IE的分析方法和工具(ppt 49页)
精益生产之IE七大手法(PPT 53张)

28
三.流程法
应用范围
1.该件工作必需经另一个以上不同地点的动作才能完成 2.该件工作必需经由一个以上的人来完成 名词释义 (使用符号及图例介紹) 为简易明示记录流程之过程,美国机械工程学会(ASME)制定下列之代表符号及分类如下: • 作业:凡物体任何物理或化学的性质,或装上另一物体或从另一物体拆下,或为另一作业, 搬运,储存及检验而作之安排或准备,均谓之作业. • 检验:为监定物体而加以检查其数量,质量或数值者,谓之检验. • 搬运:物体同一处运至另一处,人同一工作点移动至另一工作点,谓之搬运. • 储存:储存为物品之保存或等待,惟此行动乃在控制力之下.储存行动之取消,必须经过制 度或法定上的认可. • 等待:物体或人员因情况不容许或不立即采取迟一步骤时,称为等待. 工作人流程图:按工作人之动作来记录之流程图 工作物流程图:以加工物为对象,记录其补工完成之记录之流程图.
4.复制原理
同一件工作,如需做二次以上,最 好采用“复制”方式来达成,省时 又不错误.
9
一.防错法(防呆法)
应用原理I
5.顺序原理
避免工作之顺序或流程前后倒置,可依编号顺序排列,可以减少或避免错误的发生.
6.隔离原理
借分隔不同区域的方式,来达到保护某些地区,使其不能造成危险或错误的现象发生.
1 2
.
33
四.五五法(质疑创意法)
质问的技巧:
1.对“目的”(WHAT)的质问 *做了些什么? *是否可以做些別的事物? *为何要这么做? *做些什么较好? 這一质问的主要目的是在删除不必要的动作.
34
四.五五法(质疑创意法)
质问的技巧:
2.对有关“人”(MAN)的方面的质问 *是谁做的? *为何由他做? *是否可由別人做? 此一质问的目的,在寻求可能的“合并,重组/变更”的改善方向. 3.对“工作顺序”(WHEN)的质问 *在何时做的? *为何要在当时做? *改在別的時候做是否更有利? *在何时做最好? 此一质问的目的,在尋求可能的“合并,重组/变更”的改善方向
IE七工具

.
IE七工具
什么是IE
IE(Industrial Engineering)是藉由設計、改善或設定 人、材料、設備的綜合性系統即工作系統,以 謀求提高生產力的技術
所謂「設計」是指工制作定更新轻的松系統,「改善」是把現 在的系統修正為更好的系更統快,而「設定」是引進設計 或已經改善的系統,並更使便其宜根基穩固,以期所期待的 機能能夠發揮。
IE七工具
作业研究与时间的关系
作
基本生产 时间
总生产所需时间
外观上的生产时间
业方法的改善
设计拙劣的浪 生产系统的 作业方法的
费
浪费
浪费
无效时间
IE活动的对象
管理拙劣所致 作业员所致无
无效时间
效时间
• • •
• • •
• • •
• • •
• • •
真正有效 生产时间
IE七工具
不安产 及全品 同质研 业量究 公设不 司计周 设差 计
IE手法光学习是没有用的,以日常实践来彻底消除浪 费才是重点!
IE七工具
IE七工具
生产方式的演变 工业工程发展简史 IE七工具
工程分析 → 1.动作研究 稼动分析 联合工程分析 生产线平衡分析 材料处理(搬运分析) 设施布置 事务工程分析
2.时间研究
目录
生产方式的演变
第三阶段:以70年代计算机在管理中 的应用为特征,它主要是柔性制造系 统、MRP、ERP的运用
美國IE協會(AIIE)
IE七工具
你适合当IE人员吗?
