冷轧薄板连续退火技术简介
冷轧薄板连续退火技术简介
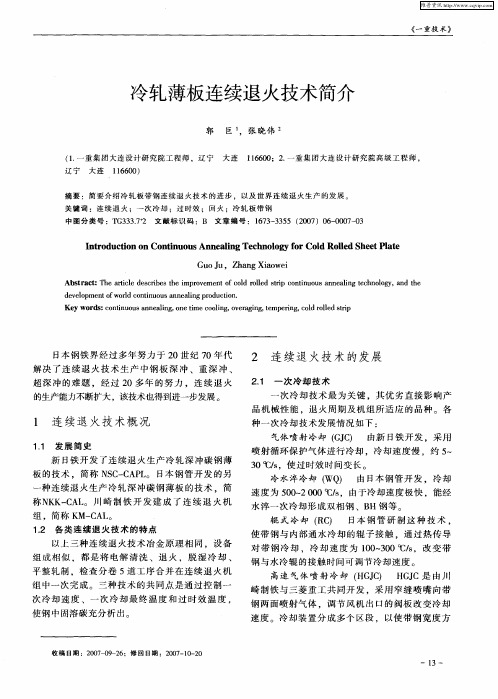
喷射循 环保 护气 体进行 冷却 ,冷却 速度 慢 ,约 5 ~
3 O℃,,使过 时效 时 间变 长 。 s
冷水 淬冷 却 ( ) 由 1本钢 管 开发 ,冷却 WQ 3
速 度 为 5 0 20 0℃/,由于冷却速 度极 快 ,能经 0 ~ 0 s
种连续 退火 生产 冷 轧深 冲碳 钢 薄板 的技 术 .简
Ab t a t T e at l e c b st e i r v me t fc l o l d sr o t u u n e l gt c n lg , n h s r c : h r c e d s r e h mp o e n od r l ti c n i o s a n a i h oo y a d t e i i o e o n n e d v lp n f d o t u u n e l gp o u t n e eo me t d c n i o s n ai r d ci . o wo n a n o Ke r s c ni u u n xig o et o l g o e a i g t mp r g c l old sr y wo d : o t o s n n a e n , n mec oi , v r g n , e ei , odr l i i n n e tp
崎制 铁 与三菱 重 工共 同开发 ,采 用 窄缝 喷嘴 向带
钢两 面 喷射气 体 ,调 节 风机 出 口的 阀板 改变 冷却
速度 。冷 却装 置 分成 多个 区段 ,以使 带钢 宽 度方
收 稿 日期 :2 0 — 9 2 0 7 0 — 6;修 回 日期 :2 0 — 0 2 07 1—0
辽宁 大连 16 0 ) 1 6 0
摘 要 :简 要 介 绍 冷 轧板 带 钢 连续 退 火 技 术 的进 步 ,以 及世 界 连 续 退 火 生 产 的 发展 。
冷轧连续退火炉工艺

冷轧连续退火炉工艺一、引言冷轧连续退火炉工艺是钢材加工中的一个重要环节,能够使冷轧钢板获得良好的力学性能和表面质量。
本文将系统介绍冷轧连续退火炉的工艺流程、设备特点以及其在钢材加工中的应用。
二、工艺流程1. 上料区:将冷轧钢卷通过输送设备送入连续退火炉。
为了保证钢卷的均匀受热,需要设置上料辊道和预热区。
2. 加热区:在连续退火炉中,通过燃烧器向钢卷表面提供热能,使其达到退火温度。
加热区通常分为预热段、加热段和保温段。
预热段用于加热钢卷,并使其温度均匀;加热段是主要加热区域,通过高温燃烧器提供热源,使钢卷达到退火温度;保温段用于保持钢卷温度,使其均匀受热。
3. 保温区:在加热段达到退火温度后,钢卷进入保温区域,保持一定时间,使钢材内部结构发生改变,消除残余应力,提高塑性。
4. 冷却区:经过保温区的处理后,钢卷进入冷却区,通过水冷或风冷方式,使钢材迅速冷却,固定组织结构,提高硬度和强度。
5. 出料区:冷却后的钢卷通过输送设备送出连续退火炉,进入下一个工序。
三、设备特点1. 设备结构紧凑:冷轧连续退火炉由上料区、加热区、保温区、冷却区和出料区组成,整体结构紧凑,占地面积小。
2. 温度控制精确:连续退火炉采用先进的温度控制系统,能够实时监测钢材的温度变化,并通过调节燃烧器的工作状态,控制加热温度,确保钢材达到所需的退火温度。
3. 生产效率高:连续退火炉采用连续式生产方式,钢卷不间断地通过炉内各个区域,实现了高效连续生产,大大提高了生产效率。
4. 能源消耗低:连续退火炉采用高效的燃烧器和热交换设备,能够最大限度地利用燃料能量,减少能源的浪费,降低生产成本。
四、应用领域冷轧连续退火炉广泛应用于冷轧钢板的生产中,特别是在汽车、家电、建筑和机械制造等领域。
通过连续退火炉的处理,冷轧钢板的力学性能得到提高,表面质量得到改善,能够满足各个行业对高品质钢材的需求。
五、总结冷轧连续退火炉工艺是钢材加工中的重要环节,通过精确控制加热温度和保持时间,能够使冷轧钢板获得理想的力学性能和表面质量。
冷轧生产:连续退火发展

不同退火方法和特点
(1)森吉米尔法的特点 森吉米尔法的退火炉主要包括氧化炉、还原炉两个独立组成部分。
优点:明火燃烧,烧掉轧制油,净化带钢表面。 缺点:明火加热。带钢在氧化炉中生成了较厚的氧化层,在还原炉中还
原十分的困难。
连续退火发展
(2)改良森吉米尔法的特点
把森吉米尔法中的各自独立的氧化炉和还原炉,由一个截面积较小 的过道连接起来。把预热段、还原段、和冷却段构成了一个整体的 退火炉。 优点:氧化炉采用还原性气氛,明火加热,减少了氧化,减轻了还原段的 负担。 缺点:加热温度受限制。
任务六:连续退火机组
《板带冷轧生产》
连续ห้องสมุดไป่ตู้火发展
1、发展历史 ➢ 连续镀锌技术是本世纪30年代由波兰人森吉米尔发明的。是森吉米尔
