潜在失效模式及后果分析(表格1)
潜在失效模式及后果分析FMEA新版表格2020.10.9

第2步 结构分析
第3步 功能分析
1.上一较高级别 2.关注要素
3.低一较低级别或 特性类型
1.上一较高 级别功能及
要求
2.关注要素功 能及要求
3.下一较低级别 功能及要求或特
性
AIAG - VDA DFMEA
项目: DFMEA开始时间: DFMEA修订日期: 多功能组:
FC的频度 (O)
针对FC或FM的 当前探测控制
DC
FC/FM 探测度
(D)
设计 FMEA措 标识(选 预防 施优先级 填) 措施
AP
探测 措施
责任人
计划完成 时间
第6步 改进措施
第6步 改进措施
状态:
采取基于证 据的措施
实际 完成 时间
S
O
D AP
第7步 结果文件化
第4步
失效分析
风
1.对于上一较高级 别要素和/或最终 用户的失效影响 (即:失效影响)
FE
FE的严重度 (S)
2.关注要ቤተ መጻሕፍቲ ባይዱ的失效模式 (即:失效模式) FM
3.下一较低级别要素 或特性的失效起因 (即:失效起因)
FC
对FC的当前 预防控制 PC
VDA DFMEA
第5步 风险分析
DFMEA ID 编号: 设计责任: 保密级别:
潜在失效模式及后果分析(PFMEA)

4 2 5 4 3
进料检验试产测试 要求供应商排版确认样品。 要求供应商排版确认样品。 要求供应商排版确认样品。 要求供应商提供确认样品。
2 2 3 2 3
32 28 75 40 54
保丽龙
重量 保丽龙 尺寸 外观不良 唛头
产品不安全,破损 外观不良,影响安全 客户投诉 唛头错误、客户投诉,
6 4 6 5
2
现行控制方法
l 来 料 检 验
外观不良
透明度不够,导致产品缺陷
供应商材料发生了变化
要求供应商固定客户原材料订购
树脂
浓度 重量 含铅 拉力不够
调配后产品收缩比列大,变形 数据预算错误,导致产品重量不足 不符合标准 翻次过低、影响使用次数
6 4 8 7
原材料过浓或者偏稀 供应商称重失误 供应商材料不达标 材料发生质变
3
按作业指导书操作。 现场巡检及日检查报表
4 3 2 3 3 2 2
60 0 12 48 27 12 20
2 4
现场巡检及日检查报表 现场巡检及日检查报表 现场管理巡检、操作员自检 现场巡检及日检查报表 核对产品所需物料全数清点
白坯检验功能不良
重量不符 尺寸
核对标准样件、按客户要求,每件称 3 重保重。 操4
供应商供应材料不符合欧美RoHS元素
3
要求供应商提供最新第三方检测报告,生产前送 第三方检测。
2
24
颜色易脱落,客服投诉 字体错误、印刷部清楚 导致条码无法读数,客户投诉 字体错误、印刷不清楚 产品不安全,破损
4 7 5 5 6
供应商品质部符合质量要求 供应商品质部符合质量要求 供应商品质部符合质量要求 供应商排版不挡 要求供应商按标准密度生产
IATF16949潜在失效模式及后果分析程序(含配套表格)

潜在失效模式及后果分析流程图1. 目的认可并评价在设计和制造过程中潜在的失效模式,分析其后果,评估其风险,从而预先采取措施,消除或减少失效发生的机会,有效地提高产品质量和可靠性,达到顾客满意。
2. 适用范围适用于新的或更改后的产品/过程的策划设计阶段,对构成产品的各子系统、零部件,对构成过程和服务的各个过程的潜在失效模式及后果进行分析的活动。
3. 术语和定义3.1 DFMEA:设计潜在失效模式和后果分析,是指产品设计人员采用的一门分析技术,在最大范围内保证充分地考虑失效模式及其相关的后果起因/机理,DFMEA以最严密的形式总结了工程技术人员进行产品设计时的指导思想。
3.2 PFMEA:过程潜在失效模式和后果分析,主要是由负责制造的工程师/多方论证小组采用的一种分析技术,用来保证在可能的范围内已充分地考虑到并指明潜在失效模式及其相关的起因或机理。
4. 职责4.1技术部职责4.1.1 组织由负责过程设计、制造、装配、售后服务、质量及可靠性等方面的专家成立多方论证小组。
4.1.2负责计算风险顺序数RPN,并编制《风险顺序数序列表》。
4.1.3负责对FMEA的输出整理归档。
4.2 多方论证小组职责4.2.1负责收集与PFMEA相关数据资料。
4.2.2负责进行PFMEA分析、评审、效果跟踪和确认。
5. 工作程序5.1 DFMEA5.1.1 由技术部组织设计人员、工艺人员、市场部、质量部、采购部相关人员成立多方论证小组,报管理者代表批准。
5.1.2多方论证小组根据设计任务书的设计要求和预期的工艺流程,对设计方案进行分析评审,分析产品在设计结构中的每一个关键部位、结构的风险,并确定需执行DFMEA的高风险的零部件/子系统/系统。
5.1.3 多方论证小组对确定为高风险的部位、结构进行DFMEA,并记录于表格《潜在的失效模式及后果分析(DFMEA)》,当顾客或总经办要求对中等风险的部位、结构进行DFMEA时,按确定的步骤实施。
3阶段.PFMEA_1潜在失效模式及后果分析。失效模式风险顺序排列表

項目名稱 Project name: 過程責任部門 Process responsible Dept.: 車型年度/車 輛: Model Year/Vehicle
核心小組 Core team:
過程功能 Process Function
要求 Requirement
S6前灯支架
工程部
S6-6205450
核心小組 Core team:
過程功能 Process Function
要求 Requirement
S6前灯支架
工程部
S6-6205450
生产部/李胜
建;品质部/
冯厚荣,工程
部/张学
志,PMC部/范
永峰,
营业部/沈君雷,工模部/陈声波,体系推行/刘黎
潛在的 Potential
R. P. N.
來料检查
影响功能,性 材质用错 能下降,导致
客户退货
6
Ⅱ
供应商供料材质 出错,影响生产
4
IQC按受入检查 基准书和材质 证明书检查材
质
IQC按 AQL0.65检查 材料
5
120
IQC按受入检查 基准书和材质 证明书、正确 的样板检查材 质
按检查基准书、 IQC (2011- 材质证明书和样
潛在的 Potential
失效后果 Failure Result
嚴 重 度
分 级 (重 要程
(S) 度)
潛在失效 Potential Failure 起因/機理
Origin /Machanism
FMEA編號 FMEA No.:
20110630001
關鍵日期 Key date:
11.06.30
FMEA日期: FMEA date:
FMEA潜在失效模式及分析表格模版
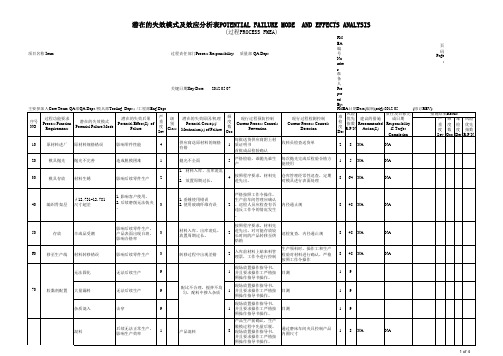
2
入库前材料上贴来料管 理票
生产领料时,操作工和生产 检验对材料进行确认
4
24
NA
NA
∮15.840-15.870 尺寸超差 140 外圆磨削
影响客户装配
4
1.砂轮磨损 2.零件装夹不到位
2
1. 定期维护保养磨床 2. 现场放置操作指导 书,并且要求操作工严 格按照操作指导书操作 。 3.确保砂轮无振动
工 AND EFFECTS ANALYSIS
现行过程检测控制 Current Process Controls Detection
FMEA编号Number: 页码Page: 准备人Prepared By: FMEA日期Data(编制(orig):2012.05 (修订REV): 责任及目标完 措施结果Result 难 风险 建议的措施 严 频 难 成日期 检 优先 Recommended Responsibility 重 度 检 度 指数 Action(S) 度 数 度 & Target Det R.P.N Sev Occ Det . Completion
2
生产领料时,操作工和生产 检验对材料进行确认,严格 按照工作令操作 目测
8
48
NA
NA
无法固化
无法后续生产
9
1
1
9
70
胶黏剂配置
大量漏料
无法后续生产
9
配比不合理,搅拌不均 匀,配料中掺入杂质
1
目测
1
9
杂质混入
击穿
9
1
目测
1
9
混料
后续无法正常生产, 影响生产效率
1
产品混料
8
通过磨床车间夹具控制产品 内圆尺寸
潜在失效模式及后果分析(DFMEA)

FMEA编号: 共 5页 , 第 1~5 页 编制人: FMEA日期(编制)2015.3.14 FMEA日期(修订) 2016.5.15 措施结果 责任及目标 建议措施 采取的措施 S O D 完成日期
RPN
胶带宽度不足 胶带宽度符合产品 要求,不可露铜线 。 绕线胶带
1、露铜线 2、造成耐压不良, 产品功能丧失 3、绕组之间安规距 离不足。
FMEA编号: 共 5页 , 第 1~5 页 编制人: FMEA日期(编制)2015.3.14 FMEA日期(修订) 2016.5.15 措施结果 责任及目标 建议措施 采取的措施 S O D 完成日期
RPN
含浸/烘烤
产品外观凡立水不 产品外观凡立水不能烘 烘干,不能粘手 干,粘手
1、磁芯、线圈松动 2、产品整机使用会 产生异音 3、绝缘度不足易产 生耐压不良或短路
1
20
含浸/烘烤
潜在失效模式及后果分析
(DFMEA)
项目名称:变压器类 核心小组: 过程 要求 功能 组长: 潜在 失效模式 潜在 失效后果 严 重 度 S 级 别 潜在失效 起因/机理 发 生 度 O 现行过程 控制预防 现行过程 控制探测 探 测 RPN 度 D 过程责任部门 :APQP小组 关键日期 : 2015.3.14
2
40
1、造成铜线上挡墙 2、安规距离不足 3、对功能无影响 5
1:选择挡墙厚度不合理 2:定义挡墙圈数不合理
2
50
理线
1、产品外观不符, 理线缠线不能超出 理线缠线超出线架凸点高 量产难度大,客户 线架凸点高度 度 装板浮高。
5
1:引出线股数太多; 2:引出线线径太大; 3:骨架凸点太低.