• 请回答下列十个问题:
问题 ①初次读一本书时,先看目录吗? ②早晨刷牙,是饭前、或饭后? ③洗手前,是否先掏出手帕? ④在打电话前,是否先将事情要点笔记起来? ⑤结帐排队于收银台时,是否准备零钱? ⑥吃饭的地方很多时,是否大致决定后才出发? ⑦在停车场,通常是后退停车? ⑧在桌上放置原子笔,笔尖朝哪一方? ⑨与人约定事情,是否用笔记起来? ⑩依先前之约,等到访问时是否再打电话?
IE七大手法培训PowerPoint演示文稿
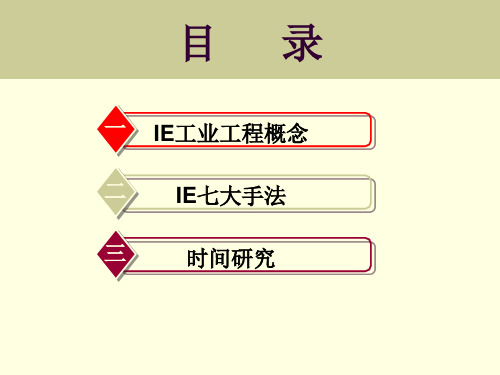
职业卫生与医学
----美国国家标准ANSI--Z94(82年)
5
工 业 工 程 在 制 造 业 中 的 应 用
➢工业工程发展简史
7
➢工业工程意识
• 增值与非增值 • 成本和效率意识 • 问题和改革意识 • 工作简化和标准化意识 • 全局和整体化意识 • 以人为中心的意识。
9
生产系 统
生产要素 人财物
A、使作业的动作轻松 难于观察、难拿、难动等作业即变得难做,变得易疲劳而发生失误。区分
颜色使得容易看,或放大标示,或加上把手使得容易拿,或使用搬运器具使 动作轻松。
B、使作业不要技能与直觉
需要高度技能与直觉的作业,容易发生失误,考虑治具及工具,进行 机械化,使新进人员或支援人员也能做不出错的作业
C、使作业不会有危险
22
➢ IE七大手法
手法名称
防止错误法 (Fool-Proof) 动作改善法 (动作经济原则)
流程程序法
5X5W1H (5X5何法) 人机配合法 (多动作法) 双手操作法 (左右手法)
工作抽查法
简称
防错法 动改法 流程法 五五法 人机法 双手法 抽查法
目的
如何避免做错事情,使工作第一次就做好的精神能 够具体实现。 改善人体动作的方式,减少疲劳使工作更为舒适、 更有效率、不要蛮干。 研究探讨牵涉到几个不同工作站或地点之流动关 系,藉以发掘出可以改善的地方。
例:抽水马桶之水箱内设有浮球,水升至某一高度时,浮球推动拉杆,切断水源。 D、相符原理
藉用检核是否相符合的动作,来防止错误的发生。 例:开刀手术前后必须点核数量有否符合,以免有工具遗留在人体内,忘了拿出来。 例:物料配送制,就是根据配送的配件数与成品数是否相符来确认配件是否漏装配。 E、顺序原理
IE工具培训课件ppt(44张)

双手法、人机法、流程法:协助我们做进一步的认清事实的状况,以及建立其改善的基 础及启发点.
五五法、防呆法、动改法:协助我们对已知的问题,质问探寻改善的具体方法,以实现改
善的目标.
14
IE工具培训课件(ppt44页)
IE工具培训课件(ppt44页)
IE七大手法用途
名称
用途
防呆法 如何避免做错事情,使工作第一次就做好的精神能够具体实现
动改法
流程法
五五法 人机法 双手法 抽查法
IE工具培训课件(ppt44页)
改善人体动作的方式,减少疲劳使工作更为舒适、更有效率,不要蛮 干 研究探讨牵涉到几个不同工作站或地点之流动关系,藉以发掘出可资 改善的地方
借着质问的技巧来发掘出改善的构想
研究探讨操作人员与机器工作的过程,藉以掘出可资改善的地方
2 标准时间的意义和用途
标准时间是时间研究的基准。凡欲对某一领域、某一过程的时间序 列进行科学的分析研究,都不可避免地要确立相应的标准时间,非此则 无法进行比较、分析、定量的考察。
标准工时
观察时间
评比因素
私事 疲劳 延迟 政策 其他 宽放 宽放 宽放 宽放 宽放
正常时间
标准时间
图一 标准时间的构成
总出勤工时 总出勤工时
总出勤工时=实际出勤工时-间接工时 - 异常工时
实际出勤工时=协鑫正常一般按12小时计算 间接工时= 1.5小时(吃饭、休息、上厕所等) 异常工时= 发生的停机异常等
1、什么是工时??? 2、什么是标准工时???
