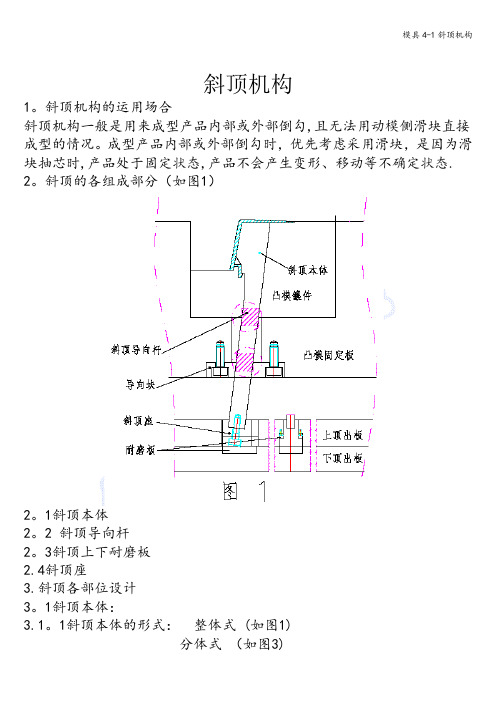
斜顶机构1。
斜顶机构的运用场合斜顶机构一般是用来成型产品内部或外部倒勾,且无法用动模侧滑块直接成型的情况。
成型产品内部或外部倒勾时,优先考虑采用滑块,是因为滑块抽芯时,产品处于固定状态,产品不会产生变形、移动等不确定状态. 2。
斜顶的各组成部分(如图1)2。
1斜顶本体2。
2 斜顶导向杆2。
3斜顶上下耐磨板2.4斜顶座3.斜顶各部位设计3。
1斜顶本体:3.1。
1斜顶本体的形式:整体式 (如图1)分体式(如图3)在条件允许的情况下,尽可能采用分体式斜顶结构,易加工易维修,加工成本低。
导向杆采用圆杆,与斜顶块头部用螺纹销钉骑缝连接,防止销钉脱落,与滑动块连接头部削扁,用螺钉连接,要求螺钉能够从模具后面拆卸,底板和推板铣通孔,方便模具维修保养。
分体式结构设计时,斜顶本体的背面斜度大于斜顶导向杆的度数1~2度,防止斜顶本体背面与凸模产生磨擦,同时斜顶的两侧面要求设计配作斜度,一般情况下,斜度为3度.3.1.2斜顶的抽芯距离及斜度计算抽芯距离: S =倒勾 + (3~5)mm余量斜度: tgα= S / H (H:顶出行程)α要取整,且一般 3°≦α≦ 15°(特殊情况α可以加大)3。
1.3斜顶的基本拆模:当斜顶的宽度在取值方面不受产品的形状限制时,可以如图A中一样宽度方向取值,否则,当受产品形状限制时,则如B中宽度应取保证在产品的公差范围内,这样处理以便于线割加工处理.另外,在斜顶成型的产品成型面应尽量减小,即尽量减小斜顶成型面,增大成型面的脱模角,以防止斜顶脱模后退时,拉弯成型面。
(如图4)在条件允许的前提下,斜顶本体与导向杆之间设计台阶止退面,承受注塑压力,避免注塑压力引起导向杆和推板变形,确保产品尺寸稳定和模具使用寿命。
止退面宽度3~5mm,与导向杆连接处增加工艺R角,防止应力开裂。
根据产品的具体情况,台阶止退面可以是一个面、两个面、三个面或四个面,同时两侧或背面要设计配合角度,一般为3度。
注塑模具斜顶(Slider)设计介绍本月修正简版
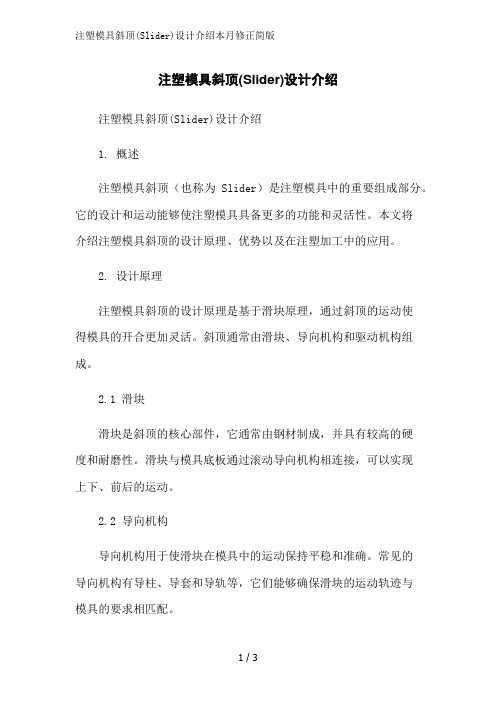
注塑模具斜顶(Slider)设计介绍注塑模具斜顶(Slider)设计介绍1. 概述注塑模具斜顶(也称为Slider)是注塑模具中的重要组成部分。
它的设计和运动能够使注塑模具具备更多的功能和灵活性。
本文将介绍注塑模具斜顶的设计原理、优势以及在注塑加工中的应用。
2. 设计原理注塑模具斜顶的设计原理是基于滑块原理,通过斜顶的运动使得模具的开合更加灵活。
斜顶通常由滑块、导向机构和驱动机构组成。
2.1 滑块滑块是斜顶的核心部件,它通常由钢材制成,并具有较高的硬度和耐磨性。
滑块与模具底板通过滚动导向机构相连接,可以实现上下、前后的运动。
2.2 导向机构导向机构用于使滑块在模具中的运动保持平稳和准确。
常见的导向机构有导柱、导套和导轨等,它们能够确保滑块的运动轨迹与模具的要求相匹配。
2.3 驱动机构驱动机构通过控制斜顶的运动方式和速度,实现模具的开合和产品的成型。
驱动机构通常由液压缸、气缸或电机等组成,根据注塑加工的需求选择合适的驱动机构。
3. 优势注塑模具斜顶在注塑加工中具有以下优势:3.1 提高产品质量斜顶的运动可以使模具开合更为灵活,从而使产品的成型更加完整和精确。
它可以减少产品的缺陷和变形,提高产品的质量。
3.2 扩展模具功能通过合理设计和安装斜顶,可以实现多腔模具、插件腔、嵌件及特殊结构的模具设计。
这种灵活的设计使得模具具备更多的功能,满足不同产品的需求。
3.3 增加生产效率斜顶的运动速度较快,可以加快模具的开合速度,从而提高注塑生产效率。
,斜顶还能够减少模具的运动阻力,降低注塑机的能耗。