1:重新选择引出线股数; 5 2:重新选择引出线线径; 3:重新选择高凸点骨架.
FMEA失效模式及后果分析
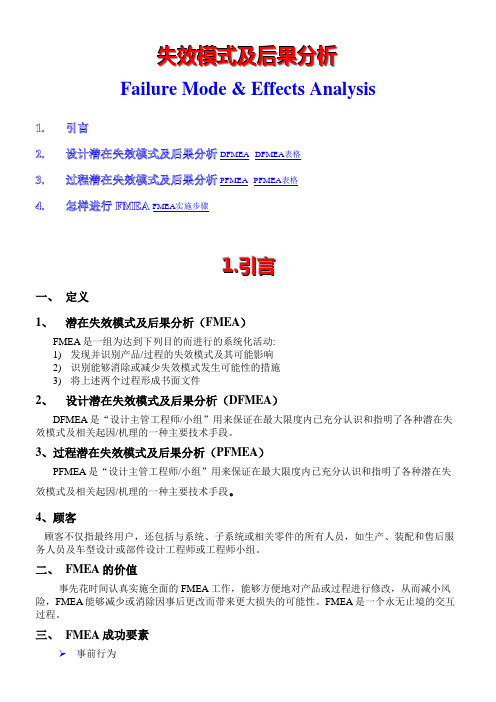
失效模式及后果分析Failure Mode & Effects AnalysisDFMEA DFMEA表格PFMEA PFMEA表格FMEAFMEA实施步骤1.引言一、定义1、潜在失效模式及后果分析(FMEA)FMEA是一组为达到下列目的而进行的系统化活动:1)发现并识别产品/过程的失效模式及其可能影响2)识别能够消除或减少失效模式发生可能性的措施3)将上述两个过程形成书面文件2、设计潜在失效模式及后果分析(DFMEA)DFMEA是“设计主管工程师/小组”用来保证在最大限度内已充分认识和指明了各种潜在失效模式及相关起因/机理的一种主要技术手段。
3、过程潜在失效模式及后果分析(PFMEA)PFMEA是“设计主管工程师/小组”用来保证在最大限度内已充分认识和指明了各种潜在失效模式及相关起因/机理的一种主要技术手段。
4、顾客顾客不仅指最终用户,还包括与系统、子系统或相关零件的所有人员,如生产、装配和售后服务人员及车型设计或部件设计工程师或工程师小组。
二、FMEA的价值事先花时间认真实施全面的FMEA工作,能够方便地对产品或过程进行修改,从而减小风险,FMEA能够减少或消除因事后更改而带来更大损失的可能性。
FMEA是一个永无止境的交互过程。
三、FMEA成功要素➢事前行为➢集体协作➢动态行为➢管理者支持2、设计潜在失效模式及后果分析(Potential Failure Mode and Effects Analysis in Design)一、D FMEA的价值DFMEA的价值体现在如下方面,并且正是由于这些方面的原因减少了设计过程中设计失效的风险。
➢有助于设计要求和设计方案的客观评价➢有助于制造和装配要求的初始设计➢提高了设计开发过程中考虑潜在失效模式及其对系统和车辆运行影响的概率➢对制定全面、有效的设计实验计划和开发程序提供了更多信息➢根据对顾客的影响编制失效模式风险顺序表,据此建立设计改进和开发试验的优先控制系统➢为确定和跟踪降低风险措施提供了一个开放的讨论形式➢为未来分析相关问题、评价设计更改和提高设计水平提供参考二、群策群力DFMEA是集体努力的结果,是集体智慧的结晶。
FMEA潜在失效模式及分析标准表格模版

FMEA 编号Number:页码Page:准备人Prepared By:潜在的失效模式及效应分析表(过程PROCESS FMEA)过程责任部门Process Responsibility: 质量部 QA Dept.项目名称 Item: 关键日期Key Date: 2009.09.07车型年/车辆类工FMEA 编号Number:页码Page:准备人Prepared By:潜在的失效模式及效应分析表(过程PROCESS FMEA)过程责任部门Process Responsibility: 质量部 QA Dept.项目名称 Item: 关键日期Key Date: 2009.09.07车型年/车辆类工FMEA 编号Number:页码Page:准备人Prepared By:潜在的失效模式及效应分析表(过程PROCESS FMEA)过程责任部门Process Responsibility: 质量部 QA Dept.