时间研究
国际劳工组织的工作研究专家为时间研究下的定义 是:
“时间研究”是运用一些技术来确定合格工人, 在标准状态下,对一种特定的工作,以正常速度操作 所需时间的一种方法。”
IE流程分析法ppt课件
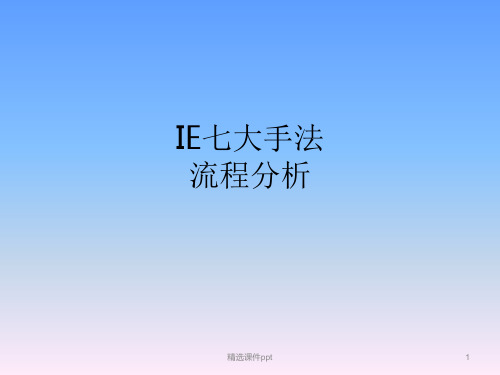
标 签
改
善
数检改善
6.标准化
2.流程程序分析
精选课件ppt
20
1.简介
1.1 概念 流程程序分析是以全过程为研究对象,并把过程划分为加工、检查、 搬运、等待和储存等五种状态加以记录和分析,特别适用于对搬运、 储存、等待等易于忽视的成本浪费之分析,是程序分析中最基本、 最重要的分析技术。
以全过程 为对象
2.58S 1 卡线
工序名称
4.45S 2 压卡簧 4.89S 3 打卡扣
6mm垂直线 表示工艺顺序
1.21S 4 盖油盖
5 3.67S
贴标签
加工符号 并编序
2.25S 6 包装 1.13S 1 数检
检验符号 并编序
4.及实施
5.1 提问技术:5W1H+5WHY
考察点 第一次提问
TOTAL 9
20.18 8 48
1497
储存
2.物型流程分析
2.2 改善后
流程分析
作业对象 制作人
日期 版本
审核
序号
风扇组装 王XX
2010/6/18 B
林XX
活动 加工 搬运 检验 等待 储存 TOTAL
数量
6
0
0
0
1
7
统计 工时 16.3
人力
6
16.3
1
7
距离
6
30
36
WIP
92
1000 1092
工序
工时 人力 距离 WIP 加工 搬运 检验 等待 储存
1
压卡簧
2.58
1
1
6
2
卡线
4.45
1
1
IE七大手法及其应用课件

Where
在什么地方干
为何在此干
能否在别处干
应该在哪儿干
When
在什么时间干
为何此时干
能否在别的时间 应该在什么时
干
间干
Who
由谁干
为何由它干
能否由别人干
How
怎么干
为何这样干
能否用别的方法 应该怎样干
干
5W1H
应该由谁干
30
产生创意的思考法则
1.相反法则:上下颠倒,左右互换,作业次序
改变.
2.拼图法则:将一个整体的基本单元分解
对操作者的动作进行细微的分析,消除不
合理的和浪费的动作,以找出轻松,快速,准
确的操作动作的一种研究方法.
目的:是简化操作方法,提高生产效率,减轻
工人疲劳,进而确定操作方法和制定动作
时间标准.
11
动改法
动作分析的方法:
1.目视动作分析
2.动素分析
3.影片分析
动素:
人完成工作的动作,可由17个基本动作构
---工作改善最大的阻碍,并不在于技朮不足,而
在于一个人的想法.