首先把连续退火工艺和热镀锌工艺联合起来,并于1931年在波兰建设 了第一套宽度为300毫米的带钢连续生产线。 ➢ 美国钢铁公司于1948年设计并投产的一条热镀锌线改良了森吉米尔发 明的退火方法,采用一个碱性电解脱脂槽取代了森吉米尔法中的氧化 炉的脱脂作用,其余的工序和森吉米尔法基本相同。
连续退火发展
➢ 1965年美国的阿姆柯公司发展了森吉米尔法,将森吉米尔法中的氧化 炉直火加热方式改造成为无氧化直火加热方式,将退火炉工艺推进了 一大步。
➢ 80年代后,由于对板带的质量的要求的提高,出现了全辐射管立式退 火炉。
连续退火发展
2. 连续退火炉的分类方式和退火方式 ➢ 按照炉子的形式来分---立式、卧式和L型炉子。 ➢ 按照加热方式来分---直接加热方式和间接加热方式。 ➢ 按照设备的配置情况来分---森吉米尔法、改良的森吉米尔法和美钢联
法等。 ➢ 按照退火后进行热处理方式来分---再结晶退火后进行过时效和再结晶
冷轧连续退火硬度

冷轧连续退火硬度冷轧连续退火是金属材料加工中常用的一种工艺,可以改善冷轧材料的硬度和性能,提高其加工性能和使用寿命。
本文将从硬度的定义、冷轧连续退火的工艺特点、影响硬度的因素以及硬度测试方法等方面进行探讨,并对冷轧连续退火硬度的相关知识进行详细阐述。
首先,我们来了解一下硬度的概念。
硬度是指材料抵抗外力和划痕的能力,也是材料抗压强度的一种体现。
硬度越高,材料越难被切削、划伤或变形。
硬度测试是确定材料硬度的常用手段,可以通过不同的试验方法来得出材料的硬度值。
冷轧连续退火硬度是指经过冷轧处理后,再进行连续退火处理后的材料硬度。
冷轧连续退火工艺是将冷轧后的金属在连续退火炉中进行退火处理,通过加热和冷却过程,使材料的结晶粒度变细,晶界清晰,并恢复其原有的塑性,提高材料的硬度和韧性。
冷轧连续退火硬度受多种因素的影响。
首先是材料本身的化学成分和物理性质,比如金属的成分、纯度、晶体结构等。
不同的金属具有不同的硬度和韧性,因此在冷轧连续退火前后的硬度值也会有所不同。
其次是连续退火的工艺参数,如退火温度、保温时间、冷却速度等,这些参数的不同组合会对冷轧连续退火硬度产生影响。
此外,冷轧连续退火之前的冷轧工艺也会对硬度产生影响,冷轧的压下量和轧辊的摩擦力也会影响材料的硬度。
在实际生产中,冷轧连续退火硬度是通过硬度测试来确定的。
硬度测试方法有多种,常用的有巴氏硬度(HB)、维氏硬度(HV)、洛氏硬度(HRC)等。
巴氏硬度是指材料表面被印入准圆锥形试验钻头的深度,维氏硬度是通过将压头施加在材料表面上,测量压头的印入深度来确定硬度值,洛氏硬度是通过将金属试件放在洛氏硬度试验机上,通过读数确定硬度值。
总之,冷轧连续退火硬度是冷轧连续退火工艺对材料硬度和性能的影响的一种表现形式。
硬度测试可以通过不同的测试方法来得到硬度值,用以评估材料的硬度和韧性。
冷轧连续退火硬度的变化与材料的成分、物理性质以及工艺参数等因素密切相关。
了解冷轧连续退火硬度的知识可以更好地指导生产实践和优化工艺参数,提高冷轧材料的性能和质量。
冷轧生产线退火工艺

冷轧生产线退火工艺本文档旨在介绍冷轧生产线的退火工艺,以帮助读者了解和掌握该工艺的基本原理和操作流程。
2.1 原料准备在退火工艺开始之前,需要对原料进行准备。
原料包括待退火的冷轧钢板、保护气体、冷却介质等。
这些原料的准备对于保证退火工艺的稳定性和产品质量至关重要。
2.2 加热加热是冷轧生产线退火工艺的关键步骤之一。
通过加热将冷轧钢板的温度升高至一定程度,以促进晶粒生长和内部应力的消除。
2.3 保温保温是在加热后将钢板保持在一定温度区间内的过程,在该温度区间内进行足够的时间,使得钢板的温度达到均匀稳定,并使晶粒生长得以完成。
2.4 冷却冷却是将钢板从退火温度迅速冷却至室温的过程。
冷却方式可以采用空冷、水冷、盐浴冷却等不同方式,具体的冷却方式需要根据产品需求和工艺要求进行选择。
2.5 质量检验退火后的钢板需要进行质量检验,包括外观质量检验、力学性能测试、化学成分分析等。
通过质量检验,可以确保产品符合相关标准和要求。
3.1 加热温度控制加热温度的控制对于退火工艺的成功至关重要。
需要根据不同钢种和产品要求确定适当的加热温度范围,并确保在加热过程中温度的均匀性和稳定性。
3.2 保温时间控制保温时间的控制也是冷轧生产线退火工艺的重要因素之一。
保温时间过短可能导致晶粒生长不完全,从而影响产品的性能;而保温时间过长则可能造成能源浪费和生产效率的降低。
3.3 冷却方式选择根据产品需求和工艺要求,选择合适的冷却方式对于保证产品质量具有重要意义。
不同冷却方式会对钢板的组织结构和性能产生不同的影响,需要进行合理选择和控制。
在进行冷轧生产线退火工艺时,必须严格按照相关安全规范操作,做好安全防护措施。
确保相关设备的运行安全,预防事故的发生,保障工人的人身安全。
冷轧生产线退火工艺是冷轧钢板制造过程中不可或缺的环节。
通过合理的工艺参数控制和操作流程控制,可以获得符合要求的产品。
在实际操作中,需要根据不同产品的要求和工艺特点进行灵活调整和改进,以提高产品质量和生产效率。
冷轧板的退火工艺:连续退火和罩式退火的比较

冷轧板的退火工艺:连续退火和罩式退火的比较冷轧产品是钢材中的精品,属高端产品,具有加工精细、技术密集、工艺链长、品种繁多、用途广泛等特点。