项目名称 Item: 关键日期Key Date: 2009.09.07车型年/车辆类工FMEA 编号Number:页码Page:准备人Prepared By:潜在的失效模式及效应分析表(过程PROCESS FMEA)过程责任部门Process Responsibility: 质量部 QA Dept.项目名称 Item: 关键日期Key Date: 2009.09.07车型年/车辆类工FMEA 编号Number:页码Page:准备人Prepared By:潜在的失效模式及效应分析表(过程PROCESS FMEA)过程责任部门Process Responsibility: 质量部 QA Dept.项目名称 Item: 关键日期Key Date: 2009.09.07车型年/车辆类工machiningFMEA 编号Number:页码Page:准备人Prepared By:潜在的失效模式及效应分析表(过程PROCESS FMEA)过程责任部门Process Responsibility: 质量部 QA Dept.项目名称 Item: 关键日期Key Date: 2009.09.07车型年/车辆类工FMEA 编号Number:页码Page:准备人Prepared By:潜在的失效模式及效应分析表(过程PROCESS FMEA)过程责任部门Process Responsibility: 质量部 QA Dept.项目名称 Item: 关键日期Key Date: 2009.09.07车型年/车辆类工FMEA 编号Number:页码Page:准备人Prepared By:潜在的失效模式及效应分析表(过程PROCESS FMEA)过程责任部门Process Responsibility: 质量部 QA Dept.项目名称 Item: 关键日期Key Date: 2009.09.07车型年/车辆类工FMEA 编号Number:页码Page:准备人Prepared By:潜在的失效模式及效应分析表(过程PROCESS FMEA)过程责任部门Process Responsibility: 质量部 QA Dept.项目名称 Item: 关键日期Key Date: 2009.09.07车型年/车辆类工FMEA 编号Number:页码Page:准备人Prepared By:潜在的失效模式及效应分析表(过程PROCESS FMEA)过程责任部门Process Responsibility: 质量部 QA Dept.项目名称 Item: 关键日期Key Date: 2009.09.07车型年/车辆类工。
潜在失效模式及后果分析表
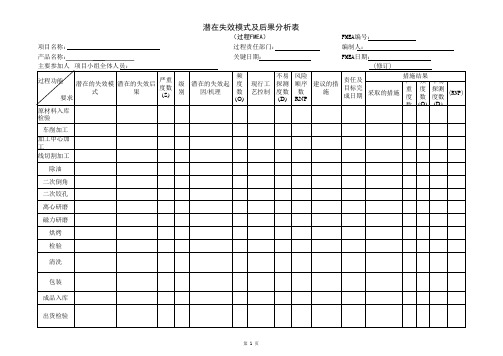
FMEA编号:
项目名称:
过程责任部门:
编制人:
产品名称:
关键日期:
FMEA日期:
主要参加人 项目小组全体人员:
(修订)
过程功能 要求
潜在的失效模 式
潜在的失效后 果
严重 度数 (S)
级 别
频 潜在的失效起 度
因/机理 数
(O)
现行工 艺控制
不易 探测 度数
(D)
风险 顺序
数
RNP
建议的措 施
责任及 目标完 成日期
风险 顺序
数
RNP
建议的措 施
责任及 目标完 成日期
措施结果 严 频 不易
采取的措施
重 度
度 数
探测 度数
(RNP)
数 (O) (D)
原材料入库
检验
车削加工 加工中心加 工 线切割加工
除油
二次倒角
二次铰孔
离心研磨
磁力研磨
烘烤
检验
清洗
包装 成品入库
出货检验
第1页
潜在失效模式及后果分析表
(过程FMEA)