---尝试从另一个角度来思考
---发挥直觉力----创造力的源泉
29
5W1H分析表
第一次提问
第二次提问
第三次提问
第四次提问
现状
为什么
能否改进
新方案
Why
干的必要性
理由是否充分
有无新的理由
新的理由
What
干什么
为何要干它
能否干别的
应该干什么
成,这17个基本动作又称为17个动素.
12
动改法之动素
IE的分析方法及工具

IE得分析方法及工具——(摘自林荣瑞先生著作《管理技术》章节)一、对IE得认识1.IE就是以工程技术为基础,配合科学管理得技巧来发现问题、解决问题、预防问题。
2.IE最终目得就是经由管理得运作,使企业能获得最大得利益,就是故与成本或经济效益有关,包括制度、作业方法、机器、模具、夹具均应予掌握并加以改善。
3.IE就是一门应用科学,其操作理论均要能符合实际得需要,就是故IE工程师均应具备身体力行得能力,而使理论与实务相得益彰,保证管理效果。
4.IE就是运用重点管理得技巧,在任何问题上做重点突破。
5.美国IE协会(AIIE)对IE下得定义如下:IE就是在工学之中以设计,改善,设定来综合人、材料、设备等系统得结合。
为了明示、预测、评价该系统所产生得结果而使用工学分析或设计原理与技法,并融合数学、自然科学、社会科学等专门知识与经验。
对上面得定义我们可以了解:IE就是藉着设计、改善或设定人、料、机得工作系统,以求得到更高生产力得专门技术。
ﻫ上面所提得“设计”就是指制订新得系统。
“改善”就是指把原有得系统修改得更完美更适合。
“设定”意指将“设计”或“改善”之系统,导入企业动作体系,并能够稳固得发挥。
6.IE(工业工程)在日本也被称为“生产技术”或“管理工学”。
7.IE 得基础也就是最早得起源来自于“工作研究“,而”工作研究“得主要构成就是来自泰勒(F。
W。
TOYLOR 1856—1915)得”时间研究“与吉尔布雷斯(F。
B。
GILBRETH 1868—1924)得“动作研究”二者所构成。
8.现阶段得工业工程师主要得范围大致如下:1.工程分析2.工作标准3.动作研究4.时间研究5.时间标准6.价值分析(V A)7.工厂布置8.运搬设计二、工作研究(OPERATION RESEARCHOR)1、工作研究得目得就是人们藉着物料、机器、工具及工作方法而产出产品,而此产出得方法就是否就是:•生产过程最理想?•生产得工作方法最好?•机器及工具就是否最适当?•物料就是否最正确?工作研究以研究及分析现有得生产过程及方法,并能找出一个最佳生产方法得一种管理科学。
IE七大手法PPT课件
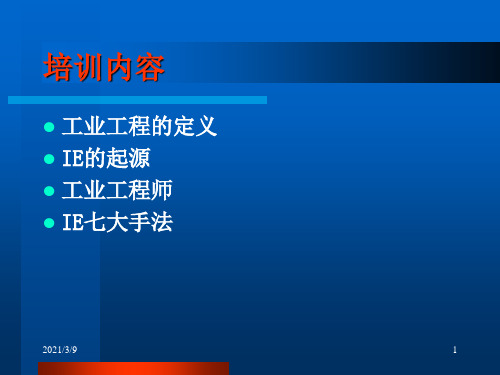
*
IE七大手法之三——工序分析法
产品设备作业内容的最佳化 在各工序上考虑最佳(低费用、高性能、自动化)设备; 简化(生手也容易做到)各工序上选定最佳的加工条件; 研讨减少搬运量及装载次数 减少搬运量:减少削、冲压等费用; 减少搬运次数:增加1次搬运量、装载次数、取消中间环节; 改善搬运方式:利用最有利的包装方法、容器、推车进行改善; 搬运距离、路线的合理化;直线化、圆形化、工序组合变更、布置变更; 搬运方式的系统化:探讨巡回运输方式; 缩短搬运时间、装载时间、周期;
2021/3/9
*
IE七大手法之三——工序分析法
工序改善 目的: 降低成本 提高生产率 材料损失德减少和质量保证 减少半成品 有效利用空间 提高安全等环境条件
2021/3/9
*
IE七大手法之三——工序分析法