4. 应用领域注塑模具斜顶在各个领域的注塑加工中都有广泛的应用。
它适用于各种注塑产品的生产,包括塑料零件、橡胶制品、注塑包装等。
5. 结论注塑模具斜顶的设计和运动原理使得注塑加工更加灵活和高效。
它的优势在提高产品质量、扩展模具功能和增加生产效率方面都得到了充分的展现。
在实际注塑加工中,合理设计和运用注塑模具斜顶将带来更好的加工效果和经济效益。
模具斜顶

模具斜顶模具斜顶又名斜梢,斜顶是以港资模具厂为主的珠三角地区模具行业的惯用说法,是模具设计中用来成形产品内部倒钩的机构,适用于比较简单的倒钩情况。
模具种类模具分类方法很多,过去常使用的有:按模具结构形式分类,如单工序模,复式冲模等;按使用对象分类,如汽车覆盖件模具、电机模具等;按加工材料性质分类,如金属制品用模具,非金属制用模具等;按模具制造材料分类,如硬质合金模具等;按工艺性质分类,如拉深模、粉末冶金模、锻模等。
这些分类方法中,有些不能全面地反映各种模具的结构和成形加工工艺的特点,以及它们的使用功能。
为此,采用以使用模具进行成形加工的工艺性质和使用对象为主的综合分类方法,将模具分为十大类,见表1各大类模具,又可根据模具结构、材料、使用功能以及制模方法等分为若干小类或品种。
序号模具类型模具品种成形加工工艺性质及使用对象1 冲压模具(冲模)冲裁模(无、少废料冲裁、整修、光洁冲裁、深孔冲裁精冲模等),弯曲模具,拉深模具,单工序模具(冲裁、弯曲、拉深、成形等),复合冲模,级进冲模;汽车覆盖件冲模,组合冲模,电机硅钢片冲模板材冲压成形2 塑料成型模具压塑模具,挤塑模具,注射模具(立式、式、角式注射模具);热固性塑料注射模具,挤出成形模具(管材、簿膜扁平机头等)发泡成形模具,低刀具工具泡注射成形模具,吹塑成形模具等塑料制品成形加黄岩工艺(热固性和热塑性模塑料)3 压铸模热室压铸机用压铸模,立式冷室压铸机用压铸模,臣式冷室压铸机用压铸模,全立式压铸机用压铸模,有色金属(锌、铝、铜、镁合金)压铸,黑色金属压铸模有色金属与黑色金属压力铸造成形工艺4 锻造成形模具模锻和大型压力机用锻模,螺旋压力机用锻模,平锻机锻模,辊锻模等;各种紧固件冷镦模,挤压模具,拉丝模具,液态锻造用模具等金属零件成形,采用锻压、挤压5 铸造用金属模具各种金属零件铸造时采用的金属模型金属浇铸成形工艺6 粉末冶金模具成形模:手动模:实体单向压制、实体双向压制手动模;实体浮动压模机动模:大型截面实体浮动压模,极掌单向压模,套类单向、双向压模,套类浮动压模整形模:手动模:径向整形模,带外台阶套类全整形模,带球面件整形模等机动模:无台阶实体件自动整形模,轴套拉杆式半自动整形馍,轴套通过式自动整形模轴套全整形自动模,带外台阶与带外球面轴套全整形自动模等粉末制品压坯的压制成形黄岩艺。
注塑模具斜顶(侧抽芯.-滑块)介绍-(含动画演示)知识分享
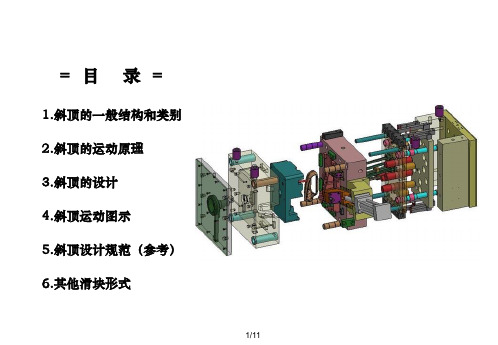
为M°。这个角度才是我们所需要的斜顶斜面的倾角度。 6. 其它的内容可根据前面所讲的结构及其要求完成斜顶其他部分 的设计。
其实,像上面这么复杂的内容主要的目地是教我们如何去求出 顶的倾角度。我们可以简化为如右图所示:我们可以得出三角函数 tgM°=顶行程/顶出行程。此时要求出M°是多大就很容易了,也可 以直接在图纸上测量出来。
8/11
5.斜顶设计规范(参考)
*斜顶要注意的问题: 1)斜顶的斜度一般在15度以下,度要尽可能小. 2)斜顶的强度,顶的斜度与顶出距离之间要协调. 3)要考虑产品是否会粘顶,有否做定位拉住产品.一般不用图C)的形式,尽量采用图A)与图B)形式.
图A
图B
图C
9/11
5.斜顶设计规范(参考)
*斜顶要注意的问题: 4)要检查顶头部是否为反度(顶出会铲胶),要注意斜顶是否会与其它部件干涉(如其它斜顶,顶针,骨位),一定要校核.