潜在失效模式及后果分析表
(过程FMEA)
FMEA编号:
项目名称:
过程责任部门:
编制人:
产品名称:
关键日期:
FMEA日期:
主要参加人 项目小组全体人员:
(修订)
过程功能 要求
潜在的失效模 式
潜在的失效后 果严重Fra bibliotek度数 (S)级 别
频 潜在的失效起 度
因/机理 数
(O)
现行工 艺控制
不易 探测 度数
(D)
措施结果 严 频 不易
采取的措施
设备潜在失效模式及后果分析
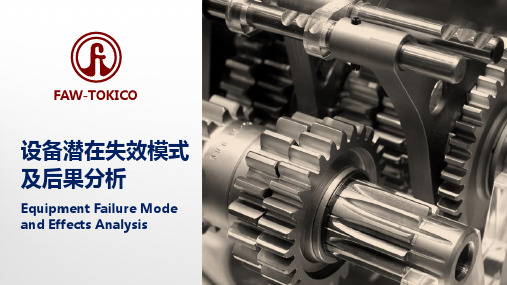
S O D RPN 维修策略 预防措施 5 1 1 1 3 2 3 1 1 15 状态维修 3 2 更换密封 圈 调节节流 阀
事后维修 润滑导杆 事后维修
2
3
1
4 2
6
事后维修 检查保护
优化保护 措施
10 1 7 1
40 改善维修
14 状态维修 点检巡检
设备潜在失效模式及后果分析表
17
一汽东机工减振器有限公司成都公司 保障组
想。
二、EFMEA的输出为制定设备维修和管理提供可靠 的依据。
设备FMEA分析实施目的
4
一汽东机工减振器有限公司成都公司 保障组
• EFMEA计划 • 失效模式 • 失效模式产生的原因、后果、频度、探 测度、严重度
• 风险分析和潜在的失效模式及后果分析
• 预防措施的制定并验证其有效性
EFMEA的基本要素和组成部分
各项未考虑的失效 模式的发现、评审 和更新
修正 EFMEA2
各项未考虑的失效 模式的发现、评审 和更新
动态的EFMEA文件
10
EFMEA分析的三个量化指标包括:严重度S、频度O、探测度D。
设备EFMEA严重度S的评估
等级 1 2 3 4 5 故障严重程度 设备事故:事故可能使在故障或操作期间涉及到个人的安全问题; 或不适合该生产线继续从事生产任务。 严重故障:严重失效,修复时间TI≥1440min或出现因设备精度 下降产生废品。 中等故障:主要的失效,需长期的修理,480min≤TI< 1440min或影响到设备的精度,被设备的操作人员注意到并在设 备技术人员的作用下得到纠正。 轻微故障:一般的失效,需要短期的修理,60min≤TI<480min 。 设备异常:较小的失效,对设备的使用无主要影响,修复时间TI <60min。 评分(S) 9-10 6-8 4-5 2-3 ≤2 不可修复
DFMEA设计潜在失效模式及后果分析表模板

8
Designer wrong input dimension data 设计人员标错尺寸
1. According design SOP (XJ-SJ-SOP-001)
3
2. Design leader re-check design 依照设计SOP参考,双人确认图档无误后,主管
Check Key dimension in CAD file
1. According design SOP (XJ-SJ-SOP-001)
0
2. Design leader re-check design
Remove shrinkage ratio to recheck
依照设计SOP参考,双人确认图档无误后,主管 3D dimension
1
确认
0
Team leader approve 设计开发部负责人审核确认
CNC加工
Electrode discharge allowance does Tooling dim. issue and product dim.