国际钢铁工业发展实践表明,随着经济社会发展,冷轧产品在钢材消费总量中的比重在不断提高,并发挥着越来越重要的作用。
冷轧后热处理是冷轧生产中的重要工序,冷轧板多为低碳钢,其轧后热处理通常为再结晶退火,冷轧板通过再结晶退火达到降低钢的硬度、消除冷加工硬化、改善钢的性能、恢复钢的塑性变形能力之目的。
冷轧板的再结晶退火在退火炉中进行,冷轧板退火炉分为罩式退火炉和连续退火炉,罩式退火炉又分为全氢罩式退火炉与普通罩式退火炉。
冷轧板退火技术的发展与罩式退火炉和连续退火炉的发展是密不可分的[10]。
退火工艺流程如图2.1所示:图2.1 退火工艺流程示意图表2.4 某钢厂罩式退火炉工艺参数热点/冷点温度CQ:710℃/640℃DQ:710 ℃/660℃DDQ:710 ℃/680℃HSLA:680℃/660℃一般生产中CQ、DQ热点和冷点温度差要大一些。
分别为90 ℃、70 ℃开始喷淋冷却温度内罩表面温度200 ℃,卷心温度:380℃左右生产调试中进行检测试验以确定不同钢卷开始喷淋冷却工艺出炉温度160 ℃出炉吊至终冷台冷却到平整温度约40 ℃图2.3 典型的罩式炉退火工艺温度曲线图罩式退火工艺罩式退火是冷轧钢卷传统的退火工艺。
在长时间退火过程中,钢的组织进行再结晶,消除加工硬化现象,同时生成具有良好成型性能的显微组织,从而获得优良的机械性能。
退火时,每炉一般以4个左右钢卷为一垛,各钢卷之间放置对流板,扣上保护罩(即内罩),保护罩内通保护气体,再扣上加热罩(即外罩),将带钢加热到一定温度保温后再冷却。
罩式退火炉发展十分迅速,2O世纪7O年代的普通罩式退火炉主要采用高氮低氢的氮氢型保护气体(氢气的体积分数2%~4%,氮气的体积分数为96%~98%)和普通炉台循环风机,生产效率低,退火质量差,能耗高;为了弥补普通罩式炉的缺陷,充分发挥罩式炉组织生产灵活,适于小批量多品种生产,建造投资灵活,可分批进行的优点,7O年代末奥地利EBNER公司开发出HICON/H 炉(强对流全氢退火炉),8O年代初德国LOI公司开发出HPH炉(高功率全氢退火炉)。
冷轧薄板连续退火技术的发展
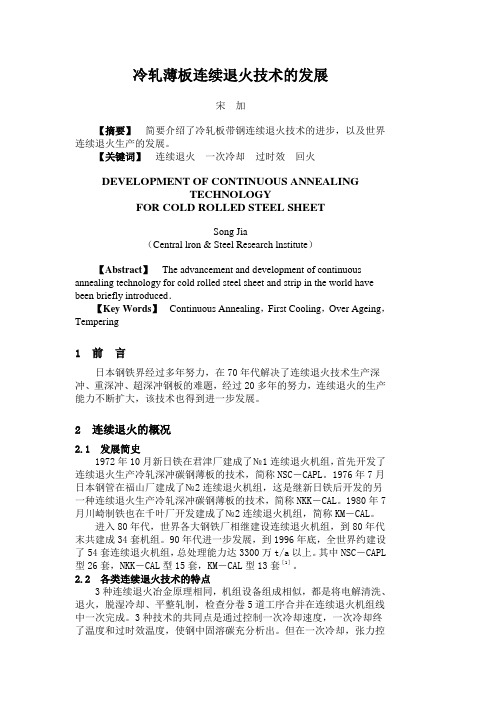
冷轧薄板连续退火技术的发展宋加【摘要】简要介绍了冷轧板带钢连续退火技术的进步,以及世界连续退火生产的发展。
【关键词】连续退火一次冷却过时效回火DEVELOPMENT OF CONTINUOUS ANNEALINGTECHNOLOGYFOR COLD ROLLED STEEL SHEETSong Jia(Central lron & Steel Research lnstitute)【Abstract】The advancement and development of continuous annealing technology for cold rolled steel sheet and strip in the world have been briefly introduced.【Key Words】Continuous Annealing,First Cooling,Over Ageing,Tempering1 前言日本钢铁界经过多年努力,在70年代解决了连续退火技术生产深冲、重深冲、超深冲钢板的难题,经过20多年的努力,连续退火的生产能力不断扩大,该技术也得到进一步发展。
2 连续退火的概况2.1 发展简史1972年10月新日铁在君津厂建成了№1连续退火机组,首先开发了连续退火生产冷轧深冲碳钢薄板的技术,简称NSC-CAPL。
1976年7月日本钢管在福山厂建成了№2连续退火机组,这是继新日铁后开发的另一种连续退火生产冷轧深冲碳钢薄板的技术,简称NKK-CAL。
1980年7月川崎制铁也在千叶厂开发建成了№2连续退火机组,简称KM-CAL。
进入80年代,世界各大钢铁厂相继建设连续退火机组,到80年代末共建成34套机组。
90年代进一步发展,到1996年底,全世界约建设了54套连续退火机组,总处理能力达3300万t/a以上。
其中NSC-CAPL 型26套,NKK-CAL型15套,KM-CAL型13套[1]。
连续退火带钢冷却技术最新进展
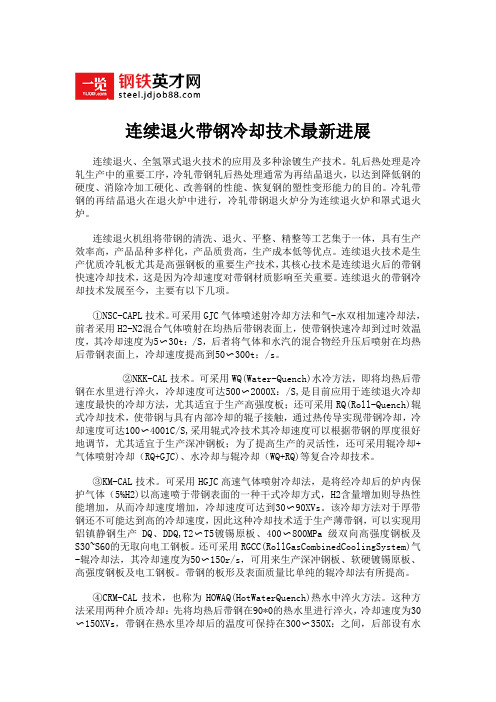
连续退火带钢冷却技术最新进展连续退火、全氢罩式退火技术的应用及多种涂镀生产技术。
轧后热处理是冷轧生产中的重要工序,冷轧带钢轧后热处理通常为再结晶退火,以达到降低钢的硬度、消除冷加工硬化、改善钢的性能、恢复钢的塑性变形能力的目的。
冷轧带钢的再结晶退火在退火炉中进行,冷轧带钢退火炉分为连续退火炉和罩式退火炉。
连续退火机组将带钢的清洗、退火、平整、精整等工艺集于一体,具有生产效率高,产品品种多样化,产品质贵高,生产成本低等优点。
连续退火技术是生产优质冷轧板尤其是高强钢板的重要生产技术,其核心技术是连续退火后的带钢快速冷却技术,这是因为冷却速度对带钢材质影响至关重要。
连续退火的带钢冷却技术发展至今,主要有以下几项。