干涉 干涉
10/11
刻字区域干涉
6.其他滑块形式
一、液压或气动抽芯机构 液压或气动抽芯与机动抽芯的区别: 液压或气压抽芯是通过一套专用的控制系统来控制活塞的运动实现的,其抽芯动作可不受开模时间和
推出时间的影响。 液压传动与气压传动抽芯机构的比较:液压传动平稳,且可得到较大的抽拔力和较长的抽芯距离。
可以处理死角了。
动画演示
动画演示
4/11
3.斜顶的设计
前提条件:已经确定了模板、模仁、模架的尺寸。具体如右图所示。
1. 查看图纸,仔细分析,确定死角的大小。如图所示。 2. 确定0°靠破面的起点,并且确定其长度(如图AB)。如果不设
模具斜顶结构设计和顶出行程计算
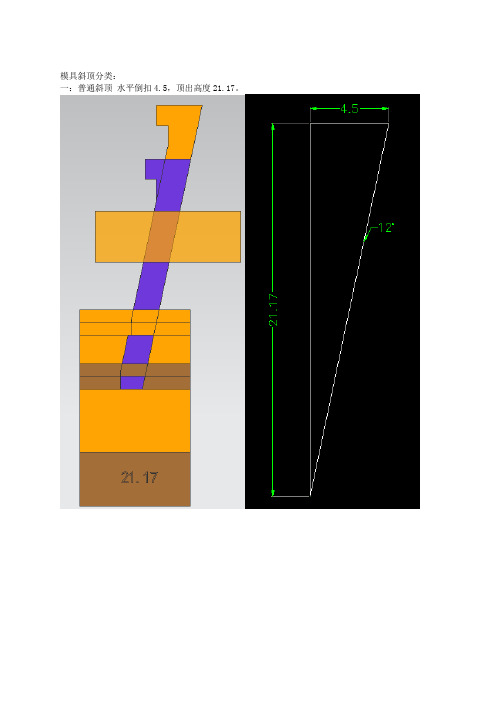
模具斜顶分类:
一:普通斜顶水平倒扣4.5,顶出高度21.17。
模具斜顶分类:
二. (1)斜斜顶(下落斜顶/下坡斜顶/延迟斜顶)水平倒扣4.5,顶出高度21.96
模具斜顶分类:
二. (2)斜斜顶(上坡斜顶/加速斜顶),水平倒,顶出行程20.37
模具斜顶分类:
三.(1)大角度斜顶—平行杆斜顶,计算方法和普通斜顶一样。
详解:产品倒扣较大,斜顶角度超过12°,斜顶多次斜向受力容易损坏,增加平行辅助杆。
可延伸为平行杆斜斜顶结构。
增加了平行杆的斜顶,斜顶座沿着平行杆运动,即:斜顶座也沿着倒扣轨迹运动,斜顶顶出距离和普通斜顶计算方法一样。
三.(2) 大角度交叉杆斜顶。
其他参数不变,分
解的角度5.51°
其他参数不变,分
解的角度5.61°
产品斜向倒扣角度比较大,控制斜斜顶运动轨迹的斜顶座角度太大,容易卡机构。
为了分解斜顶
座角度设置的辅助结构。
资料整理工程:赵小强 2019.11.20 上海立卡塑料托盘制造有限公司。
注塑模具结构及设计斜顶强脱

注塑模具结构及设计斜顶强脱注塑模具是在注塑中使用的一种工具,其作用是为塑料制品提供形状和尺寸。
注塑模具包括模板、压头、割切刀、定位装置和脱模系统等组成部分。
其中,斜顶强脱是注塑模具中常见的设计特征之一。
本文将介绍注塑模具的结构以及斜顶强脱的设计原理和优势。
注塑模具的结构注塑模具的结构由一些不同部分组成,如模板、压头和割切刀。
这些部分通常由坚固的金属制成,以承受高压和高温的注塑流体。
注塑模具的主要部分包括:1.模板:模板是注塑模具的主要结构部分,它最终将塑料制品成型。
模板的形状和尺寸会确定成品产品的形状和尺寸。
2.压头:压头是通过注塑流体将塑料材料流入模板中的部分。
它通常会被设计成尽可能接近所需形状的形态,以确保塑料材料可以很好地流动到模板中。
3.割切刀:割切刀是将成品产品从模板中切割出来的部分。
它通常在模塑设计中具有重要地位。
4.定位装置:定位装置是指导模具的移动和定位的部分,以确保在生产过程中有正确的操作序列。
5.脱模系统:用于辅助前面几个部分顺利完工的部分。
脱模系统主要由斜顶、脱模销和推力机构组成,其中斜顶强脱发挥的重要作用。
斜顶强脱的设计原理在注塑模具中,斜顶强脱是减少模具脱模间隙的重要技术。
当模具中的注塑原料加热加压,塑料材料会依据模板的形状和尺寸流入模板中。
模板最终会冷却,使材料成为一体的形态。
由于注塑材料与模具间的摩擦阻力,一旦材料冷却在模具的表面,很难将其从模板上取出。
这就需要采用斜顶强脱来帮助脱模。
在斜顶强脱的设计中,斜顶部分会斜向模板表面,以减小模具与注塑材料表面的摩擦。
斜顶的角度及形状要根据材料和模具的特性进行调整,以确保最佳效果。
脱模销通常安装在模板和斜顶之间,通过施加一定的力来将模板推离斜顶。
推力机构通常由气缸、液压缸或其他形式的弹簧组成,以提供所需的脱离力量。
斜顶强脱的优势斜顶强脱提供了许多优势,这些优势既包括质量的方面,也包括生产的效率和节约成本。
以下是斜顶强脱的一些主要优势:1.提高生产效率 - 在注塑制造过程中,利用斜顶强脱可以减少模具更换的频率,因此可以节约生产时间和提高生产效率。
“斜顶式”滑块机构在模具中的应用
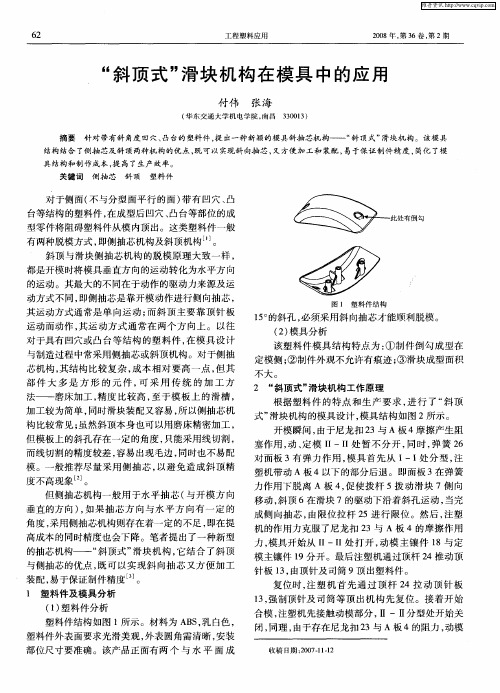
和 F 两 个 力 , 是 促使 滑 块 向外 移 动 的 力 ( 拨 : 抽
力 )F 为使 滑块 向上 移动 的力 , ,: 但滑 块安 装 在模 板
与侧抽 芯 的优 点 , 可 以实 现斜 向抽 芯 又方 便加 工 既 装配 , 易于保证 制件精 度 。
1 塑料 件及模 具分 析
力, 模具开始从 I— I I I处打开 , 动模主镶件 1 8与定
模 主镶件 l 开 。最 后注 塑机通 过顶杆 2 动顶 9分 4推 针板 1, 3 由顶 针及 司筒 9顶 出塑 料件 。
闭, 同理 , 由于存在 尼龙扣 2 3与 A板 4的阻 力 , 动模
收 稿 日期 :07 1—2 20 —11
塑料件 外表 面要求光 滑美 观 , 外表 圆角需 清 晰 , 安装