not match
failure
电机放电余量不符
影响模具尺寸,产品超尺寸公差
7
1. Gate desige/loacation issue 浇口方式不合理
Tooling Design 模具设计
Shrinkage issue 产品缩水率错误
Scrap mold core 模仁报废
Wrong dimension issue 尺寸标准错误
1.Fail to production 2.Fail to meet tooling schedule 3.Add tooling cost 模具不能量产/交期滞后/增加成本
潜在失效模式及后果分析(PFMEA)
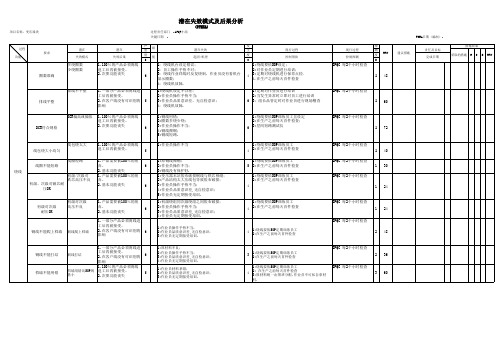
过程 要求 功能
潜在 失效模式
潜在 失效后果
潜在失效 起因/机理
现行过程 控制预防
现行过程 控制探测
焊锡不能虚焊,假焊, 焊锡虚焊,假焊,包 2.有外观项目上的问题,并 焊 包焊 且被绝大多数顾客( >75% )
察觉到 1.100%的产品在处理前,必 须在线返工。 2.有外观项目上的问题,并 焊锡不能太深 焊锡太深 且被绝大多数顾客( >75% ) 察觉到 一次焊锡 1.100%的产品在处理前,必 须在线返工。 焊锡焊满变压器引脚1圈 焊锡不能焊满变压 2.有外观项目上的问题,并 (360°) 器引脚1圈(360°) 且被绝大多数顾客( >75% ) 察觉到 1.100%的产品在处理前,必 须在线返工。 焊锡后PIN要光亮 焊锡后PIN不光亮 2.有外观项目上的问题,并 且被绝大多数顾客( >75% ) 察觉到 1.100%的产品在处理前,必 须在线返工。 胶布用错比SOP规 2.有外观项目上的问题,并 胶布不能用错 格小 且被绝大多数顾客( >75% ) 察觉到 1.100%的产品在处理前,必 须在线返工。 胶布用错比SOP规 磁芯背胶 2.有外观项目上的问题,并 胶布不能用错 格大 且被绝大多数顾客( >75% ) 察觉到 1.100%的产品在处理前,必 须在线返工。 2.有外观项目上的问题,并 胶布歪斜 胶布不能歪斜 且被绝大多数顾客( >75% ) 察觉到 1.100%的产品在处理前,必 须在线返工。 2.有外观项目上的问题,并 点黑胶面积太大 且被绝大多数顾客( >75% ) 察觉到 点黑胶正确 1.100%的产品在处理前,必 须在线返工。 点黑胶 2.有外观项目上的问题,并 点黑胶面积太小 且被绝大多数顾客( >75% ) 察觉到 1.100%的产品在处理前,必 须在线返工。 2.有外观项目上的问题,并 黑胶需要烘干 黑胶不能烘干 且被绝大多数顾客( >75% ) 察觉到
新版潜在失效模式及后果分析(FMEA)1

例举本次分析的产品失效模式:
31
➢ 步骤四:失效分析
失效链 FMEA中对失效的分析包括三个不同方面 ▲失效影响(FE) ▲失效模式(FM) ▲失效起因(FC)
30
➢ 步骤四:失效分析
失效 系统和子系统的失效模式描述是功能损失或退化。 功能的失效由功能推导而来。潜在失效模式包括但不限于以下 种: • 功能丧失(即无法操作、突然失效) • 功能退化(即性能随 间损失) • 功能间歇(即操作随机开始 停止 开始) • 部分功能丧失(即性能损失) • 非预期功能(即在错误的时间操作、意外的方向、不相等的性能) • 功能超范围(即超出可接受极限的操作) • 功能延迟(即非预期时间间隔后的操作) 例如:当向左打方向盘时,车辆向右转,这是非预期功能;
FMEA的定义和分类
FMEA的术语定义
• 失效(failure): 是指产品丧失规定功能的状态,又可译为故障。 失效与故障在含义上略有差别,失效是对不可修复产品而言;故障 是对可修复产品而言的。这里的失效含有这两方面的含义。
* 潜在失效模式(failure mode): 是指可以发生,但不一定非 得发生的失效模式,这时工程技术人员对设计、制造和装配过程中 认识到或感觉到的可能存在的隐患。