①NSC-CAPL技术。
可采用GJC气体喷述射冷却方法和气-水双相加速冷却法,前者采用H2-N2混合气体喷射在均热后带钢表面上,使带钢快速冷却到过时效温度,其冷却速度为5〜30t:/S,后者将气体和水汽的混合物经升压后喷射在均热后带钢表面上,冷却速度提高到50〜300t:/s。
②NKK-CAL技术。
可采用WQ(Water-Quench)水冷方法,即将均热后带钢在水里进行淬火,冷却速度可达500〜2000X:/S,是目前应用于连续退火冷却速度最快的冷却方法,尤其适宜于生产高强度板;还可采用RQ(Roll-Quench)辊式冷却技术,使带钢与具有内部冷却的辊子接触,通过热传导实现带钢冷却,冷却速度可达100〜4001C/S,采用辊式冷技术其冷却速度可以根据带钢的厚度很好地调节,尤其适宜于生产深冲钢板;为了提高生产的灵活性,还可采用辊冷却+气体喷射冷却(RQ+GJC)、水冷却与辊冷却(WQ+RQ)等复合冷却技术。
③KM-CAL技术。
可采用HGJC高速气体喷射冷却法,是将经冷却后的炉内保护气体(5%H2)以高速喷于带钢表面的一种干式冷却方式,H2含量增加则导热性能增加,从而冷却速度增加,冷却速度可达到30〜90XVs。
冷轧不锈钢的退火及酸洗工艺

冷轧不锈钢的退火及酸洗工艺不锈钢热轧带钢经热带退火酸洗后,为了达到一定的性能及厚度要求,需进行常温轧制处理,即冷轧。
不锈钢冷轧时发生加工硬化,冷轧量越大,加工硬化的程度也越大,若将加工硬化的材料加热到200—400℃就能够排除变形应力,进一步提高温度则发生再结晶,使材料软化。
冷轧后的退火按退火方式分为连续卧式退火和立式光亮退火;按退火工序分为中间退火和最终退火。
顾名思义,中间退火是指中间轧制后的退火,而最终退火是指最终轧制后的退火,两者在工艺操纵和退火目的上无全然区别,因此下文统称为冷轧退火或者退火。
一、连续卧式退火(连退炉)连退炉是目前广为使用的退火设备,广泛用于带钢的热处理,其特点是带钢在炉内呈水平状态,边加热边前进。
炉子的结构一样要紧由预热段、加热段和冷却段组成。
卧式退火炉通常与开卷机、焊机、酸洗线等组成一条连续退火酸洗机组。
冷轧退火对不锈钢成品材料的机械性能有专门大阻碍,如晶粒度、抗拉强度、硬度、延伸率和粗糙度等。
其中退火温度和退火时刻对冷轧材料再结晶后的晶粒度具有最直截了当的阻碍。
10 晶粒度(ASTM)5 0 2 46 8 退火时刻(分)图1.SUS304带钢1100℃时退火时刻与晶粒度关系示意图如前所述,连退炉一样由预热、加热、冷却三大部分组成。
预热段没有烧嘴燃烧,而是利用后面加热段的辐射热来加热带钢,如此能够有效的利用热能,节约能源成本。
加热段利用燃料燃烧直截了当对带钢进行加热,该段一样分为若干各区,每个区都有高温计来操纵和显示温度。
燃烧后高达700多度的废气被废气风机抽出加热室后进入换热器,在换热器内将冷的燃烧空气进行加热(可加热到400多度),加热后的燃烧空气直截了当被送到各个烧嘴。
换热器的目的在于有效回收废气热量。
●炉内燃烧条件的治理。
燃料(液化石油气或天然气)在炉内的燃烧状况对质量、成本、热效率等都有专门大阻碍。
空燃比是燃烧治理的一个重要指标。
空燃比越高,燃烧越充分,然而排废量也相应增加,炉内氧含量提高,增加了带钢的氧化程度。
冷轧板连退工艺及冷却技术的研究
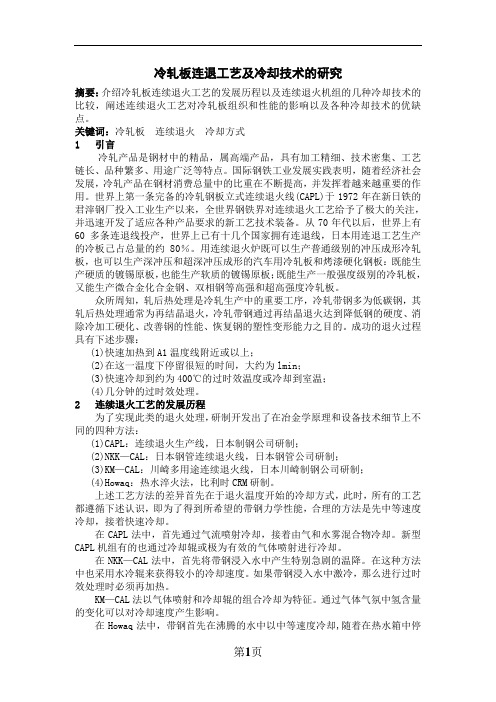
冷轧板连退工艺及冷却技术的研究摘要:介绍冷轧板连续退火工艺的发展历程以及连续退火机组的几种冷却技术的比较,阐述连续退火工艺对冷轧板组织和性能的影响以及各种冷却技术的优缺点。
关键词:冷轧板连续退火冷却方式1 引言冷轧产品是钢材中的精品,属高端产品,具有加工精细、技术密集、工艺链长、品种繁多、用途广泛等特点。
国际钢铁工业发展实践表明,随着经济社会发展,冷轧产品在钢材消费总量中的比重在不断提高,并发挥着越来越重要的作用。
世界上第一条完备的冷轧钢板立式连续退火线(CAPL)于1972年在新日铁的君滓钢厂投入工业生产以来,全世界钢铁界对连续退火工艺给予了极大的关注,并迅速开发了适应各种产品要求的新工艺技术装备。
从70年代以后,世界上有60多条连退线投产,世界上已有十几个国家拥有连退线,日本用连退工艺生产的冷板己占总量的约80%。
用连续退火炉既可以生产普通级别的冲压成形冷轧板,也可以生产深冲压和超深冲压成形的汽车用冷轧板和烤漆硬化钢板:既能生产硬质的镀锡原板,也能生产软质的镀锡原板;既能生产一般强度级别的冷轧板,又能生产微合金化合金钢、双相钢等高强和超高强度冷轧板。
众所周知,轧后热处理是冷轧生产中的重要工序,冷轧带钢多为低碳钢,其轧后热处理通常为再结晶退火,冷轧带钢通过再结晶退火达到降低钢的硬度、消除冷加工硬化、改善钢的性能、恢复钢的塑性变形能力之目的。
成功的退火过程具有下述步骤:(1)快速加热到A1温度线附近或以上;(2)在这一温度下停留很短的时间,大约为lmin;(3)快速冷却到约为400℃的过时效温度或冷却到室温;(4)几分钟的过时效处理。