部位尺 寸要准确 。该 产品 正面有 两 个 与 水 平 面 成
维普资讯
力 作用 下脱 离 A板 4 促 使拨 杆 5拨 动滑块 7侧 向 , 移 动 , 顶 6在滑块 7的驱 动下沿 着斜孑 运动 , 斜 L 当完
成 侧 向抽 芯 , 限位拉 杆 2 由 5进行 限位 。然后 , 注塑
机 的作用 力克 服 了尼 龙扣 2 3与 A板 4的摩 擦 作用
角度 , 用侧抽 芯机构 则存 在着一 定 的不足 , 采 即在提 高成本 的 同时精度也会 下 降 。笔 者提 出了一种 新型 的抽芯 机构—— “ 斜顶 式 ” 块机 构 , 滑 它结 合 了斜 顶
维普资讯
6 2
工 程 塑 料 应 用
20 0 8年 , 3 第 6卷 , 2期 第
“ 顶 式 " 块 机 构 在 模 具 中 的 应 用 斜 滑付 伟 Nhomakorabea张 海
注塑模具斜顶(Slider)设计介绍
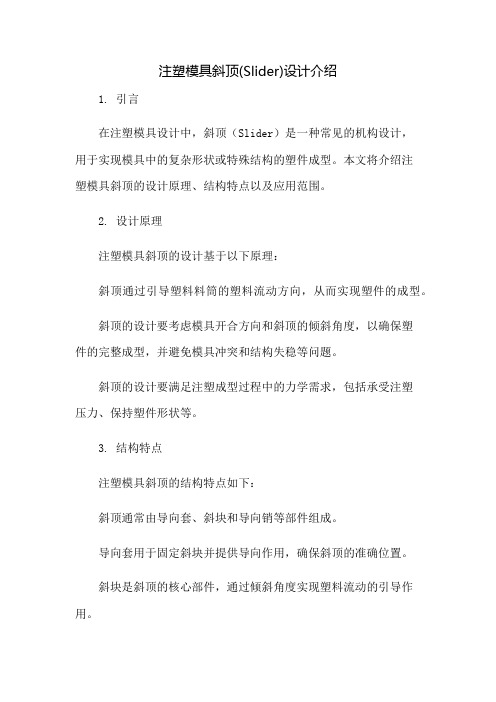
注塑模具斜顶(Slider)设计介绍1. 引言在注塑模具设计中,斜顶(Slider)是一种常见的机构设计,用于实现模具中的复杂形状或特殊结构的塑件成型。
本文将介绍注塑模具斜顶的设计原理、结构特点以及应用范围。
2. 设计原理注塑模具斜顶的设计基于以下原理:斜顶通过引导塑料料筒的塑料流动方向,从而实现塑件的成型。
斜顶的设计要考虑模具开合方向和斜顶的倾斜角度,以确保塑件的完整成型,并避免模具冲突和结构失稳等问题。
斜顶的设计要满足注塑成型过程中的力学需求,包括承受注塑压力、保持塑件形状等。
3. 结构特点注塑模具斜顶的结构特点如下:斜顶通常由导向套、斜块和导向销等部件组成。
导向套用于固定斜块并提供导向作用,确保斜顶的准确位置。
斜块是斜顶的核心部件,通过倾斜角度实现塑料流动的引导作用。
导向销用于固定斜顶和模具的其他部件,确保模具在注塑过程中的稳定性和精度。
4. 应用范围注塑模具斜顶的应用范围广泛:斜顶常用于注塑模具中塑件形状复杂、壁厚不均匀或存在特殊结构的成型。
斜顶可以实现塑件的脱模,避免模具结构复杂或受限制的情况下无法顺利脱模的问题。
斜顶的设计可以降低模具制造成本,减少模具的工序和材料损耗。
5.注塑模具斜顶是一种重要的设计机构,可以实现模具中复杂形状或特殊结构的塑件成型。
设计时需要考虑斜顶的倾斜角度、结构稳定性和塑料流动等因素。
斜顶的应用范围广泛,并可以降低模具制造成本。
在注塑模具设计中,合理使用斜顶可以提高注塑成型的效率和质量。
以上是关于注塑模具斜顶设计的介绍,希望对读者有所帮助。
注塑模具斜顶(侧抽芯. 滑块)介绍_(含动画演示)

注塑模具斜顶(侧抽芯.滑块)介绍_(含动画演示) 注塑模具斜顶(侧抽芯.滑块)介绍_(含动画演示)1.概述注塑模具斜顶是一种常见的模具结构,常用于制造具有倾斜表面的注塑产品。
它可以通过侧抽芯和滑块的组合来实现倾斜表面的成型。
本文将详细介绍注塑模具斜顶的结构和工作原理,并配备动画演示来直观展示其工作过程。
2.结构组成注塑模具斜顶主要包括以下几个部分:2.1 行动板行动板是注塑模具斜顶的主要部件,它通过导柱和导套与模具固定板连接。
行动板上安装有侧抽芯和滑块等结构。
2.2 侧抽芯侧抽芯位于行动板的侧面,通过斜顶导柱的支撑实现倾斜成型。
侧抽芯可由液压或气动驱动,具有很强的刚性和稳定性。
2.3 滑块滑块位于行动板的顶部,与侧抽芯配合完成模具的开合动作。
滑块通常采用液压或气动驱动,具有较大的滑动面积,能够承受较大的压力。
3.工作原理注塑模具斜顶的工作原理如下:3.1 开模状态在开模状态下,行动板向后移动,侧抽芯与滑块一起向上移动,使得模腔和侧抽芯脱离,产品顶出成型。
3.2 关模状态在关模状态下,行动板向前移动,侧抽芯与滑块一起向下移动,使得模腔和侧抽芯接合,形成闭合状态。
4.动画演示请参考附件中的动画演示文件,该文件将直观展示注塑模具斜顶的工作过程和各个组成部分的运动轨迹。
附件:动画演示文件(请参考附件文件名称,例如:InjectionMold_SlantingCore_Slider_Animation)法律名词及注释:1.注塑模具:指用于注塑成型的模具,可以通过模具的开合运动实现塑料制品的成形。
2.斜顶导柱:指在模具中用于支撑倾斜结构的导柱,常用于支撑侧抽芯。
3.滑块:指模具中用于实现于行动板相对运动的零件,用于模具的开合过程。
工厂实战解析-注塑模具斜顶机构问题与解决方法(顶块印)
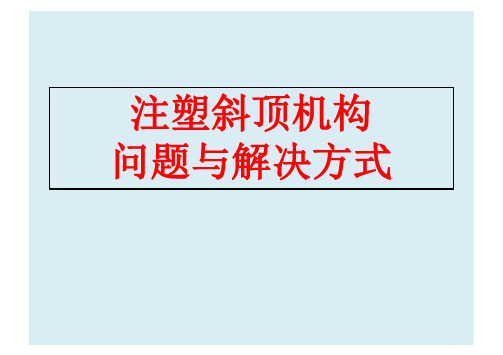
12/
顶块间隙大造成飞边
PP:0.03 ABS:0.05
在不产生飞边状况下,斜推机构 应采取松动配合,其目的是:
1.吸收斜推杆与斜推块中心 误差; 0间隙 2.防止热膨胀造成顶出阻力;
3.节省孔加工及配模工时;