24
➢ 步骤二:结构分析
3.系统结构可视化:
灯泡
3
总成
4
D
极板
5
E
+ 零件
A.灯 罩
B.电 池
C.开 关
D.灯泡总成
E.电 极
潜在失效模式分析(PFMEA)样板-1
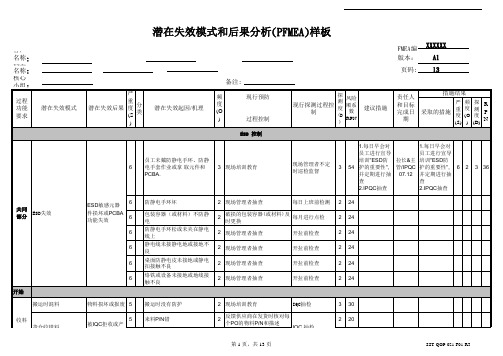
1.不同的Model 之间有相似 的的钢网设计 2.钢网上的P/N标示错误或没 标示 1.印刷速度或刮刀压力设置 不当 2.钢网孔堵塞或漏开孔 3.刮刀两边红胶收拢不及时 4.PCB板表面清洁度不够 5.红胶开封时间太长或过期 1.印刷速度或刮刀压力设置 不当 2.红胶开封时间太长或过期 3.印刷偏移位 1.钢网孔偏位 2.程序设定偏位
1.定期培训员 工"电子元件 基础知识"并 实践考核 2.每站物料上 6 线时依BOM 描述需要测量 其阻容值并记 PIE 录 /操作员 3.开线换线后 Dec-07 由技术员确认 所有方向性器 件的"方向标 示"并贴装首 6 件确认 4.换料时由两 人互检确认 5.IPQC 抽验
2
3 36
2
3 36
2
3 36
共同 ESD失效 部分
ESD敏感元器 件损坏或PCBA 功能失效
6 6 6 6 6 6
防静电手环坏 包装容器(或材料)不防静 电 防静电手环松或未夹在静电 线上 静电线未接静电地或接地不 良 桌面防静电皮未接地或静电 扣接触不良 烙铁或设备未接地或地线接 触不良
2 现场管理者抽查 2
每日上班前检测
潜在失效模式和后果分析(PFMEA)样板 样板 潜在失效模式和后果分析
FMEA编号: XXXXXX 客户名称: 机型名称: 核心小组:
严 重 分 潜在失效后果 度 类 (S ) 频 度 (O )
XXXXXX XXXXXX
过程责任部门:SMT&MI&TEST
编制者:
版本: 页码:
A1 13
备注:
现行预防
2 2 2 2 2 2
破损的包装容器(或材料)及 每月进行点检 时更换 开拉前检查
潜在失效模式及后果分析表
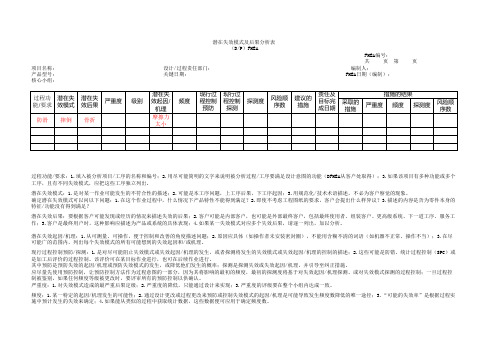
潜在失效模式及后果分析表(D/P)FMEAFMEA编号: 共 页 第 页项目名称: 设计/过程责任部门: 编制人:产品型号: 关键日期: FMEA日期(编制):核心小组:过程功能/要求:1.填入被分析项目/工序的名称和编号;2.用尽可能简明的文字来说明被分析过程/工序要满足设计意图的功能(DFMEA从客户处取得);3.如果该项目有多种功能或多个工序,且有不同失效模式,应把这些工序独立列出。
潜在失效模式:1.是对某一作业可能发生的不符合性的描述;2.可能是本工序问题,上工序后果,下工序起因;3.用规范化/技术术语描述,不必为客户察觉的现象。
确定潜在失效模式可以问以下问题:1.在这个作业过程中,什么情况下产品特性不能得到满足?2.即使不考虑工程图纸的要求,客户会提出什么样异议?3.描述的内容是否为零件本身的特征/功能没有得到满足?潜在失效后果:要根据客户可能发现或经历的情况来描述失效的后果;2.客户可能是内部客户,也可能是外部最终客户,包括最终使用者、组装客户、更高级系统、下一道工序、服务工作;3.客户是最终用户时,这种影响应描述为产品或系统的具体表现;4.如果某一失效模式对应多个失效后果,请逐一列出,加以分析。
潜在失效起因/机理:1.从可测量、可操作,便于控制和改善的角度描述问题;2.原因应具体(如操作者未安装密封圈),不能用含糊不清的词语(如机器不正常、操作不当);3.在尽可能广的范围内,列出每个失效模式的所有可能想到的失效起因和/或机理。
现行过程控制预防/探测:1.是对尽可能阻止失效模式或失效起因/机理的发生,或者探测将发生的失效模式或失效起因/机理的控制的描述;2.这些可能是防错、统计过程控制(SPC)或是加工后评价的过程控制。
该评价可在某目标作业进行,也可在后续作业进行。