2 连续退火工艺的发展历程为了实现此类的退火处理,研制开发出了在冶金学原理和设备技术细节上不同的四种方法:(1)CAPL:连续退火生产线,日本制钢公司研制;(2)NKK—CAL:日本钢管连续退火线,日本钢管公司研制;(3)KM—CAL:川崎多用途连续退火线,日本川崎制钢公司研制;(4)Howaq:热水淬火法,比利时CRM研制。
冷轧生产线退火工艺

冷轧生产线退火工艺引言退火是冷轧生产线中的重要工艺之一,它能提高材料的塑性和韧性,减少应力,并改善材料的微观组织结构。
本文将介绍冷轧生产线退火工艺的基本原理、步骤以及对材料性能的影响。
一、冷轧生产线退火的基本原理冷轧生产线退火的基本原理是通过升温、保温和冷却过程控制材料的晶粒尺寸和晶体结构,从而达到改变材料力学性能的目的。
具体来说,退火过程中材料的晶粒会逐渐长大并重新排列,同时消除或减少材料中的应力和缺陷,从而提高材料的塑性和韧性。
二、冷轧生产线退火的步骤1.清洗:首先将冷轧板材从前工序传送到退火工序,需要对板材进行清洗,以去除表面的油污、氧化皮等杂质。
2.升温:将清洗后的板材放入退火炉中,通过加热使其温度逐渐升高,一般升温速度控制在5℃/min左右。
3.保温:当板材达到指定温度后,需要进行保温一段时间,以使材料的晶粒逐渐长大、晶体结构重排并消除应力。
保温时间一般根据材料的性质和要求来确定。
4.冷却:保温结束后,将板材从退火炉中取出,进行快速冷却。
冷却方式可以是自然冷却、水冷却或气体冷却,根据具体情况选择合适的冷却方式。
三、冷轧生产线退火对材料性能的影响冷轧生产线退火可以显著改善材料的力学性能和物理性能,具体影响如下:1. 提高材料的塑性和韧性退火过程中,材料的晶粒逐渐长大,晶界移动,且晶体结构重排,从而降低了材料的内应力和缺陷,提高了材料的塑性和韧性。
退火后的材料更容易进行加工和成型。
2. 降低材料的硬度和强度冷轧板材在冷轧过程中通常会产生较高的硬度和强度,通过退火能够降低材料的硬度和强度,使其更加柔软和易于加工。
3. 改善材料的织构和微观组织结构退火能够改善材料的织构和微观组织结构,使其晶粒更为均匀和细小,晶粒内部的组织结构更加致密。
这种改善能够提高材料的均匀性、稳定性和耐腐蚀性能。
4. 消除材料中的残余应力冷轧生产线退火过程中的加热、保温和冷却能够消除或减少材料中的残余应力。
残余应力会对材料的形状稳定性和力学性能产生不良影响,因此通过退火能够提高材料的综合性能。
冷轧连退生产工艺概述

连 续 化 生 产 的生 产方 式 , 生产不 问断 , 连续性好 , 产 能高 . 占
地 面 积小 , 是 一 种 比较 先 进 的 生产 工 艺 。 冷 轧 连 退 工 艺 主 要 有 以 下几 种 优 势 :
钢 。其 产 品 拥 有 较 好 的 强 度 和 精 细 的表 面 质 量 . 满 足 了金 属 表 面 喷漆 的要 求 。 广泛应用 于汽车 、 家 电等 行 业 , 满 足 了其 对
冷 轧板 较 高 的要 求
3 . 连 续 退 火 工 艺 的 缺 点 。 工 艺技 术 繁 琐 、 复杂 , 操 作 难 度
钢材 冷轧 及罩 式退 火的 介绍
1 . 冷 轧 生 产 的工 序 冷 轧 是 用 热 轧 卷 板 为 生 产原 料 . 经 过
火、 精 整 等 一 系 列 工 艺 流 程 集 中在 一 条 机组 生 产 线 中 进 行 的
对热 轧钢 卷 的冷 轧 制 . 使其 发生 冷 变 形 的工 艺 过 程 。
的 质 量 。轧 制 则 是 通 过 轧 钢 机 使 材 料 发 生形 变 的过 程 。脱 脂 是 对 轧 材 表 面 上 附 着 的 油 脂 、 污垢 等 进 行 清 洗 和 处 理 的 工 导. 以保 证 退 火 时钢 材表 面 的 洁 净 无 杂 质 。退 火 工 序 主要 是 对轧材进 行加热 . 然 后 冷 却 处 理 的过 程 . 退 火 可 以使 轧 材 通
的 工 艺 方 式 避 免 了罩 式 退 火 工 艺 中 . 卷 钢 因多 次 搬 运 造 成 的 划伤 、 粘贴 、 折边等缺陷 。 提点 . 恢 复 了 材 料 的 机 械 性 和 可 塑 性 。精 整 是指对轧材进行检查 、 平整、 分类包装 的过程 , 保 证 产 品 的合 格. 满足对冷轧 产品较高 的包装要求 , 防 止 产 品运 输 过 程 中 的损 伤 。
冷轧带钢退火目的及种类
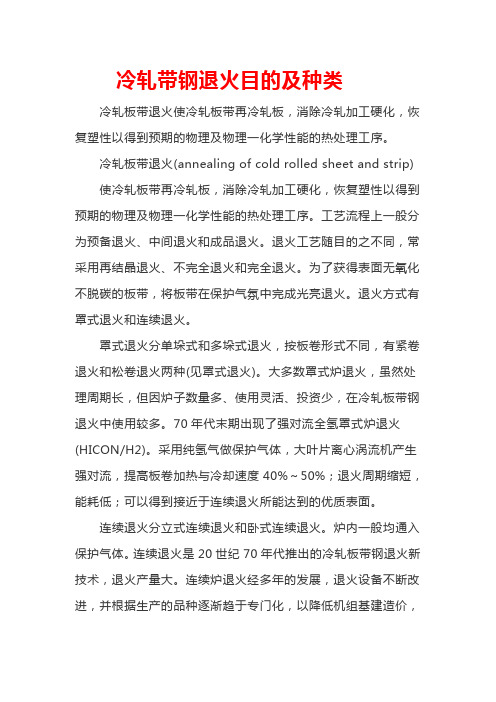
冷轧带钢退火目的及种类冷轧板带退火使冷轧板带再冷轧板,消除冷轧加工硬化,恢复塑性以得到预期的物理及物理一化学性能的热处理工序。
冷轧板带退火(annealing of cold rolled sheet and strip) 使冷轧板带再冷轧板,消除冷轧加工硬化,恢复塑性以得到预期的物理及物理一化学性能的热处理工序。
工艺流程上一般分为预备退火、中间退火和成品退火。
退火工艺随目的之不同,常采用再结晶退火、不完全退火和完全退火。
为了获得表面无氧化不脱碳的板带,将板带在保护气氛中完成光亮退火。