0间隙 对策: 如左图间隙值采取松动配合。
13/
顶块旋转
塑料射压
∴钢料允许压缩压力 ∴塑料射压
HRC32:0.5t/c㎡ PP料 :350kgf/ c㎡
HRC44:0.8t/c㎡
ABS料: 400kgf/ c㎡
∴因此 (a ×b) ≥1/2(A ×B)
即斜顶块底部面积需大于顶部面积一半。
7/
斜顶杆长度太长
原因1:热膨胀因素 左图是杆长600mm,由30 ℃升到
10/
顶出板变形、翘曲
原因: 顶出板变形(强度不足)将造成顶出印与顶块
印,一般发生在细长型模具中央部位,与成形中可 用千分表接触后,观察成形射压后千分表变动状况 (允许值在0.05mm范围); 对策:
1.调整注塑机的顶出杆数量,一般细长型模具 顶出数5支,达到平衡顶出力,避免顶出集中变形;
2.检查顶针及顶杆配合公差,过紧状况增加顶 出力将会使顶针板变形。
腊 片
厚
L=0.9903 =2.827mm
故杆长研磨量=L-2mm=0.827mm
可于车床上切削研磨量即可达标准杆长。
9/
顶块冷却效果差
原因: 由第5页知道,温差50度时将造成侧壁面0.024膨胀,此膨胀量使推块上浮,使侧
壁紧压加大离模困难。 对策:
1.如第5页侧避面避空; 2.如上图,佛吉亚标准在宽度50mm以上时,加冷却水孔; 3.斜推侧壁间隙合模后必须以间隙规检测,在标准 范围(PP料0.03以内,ABS料 0.05以内)。
注塑模具斜顶(侧抽芯.-滑块)介绍-(含动画演示)资料讲解

液压抽芯机构带有锁紧装置,侧向活动 型芯设在动模一侧。成型时,侧向活动型芯 由定模上的锁紧块锁紧,开模时,锁紧块离 去,由液压抽芯系统抽出侧向活芯,然后再 推出制件,推出机构复位后,侧向型芯再复 位。
11/11
6.其他滑块形式
动画演示
二、机动侧向抽芯机构
利用注射机的开模力,通过传动机构改变运动方向,将侧向的活动型芯抽出。 机动抽芯机构的优、缺点: 结构较复杂,抽拔力较大,灵活、方便、生产效率高、容易实现全自动操作、 无需另外添置设备等。 结构形式为: 斜销、弹簧、弯销、斜导槽、斜滑块、楔块、齿轮齿条等 。
可以处理死角了。
动画演示
动画演示
4/11
3.斜顶的设计
前提条件:已经确定了模板、模仁、模架的尺寸。具体如右图所示。
1. 查看图纸,仔细分析,确定死角的大小。如图所示。 2. 确定0°靠破面的起点,并且确定其长度(如图AB)。如果不设
计0°靠破面,则选择A点作为斜顶斜面的起点。 3. 以B点为基准,偏一距离,如图BC,BC=顶出行程。 4. 以C点为基准,向顶移动的反方向偏一距离,如图CD。CD=斜
8/11
5.斜顶设计规范(参考)
*斜顶要注意的问题: 1)斜顶的斜度一般在15度以下,度要尽可能小. 2)斜顶的强度,顶的斜度与顶出距离之间要协调. 3)要考虑产品是否会粘顶,有否做定位拉住产品.一般不用图C)的形式,尽量采用图A)与图B)形式.
图A
图B
图C
9/11
5.斜顶设计规范(参考)
*斜顶要注意的问题: 4)要检查顶头部是否为反度(顶出会铲胶),要注意斜顶是否会与其它部件干涉(如其它斜顶,顶针,骨位),一定要校核.
2/11
1.斜顶的一般结构和类别
模具斜顶设计注意事项
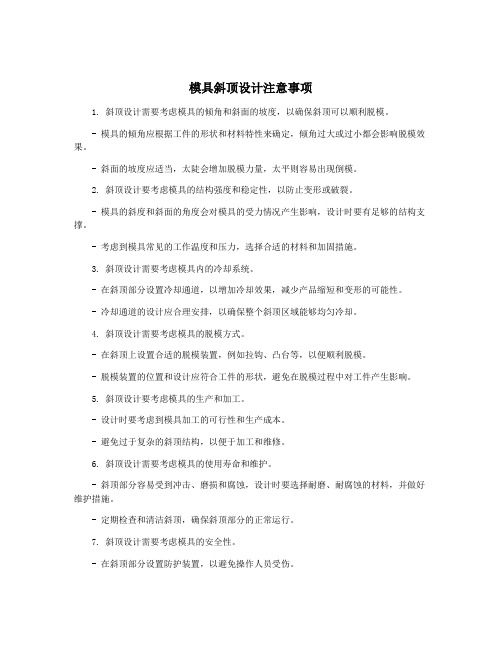
模具斜顶设计注意事项1. 斜顶设计需要考虑模具的倾角和斜面的坡度,以确保斜顶可以顺利脱模。
- 模具的倾角应根据工件的形状和材料特性来确定,倾角过大或过小都会影响脱模效果。
- 斜面的坡度应适当,太陡会增加脱模力量,太平则容易出现倒模。
2. 斜顶设计要考虑模具的结构强度和稳定性,以防止变形或破裂。
- 模具的斜度和斜面的角度会对模具的受力情况产生影响,设计时要有足够的结构支撑。
- 考虑到模具常见的工作温度和压力,选择合适的材料和加固措施。
3. 斜顶设计需要考虑模具内的冷却系统。
- 在斜顶部分设置冷却通道,以增加冷却效果,减少产品缩短和变形的可能性。
- 冷却通道的设计应合理安排,以确保整个斜顶区域能够均匀冷却。
4. 斜顶设计需要考虑模具的脱模方式。
- 在斜顶上设置合适的脱模装置,例如拉钩、凸台等,以便顺利脱模。
- 脱模装置的位置和设计应符合工件的形状,避免在脱模过程中对工件产生影响。
5. 斜顶设计要考虑模具的生产和加工。
- 设计时要考虑到模具加工的可行性和生产成本。
- 避免过于复杂的斜顶结构,以便于加工和维修。
6. 斜顶设计需要考虑模具的使用寿命和维护。
- 斜顶部分容易受到冲击、磨损和腐蚀,设计时要选择耐磨、耐腐蚀的材料,并做好维护措施。
- 定期检查和清洁斜顶,确保斜顶部分的正常运行。
7. 斜顶设计需要考虑模具的安全性。
- 在斜顶部分设置防护装置,以避免操作人员受伤。
- 检查和保持防护装置的完好性,及时修复或更换损坏的部件。
8. 斜顶设计需要考虑模具的产品质量。