原则 减少对最终目的不产生价值的工序 要考虑<此作业是为了什么而做?>; 产品设计(形象、表面处理、涂装、标准化)的变更; 材料规格(材质、形象、尺寸、材料截断、内外作业区)的变更。 考虑变更工序组合 组合:考虑将分离的工序合在一起; 分离:将结合的工序进行分解,达到分工化; 替换:考虑交替前后工序的顺序; 并行:考虑设备、作业内容的并行,同步作业
2021/3/9
*
IE七大手法之二——防错法
1.意义 防错法又称防愚法,其义为防止愚笨的人作错事。也就是说,连愚笨的人也不回做错事的设计方法。 狭义:如何设计一个东西(一套方法),使错误绝不会发生。 广义:如何设计一个东西(一套方法),而使错误发生的机会减至最低的程度。 因此,更具体的说“防错法”是: 1>.具有即使有人为疏忽也不会发生错误的构造 ——不需要注意力。 2>.具有外行人来做也不会做错的构造 ——不需要经验也直觉。 3>.具有不管水或在何时工作能不出差错的构造 ——不需要专门知识与高度的技能。 2.功用 1> .积极:使任何的错误,绝不会发生。 2>.消极:使错误发生的机会减少至最低程度。 3.应用范围 任何工作无论是在机械操作、产品使用上,以及文书处理等皆可应用到。
IE的分析方法和工具(49

圈、隔离圆筒 及内部套圈于
接合器套上
日工 5 检验
开关转子
停档 直经5mm 30钢
模压塑料体 模压
轴 直经10mm 45钢
车柄部、倒 0.025 10 角、切断
车两边 0.025 1 车端面、肩
0.080 7 镗、铰孔
面并切断
0.005 11 不规定时间 5
去尖头
0.022 8
检查尺寸与表
0.010 2 钻横孔、
机 空闲 精铣第二面
人机操作顺序剖析图
比较项目
人的工作(min)
机器的工作(min)
拿起铸件,放上钻模,夹紧, 放低钻头,准备进刀,时间0.5
空闲
工作 内容
空闲
在铸件上钻Φ12.7的孔, 时间2.5
抬起钻头,取出铸件放在一边, 清除钻模的铁屑,时间0.75
空闲
空闲时间 工作时间 整个周期
利用率
2.5 1.25
去毛刺 不规定时间 1
面粗糙度
最终检查
不规定时间 4 尺寸及表 0.070 3
面粗糙度
车另一端面
检查尺寸与 表面粗糙度
铣端部4 个平面
0.0015 12 去除油污
0.020 4 去毛刺
0.006 13 镀隔
不规定时间 2
机加工最 终检查
不规定时间 6 最终检查
0.0015 5 去除油污
0.008 6 镀隔
运用人机操作图,可将消费进程中,工人操作 的手动时间和机器的机动时间清楚地表现出来。
人机操作图的构成
以适当的线段的长短代表时间比例。
如1cm代表10min等。
人
在纸上采用适当的距离分开人与机, 移开铣成件
作出垂线。最左方为工人操作时的 用模板量深度
IE动作分析ppt课件
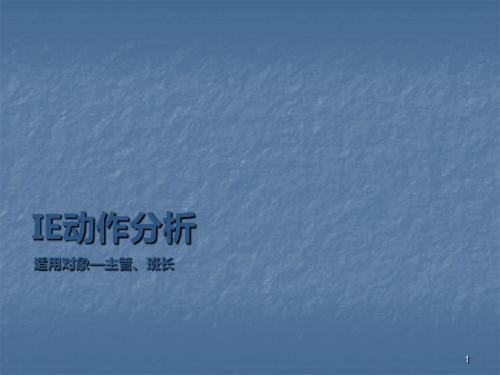
IE动作分析与动作经济原则
(1)整体作业观察;
作业顺序观察达到了如指掌的程度。
(2)记录动作;
先左、右手的动作顺序进行记录,再对左、右手组合动作记录。
(3)校核记录;
先左、右手的动作顺序进行记录,再对左、右手组合动作记录。
(4)填写动作分析表;
(5)动作要素分类汇总;
12
组装螺栓和螺帽基本动作分析表
常常发现「持住」(Hold)之工作由宝贵的手来作 应设计适当的治具或夹具,以代替手去执行「持住」的动作. 可以利用足踏方式代替手执行某些操作.