退火方式有罩式退火和连续退火。
罩式退火分单垛式和多垛式退火,按板卷形式不同,有紧卷退火和松卷退火两种(见罩式退火)。
大多数罩式炉退火,虽然处理周期长,但因炉子数量多、使用灵活、投资少,在冷轧板带钢退火中使用较多。
70年代末期出现了强对流全氢罩式炉退火(HICON/H2)。
采用纯氢气做保护气体,大叶片离心涡流机产生强对流,提高板卷加热与冷却速度40%~50%;退火周期缩短,能耗低;可以得到接近于连续退火所能达到的优质表面。
连续退火分立式连续退火和卧式连续退火。
炉内一般均通入保护气体。
连续退火是20世纪70年代推出的冷轧板带钢退火新技术,退火产量大。
连续炉退火经多年的发展,退火设备不断改进,并根据生产的品种逐渐趋于专门化,以降低机组基建造价,有利于提高产品的质量。
连续炉退火不但能生产表面等级良好的特殊深冲级别的带钢,也可以生产高强度板连续退火。
连续退火与罩式退火相比有哪些优点和问题?连续退火既可以生产软钢板又可以生产级别较高的高强钢板。
产品开发优势明显,如:生产连续化、生产周期短、板形好、产品表面光滑等优点。
但是投资大且技术过于复杂,比较适合大批量、少品种生产,这种退火工艺越来越受到大型冷轧厂的欢迎。
罩式退火与连续退火相比,具有生产软钢板、生产灵活、施工投资少等优势,但在高强度钢板生产上有所欠缺,有间歇生产、生产周期长、效率低等不足,适用于小批量和多品种生产,这种退火工艺在民营冷轧厂或小型冷轧厂中非常受欢迎。
冷轧钢板中退火的应用
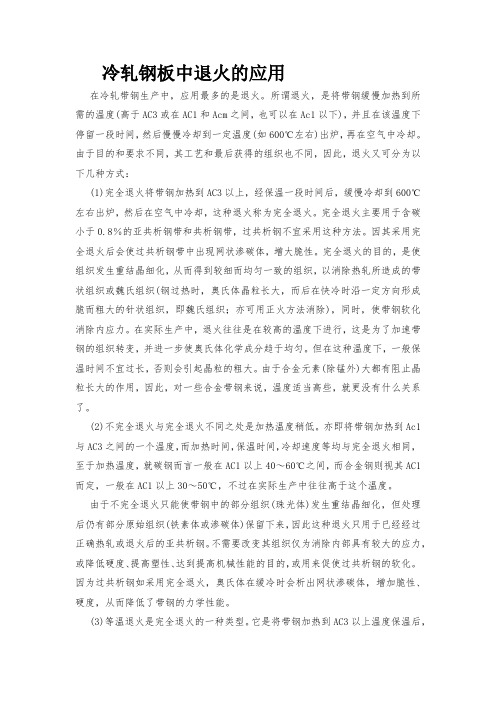
冷轧钢板中退火的应用在冷轧带钢生产中,应用最多的是退火。
所谓退火,是将带钢缓慢加热到所需的温度(高于AC3或在AC1和Acm之间,也可以在Ac1以下),并且在该温度下停留一段时间,然后慢慢冷却到一定温度(如600℃左右)出炉,再在空气中冷却。
由于目的和要求不同,其工艺和最后获得的组织也不同,因此,退火又可分为以下几种方式:(1)完全退火将带钢加热到AC3以上,经保温一段时间后,缓慢冷却到600℃左右出炉,然后在空气中冷却,这种退火称为完全退火。
完全退火主要用于含碳小于0.8%的亚共析钢带和共析钢带,过共析钢不宜采用这种方法。
因其采用完全退火后会使过共析钢带中出现网状渗碳体,增大脆性。
完全退火的目的,是使组织发生重结晶细化,从而得到较细而均匀一致的组织,以消除热轧所造成的带状组织或魏氏组织(钢过热时,奥氏体晶粒长大,而后在快冷时沿一定方向形成脆而粗大的针状组织,即魏氏组织;亦可用正火方法消除),同时,使带钢软化消除内应力。
在实际生产中,退火往往是在较高的温度下进行,这是为了加速带钢的组织转变,并进一步使奥氏体化学成分趋于均匀。
但在这种温度下,一般保温时间不宜过长,否则会引起晶粒的粗大。
由于合金元素(除锰外)大都有阻止晶粒长大的作用,因此,对一些合金带钢来说,温度适当高些,就更没有什么关系了。
(2)不完全退火与完全退火不同之处是加热温度稍低。
亦即将带钢加热到Ac1与AC3之间的一个温度,而加热时间,保温时间,冷却速度等均与完全退火相同,至于加热温度,就碳钢而言一般在AC1以上40~60℃之间,而合金钢则视其AC1而定,一般在AC1以上30~50℃,不过在实际生产中往往高于这个温度。
由于不完全退火只能使带钢中的部分组织(珠光体)发生重结晶细化,但处理后仍有部分原始组织(铁素体或渗碳体)保留下来,因此这种退火只用于已经经过正确热轧或退火后的亚共析钢。
不需要改变其组织仅为消除内部具有较大的应力,或降低硬度、提高塑性、达到提高机械性能的目的,或用来促使过共析钢的软化。
冷轧薄板连退工艺培训教材
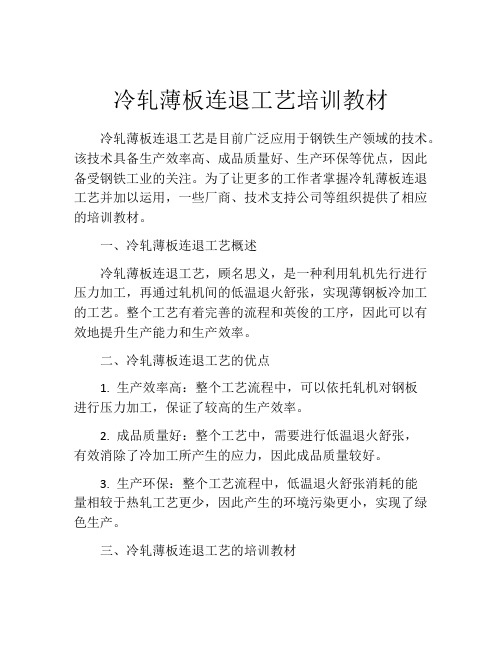
冷轧薄板连退工艺培训教材冷轧薄板连退工艺是目前广泛应用于钢铁生产领域的技术。
该技术具备生产效率高、成品质量好、生产环保等优点,因此备受钢铁工业的关注。
为了让更多的工作者掌握冷轧薄板连退工艺并加以运用,一些厂商、技术支持公司等组织提供了相应的培训教材。
一、冷轧薄板连退工艺概述冷轧薄板连退工艺,顾名思义,是一种利用轧机先行进行压力加工,再通过轧机间的低温退火舒张,实现薄钢板冷加工的工艺。
整个工艺有着完善的流程和英俊的工序,因此可以有效地提升生产能力和生产效率。
二、冷轧薄板连退工艺的优点1. 生产效率高:整个工艺流程中,可以依托轧机对钢板进行压力加工,保证了较高的生产效率。
2. 成品质量好:整个工艺中,需要进行低温退火舒张,有效消除了冷加工所产生的应力,因此成品质量较好。
3. 生产环保:整个工艺流程中,低温退火舒张消耗的能量相较于热轧工艺更少,因此产生的环境污染更小,实现了绿色生产。
三、冷轧薄板连退工艺的培训教材对于广大的钢铁从业人员而言,学习并掌握冷轧薄板连退工艺是非常有必要的。
对于想要透彻理解该工艺的工作者而言,相关厂商、技术支持公司等会适时发布冷轧薄板连退工艺的培训教材,以帮助大家学习和掌握该技术。
这些培训教材通常包含有关冷轧薄板连退工艺的完整流程介绍,从生产前期的钢材选用到加工、退火等各个工序都有详细的介绍。