- 斜顶部分对于工件的形状和尺寸有直接影响,设计时要确保产品的质量符合要求。
- 注意斜顶结构中可能出现的缺陷,例如水刀线、气泡等。
9. 斜顶设计需要考虑模具的使用方便性。
- 斜顶部分的设计应方便清理、维修和更换。
- 考虑到斜顶部分的可拆卸性,以方便模具的组装和拆卸。
10. 斜顶设计需要考虑模具的适应性和灵活性。
- 考虑产品的变更和新产品的开发,设计时要保证斜顶的适应性。
斜顶分型原则
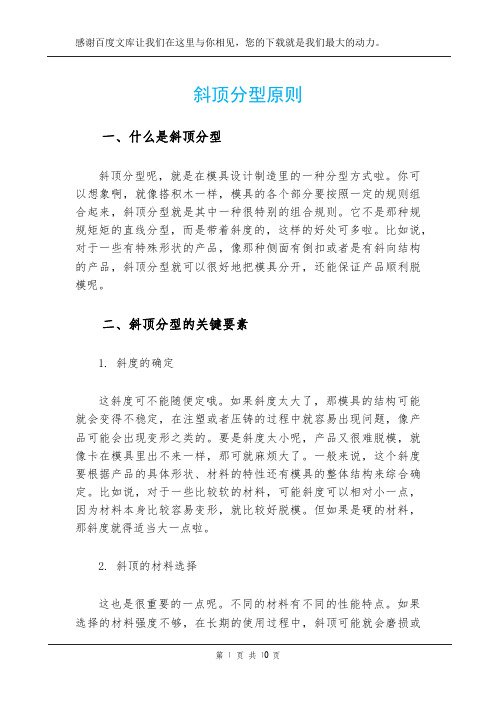
斜顶分型原则一、什么是斜顶分型斜顶分型呢,就是在模具设计制造里的一种分型方式啦。
你可以想象啊,就像搭积木一样,模具的各个部分要按照一定的规则组合起来,斜顶分型就是其中一种很特别的组合规则。
它不是那种规规矩矩的直线分型,而是带着斜度的,这样的好处可多啦。
比如说,对于一些有特殊形状的产品,像那种侧面有倒扣或者是有斜向结构的产品,斜顶分型就可以很好地把模具分开,还能保证产品顺利脱模呢。
二、斜顶分型的关键要素1. 斜度的确定这斜度可不能随便定哦。
如果斜度太大了,那模具的结构可能就会变得不稳定,在注塑或者压铸的过程中就容易出现问题,像产品可能会出现变形之类的。
要是斜度太小呢,产品又很难脱模,就像卡在模具里出不来一样,那可就麻烦大了。
一般来说,这个斜度要根据产品的具体形状、材料的特性还有模具的整体结构来综合确定。
比如说,对于一些比较软的材料,可能斜度可以相对小一点,因为材料本身比较容易变形,就比较好脱模。
但如果是硬的材料,那斜度就得适当大一点啦。
2. 斜顶的材料选择这也是很重要的一点呢。
不同的材料有不同的性能特点。
如果选择的材料强度不够,在长期的使用过程中,斜顶可能就会磨损或者变形,那模具的寿命就会大大缩短。
像一些高强度的合金钢就比较适合做斜顶,它不仅强度高,而且耐磨性也很好。
不过呢,合金钢的成本相对也比较高,所以在选择的时候也要考虑成本因素啦。
有时候也可以选择一些经过特殊处理的普通钢材,通过表面处理来提高它的硬度和耐磨性,这样既能满足要求,又能降低成本。
三、斜顶分型在不同模具中的应用1. 注塑模具中的斜顶分型在注塑模具里,斜顶分型用得可不少呢。
比如说在制作一些塑料盒子的时候,如果盒子的侧面有个小凸起或者是小凹陷,这个时候就可以用斜顶分型来制作模具。
在注塑的时候,塑料材料会填充到模具的型腔里,当注塑完成后,斜顶就可以沿着斜向运动,把产品从模具里顶出来,而且还能保证那个小凸起或者小凹陷的形状完整。
2. 压铸模具中的斜顶分型压铸模具和注塑模具有一些相似之处,但也有不同的地方。
模具行位和斜顶的设计经验要点
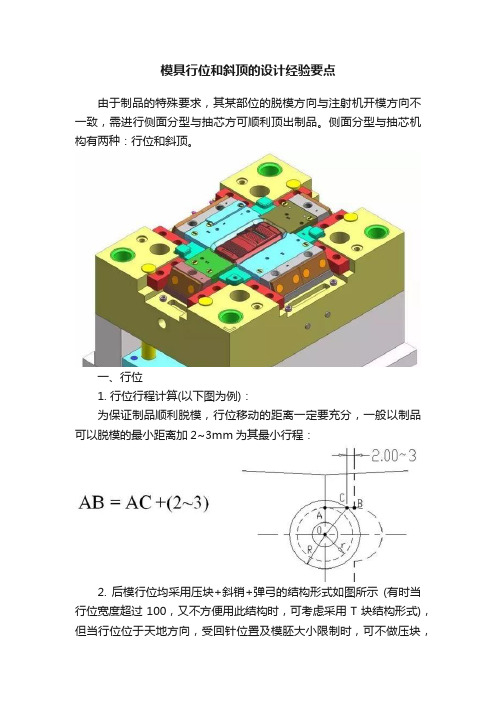
模具行位和斜顶的设计经验要点由于制品的特殊要求,其某部位的脱模方向与注射机开模方向不一致,需进行侧面分型与抽芯方可顺利顶出制品。
侧面分型与抽芯机构有两种:行位和斜顶。
一、行位1. 行位行程计算(以下图为例):为保证制品顺利脱模,行位移动的距离一定要充分,一般以制品可以脱模的最小距离加2~3mm为其最小行程:2. 后模行位均采用压块+斜销+弹弓的结构形式如图所示(有时当行位宽度超过100,又不方便用此结构时,可考虑采用T块结构形式),但当行位位于天地方向,受回针位置及模胚大小限制时,可不做压块,由模板原身出。
3. 行位底面、顶面与前后模底、顶面的关系,见图:4. 不论行位侧面是否有封胶,其两侧均要做斜度,一般值为单边3~5°,但当两个运动方向垂直的行位贴合时,角度为45°。
若产品四面均有行位互相贴合,设计时应考虑将其中一个行位伸出一耳朵,以保证准确定位。
5. 行位高度与厚度的比值最大为1,否则行位运动时会受翻转力矩影响,造成运动失效,一般要求L≧1.5H。
6. 行位斜销角度一般为15°~25°,最大不能超过25°,斜销角度比行位小2°,一般尽量不采用细小的斜销,以保证行位运动的顺利。
7. 斜销孔比斜销单边大1/64",约0.4,当斜销穿过行位时,需在模板上为其留出足够的让位空间。
8. 斜销在行位中位置的确定:斜销尽量置于行位的中间位置,具体尺寸要求如图:9. 铲鸡与行位的配合面要求超过行位高度的2/3,并且用于铲鸡的螺丝应尽量大,下图为两种不同结构的铲鸡,尽量避免采用图b的结构。
10. 行位弹弓长度的确定,应保证弹弓空间足够,防止弹弓失效。
设定行位行程为M,弹弓总长为L,设弹簧压缩40%,行位完全退出后,弹弓仍预压10%,则有:(40%-10%)L=ML=(10/3)M弹弓空间为0.6L但当L过小时,为了防止弹弓失效,往往要加大弹弓长度。
斜顶模具都说难,看完这个其实很简单

斜顶模具都说难,看完这个其实很简单斜顶、摆杆机构斜顶、摆杆机构主要⽤于成型胶件内部的侧凹及凸起,同时具有顶出功能,此机构结构简单,但刚性较差,⾏程较⼩。