用脚操作的转盘,以调整工件位置,使双手可以完全从事焊接。
26
5.2动作改善原则
(12)设法将两种工具合并为之。 将两端两用之手工具掉转头来使用,比放下一只现用的手工
14
五、动作经济改善原则
5.1动作经济原则概要:
1. 动作经济的原则,是要为了排除人的无谓(浪 费)动作. 2. 利用人体工学使其动作做最经济而获得正 确、快速、轻松、安全的工作,提高效率的一 种动作改善方法,也叫动改法.
15
5.2动作改善原则
(1)双手同时作业,同时开始, 同时结束
(2)双手动作对称运动,不要向 同一方向
(3)除休息时间外,双手不应 空闲
16
5.2动作改善原则
(4)动作等级使用原则
级别
一
二
三
四
运动枢轴
指节
手腕
肘
肩
人体运动部份
手指
+手掌
不经 +前臂
+上臂
动作范围 速度 体力消耗
手指节之长度
济的 1 经济的动作范围 动作 最少
手掌之张度
- 1、下载文档前请自行甄别文档内容的完整性,平台不提供额外的编辑、内容补充、找答案等附加服务。
- 2、"仅部分预览"的文档,不可在线预览部分如存在完整性等问题,可反馈申请退款(可完整预览的文档不适用该条件!)。
- 3、如文档侵犯您的权益,请联系客服反馈,我们会尽快为您处理(人工客服工作时间:9:00-18:30)。
3 4
空闲
5
加工
6
7
卸下工件 完成件放箱内
8 9 10
卸下工件 空闲
共同工作
单独工作
空闲
现代工业工程 - 21
改善一:
将“准备下一工件” 放在加工周期内进行
人 准备下一工件 装上工件 时间
0.0015
12 去除油污
0.020
4 去毛刺 机加工最 终检查
0.006
13 镀隔
不规定时间 2
不规定时间 6 最终检查
0.0015 5 去除油污 0.008 6 镀隔 最终检查
不规定时间 3
0.020
9 将模压体装 入轴的小端
将停档装 0.045 14 入模压体
不规定时间
7
最终检查
现代工业工程 - 8
轴 直经10mm 45钢 1 2 车端面、肩 面并切断 车另一端面 检查尺寸与 表面粗糙度 铣端部4 个平面
0.025 0.005
11 去尖头
不规定时间 5
不规定时间 1 检查尺寸与表 面粗糙度 最终检查 不规定时间 4 尺寸及表 0.070 3 面粗糙度
车两边 0.025 0.080 7 镗、铰孔 0.010 钻横孔、 0.022 8 去毛刺
现代工业工程 - 3
工艺程序图分析
流程程序图分析 路线图分析 PTS 动作经济原则 作业简化原则 联合工程分析 工作抽样 作业简化 基本动作的动作分析 PTS 动作经济原则
方法研究的分析层次及分析技术
作业单位 作 以加工、检验、 业 以材料的加工过程单位 搬运等作业单位 划 为基础的作业划分 为基础的作业划 分 分 板材切断 工 艺 分 解 汽 车 车 身 成 型 焊 接 组 装 涂 覆 分 析 技 术 程序分析 操作分析 动作分析 搬入构件 点焊 自动焊 检查制品 搬往 下工序 工 序 作业要素 以作业单位中所 包含的一系列作 业要素为基础的 划分 放好构件A 放好构件B 进行焊接 取出成品 动作单位 以一个作业要素 中所包含的一系 列动作单位为基 础的动作划分 取构件B 搬 到 夹具上 安放好 搬 运 校正位置 基本元素 以单位动作中所 包括的一系列动 作要素为基础的 动作划分
现代工业工程 - 4
工作研究(Work Study)
方法研究(Method Study)