同时,还会配备一些实例以及直观的图表,以方便理解该工艺。
在培训教材的制作过程中,通常会邀请一些业内的科研专家和实践经验丰富的生产工作者、技术人员等前来参与贡献,以确保这些教材的准确性和实用性。
四、冷轧薄板连退工艺的未来发展冷轧薄板连退工艺在目前的钢铁生产领域中已经成为了不可或缺的技术之一。
在未来的发展中,可以预测的是,冷轧薄板连退工艺将会在细分的领域中得到更加深入的应用。
对于不同行业的需求,该工艺有着相应的细分,比如如何实现稀有金属的加工等细分领域。
因此,在未来的发展中,冷轧薄板连退工艺将会深入到更多的领域,并优化相应的技术实现,成为未来钢铁生产领域中的重要技术之一。
冷轧薄板连退工艺培训课件
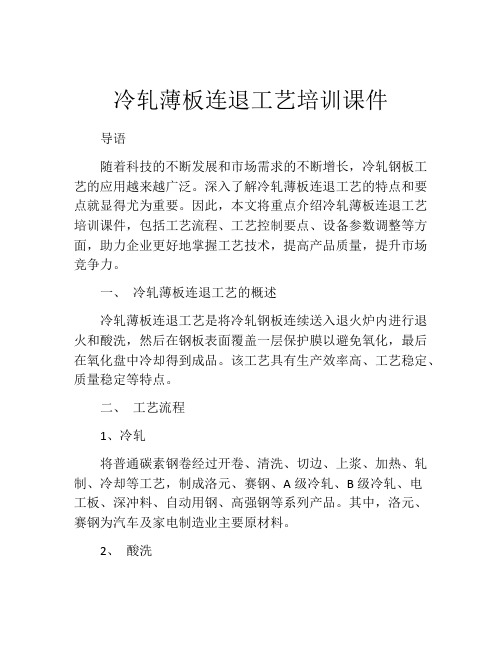
冷轧薄板连退工艺培训课件导语随着科技的不断发展和市场需求的不断增长,冷轧钢板工艺的应用越来越广泛。
深入了解冷轧薄板连退工艺的特点和要点就显得尤为重要。
因此,本文将重点介绍冷轧薄板连退工艺培训课件,包括工艺流程、工艺控制要点、设备参数调整等方面,助力企业更好地掌握工艺技术,提高产品质量,提升市场竞争力。
一、冷轧薄板连退工艺的概述冷轧薄板连退工艺是将冷轧钢板连续送入退火炉内进行退火和酸洗,然后在钢板表面覆盖一层保护膜以避免氧化,最后在氧化盘中冷却得到成品。
该工艺具有生产效率高、工艺稳定、质量稳定等特点。
二、工艺流程1、冷轧将普通碳素钢卷经过开卷、清洗、切边、上浆、加热、轧制、冷却等工艺,制成洛元、赛钢、A级冷轧、B级冷轧、电工板、深冲料、自动用钢、高强钢等系列产品。
其中,洛元、赛钢为汽车及家电制造业主要原材料。
2、酸洗经冷轧后的钢板表面会残留一些氧化铁皮或其他杂质,严重影响钢板质量。
酸洗的主要作用是去除这些氧化铁皮和杂质,保证钢板表面光洁度和耐腐蚀性。
主要使用的酸洗液是硫酸和盐酸混合液体。
3、退火退火是为了消除钢板的应力和提高其机械性能。
退火过程中需要注意温度、时间和气氛的合理配合,从而提高钢板的质量。
4、抛光在钢板表面抛光,使钢板表面光洁平滑并增加柔韧性,更进一步提高钢板的产品质量。
5、包装对于冷轧后的钢板,需要对其进行优质的包装,保证其运输和使用过程中的安全性,从而达到最终客户的满意度。
三、工艺控制要点1、轧制质量控制冷轧的轧制过程中对钢板的损伤和畸变要进行精度控制,必须保持精度和质量的稳定性。
2、退火控制退火过程中要进行不同酸洗液的选用和浓度的控制,调整温度和时间,控制气氛,保证钢板表面质量和机械性能稳定。
3、包装控制包装是保证冷轧薄板质量的最后一道工序,需要注意包装方式、包装材料的选择和捆绑强度的控制。
四、设备参数调整1、冷轧机对于不同规格和材质的钢板,需要进行冷轧机参数的调整,包括轧辊的尺寸、轧辊的形状和轧机的工作模式,以确保冷轧质量。
- 1、下载文档前请自行甄别文档内容的完整性,平台不提供额外的编辑、内容补充、找答案等附加服务。
- 2、"仅部分预览"的文档,不可在线预览部分如存在完整性等问题,可反馈申请退款(可完整预览的文档不适用该条件!)。
- 3、如文档侵犯您的权益,请联系客服反馈,我们会尽快为您处理(人工客服工作时间:9:00-18:30)。
25~150 50—200
需要 不需要
2—4 2—3.5
水淬十辊冷联合(WQ+RC)
160~l 000 需要
1.5~3
适用品种
镀锡原板 镀锡原板、冷轧板
冷轧板 冷轧板、高强度板
冷轧板 冷轧板、高强度板
冷轧饭 冷轧板、高强度板
设备 维护 简单 简单 复杂 复杂 简单 复杂 简单 复杂
带钢 表面 带钢 板形 质量 性能
收稿日期:2007-09—26;修回日期:2007—10-20
万方数据
一13一
2007年第6期(总120期)
向冷却均匀。喷嘴喷射的气体中含氢,这能增加导 热性。可加速一次冷却,冷却速度可达l∞100 oC/s。
气水双相冷却(ACC) 新日铁开发的口琴 式气流雾化水冷却喷嘴,并采用了参照模式自适 应控制法及卡尔曼过滤法的控制系统。能精确控 制冷却终点温度400±5℃及冷却速度。
Introduction on Continuous Annealing Technology for Cold Rolled Sheet Plate Guo Ju,Zhang Xiaowei
Abstract:The article describes the improvement of cold rolled strip continuous annealing technology,and the development of world continuous annealing production.
相似文献(3条)
1.会议论文 石斌 1420冷轧CAPL机组一次冷却炉仿真控制模型的研究 2002
宝钢1420mm冷轧工程CAPL机组是镀锡原板退火专用生产线,采用计算机控制各炉室的带钢温度.根据一次冷却炉(1CF)在生产中出现的情况,为提高控 制的稳定、降低损耗,从风机转速、挡板量和控制策略,对原模型控制进行仿真研究.