常采⽤的典型结构如下:(1)结构1 斜顶机构图7.7.1a为最基本的斜顶机构。
在顶出过程中,斜顶1在顶出⼒的作⽤下,沿后模的斜⽅孔运动,完成侧向成型。
斜顶根部要求使⽤图⽰装配结构,图7.7.1b为其装配的分拆⽰意。
在斜顶机构中,为了保证斜顶⼯作稳定、可靠,应该注意以下⼏点:(A)斜顶的刚性。
增强斜顶刚性⼀般采⽤:1.在结构允许的情况下,尽量加⼤斜顶横断⾯尺⼨。
(参见第七章7.2节)2.在可以满⾜侧向出模的情况下,斜顶的斜度⾓“A”尽量选⽤较⼩⾓度,斜⾓A⼀般不⼤于20°,并且将斜顶的侧向受⼒点下移,如增加图7.7.1a中的镶块2,同时镶块可以具有较⾼的硬度,提⾼模具的寿命。
(B)斜顶横向移动空间。
如图7.7.1a所⽰尺⼨“D”,为了保证斜顶在顶出时不与胶件上的其它结构发⽣⼲涉,应充分考虑斜顶的侧向分模距离、斜顶的斜度⾓“A”,以保证有⾜够的横向移动空间“D”。
(C)斜顶在开模⽅向的复位。
为了保证合模后,斜顶回复到预定的位置,⼀般采⽤下⾯的结构形式。
如图7.7.2a;7.7.2b。
(D) 斜顶底部在顶针板上的滑动要求平顺,稳定。
(2)结构2 摆杆机构,如图7.7.3。
在顶出过程中,当摆杆1的头部(L1所⽰范围)超出后模型芯时,摆杆1在斜⾯A的作⽤下向上摆动,完成分型。
设计摆杆机构时,应保证:L2>L1;E2>E1。
缺点:图⽰“B”处易磨损,须提⾼此处硬度。
⼀般要求将此处设计成镶拼结构。
模具斜顶工作原理
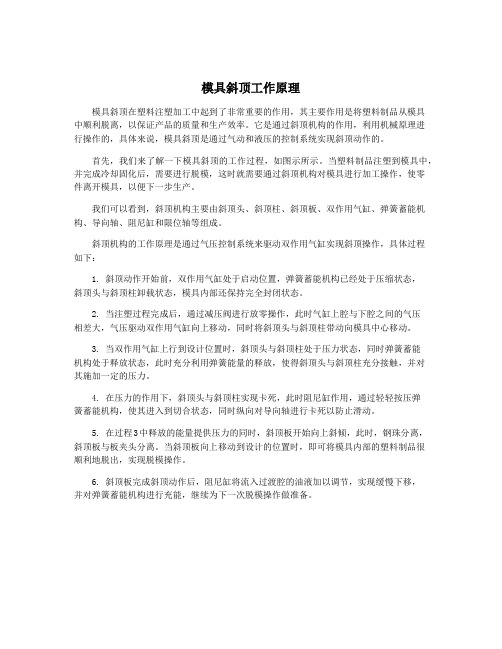
模具斜顶工作原理模具斜顶在塑料注塑加工中起到了非常重要的作用,其主要作用是将塑料制品从模具中顺利脱离,以保证产品的质量和生产效率。
它是通过斜顶机构的作用,利用机械原理进行操作的,具体来说,模具斜顶是通过气动和液压的控制系统实现斜顶动作的。
首先,我们来了解一下模具斜顶的工作过程,如图示所示。
当塑料制品注塑到模具中,并完成冷却固化后,需要进行脱模,这时就需要通过斜顶机构对模具进行加工操作,使零件离开模具,以便下一步生产。
我们可以看到,斜顶机构主要由斜顶头、斜顶柱、斜顶板、双作用气缸、弹簧蓄能机构、导向轴、阻尼缸和限位轴等组成。
斜顶机构的工作原理是通过气压控制系统来驱动双作用气缸实现斜顶操作,具体过程如下:1. 斜顶动作开始前,双作用气缸处于启动位置,弹簧蓄能机构已经处于压缩状态,斜顶头与斜顶柱卸载状态,模具内部还保持完全封闭状态。
2. 当注塑过程完成后,通过减压阀进行放零操作,此时气缸上腔与下腔之间的气压相差大,气压驱动双作用气缸向上移动,同时将斜顶头与斜顶柱带动向模具中心移动。
3. 当双作用气缸上行到设计位置时,斜顶头与斜顶柱处于压力状态,同时弹簧蓄能机构处于释放状态,此时充分利用弹簧能量的释放,使得斜顶头与斜顶柱充分接触,并对其施加一定的压力。
4. 在压力的作用下,斜顶头与斜顶柱实现卡死,此时阻尼缸作用,通过轻轻按压弹簧蓄能机构,使其进入到切合状态,同时纵向对导向轴进行卡死以防止滑动。
5. 在过程3中释放的能量提供压力的同时,斜顶板开始向上斜倾,此时,钢珠分离,斜顶板与板夹头分离。
当斜顶板向上移动到设计的位置时,即可将模具内部的塑料制品很顺利地脱出,实现脱模操作。
6. 斜顶板完成斜顶动作后,阻尼缸将流入过渡腔的油液加以调节,实现缓慢下移,并对弹簧蓄能机构进行充能,继续为下一次脱模操作做准备。
- 1、下载文档前请自行甄别文档内容的完整性,平台不提供额外的编辑、内容补充、找答案等附加服务。
- 2、"仅部分预览"的文档,不可在线预览部分如存在完整性等问题,可反馈申请退款(可完整预览的文档不适用该条件!)。
- 3、如文档侵犯您的权益,请联系客服反馈,我们会尽快为您处理(人工客服工作时间:9:00-18:30)。
斜顶机构
1.斜顶机构的运用场合
斜顶机构一般是用来成型产品内部或外部倒勾,且无法用动模侧滑块直接成型的情况。
成型产品内部或外部倒勾时,优先考虑采用滑块,是因为滑块抽芯时,产品处于固定状态,产品不会产生变形、移动等不确定状态。
2.斜顶的各组成部分(如图1)
2.1斜顶本体
2.2 斜顶导向杆
2.3斜顶上下耐磨板
2.4斜顶座
3.斜顶各部位设计
3.1斜顶本体:
3.1.1斜顶本体的形式: 整体式 (如图1)
分体式 (如图3)
在条件允许的情况下,尽可能采用分体式斜顶结构,易加工易维修,加工成本低。
导向杆采用圆杆,与斜顶块头部用螺纹销钉骑缝连接,防止销钉脱落,与滑动块连接头部削扁,用螺钉连接,要求螺钉能够从模具后面拆卸,底板和推板铣通孔,方便模具维修保养。
分体式结构设计时,斜顶本体的背面斜度大
于斜顶导向杆的度数1~2度,防止斜顶本体背面与凸模产生磨擦,同时斜顶的两侧面要求设计配作斜度,一般情况下,斜度为3度。
3.1.2斜顶的抽芯距离及斜度计算
抽芯距离: S =倒勾 + (3~5)mm余量
斜度: tgα= S / H (H:顶出行程)