程序分析(Process Analysis) 程序图(Process Chart) 装配表(Assembly Chart) 操作分析(Operation Analysis) 人机配合图(Man-Machine Chart) 双手作业图(Two Handed Operation Chart) 动作分析(Motion Analysis) 细微动作分析(Therblig) 动作经济原则(Principles of Motion Economy)
改良方法
节省
改善示例
工作时间 工作:铣平面 图号:B239/1 产品:B239铸件 机器:4号立铣 速度:80r/min 走刀量:380mm/min 制作: 通力达 日期: 2000/08/18
空闲时间
人 机
周程时间
利用率 人 机 人 时间
1 2
10
40% 40% 机 空闲 被装上工件
准备下一工件 装上工件
5 工作研究
IE的分析方法和工具
现代工业工程 - 1
工作研究 步骤
现代工业工程 - 2
方法研究分析方法
探 讨 项 目 内 容 分 析 手 法
制造整个工 程系统
工厂布置 物料移动 作业区域的 配置 组合作业或 自动机械作 业 作业中的作 业员动作
从原料→生产→成品至出货为 止。
工厂内部门与部门之间及人与 物料之活动。 作业者的位置及作业者周围的 物品的放置方法。 以组合进行的共同作业或以自 动机器作业的人与机器的配合。 短的作业周期且高反复度的作 业员动作。
人机操作图的构成
以适当的线段的长短代表时间比例。 如1cm代表10min等。 在纸上采用适当的间隔分开人与机, 作出垂线。最左方为工人操作时的 动作单元及垂线,在此垂线上按所 取的时间比例,由上向下记录工人 每一动作单元所需时间。当工人操 作时用实线(或其它方式)表示, 空闲用虚线 (或其它方法)表示, 机器同样。 待人与机器的操作时间均已记录之 后,在此图的下端将工人与机器的 操作时间、空闲时间及每周期人工 时数予以统计,供分析时参考。
现代工业工程 - 9
物料型流程程序图
举例:一张火车票自 出售、使用至收回止, 其间经过许多人之手, 试用流程图来表示。 工作任务:短途单程 快车车票的发售、使 用及收回。 开 始:票放置票房 之票架上。 结 束:票在终点站 被收回。
现代工业工程 - 10
1 1
在票架上
1
拿起并查看 票价 用手拿至柜 台上(2.4M)
现代工业工程 - 15
人机操作分析
在机器的工作过程中,调查、了解在操作周期 (加工完一个零件的整个过程称为一个操作周 期或周程)内机器操作与工人操作的相互关系, 以充分利用机器与工人的能量及平衡操作。 利用人机操作图,可将生产过程中,工人操作 的手动时间和机器的机动时间清楚地表现出来。
现代工业工程 - 16
现代工业工程 - 13
工作衡量(Work Measurement)
时间研究(Time Study) 马表测时法(Stop Watch) 速度评比(Tempo Rating) 宽放时间(Allowances) 工作抽样(Work Sampling) 预定动作时间标准(Predetermined Time Standard) 模特排时法(MOD) 方法时间衡量(MTM) 工作因素(WF)
0.0142
0.0102
9
铣断面
日工
2
0.0024
17 去毛刺
局部装配盅套 19 及接合器帽于 内部套圈上
隔离垫圈 隔离圆筒 装配隔离垫 圈、隔离圆筒 20 及内部套圈于 接合器套上 5 检验
0.0010
日工
现代工业工程 - 7
开关转子
停档 直经5mm 30钢 10 车柄部、倒 角、切断
模压塑料体 模压
空闲