其中预防是预防失效的起因/机理或预防失效模式的发生,或降低他们发生的概率;探测是探测失效或失效起因/机理,并引导至纠正措施。
潜在的失效模式及后果分析FMEA
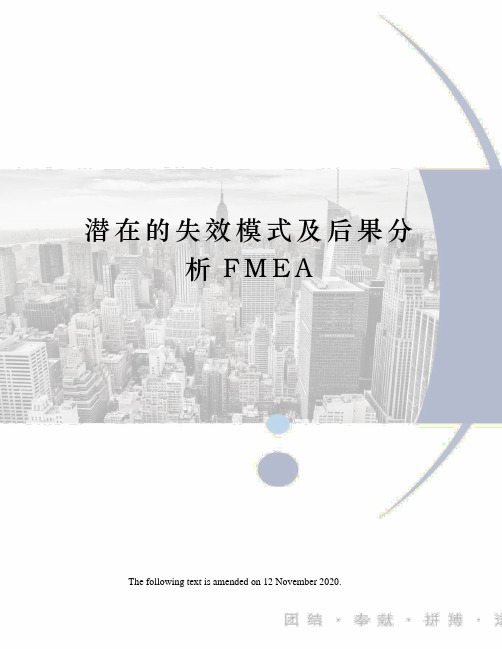
潜在的失效模式及后果分析F M E AThe following text is amended on 12 November 2020.潜在的失效模式及后果分析(FMEA)第1章概论什么是FMEA潜在的失效模式及后果分析(英文:Potential Failure Mode and Effects Analysis.简称 FMEA)。
是在产品/过程/服务等的策划设计阶段,对构成产品的各子系统,零部件,对构成过程,服务的各个程序逐一进行分析,找出潜在的失效模式,分析其可能的后果,评估其风险,从而预先采取措施,减少失效模式的严重程度,降低其可能发生的概率,以有效地提高质量与可靠性,确保顾客满意的系统化活动。
FMEA是一种系统化的工作技术和模式化的思考形式。
FMEA就是及早地指出根据经验判断出的弱点和可能产生的缺陷,及其造成的后果和风险,并在决策过程中采取措施加以消除。
FMEA是一个使问题系统地得到合理化解决的工具,实际上也是目前全世界行之有效的预防手段,实施FMEA就是根据经验和抽象思维来确定缺陷,在研究过程中系统地剔除这些缺陷的工作方法,它可划分为三个方面:SFMEA-系统FMEADFMEA-设计FMEAPFMEA-过程FMEAFMEA的历史世界上首次采用FMEA这种概念与方法的是在20世纪60年代中期美国的航天工业。
进入70年代,美国的海军和国防部相继应用推广这项技术,并制订了有关的标准。
70年代后期,FMEA被美国汽车工业界所引用,作为设计评审的一种工具。
1993年2月美国三大公司联合编写了FMEA手册,并正式出版作为QS9000质量体系要求文件的参考手册之一,该手册于1995年2月出版了第2版。
1994年,美国汽车工程师学会SAE发布了SAE J1739-潜在失效模式及后果分析标准。
FMEA还被广泛应用于其他行业,如粮食、卫生、运输、燃气等部门。
为什么要进行FMEA工程中大量的事实证明,由于策划设计阶段疏忽,分析不足,措施不够,以至造成产品/过程/服务等投入运行时严重程度不同的失效,给顾客带来损失,甚至产生诸如“挑战者”号航天飞机爆炸的惨痛事故。
潜在失效模式及后果分析FMEA

9
很高
车辆/系统无法运行(丧失基本功能)。
8
高
车辆/系统能运行,但性能下降。顾客很不满意。
7
中等
车辆/系统能运行,但舒适性/方便性方面失效。顾客不满意。
典型的失效模式可以是,但不限于下列情况:
破碎 粘结
滑动(无法保持全扭力)
变形 氧化
无法支撑(构造的)
松动 断裂
支撑不足(构造的)
泄露 无法传递扭力 粗糙的接合
脱离过快 信号不适当 间歇信号 无信号
EMC/RFI 漂移
注:应该用“物理的”、专业性的术语来描述潜在失效模式,而不同于顾客所 见的
现象。
11)潜在失效后果 潜在失效的后果就是失效模式对功能的影响,就如顾客感受 的一样。
典型的失效后果可能是,但不限于:
噪音
外观不良
粗糙
不适的异味
运行不良
不稳定
无法运作
运行减损
间歇运行 发热 泄露 定期的不符合
12)严重度(S)
严重度是对一个已假定失效模式的最严重影响的评价等级。 严重度是在单独FMEA范围内的一个比较级别。要减少失效 严重度级别数值,只能通过设计变更来实现。严重度应该 使用下一张的指南来评价:
FMEA Potential Failure Mode and Effects Analysis
潜在失效模式及后果分析
什么是FMEA
FMEA可以描述为一组系统化的活动,其目 的是:
发现和评价产品/过程中潜在的失效及其失 效后果;
找到能够避免或减少这些潜在失效发生的 措施;
将上述整个过程文件化。
轻 突然爆破的严重度,“安全带”可以减轻车辆撞击的
严 重度。
推荐的DFMEA严重度评价准则