日本钢管采用的技术交流矢量控制晶体管 变换器,多重反射式温度计和动态板温控制模型;
川崎制铁采用的技术 高功能矢量变换器和 低惯性高响应装置,可使张力精度达+98 N,利 用有限元瓢曲模拟模型设计辊子形状以防止宽带 钢瓢曲。
(3)设置炉辊辊形控制 机组通带在升温或停车后重新启动。炉辊与 带钢温度不同会影响炉辊热凸度。近年采取在炉 辊室设置冷却与加热器,以有效控制炉辊辊形。
冷却速度 后续表面 过时效或回火时间
(℃/s)
处理
(min)
气冷(GJC)
5—30
不需要
3-5
高速喷气冷却(HGJC,H—GJC) 10—100 不需要
2—4
气水双相冷却(ACC)
50—200
需要
2—3
冷水淬冷却(WQ)
500~2000 需要
l
辊冷冷却(RC)
100一300 不需要
2-3
热水淬冷却(HOWAC) 喷气与辊淬联合(GJC+RQ)
的析出;还有一种为先等温再斜坡过时效。 2.3张力及板温控制技术
新日铁采高精度张力稳 定装置外,还在炉内设置数个热张紧辊。各炉段 的张力反馈信号参与控制。
器。炉后设分段张紧辊装置。设中心位置控制 器。一次冷却段横向冷却模型控制系统,炉子段 张力监测控制系统,炉辊自动速度调节系统,低 惯性高响应张力调节系统;
在钢铁行业飞速发展的今天.各大钢厂对成 品带材的板形要求越来越严格。在设计轧机的板 形控制手段上也在不断改进。本文介绍了板形自 动检测及闭环控制的形式及控制手段。
1 板形测量辊的几种形式
我竺!篓篓竺篆竺要查罂[篓兰妻套竺苎苎 g。。t签,.t,。妻翌芝竺鬯堡雹薹?『i|皂芝鬯芝型,_烹苎竽
机组中都采用了板形自动检测和闭环控制装置。
热水淬冷却(HOWAC) 是新日铁与比利时 考柯尔桑布尔钢铁公司联合开发的冷却技术,通 过沉没辊的上下移动。使一次冷却的终点温度控 制十分简单.并在热水淬系统后设有水雾冷却, 用于生产高强度板或镀锡原板。采用HOWAC需要 后续表面处理。各种一次冷却技术特点比较见表1。
表1 一次冷却技术特性比较
冷却方法
Key words:COUtillUOUS annealing,one time cooling,overaging,tempering,cold rolled strip
日本钢铁界经过多年努力于20世纪70年代 解决了连续退火技术生产中钢板深冲、重深冲、 超深冲的难题,经过20多年的努力,连续退火 的生产能力不断扩大,该技术也得到进一步发展。
辊式冷却(RC) 日本钢管研制这种技术, 使带钢与内部通水冷却的辊子接触,通过热传导 对带钢冷却,冷却速度为100—300 oC/s,改变带 钢与水冷辊的接触时间可调节冷却速度。
高速气体喷射冷却(HGJC) HGJC是由川 崎制铁与三菱重工共同开发,采用窄缝喷嘴向带 钢两面喷射气体,调节风机出口的阀板改变冷却 速度。冷却装置分成多个区段,以使带钢宽度方
一14一
国内现有连续退火机组约有15条.在建的
万方数据
‘一重技术》
板形自动检测及闭环控制技术的应用
郭 if_1。高成章2
(1.一重集团大连设计研究院工程师,辽宁 辽宁大连116600)
大连
116600;2.一重集团大连设计研究院高级工程师,
摘要:介绍冷连轧机组设计中应用板形辊的几种形式、板形自动检测装置和闭环控制系统功能。 关键词:板形仪;自动检测;板形控制;冷连轧机 中图分类号:TG334.9文献标识码:B文章编号:1673—3355(2007)06-0008--02
4连续退火的优点
(1)产品质量好,板形平直,表面清洁,性 能均匀:
(2)成材率高,不会产生罩式退火易出现的 粘结、折边等缺陷,成材率可提高2%一3%;
3 连续退火生产发展趋势
3.1专业化生产 近年建设的连续退火机组多将镀锡原板与冷
轧薄板分开.不在同一套机组生产。这样便于合 理选择设备。使机组能更精细地控制全线各段张 力,运行稳定.提高机组作业率。 3.2连续炉更趋完善
1连续退火技术概况
1.1 发展简史 新日铁开发了连续退火生产冷轧深冲碳钢薄
板的技术,简称NSC—CAPL。日本钢管开发的另 一种连续退火生产冷轧深冲碳钢薄板的技术。简 称NKK—CAL。川崎制铁开发建成了连续退火机 组,简称KM—CAL。 1.2各类连续退火技术的特点
以上三种连续退火技术冶金原理相同,设备 组成相似。都是将电解清洗、退火,脱湿冷却、 平整轧制.检查分卷5道工序合并在连续退火机 组中一次完成。三种技术的共同点是通过控制一 次冷却速度、一次冷却最终温度和过时效温度, 使钢中固溶碳充分析出。
本文链接:/Periodical_ycjs200706007.aspx
下载时间:2010年3月14日
(I)生产厚度>2.0 mm的产品较困难,尚不 能生产厚度I>2.5 mm的产品:
(2)规格范围覆盖面不宜太宽; (3)产品变化灵活性略差,年产量变化时, 罩式退火炉增减开停十分灵活。连续退火炉难以
6结 语
世界上连续退火技术发展很快,已有了很大 进步,我国冷轧薄板生产技术和装备比较薄弱, 每年需进口冷轧产品350~400万t。随着今后冷 轧薄板生产能力的提高。为满足市场对高质量冷 轧板的需求.将会在一些重点钢铁企业新建连续 退火机组。
Application on Shape of Strip Automatic Detection and Closed Loop Control Technology
Guo Ju Gao,Chengzhang
Abstract:The article describes several types of profile roll,profile automatic detection device and closed loop control system functions in the design of cold tandem mill. Key words:shapemeter;automatic detection;profile control;cold tandem mill
3.学位论文 陆永强 无铬耐指纹板表面皱纹缺陷产生原因分析及对策 2006
宝钢分公司冷轧连续退火机组生产CQ钢种耐指纹基板过程中发生的表面皱纹缺陷影响了耐指纹产品的表面质量。通过对钢板在退火过程和平整过程 的影响分析,表面皱纹缺陷是钢板在连续退火过程中碳、氮等固溶元素在位错周围形成柯氏气团,在塑性变形过程中产生屈服平台导致的。为了消除表 面皱纹缺陷,可以采用提高加热温度、降低机组速度、提高一次冷却温度和速度、提高时效温度、加大平整延伸率、增加轧制力等改进措施。结合宝钢 生产现场的实际情况,重新制定了退火和平整工艺。
2.期刊论文 陆永强.倪富荣.张宝平.Lu Yongqiang.Ni Furong.Zhang Baoping 无铬耐指纹板表面皱纹缺陷产生原
因分析及对策 -宝钢技术2006(2)
宝钢分公司冷轧连续退火机组生产CQ钢种耐指纹基板过程中发生的表面皱纹缺陷影响了产品的表面质量.通过对钢板在退火过程和平整过程的影响的 分析,表面皱纹缺陷是钢板在连续退火过程中碳、氮等固溶元素在位错周围形成柯氏气团,在塑性变形过程中产生屈服平台导致的.为了消除表面皱纹缺陷 ,可以采取提高加热温度、降低机组速度、提高一次冷却温度和速度、提高时效温度、加大平整延伸率、增加轧制力等改进措施.结合宝钢生产现场的实 际情况,重新制定了退火和平整工艺.
收稿日期:20ff'l—lo_lO:修回B期:200r7—10-22
万方数据
一15一
冷轧薄板连续退火技术简介
作者: 作者单位: 刊名:
英文刊名: 年,卷(期): 引用次数:
郭巨, 张晓伟, Guo Ju, Zhang Xiaowei 一重集团大连设计研究院,辽宁,大连,116600
一重技术 CFHI TECHNOLOGY 2007,(6) 0次