在铸件上钻Φ12.7的孔, 时间2.5 空闲 1.25 2.5
抬起钻头,取出铸件放在一边, 清除钻模的铁屑,时间0.75
空闲时间 工作时间 整个周期 利用率 2.5 1.25 3.75 1.25/3.75=33%
2.5/3.75=67%
现代工业工程 - 18
项目
现行方法 人 机 人 机 1.2 0.8 0.8 1.2 2.0 60% 40%
空闲时间 (min)
周程时间(min) 利用率 人 机 时间(min)
0.2
机
0.4
0.6 0.8 1.0 1.2 1.4
空闲
空闲
1.6 1.8 2.0
精铣第二面
共同工作
单独工作
空闲
现代工业工程 - 19
改良方法:
项目 工作时间 (min) 工作:铣平面 图号:B239/1 产品:B239铸件 机器:4号立铣 速度:80r/min 走刀量:380mm/min 制作: 通力达 日期: 2000/08/18 空闲时间 (min) 人 机 人 机 现行方法 1.2 0.8 0.8 1.2 2.0 60% 40% 改良方法 1.2 0.8 0.2 0.6 1.4 86% 57% 节省 --0.6 0.6 0.6 26% 17% 周程时间(min) 利用率 人 机
工艺程序图
引入原料 引入物件 (或零件) 局 部 装 配 或 加 工 局 部 装 配 或 加 工 引入原料 (或零件) 局 部 装 配 或 加 工 在 零 件 上 完 成 很 多 的 作 业
1 2 1 3 2
材料、采购的部件
现代工业工程 - 6
工艺程序图实例
销No.1106 黄铜杆 车外部直 径及切断 车大外部 直径及钻 切槽 接合器套No.1105 青铜杆 车钻铰螺 纹及切断 检验 钻平头大 内部直径 检验 0.0060 0.0069 接合器帽No.1109 黄铜杆 车钻铰压 盅套圈No.1108 花及切断 黄铜杆 14 车钻铰及 切断 15 去毛刺 0.0076 16 内部套圈No.1107 黄铜杆 0.0270 0.0135 日工 18 镀镉 0.0025 日工 4 检验 0.0030 13 去毛刺 日工 11 镀镉 日工 5 镀镉 0.0130 车钻铰及 12 切口 日工 3 检验 0.0084 4 去毛刺 10 铣8个槽 0.0270 3 铣8个槽 8 0.0145 2 6 0.0165 1 7 日工 1
改良方法
节省
人机操作图 实例分析
工作时间 (min)
工作:铣平面 图号:B239/1 产品:B239铸件 机器:4号立铣 速度:80r/min 走刀量:380mm/min 制作: 通力达 日期: 2000/08/18
人 移开铣成件,用压缩空气清洁 在面板上用模板量深度 锉锐边,用压缩空气清洁 放入箱内,取新铸件 用压缩空气清洁机器 装铸件,开动机器精铣
2
打印日期
1
D
3
等待找钱
拿给旅客 旅客带至入口 处(30M)
2
4 查看并打孔
3 5
旅客带至旅 途上 在终点查看并收回
实例分析
线路图与流程图结合
某飞机工厂仓库原来 的平面布置。物品从 送货车到零件架的运 输路线以粗线表示, 各种活动均用符号绘 于线上。
现代工业工程 - 11
改进
在接收台的对面开一个进库 的新入口,使箱子可沿最短 路线运进库房。 箱子从送货车滑下滑板,直 接放到手推车上,并送到开 箱处。就在车上开箱,取出 送货单。然后运到收货台, 等待片刻,打开箱子,把零 件放到工作台上,对照送货 单点数并检查。检查与点数 的工作台现已布置在收货台 旁,因为可以用手传递零件 来检查、测量并点数。最后, 把零件放回纸盒,重新装箱。