α要取整,且一般 3°≦α≦ 15°(特殊情况α可以加大) 3.1.3斜顶的基本拆模:
当斜顶的宽度在取值方面不受产品的形状限制时,可以如图A中一样宽度方向取值,否则,当受产品形状限制时,则如B中宽度应取保证在产品的公差范围内,这样处理以便于线割加工处理. 另外,在斜顶成型的产品成型面应尽量减小,即尽量减小斜顶成型面,增大成型面的脱模角,以防止斜顶脱模后退时,拉弯成型面.(如图4)
在条件允许的前提下,斜顶本体与导向杆之间设计台阶止退面,承受注塑压力,避免注塑压力引起导向杆和推板变形,确保产品尺寸稳定和模具使用寿命。
止退面宽度3~5mm,与导向杆连接处增加工艺R角,防止应力开裂。
根据产品的具体情况,台阶止退面可以是一个面、两个面、三个面或四个面,同时两侧或背面要设计配合角度,一般为3度。
3.1.4斜顶干涉:
斜顶后退行程与筋干涉(如图6)
斜顶后退与产品形状干涉(如图7)
两只斜顶对面时,底部干涉(如图8)
采用半截式斜顶本体或斜顶加宽,建议采用斜顶加宽方案。
斜顶背面相对顶出干涉(如图9)布置斜顶附近的顶杆要尤其注意。
斜顶之间的运动干涉(如图10)布置相靠近的两根斜顶时,一定要做运动的干涉检查,以提前发现状况
3.1.5大斜顶的作法
当斜顶本体的宽度超过50mm时,我们称它为大斜顶。
考虑到材料成本、加工工作量以及模具的维修,大斜顶大多数情况下采用分体结构。
斜顶本体的背面斜度大于斜顶导向杆的度数1~2度,防止斜顶本体背面与凸模产生磨擦,同时斜顶的两侧面要求设计配作斜度,一般情况下,斜度为3度。
大多数情况下,采用圆导向杆,加工及维修方便。
特殊情况下,也可以采用方导向杆或整体结构。
斜顶本体虽然很宽很厚,但是由于中间镶了一只圆镶件,没有圆杆固定的地方,因此采用方形导向杆。
斜顶本体虽然很宽很厚,但是由于产品结构及模具结构因素,导向杆的厚度非常小,只能采用整体结构。
由于成型面积大,大斜顶需要设计冷却系统,要特别考虑冷却水的引出,具体结构形式参照冷却系统设计规范。
3.1.6斜顶机构凸模固定板部分让位孔
斜顶穿过凸模固定板,所以在凸模固定板部分需有让位孔,
孔径大小及位置应保证斜顶能顺利通过,若在实际设计时, 让位圆孔有干涉其它组件时,可以考虑让位长圆形孔,位置尽量取整。
也可以钻斜孔让位或铣台阶椭圆孔让位。
3.2斜顶耐磨板
斜顶导向板的作用是支撑斜顶,防止运动变形及加长斜顶的导向长度
斜顶导向板参照标准设计
一般情况下,斜顶要设计两段导向,第一段靠近成形端,第二段在B板底部,第一段导向根据具体情况可以设计为镶套或整体结构,第二段导向大多数情况下设计镶套结构。
3.3斜顶底座连接部分形式参照标准设计
斜顶底座连接部分中的滑动块与顶杆固定板之间设计配合间隙,配合间隙为双面1mm。
3.4有斜顶结构的模具,顶出空间尽可能控制在180MM以内,斜顶的度数尽可能控制在15度以内,斜顶的导向杆截面积尽可能大,确保斜顶导向杆运动过程中不会弯曲变形。
当斜顶距离大于120mm,斜顶运动角度大于10度,适用于500吨以上设备的模具,斜顶底座连接部分中的滑动块优先采用可旋转的结构,确保斜顶导向杆运动过程中不会弯曲变形。
4.斜顶的特别设计:
4.1在某些特殊情况下,斜顶的顶出行程太小,而又必须较大的顶出后退量时,我们应如何保险地增大斜顶斜度呢?如图14.在斜顶座上追加一个辅助的导向块,以增强斜顶顶出时的稳定性.
此机构设计时,请注意钳工要便于装配.
增加两端固定的导向杆设计,保护斜顶导向杆在运动过程中不会变形折断。
4.2若斜顶成型机构中,有局部的小型芯或其它需要特别大的后退量时,可以采取斜顶内跑滑块机构.如图15,此类机构设计时,可能是局部细节的作业比较多,且斜顶有一定的强度影响.一般是不十分建议设计者过分将机构零件做得特别小巧.但若能保障在运动和寿命方面无问题时,可以考虑
4.3斜顶上成型部分对斜顶的包紧力比较大,斜顶抽芯运动过程中,产品会跟随斜顶运动,造成产品变形或抽芯不能完成。
我们要根据不同的产品结构和模具结构,设计阻挡机构,解决产品跟随斜顶运动。
4.3.1利用斜顶背面度数差,让弹顶型芯复位。
顶出开始时,斜顶杆沿着斜面开始抽芯,弹顶型芯由于背面直面的作用保持在原始位置,顶住塑件保持不动。
当弹顶型芯脱离背面直面时,塑件已离开斜顶一段距离,对斜顶不再有包紧力,斜顶可以顺利完成抽芯动作。
设计是一定要注意,d2>d1,否则斜顶复位时,弹顶型芯与凸模干涉。
4.3.2弹顶型芯运动范围没有超出凸模高度,复位时依靠滑块撞击复位。
4.3.3弹顶型芯复位时依靠斜顶与凸模的分型面撞击复位
弹顶型芯在完成阻挡功能后需要施加压力定位,保持在斜顶的后续动作中位置不变。
弹顶型芯在起始位置及最终位置需要钢性定位,同时要求a>=0,5mm,h1>=3mm(h1与弹顶型芯的总高度有关,高度越高,要求h1尺寸越大,保证弹顶型芯滑动顺畅)。